
METODAAA_33__33__33_0001
.pdfсоким сопротивлением контактной усталости и применяется для изготовления шариков, роликов и колец подшипников качения.
К металлургическому качеству стали предъявляются особо высокие требова ния. Эта сталь, как любая подшипниковая, должна отличаться максимальной чис тотой по оксидным и сульфидным включениям, а также иметь малую карбидную ликвацию.
Подшипниковая сталь, помимо высокого содержания углерода, имеет в своем составе хром. Легирование хромом позволяет обеспечить необходимую прокаливаемость. С увеличением размера деталей должно быть большее содержание хро ма.
Термическая обработка подшипниковой стали производится для снижения твёрдости (умягчения), для получения микроструктуры мелкозернистого перлита при минимальном обезуглероживании, а также для предотвращения флокенов. Нормы твердости, структуры и глубины обезуглероженного слоя по ГОСТ 801-60.
Избыточные карбиды в структуре подшипниковой стали могут иметь различ ную форму и это зависит от температуры окончания прокатки и скорости охлаж дения проката. Температура окончания прокатки свыше 850 °С позволяет иметь в структуре стали карбидную сетку и тем значительнее, чем медленнее охлаждение проката в интервале 850...700 °С. При более низкой температуре конца прокатки (ниже 850 °С) сталь получается мелкозернистой и карбидная сетка либо отсутст вует, либо оказывается очень тонкой.
Отжиг подшипниковой стали производят при температурах выше Ас\ (но ниже
А-Сст)-
Незначительный перегрев (до 810...820 °С) вызывает поверхностное обезугле роживание, что для проката малого диаметра недопустимо. При перегреве стали на 20...30 °С в микроструктуре стали появляется пластинчатый перлит, а при очень значительном перегреве - 50 °С может образоваться карбидная сетка.
В целях предотвращения образования флокенов прокат подшипниковой стали толщиной или диаметром более 60 мм охлаждают после прокатки в колодцах по режиму: температура посадки не ниже 700 °С, охлаждение 24 часа, температура выгрузки не выше 150 °С или передают с температурой не ниже 250 °С на отжиг.
Отжиг проводится, если состояние поставки - в отожженном состоянии, ого варивается условиями поставки, а также для предупреждения появления флокенов - в этом случае выдержка в 1,5-2 раза меньшей продолжительности.
Термическая обработка деталей из подшипниковой стали состоит из закалки с температуры нагрева на 830...840 °С в масле и низкого отпуска при 150... 160 °С в течение 1...2 часов. Структура деталей после такой обработки должна быть мел коигольчатый мартенсит с равномерно распределенными избыточными карбида ми, твёрдость HRC 62.
Сортамент подшипниковой стали ОАО ЗМЗ ШХ6, ШХ9, ШХ15, ШХ15СГ приведен в табл. 2.8.2 и 2.8.3. Помимо выплавки в мартеновских печах (в том числе стали, обработанной синтетическим шлаком) и открытых электродуговых печах, ЗМЗ производил сталь электрошлакового переплава, вакуумно-дугового
203
переплава и двойного переплава: электрошлаковый переплав + вакуумно-дуговой переплав.
