
6_Podgotovka_topliva_k_szhiganiyu
.pdf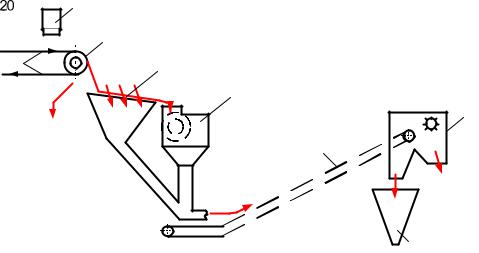
97
6.ПОДГОТОВКА ТОПЛИВА К СЖИГАНИЮ
6.1.Подготовка твердого топлива для камерного сжигания
Дробление. На электростанцию топливо поступает в виде кусков различных размеров: от долей миллиметра до 150–200 мм и более. В процессе подготовки топливо измельчают и подсушивают. Превращение твердого кускового топлива в порошок осуществляют в два этапа: первый этап – дробление до размеров 15–25 мм; второй этап – размол до пылевидного состояния с одновременной подсушкой.
Схема наиболее распространенной одноступенчатой дробильной установки показана на рис. 6.1. В дробильную установку кусковое топливо подается ленточным конвейером. До поступления в дробилку из потока топлива удаляют металлические предметы, повышающие износ и вызывающие поломку оборудования, а также древесную щепу. Металлические предметы, несущиеся на поверхности потока топлива, улавливаются подвесными электромагнитными сепараторами 4, а находящиеся в глубине потока – барабанными электромагнитными сепараторами 5. Щепоуловитель 8 представляет собой вращающийся гребенчатый барабан, который прочесывает поток топлива. Прошедшее между гребнями дробленое топливо проваливается в бункер 9, а щепа сбрасывается в отдельный бункер.
Рис. 6.1. Схема дробильной установки: 1 – ленточный конвейер; 2 – грохот; 3 – дробилка; 4 – подвесной электромагнитный сепаратор; 5 – барабанный электромагнитные сепаратор: 6 – отвод металлических предметов; 7 – конвейер; 8 – щепоуловитель; 9 – бункер дробленого угля; 10 –отвод щепы
В топливе содержится много мелочи, не требующей дробления. Чтобы не перегружать дробилку и более эффективно ее использовать, мелкие кусочки топлива отсеивают на грохотах 2 и затем смешивают их с дробленым топливом, прошедшим через дробилку 3. Грохоты различают неподвижные и
98
подвижные (качающиеся). Неподвижные грохоты выполняют в виде наклонных колосников (угол наклона около 40°). Качающиеся грохоты представляют собой опирающуюся на пружинные опоры наклонную решетку (сито), которую приводят в колебательное движение от специального механизма. Не прошедшие через грохот крупные куски топлива поступают в дробилку.
Размер кусочков топлива после дробления оказывает существенное влияние на работу системы пылеприготовления в отношении ее производительности, эффективности сушки, износа мелющих элементов и расхода электроэнергии на пылеприготовление. С увеличением размеров кусочков топлива эти показатели снижаются.
На выбор конечного размера кусочков топлива после дробления сильное влияние оказывает влажность, так как с ее увеличением наблюдаются потеря сыпучести топлива и замазывание рабочих органов дробильного и пылеприготовительного оборудования. Максимальный размер кусочков после дробления для влажного топлива принимают равным 20–25 мм, для сухого – около 15 мм.
6.2. Угольная пыль и ее характеристики
Дробленое топливо превращают в пылевидное состояние в мельницах, в которых получают полидисперсный порошок, т. е. смесь частиц различных размеров – от 0,1 до 300–500 мкм, а при грубом размоле бурых углей – до 1000 мкм. Полидисперсный характер пыли является следствием того, что размольные устройства не могут выдавать монодисперсную пыль, состоящую из частиц одного, наперед заданного размера, определяемого требованиями наиболее эффективного сжигания топлива. Этому условию отвечала бы пыль с размером частиц 50–100 мкм.
