
- •Foreword
- •1. General Introduction
- •2. Processes and Techniques for Droplet Generation
- •2.1.0 Atomization of Normal Liquids
- •2.1.1 Pressure Jet Atomization
- •2.1.3 Fan Spray Atomization
- •2.1.4 Two-Fluid Atomization
- •2.1.5 Rotary Atomization
- •2.1.6 Effervescent Atomization
- •2.1.7 Electrostatic Atomization
- •2.1.8 Vibration Atomization
- •2.1.9 Whistle Atomization
- •2.1.10 Vaporization-Condensation Technique
- •2.1.11 Other Atomization Methods
- •2.2.0 Atomization of Melts
- •2.2.1 Gas Atomization
- •2.2.2 Water Atomization
- •2.2.3 Oil Atomization
- •2.2.4 Vacuum Atomization
- •2.2.5 Rotating Electrode Atomization
- •2.2.7 Electron Beam Rotating Disk Atomization
- •2.2.9 Centrifugal Shot Casting Atomization
- •2.2.10 Centrifugal Impact Atomization
- •2.2.11 Spinning Cup Atomization
- •2.2.12 Laser Spin Atomization
- •2.2.14 Vibrating Electrode Atomization
- •2.2.15 Ultrasonic Atomization
- •2.2.16 Steam Atomization
- •2.2.17 Other Atomization Methods
- •3.1.0 Droplet Formation
- •3.1.1 Droplet Formation in Atomization of Normal Liquids
- •3.1.2 Secondary Atomization
- •3.1.3 Droplet Formation in Atomization of Melts
- •3.2.0 Droplet Deformation on a Surface
- •3.2.3 Droplet Deformation and Solidification on a Cold Surface
- •3.2.4 Droplet Deformation and Evaporation on a Hot Surface
- •3.2.5 Interaction, Spreading and Splashing of Multiple Droplets on a Surface
- •3.2.6 Sessile Droplet Deformation on a Surface
- •3.2.7 Spreading and Splashing of Droplets into Shallow and Deep Pools
- •4.1.0 Concept and Definitions of Droplet Size Distribution
- •4.2.0 Correlations for Droplet Sizes of Normal Liquids
- •4.2.1 Pressure Jet Atomization
- •4.2.5 Rotary Atomization
- •4.2.6 Effervescent Atomization
- •4.2.7 Electrostatic Atomization
- •4.2.8 Ultrasonic Atomization
- •4.3.0 Correlations for Droplet Sizes of Melts
- •4.3.1 Gas Atomization
- •4.3.2 Water Atomization
- •4.3.3 Centrifugal Atomization
- •4.3.4 Solidification and Spheroidization
- •4.4.0 Correlations for Droplet Deformation Characteristics on a Surface
- •4.4.1 Viscous Dissipation Domain
- •4.4.2 Surface Tension Domain
- •4.4.3 Solidification Domain
- •4.4.4 Partial Solidification Prior to Impact
- •5.1.0 Energy Requirements and Efficiency
- •5.2.0 Modeling of Droplet Processes of Normal Liquids
- •5.2.1 Theoretical Analyses and Modeling of Liquid Jet and Sheet Breakup
- •5.2.2 Modeling of Droplet Formation, Breakup, Collision and Coalescence in Sprays
- •5.2.3 Theories and Analyses of Spray Structures and Flow Regimes
- •5.2.5 Modeling of Multiphase Flows and Heat and Mass Transfer in Sprays
- •5.3.0 Modeling of Droplet Processes of Melts
- •5.3.4 Modeling of Multiphase Flows and Heat Transfer in Sprays
- •5.4.0 Modeling of Droplet Deformation on a Surface
- •5.4.1 Modeling of Deformation of a Single Droplet on a Flat Surface
- •5.4.2 Modeling of Droplet Deformation and Solidification on a Cold Surface
- •6. Measurement Techniques for Droplet Properties and Intelligent Control of Droplet Processes
- •6.1.0 Measurement Techniques for Droplet Size
- •6.1.1 Mechanical Methods
- •6.1.2 Electrical Methods
- •6.1.3 Optical Methods
- •6.1.4 Other Methods
- •6.2.0 Measurement Techniques for Droplet Velocity
- •6.3.0 Measurement Techniques for Droplet Number Density
- •6.4.0 Measurement Techniques for Droplet Temperature
- •6.5.0 Measurement Techniques for Droplet Deformation on a Surface
- •6.6.0 Intelligent Control of Droplet Processes
- •Index
Fundamental Phenomena and Principles 217
that a droplet superheated at impact solidified from the periphery of the splat, and the solidification proceeded radially inward to the center parallel to the splat interface with only slight undercooling. Undercooled droplets solidified immediately on impact with no additional undercooling. These experimental results are counterintuitive to our knowledge of transient nucleation behavior and shed some light on the physics of nucleation and solidification in droplet impact.