Таблица 2.8.2
Режимы отжига подшипниковой стали
|
|
Размер |
Темпера |
Ско |
Предель |
|
Условия |
|
Груп |
|
рость |
ная темпе |
Выдерж |
||||
Марка стали |
заготов |
тура по |
охлажде |
|||||
па |
|
ки, мм |
садки, °С |
нагрева, |
ратура на |
ка, ч |
ния |
|
|
|
°С/ч |
грева, °С |
|
||||
|
|
|
|
|
|
|||
|
|
5...15 |
|
|
770 |
5+1хвес |
|
|
|
|
|
|
садки, т |
20-30 °С/ч |
|||
|
|
|
|
|
|
|||
I |
ШХ6, ШХ9 |
16...30 |
Не огра |
100 |
780 |
5+0,9хвес |
до 650 °С, |
|
ничена |
садки, т |
далее на |
||||||
|
|
|
|
|
||||
|
|
|
|
|
|
|
воздухе |
|
|
|
31 и |
|
|
800 |
5+0,8хвес |
||
|
|
выше |
|
|
садки, т |
|
||
|
|
|
|
|
|
|||
|
|
|
|
|
|
|
|
|
|
|
5...15 |
|
|
780 |
5+0,9хвес |
|
|
|
|
|
|
садки, т |
|
|||
|
|
|
|
|
|
|
||
|
ШХ15, |
|
|
|
|
|
|
|
II |
16...30 |
— |
— |
790 |
5+0,8хвес |
— |
||
ШХ15СГ |
садки, т |
|||||||
|
|
|
|
|
|
|||
|
|
|
|
|
|
|
|
|
|
|
31 и |
|
|
810 |
5+0,8хвес |
|
|
|
|
выше |
|
|
садки, т |
|
||
|
|
|
|
|
|
|||
|
|
|
|
|
|
|
|
Для переплавов назначалась сталь с несколько большим содержанием Mn, Si: Мп 0,30...0,40 против 0,20...0,40;
Si 0,27...0,37 против 0,17...0,37 вследствие угара этих элементов в процессе переплавов.
Порядок выполнения работы и обработка результатов
Измерение твёрдости образцов до термообработки и после
В данной работе испытанию на твёрдость подвергаются образы подшипнико вой стали (ШХ15). Числа твёрдости определяются каким-либо одним или двумя рассмотренными ранее способами, в зависимости от твёрдости и чистоты поверх ности образцов (см. учебно-исследовательскую работу № 5). В связи с разбросом
204
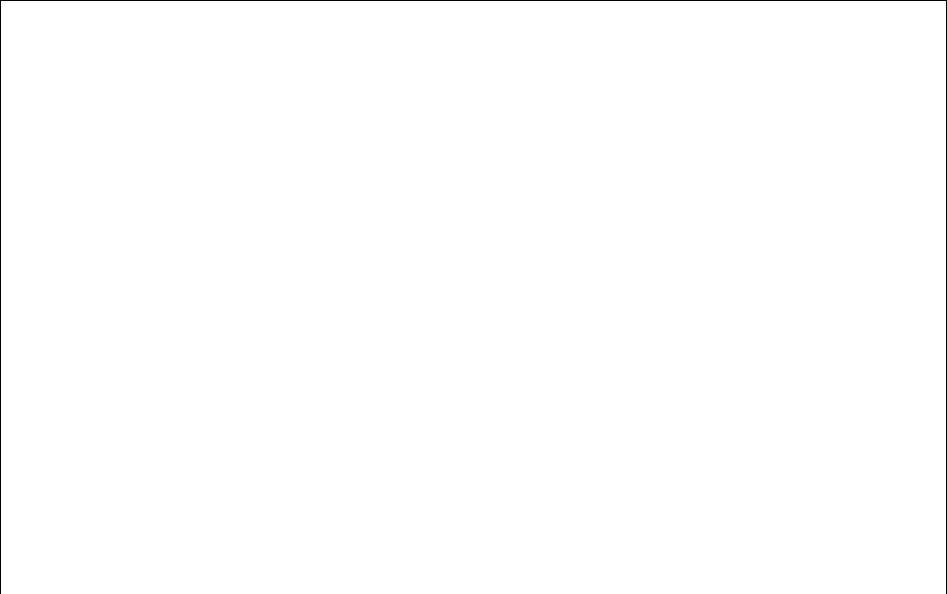
Таблица 2.8.3 Режимы термической обработки подшипниковой стали на Златоустовском металлургическом заводе по ТИ 05-Т-88
Режимы термической обработки сортового металла в камерных печах с выдвижным подом
|
|
Профиле- |
Вид |
|
Термообработка |
Масса |
Допус |
|
|
№ |
Марка ста |
размер |
термо |
Техноло- |
Вы |
|
тимая |
|
|
|
садки, не |
Примечание |
|||||||
гр. |
ли |
металла, |
обра |
гич. |
держ |
Охлаждение |
подгруз- |
||
|
|
мм |
ботки |
т-ра, °С |
ка, ч |
|
более, т |
ка |
|
|
|
|
|
|
|||||
26 |
ШХ15 |
До 80 |
Отжиг |
800 |
10 |
По 40°С /ч до |
10 |
|
1. При наличии в садке ста |
|
ШХ15СГ |
|
|
|
|
700°С, выдержка |
|
|
ли марок ШХ15, ШХ15СГ |
|
|
|
|
|
|
2 ч, охлаждение |
