
- •ЧЕРНАЯ
- •МЕТАЛЛУРГИЯ
- •НА ПРЕДПРИЯТИЯХ И В ИНСТИТУТАХ
- •Аглодоменное производство
- •Сталеплавильное производство
- •Прокатное производство
- •ПОЗДРАВЛЯЕМ С ЮБИЛЕЕМ!
- •Продукция
- •экспортные цены Турции при поставках в третьи страны
- •на условиях FOB турецкие порты, долл/т*
- •Продукция
- •Подготовлено В.В. Смильтиной
- •динамика производства продукции в топливно-энергетических отраслях
- •Объем погрузки основных видов грузов на железнодорожном транспорте
- •ТОВАРНЫЙ СОСТАВ ЭКСПОРТА
- •Индексы цен и тарифов на конец периода, %
- •Подготовлено В.В. Смильтиной
- •Продукция
- •Производство огнеупоров
- •Производство метизов
- •Нефтедобывающая
- •Угольная
- •Металлургическое машиностроение
- •Добыча полезных ископаемых
- •Дата
- •Подготовлено В.В. Смильтиной
- •Дата

ОТКРЫТОЕ АКЦИОНЕРНОЕ ОБЩЕСТВО “ЦЕНТРАЛЬНЫЙ НАУЧНО-ИССЛЕДОВАТЕЛЬСКИЙ ИНСТИТУТ ИНФОРМАЦИИ И ТЕХНИКО-ЭКОНОМИЧЕСКИХ
ИССЛЕДОВАНИЙ ЧЕРНОЙ МЕТАЛЛУРГИИ”
ЧЕРНАЯ__
МЕТАЛЛУРГИЯ
2011
ВЫПУСК 7 (1339) МОСКВА
БЮЛЛЕТЕНЬ научно-технической и экономической информации
Основан в марте 1944 г. |
Журнал |
зарегистрирован Федеральной службой по надзору за соблюдением |
||
Выходит 1 раз в месяц |
||||
|
законодательства в сфере массовых коммуникаций и охране культурного наследия |
|||
|
|
|
Регистрационный номер ПИ № 77-18479 |
|
С О Д Е Р Ж А Н И Е |
|
|||
Петракова Т.М., Иванова И.М. Итоги работы предпри- |
|
производства высококачественной продукции на са- |
|
|
ятий черной металлургии России за I квартал 2011 г. ...... |
5 |
мом новом в Украине среднесортно-мелкосортном |
|
|
Юзов О.В., Седых А.М., Афонин С.З. Экономические |
|
стане 390.............................................................................. |
56 |
|
показатели и проблемы посткризисного развития чер- |
|
Трубное производство |
|
|
ной металлургии России..................................................... |
|
16 |
Пышминцев И.Ю., Выдрин А.В., Космацкий Я.И., |
|
НА ПРЕДПРИЯТИЯХ И В ИНСТИТУТАХ |
|
Восходов В.Б., Ананян В.В., Зубков А.М., Денисюк |
|
|
Горнорудное производство |
|
|
С.А., Шлямнев А.П. Анализ результатов опытно-про- |
|
Пестонова Е.А., Ануфриева С.И., Шувалова Ю.Н. |
|
мышленного производства труб из новой коррозион- |
|
|
Обесфосфоривание концентратов обогащения окис- |
|
ностойкой стали.................................................................. |
66 |
|
ленных марганцевых руд химическими способами......... |
22 |
Метизное производство |
|
|
Коксохимическое производство |
|
|
Савенок А.Н., Веденеев А.В., Игнатенко О.И., Бобари- |
|
Рудыка В.И., Малина В.П. Последние тенденции в |
|
кин Ю.Л., Верещагин М.Н., Целуев М.Ю. Использова- |
|
|
развитии мирового металлургического и коксового |
|
ние температурного критерия для оптимизации гео- |
|
|
производств (обзор материалов cаммита “Европейский |
|
метрии деформирующей и калибрующей зон канала |
|
|
кокс 2011”, 5−7 апреля 2011 г., г. Вена, Австрия)............ |
28 |
волоки .................................................................................. |
70 |
|
Аглодоменное производство |
|
|
Металлургическое оборудование и литейное произ- |
|
Шевченко А.Ф. Комплексная оценка различных тех- |
|
водство |
|
|
нологий внепечной десульфурации чугуна....................... |
|
33 |
Шебаниц Э.Н., Мурашкин А.В., Форман С.В., По- |
|
Миса В.В., Лысенко Т.И., Паниотов Ю.С. Изменение |
|
ляк О.Ю., Лукьянчиков А.Н., Лещинский Л.К., |
|
|
параметров чугуна за время пребывания в миксере......... |
41 |
Дубинский Б.Е., Матвиенко В.Н., Степнов К.К. |
|
|
Сталеплавильное производство |
|
|
Повышение работоспособности обжимных валков |
|
Величко А.Г., Бойченко Б.М., Гришин B.C., Попов |
|
клети 1150 на Мариупольском металлургическом |
|
|
А.В., Шибко А.В., Пищида В.И., Шпак В.И., Чмырков |
|
комбинате им. Ильича........................................................ |
75 |
|
К.Ф. Применение в конвертерах кислородных фурм с |
|
Ресурсосбережение и экология |
|
|
двухрядным расположением сопел.................................... |
|
44 |
Меркер Э.Э., Харламов Д.А., Ансимов А.А. Совер- |
|
Семыкин С.И., Поляков В.Ф., Семыкина Е.В., Кияш- |
|
шенствование методики контроля и параметров ре- |
|
|
ко Т.С. Исследование особенностей рафинирования |
|
жима сжигания топлива во вращающихся обжиговых |
|
|
железоуглеродистого расплава при наложении низко- |
|
печах..................................................................................... |
78 |
|
вольтного электрического потенциала.............................. |
|
46 |
Аннотации к статьям .......................................................... |
82 |
Харлашин П.С., Ковура А.Б., Куземко Р.Д. Модель |
|
ВЫСТАВКИ, КОНФЕРЕНЦИИ, СИМПОЗИУМЫ... |
88 |
|
расчета термогазодинамических параметров струи при |
|
Цены на сырье и металлопродукцию................................ |
89 |
|
раздуве шлака в конвертере................................................ |
|
51 |
Статистика........................................................................... |
91 |
Прокатное производство |
|
|
Динамика курсов основных иностранных валют............. |
99 |
Цкитишвили Э.О., Чудновец А.Н., Бруханский В.Н., |
|
|
|
|
Кукуй Д.П., Солод В.С., Мальцев А.А. |
Освоение |
|
|
|
C O N T E N T S
Petrakova T.M., Ivanova I.M. Results of Activities of the Iron and |
|
Rolling Mill Practice |
|
||||||
Steel Industry Enterprises in the First Quarter of 2011........................ |
|
|
5 |
Tskitishvili E.O., Chudnovets A.N., Brukhanskiy V.N., Kukuy |
|
||||
Yuzov O.V., Sedykh A.M., Afonin S.Z. Economic Indices and |
|
D.P., Solod V.S., Mal’tsev A.A. Mastering the Manufacturing of |
|
||||||
Problems of Postcrisis Development of |
the Iron |
and |
Steel |
|
High-Quality Products in the Newest Ukrainian Medium-Section |
|
|||
Industry in Russia ................................................................................ |
|
|
|
|
|
16 |
– Light-Section 390 Mill...................................................................... |
56 |
|
AT ENTERPRISES AND INSTITUTES |
|
|
|
|
Production of Pipes and Tubes |
|
|||
The Ore-Mining Industry |
|
|
|
|
|
Pyshmintsev I.Yu., Vydrin A.V., Kosmatskiy Ya.I., Voskhodov |
|
||
Pestonova |
E.A., |
Anufrieva |
S.I., |
Shuvalova |
E.G. |
|
V.B., Ananyan V.V., Zubkov A.M., Denisyuk S.A., Shlyamnev |
|
|
Dephosphorization of Concentrates Produced during Oxidized |
|
A.P. Analysis of Results of Pilot-Industrial Manufacturing of |
|
||||||
Manganese Ore Concentration by Chemical Methods........................ |
|
|
22 |
New Stainless Steel Pipes and Tubes .................................................. |
66 |
||||
The Coking and By-Product Process |
|
|
|
|
Wire Products Manufacturing |
|
|||
Rudyka V.I., Malina V.P. The Last Trends in Development of the |
|
Savenok A.N., Vedeneev A.V., Ignatenko O.I., Bobarikin Yu.L., |
|
||||||
World’s Metallurgical and Coking Processes (Review of Summit |
|
Vereshchagin M.N., Tseluev M.Yu. Use of Temperature Criterion |
|
||||||
Information on “European Coke 2011” Held on April 5–7 in |
|
for Optimizing the Geometry of the Deforming and Sizing Zones |
|
||||||
Vienna, Austria)................................................................................... |
|
|
|
|
|
28 |
of the Die Channel .............................................................................. |
70 |
|
The Sintering and Blast Furnace Processes |
|
|
|
Metallurgical Equipment and Foundry Practice |
|
||||
Shevchenko A.F. Comprehensive Evaluation of |
Various |
|
Shebanits E.N., Murashkin A.V., Forman S.V., Polyak O.Yu., |
|
|||||
Technologies for Ladle Desulfurization of |
Cast Iron......................... |
|
|
33 |
Luk’yanchikov A.N., Leshchinskiy L.K., Dubinskiy B.E., |
|
|||
Misa V.V., Lysenko T.I., Paniotov Yu.S. Variation of |
Parameters |
|
Matvienko V.N., Stepnov K.K. Improvement in Serviceability of |
|
|||||
of Cast Iron during Residence in the Mixer ....................................... |
|
|
41 |
the Breakdown Rolls of the 1150 Stand at the Il’ich Mariupol’ |
|
||||
Steelmaking |
|
|
|
|
|
|
|
Integrated Iron and Steel Works .......................................................... |
75 |
Velichko A.G., Boichenko B.M., Grishin V.S., Popov A.V., |
|
Resource Saving and Ecology |
|
||||||
Shibko A.V., Poshchida V.I., Shpak V.I., Chmyrkov K.F. |
|
Merker E.E., Kharlamov D.A., Anisimov A.A. Improvement in |
|
||||||
Application of |
the Two-Row Nozzle Oxygen Lances in the Basic |
|
Procedure of Monitoring and Parameters of Fuel Combustion |
|
|||||
Oxygen Converters .............................................................................. |
|
|
|
|
|
44 |
Conditions in Rotary Firing Furnaces.................................................. |
78 |
|
Semykin S.I., Polyakov V.F., Semykina E.V., Kiyashko T.S. |
|
EXHIBITIONS, CONFERENCIES, SYMPOSIA ......................... |
88 |
||||||
Investigation into Peculiarities in Refining the Iron-Carbon Melt |
|
Prices for Raw Materials and Metal Products ..................................... |
89 |
||||||
during Applying the Low-Voltage Electric Potential.......................... |
|
|
46 |
Statistics ............................................................................................... |
91 |
||||
Kharlashin P.S., Kovura A.B., Kuzemko R.D. Model of |
|
Dynamics of Exchange Rates of the Main Foreign Currencies .......... |
99 |
||||||
Calculating the Thermal – Gas Dynamic Parameters of Jet during |
|
|
|
||||||
Blowing-Out the Slag in the Basic Oxygen Converter ....................... |
|
|
51 |
|
|
I N H A L T
Petrakowa T.M., Iwanowa I.M. Ergebnisse der Arbeit von |
|
|||||
Eisenhüttenbetrieben Russlands im 1 Quartal 2011.............................. |
|
5 |
||||
Ujsow O.W., Sedych A.M., Afonin S.Z. Wirtschaftliche Leistung |
|
|||||
und Probleme der Zeit nach der Eisenhüttenkunde in Russland......... |
16 |
|||||
IN DEN BETRIEBEN UND INSTITUTEN |
|
|
|
|||
Erzbergbau |
|
|
|
|
|
|
Pestonowa E.A., Anufriewa S.I., Schuwalowa Ju.N. |
|
|||||
Entphosphorung von Aufbereitungskonzentraten aus oxidierten |
|
|||||
Manganerzen durch chemische Methoden .......................................... |
|
|
22 |
|||
Kokereibetrieb |
|
|
|
|
|
|
Rudyka W.I., Malina W.P. Aktuelle Trends in der Produktion von |
|
|||||
Stahl und Koks in der Welt (Überprüfung der Materialien Gipfel |
|
|||||
“Europäische Koks 2011”, 5−7 April 2011, Wien, Österreich).......... |
28 |
|||||
Sinter-und Roheisenerzeugung |
|
|
|
|
||
Schewtschenko A.F. Komplexbewertung der verschiedenen |
|
|||||
Technologien von Roheisenentschwefelung in der Pfanne................. |
|
33 |
||||
Misa W.W., Lysenko T.I., Paniotow Ju.S. Änderung des |
|
|||||
Parameters von Roheisen während seines Aufenthalts in den |
|
|||||
Roheisenmischer .................................................................................. |
|
|
|
|
41 |
|
Stahlschmelzerei |
|
|
|
|
|
|
Welitschko A.G., Boitschenko B.M., Grischin W.S., Popow |
|
|||||
A.W., |
Schibko |
A.W., |
Pischtschida |
W.I., |
Schpak |
|
W.I.,Tschmyrkow K.F. Anwendung der Sauerstofflangen mit den |
|
|||||
zweireihigen Düseanordnung in den Konverter .................................. |
|
|
44 |
|||
Semykin S.I., Poljakow W.F., Semykina E.W., Kijaschko T.S. |
|
|||||
Untersuchung der Eigenheit der Raffination von Eisen- |
|
|||||
Kohlenstoff-Schmelze bei Anlegung von Niederspannungs- |
|
|||||
Elektrisches Potential........................................................................... |
|
|
|
|
46 |
|
Charlaschin P.S., Kowura A.B., Kusemko R.D. Modell zur |
|
|||||
Berechnung der thermogasdynamischen Parameter des Strahls am |
|
|||||
Anblasen der Schlacke in den Konverter............................................. |
|
|
51 |
Walzgutproduktion |
|
|
|
|
|
Zkitischwili E.O., Tschudnowez A.N., Bruchanski W.N., Kukui |
|
||||
D.P., Solod W.S., Malzew A.A. Aufnahme der Produktion von |
|
||||
Qualitätsproduktion |
auf |
dem |
neuesten |
Mittelstahl- |
|
Feinstahlwalzwerk 380 in der Ukraine................................................ |
|
|
56 |
||
Rohrherstellung |
|
|
|
|
|
Pyschminzew I.Ju., Wydrin A.W., Kosmazki Ja.I., Woschodow |
|
||||
W.B., Ananjan W.W., Subkow A.M., Denisjuk S.A., Schljamnew |
|
||||
A.P. Analyse der Ergebnisse der experimentell-industrielle |
|
||||
Herstellung von Rohren aus dem neuen korrosionsbeständigen |
|
||||
Stahl...................................................................................................... |
|
|
|
|
66 |
Metallwarenherstellung |
|
|
|
|
|
Sawenok A.N., Wedeneew A.W., Ignatenko O.I., Bobarikin Ju.L, |
|
||||
Wereschtschagin |
M.N., |
Zeluew |
M.Ju. Ausnutzung der |
|
|
Temperaturkriterium für die Optimierung der Geometrie von |
|
||||
Verformungsund Kalibrieren Zone des Ziehdüsekanals................... |
70 |
||||
Hüttenausrüstungen und Gießerei |
|
|
|
||
Schebaniz E.N., Muraschkin A.W., Forman S.W., Poljak O.Ju., |
|
||||
Lukjantschikow A.N., Leschtschinski L.K., Dubinski B.E., |
|
||||
Matwienko W.N., Stepnow K.K. Erhöhte Arbeitsfähigkeit der |
|
||||
Vorwalzen von Gerüst 1150 am Mariupol Hüttenwerk ihnen. Ilich... |
75 |
||||
Ressourceneinsparung und Ökologie |
|
|
|
||
Merker E.E., Charlamow D.A., Ansimow A.A. Verbesserung der |
|
||||
Methoden der Kontrolle und dem Parameter der Verbrennung von |
|
||||
Kraftstoff in Drehrohöfen78 |
|
|
|
|
|
AUSSTELLUNGEN, KONFERENZEN, SYMPOSIEN ............... |
88 |
||||
Preise für Rohstoffe und Metallwaren................................................. |
|
|
89 |
||
Statistik................................................................................................. |
|
|
|
|
91 |
Dynamik der Entwicklung der grundsätzlichen Auslandsvaluta ........ |
99 |
ПОЗДРАВЛЯЕМ С ЮБИЛЕЕМ!
ЯРОШЕВСКОМУ СТАНИСЛАВУ ЛЬВОВИЧУ
80лет
С.Л. Ярошевский родился 24 августа 1931 г. в г. Горьком. В 1955 г. он окончил Киевский политехнический институт и получил специальность инженера-металлурга черных металлов.
Дальнейшие этапы трудового пути Станислава Львовича инженер, младший научный сотрудник Украинского научно-исследовательского института металлов (1955−1959 гг., г. Харьков), инженер ЦЛЗ Донецкого металлургического завода (1959−1961 гг.), инженер, старший научный сотрудник, заведующий группой и заведующий лабораторией ДонНИИчермета (1961−1988 гг.).
В 1963 г. по предложению директора ДонНИИчермета Николая Ивановича Красавцева Станислав Львович начал работу по применению пылеугольного топлива (ПУТ) для выплавки чугуна. Это был период, когда эта технология отрабатывалась только в США и Китае, сведения о ней были крайне скудны. Пришлось создавать теорию процесса, находить технические и технологические решения по стыковке традиционной технологии выплавки чугуна на коксе с качественно новой технологией, использующей энергоноситель, существенно отличающийся от кокса как по своим свойствам, так и агрегатному состоянию.
В результате выполненного комплекса работ Станислав Львович создал теорию процесса выплавки чугуна с применением ПУТ и разработал основополагающие теоретические положения метода полной и комплексной компенсации негативных изменений технологического режима, определяемых горением ПУТ и снижением доли кокса в шихте ключевой момент, обеспечивающий возможность достижения наивысшей эффективности технологии.
Данная теория базируется на физико-химических закономерностях доменного процесса:
ееосновой является сохранение при вдувании ПУТ на первом этапе на базовом уровне, а далеесущественное улучшение основных технологических параметров технологии (условий нагрева шихты и сгорания ПУТ , газодинамических условий в определяющей зоне, условий восстановления вюстита и т.д.).
Подобные теории существовали и до работ С.Л. Ярошевского. Однако, в силу их несовершенства, на практике в основном преобладал традиционный метод “проб и ошибок”, а он хорош в лучшем случае только на начальном этапе работы.
Использование метода полной и комплексной компенсации обеспечивает достижение максимального результата от применения ПУТ не через 10−15 лет после начала работ, как это уже было в отечественной и мировой практике, а в течение 6−12 месяцев.
Материалы теоретических, технологических и технических разработок процесса доменной плавки с применением ПУТ легли в основу кандидатской и докторской диссертаций, защищенных Станиславом Львовичем в 1967 и 1984 г. За решение названной пр о- блемы в 1984 г. ему в составе творческого коллектива присуждена Государственная пр е- мия СССР. В 1990 г. Станислав Львович стал профессором, а в 1992 г. академиком инженерной академии Украины.
С1988 г. Станислав Львович Ярошевский работает профессором на кафедре “Руднотермические процессы и малоотходные технологии” Донецкого национального технического университета и одновременно возглавляет лабораторию использования ПУТ.
Станислав Львович является автором монографий: “Выплавка литейного чугуна с применением природного газа” (1971 г. с соавторами); “Применение пылеугольного топлива для выплавки чугуна” (1974 г., с соавторами); “Выплавка чугуна с применением пылеугольного
топлива” (1988 г.); “Интенсификация использования пылеугольного топлива в доменной плавке” (1993 г., с соавторами); “Перспективные технологии доменной плавки с применением кислорода и пылеугольного топлива” (1996 г., с соавторами), “Повышение эффективности использования природного газа в доменной плавке” (2002 г., с соавторами), “Резервы эффективности комбинированного дутья в доменных цехах Украины” (2006 г.).
Им опубликовано более 200 научных статей и создано 50 изобретений. Под его руководством подготовлено и защищено 7 кандидатских диссертаций.
В последние годы в Украине проблема применения ПУТ в доменном процессе стала как никогда актуальна, в данной проблеме Станислав Львович Ярошевский является одним из самых авторитетных специалистов.
Поздравляем Вас с 80-летием, и желаем Вам здоровья, счастья, успехов в дальнейшем решении актуальнейшей проблемы, которой занимаетесь практически всю свою творческую жизнь! Счастья в личной жизни, исполнения желаний!
Коллеги, друзья, ученики.
УДК 669.1:338.3 |
Т. М. ПЕТРАКОВА, к.э.н. (ОАО “Черметинформация”) |
ИТОГИ РАБОТЫ ПРЕДПРИЯТИЙ ЧЕРНОЙ МЕТАЛЛУРГИИ РОССИИ ЗА I КВАРТАЛ 2011 г.*
ОСНОВНЫЕ ПОКАЗАТЕЛИ РАБОТЫ ЧЕРНОЙ МЕТАЛЛУРГИИ ЗА I КВАРТАЛ 2011 г.
За I кв. 2011 г. индекс промышленного производства** составил 105,9 % по сравнению с соответствующим периодом 2010 г. Производство промышленной продукции по основным обрабатывающим производствам характеризуется следующими данными:
|
I кв. 2011 г. |
|
к I кв. 2010 г., % |
Обрабатывающие производства |
110,6 |
В том числе: |
|
производство кокса инефтепродуктов |
104,6 |
химическое производство |
108,0 |
металлургическое производство и |
|
производство готовых металличе- |
|
ских изделий |
109,1 |
в том числе металлургическое про- |
|
изводство |
105,7 |
производство машин и оборудования |
111,6 |
производство электрооборудования, |
|
электронного и оптического обору- |
|
дования |
106,3 |
производство транспортных средств |
|
и оборудования |
159,6 |
Из приведенных данных видно, что в обрабатывающих производствах наблюдается рост производства промышленной продукции. При этом рост непосредственно в металлургическом производстве составил 5,7 %, что ниже, чем в целом по обрабатывающим производствам.
За I кв. 2011 г. отмечается увеличение объемов производства практически во всех металлоемких отраслях:
I кв. 2011 г.
к I кв. 2010 г., %
Лишь при производстве изделий медицинской техники, средств измерений, оптических приборов и аппаратуры, часов наблюдается снижение объемов производства на 4,2 %.
За I кв. 2011 г. объем выполненных работ в строительстве составил 663,7 млрд руб., или 101,6 % к уровню соответствующего периода2010 г.
Динамика производства основных видов продукции черной металлургии в рассматриваемом периоде приведена в табл. 1. По всем основным позициям отмечается рост производства продукции к соответствующему периоду предыдущего года.
ТАБЛИЦА 1. ДИНАМИКА ПРОИЗВОДСТВА ПРОДУКЦИИ ЧЕРНОЙ МЕТАЛЛУРГИИ ЗА I кв. 2011 И 2010 г., млн т
Продукция |
I кв. |
I кв. |
Темп |
|
2011 г. |
2010 г. |
роста, % |
||
|
||||
Руда железная товарная |
|
|
|
|
необогащенная |
16,12 |
14,49 |
111,2 |
|
Железорудный концентрат |
24,36 |
22,67 |
107,5 |
|
Железорудные окатыши |
9,61 |
9,05 |
106,2 |
|
Чугун |
12,07 |
11,98 |
100,8 |
|
Сталь |
17,31 |
15,85 |
109,2 |
|
Готовый прокат черных |
|
|
|
|
металлов |
14,65 |
13,58 |
107,9 |
|
В том числе: |
|
|
|
|
сортовой (с заготовкой для |
|
|
|
|
переката на экспорт) |
7,66 |
6,95 |
216,7 |
|
листовой |
6,99 |
6,62 |
105,6 |
|
Стальные трубы |
2,56 |
2,11 |
121,2 |
|
Кокс |
6,77 |
6,78 |
99,9 |
Производство автомобилей, прицепов и |
|
полуприцепов |
В 2,1 р. |
Производство судов, летательных и кос- |
|
мических аппаратов и прочих транспорт |
|
ных средств |
134,9 |
Производство офисного оборудования и |
|
вычислительной техники |
133,4 |
Производство прочих машин и оборудо- |
|
вания специального назначения |
124,3 |
Производство бытовых приборов, не |
|
включенных в другие группировки |
123,5 |
Производство прочего оборудования |
|
общего назначения |
120,6 |
Производство станков |
110,3 |
Производство электрических машин и |
|
электрооборудования |
109,1 |
Производство машин и оборудования для |
|
сельского и лесного хозяйства |
106,1 |
Производство механического оборудования |
105,8 |
Использованы материалы Федеральной службы
государственной статистики РФ, Минэкономразвития РФ, Минпромторга РФ, ОАО “Черметинформация”, корпорации “Чермет”, публичной отчетности предприятий.
По данным Федеральной службы государственной статистики, индекс промышленного производства охватывает следующие виды деятельности: “добыча полезных ископаемых”, “обрабатывающие производства”, “производство и распределение электроэнергии, газа и воды”. Он рассчитывается на основе динамики производства 730 важнейших товаров-представителей (в натуральном или стоимостном выражении). В качестве весов используется структура валовой добавленной стоимости по видам экономической деятельности за базисный (2002) год с учетом поправки на неформальную деятельность.
ОАО «Черметинформация» • Бюллетень «Черная металлургия» • 7• 2011 ―――――――――――――――― |
5 |
В сталеплавильном производстве доля ки- |
в I кв. 2010 г. до 94,3 % в I кв. 2011 г. |
|||||
слородно-конвертерной стали и электростали в |
Изменение структуры выплавляемой стали по |
|||||
общем объеме выплавки стали возросла с 92,1 % |
видам характеризуется следующими данными: |
|||||
|
|
|
|
|
|
|
Сталь |
|
I кв. 2010 г. |
|
I кв. 2011 г. |
||
производство, |
|
доля в общем объеме |
производство, |
доля в общем объеме |
||
|
тыс. т |
|
производства стали, % |
тыс. т |
производства стали, % |
|
Кислородно-конвертерная |
10362,9 |
|
|
65,4 |
10837,8 |
62,6 |
Электросталь |
4240,7 |
|
|
26,8 |
5479,2 |
31,7 |
Мартеновская |
1248,7 |
|
|
7,9 |
991,8 |
5,7 |
В I кв. 2011 г. внутреннее потребление проката черных металлов ориентировочно составило 10,4 млн т и выросло по сравнению с I кв. 2010 г. примерно на 3,9 млн т, или на 60 %. Поставки отечественного проката на внутренний рынок составили 9,4 млн т, или 164,9 % к уровню I кв. 2010 г., а импортного 1,0 млн т, или 125 % к уровню I кв. 2010 г. Рост потребления проката обусловлен увеличением внутриотраслевого потребления (рост производства труб), а также ростом темпов производства в металлопотребляющих отраслях экономики.
Внутреннее потребление стальных труб оценивается на уровне 2,8 млн т, или 133,7 % по сравнению с соответствующим периодом 2010 г. Поставки на внутренний рынок труб отечественного производства составили, по оценке, 2,33 млн т (рост на 22,1 %), импортных 0,48 млн т (рост в 2,5 раза).
Комбинат
Западно-Сибирский (ЗСМК) Магнитогорский (ММК) Нижнетагильский (НТМК) Новолипецкий (НЛМК)
Оскольский электрометаллургический (ОЭМК) “Уральская сталь” Челябинский (ЧелМК)
Череповецкий (ЧерМК)
По восьми предприятиям
За I кв. 2011 г. доля основных производителей металлопродукции (девять крупнейших металлургических комбинатов отрасли*) в общеотраслевом объеме производства составляет, %:
|
Чугун |
Сталь |
Прокат |
I кв. 2010 г. |
92,2 |
85,6 |
87,7 |
I кв. 2011 г. |
92,9 |
83,7 |
83,0 |
Из приведенных данных видно, что высокая концентрация производства в отрасли сохраняется и доля ведущих комбинатов в общем объеме производства стали и проката снизилась.
Производство готового проката на восьми ведущих предприятиях отрасли в I кв. 2011 г. составило 11,8 млн т, или 103,8 % по отношению к I кв. 2010 г., а выручка от реализации продукции в фактических ценах (без НДС) на указанных предприятиях выросла на 33,7 % и составила:
I кв. 2011 г., |
I кв. 2011 г. к |
млн руб. |
I кв. 2010 г., % |
30739,1 |
148,7 |
62333,9 |
147,9 |
25686,3 |
144,8 |
44498,1 |
126,2 |
17053,7 |
143,5 |
Нет св. |
Нет св. |
26828,7 |
147,4 |
59566,1 |
143,5 |
266706,0 |
133,7 |
На всех рассматриваемых комбинатах имело |
производства, так и среднего уровня цен. |
место значительное увеличение объемов реали- |
Наиболее высокие темпы роста объемов |
зованной продукции по сравнению с I кв. 2010 г. |
реализованной продукции по отношению к I кв. |
На НЛМК, ОЭМК и ЧелМК это произошло при |
2010 г. наблюдались на ЗСМК, ММК и ЧелМК. |
снижении физического объема производства за |
В I кв. 2011 г. по сравнению с I кв. 2010 г. вы- |
счет роста среднего уровня отпускных цен на |
ручка от реализации продукции на семи крупных |
27,6, 49,3 и 51 % соответственно. На остальных |
предприятиях трубной отрасли увеличилась на |
комбинатах увеличение объемов товарной про- |
37,5 % и составила: |
дукции было обусловлено ростом как объемов |
|
Комбинаты: ЗСМК, ММК, НТМК, НКМК, НЛМК, ОЭМК, ЧерМК, “Уральская сталь”, ЧелМК.
6 ―――――――――――――――――ОАО «Черметинформация» • Бюллетень «Черная металлургия» • 7• 2011

Завод |
I кв. 2011 г., млн руб. |
I кв. 2011 г. к I кв. 2010 г., % |
Волжский трубный (ВТЗ) |
16311,6 |
141,2 |
Выксунский металлургический (ВМЗ) |
27142,0 |
105,0 |
Первоуральский новотрубный (ПНТЗ) |
8165,9 |
158,0 |
Северский трубный (СТЗ) |
6996,3 |
134,8 |
Синарский трубный (СинТЗ) |
6352,0 |
128,7 |
Таганрогский металлургический (ТагМЗ) |
6187,4 |
138,0 |
Челябинский трубопрокатный (ЧТПЗ) |
20107,1 |
218,7 |
Итого |
91262,3 |
137,5 |
На всех рассматриваемых трубных заводах, кроме ВМЗ, увеличились физические объемы производства и повысился средний уровень отпускных цен. Это обусловило увеличение объемов реализованной продукции на всех трубных заводах в I кв. 2011 г. На ВМЗ рост реализованной продукции вызван только повышением отпускных цен. Наиболее значительное увеличение реализованной продукции наблюдалось наЧТПЗ, ПНТЗ и ВТЗ.
Изменение темпов роста производства основных видов металлопродукции ведущими комбинатами отрасли составило, %:
Комбинат |
I кв. 2011 г. к I кв. 2010 г. |
|||
чугун |
сталь |
прокат |
||
ЗСМК |
||||
98,1 |
106,8 |
104,7 |
||
ММК |
110,4 |
114,3 |
111,5 |
|
НТМК |
106,7 |
108,7 |
106,7 |
|
НКМК |
|
134,5 |
112,4 |
|
НЛМК |
93,2 |
99,2 |
98,9 |
|
ОЭМК |
|
96,8 |
96,1 |
|
“Уральская сталь” |
89,4 |
88,6 |
83,3 |
|
ЧелМК |
96,4 |
106,7 |
97,6 |
|
ЧерМК |
105,1 |
108,5 |
108,6 |
По основным трубным предприятиям производство стальных труб характеризуется следующими данными:
Завод |
I кв. 2011 г. к I кв. 2010 г., % |
ВТЗ |
123,8 |
ВМЗ |
89,5 |
ПНТЗ |
120,2 |
СТЗ |
108,8 |
СинТЗ |
107,4 |
ТагМЗ |
111,7 |
ЧТПЗ |
164,0 |
Наиболее значительно увеличилось производство труб на ЧТПЗ, ВТЗ и ПНТЗ.
Уровень производства труб различного сортамента по сравнению с I кв. 2010 г. составил, %: сварных, клепаных или соединенных аналогичным способом для нефте- и газопроводов из черных металлов наружным диаметром более 406,4 мм –– 121,1; бурильных для бурения нефтяных или газовых скважин из черных металлов (кроме литейного чугуна) 148,8; обсадных 112,7; насосно-компрессорных 98,9; бесшовных для нефте- и газопроводов 107,2; тонкостенных электросварных 141,4.
За I кв. 2011 г. коэффициент использования производственной мощности по сравнению с I кв. 2010 г. увеличился по стальным трубам и чугуну на 9 %, железной руде на 8 %, стали и готовому прокату на 6 %, а по коксу остался практически без изменения.
В I кв. 2011 г. суммарный стоимостный объем экспорта продукции черной металлургии сырья (железных руд и концентратов, кокса, лома, отходов), ферросплавов, стальных слитков, заготовки и проката составил около 5,51 млрд долл. и увеличился по сравнению с I кв. 2010 г. на 16,7 %, в том числе в страны дальнего зарубежья на 20,2 %, а в страны СНГ снизился на 10,4 %. Изменение стоимостного объема экспорта было обусловлено изменением его физических объемов (табл. 2) и уровня средних фактических экспортных цен за I кв. 2011 г. по сравнению с I кв. 2010 г. (табл. 3).
ТАБЛИЦА 2. ФИЗИЧЕСКИЙ ОБЪЕМ ЭКСПОРТАПРОДУКЦИИ ЧЕРНОЙ МЕТАЛЛУРГИИ (по данным ФТС РФ)*, тыс. т
|
|
I кв. 2010 г. |
|
|
I кв. 2011 г. |
|
Продукция |
всего |
в том числе |
всего |
в том числе |
||
|
дальнее |
страны СНГ |
дальнее |
страны |
||
|
|
зарубежье |
|
зарубежье |
СНГ |
|
|
|
|
|
|||
Железные руды и концентраты |
5325,9 |
4074,2 |
1251,7 |
5654,8 |
5325,2 |
329,6 |
Кокс |
599,7 |
345,3 |
254,4 |
381,9 |
375,8 |
6,1 |
Чугун |
1091,8 |
1071,3 |
20,5 |
1103,2 |
1065,2 |
38,0 |
Ферросплавы |
237,7 |
230,6 |
7,1 |
175,9 |
172,8 |
3,1 |
Слитки и заготовка из углеродистой стали |
4426,0 |
4367,9 |
58,1 |
2914,1 |
2831,1 |
83,0 |
Прокат листовой из углеродистой стали |
2223,7 |
2018,9 |
204,8 |
1623,0 |
1476,9 |
146,1 |
* В общих итогах экспорта (без распределения по товарам) учтены показатели |
о торговле |
с Республикой Беларусь на |
||||
основе данных Федеральной службы государственной статистики и Республикой Казахстан на основе данных |
||||||
Комитета таможенного контроля Министерства финансов Республики Казахстан. |
|
|
ОАО «Черметинформация» • Бюллетень «Черная металлургия» • 7• 2011 ―――――――――――――――― |
7 |

ТАБЛИЦА 3. УРОВЕНЬ СРЕДНИХ ФАКТИЧЕСКИХ ЦЕН ЭКСПОРТНЫХ ОПЕРАЦИЙВ МАРТЕ 2011 г.*
|
|
|
|
|
|
|
|
Средняя |
|
|
|
В том числе по |
|
Март2011 г.к |
|||||
|
|
|
|
|
|
|
|
|
странам |
|
|
|
|
|
|
||||
|
|
Продукция |
|
|
фактическая цена |
|
|
|
государствам- |
|
|||||||||
|
|
|
|
|
дальнего |
|
|
|
марту2010 г., % |
||||||||||
|
|
|
|
|
|
|
|
за 1 т, долл. |
|
|
|
участникам СНГ |
|
||||||
|
|
|
|
|
|
|
|
|
зарубежья |
|
|
|
|
||||||
|
|
|
|
|
|
|
|
|
|
|
|
|
|
|
|
|
|||
|
Железные руды и концентраты |
|
|
109,1 |
110,9 |
|
|
|
|
76,5 |
|
|
183,7 |
||||||
|
Передельный чугун |
|
|
465,6 |
461,3 |
|
|
|
|
594,3 |
|
|
160,1 |
||||||
|
Ферросплавы |
|
|
1659,1 |
1651,8 |
|
|
|
2065,9 |
|
|
113,3 |
|||||||
|
Полуфабрикаты из углеродистой стали |
|
|
613,5 |
610,5 |
|
|
|
|
703,7 |
|
|
164,9 |
||||||
|
* Отношение стоимости экспортированных товаров к их количеству. |
|
|
|
|
|
|
|
|
||||||||||
|
|
В I кв. 2011 г. стоимостный объем импорта |
из стран дальнего зарубежья — на 25,2 %, а из |
||||||||||||||||
|
черных металлов (стальных слитков, заготовки, |
стран СНГ снизился на 5,9 %. Средние цены им- |
|||||||||||||||||
|
сортового и листового проката) увеличился на |
порта повысились на 26,3 % (табл. 4). |
|||||||||||||||||
|
26,0 %, в том числе из стран дальнего зарубежья |
Изменение |
стоимостного объема импорта |
||||||||||||||||
|
на 50,2 %, а из стран СНГ на 6,6 %. В це- |
было обусловлено изменением его физических |
|||||||||||||||||
|
лом физический объем импорта черных метал- |
объемов и уровня средних фактических импорт- |
|||||||||||||||||
|
лов (стальных слитков, заготовки, сортового и |
ных цен. |
|
|
|
|
|
|
|
|
|||||||||
|
листового проката) вырос на 3,8 %, в том числе |
|
|
|
|
|
|
|
|
|
|
|
|||||||
|
|
ТАБЛИЦА 4. ФИЗИЧЕСКИЙ ОБЪЕМ ИМПОРТА ПРОДУКЦИИ ЧЕРНОЙ МЕТАЛЛУРГИИ |
|||||||||||||||||
|
|
|
|
|
(по даннымФТС РФ)*, тыс. т |
|
|
|
|
|
|
|
|||||||
|
|
|
|
|
|
|
|
|
|
|
|
|
|
|
|
|
|
|
|
|
|
|
|
|
|
|
|
I кв. 2010 г. |
|
|
|
|
|
|
|
I кв. 2011 г. |
|
||
|
|
Продукция |
|
|
|
|
|
в том числе |
|
|
|
|
|
в том числе |
|||||
|
|
|
всего |
|
|
|
дальнее |
страны СНГ |
|
всего |
|
дальнее |
страны |
||||||
|
|
|
|
|
|
|
|
|
|||||||||||
|
|
|
|
|
|
|
|
зарубежье |
|
|
|
|
|
|
|
зарубежье |
СНГ |
||
|
Стальные слитки, заготовки, |
|
|
|
|
|
|
|
|
|
|
|
|
|
|
|
|
|
|
|
прокат сортовой и листовой |
|
931,6 |
|
290,3 |
641,3 |
|
966,8 |
|
363,6 |
|
|
603,2 |
||||||
|
Стальные трубы |
|
181,2 |
|
|
67,2 |
114,0 |
|
468,1 |
|
187,5 |
|
|
280,6 |
|||||
|
* В общих итогах экспорта (без |
распределения по товарам)учтены показатели |
о торговле с Республикой Беларусь на основе |
||||||||||||||||
|
данных Федеральной службы государственной статистики и Республикой Казахстан на основе данных Комитета |
||||||||||||||||||
|
таможенного контроля Министерства финансов Республики Казахстан. |
|
|
|
|
|
|
|
|
||||||||||
|
|
Стоимостный объем импорта стальных труб |
числе из стран дальнего зарубежья в 2,8 раза, |
||||||||||||||||
|
вырос в 2,9 раза, в том числе из стран дальнего |
а из стран СНГ (из Украины) в 2,5 раза. |
|||||||||||||||||
|
зарубежья в 2,7 раза, а из стран СНГ (из |
В марте 2011 г. по сравнению с декабрем2010 г. |
|||||||||||||||||
|
Украины) в 3,1 раза. Средние импортные цены |
отмечается рост цен мирового рынка на арма- |
|||||||||||||||||
|
на стальные трубы увеличились на 11,4 %. При |
турную сталь (14,6 %), катанку (14,4 %), средний |
|||||||||||||||||
|
этом средние цены импорта из стран дальнего |
лист (27,8 |
%), |
|
рулонную сталь: горячекатаную |
||||||||||||||
|
зарубежья снизились на 2,6 %, а из Украины |
(28,3 %), холоднокатаную (12,6 %), оцинкованную |
|||||||||||||||||
|
увеличились на 25,9 %. Физический объем |
рулонную (17,1 %). Динамика изменения цен на |
|||||||||||||||||
|
импорта стальных труб вырос в 2,6 раза, в том |
прокат черных металлов приведена в табл. 5. |
|||||||||||||||||
|
|
ТАБЛИЦА 5. ЦЕНЫ ЗАПАДНОЕВРОПЕЙСКОГО РЫНКА НА ПРОКАТ ЧЕРНЫХ МЕТАЛЛОВ |
|||||||||||||||||
|
|
|
|
|
|
|
|
|
|
|
|
|
|
|
|
|
|
|
|
|
|
Продукция |
|
|
|
|
Декабрь |
|
|
|
|
|
|
|
2011 г. |
|
|||
|
|
|
|
|
|
2010 г. |
|
январь |
|
|
|
февраль |
|
|
март |
||||
|
|
|
|
|
|
|
|
|
|
|
|
|
|||||||
|
Арматурная сталь*1 |
|
|
|
|
610−620 |
|
680−690 |
|
|
|
690−700 |
|
|
700−710 |
||||
|
Катанка*1 |
|
|
|
|
620−630 |
|
690−700 |
|
|
|
700−710 |
|
|
710−720 |
||||
|
Толстый лист*2 |
|
|
|
|
550−560 |
|
550−560 |
|
|
|
550−560 |
|
|
550−560 |
||||
|
Средний лист*2 |
|
|
|
|
530−550 |
|
530−550 |
|
|
|
530−550 |
|
|
680−700 |
||||
|
Полоса в рулонах: |
|
|
|
|
|
|
|
|
|
|
|
|
|
|
|
|
||
|
|
горячекатаная *2 |
|
|
|
|
490−500 |
|
490−500 |
|
|
|
570−580 |
|
|
620−650 |
|||
|
|
|
|
|
|
|
|
|
|
|
|
||||||||
|
|
холоднокатаная *2 |
|
|
|
|
590−600 |
|
590−600 |
|
|
|
670−680 |
|
|
650−690 |
|||
|
*1 |
оцинкованная*2 |
|
|
|
|
580−590 |
|
580−590 |
|
|
|
650−660 |
|
|
680−690 |
|||
|
ЕС, экспорт в третьи страны, включая 2,5 % |
комиссионных, предоставляемых экспортерам, fob, долл/т. |
|||||||||||||||||
|
*2 |
ЕС, импорт, cfr, Западная Европа, евро/т. |
|
|
|
|
|
|
|
|
|
|
|
|
|
|
|
8 ―――――――――――――――――ОАО «Черметинформация» • Бюллетень «Черная металлургия» • 7• 2011

|
За рассматриваемый период индекс измене- |
ношению к декабрю 2010 г. составили, %: |
|||||||||
|
ния цен в марте 2011 г. по сравнению с декаб- |
Электроэнергия, отпущенная |
|
|
|
|
|||||
|
рем 2010 г. в металлургическом производстве |
|
|
|
|
||||||
|
промышленным потребителям |
|
|
113,5 |
|||||||
|
(110,2 %) был выше, чем в целом по промыш- |
Природный газ |
|
|
104,4 |
||||||
|
ленности (106,9 %). Индекс цен при производ- |
Уголь для коксования |
|
|
112,5 |
||||||
|
стве и распределении электроэнергии, газа и |
Топочный мазут |
|
|
101,9 |
||||||
|
воды (111,1 %) выше индекса цен в целом по |
Дизельное топливо |
|
|
102,5 |
||||||
|
промышленности. Тарифы на грузовые желез- |
|
|
|
|
|
|
|
|
||
|
нодорожные перевозки внутри страны выросли |
|
Динамика изменения цен, тарифов, инфляции и |
||||||||
|
на 7,5 %. Индексы цен на основные топливно- |
курса доллара вмарте 2011 г. по сравнению с де- |
|||||||||
|
энергетические ресурсы в марте 2011 г. по от- |
кабрем 2010 г. приведена ниже, %: |
|
|
|||||||
|
|
|
|
|
|
|
|
|
|
|
|
|
Курс рубля к доллару |
|
|
|
|
|
|
|
93,6 |
||
|
Инфляция |
|
|
|
|
|
|
|
103,8 |
||
|
Промышленность |
|
|
|
|
|
|
|
106,9 |
||
|
Добыча топливно-энергетических полезных ископаемых |
|
|
|
|
|
|
113,3 |
|||
|
Производство и распределение электроэнергии, газа и воды |
|
|
|
|
|
111,1 |
||||
|
Грузовые железнодорожные перевозки |
|
|
|
|
|
|
|
107,5 |
||
|
Металлургическое производство* |
|
|
|
|
|
|
|
110,2 |
||
|
Добыча железных руд |
|
|
|
|
|
|
|
126,7 |
||
|
Производство чугуна и доменных ферросплавов |
|
|
|
|
|
|
|
113,1 |
||
|
Производство горячекатаного стального проката |
|
|
|
|
|
|
|
117,1 |
||
|
Производство холоднокатаного плоского проката |
|
|
|
|
|
|
|
111,1 |
||
|
Производство чугунных и стальных труб |
|
|
|
|
|
|
|
107,8 |
||
|
Производство электроферросплавов |
|
|
|
|
|
|
|
101,4 |
||
|
Производство кокса |
|
|
|
|
|
|
|
111,5 |
||
|
Огнеупорные изделия |
|
|
|
|
|
|
|
106,8 |
||
|
* Индекс изменения цен по металлургическому производству установлен Федеральной службой |
|
государственной |
||||||||
|
статистики РФ без учета данных по добыче железных руд, производства кокса и изделий огнеупорных. |
|
|
||||||||
|
В I кв. 2011 г. отмечается рост средних цен в |
торым видам металлопродукции в I кв. 2011 г. |
|||||||||
|
целом по металлургическому производству. |
|
приведена в табл. 6. |
|
|
|
|
||||
|
Динамика цен на российском рынке по неко- |
|
|
|
|
|
|
|
|
||
|
ТАБЛИЦА 6. ЦЕНЫ НА ПРОДУКЦИЮ ЧЕРНОЙ МЕТАЛЛУРГИИ, руб/т |
|
|
||||||||
|
|
|
|
|
|
|
|
|
|
|
|
|
Продукция |
|
Декабрь 2010 г. |
|
|
2011 г. |
|
|
|||
|
|
январь |
|
февраль |
|
март |
|||||
|
|
|
|
|
|
|
|
||||
|
Руда железная товарная необогащенная |
|
|
1103 |
|
1065 |
|
1320 |
|
|
1343 |
|
Концентрат железорудный |
|
|
2264 |
|
2313 |
|
2753 |
|
|
2914 |
|
Агломерат железорудный доменный |
|
|
3230 |
|
3280 |
|
3965 |
|
|
4290 |
|
Окатыши железорудные (окисленные) |
|
|
3458 |
|
3644 |
|
4292 |
|
|
4727 |
|
Чугун передельный нелегированный |
|
|
12784 |
|
13932 |
|
15027 |
|
|
14472 |
|
Прокат: |
|
|
|
|
|
|
|
|
|
|
|
толстолистовой (от 4 мм) горячекатаный из |
|
|
|
|
|
|
|
|
|
|
|
стали, кроме нержавеющей и быстрорежущей |
|
|
19811 |
|
20529 |
|
21322 |
|
|
23725 |
|
тонколистовой (до 4 мм) горячекатаный из |
|
|
|
|
|
|
|
|
|
|
|
стали, кроме нержавеющей и быстрорежущей |
|
|
17183 |
|
17906 |
|
19747 |
|
|
21463 |
|
плоский холоднокатаный из стали, кроме |
|
|
|
|
|
|
|
|
|
|
|
нержавеющей и быстрорежущей |
|
|
26091 |
|
25560 |
|
26078 |
|
|
29772 |
|
Катанка из нелегированной стали |
|
|
18360 |
|
18356 |
|
18676 |
|
|
20646 |
|
Рельсы из черных металлов, включая токоведущие |
|
|
|
|
|
|
|
|
|
|
|
рельсы с деталями из цветных металлов |
|
|
17648 |
|
17811 |
|
17546 |
|
|
17960 |
|
Трубы стальные: |
|
|
40888 |
|
43200 |
|
43290 |
|
|
45088 |
|
бесшовные для нефте- и газопроводов черных |
|
|
|
|
|
|
|
|
|
|
|
металлов (кроме литейного чугуна) |
|
|
41711 |
|
39991 |
|
42261 |
|
|
42602 |
|
обсадные |
|
|
35229 |
|
36481 |
|
38732 |
|
|
38858 |
|
Трубы сварные, клепаные или соединенные |
|
|
|
|
|
|
|
|
|
|
|
аналогичным способом для нефте- и газопроводов |
|
|
|
|
|
|
|
|
|
|
|
из черных металлов наружным диаметром более |
|
|
53814 |
|
54609 |
|
52747 |
|
|
58253 |
|
406,4 мм |
|
|
|
|
|
|
ОАО «Черметинформация» • Бюллетень «Черная металлургия» • 7• 2011 ―――――――――――――――― |
9 |

