
Vladimirov_S.V._Mehanizats._pogruz.-razgruz.,_transport._i_sklad._rabot2010
.pdfМинистерство образования и науки Украины Донецкий национальный университет экономики и торговли
имени Михаила Туган – Баранвского
кафедра оборудования пищевых производств
С.В. Владимиров
Механизация погрузочно – разгрузочных, транспортных и складских работ
Курс лекций
Донецк, 2010
Тема 1. Ленточные конвейеры
1.Вступление. Классификация ленточных конвейеров
2.Принцип расчета и проектирование конвейеров
3.Основные параметры транспортирующих машин
4.Общие сведения. Конструкция ленточных конвейеров.
5.Методика и последовательность тягового расчета ленточного кон-
вейера
1. Вступление.
МехПРТС работ – это механизация погрузочно – разгрузочных, транспортных и складках работ.
На предприятиях пищевой промышленности особенно трудоемкими являются погрузочные, разгрузочные, транспортные и складские процессы, около 70% которых выполняются вручную. Численность трудящихся, занятых на этих процессах, составляет свыше 20% общей численности рабочих предприятий. Кроме этого на выполнение погрузочно-разгрузочных работ отвлекаются рабочие основных профессий.
Объем погрузочно-разгрузочных работ на предприятиях различных пищевой промышленности составляет тысячи тонн различных грузов.
Механизация этих работ способствует:
общему повышению производительности труда,
высвобождает большое число рабочих для выполнения основных
работ,
сокращает время простоя транспорта под погрузочноразгрузочными операциями и этим самым ускоряет его оборот,
облегчает условия труда,
снижает себестоимость транспортных работ на предприятиях.
В настоящее время на предприятиях пищевой промышленности выполняются самые разнообразные по виду, характеру и объему перемещения различных грузов. Этим объясняется и большое разнообразие современных средств механизации - от простого домкрата-подъемника до роботаманипулятора.
Из всего многообразия по характеру выполнения рабочего движения можно выделить два класса машин:
периодического (циклического),
непрерывного действия.
комбинированные установки, состоящие из машин периодического
инепрерывного действия.
Классификация конвейеров
Конвейер (транспортер) – это машина непрерывного действия, предназначенная для перемещения сыпучих, кусковых или штучных грузов.
Основным признаком конвейера – это тип тягового и грузонесущего органа.
Конвейеры бывают ленточным, цепным, канатным и другими тяговыми органами, а также существуют конвейеры без тягового органа (винтовые, инерционные, вибрационные, роликовые).
По типу грузонесущего органа конвейеры подразделяются на: ленточные, пластинчатые, скребковые, подвесные (толкающие, грузонесущие, тележечные), ковшовые и люлечные, а также винтовые, инерционные, вибрационные и роликовые.
По принципу действия различают конвейеры, перемещающие груз на непрерывно движущейся ленте и настиле, в непрерывно движущихся ковшах, подвесках, платформах, тележках; по неподвижному желобу или трубе непрерывно движущимися скребками.
По назначению конвейеры бывают: стационарные и передвижные для насыпных, штучных грузов и для паcсажиров, а по направлению перемещения грузов: с вертикально замкнутой, горизонтально замкнутой и пространственной трассами. По областям применения конвейеры подразделяют на машины общего назначения и специальные (элеваторы, эскалаторы, движущиеся тротуары и др.)
Конвейеры являются составной, неотъемлемой, иногда очень важной частью современного технологического процесса, они устанавливают и регулируют темп производства, обеспечивают его ритмичность, способствуют повышению производительности труда и увеличению выпуска продукции. Наряду с этим конвейеры являются основными средствами комплексной механизации и автоматизации погрузочно-разгрузочных и складских работ.
На предприятиях конвейеры используются в качестве:
–высокопроизводительных транспортных машин, передающих грузы из одного места в другое на участках внутризаводского и внешнего транспорта;
–транспортных агрегатов мощных перегрузочных устройств(мостовых перегружателей, отвалообразователей и т.п.) и погрузочно-разгрузочных машин;
–машин для перемещения грузов-изделий по технологическому процессу поточного производства от одного рабочего места к другому, от одной технологической операции к другой, регулируя темп производства и со-
вмещая, иногда, функции накопителей (подвижных складов) и распределителей грузов-изделий по отдельным технологическим линиям;
–машин и передаточных устройств в технологических автоматических линиях изготовления и обработки деталей и узлов изделий.