Пылинки топлива имеют неправильную форму, зависящую главным образом от рода топлива, размера его частиц и метода размола. Этим объясняются трудности определения поверхности пыли расчетным путем. Мелкие фракции топлива (с размером менее 20 мкм) по форме близки к кубу или ромбу, остальные имеют довольно сложную изрезанную внешнюю поверхность. В основном суммарная поверхность всех частиц исходной порции угольной пыли определяется ее мелкими фракциями, количество которых велико (хотя общая их масса может быть не определяющей), а удельная поверхность(на единицу массы) больше, чем у крупных частиц. Пыль топлива адсорбирует значительное количество воздуха, и поэтому свежеприготовленный порошок имеет объемную массу 400–500 кг/м3; со временем пыль слеживается, и объемная масса увеличивается до 800–900 кг/м3. Для предупреждения слеживания пыль в бункерах периодически срабатывают до минимального уровня.
Пыль характеризуется высокой текучестью, в бункере пыли можно утонуть и задохнуться. В бункерах работать разрешается только после освобож-
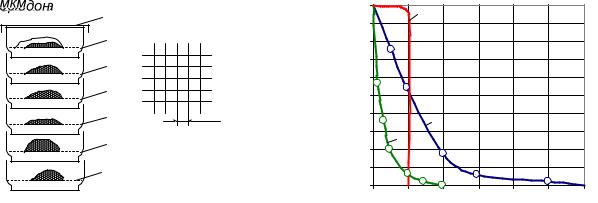
99
дения их от пыли при соблюдении специальных мер предосторожности. Пыль в смеси с воздухом (аэропыль) образует эмульсию, которая подобно жидкости легко транспортируется по трубопроводам. Это положительное свойство широко используется при пневмотранспорте в сушильно-мельничных системах.
Тонкость размола и фракционный состав являются основными характеристиками пыли. Они оказывают большое, а иногда решающее влияние на экономичность пылеприготовительной установки и на работу парового котла. Тонкость размола определяют по рассеву заданной порции полученного порошка на ситах (рис. 6.2). Отобранную порцию пыли просеивают через четыре – пять сит с постепенно убывающим размером ячеек сита (ячейка – квадратное отверстие в решетке сита размером x ). Рассев производят на вибрационной машине. Сита нумеруют по размеру отверстия в свету, выраженному в микрометрах.
Рис. 6.2. Схема производства ситового анализа топлива на комплекте из пяти сит: x – размер ячейки решетки сита, 1– 5 – сита с размером ячейки соответст-
венно 1000, 500, 200, 90, 50 мкм
R |
х |
Рис. 6.3. Зерновая характеристика пыли; 1 – грубая пыль размола бурого угля; 2 – тонкая пыль размола антрацита; 3 – «идеальная» пыль для сжигания
По принятой методике ситового анализа пыли за суммарный остаток на сите заданного размера принимают общее количество частиц с размером больше, чем размер ячейки сита x , мкм, и выражают его в процентах первоначальной массы навески. Этот остаток обозначают через Rx . Так, R1000 (рис.
6.2) представляет долю остатка на сите 1000 мкм. Поэтому такие остатки на ситах называют интегральными. Прошедшую часть угольного порошка называют проходом и обозначают Dx . Обе составляющие выражают в процентах
первоначальной массы пробы. Для каждого сита сохраняется равенство
Rx + Dx = 100% .
С помощью сит возможно рассеивать только пыль с размером зерен более 40 мкм. Более мелкие фракции легко цепляются за шероховатости материала сетки, соединяются друг с другом и, имея малую массу, не проходят сквозь очень тонкие отверстия. Фракционный анализ мельчайшей пыли производят методом отвеивания на воздушном классификаторе с применением
100
различных скоростей воздуха в разделительных цилиндрах. Для рассева берется проба пыли массой 25 или 50 г и доводится в сушильном шкафу до воз- душно-сухого состояния при температуре 50–70 °С.
По данным рассева строят зерновую характеристику, т.е. зависимость остатков Rx от размера частиц x (рис. 6.3), Для ее построения откладывают
значения полных остатков на ситах по оси ординат и соответствующие размеры частиц (т. е. размер ячеек сит) по оси абсцисс. Соединяя плавной кривой экспериментальные точки, получают зерновую характеристику, которую называют интегральной зерновой характеристикой.
Из рис. 6.3 следует, что чем круче зерновая характеристика, тем больше в пыли мелких частиц, легко сгорающих в топках котлов, и уменьшается масса крупных частиц (размером более 200 мкм), ведущих к недожогу топлива. Вместе с тем на получение мелкой пыли затрачивается больше энергии в процессе размола. «Идеальная» топливная пыль (рис. 6.3, кривая 3) характеризуется отсутствием очень мелких частиц, требующих большой затраты энергии на размол, и крупных, которые могут привести к недожогу топлива и экономическим потерям. Однако получить такую монодисперсную пыль в настоящее время невозможно.