В I кв. 2011 г. по сравнению с I кв. 2010 г. сни- |
1 руб. реализованной продукции на 3,4 коп. Про- |
|||||||||||||
зилась рентабельность продаж на рассматри- |
изводительность труда в стоимостном выраже- |
|||||||||||||
ваемых ведущих металлургических комбинатах |
нии выросла на 31,5 %. Снижение чистой при- |
|||||||||||||
на 1,4 %, возросли затраты на 1 руб. реализо- |
были составило 2,7 %. |
|
|
|
||||||||||
ванной продукции на 1,4 коп. Производитель- |
|
Данные, характеризующие экономические по- |
||||||||||||
ность труда в стоимостном выражении выросла |
казатели работы крупных комбинатов и ведущих |
|||||||||||||
на 44,1 %. Рост чистой прибыли составил 11,4 %. |
заводов трубной промышленности, приведены в |
|||||||||||||
На крупных трубных заводах в I кв. 2011 г. по |
табл. 7 и 8. В рассматриваемом периоде темп |
|||||||||||||
сравнению с I кв. 2010 г. снизилась рентабель- |
роста инфляции издержек был выше темпа |
|||||||||||||
ность продаж на 3,4 |
%, возросли затраты на |
роста выручки от реализации продукции. |
|
|||||||||||
|
ТАБЛИЦА 7. ЭКОНОМИЧЕСКИЕ ПОКАЗАТЕЛИ, ХАРАКТЕРИЗУЮЩИЕ РАБОТУ |
|
||||||||||||
|
|
|
|
|
МЕТАЛЛУРГИЧЕСКИХ КОМБИНАТОВ |
|
|
|
||||||
|
|
|
|
|
|
|
|
|
|
|
|
|
|
|
|
|
Прибыль от |
|
Затраты на 1 руб. |
|
Рентабельность |
Производительность |
Чистая прибыль, |
||||||
|
|
реализации |
|
реализованной |
|
|||||||||
Предприятие |
|
|
|
продаж, % |
труда, тыс. руб/чел.* |
млн руб. |
||||||||
|
продукции, млн руб. |
|
продукции, коп. |
|
||||||||||
|
|
2011 г. |
|
2010 г. |
|
2011 г. |
2010 г. |
|
2011 г. |
2010 г. |
2011 г. |
2010 г. |
2011 г. |
2010 г. |
ЗСМК |
|
2121,3 |
|
449,7 |
|
93,1 |
97,8 |
|
6,9 |
2,2 |
10496,5 |
6829,3 |
599,7 |
−229,6 |
ММК |
|
7922,7 |
|
5946,1 |
|
87,3 |
85,9 |
|
12,7 |
14,1 |
11843,2 |
7745,8 |
4516,7 |
6310,4 |
НТМК |
|
2952,9 |
|
4063,5 |
|
88,5 |
77,1 |
|
11,5 |
22,9 |
6551,8 |
4518,3 |
1127,8 |
3873,7 |
НЛМК |
|
5648,3 |
|
5087,6 |
|
87,3 |
85,6 |
|
12,7 |
14,4 |
6000,9 |
4615,9 |
6962,5 |
2659,4 |
ОЭМК |
|
3278,2 |
|
1724,7 |
|
80,8 |
85,5 |
|
19,2 |
14,5 |
5904,0 |
4316,8 |
2926,1 |
2307,8 |
ЧелМК |
|
1913,0 |
|
234,4 |
|
92,9 |
98,7 |
|
7,1 |
1,3 |
7076,5 |
4757,6 |
1851,4 |
47,4 |
ЧерМК |
|
9032,8 |
|
8167,4 |
|
84,8 |
80,3 |
|
15,2 |
19,7 |
10448,4 |
7274,0 |
8201,1 |
8403,8 |
Итого по |
|
|
|
|
|
|
|
|
|
|
|
|
|
|
перечисленным |
|
|
|
|
|
|
|
|
|
|
|
|
|
|
предприятиям |
|
32869,2 |
|
25673,4 |
|
87,7 |
86,3 |
|
12,3 |
13,7 |
8358,5 |
5798,9 |
26185,2 |
23510,1 |
* В расчете на год |
. |
|
|
|
|
|
|
|
|
|
|
|
|
ТАБЛИЦА 8. ЭКОНОМИЧЕСКИЕ ПОКАЗАТЕЛИ, ХАРАКТЕРИЗУЮЩИЕ РАБОТУ ВЕДУЩИХ ТРУБНЫХ ЗАВОДОВ
|
Прибыль от |
Затраты на |
|
|
Производительность |
|
|
||||
|
1 руб. |
Рентабельность |
Чистая прибыль, |
||||||||
Предприятие |
реализации |
реализованной |
продаж, % |
труда, |
млн руб. |
||||||
продукции, млн руб. |
тыс. руб/чел.* |
||||||||||
|
продукции, коп. |
|
|
|
|
||||||
|
2011 г. |
2010 г. |
2011 г. |
2010 г. |
2011 г. |
2010 г. |
2011 г. |
2010 г. |
2011 г. |
2010 г. |
|
ВТЗ |
1887,1 |
2086,2 |
88,4 |
81,9 |
11,6 |
18,1 |
5186,5 |
4062,6 |
1227,4 |
1621,2 |
|
ВМЗ |
5550,0 |
7528,9 |
79,6 |
70,9 |
20,4 |
29,1 |
9587,4 |
10004,4 |
4457,0 |
6259,0 |
|
ПНТЗ |
1082,9 |
430,7 |
86,7 |
91,7 |
13,3 |
8,3 |
3207,0 |
2298,2 |
590,8 |
−155,3 |
|
СТЗ |
602,3 |
105,0 |
91,4 |
98,0 |
8,6 |
2,0 |
3971,2 |
2709,4 |
145,0 |
23,6 |
|
СинТЗ |
348,0 |
13,1 |
94,5 |
99,7 |
5,5 |
0,3 |
3545,7 |
2575,2 |
64,4 |
−314,6 |
|
ТагМЗ |
172,7 |
−103,2 |
97,2 |
102,3 |
2,8 |
−2,3 |
2992,0 |
1983,2 |
−74,0 |
11,0 |
|
ЧТПЗ |
4704,1 |
2614,5 |
76,6 |
71,6 |
23,4 |
28,4 |
10457,5 |
5752,4 |
2488,1 |
1698,5 |
|
Итого по |
|
|
|
|
|
|
|
|
|
|
|
перечисленным |
|
|
|
|
|
|
|
|
|
|
|
предприятиям |
14347,1 |
12675,2 |
84,3 |
80,9 |
15,7 |
19,1 |
5680,4 |
4318,6 |
8898,6 |
9143,5 |
* В расчете на год.
Приоритетным направлением развития металлургических и трубных предприятий является интенсификация производства с целью получения продукции с высокой добавленной стоимостью и повышения качества продукции, расши-
рения рынков сбыта продукции, увеличения поставок на внутренний рынок. Продолжается реализация программ по сокращению затрат производства, прежде всего по снижению расхода сырья и топливно-энергетических ресурсов.
10 ―――――――――――――――――ОАО «Черметинформация» • Бюллетень «Черная металлургия» • 7• 2011

|
И. М. ИВАНОВА (ОАО “Черметинформация”) |
ИСПОЛЬЗОВАНИЕ МАТЕРИАЛЬНЫХ И ЭНЕРГЕТИЧЕСКИХ РЕСУРСОВ |
|
Изменение удельных затрат сырья, материа- |
нию с аналогичными показателями в I кв. 2010 г. |
лов и технологического топлива на производство |
приведено в табл. 1. |
чугуна, стали и проката в I кв. 2011 г. по сравне- |
|
ТАБЛИЦА 1. УДЕЛЬНЫЙ РАСХОД ОСНОВНЫХ МАТЕРИАЛОВ НА ПРОИЗВОДСТВО 1 т ЧУГУНА, СТАЛИ И ПРОКАТА В ЦЕЛОМ ПО ОТРАСЛИ ЧЕРНАЯ МЕТАЛЛУРГИЯ, кг
Материалы и технологическое топливо |
I кв. 2010 г. |
I кв. 2011 г. |
Изменение |
При производстве чугуна |
|
|
|
Железорудная часть шихты |
1648,4 |
1637,8 |
−10,6 |
В том числе: |
10,4 |
13,1 |
+2,7 |
руда железная доменная |
|||
агломерат |
1133,5 |
1163,3 |
+29,8 |
окатыши |
504,5 |
461,5 |
−43,0 |
Металлодобавки |
13,2 |
14,1 |
+0,9 |
Скиповый кокс (сухой) |
437 |
437,5 |
+0,5 |
Природный газ, м3 |
101,1 |
103,8 |
+2,7 |
Кислород, м3 |
98,8 |
104,0 |
+5,2 |
Известняк (весь расход) |
126,4 |
130,8 |
+4,4 |
В том числе в доменную печь |
0,6 |
22,6 |
+22,3 |
При производстве стали |
|
|
|
Металлошихта |
1142,1 |
1143,6 |
+1,5 |
В том числе: |
755,7 |
722,4 |
−33,3 |
чугун |
|||
шихтовая заготовка |
0,6 |
0,7 |
+0,1 |
стальной лом |
317,9 |
354,1 |
+36,2 |
чугунный лом |
2,7 |
2,0 |
−0,7 |
металлизованные окатыши |
47,6 |
45,6 |
−2,0 |
железо из руды |
2,4 |
2,3 |
−0,1 |
раскислители и легирующие |
15,2 |
16,5 |
+1,3 |
Кислород, м3 |
57,9 |
56,1 |
−1,8 |
Природный газ, м3 |
10,5 |
10,5 |
|
При производстве проката |
|
|
|
Всего стали на готовый прокат |
1100,6 |
1095,1 |
−5,5 |
В том числе: |
1259,1 |
1193,5 |
−65,6 |
слитки |
|||
литая заготовка |
1092,9 |
1092,0 |
−0,9 |
Как видно из данных табл. 1, в доменном про- |
− расход кислорода увеличился на 5,2 м3/т. |
||
изводстве по итогам работы в I кв. 2011 г. по |
Состав железорудной части шихты (ЖРЧ) ха- |
||
сравнению с аналогичным периодом 2010 г. в |
рактеризуется изменением соотношения основ- |
||
целом по отрасли произошло изменение удель- |
ных компонентов: расход агломерата увели- |
||
ных затрат шихтовых материалов на 1 т выплав- |
чился на 29,8 кг/т, расход окатышей снизился на |
||
ленного чугуна: |
43,0 кг/т. |
|
|
− суммарный расход железорудной шихты |
Данные об изменении удельного расхода |
||
снизился на 10,6 кг/т; |
ЖРЧ, содержания железа в ЖРЧ и расхода ски- |
||
− расход скипового кокса снизился на 0,5 кг/т; |
пового кокса по доменным цехам приведены в |
||
− расход природного газа увеличился на 2,7 |
табл. 2 и 3. |
|
|
м3/т; |
|
|
|
ОАО «Черметинформация» • Бюллетень «Черная металлургия» • 7• 2011 ―――――――――――――――― 11

ТАБЛИЦА 2. ИЗМЕНЕНИЕ УДЕЛЬНОГО РАСХОДА ЖРЧ НА ПЕРЕДЕЛЬНЫЙ ЧУГУН И СОДЕРЖАНИЯ ЖЕЛЕЗА В ШИХТЕ ПО ПРЕДПРИЯТИЯМ
|
Расход ЖРЧ, кг/т чугуна |
Изменение, |
Содержание железа |
|||
Предприятие |
|
|
в ЖРЧ, % |
|||
I кв. 2010 г. |
I кв. 2011 г. |
кг/т |
||||
|
I кв. 2010 г. |
I кв. 2011 г. |
||||
|
|
|
|
|||
ЧерМК |
1593,4 |
1566,7 |
−26,7 |
60,2 |
60,4 |
|
НЛМК |
1602,6 |
1601,7 |
−0,9 |
Нет. св. |
Нет. св. |
|
ММК |
1674,1 |
1656,5 |
−17,6 |
58,4 |
58,0 |
|
ЧелМК |
1644,0 |
1633,6 |
−10,4 |
58,3 |
58,8 |
|
НТМК (ванадиевый чугун) |
1699,3 |
1703,5 |
+4,2 |
57,0 |
56,7 |
|
ЗСМК |
1677,3 |
167,5 |
−2,8 |
Нет. св. |
Нет. св. |
|
“Тулачермет” |
1642,6 |
1616,7 |
−25,9 |
57,2 |
57,7 |
|
Чусовской МЗ (ванадиевый чугун) |
1754,9 |
1752,5 |
−2,4 |
57,1 |
56,1 |
|
“Уральская сталь” |
1727,5 |
1738,3 |
+10,8 |
56,4 |
57,2 |
|
МЗ им. А.К. Серова |
1827,0 |
1807,7 |
−19,3 |
52,9 |
52,4 |
ТАБЛИЦА 3. УДЕЛЬНЫЙ РАСХОД СКИПОВОГО КОКСА (В СУХОМ ВЕСЕ) НА 1 т ПЕРЕДЕЛЬНОГО ЧУГУНА, кг
Предприятие |
|
|
I кв. 2010 г. |
|
I кв. 2011 г. |
Изменение |
НТМК |
|
|
406,8 |
|
398,9 |
−7,9 |
ЧерМК |
|
|
414,0 |
|
419,8 |
+5,8 |
НЛМК |
|
|
414,8 |
|
421,1 |
+6,3 |
ЗСМК |
|
|
441,4 |
|
446,6 |
+5,2 |
ММК |
|
|
449,3 |
|
445,2 |
−4,1 |
“Уральская сталь” |
|
|
538,8/3,9* |
|
499,6/0* |
−39,2/−3,9* |
“Тулачермет” |
|
|
458,0 |
|
466,8 |
+8,8 |
ЧелМК |
|
|
443,6 |
|
455,1 |
+11,5 |
МЗ им. А.К. Серова |
|
510,2/20,0* |
|
529,2/7,9* |
+19,0/−12,1* |
|
Чусовской МЗ |
|
|
523,0 |
|
499,4 |
−23,6 |
* В знаменателе каменный уголь. |
|
|
|
|
|
|
Как видно из данных табл. 2, практически на |
|
|
|
|
||
всех предприятиях отрасли в I кв. 2011 г. по |
|
|
|
|
||
сравнению с аналогичным периодом прошлого |
|
|
|
|
||
года произошло снижение удельного расхода |
|
|
|
|
||
ЖРЧ. Возрос расход ЖРЧ на 1 т чугуна только на |
|
|
|
|
||
НТМК (4,2 кг) и “Уральской стали” (10,8 кг). |
|
|
|
|
|
|
Качество железорудной шихты по содержа- |
|
|
|
|
||
нию железа улучшилось на ЧелМК (+0,5 |
%), |
|
|
|
|
|
“Уральской стали” (+0,8 %) и “Тулачермете” |
|
|
|
|
||
(0,5 %). |
|
|
|
|
|
|
По расходу скипового кокса в течение I кв. |
|
|
|
|
||
2011 г. с перерасходом работали ЧерМК (+5,8 |
|
|
|
|
||
кг/т), НЛМК (6,3 кг/т), ЗСМК (+5,2 кг/т), |
МЗ |
|
|
|
|
|
им. А.К. Серова (+19,0 кг/т). |
|
|
|
|
|
|
Одним из факторов, повлиявшим на перерас- |
|
|
|
|
||
ход кокса по перечисленным предприятиям, яви- |
|
|
|
|
||
лось снижение температуры горячего дутья до- |
|
|
|
|
||
менной плавки. На НЛМК снижение температуры |
Рис. 1. Температура горячего дутья доменных печей |
|||||
горячего дутья составило 12 °С, на ЗСМК 8 °С, |
Суммарный показатель затрат сырьевых ма- |
|||||
на МЗ им. А.К. Серова 60 °С. Кроме того, на |
||||||
МЗ им. А.К. Серова на 12,1 кг/т снижен расход |
териалов доменной плавки (железорудные ма- |
|||||
каменного угля как дополнительного источника |
териалы, кокс, природный газ, кислород), рас- |
|||||
тепловой энергии. |
|
считанный по |
коэффициентам |
энергоемкости |
||
Данные об изменении температуры горячего |
каждого материала и топлива, приведен как |
|||||
дутья приведены на рис. 1. |
|
удельная энергоемкость чугуна на рис. 2. |
12 ―――――――――――――――――ОАО «Черметинформация» • Бюллетень «Черная металлургия» • 7• 2011

Наибольшую энергоемкость чугуна (более 700 кг у.т/т чугуна) в I кв. 2011 г. имели “Уральская сталь” и МЗ им. А.К. Серова, минимальные энергозатраты НЛМК, НТМК и ЧерМК, т. е. комбинаты с наименьшим расходом скипового кокса.
При производстве стали в I кв. 2011 г. по сравнению с аналогичным периодом 2010 г. в целом по отрасли расход металлошихты на производство стали увеличился на 0,5 кг/т. В составе металлошихты расход чугуна снизился на 35,1 кг/т, металлизованных окатышей на 2,0 кг/т. Расход стального лома увеличился на 37,0 кг/т, раскислителей и легирующих на 1,3 кг/т. Остальные показатели расхода сырья и топлива
|
существенно не изменились (см. табл. 1). |
||||
|
Работа большинства конвертерных цехов ха- |
||||
|
рактеризуется снижением расхода чугуна по |
||||
|
сравнению с аналогичным периодом прошлого |
||||
|
года. Исключение составили ММК (перерасход |
||||
Рис. 2. Удельная энергоемкость передельного чугуна |
10,6 кг/т) и ЧерМК (перерасход 11,4 кг/т) (табл. 4). |
||||
ТАБЛИЦА 4. ИЗМЕНЕНИЕ УДЕЛЬНОГО РАСХОДА ЧУГУНА ПРИ ПРОИЗВОДСТВЕ |
|
|
|||
КОНВЕРТЕРНОЙ СТАЛИ, кг/т |
|
|
|
|
|
|
|
|
|
|
|
Предприятие |
I кв. 2010 г. |
I кв. 2011 г. |
|
Изменение |
|
В целом по отрасли |
913,2 |
901,5 |
|
−11,7 |
|
ЗСМК |
851,0 |
815,0 |
|
−36,0 |
|
ММК |
878,6 |
889,2 |
|
+10,6 |
|
ЧерМК |
858,9 |
810,3 |
|
+11,4 |
|
НЛМК* |
940,5 |
929,0 |
|
−11,5 |
|
ЧелМК |
993,8 |
918,6 |
|
−75,2 |
|
НТМК |
1083,0 |
1063,6 |
|
−19,4 |
|
* В связи с внедрением и отработкой на комбинате информационно-интегрированной системы SAP ERP удельный
расход чугуна принят на уровне расхода в 2010 г.
На рис. 3 приведены результаты расчетов удельной энергоемкости конвертерной стали.
Из данных рис. 3 следует, что удельная энергоемкость конвертерной стали находится в прямой зависимости от расхода чугуна и его энергоемкости, полученной в доменном переделе.
В электросталеплавильном производстве снижен удельный расход чугуна на большинстве предприятий с полным металлургическим циклом (т. е. имеющих в своем составе доменные цеха). В табл. 5 это предприятия, входящие в первую группу. Исключением является ММК, где перерасход чугуна составил 16,0 кг/т электропечной стали.
Рис. 3. Удельная энергоемкость конвертерной стали
ОАО «Черметинформация» • Бюллетень «Черная металлургия» • 7• 2011 ―――――――――――――――― 13

ТАБЛИЦА 5. УДЕЛЬНЫЙ РАСХОД ЧУГУНА ПРИ ПРОИЗВОДСТВЕ ЭЛЕКТРОСТАЛИ, кг/т
Группа |
Предприятие |
I кв. 2010 г. |
I кв. 2011 г. |
Доля чугуна в шихте, % |
||
I кв. 2010 г. |
I кв. 2011 г. |
|||||
|
|
|
|
|||
|
Всего по отрасли |
217,7 |
207,6 |
|
|
|
|
ММК |
242,0 |
258,0 |
21,1 |
22,3 |
|
|
НКМК |
343,1 |
232,0 |
30,9 |
20,9 |
|
1 |
“Уральская сталь” |
436,7 |
377,8 |
38,6 |
33,6 |
|
ЧерМК |
338,6 |
335,5 |
29,3 |
29,0 |
||
|
||||||
|
ЧелМК |
366,9 |
310,4 |
33,1 |
27,4 |
|
|
МЗ им. А.К. Серова |
464,6 |
383,2 |
39,5 |
32,9 |
|
|
МЗ “Красный Октябрь” |
2,8 |
3,3 |
0,24 |
0,28 |
|
|
“Электросталь” |
4,9 |
8,4 |
0,42 |
0,72 |
|
2 |
“Ижсталь” |
4,1 |
0 |
0,35 |
|
|
|
Златоустовский МЗ |
7,6 |
4,5 |
0,66 |
0,38 |
|
|
Северский ТПЗ |
78,2 |
3,6 |
6,67 |
0,31 |
В целом по отрасли удельный расход чугуна |
Расчеты удельной энергоемкости электро- |
||||
на электроплавку снижен с 217,7 до 207,6 кг/т, |
печной стали показывают, что прямой зависимо- |
||||
или на 10,1 кг/т (см. табл. 5). Доля чугуна в шихте |
сти между расходом чугуна и энергоемкостью |
||||
по отрасли составляет 18,0 %, что на 0,9 % ниже |
нет, поскольку действуют еще и другие факторы, |
||||
аналогичного периода прошлого года. С пере- |
важнейшим из которых является расход элек- |
||||
расходом чугуна работали комбинаты: ЧерМК |
троэнергии на плавку. |
|
|||
(60,4 кг/т), ЧелМК (11,3 кг/т), МЗ им. А.К. Серова |
Данные об удельном расходе электроэнергии |
||||
(13,9 кг/т), что, в свою очередь, повлияло на ве- |
при производстве электростали |
приведены в |
|||
личину энергоемкости электропечной стали на |
табл. 6. |
|
|
|
|
этих предприятиях. |
|
|
|
|
|
ТАБЛИЦА 6. УДЕЛЬНЫЙ РАСХОД ЭЛЕКТРОЭНЕРГИИ ПРИ ПРОИЗВОДСТВЕ ЭЛЕКТРОСТАЛИ, кВт ч/т |
|||||
|
|
|
|
|
|
Предприятие |
|
I кв. 2010 г. |
I кв. 2011 г. |
|
Изменение |
ММК |
|
310,2 |
216,1 |
|
−94,1 |
ЧерМК |
|
274,8 |
265,3 |
|
−9,5 |
“Уральская сталь” |
|
258,1 |
254,2 |
|
−3,9 |
НКМК |
|
469,5 |
437,7 |
|
−31,8 |
ЧелМК |
|
347,4 |
346 |
|
−1,4 |
МЗ им. А.К. Серова |
|
345,8 |
324,0 |
|
21,8 |
МЗ “Красный Октябрь” |
|
552,2 |
558,9 |
|
+6,7 |
“Электросталь” |
|
717,3 |
731,5 |
|
+14,2 |
“Ижсталь” |
|
668,6 |
686,8 |
|
+18,2 |
Златоустовский МЗ |
|
935,9 |
874,1 |
|
−61,8 |
ОЭМК |
|
574,5 |
548,6 |
|
−25,9 |
Северский ТПЗ |
|
339,8 |
494,8 |
|
+155,1 |
На рис. 4 приведены результаты расчета удельной энергоемкости электростали по предприятиям.
При производстве проката среднеотраслевой показатель расхода стали на готовый прокат в I кв. 2011 г. по сравнению с аналогичным периодом 2010 г. снизился на 5,5 кг/т (см. табл. 1), при этом удельный расход литой заготовки уменьшился на 0,9 кг/т, расход слитков на 65,6 кг/т.
На общее снижение расхода стали на прокат повлияло изменение структуры заданного в прокат (доли слитков и литой заготовки). В целом по отрасли доля литой заготовки в прокатном производстве возросла с 79 до 80,8 % (табл. 7). Данные о доле литой заготовки, заданной в прокат, приведены в табл. 7.
Рис. 4. Удельная энергоемкость электростали
14 ―――――――――――――――――ОАО «Черметинформация» • Бюллетень «Черная металлургия» • 7• 2011

ТАБЛИЦА 7. ДОЛЯ ЛИТОЙ ЗАГОТОВКИ В СТРУКТУРЕ ЗАДАННОГО В ПРОКАТ, %
Предприятие |
I кв. 2010 г. |
I кв. 2011 г. |
Россия (ЧМ) |
79,0 |
80,8 |
ММК |
100,0 |
100,0 |
НЛМК |
100,0 |
100,0 |
ОЭМК |
100,0 |
100,0 |
ЧерМК |
100,0 |
100,0 |
НТМК |
100,0 |
100,0 |
НКМК |
73,6 |
77,8 |
ЧелМК |
53,7 |
51,6 |
ЗСМК |
34,1 |
39,0 |
“Уральская сталь” |
41,4 |
60,7 |
Показатели удельного расхода стали на готовый прокат на отдельных предприятиях за рассматриваемые периоды приведены в табл. 8.
ТАБЛИЦА 8. РАСХОД СТАЛИ НА ПРОИЗВОДСТВО ГОТОВОГО ПРОКАТА, кг/т
Предприятие |
I кв. 2010 г. |
I кв. 2011 г. |
Изменение |
ОЭМК |
1051,8 |
1054,0 |
+2,2 |
НЛМК* |
1052,9 |
1054,7 |
+1,8 |
ММК |
1088,6 |
1087,4 |
−1,2 |
ЗСМК |
1099,3 |
1043,7 |
−55,6 |
ЧерМК |
1084,4 |
1081,6 |
−2,8 |
НТМК |
1060,7 |
1064,6 |
+3,9 |
НКМК |
1105,7 |
1108,9 |
+3,2 |
ЧелМК |
1135,2 |
1156,1 |
+20,9 |
“Уральская сталь” |
1246,4 |
1190,2 |
−56,2 |
* В связи с внедрением и отработкой на комбинате информационно-интегрированной системы SAP ERP удельный
расход стали на прокат принят на уровне расхода в 2010 г.
Значительная экономия стали на прокат имела место на ЗСМК (−55,6 кг/т) и “Уральской стали” (−56,2 кг/т).
Результаты расчета удельной энергоемкости проката по отдельным металлургическим комбинатам приведены на рис. 5.
Рис. 5. Удельная энергоемкость проката
Оценивая сравнительные итоги работы предприятий черной металлургии по удельным затратам энергии на конечную продукцию (готовый прокат), можно отметить, что минимальный уровень удельных энергозатрат в отрасли показывают предприятия, имеющие а производстве высокую долю электростали и разливку на МНЛЗ.
По сравнению с аналогичным периодом прошлого года в I кв. 2011 г. существенно снижены удельные энергозатраты на НКМК, ОЭМК, ЗСМК, ЧелМК, а также на “Уральской стали”.
Из вышеизложенного следует, что за сравниваемый период (I кв. 2010 г. – I кв. 2011 г.) в целом по предприятиям черной металлургии России перерасходовано 6,8 тыс. т скипового кокса и сэкономлено 127,4 тыс. т железорудной шихты.
В сталеплавильном переделе сэкономлено 597,0 тыс. т чугуна, при производстве проката перерасходовано 74,3 тыс. т слитков и литой заготовки.
ОАО «Черметинформация» • Бюллетень «Черная металлургия» • 7• 2011 ―――――――――――――――― 15

УДК 669.1:658 О. В. ЮЗОВ1, А. М. СЕДЫХ2, С. З. АФОНИН3 ( 1 Национальный исследовательский технологический университет “МИСиС”, 2 Объединенная металлургическая компания, 3 Союз экспортеров металлопродукции России)
ЭКОНОМИЧЕСКИЕ ПОКАЗАТЕЛИ И ПРОБЛЕМЫ ПОСТКРИЗИСНОГО РАЗВИТИЯ ЧЕРНОЙ МЕТАЛЛУРГИИ РОССИИ
Максимальный до кризиса мировой объем |
Близкие по своему характеру к вышеописан- |
производства стали (1346 млн т) был достигнут в |
ным изменения объемов производства продук- |
2007 г. В 2008 г. в условиях начавшегося во вто- |
ции черной металлургии в условиях финансо- |
ром полугодии финансового кризиса мировой |
вого кризиса наблюдались и в России. |
объем производства стали снизился по сравне- |
В 1998−2008 гг. в отечественной черной ме- |
нию с 2007 г. на 1,4 %. В 2009 г. падение миро- |
таллургии происходили большие позитивные из- |
вого объема производства стали продолжилось |
менения объемов производства, технического |
и составило по отношению к 2008 г. 7,4 %, в I, II |
уровня производства и его экономических пока- |
и III кв. 2009 г. по сравнению с соответствую- |
зателей. |
щими периодами 2008 г. оно составило 22,8; 19,9 |
Объемы производства черных металлов (чу- |
и 6,2 % соответственно. В IV кв. 2009 г. мировой |
гуна, стали и проката) увеличились за 1998− |
объем производства стали увеличился по срав- |
2007 гг. на 48−69 %, стальных труб в 3,1 раза, |
нению с IV кв. 2008 г. на 24,1 % [1]. |
сырья (кокса и руды) на 43−44 % (табл. 1). |
В 2010 г. мировой объем производства стали |
Структура производства продукции отрасли |
достиг 1414 млн т, т. е. увеличился по сравнению с |
улучшилась, так как темпы роста объемов произ- |
2009 г. на 15 % и превысил уровень 2007 на 5 %. |
водства конечной продукции (проката и тем более |
При этом во всех промышленно развитых странах |
стальных труб) были выше, чем стали, стали |
объем производства стали в 2010 г. оказался |
выше, чем чугуна, а чугуна выше, чем руды и |
заметно ниже максимального докризисного уровня. |
кокса. |
ТАБЛИЦА 1. ПРОИЗВОДСТВО ОСНОВНЫХ ВИДОВ ПРОДУКЦИИ ЧЕРНОЙ МЕТАЛЛУРГИИ В РОССИИ, млн т
Продукция |
|
|
|
|
|
|
|
Год |
|
|
|
|
|
|
|
1990 |
|
1998 |
|
2000 |
2005 |
|
2007 |
2008 |
|
2009 |
2010 |
|
|
|
|
|
|
|
|
|
||||||||
Чугун |
|
59,4 |
|
34,7 |
|
44,6 |
49,2 |
|
51,5 |
48,3 |
|
44,0 |
48,2 |
|
Сталь |
|
89,6 |
|
43,7 |
|
59,2 |
66,3 |
|
72,4 |
68,7 |
|
59,2 |
66,3 |
|
Готовый прокат |
|
63,7 |
|
35,2 |
|
46,7 |
54,7 |
|
59,6 |
56,7 |
|
52,4 |
57,8 |
|
Стальные трубы |
|
11,9 |
|
2,8 |
|
5,0 |
6,7 |
|
8,7 |
7,8 |
|
6,7 |
9,1 |
|
Кокс |
|
41,2 |
|
23,6 |
|
30,0 |
31,7 |
|
33,9 |
32,1 |
|
26,7 |
29,4 |
|
Железная руда |
|
106,8 |
|
72,6 |
|
86,8 |
95,1 |
|
105,0 |
100,1 |
|
92,0 |
102,0 |
|
Однако мировой финансовый кризис оказал |
водства в 2010 г. по-прежнему был на 8,4 % ниже, |
|||||||||||||
негативное влияние на развитие отечественной |
чем в 2007 г. Среднесуточное производство стали |
|||||||||||||
черной металлургии начиная с IV кв. 2008 г., когда |
в IV кв. 2010 г. на 6 % ниже, чем в 2007 г., и на |
|||||||||||||
падение объемов производства в октябре, ноябре |
10,6 % ниже, чем вI−III кв. 2008 г. |
|
|
|
||||||||||
и декабре приняло обвальный характер |
|
|
|
|
|
|
|
|
||||||
снижение по сравнению с соответствующими |
|
|
|
|
|
|
|
|
||||||
месяцами 2007 г. составило 21,0; 41,9 и 43,2 %. В |
|
|
|
|
|
|
|
|
||||||
целом за 2008 г. снижение отечественного объема |
|
|
|
|
|
|
|
|
||||||
производства стали по сравнению с 2007 г. |
|
|
|
|
|
|
|
|
||||||
составило 5,1 %,а в 2009 г. он уменьшился еще на |
|
|
|
|
|
|
|
|
||||||
13,9 %. Таким образом, если падение мирового |
|
|
|
|
|
|
|
|
||||||
объема производства стали за 2007−2009 гг. |
|
|
|
|
|
|
|
|
||||||
составило 8,7 %, то в России оно достигло 18,2 %. |
|
|
|
|
|
|
|
|
||||||
Начиная с I кв. 2009 г. среднесуточный объем |
|
|
|
|
|
|
|
|
||||||
производства стали в России постепенно увели- |
Рис. 1. Динамика среднесуточного производства стали |
|||||||||||||
чивался (рис. 1), |
однако годовой |
объем |
произ- |
|
|
|
|
|
|
|
|
16 ―――――――――――――――――ОАО «Черметинформация» • Бюллетень «Черная металлургия» • 7• 2011

Изменение объемов производства всех видов продукции обусловлено совместным влиянием двух факторов изменением внутреннего потребления и изменением величины сальдо внешней торговли. Рост внутреннего потребления отдельных видов продукции явился основной причиной прироста объема их производства в России в 1998−2007 гг. На долю этого фактора пришлась следующая часть общего прироста объема производства, %: руды 82, кокса 82, чугуна 80, стали 100, проката
91, труб 97 [2].
В2008 г. видимое потребление готовой стальной продукции в мире снизилось на 1,4 %. В 2009 г. падение мирового объема видимого потребления готовой стальной продукции продолжилось и составило 6,7 % по отношению к
2008 г. [1].
ВРоссии видимое потребление проката в
2008 и 2009 г. снизилось на 11,1 и 23,3 % соот-
ветственно [3]. В 2010 г. видимое потребление проката значительно увеличилось и составило 32,7 млн т по сравнению с 26,9 млн т в 2009 г.
Таким образом, в 2009−2010 гг. среднесуточное видимое потребление проката постепенно восстанавливалось (рис. 2), но и в 2010 г. оно составило в среднем лишь около 88 % от показателей 2007 г. При этом среднесуточное производство проката в 2010 г. было на уровне 97 % от показателей 2007 г. Такое соотношение стало следствием увеличения в 2007−2010 гг. среднесуточного сальдо внешней торговли прокатом на
11,5 % (рис. 3).
Рис. 2. Динамика среднесуточного видимого потребления готового проката
Рис. 3. Динамика среднесуточного сальдо внешней торговли России прокатом
За 2001−2010 гг. в черную металлургию России инвестировано более 1 трлн руб. (около 35 млрд долл.), в том числе в 2007–2010 гг. около 650 млрд руб. (около 23 млрд долл.), хотя в 2009 г. имело место сокращение объема инвестиций по сравнению с 2008 г. примерно на 20 %. Вследствие увеличения за период после 1998 г. объема инвестиций средний показатель степени износа основных фондов отрасли снижается, хотя и остается достаточно высоким, %: 1990 г. — 50,1;
1998 г. — 53,1; 2010 г. — 41,8 [4]. Тем не менее технический уровень производства растет, до 2008 г. улучшался также сортамент производимой продукции. На отечественных металлургических предприятиях в 2000–2010 гг. реализован и продолжает реализовываться ряд важнейших инвестиционных проектов.
Отметим некоторые результаты реализации указанных инвестиционных проектов за 2000−2010 гг. Производство мартеновской стали снизилось в 3,5 раза, а объем непрерывной разливки стали увеличился в 1,7 раза. Объем стали, подвергнутой внепечному вакуумированию, вырос более чем в 2 раза. Производство холоднокатаного листа увеличилось в 1,4 раза, а холоднокатаного листа с покрытиями в 2,5 раза.
За рассматриваемый период был практически решен вопрос по обеспечению строительства газовых и нефтяных магистралей отечественными трубами большого диаметра (до 1420 мм). Были введены в эксплуатацию современные трубоэлектросварочные станы на Выксунском металлургическом, Ижорском трубном, Волжском трубном и Челябинском трубопрокатном заводах. При этом вплоть до последнего времени
ОАО «Черметинформация» • Бюллетень «Черная металлургия» • 7• 2011 ―――――――――――――――― 17
для производства труб большого диаметра оте- |
2008 гг. примерно в 10,7 раза в рублевой оценке |
|||||
чественные предприятия вынуждены были заку- |
и в 4,3 раза в долларовом эквиваленте. Необхо- |
|||||
пать по импорту широкий толстолистовой про- |
димо подчеркнуть, что значительное повышение |
|||||
кат. Однако после коренной реконструкции лис- |
себестоимости |
товарной |
продукции |
отрасли |
||
топрокатного цеха “Северстали” со станом 5000, |
произошло, несмотря на улучшение показателей |
|||||
пуска в 2009 г. такого же стана на Магнитогор- |
использования всех видов потребляемых и ис- |
|||||
ском металлургическом комбинате и ожидаемого |
пользуемых на предприятиях ресурсов в нату- |
|||||
пуска в середине 2011 г. стана 5000 на Выксун- |
ральном выражении. За 1998–2008 гг. средний |
|||||
ском металлургическом заводе эта проблема |
расходный коэффициент стали на прокат сни- |
|||||
будет полностью решена. |
|
зился с 1175 до 1112 кг/т, средний удельный |
||||
Можно отметить реализацию и некоторых |
расход электроэнергии на производство элек- |
|||||
других инвестиционных проектов, имеющих |
тростали и готового проката — на 31 и 19 % со- |
|||||
принципиальное значение для повышения тех- |
ответственно, средний удельный расход топлива |
|||||
нического уровня отечественной черной метал- |
на производство готового проката — на 38 %, |
|||||
лургии, ввод в IV кв. 2008 г. Объединенной |
средняя производительность труда увеличилась |
|||||
металлургической компанией в г. Выкса первой |
в 1,8 раза, а средний коэффициент использова- |
|||||
очереди литейно-прокатного комплекса по вы- |
ния производственных мощностей в сталепла- |
|||||
пуску рулонных штрипсов (заготовки для произ- |
вильном и прокатном производствах вырос с 59– |
|||||
водства труб диаметром до 530 мм) мощностью |
63 до 83–89 %. |
|
|
|
||
1,2 млн т и ожидаемый ввод в 2011 г. первой |
Однако положительное |
влияние указанных |
||||
очереди стана 2000 холодной прокатки на Маг- |
изменений было перекрыто удорожанием всех |
|||||
нитогорском металлургическом комбинате (пол- |
потребляемых и используемых ресурсов. Сред- |
|||||
ная мощность комплекса составит 2,0 млн т). |
ние цены на потребляемые отраслью электро- |
|||||
В настоящее время впервые за постсоветский |
энергию, природный газ и уголь для коксования |
|||||
период на |
Новолипецком |
металлургическом |
за 1998–2008 гг. увеличились в 5,5; 6,7 и 8,9 раза |
|||
комбинате решается задача значительного уве- |
соответственно, а тарифы на железнодорожные |
|||||
личения объема производства продукции за счет |
грузовые перевозки — в 6,9 раза. Средняя номи- |
|||||
нового строительства. В 2011 г. на комбинате |
нальная заработная плата персонала увеличи- |
|||||
ожидается пуск доменной печи № 7 мощностью |
лась примерно в 12 раз, а средняя реальная |
|||||
3,4 млн т, оснащенной впервые в нашей стране |
зарплата — примерно в 1,8 раза. Стоимость ос- |
|||||
установкой |
для вдувания пылеугольного |
новных фондов отрасли выросла более чем в 2 |
||||
топлива, и кислородного конвертера емкостью |
раза. |
|
|
|
||
300 т с целью увеличения объема выплавки |
Динамика экономических показателей пред- |
|||||
стали до 12,4 млн т. |
|
приятий отрасли приведена в табл. 2. Анализ по- |
||||
В период финансового кризиса повышению |
казывает, что основным фактором улучшения |
|||||
среднего по отрасли технического уровня произ- |
экономических |
показателей металлургических |
||||
водства способствует также ускорение вывода |
предприятий после 1998 г. был рост цен на ме- |
|||||
из эксплуатации устаревших цехов и отдельных |
таллопродукцию. Внутренние цены на передель- |
|||||
металлургических агрегатов. Объем производ- |
ный чугун, готовый прокат и стальные трубы с |
|||||
ства стали в 2009 г. сократился по сравнению с |
декабря 1998 г. по август 2008 г. в рублевой |
|||||
2008 г. на 9,5 млн т, или на 13,8 %, в том числе |
оценке увеличились в 18,8; 10,3 и 10,6 раза, а в |
|||||
конвертерной стали — на 2,1 %, электростали — |
долларовом эквиваленте — в 15,5; 8,5 и 8,7 раза |
|||||
на 19,5 %, а мартеновской стали — практически |
соответственно. Такой рост цен позволил не |
|||||
в 2 раза. Это сопровождалось значительным |
только поддерживать в 2000–2007 гг. средний |
|||||
увеличением доли конвертерной и электростали |
показатель рентабельности |
продукции |
отрасли |
|||
и доли непрерывной разливки стали в общем |
на уровне около 23 %, но и довести его в III кв. |
|||||
объеме производства. |
|
2008 г. до 32 %. Однако в условиях финансового |
||||
Важнейшая внутренняя |
проблема развития |
кризиса рентабельность продукции отрасли в IV |
||||
отрасли — быстрый рост себестоимости всех |
кв. 2008 г. упала до 3 %, а в 2009 и 2010 г. соста- |
|||||
видов продукции. Средняя себестоимость еди- |
вила 14,3 и 14,5 % соответственно. |
|
||||
ницы товарной продукции увеличилась за 1998– |
|
|
|
|
18 ―――――――――――――――――ОАО «Черметинформация» • Бюллетень «Черная металлургия» • 7• 2011

ТАБЛИЦА 2. ДИНАМИКА ЭКОНОМИЧЕСКИХ ПОКАЗАТЕЛЕЙ РАБОТЫ ПРЕДПРИЯТИЙ ЧЕРНОЙ МЕТАЛЛУРГИИ РОССИИ
Показатель |
|
|
|
Год |
|
|
|
|
1998 |
2000 |
2005 |
2007 |
2008 |
2009 |
2010 |
||
|
||||||||
Индексы цен и тарифов, ед.*1 |
|
|
|
|
|
|
|
|
электроэнергия |
1 |
1,71 |
3,66 |
4,64 |
5,50 |
6,24 |
7,17 |
|
природный газ |
1 |
1,39 |
4,22 |
5,47 |
6,73 |
6,46 |
7,39 |
|
уголь для коксования |
1 |
2,45 |
6,15 |
5,99 |
8,95 |
6,34 |
9,69 |
|
железнодорожные грузовые перевозки |
1 |
1,86 |
4,83 |
5,66 |
6,91 |
7,64 |
8,36 |
|
Индекс внутренних цен на продукцию черной |
|
|
|
|
|
|
|
|
металлургии, ед. |
1 |
2,44 |
7,03 |
8,89 |
11,96 |
8,57 |
11,12 |
|
Индекс средних экспортных цен проката, ед. |
1 |
0,89 |
1,97 |
2,60 |
3,59 |
1,83 |
2,34 |
|
Среднегодовая численность промышленно- |
|
|
|
|
|
|
530*3 |
|
производственного персонала, тыс. чел. |
673 |
711 |
670 |
662 |
600 |
550 |
||
Индекс производительности труда, ед.*2 |
1 |
1,28 |
1,52 |
1,68 |
1,76 |
1,65 |
1,92*3 |
|
Среднемесячная заработная плата промышленно- |
|
|
|
|
|
|
18000*3 |
|
производственного персонала, руб. |
1432 |
3521 |
10830 |
15300 |
17000 |
17150 |
||
Средняя рентабельность продукции, % |
10,3 |
25,6 |
23,8 |
24,0 |
22,6 |
14,3 |
14,5*3 |
|
Сальдированный финансовый результат (прибыль |
|
|
|
|
|
|
270,0*3 |
|
минус убыток), млрд руб. |
–9,0 |
68,4 |
284,2 |
430,0 |
484,5 |
94,8 |
||
*1 На конец периода в целом по отрасли. |
|
|
|
|
|
|
|
|
*2 Производительность труда рассчитана по выплавке стали на одного работающего. |
|
|
|
|||||
*3 Оценка. |
|
|
|
|
|
|
|
|
Подробный анализ влияния финансового кри- |
нить на основе динамики экспортных цен на оте- |
|||||||
зиса на производственно-технические и эконо- |
чественный прокат (рис. 5). В 2009 и 2010 г. цены |
|||||||
мические показатели работы предприятий чер- |
снизились по сравнению с их максимальным |
|||||||
ной металлургии провели на примере восьми |
значением, достигнутым в III кв. 2008 г., в 2,5 и 2 |
|||||||
крупнейших комбинатов — Магнитогорского, Че- |
раза соответственно. Характер изменения сред- |
|||||||
реповецкого, Новолипецкого, Западно-Сибир- |
них экспортных (см. рис. 5) и средних внутренних |
|||||||
ского, Нижнетагильского, Челябинского, “Ураль- |
(рис. 6) цен на прокат до начала и в период фи- |
|||||||
ской стали” и Оскольского. Динамика среднесу- |
нансового кризиса оказался практически одина- |
|||||||
точного объема производства проката на ука- |
ковым. Уровень цен в III кв. 2008 г. был в 1,7–1,8 |
|||||||
занных комбинатах за 2007–2010 гг. приведена |
раза выше, чем в 2007 г. В 2009–2010 гг. как экс- |
|||||||
на рис. 4. |
|
портные, так и внутренние цены значительно |
||||||
|
|
снизились по сравнению с их максимальным |
||||||
|
|
уровнем, достигнутым в III кв. 2008 г. Однако в |
||||||
|
|
2009 и 2010 г. средние внутренние цены умень- |
шились по сравнению с их максимальным значением, достигнутым в III кв. 2008 г., в гораздо меньшей степени, чем экспортные, в 1,9 и 1,4 раза соответственно (cм. рис. 6).
Рис. 4. Динамика среднесуточного производства проката на восьми комбинатах
В период финансового кризиса одновременно со снижением объема производства происходит
значительное изменение цен на металлопродук- Рис. 5. Динамика средних экспортных цен на прокат цию. Конъюнктуру мирового рынка можно оце-
ОАО «Черметинформация» • Бюллетень «Черная металлургия» • 7• 2011 ―――――――――――――――― 19

