
- •СОДЕРЖАНИЕ
- •ВВЕДЕНИЕ………………………………………………………………………………………3
- •1 ОБЩИЕ ПОЛОЖЕНИЯ………………………………………………………………………..4
- •2 АППАРАТУРА…………………………………………………………………………………..7
- •3. ПОДГОТОВКА К КОНТРОЛЮ……………………………………………………………….9
- •4 ПРОВЕДЕНИЕ КОНТРОЛЯ………………………………………………………………….38
- •6 ОФОРМЛЕНИЕ РЕЗУЛЬТАТОВ КОНТРОЛЯ…………………………………………... 45
- •Форма журнала контроля
- •ПРИЛОЖЕНИЕ 1
- •Пример использования SKH – шкалы
И Н С Т Р У К Ц И Я
по контролю качества сварных стыковых и тавровых соединений конструкций стальных мостов
СОДЕРЖАНИЕ
ВВЕДЕНИЕ………………………………………………………………………………………3
1 ОБЩИЕ ПОЛОЖЕНИЯ………………………………………………………………………..4
1.1Объекты контроля и требования, предъявляемые к ним……………………………..4
1.2Предприятия, на которые распространяется инструкция……………………………..4
1.3Дефекты подлежащие выявлению………………………………………………………..5
1.4Метод контроля……………………………………………………………………………….5
1.5Требования к уровню квалификации специалистов……………………………………5
1.6Требования по организации и проведению контроля………………………………….5
2 АППАРАТУРА…………………………………………………………………………………..7
2.1Тип применяемой аппаратуры и особенности её эксплуатации……………………..7
2.2Органы управления дефектоскопа………………………………………………………..7
2.3Преобразователи ультразвуковых колебаний…………………………………………..7
2.4Основные параметры контроля…………………………………………………………...8
2.5Стандартные и испытательные образцы и устройства для настройки дефектоскопа и проверки основных параметров контроля………………………………8
3. ПОДГОТОВКА К КОНТРОЛЮ……………………………………………………………….9
3.1Требования к окружающей среде………………………………………………………….9
3.2Требования к температуре объекта контроля…………………………………………..9
3.3Положение объекта контроля………………………………………………………………9
3.4Условия прозвучиваемости стыковых сварных соединений………………………...10
3.5Параметры контроля стыковых сварных соединений………………………………..11
3.6Параметры контроля тавровых сварных соединений………………………………..18
3.7Подготовка и настройка аппаратуры к работе.
Проверка основных параметров контроля……………………………………………..26
3.8Подготовка сварного соединения к контролю………………………………………….37
4 ПРОВЕДЕНИЕ КОНТРОЛЯ………………………………………………………………….38
5 ОЦЕНКА КАЧЕСТВА ШВОВ СВАРНЫХ СОЕДИНЕНИЙ…………………………….. 43
6 ОФОРМЛЕНИЕ РЕЗУЛЬТАТОВ КОНТРОЛЯ…………………………………………... 45
ПРИЛОЖЕНИЯ:
Приложение 1………………………………………………………………………………………46 Приложение 2………………………………………………………………………………………51 Приложение 3………………………………………………………………………………………52
2
3
1 ОБЩИЕ ПОЛОЖЕНИЯ
1.1 Объекты контроля и требования, предъявляемые к ним
1.1.1Инструкция распространяется на выполненные электродуговой сваркой: -стыковые соединения толщиной 10-50 мм;
-тавровые соединения с полным проваром корня шва и толщиной привариваемого элемента 10-40 мм.
1.1.2Требования дефектоскопичности:
-соотношение ширины валика усиления и толщины в стыковом (размер катетов в тавровом) соединении обеспечивает возможность прозвучивания сечения шва
акустической осью ультразвукового луча ( условия прозвучивания сечения стыковых швов акустической осью приведены в табл. 3.1);
-отношение высоты и ширины валиков усиления стыкового шва не более 0,2;
-имеется свободный доступ к околошовной зоне (зоне контроля) контролируе-
мого участка шва с обеих сторон одной плоскости (как исключение - с одной сторо-
ны) - для стыкового соединения; одной из плоскостей привариваемого элемента (листа) – для таврового соединения на ширину, достаточную для поперечного перемещения преобразователя в заданных пределах, согласно:
-табл.3.3- для стыковых швов; -табл. 3.8- для тавровых швов.
-с противоположной поверхности листов в зоне контроля отсутствуют прива-
ренные элементы, а также вмятины, поджоги и брызги металла, которые могут при-
вести к отражениям от них ультразвуковых колебаний; -отсутствуют или удалены механической обработкой подрезы, не удовлетво-
ряющие требованиям НТД (СниП) на объект контроля.
1.2 Предприятия на которые распространяется инструкция
Инструкция может быть применена для:
-строительных (монтажных) организаций, осуществляющих монтаж (сооруже-
ние) автодорожных и железнодорожных мостов;
-мостовых заводов.
4
1.3 Дефекты подлежащие выявлению
Допуски по технологическим дефектам швов сварных соединений строитель-
ных металлоконструкций соответствуют ОСТ 32 100-87:
- при контроле прямым и однократно отраженным лучом значения предельной
чувствительности оценки и поиска для дефектов, расположенных в середине контролируемой зоны, указаны в табл. 1.1.
Таблица 1.1 Значения предельной чувствительности при контроле
прямым и однократно отражённым лучом
Частота |
Толщина шва, |
Предельная чувствительность, мм² |
||
контроля, МГц |
мм |
|
|
|
оценки |
поиска |
|||
|
|
|
|
|
2,5 |
10-20 |
2 |
1 |
|
|
|
|
||
свыше 20 |
3 |
1,5 |
||
|
||||
|
|
|
|
П р и м е ч а н и е - Значения глубины расположения середины контролируе-
мой зоны приведены в приложении 1 ( табл. П. 1 - П.3).
1.4 Метод контроля
Инструкция распространяется на проведение ультразвукового контроля
эхо-методом.
1.5 Требования к уровню квалификации специалистов
1.5.1Оценка качества швов сварных соединений по результатам ультразвукового контроля выполняется специалистами 2 или 3 уровней квалификации.
1.5.2Ультразвуковой контроль выполняется специалистами:
-2 или 3 уровней квалификации; -1 уровня, прошедшими производственную стажировку со специалистом 2
уровня в течение минимум 1 месяца.
1.6 Требования по организации и проведению контроля
1.6.1Контроль сварных швов производится звеном из двух дефектоскопистов,
один из которых является старшим по звену. С целью исключения снижения достоверности результатов ультразвукового контроля вследствие утомляемости дефектоскописта рекомендуется в течение смены поочерёдная работа каждого дефектоскописта непосредственно с прибором по 70-75 мин.
1.6.2Качество шва 1 категории в металлоконструкциях «Северного исполне-
5
ния» и других особо ответственных соединениях должно оцениваться по результатам ультразвукового контроля, проводимого последовательно и независимо двумя
звеньями.
Дефект считается выявленным, если он выявлен хотя бы одним звеном.
1.6.3Швы, проверенные каждым звеном за смену, должны подвергаться выборочному инспекционному контролю в объёме не менее 5%. Инспекционный контроль выполняется руководителем подразделения или старшим дефектоскопистом.
Вслучае обнаружения при инспекционном контроле неправильной оценки качества шва, сварные соединения, проверенные за смену данным звеном, должны быть
подвергнуты повторному контролю этим звеном с выдачей заключения о качестве швов.
1.6.4Результаты контроля каждого участка сварного соединения заносят в
журнал непосредственно после контроля. В этом же журнале отражают сведения о
ремонте забракованных участков и результатах их повторного контроля.
1.6.5Ответственность за соблюдение НТД на контроль, организацию и качество неразрушающего контроля сварных соединений на предприятии (организации) возлагается на главного инженера.
1.6.6За качество выполнения контроля сварных соединений отвественность несёт дефектоскопист звена, назначенный старшим.
1.6.7За организацию контроля, состояние дефектоскопических приборов, на-
ходящихся в подразделении, ответственность несет руководитель этого подразде-
ления.
1.6.8За организацию места контроля, соответствующих условий для его проведения (освещение, температура, вентиляция и т.п.) с учетом требований правил техники безопасности, за качество подготовки к контролю сварных соединений от-
ветственность несет руководитель сварочного подразделения объекта, на котором производится контроль.
1.6.9Ответственность за правильность ведения журналов и карт контроля,
своевременное представление выписки о результатах контроля представителю ОТК и руководителю сварочного подразделения, хранение документации по контролю в период выполнения работ, а также за оформление и сдачу этих документов в ус-
тановленном порядке в архив несёт руководитель подразделения неразрушающего контроля.
6
1.6.10Ответственность за устранение недопустимых дефектов, обнаруженных при контроле, и представление отремонтированного участка на повторный контроль
несет руководитель сварочного подразделения.
1.6.11Дефектоскописты, выполняющие ультразвуковой контроль, должны
обеспечиваться спецодеждой.
1.6.12Требования представителей подразделения неразрушающего контроля по созданию дополнительных условий, необходимых для обеспечения тщательного
неразрушающего контроля, являются обязательными для исполнения администрацией подразделения, представляющего соединения на контроль.
2. АППАРАТУРА
2.1 Тип применяемой аппаратуры и особенности её эксплуатации
2.1.1Настоящая инструкция предусматривается проведение контроля вручную с исполнением ультразвукового дефектоскопа УД2-12.
2.1.2Особенности эксплуатации дефектоскопа УД2-12, введённые в Настоящую инструкцию:
- используется два (из имеющихся трёх) пороговых уровня блока АСД, соот-
ветствующих: чувствительности поиска – порог зажигания зелёной лампы АСД; чувствительности оценки – порог желтой лампы АСД;
- ВРЧ используется для подавления зондирующего импульса и шумов преобразователя с целью уменьшения «мёртвой зоны» (для выравнивания чувствитель-
ности – не используется).
2.2 Органы управления дефектоскопа
Обозначение, расположение и назначение органов управления приведены в
Руководстве по эксплуатации (РЗ) на дефектоскоп УД2-12.
2.3 Преобразователи ультразвуковых колебаний
Параметры применяемых преобразователей: -для контроля стыковых швов – см. п. 2.3.5.2;
-для контроля тавровых швов – см. п. 2.3.6.2.
7
2.4 Основные параметры контроля
2.4.1Частота ультразвуковых колебаний – 2,5 МГц.
2.4.2Параметры преобразователя:
-для контроля стыковых швов – см. п. 3.5.2;
-для контроля тавровых швов – см. п. 3.6.2.
2.4.3Коэффициенты выявляемости, соответствующие чувствительности оценки Ко и чувствительности поиска Кп, указаны:
-для стыковых швов – в табл. 3.6-3.7;
-для тавровых швов- в табл. 3.11- 3.14.
2.4.4Погрешность настройки глубиномера – см. табл. 18.
2.2.4.5 «Мертвая зона» для преобразователей с углами ввода в сталь: 50º ± 2º - не более 8 мм;
65º ± 2º - не более 3 мм.
2.5 Стандартные и испытательные образцы и устройства для настройки дефектоскопа и проверки основных параметров контроля ( табл. 2.1)
Таблица 2.2
Операции по настройке или |
Используемые образцы |
№ № пп. |
|
проверке параметров |
или устройства |
|
инструкции |
|
|
|
|
Определение (проверка) точки |
Стандартный образец |
СО-3 |
3.7.6, а |
выхода луча преобразователя |
ГОСТ 14782-86 |
|
|
|
|
||
|
|
|
|
Определение (проверка) угла |
Стандартный образец |
СО-2 |
3.7.8, а |
ввода луча в сталь |
ГОСТ 14782-86 |
|
|
|
|
||
|
|
|
|
|
Стандартный образец СО-2 |
|
|
Настройка чувствительности |
ГОСТ 14782-86 или |
|
3.7.12 - 3.7.15 |
|
испытательные образцы 1-го |
|
|
|
или 2-го вида ОСТ 32 100-87 |
|
|
Настройка глубиномера и его |
Стандартный образец |
СО-2 |
3.7.6 - 3.7.9 |
проверка |
ГОСТ 14782-86 |
|
|
|
|
||
|
|
|
|
|
Стандартный образец |
|
|
Проверка «мёртвой зоны» |
СО-2 ГОСТ 14782-86 или |
3.7.16 |
|
|
испытательный образец |
|
|
|
2-го вида ОСТ 32 100-87 |
|
|
Проверка аттенюатора |
Стандартный образец СО-2 |
3.7.14, а - 3.7.14, ж |
|
ГОСТ 14782-86, |
|
||
|
БЦО дефектоскопа |
|
|
8
3. ПОДГОТОВКА К КОНТРОЛЮ
3.1 Требования к окружающей среде
3.1.1Для обеспечения нормальных условий работы дефектоскописта, обу-
славливающих надёжность и достоверность результатов ультразвукового контроля, последний должен выполняться, как правило, при температуре не ниже +5ºС. При температуре окружающего воздуха ниже + 5ºС необходимо оборудовать тепляки.
П р и м е ч а н и е- Работы по оборудованию тепляков и их перестановке не входят в обязанности дефектоскопистов и должны выполняться специально выде-
ленными для этой цели работниками.
3.1.2На участке контроля соединения должна быть обеспечена защита от ярких источников света, шума, загрязненного пылью и газами воздуха, ветра и осадков.
3.2 Требования к температуре объекта контроля
Ультразвуковой контроль допускается проводить вслед за сваркой после остывания металла в зоне перемещения преобразователя до +40ºС и ниже.
3.3 Положение объекта контроля
На участке контроля должно быть обеспечено удобное для дефектоскописта
расположение соединения и свободный доступ к контролируемым участкам. Для этого (в необходимых случаях) должны быть оборудованы леса и подмости, обеспечивающие удобное взаимное расположение дефектоскописта, аппаратуры и контролируемого соединения.
9

