
Антонов - Прикладная механика - 2004
.pdf
141
σ = Ml r sinωt = WM sinωt.
Влияние формы кривой изменения напряжений на сопротивление усталости невелико, а решающую роль играют значения максимального и минимального напряжений цикла и их отношение. Поэтому в дальнейшем будем рассматривать циклы, в которых изменение напряжений происходит по синусоиде.
11.2. Основные характеристики цикла
Рассмотрим график зависимости напряжения от времени (рис. 11.2). Согласно этому графику установим следующие характеристики цикла:
Рис. 11.2
1.σmax - алгебраически наибольшая величина цикла;
2.σmin - алгебраически наименьшая величина цикла;
σm = |
σmax +σmin |
(±) |
|
|
2 |
- среднее напряжение цикла (иногда его называют |
|||
3. |
|
постоянной величиной цикла);
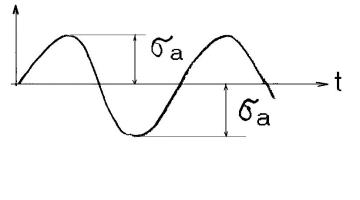
|
|
|
142 |
|
σ |
a |
= σmax −σmin |
|
|
4. |
2 |
(всегда со знаком плюс) - амплитуда напряжений цик- |
||
|
ла, численно равна максимальному отклонению от среднего напряжения (иногда ее называют - переменная величина цикла) ;
5. R = σmin /σmax - коэффициент асимметрии цикла.
Приведем примеры некоторых основных циклов:
Симметричный цикл (рис.11.3)
Рис.11. 3
Для этого цикла имеем
σmax = _− σmin; σm = 0; σa = σmax; R = σmin/σmax = -1
Пульсационный цикл (рис. 11.4).

143
Рис. 11.4
Для этого цикла имеем
σmax ; σmin = 0;
σm =σa = σ2max ;
R = 0
Наиболее опасным является симметричный цикл, у него переменная часть наибольшая. Например, из жизненного опыта известно, что проволока сломается значительно быстрее (при меньшем числе циклов нагружeния), если ее перегибать в обе стороны от прямолинейного положения (симметричный цикл), а не в одну сторону (пульсационный цикл).
Механизм усталостного разрушения заключается в следую-
щем. На возникновение и развитие усталостных трещин влияют дефекты (микродефекты) внутреннего строения материала (поры, внутренние трещины, шлаковые включения и др.) и дефекты обработки поверхности детали. Повторное деформирование вызывает пластические деформации отдельных кристаллитов, в результате че-
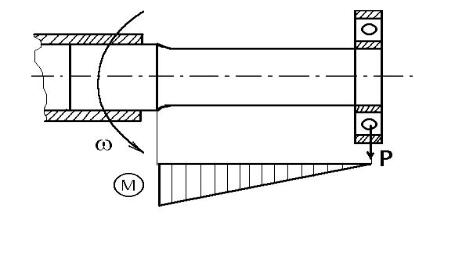
144
го скопления переместившихся на границы зерен дислокаций (местные искажения кристаллической структуры или микродефекты) инициируют образование новых микротрещин. Имеющиеся и вновь образовавшиеся микротрещины увеличиваются при повторных нагружениях, сливаются, порождая макротрещины. Этому способствует возрастание прочности по границам трещин из-за наклепа, т. е. повышается хрупкость материала. Скорость роста трещин невелика. Их рост продолжается до тех пор, пока площадь сечения не окажется столь малой, что действующие в нем напряжения превысят разрушающие. Тогда происходит быстрое разрушение элемента конструкции.
11.3. Испытания на усталость
Механические характеристики материала при действии циклических нагрузок определяют путем испытания на усталость. Один из способов нагружения переменной нагрузкой представлен на рис.11.5.
Рис. 11. 5