Sobolev et al.[408] used analytical models to investigate the mechanisms governing coating-substrate adhesion in thermal spray. They indicated that one of the most important mechanisms is the mechanical interlocking formed mainly due to the roughness of the substrate surface and the high pressure developed during droplet impact and solidification on the surface. Possible deformation, partial/complete melting, and subsequent solidification of the substrate surface, as well as splashing and rebounding of impinging droplets all influence the adhesion mechanisms. The roughness of the substrate surface was shown to be of critical importance for obtaining good adhesion.
3.2.4Droplet Deformation and Evaporation on a Hot Surface
In case of droplet evaporation during impingement, droplet breakup behavior relates well with some specific surface temperatures, such as the maximum evaporation point and the Leidenfrost point.[335][411] The concomitant heat transfer process may be affected by many parameters, such as droplet size, contact angle, impact velocity, impact angle, liquid temperature, initial substrate surface temperature, surface roughness, and their thermophysical properties, as well as surfactant and gravity.[17] In most spray cooling systems, heat transfer during impingement and deformation of droplets on a surface may be categorized into the commonly known boiling curve regimes, i.e., nucleation, transition, and film boiling, in addition to thin film evaporation.[412][413]
218 Science and Engineering of Droplets
Using different criteria, Shi et al.[336] suggested that heat transfer and surface cooling may be classified into two primary regimes: (1) cooling with wetting contact and (2) cooling with nonwetting contact, depending on substrate surface temperature. Liquidsolid wetting contact without bubble nucleation may be achieved in the initial stage when a liquid droplet impinges on a heated surface where heat flow is quasi-steady and conduction-dominant.[336][414] Following this initial transient stage, the heat transfer between the droplet and the surface will enter into nucleation, transition, and film boiling stages, depending primarily on the substrate surface temperature. In the wetting contact cooling regime, heat transfer rate is high due to the continuous or semi-continuous direct contact, followed by the nucleation boiling or transition boiling. In the non- wetting contact cooling regime, heat transfer rate is much lower due to the resistance of vapor generated between the liquid and hot surface, followed by the film boiling. At lower substrate surface temperatures, increasing droplet impact velocity may enhance the heat transfer rate due to the increased contact area, while it turns to lower the heat transfer rate at higher substrate surface temperatures due to rebounding of liquid from the surface. Heat transfer efficiency may be improved by lowering droplet temperature and impact angle. The initial substrate surface temperature has been found to be the most important parameter that influences the impinging heat transfer characteristics[336] because it determines to a large extent in which heat transfer regime the actual cooling process takes place. Numerical modeling[414] has been conducted to calculate the Nusselt number for droplet evaporation on a heated solid surface in the low superheat regime, including the effects of droplet contact angle, solid conductivity, and droplet concentration on heat transfer.
Chandra and Avedisian[411] studied the collision dynamics of a liquid (n-heptane) droplet on a polished, solid, stainless steel surface, and on a liquid film created by deposition of a preceding droplet using a flash photographic method. They presented a comprehensive series of clear images of droplet shape, morphology, and structure during the deformation process. In their experiments, the
Fundamental Phenomena and Principles 219
impact Weber number was fixed at 43, with an initial droplet diameter of 1.5 mm, and an ambient pressure of 0.101 MPa. Surface temperature ranged from 24 ºC to above the Leidenfrost temperature of the liquid. The evolution of wetted area and spreading rate of a droplet both on a stainless steel surface and over a thin liquid film were found to be independent of surface temperature only during the early stages of impact due to negligible surface tension, and viscous effects under the experimental conditions. The influence of surface temperature on the overall deformation and breakup behavior of a droplet is illustrated in Fig. 3.26, where the transition from nucleation boiling to film boiling as the surface temperature is raised above the Leidenfrost temperature (200 ºC) of n-heptane is also shown. At low surface temperatures, a single bubble was observed within the droplet at the point of impact during deformation (Fig. 3.26a). With increasing surface temperature, the population of bubbles within the droplet increased as a result of progressive activation of nucleation sites on the surface. At surface temperatures near to the boiling point (98.4 ºC) of the liquid, a spoke-like cellular structure formed in the center of the circular liquid film of the flattened droplet due to the coalescence of a ring of bubbles that formed within the droplet during spreading (Figs. 3.26b and c). At higher surface temperatures, but below the Leidenfrost point, numerous bubbles appeared within the droplet (Figs. 3.26d and e). However, the overall droplet shape in the early stages of impact was unaffected by the occurrence of these bubbles. At even higher surface temperatures above the Leidenfrost point, no bubbles formed and droplet deformation/breakup entered into the film boiling regime (Fig. 3.26f). This was attributed to the fact that there is no longer solid-liquid contact and thus no opportunity for heterogeneous nucleation to occur on the heated surface.