|
|
045-80 мм выдержка |
|
|
|
|
|
|
по 50°С/ч до |
|
|
должна быть 14 ч, незави |
|
|
|
|
|
|
|
|
симо от массы садки. |
|
|
|
|
|
|
|
630°С, далее сорт. |
|
|
|
|
|
|
|
|
|
|
|
2. Отжиг в печи № 1 при |
|
|
|
|
|
|
|
- на воздухе, под |
|
|
|
|
|
|
|
|
|
|
|
наличии в садке подшипни |
|
|
|
|
|
|
|
кат - 2 ч. с печью |
|
|
|
|
|
|
|
|
|
|
|
ковой стали любых профи- |
|
|
|
|
|
|
|
и в воде |
|
|
|
|
|
|
|
|
|
|
|
леразмеров должен произ |
|
|
|
|
|
|
|
|
|
|
|
2в |
ШХ15 |
Свыше 80 |
Отжиг |
810 |
10 |
По 507ч до |
30 |
|
|
|
водиться по режиму: нагрев |
||||||||
|
ШХ15СГ |
и круглая |
|
|
|
600°С, далее на |
|
|
|
|
|
|
|
|
|
по программе 790 °С, вы |
|||
|
|
заготовка |
|
|
|
воздухе |
|
|
|
|
|
|
|
|
|
|
держка и охлаждение по |
||
|
|
под об |
|
|
|
|
|
|
|
|
|
|
|
|
|
|
|
режиму гр. 26 или 2в |
|
|
|
точку |
|
|
|
|
|
|
|
|
|
|
|
|
|
|
|
|
|
|
|
|
|
|
|
|
|
|
|
|
Режимы термической обработки мотков (сортовых и подката) металла в камерных печах с выдвижным подом |
||||||||
№ |
Марка ста |
Вид про |
Вид |
|
Термообработка |
Условия |
Допус |
Примечание |
|
гр. |
ли |
дукции |
термо |
Техно- |
Вы |
Охлаждение |
погрузки |
тимая |
|
|
|
|
обра |
логич. |
держ |
|
|
подгруз- |
|
|
|
|
ботки |
т-ра, °С |
ка, час |
|
|
ка |
|
|
|
|
|
|
|
|
|
|
|
2а |
ШХ15 |
Сортовой |
Отжиг |
810 |
1 |
По 40°С/ч до |
Связка |
|
|
|
|
подкат |
|
800 |
4 |
700 °С |
ми в 1 |
|
|
|
|
|
|
|
|
|
ряд |
|
|
|
|
|
|
700 |
4...5 |
1 ч с печью через |
|
|
|
|
|
|
|
|
|
10-15 мин замо |
|
|
|
|
|
|
|
|
|
чить в воде |
|
|
|
|
|
|
|
|
|
|
|
|
|
205

№ Марка гр. стали
2а ШХ15
ШХ15
ШХ15СГ
Продолжение табл. 2.8.3
Режимы термической обработки подката в камерных печах со стационарным подом
|
|
|
Термообработка |
и |
|
Допускается |
|
||
|
|
|
Выдержка |
|
о |
|
подгрузка |
|
|
Вид |
|
|
|
н |
|
|
|||
|
|
без |
|
|
|
|
|
|
|
термо |
|
о |
|
оЗ |
|
|
|
|
|
|
пода |
|
|
|
|
Примечание |
|||
|
О |
|
С |
|
|
|
|||
обра |
|
оЗ |
Охлаждение |
03 |
о |
|
калиб |
||
О |
|
|
|
||||||
|
|
чи то |
о |
|
|
||||
ботки |
к |
|
|
о |
|
подкат |
ровка |
|
|
X |
|
плива, |
|
03 |
|
|
|
н |
ч |
|
790 |
3-4 ч с приот |
|
крытым шибе |
|
ром, затем, на |
воздухе и за мочить в воде: мотки через 5- 15 мин, прутки через 30-40 мин
790
На мотки, прилегающие к за слонке, перед отжигом наве шиваются спец. бирки для от бора проб для контроля мик роструктуры