3.4 Условия прозвучиваемости стыковых сварных соединений (табл. 3.1)
Таблица 3 |
|
|
|
|
|
|
|
|
|
|
|
|
|
|
|
Толщина, |
Условия |
|
Толщина, |
Условия прозвучиваемости, |
|||
мм |
прозвучиваемости, |
||||||
мм |
мм |
|
|||||
|
мм |
|
|
||||
|
|
|
|
|
|||
10 |
|
|
7 |
28 |
|
33 |
|
12 |
|
|
15 |
30 |
|
37 |
|
14 |
|
|
24 |
32 |
|
41 |
|
|
|
|
33 |
|
|
45 |
|
16 |
|
|
34 |
|
|||
18 |
b1+ b1< |
|
41 |
36 |
|
49 |
|
20 |
|
|
50 |
38 |
0.47b1+ 0.84b1< |
53 |
|
|
|
|
|
|
|
||
22 |
|
|
58 |
40 |
57 |
||
|
|
|
|||||
24 |
|
|
67 |
42 |
|
61 |
|
26 |
|
|
76 |
44 |
|
65 |
|
|
|
|
|
|
|
63 |
|
|
|
|
|
46 |
|
||
|
|
|
|
48 |
|
73 |
|
|
|
|
|
50 |
|
77 |
|
|
|
|
|
|
|
|
П р и м е ч а н и я
1)Значения b1 и b2 (ширина облицовочного и обратного валиков) измеряются мерительным инструментом в соответствии с рис. 3.1.
2)При невыполнении условия прозвучиваемости следует использовать пре-
образователи с большими углами ввода α ( по отношению к указанным в табл. 3.1),
например α =70º и меньшей стрелой n.
Рисунок 3.1
10

3.5 Параметры контроля стыковых сварных соединений
3.5.1 Схемы прозвучивания стыковых сварных соединений приведены в
табл.3.2 и рис. 3.2.
Таблица 3.2
Схемы прозвучивания швов
при одинаковой толщине свариваемых листов |
при разной |
||
|
|
|
|
в случае двухстороннего |
в случае одностороннего |
толщине свариваемых |
|
доступа к одной поверх- |
доступа |
листов |
|
ности |
|||
|
|
||
|
|
|
|
с двух сторон одной |
как исключение- с одной |
со стороны листа |
|
меньшей толщины |
|||
плоскости (рис.3.2,а) |
стороны (рис.3.2,б) |
||
(рис.3.2, в или 3.2, г) |
|||
|
|
||
|
|
|
Рисунок 3.2 –Схема прозвучивания стыковых сварных швов
11