In a subsequent study, Chandra and Avedisian[385] investigated droplet impingement on a ceramic porous surface. It was found that the spreading rate of a droplet on the porous surface at 22 °C is lower than that on the stainless steel surface, and for a given temperature the maximum spread diameter is smaller on the ceramic surface
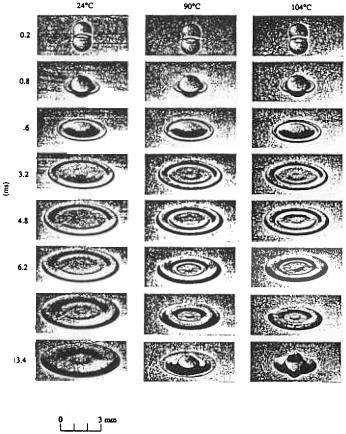



224 Science and Engineering of Droplets
Type RB. With increasing droplet diameter and/or impinging velocity, the shrinking process of the radial film may become unstable, leading to disturbances on the film surface as the film leaves the substrate surface. As the disturbances become larger, the radial film may break up during shrinking or during rebounding. The mode is therefore referred to as RB type.
Type N. With further increasing droplet diameter and/or impinging velocity, the breakup mode may change from the RB type to a completely different type depending on substrate surface temperature. At a surface temperature of 200 ºC, the radial film breaks up due to the formation of vapor that blows through the center of the film before any shrinking takes place. Small droplets are blown upwards by the vapor, while the large pieces of the broken radial film remain on the substrate surface.
Type H. Further increasing droplet diameter and/or impinging velocity from the level in type N, the number of spots where the vapor blows through the radial film increases as compared to that in type N. Small droplets blown by the vapor are distributed even over the radial film, but the blowing-through of the vapor is weaker than in the type N. The pieces of the broken radial film that remain on the substrate surface are similar to those in type N.
Type V. At surface temperatures of 300 ºC and 400 ºC, the radial film does not shrink. The film breaks up and nearly all the small droplets resulted from the breakup are blown upwards by the vapor. The substrate surface becomes dry within a short time period.
Type F. As the droplet diameter and/or impinging velocity further increases from the level in type V, the small droplets resulted from the breakup disperse in the radial direction, leading to transition into type F. In this mode, the radial film leaves the substrate surface in whole because the vapor beneath the film blows through in the radial direction. Thereafter, as the diameter of the film further increases, it is torn and broken up by the vapor into small droplets while the vapor flows beneath it. The small droplets are dragged by the vapor and disperse in the radial direction at velocities faster than
Fundamental Phenomena and Principles 225
that of the radial film. It is interesting to note that droplet dispersion is vertically long-shaped in type N, while it tends to toward the radial direction in types H and V, and finally becomes completely in radial direction in type F.
Senda et al.[335][415] also derived equations describing the thickness and diameter of the radial film formed on a hot surface as a function of the Weber number, and correlated the mean diameter of droplets resulted from the breakup of the radial film with the thickness of the radial film and the Weber number.
Generally, the occurrence of a specific mode is determined by droplet impact properties (size, velocity, temperature), surface properties (temperature, roughness, wetting), and their thermophysical properties (thermal conductivity, thermal capacity, density, surface tension, droplet viscosity). It appeared that the surface temperature and the impact Weber number are the most critical factors governing both the droplet breakup behavior and ensuing heat transfer.[335][412][415]
The droplet impact regime maps developed by Bernardin et al.[412][413] revealed that the droplet lifetime increases systematically with decreasing surface temperature, and the impact Weber number has a strong influence on droplet spreading characteristics and integrity. In the film boiling regime, strong surface tension forces in a droplet of low Weber number (We= 20) preserve the liquid continuum, causing rebound of the entire droplet following impact. In all boiling regimes, an increase in the impact Weber number decreases the droplet spreading time, and increases the instability responsible for liquid breakup, leading to a more violent breakup. Different Weber numbers correspond to distinct temperature dependent heat transfer regimes, possessing different droplet impact characteristics and heat transfer modes. However, temperatures corresponding to the critical heat flux and the Leidenfrost point seemed to be little sensitive to both the droplet impact Weber number, and impact frequency under their experimental conditions.[412]
Andreani and Yadigaraoglu[309] indicated that if the impact Weber number is smaller than 30, practically no breakup occurs;
226 Science and Engineering of Droplets
If the impact Weber number is larger than a critical value of about 50–80, a droplet will form a thin liquid film on the impact surface, and soon disintegrate into smaller droplets. For intermediate Weber numbers, a certain fraction of droplets will break up after moving away from the hot surface, ejecting only a few droplets. The impact angle exhibits a strong influence on the critical Weber number. For compressible flow during droplet impact on a flat substrate, there is evidence that the liquid directed toward the surface may rebound from the substrate after shock wave detaches from the substrate, creating a mist.[390]
As reviewed by Bernardin et al.,[413] previous experiments of sessile droplet film boiling heat transfer revealed that surface features may promote liquid-solid contact in film boiling. A rough surface may require a thicker vapor layer between a droplet and the surface to sustain film boiling, and thus, possess a higher Leidenfrost point (LFP) temperature. The LFP temperature for water droplets on porous ceramic surfaces was found to increase with increasing porosity, possibly due to the increased vapor absorption in the surface pores, so that a larger surface superheat may be required to maintain a sufficiently thick vapor layer sustaining film boiling. A few investigations of the effects of surface roughness on impinging droplet heat transfer showed that surface roughness may promote droplet breakup,[395] and enhance liquid-solid contact in dispersed droplet flow, thus increasing film boiling heat transfer.
