
Литература / Комар_строймат
.pdfлотые доменные гранулированные шлаки, диатомит, трепел, опоки, туф, пемзу, трасс. Кроме указанных в легкие бетоны вводят добавки, являющиеся замедлителями или ускорителями твердения. В качестве порообразователей для снижения плотности в состав легких бетонов вводят алюминиевый порошок, пергидроль, смолосапониновый порообразователь и другие добавки.
Для приготовления и увлажнения легкого бетона используют питьевую воду, отвечающую тем же требованиям, что и для тяжелых бетонов.
Защита стальной арматуры в легких бетонах. Повышенная пористость легких бетонов способствует возникновению и разви тию коррозии арматуры в железобетонных изделиях. Поэтому в агрессивной среде легкий бетон армированной конструкции должен быть плотным. Как показывает практика, в таком бето не содержание цемента должно быть не менее 250 кг/м3. Иногда арматуру покрывают различными составами: цементно-казеино- вой суспензией с нитритом натрия; битумной мастикой с молотым песком, золой и растворителем — толуолом, битумоцементной мастикой.
§ 6.12. Основы проектирования состава легких бетонов
При подборе состава легких бетонов исходят из условия получения экономичного бетона, обеспечивающего не только удобоукладываемость бетонной смеси и прочность бетона, но и
заданную плотность при наименьшем расходе цемента.
Задача подбора состава легкого бетона усложняется по сравнению с подбором состава тяжелого бетона. Подбирая состав тяжелого бетона, обычно находят соотношение между щебнем и песком, требуемое В/Ц и расход цемента. В легком бетоне трудно установить расчетом В/Ц, а удобоукладываемость колеблется в больших пределах. Это связано с тем, что пористые заполнители обладают значительным водопоглощением, интенсивно отсасывая воду из цементного теста. Шероховатая поверхность пористых заполнителей затрудняет получение точных показателей удобоукладываемости смеси. Эти обстоятельства приводят к тому, что состав легкобетонной смеси подбирают опытным путем, определяя оптимальный расход воды для каждого состава бетона, устанавливая зависимость прочности бетона от расхода цемента при оптимальных расходах воды.
Существует несколько методов подбора состава легкого бетона, но чаще всего применяют метод подбора состава легкого бетона по оптимальному расходу воды. При этом пользуются способом опытных затворений, который включает следующие операции: выбор наибольшей крупности и определение содержания крупного и мелкого заполнителей (рис. 6.15); определение расхода вяжущих и добавок для пробного замеса; предварительный расчет расхода заполнителей на 1м3 смеси для приготовления пробных замесов; уточнение расхода воды по заданной
— 231 —

Рис. 6.15. График зернового состава пористых заполнителей:
а — пористого щебня и песка; б — пористого гравия и песка; 1 — предельная крупность заполнителя 10 мм; 2 — то же, 20 мм; 3 — то же, 40 мм
подвижности или выявление оптимального содержания воды по наибольшей плотности уплотненной легкобетонной смеси; установление зависимости между расходом вяжущего и прочностью бетона при заданной подвижности смеси. Одновременно устанавливают зависимость между расходом цемента и плотностью бетона при принятых условиях уплотнения смеси.
Обычно для приготовления легкого бетона принимают наибольшую крупность гравия до 40 мм, а щебня — до 20 мм. При использовании пористого заполнителя с предельной крупностью до 20 мм бетон при прочих равных условиях получают более однородным.
Типовые нормы расхода цемента для приготовления различных видов легкого бетона приведены в СНиП 5.01.23—83.
Бетонные смеси с легкими заполнителями приготовляют аналогично обыкновенным бетонным смесям. Однако легкобетонную смесь следует более тщательно перемешивать. Уплотнение легкого бетона производят теми же методами, что и тяжелого бетона. При этом следует учитывать, что плотность легкого бетона можно повысить не только подбором соответствующего гранулометрического состава бетонной смеси, расходом воды и применением пластифицирующих добавок, но и интенсивным и длительным уплотнением. Воздействие вибрирования на легкобетонные смеси отличается рядом особенностей. Большая разница в плотности заполнителя и цементного теста приводит при вибрировании к слабому уплотнению в нижней зоне и разуплотнению смеси в верхней зоне изделия, поэтому легкобетонные смеси требуют вибрирования с пригрузом, компенсирующим недостаток собственной массы заполнителей. Чем меньше плотность заполнителя, тем больше требуется пригруз.
