
Recent Progress in Bioconversion of Lignocellulosics
.pdf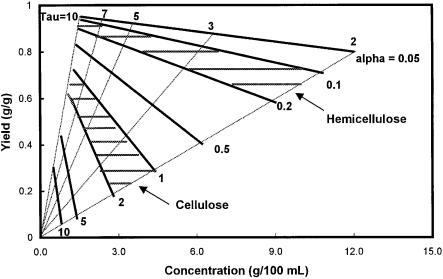
102 |
Y.Y. Lee et al. |
Fig. 3. Yield vs. concentration in a percolation reactor
throughput, a high yield of sugar is obtained but it is done at the expense of the sugar concentration. An inverse relationship thus exists between the yield and the product concentration as shown in Fig. 3. The higher the concentration, the less processing cost and energy would be required in the product separation phase.A trade-off thus exists between the two factors. The point is that the yield value alone without the corresponding concentration is meaningless as a performance indicator. The plot of Fig. 3 (yield vs. concentration) is a simple and the most appropriate way of presenting the reactor performance. The figure has two shaded regions representing the hemicellulose and the cellulose in biomass as they are subjected to dilute acid hydrolysis in a percolation reactor. Taking a point where the concentration is 3%, the figure indicates that the yield for hemicellulose is upward of 90% whereas that for cellulose it is only 50–60%.
The percolation reactor is the one that was used in most of the old wood sugar processes such as the Scholler process [1], the Madison wood sugar process [32, 33], and some of the Soviet processes. Although each process has some unique features in the process details, they all employed a reactor that falls under the category of percolation reactor. For example, in the Scholler process, the reactor was run in a repeated batch manner. For one batch of solid feed, the liquid was replaced several times. The overall reaction mode is similar to the percolation process except that the liquid is fed intermittently, rather than continuously. In all of these processes, the reported yield and sugar concentrations are in the range of 45–55% and 2–4 wt% respectively, in general agreement with the predictions of Cahela et al. [5] (Fig. 3). In one laboratory investigation [34], yields of 80–87% were reported in hydrolysis of wood using a cyclone reactor. The operation mode of this reactor is similar to a percolation reactor in that the
Dilute Acid Hydrolysis of Lignocellulosic Biomass |
103 |
residence times for solid and liquid are varied, the liquid traveling much faster than the solid. However, the high yields were obtainable only with dilute sugar concentration because of the high liquid throughput in the cyclone reactor.
3.4
Hemicellulose Hydrolysis/Pretreatment
With the emergence of cellulase enzymes and their application as saccharification catalysts in the early 1980s, dilute acid hydrolysis has been primarily used as a method of pretreatment for enzymatic hydrolysis. Lignocellulosic materials are only partially digestible in their native form. Increasing their digestibility is of great concern in the enzymatic process. The two factors widely believed to control enzymatic digestibility are the accessible surface area and the crystallinity of the substrate. Increased accessibility of cellulose enables more enzymes to bind to cellulose fiber surfaces, whereas decreased crystallinity increases the reactivity of cellulose, i.e. the rate at which bound enzyme hydrolyzes glucosidic linkages. One common trait of the dilute-acid treatment of lignocellulosic biomass is the increase of porosity and overall surface area. This is achieved by complete or partial removal of hemicellulose and/or lignin. Disruption of crystalline structure of the cellulose fibrils is also evident in many chemical pretreatment methods as indicated by the fact that many pretreated biomasses has shown digestibility higher than that of pure a-cellulose [35–37].
The effectiveness of dilute acid hydrolysis as a pretreatment has been verified experimentally. Researchers at NREL have characterized the susceptibility of a variety of short rotation woody and herbaceous crops and agricultural residues upon dilute acid pretreatment [17, 38–41]. What is more interesting is that the maximum digestibility usually coincides with complete hemicellulose removal. The dilute acid treatment of biomass aimed at hemicellulose hydrolysis has since become a widely accepted pretreatment method for enzymatic hydrolysis [16, 42–44].
3.5
Variations of Percolation Reactor Operation
3.5.1
Step Change of Temperature and Optimum Temperature Difference
Further improvements in the percolation reactor performance can be obtained by exploiting the kinetics of the hydrolysis reaction. The hemicellulose has been modeled to be biphasic as stated in the kinetic section [15, 21, 45–47] i.e. it is composed of two different fragments (a fast-hydrolyzing fraction and a slowhydrolyzing fraction). The biphasic nature of the substrate brings about a number of interesting points concerning the reactor design and operation, especially with regard to the temperature policy and flow configuration in the reactor system. For a simple serial reaction, high temperature is preferred because of the activation energy difference between hydrolysis and decomposition. For biphasic substrates, however, applying uniformly high temperature may cause ex-
104 |
Y.Y. Lee et al. |
cessive decomposition of the sugar released from the fast-hydrolyzing hemicellulose fraction, which builds up at the early phase of the reaction. Therefore, the uniform temperature policy may not be the best solution. Kim and Lee [48] verified the impact of the non-uniform optimum temperature policy on theoretical grounds.