Рис. 6. Динамика средних показателей себестоимости и внутренних цен на прокат |
|
|
|
|
|||||||||||||
Уровень средней себестоимости проката в III |
вого кризиса средняя рентабельность продукции |
||||||||||||||||
и IV кв. 2008 г. оказался в 1,5 раза выше сред- |
металлургических комбинатов снизилась с 39,5 % |
||||||||||||||||
него уровня себестоимости в 2007 г. (см. рис. 6). |
в 2007 и 2008 г. до 15,8 % в 2009 г. и до 14,6 % в |
||||||||||||||||
Основной причиной роста себестоимости про- |
2010 г., т. е. более чем в 2,5 раза (рис. 7). |
|
|
||||||||||||||
дукции был рост цен на материальные ресурсы |
|
|
|
|
|
|
|
|
|
|
|||||||
производства. В 2008 г. их цены выросли по |
|
|
|
|
|
|
|
|
|
|
|
||||||
сравнению с 2007 г. в среднем в 1,4 раза. В 2009 г. |
|
|
|
|
|
|
|
|
|
|
|||||||
средние цены на материальные ресурсы вновь |
|
|
|
|
|
|
|
|
|
|
|
||||||
снизились практически до уровня 2007 г. Однако |
|
|
|
|
|
|
|
|
|
|
|
||||||
заметно возросли по сравнению с 2007 г. удель- |
|
|
|
|
|
|
|
|
|
|
|
||||||
ные затраты на оплату труда, амортизационные |
|
|
|
|
|
|
|
|
|
|
|
||||||
отчисления и прочие затраты. В связи с этим |
|
|
|
|
|
|
|
|
|
|
|
||||||
средняя себестоимость проката в 2009 г. оказа- |
|
|
|
|
|
|
|
|
|
|
|
||||||
лась ниже, чем в 2008 г., примерно на 19 %, но |
|
|
|
|
|
|
|
|
|
|
|
||||||
выше, чем в 2007 г., примерно на 10 %. В то же |
|
|
|
|
|
|
|
|
|
|
|
||||||
время средние цены на прокат в 2009 г. были |
|
|
|
|
|
|
|
|
|
|
|
||||||
примерно на 9 % ниже, чем в 2007 г. |
|
|
|
|
Рис. 7. Динамика средней рентабельности продукции |
||||||||||||
В 2010 г. и средняя себестоимость, и средняя |
|
Подробные данные о динамике экономиче- |
|||||||||||||||
цена на прокат были уже выше, чем в 2007 г. Но |
|
||||||||||||||||
себестоимость по сравнению с 2007 г. увеличи- |
ских показателей работы металлургических ком- |
||||||||||||||||
лась на 48 %, а цена — лишь на 21 %. В связи с |
бинатов до и в период кризиса в поквартальном |
||||||||||||||||
отмеченными изменениями в период финансо- |
разрезе приведены в табл. 3. |
|
|
|
|
|
|||||||||||
ТАБЛИЦА 3. ДИНАМИКА ЭКОНОМИЧЕСКИХ ПОКАЗАТЕЛЕЙ РАБОТЫ МЕТАЛЛУРГИЧЕСКИХ |
|
|
|||||||||||||||
|
|
|
КОМБИНАТОВ ДО И В ПЕРИОД КРИЗИСА |
|
|
|
|
|
|
|
|||||||
|
|
|
|
|
|
|
|
|
|
|
|
|
|
|
|
|
|
Показатель |
|
|
2008 г. |
|
|
|
|
2009 г. |
|
|
|
|
2010 г. |
|
|
|
|
2007 г. |
9 мес. |
ΙV кв. |
год |
Ι кв. |
|
ΙΙ кв. |
ΙΙΙ кв. |
ΙV кв. |
год |
Ι кв. |
ΙΙ кв. |
ΙΙΙ кв. |
ΙV кв. |
|
год |
|
|
|
|
|
|
||||||||||||||
Средняя |
|
|
|
|
|
|
|
|
|
|
|
|
|
|
|
|
|
рентабельность |
|
|
|
|
|
|
|
|
|
|
|
|
|
|
|
|
|
продукции, % |
39,6 |
48,1 |
3,3 |
39,3 |
5,9 |
|
9,7 |
25,3 |
19,8 |
15,8 |
15,2 |
18,9 |
11,8 |
12,8 |
|
14,6 |
|
Индексы показателей, |
|
|
|
|
|
|
|
|
|
|
|
|
|
|
|
|
|
ед. |
|
|
|
|
|
|
|
|
|
|
|
|
|
|
|
|
|
физический объем |
|
|
|
|
|
|
|
|
|
|
|
|
|
|
|
|
|
производства, руб. |
1 |
1,04 |
0,63 |
0,94 |
0,76 |
|
0,80 |
0,93 |
0,91 |
0,85 |
0,91 |
0,92 |
0,92 |
0,95 |
|
0,92 |
|
выпуск продукции, |
|
|
|
|
|
|
|
|
|
|
|
|
|
|
|
|
|
руб. |
1 |
1,45 |
0,71 |
1,26 |
0,65 |
|
0,67 |
0,87 |
0,90 |
0,77 |
0,95 |
1,18 |
1,15 |
1,20 |
|
1,12 |
|
средние цены |
|
|
|
|
|
|
|
|
|
|
|
|
|
|
|
|
|
продукции, руб. |
1 |
1,39 |
1,12 |
1,35 |
0,86 |
|
0,84 |
0,93 |
0,98 |
0,91 |
1,05 |
1,28 |
1,25 |
1,27 |
|
1,22 |
|
средняя |
|
|
|
|
|
|
|
|
|
|
|
|
|
|
|
|
|
себестоимость |
|
|
|
|
|
|
|
|
|
|
|
|
|
|
|
|
|
продукции, руб. |
1 |
1,31 |
1,52 |
1,35 |
1,13 |
|
1,07 |
1,04 |
1,14 |
1,10 |
1,27 |
1,51 |
1,55 |
1,57 |
|
1,48 |
|
прибыль от |
|
|
|
|
|
|
|
|
|
|
|
|
|
|
|
|
|
реализации |
|
|
|
|
|
|
|
|
|
|
|
|
|
|
|
|
|
продукции, руб. |
1 |
1,66 |
0,08 |
1,26 |
0,13 |
|
0,21 |
0,62 |
0,52 |
0,37 |
0,44 |
0,66 |
0,43 |
0,48 |
|
0,50 |
|
20 ―――――――――――――――――ОАО «Черметинформация» • Бюллетень «Черная металлургия» • 7• 2011

При анализе тенденций изменения экономи- |
тели этих групп комбинатов значительно разли- |
ческих показателей отрасли авторы традиционно |
чались. Средняя рентабельность продукции по |
делили указанные выше восемь комбинатов на |
группам комбинатов приведена на рис. 8. Финан- |
две группы к I относили крупнейшие комби- |
совый кризис особенно в 2009 г. привел к более |
наты: Магнитогорский, Череповецкий и Новоли- |
значительному снижению рентабельности про- |
пецкий, а ко II — остальные пять предприятий. В |
дукции на предприятиях второй группы. |
условиях финансового кризиса средние показа- |
|
Рис. 8. Динамика средней рентабельности продукции по группам комбинатов
Выводы
1. За последнее десятилетие средний тех- |
несуточное производство стали и средние |
нический уровень отечественных металлурги- |
цены металлопродукции близки или уже дос- |
ческих предприятий значительно повысился. |
тигли докризисного уровня. В то же время |
Однако он по-прежнему ниже, чем в промыш- |
средняя себестоимость продукции уже значи- |
ленно развитых странах. Поэтому показатели |
тельно превысила этот уровень и это обусло- |
использования производственных ресурсов в |
вило резкое снижение рентабельности продук- |
черной металлургии России хуже, чем за ру- |
ции. |
бежом. |
4. Для отечественной черной металлургии |
2. Мировой финансовый кризис оказал |
необходимо еще более активное осуществле- |
сильное негативное влияние на показатели |
ние мероприятий по повышению технического |
работы отечественных предприятий черной |
уровня производства и качества производимой |
металлургии. Особенно заметно он отразился |
и экспортируемой продукции. Последнее |
на предприятиях с более низким техническим |
должно также обеспечить повышение эффек- |
уровнем. |
тивности использования материальных, топ- |
3. В настоящее время мировая и отечест- |
ливно-энергетических и трудовых ресурсов и в |
венная черная металлургия находятся в ста- |
конечном счете — эффективности производ- |
дии восстановительного роста. В России сред- |
ства. |
БИБЛИОГРАФИЧЕСКИЙ СПИСОК
1.Юзов О. В., Седых А. М. Тенденции развития мирового рынка стали в период финансового кризиса // Черная металлургия: Бюл. ин-та “Черметинформация”. 2010. № 11. С. 8–18.
2.Юзов О. В., Седых А. М., Афонин С. З. Тенденции изменения экономических показателей черной металлургии России // Там же. 2008. № 4. С. 29–36.
3.Юзов О. В., Седых А. М., Афонин С. З. Экономические показатели и проблемы развития черной металлургии России в период финансового кризиса // Там же. 2010. № 7. С. 5–13.
4.Юзов О. В., Седых А. М., Афонин С. З. Экономические показатели и проблемы развития черной металлургии России во время финансового кризиса // Сталь. 2010. № 12. С. 72−76.
ОАО «Черметинформация» • Бюллетень «Черная металлургия» • 7• 2011 ―――――――――――――――― 21

НА ПРЕДПРИЯТИЯХ И В ИНСТИТУТАХ
УДК 661.631:553.32+622-15 |
Е. А. ПЕСТОНОВА, к.б.н.; С. И. АНУФРИЕВА, к.х.н.; |
|
Е. Г. ОЖОГИНА, д.г.-м.н., chimtech@vims-geo.ru |
|
(ФГУП “Всероссийский научно-исследовательский институт |
|
минерального сырья им. Н.М. Федоровского”) |
ОБЕСФОСФОРИВАНИЕ КОНЦЕНТРАТОВ ОБОГАЩЕНИЯ ОКИСЛЕННЫХ МАРГАНЦЕВЫХ РУД ХИМИЧЕСКИМИ СПОСОБАМИ
Основным недостатком отечественных мар- |
обесфосфоривания концентратов, получение |
||||||||||
ганцевых руд является низкое содержание мар- |
высококачественных |
концентратов |
можно |
||||||||
ганца при повышенном содержании фосфора. |
реализовать только с помощью химических спо- |
||||||||||
Повышение содержания марганца в концентра- |
собов. В этом случае обесфосфоривание дости- |
||||||||||
тах достигается традиционными способами обо- |
гается путем перевода фосфора в раствор под |
||||||||||
гащения (гравитационными и магнитными), при |
действием различных реагентов, в то время как |
||||||||||
этом практически не снижается содержание |
марганцевые соединения остаются в нераство- |
||||||||||
фосфора, присутствующего в рудных минералах |
римом остатке [3, 4]. |
|
|
|
|||||||
в виде тонкодисперсной механической примеси |
Целью |
настоящего |
исследования |
являлся |
|||||||
[1]. Существуют ограничения на содержание |
выбор эффективного способа обесфосфорива- |
||||||||||
фосфора в товарном концентрате. В концентра- |
ния и его оптимизация для концентратов магнит- |
||||||||||
тах для выплавки ферромарганца отношение |
ного обогащения окисленных марганцевых руд с |
||||||||||
P/Mn не должно превышать 0,0044 (0,0053 для |
различным содержанием марганца, железа, |
||||||||||
выплавки с добавкой малофосфористого шлака) |
фосфора. |
|
|
|
|
|
|
||||
[2]. Так как традиционные методы глубокого |
Объекты исследования марганцевые кон- |
||||||||||
обогащения труднообогатимых руд не позволяют |
центраты магнитного обогащения, химический |
||||||||||
достичь |
необходимой |
степени |
состав которых представлен в табл. 1. |
|
|||||||
|
ТАБЛИЦА 1. ХИМИЧЕСКИЙ СОСТАВ КОНЦЕНТРАТОВ ОБОГАЩЕНИЯ |
|
|||||||||
|
|
|
|
|
|
|
|
|
|
|
|
Концентрат |
|
Содержание, % |
|
|
|
|
|
Отношение |
|
||
Mn |
P |
|
Fe |
|
SiO2 |
|
|
P/Mn |
|
Fe/P |
|
|
|
|
|
|
|
||||||
КЕ-1 |
38,7 |
0,52 |
|
4,5 |
|
7,6 |
|
|
0,0134 |
|
8,52 |
КС-1 |
44,1 |
0,34 |
|
2,6 |
|
9,2 |
|
|
0,0077 |
|
7,70 |
КС-2 |
43,5 |
0,56 |
|
4,3 |
|
13,5 |
|
|
0,0129 |
|
7,68 |
КС-3 |
35,3 |
0,48 |
|
11,0 |
|
11,6 |
|
|
0,0136 |
|
22,92 |
Проба КЕ-1 концентрат обогащения мар- |
которого является фторапатит. В рудах установ- |
||||||||||
ганцевых руд Порожинского месторождения. По |
лено две разновидности минерала (рис. 1). Это |
||||||||||
минеральному составу руды существенно пси- |
тонковкрапленный апатит в рудных минералах, |
||||||||||
ломелановые. Исходная проба представлена |
присутствующий в виде кристаллов размером |
||||||||||
нсутит-псиломелановой рудой. Марганцевая ми- |
менее 0,005 мм или образующий скопления ксе- |
||||||||||
нерализация отличается полиминеральным со- |
номорфных зерен, обладающих высокой степе- |
||||||||||
ставом, тесным срастанием минералов, близо- |
нью изрезанности. В обоих случаях механиче- |
||||||||||
стью их физических свойств, что определяет не- |
скими методами обогащения избавиться от апа- |
||||||||||
возможность селективного выделения конкрет- |
тита этой разновидности не представляется |
||||||||||
ных минеральных видов в отдельные продукты. |
возможным. Апатит второй разновидности, вы- |
||||||||||
Главная вредная примесь в окисленных марган- |
явленный в рудах впервые, входит в состав |
||||||||||
цевых рудах фосфор, минеральной формой |
кварц-опаловых агрегатов [5]. |
|
22 ―――――――――――――――――ОАО «Черметинформация» • Бюллетень «Черная металлургия» • 7• 2011

а |
б |
Рис. 1. Апатит в марганцевых агрегатах:
атонкая вкрапленность призматических кристаллов апатита в псиломелане; б скопления апатита, приуроченные
ктрещинам в агрегате существенно псиломеланового состава (изображения в обратно рассеянных электронах)
Основными методами обесфосфоривания |
Исследования по обесфосфориванию кон- |
||
для всех исследуемых проб были выбраны наи- |
центрата КЕ-1 гаусманитовым способом пока- |
||
более изученные в настоящее время содовый и |
зали его эффективность. Гаусманитовый способ |
||
гаусманитовый способы. |
включает в себя две операции: высокотемпера- |
||
Основные технологические операции содо- |
турный обжиг, который обеспечивает перевод |
||
вого способа: спекание с кальцинированной со- |
оксидов марганца в труднорастворимый оксид |
||
дой (800 900 С) и выщелачивание спека горя- |
Mn3O4 (гаусманит), и обесфосфоривание обож- |
||
чей водой (70 80 С). При спекании образуются |
женных продуктов агитационным выщелачива- |
||
водорастворимые силикаты и фосфаты натрия, |
нием в разбавленных растворах азотной ки- |
||
переходящие в раствор при последующем вод- |
слоты. |
|
|
ном выщелачивании. В процессе регенерации |
В проведенной серии опытов были опреде- |
||
соды в качестве побочных продуктов из раство- |
лены оптимальные условия обесфосфоривания: |
||
ров выделяют кремнегель и фосфорсодержащий |
обжиг при температуре 950 С в течение 1 ч, |
||
известковый осадок. |
выщелачивание 5 %-ным раствором азотной ки- |
||
При применении содового способа количе- |
слоты в течение 15 мин при t = 18 20 С. Иссле- |
||
ство соды для приготовления шихты, рассчитан- |
дования по влиянию крупности материала на из- |
||
ное из содержаний кремния, фосфора и железа |
влечение фосфора в раствор были проведены |
||
в концентрате, составляло 50 % (мас.) от на- |
на концентратах исходной крупности (–2+0 мм) и |
||
вески концентрата КЕ-1. Спекание проводили |
измельченных до крупности –0,074 мм. Степень |
||
при t = 900 С в течение 1 ч, водное выщелачи- |
обесфосфоривания составила 66 и 82 % соот- |
||
вание при соотношении Т:Ж = 1:5 при t = |
ветственно. Уменьшение крупности до –0,074 мм |
||
= 75 80 C в течение 1 ч. Извлечение фосфора в |
значительно повышает |
степень |
извлечения |
раствор составило всего 8,5 %. При содовом |
фосфора в раствор (на 16 %). Получен кондици- |
||
способе извлекается в раствор фосфор, который |
онный по фосфору марганцевый концентрат с |
||
окружен слоями кремнезема за счет перевода |
отношением P/Mn = 0,0024. Для определения |
||
последнего в раствор в виде растворимых на- |
оптимальной крупности концентрата был прове- |
||
триевых солей [6]. По данным рентгенографиче- |
ден эксперимент по обесфосфориванию концен- |
||
ского анализа, содержание кварца в исследуе- |
трата, измельченного до |
крупности |
–0,315 мм |
мых концентратах составляет всего около 2 %, и, |
(табл. 2). |
|
|
вероятно, количество фосфора, связанного с |
|
|
|
кремнеземом, незначительно. |
|
|
|
ОАО «Черметинформация» • Бюллетень «Черная металлургия» • 7• 2011 ―――――――――――――――― 23

ТАБЛИЦА 2. РЕЗУЛЬТАТЫ ОБЕСФОСФОРИВАНИЯ МАРГАНЦЕВОГО КОНЦЕНТРАТА ПРОБЫ КЕ-1 ГАУСМАНИТОВЫМ СПОСОБОМ
Проба |
|
Выход |
Единицы |
|
|
|
|
|
Элемент, компонент* |
|
|
|
|
Отношение |
|||||||||||
|
продукта |
|
|
Mn |
|
|
Р |
|
Fe |
|
|
SiO2 |
|
P/Mn |
|||||||||||
|
|
|
|
|
|
|
|
|
|
|
|
|
|
|
|
||||||||||
Исходный |
|
100,0 % |
|
% |
|
|
38,7 |
|
0,52 |
|
4,54 |
|
|
7,63 |
|
|
0,0134 |
||||||||
концентрат |
|
|
|
|
|
|
|
|
|
|
|||||||||||||||
|
|
|
|
|
|
|
|
|
|
|
|
|
|
|
|
|
|
|
|
|
|
|
|
|
|
Кек |
|
78,0 % |
|
% |
|
|
|
49, 4 |
|
|
0,14 |
|
|
4, 62 |
|
|
|
6,87 |
|
|
0,0028 |
||||
|
|
|
|
|
|
|
0, 4 |
|
79, 0 |
|
20, 6 |
|
|
29, 77 |
|
|
|||||||||
|
|
% |
|
|
|
|
|
|
|
|
|||||||||||||||
|
|
|
|
|
|
|
|
|
|
|
|
|
|||||||||||||
Раствор |
|
133 мл |
|
|
г/л |
1, 3 |
|
|
0,85 |
|
0, 07 |
|
|
0,38 (Si) |
|
||||||||||
|
|
|
|
|
|
|
|
|
|
|
|
|
|
|
|
|
|
|
|
|
|
|
|||
|
|
% |
|
|
1, 5 |
|
|
72, 5 |
|
0, 72 |
|
|
2,19 |
|
|
||||||||||
|
|
|
|
|
|
|
|
|
|
|
|
|
|
||||||||||||
* В числителе содержание; в знаменателе извлечение в раствор. |
|
|
|
|
|
|
|
|
|
||||||||||||||||
Как видно из данных табл. 2, в оптимальных |
|
Пробы КС-1, КС-2 и КС-3 концентраты маг- |
|||||||||||||||||||||||
условиях (обжиг t = 950 С в течение 1 ч, выще- |
нитного обогащения марганцевых руд Сейбин- |
||||||||||||||||||||||||
лачивание |
5 %-ным раствором азотной кислоты |
ского рудного узла с различным соотношением |
|||||||||||||||||||||||
в течение 15 мин при t = 18 20 |
С, крупность |
железа, марганца и фосфора. |
|
|
|||||||||||||||||||||
концентрата –0,315 мм) удается получить обес- |
|
Минералогическими |
|
исследованиями уста- |
|||||||||||||||||||||
фосфоренный марганцевый концентрат с отно- |
новлено, что окисленные марганцевые и желе- |
||||||||||||||||||||||||
шением P/Mn равным 0,0028. Анализ кеков и |
зомарганцевые руды Сейбинского рудного узла |
||||||||||||||||||||||||
растворов показал, что величина расхождения |
характеризуются сложным |
полиминеральным |
|||||||||||||||||||||||
по извлечению фосфора, рассчитанная по кеку и |
составом и неоднородным строением, что по- |
||||||||||||||||||||||||
раствору, не превышает 7 %. Остаточная |
зволяет отнести их к категории труднообогати- |
||||||||||||||||||||||||
кислотность раствора составила 3,53 г/л. |
|
|
|
|
мых. |
|
|
|
|
|
|
|
|
|
|||||||||||
Таким образом, исследования показали, что |
|
Главным рудным минералом является пси- |
|||||||||||||||||||||||
для обесфосфоривания концентрата обогаще- |
ломелан, в подчиненном количестве присутст- |
||||||||||||||||||||||||
ния окисленных марганцевых руд (КЕ-1) эффек- |
вуют пиролюзит, криптомелан, тодорокит. В не- |
||||||||||||||||||||||||
тивным способом является гаусманитовый. Он |
значительном количестве обнаружены манганит, |
||||||||||||||||||||||||
обеспечивает извлечение фосфора в раствор до |
браунит, гаусманит, вернадит, силикаты мар- |
||||||||||||||||||||||||
70 80 % и повышение содержания марганца в |
ганца бустамит и пироксмангит. Следует от- |
||||||||||||||||||||||||
конечном продукте на 9 11 %. Полученный кон- |
метить, что текстурно-структурные характери- |
||||||||||||||||||||||||
центрат с отношением Р/Mn = 0,0028 и Mn/SiO2 = |
стики существенно псиломелановых агрегатов |
||||||||||||||||||||||||
= 7,2 может быть использован в ферросплавной |
(рис. 2) являются неблагоприятными для обога- |
||||||||||||||||||||||||
промышленности для производства стандарт- |
щения руд механическими методами, в то же |
||||||||||||||||||||||||
ного ферромарганца. |
|
|
|
|
|
|
|
|
|
|
время они могут являться благоприятными для |
||||||||||||||
|
|
|
|
|
|
|
|
|
|
|
|
|
их химического обогащения. |
|
|
а б
Рис. 2. Марганцевые агрегаты существенно псиломеланового состава:
а оолитоподобные образования радиально-лучистого строения; б концентрически-зональные выделения (отраженный свет, николи параллельны)
Главным рудным минералом железомарган- |
Как правило, существенно гетитовые образова- |
цевых руд (проба КС-3) наряду с псиломеланом |
ния содержат гидроксиды марганца и слоистые |
является гетит, образующий внешне однород- |
алюмосиликаты в переменном количестве. |
ные участки скрытокристаллического строения. |
|
24 ―――――――――――――――――ОАО «Черметинформация» • Бюллетень «Черная металлургия» • 7• 2011

Минеральными формами фосфора являются |
агрегатами, легко разрушающимися при |
|
апатит и крандаллит. Апатит встречается исклю- |
надавливании лопаткой. По данным качествен- |
|
чительно в обломках кремнистых пород и, веро- |
ного рентгенографического анализа спека, пре- |
|
ятно, может быть удален совместно с кварцем. |
обладающей фазой в нем являются манганиты |
|
Весьма тесная ассоциация крандаллита с тонко- |
натрия (Na0,7MnO2,05; NaMnO2). Железо присутст- |
|
дисперсными гидроксидами железа, его грану- |
вует в форме гематита и входит в состав фос- |
|
лярные характеристики позволяют говорить о |
фатных соединений Fe4(PO4)2O; |
FeH2P3O10 . |
невозможности его извлечения (удаления) физи- |
Также в процессе спекания образуются гаусма- |
|
ческими методами обогащения. |
нит и манганиты бария и калия. |
|
Для обесфосфоривания проб КС-1 и КС-2 был |
При выщелачивании спека манганиты гидро- |
|
использован содовый способ (температура спе- |
лизуются марганец остается в твердой фазе, |
|
кания t = 850 С в течение 1 ч, водное выщела- |
а натрий, фосфор и кремний переходят в рас- |
|
чивание при соотношении Т:Ж = 1:5 и t = 75 C в |
твор. Химический состав обесфосфоренных кон- |
|
течение 80 мин). Спек представлял собой рых- |
центратов приведен в табл. 3. |
|
лую массу с небольшими (до 1,5 см) спекшимися |
|
|
ТАБЛИЦА 3. РЕЗУЛЬТАТЫ ОБЕСФОСФОРИВАНИЯ КОНЦЕНТРАТОВ ГЛУБОКОГО ОБОГАЩЕНИЯ СОДОВЫМ СПОСОБОМ
Проба |
|
Выход кека, % |
|
|
Элемент, компонент* |
|
|
Отношение P/Mn |
|
|||
|
Mn |
Р |
Fe |
SiO2 |
|
Ni |
|
Na |
|
|||
|
|
|
|
|
|
|
||||||
КС-1 |
|
99,3 |
50,8 |
0,089 |
1,89 |
3,39 |
|
0,61 |
|
8,68 |
0,0017 |
|
|
|
74,0 |
28,3 |
63,6 |
|
12,2 |
|
|
||||
|
|
|
|
|
|
|
|
|||||
КС-2 |
|
99,2 |
48,5 |
0,11 |
3,02 |
4,40 |
|
0,43 |
|
8,75 |
0,0023 |
|
|
|
80,5 |
30,3 |
67, 7 |
|
3,0 |
|
|
||||
|
|
|
|
|
|
|
|
|||||
КС-3 |
|
101,1 |
34,8 |
0,28 |
10,20 |
2,22 |
|
0,15 |
|
|
0,0080 |
|
|
0,33 |
41,0 |
6,2 |
80,6 |
|
10,8 |
|
|
||||
|
|
|
|
|
|
|
|
|||||
* В числителе содержание, %; в знаменателе извлечение в раствор, %. |
|
|
|
|
||||||||
По данным табл. 3 видно, что при указанных |
нако отмечаются потери марганца в растворе до |
|||||||||||
условиях удается извлечь в раствор до 80 % Р. |
14 %. В пробах КС-1, КС-2 и КС-3 отношение |
|||||||||||
Для проб КС-1 и КС-2 отношение Р/Mn состав- |
Р/Mn составило 0,0036, 0,0045 и 0,0054 соответ- |
|||||||||||
ляет 0,0017 и 0,0023 соответственно. Необхо- |
ственно. |
|
|
|
|
|||||||
димо отметить, что в процессе выщелачивания |
|
|
|
|
|
|
|
|||||
не удается полностью отмыть концентрат от на- |
|
|
|
|
|
|
|
|||||
трия ( 8,5 %). Это связано с образованием |
|
|
|
|
|
|
|
|||||
сложных натриевых соединений, которые не |
|
|
|
|
|
|
|
|||||
выщелачиваются в условиях проведенного экс- |
|
|
|
|
|
|
|
|||||
перимента. |
|
|
|
|
|
|
|
|
|
|
|
|
Из пробы КС-3, которая характеризуется вы- |
|
|
|
|
|
|
|
|||||
соким содержанием железа (11 %), удается из- |
|
|
|
|
|
|
|
|||||
влечь не более 41 % фосфора в раствор, неза- |
|
|
|
|
|
|
|
|||||
висимо от количества расходуемой соды. Отно- |
|
|
|
|
|
|
|
|||||
шение Р/Mn в концентрате после обесфосфори- |
|
|
|
|
|
|
|
|||||
вания составляет 0,0080. Рассчитанное отноше- |
Рис. 3. Зависимость извлечения фосфора в раствор от |
|||||||||||
ние Fe/P показывает, что степень обесфосфори- |
отношения содержания Fe/P в исходном концентрате |
|||||||||||
вания существенно зависит от его значения в |
На рис. 4 представлены данные по извлече- |
|||||||||||
исходном концентрате: с увеличением отноше- |
||||||||||||
ния Fe/P показатели обесфосфоривания ухуд- |
нию фосфора в раствор из всех исследуемых |
|||||||||||
шаются (рис. 3). Вероятно, это связано с образо- |
проб содовым и гаусманитовым способами. Ус- |
|||||||||||
ванием в процессе спекания фосфатов железа, |
тановлено, что для концентратов разного хими- |
|||||||||||
труднорастворимых в щелочных условиях. |
|
ческого и минерального составов эффективность |
||||||||||
Проведенные исследования по обесфосфо- |
разных способов обесфосфоривания сильно от- |
|||||||||||
риванию проб КС-1, КС-2 и КС-3 гаусманитовым |
личается. Содовый способ наиболее эффекти- |
|||||||||||
способом показали, что удается извлечь от 60 до |
вен для концентратов КС-1 и КС-2. Гаусманито- |
|||||||||||
70 % Р из всех исследуемых концентратов. Од- |
вый |
способ |
может быть |
рекомендован для |
ОАО «Черметинформация» • Бюллетень «Черная металлургия» • 7• 2011 ―――――――――――――――― 25

обесфосфоривания концентрата КЕ-1. Для концентрата КС-3 содовый способ обесфосфоривания оказался неэффективным в связи с образованием в процессе спекания труднорастворимых фосфатов железа. Гаусманитовым способом также не удается достичь требуемого отношения Р/Mn в конечном продукте. В связи с этим были проведены исследования по нахождению эффективного способа обесфосфоривания концентрата КС-3, характеризующегося повышенным содержанием железа.
Рис. 4. Степень обесфосфоривания марганцевых концентратов содовым и гаусманитовым способами
По данным минералогического анализа, фосфор в исследуемых пробах находится в форме крандаллита СаАl3(РО4)2(ОН)5·Н2О . Крандаллит относится к алюмофосфатам, вскрытие которых происходит под воздействием щелочей. Применение в качестве выщелачивающего реагента щелочи позволит удалить фосфор и полностью сконцентрировать марганец в кеке.
В процессе агитационного выщелачивания раствором едкого натра происходит разложение крандаллита по следующим реакциям:
СаАl3(РО4)2(ОН)5 + 9NaOHконц → 3Na[Al(OH)4] + + 2Na3PO4 + Ca(OH)2
СаАl3(РО4)2(ОН)5 + 6NaOHразб → 3Al(OH)3 + + 2Na3PO4 + Ca(OH)2
Фосфор переходит в раствор в виде ортофосфата натрия. Поскольку оксиды марганца не реагируют с водными растворами щелочей, отсутствуют потери марганца с раствором. Таким образом, удается селективно извлечь фосфор в раствор, не прибегая при этом к дорогостоящей операции высокотемпературного обжига или спекания. В проведенной серии опытов по нахождению оптимальных условий обесфосфоривания варьировали концентрацию и расход реагента, температуру и продолжительность выщелачивания. Уменьшение крупности (до –0,315 мм) позволяет незначительно повысить степень обесфосфоривания (на 3 %). Основными факторами, влияющими на процесс разложения крандаллита, являются:
концентрация раствора едкого натра 200 250 г/л (при более низкой концентрации извлечение фосфора в раствор не превышает 55 %);
температура 85 С (понижение температуры до 18 20 С приводит к падению степени обесфосфоривания до 40 %);
продолжительность процесса 5 6 ч. Повышение температуры способствует более
полному разложению крандаллита и уменьшает растворимость образующегося гидроксида кальция, который может осаждать фосфат-ионы в виде ортофосфата кальция. Расход раствора едкого натра в соотношении Т:Ж = 1:3 является достаточным для разложения крандаллита. Совокупность этих факторов обеспечивает извлечение фосфора на уровне 65 70 %. В оптимальных условиях, в которых удается получить кондиционный по фосфору концентрат (P/Mn = = 0,0044), степень обесфосфоривания составляет 67 %.
Рентгенографический анализ концентратов после щелочного выщелачивания показал, что под воздействием раствора едкого натра удается разложить и вывести из твердой фазы50 60 % крандаллита (табл. 4).
ТАБЛИЦА 4. МИНЕРАЛЬНЫЙ СОСТАВ КОНЦЕНТРАТА КС-3
|
Исходный концентрат |
После обработки раствором NaOH |
||
минерал |
|
количество, % |
минерал |
количество, % |
Кварц |
|
8 |
Кварц |
10 |
Пиролюзит |
|
8 |
Пиролюзит |
8 |
Гетит |
|
13 |
Гетит |
18 |
Псиломелан |
|
60 |
Псиломелан |
60 |
Крандаллит |
|
2 3 |
Крандаллит |
1 2 |
Криптомелан |
|
5 |
Криптомелан |
5 |
Фторапатит |
|
1 1,5 |
Барит |
1 2 |
26 ―――――――――――――――――ОАО «Черметинформация» • Бюллетень «Черная металлургия» • 7• 2011
Фильтрат от выщелачивания марганцевого концентрата может быть обработан известковым молоком для осаждения фосфат-ионов и регенерации раствора едкого натра. В этом случае происходит реакция
2Na3PO4 + 3Ca(OH)2 → Ca3(PO4)2↓ + 6NaOH,
в результате которой образуется ортофосфат кальция, который может быть утилизирован в строительной индустрии.
На основании проведенных экспериментов разработана технологическая схема обесфосфоривания концентрата обогащения (проба КС- 3), включающая следующие операции: выщелачивание концентрата раствором едкого натра, фильтрацию и сушку обесфосфоренного концентрата, регенерацию раствора едкого натра известкованием с получением фосфорсодержащего известкового осадка. Способ щелочного выщелачивания дает возможность исключить из технологической схемы высокотемпературный обжиг.
Таким образом, проведенные исследования по химическому обесфосфориванию концентратов обогащения окисленных марганцевых руд выявили следующие факторы, определяющие эффективность протекания процесса обесфосфоривания: минеральная форма фосфора, отношение Fe/P в исходном концентрате и содержание кремнезема. Это позволит прогнозировать эффективность применяемых способов обесфосфоривания. Эффективность содового способа определяется отношением Fe/P в исходном концентрате: чем выше значение Fe/P, тем меньше степень обесфосфоривания. Также возможность применения содового способа обусловлена содержанием кремнезема в исходном концентрате: при низком его значении содовый способ неэффективен. При нахождении фосфора в форме крандаллита возможно использование щелочного выщелачивания для обесфосфоривания марганцевых концентратов, которое позволяет получить обесфосфоренный концентрат, пригодный для выплавки стандартных ферросплавов.
БИБЛИОГРАФИЧЕСКИЙ СПИСОК
1.Ожогина Е. Г., Кузьмин В. И., Шувалова Ю. Н. Комплекс минералогических исследований при обогащении карбонатных марганцевых руд // Черная металлургия: Бюл. ин-та “Черметинформация”. 2001. № 3. С. 16 25.
2.Минеральное сырье. Марганец: Справочник / Н. И. Потконен, А. С. Столяров, А. А. Шарков и др. М.: ЗАО “Геоинформмарк”. 1999. 51 с.
3.Гасик М. И. Марганец. М.: Металлургия. 1992. 608 с.
4.Марганец / К. Н. Трубецкой, В. А. Чантурия, А. Е. Воробьев и др.; под ред. акад. К. Н. Трубецкого. М.: Изд-во Академии горных наук. 1999. 271 с.
5.Ожогина Е. Г., Рогожин А. А. Технологическая минералогия: инновационные подходы к оценке минерального сырья // Минералого-технологическая оценка месторождений полезных ископаемых и проблемы раскрытия минералов. Петрозаводск: Карельский научный центр РАН. 2011. С. 7 12.
6.Хитрик С. И., Гасик М. И., Кучер А. Г. Гидрометаллургический способ получения низкофосфористых марганцевых концентратов // Горный журнал. М.: Недра. 1966. № 9. С. 66 69.
ОАО «Черметинформация» • Бюллетень «Черная металлургия» • 7• 2011 ―――――――――――――――― 27

УДК 662.749 В. И. РУДЫКА, к.э.н; В. П. МАЛИНА (Государственный институт по проектированию предприятий коксохимической промышленности “Гипрококс”)
ПОСЛЕДНИЕ ТЕНДЕНЦИИ В РАЗВИТИИ МИРОВОГО МЕТАЛЛУРГИЧЕСКОГО
И КОКСОВОГО ПРОИЗВОДСТВ
(Обзор материалов саммита “Европейский кокс 2011”, 5 7 апреля 2011 г., г. Вена, Австрия)
Саммит “Европейский кокс 2011” был организован компанией IntertechPira, США–Великобри- тания. В нем приняло участие 132 представителя 79 фирм и компаний из 30 стран (Бразилия, Великобритания, Германия, Индия, Италия, Китай, Колумбия, Нидерланды, Польша, Пакистан, Россия, США, Украина, Швеция, Чехия и др.). От Украины участвовали 12 делегатов от УНПА “Укркокс”, Гипрококса, УХИНа, ЗАО “Макеевкокс”, ТД “Донбассуголь” и др.).
Вниманию участников саммита было представлено 15 докладов (презентаций) по направлениям:
анализ ситуации в мировом производстве стали и коксохимической промышленности и тенденции рынка стали, угля, и кокса; состояние производства кокса в Китае, Индии, США; развитие коксовой и угольной отраслей в России;
технические достижения (инновации) в коксовом производстве (производство кокса с улавливанием тепла, без улавливания химических продуктов коксования; автоматизация коксовых машин; новые направления в технологии загрузки трамбованной угольной шихты; сокраще-
ние вредных выбросов коксового производства в окружающую среду и др.).
На первое место повестки дня саммита его организаторы поставили вопросы, связанные с анализом ситуации, которая сложилась на мировых рынках стали, кокса и коксующегося угля, а также с прогнозом потребности в стали и сырьевых материалах. Были рассмотрены перспективы развития сталеплавильной и коксовой отраслей на период до 2015 г. Эти вопросы рассматривались в увязке с состоянием сталеплавильной и коксовой промышленностей в Китае крупнейшем мировом производителе металла и кокса.
Вышеприведенной тематике были посвящены доклады (презентации), сделанные представи-
телями компаний CRU Analysis, США; Thyssen Krupp Minenergy, Китай; Mechel Carbon, Швейцария; Wood Mackenzie, США, и др.
На базе представленных вниманию участников саммита материалов последние тенденции в развитии мирового металлургического и коксового производств можно охарактеризовать следующим образом.
|
Сталь |
Согласно данным World Steel Association |
изводство стали в Азии в 2010 г. составило 881,2 |
(WSA), представляющей 170 производителей |
млн т (на 11,8 % больше, чем в 2009 г.), это |
стали, на долю которых приходится 85 % миро- |
65,5 % мирового объема. |
вого объема выплавляемой стали, в 2010 г. в |
Китай выплавил 626,7 млн т (на 9,3 % больше, |
мире было произведено 1414 млн т стали, что |
чем в 2009 г.), Япония 109,6 млн т, Индия |
является новым рекордным уровнем. По сравне- |
66,8 млн т, Южная Корея 58,5 млн т. |
нию с 2009 г. рост составляет 15 %. В 2010 г. все |
ЕС в 2010 г. продемонстрировал рекордный |
основные производящие сталь страны и регионы |
рост производства стали на 24,5 % больше, чем |
показали прирост выплавки. |
в 2009 г., абсолютное количество 172,9 млн т. |
ЕС и Северная Америка имеют более высо- |
Однако в Великобритании и Греции выплавка |
кие темпы роста в связи с тем, что у них базовые |
стали в 2010 г. продолжала падать. В таблице |
цифры прироста за 2009 г. ниже, чем, например, |
приведены данные о производстве стали в 2010 г. |
у азиатских стран или стран СНГ. Годовое про- |
десятью крупнейшими продуцентами. |
28 ―――――――――――――――――ОАО «Черметинформация» • Бюллетень «Черная металлургия» • 7• 2011
ДЕСЯТЬ КРУПНЕЙШИХ СТРАН-ПРОИЗВОДИТЕЛЕЙ СТАЛИ В 2010 г.
Место |
Страна |
2010 г., |
2009 г., |
Изменение 2010 г. |
|
млн т |
млн т |
к 2009 г., % |
|||
|
|
||||
1 |
Китай |
626,7 |
573,6 |
9,3 |
|
2 |
Япония |
109,6 |
87,5 |
25,2 |
|
3 |
США |
80,6 |
58,2 |
38,5 |
|
4 |
Россия |
67,0 |
60,0 |
11,7 |
|
5 |
Индия |
66,8 |
62,8 |
6,4 |
|
6 |
Южная Корея |
58,5 |
48,6 |
20,3 |
|
7 |
Германия |
43,8 |
32,7 |
34,1 |
|
8 |
Украина |
33,6 |
29,9 |
12,4 |
|
9 |
Бразилия |
32,8 |
26,5 |
23,8 |
|
10 |
Турция |
29,0 |
25,3 |
14,6 |
Согласно прогнозам, макроэкономические по- |
блюдается рост инфляции (в январе феврале |
казатели свидетельствуют о дальнейшем росте |
2011 г. она составила 5 %), поэтому китайское |
ВВП на период до 2015 г. в Китае, ЕС-27, Япо- |
правительство уже предприняло ряд мер для |
нии, США. Рост мирового производства стали |
контроля ситуации. В 2008 2009 гг. в Китае на- |
будет происходить плавно, но оно достигнет |
блюдалось падение ВВП, и это негативное явле- |
значительной величины (до 1,9 млрд т), причем |
ние еще не ликвидировано. |
выплавка стали из доменного чугуна и далее бу- |
Сложной остается ситуация с сырьевыми ма- |
дет намного превышать электросталеплавильное |
териалами на мировом рынке. В связи с недав- |
производство, что обусловит рост потребности в |
ним наводнением в Австралии возникли сложно- |
коксе до 2015 г. на величину более 130 млн т. |
сти с поставками коксующегося угля, а полити- |
Эксперты ожидают, что 2011 г. будет непро- |
ческий кризис на Ближнем Востоке вызвал рост |
стым для всех стран, и Китая в частности. Пре- |
цен на нефть до 100 долл. за баррель. |
жде всего в связи с тем, что в этой стране на- |
|
Кокс
После падения мирового производства кокса в 2008 2009 гг. (до 526,9 и 522,2 млн т на сухой вес соответственно) в 2010 г., по данным европейских экспертов, оно не только восстановилось до предкризисного уровня (544,5 млн т в 2007 г.), но и значительно превзошло его, достигнув 608,4 млн т (сухой вес). Доля Китая попрежнему оставалась высокой (65,8 %).
По оценке китайских экспертов, в 2010 г. Китай имел мощности по производству кокса в объеме 440 млн т, производство кокса составило 388 млн т, имел место избыток мощностей. Экспорт кокса из Китая составил 3,35 млн т. Китай утратил свои позиции основного поставщика кокса на мировой рынок.
В ближайшем будущем экспорт кокса из Китая не выйдет на прежний уровень (до 15 млн т/год) и сохранится в объеме 3 5 млн т/год, хотя он крайне необходим для сбалансированности мирового рынка кокса, который до кризиса был на уровне 30 35 млн т.
Это обстоятельство усилит стремления производителей металла к самообеспеченности коксом и тенденции к сокращению расхода высококачественных коксующихся углей при его производстве, а также сделает использование в доменных печах пы-
леугольного топлива еще более привлекательным. На удовлетворение потребности в коксе негативно повлиял вывод из эксплуатации в 2008 2009 гг. европейских коксовых мощностей в объеме 9,71 млн т в Болгарии, Франции, Польше, Румынии, России и других странах, а также сокращение складских запасов кокса.
Вопросам повышения спроса на кокс в Индии, возможностям коксохимической отрасли этой страны относительно обеспечения потребностей металлургии и ее развитию в ближайшие годы посвятили свои доклады представители индий-
ских компаний Ennore Coke Ltd., Global Coke Ltd.
Как известно, в последние годы в Индии наблюдается стабильный рост производства стали. Ожидают, что к 2015 2016 гг. производство стали в Индии составит 112 млн т, потребность в коксе 60,3 млн т/год (нынешние мощности составляют 30 млн т/год кокса). Имея достаточные запасы железной руды, Индия целиком зависит от импорта коксующегося угля, что в значительной степени усложняет решение поставленной в стране задачи удержания темпов развития металлургии (85 % коксующегося угля импортируется из Австралии, 10 % из США, остальноеиз СНГ и других стран).
ОАО «Черметинформация» • Бюллетень «Черная металлургия» • 7• 2011 ―――――――――――――――― 29

