
Подземная разработка месторождений
.pdf
1-й способ — линия забоя располагается вертикально, подэтажи обуриваются снизу и сверху из подрезных ортов шпурами глубиной по 2—2,5 м.
По сравнению со 2-м способом — расположением линии забоя потолкоуступно — он более безопасен, так как в нем при недостаточно устойчивой руде, наличии в ней скрытых крупных трещин и слабом контакте возможно массовое обрушение —
сползание |
нависающей части подэтажа. |
|
Высота |
подэтажа при обоих способах ограничивается |
глубиной шпуров, |
которые возможно выбурить обычными бурами из подрезного орта высотой 2—2,5 м. При глубине шпура 2,25 м высота подэтажа может быть получена до
2,5+2,0*2+ 1,5 = 8,5 м,
3-й способ — обуривание подэтажа глубокими восстающими «штанговыми» шпурами
— описан при изложении типового варианта (см. рис. 4.5.). Особым его достоинством является возможность увеличения высоты подэтажа до 10—12 м (редко до 15 м). Из недостатков можно указать на: 1) повышенную крупность кусков, получающихся при взрыве, в связи с чем часто возникает необходимость в устройстве горизонта дробления;
Рис. 4.7. Способы отбойки подэтажей
2) известную трудность контроля за полнотой отрывания руды у контактов, особенно при большой прочности и неровности последних. Этот недостаток оказывается более ощутительным при разработке камерами по простиранию, особенно при сравнительно небольшой мощности рудного тела. Заложение глубоких шпуров с тяжелыми зарядами очень близко к контакту приводит к раздроблению боков, нарушению их прочности и разубоживанию; при увеличении же расстояния часть руды, особенно в неровностях боков, остается невзорванной и теряется.
4-й способ — отбойка только нисходящими шпурами применяется при очень крепкой, устойчивой руде. Подэтажная толща высотой до 8—10 м обуривается за 3— 4 приема ш п у р ами глубиной 2—3 м. Минимальная глубина шпуров, ограниченная высотой подрезного орта, берется на верхнем уступе и увеличивается до 3—4 м
151
на нижних. В зависимости от крепости руды, характера контакта, наличия горизонта дробления паление шпуров может производиться с простреливанием и без такового.
5-й способ - отбойка «круговыми комплектами шпуров существенно отличается от
предыдущих |
тем, что бурение шпуров производится непосредственно |
из |
подэтажного |
штрека (или орта) без проведения подрезных заходок. В одном |
«круговом» комплекте выбуривается от 12 до 25 шп уров глубиной по 2—2,5 м. Расстояние между комплектами 1,2—1,5 м. При мощности месторождения свыше 7—8 м на каждом подэтаже проводятся два параллельных штрека. Этот способ представляет практический интерес при разработке неустойчивых, трещиноватых руд,
когда работа из подрезных ортов становится опасной. |
|
|
|
6-й способ применяется очень редко, при |
недостaточно устойчивых рудах, когда |
||
нависающие уступы при обычных методах |
отбойки |
могли |
бы обрушиться. |
Значительные затраты труда на отгребку руды, попадающей в заходки нижележащих подэтажей при отбойке вышележащих, составляет большой его недостаток. Так как система подэтажных штреков в недостаточно устойчивых рудах имеет очень ограниченное применение, то данный способ отбойки большого практического значения не представляет.
Особое место при системе разработки подэтажными штреками занимает отбойка руды глубокими скважинами.
Глубокие скважины на рудниках ОАО «ППГХО» уже много лет в широком масштабе применяют для массовой отбойки как запасов между подэтажами, так запасов потолочных и междукамерных целиков. Расстояние между подэтажами (почва вышележащего подэтажа – кровля нижележащего подэтажа составляет в среднем 12. Бурение вееров скважин осуществляется буровыми станками НКР-100М диаметром 75-100 мм. Расстояние между веерами скважин в зависимости от диаметра скважин составляет 1,2 – 1,8 м, расстояние между концами скважин в веере также равно 1,2 – 1,8 м. Т.е. при бурении создается квадратная сетка, что позволяет все запасы обурить с равномерной плотностью и создать гарантированные условия для полной отбойки запасов с заданной крупностью куска.
Повышение эффективности использования данной системы разработки может быть достигнута с помощью предлагаемого ниже способа (патент на изобретение №
2223401).