Реальная топливная пыль полидисперсна, так как представляет собой смесь различного фракционного состава, и зерновые характеристики полидисперсной топливной пыли резко отличаются от идеальной. Анализ многочисленных зерновых характеристик размола различных видов топлива показал, что все кривые описываются уравнением
R = 100e−bxn |
, |
(6.1) |
x |
|
|
где Rx – остаток на сите с линейным размером отверстий x , %; b и n – по-
стоянные коэффициенты, характеризующие соответственно тонкость измельчения и равномерность зернового состава; e – основание натурального логарифма.
Коэффициент b изменяется в пределах 0,0025–0,1; чем тоньше пыль, тем меньше b. Коэффициент полидисперсности пыли n характеризует структуру пыли, ее распределение по фракциям. При n >1 пыль характеризуется незначительным количеством мельчайших фракций ( x = 15–25 мкм). При n > 1 в пыли растет количество средних и крупных фракций (грубая пыль). При n ≤ 1 масса мелких частиц в пыли увеличивается (тонкая пыль). Коэффициент полидисперсности топливной пыли, являющийся показателем ее структуры, зависит от совершенства мельничной системы и свойств топлива и обычно имеет значения n = 0,8–1,2.
В эксплуатации для быстрой (оперативной) оценки качества угольной пыли пользуются обычно ситом с отверстиями 90 мкм, дающим четкое представление о характере пыли (тонкая или грубая), т.е. пользуются ос-
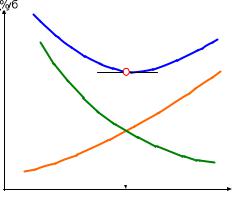
|
|
|
|
|
101 |
|
|
|
|
|
татком R90 . |
|
|
|
|
|
|
|
|
|
|
Для каждого сорта топлива, типа пылеприготовительного и топочного |
||||||||||
устройства имеется наивыгоднейшая, так называемая экономическая тон- |
||||||||||
кость размола, соответствующая минимуму суммарных затрат (рис. 6.4). Эко- |
||||||||||
номическую тонкость размола устанавливают испытанием в процессе экс- |
||||||||||
С |
|
|
|
|
плуатации. |
Основным |
фактором, |
|||
|
|
|
|
|
влияющим на экономическую тонкость |
|||||
|
|
Спп + Смн |
Смн |
|
размола, |
является |
выход |
летучих |
||
|
|
|
|
V Г . Чем больше выход летучих, тем |
||||||
|
|
|
|
|
грубее может быть размол: для бурых |
|||||
|
|
|
|
|
углей R90 ≈ 50–60 %, каменных углей |
|||||
|
|
|
Спп |
|
20–35%, А и ПА 7–8%, поскольку вы- |
|||||
|
|
|
|
ход летучих уменьшает размер коксо- |
||||||
|
|
|
|
|
||||||
|
|
Rопт |
|
|
вого |
остатка |
и обеспечивает раннее |
|||
|
|
R |
|
воспламенение топлива. |
|
|||||
|
|
90 |
90 |
|
|
|||||
|
|
|
|
|
|
|||||
Рис. 6.4. К определению экономическое |
|
В зависимости от выхода летучих |
||||||||
тонкости размола: Cпп – затраты энергии |
веществ (V г , |
%) и фракционного со- |
||||||||
на пылеприготовление; Смн – затраты, |
става пыли экономически оправданную |
|||||||||
вызванные механическим недожогом то- |
тонкость размола можно оценить по |
|||||||||
плива |
|
|
|
|
формуле |
|
|
|
|
|
|
|
|
|
|
Rопт = 4 + 0,8nV г . |
|
(6.2) |
|||
|
|
|
|
|
90 |
|
|
|
|
|
Механические (прочностные) свойства различных видов топлива раз- |
||||||||||
личны. Одна и та же мельница при размоле различных видов топлива имеет |
||||||||||
разную производительность. Для размольной характеристики топлива введе- |
||||||||||
но понятие о лабораторном относительном коэффициенте размолоспособно- |
||||||||||
сти Кло под которым условно принято понимать отношение удельного рас- |
||||||||||
хода электроэнергии Ээт |
на размол эталонного топлива к удельному расходу |
|||||||||
испытуемого топлива Эи |
при одинаковой начальной крупности проб и одина- |
|||||||||
ковой тонкости полученной пыли, т. е. Кло |
= Ээт / Эи . В практике удобнее его |
|||||||||
определять как отношение производительностей лабораторной мельницы на |
||||||||||
испытуемом |
и |
эталонном |
топливах |
за |
одинаковое |
время |
работы: |
|||
′ |
, при этом оба топлива размалывают в воздушно-сухом состоя- |
|||||||||
Кло = Ви / Вэт |
||||||||||
нии. |
|
|
|
|
|
|
|
|
|
|
Расчетный коэффициент размолоспособности получают по формуле |
′ |
+ 0,61. |
(6.3) |
Кло = 0,34Кло |
Эталонным является топливо, отличающееся высокой механической прочностью (донецкий антрацит) и требующее большого расхода энергии на

102
размол, поэтому в подавляющем большинстве случаев коэффициент Кло для испытуемых топлив получается больше единицы. Чем выше значение Кло то-
плива, тем мягче топливо и легче оно разрушается при размоле, тем выше производительность углеразмольной мельницы.