Поэтому усилия индийских металлургов и |
оживление торговли коммерческим коксом и рост |
|
коксохимиков направлены на поиски альтерна- |
цен на кокс. |
|
тивных поставщиков коксующегося угля (Индо- |
Ранее отмечалось, что во втором полугодии |
|
незия, Мозамбик) на долгосрочной контрактной |
2010 г. цены на кокс начали выходить на уро- |
|
основе, усовершенствование технологии коксо- |
вень, делающий его экспорт опять привлека- |
|
вания, оптимизацию логистики, энергосбереже- |
тельным для производителей. |
|
ние, повышение привлекательности отрасли для |
В I кв. 2010 г. экспортная цена китайского до- |
|
иностранных инвесторов с целью создания со- |
менного кокса с содержанием золы 12,5 % со- |
|
вместных предприятий. |
ставляла 500 520 долл/т FOB. |
|
Несмотря на то что Китай утратил свои пози- |
Индийские производители покупали кокс по |
|
ции лидера в поставках кокса на мировой рынок, |
цене 530 540 долл/т CFR. В Европе доменный |
|
цены на китайский кокс по-прежнему оказывают |
кокс покупали по цене 520 530 долл/т CFR; |
|
влияние на рынок, хотя и перестали играть роль |
польский кокс стоил около 520 долл/т на поль- |
|
базовых. |
ской границе. |
|
Рост мирового производства металла в 2010 г. |
|
|
вызвал увеличение спроса на доменный кокс, |
|
|
Уголь для коксования |
|
|
Мировая торговля углем для коксования зна- |
В 2010 г. экспорт австралийского твердого |
|
чительно оживилась в 2009 2010 гг., и в бли- |
коксующегося угля возрос на 20 % по сравнению |
|
жайшие годы рост торговли углем, доставляе- |
с 2009 г. и достиг более 100 млн т, хотя мощно- |
|
мым морским транспортом, будет иницииро- |
сти основных угледобывающих компаний не |
|
ваться странами Азии, прежде всего Китаем и |
увеличились. Наводнение в австралийском |
|
Индией (рис. 1). Китай превратился в чистого |
штате Квинсленд, |
безусловно, скажется на |
импортера угля и будет оставаться таковым. |
рынке угля в 2011 г. и, наряду с другими факто- |
|
|
||
|
рами, на его ценах. На II кв. 2011 г. цена на вы- |
|
|
сококачественный |
твердый коксующийся уголь |
|
зафиксирована на уровне 330 долл/т FOB. Ки- |
|
|
тайские компании готовы покупать твердый кок- |
сующийся уголь по цене 280 290 долл/т CFR. Природные катаклизмы в Австралии еще раз
показали, насколько рынок угля, основными поставщиками которого являются Австралия, Россия, Канада и США, зависит от Австралии. Особенно это сказывается на странах, в наибольшей степени зависящих от австралийских поставок
Рис. 1. Рост импорта коксующегося угля по регионам |
коксующегося угля (Индия, Япония, Тайвань). |
|
|
в 2010 2015 гг. |
|
Технические инновации в коксовом производстве |
Этой тематике была посвящена отдельная сессия саммита, на которой было сделано девять докладов. Если сгруппировать доклады по темам, то они касались следующих проблем:
1. Производство высококачественного доменного кокса из угольной шихты ухудшенного качества (Институт химической переработки угля
ICHPW, Польша).
Польша является одним из крупнейших в ЕС производителей (10 млн т/год) и экспортеров кокса (>5,0 млн т/год). При ограниченных запасах собственного высококачественного коксующе-
гося угля в Польше производят кокс, отвечающий высоким требованиям европейских производителей металла (CRI <30, CSR >60). Поэтому там стараются учитывать все факторы, влияющие на качество кокса (компоненты угольной шихты и ее подготовку, технологию коксования, обработку кокса). К технологиям, направленным на совершенствование подготовки шихты, относят избирательное измельчение, подсушивание, обмасливание шихты, уплотнение (брикетирование, трамбование). Уделяют большое внимание сухому тушению кокса.
30 ―――――――――――――――――ОАО «Черметинформация» • Бюллетень «Черная металлургия» • 7• 2011
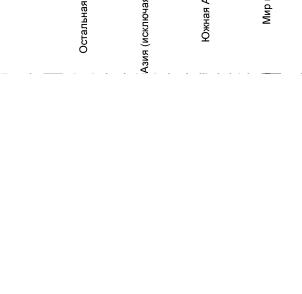
2.Технология производства кокса с улавливанием тепла, без улавливания химических продуктов коксования (компании Suncoke Energy,
Польша; Iron&Steel, HATCH, Канада; Mayan Global Consultants, Индия).
В последние годы в мировой практике производства металлургического кокса получила распространение технология коксования без улавливания химических продуктов, или технология с улавливанием тепла с последующей выработкой электроэнергии. Она применяется в США, Индии, Бразилии, Китае. Наибольших успехов в продвижении данной технологии на современном уровне достигла американская компания Suncoke Energy, построившая пять заводов с печами “без улавливания” в США и Бразилии общей мощностью около 6,0 млн т/год кокса.
Основной мыслью доклада этой компании было то, что на данный момент технология “без улавливания” еще не внедрена в Европе и Suncoke Energy имеет знания и опыт, достаточные для применения технологии на европейских заводах.
Представители канадских и индийской компаний также приводили в своих докладах доводы в пользу технологии “без улавливания” (более чистая с экологической точки зрения, улучшает качество кокса, более проста в эксплуатации, позволяет иметь более гибкую сырьевую базу, обеспечивает производство электрической энергии и др.). Подчеркивалась целесообразность использования этой технологий в сочетании с трамбованием угольной загрузки. Высказывались предложения о сочетании технологий “с улавливанием” и “без улавливания” при строительстве новых металлургических заводов и реконструкции существующих предприятий (для выработки дешевого коксового газа для нужд предприятия и электроэнергии).
3.Коксовые машины нового поколения, автоматизация коксовых машин (компании Schalker Eisenhutt, Германия; John M Henderson, Велико-
британия).
Указанные компании являются известными европейскими изготовителями коксовых машин. Представители этих компаний сосредоточили внимание в своих презентациях на конструктивных особенностях коксовых машин нового поколения, которые имеют высокие технико-экономи- ческие и экологические показатели, а также высокий уровень автоматизации. В работе компаний прослеживается тенденция создания коксовых машин, предназначенных для дистанционного управления с операторского пункта и обес-
печивающих сокращение эксплуатационных затрат и надежность работы.
4.Новые направления в технологии трамбования шихты (Vecon GmbH, Германия).
В представленном компанией докладе приведены ее разработки в совершенствовании технологии трамбования угольной шихты применительно к печам “без улавливания” и “с улавливанием”.
Для печей “без улавливания” разрабатывается оснащение их стационарными устройствами для трамбования угольной загрузки и передвижными устройствами для транспортировки и подачи ее в печи, а также для выталкивания готового коксового пирога.
Для печей “с улавливанием“ предлагаются новые технические решения по отводу газов загрузки в сочетании с регулированием давления в системе отсоса газов (система Sopreco компа-
нии Paul Wurt).
5.Новейшие технологии как основа экономичного производства кокса без ущерба для окружающей среды (Uhde GmbH, Германия).
По мнению немецких специалистов, первоочередное внимание должно быть уделено обновлению мировых мощностей по производству кокса, которые на сегодня практически отработали свой ресурс (рис. 2).
Рис. 2. Средний возраст коксовых заводов в мире
В Западной Европе с 2003 г. уже реализованы контракты по обновлению 9 млн т/год коксовых мощностей и по их расширению на 25 млн т/год. Немецкие компании пошли по пути увеличения высоты и объема коксовых печей (3→4→6→8 м
ОАО «Черметинформация» • Бюллетень «Черная металлургия» • 7• 2011 ―――――――――――――――― 31
и 13→32→39→53→76→94 м3 соответственно), |
Компания DМТ GmbH специализируется на |
считая, что печи большого объема имеют пре- |
оказании широкого спектра услуг безопасного |
имущества по капитальным затратам, эксплуа- |
проведения работ в горнорудном производстве, |
тационным расходам, защите окружающей |
строительстве, в области защиты окружающей |
среды, сроку службы, численности персонала. |
среды, в энергетике. При ее участии сформули- |
Кроме Европы компания Uhde GmbH по- |
рованы основные требования по защите окру- |
строила печи высотой 7,6 м в Китае (общей |
жающей среды от выбросов европейских коксо- |
мощностью 14 млн т/год) и Южной Корее (общей |
химических предприятий, созданы нормативные |
мощностью 8,0 млн т/год). Ее коксовые батареи |
документы, приняты законодательные акты. |
оснащаются системами регулирования давления |
В докладе приводятся основные требования к |
в камере коксования (PROven), беспылевой вы- |
производству кокса, изложенные в нормативном |
дачи кокса, совершенствованного мокрого туше- |
документе по защите воздушной среды (TALuft), |
ния, очистки коксового газа от сероводорода и |
а также в ряде европейских директив и законо- |
аммиака. |
дательных актов. Приводится краткое описание |
6. Снижение выбросов от коксохимических |
наилучших технологий (ВАТ) в области очистки |
производств в EC (DМТ GmbH, Германия). |
коксового газа и сточных вод. |
Заключение |
|
2010 г. ознаменовался очередным мировым |
Ситуация с обеспечением доменного производ- |
рекордом производства стали (более 1,4 млрд т). |
ства коксом и далее будет оставаться непростой. |
Практически все производящие сталь регионы и |
Оживилась мировая торговля коксующимся уг- |
страны показали прирост выплавки. Согласно |
лем. Рост спроса на него и стихийные бедствия в |
прогнозам на период до 2015 г., в ЕС-27, Китае, |
Австралии вызвали рост цен на высококачест- |
Японии, США будет наблюдаться дальнейший |
венный коксующийся уголь. Все большее внима- |
рост ВВП, а мировая выплавка стали достигнет |
ние уделяется внедрению технологий подготовки |
1,9 млрд т. Мировое производство кокса в 2010 г. |
угольной шихты, направленных на расширение |
составило 608,4 млн т (доля Китая около 66 %). |
сырьевой базы коксования. Получает распро- |
Мировой рынок кокса не восстановился до |
странение технология коксования без улавлива- |
прежних объемов (30 35 млн т) в связи с резким |
ния химических продуктов. Совершенствуется |
снижением китайских экспортных поставок, что |
технология трамбования шихты. Большое вни- |
усилило стремление металлопроизводителей к |
мание уделяется внедрению природоохранных |
самообеспечению коксом. В связи с ростом про- |
мероприятий, улучшению условий труда, авто- |
изводства металла спрос на кокс увеличился, |
матизации производства. |
что сопровождалось повышением цен на него. |
|
32 ―――――――――――――――――ОАО «Черметинформация» • Бюллетень «Черная металлургия» • 7• 2011

УДК 669.162 |
А. Ф. ШЕВЧЕНКО, д.т.н. |
|
(Институт черной металлургии им. З.И. Некрасова Национальной академии наук Украины) |
КОМПЛЕКСНАЯ ОЦЕНКА РАЗЛИЧНЫХ ТЕХНОЛОГИЙ ВНЕПЕЧНОЙ ДЕСУЛЬФУРАЦИИ ЧУГУНА
Происходящая в настоящее время активная модернизация сталеплавильного производства включает все технологические составляющие процессов подготовки, выплавки и разливки стали, в том числе процессы внепечной подготовки и десульфурации жидкого чугуна перед конвертерным переделом. Металлурги многих стран имеют значительный опыт и практику внепечной десульфурации чугуна, что позволяет достаточно всесторонне оценить имеющиеся технологические наработки в этой области с целью квалифицированного подхода при выборе рациональной технологии внепечного обессеривания чугуна.
При выборе наиболее рациональной технологии внепечной подготовки чугуна к конвертерному переделу необходимо учитывать следующее:
достигаемую глубину десульфурации чугуна
вусловиях работы современного конвертерного цеха (с производством не менее 2,5 3 млн т/год стали);
обеспеченность технологического процесса базой реагентов;
продолжительность цикла операций и производительность комплекса внепечной обработки;
технологические показатели процесса десульфурациичугуна и потенциальные возможности;
потери, связанные с осуществлением технологии;
капитальные затраты при создании комплекса десульфурации чугуна по реализуемой технологии;
экологию технологического процесса;
уровень гарантий показателей процесса, технологического оборудования и комплекса в целом;
себестоимость (затраты) сквозной технологии внепечной обработки чугуна.
Ниже приведен анализ наиболее конкурентоспособных в настоящее время технологий внепечной десульфурации чугуна на основе фактических и опубликованных данных промышленной эксплуатации комплексов десульфурации чугуна
искачивания шлака.
Сучетом приведенного выше перечня показателей технологии и оборудования внепечной десульфурации к наиболее конкурентоспособным в настоящее время и на ближайшую пер-
спективу можно отнести промышленные процессы десульфурации чугуна вдуванием гранулированного магния без пассивирующих добавок, вдуванием магния в смеси с известью и KRСаО-процесс на основе извести с добавкой плавикового шпата. Сущность этих трех процессов заключается в следующем:
Вариант I. Десульфурация гранулированным магнием осуществляется вдуванием зернистого (0,5 1,6 мм) “чистого” магния (без любых пассивирующих добавок) через погружаемую фурму.
Вариант II. Десульфурация реализуется вдуванием магния в смеси с пассивирующей добавкой извести (в соотношении 1:3–1:4) через погружаемую фурму.
Вариант III. KRСаО-процесс осуществляется предварительным удалением ковшового шлака с последующей засыпкой в ковш извести и плавикового шпата и перемешиванием расплава погружаемой вращающейся (огнеупорной) мешалкой.
Достигаемая глубина десульфурации. Инжекционные процессы вдувания “чистого” магния (вариант I) и магния в смеси с известью (вариант II) обеспечивают широкие возможности по степени и глубине десульфурации жидкого чугуна со снижением содержания серы до уровня0,002 % [1 7], а если необходимо, то до уровня0,001 % [3, 6, 8]. В силу изложенного процессы вдувания магнийсодержащих реагентов получили наибольшее распространение [1 13].
Фактические данные работы ряда предприятий Тайваня [9] и Китая [10, 11] свидетельст-
вуют о том, что при KRСаО-процессе (с использованием в качестве основного реагента извести)
содержание серы в чугуне снижают до уровня ниже 0,010 0,015 %. Количество чугуна с содержанием серы 0,002 % получают нестабильно и только около 17 %. К наиболее эффективным KRСаО-комплексам десульфурации можно отнести установки десульфурации компании CSC, Тайвань, в регламентах которых наиболее низкое содержание серы после обработки гарантировано величиной 0,003 %. Более низкие пределы значений серы не оговорены, хотя при очень тщательном удалении исходного ковшового шлака, при увеличении расхода извести более 9 кг/т чугуна и более длительной операции перемешивания (более 15 мин) в ряде ковшей
ОАО «Черметинформация» • Бюллетень «Черная металлургия» • 7• 2011 ―――――――――――――――― 33
содержание серы в чугуне снижается до уровня
0,002 % [9, 10].
Обеспеченность базой реагентов. При десульфурации чугуна вдуванием магнийсодержащих реагентов как по варианту I, так и по варианту II применяется гранулированный из рас-
плава [5, 8, 14] или зернистый [2, 4, 5, 13, 15]
магний, который в настоящее время получают методом виброфрезерования слитков [1, 12, 13] с последующей обработкой диспергированного магния с округлением частиц и пассивирующей добавкой кальций- и натрийсодержащих соединений. Диспергированный магний производится очень многими странами Европы, Азии и Америки и неограниченно поставляется в товарном виде на мировой рынок. Основным поставщиком магния на мировой рынок является Китай. Цена диспергированного магния колеблется в преде-
лах 2500 3000 долл/т.
При десульфурации вдуванием магния в смеси с известью применяется высококачественная порошковая известь, для получения которой создается, как правило, новое специализированное производство молотого порошка с регламентированным фракционно-дисперсным составом извести, высоким содержанием СаОакт (более 95 %), низкой величиной потерь ( 1,5 %) при прокаливании и отсутствием других примесей. Помол и приготовление этих порошков осу-
ществляют в условиях исключения их увлажнения и добавкой специальных поверхностно-ак- тивных материалов для обеспечения высокой текучести извести [12, 13]. Цена такой извести значительна и составляет 250 долл/т и выше.
При KRСаО-процессе используется высококачественная обожженная металлургическая известь, производимая, как правило, в печах Мерца. Цена такой извести составляет в среднем 140 долл/т. Для повышения активности ковшового шлака к извести добавляют CaF2-содер- жащие материалы (около 10 %).
Продолжительность цикла и производительность процесса. Основные выполняемые операции, их продолжительность и полный цикл по анализируемым технологиям представлены в табл. 1, из которой видно, что большинство операций по различным способам совпадают, но имеются и существенные различия. Первое отличие инжекционные процессы (вариант I и II) не требуют обязательного удаления ковшового шлака перед десульфурацией, а при KRСаО-процессе эта операция является обязательной. Объясняется это тем, что процесс по варианту III осуществляется высокоактивным ковшовым шлаком на основе оксида кальция, а все другие примеси этому мешают. Если указанное требование не обеспечивается, то KRСаО-процесс не обеспечивает требуемую десульфурацию чугуна.
ТАБЛИЦА 1. СОСТАВЛЯЮЩИЕ РАСЧЕТНОГО ЦИКЛА И ПРОДОЛЖИТЕЛЬНОСТИ ОПЕРАЦИЙ ДЕСУЛЬФУРАЦИИ ЧУГУНА И СКАЧИВАНИЯ ШЛАКА В 300-т ЗАЛИВОЧНЫХ КОВШАХ (СНИЖЕНИЕ СОДЕРЖАНИЯ СЕРЫ В ЧУГУНЕ С 0,020 0,025 ДО 0,002 0,003 %)
|
Продолжительность операции при различных технологиях, мин |
||||
Операция |
|
вариант I |
|
вариант II |
вариант III |
|
вдувание |
|
вдувание |
|
|
|
гранулированного |
|
магния в смеси с |
KRСаО-процесс |
|
|
|
магния |
|
известью |
|
Постановка ковша с чугуном на пост обработки |
|
1,5 |
|
1,5 |
1,5 |
Отбор пробы чугуна и замер температуры |
|
1 |
|
1 |
1 |
Наклон ковша и подготовка к предварительному |
|
|
|
|
|
скачиванию ковшового шлака |
|
|
|
|
1 |
Скачивание шлака перед десульфурацией |
|
|
|
|
5,5 |
Возврат ковша в вертикальное положение |
|
|
|
|
1 |
Подготовка к десульфурации |
|
1 |
|
1 |
1 |
Выполнение операции десульфурции (вдувание |
|
|
|
|
|
магния, вдувание смеси, перемешивание мешалкой) |
|
4 |
|
10 |
17 |
Завершение десульфурации, подготовка к |
|
|
|
|
|
скачиванию шлака |
|
1,5 |
|
1,5 |
1,5 |
Скачивание шлака из ковша после десульфурации |
|
5,0 |
|
5,5 |
6 |
Возврат ковша в вертикальное положение |
|
1 |
|
1 |
1 |
Отбор пробы чугуна и замер температуры |
|
1 |
|
1 |
1 |
Выдача ковша с чугуном в позицию съема краном, |
|
|
|
|
|
съем ковша краном |
|
2 |
|
2 |
2 |
Итого |
|
18 |
|
24,5 |
40,5 |
Второе существенное отличие заключается в |
характерна для вдувания гранулированного или |
||||
различной длительности операций десульфура- |
зернистого магния без добавок, что обусловлено |
||||
ции. Самая кратковременная операция (4 мин) |
наименьшим |
расходом обессеривающего реа- |
34 ―――――――――――――――――ОАО «Черметинформация» • Бюллетень «Черная металлургия» • 7• 2011

гента и высокой интенсивностью вдувания магния (до 22 26 кг/мин) [3, 5, 15]. По варианту II вдувание смеси магния и извести происходит с интенсивностью подачи смеси около 70 кг/мин [1, 7, 10, 12, 13] и занимает в среднем 10 мин. При десульфурации KRСаО-процессом перемешивание вращающейся мешалкой осуществляется в течение 17 мин [9] и даже более.
Различается также длительность операции удаления шлака после десульфурации: наименее продолжительна (5 мин) эта операция при варианте I, а наиболее продолжительна (6 7
мин) при KRСаО-процессе, что связано с большим дополнительным шлакообразованием в резуль-
тате десульфурации.
В итоге по варианту I (десульфурация гранулированным магнием) процесс является самым кратковременным с общим циклом всех опера-
ций 18 мин, а по варианту III (KRСаО-процесс) наиболее длительным (40,5 мин), т. е. в 2,2 раза
более продолжительным. Вдувание смеси магния с известью занимает промежуточное положение. Инжекционные процессы (варианты I и II) по длительности имеют цикл меньше, чем цикл конвертерной плавки, а KRСаО-процесс более длительный. Это, соответственно, свидетельствует о производительности поста десульфурации по каждой технологии. При инжекционных процессах один пост обеспечивает работу конвертера, а при KRСаО-процессе требуются два
поста десульфурации на каждый конвертер [9], что, соответственно, сопровождается двойными капитальными и текущими затратами.
Технологические показатели процесса десульфурации. Технологические показатели процесса десульфурации включают значительное количество составляющих. Основные из них представлены в табл. 2, в которой приведены опубликованные данные по различным технологиям. Из табл. 2 следует, что наиболее выигрышным является процесс вдувания магния без разубоживающих добавок (вариант I), так как сопровождается наименьшим расходом магния (например, при исходном содержании серы
0,020 0,023 % и конечном 0,002 0,003 % расход магния составляет 0,31 кг/т чугуна), самым коротким циклом обработки (18 мин, включая пробоотбор, десульфурацию, скачивание шлака и др.), наименьшим расходом реагента на удаленную серу (1,72 кг/кг) и на всю обработку (86 кг/ковш), самой короткой операцией десульфурации (5 мин), наиболее высокой степенью усвоения магния на серу (44 % при исходной сере 0,020 % и конечной 0,002 %), наименьшим дополнительным шлакообразованием (0,62 кг/т чугуна), наименьшим снижением температуры ( 5 С) и незначительными потерями чугуна (0,28 кг/т) с дополнительно образующимся шлаком.
ТАБЛИЦА 2. ОСНОВНЫЕ ТЕХНОЛОГИЧЕСКИЕ ПАРАМЕТРЫ И ПОКАЗАТЕЛИ ДЕСУЛЬФУРАЦИИ ЧУГУНА ПО РАЗЛИЧНЫМ ТЕХНОЛОГИЯМ В 300-т ЗАЛИВОЧНЫХ КОВШАХ
|
Вариант I |
|
Вариант II |
Вариант III |
Параметр, показатель |
вдувание |
|
вдувание магния |
KRСаО-процесс, смесь |
гранулированного |
|
в смеси |
СаО + СаF2 и |
|
|
магния |
|
с известью |
перемешивание |
|
[3, 5, 8, 15] |
[2, 7,`13, 16] |
мешалкой |
|
Содержание серы в чугуне, %: |
|
|
|
|
исходное |
0,020 |
0,020 |
0,022 |
|
после десульфурации |
0,002 |
0,002 |
0,003 |
|
Удельный расход реагентов, кг/т чугуна: |
1 |
1 |
1 |
|
магния |
0,31 |
0,49 |
|
|
извести |
|
1,55 |
6,2 |
|
всего реагентов |
0,31 |
2,04 |
6,9 |
|
Длительность цикла операций десульфурации |
|
|
|
|
и скачивания шлака, мин |
18 |
24,5 |
40,5 |
|
Расход реагентов на удаленную серу, кг/кг |
1,72 |
11,3 |
36,3 |
|
Расход реагентов на обработку (280 т чугуна), |
|
|
|
|
кг/ковш |
86 |
570 |
1932 |
|
Длительность операций скачивания шлака, мин |
5 |
5,5 |
11 |
|
Степень усвоения магния на удаленную серу, % |
44 |
28 |
|
|
Количество дополнительно образующегося в ковше |
|
|
|
|
шлака: |
|
|
|
|
удельное, кг/т чугуна |
0,62 |
4,08 |
13,8 |
|
общее, кг/ковш |
175 |
1140 |
3860 |
|
Снижение температуры чугуна, оС |
5 |
6,7 |
35 42 |
|
Потери чугуна с дополнительно образующимся |
|
|
|
|
шлаком, кг/т чугуна |
0,28 |
|
2 |
6,8 |
ОАО «Черметинформация» • Бюллетень «Черная металлургия» • 7• 2011 ―――――――――――――――― 35
KRСаО-процесс (вариант III) в противополож- |
внимание на то, что использование метода ко- |
||
ность варианту I имеет комплекс невысоких тех- |
инжекции на установках десульфурации чугуна |
||
нологических показателей, основными из кото- |
значительно увеличивает капитальные затраты |
||
рых являются наибольший расход |
реагентов |
[3] за счет большего объема технологического |
|
(более 5 кг/т чугуна) [9 11], необходимость пред- |
оборудования и средств автоматизации. По мне- |
||
варительного скачивания шлака, большая дли- |
нию автора, применение метода коинжекции для |
||
тельность обработки (40 мин и более), невысо- |
вдувания магния в смеси с известью на установ- |
||
кая степень усвоения реагентов, значительное |
ках десульфурации обусловлено в значительной |
||
шлакообразование, большие потери темпера- |
степени коммерческими интересами поставщика |
||
туры расплава (около 40 С) и чугуна со шлаком |
и неумением разработчиков этого процесса |
||
(6,8 кг/т чугуна). Поэтому кажущаяся простота |
обеспечить плавную нарастающую подачу по- |
||
технологии KRСаО-процесса и дешевизна реа- |
рошковых реагентов через фурму, погруженную |
||
гента (извести) сопровождается весьма ощути- |
в расплав, и последующее устойчивое и надеж- |
||
мыми технологическими и техническими недос- |
ное вдувание магния без разубоживающих доба- |
||
татками. |
|
вок. |
|
Вдувание магния в смеси с пассивирующей |
При объективном анализе применяемых тех- |
||
добавкой извести (вариант II) занимает проме- |
нологий нужно учитывать данные ряда исследо- |
||
жуточное положение между вариантами I и III. |
ваний, которые свидетельствуют о том, что |
||
При рассмотрении этого процесса необходимо |
сульфидная емкость многих ковшовых шлаков |
||
обратить внимание на следующие вопросы. Тео- |
меньше необходимой [17, 23 25], а сера в шла- |
||
ретическая и практическая полезность вдувания |
ках после десульфурации магнием представлена |
||
магния в смеси с известью не доказана. Наобо- |
сульфидами CaS и MnS [24], а не MgS. Этим |
||
рот, начиная с 80-х годов прошлого |
столетия, |
обусловливается рациональность |
увеличения |
металлурги Украины показали нерациональ- |
содержания СаО в шлаках. Изложенное выше |
||
ность и вред вдувания магния в смеси с напол- |
явилось обоснованием разработчикам коинжек- |
||
нителями [3, 12, 16], поэтому были разработаны |
ционных процессов десульфурации магнийсо- |
||
процессы вдувания “чистого” магния (без доба- |
держащими смесями осуществлять |
вдувание |
|
вок) [3, 12, 17]. Впоследствии этот вывод был |
магния совместно с известью. |
|
|
подтвержден широкой промышленной практикой |
С таким технологическим решением ввода |
||
на китайских металлургических комбинатах [1, 3, |
магния в жидкий чугун нельзя согласиться. Без- |
||
8, 11 13, 18, 19], в том числе на предприятиях |
условно, невысокая основность ковшовых шла- |
||
г. Уханя, Шагана и Тайюаня, где вдувание смеси |
ков (0,3 0,8) [17, 24] указывает на целесообраз- |
||
магния с известью было заменено украинской |
ность ввода оксида кальция в систему рафини- |
||
технологией вдувания гранулированного магния |
рования чугуна магнием, но это нельзя осущест- |
||
(без извести). Нерациональность совместного |
влять совместным вдуванием магния и извести, |
||
вдувания магния и извести отмечена также дру- |
так как пассивирующая добавка извести ухуд- |
||
гими исследователями [20] по опыту работы ус- |
шает массообменные процессы магния с рас- |
||
тановок десульфурации чугуна в 300-т заливоч- |
плавом чугуна и сильно снижает степень усвое- |
||
ных ковшах Алчевского (технология Simens VAI), |
ния магния [1, 3, 5, 12, 17, 19], увеличивая его |
||
Новолипецкого (технология ESM) металлургиче- |
удельный расход. |
|
|
ских комбинатов, а также рядом других зарубеж- |
Наиболее рациональным решением является |
||
ных специалистов [21]. |
|
вдувание магния без любых пассивирующих до- |
|
Неубедительны также доводы ряда разработ- |
бавок, а СаО-содержащие материалы (в каче- |
||
чиков [1, 12, 13] о необходимости совместной |
стве корректирующей добавки) целесообразно |
||
подачи магния и извести со смешиванием их в |
загружать в ковш отдельно (без магния). Такая |
||
трубопроводе (метод коинжекции), так как в 70-е |
технологическая схема обеспечивает наиболее |
||
годы прошлого столетия украинскими исследо- |
благоприятные условия для высокого усвоения |
||
вателями было установлено [17], что качествен- |
вдуваемого магния и одновременно решается |
||
ная готовая порошковая смесь магния с изве- |
задача увеличения сульфидной емкости ковшо- |
||
стью не изменяет свои свойства при транспорти- |
вого шлака и создания требуемого шлакового |
||
ровании и не отличается от смеси, полученной |
режима. В качестве корректирующей добавки в |
||
методом коинжекции. Кроме этого принцип ко- |
шлак при этой схеме могут применяться неде- |
||
инжекции является более затратным в аппара- |
фицитные дешевые материалы (с широкими |
||
турном исполнении, достаточно сложным и не |
пределами физико-химических свойств), в том |
||
гарантирует однородность состава смеси. Этим |
числе из отходов обжига и утилизации СаО-со- |
||
можно объяснить применение в свое время го- |
держащих материалов (а не высококачественная |
||
товых магнийсодержащих смесей на ряде ме- |
с особыми свойствами молотая известь). Техно- |
||
таллургических комбинатов Украины [17] и зару- |
логический процесс десульфурации чугуна маг- |
||
бежья [22]. Дополнительно необходимо обратить |
|
|
36 ―――――――――――――――――ОАО «Черметинформация» • Бюллетень «Черная металлургия» • 7• 2011

нием по этой схеме проверен и реализован для ряда металлургических комбинатов [3, 5, 8, 15].
При анализе технологических факторов различных процессов десульфурации дополнительно необходимо учитывать влияние собственно технологии десульфурации на физические свойства шлака с учетом последующей операции скачивания шлака из ковша. Обработка чугуна реагентами, содержащими оксид СаО, сопровождается увеличением вязкости ковшовых шлаков [13], повышением содержания Feмет в шлаках до 50 60 % и, соответственно, увеличением потерь чугуна с этими шлаками.
При обработке чугуна вдуванием магния без пассивирующих добавок (СаО, СаС2) физико-хи- мические свойства ковшовых шлаков существенно не отличаются от исходных шлаков. Это обусловлено значительным количеством исходного ковшового шлака перед десульфурацией (больше 10 15 кг/т чугуна) и очень малым количеством (в среднем 0,6 1,0 кг/т чугуна) дополнительно образующегося в ковше шлака. В итоге ковшовый шлак после десульфурации магнием (обогащенный до 40 % корольками чугуна и выделившейся графитовой спелью) является также весьма вязким. Тем не менее такие шлаки непосредственно после завершения десульфурации могут быть подвижными, что является следствием барботирования расплава в ковше и дробления шлакового покрова.
Анализ физико-химических свойств ковшовых шлаков, образующихся в промышленных условиях, показывает, что эти шлаки, как правило, не являются жидкими. Тем не менее для улучшения условий их удаления рациональными являются
добавки в ковш материалов для загущения шлаков (перед их скачиванием) и применение барботирования ванны азотом для перемещения шлакового покрова в сторону машины скачивания шлака [5, 15]. Такие меры увеличивают степень очищения чугуна от шлака и уменьшают количество шлака, попадающего в конвертер со сливаемым чугуном.
Загущение ковшовых шлаков при десульфурации чугуна вдуванием смеси магния с известью и барботирование ванны азотом также осуществляются на ряде металлургических комбинатов [1, 12, 16, 17], подтверждая рациональность этих технологических приемов при различных технологиях десульфурации чугуна, а также для условий, когда внепечная десульфурация не применяется.
Потери при внепечной обработке. Потери при внепечной десульфурации чугуна и скачивании шлака связаны в основном (см. табл. 2) с потерями чугуна и снижением температуры расплава [11]. Величины этих потерь обусловлены в основном видом применяемого процесса десульфурации [3, 5, 10, 11]. Как показали ранее выполненные исследования, наибольшие потери характерны для KRСаО-процесса, при котором снижение температуры чугуна составляет около 40 С (см. табл. 2), а потери металла 10,85 кг/т обрабатываемого металла [11] (табл. 3). Основными причинами столь больших потерь являются большой расход реагентов, большое дополнительное шлакообразование, значительная длительность операций, существенный недолив ковшей чугуном и значительное вращение поверхности расплава в период обработки.
ТАБЛИЦА 3. ПОТЕРИ ЧУГУНА ПРИ ДЕСУЛЬФУРАЦИИ ЧУГУНА ПО РАЗЛИЧНЫМ ТЕХНОЛОГИЯМ [11]
|
Вариант I |
|
Вариант II |
Вариант III |
|
вдувание |
|
вдувание магния в |
KRСаО-процесс, |
Потери чугуна |
гранулирован- |
|
смеси с известью |
|
|
смесь СаО + СаF2 |
|||
ного магния |
|
(процесс ESM, |
||
|
|
и перемешивание |
||
|
(украинский |
|
Polysius-SVAI, |
|
|
|
мешалкой |
||
|
процесс) |
|
Danieli) |
|
|
|
|
||
Потери чугуна за счет операции скачивания |
0 |
|
0 |
|
шлака перед десульфурацией, кг/т чугуна |
(шлак |
|
(шлак |
1,28 |
|
не скачивается) |
|
не скачивается) |
|
Потери чугуна со шлаком, образующимся при |
|
|
|
|
десульфурации, кг/т чугуна |
0,28 |
|
1,82 |
7,65 |
Потери чугуна от операции скачивания шлака |
|
|
|
|
после десульфурации, кг/т чугуна |
1,56 |
|
1,91 |
1,92 |
Суммарные потери чугуна, кг/т чугуна |
1,84 |
|
3,73 |
10,85 |
Десульфурация чугуна вдуванием гранулиро- |
Десульфурация чугуна вдуванием магния в |
ванного магния без разубоживающих добавок |
смеси с известью (вариант II) занимает промежу- |
(вариант I) имеет (см. табл. 3) наименьшие по- |
точное положение: потери при варианте II меньше в |
тери температуры (5 оС) и чугуна (1,84 кг/т чу- |
2,9 раза, чем при KRСаО-процессе, но практически |
гуна) при обеспечении операций десульфурации |
вдвое больше, чем при вдувании гранулированного |
и скачивания шлака из ковша. |
магния по украинской технологии. |
ОАО «Черметинформация» • Бюллетень «Черная металлургия» • 7• 2011 ―――――――――――――――― 37
Капитальные затраты на создание комплекса десульфурации. Данные по капитальным затратам при строительстве комплексов десульфурации и скачивания шлака по понятным причинам не публикуются и не освещаются. Но по анализу структурного содержания комплексов по различным технологиям с учетом их пропускной способности можно констатировать, что при KRСаО- процессе капитальные затраты самые высокие и в 1,5 2 раза больше, чем при инжекционных технологиях вдувания диспергированных реагентов.
Вдувание гранулированного магния без извести (вариант I) включает наименьшее количество оборудования и металлоконструкций и поэтому требует наименьших капитальных затрат.
Вдувание магния в смеси с известью (вариант II) требует большего количества оборудования для приготовления смесей, более сложной и емкой системы автоматизации, а поэтому капитальные затраты по этой технологии больше, чем по варианту I (вдувание магния без разубоживающих добавок).
Экология технологических процессов. Рассматриваемые технологические процессы десульфурации реализуются со связыванием серы в твердые сульфиды кальция и магния. Образующиеся сульфиды в основном попадают в ковшовый шлак, изменяя (совместно с другими составляющими) его состав и частично физические характеристики. Образующиеся шлаки не являются токсичными и по своим характеристикам вписываются в применяемую на комбинатах схему утилизации доменных и конвертерных шлаков.
Выделяющийся из ковшей дым содержит газовую и пылевидную фазы, которые также не являются токсичными. Газовая фаза включает в основном подсасываемый воздух, за счет чего температура дыма в газоходе снижается до 160 300 С. Газовая фаза дыма включает: 17 20 % О2, более 79 % N2, 0,2 0,9 % СО2, содержание СО, SO2, NO2 не превышает допустимые нормы.
Запыленность отходящих газов составляет 2 15 г/нм3. Пылевая часть в основном содержит оксиды магния, кальция, кремния и железа (в сумме более 70 %). Содержание спели достигает 26 %.
По своему химическому составу выделяющийся из ковша дым (по всем трем вариантам технологий десульфурации) не является токсичным, но требует улавливания и очистки от пыли. Наиболее распространенный вариант очистки сухая газоочистка с тканевыми фильтрами. При наличии на комбинате резервов выделяющийся дым может направляться в имеющиеся газоочистные сооружения.
Несмотря на различные реагенты и их удельные расходы, сравниваемые процессы по пылегазовым выбросам можно принять равноценными.
Потенциальный уровень гарантий технологий десульфурации. Анализируемые технологии десульфурации чугуна реализуют различные механизмы массообменных процессов. KRСаО-про- цесс реализует взаимодействие создаваемого ковшового шлака с жидким чугуном при перемешивании системы металл шлак, вращаемой погружаемой мешалкой. Инжекционные процессы (варианты I и II) реализуются за счет создания в объеме чугуна развитой и высокоактивной магнийсодержащей зоны, т. е. все процессы осуществляются в объеме расплава. Поэтому негативное влияние ковшового шлака не играет решающего значения, вследствие чего имеющиеся ковшовые шлаки перед десульфурацией по вариантам I и II не скачивают.
В силу изложенного, сравнивая KRСаО-про- цесс и инжекционные процессы (варианты I и II), следует заключить, что инжекционные технологии имеют более предпочтительный и приоритетный уровень гарантий, так как реализуют наиболее управляемый и стабильный физикохимический потенциал взаимодействия обессеривающей среды с рафинируемым расплавом.
Из двух инжекционных процессов (варианты I и II) наиболее выигрышным является украинский процесс вдувания гранулированного магния (вариант I), так как реализуется через активное растворение магния в чугуне и последующее взаимодействие растворенного магния с серой чугуна [1, 3, 5, 6, 12, 19]. Преимущества украинской технологии усиливаются исключением негативного влияния окружающей среды на эффективное усвоение магния чугуном.
Себестоимость внепечной десульфурации. При оценке затрат на десульфурацию чугуна по различным технологиям необходимо учитывать не только расходы реагентов и их цену, а также все статьи расходов, связанных с реализацией процессов внепечной обработки. На примере оценки процессов по вариантам I, II и III выполнено такое сопоставление для условий обработки чугуна в 300-т заливочных ковшах при снижении серы с 0,020 до 0,002 % (табл. 4).
Из табл. 4 следует, что наибольшие затраты на обессеривающий реагент характерны для варианта II (вдувание смеси магния с известью). Самые высокие затраты, связанные с потерей чугуна, снижением температуры, удалением и утилизацией шлаков, сопровождают KRСаО-про- цесс.
38 ―――――――――――――――――ОАО «Черметинформация» • Бюллетень «Черная металлургия» • 7• 2011
ТАБЛИЦА 4. СОПОСТАВЛЕНИЕ ОСНОВНЫХ ЗАТРАТ ПРИ ДЕСУЛЬФУРАЦИИ ЧУГУНА ПО РАЗНЫМ ТЕХНОЛОГИЯМ В 300-т ЗАЛИВОЧНЫХ КОВШАХ
(СНИЖЕНИЕ СОДЕРЖАНИЯ СЕРЫ С 0,020 ДО 0,002 %)
|
Вариант I |
Вариант II |
Вариант III |
|
|
вдувание |
вдувание магния в смеси |
KRСаО-процесс, |
|
Показатель |
гранулирован- |
с известью |
||
смесь СаО + СаF2 и |
||||
ного магния |
(процесс ESM, |
|||
|
перемешивание |
|||
|
(украинский |
Polysius-SVAI, |
||
|
мешалкой |
|||
|
процесс) |
Danieli) |
||
|
|
|||
Расход реагентов, кг/т чугуна: |
|
|
|
|
магний |
0,31 [3, 8] |
0,49 [2, 16] |
|
|
молотая известь |
|
1,55 |
|
|
известь + СаF2 |
|
|
6,9 [9] |
|
всего реагентов |
0,31 |
2,04 |
6,9 |
|
Стойкость фурмы (мешалки), количество |
|
|
|
|
обработок [2, 6] |
150 |
150 |
450 |
|
Снижение температуры чугуна, С [11] |
5 |
7 |
42 |
|
Потери чугуна с дополнительно образующимся |
|
|
|
|
шлаком и при скачивании шлака, кг/т чугуна |
|
|
|
|
[11] |
1,84 |
3,73 |
10,85 |
|
Затраты при десульфурации, долл/т чугуна: |
2,431 |
4,168 |
7,323 |
|
на магний [26] |
0,93 |
1,47 |
|
|
на молотую порошковую известь [26] |
|
0,388 |
|
|
на смесь фракционированной извести с |
|
|
|
|
плавиковым шпатом [9] |
|
|
1,38 |
|
на компенсацию потерь температуры |
|
|
|
|
чугуна [26] |
0,15 |
0,20 |
1,26 |
|
на фурму (мешалку) [26] |
0,056 |
0,056 |
0,025 |
|
на потери чугуна [11, 26] |
0,575 |
1,044 |
3,038 |
|
затраты на удаление и утилизацию |
|
|
|
|
ковшового шлака [26] |
0,30 |
0,50 |
1,20 |
|
расходы по переделу и все прочие расходы |
|
|
|
|
по обслуживанию комплекса |
|
|
|
|
десульфурации |
0,42 |
0,51 |
0,42 |
|
Суммарные затраты в относительных единицах |
1 |
1,72 |
3,01 |
В итоге самые низкие суммарные затраты характерны для процесса вдувания гранулированного магния без разубоживающих добавок (2,431 долл/т чугуна), а самые высокие (7,323 долл/т чугуна) при KRСаО-процессе. Вдувание магния в смеси с известью занимает промежуточное положение. В относительных единицах варианты I, II и III соотносятся как 1:1,72:3,01 (см. табл. 4).
Необходимо отметить, что приведенные в табл. 4 затраты на потери чугуна для всех технологий десульфурации включают одинаковые затраты (около 0,5 долл/т) с исходным ковшовым шлаком по вине доменщиков, не обеспечивших подачу ковшей с чугуном без шлака.
Сопоставление затрат по разным технологиям десульфурации чугуна, свидетельствует о том, что несмотря на то что технологии по вариантам II и III применяют в составе реагентов более дешевую известь, затраты на их реализацию наиболее высокие. Самым экономичным является процесс вдувания гранулированного (зернистого) магния без различных разубоживающих добавок, и прибыль от его применения в сравнении с процессом вдувания смесей составляет 1,72 долл/т чугуна, а в сравнении с KRСаО-про- цессом 4,89 долл/т чугуна. При увеличении количества удаляемой серы экономические преимущества технологии по варианту I возрастают.
ОАО «Черметинформация» • Бюллетень «Черная металлургия» • 7• 2011 ―――――――――――――――― 39
Заключение
Таким образом, приведенный метод комплексной оценки показателей процессов внепечной десульфурации чугуна позволяет более глубоко и всесторонне проанализировать различные технологические решения.
Показано, что, несмотря на то что магний значительно дороже извести, все процессы десульфурации с применением извести являются наиболее затратными, из них KRСаО-процесс самый неэкономичный.
Инжекционные процессы с вдуванием диспергированных магнийсодержащих реагентов
являются более экономичными и рациональными, так как используют наименьшее количество реагентов и обладают большей степенью гарантий.
Из всех применяемых процессов внепечной десульфурации наиболее экономичным, рациональным и предпочтительным является украинский процесс внепечной десульфурации чугуна вдуванием диспергированного (зернистого, гранулированного) магния без разубоживающих добавок через погружаемые фурмы с применением специальной системы дозирования и инжекции.
БИБЛИОГРАФИЧЕСКИЙ СПИСОК
1. IX Международный симпозиум по десульфурации чугуна и стали: Сб. докладов. г. Галати, Румыния, 18 21 сентября 2006 г. 91 с.
2.Освоение технологии производства сталей с использованием установки десульфурации чугуна в условиях конвертерного производства ОАО “Северсталь” / А. А. Степанов, А. М. Ламухин, С. Д. Зинченко и др.: Сб. трудов
VIII Международного симпозиума по десульфурации чугуна и стали. г. Нижний Тагил, Россия. 2004 г. С. 83 87. 3. Создание и развитие рациональных технологий внепечной десульфурации чугуна / В. И. Большаков,
А. Ф. Шевченко, Лю Дун Ие и др. // Сталь. 2009. № 4. С. 13 20.
4.Кушнарев А. В. Опыт использования инжекционных технологий внепечной десульфурации ванадийсодержащего чугуна-полупродукта в конвертерном цехе НТМК: Сб. трудов VIII Международного симпозиума по десульфурации чугуна и стали. г. Нижний Тагил, Россия. 2004 г. С. 5 11.
5.Шевченко А. Ф., Вергун А. С., Двоскин Б. В. Внепечная десульфурация чугуна магнием в заливочных ковшах // Металлургическая и горнорудная промышленность. 2010. № 7. С. 101 103.
6.Процесс особо глубокой десульфурации чугуна вдуванием магния в условиях крупнопромышленного производства
стали / А. Ф. Шевченко, А. С. Вергун, А. С. Булахтин и др. // Металл и литье Украины. 2006. № 1. С. 84 89.
7. Сравнение эффективности современных технологий внедоменной десульфурации чугуна / А. М. Зборщик, С. В. Куберский, К. Е. Писмарев и др. // Сталь. 2010. № 1. С. 21 23.
8.Большаков В. И., Шевченко А. Ф. Технология особо глубокой десульфурации чугуна // Металлургическая и горнорудная промышленность. 2009. № 6. С. 9 12.
9.Технологические регламенты на десульфурацию чугуна известьсодержащими материалами в заливочных ковшах стальзавода № 2 компании СSC (Тайвань) при обработке KR-процессом.
10.Инь Жуй Ю. Отечественное сталеплавильное производство обзор состояния и развития технологий до 2010 г.: Сб. докладов // Научно-техническая конференция по выплавке и непрерывной разливке стали. г. Ханчжоу, Китай.
11.Влияние внепечной подготовки чугуна на потери чугуна с ковшовым шлаком / А. Ф. Шевченко, Лю Дун Ие, Л. П. Курилова и др. // Черная металлургия: Бюл. ин-та “Черметинформация”. 2009. № 2. С. 31 35.
12.VII Международный симпозиум по десульфурации чугуна и стали: Сб. докладов. г. Аниф, Австрия. 2002 г. 93 с.
13.VIII Международный симпозиум по десульфурации чугуна и стали: Сб. докладов. г. Нижний Тагил, Россия. 2004 г.
87 с.
14.Баранник И. А., Комелин И. М., Савенец Ю. И. История и перспективы производства гранулированного магния // Цветные металлы. 2008. № 3. С. 66 71.
15.Новый комплекс особо глубокой десульфурации чугуна в большегрузных заливочных ковшах / В. И. Большаков, А. Ф. Шевченко, А. М. Башмаков и др. // Металлург. 2010. № 11. С. 34 37.
16.Опыт работы Череповецкого металлургического комбината по достижению ультранизкого содержания серы в чугуне с использованием крупнотоннажной установки десульфурации чугуна / А. Н. Луценко, А. А. Немтинов, С. Д. Зинченко и др. // Черная металлургия: Бюл. ин-та “Черметинформация”. 2009. № 7. С. 61 63.
17.Воронова Н. А. Десульфурация чугуна магнием. М.: Металлургия. 1980. 239 с.
18.Применение технологии десульфурации чугуна чистым гранулированным магнием на Уханьском металлургическом комбинате / А. Ф. Шевченко, Б. В. Двоскин, А. С. Вергун и др. // Сталь. 2002. № 4. С. 46 48.
19.Создание и промышленное применение современных аппаратурно-технологических комплексов десульфурации чугуна на металлургических комбинатах Китая / В. И. Большаков, А. Ф. Шевченко, В. А. Александров и др. //
Металлургическая и горнорудная промышленность. 2004. № 4. С. 6 10.
20. Сравнение эффективности современных технологий внедоменной десульфурации чугуна / А. М. Зборщик, С. В. Куберский, В. В. Акулов, Г. Я. Довгалюк // Сталь. 2010. № 1. С. 21 23.
21.Корос П. И., Турунен М. Т. Вдувание извести и магния для десульфурации металла / Пер. с англ. Инжекционная металлургия. г. Лулсо, Швеция. 1977 г. М.: Металлургия. 1981. С. 157 160.
22.The Global Voice For Magnesium. International Magnesium Association. Prague / Czech Republic. 1999. 173 р.
40 ―――――――――――――――――ОАО «Черметинформация» • Бюллетень «Черная металлургия» • 7• 2011
23.Б. В. Двоскин, Н. Т. Ткач, М. И. Шеенко и др. // РЖМет. 1987. № 10. С. 18. 10В126. Деп. Депонированные научные работы. № 4061-ЧМ87.
24.Особенности формирования шлака в ковше при внедоменной десульфурации инжектированием гранулированного магния / А. С. Вергун, П. С. Лындя, А. Ф. Шевченко, А. Л. Руденко // Металознавство та термічна обробка металів: Сб. ДСНАУ. Днепропетровск, 2007. С. 48 51.
25.Особенности структуры металлической и неметаллической фаз шлака, формирующегося в ковше при десульфурации чугуна магнием без добавок / А. С. Вергун, А. М. Нестеренко, В. Г. Кисляков, А. Ф. Шевченко // Теория и практика металлургии. Днепропетровск, 2009. С. 86 90.
26.Международная научно-техническая конференция по выплавке и непрерывной разливке стали: Сб. докладов. г. Ханчжоу, Китай. 2008 г. 468 с.
669.162:54 |
В. В. МИСА1, Т. И. ЛЫСЕНКО2, Ю. С. ПАНИОТОВ2, к.т.н. |
|
( 1 ПАО “АрселорМиттал Кривой Рог”, 2 Национальная металлургическая академия Украины) |
ИЗМЕНЕНИЕ ПАРАМЕТРОВ ЧУГУНА ЗА ВРЕМЯ ПРЕБЫВАНИЯ В МИКСЕРЕ
Проведена статистическая обработка на ПЭВМ с использованием электронных таблиц Exсel массива данных о поступлении 270 чугуновозных ковшей из доменного цеха в миксерное отделение конвертерного цеха и такого же количества заливочных ковшей, наполняемых из миксера в тот же период.
Чугун поступает в типовых 140-т чугуновозных ковшах, заполненных чугуном на 90 %. Заливочные ковши имеют вместимость 140 т, масса чугуна на плавку 120–130 т. Миксер емкостью 1300 т, среднее время пребывания чугуна в миксере составляет около 7 ч.
Доменный шлак скачивался. Производился химический анализ чугуна и измерялась его температура перед сливом в миксер и заливочный ковш. Эти сведения составили базу данных ПЭВМ для дальнейшей обработки.
Содержание углерода в чугуне рассчитали по выражению*:
С= 1,3 + 2,57 10 3Т– 0,27Si + 0,06Mn 0,0032P 0,003S.
Втаблице приведено сравнение параметров чугуна, сливаемого в миксер и выливаемого из него, по средним величинам массива и величине стандартного отклонения.
ПАРАМЕТРЫ ЧУГУНА, СЛИВАЕМОГО В МИКСЕР И ВЫЛИВАЕМОГО ИЗ МИКСЕРА*
Параметр |
|
Si |
|
Mn |
|
S |
P |
|
Т, С |
Cрасч, % |
|
|
|
|
Средние |
|
|
|
|
||
Чугун, сливаемый в миксер |
|
80,75 |
|
44,56 |
|
23,73 |
78,00 |
|
1368,23 |
4,58 |
Чугун, выливаемый из миксера |
|
81,39 |
|
41,42 |
|
28,96 |
80,54 |
|
1330,56 |
4,48 |
Отклонение |
|
0,64 |
|
3,14 |
|
5,23 |
2,53 |
|
37,67 |
0,10 |
|
|
Стандартное отклонение |
|
|
|
|
||||
Чугун, сливаемый в миксер |
|
16,99 |
|
8,12 |
|
8,18 |
7,25 |
|
34,38 |
1,34 |
Чугун, выливаемый из миксера |
|
11,26 |
|
4,61 |
|
5,66 |
5,23 |
|
17,06 |
1,31 |
Отклонение |
|
5,74 |
|
3,51 |
|
2,52 |
2,03 |
|
17,31 |
0,03 |
* Концентрация углерода выражена |
в процентах, концентрации кремния и марганца в сотых долях, серы и фосфора |
|||||||||
в тысячных долях. Эти же размерности сохраняются на всех приведенных ниже рисунках. |
|
|
||||||||
Сравнение средних величин показывает, что |
Увеличение концентрации серы, вероятно, |
|||||||||
за время пребывания в миксере содержание |
связано с попаданием в миксер некоторого коли- |
|||||||||
кремния практически не изменилось, концентра- |
чества доменного шлака, что при окислительной |
|||||||||
ция марганца уменьшилась на 0,031 %, углерода |
атмосфере миксера ведет к восстановлению |
|||||||||
на 0,1 %, а концентрации серы и фосфора |
серы из шлака в металл. |
|
|
|||||||
увеличились на 0,0052 и 0,0025 % соответст- |
Снижение температуры чугуна происходит в |
|||||||||
венно. Температура чугуна снизилась на 38 С. |
|
основном за счет перелива чугуна из миксера в |
||||||||
|
|
|
|
|
заливочный ковш. Уменьшение концентрации уг- |
|||||
|
|
|
|
|
лерода в чугуне вызвано |
снижением темпера- |
||||
|
|
|
|
|
туры. |
|
|
|
|
|
Теорія металургійних процесів: |
Підручник / В.Б. Охотський, О.Л. Костьолов, В.К. Сімонов та інш. Кiев: ІЗМН. |
|||||||||
1997. 512 с. |
|
|
|
|
|
|
|
|
|
|
ОАО «Черметинформация» • Бюллетень «Черная металлургия» • 7• 2011 ―――――――――――――――― 41