Сущность данного способа состоит в том, что способ разработки крутопадающих и наклонных месторождений, включающий проходку подготовительно-нарезных выработок, подэтажную выемку полезного ископаемого камерами, формирование под висячим боком подэтажа временного рудного целика с обнаженной стенкой, оформляемой под наклоном, противоположным углу падения рудного тела, образование отрезной щели на высоту подэтажа, отбойку руды в камере взрывными скважинами последующее обрушение целика и выпуск отбитой руды через выпускные выработки, отличается тем, что отбойку руды и породных прослоев осуществляют раздельно наклонными слоями, отрезную щель и отбиваемые слои оформляют согласно с элементами залегания рудного тела, а обнаженную стенку временного рудного целика оформляют под углом, равным углу сдвижения рудного массива, причем часть массива, ограниченную с одной стороны отрезной щелью и с другой - обнаженной стенкой временного рудного целика, отбивают в первую очередь, часть массива, ограниченного с
152
одной стороны отрезной щелью и с другой - лежачим боком - во вторую очередь, а в третью - производят обрушение временного рудного целика.
Вертикально оформленные отрезная щель и отбиваемые слои пересекает руду и породные прослои. Процесс их раздельной выемки с применением скважинной отбойки в этом случае существенно усложняется, во-первых, за счет разрушения взрывных скважин, пересекающих разно-прочные руды и породные прослои, и, во-вторых, вследствие засорения отбитой руды породами прослоев и снижения за счет этого полноты и качества извлечения полезного ископаемого из недр. Напротив - оформление отрезной щели и отбиваемых слоев согласно с элементами залегания рудного тела создает благоприятные условия для раздельной выемки руды и породных прослоев, согласных с элементами залегания рудного тела. При этом достигается необходимая устойчивость стенок как отрезной щели, так и отбиваемых слоев, а вероятность самообрушения массива и разрушение взрывных скважин исключаются. Тем самым обеспечиваются высокие качественные и количественные показатели извлечения полезного ископаемого из недр, создаются безопасные условия очистных работ и исключается вероятность разрушения взрывных скважин.
Формирование обнаженной стенки временного рудного целика под углом, равным углу сдвижения массива, существенно снижает вероятность возникновения зоны пиковых нагрузок в области целика, прилегающей к нижней границе его обнаженной стенки, и опасных динамических проявлений горного давления, в частности обрушения массива в нижней части целика. В свою очередь, уменьшение его объема позволяет снизить количественные значения потерь руды при его обрушении.
Применение данного технического решения при отработке рудных тел со сложной морфологией, включающих породные прослои согласные с элементами залегания рудного тела, в условиях с неустойчивыми вмещающими породами позволит повысить полноту и качество извлечения полезного ископаемого из недр, обеспечить безопасные условия ведения очистных работ.
На рис. 4.8. представлены конструктивные элементы данного способа разработки в проекции очистной камеры С-С на вертикальную плоскость вкрест простирания рудного тела. На Рис. 4.9. показан разрез по плоскости А-А
На чертежах изображены: 1 - подэтажные полевые штреки; 2 - буровые орты; 3 - погрузочные заезды; 4 - отрезная щель; 5 - временный рудный целик; 6 - контуры отбиваемых слоев; 7 - породные прослои; 8 - поверхность борта траншеи; 9 - плоскость отбиваемого слоя.
Способ разработки осуществляют следующим образом.
Для выемки запасов крутопадающего или наклонного рудного тела проводят подэтажные подготовительно-нарезные выработки, включающие полевые штреки 1, буровые, доставочные орты 2 и погрузочные заезды 3, после чего в проектных контурах очистной камеры и в пределах высоты подэтажа оформляют отрезной восстающий, располагаемый под углом, равным углу падения залежи а, который посредством скважинной отбойки расширяют до необходимых размеров компенсационного пространства (отрезной щели 4), ориентируемого по простиранию залежи. Расположение отрезной щели под углом, равным углу падения залежи, предотвращает пересечение отрезной щелью породных прослоев, повышая тем самым устойчивость ее стенок и улучшая качественные и коли чественные характеристики попутно добываемой руды.
153

Выемку камерных запасов производят комплектами веерных скважин вкрест простирания рудного тела наклонными слоями 6, причем в первую очередь отрабатывает запасы, ограниченные с одной стороны отрезной щелью 4, а с другой - обнаженной стенкой временного рудного целика 5. Обнаженную стенку временного рудного целика оформляют под углом, равным углу сдвижения массива фс. При этом условии исключается вероятность неконтролируемого обрушения массива, а объем запасов, локализованных в его границах, уменьшается, вследствие чего повышается безопасность работ на всех стадиях очистной выемки и снижаются потери руды при обрушении целика.
