
ТСП конспект
.pdf
Скорость охлаждения при наплавке валика на массивное тело:
ωОХЛ = |
2πλ(T − T )2 |
|
0 |
. |
|
|
||
|
q / v |
При сварке листа со сквозным проплавлением
ωохл = |
2πλcρ(T − T0 )3 |
. |
|
||
|
q /(vδ )2 |
6.2 Зона термического воздействия при сварке низкоуглеродистых сталей
Низкоуглеродистые нелегированные стали малочувствительны к скорости охлаждения и практически не закаливаются с получением мартенситных структур.
Характер структур в отдельных участках зоны термического влияния можно получить путем сопоставления кривой распределения максимальных температур с диаграммой состояния сплава (рис 6.3).
Рис. 6.3. Структурные превращения в зоне термического влияния при сварке малоуглеродистой стали. Участки: 1 – неполного расплавления; 2 – перегрева; 3 – нормализации; 4 – неполной кристаллизации; 5 –
рекристаллизации; 6 – синеломкости.
Металл, который при сварке нагревался ниже 7000С, не претерпевает структурных превращений. Однако при сварке стали, подвергшейся действию наклепа (например, вследствие холодного проката), происходит рекристаллизация: из вытянутых и раздробленных вследствие наклепа зерен вырастают новые, равноосные зерна. Структура участка рекристаллизации состоит из равноосных зерен феррита и перлита, в отличие от вытянутых, деформированных зерен основного металла, подвергшегося до сварки наклепу.
Участок металла, подвергшийся нагреву в пределах температур от АС1 до АС3 (для малоуглеродистой стали примерно в интервале температур 720 – 9000С),
претерпевает неполную перекристаллизацию.
Сущность процесса перекристаллизации заключается в следующем. При нагреве стали до температуры АС1 перлит превращается в зерна аустенита. Зерна
аустенита при температуре эвтектоидного превращения имеет концентрацию
111
углерода, равную 0,83%. При дальнейшем повышении температуры образовавшиеся зерна аустенита стремятся растворить окружающие их зерна феррита, причем каждой температуре соответствует строго определенное количество феррита, перешедшее в твердый раствор аустенита. В связи с этим концентрация углерода в аустените понижается. Растворение феррита в аустените заканчивается при температуре АС3; металл, нагретый выше этой температуры, состоит только из зерен аустенита.
При охлаждении металла процесс протекает в обратном направлении: из аустенита выделяется феррит и при температуре Ar1 происходит эвтектоидное превращение, весь оставшийся аустенит превращается в перлит. Металл, нагревавшийся при сварке до температуры выше АС1, но ниже АС3 проходит только частичную перекристаллизацию, и структура этой зоны весьма своеобразна: наряду со старыми, более крупными зернами феррита, не проходившими перекристаллизацию, имеются новые, мелкие зерна феррита и перлита, располагающиеся в виде «колоний» по границам крупных ферритных зерен, не прошедших перекристаллизацию.
При охлаждении металла, нагретого до температуры несколько выше АС3 (для малоуглеродистой стали 900 – 11000С), мелкозернистость сохраняется: структура этого участка зоны термического влияния, называемого участком нормализации, представляет собой мелкие зерна феррита и участки перлита. Механические свойства металла этой части зоны термического влияния весьма высокие.
При более высокой температуре нагрева (свыше 11000С) образовавшиеся зерна аустенита начинают расти тем интенсивнее, чем выше температура нагрева и чем дольше находится металл при данной температуре. Поэтому при приближении ко шву наблюдается постепенное увеличение размера зерен и в области, прилегающей к границе сплавления, имеются только крупные зерна. Этот участок называют участком перегрева.
Непосредственно к металлу шва прилегает участок неполного расплавления, включающий узкую полоску основного металла, нагреваемую при сварке до температур начала и конца плавления. Этот участок также характеризуется резко выраженной крупнозернистостью.