На электростанциях топливо измельчается не в воздушно-сухом со-
стоянии, а при рабочей влажности W р . Фракционные составы рабочей и лабораторной проб также различны. Оба обстоятельства оказывают сильное влияние на производительность мельницы, в связи с чем введено понятие ко-
эффициента размолоспособности рабочего топлива:
Kрт = Кло ППвл , (6.4)
др
где Пдр – поправочный коэффициент на изменение производительности мельницы в зависимости от степени дробления топлива; Пвл – поправочный
коэффициент, учитывающий отрицательное влияние влажности топлива на его размолоспособность (чем выше влажность, тем хуже размалывается топливо и тем меньше этот коэффициент).
Абразивность – одна из важных характеристик топлива, определяющая степень износа мелющих органов и длительность кампании мельничной установки. Это свойство топлива характеризуют коэффициентом абразивности, под которым понимают износ мелющих органов, выполненных из эталонного металла, т. е. убыль их массы G , приходящийся на единицу подведенной к мельнице энергии Э , г/(кВт∙ч):
Кабр = G / Э , |
(6.5) |
В качестве эталонного металла принята сталь марки Ст. 3. Коэффициент абразивности для энергетических углей составляет 0,3–3,0 г/(кВт·ч). Рассмотренные выше характеристики топлива Кло и Кабр связаны между собой.
Более твердые топлива, потребляющие больше энергии на размол, вызывают и более сильный износ мелющих органов.
Срок службы мелющих органов зависит и от износостойкости металла, из которого выполнены мелющие органы. Это имеет особо важное значение для расчета и эксплуатации быстроходных мельниц, для которых велик износ мелющих органов, а их замена требует остановки мельницы.
Наиболее эффективным является применение твердых сплавов для наплавки на мелющие органы. Их использование приводит к увеличению стойкости металла в 2–4 раза, что характеризует повышение рабочей кампании мельниц в том же соотношении.
Конечная влажность пыли (W пл , % влажность после размола топлива)
103
оказывает большое влияние на производительность мельницы, надежность и безопасность сушильно-мельничной системы, бесперебойность подачи пыли
втопку.
Впроцессе размола топлива образующаяся пыль подсушивается горячим воздухом либо высокотемпературными газами, отобранными из газохода котла. Этот сушильный агент используется и для транспорта пыли к горелкам. Угольная пыль не должна иметь чрезмерно высокую влажность, но вместе с тем не должна быть пересушенной. Высокая влажность ограничивает производительность мельницы, приводит к слеживанию пыли в бункерах и налипанию на стенки пылепроводов и оборудование, затрудняет воспламенение и ограничивает скорость сгорания. Вместе с тем чрезмерно сухая пыль склонна к самовозгоранию и взрывоопасна.