При снижении температуры по двум и более термопарам через 1 ч томления до 40 °С должен производиться повторный на грев до 790 °С с выдержкой 2- 3 ч При снижении температуры по
двум и более термопарам через 1 ч томления до 40 °С должен производиться повторный на грев до 790 °С с выдержкой 2- 3 ч «Нережимный» после низко-
температурной прокатки
206
Окончание таблицы 2.8.3
Режимы термической обработки подката в камерных печах со стационарным подом
|
|
|
|
|
Термообработка |
Массапакетов порядам |
Условияпогруз |
|
Допускается |
|
|||
|
|
|
|
°С |
Выдержка |
|
бунтовки |
подгрузка |
|
||||
|
|
Вид |
Вид |
Тех- |
с по |
без |
|
|
|
|
|
|
|
№ |
Марка |
про |
термо |
ноло- |
дачей |
пода |
Охлаждение |
|
|
|
|
калиб |
Примечание |
гр. |
стали |
ката |
обра |
гич. |
топ |
чи то |
|
|
|
подкат |
|
||
|
|
ботки |
т-ра, |
|
|
|
|
ровка |
|
||||
|
|
|
|
|
лива, |
плива, |
|
|
|
|
|
|
|
|
|
|
|
|
ч |
ч |
|
|
|
|
|
|
|
|
|
|
|
|
|
|
|
|
|
|
|
|
|
26 |
ШХ15, |
Прут |
|
780 |
9...11 |
|
По 20 °С /ч до |
1-2-й |
|
|
|
|
|
|
ШХ15СГ |
ки ст. |
|
|
|
|
720 °С |
ряд |
|
|
|
|
|
|
|
«400» |
|
|
|
|
|
н.б. |
|
|
|
|
|
|
|
|
|
|
|
|
|
1,0 т |
|
|
|
|
|
|
ШХ15СГ |
Прут |
Отжиг |
720 |
2 |
|
За 1 ч до 720 °С |
|
|
|
|
|
|
|
|
ки ст. |
|
700 |
2 |
|
За 1 ч до 700 °С |
|
|
|
|
|
|
|
|
«280» |
|
|
|
|
|
|
|
|
|||
|
|
|
680 |
2 |
|
4 ч при разря |
|
|
|
|
|
|
|
|
|
|
|
|
|
|
|
|
|
|
|||
|
|
|
|
|
|
|
жении до 0,5 |
|
и |
|
|
|
|
|
|
|
|
|
|
|
мм водного |
|
|
|
|
|
|
|
|
|
|
|
|
|
|
к |
|
|
|
|
|
|
|
|
|
|
|
|
столба, через |
|
03 |
|
|
|
|
|
|
|
|
|
|
|
|
|
|
|
|
|
|
|
|
|
|
|
|
|
30...40 мин |
|
и |
|
|
|
|
|
|
|
|
|
|
|
|
СО |
|
|
|
|
|
|
|
|
|
|
|
|
после выгруз |
|
и |
|
|
|
|
|
|
|
|
|
|
|
ки из печи за |
|
и |
|
|
|
|
|
|
|
|
|
|
|
мочить |
|
|
|
|
|
|
|
|
|
|
|
|
|
|
|
|
|
|
|
|
|
ШХ15-Ш, |
Прут |
Отжиг |
790 |
7 |
|
По 30 °С /ч до |
1-2-й |
|
|
|
|
|
|
ШХ15ШД |
ки, |
|
|
|
|
680-700 °С |
ряд |
|
|
|
|
|
|
|
мот |
|
|
|
|
|
н.б. |
|
|
|
|
|
|
|
ки |
|
|
|
|
|
1,0 т |
|
|
|
|
|
|
|
|
|
|
|
|
|
3-4-й |
|
|
|
|
|
|
|
|
|
|
|
|
|
ряд |
|
|
|
|
|
|
|
|
|
|
|
|
|
н.б. |
|
|
|
|
|
|
|
|
|
|
|
|
|
1,5 т |
|
|
|
|
|
|
|
|
|
|
|
|
|
|
|
|
|
|
|
207

данных измерений испытания на твёрдость повторяют 2-3 раза и берут средний результат.