6.3. Структура и свойства металла зоны термического влияния при сварке закаливающихся сталей
Повышение содержания углерода в стали или введение легирующих элементов в низкоуглеродистые стали значительно затормаживает распад аустенита при охлаждении. При этом снижается температура распада аустенита и в ряде случаев в качестве конечных структур появляется мартенсит – пересыщенный раствор углерода в α-железе.
Склонность стали к получению закаленных структур при распаде аустенита может характеризоваться диаграммами изотермического распада аустенита (S- образными кривыми, рис.6.4). Верхняя часть S-образной кривой характеризует
распад устойчивого аустенита по диффузионному механизму с получением равновесных структур. По мере снижения температуры распада уменьшается
112
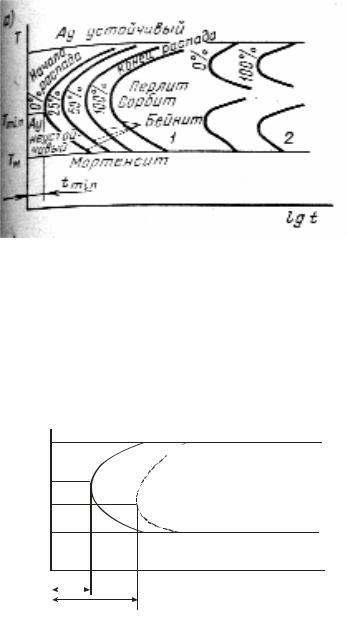
инкубационный период (время существования устойчивого аустенита – левее кривой с 0% превращения). Структура становится дисперсной и носит название сорбита.
Распад аустенита ниже, характерной для каждой стали температуры ТМ,
осуществляется бездиффузионно и конечная мартенситная структура получается при перестройке кристаллической решетки посредством сдвигов.
Превращения ниже температуры минимальной устойчивости аустенита Tmin,
но выше температуры начала мартенситного превращения ТМ имеют промежуточный характер и получаемая при этом структура называется бейнитной.
Рис. 6.4. S-образные кривые.
Чем больше минимальное значение инкубационного периода tmin, тем с большей вероятностью будет получен мартенсит, а не пластинчатые структуры распада аустенита (перлит и др.).
При непрерывном охлаждении (в условиях сварки) зависимости кинетики
распада аустенита от температуры и времени отличаются от его распада при изотермических условиях. На рис. 6.5 показано сопоставление изотермического и
анизотермического распада аустенита для одного типового состава закаливающейся стали (углеродистой с С = 0,45%).
Т
0% 0%
Tmin
Tmin
tmin |
Lg t |
1,5tmin |
Рис. 6.5. Кривые анизотермического распада аустенита.
Из сопоставления следует, что при анизотермическом распаде снижается температура минимальной устойчивости аустенита Tmin и увеличивается инкубационный период, т.е. аустенит становится устойчивее и вероятность образования мартенсита увеличивается. Для многих сталей Т!min = Tmin – 55.
В случае, когда известны кривые распада аустенита, можно схематически
оценить влияние различных скоростей охлаждения металла на получение той или иной конечной структуры, а следовательно, и свойств.
113
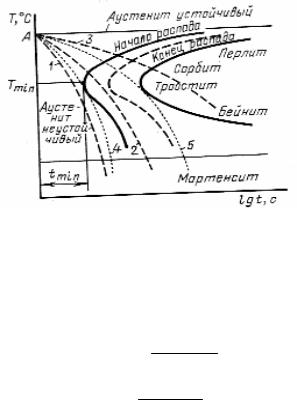
На рис. 6.6 штриховыми кривыми 1, 2, 3 изображены различные скорости охлаждения свариваемой стали при различных способах сварки (дуговой, газовой и электрошлаковой при типичных для них значениях qn). Кривая 1 целиком проходит
внутри инкубационного участка и пересекается только с линией мартенситного превращения, следовательно, конечной структурой будет мартенсит. Кривая 2 пересекается с линией более стабильных продуктов распада – структура в этом случае будет смешанная. Для кривой 3 характерной конечной структурой является сорбит.
Рис. 6.6. Различные скорости охлаждения свариваемой стали при различных способах сварки.