Для большинства видов энергетического топлива конечную влажность пыли выбирают равной или близкой его гигроскопической влажности, т. е. к остаточной влажности топлива при его сушке в комнатных (лабораторных) условиях. Допустимая по условиям взрывобезопасности и транспортировки влажность пыли после мельницы должна находиться в следующих пределах:
– для топлив марок А, ПА и Т |
W ги +1 > W пл > W ги ; |
– для каменных углей и сланцев |
W ги ³ W пл > 0,5W ги ; |
– для бурых углей |
W ги + 8 > W пл > W ги . |
Взрываемость. Топливная пыль вместе с воздухом в определенных условиях может образовать взрывоопасную смесь. Взрывоопасность определяется выделением частицами пыли горючих газов, создающих взрывоопасную смесь с воздухом. Интенсивность выхода газов определяется температурой частиц, взвешенных в воздухе. Процентное содержание кислорода в газовоздушной смеси имеет при этом решающее значение. При недостатке кислорода возникновение взрыва невозможно. Предельное содержание О2 в сушиль-
ном агенте, ниже которого топливная пыль не взрывается, равно для торфяной н сланцевой пыли 16%, пыли бурых углей 18%, пыли каменных углей 19%. Присутствие в сушильном агенте инертных продуктов сгорания, а также водяных паров снижает взрывоопасность аэросмеси вследствие снижения доли кислорода.
Квзрывоопасным относят пыль всех твердых топлив, кроме антрацитов
иполуантрацитов. Наибольшую опасность представляют торфяная пыль и
пыль углей, у которых выход летучих веществ выше 25%. Наиболее опасными являются концентрации угольной пыли от 0,3 до 0,6 кг на 1 м3 воздуха. В целях взрывобезопасности на элементах пылеприготовительной установки устанавливают взрывные клапаны, которые при мгновенном росте давления в месте взрыва открываются и сбрасывают часть среды вовне и тем самым снижают давление и исключают разрушение оборудования. Для гашения пожара, который может возникнуть в оборудовании пылесистемы в результате взрыва или при возгорании ранее отложившейся пыли, предусматриваются
104
устройства ввода насыщенного пара, распыление воды или подача углекислоты. Во избежание отложений пыли внутри устройств пылесистемы не допускаются горизонтальные участки на пылепроводах, резкие прямые повороты и неомываемые потоком воздуха углы и участки (зоны застоя движения). Температура аэросмеси после мельниц не должна превышать 80–130 °С и устанавливается в зависимости от качества топлива, склонности полученной пыли к созданию взрывоопасной ситуации (более низкая для топлив с высоким выходом летучих горючих веществ).
6.3. Сушка топлива в процессе пылеприготовления
6.3.1. Цели и задачи сушки топлива
Процесс термической обработки топлива, при котором снижается процент влажности с некоторой начальной величины W1 до конечной W2 , назы-
вается сушкой.
Для сравнительно сухих углей с внешней влажностью 8–10% сушка осуществляется непосредственно в процессе размола путем подачи в корпус мельницы горячих газов или воздуха. Для влажных топлив при внешней влажности 15–20% необходима предварительная подсушка перед поступлением их в мельницу. Она осуществляется обычно во взвешенном состоянии в сушильных трубах с нисходящим или восходящим потоком газов.
Для топлив с внешней влажностью более 20% необходима сушка отделенная от системы пылеприготовления. В этом случае необходима так называемая разомкнутая система пылеприготовления, в которой водяные пары выбрасываются с сушильным агентом в атмосферу, в отличие от первых двух.
По конструктивному оформлению различают следующие виды сушилок: барабанные сушилки; трубчатые сушилки; трубы-сушилки.
По сушильному агенту сушилки могут быть классифицированы: огневые сушилки (сушка дымовыми газами); паровые сушилки; пневматические сушилки.
Подробно конструкции сушилок будут рассмотрены ниже.
6.3.2 Процесс сушки
Процесс сушки для всех видов сушилок представляется следующим образом. В первый момент топливо прогревается до температуры, соответствующей температуре мокрого термометра (рис. 6.5). Количество влаги ( xn − x1 ), испаряемой за этот промежуток времени, составляет всего 1–2% от
первоначального влагосодержания топлива. Второй период сушки (А–В) характеризуется постоянной температурой топлива и постоянной скоростью сушки. Сушка за данный период может быть оценена как выделение влаги со
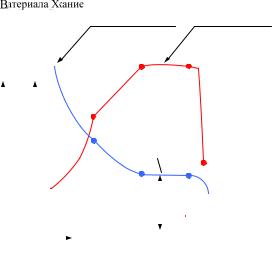
105
свободной поверхности воды, т. е. сопротивление внутренней диффузии за этот период невелико. После прохода точки В идет повышение температуры топлива, а скорость сушки падает пропорционально уменьшению влагосодержания топлива. Процесс протекает подобным образом до второй критической точки С, которая соответствует достижению внешней поверхностью топлива воздушно-сухой (гигроскопической) влажности. После точки С процесс сушки еще более замедляется, а температура топлива соответственно повышается. Сушка обычно прекращается, когда топливо достигает гигроскопической влажности.