Камерные запасы, ограниченные отрезной щелью 4 с одной стороны и лежачим боком - с другой, вынимают во вторую очередь, а временный рудный целик 5 обрушают в последнюю очередь. Оформление отбиваемых слоев 6 под углом, согласным с элементами залегания рудного тела, создает благоприятные условия для раздельной выемки руды и породных прослоев 7, что позволяет, во-первых, снизить уровень первичного (конструктивного) разубоживания, а во-вторых, повысить полноту извлечения полезного ископаемого из недр.
Предлагаемая технология способствует формированию устойчивых стенок камеры. При этом исключается вероятность неконтролируемого обрушения ослабленных рудного и породного массивов, уровни первичного и вторичного разубоживания руды и эксплуатационных потерь снижаются. Кроме того, обеспечиваются безопасные условия ведения очистных работ и исключается вероятность разрушения взрывных скважин.
Рис. 4.8. Проекция блока на вертикальную плоскость
154

Рис. 4.9. Днище камеры
Рис. 4.9.а. Разрез камеры вкрест простирания
Производительность бурильщика при системе подэтажных штреков в зависимости от крепости руды и применяемого способа отбойки изменяется в среднем в пределах от 40-50 до 60—70 т при отбойке мелкими шпурами, а при
отбойке |
скважинами — от |
80—100 до 150 г и более, расход |
взрывчатого |
соответственно — 150—250 и |
120—180 г/т. |
|
Вторичное дробление применяется довольно часто при отбойке скважинами. Оно производится специальном на горизонте дробления или, значительно реже, в камерах, устраиваемых над выпускными люками.
Доставка руды при очистной выемке происходит в осн овном под действием собственного веса. При проведении подземных ортов, подэтажных штреков и заходок применяется погрузодоставочная техника (ПДМ), работающая на пневматической или электрогидравлической основе. Недостатком при использовании ПДМ является то, что сечение подготовительных, нарезных и очистных выработок колеблется в пределах 8,6 –10 м2, что при проходке выработок по пустой породе приводит к отбойке значительного количества пустых пород. Положительным моментом использования ПДМ является - увеличение производительности при подготовке и нарезке блоков, а значитускорение
ввода их в эксплуатацию. |
|
|
Поддержание |
очистного пространства осуществляется междуэтажными |
и |
междукамерными |
целиками. Правильный подбор размеров этих целиков и размеров |
камер в соответствии с устойчивостью руды и боковых пород составляет важное условие безопасного ведения работ. Чрезмерное обнажение кровли и боков камеры или
недостаточные размеры целиков |
может послужить причиной преждевременного, |
|
155 |
иногда массового обрушения боков и потолочины, а отсюда — причиной излишнего разубоживания, небольших или массовых потерь и несчастных случаев.
Толщина потолочного целика устанавливается в зависимости, главным образом, от трех факторов: ширины камеры, длины ее и устойчивости руды. В зависимости от устойчивости и длины камеры потолочине придают толщину в среднем от 0,25 до 0,50 ширины камеры.
Выемку руды непосредственно под потолочиной производят, придавая потолочине по ширине камеры сводообразную форму с тщательной оборкой кровли.
Толщина целика над выработками |
основного |
горизонта обычно не менее 5 |
||
м, а над горизонтом дробления — 3 м. |
Толщина этих |
целиков зависит |
от |
|
принятого расстояния между выпускными дучками, |
так как |
известно, что угол |
наклона воронок должен быть 45—50°, длина же дучки от люка до начала воронки
1,0—1,5 м.
Ширина междукамерных целиков зависит от крепости руды и устойчивости боков, мощности месторождения и других факторов. Расчетных методов для определения размеров этих целиков, так же как и для междуэтажных, не имеется. Минимальная ширина междукамерных целиков при мощности месторождения до 10 м составляет
4—6 м, а при большей — 6—8 м. |
|
|
|
|
|
4.10.1.4. Размеры элементов системы подэтажных штреков и |
отдельные |
||||
|
детали подготовки |
|
|
|
|
Высота |
этажа при системе |
подэтажных штреков слагается из: 1) высоты |
|||
штрека (орта) основного горизонта |
и надштрекового |
целика; |
2) |
толщины |
|
потолочины |
и 3) высоты камеры от горизонта подсечки до потолочины. |
|
|
||
Увеличение высоты этажа до возможных технических пределов при данной |
|||||
системе разработки особенно важно потому, что оно сопровождается |
не |
только |
|||
снижением |
расходов по подготовке на 1 т запасов, но и сокращением |
общих |
потерь руды по этажу за счет снижения доли запасов, заключенных междуэтажных целиках.