Если пунктирной кривой 4 представить ту минимальную скорость охлаждения wохл1, при которой структура получается полностью мартенситной, а пунктирной кривой 5 – максимальную скорость охлаждения wохл2, при которой мартенсит полностью исключен, то приближенно:
wохл1 = Т1 - Т×min -× 55 ,
2 1,5 tmin
wохл2 = Т×1 - 350× , 2 1,5 t350
где Т1 – температура, соответствующая распаду аустенита при охлаждении с
минимальными скоростями (Ar1), 0С;
Tmin – температура минимальной устойчивости аустенита при распаде в изотермических условиях, 0С;
tmin – минимальное значение инкубационного периода начала распада аустенита (при изотермическом распаде).
Температура 3500С принята как наиболее характерная для мартенситной точки большинства закаливающихся сталей. Поправка к Tmin 550C является обычной для многих сталей для характеристики снижения Tmin при непрерывном охлаждении в сравнении с Tmin при изотермическом распаде.
Поправочный коэффициент 2 в знаменателе обеих формул приближенно учитывает отсутствие достаточной гомогенизации аустенита в период, предшествующий его распаду.
В связи с тем, что хрупкие структуры в сварном соединении могут способствовать образованию трещин из-за протекания деформаций и возникновения внутренних напряжений, они являются весьма нежелательными и в ряде случаев
114
опасными. Технология изготовления сварных конструкций (выбор способа сварки, сварочных материалов, режимов и пр.) должна обеспечить максимальное исключение хрупких структур в сварных соединениях.
6.4 Холодные трещины в сварных соединениях
Свое название они получили в связи с тем, что начало их появления происходит либо при относительно умеренных температурах (значительно ниже, чем температуры горячей обработки), либо при комнатной и более низкой температурах.
Наиболее типичными холодными трещинами являются поперечные трещины в металле швов, поперечные трещины вблизи границы сплавления в околошовной зоне, а также параллельные границе сплавления, так называемые отколы.
В закаливающихся сталях образование холодных трещин связано как с образованием структур с низкими пластическими свойствами (мартенсита), так и с влиянием водорода, растворяющегося при сварке в жидком металле и затем поступающего в околошовную зону.
Одним из наиболее действенных методов для исключения холодных трещин является сварка с предварительным общим или местным подогревом. Это приводит к уменьшению скорости охлаждения при температурах распада аустенита. Степень подогрева зависит от характеристик свариваемой стали, применяемого способа и режимов сварки. Чем более склонной к закалке является сталь и чем менее пластичным получается мартенсит, тем вероятнее образование трещин и тем выше должна быть температура предварительного подогрева перед сваркой.
Основным элементом, увеличивающим закаливаемость сталей, является углерод. Ориентировочно влияние других элементов, в частности легирующих, снижающих скорость распада аустенита, может быть оценено пересчетом их
количества в количество как бы эквивалентно действующего заменяющего их углерода. Одна из наиболее распространенных формул расчета эквивалентного содержания углерода:
СЭ |
= С% + |
Mn% |
+ |
Cr% |
+ |
V % |
+ |
Mo% |
+ |
Ni% |
+ |
Cu% |
+ |
P% |
, |
|
|
|
|
|
|
|
|||||||||
|
6 |
5 |
5 |
4 |
15 |
13 |
2 |
|
причем содержание меди учитывается при Cu ≥ 0,5%, а фосфора при Р ≥
0,05%.
В случае если СЭ больше 0,45 – 0,55, в американской практике рекомендуется применять предварительный подогрев. В отечественной практике ряд сталей повышенной прочности с большим эквивалентным углеродом (примерно до 0,7%)
сваривают дуговой сваркой низководородистыми электродами без подогрева с применением специальной технологии.
Д. Сефериан предложил формулу для расчета эквивалентного углерода, связав ее не только с химическим составом свариваемой стали, но и с толщиной металла, а также расчетную формулу температуры предварительного подогрева.