Свежеотформованные предельно уплотненные легкие бетоны обладают высокой структурной прочностью, позволяющей немедленную распалубку. Легкобетонные изделия можно формо-
— 232 —
вать всеми способами, применяемыми для формования тяжелых бетонов (см. гл. 11 ) . Аналогичным образом организуется и ускоренное твердение их.
Свойства легких бетонов. По структуре легкие бетоны подразделяют на плотные, поризованные и крупнопористые.
Основным показателем прочности легкого бетона является класс бетона установленный по прочности его на сжатие: В2; 2,5; 3,5; 5; 7,5; 10; 12,5; 17,5; 20; 22,5; 25; 30; 40; для теплоизо-
ляционных бетонов, кроме того, предусмотрены классы В0,35; 0,75 и 1.
Наряду с прочностью важной характеристикой легкого бетона является его плотность в сухом состоянии. По этому показателю легкие бетоны подразделяют на марки: Д200; 300; 400; 500; 600; 700; 800; 900; 1000; 1100; 1200; 1300; 1400; 1500; 1600; 1700; 1800; 1900 и 2000. Уменьшить плотность легких бетонов можно путем образования в цементном камне мелких пор с помощью пено- и газообразующих веществ.
Теплопроводность легких бетонов зависит в основном от плотности и влажности. Увеличение влажности на 1 % повышает теплопроводность на 0,016...0,035 Вт/(м°·С).
По морозостойкости легкие бетоны делят на 10 марок: F 25, 35, 50, 75, 100, 150, 200, З00, 400 и 500. Для наружных стен зданий применяют бетоны с морозостойкостью не ниже F 25.
Водонепроницаемость конструкционных легких бетонов может быть высокой. Установлены следующие марки легкого бетона на пористых заполнителях по водонепроницаемости W 0,2; 0,4; 0,6; 0,8; 1; 1,2 (МПа гидростатического давления).
Легкий бетон — эффективный материал, который имеет большую перспективу.
§6.13. Ячеистые бетоны
Ячеистые бетоны являются разновидностью легких бетонов с равномерно распределенными порами (до 85% от общего объема бетона); их получают в результате затвердевания предварительно вспученной порообразователем смеси вяжущего, водыикремнеземистогокомпонента.
По виду применяемого вяжущего ячеистые бетоны делят на следующие группы: газобетоны и пенобетоны, получаемые на основе портландцемента или цементно-известкового вяжущего;
газосиликаты и пеносиликаты, получаемые на основе смеси извести-кипелки и кварцевого песка; газошлакобетоны и пеношлакобетоны, получаемые из смеси извести и тонкомолотых доменных гранулированных шлаков или золы-уноса.
По условиям твердения различают ячеистые бетоны пропа-
ренные и автоклавного твердения.
По назначению и плотности ячеистые бетоны делят на теплоизоляционные с плотностью в сухом состоянии до 500 кг/м3;
конструкционно-теплоизоляционные с плотностью 500...900 кг/м3
— 233 —
иконструкционные с плотностью 900... 1200 кг/м3. По показателям плотности установлено десять марок ячеистого бетона от Д300 до Д1200.
Ячеистые бетоны, будучи материалами весьма пористыми, отличаются низкой плотностью и соответственно относительно невысокой прочностью. Такая же связь, но несколько другого порядка, существует между плотностью и теплопроводностью — показателем, особо важным для ячеистых бетонов. Теплопроводность ячеистых бетонов изменяется 0,07...0,25 Вт/(м·°С).
Видеальном случае структура ячеистого бетона представляет замкнутые ячейки размером 0,4... 1,5 мм. Равномерность размеров
изамкнутый характер пор уменьшают концентрацию напряжений
вцементной оболочке ячеек, распределение напряжений происходит равномерно по сечению элемента, и прочность ячеистого бетона увеличивается. При неудовлетворительной структуре наряду с мелкими замкнутыми порами присутствуют открытые крупные ячейки, которые могут сообщаться не только между собой, но и с окружающей средой. При такой структуре ячеистого бетона уменьшаются прочность и морозостойкость, увеличиваются теплопроводность и водопоглощение. Высокая морозостойкость ячеистых бетонов объясняется особенностями их строения — большим количеством замкнутых пор, наполненных воздухом или газом. Для ячеистых бетонов установлены следующие марки морозостойкости: F15, 25, 35, 50 и 100.