The concept involves two-stage processing of biomass, a low-temperature stage and a high-temperature stage. They found that variation in the temperature during the process, especially a step change from uniform low to uniform high, gives better results than either limit case. They have further determined the optimum temperature difference in step-change operation to be 30°C for a wide range of reaction temperature. The increases in yield was about 6.5% over that of the low uniform temperature case and about 2.5% over the uniform high temperature case for hybrid poplar. In another study involving a corn cobs/ stover mixture (CCSM), increase in yields by 3–11% (depending on the reaction conditions) over that of the uniform temperature operation has been reported [22].
3.5.2
Two-Stage Reverse-Flow Percolation Reactor
Kim et al. [49] introduced a further variation in the percolation reactor operation involving a two-stage reverse-flow scheme. The advantages of it were later verified experimentally by Torget [9]. The process is shown schematically in Fig. 4. The biomass is first treated at a low temperature in percolation mode. It is then treated again at a high temperature. Up to this point, the procedure is identical to the two-stage process with a step change in temperature. The difference is that the stream from the high-temperature treatment is again put through a reactor packed with fresh biomass at low temperature. The reacted solid residue in this reactor is then treated with fresh acid at high temperature. This process is repeated. Figure 4 also illustrates the difference between the temperature step change and the two-stage reverse-flow configuration.
The simulation results of the two-stage reverse-flow reactor arrangement with temperature change indicate that further improvements in performance over that of non-isothermal operation can be achieved. Chen et al. [22] in their modeling study found that the sugar concentration essentially doubles over that of the best-case percolation reactor employing temperature step change only. Viewing this from another angle, about 5% improvement in product yield is obtained over that of the temperature step-change operation for the same product concentration [49]. These modified versions of the percolation reactor and their operational strategies concern mostly the modeling work. They have been suggested as a method of pretreatment for enzymatic hydrolysis.
3.6
Counter-Current Reactor
The most unusual development in reactor design in dilute acid hydrolysis of cellulose hydrolysis is that of a counter-current reactor. It is defined as a mov-
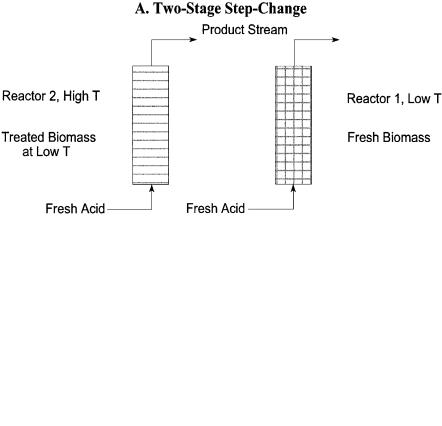
Dilute Acid Hydrolysis of Lignocellulosic Biomass |
105 |
Fig. 4. Schematics of temperature step-change and two-stage reverse flow
ing-bed reactor in which the direction of solid and liquid are reversed (Fig. 2). It was first introduced and analyzed by Song and Lee [7] as a conceptual reactor. The modeling results of this reactor indicate that it outperforms all other known reactors in acid saccharification of lignocellulose rendering high yield and sugar concentration [7]. The supremacy of a counter-current reactor is best explained by the sugar profile curves shown in Fig. 5. In this figure, the calculated sugar concentration profiles are shown for a co-current and a counter-cur- rent reactor. These curves were calculated for identical reaction conditions (a representative condition for cellulose hydrolysis) except that the flow directions of solid and liquid are reversed. In the counter-current reactor scheme, the major portion of the sugar is produced in the vicinity of the liquid outlet point. The stream then travels a relatively short distance before it is washed out of the reactor, thus reducing the time period for the sugar to decompose, consequently raising the yield and sugar concentration.