Тм = 550 – 360*Сэ,
где Тм – температура мартенситного превращения, 0С; СЭ – эквивалентный углерод в стали, %;
115
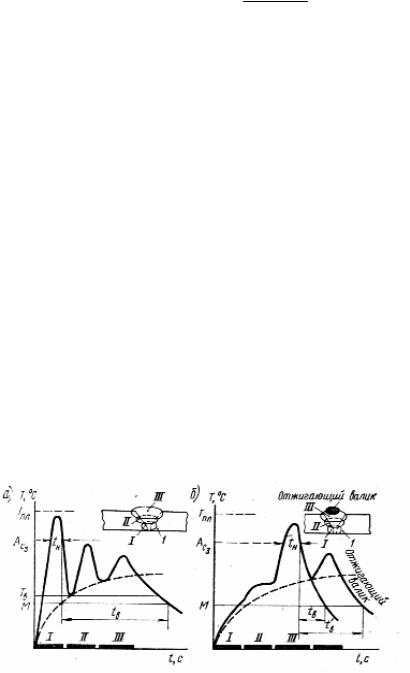
СЭ |
= |
Mn% + Cr% |
+ |
Ni% |
+ |
Mo% |
. |
9 |
18 |
|
|||||
|
|
|
13 |
|
Влияние толщины свариваемого металла (δ, мм) учитывается поправкой С!Э = 0,005δСЭ.
Тогда полный эквивалент углерода С!!Э = СЭ + С!Э = СЭ(1+ 0,005δ),
а температура предварительного подогрева
Т ПОД = 350СЭ!! − 0,25.
Японские исследователи сделали попытку учесть в склонности РС к образованию трещин не только толщину металла, но и содержание в нем водорода:
P = C% + |
Si% |
+ |
Mn% |
+ |
Cr% |
+ |
Ni% |
+ |
Cu% |
+ |
Mo% |
+ |
V % |
+ 5B + δ 2 |
+ |
H |
, |
|
|
|
|
|
|
|
|
||||||||||
C |
30 |
20 |
20 |
60 |
20 |
15 |
20 |
60 |
60 |
|
|||||||
|
|
где δ – толщина свариваемой стали, мм; Н – концентрация в шве водорода,
см3/100 г.
Температура подогрева:
ТПОД = 1440РС – 3920С (для температуры воздуха 13 – 25 0С).
В отечественной практике стараются избегать предварительного подогрева, применением либо аустенитных, либо низководородистых материалов. Высокопрочные стали (120 – 150 кгс/мм2) предпочитают сваривать также без подогрева, создавая специальными приспособлениями сжимающие напряжения в районе сварных швов при высоких температурах. Кроме того, после сварки применяется термическая обработка сварных соединений.
При сварке металла большой толщины швы обычно выполняют многослойными. Для борьбы с холодными трещинами в этом случае применяют следующие технологические приемы. Длинный шов разбивают на короткие участки, чтобы было возможно выполнение последующего валика, пока предыдущий валик еще не остыл. Тогда последующий валик выполняется как бы по предварительно подогретому металлу. Схематически термические циклы при многослойной сварке короткими участками показаны на рис. 6.6.
Рис. 6.6. Термические циклы при сварке короткими участками (а – вблизи корня шва; б – вблизи поверхности шва).
Для ручной или полуавтоматической сварки, если осуществлять нагрев следующей тепловой волной, когда металл предыдущего слоя еще не остыл ниже какой-то выбранной температуры ТВ, длина участка шва L:
L = 0,7K |
2 |
K |
|
q2 |
|
3 |
2 |
|
, |
||
δ 2vCB (TB − T0 )2 |
116
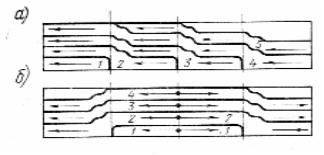
где Т0 – начальная температура изделия, 0С;
ТВ – допустимая температура охлаждения после сварки предыдущего слоя; выбирается несколько выше температуры, опасной для образования трещин;
К3 – поправочный коэффициент, для стыкового соединения К3 = 1,5; для таврового К3 = 0,9;
К2 – коэффициент горения дуги (обычно 0,5 – 0,8).