Разработка технологии термической обработки стали
Разработка для представленной подшипниковой стали возможных режимов термической обработки (отжиг, закалка, отпуск). Обосновать выбор температур, время изотермических выдержек и режим (среда) охлаждения.
Проведение термической обработки по разработанным режимам. Контроль твёрдости материалов после проведения термической обработки.
Оформление отчёта об исследовании
1.Измерение твёрдости исходных материалов до термообработки.
2.Охарактеризовать по данным твёрдости состояние материала и сделать вы воды о его механических и физических свойствах (по учебно-исследовательской работе № 5).
3.Проведение термической обработки стали по разработанным режимам (табл. 2.8.4).
|
|
|
|
|
|
Таблица 2.8.4 |
|
|
|
Режимы термической обработки |
|
|
|
||
|
|
|
|
|
|
|
|
Марка |
Вид прово |
Т нагре |
Скорость на |
Время вы |
Среда ох |
|
Примеча |
стали |
димой т/о |
ва, °С |
грева, °С/ч |
держки, мин |
лаждения |
|
ния |
|
|
|
|
|
|
|
|
|
|
|
|
|
|
|
|
|
|
|
|
|
|
|
|
Цель работы.
Тип, характеристика печи, вспомогательного оборудования.
4.Измерение твёрдости материалов после термообработки.
5.Анализ влияния термической обработки на свойства стали (табл. 2.8.5).
Таблица 2.8.5
Влияние термической обработки на свойства стали
Марка стали Твёрдость до т/о Вид проводимой т/о Твёрдость после т/о Примечания
6. Зарисовать микроструктуры сталей до проведения термической обработки и после неё. Описать изменения, произошедшие в структуре стали.
Контрольные вопросы
1.Какие существуют виды термической обработки, их характеристика?
2.Требования к подшипниковым сталям, их классификация.
3.Чем регламентируется выбор подшипниковой стали в зависимости от раз мера изделия и сферы применения?
4.Назначение и режим отжига подшипниковых сталей.
208
5.Из каких соображений назначается температура под отжиг подшипниковых сталей?
6.Как влияет скорость охлаждения на структуру и твёрдость закалённой под шипниковой стали? Какова критическая скорость закалки?
7.Назначение отпуска для подшипниковых сталей, виды отпуска.
8.Варианты дополнительного повышения твёрдости при термической обработке.
9.Как влияет температура отпуска на структуру и механические свойства за каленной стали?
10.Правила техники безопасности при проведении термической обработки сталей и сплавов.
2.9. Учебно-исследовательская работа № 9. Практика термообработки аустенитных сплавов на никелевой основе
Цель работы
Данная работа предполагает:
-знакомство с жаропрочными аустенитными сталями на никелевой основе;
-контроль качества термически обработанных изделий путём замера твёрдо сти (в предыдущих учебно-исследовательских работах проводилась термическая обработка и замер твёрдости после термической обработки образцов сталей, имеющих превращения при критических точках; в данной работе - замер твёрдо сти и анализ микроструктуры образцов сплавов на никелевой основе - аустенит ных сплавов - после высокотемпературной одинарной и двойной закалок и по следующего старения изделий, так называемая химико-термическая обработка);
-проведение анализа микроструктуры термически обработанных образцов:
а) после закалки; после закалки и старения;
б) после одинарной закалки; после двойной закалки;
после двойной закалки и старения.
Основные положения
Характеристика жаропрочных аустенитных сплавов на никелевой основе
Для многих деталей котлов, газовых турбин, реактивных двигателей, ракет, атомных устройств и др., работающих при высоких температурах применяют жаростойкие и жаропрочные стали и сплавы.
Под жаростойкими (окал и постой ким и) сталями и сплавами понимают стали и сплавы, обладающие стойкостью против химического разрушения поверхности в газовых средах при температурах выше 550 °С и работающие в ненагруженном или слабонагруженном состоянии. Таким образом, жаростойкость характеризует сопротивление металла окислению при высоких температурах.