3.5.2 Параметры сканирования стыковых сварных соединений:
-применяемый преобразователь:
тип – наклонный; схема включения – совмешенная;
частота – 2,5 МГц; угол ввода в сталь – см. табл. 3.3;
размеры пьезопластины – диаметр 12 мм или стороны 12х18 мм;
-перемещение преобразователя (рис. 3.3);
схема – поперечно-продольное сканирование;
лучи, используемые для прозвучивания:
-прямой (количество отражений от поверхности m = 0) - для контроля нижней части шва;
-однократно отражённый (m =1) –для контроля верхней части шва;
пределы поперечного перемещения – см. табл. 3.3;
шаг сканирования – см. табл.3.3.
Рисунок 3.3 Параметры сканирования стыковых сварных швов
12

Таблица 3.3 |
Параметры сканирования |
|
|
|
|
|
|
|||||
|
|
Параметры сканирования (поперечно-продольное сканирование) |
|
|||||||||
|
|
|
||||||||||
|
Контроль прямым лучом |
Контроль однократно отражённым лучом |
||||||||||
Толщина, |
|
|
(m=0) |
|
|
|
(m=0) |
|
||||
Угол |
Пределы |
Шаг |
Угол |
Z |
Пределы переме- |
|
Шаг |
|||||
δ, |
ввода |
сканиро- |
ввода |
мм |
щения преобра- |
|
скани- |
|||||
мм |
перемещения |
|
||||||||||
|
луча |
преобразова- |
вания, |
луча |
(см.рис. |
|
зо- |
|
рования |
|||
|
α1 |
1 |
|
3.3) |
|
вателя, |
|
2 |
||||
|
теля, мм |
град |
|
|
||||||||
|
град |
мм |
|
|
мм |
|
мм |
|||||
|
|
|
|
|
|
|
||||||
|
|
n |
|
L1 |
|
|
|
L2 |
|
L3 |
|
|
10 |
|
|
|
22 |
|
|
|
25 |
|
43 |
|
5 |
12 |
|
|
|
26 |
|
|
|
29 |
|
52 |
|
6 |
14 |
|
|
|
30 |
|
|
|
33 |
|
60 |
|
7 |
16 |
|
|
|
35 |
|
|
3 |
38 |
|
69 |
|
7 |
18 |
|
|
|
39 |
|
65±2 |
42 |
|
78 |
|
8 |
|
20 |
|
|
|
43 |
|
|
|
46 |
|
86 |
|
9 |
22 |
|
|
|
48 |
|
|
|
50 |
|
95 |
|
10 |
24 |
|
|
|
52 |
|
|
|
55 |
|
103 |
|
11 |
26 |
|
|
|
56 |
|
|
|
59 |
|
112 |
|
12 |
28 |
|
12 |
|
60 |
1 |
|
|
38 |
|
67 |
|
6 |
30 |
65±2 |
|
65 |
|
|
41 |
|
72 |
|
6 |
||
32 |
|
|
|
69 |
|
|
|
43 |
|
77 |
|
7 |
34 |
|
|
|
73 |
|
|
|
46 |
|
82 |
|
7 |
36 |
|
|
|
78 |
|
|
|
48 |
|
87 |
|
7 |
38 |
|
|
|
82 |
|
50± 2 |
5 |
50 |
|
91 |
|
8 |
40 |
|
|
|
86 |
|
53 |
|
96 |
|
8 |
||
|
|
|
|
|
|
|
|
|||||
42 |
|
|
|
90 |
|
|
|
55 |
|
101 |
|
9 |
44 |
|
|
|
95 |
|
|
|
58 |
|
106 |
|
9 |
46 |
|
|
|
99 |
|
|
|
60 |
|
111 |
|
10 |
48 |
|
|
|
103 |
|
|
|
62 |
|
115 |
|
10 |
50 |
|
|
|
108 |
|
|
|
65 |
|
120 |
|
10 |
П р и м е ч а н и е -При контроле швов с разной толщиной свариваемых листов параметры сканирования следует выбирать для листа меньшей толщины.
3.5.3 Параметры селектирования (стробирования) при контроле стыковых сварных соединений приведены в табл. 3.4 и рис 3.4.
13
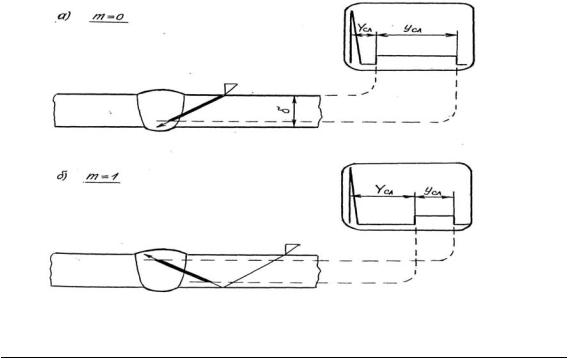
Рисунок 3.4 Параметры селектирования при контроле стыковых сварных швов
Таблица 3.4 |
Параметры селектирования |
|
|
|||
|
|
|
Параметры селектирования, мм |
|
||
|
|
|
|
|||
Толщина, |
|
Контроль прямым лучом |
Контроль однократно |
|||
|
(m=0) |
отраженным лучом ( m=1) |
||||
δ, мм |
|
|||||
|
задержка |
длительность |
задержка |
длительность |
||
|
|
|||||
|
|
строба У сл |
строба Усл |
строба |
Усл |
строба Усл |
10 |
|
|
8 |
|
12 |
6 |
12 |
|
|
10 |
|
14 |
8 |
14 |
|
|
12 |
|
16 |
9 |
16 |
|
|
14 |
|
18 |
12 |
18 |
|
|
16 |
|
20 |
14 |
20 |
|
|
18 |
|
22 |
16 |
22 |
|
|
20 |
|
24 |
18 |
24 |
|
|
22 |
|
26 |
20 |
26 |
|
|
24 |
|
28 |
22 |
28 |
|
(2tп)у |
26 |
(2tп)у + |
30 |
24 |
30 |
|
28 |
32 |
26 |
||
32 |
|
|
30 |
|
34 |
28 |
34 |
|
|
32 |
|
36 |
30 |
36 |
|
|
34 |
|
38 |
32 |
38 |
|
|
36 |
|
40 |
34 |
40 |
|
|
38 |
|
42 |
36 |
42 |
|
|
40 |
|
44 |
38 |
44 |
|
|
42 |
|
46 |
40 |
46 |
|
|
44 |
|
48 |
42 |
48 |
|
|
46 |
|
50 |
44 |
50 |
|
|
48 |
|
52 |
46 |
П р и м е ч а н и я 1) Параметр (2tп)у для конкретного преобразователя опре-
деляется согласно пп. 3.7.17, а – 3.7.17, г.
2) При контроле швов с равной толщиной свариваемых листов параметры селектирования следует выбирать для листа меньшей толщины.
14

3.5.4 Чувствительность при контроле стыковых сварных соединений определяется с учетом следующих факторов:
-ВРЧ- действует только в зоне зондирующего импульса; -отсечка – «слабая» или отключена;
-образцы для настройки чувствительности – см. табл. 3.5; -значения коэффициентов выявляемости, соответствующих чувствительности
поиска Кп и оценки Ко:
-для толщин 10-12 мм см. табл. 3.6; -для толщин свыше 20 мм – см. табл. 3.7;
-допустимое значение ослабления ( введённое на аттенюаторе ) N0. доп, соответствующее максимуму эхо-сигнала от эталонного отражателя при нахождении его
вершины на уровне 6 больших клеток по экрану ЭЛТ дефектоскопа (N0 ≈ 2,5 дБ ): для толщин 10-12 мм – см. табл. 3.6; для толщин свыше 20 мм – см. табл. 3.7.
Таблица 3.5 |
|
|
|
|
|
|
|
|
|
|
Толщина 10-20 мм |
Толщина свыше 20 мм |
||
|
|
|
Стандартный образец |
|
Образец для |
Испытательный |
Испытательный |
||
настройки чув- |
образец 1-го вида |
образец 2-го вида |
СО-2 |
|
ствительности |
ОСТ 32 100-87 |
ОСТ 32 100-87 |
ГОСТ 14782-86 |
|
|
(рис.3.5, а) |
(рис.3.5, б) |
|
|
|
|
|
|
|
|
Цилиндрический отражатель диаметром |
|
||
|
2 мм, выполненный на глубине: |
Цилиндрический |
||
|
h1 (m=0) |
h3 (m=0) |
||
|
отражатель |
|||
Эталонный |
h2 (m=1) |
h4 (m=1) |
||
диаметром 6 мм |
||||
отражатель |
(конкретные значения – см.табл.П.1 |
|||
на глубине |
||||
|
в приложении 1), |
|||
|
44 мм |
|||
|
соответствующей середине контроли- |
|||
|
|
|||
|
руемой зоны Но |
|
||
|
|
|
|
15