После пребывания в миксере величина стандартного отклонения, которая характеризует рассеивание данных, снизилась на 30–40 %, что свидетельствует об усреднении состава чугуна в миксере.
На рис. 1 показано частотное распределение состава чугуна по кремнию, сере и температуре до и после миксера. Первый массив характеризует чугун перед заливкой в миксер, а второй при выливании из миксера.
Рис. 1. Частотные распределения состава чугуна: а по кремнию; б по сере; в по температуре (концентрация кремния выражена в сотых долях процента, серы в тысячных долях)
Распределение по кремнию показывает, что после миксера уменьшился интервал варьирования и возросла частота при среднем значении концентрации кремния. Наблюдается сдвиг максимума распределения по сере в область более высоких содержаний, а по температуре в область более низких температур. В общих случаях интервал варьирования уменьшается.
На рис. 2 показана связь между температурой доменного чугуна и температурой чугуна в заливочных ковшах, также приведены данные о разнице этих температур.
Рис. 2. Зависимость температуры чугуна в заливочных ковшах от температуры доменного чугуна
На рис. 2 приведены уравнения регрессии, характеризующие данные зависимости. В исследуемом диапазоне повышение температуры доменного чугуна на 1 С ведет к повышению температуры в заливочных ковшах на 0,3 С.
Как видно из рис. 3, наблюдается достаточно надежная связь между содержанием кремния в чугуне и его температурой. Эта зависимость определяется технологией доменного процесса, когда повышение температуры в горне печи способствует росту степени восстановления кремния.
Рис. 3. Зависимость концентрации кремния от температуры чугуна:
а сливаемого в миксер; б заливаемого в конвертер (концентрация кремния выражена в сотых долях процента)
42 ―――――――――――――――――ОАО «Черметинформация» • Бюллетень «Черная металлургия» • 7• 2011

Сравнение уравнений регрессии для доменного чугуна и чугуна после миксера показывает, что степень влияния и теснота связи между факторами в доменном чугуне ниже, чем в чугуне после миксера. Это связано с тем, что чугун в конвертерный цех поступает от нескольких доменных печей.
На рис. 4 показана связь содержания кремния с другими примесями чугуна. Уравнения регрессии представлены степенными зависимостями, которые дают более высокую тесноту связи между факторами, чем линейные.
Из рис. 4 видно, что как в доменном чугуне, так и в чугуне после миксера имеют место достаточно четкие зависимости между содержанием кремния и других примесей. Наиболее значительная между кремнием и серой.
Зависимости, которые наблюдаются в доменном чугуне, следует объяснить технологическими особенностями доменного процесса. Они остаются, несмотря на усреднение состава чугуна в миксере, но теснота связи между ними уменьшается.
Таким образом, несмотря на усреднение чугуна в миксере, сохраняются зависимости между температурой чугуна, концентрацией кремния и других примесей, определяемые технологией доменного процесса.
Рис. 4. Взаимосвязь содержания примесей в чугуне: а сливаемом в миксер; б заливаемом в конвертер (концентрация кремния и марганца выражена в сотых долях процента, серы и фосфора в тысячных долях)
Выводы
Усреднение чугуна в миксере уменьшает диапазон колебаний как состава, так и температуры чугуна, снижает дисперсию по составу и температуре, что благоприятно сказывается на стабильности работы сталеплавильных агрега-
тов. Однако следует отметить, что повышается содержание серы и снижается температура чугуна. В качестве комплексного показателя качества чугуна следует ориентироваться на концентрацию кремния.
ОАО «Черметинформация» • Бюллетень «Черная металлургия» • 7• 2011 ―――――――――――――――― 43

УДК 669.184.244.66:669.184.242 А. Г. ВЕЛИЧКО1, д.т.н.; Б. М. БОЙЧЕНКО1, д.т.н., проф.,
boichenko@metal.nmetau.edu.ua; B. C. ГРИШИН1, к.т.н.; А. В. ПОПОВ1,
А. В. ШИБКО2, к.т.н.; В. И. ПИЩИДА2, к.т.н.; В. И. ШПАК2, К. Ф. ЧМЫРКОВ2 ( 1 Национальная металлургическая академия Украины, 2 ПАО “Евраз − Днепропетровский металлургический завод им. Петровского”)
ПРИМЕНЕНИЕ В КОНВЕРТЕРАХ КИСЛОРОДНЫХ ФУРМ С ДВУХРЯДНЫМ РАСПОЛОЖЕНИЕМ СОПЕЛ
Повышение доли лома в металлошихте с соответствующим снижением расхода жидкого чугуна за счет улучшения теплового режима и шлакообразования кислородно-конвертерной плавки в значительной мере происходит при внедрении технологии дожигания газов, прежде всего окиси углерода, в кислородном конвертере [1]. В связи с этим в кислородно-конвертерном цехе ПАО “Евраз − Днепропетровский металлургический завод (ДМЗ) им. Петровского” актуальной задачей стало преобразование стандартных наконечников фурм в наконечники, используемые для дожигания отходящих газов .
Современные конструкции наконечников кислородных фурм для дожигания газов в кислородном конвертере можно разделить на две группы: с двухрядным расположением сопел основных для обезуглероживания и вспомогательных для дожигания газов, а также с двухъярусным расположением [1, 2].
Преимуществом двухрядных наконечников является то, что для их применения не требуется изменение конструкции фурмы в целом. При их использовании происходит уменьшение выбросов из конвертеров, повышается выход стали, обеспечивается повышение утилизации лома, однако затруднения с расположением вторичных сопел и недостаточное регулирование расхода вторичного кислорода приводили к излишнему нагреву некоторых участков конвертера и тем самым к снижению срока службы футеровки.
Место и эффекты реакции дожигания изменяют путем поднятия вспомогательных кисло-
В работе принимали участие Г.В. Бергеман, А.С. Заспенко, С.М. Онацкий, С.Н. Кудря, Ю.Г. Горбенко, Д.П. Васильев, М.А. Бутрименко (ПАО “Евраз − ДМЗ им. Петровского”).
родных сопел над основными. С этой целью разработаны двухъярусные фурмы с одним и разделенным потоками кислорода. В вспомогательных потоках используется до 10 % всего кислорода, поступающего в фурму. Вторичные сопла выполняются цилиндрическими. Скорость кислорода в них ограничивается таким образом, чтобы число Маха составляло 1, а расширение выходящего кислорода происходило с наружной стороны фурмы. Получающиеся ударные волны приводят к возникновению быстрого рассеяния газовой струи, это облегчает перемешивание кислорода с окисью углерода, выходящей из эмульсии стали и шлака.
Вреакции дожигания газов выделяется больше энергии, чем в главной реакции обезуглероживания, поэтому повышение степени дожигания газов с обычного уровня до повышенного приводит к увеличению общей энергии.
Ограничением применения двухъярусных фурм является существенная переделка трактов для подачи кислорода и охлаждающей воды. Специфика конструкции фурм, используемых в кислородно-конвертерном цехе ПАО “Евраз − ДМЗ им. Петровского”, не позволяет производить их переделку в двухъярусные фурмы.
Вкислородно-конвертерном цехе ПАО “Евраз − ДМЗ им. Петровского” работают три конвертера с садкой (жидкий чугун + твердая часть шихты) 67 т, футерованные достаточно теплопроводными периклазоуглеродистыми огнеупорами.
Доля твердой части металлошихты без учета раскислителей не превышает 20 % даже с учетом специально применяемых мер: прямой перелив жидкого чугуна, минуя миксер, предварительный подогрев лома, тогда как возможности теплового баланса плавки позволяют перерабатывать до 25 % твердой части шихты [2]. Это оз-
44 ―――――――――――――――――ОАО «Черметинформация» • Бюллетень «Черная металлургия» • 7• 2011

начает, что тепловые резервы плавки использу- |
строя опытного наконечника фурмы с общей |
|||||||
ются еще не в полной мере. |
|
|
стойкостью на уровне 307 плавок был проведен |
|||||
Для решения проблемы “Укрфурмет” по за- |
анализ полученных результатов в сравнении с |
|||||||
казу ПАО “Евраз − ДМЗ им. Петровского” изгото- |
плавками, продутыми штатной фурмой на кон- |
|||||||
вил экспериментальные наконечники фурм (см. |
вертере № 3 в тот же период. |
|
||||||
рисунок), которые позволят увеличить степень |
Анализ данных показывает, что эксперимен- |
|||||||
дожигания СО до СО2 в полости конвертера. |
тальная фурма обеспечивает экономию жидкого |
|||||||
|
|
|
чугуна почти на 13 кг/т стали, что свидетельст- |
|||||
|
|
|
вует о наличии эффекта дожигания. При этом |
|||||
|
|
|
резервы теплового баланса использованы не |
|||||
|
|
|
полностью: на опытных плавках использовали |
|||||
|
|
|
больше железосодержащих брикетов и извести, |
|||||
|
|
|
которые можно было бы заменить металлоло- |
|||||
|
|
|
мом. Обращает на себя внимание сокращение |
|||||
|
|
|
продолжительности продувки, а главное, повы- |
|||||
|
|
|
шение пропускной способности эксперименталь- |
|||||
|
|
|
ной фурмы по кислороду (на 20−30 м3/мин), ко- |
|||||
|
|
|
торый и расходовался на дополнительное дожи- |
|||||
|
|
|
гание СО до СО2 без увеличения степени окис- |
|||||
|
|
|
ленности шлака. |
|
|
|
||
|
|
|
Особый интерес в ходе исследования вы- |
|||||
|
|
|
звала служба футеровки. Принято считать, что |
|||||
|
|
|
дожигание СО до СО2 на этот показатель оказы- |
|||||
|
|
|
вает отрицательное влияние [3]. В данном слу- |
|||||
|
|
|
чае снижения стойкости футеровки не про- |
|||||
|
|
|
изошло. Замеры остаточной толщины рабочего |
|||||
Конструкция двухрядного наконечника кислородной |
слоя |
футеровки |
после |
окончания кампании |
||||
опытной фурмы показали скорость износа 0,33 |
||||||||
фурмы “Укрфурмет” |
|
|||||||
|
мм/плавку. Такая скорость износа вполне удов- |
|||||||
|
|
|
||||||
Основные характеристики |
эксперименталь- |
летворительна и обеспечивает выполнение га- |
||||||
ного наконечника фурмы изготовления “Укрфур- |
рантийной стойкости. |
|
|
|||||
мет” следующие: |
|
|
Остальные показатели опытных и сравни- |
|||||
Число основных сопел |
|
4 |
тельных плавок почти не отличались. Отклоне- |
|||||
|
ний от технологии в процессе продувки плавок |
|||||||
Критический диаметр, мм |
|
31 |
||||||
|
экспериментальным наконечником не наблюда- |
|||||||
Угол наклона к вертикали, град. |
|
16 |
||||||
Число вспомогательных сопел |
|
8 |
лось (выносы, выбросы, заметалливания фурмы |
|||||
Диаметр, мм |
|
8 |
и т. п.) |
|
|
|
|
|
Угол наклона вспомогательных сопел к |
На |
основании |
первого |
этапа исследования |
||||
вертикали, град. |
|
30 |
||||||
|
было принято решение о целесообразности |
|||||||
|
|
|
||||||
Сопла расположены в два ряда: внутренний |
применения фурм данной конструкции в даль- |
|||||||
ряд основные, наружный |
ряд |
— вспомога- |
нейшем. |
|
|
|
||
тельные. Оба ряда сопел питались кислородом |
На втором этапе исследования было прове- |
|||||||
дено |
еще четыре кампании с применением |
|||||||
из одного тракта. |
|
|
опытных наконечников фурм на различных |
|||||
В штатном наконечнике число сопел 5, их |
||||||||
критический диаметр 23 мм, угол наклона к вер- |
конвертерах. Стойкость наконечников фурм |
|||||||
тикали 12 град. Все сопла расположены в один |
колебалась от 137 до 404 плавок. |
|
||||||
ряд. |
|
|
С начала февраля до 1 июня 2010 г. с ис- |
|||||
|
|
пользованием пяти фурм проведено 1032 |
||||||
Первая опытная фурма была поставлена |
||||||||
7.12.09 г. на конвертер № 2 на 137-й плавке от |
плавки, их средняя стойкость составила 283 |
|||||||
начала кампании по футеровке. |
По выходу из |
плавки, что ниже, чем стойкость штатных нако- |
||||||
|
|
|
нечников, и объясняется сложностью конструк- |
|||||
ОАО «Черметинформация» • Бюллетень «Черная металлургия» • 7• 2011 ―――――――――――――――― |
45 |
ции опытных наконечников. При этом следует |
чугуна 921,77 кг/т стали на сравнительных |
отметить, что стойкость опытных наконечников |
плавках средний фактический расход чугуна на |
на ПАО “Евраз − ДМЗ им. Петровского” |
плавках с одноконтурными двухрядными |
находится на уровне стойкости обычных, |
фурмами составил 914,67 кг/т стали. Снижение |
используемых на других заводах, и для ее |
расхода чугуна при использовании опытных |
повышения имеются резервы. На этих 1133 |
фурм достигло 7,1 кг/т стали. |
плавках при среднем фактическом расходе |
|
Выводы |
|
1. Показана возможность применения одно- |
2. Определено, что даже при относительно |
контурных двухрядных фурм для продувки стали |
низкой стойкости фурм на уровне 283 плавок |
в конвертерах с обеспечением экономии чугуна в |
эффективность их применения очевидна и не |
количестве 7−13 кг/т стали, что соответствует |
приводит к существенным задержкам технологи- |
увеличению степени дожигания СО до СО2 в от- |
ческого процесса. |
ходящих газах на 4 %. |
3. Увеличения износа футеровки конвертеров |
|
не выявлено. |
БИБЛИОГРАФИЧЕСКИЙ СПИСОК
1.Petrushka R., Manley S. Improvement in Oxygen Lance Life // Steelmaking Conference Proceedings. 2000. Р. 245−250.
2.Баптизманский В. И., Бойченко Б. М., Черевко Д. П. Тепловая работа кислородных конвертеров. М.: Металлургия. 1988. 174 с.
3.Бойченко Б. М., Охотский В. Б., Харлашин П. С. Конвертерное производство стали. Днепропетровск: Днепро-
ВАЛ. 2006. 454 с.
УДК 669.18:669.17.046.001.5 |
С. И. СЕМЫКИН, к.т.н.; В. Ф. ПОЛЯКОВ, д.т.н., проф.; |
|
Е. В. СЕМЫКИНА, Т. С. КИЯШКО |
|
(Институт черной металлургии им. З.И. Некрасова |
|
Национальной академии наук Украины) |
ИССЛЕДОВАНИЕОСОБЕННОСТЕЙРАФИНИРОВАНИЯ ЖЕЛЕЗОУГЛЕРОДИСТОГОРАСПЛАВАПРИНАЛОЖЕНИИ НИЗКОВОЛЬТНОГОЭЛЕКТРИЧЕСКОГОПОТЕНЦИАЛА
В связи с постоянным повышением требований к качеству металлопродукции рафинирование металла с целью снижения содержания вредных примесей стало неотъемлемым элементом современного металлургического производства. Оно реализуется в основном в сталеплавильном переделе как непосредственно в агрегатах, так и в сталеразливочных ковшах. Институтом черной металлургии им. З.И. Некрасова (ИЧМ) Национальной академии наук (НАН)
Украины разработан предназначенный для промышленного использования способ воздействия на железоуглеродистый расплав путем наложения низковольтного электрического потенциала. Его основное предназначение состоит в ресурсо- и энергосбережении, что проявляется в увеличении выхода жидкой стали, сокращении расхода кислорода, извести, раскислителей и других материалов, а также в повышении теплосодержания расплава к
46 ―――――――――――――――――ОАО «Черметинформация» • Бюллетень «Черная металлургия» • 7• 2011
моменту выпуска. Как показали промышленные |
пользовали оборотный |
шлак |
конвертерной |
|||
испытания, этот способ оказывает также |
плавки в количестве 40−50 кг/т. Количество |
|||||
положительное влияние на снижение вредных |
шлака в обоих случаях определяли из условий |
|||||
примесей в металле, причем этот эффект |
изоляции зеркала расплава, которые зависят от |
|||||
проявляется как при производстве стали в |
интенсивности продувки. Обработку металла в |
|||||
конвертерах, так и при ее внепечной обработке в |
сталеразливочном ковше осуществляли по сле- |
|||||
сталеразливочных ковшах. |
|
дующим вариантам: |
|
|
||
В настоящей статье описываются результаты |
1. Без электрических воздействий. |
|||||
исследования особенностей влияния электриче- |
2. С подведением к продувочной фурме тока |
|||||
ского потенциала при рафинировании металла в |
отрицательной полярности. |
|
||||
металлоразливочных емкостях. |
|
3. С подведением к продувочной фурме тока |
||||
Цель исследования состоит в дополнитель- |
положительной полярности. |
|
||||
ной оценке влияния условий использования |
В случае обработки в конвертере число ис- |
|||||
электрического потенциала на степень измене- |
следуемых вариантов увеличилось в связи с |
|||||
ния содержания основных примесей (сера, фос- |
тем, что обработке в сталеразливочном ковше |
|||||
фор) и в уточнении механизма исследуемого |
подвергался металл, полученный традиционным |
|||||
воздействия. Для обычной практики содержание |
способом, а в конвертере дополнительно иссле- |
|||||
и возможности соответствующих операций ши- |
довалось влияние наследственности предыду- |
|||||
роко описаны в технической литературе. |
|
щих опытов. Металл в конвертере выплавляли |
||||
Были выполнены эксперименты в лаборатор- |
по трем вариантам: |
|
|
|||
ных условиях ИЧМ НАН Украины, в том числе на |
1. Без электрических воздействий. |
|||||
0,3-т конвертере, оборудованном устройством |
2. С подведением к фурме тока отрицатель- |
|||||
для замены технологических газов (кислорода на |
ной полярности. |
|
|
|||
азот), и на сталеразливочном ковше, оснащен- |
3. С подведением к фурме тока положитель- |
|||||
ных системами наложения низковольтных элек- |
ной полярности. |
|
|
|||
трических потенциалов. |
|
Дальнейшую обработку металла вели сле- |
||||
Во всех изучаемых |
вариантах исследования, |
дующим образом: металл, выплавляемый без |
||||
как в конвертере, так и в ковше, обработке под- |
электрических воздействий, в дальнейшем так |
|||||
вергли примерно одинаковое количество метал- |
же при отсутствии воздействия продували |
|||||
лического расплава. В первом случае металл |
струями азота, а металл, полученный при элек- |
|||||
предварительно продували кислородом (интен- |
трических воздействиях, |
обрабатывали по че- |
||||
сивность его подачи была соизмеримой с интен- |
тырем вариантам: |
|
|
|||
сивностью последующей подачи азота). Во вто- |
2.2. На фурме как при выплавке, так и при |
|||||
ром металл предварительно расплавляли в |
азотной продувке использовали отрицательную |
|||||
0,4-т индукционной печи, после чего его перели- |
полярность тока. |
|
|
|||
вали в специально подготовленный сталеразли- |
2.3. На фурме при выплавке использовали |
|||||
вочный ковш, на днище которого перед сливом |
отрицательную полярность тока, а при азотной |
|||||
металла присаживали твердые материалы, ис- |
обработке положительную. |
|
||||
пользуемые в качестве покровного шлака. |
|
3.2. На фурме при выплавке использовали |
||||
В обоих агрегатах азотом продували сверху с |
положительную полярность тока, а при азотной |
|||||
интенсивностью |
подачи в конвертере 1,5−2,0 |
обработке отрицательную. |
|
|||
м3/т в минуту, в ковше 0,1−0,2 м3/т в минуту. |
3.3. На фурме как при выплавке, так и при |
|||||
Обработку металла азотом в конвертере про- |
азотной продувке применяли |
положительную |
||||
изводили под шлаком, полученным при окисли- |
полярность тока. |
|
|
|||
тельной плавке. |
Его |
масса составляла |
80− |
Химический состав обрабатываемого металла и |
||
90 кг/т. С целью сопоставимости результатов в |
конвертерных шлаков указанв табл. 1 и2. |
|||||
ковше в качестве рафинирующего покрытия |
ис- |
|
|
|
ОАО «Черметинформация» • Бюллетень «Черная металлургия» • 7• 2011 ―――――――――――――――― 47
ТАБЛИЦА 1. РЕЗУЛЬТАТЫ ИССЛЕДОВАНИЙ ПРИ ОБРАБОТКЕ МЕТАЛЛА В КОНВЕРТЕРЕ
Параметр |
|
Варианты исследования |
|
|||
1 |
2.2 |
2.3 |
3.2 |
3.3 |
||
|
||||||
Число плавок |
8 |
5 |
4 |
6 |
5 |
|
Химический состав металла, %: |
|
|
|
|
|
|
до обработки азотом: |
|
|
|
|
|
|
углерод |
0,040 |
0,045 |
0,036 |
0,037 |
0,039 |
|
марганец |
0,060 |
0,071 |
0,065 |
0,110 |
0,110 |
|
сера |
0,032 |
0,030 |
0,031 |
0,021 |
0,028 |
|
фосфор |
0,023 |
0,023 |
0,021 |
0,024 |
0,021 |
|
после обработки: |
|
|
|
|
|
|
углерод |
0,036 |
0,040 |
0,034 |
0,037 |
0,035 |
|
марганец |
0,045 |
0,057 |
0,065 |
0,062 |
0,084 |
|
сера |
0,033 |
0,032 |
0,027 |
0,022 |
0,025 |
|
фосфор |
0,019 |
0,015 |
0,017 |
0,016 |
0,017 |
|
Изменение содержания элементов в металле |
|
|
|
|
|
|
за период обработки, %: |
|
|
|
|
|
|
углерод |
−0,004 |
−0,005 |
−0,002 |
|
−0,004 |
|
марганец |
−0,015 |
−0,014 |
|
−0,048 |
−0,026 |
|
сера |
+0,001 |
+0,002 |
−0,004 |
+0,001 |
−0,003 |
|
фосфор |
−0,004 |
−0,008 |
−0,004 |
−0,008 |
−0,004 |
|
Степеньокисленияэлементовзапериодобработки, %: |
|
|
|
|
|
|
углерод |
10,00 |
11,11 |
5,56 |
0 |
10,26 |
|
марганец |
25,00 |
19,72 |
0 |
43,64 |
23,64 |
|
сера |
−3,1 |
−6,7 |
+12,9 |
−4,8 |
+10,7 |
|
фосфор |
17,4 |
34,8 |
19,0 |
33,3 |
19,0 |
|
Температура металла, °С: |
|
|
|
|
|
|
до обработки |
1640 |
1640 |
1650 |
1680 |
1680 |
|
после обработки |
1540 |
1560 |
1590 |
1610 |
1540 |
|
Снижениетемпературызавремяпродувкиазотом, оС |
100 |
80 |
60 |
70 |
60 |
|
Параметры шлака, %: |
|
|
|
|
|
|
до обработки: |
|
|
|
|
|
|
основность |
2,68 |
2,77 |
3,00 |
3,40 |
3,31 |
|
FeOобщ |
19,2 |
16,2 |
17,3 |
20,2 |
21,3 |
|
S |
0,062 |
0,053 |
0,068 |
0,098 |
0,115 |
|
P2O5 |
1,25 |
1,87 |
1,54 |
1,20 |
1,03 |
|
LS, ед. |
1,94 |
1,77 |
2,19 |
4,67 |
4,11 |
|
LP, ед. |
54,35 |
81,30 |
73,33 |
50,00 |
49,05 |
|
после обработки: |
|
|
|
|
|
|
основность |
2,54 |
2,50 |
3,28 |
3,17 |
3,30 |
|
FeOобщ |
19,4 |
17,2 |
16,8 |
22,6 |
18,8 |
|
|
|
|
(−2,4) |
(+3,2) |
|
|
S |
0,038 |
0,037 |
0,081 |
0,058 |
0,110 |
|
P2O5 |
1,41 |
2,77 |
1,81 |
1,94 |
1,67 |
|
LS, ед. |
1,15 |
1,16 |
3,00 |
2,64 |
4,40 |
|
LP, ед. |
74,21 |
184,67 |
106,47 |
121,25 |
98,24 |
|
Изменениепараметровшлаказапериодобработки, %: |
|
|
|
|
|
|
основность |
−0,14 |
−0,27 |
+0,28 |
−0,27 |
0 |
|
FeOобщ |
+0,20 |
+1,0 |
−0,5 |
+2,4 |
−2,5 |
|
S |
−0,024 |
0,016 |
+0,013 |
−0,040 |
−0,005 |
|
P2O5 |
+0,16 |
+0,90 |
+0,27 |
+0,74 |
+0,64 |
|
LS, ед. |
−0,79 |
−0,61 |
+0,81 |
−2,03 |
+0,29 |
|
LP, ед. |
+19,86 |
+103,37 |
+33,14 |
+71,25 |
+49,19 |
48 ―――――――――――――――――ОАО «Черметинформация» • Бюллетень «Черная металлургия» • 7• 2011
ТАБЛИЦА 2. РЕЗУЛЬТАТЫ ИССЛЕДОВАНИЙ ПРИ ОБРАБОТКЕ МЕТАЛЛА АЗОТНЫМИ СТРУЯМИ В 0,5-т СТАЛЕРАЗЛИВОЧНОМ КОВШЕ (В КАЧЕСТВЕ ПОКРОВНОГО ОБОРОТНЫЙ
КОНВЕРТЕРНЫЙ ШЛАК)
Параметр |
|
Варианты исследования |
|
||
|
1 |
2 |
3 |
|
|
|
|
|
|||
Число продувок |
|
3 |
4 |
4 |
|
Химический состав металла, %: |
|
|
|
|
|
до обработки: |
|
|
|
|
|
углерод |
|
0,23 |
0,26 |
0,25 |
|
кремний |
|
0,32 |
0,39 |
0,42 |
|
марганец |
|
0,40 |
0,39 |
0,36 |
|
сера |
|
0,029 |
0,026 |
0,026 |
|
фосфор |
|
0,053 |
0,056 |
0,053 |
|
после обработки: |
|
|
|
|
|
углерод |
|
0,24 |
0,27 |
0,21 |
|
кремний |
|
0,25 |
0,30 |
0,30 |
|
марганец |
|
0,30 |
0,34 |
0,31 |
|
сера |
|
0,031 |
0,027 |
0,025 |
|
фосфор |
|
0,054 |
0,054 |
0,054 |
|
Усредненные параметры шлака до обработки, %: |
|
|
|
|
|
CaO |
|
42,0 |
42,0 |
42,0 |
|
SiO2 |
|
23,7 |
23,7 |
23,7 |
|
MgO |
|
8,5 |
8,5 |
8,5 |
|
FeO |
|
13 |
13 |
13 |
|
основность шлака |
|
1,77 |
1,77 |
1,77 |
|
Изменение содержания элементов за обработку, %: |
|
|
|
|
|
углерода |
|
−4,4 |
−3,8 |
+16,0 |
|
кремния |
|
+21,8 |
+23,0 |
+9,5 |
|
марганца |
|
+25,0 |
+17,9 |
+13,7 |
|
серы |
|
−6,9 |
−3,9 |
+3,8 |
|
фосфора |
|
−2,1 |
+3,6 |
−1,9 |
|
Степень окисления примесей за обработку, %: |
|
|
|
|
|
dC |
|
+4,35 |
+3,85 |
+16,00 |
|
dSi |
|
+21,2 |
+23,1 |
+28,6 |
|
dMn |
|
+25,00 |
+12,82 |
+13,89 |
|
dS |
|
−6,90 |
−3,85 |
+3,85 |
|
dР |
|
−1,89 |
+3,57 |
−1,89 |
|
Температура металла, °С: |
|
|
|
|
|
до обработки |
|
1560 |
1570 |
1550 |
|
после обработки |
|
1530 |
1552 |
1530 |
|
Снижение температуры за время обработки, °С |
|
30 |
18 |
20 |
|
Анализ результатов по влиянию электриче- |
повышению уровня |
остаточного |
содержания |
||
ского потенциала во время продувки его азот- |
марганца при некотором возврате части серы из |
||||
ными струями в конвертере после окислитель- |
шлака в металл. В варианте с подводом к фурме |
||||
ного периода (см. табл. 1) показал в ряде слу- |
тока положительной полярности при подаче |
||||
чаев схожие результаты с обработкой металла |
обоих газов отмечается самая низкая скорость |
||||
азотом в ковше (см. табл. 2). В то же время дан- |
охлаждения металла при высокой скорости его |
||||
ные, полученные при выплавке в конвертере, |
десульфурации и некоторое ухудшение про- |
||||
указывают на ряд существенных различий. В |
цесса дефосфорации. |
|
|
|
|
опытах с замещением кислорода на азот на за- |
Положительная полярность тока на этапе |
||||
ключительной стадии обработки металла харак- |
азотной продувки, сменяющая отрицательную |
||||
тер воздействия и величина достигаемого эф- |
полярность тока при кислородной продувке, от- |
||||
фекта зависели не только от полярности тока на |
личалась наиболее высокой степенью десуль- |
||||
фурме, но и от параметров шлакометаллической |
фурации металла и самой низкой степенью |
||||
системы, сформированной к моменту начала об- |
окисления марганца из металла. При этом ско- |
||||
работки азотом. Подвод к фурме тока отрица- |
рость охлаждения ванны была достаточно низ- |
||||
тельной полярности как во время кислородной |
кой. Вариант подвода отрицательной полярности |
||||
продувки, так и при подаче азота способствовал |
во время азотной продувки, сменяющей положи- |
||||
существенному удалению фосфора из металла, |
тельную полярность, отличался достаточно вы- |
||||
ОАО «Черметинформация» • Бюллетень «Черная металлургия» • 7• 2011 ―――――――――――――――― |
49 |
сокой степенью дефосфорации с весьма незначительным восстановлением серы из шлака. Это связано прежде всего с более высоким уровнем основности шлака, сформированного за время кислородной продувки при положительной полярности.
Анализ изменения параметров покровного шлака (его химического состава, основности и коэффициентов распределения серы и фосфора между шлаком и металлом) за период продувки азотом соответствует тенденциям поведения изучаемых элементов в металлическом расплаве при воздействии той или иной полярности
(см. табл. 1 и 2).
За время кислородной продувки ток положительной полярности способствовал увеличению содержания окислов железа в шлаке по сравнению с продувками без электрического потенциала, а ток отрицательной полярности приводил к снижению этого показателя.
Последующая продувка сформированного шлакометаллического расплава азотом при положительной полярности снижала содержание окислов железа в шлаке, а при отрицательной полярности увеличивала.
Содержание серы в шлаке в период кислородной продувки на плавках с положительной полярностью отличалось более высокими значениями (0,098−0,115 %) по сравнению с контрольными продувками (0,062 %). Последующая продувка азотом при той же полярности приводила к дальнейшему повышению концентрации серы в шлаке и, как результат, к снижению содержания серы в металле.
Коэффициент распределения серы между металлом и шлаком LS, определенный отношением (S)/[S], под воздействием положительной полярности увеличивался в 1,5−2,4 раза при кислородной продувке и более значимо при азотной обработке в 2,6−3,8 раза по сравнению с обработкой без электрических воздействий.
Коэффициент распределения фосфора между металлом и шлаком LР, определенный отношением (Р2О5)/[Р], при обработке металла азотом также увеличивался более значимо, чем при кислородной продувке, в 1,6−2,4 раза против 1,3−1,5 раза при окислительной продувке, однако данное существенное увеличение отмечено только при подведении отрицательной полярности потенциала.
Наибольший уровень содержания окислов железа в конечных шлаках как при кислородной, так и при азотной продувке получен при отрицательной полярности, а наименьший при положительной (см. табл. 1). Повышение основности шлака под воздействием электрического потенциала вызвано направленным перемещением заряженных компонентов шлакового расплава под действием градиента электрических сил, на-
пример окислов кальция к положительному полюсу, за счет чего увеличивается полнота ассимиляции частиц извести в шлаковом расплаве. Этому же способствуют более высокие температурные условия, реализуемые при этой полярности тока.
Характерным отличием всех вариантов конвертерной плавки с электрическим воздействием, при котором осуществляется подача азота вместо кислорода, является то, что в первый период температура расплава повышается, а при перемешивании ванны азотными струями заметно снижается. Данное обстоятельство способствует удалению фосфора из металла вследствие более низкой температуры и ухудшает условия протекания реакции удаления серы. Как и следовало ожидать, в опытах без электрических воздействий продувка ванны азотом несколько углубляет процесс дефосфорации с одновременно протекающим процессом ресульфурации металла. В этом отношении подвод положительной полярности следует рассматривать как более рациональное воздействие, при котором значительно активизируется процесс удаления серы (от ресульфурации к десульфурации) с сохранением положительного влияния на процесс дефосфорации за счет перемешивания.
Улучшение процесса десульфурации при подведении тока положительной полярности при продувке ванны азотом происходит, во-пер- вых, за счет непосредственного влияния электричества на заряженные ионы металла и шлака, что позволяет увеличить поток отрицательно заряженных ионов, в том числе серы, от металла к шлаку, во-вторых, вследствие развития процесса прямого выгорания серы по реакции
(S2−) + {O2} = {SO2} + 2e.
В противоположность сере фосфор переходит в шлаковый расплав, связываясь с атомами кислорода по реакции
[Fe2P] + (O2−) = 2[Fe] + ( РО34− )+ 5e.
При этом варианте ликвидацию непрерывного накопления электронов в электрическом расплаве, вероятно, обеспечивает компенсационный возврат в металл ионов железа из его окислов. В обычном процессе дефосфорация стали не получает полноты своего развития вследствие большой энергии связи между ионами железа и кислорода в соединении (FeO). В опытах с наложением отрицательного полюса на контактный электрод, а следовательно и на шлаковый расплав, а на металлическую ванну положительного полюса источника тока происходит отвод избытка электронов, что облегчает процесс перехода фосфора в шлак.
50 ―――――――――――――――――ОАО «Черметинформация» • Бюллетень «Черная металлургия» • 7• 2011
Понимание возможной причины и механизма |
Таким образом, анализ экспериментов на 0,3-т |
влияния низковольтных потенциалов на тепло- |
лабораторном конвертере и опытном 0,5-т ста- |
вую сторону процесса в условиях продувки азо- |
леразливочном ковше показал возможность су- |
том следует рассматривать через влияние по- |
щественного улучшения тепловых и рафиниро- |
тенциала (прежде всего это относится к положи- |
вочных процессов за счет электрической энергии |
тельной полярности) на активизацию процесса |
при подводе низковольтных потенциалов как при |
выгорания углерода из расплава. При этом про- |
дополнительном перемешивании металличе- |
слеживается прямая связь между снижением |
ского и шлакового расплава инертными струями |
степени охлаждения металла и глубиной обезуг- |
в конвертере, так и при внепечной обработке ме- |
лероживания металла. |
талла. |
Выводы
Влияние электрического потенциала имеет схожий характер как при окислительной продувке, так и при подаче нейтрального газа.
Уровень влияния электрического воздействия в конвертере выше, чем в сталеразливочном ковше, но для получения максимального эффекта целесообразным является комплексное применение воздействия в обоих случаях.
Результаты, полученные при конвертерной плавке с различным составом шлака и началом азотной продувки, подтверждают ранее высказанное заключение о целесообразности повы-
шения эффективности использования электрического потенциала при внепечной обработке стали за счет целенаправленной корректировки состава покровного шлака в ковше.
Сопоставление температурных показателей при электрическом воздействии на расплав в конвертере и сталеразливочном ковше свидетельствует о том, что одним из источников повышения теплосодержания металла, в частности при обработке в ковше, является частичное окисление углерода.
УДК 669.18:553.694.6 |
П. С. ХАРЛАШИН, А. Б. КОВУРА, Р. Д. КУЗЕМКО |
|
(ГВУЗ “Приазовский государственный технический университет”) |
МОДЕЛЬ РАСЧЕТА ТЕРМОГАЗОДИНАМИЧЕСКИХ ПАРАМЕТРОВ СТРУИ ПРИ РАЗДУВЕ ШЛАКА В КОНВЕРТЕРЕ
Освоение технологии раздува конечного |
ряется, но значительная часть этой, уже |
|
шлака в кислородном конвертере приводит к ра- |
располагаемой на срезе сопла кинетической |
|
дикальному повышению стойкости футеровки [1]. |
энергии не доносится до расплава шлака. Из-за |
|
Мировые тенденции общеизвестны рекордная |
диссипативных процессов в прямых скачках |
|
стойкость футеровки уже достигает 20−30 тыс. |
уплотнения и ударных волнах, а также присоеди- |
|
плавок, а в конвертерных цехах металлургиче- |
нения газа из полости конвертера часть |
|
ских комбинатов Украины она составляет ~4 тыс. |
механической энергии струи теряется. По этой |
|
плавок. Существуют проблемы, сдерживающие |
причине кинетическая энергия струи при встрече |
|
рост стойкости футеровки. Качество нанесения |
со шлаковым расплавом существенно ниже, чем |
|
защитного гарнисажа существенно зависит и от |
на срезе сопла. Энергия струи, передаваемая |
|
начальной, подведенной к шлаковому расплаву |
шлаку, зависит главным образом от того, сколько |
|
энергии. Например, при скорости истечения из |
струя на расстоянии x присоединит газа (и |
|
сопла w1 = 500 м/с и расходе через сопло при |
шлака) из окружающей среды. Не моделируя эти |
|
нормальных условиях Vн = 210 м3/мин (350-т кон- |
процессы, внедрить с высокой эффективностью |
|
вертер) мощность одной из пяти азотных струй |
и в короткое время такую передовую ресурсо- |
|
на срезе сопла составляет ~550 кВт. Ради дос- |
сберегающую технологию, как ошлаковка |
|
тижения высоких значений мощности истекаю- |
футеровки конвертера, затруднительно. |
|
щего потока азот в сверхзвуковых соплах уско- |
|
|
ОАО «Черметинформация» • Бюллетень «Черная металлургия» • 7• 2011 ―――――――――――――――― |
51 |

Принятые обозначения: m массовый рас-
ход; g = mг/m1 |
присоединенная масса; g = |
= m1/(m1 + mг), |
gг = mг/(m1 + mг) концентрация |
истекающего из сопла азота и газа из полости
конвертера; Vн объемный расход; а, акр местная скорость звука и критическая скорость; Т термодинамическая температура; р абсолютное давление; θ = Тг/То относительная температура; ρ плотность; w средняя скорость в произвольном сечении струи; М = w/a число Маха; λ = w/aкр приведенная скорость; Т1/То = τ(λ) газодинамическая функция температуры; n = p1/pг степень
нерасчетности истекающей |
струи; |
k = |
ср/сv |
||||
показатель адиабаты; C = |
|
− |
k −1 |
M |
2 |
−1 |
|
1− 1 |
2 |
|
|
|
|||
|
|
|
|
|
|
|
число Крокко; β коэффициент количества движения; α коэффициент кинетической
энергии; F площадь сечения; ϑ0 начальный
угол наклона границы сверхзвуковой струи; х
длина струи в диаметрах критического сечения
dкр.
Индексы обозначают параметры: о торможения; 1 на срезе сопла; кр в критическом сечении; х в произвольном сечении истекающей струи; i на границе струи; г газа в полости конвертера; н при нормальных физических условиях.
Цель настоящей работы установить влияние относительной температуры θ, температуры азота перед соплом tо и в полости конвертера tг, расхода через сопло Vн на величину присоединенной массы g, на осредненные значения скорости wх и температуры tх в произвольном сечении х сверхзвуковой нерасчетной струи до встречи ее со шлаковым расплавом в полости конвертера.
Расчетная модель
Исследование закономерностей присоединения газа из полости конвертера в истекающую из сопел фурмы нереагирующую сверхзвуковую струю главный вопрос в теории взаимодействия этой струи со шлаковым расплавом. Ее разработка усложняется тем, что режим истечения нестационарный, так как невозможно поддержать неизменным давление азота перед фурмой с соплами постоянного сечения. Например, в кислородно-конвертерном цехе металлургического комбината “Азовсталь” за 4−7 мин продувки азотом давление изменяется в диапазоне р = 1,8–1,0 МПа. При этих условиях истекающие струи будут только нерасчетными недорасширенными или перерасширенными. Газодинамическая структура таких сверхзвуковых струй известна: течение будет сопровождаться периодическим расширением и сжатием (рис. 1). В струе образуется серия взаимодействующих между собой прямых и косых скачков уплотнения. В работе [2] учтены внутриструйные процессы, влияющие на эффективность турбулентного переноса на границе с газом в полости конвертера. Схема расчета основана на существовании идеальной границы, через которую в струю проникает газ окружающей среды. Начальный угол наклона границы сверхзвуковой струи определяли по формуле
|
ϑ0 = ω(Mi) − ω(M1) + α, |
(1) |
|||
где функция |
|
|
|
|
|
ω(M )= |
k +1arc tg |
k −1 |
(M 2 |
−1) −arc tg |
M 2 −1 . (2) |
|
k −1 |
k +1 |
|
|
|
Рис. 1. Мгновенная картина распределения волн возмущения в сверхзвуковой части нерасчетной воздушной струи, истекающей в атмосферу.
Абсолютное давление ро = 1 МПа, диаметр в критическом сечении сопла Лаваля dкр = 4,2 мм
Максимальный радиус первой бочки нерас-
|
|
|
|
|
ϑ |
1/ 2 |
||
четной струи составляет |
r max |
+ |
||||||
= 1 |
0 |
|
, где |
|||||
|
|
|
|
|
ψ |
|
|
функция Прандтля−Майера
52 ―――――――――――――――――ОАО «Черметинформация» • Бюллетень «Черная металлургия» • 7• 2011

|
|
ψ |
= |
|
|
|
|
1 |
|
|
|
|
|
|
q (Mi |
) |
. |
|
|
|
|
|
(3) |
входа в шлаковый расплав, и запишем для него |
|||||||||||||||
|
|
|
|
|
|
|
|
|
|
|
|
|
|
|
|
|
|
|
|
|
|
|
закон постоянства количества движения: |
|
|||||||||||||||
|
|
|
|
|
|
|
|
1/ 2 |
|
|
q (M1 ) |
|
|
|
|
|
|
||||||||||||||||||||||
|
|
|
|
|
(Mi2 |
− |
1) |
|
|
|
|
|
|
|
|
|
|
|
F1 ( p1 − pг ) +βρ1w12 F1 |
= ∫ρw2 dF + ∫( p − pг )dF. |
(9) |
||||||||||||||||||
Газодинамическая |
функция |
|
|
расхода, |
|
выра- |
|
|
|
|
F |
|
F |
|
|
||||||||||||||||||||||||
|
|
|
Коэффициенты, характеризующие неравно- |
||||||||||||||||||||||||||||||||||||
женная через число Маха М1, представляется как |
|||||||||||||||||||||||||||||||||||||||
мерность распределения количества движения β |
|||||||||||||||||||||||||||||||||||||||
|
k +1 |
|
|
k + 1 |
|
|
|
|
|
|
k −1 |
|
|
|
− |
k |
+ 1 |
|
|
|
и кинетической энергии α по сечению сверхзву- |
||||||||||||||||||
|
2(k |
− 1) |
|
|
|
+ |
|
|
|
2 |
2(k |
− 1) |
|
. |
(4) |
ковой струи, находят как |
|
|
|
|
|
||||||||||||||||||
q(M1 ) = |
2 |
|
|
|
|
|
M1 1 |
2 |
|
M1 |
|
|
|
|
|
|
|
|
|
|
|
|
|
||||||||||||||||
|
|
|
|
|
|
|
|
|
|
|
|
|
|
|
|
|
|
|
|
|
β = ∫w2dF / (wcp2 F) ; |
|
|
α = ∫w3dF / (wcp3 F) . |
|
||||||||||||||
Присоединенная масса определяется форму- |
|
|
|
||||||||||||||||||||||||||||||||||||
F |
|
|
|
|
|
F |
|
|
|||||||||||||||||||||||||||||||
лой |
|
|
|
|
|
|
|
|
|
|
|
|
|
|
|
|
|
|
|
|
|
|
|
|
|
|
|
|
После интегрирования правой части уравне- |
||||||||||
|
|
|
|
|
|
|
g = mг/m1 , |
|
|
|
|
|
|
|
|
(5) |
ние (9) представляется в виде |
|
|
||||||||||||||||||||
где расход через сопло m1 = ρ1w1F1. |
|
|
|
|
|
|
F1 ( p1 − pг ) +βρ1w12 F1 |
= ρхwx2 Fx +(px − pг )Fx . |
(10) |
||||||||||||||||||||||||||||||
В настоящей работе присоединенную массу g |
Из уравнения (10) среднемассовую скорость |
||||||||||||||||||||||||||||||||||||||
рассчитывали по соотношению |
|
|
|
|
|
|
|
|
|
||||||||||||||||||||||||||||||
|
|
|
|
|
|
|
|
|
|
|
|
|
|
|
|
|
|
|
|
|
|
|
|
|
|
|
|
|
струи на расстоянии х от среза сопла в сечении, |
||||||||||
|
g = 2rmax x |
Ci (1 |
|
|
1/2 |
|
(I1R − I2R ), |
|
|
|
|
где статическое давление рх уравнивается с ат- |
|||||||||||||||||||||||||||
|
−Ci2 ) |
|
|
|
|
|
|
(6) |
мосферным рг, рассчитывали по формуле |
|
|||||||||||||||||||||||||||||
|
|
Dσ |
|
|
|
|
|
|
|
|
|
|
|
|
|
|
|
|
|
|
|
|
|
|
|
|
|
|
|
|
|
|
|
|
|
|
|||
где |
D = |
(k −1/ 2)M1n |
k |
+ 1 |
|
|
|
|
|
|
параметр, |
|
|
рг (n −1) |
|
|
|
1 |
|
|
|
||||||||||||||||||
2k |
|
|
|
|
|
|
|
|
w = |
+βw |
|
, |
(11) |
||||||||||||||||||||||||||
|
|
|
|
|
|
|
|
|
|
|
|
|
(1+ g )β |
||||||||||||||||||||||||||
связывающий число Маха М1 |
|
и степень |
x |
|
ρ w |
1 |
|
|
|||||||||||||||||||||||||||||||
|
|
|
1 1 |
|
|
|
|
|
|
|
|||||||||||||||||||||||||||||
нерасчетности n, рассчитанную по условию |
где скорость истечения из сопла w1 = λ1акр. Ско- |
||||||||||||||||||||||||||||||||||||||
среза сопла. |
|
|
|
|
|
|
|
|
|
|
|
|
|
|
|
|
|
|
|
|
|
|
|
|
|
|
рость λ1 находили, используя газодинамическую |
||||||||||||
Параметр подобия |
|
|
|
|
|
|
|
|
|
|
|
|
|
|
|
|
|
|
|
||||||||||||||||||||
|
|
|
|
|
|
|
|
|
|
|
|
|
|
|
|
|
|
|
функцию расхода q(λ1) = Fкр/F1, которая из- |
||||||||||||||||||||
|
|
|
|
|
|
σ = 12 + 2,58Мi |
|
|
|
|
|
|
|
|
(7) |
||||||||||||||||||||||||
|
|
|
|
|
|
|
|
|
|
|
|
|
|
вестна, так как диаметры dкр и d1 задавали. При- |
|||||||||||||||||||||||||
характеризует степень турбулентности струи. |
нимали, что рг = 0,1 МПа. |
|
|
|
|
|
|||||||||||||||||||||||||||||||||
Для нахождения среднемассовой темпера- |
|||||||||||||||||||||||||||||||||||||||
Степень нерасчетности можно выразить че- |
|||||||||||||||||||||||||||||||||||||||
туры tх решали уравнение теплового баланса |
|||||||||||||||||||||||||||||||||||||||
рез число Маха на срезе сопла М1 и на границе |
для участка струи от среза сопла до сечения х |
||||||||||||||||||||||||||||||||||||||
струи Мi: |
|
|
|
|
|
|
|
|
|
|
|
|
|
|
|
|
k |
|
|
|
|
|
|
|
|
|
(излучением пренебрегали): |
|
|
||||||||||
|
|
|
|
|
|
|
k −1 |
|
|
|
2 |
|
|
|
|
|
|
|
|
|
|
|
|||||||||||||||||
|
|
|
|
1 |
+ |
|
|
|
k − 1 |
|
|
|
|
|
|
|
|
|
|
|
|
|
|
|
|
|
|
|
|
||||||||||
|
|
|
|
|
|
|
2 |
|
Mi |
|
|
|
|
|
|
|
|
|
|
|
m1cp1Tо +mгсргТг = (m1 +mг )срxТx |
|
|
|
2 |
(12) |
|||||||||||||
|
|
|
|
|
|
|
|
|
|
|
|
|
|
|
|
|
|
|
|
|
|
|
+α(m1 +mг )wx / 2000 . |
||||||||||||||||
|
|
п = |
|
|
|
|
|
|
|
|
|
|
|
. |
|
|
|
|
|
|
(8) |
|
|
|
|
|
|
|
|
|
|
||||||||
|
|
|
|
|
|
|
|
|
|
|
|
|
|
|
|
|
|
|
|
|
|
|
|
|
|
|
|
|
|||||||||||
|
|
|
|
1+ k −1 M12 |
|
|
|
|
|
|
|
|
|
|
|
Из уравнения (12) температуру Tx струи в се- |
|||||||||||||||||||||||
|
|
|
|
|
|
|
|
|
2 |
|
|
|
|
|
|
|
|
|
|
|
|
|
|
|
|
чении х представляли в форме
Более подробные преобразования, связанные с переходом от формулы (5) к (6), выполнены в работе [2].
Рассмотрим участок сверхзвуковой нерасчетной струи, заключенный между срезом сопла и сечением х, находящийся, например, на уровне
Tx = Tо gcрo / cрx +Tг gгcрг / cрx −αwx2 / (2000cрx ) . (13)
Таким образом, в настоящей модели решали систему ~45 алгебраических уравнений и так же, как в работе [2], численно рассчитывали интегралы I1R и I2R в зависимости от числа Крокко.
Исходные данные
Температуру торможения азота (т. е. на входе |
расчетном режиме (n = 1) расход азота через |
в сопло) изменяли в пределах tо = 25−600 °С, а |
одно сопло составлял Vн = 210 м³/мин. Диаметр |
температуру газов в полости конвертера в |
сопла был равен в критическом dкр = 47 мм и |
интервале tг = 300–1000 °C. Теплоемкость азота |
выходном d1 = 69 мм сечениях. Коэффициент |
в окружающей среде (полость конвертера) |
количества движения β = 1,04, коэффициент |
принимали равной ср = 1,25 кДж/(кг К). При |
кинетической энергии α = 1,3. |
ОАО «Черметинформация» • Бюллетень «Черная металлургия» • 7• 2011 ―――――――――――――――― 53