Bernardin et al.[413] further studied the effects of surface roughness on water droplet impact history, and heat transfer regimes over broad ranges of Weber number and surface temperature using still and high-speed photographic techniques, and a heat transfer measurement module. The droplet Weber number ranged from 20, 60, to 220, with substrate surface temperatures of 100–280 ºC. Three different surface finishes, i.e., polished, particle blasted and rough sanded, were examined that correspond to arithmetic average surface roughness values of 97, 970, and 2960 nm. The experimental measurements showed that similarly to most boiling systems, the heat
Fundamental Phenomena and Principles 227
transfer during droplet impingement on rough surfaces may be categorized into the commonly known boiling curve regimes, i.e., nucleation, transition, and film boiling, in addition to thin film evaporation. However, the heat transfer processes on rough surfaces involve liquid-surface interactions far more complex than those on smooth surfaces, and the interactions are influenced to varying degrees by surface roughness. The LFP temperature is especially sensitive to surface finish, while the temperature corresponding to critical heat flux (CHF) is fairly independent of surface roughness. In addition, the influence of the surface roughness on the LFP temperature for an impinging droplet is quite different from that for a sessile droplet. For an impinging droplet, protruding features on rough surfaces tend to rupture the liquid film produced by the droplet impact, greatly reducing the pressure beneath the droplet and thus yielding a lower LFP temperature as compared to that on a smooth surface. For a sessile droplet, surface features penetrate the vapor layer beneath the droplet, yielding a higher LFP temperature on rougher surfaces. It was speculated that surface features influence the boiling regimes of droplets in two major ways. First, it leads to violent breakup of the spreading liquid film at high temperatures corresponding to the film boiling and the upper portion of the transition boiling regime. Second, it increases nucleation site density at lower temperatures corresponding to the nucleation boiling and the lower portion of the transition boiling regime. Enhanced nucleation at lower temperatures is largely responsible for the decrease of droplet lifetime on rougher surfaces. The droplet impact regime maps constructed by these researchers for each of the three surface roughness values encompass the parametric effects of the Weber number and surface temperature, and illustrate the complex liquidsolid interactions that occur during the lifetime of the impacting droplet within each regime (nucleation, transition and film boiling). These maps revealed some key trends in droplet impact processes and may serve as an effective reference for understanding droplet
228 Science and Engineering of Droplets
impact behavior and for analytical or numerical modeling of droplet heat transfer on surfaces.
Experiments of Chandra et al.[17] showed that ridges on a surface with a height of the same magnitude as the thickness of the vapor film under an impinging droplet cause vapor bubble nucleation in the droplet, and significantly reduce the droplet evaporation time. Addition of a surfactant (sodium dodecyl sulfate) to water droplets largely reduces the lifetime of the droplets in the state of evaporation or nucleation boiling, and enhances nucleation boiling heat flux by up to 300%. For surface temperatures below those required to initiate nucleation boiling, the primary effect of the surfactant is to reduce liquid-solid contact angle, increasing the surface area wetted by a droplet and decreasing the temperature at which a droplet starts to wet the surface. A decrease in the liquid-solid contact angle also reduces the droplet thickness on the surface, enhancing heat conduction through the droplet and thus increasing the droplet evaporation rate.[363] At higher surface temperatures, the surfactant promotes vapor bubble nucleation and foaming in the liquid, greatly enhancing heat transfer and lowering the vapor bubble nucleation temperature. Addition of the surfactant did not affect the droplet shape during the initial stage of impact, but did increase the maximum spread diameter and reduce the recoil height. An increase in the surfactant concentration reduces the Leidenfrost temperature, above which a droplet is levitated above the surface on a thin film of its own vapor. Changing the orientation of the surface with respect to gravity has no effect on heat transfer. In addition, nucleation boiling is not affected by a reduction in gravity. However, in low gravity, droplets can not remain in stable film boiling and the pressure of vapor under the droplets pushes them away from the surface. Vapor bubbles nucleating on the surface separate and rise into the liquid even in the absence of buoyancy forces.