
МУ РГР МСП
.pdf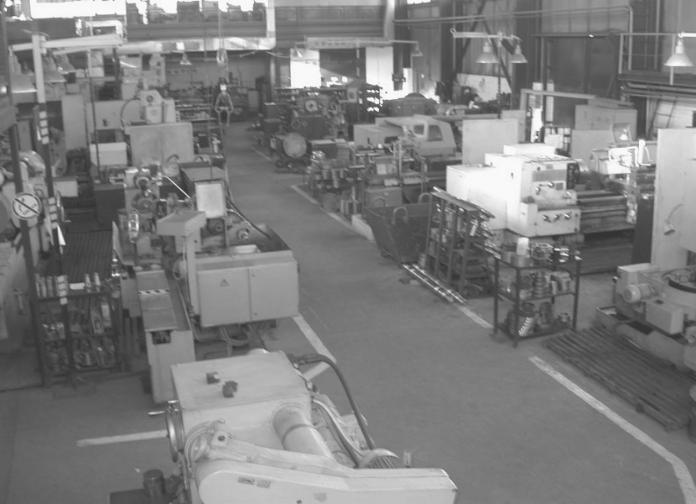
ФЕДЕРАЛЬНОЕ АГЕНСТВО ПО ОБРАЗОВАНИЮ Государственное образовательное учреждение высшего профессионального образования
ВЯТСКИЙ ГОСУДАРСТВЕННЫЙ УНИВЕРСИТЕТ
Кафедра технологии автоматизированного машиностроения
Проектирование механосборочного цеха
Методические указания для выполнения расчетно-графической работы по курсу
“Проектирование машиностроительного производства”
Для студентов дневного отделения специальности 151001 – технология машиностроения
К И Р О В 2009
Печатается по решению редакционно-издательского совета Госудаоственного образовательного учреждения высшего профессионального образования “Вятский государственный универсистет”
УДК 621.658.2.002 П37
ИНПИ ГОУ “ВятГУ” У 001046
Составитель к. т. н., доцент кафедры ТАМ В.А. Жуйков
Авторская редакция
©Жуйков В.А., 2009
©ГОУ ВПО “ВятГУ”, 2009
|
Содержание |
|
1 Цель работы |
4 |
|
2 Общие положения |
4 |
|
3 Расчетная часть |
5 |
|
3.1 |
Определение количества основного оборудования5 |
|
механосборочного цеха |
7 |
|
3.2 |
Определение числа основных рабочих |
|
3.3 |
Определение площади механического отделения8 |
|
цеха |
Расчет сборочного отделения |
8 |
3.4 |
||
3.5 Проектирование вспомогательных отделений |
10 |
|
3.6 |
Определение количества вспомогательных рабочих 15 |
|
3.7 |
Определение численности ИТР |
16 |
3.8 |
Определение численности служащих |
16 |
3.9 |
Определение количества младшего обслуживающего17 |
|
персонала (МОП) |
17 |
|
3.10 Сводная таблица всех работающих |
3.11Распределениеработающихпокатегориямсанитарной18 характеристики производства
3.12 Расчет площадей бытовых помещений |
19 |
4 Разработка компоновочного плана |
22 |
Приложение. Библиографический список |
32 |
3
1Цель работы
Расчетно-графическая работа выполняется после изучения основных теоретических положений по курсу «Проектирование машиностроительного производства». При ее выполнении студент получает практические навыки расчета основных параметров механосборочного производства (МСП), осуществляемого на стадии предварительного проектирования (технико-экономического обоснования) МСП, в т.ч. количества оборудования, работающих и площадей всех отделений – основных, вспомогательных и служебно-бытовых - механосборочного цеха и разработки его компоновочного плана.
2 Общие положения
Работа состоит из двух частей – расчетной, на которой определяются числовые показатели проектируемого производства и исходные данные для разработки компоновочного плана, и графической - проектирование компоновочного плана.
Соответственно, работа включает пояснительную записку с расчетами, выполненную в соответствии с правилами оформления технической документации, и 1 л ф. А1 компоновочного плана.
Пояснительная записка должна содержать выданное индивидуальное задание с исходными данными. В пояснительной записке нужно привести наименования рассчитываемых показателей, формулы для расчета со всеми использованными числовыми значениями, размерность полученных величин.
Требования к компоновочному плану изложены в разделе
4.