Есть несколько методов заполнения разделки многослойными швами, выполняемыми короткими участками. Практически применяется сварка блоками, горкой и каскадом рис. 6.7. Сварка блочным способом заключается в разделении всего шва на участки, которые завариваются параллельно несколькими сварщиками.
Рис. 6.7. Сварка каскадом и горкой.
6.5. Изменение свойств металла в околошовных зонах высоколегированных сталей
Наиболее характерными из высоколегированных сталей, применяемых в сварных конструкциях, являются хромистые ферритные, феррито-мартенситные и мартенситные, а также хромоникелевые аустенитные.
К высокохромистым сталям относятся низкоуглеродистые (обычно С ≤ 0,2%) с содержанием хрома от 5 до 30%.
Низкоуглеродистые хромистые стали имеют ограничиваемую содержанием хрома высокотемпературную область γ – раствора (рис. 6.8). Поэтому металл, нагретый выше температуры превращения α → γ, при достаточно быстром охлаждении получает структуру мартенсита. При увеличении концентрации (рис.6.8, б) углерода область хромистых сталей, закаливающихся на мартенсит, расширяется в сторону больших концентраций хрома, а сам мартенсит получается более твердым.
Увеличение концентрации хрома при той же концентрации углерода изменяет сталь так, что при повышенных температурах появляется область смешанного α + γ раствора. Сварочные скорости охлаждения приведут к получению смешанной ферритно-мартенситной структуры. Такая структура также характеризуется достаточно высокой твердостью, хотя с точки зрения образования трещин является менее опасной.
Эти стали сваривают сварочными материалами, при которых металл шва оказывается подобным свариваемому (предварительный подогрев до 300 – 5000С), либо материалами, обеспечивающими получение в шве металла с аустенитной структурой.
117
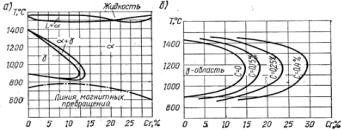
Рис. 6.8. Структурная диаграмма состояния Fe – Cr и влияние углерода на расширение γ – раствора.
Более высокохромистые стали, при том же содержании углерода, имеют полностью ферритную структуру. Они не претерпевают превращений от комнатной температуры до температуры плавления. При нагреве до высоких температур и последующем охлаждении такие стали получают значительное увеличение зерна. Хотя такая структура и не приводит к увеличению твердости, однако металл
обладает малой деформационной способностью и в нем могут образовываться трещины. Сварка таких сталей производится с невысоким (около 2000С) предварительным подогревом.
Хромоникелевые стали аустенитного класса применяются как нержавеющие, кислотостойкие и жаропрочные. Они содержат от 15 до 25 % Cr и от
8 до 35 % Ni при содержании углерода до о,14 % и некоторых других элементов: Mo, V, Ti, Nb. Типичным представителем этой группы сталей является нержавеющая с 18 % Cr; 9 % Ni и 0,1% С. Такая сталь получает наилучшие свойства после аустенизации при Т = 1050 – 11000С и быстрого охлаждения. После такой обработки в металле фиксируется состояние аустенита, растворившего повышенное для комнатной температуры количества углерода. Последующий нагрев такого металла в определенной области температур способствует образованию карбидов хрома, выпадающих в основном вблизи границ зерен. Раствор в этом месте обедняется не только углеродом, но и хромом. Неоднородность состава (карбид; раствор, обедненный хромом у границ зерен, и нормальный в центре зерна, с различными электрохимическими потенциалами) вызывает склонность стали к развитию коррозии от поверхности внутрь металла по границам зерен (межкристаллитной коррозии).
Сварные соединения, обладающие необходимой стойкостью против межкристаллитной коррозии, можно получить, когда и шов, и околошовная зона не проявляют склонности к МКК. Для этого основной металл при ограничении в нем углерода обычно легируют титаном, а сварочные материалы подбирают с еще более низким содержанием углерода, легированные титаном или ниобием. При этом
автоматическая сварка под бескислородными флюсами и аргонодуговая сварка позволяют в металле шва сохранить необходимое количество титана. При ручной
дуговой сварке с применением любых покрытий титан почти полностью выгорает и в этом случае для легирования предпочитают в качестве стабилизатора применять ниобий или для более простых условий эксплуатации изделий – молибден.