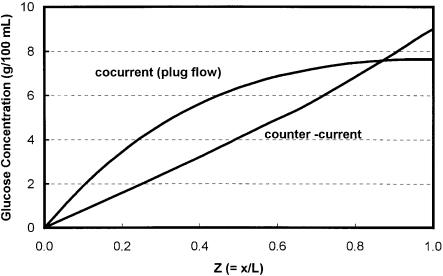
106 |
Y.Y. Lee et al. |
Fig. 5. Profiles of sugar concentration in co-current and counter-current reactors. Substrate: yellow poplar; reaction conditions: acid concentration = 0.08 wt% sulfuric acid, u = 1.0 cm/ min, vo = 1.0 cm/min, T = 230°C, reactor length = 6 inches
3.6.1
Progressing Batch Reactor
Wright et al. [6] made the first attempt at the design and operation of a coun- ter-current reactor in dilute acid hydrolysis of cellulose. In this design, a bank of percolation reactors connected in series was used in order to simulate the counter-current flow pattern. The system used seven percolation reactors in total, one reactor for filling, another for emptying, five in operation. Two of the five reactors were used for prehydrolysis (for hemicellulose), and three for main hydrolysis (cellulose). The five-reactor system was put into operation for a preset duration after which one reactor at the liquid entering side was disconnected for emptying while another reactor prefilled with biomass was added to the other side of the cascade. As this process was repeated, a counter-current flow was simulated, reactors containing biomass moving in one direction, the flow of liquid moving in the other direction. The actual operation was done with flow switching not involving movement of reactors.While a significant improvement was predicted from an ideal counter-current reactor over a single-stage percolation reactor (20% increase in yield and concentration), a number of potential problems were also cited. As the hydrolysis reaction progresses, up to 80% of the wood is converted to soluble products. The wood particles also lose their rigidity and collapse increasing the voidage from approximately 35 to 85% [6], a rather drastic departure from the model assumption. They also pointed out that mass and heat transfer effects within chip size solid particles might adversely

Dilute Acid Hydrolysis of Lignocellulosic Biomass |
107 |
affect the reactor performance. This was verified in single-reactor hydrolysis experiments using wood chips of 1/8–1/4 inch [50]. The sugar concentrations obtainable from the single-reactor study were lower than those reported in previous studies [51]. Overall the performance of the progressing batch hydrolysis reactor was far below the level predicted by the ideal reactor model due to the severity of non-ideal behavior and the operational difficulties.
3.6.2
Effect of Bed Shrinking
A very significant portion of cellulosic biomass is converted to soluble products during acid hydrolysis. This causes either collapse of bed or increase of bed voidage. This was one of the major problems associated with operation of a percolation reactor as noted by Wright et al. [6]. This very phenomenon, although perceived here as a negative point, can become a positive point. In order for this to happen, one condition must be met, i.e. that the bulk density of the solid (or the solid/liquid ratio) in the reactor must remain relatively constant. In this regard, a unique packed reactor was designed by Torget et al. [10] as shown in Fig. 6. The reactor has a fixed and a movable end; the movable end is supported by a compressed spring. As the reaction progresses, gradual depletion of the biomass occurs, making the bed less dense. The spring-attached movable end
Fig. 6. A simplified diagram of a shrinking-bed reactor
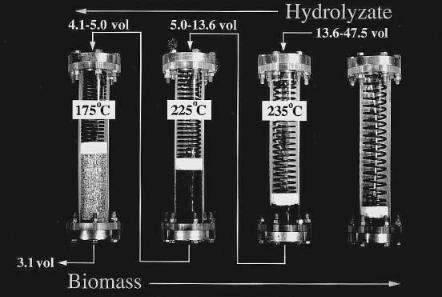
108 |
Y.Y. Lee et al. |
then takes effect pressing the loose biomass particles maintaining the bulk packing density constant. This is strictly a proof-of-concept type reactor designed specifically to keep the bed packing density constant. This is also a reactor with a shrinking-bed depth (reactor volume), hence named a shrinking-bed reactor.
In a shrinking-bed reactor, the flow pattern of liquid becomes more consistent.We now have a well behaved packed-bed reactor throughout the operation without any dead zone. More importantly, the bed shrinkage increases the relative liquid throughput per solid mass in the reactor. We have previously introduced one of the dimensionless parameters in the percolation reactor, t=ut/L. As this parameter increases, the yield increases, but the concentration is expected to decrease (see Fig. 3). However, in the bed-shrinking reactor, we can increase this parameter simply by decreasing the bed depth (L) without increasing the liquid input. The net effect of all this is that an increase in the yield without a decrease in the concentration can be expected. Such an improvement in the reactor performance has been verified experimentally [52] as well as theoretically [53]. The experimental setup of Torget et al. (1998) is based on the shrinking-bed reverse-flow three-stage percolation reactor shown in Fig. 7. This reactor assembly is similar to that of the “progressing batch reactor” previously described [6]. This has three active reactors, one for prehydrolysis and two for main hydrolysis. It is still a simulated counter-current reactor as the direction of liquid flow is the opposite of the reactor movement. The performance of this reactor system is summarized in Fig. 8. Shown in the figure are 83% yield of glucose and near quantitative yield of xylose with 3.6% total monomeric sugar
Fig. 7. Shrinking-bed reverse-flow three-stage percolation reactor

Dilute Acid Hydrolysis of Lignocellulosic Biomass |
109 |
Fig. 8. Three-stage shrinking-bed reactor performance
concentration. It is indeed a phenomenal improvement over that of any other known reactor to date. It is a development significant enough to change the perspective of acid hydrolysis technology and perhaps may even emerge as a viable alternative in biomass saccharification.