Связь транспортирующих машин с общим технологическим процессом производства обуславливает соответствующую ответственность их работы и назначения. Поэтому конвейеры должны быть надежными, прочными, удобными в эксплуатации и способными работать в автоматических режимах.
Развитие всех отраслей промышленности обуславливают следующие основные направления развития конвейеров.
1.Создание машин для бесперегрузочного транспорта грузов от начального до конечного пунктов по прямолинейной и сложной пространственной трассе большой протяженности. Этому направлению подчинено создание многоприводных конвейеров различных типов (подвесных, пластинчатых, скребковых, ленточных), мощных ленточных конвейеров со сверхпрочными лентами, ленточно-канатных и ленточно-цепных конвейеров с прочным тяговым органом в виде канатов или цепей, изгибающихся скребковых и пластинчатых конвейеров, сложных разветвленных систем подвесных толкающих конвейеров, трубчатых скребковых конвейеров с пространственной цепью и др.
2.Повышение производительности конвейерных установок реализуется путем выбора наиболее рациональной формы грузонесущего органа конвейера для увеличения количества груза на единице его длины, а также путем повышения скорости грузонесущих органов.
3.Повышение надежности машин и упрощение их обслуживания в тяжелых условиях эксплуатации являются основными предпосылками для перехода к полной автоматизации управления машинами и комплексами машин.
4.Автоматизация управления машинами и комплексными конвейерами с использованием ЭВМ.
5.Снижение массы и уменьшение габаритных размеров конвейеров за счет принципиально новых, облегченных конструкций машин и их узлов, широкого применения пластмасс и легких сплавов, гнутых профилей вместо прокатных и т.п.
6.Улучшение условий работы обслуживающего персонала и производственных рабочих, исключение возможности потерь транспортируемого груза, изоляция от окружающей среды пылевидных, горячих, газирующих и химически агрессивных грузов.
7.Унификация и нормализация оборудования с одновременным увеличением количества его типоразмеров.
8.Повышение качества и культуры производства машин за счет широкого применения методов передовой технологии и технической этики.
2. Принцип расчета и проектирование конвейеров.
Расчет конвейеров при проектировании проводится в два этапа: предварительный расчет основных параметров конвейерной установки в соответствии с техническим заданием на проектирование и поверочный расчет, определяющий прочность узлов и деталей и соответствие техническому заданию (уточняются значения параметров конвейера, определенные в предварительном расчете).
Исходные данные для расчета.
Данные для расчета должны содержать характеристику транспортируемого груза, максимальную производительность машины, сведения об условиях работы и схемы трассы транспортирования со всеми необходимыми размерами. В характеристике насыпного груза указывается его наименование, насыпная плотность, род груза (рядовой, сортированный), максимальный размер типичных кусков a и наибольших кусков amax , влажность, коэффициент внутреннего fв и внешнего
fтрения.
Вхарактеристике штучных грузов указывается их наименование, масса одной штуки, форма и размеры груза. При необходимости приводятся сведения об особых свойствах грузов (взрывоопасность, абразивность, липкость и т.п.)
Вусловия работы включаются сведения: число часов работы в сутки и дней работы в год; место установки (отапливаемое или неотапливаемое помещение, на открытом воздухе и т.п.); пределы колебаний температуры окружающей среды; наличие повышенной влажности, запыленность воздуха и т.п.
Условия работы конвейера.