4
3 Расчетная часть
3.1 Определение количества основного оборудования механосборочного цеха
Tг |
3.1.1 |
Определяется |
годовая суммарная |
станкоемкость |
с-ч, механической обработки исходя из заданных |
||||
станкоемкости одного изделия Т и годовой программы выпуска |
||||
N. |
|
|
|
|
|
3.1.2 |
Определяется |
расчетное Ср и |
потребное Cп |
«обезличенное» количество станков в цехе, необходимое
для выполнения годовой программы
Tг
Ср= ---,шт, Fд
где Fд – эффективный годовой фонд времени работы оборудования, ч. Принимается из таблицы 1 в зависимости от числа смен и вида оборудования.
Потребное количество станков
Cр
Cп= -----,шт,
Kзср
где Кзср – средний коэффициент загрузки станков.
Для единичного и мелкосерийного производства Кзср =0.8- 0.9; для серийного 0.75 - 0.85; для массово-поточного и крупносерийного - 0.65-0.75.В расчете принять Кзср для серийного или средне-серийного производства.
Полученное количество оборудования округляем до целого числа и, разбив его по видам оборудования в соответствии с рекомендациями, приведенными в таблице 2, заносим в таблицу 3: «Состав оборудования цеха»
5

Таблица 1 -Эффективные годовые фонды времени
Тип Оборудования |
фонд времени в час при числе смен |
|||
1 |
2 |
3 |
||
|
|
|
|
|
Металлорежущее |
2030 |
4015 |
5960 |
|
оборудование,Fд |
||||
|
|
|
||
Уникальное |
- |
3890 |
5590 |
|
оборудование, Fд |
||||
|
|
|
||
Автоматические |
- |
3725 |
5465 |
|
линииРабочее, Fд место без |
||||
2070 |
4140 |
6210 |
||
оборудования,Fдрм |
||||
|
|
|
Таблица 2 - Ориентировочное процентное соотношение типов станков
|
|
|
|
|
|
№ |
|
Типы станков |
Цех токарных, |
Цех расточных |
Цех |
|
специальных |
и фрезерных |
|||
|
|
|
и агрегатных |
станков |
|
|
|
|
станков |
|
|
1 |
|
Токарно-винторезные |
19 |
16 |
18 |
2 |
|
Токарно-револьверные |
4 |
3 |
5 |
3 |
|
Токарные автоматы и п/а |
2,5 |
- |
1 |
4 |
|
Токарно-карусельные |
2 |
1 |
2,5 |
5 |
|
Расточные |
6 |
7 |
6 |
6 |
|
Координатно-расточные |
1,5 |
- |
- |
7 |
|
Сверлильные |
10 |
5 |
5 |
8 |
|
Фрезерные |
15 |
13 |
11 |
9 |
|
Строгальные и долбежные |
5 |
8 |
4 |
10 |
|
Протяжные |
1 |
1 |
1 |
11 |
|
Шлифовальные |
12 |
13 |
12 |
12 |
|
Зубообрабатывающие |
6 |
9 |
10 |
13 |
|
Специальные, агрегатные, |
15 |
22 |
23 |
|
автоматы и п/а |
||||
14 |
|
Отрезные |
1 |
2 |
1,5 |
ИТОГО |
|
100 |
100 |
100 |
|
Из них с ЧПУ |
22 |
15 |
16 |
Таблица 3 - Состав оборудования цеха
|
|
|
|
|
Типы станков |
% |
Количество |
1. |
|
|
|
2. |
|
|
|
|
|
|
|
|
Итого |
100 |
Сп |
6
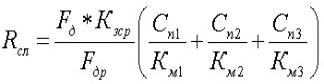
К принятому числу станков добавляются 5-30% дополнительного оборудования Сд, не предусмотренного техпроцессами изготовления деталей и используемого, например, для удаления заусенцев, правки заготовок, нагрева их и других действий. Эти станки в таблицу 9 не заносятся, но учитываются в дальнейшем при расчете ремонтного отделения, площади механического отделения цеха и числа участков цеха.
3.1.3 Определяется тип цеха в зависимости от массы обрабатываемых деталей и количества оборудования
(табл.4)
Таблица 4 - Тип цеха (малый, средний, крупный) |
||||
Максимальная |
Число станков в цехе |
|||
масса деталей |
||||
в тн, до |
|
|
|
|
|
малом до |
среднем |
крупном св. |
|
0,02 |
150 |
150 |
- 300 |
300 |
2,0 |
125 |
125 |
- 250 |
250 |
Тип цеха учитывается при проектировании вспомогательных отделений.