Таблица 3.6
|
|
|
|
Применяемые образцы для настройки чувствительности |
|
|||||||||||||||||
Тол- |
|
|
|
|
|
|
|
|
|
|
|
|
|
|
|
|
|
|
|
|
|
|
испытательный образец 1-го вида |
|
испытательный образец 2-го вида |
||||||||||||||||||||
щина |
|
|||||||||||||||||||||
δ, |
|
|
|
ОСТ 32 100-87 |
|
|
|
|
|
|
ОСТ 32 10087 |
|
||||||||||
|
m=0 |
|
|
|
|
m=1 |
|
|
|
m=0 |
|
|
|
|
|
m=1 |
|
|||||
мм |
|
|
|
|
|
|
|
|
|
|
|
|
|
|
||||||||
|
Ко |
Кп |
|
No.доп |
Ко |
Кп |
|
No.доп. |
|
Ко |
|
Кп |
|
Nо.доп. |
Ко |
Кп |
|
Nо.доп. |
||||
|
|
|
|
|
|
|
|
|
|
|
|
|
|
|
|
|
|
|
|
|
|
|
10 |
-4 |
-10 |
|
4…56 |
|
-6 |
-12 |
|
6…56 |
-10 |
|
-16 |
|
10..56 |
|
-12 |
-18 |
|
12..56 |
|||
12 |
-4 |
-10 |
|
4…56 |
|
-8 |
-14 |
|
8…56 |
-10 |
|
-16 |
|
10..56 |
|
-14 |
-20 |
|
14..56 |
|||
14 |
-6 |
-12 |
|
6…56 |
|
-8 |
-14 |
|
8…56 |
-12 |
|
-18 |
|
12..56 |
|
-14 |
-20 |
|
14..56 |
|||
|
|
|
|
|
|
|
|
|
|
|
|
|
|
|
|
|
|
|
|
|
|
|
16 |
-6 |
-12 |
|
6…56 |
|
-8 |
-14 |
|
8…56 |
-12 |
|
-18 |
|
12..56 |
|
-14 |
-20 |
|
14..56 |
|||
18 |
-6 |
-12 |
|
6…56 |
|
-8 |
-14 |
|
8…56 |
-12 |
|
-18 |
|
12..56 |
|
-14 |
-20 |
|
14..56 |
|||
20 |
-8 |
-14 |
|
8…56 |
|
-10 |
-16 |
|
10..56 |
-14 |
|
-20 |
|
14..56 |
|
-16 |
-22 |
|
16..56 |
|||
|
|
|
|
|
|
|
|
|
|
|
|
|
|
|
|
|
|
|
|
|
|
|
Таблица 3.7 |
|
|
|
|
|
|
|
|
|
|
|
|
|
|
|
|
|
|
|
|||
|
|
|
|
|
|
|
|
|||||||||||||||
Тол- |
|
|
Применяемый образец для настройки чувствительности: |
|
||||||||||||||||||
щина |
|
|
|
|
|
стандартный образец СО-2 ГОСТ 14782-86 |
|
|
|
|
|
|||||||||||
δ, |
|
|
|
|
|
m=0 |
|
|
|
|
|
|
|
|
m=1 |
|
|
|
||||
мм |
|
Ко |
|
Кп |
Nо.доп. |
|
|
Ко |
|
Кп |
|
|
Nо.доп. |
|||||||||
22 |
|
0 |
|
|
|
-6 |
|
0…56 |
|
|
-14 |
|
-20 |
|
|
|
14…56 |
|||||
24 |
|
-2 |
|
|
|
-8 |
|
2…56 |
|
|
-16 |
|
-22 |
|
|
|
16…56 |
|||||
26 |
|
-4 |
|
|
-10 |
|
4…56 |
|
|
-18 |
|
-24 |
|
|
|
18…56 |
||||||
|
|
|
|
|
|
|
|
|
|
|
|
-24 |
|
|
|
|
||||||
28 |
|
-4 |
|
|
-10 |
|
4…56 |
|
|
-18 |
|
|
|
|
18…56 |
|||||||
30 |
|
-6 |
|
|
-12 |
|
6…56 |
|
|
-20 |
|
-26 |
|
|
|
20…56 |
||||||
32 |
|
-6 |
|
|
-12 |
|
6…56 |
|
|
-20 |
|
-26 |
|
|
|
20…56 |
||||||
|
|
|
|
|
|
|
|
|
|
|
|
-28 |
|
|
|
|
||||||
34 |
|
-6 |
|
|
-12 |
|
6…56 |
|
|
-22 |
|
|
|
|
22…56 |
|||||||
36 |
|
-8 |
|
|
-14 |
|
8…56 |
|
|
-22 |
|
-28 |
|
|
|
22…56 |
||||||
38 |
|
-10 |
|
|
-16 |
10…56 |
|
|
-24 |
|
-30 |
|
|
|
24…56 |
|||||||
|
|
|
|
|
|
|
|
|
|
|
-30 |
|
|
|
|
|||||||
40 |
|
-10 |
|
|
-16 |
10…56 |
|
|
-24 |
|
|
|
|
24…56 |
||||||||
42 |
|
-10 |
|
|
-16 |
10…56 |
|
|
-26 |
|
-32 |
|
|
|
26…56 |
|||||||
44 |
|
-12 |
|
|
-18 |
12…56 |
|
|
-28 |
|
-34 |
|
|
|
28…56 |
|||||||
|
|
|
|
|
|
|
|
|
|
|
-34 |
|
|
|
|
|||||||
46 |
|
-12 |
|
|
-18 |
12…56 |
|
|
-28 |
|
|
|
|
28…56 |
||||||||
48 |
|
-14 |
|
|
-20 |
14…56 |
|
|
-30 |
|
-36 |
|
|
|
30…56 |
|||||||
50 |
|
-14 |
|
|
-20 |
14…56 |
|
|
-30 |
|
-36 |
|
|
|
30…56 |
|||||||
|
|
|
|
|
|
|
|
|
||||||||||||||
П р и м е ч а н и е - |
|
При контроле швов с разной толщиной свариваемых лис- |
тов значения чувствительности следует выбирать для листа меньшей толщины.
16

А) первого вида - изготавливается из образца контролируемого соединения
Б) второго видаизготавливается из материала контрольного соединения
Рисунок 3.5 Образца для настройки чувствительности при контроле стыковых сварных швов
17
3.6 Параметры контроля тавровых сварных соединений
3.6.1 Схема прозвучивания тавровых сварных соединений показана на рис.
3.6.
Контроль осуществляется с одной из поверхностей привариваемого элемента
вдва этапа:
1)контроль корня шва ( на отсутствие непровара);
2)контроль всего сечения.
3.6.2 Параметры сканирования тавровых сварных соединений: -применяемый преобразователь:
-тип- наклонный;
-схема включения – совмещённая;
-частота- 2,5 МГц;
-угол ввода в сталь – см. табл.10;
-размеры пьезопластины – диаметр 12 мм или стороны 12х18 мм;
-перемещение преобразователя ( рис.3.7)
-схема для прозвучивания:
1)корня шва – продольное сканирование;
2)всего сечения – поперечно-продольное сканирование; -лучи используемые для прозвучивания:
1) корня шва –однократно отражённый (количество отражений от
поверхности m=1);
2)всего сечения: - прямой ( количество отражений от поверхности m=0)- для контроля нижней части шва;
однократно отраженный (m=1) – для контроля верхней части шва; пределы перемещения преобразователя – см. табл. 3.8;
шаг сканирования – см. табл. 3.8.
18