Результаты расчета и их анализ
Присоединенную массу g рассчитывали по |
ление ро также возрастает, что в конечном счете |
уравнению (6). Получено, что чем больше отно- |
приводит к снижению присоединенной массы g. |
сительная температура θ (больше tг), тем |
Например, при повышении температуры tо с 30 |
меньше масса газа, присоединяемая из полости |
до 600 °С на расстоянии 20 калибров присоеди- |
конвертера (рис. 2). На расстоянии х = 20 при |
ненная масса g уменьшается с 0,32 до 0,23. При |
θ = 1 присоединенная масса g = 0,98, а при θ = 5 |
этом относительная скорость wx/w1 возрастает с |
она составляет только g = 0,35. Это объясняется |
0,54 до 0,58. |
тем физически бесспорным фактом, что при уве- |
|
личении θ плотность эжектируемой среды па- |
|
дает, снижается и масса подсасываемого газа. |
|
Рис. 2. Влияние относительной температуры θ на изменение относительной скорости wx/w1 (—) и при-
соединенной массы g (- - -) по длине струи х. Исходные данные: to = 30 oC, Vн = 210 м3/мин, tг = 30−1500 oC
Как следует из рис. 2, по мере удаления от среза сопла отношение скоростей wx/w1 снижается при любом θ. Характерно, что чем больше θ, тем сильнее разогрета окружающая среда, тем ниже присоединенная масса g, и по этой причине отношение скоростей wx/w1 увеличивается. Например, при θ = 1 и х = 30 относительная скорость wx/w1 = 0,28, а при повышении θ до 5 wx/w1 составляет 0,38.
Несколько неожиданной является зависимость присоединенной массы g от температуры подогрева азота to. Из рис. 3 следует, что при удалении от среза сопла присоединенная масса g увеличивается при любом tо. С повышением температуры tо присоединенная масса g, казалось бы, должна расти. Однако с нагревом азота перед соплом при m = const и появлением дополнительного теплового сопротивления дав-
Рис. 3. Зависимость отношения скоростей wx/w1 (—) и присоединенной массы g (- - -) от температуры азота на входе в сопло to при различном удалении х от среза сопла.
Исходные данные: to = 30 oC, Vн = 210 м3 /мин, tг = 30−1500 °C
Из рис. 4 видно, что при увеличении tг температура tх возрастает, причем весьма существенно. Например, если tг увеличивается с 600 до 1000 °С, то на расстоянии х = 20 калибров температура tг возрастает с 175 до 275 °С. Скорость струи wx с увеличением tг повышается, так как струя попадает в более разогретое пространство, плотность окружающей среды снижается и при тех же условиях струя, не встречая значительного сопротивления, ускоряется с 207 до
307 м/с.
Расход Vн увеличивается за счет повышения давления, и по этой причине присоединенная масса g в одном и том же сечении струи будет меньше (рис. 5). Тогда температура tх будет также снижаться, а скорость wx с увеличением расхода Vн возрастать. Например, на расстоянии х = 20 калибров при увеличении Vн с 180 до 360 м3/мин температура снижается с 272 до 542 °С, а скорость возрастает с 197 до 328 м/с.
54 ―――――――――――――――――ОАО «Черметинформация» • Бюллетень «Черная металлургия» • 7• 2011

Рис. 4. Зависимость температуры tх (—) и скорости |
Рис. 5. Изменение температуры tх (—) и скорости |
wx (- - -) от температуры газа в полости конвертера tг на |
wx (- - -) на расстоянии х от среза сопла при различном |
различном удалении х. Исходные данные: to = 30 oC, |
расходе через сопло Vн. Исходные данные: to = 30 oC, |
Vн = 210 м3/мин, tг = 30−1500 oC |
Vн = 210 м3/мин, tг = 30−1500 oC |
Подтверждение адекватности модели
Так как подтвердить численные расчеты проведением эксперимента в полости конвертера нереально, то применим метод тестовой проверки достоверности модели. Например, подтверждается, что:
−на срезе сопла ( х = 0) присоединения окружающего газа нет (g = 0) и wx/w1 = 1 при любых θ
иto (см. рис. 2, 3);
−если х = 0, то и wx = w1 = λ1акр, а tх = t1 = −123 °С,
что так же следует из формулы Т1 = Тоτ(λ) (см.
рис. 4);
−если х = 0, то и tх = t1 = −123 °С, а wx = w1 =
=λ1акр;
−чем дальше от среза сопла, то независимо
от to, tг, Vн, wx снижается, а tх возрастает, что соответствует физической картине присоединения горячего газа окружающей среды к любой струе.
В дальнейшем следует решить подобную задачу по влиянию различных факторов на мощность сверхзвуковой нерасчетной струи, внедряющейся в шлаковый расплав.
Выводы
1.Численное моделирование течения в шение давления ро перед соплом постоянного
сверхзвуковой струе позволило определить, насколько с повышением температуры газа tг в полости конвертера снижается присоединенная масса окружающего газа g и увеличиваются скорость wx и температура tх на любом удалении от сопла.
2. Установлено, что на длине струи х возрастание температуры to и связанное с этим повы-
сечения приводит к уменьшению присоединенной массыg окружающего газа иросту скорости wx.
3. Показано, что если не изменять диаметры в критическом dкр и выходном d1 сечениях сопла, то при увеличении расхода Vн холодного азота температура tх снижается и увеличивается скорость wx в произвольном сечении струи х.
БИБЛИОГРАФИЧЕСКИЙ СПИСОК
1. Смирнов А. Н., Дюдкин Д. А. Мировые тенденции развития технологии производства и разливки стали //
Металлургическая и горнорудная промышленность. 2010. № 2. C. 55−58.
2. Исследование присоединенной массы сверхзвуковой струи на газодинамическом участке / Б. А. Баланин, О. С. Зеленков, Е. А. Капустин и др.: Сб. “Тепло- и массообменные процессы в ваннах сталеплавильных агрегатов”.
М.: Металлургия. 1975. C. 19−35.
ОАО «Черметинформация» • Бюллетень «Черная металлургия» • 7• 2011 ―――――――――――――――― 55

УДК 621.771.25.004.68 Э. О. ЦКИТИШВИЛИ1, А. Н. ЧУДНОВЕЦ1, В. Н. БРУХАНСКИЙ1,
Д. П. КУКУЙ2, к.т.н.; В. С. СОЛОД2, к.т.н., solod_vs2010@ua.fm; А. А. МАЛЬЦЕВ3
( 1 ЗАО “Макеевский металлургический завод”, 2 НПО “Доникс”, 3 Донецкий национальный технический университет)
ОСВОЕНИЕ ПРОИЗВОДСТВА ВЫСОКОКАЧЕСТВЕННОЙ ПРОДУКЦИИ НА САМОМ НОВОМ В УКРАИНЕ СРЕДНЕСОРТНО-МЕЛКОСОРТНОМ СТАНЕ 390
Для повышения эффективности производства |
лочного стана 150, поставленного также фирмой |
|||||||||
в ЗАО |
“Макеевский |
металлургический завод” |
SKET. |
|
|
|
|
|||
(ЗАО ММЗ) в июле 2009 г. введен в эксплуата- |
В соответствии с проектом фирмы SKET стан |
|||||||||
цию среднесортно-мелкосортный стан 390. |
390 представляет собой непрерывный однони- |
|||||||||
Строительство стана имеет длительную ис- |
точный бескантовочный 18-клетевой стан, пер- |
|||||||||
торию, которая началась еще в период послед- |
воначально планировавшийся как среднесорт- |
|||||||||
них лет СССР, когда сортопрокатное производ- |
ный, ориентированный на использование ката- |
|||||||||
ство СССР было ориентировано на фирму SKET, |
ной заготовки собственного производства сече- |
|||||||||
Германия. Закладка фундамента в существую- |
нием 156×156 мм и выпуск продукции в прутках |
|||||||||
щем здании старого сортопрокатного стана и |
длиной 6−12 м. Схема расположения оборудова- |
|||||||||
первые поставки оборудования относятся к |
ния стана 390 показана на рис. 1. |
|
|
|||||||
1994−1995 гг. послепусковому периоду прово- |
|
|
|
|
|
|||||
|
|
|
|
|
|
|
|
|
|
|
|
36000 |
33000 |
33050 |
33100 |
33000 |
195000 |
4100 |
33000 33100 |
33 |
65000 |
35000 |
79200 |
21 |
20 |
19 |
18 |
17 |
16 |
15 |
14 |
13 |
12 |
11 10 9 |
8 |
7 |
6 |
5 4 |
3 |
2 |
1 |
Рис. 1. Схема расположения оборудования стана 390 ЗАО ММЗ:
1 загрузочные решетки; 2 загрузочный рольганг с весами; 3 методическая комбинированная нагревательная печь с шагающим подом; 4 рольганг-термостат; 5 трайб-аппарат; 6 разрывные аварийные ножницы; 7 рабочие клети черновой группы (№ 1−6); 8 аварийные кривошипно-рычажные ножницы; 9 рабочие клети промежуточной группы (№ 7−12); 10 устройство для смены клетей промежуточной и чистовой групп; 11 рабочие клети чистовой группы (№ 13−18); 12 устройство ускоренного охлаждения; 13 трайб-аппарат; 14 двухсистемные делительные ножницы; 15 подводящий рольганг; 16 реечный холодильник; 17 многониточная роликоправильная машина;
18 ножницы холодной резки; 19 сборная решетка с весами для пакетов; 20 транспортер слоев проката; 21 вязальная машина
Минимальными профилями проектного сор- |
прокат арматурный для железобетонных конст- |
тамента были определены прокат круглый диам. |
рукций № 14, уголок равнополочный 32×32×4 мм. |
20 мм, квадратный со стороной 18 мм, шести- |
В 90-е годы прошлого века в связи с отсутст- |
гранный с диаметром вписанного круга 20 мм, |
вием стратегического инвестора строительство |
В работе принимали участие Э.В. Головин, А.В. Долгопол.
56 ―――――――――――――――――ОАО «Черметинформация» • Бюллетень «Черная металлургия» • 7• 2011
было прекращено и возобновилось только в 2006 г. после прихода стратегического инвестора в лице “Смарт-холдинга” и заключения контракта на допоставку оборудования и технологии с на-
следником SKET фирмой Magdeburger Walzwerk Engineering (MWE), Германия.
В связи с изменением рыночной ситуации новый контракт предполагал расширение сортамента стана в сторону мелкого сорта и арматуры.
Поставщиками оборудования были фирмы LOI, Германия (нагревательная печь и автоматизация нагрева), и Transresh, Германия (электропривод и автоматизация первого и второго уровней). К разработке технологии прокатки пускового сортамента, включая двухручьевую прокатку−разделение (ДПР), к разработке конструкции привалковой арматуры скольжения, а также к разработке автоматизированной системы оперативного управления производством (СОУП) было привлечено НПО “Доникс”, Украина. Роликовую арматуру для прокатки круглых и угловых профилей поставила фирма Morgardshammar AB, Швеция.
Задачу расширения сортамента решили путем использования двух типоразмеров заготовки
150×150×7500−11800 и 125×125×7500−11800
мм. Заготовка меньшего сечения используется для производства круглых профилей диам. 12−14 мм и арматурного проката № 8−12.
Проектная производственная мощность стана составляет от 600 до 700 тыс. т/год проката в зависимости от рабочего сортамента.
Проектный сортамент производимой на стане продукции следующий:
марочный
−углеродистая сталь Ст0, Ст3, Ст4, Ст5, Ст6
по ГОСТ 380−94 и ДСТУ 2651−94;
−углеродистая конструкционная качествен-
ная сталь 08, 10, 20, 30, 40, 45, 50, 60 по ГОСТ 1050−88;
−сталь для армирования железобетонных конструкций 10ГТ, 35ГС, 80С по ГОСТ 5781−82;
−легированная конструкционная сталь 45Х, 50Х, 35Г2, 30ХГС, 38ХГСА, 38ХС, 30ХГТ, 40ХН по ГОСТ 4543−71;
профильный
−прокат арматурный для железобетонных конструкций классов А240С, А400, А500−А800
№8−36;
−прокат круглый диам. 12−60 мм;
−швеллеры № 5, № 6,5, № 8;
−прокат для рессор размерами 75×8, 75×9,5, 90×10, 90×12 мм.
В соответствии с составом и расположением оборудования последовательность технологических операций на стане следующая.
Перед посадкой в печь заготовки одной плавки поштучно взвешивают на загрузочном рольганге и измеряют их длину, каждой плавке присваивают номер партии. Нагрев заготовки осуществляют в методической комбинированной нагревательной печи с шагающими водоохлаждаемыми балками и шагающим подом. Проектная производительность печи по всаду 120 т/ч на заготовке 150×150×11800 мм.
После выхода из печи по отводящему рольгангу заготовка поступает на рольганг-термостат, предназначенный для стабилизации и выравнивания температуры металла по сечению. Проектная потеря температуры задним концом внутри термостата составляет 40 °С.
В клеть № 1 стана заготовку задают с помощью трайб-аппарата. В аварийных ситуациях в черновой группе резка заготовки осуществляется пневматическими разрывными ножницами, установленными перед клетью № 1.
Черновая группа клетей включает три горизонтальные (№ 1, 3, 5) и три вертикальные (№ 2, 4, 6) клети. В состав промежуточной группы входят шесть клетей, из которых три горизонтальные (№ 7, 9, 11), одна вертикальная (№ 10) и две комбинированные (№ 8, 12). Чистовая группа состоит из двух горизонтальных (№ 13, 15) и четырех комбинированных (№ 14, 16, 17,18) клетей. Основным видом перевалки на стане является смена клетей. В черновой группе смену клетей выполняют с помощью мостового крана, а в двух остальных с помощью устройства групповой смены клетей. Перевалку валков осуществляют, как правило, на стендах. В экстренных случаях возможна перевалка валковыми кассетами на стане.
Между черновой и промежуточной, промежуточной и чистовой группами клетей установлены аварийные кривошипно-рычажные ножницы, осуществляющие также зачистку переднего конца раската. Прокатка в черновой и промежуточной группах осуществляется с минимальным натяжением, обеспечиваемым автоматизированной системой контроля натяжения. Между промежуточной и чистовой группами клетей и
−прокат квадратный со стороной 14−45 мм; между всеми клетями чистовой группы установ-
−прокат шестигранный с диаметром вписанлены пневматические вертикальные петлерегу-
ного круга 14−48 мм; |
ляторы, обеспечивающие прокатку без натяже- |
− уголки равнополочные от 25×25×3 до |
ния. |
63×3×4−6 мм; |
В табл. 1 приведены параметры рабочих кле- |
− уголки неравнополочные от 45×28×3−4 до |
тей, двигателей, линий привода и допускаемые |
63×40×4−8 мм; |
параметры прокатного оборудования. |
ОАО «Черметинформация» • Бюллетень «Черная металлургия» • 7• 2011 ―――――――――――――――― 57

ТАБЛИЦА 1. ПАРАМЕТРЫ РАБОЧИХ КЛЕТЕЙ И ПРИВОДА ВАЛКОВ СТАНА 390
|
|
|
Диаметр |
Номиналь- |
Обороты двигателя, об/мин |
Переда- |
Максималь- |
Максималь- |
Номи- |
||
|
|
1 |
ная |
|
|
|
нальный |
||||
Номер |
Тип* |
2 |
|
|
|
|
|
|
|||
|
валков* |
мощность |
мини- |
номи- |
макси- |
точное |
ная сила |
ный момент |
момент |
||
клети |
клети |
(длина |
двигателя, |
маль- |
наль- |
маль- |
отношение |
прокатки, |
прокатки, |
двига- |
|
|
|
|
бочки), мм |
кВт |
ные |
ные |
ные |
редуктора |
кН |
кНм |
теля, |
|
|
|
|
|
|
|
|
|
|
|
Нм |
1 |
Г600 |
590/520×250 |
400 |
50 |
500 |
1000 |
71,000 |
4000 |
500 |
7639 |
|
2 |
В600 |
590/520×250 |
400 |
50 |
500 |
1000 |
56,200 |
4000 |
500 |
7639 |
|
3 |
Г440 |
450/380×180 |
400 |
50 |
500 |
1000 |
32,100 |
2100 |
190 |
7639 |
|
4 |
В440 |
450/380×180 |
400 |
50 |
500 |
1000 |
22,200 |
2100 |
190 |
7639 |
|
5 |
Г440 |
450/380×180 |
400 |
50 |
500 |
1000 |
17,900 |
2100 |
190 |
7639 |
|
6 |
В440 |
450/380×180 |
400 |
50 |
500 |
1000 |
14,100 |
2100 |
190 |
7639 |
|
7 |
Г390 |
390/340×630 |
630 |
50 |
500 |
1000 |
9,960 |
1600 |
140 |
12032 |
|
8 |
К390 |
390/340×630 |
630 |
50 |
500 |
1000 |
7,130 |
1600 |
140 |
12032 |
|
9 |
Г390 |
390/340×630 |
800 |
50 |
320 |
1000 |
5,610 |
1600 |
140 |
23873 |
|
10 |
В390 |
390/340×630 |
630 |
50 |
500 |
1000 |
3,960 |
1600 |
140 |
12032 |
|
11 |
Г390 |
390/340×630 |
800 |
50 |
320 |
1000 |
3,190 |
1600 |
140 |
23873 |
|
12 |
К390 |
390/340×630 |
800 |
50 |
320 |
1000 |
2,483 |
1600 |
140 |
23873 |
|
13 |
Г390 |
390/340×630 |
800 |
50 |
320 |
1000 |
2,250 |
1600 |
140 |
23873 |
|
14 |
К390 |
390/340×630 |
800 |
50 |
320 |
1000 |
1,806 |
1600 |
140 |
23873 |
|
15 |
Г390 |
390/340×630 |
800 |
50 |
320 |
1000 |
1,591 |
1600 |
140 |
23873 |
|
16 |
К390 |
390/340×630 |
800 |
50 |
320 |
1000 |
1,196 |
1600 |
140 |
23873 |
|
17 |
К390 |
390/340×630 |
800 |
50 |
320 |
1000 |
1,020 |
1600 |
140 |
23873 |
|
18 |
К390 |
390/340×630 |
800 |
50 |
320 |
1000 |
0,712 |
1600 |
140 |
23873 |
|
|
|
*1 |
Г горизонтальная; В вертикальная; К комбинированная. |
|
*2 |
В числителе максимальный, в знаменателе минимальный диаметр валков. |
|
|
За чистовой клетью расположен участок уско- |
ром до 50 мм на кратные длины на скоростях |
ренного охлаждения (УУО) длиной 29 м, предна- |
2,3–11,6 м/с кривошипно-рычажной, 11,7−17 м/с |
|
значенный для термической обработки проката с |
кривошипной системами. Транспортирование го- |
|
прокатного нагрева конструкции Thermex, Гер- |
рячего проката от делительных ножниц к прием- |
|
мания. Устройство ускоренного охлаждения со- |
ному рольгангу осуществляется по подводящему |
|
стоит из шести автономных секций длиной 4,5 м, |
рольгангу. Длина реечного холодильника 102 м, |
|
смонтированных в линиях рольгангов на плат- |
он оснащен подтягивающим устройством для |
|
формах совместно с параллельно установлен- |
выравнивания передних концов штанг и накопи- |
|
ными секциями рольгангов. Платформы сег- |
телем слоев проката после охлаждения. |
|
ментного типа обеспечивают возможность ввода |
После охлаждения на холодильнике и накоп- |
|
одной из секций охлаждающего устройства или |
ления слоя прокат послойно передают к летучим |
|
рольганга в технологический поток стана при по- |
ножницам холодной резки, при этом фасонный |
|
вороте ее на угол 25 град. командой с пульта. |
прокат перед резкой проходит через роликопра- |
|
Кроме этого проектом предусмотрена установка |
вильную машину (РПМ), выдвинутую в линию |
|
за клетью № 16 устройства предварительного |
резки. Скорость транспортирования слоев за- |
|
охлаждения для термоупрочнения крупных ар- |
дают либо прижимным роликом (при резке сорта |
|
матурных профилей на высокий класс прочно- |
и арматуры), либо РПМ. Порезанные на мерные |
|
сти. |
длины слои по отводящему рольгангу транспор- |
|
|
Комбинация трех типоразмеров охлаждаю- |
тируют к поперечному транспортеру, оснащен- |
щих труб калибрами 33, 42 и 48 мм и двух типо- |
ному устройством для выравнивания концов |
|
размеров по длине участка охлаждения (длин- |
штанг, дозатором и кантователем, предназна- |
|
ные и короткие) позволяет достаточно гибко |
ченным для поворота на 180 град. слоев уголка |
|
осуществлять подбор продолжительности охла- |
при упаковке его в прямоугольные пакеты. |
|
ждения для обеспечения заданных механических |
За поперечным транспортером установлены |
|
свойств. Упрочнение мелких арматурных профилей, |
две вязальные машины производства Sund Birsta |
|
прокатываемых в две нитки, обеспечивают две |
AB, Швеция, производящие обвязку пачек катан- |
|
двухниточные секции калибром 33 мм (длинная и |
кой. Обвязанные пачки транспортируют на сбор- |
|
короткая). |
ную решетку, перед которой установлены весы |
|
|
За устройством ускоренного охлаждения на |
для взвешивания пакетов. |
расстоянии 4,5 м расположены двухсистемные |
Основными принципами, заложенными в раз- |
|
делительные ножницы, обеспечивающие рас- |
работку схемы калибровки, были универсаль- |
|
крой сортового и арматурного проката диамет- |
ность использования калибров при применении |
58 ―――――――――――――――――ОАО «Черметинформация» • Бюллетень «Черная металлургия» • 7• 2011

непрерывнолитой или катаной заготовки, минимальное количество овальных и круглых калибров, максимальная равномерность деформации в черновых калибрах, максимальное использование вытяжной способности черновой и промежуточной групп клетей. Этим требованиям в полной мере отвечало применение черновой пары ящичный − ящичный овал и вытяжная система калибров овал−круг. Таким образом, для всего сортамента круглых и арматурных профилей было выбрано 18 типоразмеров овальных, 15 типоразмеров круглых подготовительных калибров, по 2 ящичных и ящичных овалов.
Калибровка угловой стали выполнена по системе фасонных открытых угловых калибров с прямыми полками и контрольных ребровых калибров, расположенных в вертикальных клетях.
Производственной программой стана предусмотрено использование ДПР в прокатных валках клети № 16 для производства арматурной стали от № 8 до № 14 в прутках длиной до 12 м.
Формирование сдвоенного раската при ДПР осуществляется по схеме круг−ромб−квадрат− −формирующий. При этом в клетях № 13−16 используется привалковая арматура скольжения, а квадратный раскат кантуют в формирующий калибр с помощью кантующей головки.
Впроцессе опробования проведено испытание формирования сдвоенного раската из круглого подката, направляемого в калибр клети
№15 с помощью четырехроликовой вводной арматуры. В этом случае упрощается процесс передачи раската за счет исключения кантовки перед клетью № 14. Испытание показало практическую возможность применения такого способа и достаточную устойчивость входа металла в калибр, однако стойкость формирующего калибра при этом снизилась.
Проектные режимы прокатки разработаны с учетом соответствия скоростных и нагрузочных параметров допускаемым. Для этого расчеты температурного, скоростного и нагрузочного режимов произведены с использованием системы автоматизированного проектирования и моделирования технологии прокатки сортовых профилей и катанки (“Сорт-Про”), предназначенной для оперативного моделирования, проектирования и анализа основных технологических параметров процесса прокатки в интерактивном режиме [1].
Всвязи с наличием на стане современной системы автоматизации, обеспечивающей подготовку, управление, регулирование и контроль технологического процесса, в процессе освоения стана появилась возможность оценки загрузки оборудования и проверки адекватности разработанных режимов практическим данным.
Вбазах данных системы СОУП поплавочно для каждой заготовки накапливаются данные по температуре поверхности металла на выходе из печи, за клетью № 1, за чистовой клетью № 18 и на клапанах холодильника, данные о базовых и текущих настройках скоростного режима в ли-
нейных скоростях и оборотах двигателей, а также о загрузке двигателя по вращающему моменту по отношению к номинальному по всем клетям стана. Учитывая проектные режимы обжатий и возможности обеспечения минимального натяжения и петлеобразования в промежутках клетей, провели моделирование параметров прокатки ряда арматурных профилей, освоенных на стане.
Сопоставление расчетных и практических данных по формоизменению металла, скоростным режимам с минимальным натяжением, температурным режимам и механическим моментам главных двигателей электропривода прокатных клетей проведено при прокатке десяти профилей пускового сортамента. Среди них круг диам. 40 мм из стали М4 (аналог сталь 80); термоупрочненные на класс А400 и А500 арматурные профили (Ст3сп): № 16, № 18, № 20, № 25,
№ 28; арматурные профили № 10 и № 14, прокатанные по технологии ДПР (Ст4сп); угловые профили 32×32×4 и 40×40×4 (Ст3сп).
Поскольку сравнение расчетных и зарегистрированных нагрузок можно произвести только по усредненному по длине проката вращающему моменту двигателя, адекватность моделирования оценивали по этому параметру.
Вкачестве исходных данных использованы размеры непрерывнолитой заготовки, температура металла на выходе из печи, проектные конструкция калибров и режим обжатий, зарегистрированные значения оборотов двигателей, диаметры установленных валков (табл. 2).
Втабл. 2 и на рис. 2 показаны результаты моделирования параметров прокатки при производстве арматуры № 10 по технологии ДПР.
Рис. 2. Диаграмма достоверности аппроксимации моментов на двигателях при прокатке арматурного
профиля № 10×2 по технологии ДПР при tнаг = 1005 °C и скорости прокатки V18 = 11,3 м/с (×2 кратность
прокатки−разделения)
ОАО «Черметинформация» • Бюллетень «Черная металлургия» • 7• 2011 ―――――――――――――――― 59
2011 7• • »металлургия Черная« Бюллетень • »Черметинформация« ОАО――――――――――――――――― 60
ТАБЛИЦА 2. РАСЧЕТНЫЕ И ЗАРЕГИСТРИРОВАННЫЕ ПАРАМЕТРЫ ПРОКАТКИ АРМАТУРНОГО ПРОФИЛЯ № 10
|
|
|
|
|
|
|
|
|
|
|
|
|
|
Момент двигателя |
|
|
Кине- |
||
|
|
|
|
|
|
Коэф- |
|
Оборо- |
Оборо- |
Ско- |
Темпе- |
Сила |
Мо- |
|
|
|
Ошиб- |
|
матиче- |
|
|
|
|
|
Пло-щадь |
фици- |
Диаметр |
мент |
рас- |
ре- |
ре- |
ка мо- |
Const |
ское |
|||||
|
|
|
Высота, |
Шири- |
ты дви- |
ты |
рость |
ратура |
про- |
гист- |
|||||||||
|
Клеть |
Калибр |
мм |
на, мм |
сечения, |
ент |
валка, |
гателя, |
валков, |
прокат- |
входа, |
катки, |
про- |
чет- |
гистри- |
дели- |
Сi, |
рассо- |
|
Номер |
|
|
|
|
мм2 |
вытяж- |
мм |
об/мин |
об/мин |
ки, м/с |
С |
кН |
катки, |
ный, |
руемый, |
рируе |
рова- |
мм2 м/с |
гласо- |
клети |
|
|
|
|
|
ки |
|
|
|
|
|
|
кНм |
Нм |
% |
мый, |
ния, % |
|
вание |
|
|
|
|
|
|
|
|
|
|
|
|
|
|
|
|
Нм |
|
|
Сi/Сi 1 |
|
Заго- |
|
127 |
127 |
16115,0 |
|
|
|
|
|
1005 |
|
|
|
|
|
|
|
|
|
товка |
|
|
|
|
|
|
|
|
|
|
|
|
|
|||||
|
|
|
|
|
|
|
|
|
|
|
|
|
|
|
|
|
|
|
|
1 |
Г600 |
|
78,9 |
148,2 |
11045,0 |
1,459 |
590 |
402 |
5,66 |
0,159 |
1002 |
1766 |
176,6 |
3013 |
36,3 |
2776 |
8,5 |
1756 |
|
2 |
В600 |
|
98 |
98 |
8007,0 |
1,378 |
590 |
445 |
7,93 |
0,22 |
987 |
1209 |
119 |
2558 |
32,4 |
2472 |
3,5 |
1762 |
1,003 |
3 |
Г440 |
|
59,3 |
110,9 |
5568,0 |
1,438 |
430 |
486 |
15,1 |
0,316 |
976 |
1113 |
76,8 |
2887 |
37,8 |
2886 |
0 |
1759 |
0,999 |
4 |
В440 |
|
71 |
72 |
4013,0 |
1,388 |
450 |
452 |
20,4 |
0,434 |
976 |
749,4 |
54,4 |
2832 |
37,0 |
2823 |
0,3 |
1742 |
0,990 |
5 |
Г440 |
|
39,3 |
84,4 |
2805,0 |
1,430 |
450 |
488 |
27,3 |
0,62 |
962 |
877,6 |
55,5 |
3590 |
49,7 |
3798 |
5,5 |
1739 |
0,999 |
6 |
В440 |
|
51 |
51,1 |
2070,0 |
1,356 |
450 |
535 |
37,8 |
0,844 |
959 |
546,2 |
36,3 |
2965 |
40,5 |
3090 |
4,1 |
1747 |
1,005 |
7 |
Г390 |
|
28 |
63,5 |
1404,0 |
1,474 |
390 |
606 |
60,8 |
1,242 |
942 |
677,6 |
33,8 |
3925 |
29,9 |
3592 |
9,3 |
1744 |
0,998 |
8 |
К390 |
|
36 |
36 |
1048,0 |
1,340 |
390 |
617 |
86,6 |
1,681 |
946 |
343,5 |
18,5 |
2982 |
24,9 |
3001 |
0,6 |
1762 |
1,010 |
9 |
Г390 |
|
21,2 |
44,7 |
768,9 |
1,363 |
390 |
632 |
112,8 |
2,302 |
950 |
391,8 |
16 |
3300 |
14,2 |
3383 |
2,4 |
1770 |
1,005 |
10 |
В390 |
|
27 |
28,2 |
600,4 |
1,281 |
390 |
599 |
151,4 |
2,959 |
954 |
226,8 |
9,98 |
2749 |
25,1 |
3014 |
8,8 |
1777 |
1,004 |
11 |
Г390 |
|
16,5 |
35 |
468,7 |
1,281 |
390 |
601 |
188,7 |
3,82 |
959 |
254,1 |
9,01 |
3090 |
14,2 |
3385 |
8,7 |
1790 |
1,008 |
12 |
К390 |
|
21,5 |
22 |
381,3 |
1,229 |
390 |
590 |
237,7 |
4,68 |
963 |
154,1 |
6,02 |
2648 |
11,0 |
2626 |
0,8 |
1784 |
0,997 |
13 |
Г390 |
|
14,3 |
25,3 |
297,6 |
1,281 |
390 |
657 |
292 |
6,01 |
961 |
162,7 |
4,94 |
2406 |
9,2 |
2194 |
9,7 |
1789 |
1,002 |
14 |
К390 |
|
19,9 |
15,5 |
259,3 |
1,148 |
390 |
624 |
345,4 |
6,9 |
963 |
67,5 |
1,814 |
1105 |
4,9 |
1163 |
5,0 |
1789 |
1,000 |
15 |
Г390 |
|
13,6 |
22,5 |
234,2 |
1,107 |
390 |
593 |
372,8 |
7,64 |
960 |
83,7 |
2,11 |
1462 |
5,6 |
1346 |
8,6 |
1789 |
1,000 |
16 |
К390 |
|
13,6 |
11,7 |
113,0 |
1,036 |
390 |
466 |
390 |
7,92 |
955 |
31,2 |
1,381 |
146 |
0,7 |
167 |
12,6 |
1790 |
1,000 |
17 |
К390 |
|
7,6 |
15,8 |
93,9 |
1,204 |
390 |
459 |
450,2 |
9,53 |
946 |
179,6 |
3,84 |
4180 |
16,6 |
3953 |
5,7 |
1790 |
1,000 |
18 |
К390 |
|
9,8 |
10 |
78,5 |
1,190 |
390 |
387 |
543,9 |
11,3 |
948 |
112,3 |
2,834 |
4455 |
18,4 |
4385 |
1,6 |
1783 |
0,996 |
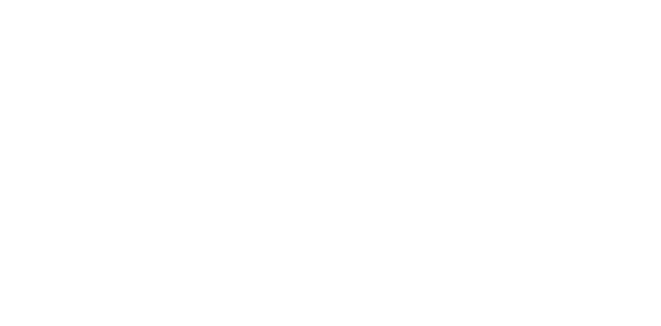
Из табл. 2 следует, что система “Сорт-Про” |
|
Показатели |
адекватности математического |
|||||||||||
достоверно моделирует и кинематический режим |
моделирования момента двигателей при произ- |
|||||||||||||
прокатки, так как адекватно отражает настройку |
водстве арматурных профилей № 10, № 14, |
|||||||||||||
режима минимального кинематического рассо- |
№ 18, № 20, № 25, № 28 таковы: |
|
|
|||||||||||
гласования в смежных прокатных клетях стана |
|
|
|
|
|
|
|
|
||||||
(разница Сi и Ci−1 не выше 1 %). |
|
|
|
|
|
|
|
|
|
|
|
|||
|
|
|
|
|
|
|
|
|
|
|
|
|
|
|
Номер профиля |
|
10 |
|
14 |
|
16 |
|
18 |
|
20 |
25 |
|
28 |
|
Среднеквадратичное |
|
|
|
|
|
|
|
|
|
|
|
|
|
|
отклонение, % |
|
6,7 |
|
6,8 |
|
6,6 |
|
4,5 |
|
6,7 |
5,2 |
|
6,3 |
|
R2 |
|
0,973 |
|
0,942 |
|
0,954 |
|
0,968 |
|
0,967 |
0,983 |
|
0,963 |
|
Полученные |
результаты свидетельствуют |
о |
|
После проведения технического аудита печи |
||||||||||
высокой точности (среднеквадратичная погреш- |
специалистами НПО “Доникс” и выполнения ра- |
|||||||||||||
ность не более 7 %) прогнозирования парамет- |
боты по настройке сводовых горелок и внедре- |
|||||||||||||
ров прокатки с помощью системы “Сорт-Про”. |
|
ния нового температурного режима нагрева с |
||||||||||||
В процессе освоения стана возникла про- |
перераспределением теплового баланса между |
|||||||||||||
блема с качеством нагрева заготовки. В то время |
верхним и боковым нагревом качество нагрева |
|||||||||||||
как ее концы перегревались, температура сред- |
значительно улучшилось, нагрузки двигателей |
|||||||||||||
ней части заготовки оставалась ниже на 50− |
черновой группы снизились на 7−10 %. |
|
|
|||||||||||
70 °С. Повышение задания на температуру на- |
|
Диаграмма угловых скоростей двигателей по |
||||||||||||
грева в системе управления печью приводило к |
клетям стана 390 при прокатке арматурных про- |
|||||||||||||
провисанию концов и усложнению транспорти- |
филей в процессе освоения технологии показана |
|||||||||||||
рования нагретой заготовки из печи к первой |
на рис. 4. Из диаграммы угловых скоростей |
|||||||||||||
прокатной клети стана. Поэтому вначале освое- |
видно, что практически во всех режимах про- |
|||||||||||||
ния стан работал с минимально нагретой заго- |
катки арматурных профилей двигатели клетей |
|||||||||||||
товкой. |
|
|
|
|
|
|
№ 7−18 работают в зоне регулирования |
|||||||
Диаграммы распределения расчетной сред- |
ослаблением поля, т. е. с понижением допускае- |
|||||||||||||
немассовой температуры прокатки арматурных |
мого вращающего момента. Это свидетельствует о |
|||||||||||||
профилей по клетям стана (рис. 3) свидетельст- |
нерациональном выборе поставщиком оборудо- |
|||||||||||||
вуют о том, что температура нагрева заготовки в |
ванияскоростныхпараметров двигателей. |
|
|
|||||||||||
процессе освоения была близка к нижней пре- |
|
|
|
|
|
|
|
|
||||||
дельной и составляла 1020−1060 |
°С. Это спо- |
|
|
|
|
|
|
|
|
собствовало повышению нагрузок на оборудование, особенно в клетях черновой группы, но, с другой стороны, дало возможность оценки верхних возможных пределов нагрузки стана.
|
Рис. 4. Распределение угловых скоростей двигателей по |
||
|
клетям стана 390 при прокатке арматурных профилей |
||
Рис. 3. Распределение среднемассовой температуры |
Распределение моментов двигателей по кле- |
||
тям стана 390 при прокатке арматурных профи- |
|||
прокатки арматурных профилей № 10−№ 28 |
|||
лей в режимах с наиболее нагруженными по уг- |
|||
по клетям стана 390 |
|||
|
ловым скоростям двигателями (профили № 20, |
||
|
№ 25 и № 28) показано на рис. 5. Анализ |
меха- |
|
ОАО «Черметинформация» • Бюллетень «Черная металлургия» • 7• 2011 ―――――――――――――――― |
61 |

нических нагрузок линии прокатных клетей показал, что при температуре нагрева заготовки размерами 150×150 мм до 1020−1060 °С наиболее нагруженным по моменту является двигатель клети № 5 черновой группы (80−95 % от номинала). По остальным параметрам существует резерв нагрузок, позволяющий в будущем осваивать более энергоемкие профили, полосовые и фасонные.
Рис. 5. Распределение моментов двигателей по клетям стана 390 при прокатке арматурных профилей № 20,
№ 25 и № 28
Диаграммы распределения силы прокатки по клетям стана 390 при прокатке арматурных профилей (рис. 6) и момента прокатки (рис. 7) подтверждают выводы о максимальной загрузке черновой группы клетей. При указанных выше минимальных температурах нагрева расчетный запас прочности валков черновой группы составляет от 1,5 до 2, а запас линии привода от
1,8 до 3.
Рис. 6. Распределение силы прокатки по клетям стана 390 при прокатке арматурных профилей № 10−№ 28
Рис. 7. Распределение момента прокатки по клетям стана 390 при прокатке арматурных профилей № 10−№ 28
Для определения технологических возможностей установки ускоренного охлаждения произведен анализ распределения температуры металла на выходе из стана (рис. 8). Мониторинг температуры производится автоматически на каждой заготовке путем расчета среднего значения температуры поверхности за чистовой клетью по каждой отрезанной штанге.
Рис. 8. Распределение температуры поверхности металла за чистовой клетью по длине проката
Полученный характер изменения температуры обусловлен установленным режимом нагрева с повышенной температурой концов, обеспечивающей при их свободной прокатке отсутствие переполнения калибров.
Установлено, что максимальная разница в температуре концов и средней части штуки проката не превышала 30 °С, что позволяет обеспечить достаточную стабильность механических свойств арматурного проката по длине раската при его термоупрочнении в устройстве ускоренного охлаждения.
Процесс освоения арматурных профилей проходил одновременно с освоением процесса
62 ―――――――――――――――――ОАО «Черметинформация» • Бюллетень «Черная металлургия» • 7• 2011

термоупрочнения. Для разработки режимов тер- |
98 % максимальной производительности нагре- |
|
моупрочнения использовали рекомендации по- |
вательной печи, а применение ДПР профиля |
|
ставщика оборудования, а также результаты |
№ 20 не обеспечивает повышения производи- |
|
расчета, полученные при помощи разработаной |
тельности стана. |
|
в НПО “Доникс” комплексной математической |
Ответ на этот вопрос получен моделирова- |
|
модели многостадийного ускоренного охлажде- |
нием технологических параметров прокатки с |
|
ния, структурообразования и механических |
помощью системы “Сорт-Про”, для чего прове- |
|
свойств низкоуглеродистых сталей в термоуста- |
дены сравнительные расчеты удельных энерго- |
|
новках различных конструкций [2]. |
затрат при традиционной прокатке и ДПР ряда |
|
Математическая модель формирования ме- |
арматурных профилей, включая и указанные |
|
ханических свойств позволяет достаточно точно |
профили. Приняты следующие условия модели- |
|
для достижения требуемого их уровня опреде- |
рования: одинаковая среднемассовая темпера- |
|
лять температуру самоотпуска стали с заданным |
тура нагрева заготовки 1150 °С и одинаковая |
|
химическим составом и позволяет устанавливать |
температура конца прокатки для одно- и двухни- |
|
интенсивность охлаждения металла в УУО для |
точной прокатки одного профилеразмера. |
|
поддержания ее в заданном диапазоне. |
На рис. 9 показаны результаты моделирова- |
|
Разработанная математическая модель ус- |
ния энергозатрат на прокатку, из которых сле- |
|
пешно прошла опробование при пуске и освое- |
дует, что независимо от изменения производи- |
|
нии стана 390 при упрочнении арматурных про- |
тельности ДПР профилей № 16, № 18 и № 20 |
|
филей № 10, № 14, № 16, № 18, № 25, № 28 и |
обеспечивает экономию удельных затрат элек- |
|
№ 32 на класс А500С по ДСТУ 3760−98 из ста- |
троэнергии на деформацию порядка 27−30 %. |
|
лей Ст3сп, Ст4сп (ГОСТ 380−2005) при различ- |
Кроме того, за счет вывода двух клетей из про- |
|
ных температурах, скоростях прокатки и интен- |
катки при ДПР обеспечивается экономия парка |
|
сивности охлаждения. Погрешность прогноза |
валков. |
|
механических свойств по прочностным парамет- |
|
|
рам не превышала ±12 МПа. |
|
|
В табл. 3 приведены результаты верифика- |
|
|
ции математической модели ускоренного охлаж- |
|
|
дения при прокатке арматурных профилей, ос- |
|
|
военных на стане за два месяца работы. |
|
|
Контрольные замеры размеров готового про- |
|
|
филя показывают, что точность настройки вал- |
|
|
ков, кинематические и температурные режимы |
|
|
прокатки могут обеспечить прокатку не только |
|
|
строительного, но и сортового сортамента про- |
|
|
ката повышенной точности. |
|
|
В процессе освоения проектного сортамента |
|
|
арматурных профилей возник вопрос о целесо- |
Рис. 9. Удельные энергозатраты Aуд при традиционной |
|
образности использования технологии ДПР ар- |
||
прокатке и ДПР арматурных профилей № 12−№ 20 |
||
матурных профилей № 16, № 18, № 20. Дело в |
||
|
||
том, что при существующих ограничениях по |
Анализ данных математического моделиро- |
|
скорости прокатки (17 м/с) и производительности |
вания (рис. 10) позволил получить статистиче- |
|
нагрева (120 т/ч) при ДПР профиля № 16 может |
скую зависимость удельных затрат электроэнер- |
|
быть достигнуто повышение производительности |
гии на деформацию на стане 390 от суммарной |
|
на 25 %. При прокатке профиля № 18 в одну |
вытяжки (рис. 11). |
|
нитку на максимальной скорости достигается уже |
|
ОАО «Черметинформация» • Бюллетень «Черная металлургия» • 7• 2011 ―――――――――――――――― 63

2011 7• • »металлургия Черная« Бюллетень • »Черметинформация« ОАО――――――――――――――――― 64
ТАБЛИЦА 3. РЕЖИМЫ ТЕРМОУПРОЧНЕНИЯ И МЕХАНИЧЕСКИЕ СВОЙСТВА АРМАТУРНЫХ ПРОФИЛЕЙ КЛАССА А500 ПО ДСТУ 3760 98
Номер |
|
Vпр, |
tауст, |
Марка |
Тип |
|
Давление Рф, ати |
|
|
Tхол, С |
0,2, МПа |
в, МПа |
||||||
про- |
Партия |
|
|
|
|
|
Tсо, С |
|
|
|
|
|
|
|||||
м/с |
С |
стали |
трубы |
KR2 |
KR3 |
KR4 |
KR5 |
KR6 |
расчет. |
испыт. |
расчет. |
испыт. |
расчет. |
испыт. |
||||
филя |
|
|
||||||||||||||||
|
|
|
|
|
|
|
|
|
|
|
|
|
|
|
|
|
||
18 |
66 |
10,5 |
945 |
Ст3сп |
Ду42 |
10 |
10 |
11 |
|
|
602 |
590 |
575 |
553 |
544 |
661 |
648 |
|
14 2 |
81 |
10,5 |
980 |
Ст3сп |
Ду33 2 |
7 |
7 |
7 |
|
|
518 |
499 |
550 |
676 |
682 |
798 |
772 |
|
16 |
241 |
9,5 |
960 |
Ст3сп |
Ду42 |
14 |
14 |
|
|
|
578 |
559 |
570 |
574 |
582 |
684 |
673 |
|
10 2 |
341 |
11,4 |
945 |
Ст4сп |
Ду33 2 |
19 |
|
|
|
|
632 |
593 |
580 |
535 |
545 |
639 |
631 |
|
10 2 |
343 |
11,4 |
938 |
Ст4сп |
Ду33 2 |
15 |
|
|
|
|
645 |
604 |
590 |
511 |
507 |
615 |
612 |
|
25 |
570 |
8,5 |
972 |
Ст4сп |
Ду48 |
16 |
16 |
16 |
16 |
|
576 |
570 |
580 |
590 |
607 |
692 |
697 |
|
28 |
818 |
7,1 |
990 |
Ст4сп |
Ду48 |
18 |
18 |
18 |
18 |
|
613 |
607 |
620 |
540 |
537 |
647 |
658 |
|
32 |
866 |
5,5 |
1040 |
Ст4сп |
Ду48 |
18 |
18 |
18 |
17 |
14 |
584 |
580 |
570 |
556 |
548 |
665 |
668 |
Примечание: Vпр скорость прокатки; tауст температура аустенизации металла; тип трубы типоразмер охлаждающей трубы; KR2 KR6 номера секций охлаждения; tсо температура самоотпуска, tхол температура поверхности металла перед реечным холодильником.