209
Установлено, что при высоких температурах металл ведёт себя во многих отношениях иначе, чем при нормальных, или даже 300...350 °С. При высоких температурах активно происходит процесс окисления. Начальная стадия окисления стали это чисто химический процесс. Но дальнейшее течение окисления представляет собой уже сложный процесс, заключающийся не только в химическом соединении кислорода и металла, но и в диффузии атомов кислорода
иметалла через многофазный окисленный слой. При плотной окисной плёнке скорость нарастания окалины определяется скоростью диффузии атомов сквозь толщину окалины, что в свою очередь зависит от температуры и строения окисной плёнки.
Железо с кислородом образует ряд химических соединений: FeO (вюстит), РезС>4 (магнетит) и РегОз (гематит). Строение диффузионного слоя соответствует изотермическим разрезам соответствующих диаграмм состояния при температурах диффузии.
При температурах ниже эвтектоидной (570 °С) окисленный слой состоит из двух зон окислов: БегОз и БезС^ Кристаллическая структура этих окислов сложна,
искорость диффузии в них мала.
При температурах выше 570 °С структура окалины состоит из трёх окислов: БегОз, БезС^ и FeO, причём основным слоем окалины является окись FeO. Скорость окисления возрастает при переходе через эвтектоидную температуру (570 °С), что является следствием более ускоренной диффузии атомов сквозь простую кристаллическую решётку вюстита, кристаллизующегося как и фазы внедрения с дефицитом в неметаллических атомах (кислорода).
Для повышения окалиностойкости сталь легируют элементами, которые благоприятным образом изменяют состав и состояние окалины. Так, в результате введения в сталь соответствующих количествах хрома, алюминия или кремния, обладающих большим сродством к кислороду, чем железо, в процессе окисления на поверхности образуются плотные окислы Сг20з, А120з или S1O2, диффузия сквозь которые происходит с трудом. Образовавшаяся тонкая плёнка этих окислов затрудняет процесс дальнейшего окисления.
Чем выше содержание хрома, алюминия или кремния в стали, тем выше окалиностойкость стали и тем выше может быть рабочая температура. При рабочей температуре 900 °С для достаточной окалиностойкости сталь (сплав) должна содержать не менее 10 % Сг, а при рабочей температуре 1000 °С, уже не менее 20...25 % Сг.
Оклиностойкость, столь существенно зависящая от состава стали или сплава, не зависит от его структуры, т.е. это свойство структурно нечувствительное. Так,
окалиностойкость |
ферритных |
(чисто |
хромистых) |
и |
аустенитных |
(хромоникелевых) сплавов практически одинакова. |
|
|
|||
Под жаропрочными |
сталями и |
сплавами |
понимают |
стали |
и сплавы, |
обладающие повышенными механическими свойствами при высоких температурах. Таким образом, жаропрочность - это способность материала противостоять механическим нагрузкам при высоких температурах.
210
Напряжение, которое вызывает разрушение металла при повышенных температурах, сильно зависит от продолжительности приложенной нагрузки. Оно может быть велико при кратковременном приложении нагрузки и мало, если нагрузка действует длительное время.
Жаропрочные, аустенитные стали (сплавы) на никелевой основе занимают существенное место в ряду жаропрочных материалов.
Аустенитные жаропрочные стали применяют для изготовления клапанов двигателей, лопаток газовых турбин и других «горячих» деталей реактивных двигателей, предполагающих работу при 600.. .700 °С.
Все аустенитные жаропрочные стали содержат большое количество хрома и никеля, а также добавки других элементов. Для получения структуры аустенита эти стали должны содержать большое количество никеля (марганца), а для получения высокой жаростойкости - хрома. При недостатке никеля возможно частичное образование ос-фазы, что ухудшает жаропрочность. Жаропрочность аустенитных сталей выше, чем перлитных, мартенситных, мартенсито-ферритных и ферритных.
Аустенитные жаропрочные стали обладают рядом общих свойств: высокой жаропрочностью и окалиностойкостью, большой пластичностью, хорошей свариваемостью, большим коэффициентом линейного расширения. Тем не менее, по сравнению с перлитными и мартенситными сталями они менее технологичны: обработка давлением и резаньем этих сплавов затруднена; сварной шов обладает повышенной хрупкостью; полученное вследствие перегрева крупнозернистое строение не может быть исправлено термической обработкой, так как в этих сталях отсутствует фазовая перекристаллизация. В интервале 550...600 °С эти стали часто охрупчиваются из-за выделения по границам зёрна различных фаз.