РЕЖИМЫ |
ХАРАКТЕРИСТИКА |
|
|
|
|
ЛЕГКИЕ (Л) |
Чистое, сухое, отапливаемое, хорошо освещенное по- |
|
мещение; отсутствует абразивная пыль; конвейер |
||
|
доступен для обслуживания, осмотра и ремонта |
|
|
Отапливаемое помещение; небольшое количество аб- |
|
СРЕДНИЕ (С) |
разивной пыли; временами влажный воздух; средние |
|
|
освещенность и доступность для обслуживания |
|
|
Работа в неотапливаемом помещении и на открытом |
|
ТЯЖЕЛЫЕ (Т) |
воздухе; возможны большое количество абразивной |
|
пыли или повышенная влажность воздуха; плохие ос- |
||
|
||
|
вещенность и доступность для обслуживания |
|
ВЕСЬМА ТЯЖЕЛЫЕ |
Очень пыльная атмосфера и наличие факторов, вредно |
|
(ВТ) |
влияющих на работу конвейера |
Параметры, определяющие условия работы конвейера.
ПАРАМЕТР |
|
РЕЖИМ УСЛОВИЙ РАБОТЫ |
|
|
ЛЕГКИЕ |
СРЕДНИЕ |
ТЯЖЕЛЫЕ |
ВЕСЬМА ТЯ- |
|
|
ЖЕЛЫЕ |
|||
|
|
|
|
|
Время работы в сутки, ч |
До 6 |
6-12 |
12-18 |
Св.18 |
Свойства груза: |
|
|
|
|
насыпная плотность т/м3 |
До 0,6 |
0,6-1,1 |
1,1-2,0 |
Св.2,0 |
размер куска, мм |
До 20 |
20-60 |
60-160 |
Св.160 |
абразивность и коррозионность |
Нет |
Слабые |
Средние |
Сильные |
Влажность воздуха, % |
До 50 |
50-65 |
65-90 |
Св. 90 |
Запыленность воздуха, мг/м3 |
До 10 |
10-100 |
100-150 |
Св. 150 |
Температура окружающей среды, С |
+5 |
0 |
-20 |
-40 |
от |
||||
до |
+25 |
+30 |
+30 |
+40 |
Все транспортирующие машины, как и любые другие, должны обладать следующими факторами:
а) простота конструкции; б) надежность; в) долговечность;
г) экономичность; д) блочность; е) безопасность;
ж) удобство обслуживания и комфортность.
Основными параметрами транспортирующих установок являются: производительность; скорость транспортирования; ширина несущего органа; мощность привода.
Количество груза, выдаваемого транспортными устройствами в единицу времени, называют их производительностью.
Для машин, выдающих груз непрерывным потоком (рис.1 ,а,б), производительность равна количеству груза, проходящее через данное сечение в единицу времени,
Q = 3600 F , т/ч
или
V = 3600 F , м3/ч,
где
F– площадь сечения потока насыпного груза, м2.
- плотность транспортируемого груза
- скорость движения груза, м/с;
Производительность транспортирующей машины можно выразить также через погонную нагрузку q на рабочем органе.

Q 36001000qV 3,6qV,
Если известна часовая производительность и скорость движения груза, то отсюда можно определить погонную нагрузку
q 3,6QV , кг/м.
Рис.1. Схемы к определению производительности транспортирующих устройств непрерывного действия
При перемещении насыпных грузов в ковшах рис.1, а, б количеством груза в сосуде i(л) и расстоянием (шагом) между ними а (м)
q ai g io a g, кг/м,
где io - емкость сосуда, Л;
- коэффициент заполнения.
Если перемещают штучные грузы весом G (кг) каждый (рис.1,в) или партиями по Z (шт), тогда
q Gga , кг/м
или
q GZga , кг/м
Подставляя значение q, получим:
Для элеваторов производительность равна
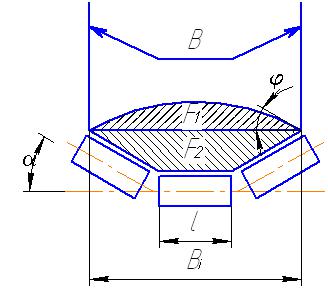
Q |
3,6io |
, т/час |
|||
a |
|
|
|||
|
|
|
|
|
|
Производительность при транспортировке штучных грузов |
|||||
Q |
3,6G |
, |
т / час |
|
|
a |
|
||||
Q 3,6GZ |
|
|
|
||
, т / час |
|||||
|
a |
|
|
|
|
|
|
|
|
|
|
С учетом угла установки |
конвейера, |
производительность (мак- |
симальная) вычисляется по формуле
Q 3600 F K y , т/ч,
где K y - коэффициент, учитывающий угол установки конвейера ( K y =1,0 при =0 10°; K y =0,97- =10 12°; K y =0,95- =12 18°; K y =0,9-
=18 25°).