Рисунок 3.6 Схема прозвучивания тавровых сварных швов
Рисунок 3.7 Параметры сканирования сварных швов тавровых соединений
а- контроль корня шва; б-в – контроль всего сечения.
19

Таблица 3.8 Параметры сканирования тавровых сварных соединений
Тол- |
|
|
|
|
Параметры сканирования |
|
|
|
|
|
|
|
|
|
|
||||||
щина |
|
|
|
|
|
|
|
|
|
|
|
|
|
|
|
|
|
|
|
|
|
контроль |
контроль всего сечения (поперечно-продольное сканирование) |
||||||||||||||||||||
при- |
|||||||||||||||||||||
корня шва |
|
|
|
|
|
|
|
|
|
|
|
|
|
|
|
|
|
|
|||
вари- |
|
|
|
|
|
|
|
|
|
|
|
|
|
|
|
|
|
|
|||
контроль прямым лучом |
|
контроль однократно |
|
||||||||||||||||||
вае- |
(продольное |
|
|
||||||||||||||||||
|
|
|
|
|
|
|
|
|
|
|
|
|
|
|
|
|
|
||||
мого |
сканирование) |
|
|
(m=0) |
|
|
отраженным лучом (m=1) |
|
|||||||||||||
эле- |
|
|
|
|
|
|
|
|
|
|
|
|
|
|
|
|
|
|
|
|
|
мента |
|
|
|
|
пределы |
|
шаг |
|
|
|
|
пределы |
|
|
|
шаг |
|||||
δ, |
угол |
|
угол |
|
|
ска- |
угол |
|
|
|
|
|
|
ска- |
|||||||
|
перемещения |
|
|
перемещения |
|
||||||||||||||||
|
ни- |
|
|
|
ни- |
||||||||||||||||
мм |
ввода |
Lср, |
ввода |
преобразователя, |
ввода |
|
преобразователя, |
|
|||||||||||||
|
луча |
луча |
|
|
мм |
|
рова- |
луча |
|
|
|
|
мм |
|
|
|
ро- |
||||
|
мм |
|
|
|
ния |
|
|
|
|
|
|
|
ва- |
||||||||
|
α1 |
α1 |
|
|
|
|
|
α2 |
|
|
|
|
|
|
|
|
|
||||
|
|
|
|
|
|
|
1, |
|
|
|
|
|
|
|
|
|
ния |
||||
|
град. |
|
град. |
n |
|
L1 |
|
град. |
|
|
L2 |
|
|
L3 |
|
||||||
|
|
|
|
|
|
|
|
|
2, |
||||||||||||
|
|
|
|
|
|
мм |
|
|
|
|
|
|
|||||||||
|
|
|
|
|
|
|
|
|
|
|
|
|
|
|
|
|
|
|
|
мм |
|
10 |
|
32 |
|
|
|
22 |
|
|
|
|
|
17 |
|
|
|
24 |
|
|
|
|
|
12 |
|
39 |
|
|
|
26 |
|
|
|
|
|
19 |
|
|
|
29 |
|
|
|
|
|
14 |
|
45 |
65±2 |
|
|
30 |
|
|
|
|
|
22 |
|
|
|
34 |
|
|
|
|
|
|
|
|
|
|
|
|
|
|
|
|
|
|
|
|
|
|
|
|
|
||
16 |
|
52 |
|
|
34 |
|
|
|
|
|
24 |
|
|
|
38 |
|
|
|
|
||
|
|
|
|
|
|
|
|
|
|
|
|
|
|
|
|
||||||
18 |
|
58 |
|
|
|
39 |
|
|
|
|
|
26 |
|
|
|
43 |
|
|
|
3 |
|
20 |
|
64 |
|
|
|
43 |
|
|
|
|
|
29 |
|
|
|
48 |
|
|
|
||
|
|
|
|
|
|
|
|
|
|
|
|
|
|
|
|
||||||
|
|
|
|
|
|
|
|
|
|
|
|
|
|
|
|
|
|
|
|
|
|
22 |
|
70 |
|
|
|
26 |
|
|
|
|
|
31 |
|
|
|
53 |
|
|
|
|
|
24 |
65±2 |
77 |
|
12 |
|
29 |
|
+К1 |
1 |
50±2 |
|
34 |
|
+К1 |
|
58 |
|
+К1 |
|
|
|
26 |
84 |
|
|
31 |
|
|
36 |
|
|
62 |
|
|
|
||||||||
|
|
|
|
|
|
|
|
|
|
|
|
|
|
|
|
|
|
|
|
|
|
28 |
|
90 |
|
|
|
33 |
|
|
|
|
|
38 |
|
|
|
67 |
|
|
|
|
|
30 |
|
97 |
50±2 |
|
|
36 |
|
|
|
|
|
41 |
|
|
|
72 |
|
|
|
|
|
32 |
|
103 |
|
|
38 |
|
|
|
|
|
43 |
|
|
|
77 |
|
|
|
|
||
|
|
|
|
|
|
|
|
|
|
|
|
|
|
|
|
||||||
|
|
|
|
|
|
|
|
|
|
|
|
|
|
|
|
|
|
|
|
|
|
34 |
|
110 |
|
|
|
41 |
|
|
|
|
|
46 |
|
|
|
82 |
|
|
|
5 |
|
36 |
|
116 |
|
|
|
43 |
|
|
|
|
|
48 |
|
|
|
86 |
|
|
|
|
|
38 |
|
122 |
|
|
|
45 |
|
|
|
|
|
50 |
|
|
|
91 |
|
|
|
|
|
|
|
|
|
|
|
|
|
|
|
|
|
|
|
|
|
|
|
|
|
|
|
40 |
|
129 |
|
|
|
48 |
|
|
|
|
|
53 |
|
|
|
96 |
|
|
|
|
|
|
|
|
|
|
|
|
|
|
|
|
|
|
|
|
|
|
|
|
|
|
2.3.6.3 Параметры селектирования (стробирования) при контроле тавровых сварных соединений приведены в табл. 3.9 и на рис. 3.8.
20

а
б
в
Рисунок 3.8- Параметры селектирования при контроле сварных швов
тавровых соединений
а- контроль корня шва;
б- в – контроль всего сечения.
21