Аустенитные стали по способу упрочнения можно разделить на три группы:
1)твёрдые растворы, содержащие сравнительно мало легирующих элементов
ине склонные к дисперсионному твердению (условно можно назвать их гомогенными, хотя на самом деле они содержат вторичные фазы, но в количествах, не вызывающих сильного эффекта старения), а следовательно, мало упрочняемые термической обработкой;
2)твёрдые растворы с карбидным упрочнением, упрочняющими фазами выступают как первичные карбиды (TiC, VC, ZrC, NbC и др.), так и вторичные карбиды (МегзСб, МебС, МеуСз), выделяющимися из твёрдого раствора;
3)твёрдые растворы с интерметаллидным упрочнением, упрочняющими фазами являются у -фаза типа №зТ1, №зА1, №з№> и др.
Последние две группы существенно упрочняются термической обработкой с применением закалки+отпуск. Допустимое количество вторичной фазы - 5 %, а структурная стабильность достигается усложнением состава фаз и матрицы путём введения элементов с низкой диффузионной подвижностью (Mo, W, Nb и др.).
211
Характеристика |
аустенитных сплавов на никелевой основе |
с |
интерметаллидным упрочнением |
В современных турбинах и реактивных двигателях важнейшей деталью является лопатка турбины. Мощность реактивного двигателя в большой степени зависит от максимальной температуры рабочего тела (газа), при которой длительное время могут работать лопатки. В современных реактивных двигателях лопатки турбин разогреваются до 700... 1000 °С и имеется тенденция повышения этой температуры.
Для лопаток турбин, крепёжных деталей паровых и газовых турбин применяют аустенитные стали и сплавы на основе никеля и кобальта.
Как и аустенитные стали, сплавы на основе никеля могут быть разделены на три группы:
1) сплавы с содержанием 14... 16 % Сг, 32...38 % Ni (ХН35ВТЮ, ХН38ВТ и др.), дополнительно легированные вольфрамом, титаном и алюминием, после закалки и старения характеризуются высокой жаропрочностью;
2) сплавы с содержанием 20...25 % Сг, 25...45 % Ni (ХН28ВМАБ, 06ХН28МДТ и др.), которые благодаря высокому содержанию хрома обладают хорошей коррозионной стойкостью, жаростойкостью, но пониженной жаропрочностью;
3) сплавы на никелевой основе с содержанием никеля 30...60 % и более, стареющие.
Первые две группы сплавов называемые инконели или нихромы, представляют собой сплавы никеля и хрома или никеля, хрома и железа с минимальным содержанием углерода и других элементов, которые могли бы образовывать вторичные фазы. Структура этих сплавов представляет собой твёрдый раствор этих элементов в никеле (гранецентрированная кубическая решётка). Гомогенный твёрдый раствор не обладает высокой жаропрочностью. Сплавы этого типа, как правило, используют как материал высокой жаростойкости, а также как материал для электрических нагревательных элементов сопротивления.
Практически как высокожаропрочные сплавы применяют стареющие никелевые сплавы - нимоники. К этой группе относятся хромоникелевые дисперсионно твердеющие стали аустенитного класса, упрочняемые введением титана, алюминия, бора и тугоплавких элементов - вольфрама, молибдена, ниобия. Нимоник основного «классического» состава представляет собой четверной сплав Ni-Cr-Ti-Al. Для получения высокой окалиностойкости никель легируют хромом, а для повышения жаропрочности - титаном (1,0... 1,8 %) и алюминием (0,5...5,5 % ) . Наиболее эффективным упрочнителем в этой системе является титан, который при благоприятных температурных условиях, взаимодействуя с никелем, образует у'-фазу, что значительно повышает твёрдость и прочностные свойства стали. Закалка с 1050... 1150 °С приводит к образованию твёрдого у-раствора с гранецентрированной кубической решёткой. Нагрев такого
212