Важным показателем прочности ячеистого бетона является прочность камня-оболочки ячейки, которая зависит не только от вида вяжущего, но и условий его твердения и влажности бетона. Наиболее высокую прочность имеют бетоны после автоклавной обработки, при этом значительно экономится вяжущее вещество. В зависимости от гарантированных значений прочности ячеистого бетона на сжатие установлены следующие классы (МПа):
В0,35; 0,75; 0,85; 1; 1,5; 2,5; 3,5; 7,5; 10; 12,5; 15; 17,5 и 20.
Большие усадочные деформации вызывают изменением влажности при высыхании бетона, их величина зависит главным образом от начальной влажности изделий после тепловлажностной обработки. После автоклавного твердения влажность изделий доходит до 25% по массе, а после пропаривания— до 50%. Усадка после высыхания достигает соответственно 1,2 и 2,5 мм/м. От усадочных деформаций могут появиться трещины, значительно снижающие долговечность изделий.
Введение в состав ячеистого бетона немолотого песка или снижение расхода воды затворения, а также применение более совершенной технологии изготовления изделий — вибровспучивания с последующей автоклавной обработкой — позволяет значительно снизить усадочные деформации.
Вяжущим для приготовления ячеистых бетонов обычно служат портландцемент, молотая негашеная известь. В качестве кремнеземистого компонента используют измельченный кварцевый песок, молотые доменные шлаки и золу-унос.
—234 —
Вода для ячеистых бетонов должна удовлетворять общим требованиям, предъявляемым к воде для бетонов.
Для образования ячеистой структуры бетона применяют пено- и газообразователи. В качестве пенообразователей используют несколько видов поверхностно-активных веществ, способствующих получению устойчивых пен. Клееканифольный пенообразователь приготовляют из мездрового клея, канифоли и водяного раствора едкого натра; смолосапониновый — из мыльного корня и воды, иногда для увеличения стойкости пены в него вводят жидкое стекло; алюмосульфонафтеновый — из керосинового контакта, сернокислого глинозема и едкого натра; пенообразователь ГК — из гидролизованной боенской крови и сернокислого железа. В качестве газообразователей используют алюминиевую пудру ПАК-3 или ПАК-4 с содержанием активного алюминия 82% и тонкостью помола 5000...6000 см2/г. Расход алюминиевой пудры зависит от плотности получаемого газобетона и состав-
ляет 0,25...0,6 кг/м3.
Пенобетоны получают смешиванием цементного теста или
раствора с устойчивой пеной. Пену получают взбиванием жидкой смеси канифольного мыла и животного клея или водного раствора сапонина (вытяжки из растительного мыльного корня). Такая пена имеет устойчивую структуру, хорошо смешивается с цементным тестом и раствором, которые распределяются по пленкам, окружающим воздушные ячейки, и в этом положении затвердевают. Лучшими пенообразователями являются алюмосульфонафтеновые и препарат ГК (гидролизованная боенская кровь).
Пену, цементное тесто или раствор, а также их смесь приготовляют в специальных пенобетоносместителях, состоящих из трех барабанов, внутри которых вращаются валы с лопастями. Готовое тесто из верхнего барабана переливается в нижний, туда же из второго верхнего барабана поступает готовая пена, после чего тесто и пену тщательно перемешивают в течение 2...
3 мин. Приготовленная смесь поступает в бункера, из которых разливается в формы для изделий. До тепловлажностной обработки смесь выдерживают в формах. За это время пеномасса приобретает начальную прочность, не разрушаясь при встряхивании. Сократить время выдержки можно путем использования быстросхватывающихся цементов или путем введения добавок — ускорителей твердения.
По физико-механическим свойствам различают пенобетон теплоизоляционный, конструктивно-теплоизоляционный и конструктивный. Теплоизоляционный пенобетон отливается в виде блоков размером 100×50×50 см и больше, которые после затвердевания распиливают на плиты. Теплоизоляционный пенобетон имеет прочность до 2,5 МПа, теплопроводность — 0,1...
0,2 Вт/(м·0С). Этот вид пенобетона применяют для теплоизоляции железобетонных покрытий, перегородок и т. д. Конструктивнотеплоизоляционный пенобетон имеет прочность 2,5...7,5 МПа,
— 235 —

теплопроводность 0,2...0,4 Вт/(м·°С), применяют его для ограждающих конструкций. Из конструктивного пенобетона изготовляют изделия для покрытий. Их армируют двумя сетками из проволоки диаметром 3...5 мм. Конструктивный пенобетон имеет прочность до 20 МПа и теплопроводность 0,4...0,6 Вт (м·°С). Конструктивный пенобетон широко используют в трехслойных ограждающих конструкциях отапливаемых зданий.