3.7
Shrinking-Bed Counter-Current Reactor
The shrinking-bed counter-current reactor demonstration was limited to theoretical studies and proof-of-concept experiments dealing only with a simulated counter-current scheme. It is conceivable that a continuous counter-current reactor that retains the property of bed shrinking can bring about additional improvements in the reactor performance. A theoretical investigation was conducted by Iyer et al. [54] to study the effect of bed shrinking in a continuous counter-current reactor. It is noteworthy that the concept of shrinking bed causes the change of solid velocity within the reactor. The advantage of the shrinking-bed operation over the non-shrinking one is clearly demonstrated in the simulation results shown in Fig. 9. The thin lines connecting the yield and concentration represent the constant liquid velocity contours under shrinkingand non-shrinking-bed operation. As shown in Fig. 9, at a liquid velocity of 3 cm/min, the yield for cellulose hydrolysis is 88% under shrinking-bed operation and 69% under the non-shrinking-bed operation. It is also noted that glucose concentration is much lower in the non-shrinking mode than that in the shrinking mode under identical operating conditions. The drop in yield and concentration in the non-shrinking operation is not entirely due to sugar degradation. The extent of conversion was 99.9% under shrinking while it was only 81% under non-shrinking under identical process conditions. In other words, the optimum solid feeding rate was much lower under non-shrinking than that

110 |
Y.Y. Lee et al. |
Fig. 9. Yield vs. product concentration in shrinking-bed and non-shrinking-bed counter-cur- rent flow reactor. Substrate: yellow poplar; reaction conditions: acid concentration = 0.08 wt% sulfuric acid, T = 230°C, reactor length = 6 inches
under shrinking for the same process conditions. At a liquid velocity of 3 cm/min, the maximum solid feeding rate was found to be only 0.17 cm/min under non-shrinking while it was as high as 0.6 cm/min for shrinking. Even under the reduced solid feeding rate, the yield obtained under non-shrinking is lower than that obtainable under shrinking at any given level of sugar concentration. Taking a sample point in the modeling, in order to achieve a glucose yield of 92%, the simulation results in Fig. 9 indicate that a glucose concentration in the product stream of 2.4 g/100 ml is obtained for the shrinking-bed operation. For the non-shrinking operation, however, the product concentration corresponding to the same yield is only 1.1 g/100 ml, a difference of a factor of two.
Work is currently in progress at NREL to develop a pilot-scale continuous counter-current reactor that retains the property of bed shrinking. This 200 kg/day unit is being constructed in cooperation with Sunds, Inc., Norcross, GA, USA. It consists of two screw-driven reactors (Fig. 10). The first reactor is a screw-fed horizontal plug flow reactor. It is designed for prehydrolysis in which the hemicellulose fraction of the biomass is hydrolyzed. The main hydrolysis reactor is of vertical design with solid moving upward. It is equipped with coun- ter-current mechanism. It contains a broken flight screw within the reactor and two additional screws for solid feeding and withdrawal. The liquid is driven down the reactor by exerting a positive pressure above the reactor pressure to

Dilute Acid Hydrolysis of Lignocellulosic Biomass |
111 |
Fig. 10. Continuous counter-current shrinking-bed reactor
overcome frictional forces and forces exerted by the solids moving upward. A large part of the feasibility study on a true counter-current reactor may come from the test data from this system.
4
Economic Factors
A few economic factors concerning the dilute acid process are discussed here in comparison to the enzymatic process. It must start with the yield that has been the focus of the reactor analysis and development. Production of fuels and chemicals from biomass is substrate cost intensive with feedstock costs representing roughly one half of total production costs [42, 55]. It is of paramount importance in most bioconversion processes to maximize the yield of the product from the biomass substrates. The most advanced dilute acid process has brought the saccharification yield to above 80% as verified by NREL benchscale experiments [10]. The actual yield of the enzyme saccharification is dependent on the effectiveness of the pretreatment. However, it rarely surpasses 90% even with a highly efficient pretreatment. The enzymatic process also requires additional substrate because it has to be produced from cellulosic biomass. The amount of biomass feedstock needed for enzyme production is estimated to be about 9% of the total. With these in consideration, the yield of the acid saccharification is about even with that of the enzymatic process.What can