Рис. 10. Изменение удельных затрат электроэнергии Ауд на прокатку арматурных профилей № 12−№ 20 по традиционной технологии и ДПР от суммарной вытяжки μсум
Впоследствии технология ДПР арматурных профилей № 16, № 18 и № 20 была разработана и внедрена специалистами завода.
В 2010 г. стан 390 вышел на проектную мощность.
|
Заключение |
|
|
Впервые за последние 10 лет на Украине вве- |
|
|
ден в эксплуатацию новый сортопрокатный стан |
|
|
390 широкого сортамента, оснащенный современ- |
|
|
ными оборудованием и средствами автоматизиро- |
|
Рис. 11. Статистическая зависимость суммарных |
ванного управления и контроля состояния обору- |
|
дования и технологии, способный производить как |
||
удельных затрат электроэнергии Ауд на прокатку |
||
профили строительного сортамента, так и сорто- |
||
арматурных профилей № 12−№ 20 от суммарной |
||
вой прокат повышенной точности. |
||
вытяжки μсум |
||
|
БИБЛИОГРАФИЧЕСКИЙ СПИСОК
1.Солод В. С., Бенецкий А. Г., Мамаев А. Н. Моделирование процесса сортовой прокатки с помощью программного комплекса “Сорт-Про”. Обработка материалов давлением // Сб. научн. трудов. Донбасская государственная машиностроительная академия. 2010. № 3 (24). С. 60−63.
2.Новые математические модели процессов сортовой прокатки / В. С. Солод, А. Г. Бенецкий, А. В. Харченко, М. Н. Тытюк // Труды I Междунар. научно-практич. конф. ИНТЕХМЕТ 2008. СПб., 9−10 сентября 2008 г. С. 280−283.
ОАО «Черметинформация» • Бюллетень «Черная металлургия» • 7• 2011 ―――――――――――――――― 65

УДК 621.774.38 И. Ю. ПЫШМИНЦЕВ1, д.т.н.; А. В. ВЫДРИН1, д.т.н.; Я. И. КОСМАЦКИЙ1, В. Б. ВОСХОДОВ2, В. В. АНАНЯН2, А. М. ЗУБКОВ2, С. А. ДЕНИСЮК2, А. П. ШЛЯМНЕВ3, к.т.н.
( 1 ОАО “Российский научно-исследовательский институт трубной промышленности”, 2 ОАО “Волжский трубный завод”, 3 ФГУП “ЦНИИчермет им. И.П. Бардина”)
АНАЛИЗ РЕЗУЛЬТАТОВ ОПЫТНО-ПРОМЫШЛЕННОГО ПРОИЗВОДСТВА ТРУБ ИЗ НОВОЙ КОРРОЗИОННОСТОЙКОЙ СТАЛИ
Одним из перспективных направлений разви- |
В настоящее время в ОАО “РосНИТИ” разрабо- |
тия трубной промышленности является исполь- |
тана технологическая схема изготовления труб из |
зование при производстве труб новых видов |
стали 03Х17Н9АМ3, предусматривающая выплавку |
коррозионностойких сталей и сплавов, обла- |
и подготовку трубной заготовки с наружным диа- |
дающих более высокой стойкостью по отноше- |
метром 170 мм в ОАО “Златоустовский металлурги- |
нию к различным видам коррозии. Применение |
ческий завод” (ЗМЗ), последующее производство |
таких труб позволит увеличить в первую очередь |
передельной горячепрессованной трубы размером |
количество используемых месторождений нефти |
89×9 мм в ОАО “Волжский трубный завод” (ВТЗ) и |
и газа за счет использования месторождений с |
окончательное изготовление холоднодеформиро- |
агрессивными средами. |
ванных труб размерами 32×3, 20×2, 16×1,5 мм в |
Для производства труб повышенной коррози- |
ОАО “Синарский трубный завод”. |
онной стойкости ФГУП “ЦНИИчермет им. И.П. |
Выбор в качестве поставщика заготовки ОАО |
Бардина” совместно с ОАО “РосНИТИ” была |
ЗМЗ был сделан на основе имеющегося у него |
предложена новая сталь 03Х17Н9АМ3, защи- |
богатого опыта освоения новых сложнолегиро- |
щенная патентом РФ [1]. Заявленная марка |
ванных сплавов и наличия соответствующего |
стали близка по химическому составу к стали |
оборудования сталеплавильного комплекса для |
03Х17АН9-В, но отличается от нее тем, что она |
производства малотоннажных опытных партий. |
дополнительно содержит гафний в количестве |
Для поставки трубной заготовки в ОАО “РосНИТИ” |
0,001–0,01 %. Микролегирование гафнием влия- |
разработаны и согласованы между ОАО ВТЗ и |
ет на уменьшение склонности к росту аустенит- |
ОАО ЗМЗ соответствующие технические условия. |
ного зерна в интервале температур горячей об- |
Проведенные металлографические исследо- |
работки давлением. Кроме этого влияние гафния |
вания показали, что микроструктура металла за- |
проявляется в изменении тонкой структуры ау- |
готовки имеет аустенитную структуру с незначи- |
стенита, а именно в уменьшении зон предвыде- |
тельным количеством δ-феррита. Оценку коли- |
ления карбидной фазы. Это должно повышать |
чества ферритной фазы в металле заготовки |
стойкость стали к различным видам коррозии. |
проводили неразрушающим способом при по- |
Для оценки эксплуатационных свойств, таких |
мощи локального ферритометра ФХ-3 ИФМ. Ко- |
как прочностные характеристики, устойчивость к |
личество ферритной фазы составляет 1±0,1 %. |
воздействию химических соединений и активных |
Как показано на рис. 1, размер зерна аустенита |
веществ, труб из разработанной коррозионно- |
на наружной поверхности составляет номер 6, 7 |
стойкой стали была изготовлена опытно-про- |
по ГОСТ 5639−82, в средней части заготовки |
мышленная партия. |
номер 5, 6, в центре номер 3−5. |
Рис. 1. Микроструктура металла трубной заготовки из стали 03Х17Н9АМ3 (слева направо от наружной поверхности к центру заготовки)
66 ―――――――――――――――――ОАО «Черметинформация» • Бюллетень «Черная металлургия» • 7• 2011
Анализ результатов проведенных механиче- |
соответствии с картой раскроя подготовлено |
||||||||||||||
ских испытаний образцов, изготовленных из тем- |
семь заготовок длиной 540 мм (6 шт.) и 520 мм |
||||||||||||||
плета трубной заготовки, показал, что требова- |
(1 шт.). В заготовках выполнено сверление диам. |
||||||||||||||
ния к механическим характеристикам металла |
25 мм и произведена обработка торцов. |
|
|||||||||||||
трубной заготовки, оговоренные в согласован- |
|
Для определения силовых параметров про- |
|||||||||||||
ном между ОАО ЗМЗ и ОАО ВТЗ техническом |
цесса прессования труб из стали 03Х17Н9АМ3 |
||||||||||||||
протоколе, были выполнены. Например, времен- |
на прессовой линии 20 МН в соответствии с ре- |
||||||||||||||
ное сопротивление σв находится в интервале |
комендациями, приведенными в работе [2], оп- |
||||||||||||||
652−655 МПа при утвержденном в техническом |
ределен модуль сопротивления деформации, |
||||||||||||||
протоколе не менее 600 МПа, а относительное |
величина которого составила 265−275 МПа, что |
||||||||||||||
удлинение δ5 43−50 % при утвержденном не |
предопределило пиковую нагрузку пресса, рав- |
||||||||||||||
менее 40 %. |
|
|
|
|
|
|
ную 14,7−15,3 МН. |
|
|
|
|
|
|||
Для производства опытной партии труб раз- |
|
Прессование труб на прессовой линии 20 МН |
|||||||||||||
мером 89×9 мм была задана в производство в |
ТПЦ № 2 ОАО ВТЗ проводилось при темпера- |
||||||||||||||
ОАО ВТЗ одна трубная заготовка массой 0,7 т, |
туре нагрева заготовок в вертикальной индукци- |
||||||||||||||
имеющая наружный диаметр 170 мм и длину |
онной печи до 1160−1180 °С. Фактические пара- |
||||||||||||||
3880 мм. Заготовка была обточена на станке |
метры процесса прессования и геометрические |
||||||||||||||
VDHI-250 до наружного диаметра 164+0,3 мм. В |
размеры готовых труб представлены в табл. 1. |
||||||||||||||
|
|
ТАБЛИЦА 1. ПАРАМЕТРЫ ПРЕССОВАНИЯ ТРУБ ИЗ СТАЛИ 03Х17Н9АМ3 |
|
|
|
||||||||||
|
|
|
|
НА ЛИНИИ 20 МН ТПЦ № 2 ОАО ВТЗ |
|
|
|
|
|
||||||
|
|
|
|
|
|
|
|
|
|
|
|
|
|
|
|
Номер |
Экспандирование |
|
|
Прессование |
|
|
Геометрические параметры труб |
|
|||||||
заго- |
|
|
|
|
|
|
|
|
|
|
|
|
|
|
|
Tзаготовки, |
Vэкспанд, |
Tгильз, |
Vпресс, |
|
P, МН |
|
Pпик, |
Tтруб, |
hmin−max, |
hср, |
Dmin−max, |
Dср, |
|
L, мм |
|
товки |
°С |
мм/с |
°С |
мм/с |
|
|
МН |
°С |
мм |
мм |
мм |
мм |
|
||
1 |
1090 |
220 |
1177 |
240 |
|
10,5 |
|
14,9 |
1200 |
8,1–9,8 |
9,1 |
89,0−89,2 |
89,1 |
|
4630 |
2 |
1105 |
230 |
1158 |
220 |
|
10,7 |
|
16,3 |
1195 |
8,5–9,7 |
9,0 |
88,8−89,1 |
88,9 |
|
4622 |
3 |
1092 |
220 |
1156 |
210 |
|
11,3 |
|
16,3 |
1195 |
8,4–9,8 |
9,0 |
88,8−89,1 |
89,0 |
|
4560 |
4 |
1100 |
220 |
1157 |
220 |
|
11,1 |
|
16,7 |
1195 |
8,5–9,6 |
9,0 |
88,7−89,2 |
89,0 |
|
4460 |
5 |
1092 |
220 |
1178 |
220 |
|
10,9 |
|
16,2 |
1210 |
8,6–9,6 |
9,0 |
88,9−89,2 |
89,1 |
|
4560 |
6 |
1094 |
210 |
1153 |
210 |
|
11,5 |
|
16,8 |
1195 |
8,7–9,7 |
9,0 |
88,8−89,2 |
89,0 |
|
4600 |
7* |
1090 |
220 |
1163 |
202 |
|
11,0 |
|
15,7 |
1200 |
8,6–9,4 |
9,0 |
88,8−89,3 |
89,0 |
|
4222 |
* От данной трубы отбирались образцы для подбора режима химической обработки (расстеклования). |
|
|
|
Трубы из стали 03Х17Н9АМ3 аттестовались с применением требований ТУ 14-3Р-85−2005 на передельные горячепрессованные трубы из нержавеющих сталей и сплавов, механические свойства которых, в свою очередь, определяются требованиями ГОСТ 9940–81. В то же время, поскольку новая сталь 03Х17Н9АМ3 не предусмотрена ГОСТ 9940–81, требования к механическим свойствам металла труб были установлены факультативными. В результате испытаний на статическое растяжение по ГОСТ 1497– 84 и испытаний на ударный изгиб, проведенных по ГОСТ 9454–78, были определены механические свойства заявленной стали. Анализ результатов проведенных механических испытаний показал, что механические свойства горячепрессованных труб соответствовали требованиям ГОСТ 9940–81, например временное сопротивление σв находится в интервале 688−697 МПа, относительное удлинение δ5 составило 50 %.
Как известно, при разработке технологии любого процесса обработки металлов давлением в горячем состоянии необходимо иметь зависимость сопротивления этого металла пластической деформации от термомеханических параметров процесса.
Для получения такой зависимости, описывающей деформационное поведение стали 03Х17Н9АМ3, на автоматизированном кулачковом пластометре Южно-Уральского государственного университета проведены испытания на осадку цилиндрических образцов [3], изготовленных из темплета трубной заготовки стали
03Х17Н9АМ3.
Диапазоны изменения скорости, степени и температуры деформации в процессе проведения пластометрических исследований были выбраны с учетом значений этих показателей, имеющих место при прессовании труб: температура испытаний 1050−1200 °С, степень де-
формации 0,1−0,9, скорость деформации
0,1−20 с–1.
Для аппроксимации экспериментальной информации выбрана формула, полученная на основе метода термомеханических коэффициентов:
σsc = k0UckU ε1kε exp(−kθθ).
Для определения значений эмпирических коэффициентов k0, kε, kθ, kU использовался метод наименьших квадратов. В результате получено
ОАО «Черметинформация» • Бюллетень «Черная металлургия» • 7• 2011 ―――――――――――――――― 67

σsc = 3506,3Uс0,0897ε10,1668e−0,00289t .
где Uc средняя скорость деформации, с–1; ε1 конечная степень деформации; t температура деформации, °С.
Коэффициент множественной корреляции при статистической обработке данных, полученных в
процессе проведения исследований, составил
R2 = 0,926.
По полученной зависимости сопротивления стали 03Х17Н9АМ3 пластической деформации для реальных деформационных условий (ε1 = = 2,15, Uc = 19,5 с–1) процесса прессования труб размером 89×9 мм были определены значения сопротивления деформации стали 03Х17Н9АМ3. Для сравнения на рис. 2 представлены графики зависимости сопротивления деформации стали 03Х17Н9АМ3 и 12Х18Н10Т при разной температуре нагрева металла.
Рис. 2. Зависимость сопротивления деформации от температуры прессования труб для деформационных
условий процесса: ε1 = 2,15, Uc = 19,5 с–1
Полученные данные показывают, что с увеличением температуры нагрева от 1100 до 1200 °С разница между средним значением сопротивления деформации стали 03Х17Н9АМ3 и 12Х18Н10Т увеличивается от 13,3 до 25 МПа.
Для сравнения на рис. 3 представлены графики зависимости сопротивления деформации от степени деформации стали 12Х18Н10Т и 03Х17Н9АМ3 для деформационных условий процесса прессования труб: Т = 1140 °С, Uc = 19 с–1.
Рис. 3. Зависимость сопротивления деформации от степени деформации для деформационных условий процесса прессования труб: Т = 1140 °С, Uc = 19 с–1
Анализ графиков зависимостей сопротивления деформации от степени деформации (см. рис. 3) показывает, что с увеличением степени деформации от 1,8 до 2,4 разница между средним значением сопротивления деформации стали 03Х17Н9АМ3 и 12Х18Н10Т увеличивается от 16,5 до 20,5 МПа.
Расчет пикового усилия прессования производился по зависимости Ж. Сежурне [4], так как названная формула была выведена с учетом особенностей прессования стали и многократно проверялась, что показывает сходимость с экспериментальными данными, приведенными в работе [5]. Для реального диапазона температуры гильз 1153−1178 °С расчетное пиковое усилие прессования, определенное по зависимости Ж. Сежурне, с использованием полученной экспериментальной зависимости составило 14,5−15,75 МН. Это подтверждает возможность использования прессового оборудования ОАО ВТЗ для получения передельных труб из стали 03Х17Н9АМ3. С учетом выполненных исследований была разработана технология и проведено опытное прессование труб.
Анализ результатов прессования опытной партии труб стали 03Х17Н9АМ3 показал практическое совпадение результатов определения силовых параметров процесса при использовании различных методик определения сопротивления деформации (табл. 2).
ТАБЛИЦА 2. СИЛОВЫЕ ПАРАМЕТРЫ ПРЕССОВАНИЯ ТРУБ С НАРУЖНЫМ ДИАМЕТРОМ 89 мм С ТОЛЩИНОЙ СТЕНКИ 9 мм ИЗ СТАЛИ 03Х17Н9АМ3 НА ЛИНИИ 20 МН ТПЦ № 2 ВТЗ
|
Расчетные значения |
Экспериментальные |
|
Параметр |
|
по результатам |
значения (по итогам |
по зависимости, |
|||
|
приведенной в работе |
пластометрических |
изготовления опытной |
|
[2] |
исследований |
партии труб) |
Температура деформации, °С |
1140–1160 |
1140–1160 |
1153–1178 |
Сопротивление деформации, МПа |
265–275 |
181,8–192,2 |
|
Пиковое усилие прессования, МН |
14,7–15,3 |
14,50–15,75 |
14,90–16,80 |
68 ―――――――――――――――――ОАО «Черметинформация» • Бюллетень «Черная металлургия» • 7• 2011

Анализ приведенных данных показывает, что |
Исследование микроструктуры металла горя- |
полученная эмпирическая зависимость позво- |
чепрессованной трубы проводили методом оп- |
ляет достаточно точно определить сопротивле- |
тической металлографии на продольных образ- |
ние деформации и, соответственно, силовые па- |
цах. Для выявления структуры использовалась |
раметры процесса прессования. Относительная |
методика электролитического травления в кон- |
разность величины пикового усилия, определен- |
центрированной азотной кислоте. На рис. 4 при- |
ной по формуле Ж. Сежурне с использованием |
ведена микроструктура металла горячепрессо- |
результатов пластометрических исследований и |
ванной трубы из стали 03Х17Н9АМ3. |
зарегистрированной в реальном технологиче- |
|
ском процессе, не превысила 7,2 %. |
|
Рис. 4. Микроструктура металла горячепрессованной трубы размером 89×9 мм из стали 03Х17Н9АМ3 (слева направо от наружной поверхности к внутренней)
По результатам исследований микрострук- |
однородную и благоприятную с точки зрения ме- |
туры металла заготовки и горячепрессованных |
таллографии микроструктуру. |
труб из стали 03Х17Н9АМ3 сделаны следующие |
Стойкость к межкристаллитной коррозии |
выводы. |
(МКК) металла горячепрессованной трубы опре- |
1. Микроструктура металла горячепрессован- |
деляли методом АМУ по ГОСТ 6032−2003. Для |
ной трубы имеет аустенитную структуру с незна- |
испытаний на МКК образцы подвергали прово- |
чительным количеством δ-феррита. Количество |
цирующему нагреву до температуры 650 °С с |
ферритной фазы на внутренней поверхности со- |
продолжительностью выдержки 1 ч и выдержке в |
ставляет 1,5 балла, 1 балл в центральной части |
кипящем водном растворе сернокислой меди и |
толщины стенки и на наружной поверхности. |
серной кислоты в присутствии медной стружки в |
Размер зерна аустенита составляет номер 7, 9 |
течение 8 ч. |
по ГОСТ 5639−82. Количество ферритной фазы в |
Для обнаружения МКК образцы подвергли из- |
металле заготовки составляет 1±0,1 %. Размер |
гибу на угол 90 град. Осмотр изогнутых образцов |
зерна аустенита на наружной поверхности со- |
с помощью лупы показал отсутствие трещин как |
ставляет номер 6, 7, в средней части заготовки |
на образцах после провоцирующего отжига, так |
номер 5, 6, в центре номер 3−5 по ГОСТ |
и на контрольных образцах. |
5639−82. |
В образцах, отобранных от горячепрессован- |
2. Горячепрессованные трубы, изготовленные |
ной трубы, трещин не обнаружено, что свиде- |
с последующим охлаждением на воздухе, имеют |
тельствует об их стойкости к МКК. |
БИБЛИОГРАФИЧЕСКИЙ СПИСОК
1.Пат. 2413031 РФ, МПК7 С 22 С 38/58, С 22 С 38/54. Аустенитная коррозионностойкая сталь для хлоридсодержащих сред и изделие, выполненное из нее / Е. Х. Шахпазов, А. П. Шлямнев, Г. А. Филиппов и др.; № 2009137647/02; заявл. 13.10.09; опубл. 27.02.11. Бюл. № 6. 8 с.
2.Медведев М. И., Беспалова Н. А., Царьков А. К. Методика определения основных параметров прессования труб из труднодеформируемых сталей и сплавов // Металлургическая и горнорудная промышленность. 2007. № 3. С. 56–59.
3.Крайнов В. И. Оборудование, методика, результаты пластометрических исследований: Учебное пособие. Челябинск: Изд-во ЧГТУ. 1995. 95 с.
4.Горячее прессование труб и профилей / Ю. В. Манегин, А. Е. Притоманов, Т. Шпиттель, А. Кнаушнер. М.: Металлургия. 1980. 272 с.
5.Прессование стальных труб и профилей / Г. И. Гуляев, А. Е. Притоманов, О. П. Дробич, В. В. Верховод. М.: Металлургия. 1973. 192 с.
ОАО «Черметинформация» • Бюллетень «Черная металлургия» • 7• 2011 ―――――――――――――――― 69

УДК 621.778 А. Н. САВЕНОК1, А. В. ВЕДЕНЕЕВ1, О. И. ИГНАТЕНКО1, Ю. Л. БОБАРИКИН2, М. Н. ВЕРЕЩАГИН2, М. Ю. ЦЕЛУЕВ2 ( 1 РУП “Белорусский металлургический завод”,
2 Гомельский государственный технический университет им. П.О. Сухого)
ИСПОЛЬЗОВАНИЕ ТЕМПЕРАТУРНОГО КРИТЕРИЯ ДЛЯ ОПТИМИЗАЦИИ ГЕОМЕТРИИ ДЕФОРМИРУЮЩЕЙ И КАЛИБРУЮЩЕЙ ЗОН КАНАЛА ВОЛОКИ
Оптимизацию |
геометрии деформирующей и |
также физические уравнения связи из теории |
||||||
калибрующей зон канала волоки |
связывают с |
пластичности и теории упругости. |
|
|||||
поиском таких |
геометрических |
характеристик |
Решение рассматриваемой задачи осущест- |
|||||
этих зон, которые обеспечивают минимальное |
вим в цилиндрической системе координат при |
|||||||
усилие волочения проволоки. Под каналом во- |
следующих основных упрощениях: |
|||||||
локи понимается форма и размеры деформи- |
1. Напряженно-деформированное и темпера- |
|||||||
рующей и калибрующей зон волоки. Однако кри- |
турное состояние материала проволоки считаем |
|||||||
терий оптимизации по минимальному усилию |
асимметричным, для чего будем пренебрегать |
|||||||
волочения не обеспечивает минимальные тем- |
внешними массовыми силами. |
|
||||||
пературы в очаге деформации при волочении |
2. Считаем, что в процессе пластического |
|||||||
проволоки ввиду сложности распределения тем- |
деформирования в объеме проволоки действует |
|||||||
пературных полей в деформируемой проволоке |
распределенный источник тепловой энергии, |
|||||||
[1]. Оптимальной геометрией волоки по темпера- |
равный 90 % работы пластического деформиро- |
|||||||
турному критерию принимается такой вариант |
вания. |
|
|
|
|
|||
геометрии канала волоки, при котором прово- |
3. На поверхности контакта проволоки и во- |
|||||||
лока при протяжке через эту волоку нагревается |
локи действуют силы трения Амонтона−Кулона и |
|||||||
до минимальной температуры сравнительно с |
распределенный источник тепловой энергии, |
|||||||
другими геометриями канала волоки. Это обес- |
равный 50 % работы сил трения. Через поверх- |
|||||||
печивает снижение динамического деформаци- |
ность контакта между волокой и проволокой |
|||||||
онного старения стальной проволоки и, как след- |
осуществляется теплопередача по закону Нью- |
|||||||
ствие, уменьшение падения ее пластичности, а |
тона |
с |
коэффициентом |
теплопередачи |
||||
также снижение |
износа волок и температурного |
α = 15×104 Вт/(м2 °С). |
|
|
||||
окисления технологических смазок. |
4. Материал проволоки считаем деформаци- |
|||||||
Для решения поставленной задачи использо- |
онно и кинематически упрочняемой упруго-пла- |
|||||||
вался численный метод расчета деформации |
стической средой с плотностью ρ = 7745 кг/м3, |
|||||||
проволоки при волочении с помощью метода ко- |
модулем Юнга Е = 207 ГПа, коэффициентом Пу- |
|||||||
нечных элементов и методов математической |
ассона μ = 0,3 и зависимостью сопротивления |
|||||||
статистики. |
|
|
пластическому деформированию: |
|
||||
В основе математической формулировки рас- |
σs = [1,374 + 0,114 lg(ξi)][999 + 544,31 ln(εi)], МПа, |
|||||||
сматриваемого процесса волочения проволоки |
||||||||
|
|
|
|
|
||||
лежит система зависимостей механики дефор- |
где ξi интенсивность скоростей деформаций, |
|||||||
мируемого твердого тела: уравнения движения, |
εi интенсивность деформаций. |
пластическому |
||||||
неразрывности, связи деформаций и перемеще- |
Зависимость сопротивления |
|||||||
ний, связи скоростей деформаций и скоростей |
деформированию от |
деформации материала |
||||||
перемещений, связи ускорений и скоростей, |
проволоки |
получили |
аппроксимацией методом |
|||||
уравнение теплопроводности [1−5]. Замыкают |
наименьших квадратов экспериментальных дан- |
|||||||
систему данных уравнений начальные условия, |
ных, полученных при стандартных испытаниях |
|||||||
описывающие конфигурацию проволоки и во- |
проволоки из стали 90К на растяжение, с после- |
|||||||
локи, их температурное и деформированное |
дующей корректировкой по скорости деформа- |
|||||||
поле в начальный момент времени; граничные |
ции на основе литературных данных [5]. Тепло- |
|||||||
условия, описывающие приложенные к ограни- |
физические характеристики материала прово- |
|||||||
чивающим поверхностям проволоки и волоки ки- |
локи: коэффициент теплопроводности λ = 49 |
|||||||
нематические и |
энергосиловые |
параметры, а |
Вт/(м °С), теплоемкость с = 477 Дж/(кг °С). |
70 ―――――――――――――――――ОАО «Черметинформация» • Бюллетень «Черная металлургия» • 7• 2011

5. Материал волоки считаем упругой средой с |
Численные исследования волок с конической |
плотностью ρ = 15150 кг/м3, модулем Юнга Е = |
деформирующей зоной выполнялись для волок |
647 ГПа, коэффициентом Пуассона μ = 0,2. Теп- |
тонкого волочения, которые применяются на |
лофизические характеристики материала во- |
РУП “Белорусский металлургический завод” |
локи: коэффициент теплопроводности λ = 50,2 |
(БМЗ) (рис. 1). |
Вт/(м °С), теплоемкость с = 382 Дж/(кг °С). |
|
Рис. 1. Схема волоки с конической деформирующей зоной (lk длина калибрующей зоны; α угол конической деформирующей зоны)
Для волоки с определенной длиной калибрующей зоны lk оптимальной геометрии волоки будет соответствовать оптимальный угол конической деформирующей зоны волоки αопт. Для поиска αопт необходимо получить распределения температур в проволоке при волочении при разных углах волоки и при неизменном значении lk. После этого можно выбрать вариант волоки с минимальным значением пиковых или максимальных температур в температурном поле проволоки. Таким образом, необходимо исследовать весь диапазон углов деформирующих зон волоки и длин калибрующих зон волоки и найти соответствие между углом деформирующей волоки и длиной калибрующей зоны, которое определяет минимальный нагрев проволоки. Чтобы каждому значению lk привести в соответствие определенное значение αопт, необходимо также учесть уровень усилий волочения P и коэффициентов запаса волочения γ. Это увеличивает степень объективности представленных исследований.
Из полученных температурных полей в проволоке при ее волочении из численных моделей определено, что имеют место два температурных пика в проволоке: на выходе из калибрую-
щей зоны волоки T1max, в месте входа в калибрующую часть волоки T2max (рис. 2).
Рис. 2. Температурный цикл поверхности проволоки для α = 12 град., k = 0,4, f = 0,05
Для упрощения длину lk можно представить в виде относительной длины калибрующей зоны:
k = lk/dк,
где dк диаметр волоки в калибрующей зоне. Расчеты выполнялись для наиболее нагру-
женной волоки с номинальным диам. 0,467 мм в действующем на РУП БМЗ маршруте волочения для изготовления сверхвысокопрочной проволоки диам. 0,41 мм. При изготовлении тонкой проволоки использовалась латунированная заго-
ОАО «Черметинформация» • Бюллетень «Черная металлургия» • 7• 2011 ―――――――――――――――― 71

товка диам. 2,45 мм (сталь 90К), скорость волочения составила 8 м/с. Методика расчета может использоваться для других волок маршрута волочения по аналогии.
Результаты численного расчета величин T1max, T2max, P, γ в зависимости от значений углов кони-
ческой деформирующей зоны волоки α и значений k приведены в таблице, которая представляет собой план численного эксперимента из 18 опытов с факторами α и k, совмещенный со значениями откликов эксперимента T1max, T2max, P, γ.
ЗНАЧЕНИЯ ПАРАМЕТРОВ ВОЛОЧЕНИЯ ПРИ КОЭФФИЦИЕНТЕ КОНТАКТНОГО ТРЕНИЯ f = 0,05
Номер опыта |
α, град. |
k |
T1max, °C |
T2max, °C |
P, Н |
γ |
1 |
6 |
0,3 |
513 |
474,3 |
172 |
2,8 |
2 |
10 |
0,3 |
450,8 |
464,1 |
157,3 |
3,1 |
3 |
12 |
0,3 |
414,5 |
454,2 |
158,2 |
3,0 |
4 |
14 |
0,3 |
403,2 |
460,5 |
160,5 |
3,0 |
5 |
16 |
0,3 |
390,6 |
480,5 |
163,5 |
2,9 |
6 |
20 |
0,3 |
383,6 |
497,3 |
173,4 |
2,8 |
7 |
6 |
0,4 |
534,3 |
473,7 |
180,3 |
2,7 |
8 |
10 |
0,4 |
452,4 |
462,7 |
163,6 |
2,9 |
9 |
12 |
0,4 |
427,8 |
451,7 |
161,7 |
3,0 |
10 |
14 |
0,4 |
404,8 |
457,3 |
163,6 |
2,9 |
11 |
16 |
0,4 |
390,4 |
479,5 |
166,4 |
2,9 |
12 |
20 |
0,4 |
381,9 |
506,4 |
175,4 |
2,7 |
13 |
6 |
0,5 |
543 |
473,3 |
188,6 |
2,5 |
14 |
10 |
0,5 |
454,8 |
461,9 |
170,7 |
2,8 |
15 |
12 |
0,5 |
430,1 |
449,1 |
168,6 |
2,8 |
16 |
14 |
0,5 |
404,8 |
454 |
166,7 |
2,9 |
17 |
16 |
0,5 |
400,9 |
476,1 |
169,4 |
2,8 |
18 |
20 |
0,5 |
393,6 |
499,6 |
177,1 |
2,7 |
Анализ значений параметров таблицы показывает, что на условия волочения удовлетворительны исходя из величин P и γ. Но значения
T1max, T2max не позволят получить требуемое качество стали из-за повышенных величин. Диапазон
полученных температур достаточно широк и указывает на влияние геометрии волоки на температуру проволоки.
Для вычислительного опыта № 9 (см. таблицу) получен график термического цикла произвольной точки поверхности проволоки (см. рис. 2). На графике горизонтальный отрезок линии слева внизу соответствует величине температуры поверхности проволоки на входе в волоку. Затем наблюдается интенсивный рост температуры при движении проволоки через деформирующую зону. Первый температурный пик T2max приходится на зону стыковки деформирующей и калибрующей зон. Второй температурный пик T1max относится к зоне окончания калибрующего пояска. Величина температуры поверхности после выхода проволоки из волоки уменьшается. Интересен факт спада температуры между
двумя пиками: T1max меньше, чем T2max. Объяснения поведения температурной кривой связаны с
тем, что до первого пика источником тепловыделения служит энергия внутреннего трения (или пластической деформации), а также энергия контактного трения. После второго пика основной
вклад в нагрев поверхности проволоки вносит контактное трение.
Данные, представленные в таблице, описываются следующими математическими зависимостями, полученными обработкой данных этой таблицы по плану регрессионного анализа:
1) максимальная температура проволоки на выходе из волоки, °С:
T1max = 439,9 − 13,8α + 0,8α2 + 992,3k − 826k2 −
−59,8αk − 0,8α2k + 24,6αk2 + 2,7α2k2; |
(1) |
2) максимальная температура проволоки на входе в калибрующую зону волоки, °С:
T2max = 396,5 + 17,7α − 0,9α2 + 639,2k − 712,3k2 −
−146,1αk − 7,2α2k + 163,5αk2 − 8,3α2k2; |
(2) |
3) усилие волочения проволоки, Н: |
|
Р = 140,2 + α + 258,5k − 155,9k2 − 38,5αk + |
|
+1,4α2k + 37αk2 − 1,5α2k2. |
(3) |
Используя уравнения (1)−(3), можно вычислять величины данных параметров для других значений α и k, не вошедших в таблицу.
Уравнения (1) и (2) графически представляют собой криволинейные поверхности (рис. 3 и 4).
Совмещение поверхностей рис. 3 и 4 позволяет получить поверхность, изображенную на рис. 5. Анализ поверхности на рис. 5 показывает, что есть возможность провести линию на этой
72 ―――――――――――――――――ОАО «Черметинформация» • Бюллетень «Черная металлургия» • 7• 2011

поверхности, для которой характерна минимальная температура, выбранная из максимальных значений для определенного значения α при постоянном значении величины k. Эту линию можно представить в виде графика (рис. 6). Этот график приводит в соответствие длину калибрующей зоны, выраженную через k с оптимальным углом деформирующей зоны волоки αопт. Значения αопт не постоянны и для определенной длины калибрующей зоны принимают свое значение. На линии отмечены численные значения максимальных температур в проволоке, соответствующие точкам графика, где размещены эти цифры. Анализ этих цифр указывает на практическое постоянство минимальных значений температур при различных значениях длин калибрующей зоны волоки.
Т |
|
, o C |
|
|
|
|
|
|
|
|
1 max |
|
|
|
|
|
|
|
|
|
|
500 |
|
|
|
|
|
|
|
|
||
T1 max, °C |
500 |
|
|
|
|
|
|
|
0,5 |
|
|
450 |
|
|
|
|
|
|
|
|
|
|
|
4000 |
|
|
|
|
|
|
0,4 |
|
|
|
40 |
|
|
|
|
|
0 |
|
5 |
|
|
|
|
|
|
|
|
|
|
|
|
|
|
|
|
|
|
|
, |
|
|
|
|
10 |
|
|
|
|
|
|
4 |
k |
|
|
1 |
|
|
|
0 |
|
|
||
|
|
|
|
|
|
|
|
|
||
|
|
|
5 |
|
|
, |
|
|
||
|
|
α |
|
|
|
3 |
|
|
||
|
|
|
|
|
|
|
5 |
|
|
|
|
|
, г |
|
|
|
|
|
|
|
|
|
|
р |
|
|
|
|
|
|
|
|
|
|
|
ад. |
2 |
0 |
0 |
|
|
|
|
|
|
|
|
|
|
|
|
|||
|
|
|
|
|
|
|
, |
|
|
|
|
|
|
|
|
|
|
3 |
|
|
|
Рис. 3. Графическая зависимость максимальной температуры T1max проволоки на выходе из волоки от угла деформирующей зоны α и относительной длины калибрующей зоны k при коэффициенте контактного трения f = 0,05
Тмах, o C |
|
540 |
|
|
0 |
Tmax,°C |
54 |
520 |
|
|
0 |
|
52 |
|
500 |
|
500 |
|
480 |
|
480 |
|
460 |
|
460 |
10 α, град.
15
20
|
|
|
0, |
|
|
|
5 |
|
|
|
0.5 |
|
0, |
|
|
|
|
0.45 |
|
|
|
4 |
|
|
00.4 |
5 |
|
|
k |
||
|
,4 |
k |
|
0.353 |
|
||
|
|
||
0 |
|
|
|
, |
|
|
|
|
5 |
|
|
0 |
|
|
|
, |
|
|
|
3 |
|
|
|
0.3 |
|
|
|
Рис. 5. Графическая зависимость максимальной температурыпроволокиTmax отугладеформирующейзоныα и относительной длины калибрующей зоны k
при коэффициенте контактного трения f = 0,05
Т2 mах , o C 500 0
T2 max, ° C |
|
|
|
|
|
|
0, |
|
|
|
|
|
|
5 |
|
480 |
|
|
|
|
0 |
|
|
|
|
|
|
|
|
||
|
|
|
|
|
|
, |
|
464 60 |
|
|
|
|
|
4 |
|
0 |
|
|
|
|
|
|
5 |
|
|
|
|
0 |
|
|
|
|
|
|
|
|
|
|
|
|
|
|
|
|
, |
|
|
10 |
|
|
|
|
4 |
k |
|
|
|
|
|
|
|
||
|
|
|
0 |
|
|
|
|
|
|
|
|
|
|
|
|
|
|
|
|
, |
|
|
|
|
|
|
|
3 |
|
|
|
α, |
|
1 |
|
|
5 |
|
|
г |
5 |
|
|
|
|
|
|
|
рад. |
|
|
0 |
|
|
|
|
|
2 |
|
, |
|
|
|
|
|
0 |
3 |
|
|
|
|
|
|
|
|
|
|
|
Рис. 4. Графическая зависимость максимальной температуры T2max проволоки на входе в калибрующую зону волоки от угла деформирующей зоны α и относительной длины калибрующей зоны k
при коэффициенте контактного трения f = 0,05
Рис. 6. Зависимость величины оптимального угла αопт конической зоны деформирующей зоны волоки
от относительной длины калибрующей зоны k при f = 0,05
Для сравнения волочения с обычным контактным трением и уменьшенным его значением были проведены аналогичные вышеприведенным исследования, отличающиеся коэффициентом контактного трения, сниженным до f = 0,02. Результаты этих вычислений приведены на рис. 7. Анализ полученных данных показывает, что температура проволоки значительно уменьшилась.
ОАО «Черметинформация» • Бюллетень «Черная металлургия» • 7• 2011 ―――――――――――――――― 73

|
|
при коэффициенте контактного трения f = 0,05 |
|
|
оптимальным средним углом является угол 11 |
|
|
град., а для f = 0,02 угол 14 град. |
|
|
Данная методика была использована для |
|
|
расчета маршрута тонкого волочения сверхвы- |
|
|
сокопрочной проволоки диам. 0,35 мм из заго- |
|
|
товки диам. 1,94 мм (сталь 90К). Было получено |
|
|
распределение оптимальных углов конических |
|
|
деформирующих зон волок (рис. 8). Из рис. 8 |
|
|
видно, что по ходу маршрута волочения углы ко- |
|
|
нусов волок должны постепенно увеличиваться |
|
|
от 6 до 12 град. В отличие от действующего |
|
|
маршрута волочения для первых пяти волок угол |
|
|
конуса деформирующих зон постоянный и со- |
|
|
ставляет 10 град., для последующих девятна- |
|
|
дцати волок угол также постоянный и составляет |
|
|
12 град. В этой связи можно рекомендовать про- |
|
|
вести практический эксперимент с измененной |
Рис. 7. Зависимость величины оптимального угла αопт |
геометрией волок. |
|
конической деформирующей зоны волоки от от- |
|
|
носительной длины калибрующей зоны при коэффициенте |
|
|
|
контактного трения f = 0,02 |
|
Анализ абсолютных величин оптимальных уг- |
|
|
лов волок из рис. 6 и 7 указывает на относи- |
|
|
тельно узкий диапазон их значений, что опреде- |
|
|
ляет возможность рационального практического |
|
|
использования полученных данных. Из данных |
|
|
графиков можно определить, что оптимальной |
|
|
геометрией волоки по температурному критерию |
|
|
для коэффициента контактного трения f = 0,02 |
|
|
является геометрия с минимально возможной |
|
|
длиной калибрующей зоны. При f = 0,05, харак- |
|
|
терном для обычного “мокрого” волочения |
|
|
стальной латунированной проволоки со сколь- |
|
|
жением, длина калибрующей зоны при опти- |
|
|
мальном угле конической зоны волоки мало |
|
|
влияет на температуру в проволоке. Характерно |
|
|
значительное снижение температуры проволоки |
Рис. 8. Зависимость оптимального угла от диаметра |
|
при уменьшении контактного трения. Также |
проволоки при волочении с конечной скоростью 12 м/с |
|
можно определить, что для исследуемой волоки |
и коэффициенте трения f =0,05 |
|
|
Выводы |
|
Создана методика оптимизации геометрии |
существенно не влияет на температуру прово- |
|
канала волоки при волочении проволоки по тем- |
локи. |
|
пературному критерию, позволяющая проекти- |
Для исследованной волоки при коэффици- |
|
ровать геометрию деформирующей и калиб- |
енте контактного трения f = 0,05 оптимальным |
|
рующей зон волоки, обеспечивающую мини- |
углом является угол 11 град., а для f = 0,02 |
|
мальные температуры в обрабатываемой про- |
угол 14 град. |
|
волоке. |
коэффициента контактного трения f = |
Предложены оптимизированные углы конусов |
Для |
деформирующих зон волок для действующего |
|
= 0,02 необходимо использовать минимально |
маршрута волочения на РУП БМЗ, значения |
|
возможную длину калибрующей зоны. |
которых выбираются из графика на рис. 8. |
|
Для |
коэффициента контактного трения f = |
|
= 0,05 |
протяженность калибрующей зоны |
|
74 ―――――――――――――――――ОАО «Черметинформация» • Бюллетень «Черная металлургия» • 7• 2011

БИБЛИОГРАФИЧЕСКИЙ СПИСОК
1.Влияние скорости волочения на температуру и напряженно-деформированное состояние в проволоке из высокоуглеродистой стали / М. Н. Верещагин, Ю. Л. Бобарикин, А. Н. Савенок и др. // Литье и металлургия. 2008.
№ 1 (45). С. 40−48.
2.Аркулис Г. Э., Дорогобид В. Г. Теория пластичности. М.: Металлургия. 1987. 352 с.
3.Колмогоров В. Л. Механика обработки металлов давлением. М.: Металлургия. 1987. 688 с.
4.Теория пластических деформаций металлов / Е. П. Унксов, У. Джонсон, В. Л. Колмогоров и др.; под ред. Е. П. Унксова, А. Г. Овчинникова. М.: Машиностроение. 1983. 598 с.
5.Иванов К. М., Шевченко В. С., Юргенсон Э. Е. Метод конечных элементов в технологических задачах ОМД. СПб.: Изд-во ПИМаш. 2000. 224 с.
УДК 621.771.073.9 Э. Н. ШЕБАНИЦ1, к.т.н.; А. В. МУРАШКИН1, к.т.н., aleksandr.murashkin@ilyich.donetsk.ua;
С. В. ФОРМАН1, О. Ю. ПОЛЯК1, А. Н. ЛУКЬЯНЧИКОВ1, Л. К. ЛЕЩИНСКИЙ2, д.т.н.; Б. Е. ДУБИНСКИЙ2, к.т.н.; В. Н. МАТВИЕНКО2, к.т.н., К. К. СТЕПНОВ2
( 1 ПАО “Мариупольский металлургический комбинат им. Ильича”, 2 Приазовский государственный технический университет)
ПОВЫШЕНИЕ РАБОТОСПОСОБНОСТИ ОБЖИМНЫХ ВАЛКОВ КЛЕТИ 1150 НА МАРИУПОЛЬСКОМ МЕТАЛЛУРГИЧЕСКОМ КОМБИНАТЕ им. ИЛЬИЧА
Объем производства, качество и себестои- |
Легирующие элементы переходят в наплавлен- |
|||
мость проката во многом зависят от ресурса |
ный металл из керамического флюса, который |
|||
прокатных валков, затрат на их приобретение и |
серийно изготавливается |
на химико-металлур- |
||
обслуживание. Стоимость прокатных валков по- |
гической фабрике , входящей в состав ММК им. |
|||
стоянно возрастает и для крупных обжимных |
Ильича и располагающей необходимым обору- |
|||
валков производства Новокраматорского маши- |
дованием и поступающим сырьем. |
|
||
ностроительного завода составляет до 70 тыс. |
С целью получения требуемого состава и |
|||
руб/т. Одним из наиболее эффективных путей |
свойств наплавленного |
металла разработано |
||
снижения расходов на приобретение новых вал- |
несколько марок керамических флюсов И-КФ, |
|||
ков является наплавка [1], позволяющая не |
отличающихся содержанием легирующих эле- |
|||
только восстанавливать валки, но и повышать их |
ментов в шихте. На оптимальном режиме на- |
|||
работоспособность. Для восстановления одного |
плавки лентой 08кп под флюсом И-КФ-45 (с |
|||
горизонтального валка по всей длине бочки не- |
предварительным и сопутствующим подогре- |
|||
обходимо наплавить до 1,3–1,5 т металла. По- |
вом) получают состав |
наплавленного |
слоя |
|
этому экономическая эффективность примене- |
14Х3Г1МФС. В его структуре пластинчатые кар- |
|||
ния наплавки зависит как от работоспособности |
биды цементитного типа и мелкие округлые кар- |
|||
восстановленных валков, так и от расходов на |
биды Мe23C6, а также небольшое количество |
|||
наплавку. Резко снизить эти расходы позволяет |
дисперсных вторичных карбидов, мало струк- |
|||
разработанная и освоенная на Мариупольском |
турно свободного феррита (рис. 1). Такой металл |
|||
металлургическом комбинате (ММК) им. Ильича |
отличается достаточно высокой стойкостью про- |
|||
технология восстановления крупных прокатных |
тив образования горячих трещин (критическая |
|||
валков с использованием наплавочных материа- |
скорость деформации Акр ≈ 2 мм/мин), а также |
|||
лов собственного производства холодноката- |
пластичностью, его ударная вязкость ~0,45 |
|||
ной ленты из низкоуглеродистой стали 08кп и ле- |
МДж/м2, удельная работа разрушения |
~400 |
||
гирующего керамического флюса. Применение |
Дж/см3. Твердость такого металла (42–45 HSD) |
|||
ленты сечением 30×1,0 мм дает возможность |
|
|
|
|
обеспечить надежное проплавление и не допус- |
|
|
|
|
|
|
|
|
|
тить появления дефектов в зоне сплавления. |
В освоении технологии изготовления флюса участвовали |
|||
|
В.Д. Шепель, В.П. Синельников, В.Г. Ашхотов. |
|
||
ОАО «Черметинформация» • Бюллетень «Черная металлургия» • 7• 2011 ―――――――――――――――― |
75 |