Таблица 3.9 Параметры селектирования тавровых сварных соединений
Толщина |
|
|
|
|
Параметры селектирования, мм |
|
|
|
|
|
||||||
привари- |
|
|
|
|
|
|
|
|
|
|
|
|
|
|
|
|
контроль корня шва |
|
|
|
контроль всего сечения |
|
|
|
|||||||||
ваемого |
|
|
|
|
|
|
||||||||||
|
|
|
|
|
|
|
|
|
|
|
|
|
|
|
|
|
элемента |
однократно отражены |
|
|
|
|
|
|
|
|
|
||||||
|
прямым лучом |
|
однократно отражённым |
|||||||||||||
δ, мм |
|
лучом (m=1) |
|
|
(m=0) |
|
|
|
лучом (m=1) |
|
||||||
|
|
|
|
|
|
|
|
|||||||||
|
|
|
|
|
|
|
|
|
|
|
|
|
||||
|
задержка |
длитель |
|
задержка |
|
длительность |
задержка |
длитель- |
||||||||
|
строба |
ность |
|
строба |
|
строба |
|
строба |
ность |
|||||||
|
|
|
|
Усл |
|
строба |
||||||||||
|
|
|
|
|
|
|
|
|
|
|
|
|||||
|
|
Усл |
строба |
|
Усл |
|
|
|
|
|
Усл |
Усл |
|
|||
|
|
|
|
У сл |
|
|
|
|
|
|
|
|
|
|
|
|
10 |
12 |
|
|
6 |
|
|
|
10 |
|
|
12 |
|
|
8 |
|
|
12 |
14 |
|
|
8 |
|
|
|
12 |
|
|
14 |
|
|
10 |
|
|
14 |
16 |
|
|
10 |
|
|
|
14 |
|
|
16 |
|
|
12 |
|
|
|
|
|
|
|
|
|
|
|
|
|
|
|
|
|
|
|
16 |
18 |
|
|
12 |
|
|
|
16 |
|
|
18 |
|
|
14 |
|
|
18 |
20 |
|
|
14 |
|
|
|
18 |
|
|
20 |
|
|
16 |
|
|
20 |
22 |
|
|
16 |
|
|
|
20 |
|
|
22 |
|
|
18 |
|
|
|
|
|
|
|
|
|
|
|
|
|
|
|
|
|
|
|
22 |
24 |
|
|
18 |
|
|
|
22 |
|
|
24 |
|
|
20 |
|
|
24 |
26 |
|
+(2tn)у |
20 |
|
(2tn)у |
|
24 |
|
+К2 |
26 |
|
+(2tn)у |
22 |
|
+К |
26 |
28 |
|
22 |
|
|
26 |
|
28 |
|
24 |
|
|||||
|
|
|
|
|
|
2 |
||||||||||
|
|
|
|
|
|
|
|
|
|
|
|
|
|
|
|
|
28 |
30 |
|
|
24 |
|
|
|
28 |
|
|
30 |
|
|
26 |
|
|
30 |
32 |
|
|
26 |
|
|
|
30 |
|
|
32 |
|
|
28 |
|
|
32 |
34 |
|
|
28 |
|
|
|
32 |
|
|
34 |
|
|
30 |
|
|
|
|
|
|
|
|
|
|
|
|
|
|
|
|
|
|
|
34 |
36 |
|
|
30 |
|
|
|
34 |
|
|
36 |
|
|
32 |
|
|
36 |
38 |
|
|
32 |
|
|
|
36 |
|
|
38 |
|
|
34 |
|
|
38 |
40 |
|
|
34 |
|
|
|
38 |
|
|
40 |
|
|
36 |
|
|
|
|
|
|
|
|
|
|
|
|
|
|
|
|
|
|
|
40 |
42 |
|
|
36 |
|
|
|
40 |
|
|
42 |
|
|
38 |
|
|
|
|
|
|
|
|
|
|
|
|
|
|
|
|
|
|
|
П р и м е ч а н и е- Параметр (2tn)у для конкретного преобразователя опреде-
ляется согласно пп. 3.7.17,а – 3.7.17,г.
3.6.4 Чувствительность при контроле тавровых сварных соединений определяется с учётом следующих факторов:
-ВРЧдействует только в зоне зондирующего импульса;
-отсечка – «слабая» или отключена;
-образцы для настройки чувствительностисм. табл. 3.10;
-значения коэффициентов выявляемости, соответствующих чувствительности поиска Кn и оценки Кo:
-для толщин привариваемого элемента 0-20 мм – см. табл. 3.11-3.12;
22

-для толщин привариваемого элемента свыше 20 ммсм. табл. 3.13-3.14;
-допустимое значение ослабления ( введённое на аттенюаторе) соответствую-
щее максимуму зхо-сигнала от эталонного отражателя при нахождении его вершины на уровне 6 больших клеток по экрану ЭЛТ дефектоскопа (No ≈ 2,5 дБ):
-для толщин привариваемого элемента 10-20 мм – см. табл. 3.11 – 3.12;
-для толщин привариваемого элемента свыше 20 ммсм. табл. 3.13 – 3.14.
Таблица 3.10
Образец для |
Толщина привариваемого |
|
|
Тольщина привариваемого |
||||||||||||||
настройки |
|
|
элемента 10-20 мм |
|
|
|
элемента свыше 20 мм |
|||||||||||
чувствитель |
Испытательный образец 2-го вида |
|
Стандартный образец |
|||||||||||||||
ности |
|
|
ОСТ 32 100-87 (рис. 3.9) |
|
|
|
|
СО-2 ГОСТ 14782-86 |
||||||||||
|
|
Цилиндрический |
отражатель |
диа- |
|
|
|
|
|
|
|
|
||||||
|
|
метром 2 мм, выполненный на глу- |
|
|
|
|
|
|
|
|
||||||||
|
|
бине: (для корня шва) |
|
|
|
|
|
|
|
|
|
|
|
|||||
Эталонный |
h3 (для всего сечения; m =0) |
|
|
Цилиндрический отража- |
||||||||||||||
h4 ( для всего сечения; m =0) |
|
|
|
|
|
тель диаметром |
||||||||||||
отражатель |
|
|
|
|
|
|||||||||||||
(конкретные значения – см. табл. |
|
6 мм на глубине 44 мм |
||||||||||||||||
|
|
|
||||||||||||||||
|
|
П.2-П.3 в приложении 1), соответст- |
|
|
|
|
|
|
|
|
||||||||
|
|
вующей |
середине контролируемой |
|
|
|
|
|
|
|
|
|||||||
|
|
зоны Но |
|
|
|
|
|
|
|
|
|
|
|
|
|
|
|
|
Таблица 3.11 |
|
|
|
|
|
|
|
|
|
|
|
|
|
|
|
|||
|
|
Применяемый образец для настройки чувствительности: |
|
|||||||||||||||
|
|
|
||||||||||||||||
Толщина |
|
|
испытательный образец 2-го вида ОСТ 32 100-87 |
|
||||||||||||||
|
|
|
|
|
|
|
|
|
|
|
|
|
|
|
|
|
|
|
приварива- |
Контроль корня шва |
|
|
|
|
|
Контроль всего сечения |
|
||||||||||
емого |
|
|
|
|
|
|
|
|
|
|
|
|
|
|
||||
|
|
|
|
|
катет К2 = 0,1 δ |
|
|
|
||||||||||
элемента |
|
m=1 |
|
|
|
|
|
|
|
|
|
|||||||
|
|
|
|
|
|
|
|
|
|
|
|
|
|
|
|
|||
δ, мм |
|
|
|
|
|
|
|
m = 0 |
|
|
|
|
m= 1 |
|
||||
|
|
|
|
|
|
|
|
|
|
|
|
|
|
|
|
|
||
|
Ко |
Кп |
|
No.доп. |
|
Ко |
|
Кп |
|
No.доп. |
|
Ко |
|
Кп |
|
No.доп. |
||
|
|
|
|
|
|
|
|
|
|
|
|
|
|
|
|
|
|
|
10 |
-12 |
-18 |
|
12…56 |
|
-10 |
|
-16 |
|
10…56 |
|
|
-12 |
|
-18 |
|
12…56 |
|
12 |
-14 |
-20 |
|
14…56 |
|
-10 |
|
-16 |
|
10…56 |
|
|
-14 |
|
-20 |
|
14…56 |
|
14 |
-14 |
-20 |
|
14…56 |
|
-12 |
|
-18 |
|
12…56 |
|
|
-14 |
|
-20 |
|
14…56 |
|
|
|
|
|
|
|
|
|
|
|
|
|
|
|
|
|
|
|
|
16 |
-14 |
-20 |
|
14…56 |
|
-12 |
|
-18 |
|
12…56 |
|
|
-14 |
|
-20 |
|
14…56 |
|
18 |
-16 |
-22 |
|
16…56 |
|
-12 |
|
-18 |
|
12…56 |
|
|
-14 |
|
-20 |
|
14…56 |
|
20 |
-16 |
-22 |
|
16…56 |
|
-14 |
|
-20 |
|
14…56 |
|
|
-16 |
|
-22 |
|
16…56 |
|
|
|
|
|
|
|
|
|
|
|
|
|
|
|
|
|
|
|
|
23