В металле швов полезно иметь не чисто аустенитную, а аустенитно- ферритную структуру с содержанием ферритной фазы до 10 – 15%. Получение
двухфазной структуры определяется соотношением между количествами ферритобразующих (Cr, Mo, Si, Ti) и аустенитобразующих (Ni, C, N, Mn) элементов. Структурная диаграмма Шеффлера (рис. 6.9) связывает эквивалентные количества
118
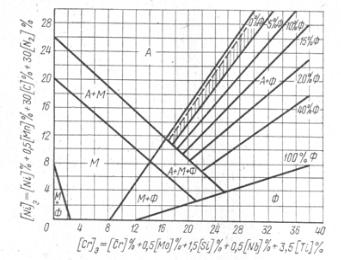
никеля и хрома с конечными структурами металла шва, получающимся после сварочных скоростей охлаждения.
Рис. 6.9. Структурная диаграмма Шеффлера.
6.6 Технологическая свариваемость металлов
Совокупность свойств металла, определяющих чувствительность к
термическому циклу сварки и способность образовывать сварное соединение со свойствами, удовлетворяющими требованиям надежности конструкции при эксплуатации, называют технологической свариваемостью.
Разница между металлами, обладающими хорошей или плохой свариваемостью, состоит в том, что последние должны свариваться по более сложной технологии, например с предварительным и сопутствующим подогревом, с обязательной последующей термообработкой и т.д.
Отехнологической свариваемости металлов и сплавов надо судить не только
всвязи с их свойствами, но также учитывать размеры конструкции, ее назначение, расположение и условия работы швов, т.е. при оценке свариваемости должна учитываться тесная взаимосвязь материалов, конструкции и технологии сварки.
Первым видом испытаний свариваемости является определение стойкости против образования горячих трещин.
Технологическая проба для определения стойкости металла шва против образования горячих трещин производится путем сварки контрольного – углового шва 1 (рис.6.10) таврового соединения с ребрами жесткости. Контрольный шов сваривается на оптимальном режиме, применяемом для данной толщины металла и марки стали. Выявление трещин производят путем внешнего осмотра шва, а также осмотра излома после разрушения шва или по макрошлифам, вырезанным из шва.
Метод позволяет получить лишь качественную характеристику стойкости против образования горячих трещин. Аналогично проверяется и стыковой шов в закрепленной на жестком основании пластине.
119
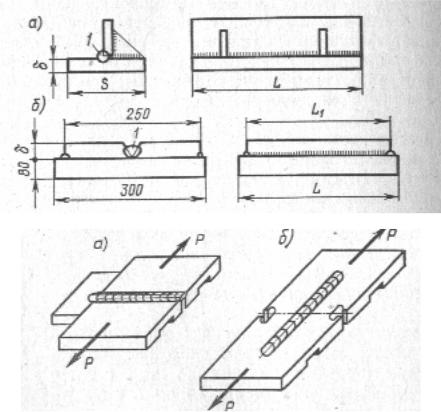
Метод МВТУ (рис. 6.11) позволяет количественно определить стойкость металла против горячих трещин. Специальные образцы с поперечным или
продольным швами в процессе сварки растягивают с постоянной скоростью и определяют критическую скорость деформации, вызывающую образование трещин.
Рис. 6.10. Технологическая проба для испытаний на стойкость против образования горячих трещин
Рис. 6.11. Метод МВТУ
Вторым видом испытания свариваемости является определение стойкости металла против образования холодных трещин. Испытания проводятся путем сварки
или наплавки специальных образцов различной степени жесткости и при различной скорости охлаждения околошовной зоны. Для примера приведем пробу ЦНИИТМАШ (рис. 6.11) и образцы, имитирующие реальное сварное соединение
(рис.6.12).
120