3.2. Определение числа основных рабочих
Количество станочников определяют по формуле:
где Fдр - действительный годовой фонд времени рабочего (1800 час. при 24 рабочих днях отпуска);
Сп1 |
– принятое число токарных автоматов и п/а, станков |
с ЧПУ и агрегатных станков, у которых коэффициент |
|
многостаночности Км1 = 1,5…2; |
|
Сп2 |
– принятое число зубообрабатывающих станков, у которых |
Км2 |
= 3…5; |
Сп3 |
– принятое число всех остальных станков, у которых |
Км3 |
=1. |
7
Проверьте чтобы Сп1 + Сп2 + Сп3 = Сп.
Количество производственных рабочих-слесарей Rсл определяется укрупнено: для единичного и мелкосерийного производства - 3-5%, для крупносерийного и массового производства 1-3% от числа рабочих – станочников.
Впервую смену работают: в массовом производстве 50%,
всерийном – 55%, в мелкосерийном – 60% от общего числа станочников и слесарей.
3.3Определение площади механического отделения цеха
Площадь механического отделения цеха может быть определена по средней удельной производственной площади на один станок и одного слесаря. Средняя удельная площадь принимается 10-12 м2 для малых, 15-25 м2 для средних, 30-45 м2 для крупных станков.
Удельная площадь на одного слесаря-верстачника составляет 5 м2.
3.4Расчет сборочного отделения
3.4.1 Определение трудоёмкости сборочных работ Сначала определяется общая годовая трудоемкость всех
сборочных работ Тсб в процентах от годовой станкоемкости изделия. Затем общая трудоемкость сборки делится на составляющие трудоемкости конвейерной сборки Тк , испытаний Тисп , прочих сборочных работ Тпр и стендовой
сборки Тст=Тсб-Тк-Тисп-Тпр. Необходимые для расчетов данные приведены в задании.
3.4.2 Количество стендов стационарной сборки
Сст= |
Т ст |
,шт, |
---------F дрм *n |
где Fдрм – эффективный годовой фонд времени рабочего места
(табл.1);
n – среднее количество рабочих, приходящихся на 1 рабочее место при сборке (плотность работы).
8
При конвейерной сборке n принимается равным 1, при стендовой - 2, 3, 4 и т.д., в зависимости от габаритных размеров и сложности сборки.
3.4.3 Определяем число рабочих мест на конвейере
T1к Zr=-------, р.м.,
t1*n
где Т1к=Тк / N - трудоёмкость сборки одного изделия на конвейере, ч-ч;
t1=Fдрм/ N- такт сборки,ч.
3.4.4 Определяем количество слесарей-сборщиков
На конвейерной сборке :
Rк=Тк / Fдр, чел.
На участке испытаний:
Rис=Тис / Fдр, чел.
На стендовой сборке:
Rст=Тст / Fдр, чел.
На прочих сборочных операциях:
Rпр=Тпр / Fдр, чел.
Примечание. Фонд времени рабочего приводился в п.3.2.
Впервую смену работают: в массовом производстве 50%,
всерийном – 55%, в мелкосерийном – 60% от общего числа сборщиков.
3.4.5Определение площади сборочного отделения
При укрупнённых расчётах площадь сборочного отделения Fсб принимают: для единичного и мелкосерийного производства 50-70%, для серийного 20-40%, для массового 18-25% от площади механического отделения цеха.
9
3.5 Проектирование вспомогательных отделений
3.5.1 Заготовительное отделение
В малых цехах заготовительное отделение располагается непосредственно в помещении склада металла и отдельно не определяется. Для средних и крупных цехов количество оборудования определяется на основании разработанных технологических процессов на заготовительные операции. В составе заготовительного отделения в этом случае должны быть предусмотрены: ленточные отрезные станки, отрезные дисковые п/а, фрезерно-центровочный, обдирочный и правильный станки. Расположено оно должно быть смежно со складом металла и заготовок.
3.5.2 Заточное отделение
Определение количества универсальных заточных станков Сзат этого отделения производится укрупнено, в процентах (таблица 5) от количества станков, обслуживаемых заточным отделением Соб. В это число не включают шлифовальные, полировальные станки, работающие абразивным инструментом, и специализированные (протяжные, шевинговальные и т.п.) станки, работающие специальным инструментом, для заточки которого требуются специальные заточные станки. Многошпиндельные и агрегатные станки включаются в число обслуживаемых станков Соб с учетом общего количества шпинделей и головок Смш аг:
Смш аг = Шса*К1+Шас*K2,
где Шса - общее число шпинделей станков-автоматов; Шас - общее число головок агрегатных станков;
К1, K2 - коэффициенты, учитывающие не одновременность работы инструментов, равные соответственно 0.4 и 0.15.
10