Образец изготавливается из материала контролируемого соединения
Рисунок 3.9 Образец второго вида для настойки чувствительности при контроле сварных швов тавровых соединений
Таблица 3.12
Толщина |
|
|
|
Применяемый образец для настройки чувствительности: |
|
|||||||||||
привари- |
|
|
|
испытательный образец 2-го вида ОСТ 32 100-87 |
|
|
|
|||||||||
ваемого |
|
|
|
|
|
Контроль всего сечения |
|
|
|
|
|
|
||||
элемента |
|
|
|
|
|
|
|
|
|
|
|
|
|
|
|
|
|
|
|
катет К2 =0,5δ |
|
|
|
|
катет К2 =0,9δ |
|
|
|
|||||
δ, мм |
|
|
|
|
|
|
|
|
m=0 |
|
|
|
|
|
||
|
m=0 |
|
|
m=1 |
|
|
|
m=1 |
|
|||||||
|
|
|
|
|
|
|
|
|
|
|
|
|
|
|
|
|
|
Ко |
Кп |
|
No.доп. |
Ко |
Кп |
No.доп. |
Ко |
Кп |
|
No.доп. |
Ко |
|
Кп |
|
Nо.доп. |
|
|
|
|
|
|
|
|
|
|
|
|
|
|
|
|
|
10 |
-12 |
-18 |
|
12…56 |
-14 |
-20 |
14…56 |
-12 |
-18 |
|
12…56 |
-14 |
|
-20 |
|
14…56 |
12 |
-12 |
-18 |
|
12…56 |
-16 |
-22 |
16…56 |
-14 |
-20 |
|
14…56 |
-14 |
|
-20 |
|
14…56 |
14 |
-14 |
-20 |
|
14…56 |
-16 |
-22 |
16…56 |
-14 |
-20 |
|
14…56 |
-16 |
|
-22 |
|
16…56 |
|
|
|
|
|
|
|
|
|
|
|
|
|
|
|
|
|
16 |
-14 |
-20 |
|
14…56 |
-16 |
-22 |
16…56 |
-14 |
-20 |
|
14…56 |
-16 |
|
-22 |
|
16…56 |
18 |
-14 |
-20 |
|
14…56 |
-16 |
-22 |
16…56 |
-16 |
-22 |
|
16…56 |
-16 |
|
-22 |
|
16…56 |
20 |
-14 |
-20 |
|
14…56 |
-16 |
-22 |
16…56 |
-16 |
-22 |
|
16…56 |
-16 |
|
-22 |
|
16…56 |
|
|
|
|
|
|
|
|
|
|
|
|
|
|
|
|
|
24

Таблица 3.13
|
|
|
Применяемый образец для настройки чувствительности: |
|
||||||||
Толщина |
|
|
стандартный образец СО-2 ГОСТ 14782-86 |
|
||||||||
приваривае- |
|
|
|
|
|
|
|
|
|
|
|
|
|
|
|
|
|
|
контроль всего сечения |
|
|||||
мого |
|
|
|
|
|
|
|
|||||
контроль корня шва |
|
|
|
|
|
|
|
|
|
|||
|
|
|
|
|
|
|
|
|
||||
элемента |
|
|
|
катет К2 = 0,1 δ |
|
|
|
|||||
δ, мм |
|
|
m=1 |
|
|
|
|
|
|
|
m=1 |
|
|
|
|
|
m=0 |
|
|
||||||
|
|
|
|
|
|
|
|
|
|
|
||
|
|
|
|
|
|
|
|
|
|
|
|
|
|
Ко |
Кп |
No.доп. |
Ко |
Кп |
|
No.доп. |
Ко |
|
Кп |
|
No.доп. |
|
|
|
|
|
|
|
|
|
|
|
|
|
22 |
-12 |
-18 |
12…56 |
0 |
-6 |
|
0…56 |
-16 |
|
-22 |
|
16…56 |
24 |
-14 |
-20 |
14…56 |
-2 |
-8 |
|
2…56 |
-16 |
|
-22 |
|
16…56 |
26 |
-16 |
-22 |
16…56 |
-4 |
-10 |
|
4…56 |
-18 |
|
-22 |
|
18…56 |
|
|
|
|
|
|
|
|
|
|
|
|
|
28 |
-16 |
-22 |
16…56 |
-4 |
-10 |
|
4…56 |
-20 |
|
-26 |
|
20…56 |
30 |
-18 |
-24 |
18…56 |
-6 |
-12 |
|
6…56 |
-20 |
|
-26 |
|
20…56 |
32 |
-20 |
-26 |
20…56 |
-8 |
-14 |
|
14…56 |
-22 |
|
-28 |
|
22…56 |
|
|
|
|
|
|
|
|
|
|
|
|
|
34 |
-20 |
-26 |
20…56 |
-8 |
-14 |
|
10…56 |
-24 |
|
-30 |
|
24…56 |
36 |
-22 |
-28 |
22…56 |
-10 |
-16 |
|
10…56 |
-24 |
|
-30 |
|
24…56 |
38 |
-22 |
-28 |
22…56 |
-10 |
-16 |
|
10…56 |
-26 |
|
-32 |
|
26…56 |
|
|
|
|
|
|
|
|
|
|
|
|
|
40 |
-24 |
-30 |
24…56 |
-12 |
-18 |
|
12…56 |
-26 |
|
-32 |
|
26…56 |
|
|
|
|
|
|
|
|
|
|
|
|
|
Таблица 3.14
Толщина |
|
|
|
Применяемый образец для настройки чувствительности: |
|
|||||||||||||
|
|
|
испытательный образец СО-2 ГОСТ 14782-86 |
|
|
|
||||||||||||
привари- |
|
|
|
|
|
|
||||||||||||
|
|
|
|
|
|
Контроль всего сечения |
|
|
|
|
|
|
|
|||||
ваемого |
|
|
|
|
|
|
|
|
|
|
|
|
|
|||||
|
|
|
|
|
|
|
|
|
|
|
|
|
|
|
|
|
|
|
|
|
|
катет К2 |
=0,5δ |
|
|
|
|
катет К2 |
=0,9δ |
|
|
|
|||||
элемента |
|
|
|
|
|
|
|
|
|
|
||||||||
|
|
|
|
|
|
|
|
|
|
|
|
|
|
|
|
|
|
|
|
m=0 |
|
|
|
m=1 |
|
m=0 |
|
|
|
m=1 |
|
||||||
δ, мм |
|
|
|
|
|
|
|
|
|
|||||||||
|
|
|
|
|
|
|
|
|
|
|
|
|
|
|
|
|
|
|
Ко |
Кп |
|
No.доп. |
|
Ко |
Кп |
No.доп. |
Ко |
Кп |
|
No.доп. |
|
Ко |
|
Кп |
|
Nо.доп. |
|
|
|
|
|
|
|
|
||||||||||||
|
|
|
|
|
|
|
|
|
|
|
|
|
|
|
|
|
|
|
22 |
-4 |
-10 |
|
4…56 |
|
-16 |
-22 |
16…56 |
-8 |
-14 |
|
8…56 |
|
-18 |
|
-24 |
|
18…56 |
24 |
-6 |
-12 |
|
6…56 |
|
-18 |
-24 |
18…56 |
-10 |
-16 |
|
10…56 |
|
-20 |
|
-26 |
|
20…56 |
26 |
-8 |
-14 |
|
8…56 |
|
-20 |
-26 |
20…56 |
-12 |
-18 |
|
12…56 |
|
-22 |
|
-28 |
|
22…56 |
|
|
|
|
|
|
|
|
|
|
|
|
|
|
|
|
|
|
|
28 |
-10 |
-16 |
|
10…56 |
|
-22 |
-28 |
22…56 |
-14 |
-20 |
|
14…56 |
|
-24 |
|
-30 |
|
24…56 |
30 |
-10 |
-16 |
|
10…56 |
|
-22 |
-28 |
22…56 |
-14 |
-20 |
|
14…56 |
|
-24 |
|
-30 |
|
24…56 |
32 |
-12 |
-18 |
|
12…56 |
|
-24 |
-30 |
24…56 |
-16 |
-22 |
|
16…56 |
|
-26 |
|
-32 |
|
26…56 |
|
|
|
|
|
|
|
|
|
|
|
|
|
|
|
|
|
|
|
34 |
-14 |
-20 |
|
14…56 |
|
-26 |
-32 |
26…56 |
-16 |
-22 |
|
16…56 |
|
-28 |
|
-34 |
|
28…56 |
36 |
-14 |
-20 |
|
14…56 |
|
-26 |
-32 |
26…56 |
-18 |
-24 |
|
18…56 |
|
-28 |
|
-34 |
|
28…56 |
38 |
-16 |
-22 |
|
16…56 |
|
-28 |
-34 |
28…56 |
-20 |
-26 |
|
20…56 |
|
-30 |
|
-36 |
|
30…56 |
|
|
|
|
|
|
|
|
|
|
|
|
|
|
|
|
|
|
|
40 |
-16 |
-22 |
|
16…56 |
|
-28 |
-34 |
28…56 |
-20 |
-26 |
|
20…56 |
|
-30 |
|
-36 |
|
30…56 |
|
|
|
|
|
|
|
|
|
|
|
|
|
|
|
|
|
|
|
25
3.7 Подготовка и настройка аппаратуры к работе. Проверка основных параметров контроля
3.7.1 Дефектоскоп должен быть укомплектован:
а) преобразователями на частоту f = 2,5 Мгц с размерами пьезопластин
12×18мм или диаметром 2а=12мм и углами ввода в сталь α=50º ±2º или α=65º± 2º (в зависимости от толщины сварных соединений, см:
-таблица 3.3 – для стыковых швов;
-таблица 3.8 - для тавровых швов);
б) кабелями и преобразователями для реализации совмещённой схемы про-
звучивания; в) стандартными образцами СО-2 и СО-3, а также при контроле соединений
толщиной 10-20 мм – испытательными образцами 1-го или 2-го вида;
г) инструментом для зачистки контактной поверхности контролируемого соединения от ржавчины и грязи;
д) мерительным инструментом;
е) контактирующей жидкостью и кистью для её нанесения на контактную
поверхность; ж) мелом или краской для отметки дефектных участков сварного шва;
з) документом ( бланками карт или журналом контроля) для регистрации результатов контроля.
3.7.2 Перед выходом на контроль необходимо:
а) осмотреть дефектоскоп; б) убедиться в его исправности;
в) выбрать преобразователь ( п. 3.7.4); г) проверить положение точки выхода ( п. 3.7. 6, а); д) проверить угол ввода ( п. 3.7.8, а);
е) настроить глубиномер ( пп. 3.7.6- 3.7.9) и проверить точность его работы
(пп. 3.7.10 - 3.7.11);
ж) настроить чувствительность ( пп. 3.7.12 – 3.7.15); з) проверить работоспособность аттенюатора ( пп. 2.3.7.14,1) – 2.3.7.14,7);
и) уточнить настройку ВРЧ (для подавления зондирующего импульса) и про-
верить «мёртвую зону» ( п. 3.7.16); к) настроить параметры строба АСД ( схемы селекции) и длительность раз-
вертки ( пп. 3.7.17- 3.7.18).
26