Газобетон получают из смеси портландцемента, кремнеземистого компонента и газообразователя. Широкое применение в качестве газообразователя получила алюминиевая пудра, которая, реагируя с водным раствором гидроксида кальция, выделяет водород
вызывающий вспучивание цементного теста. Последнее, затвердевая, сохраняет пористую структуру.
В портландцементных бетонах гидроксид кальция образуется в результате гидролиза трехкальциевого силиката, для ускорения этого процесса в смесь добавляют известь до 10% от массы цемента.
Алюминиевую пудру для лучшего распределения в смеси применяют в виде водной суспензии. Так как алюминиевый порошок при изготовлении на заводе парафинируют и частицы алюминия не смачиваются водой, то для удаления пленки парафина алюминиевую пудру предварительно прокаливают в электропечах при температуре 200°С, чтобы исключить возможность воспламенения порошка или взрыва. Кроме того, для придания пудре гидрофильных свойств ее обрабатывают водным раствором СДБ, канифольного мыла и др.
Для изготовления изделий из газобетона смесь молотого песка и воды смешивают в смесителе с цементом, алюминиевым порошком, водой и немолотым песком. Затем смесь разливают
вформы.
Внастоящее время на заводах страны для приготовления ячеистого бетона различных видов применяют современные виброгазобетоносместители СМС-40 и гидродинамический смеситель ГДС-3. Эти машины обеспечивают хорошее перемешивание, они позволяют получать высокогомогенные и активированные смеси с пониженным содержанием воды затворения (до 35...40%), при этом продолжительность процесса приготовления смеси не превышает 3 мин.
Гидродинамический смеситель ГДС-3 (рис. 6. 16) состоит из горизонтальной смесительной камеры с лопастным валом, активаторами, загрузочными устройствами, самоходного портала, щита снабжения электроэнергией и системы управления.
Виброгазосмеситель СМС-40 (рис. 6.17) состоит из корпуса, вертикального вала с лопастями, вибрационной системы и самоходного портала. На внутренней поверхности корпуса смонтиро-
— 2 3 6 —

Рис. 6.16. Гидродинамический смеситель ГДС-3: 1 —
пульт управления; 2 — привод смесителя; 3 — загрузочное устройство; 4 — горизонтальная смесительная камера; 5 — лоток; 6 — самоходный портал
ваны отбойные лопасти. По всей длине вала по винтовой линии установлены попарно лопасти, образующие двухлопастной пропеллер. Привод вертикального вала осуществляется снизу через клиноременную передачу и конический редуктор. В конструкции вибрационного устройства предусмотрено регулирование частоты вибрации и амплитуды колебаний. Исходные материалы загружаются через люки, имеющиеся в крышке. Готовая смесь выгружается через затвор, под которым расположен лоток, предназначенный для заливки газобетонной смеси в форму.
Формование ячеисто-бетонных масс производят на виброплощадках со специальной бортоснасткой. После непродолжительной выдержки газобетон разрезают машиной СМ-1211 на мелкие блоки и направляют в автоклавы. Режим автоклавной обработки изделий поддерживается по заданной программе автоматической системой регулирования. Твердение изделий в автоклаве при температуре 175°С и давлении 0,8 МПа обеспечивает высокую прочность и позволяет существенно уменьшить расход цемента путем частичной или полной замены его известью. Из автоклавов изделия поступают в пакетах на склад готовой продукции.
По свойствам газобетон аналогичен пенобетону. Однако он проще в изготовлении и позволяет получать изделия более устойчивого качества.
Рис. 6.17. Виброгазобетоно- смесительСМС-40: 1 —
корпус; 2 — самоходный портал; 3 — привод вертикального вала; 4 — вертикальный вал; 5 — лоток
— 2 3 7 —
Способ производства ячеистых бетонов методом комплексной вибрации позволяет не только управлять процессом структурообразования, но и дает ряд технико-экономических преимуществ: интенсифицирует технологический процесс, улучшает свойства ячеистых бетонов, снижает влажность готовых изделий. Вследствие этого, а также возможности использования местного сырья (извести, песка, шлака и золы) изготовление автоклавного газобетона, газосиликата и газошлакобетона стало основным направлением развития производства ячеистых бетонов.
Блоки из ячеистых бетонов автоклавного твердения применяют для кладки наружных и внутренних стен и перегородок жилых, общественных, промышленных и сельскохозяйственных зданий с относительной влажностью воздуха помещений не более 75%, а в наружных стенах при влажности более 60% должно наноситься с внутренней поверхности стен пароизоляционное покрытие. Применение блоков из ячеистых бетонов для цоколей и стен подвалов, а также стен помещений с мокрым режимом или наличием агрессивных сред не допускается.