Сечение груза на ленте можно определить по схеме (рис.4).
Рис.2. Схема к определению сечения груза
Общее сечение груза F=F1+F2,
где
F1 16 Bi2tg

F1 14 (Bi2 l)tg
Bi 0,9Вcos l(1- cos )
скорость грузонесущецо органа при транспортировании сыпучих грузов назначают в зависимости от свойств груза. Для легких (в основном) пылевидных материалов скорость ограничивается возможностью сдувания материала с полотна Для крупнокусковых, тяжелых
материалов скорость движения ограничена возможностью повреждения ленты вследствие ударов материала по ленте при набегании на ролики.
Например, скорость грузонесущего органа принимается для некоторых материалов: штучный (ящики, мешки и т.п.) - 0,4..1,5 м/с; мучнистый - 0,8…1,25 м/с; мелкий (легко сдуваемый - древесная стружка, зола и т.п.) - 0,6…1,5 м/с; уголь - до 5,0 м/с; тяжелое зерно (пшеница, рожь, кукуруза) - 2,0…4,0 м/с и т.п.
При применении лент с большим количеством прокладок или резинотросовых, скорость транспортирования для непылящих грузов ограничивается только конструктивными соображениями.
3. Основные параметры транспортирующих машин
Тяговые элементы. В качестве тяговых элементов конвейеров служат ленты, цепи и канаты.
Ленты подразделяют на резинотканевые, резинотросовые, стальные и сетчатые. Резинотканевая лента (рис. 1.6, а) состоит из нескольких пропитанных резиной тканевых прокладок. Сверху и снизу лента покрыта обкладками из резины: рабочей поверхности, обращенной к транспортируемому грузу, и нерабочей поверхности, обращенной к роликоопорам грузовой ветви.
Рисунок 1.6. Конвейерные ленты
Тканевые прокладки изготавливают из комбинированных или синтетических волокон, состоящих из полиамидных или полиэфирных нитей. (ГОСТ 2085) (табл. 3 прилож.).
Резинотросовые ленты (рис. 1.6 б) состоят из стальных тросов, покрыты с обеих сторон резиной, в которых завулканизированы тканевые прокладки, обеспечивающие каркасность ленты, т.е. необходимую изгибную жесткость ленты, стойкость к ударным нагрузкам, прочность ленты в поперечном направлении табл. 4 прилож..
Стальная холоднокатаная лента имеет толщину 0,8-1,2 мм. и ширину до 1200 мм; более широкие ленты собирают из отдельных стальных полос, соединяемых продольными заклепочными швами или при помощи специальной сварки в среде защитного газа. На рис. 1.7 показаны различные типы стальных лент, выпускаемых фирмами Швеции.
На рис. 1.8 показана сетчатая (проволочная) лента, применяемая в обжиговых и сушильных печах до t = 1000 C, а также в качестве подвижного пода для выпечки хлебных и кондитерских изделий, а также в моечных обезвоживающих, охладительных, сортировочных и других подобных установках.
В конвейерах с тяговым органом используют цепи пластинчатые, круглозвенные, разборные, вильчатые и др. При легких режимах работы применяют простые пластинчатые шарнирные (безвтулочные) цепи: штыревые, роликовые
икатковые (рис. 1-П прилож). Их звенья образуются из пластин, свободно надеваемых на концы валиков. В шарнирах из-за небольшой их площади возникают высокие удельные нагрузки и быстрый износ при повышенных скоростях
ибольших тяговых усилиях.
При средних и тяжелых режимах работы используют втулочные, втулоч- но-роликовые и втулочно-катковые цепи (рис. 2 и 3 прилож.).
Основные виды, параметры и размеры цепей приведены в таблицах приложения (табл. 5 и 6 прилож.).