|
|
|
|
|
|
|
Сушка топлива необходима для |
|
|
|
|
|
|
|
улучшения процессов размола, полу- |
|
|
|
|
|
|
|
чения устойчивости воспламенения и |
|
|
|
|
|
|
|
горения. Влажное топливо налипает |
|
|
|
|
|
|
|
на мелющие детали, замазывает их. |
|
|
|
|
|
|
|
|
|
|
|
|
|
|
|
Это ведет к снижению производи- |
|
Температураматериала Скоростьсушки |
|
х2 t0 х1 хn |
|
тельности мельниц и увеличению рас- |
||
|
|
|
хода энергии на помол. |
||||
|
|
х3 |
|
||||
|
|
|
Для того чтобы сохранить хруп- |
||||
|
|
|
|
|
|||
|
|
|
|
|
|
|
|
|
|
|
|
m |
|
|
кие качества топлива и поддержать |
|
|
|
|
t |
|
|
|
|
|
|
|
|
|
|
высокую производительность мель- |
|
|
|
|
|
|
|
|
|
|
|
|
|
|
|
ниц, необходимо не допускать при |
|
|
|
|
|
|
|
|
Рис. 6.5. Сушка топлива в процессе размо- |
размоле влажность топлива выше оп- |
||||||
ла |
ределенной величины. Эта влажность |
||||||
|
|
|
|
|
|
|
зависит от сорта размалываемого топ- |
лива. Каменные угли, например, хорошо размалываются при влажности ниже
1–3%.
Сушка топлива в процессе размола вследствие образования новых поверхностей протекает весьма интенсивно. Поэтому конечная влажность пыли определяется исключительно количеством тепла, подводимого к системе, а не динамикой сушильного процесса.
6.3.3. Мельничное устройство как сушильный агрегат
Во время размола в мельнице происходит энергичная сушка топлива, обуславливаемая соприкосновением горячего сушильного агента с непрерывно обнажаемыми влажными поверхностями топлива. При этом сушка происходит настолько быстро, что количество испаряемой влаги определяется не скоростью сушки, а количеством подведенного тепла.
Производительность объема барабана шаровой барабанной мельницы значительно выше, чем в сушилках и на подмосковном угле достигает 120 кг влаги/(м3×ч) при начальной температуре воздуха 350 °C. В шахтных мельницах, имея в виду, что сушка топлива заканчивается в полости ротора, напряжение рабочего объема по влаге составляет 600–650 кг/(м3×ч).

106
При влажных топливах, как говорилось выше, применяется подсушка топлива перед мельницей в трубах-сушилках с восходящим либо с нисходящим потоком.
6.3.4. Тепловой баланс сушильно-мельничной системы
Приход тепла в кДж на 1 кг сухого угля:
′ |
′ |
′ |
, |
(6.6) |
Qпр = qг |
+ qэ + qт |
+ qпр |
||
где qг′ – физическое тепло сушильного агента; |
|
|
||
|
|
1 |
|
|
qг′ = (Cв |
+ d′ Cвп ) |
μ t2′ , |
(6.7) |
где Cв – средняя весовая теплоемкость сухого воздуха (либо газа), кДж/(кг°C); d′ – влагосодержание газов (либо воздуха), кг/кг; Cвп – средняя весовая теплоемкость водяных паров при t′; μ – концентрация топлива в кг сырого угля на 1 кг сухого сушильного агента; t2′ – температура сушильного
агента в месте подвода сырого топлива, °C;
qэ – тепло, выделяемое в результате размола топлива, кДж/кг,
q = |
860 Kc |
Эм |
= 0,86 K Э , |
(6.8) |
|
|
|||
э |
1000 |
|
с м |
|
|
|
|
|
где Kc – коэффициент, учитывающий долю энергии, превращаемой в тепло в процессе размола; Эм – удельный расход энергии на размол, кДж/кг; qт′ – физическое тепло топлива,
qт′ = Cтtт′, |
(6.9) |
где Ст – теплоемкость топлива, кДж/(кг°С); t′т – его температура; qпр′ – фи-
зическое тепло присасываемого воздуха (при его влажности d =0,01 кг/кг), кДж/кг;
′ |
α |
|
|
= (Cв + 0,01 Cвп ) μ tпр , |
(6.10) |
||
qпр |
где tпр – температура холодного присосанного воздуха. Расход тепла