145
После приложения силы вращающийся образец доводят до разрушения при некотoром максимальном напряжении σmax = σ1 и фиксируют число циклов до разрушения N1 . Затем испытания про-
водят при других напряжениях σ1, σ2, σ3 и т. д. По результатам испытаний строят кривую усталости (кривую Вёлeра), представленную на рис. 11. 6.
Рис. 11. 6
Следует заметить, что результаты испытаний на усталость отличаются значительным разбросом, поэтому обычно при каждом из выбранных напряжений подвергаются нагружению не менее трех образцов. С уменьшением напряжения число циклов N растет довольно быстро, поэтому удобно откладывать N в логарифмической шкале. Для большинства сталей при нормальной температуре установлено, что если образец не разрушится до N=107 циклов, то разрушения не произойдет и при более длительном испытании (на кривой усталости имеется асимптота рис. 11,6.). Предварительно задаваемая
146
наибольшая продолжительность испытания на усталость называется базой испытаний. Для стальных образцов в обычных условиях база испытания равна 107 циклов.
Максимальное по абсолютному значению напряжение цикла, при котором еще не происходит усталостное разрушение до базы испытания, называется пределом выносливости σR . Для сим-
метричных циклов R=-l, поэтому в этом случае предел выносливости обозначается σ−1 , который для различных материалов приво-
дится в справочной литературе. Для черных металлов и сплавов предел выносливости приближенно равен σ1 ≈ (0.4 −0.5)σB . Для цветных металлов и сплавов диапазон изменения весьма широк:
σ1 ≈ (0.25 −0.5)σB .
Аналогичные испытания приводятся для определения характеристик усталостной прочности для касательных напряжений, возникающих при кручении.
11.4. Коэффициент запаса усталостной прочности
Приводимые обычно в справочной литературе значения пределов выносливости σ−1 , относятся к симметричному циклу напряже-
ния. Для оценки усталостной прочности в случае произвольного цикла строят диаграмму предельных амплитуд цикла в координатахσa −σm .. При σm = 0 предельным значением для σa будетσ−1 , (сим-
метричный цикл нагружения); а при σa = 0 имеет место статическое нагружение и предельным значением для σm будет σB - предел проч-
ности (рис.11. 7.)

147
Рис. 11.7
В этой системе координат любой цикл представится некоторой точкой. Точки, представляющие продельные циклы при различных соотношениях напряжений, как показывают опыты, укладываются на некоторой кривой, обращенной выпуклостью кверху (штриховая линия на рис. 11.7.). Для построения указанной линии требуется постановка значительного числа трудоемких опытов. Задачу можно упростить, приняв приближенное решение , а именно, заменив (расчеты пойдут в запас прочности) выпуклую линию на прямую А0В0, описываемую зависимостью
σa |
+ |
σm =1 |
σ1 |
|
σB , |
которая представляет собой график предельных циклов.
Если рабочая точка расположена ниже линии А0В0, то образец способен выдержать неограниченное число циклов нагруже-

148
ния. В технической литературе рассматривается значительное число способов оценки усталостной прочности и методов аппроксимации экспериментальных результатов, позволяющих получить более точные зависимости, но требующих и соответствующих затрат на опыты.
11.5. Факторы, влияющие на продел выносливости
На предел выносливости деталей влияют следующие факторы: состояние поверхности, абсолютные размеры детали, концентрация напряжений и агрессивность внешней среды.
Для предела выносливости детали можно записать выраже-
ние:
σ |
−1 |
=σ−1 |
KF Kd β |
=σ−1K |
|
||
|
|
||||||
|
|
|
|
Kσ |
, |
||
|
|
|
|
|
|
|
|
где введено обозначение |
|
|
|
|
|
|
|
K |
= |
K F K d β |
|
, |
|||
|
|||||||
|
|
|
|
K σ |
|
где К – коэффициент снижения предела выносливости (усталостной
прочности). Коэффициенты в правой части уравнения имеют
следующий смысл.
σ-1 - предел выносливости гладкого полированного образца;
К-F - коэффициент качества поверхности, К-F <1.
Грубая обработка поверхности детали снижает предел выносливости. В справочной литературе приводятся значения в зависимо-

149
сти от качества обработки поверхности (шероховатости). В справочной литературе даются также рекомендации по выбору нижеследующих коэффициентов.
Кd – коэффициент размеров (масштабный фактор) детали; Кd < 1.
Эксперименты показывают, что с увеличением размеров детали предел выносливости уменьшается. В первом приближении это можно объяснить тем, что растет абсолютное число микро- и макродефектов, ответственных за образование трещин.
β - коэффициент агрессивности внешней среды; β <1.
Агрессивная cpеда, проникая внутрь материала, увеличивает дефекты поверхности материала и тем самым снижает его прочность.
Kσ -эффективный коэффициент концентрации напряжений. Концентрацией напряжений называют местное повышение
напряжений в области резкого изменения формы или нарушения сплошности материала. На рис.11.8. показано местное изменение напряжения у отверстия при растяжении полосы, а на рис.11.9. у галтели вала при его изгибе.
Рис. 11.8

150
Рис. 11.9
Для обычной точности выполнения расчета на выносливость коэффициент усталостной прочности n =1,4 – 1,7. С учетом факторов, влияющих на выносливость детали и коэффициента усталостной прочности, в первом приближении, для уравнения коэффициента усталостной прочности можно записать
σa +σm = 1
σ−1 σT n
Эта формула представляет собой уравнение наклонной прямой АВ на рис. 11.7.
11.6. Меры повышения выносливости
Практические меры повышения сопротивления усталости в основном следующие: применять более однородные по структуре материалы; придавать деталям такие очертания, при которых была бы уменьшена концентрация напряжений; тщательно обрабатывать по-