Максимальная высота этажа — 75—80 м (очень редко 110 м) принимается при
сравнительно небольшой мощности |
месторождений, падении, |
близком |
к 90°, |
|
крепкой руде |
и весьма устойчивых |
боковых породах, увеличенных |
размерах |
междуэтажных целиков, небольшой длине камер и при наличии горизонта дробления. При разработке без горизонта дробления и прочих равных условиях высота этажа берется на 8—I0 м меньше.
Минимальная высота этажа 45—60 м принимается в условиях, противоположных приведенным.
Длина |
блока при расположении камер по простиранию обычно составляет |
40—60 м |
и определяется как экономическими, так и техническими факторами. |
Из технических факторов длину блока ограничивают: 1) устойчивость боковых пород и допускаемая площадь их обнажения; 2) прочность потолочины, зависящая от ее толщины и устойчивости руды. Хотя на прочности потолочины больше отражается ширина, а не длина камеры, однако совместное влияние длины и
ширины также может оказаться существенным. |
|
Увеличение длины блока выгодно главным образом с точки зрения : |
1) экон омии |
н а п роходк е конц евых восст аю щих , 2) уменьшения |
доли участия |
|
156 |
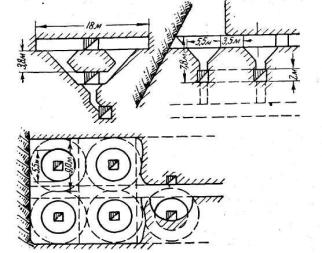
междукамерных целиков в общем запасе блока, а отсюда — уменьшения потерь руды по блоку и перерасходов, связанных с отработкой целиков.
Максимальная длина блоков 100—120 м принимается примерно в тех же условиях, в каких принимается максимальной высота этажа.
Подсечка камеры и образование воронки (рис. 4.10.). Эта стадия работ является наименее производительной при выемке камеры, а между тем объем руды, получаем из подрезки и воронок, составляет от 8—10 до 12—15% и более от запаса камеры.
Общепринятый метод |
подсечки |
заключается |
в проведении из |
нижнего |
|||
подэтажного штрека |
двухстенных |
ортов |
с одвременным обуриванием воронки |
||||
нисходящими шпурами глубиной 1,5—2 м с |
опережением над |
линией очистного |
|||||
забоя на расстояние, |
равное |
диаметру |
одной |
воронки. |
Этот |
способ |
предусматривается правилами безопасности как основной.
Ввиду того, что глубина воронки обычно превышает 4—5 м, полный ее разворот требует обуривания шпуров в несколько приемов. Расход ВВ при подсечке камеры и развороте воронок составляет при руде средней
Рис. 4.10. Подсечка камеры и образование воронок
крепости 200—300 г/т, т. е. примерно в 2—2,5 раза превышает таковой при очистной выемке, а производительность ниже в 3—4 раза.
4.10.1.5. Способы выемки междукамерных и междуэтажных целиков
Все способы выемки целиков можно объединить в две группы, существенно отличающиеся между собой по конструктив ным признакам. Первая группа: способы выемки целиков при заполненных отработанных камерах путем их закладки или перепуска пустых пород с вышележащих этажей. И вторая группа: способы выемки целиков при незаполненных камерах.
По правилам техники безопасности выемка целиков с помощь ю горных выработок разрешается только при условии, когда отработанные камеры заполнены пустой породой, закладкой или рудой. Проведение горных выработок в теле целиков до начала их погашения допускается в минимальном количестве и минимальных размеров.
На практике наиболее распространен следующий порядок выемки целиков. I. Первая стадия. Одновременное расстреливание нескольк их
потолочин, обычно не больше трех, и подпирающих их междукамерных целиков в
157

незаполненные камеры. Вторая стадия. После выпуска руды, полученной от массового взрыва потолочины и междукамерных целиков, выемка днища и целика над основным горизонтом системой подэтажного обрушения (обычно камерные варианты) под обрушенными пустыми породами.
II. Первая стадия. Расстреливание одной потолочины реже одновременно нескольких потолочин) в незаполненную нижележащую камеру. Вторая стадия. Выемка междукамерных целиков каким-либо из вариантов подэтажного обрушения или слоевым обрушением при камерах, заполненных пустой породой. Третья стадия.