§ 6.14. Экономика производства и
применения легких бетонов
Снижение массы крупноразмерных бетонных изделий — одно из основных направлений технического прогресса в сборном строительстве.
Исследованиями, проведенными в НИИЭС Госстроя СССР, установлено, что технически возможный удельный вес легких бетонов в основных конструкциях полносборного строительства может составить примерно 60%. Суммарный объем выпуска легких бетонов к 1985 г. составил 26 млн. м3, а в ближайшей перспективе увеличится до 40...45 млн. м.3, что предопределяет значительный рост объема производства пористых заполнителей.
Из табл. 6.5 видно, что применение облегченных стеновых конструкций позволяет снизить массу 1 м2 стены с 1080... 1250 до 175...560 кг, т. е. примерно в 2...7 раз (в зависимости от вида кирпичных и легкобетонных стен). Толщина ограждающих конструкций для принятых климатических условий сокращается с 52...66 до 25...40 см. Трудоемкость изготовления и монтажа конструкций уменьшается соответственно с 1,3... 1,65 чел-дн на 1 м2 стены до 0,75...0,8 чел-дн, т. е. на 30...55%. Стоимость смонтированных конструкций уменьшается (по перспективным данным) с 18,6 руб/м2 стены из полнотелого керамического кирпича до 9,7... 11,5 руб/м2, причем наиболее значительное снижение этих затрат имеют конструкции стен из ячеистых и легких бетонов на пористых заполнителях пониженной плотности
(300...350 кг/м3).
Объем капитальных вложений на развитие материальнотехнической базы строительства по конструкциям из пористых заполнителей примерно одинаков с кирпичными стенами, а по
— 238 —

Таблица 6.5. Перспективные технико-экономические показатели стеновых
конструкций для жилых зданий на 1 м2 стены при расчетной температуре
— З1°С (данные НИИЭС Госстроя СССР)*
* Показатели определены как расчетные перспективные с учетом прогрессивных проектов отрасли и фактических данных по передовым предприятиям. В целях сопоставимости в расчете приняты равные мощности предприятий по производству стеновых конструкций, одинаковые транспортные схемы по перевозке изделий, одинаковый уровень заводской готовности стеновых конструкций. Потребность в капитальных вложениях определена по нормативам удельных капитальных вложений.
ячеистым бетонам — на 15...20% меньше. При этом важным фактором, определяющим технико-экономическую эффективность применения газосиликатных панелей, является значительное уменьшение капитальных вложений на создание сырьевой базы для заводов силикатного домостроения.
— 239 —
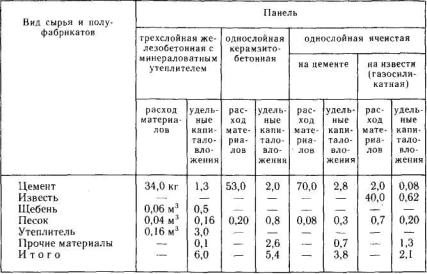
В табл. 6.6 дается расчет на перспективу удельных капитальных вложений в сырьевую базу для производства панелей наружных стен из различных материалов. Из этих данных видно, что снижение капитальных вложений на развитие смежных отраслей для газосиликатных панелей обусловлено сокращением норм расхода вяжущих и уменьшением удельных капитальных вложений на производство извести (по сравнению с цементом) и песка (по сравнению со щебнем). В целом капитальные вложения на создание сырьевой базы крупнопанельного домостроения из ячеистых бетонов в 1,5...2,5 раза меньше, чем по другим видам крупнопанельного домостроения.
Таблица 6.6. Расчет удельных капитальных затрат на создание сырьевой базы для производства 1 м2 панелей наружных стен
Перспективным является снижение массы крупноразмерных изделий путем применения легких бетонов на искусственных пористых заполнителях. Применение пористых заполнителей в производстве сборных элементов жилых домов дает значительный экономический эффект. Это подтверждено расчетами и опытом производства.
По данным НИИЭС, приведенные затраты на 1 м2 конструкций стен жилых зданий из легких бетонов на 1,4 руб ниже, чем трехслойных из тяжелого бетона; экономия в расчете на 1 м3 легкого бетона составляет 4,6 руб. При изготовлении наружных стен промышленных зданий экономия приведенных затрат в расчете на 1 м3 легкого бетона составляет 3 руб.
Эффективно также применение легких бетонов при изготовлении несущих внутренних стен промышленных зданий. Экономия
240