достаточно близка к твердости валка из стали 60ХН (36–41 HSD). Учитывая низкое содержание углерода в составе 14Х3Г1МФС и ограниченное разбавление сталью 60ХН наплавленного лентой металла, этот состав применяется для наплавки первого слоя при многослойной наплавке по всей длине бочки. Остальные слои наплавляются под флюсами И-КФ-50–60 (табл. 1) с постепенным увеличением содержания легирующих элементов и твердости наплавленного металла (на горизонтальном валке наплавляется до 20,0–25,0 мм на сторону). Вместе с тем, изменяя марку флюса и, следовательно, состав наплавленного металла, чередуют слои высокой
твердости с пластичными слоями низкой твердо- |
Рис. 1. Микроструктура металла, наплавленного лентой |
сти [2]. |
08кп под керамическим флюсом И-КФ-45 |
ТАБЛИЦА 1. СОДЕРЖАНИЕ ХИМИЧЕСКИХ ЭЛЕМЕНТОВ И СВОЙСТВА МЕТАЛЛА, НАПЛАВЛЕННОГО ЛЕНТОЙ 08кп ПОД ФЛЮСАМИ И-КФ
|
Содержание |
|
Относительная |
Ударная вязкость, |
||
Марка флюса |
элементов, % |
Твердость HSD |
||||
износостойкость |
МДж/м2 |
|||||
С |
Cr |
|||||
|
|
|
|
|||
И-КФ-45 |
0,14 |
3,47 |
45 |
1,00 |
0,40 |
|
И-КФ-50 |
0,17 |
4,50 |
50 |
1,25 |
0,35 |
|
И-КФ-60 |
0,27 |
6,14 |
57 |
1,45 |
0,27 |
Такая слоистая композиция отличается значительно более высокой стойкостью против распространения трещин, вызванных как динамической нагрузкой, так и термической усталостью.
Восстановление изношенной бочки и шеек горизонтальных и вертикальных валков обжимной клети 1150 производится на специализированном участке стана 1700 горячей прокатки ММК им. Ильича. На участке предусмотрены отделения подготовки и хранения наплавочных материалов, наплавки, термической обработки, контроля и хранения валков. Проточка валков под наплавку, а также механическая обработка наплавленной бочки и шеек производятся в вальцетокарной мастерской стана 1700. Установка для наплавки смонтирована на базе вальцетокарного станка Graven, что позволяет наплавлять валки массой до 40,0 т, диам. 500–1500 мм, общей длиной до 4800 мм. Требуемый температурный режим валка в процессе наплавки поддерживается смонтированным на станке термостатическим кожухом, оснащенным газовыми горелками. Система управления процессом наплавки позволяет не только регулировать параметры режима, но и выбирать и управлять схемой укладки швов на поверхности валка (по винтовой линии, под требуемым углом к образующей, по схеме “крестовой намотки”, с зазором
между швами). Кроме того, в автоматическом режиме может ступенчато или плавно изменяться состав наплавленного металла с привязкой координат зоны наплавки к соответствующему участку наплавляемой поверхности валка. Для предварительного (до наплавки) подогрева валка и термической обработки после наплавки участок оснащен термической печью с электрическими нагревательными элементами. Заданный режим термической обработки обеспечивается программным устройством, регулирующим
иконтролирующим температуру по длине бочки
ишейкам.
Благодаря выбору температуры подогрева, скорости нагрева и охлаждения, состава наплавленного металла, технологии наплавки и режима термической обработки работоспособность восстановленных валков выше, чем серийных. Если по объему проката за время эксплуатации валка показатели серийных и наплавленных валков примерно одинаковы, то по наработке на 1 мм износа (уменьшения диаметра) наплавленные валки превосходят серийные в 2–4 раза. При этом стоимость восстановления обжимных валков по всей бочке не превышает 35–40 % стоимости серийных валков (табл. 2).
76 ―――――――――――――――――ОАО «Черметинформация» • Бюллетень «Черная металлургия» • 7• 2011

ТАБЛИЦА 2. СРАВНИТЕЛЬНАЯ ХАРАКТЕРИСТИКА СЕРИЙНЫХ И НАПЛАВЛЕННЫХ ВАЛКОВ ОБЖИМНОЙ КЛЕТИ 1150 (данные 2009−2010 гг.)
|
|
Число валков |
|
Стоимость |
|
|
Прокатано |
Наработка на 1 мм |
||
Валки |
|
|
|
|
за время |
|||||
|
|
восстановления |
|
|||||||
|
в эксплуатации |
|
|
эксплуатации, |
износа, т/мм |
|||||
|
|
|
(% от серийного) |
|
||||||
|
|
|
|
|
|
млн т |
|
|||
|
|
|
|
|
|
|
|
|
||
Горизонтальные: |
|
|
|
|
|
|
|
|
|
|
серийные |
|
14 |
|
|
|
|
|
0,946 |
14–19 |
|
наплавленные |
|
9 |
|
|
35–40 |
|
|
1,050 |
28–56 |
|
Вертикальные: |
|
|
|
|
|
|
|
|
|
|
серийные |
|
3 |
|
|
|
|
|
1,050 |
37–43 |
|
наплавленные |
|
2 |
|
|
33–37 |
|
|
1,150 |
68–86 |
|
Нужно отметить, что в процессе эксплуатации |
|
|
|
|
||||||
уменьшается не только абсолютная величина (в |
|
|
|
|
||||||
2,0–2,5 раза), но и неравномерность износа (рис. 2). |
|
|
|
|
||||||
В решении задачи уменьшения неравномер- |
|
|
|
|
||||||
ности износа особо эффективна используемая |
|
|
|
|
||||||
технология, позволяющая в процессе наплавки |
|
|
|
|
||||||
изменять состав и свойства наплавленного слоя |
|
|
|
|
||||||
по длине бочки в зависимости от характера и ин- |
|
|
|
|
||||||
тенсивности износа. Наплавка шеек позволяет |
|
|
|
|
||||||
полностью использовать слой, наплавленный на |
|
|
|
|
||||||
бочке. |
|
|
|
|
|
|
|
|
|
|
Годовой экономический эффект от уменьше- |
|
|
|
|
||||||
ния расходов на приобретение новых горизон- |
|
|
|
|
||||||
тальных и вертикальных обжимных валков |
за |
Рис. 2. Профиль износа горизонтальных валков |
||||||||
счет их восстановления наплавкой с примене- |
||||||||||
|
|
обжимной клети 1150: |
||||||||
нием наплавочных |
|
материалов |
собственного |
|
|
|||||
|
а наплавленных (после прокатки 278774 т); |
|||||||||
производства ММК |
им. Ильича |
составляет |
не |
|
б серийных (после прокатки 267477 т) |
менее 20,0 млн руб.
БИБЛИОГРАФИЧЕСКИЙ СПИСОК
1.Увеличение срока службы опорных валков стана 2000 горячей прокатки полос в ОАО “Северсталь” / Л. И. Данилов, Н. Б. Скорохватов, В. Ф. Соболев и др. // Черная металлургия: Бюл. ин-та “Черметинформация“. 2004. № 8. С. 68, 69.
2.Лещинский Л. К., Самотугин С. С. Слоистые наплавленные и упрочненные композиции. Мариуполь: Новый мир. 2005. 392 с.
ОАО «Черметинформация» • Бюллетень «Черная металлургия» • 7• 2011 ―――――――――――――――― 77

УДК 669.041 Э. Э. МЕРКЕР, д.т.н., проф.; Д. А. ХАРЛАМОВ, к.т.н., docktn@bk.ru; А. А. АНСИМОВ (Старооскольский технологический институт (филиал)
Национального исследовательского технологического университета “МИСиС”)
СОВЕРШЕНСТВОВАНИЕ МЕТОДИКИ КОНТРОЛЯ И ПАРАМЕТРОВ РЕЖИМА СЖИГАНИЯ ТОПЛИВА ВО ВРАЩАЮЩИХСЯ ОБЖИГОВЫХ ПЕЧАХ
Эксперименты проведены на вращающихся печах в цехе обжига известняка (ЦОИ) Оскольского электрометаллургического комбината с целью определения путей возможного снижения удельного расхода тепла (топлива), повышения производительности агрегатов и уменьшения вредных выбросов в атмосферу при условии обеспечения требуемых показателей качества извести, необходимой для производства высококачественных марок сталей [1].
Анализ результатов исследования по оценке эффективности производства извести на вращающихся печах осуществляли по текущим данным работы агрегатов, а также по результатам их обследования экспериментальными методами [2] с использованием статистической обработки и применением печной компьютерной системы [3] на пульте управления в ЦОИ. Для нахождения оптимальных условий сжигания топлива в печи использовали в качестве критерия оптимальности коэффициент расхода воздуха αв(i1,2,3), являющийся выходной величиной параметров тепловой работы агрегатов, в следующем виде:
αв(i1,2,3) = (Vв.в + Vв(подс) − Vв(асп))/(VоВг), |
(1) |
где Vв.в расход вентиляционного воздуха, фиксируемый расходомером на пульте печи, м3/ч; Vо теоретический расход воздуха на сжигание 1 м3 газа, определяемый расчетом горения топ-
лива; Vв(подс), Vв(асп) подсосы воздуха в головке печи и утечки вентиляторного воздуха в
системе аспирации агрегата соответственно, м3/ч; индексы i1,2,3 относятся к коэффициентам рас-
хода воздуха соответственно для αклв при расчете на клапане печи, αвхим при определении по данным состава отходящих из печи газов и αЭВМв
по данным текущего расчета коэффициента воздуха на печном компьютере.
В связи с имеющимися трудностями регулярного определения величин Vв(подс) и Vв(асп) значения
αклв = Vв.в/VоВг.
По результатам химического анализа проб продуктов сгорания (СО, СО2, О2, NОx и др.) при выходе их из печи рассчитывали коэффициент
расхода воздуха αвхим , идущего на горение топ-
лива [2, 3], что позволяло находить текущее со-
отношение воздух−топливо и корректировать режим сжигания топлива при контрольных испытаниях на печи [3, 4]. Пределы изменения расхода газа на горение составляли от 3100 до 3500 м3/ч, при низшей теплоте сгорания топлива
около 35 МДж/м3 и расчетном значении Vо = = 9,5 м3/м3.
Из данных режимных карт установлено (рис. 1), что такие показатели работы печи, как Рп производительность, т/ч, Тв.в температура нагрева
вентиляторного воздуха, °С, qг удельный расход газа, м3/т, заметно улучшаются по мере приближения значения коэффициента расхода на
клапане αклв к единице, т. е. подтверждается об-
щеизвестный факт о необходимости установления на печах фактического значения αв ≈ 1 [4, 5], тем более что при αв >> 1 возрастают тепловые потери и окислы азота (NOx) с отходящими газами [1, 2]. Из анализа данных рис. 1 следует, что ухуд-
шение показателей работы печей при αклв <1 объясняется условиями недожога топлива, не-
учетом Vв(подс) и Vв(асп), а также ухудшением теплообменных свойств факела. Установлено
опытным путем, что при учете Vв(подс) и Vв(асп) оптимальными являются значения αвхим и αЭВМв =
= 1,03±0,02 для условий работы вращающихся обжиговых печей [2, 4, 5]. При этом настройка печ-
ного компьютера на αЭВМв осуществляется по αвхим
на основе данных определения состава отходящих из печи газов.
Представленные на рис. 1 уравнения регрессии по производственным данным являются достоверными, а значения коэффициента корреляции свидетельствуют об их адекватности. Значения стандартных отклонений величин Рп, Тв.в и qг
составляют соответственно σ(Рп) = 1,92 т/ч,
σ(Тв.в) = 15 °С, σ(qг) = 19,43 м3/т. При этом сле-
дует отметить, что данные парных коэффициентов корреляции (R = 0,6−0,7) свидетельствуют о необходимости учета подсосов и утечек воздуха на аспирацию при расчете фактических значений
αЭВМв .
78 ―――――――――――――――――ОАО «Черметинформация» • Бюллетень «Черная металлургия» • 7• 2011

Рис. 1. ЗависимостьтемпературыподогревавоздухаТв.в (а), удельного расхода топлива (б) и производительности печи (в) от коэффициента расхода воздуха на клапане
αклв = Vв.в/(9,5Вг)
аспирации, а величину подсосов воздуха в головке печи определяли по следующей зависи-
мости с учетом определения αвхим по данным хи-
мического анализа проб продуктов сгорания на выходе из печи:
V |
|
= αхим |
(V В ) − V |
в.в |
+ V |
в(асп) |
, |
(4) |
|||
|
|
в(подс) |
в |
о г |
|
|
|
||||
где αвхим = |
|
|
|
1 |
|
|
, N2, |
O2 и СО |
|||
1 |
|
|
|
|
|||||||
|
−3,76(О2 −0,5СО)N2 |
|
|
|
|
содержание элементов в отходящих газах, %. При постоянных значениях разрежения в ра-
бочем пространстве печи, скоростях ее вращения и подачи известняка в рабочее пространство
агрегата при известных данных Вг, Vв.в и Vв(асп) по нескольким контрольным пробам дыма можно
на основе определения αвхим в соответствии с выражением (4) найти фактический уровень подсосов Vв(подс) для данных конкретных условий работы агрегата.
В тех же условиях на печном компьютере рассчитываются значения фактического коэф-
фициента расхода воздуха αЭВМв в соответствии с
выражением (3) для данных условий работы печи, т. е. при существующих показателях ра-
боты агрегата (Вг, Vв.в и Vв(асп)).
Затем, наоборот, при открытом шибере
( V |
≠ 0) при известных V |
и αхим |
находили |
в(асп) |
в(подс) |
в |
|
текущее значение Vв(асп) при данных значениях Вг и Vв.в, что позволяет вносить коррективы в текущий
расчет αЭВМв в компьютерной системе оптимизации
(КСО) режима сжигания топлива (РСТ) в печи. Следовательно, предлагаемая проверка ра-
боты расчетной модели определения коэффициента расхода воздуха αЭВМв осуществляется по данным химического анализа проб дыма с контрольным определением αвхим и установления
В существующих условиях работы [4, 5] вра- |
фактических значений величины подсосов воз- |
|||||||||||||
духа Vв(подс) при |
Vв(асп) = |
0, |
т. е. при закрытии |
|||||||||||
щающихся печей обжига известняка в ЦОИ оп- |
шибера в системе аспирации вращающейся |
|||||||||||||
ределяли |
подсосы |
воздуха |
в |
головке печи |
печи. |
|
|
|
|
|
|
|||
Vв(подс), м3/ч, и утечки вентиляторного воздуха в |
Общая структурная схема КСО РСТ приве- |
|||||||||||||
системе аспирации агрегата Vв(асп), м3/ч, так как |
дена на рис. 2. При этом расчет показателей ре- |
|||||||||||||
эти показатели необходимы для расчета дейст- |
жима сжигания топлива αЭВМ , |
V опт |
и βг осуществ- |
|||||||||||
вительного |
расхода |
воздуха |
V в, |
идущего |
на |
|
в |
|
в.в |
|
в |
|
||
ляется по программе на основе применения ал- |
||||||||||||||
горение газа в факеле печи: |
д |
|
|
|||||||||||
|
|
|
горитмического языка MS Excel. |
αвЭВМ рассчиты- |
||||||||||
V в = Vв.в + Vв(подс) − Vв(асп), м3/ч. |
(2) |
вается в блоке 6 (см. рис. 2), |
V опт |
в блоке 12, а |
||||||||||
д |
|
|
|
|
|
|
|
|
|
в.в |
|
|
|
|
Тогда коэффициент расхода воздуха αвЭВМ |
при |
соотношение воздух−газ |
βг |
в |
блоке 13 |
на |
||||||||
|
|
в |
|
|
|
|
||||||||
расчете на компьютере равен: |
|
|
|
этапе II (блок 7). Oптимальный расход вентиля- |
||||||||||
|
|
|
торного воздуха |
V опт |
устанавливается |
при |
||||||||
αвЭВМ = Vдв /Vвг |
|
|
|
|
|
|
в.в |
|
|
|
|
|
||
= (Vв.в + |
Vв(подс) − |
Vв(асп))/(VоВг). |
(3) |
αвопт = 1,03 (блоки 8, 11, 13). |
|
|
|
|
||||||
Значения |
Vв(асп) находили экспериментально |
|
|
|
|
|
|
|
||||||
для каждого уровня открытия шибера в системе |
|
|
|
|
|
|
|
ОАО «Черметинформация» • Бюллетень «Черная металлургия» • 7• 2011 ―――――――――――――――― 79

Рис. 2. Структурная блок-схема модели КСО РСТ для условий работы вращающейся печи обжига известняка
Для решения задачи по определению оптимальных показателей режима сжигания топлива
[3, 5], например при αоптв = 1,03±0,02, записыва-
ются исходные данные (блок 1) по специальной схеме с овладением несложными приемами манипулирования имеющимися средствами MS Exсel с целью интерпретации характерных данных работы печи, выдаваемых компьютером в режиме реального времени.
При известных значениях Vв(асп) контрольная проверка точности работы компьютерной системы (см. рис. 2) осуществляется периодически по мере необходимости (например, после ре-
монта печи) с помощью химического анализа пробы отходящих газов на выходе из печи и c
последующим определением αвхим для уточнения
величины подсосов воздуха в соответствии с выражением (4).
Далее текущее значение коэффициента расхода воздуха αЭВМв определяется выражением (3)
непрерывно в соответствии с алгоритмом расчета (см. рис. 2) при возможных изменениях расходов топлива и вентиляторного воздуха.
По ходу работы КСО РСТ осуществляется сравнение текущей величины αЭВМв и
80 ―――――――――――――――――ОАО «Черметинформация» • Бюллетень «Черная металлургия» • 7• 2011

αоптв = 1,03±0,02 с определением разницы ±Δαв
(блок 10). Затем уточняется действительный (оптимальный) расход воздуха на горение
V в |
α |
в |
=V в |
, |
т. е. |
V в |
=V в (1± |
α |
в |
) , где |
д |
|
д(опт) |
|
|
д(опт) |
д |
|
|
||
+Δαв = αвЭВМ −αвопт |
или |
− αв = αвопт −αвЭВМ |
(блоки 9, |
10, 11). После чего находится требуемый (оптимальный для данного момента работы печи) расход вентиляторного воздуха, подаваемого на горение топлива в печи:
V опт = V в |
− V |
в (подс) |
+ V |
в(асп) |
, м3/ч. |
(5) |
|
в.в |
д(опт) |
|
|
|
|
Затем устанавливается требуемое соотношение воздух–газ ( βгв ) для данного момента работы печи в соответствии с выражением
βг |
= V опт /В |
г |
= (V в |
− V |
+ V |
)/В . (6) |
в |
в.в |
д(опт) |
в(подс) |
в(асп) |
г |
Сравнение результатов расчетов αЭВМв с помощью КСО (см. рис. 2) с данными специальных контрольных определений αвхим (рис. 3), выполненных
при одинаковых условиях работы агрегата, свидетельствует об удовлетворительной сходимости
( αв ±0,03) имеющихся данных и адекватности
разработанной для вращающихся печей ЦОИ компьютерной системы контроля параметров РСТ (см. рис. 2) по ходу работы агрегата.
Рис. 3. Корреляционная связь параметров αвЭВМ и αвхим
водинаковых условиях работы печи
Онеобходимости осуществления контроля РСТ свидетельствуют данные, приведенные в
таблице, где значения αЭВМв определены по выра-
жению (3) при Vв(асп) = 2000 м3/ч и соответствующих значениях Vв(подс).
СРАВНИТЕЛЬНЫЕ ПОКАЗАТЕЛИ РАБОТЫ ВРАЩАЮЩЕЙСЯ ПЕЧИ ПРИ РАЗЛИЧНЫХ ЗНАЧЕНИЯХ αклв , βгв И ТЕМПЕРАТУРЫ ОТХОДЯЩИХ ИЗ ПЕЧИ ГАЗОВ Тотх.г
Вариант |
Число |
Расход, м3/ч |
βвг |
αвЭВМ |
Vв3(подс), |
Рп, |
qг, м3/т |
Тотх.г, |
Тв.в, ºС |
Тизв, |
|
|
проб |
газа |
воздуха |
|
|
м /ч |
т/ч |
|
ºС |
|
ºС |
А |
12 |
3512,3 |
31270,8 |
8,90 |
1,078 |
6700 |
18,2 |
192,4 |
894,2 |
494,8 |
64,8 |
Б |
13 |
3445,3 |
29927,1 |
8,69 |
1,011 |
4500 |
19,0 |
180,0 |
888,0 |
575,4 |
87,0 |
Из приведенных данных следует, что предпочтительнее является вариант Б, так как показатели Рп, qг, Тотх.г выгодно отличаются от варианта А, что вызвано более низкими значениями
βгв, αклв и более высоким показателем нагрева
вентиляторного воздуха Тв.в, но в качестве недостатка можно отметить более высокую температуру извести Тизв по сравнению с вариантом А. Очевидным является тот факт, что режим работы печи по варианту Б является более при-
ближенным к αоптв = 1,03, чем вариант А, что обес-
печивает лучшие технико-экономические показатели производства извести.
Таким образом, предлагаемая методика установления оптимального коэффициента расхода воздуха для данного РСТ c применением алго-
ритма КСО для определения αЭВМв , Vдв(опт) и βгв по-
зволяет обеспечивать условия по улучшению тех- нико-экономических [1, 4] и энерго-экологических [5] показателей производства извести на вращающихся печах обжига известняка.
БИБЛИОГРАФИЧЕСКИЙ СПИСОК
1.Тепловые и технологические процессы в печах бездоменной металлургии / Э. Э. Меркер и др. Старый Оскол:
ООО ТНТ. 2010. 184 с.
2.Основы практической теории горения / В. В. Померанцев, К. М. Арефьев и др. Л.: Энергоатомиздат. 1986. 312 с.
3.Методы компьютерного моделирования горения и теплообмена во вращающихся печах / П. А. Трубаев и др. Белгород: Изд-во БГТУ: БИЭИ. 2008. 230 с.
4.Освоение технологии обжига известняка во вращающихся печах / А. И. Гамей и др. // Черная металлургия: Бюл. ин-та “Черметинформация”. 2002. № 6. С. 3−5.
5.Особенности эксплуатации вращающихся печей обжига известняка / Г. Л. Антонов и др. // Сталь. 2008. № 9. С. 41−44.
ОАО «Черметинформация» • Бюллетень «Черная металлургия» • 7• 2011 ―――――――――――――――― 81
Т. М. ПЕТРАКОВА, к.э.н., И. М. ИВАНОВА (ОАО “Черметинформация”)
ИТОГИ РАБОТЫ ПРЕДПРИЯТИЙ ЧЕРНОЙ МЕТАЛЛУРГИИ РОССИИ ЗА I КВАРТАЛ 2011 г.
Приведены основные показатели работы черной металлургии в I кв. 2011 г., включая объемы производства продукции, выручку от реализации продукции ведущих металлургических и трубных предприятий отрасли. Показано изменение темпов роста производства основных видов металлопродукции, физического объема экспорта продукции и уровня средних фактических цен экспортных операций и др.
Рассмотрены вопросы использования материальных и энергетических ресурсов. Приведены данные по удельному расходу: основных материалов при производстве чугуна, стали и проката; железорудной части шихты по предприятиям; скипового кокса на 1 т передельного чугуна; чугуна при производстве конвертерной стали; чугуна при производстве электростали; электроэнергии при производстве электростали; стали при производстве готового проката.
Ключевые слова: черная металлургия; металлопродукция; экспорт; импорт; материальные и энергетические ресурсы; чугун; сталь; прокат.
The main indices of activity of the iron and steel industry in the first quarter of 2011 have been presented including the article production volumes, proceeds from product sales of the leading metallurgical and pipe and tube enterprises of the sector. Variation of grown rates of manufacturing the main metal product kinds, physical product exports and levels of average real prices during export operations etc. has been shown.
Problems of utilizing the material and energy resources have been considered. Data on specific consumptions: the main materials during cast iron, steel and rolled product manufacturing, iron-ore parts of charge materials by enterprises, skip coke per 1t of pig iron, pig iron during steel production in the basic oxygen converters, pig iron during steel production in the electric furnaces, steel during rolled product manufacturing has been presented.
Key words: iron and steel industry, metal products, exports, imports, material and energy resources, pig iron, steel, rolled products.
О. В. ЮЗОВ1, А. М. СЕДЫХ2, С. З. АФОНИН3 ( 1 Национальный исследовательский технологический университет “МИСиС”, 2 Объединенная металлургическая компания, 3 Союз экспортеров металлопродукции России)
ЭКОНОМИЧЕСКИЕ ПОКАЗАТЕЛИ И ПРОБЛЕМЫ ПОСТКРИЗИСНОГО РАЗВИТИЯ ЧЕРНОЙ МЕТАЛЛУРГИИ РОССИИ
Несмотря на повышение за последнее десятилетие среднего технического уровня отечественных металлургических предприятий, показатели использования производственных ресурсов в черной металлургии России хуже, чем за рубежом.
Мировой финансовый кризис оказал сильное негативное влияние на показатели работы отечественных предприятий черной металлургии, особенно предприятий с более низким техническим уровнем.
В настоящее время мировая и отечественная черная металлургия находятся в стадии восстановительного роста. В России среднесуточное производство стали и средние цены на металлопродукцию близки или уже достигли докризисного уровня. В то же время средняя себестоимость продукции уже значительно превысила этот уровень, и это обусловило резкое снижение рентабельности продукции.
Для отечественной черной металлургии необходимо более активное осуществление мероприятий по повышению качества продукции, технического уровня производства, эффективности использования материальных, топливно-энергетических и трудовых ресурсов и в конечном счете эффективности производства.
Ключевые слова: черная металлургия России; технический уровень; показатели использования производственных ресурсов; себестоимость; рентабельность; эффективность производства.
Despite improvement in the average engineering performance standard of the domestic metallurgical enterprises over the past decade, indices of utilizing the production resources the iron and steel industry in Russia are lower than those in foreign countries.
The world’s financial crisis had the strong negative influence on indices of activities of the domestic iron and steel industry enterprises, especially enterprises with the lower engineering performance standard.
At the present, the world’s and domestic iron and steel industries are at the stage of the recovery growth. In Russia, average daily steel production and average metal product prices close to or have already reached before-crisis levels. At the same time, the average product cost has significantly exceeded such level, and this has conditioned the sharp decrease in the product profitability.
82 ―――――――――――――――――ОАО «Черметинформация» • Бюллетень «Черная металлургия» • 7• 2011
For the domestic iron and steel industry, it is necessary to more actively take the measures for improvement in the product quality, the engineering performance standard of the production, efficiency of utilizing the material, fuelenergy and labor resources and finally productive efficiency.
Key words: Russian iron and steel industry, engineering performance standard, manufacturing resource utilization indices, cost, profitability, productive efficiency.
Е. А. ПЕСТОНОВА, к.б.н.; С. И. АНУФРИЕВА, к.х.н.; Е. Г. ОЖОГИНА, д.г.-м.н., chimtech@vims-geo.ru (ФГУП “Всероссийский научно-исследовательский институт минерального сырья им. Н.М. Федоровского”)
ОБЕСФОСФОРИВАНИЕ КОНЦЕНТРАТОВ ОБОГАЩЕНИЯ ОКИСЛЕННЫХ МАРГАНЦЕВЫХ РУД ХИМИЧЕСКИМИ СПОСОБАМИ
Изучен вещественный состав технологических проб окисленных марганцевых руд Сейбинского рудного узла и Порожинского месторождения. Проведены исследования по обесфосфориванию марганцевых концентратов обогащения с повышенным содержанием фосфора химическими способами (содовым, гаусманитовым способами и щелочным выщелачиванием). Установлено, что эффективность протекания процессов обесфосфоривания определяется минеральной формой фосфора, отношением содержания железа к фосфору в исходном концентрате и содержанием кремнезема. Получены обесфосфоренные концентраты, годные для выплавки стандартных ферросплавов.
Ключевые слова: марганцевые концентраты; псиломелан; апатит; крандаллит; обесфосфоривание; содовый способ; гаусманитовый способ; щелочное выщелачивание.
Matter compositions of the technological samples of the oxidized manganese ores from Seibinskiy ore block and Porozhinskoe deposit have been studied. Investigations into chemical method (soda, hausmannite methods, alkaline leaching) dephosphorization of manganese concentrates with increased phosphorus content have been carried out. It has been established that efficiency of dephosphorization processes is determined by mineral phosphorus form, iron / phosphorus ration in the initial concentrate and silicon content. Dephosphorized concentrates have been produced which are suitable for smelting the standard ferroalloys.
Key words: manganese concentrates, psilomelan, apatite, crandallite, dephosphorization, soda method, hausmannite method, alkaline leaching.
В. И. РУДЫКА, к.э.н.; В. П. МАЛИНА (Государственный институт по проектированию предприятий коксохимической промышленности “Гипрококс”)
ПОСЛЕДНИЕ ТЕНДЕНЦИИ В РАЗВИТИИ МИРОВОГО МЕТАЛЛУРГИЧЕСКОГО И КОКСОВОГО ПРОИЗВОДСТВ
(Обзор материалов саммита “Европейский кокс 2011”, 5−7 апреля 2011 г., г. Вена, Австрия)
Представлен обзор материалов по вопросам повестки дня саммита: анализу ситуации, которая сложилась на мировых рынках стали, кокса и коксующегося угля; прогнозу потребности в стали и сырьевых материалах; перспективам развития сталеплавильной и коксовой отраслей на период до 2015 г., а также техническим достижениям в коксовом производстве.
Ключевые слова: саммит “Европейский кокс 2011”; мировой рынок стали; кокс; коксующийся уголь; прогноз потребности в стали и сырьевых материалах.
Review of information on agenda for the Summit: analysis of situation in the World’s markets for steel, coke, coking coal, steel and raw material requirement prediction, prospects for development in the steel and coke sectors in period of up to 2015, as well as technical advances in coke making has been presented.
Key words: Summit on “European Coke 2011”, world’s steel market, coke, coking coal, steel and raw material prediction.
ОАО «Черметинформация» • Бюллетень «Черная металлургия» • 7• 2011 ―――――――――――――――― 83
А. Ф. ШЕВЧЕНКО, д.т.н. (Институт черной металлургии им. З.И. Некрасова Национальной академии наук Украины)
КОМПЛЕКСНАЯ ОЦЕНКА РАЗЛИЧНЫХ ТЕХНОЛОГИЙ ВНЕПЕЧНОЙ ДЕСУЛЬФУРАЦИИ ЧУГУНА
Приведен сопоставительный анализ технико-экономических показателей различных процессов внепечной десульфурации чугуна. В отличие от ранее применявшихся методик проведена оценка по широкому перечню показателей. Показано, что затраты на реагент являются недостаточной величиной для оценки процесса, а необходимо учитывать все операции и составляющие внепечной подготовки чугуна. Наиболее приоритетным определен процесс вдувания зернистого магния без разубоживающих добавок, наиболее затратным KRCaO- процесс.
Ключевые слова: внепечная десульфурация чугуна; затраты на реагент; вдувание зернистого магния. Comparative analysis of technical – economic indices of various processes of ladle cast iron desulfurization has
been presented. In contrast to previously applied procedures, evaluation of the wide list of the indices has been made. It has been shown that costs for reagent are not sufficient value for evaluating the process, and it is necessary to take into account all the operations and components of ladle cast iron preparation. The process of grained magnesium injection without improvenishing additives is the most priority one. The KRCaO process is the most expensive one.
Key words: ladle cast iron desulfurization, reagent costs, grained magnesium injection.
А. Г. ВЕЛИЧКО1, д.т.н.; Б. М. БОЙЧЕНКО1, д.т.н., проф., boichenco@metal.nmetau.edu.ua; B. C. ГРИШИН1,
к.т.н.; А. В. ПОПОВ1, А. В. ШИБКО2, к.т.н.; В. И. ПИЩИДА2, к.т.н.; В. И. ШПАК2, К. Ф. ЧМЫРКОВ2 ( 1 Национальная металлургическая академия Украины, 2 ПАО “Евраз − Днепропетровский металлургический завод им. Петровского”)
ПРИМЕНЕНИЕ В КОНВЕРТЕРАХ КИСЛОРОДНЫХ ФУРМ С ДВУХРЯДНЫМ РАСПОЛОЖЕНИЕМ СОПЕЛ
Изложены результаты промышленных испытаний одноконтурных двухрядных наконечников кислородных фурм для дожигания газов. Показана возможность применения таких наконечников в условиях кислородноконвертерного цеха ПАО “Евраз − Днепропетровский металлургический завод им. Петровского”.
Ключевые слова: кислородный конвертер; фурма двухрядная; сопло; экономия; дожигание газов
Results of industrial tests of the single-contour two-row tips of the oxygen lances for post combustion of gases have been presented. Opportunity for applying such tips under conditions of the basic oxygen converter shop at OAO “DMZ im. Petrovskogo” has been shown.
С. И. СЕМЫКИН, В. Ф. ПОЛЯКОВ, Е. В. СЕМЫКИНА, Т. С. КИЯШКО (Институт черной металлургии им. З.И. Некрасова Национальной академии наук Украины)
ИССЛЕДОВАНИЕ ОСОБЕННОСТЕЙ РАФИНИРОВАНИЯ ЖЕЛЕЗОУГЛЕРОДИСТОГО РАСПЛАВА ПРИ НАЛОЖЕНИИ НИЗКОВОЛЬТНОГО ЭЛЕКТРИЧЕСКОГО ПОТЕНЦИАЛА
На основе анализа экспериментов на 0,3-т лабораторном конвертере и опытном 0,5-т сталеразливочном ковше показана возможность существенного улучшения тепловых и рафинировочных процессов за счет электрической энергии при подводе низковольтных потенциалов как при дополнительном перемешивании металлического и шлакового расплава инертными струями в конвертере, так и при внепечной обработке металла.
Ключевые слова: железоуглеродистый расплав; конвертер; сталеразливочный ковш; низковольтный электрический потенциал.
On basis of analysis of experiments in the 0.3t laboratory converter and pilot 0.5t steel-teeming ladle, opportunity for significant improvement in thermal and refining processes due to electric energy during low-voltage potential supply both at additional stirring of metal and slag melts by inert jets in the basic oxygen converter and at ladle treatment of metal has been shown.
Key words: iron-carbon melt, converter, steel-teeming ladle, low-voltage electric potential.
84 ―――――――――――――――――ОАО «Черметинформация» • Бюллетень «Черная металлургия» • 7• 2011
П. С. ХАРЛАШИН, А. Б. КОВУРА, Р. Д. КУЗЕМКО (ГВУЗ “Приазовский государственный технический университет”)
МОДЕЛЬ РАСЧЕТА ТЕРМОГАЗОДИНАМИЧЕСКИХ ПАРАМЕТРОВ СТРУИ ПРИ РАЗДУВЕ ШЛАКА В КОНВЕРТЕРЕ
С учетом реальной волновой структуры истекающих струй рассмотрена модель расчета присоединенной массы окружающего газа из полости конвертера. Численные расчеты позволили определить среднемассовую скорость и температуру в произвольном сечении сверхзвуковой нерасчетной струи до внедрения ее в шлаковый расплав конвертера.
Ключевые слова: сверхзвуковая струя; присоединенная масса; полость конвертера; среднемассовая скорость и температура.
Taking into account real wave structure of the elapsing jets, model of calculating the added mass of the surrounding gas from the basic oxygen converter cavity has been considered. Numerical calculations have made it possible to determine average mass velocity and temperature in arbitrary cross section of the supersonic off-design jet before its introduction into the slag melt in the basic oxygen converter.
Key words: supersonic jet, added mass, basic oxygen converter cavity, average mass velocity and temperature.
Э. О. ЦКИТИШВИЛИ1, А. Н. ЧУДНОВЕЦ1, В. Н. БРУХАНСКИЙ1, Д. П. КУКУЙ2, к.т.н.; В. С. СОЛОД2, к.т.н., solod_vs2010@ua.fm; А. А. МАЛЬЦЕВ3
( 1 ЗАО “Макеевский металлургический завод”, 2 НПО “Доникс”, 3 Донецкий национальный технический университет)
ОСВОЕНИЕ ПРОИЗВОДСТВА ВЫСОКОКАЧЕСТВЕННОЙ ПРОДУКЦИИ НА САМОМ НОВОМ В УКРАИНЕ СРЕДНЕСОРТНО-МЕЛКОСОРТНОМ СТАНЕ 390
Представлены сведения об истории создания и сортаменте стана 390. Даны схема расположения основного оборудования, параметры рабочих клетей и привода валков, представлено описание технологического процесса производства проката и калибровка прокатных валков при использовании двухручьевой прокатки−разделения.
Сделано сравнение опытных расчетных параметров прокатки, загрузки двигателей, полученных с использованием системы автоматизированного проектирования и моделирования технологии прокатки сортовых профилей и катанки. Полученные результаты свидетельствуют о высокой точности прогнозирования параметров прокатки.
Разработанная технология внедрена в производство.
Ключевые слова: стан 390; сортамент; сортовой прокат; калибровка валков; прокатка−разделение; математическая модель; энергозатраты.
Information on history of creating the 390 mill and its range has been presented. Scheme of the main equipment location, parameters of the working stands and roll drive have been described. Production process of manufacturing the rolled products and roll pass design during using the two-strand rolling-slitting have been shown.
Comparison of pilot computational parameters of rolling, motor loading, obtained with the use of the automated design system and modeling the sectional bars and wire rod rolling, has been made. Obtained results show high accuracy of predicting the rolling parameters.
The developed technology has been applied in industry.
Key words: 390 mill, range, profiled sections, roll pass design, rolling-slitting, mathematical model, power inputs.
И. Ю. ПЫШМИНЦЕВ1, д.т.н.; А. В. ВЫДРИН1, д.т.н.; Я. И. КОСМАЦКИЙ1, В. Б. ВОСХОДОВ2, В. В. АНАНЯН2, А. М. ЗУБКОВ2, С. А. ДЕНИСЮК2, А. П. ШЛЯМНЕВ3, к.т.н.
( 1 ОАО “Российский научно-исследовательский институт трубной промышленности”, 2 ОАО “Волжский трубный завод”, 3 ФГУП “ЦНИИчермет им. И.П. Бардина”)
АНАЛИЗ РЕЗУЛЬТАТОВ ОПЫТНО-ПРОМЫШЛЕННОГО ПРОИЗВОДСТВА ТРУБ ИЗ НОВОЙ КОРРОЗИОННОСТОЙКОЙ СТАЛИ
Представлен анализ результатов изготовления опытно-промышленной партии горячепрессованных труб из новой коррозионностойкой стали. Для определения величины сопротивления деформации сталей, применяемых
ОАО «Черметинформация» • Бюллетень «Черная металлургия» • 7• 2011 ―――――――――――――――― 85
при изготовлении труб из коррозионностойких марок стали, проведены исследования по осадке цилиндрических образцов на кулачковом пластометре в широком диапазоне изменения скорости, степени и температуры деформации. Проведенные исследования позволили уточнить силовые параметры процесса прессования труб.
Ключевые слова: прессование металлов, коррозионностойкая сталь, сопротивление деформации.
In the article, analysis of results o manufacturing the pilot-industrial set of the hot-pressed pipes and tubes from new stainless steel has been presented. In order to determine the deformation resistance values of steels applied during manufacturing the pipes and tubes from stainless steel grades, investigations into upsetting the cylindrical specimens at the cam plastometer in wide range of varying the speed, degree and temperature of deformation have been carried out. The carried-out investigations have made it possible to revise the force parameters of the process of extruding the pipes and tubes.
Key words: metal extrusion, stainless steel grade, deformation resistance.
А. Н. САВЕНОК1, А. В. ВЕДЕНЕЕВ1, О. И. ИГНАТЕНКО1, Ю. Л. БОБАРИКИН2, М. Н. ВЕРЕЩАГИН2, М. Ю. ЦЕЛУЕВ2 ( 1 РУП “Белорусский металлургический завод”, 2 Гомельский государственный технический университет им. П.О. Сухого)
ИСПОЛЬЗОВАНИЕ ТЕМПЕРАТУРНОГО КРИТЕРИЯ ДЛЯ ОПТИМИЗАЦИИ ГЕОМЕТРИИ ДЕФОРМИРУЮЩЕЙ И КАЛИБРУЮЩЕЙ ЗОН КАНАЛА ВОЛОКИ
Создана методика оптимизации геометрии канала волоки при волочении проволоки по температурному критерию, позволяющая проектировать геометрию деформирующей и калибрующей зон волоки, обеспечивающую минимальные температуры в обрабатываемой проволоке.
Предложены оптимизированные углы конусов деформирующих зон волок для действующего маршрута волочения на Белорусском металлургическом заводе.
Ключевые слова: волочение проволоки; геометрия канала волоки; деформирующая и калибрующая зоны волоки; оптимизированные углы конусов.
Procedure of optimizing the geometry of the die channel during wire drawing according the temperature criterion has been created, which makes it possible to design the geometry of the deforming and sizing zones of the die, providing the minimal temperatures in the processed wire.
Optimized cone angles of deforming zones of the dies for the existing drawing route at the Byelorussian Steel Works Republic Unitary Enterprise.
Key words: wire drawing, die channel geometry, deforming and sizing die zones, optimized cone angles.
Э. Н. ШЕБАНИЦ1, к.т.н.; А. В. МУРАШКИН1, к.т.н., aleksandr.murashkin@ilyich.donetsk.ua; С. В. ФОРМАН1,
О. Ю. ПОЛЯК1, А. Н. ЛУКЬЯНЧИКОВ1, Л. К. ЛЕЩИНСКИЙ2, д.т.н.; Б. Е. ДУБИНСКИЙ2, к.т.н.; В. Н. МАТВИЕНКО2, к.т.н.; К. К. СТЕПНОВ2 ( 1 ПАО “Мариупольский металлургический комбинат им. Ильича”, 2 Приазовский государственный технеческий университет)
ПОВЫШЕНИЕ РАБОТОСПОСОБНОСТИ ОБЖИМНЫХ ВАЛКОВ КЛЕТИ 1150 НА МАРИУПОЛЬСКОМ МЕТАЛЛУРГИЧЕСКОМ КОМБИНАТЕ им. ИЛЬИЧА
Показана перспективность снижения расхода валков за счет восстановления бочки и шеек наплавкой. Показано, что экономическая эффективность применения наплавки намного выше при использовании наплавочных материалов (электродной ленты и легирующего керамического флюса) собственного производства. Усовершенствованная технология восстановления валков обжимной клети 1150 на специализированном участке наплавки и термообработки обеспечивает менее интенсивный и более равномерный износ бочки, увеличивая в 2 – 3 раза наработку на 1 мм износа.
Ключевые слова: обжимные валки; восстановление валков; наплавка; наплавочные материалы; экономическая эффективность применения наплавки.
Promise of decreasing the roll consumption on account of reconditioning the reconditioning the barrel and neck with surfacing has been shown. It has been shown that cost efficiency of the surfacing application is much higher in case of using the surfacing domestic manufacture materials (electrode band and alloying ceramic flux). The improved technology for reconditioning the rolls of the breakdown 1150 stand at the specialized section for surfacing and heat treatment provides less intensive and more uniform wear of the barrel, and this increases 1 mm wear-out time by factor of 2–3.
86 ―――――――――――――――――ОАО «Черметинформация» • Бюллетень «Черная металлургия» • 7• 2011
Key words: breakdown rolls, roll reconditioning, surfacing, surfacing materials, surfacing application cost efficiency.
Э. Э. МЕРКЕР, д.т.н., проф.; Д. А. ХАРЛАМОВ, к.т.н., docktn@bk.ru; А. А. АНСИМОВ (Старооскольский технологический институт (филиал)
Национального исследовательского технологического университета “МИСиС”)
СОВЕРШЕНСТВОВАНИЕ МЕТОДИКИ КОНТРОЛЯ И ПАРАМЕТРОВ РЕЖИМА СЖИГАНИЯ ТОПЛИВА ВО ВРАЩАЮЩИХСЯ ОБЖИГОВЫХ ПЕЧАХ
Рассмотрены некоторые вопросы организации режима дожигания оксида углерода СО до СО2 струями кислорода (О2) во встречном потоке отходящих из зоны продувки газов без учета влияния вспененного шлака в конвертере.
Показано экспериментальным путем, что степень дожигания СО до СО2 струями кислорода зависит от расхода, длины и количества струй, угла их наклона, высоты расположения сопел фурмы и от температурных условий процесса продувки ванны кислородом.
Ключевые слова: вращающиеся обжиговые печи; организация режима дожигания оксида углерода; степень дожигания оксида углерода; продувка кислородом.
Some problems of organizing the carbon oxide (CO) post combustion conditions to obtain CO2 using the oxygen (O2) jets in the counter-current flow of injection zone off-gases without taking into account of the foamed slag influence in the basic oxygen converter have been considered.
It has experimentally been shown that degree of CO post combustion to obtain CO2 using the O2 jets is dependent on flow rate, length and amount of the jets, their slope angle, lance nozzle location height, and temperature conditions of process of the bath blowing with oxygen.
Key words: rotary firing furnaces, carbon oxide post combustion condition organization, carbon oxide post combustion degree, oxygen injection.
ОАО «Черметинформация» • Бюллетень «Черная металлургия» • 7• 2011 ―――――――――――――――― 87

20-22 сентября 2011
Москва, ЦВК «ЭКСПОЦЕНТР», Павильон 5
Основные разделы выставки:
•Современные технологии и оборудование термомеханической, термохимической, размерной и поверхностной обработки различных материалов
•Энергосберегающие технологии термических производств
•Нагревательное печное оборудование: вакуумные печи, дуговые печи, индукционный нагрев, электрические печи сопротивления, электронно-лучевые и электронно-пучковые нагревательные устройства
•Закалочное оборудование, масла и среды
•Электротермические установки экологического назначения
•Контроль качества термообработки
•Теплотехнические измерения в термических производствах
•Инфракрасный и СВЧ нагрев
•Плазменное формообразование и напыление
•Лазерная поверхностная обработка
|
В рамках выставки проводится специализированный салон |
|
|
«Теплоизоляционные и огнеупорные материалы и изделия» |
|
• Магнезиальные |
• Кремнезёмистые |
• Алюмосиликатные |
• Корундовые |
• Корундографитовые |
• Карбидкремниевые |
• Циркониевые |
• Окисные |
• Безкислородные |
Неотъемлемая часть выставки "Термообработка" - это традиционно проводимая в ее рамках научно-
практическая конференция "Инновационные технологии термообработки", которая существенно повышает эффективность работы экспонентов и посетителей на выставке.
Ежегодная выставка "Термообработка" является единственной в России международной специализированной выставкой термического оборудования и технологий, которая наглядно демонстрирует достижения в сфере термической обработки материалов, способствуя экспонентам в налаживании новых деловых контактов и партнерских отношений.
Цель мероприятия определяется тремя составляющими:
-способствовать развитию производственных и экономических связей;
-способствовать обмену научно-технической информацией;
-способствовать широкому внедрению и применению инновационных технологий термического воздействия.
Основные посетители выставки "Термообработка": руководители и ведущие специалисты предприятий и организаций тяжелого машиностроения, станкостроения, вагоностроения, автомобилестроения, судостроения, двигателестроения, металлообработки, металлургической, энергетической, нефтегазовой, химической, атомной, горной, авиакосмической отраслей, военнопромышленного комплекса приборостроения, инжиниринга, научно-исследовательской и внешнеэкономической сферы, строительства, а также других промышленных предприятий и образовательных учреждений.
Организатор:
Выставочная компания «Мир-Экспо»
Дирекция выставки: 115533, Москва, проспект Ю. Андропова, 22
Тел./Факс: 8 499 618 05 65, 8 499 618 36 83, 8 499 618 36 88 E-mail: ht@mirexpo.ru; Сайт: www.mirexpo.ru
88 ―――――――――――――――――ОАО «Черметинформация» • Бюллетень «Черная металлургия» • 7• 2011