Выемка |
днища (целика над |
горизонтом дробления и |
основным горизонтом) |
камерным |
вариантом подэтажного обрушения. |
|
|
При |
массовом обрушении |
междукамерных целиков |
в открытые камеры |
одновременно взрывается один или два таких целика и соответственно — две или три потолочины. В обоих случаях пустые породы, заполняющие выработанное пространство, будут прилегать к соседним невыработанным междукамерным целикам а1 и а2 (рис. 4.10.). Эти целики отрабатывают после обрушения целиков С1 и С2 и заполнения камер в1 и в2 пустой породой. Таким образом, первый и второй порядок выемки междукамерных целиков комбинируются.
Посадка потолочин. Производится глубокими минными скважинами или минными камерными зарядами.
Последний способ в данное время стал при меняться на наш их рудниках довольно редко, только в очень крепких рудах, где нельзя пробурить глубокие минные скважины. Напротивмассовая посадка потолочины глубокими минными скважинами получает все более и более широкое применение и совершенствуется.
|
|
Рис. 4.11. Порядок выемки целиков |
||
На рис. 4.11. показано |
расположение |
минных |
выработок и камерных зарядов в |
|
обрушаемых |
двух потолочинах камер, расположенных вкрест простирания. |
|||
Минные |
рассечки |
М проходятся |
из ортов |
О междукамерных целиков на |
расстоянии 6—7 м одна от другой (между осями). Эти рассечки выходят в контуры
потолочины над |
камерой только на 2,5—3,5 м; полная длина каждой рассечки |
6—7 м. |
|
Камерные заряды К по 100—300 кг укладываются в концах рассечек М, |
|
которые после |
укладки заряда и детонирующего шнура забучиваются отбитой |
рудой.
Расход в. в. на 1 т руды в потолочине составляет при даннном способе отбойки от 100 до 200—250 г.
Недостатки этого метода:
158

1)большой и очень трудоемкий объем работ по проведению минных выработок;
2)неравномерное дробление отбитой руды, наличие, наряду с рудной пылью, огромных глыб, которые требуют вторичного дробления;
3)очень низкий коэффициент извлечения обрушенной руды (обычно не больше
50%);
4) проведение в потолочине горных выработок сопровождается образованием в ней трещин, что может вызвать внезапное обрушение потолочины. В связи с этим применение минных камер для посадки потолочин довольно опасно и допустимо только в крепких, монолитных рудах с высокой устойчивостью.
Посадка потолочин при помощи минных скважин по сравнению с минными камерными зарядами обладают существенными преимуществами:
1) скважины можно равномерно расположить в массиве потолочины и обеспечить равномерное ее дробление при взрыве.
2)требуется во много раз меньше подготовительных работ;
3)работы совершенно безопасны;
4) благодаря равномерному дроблению и мгновенной посадке потолочины по всей ее площади, достигается значительно большее извлечение обрушенной руды при ее выпуске.
Типичное расположение скважин показано на рис. 4.12. При параллельном расположении скважин достигается более равномерное дробление руды, чем при веерном, но зато требует применяется при посадке больше подготовительных выработок. Поэтому в практике наиболее распространено веерное расположение.
|
|
|
|
|
|
|
|
|
|
|
|
|
12. Посадка потолочин минными камерными зарядами |
|
|
||
|
|
|
|
|
|
Пучковое |
|
расположение |
скважин |
||
'применяется при посадке |
|
потолочин большой толщины. |
|||
|
|
|
|
|
|
159

.
Рис. 4.13. Обрушение потолочины параллельными, веерообразными и пучковыми глубокими минными скважинами
4.10.1.6. Выемка междукамерных целиков
Разрез по
Рис. 4.14. Расстреливание междукамерного целика и потолочины глубокими |
|
скважинами |
|
В практике междукамерные целики наиболее часто отрабатывают |
при |
заполненных камерах системами подэтажного или слоевого обрушения. |
|
Массовая посадка междукамерных целиков (одновременно с потолочинами) минными камерными зарядами, глубокими минными скважинами или шпурами, а также комбинацией этих способов отбойки применяется реже потому, что при этом удается извлечь обычно не более 40 % обрушенной руды. Остальная часть руды смешивается при обрушении и выпуске с пустыми породами и оказывается настолько разубоженной, что становится некондиционной.
160