3.7.3 При работе с дефектоскопом УД2-12 предварительно выполнить установку органов управления в соответствии с табл. 3.15.
Таблица 3.15 Установка органов управления
пп. |
|
|
Орган |
Место рас- |
Как устанавли- |
||||||||||||
управления |
положения |
вается |
|||||||||||||||
|
|||||||||||||||||
1 |
|
|
|
2 |
|
|
|
|
|
|
3 |
4 |
|
||||
а |
кнопка ВНЕШН |
задняя |
нажать |
||||||||||||||
|
|
|
|
|
|
ВНУТР |
панель |
||||||||||
|
|
|
|
|
|
|
|
|
|||||||||
|
кнопка |
|
|
125 Нz |
задняя |
нажать |
|||||||||||
б |
|
|
|
|
|
|
500 Нz |
панель |
отжать |
||||||||
кнопка |
|
|
« х 2» |
задняя |
|||||||||||||
|
|
|
|||||||||||||||
|
|
|
|
|
|
|
|
|
|
|
|
|
|
панель |
|
|
|
|
регулятор |
|
|
|
|
|
|
передняя |
в крайнее |
||||||||
в |
|
|
|
|
|
|
|
|
|
|
|
|
|
панель |
левое |
||
|
|
|
|
|
|
|
|
|
|
|
|
|
|
|
положение |
||
|
|
|
|
|
|
|
|
|
|
|
|
|
|
|
|||
|
кнопка «2,5» пе- |
блок А7 |
нажать |
||||||||||||||
г |
реключателя |
||||||||||||||||
блок А9 |
нажать |
||||||||||||||||
|
«ЧАСТОТА МНz» |
||||||||||||||||
|
|
|
|
||||||||||||||
д |
Кнопка |
mm2 |
dB |
блок А8 |
отжать |
||||||||||||
|
|
|
|
|
|
|
|||||||||||
|
|
|
|
|
|
|
|
|
|
|
|
|
|
|
|
||
|
|
|
|
|
|
|
|
|
|
|
|
|
|
|
|
|
|
|
кнопка «НАКАЛ» |
передняя |
последовательно |
||||||||||||||
е |
|
|
|
|
|
|
|
|
|
|
|
|
|
панель |
нажать с |
||
|
|
|
|
|
|
|
|
|
|
|
|
|
|
||||
|
|
|
|
|
|
|
|
|
|
|
|
|
передняя |
интервалом |
|||
|
|
|
|
|
|
|
|
|
|
|
|
|
|
||||
|
кнопка «РАБОТА» |
1 мин |
|||||||||||||||
|
панель |
||||||||||||||||
|
|
|
|
|
|
|
|
|
|
|
|
|
|
|
|
||
|
|
|
|
|
|
|
|
|
|
|
|
|
|
|
в положения, при |
||
|
|
|
|
|
|
|
|
|
|
|
|
|
|
|
которых |
линия |
|
|
регулятор « ↕» |
блок А5 |
развертки |
нахо- |
|||||||||||||
ж |
|
|
|
|
|
|
|
|
|
|
|
|
|
|
дится на нижней |
||
|
|
|
|
|
|
|
|
|
|
|
|
|
|
линии сетки эк- |
|||
|
|
|
|
|
|
|
|
|
|
|
|
|
|
|
|||
|
регулятор «↔» |
блок А5 |
рана, её начало |
||||||||||||||
|
|
|
|
|
|
|
|
|
|
|
|
|
|
|
у первого |
края |
|
|
|
|
|
|
|
|
|
|
|
|
|
|
|
|
экрана ЭЛТ |
||
з |
кнопка |
|
|
|
|
|
|
|
|
|
|
блок А6 |
нажать |
||||
|
|
|
|
|
|
|
|
|
|
||||||||
|
|
|
|
|
|
|
|
|
|
|
|
|
|||||
|
|
|
|
|
|
|
|
|
|
|
|
|
|
|
|
|
|
|
|
|
|
|
|
|
|
|
|
|
|
|
|
|
|
|
|
|
кнопка |
|
|
|
|
|
|
ВРЧ |
|
|
|
||||||
и |
|
|
АСД |
|
блок А10 |
отжать |
|||||||||||
|
|
|
|
|
|
|
|||||||||||
|
|
|
|
|
|
|
|||||||||||
|
|
|
|
|
|
|
|
|
|
|
|
|
|
|
|
||
|
|
|
|
|
|
|
|
|
|
|
|
|
|
|
|
|
|
к |
регулятор |
блок А7 |
в крайнее правое |
||||||||||||||
|
«АМПЛ» |
положение |
|||||||||||||||
|
|
|
|||||||||||||||
|
|
|
|
|
|
|
|
|
|
|
|
|
|
|
|
||
|
|
|
|
|
|
|
|
|
|
|
|
|
|
|
в положение, |
||
|
|
|
|
|
|
|
|
|
|
|
|
|
|
|
близкое к крайне |
||
|
регулятор |
|
левому, при ко- |
||||||||||||||
|
|
|
|
|
|
|
|
|
|
|
|
|
|
|
тором левый го- |
||
л |
|
|
|
|
|
|
|
|
|
|
|
|
|
блок А8 |
ризонтальный |
||
|
|
|
|
|
|
|
|
|
|
|
|
|
|||||
|
|
|
|
|
|
|
|
|
|
|
|
|
участок кривой |
||||
|
|
|
|
|
|
|
|
|
|
|
|
|
|
|
|||
|
|
|
|
|
|
|
|
|
|
|
|
|
|
|
ВРЧ находится |
||
|
|
|
|
|
|
|
|
|
|
|
|
|
|
|
на уровне 1-2 |
||
|
|
|
|
|
|
|
|
|
|
|
|
|
|
|
больших клеток |
||
|
|
|
|
|
|
|
|
|
|
|
|
|
|
|
снизу |
|
Что происходит
5
установка режима внутренней синхронизации дефектоскопа установка частоты внутренней
синхронизации, равной 500 Гц
предварительное отключение ручного стробирования
установка частоты УЗК, равной 2,5 МГц
отключение режима измерения эквивалентной площади
включение дефектоскопа
подключение второй развертки
выведение на вторую развертку кривой ВРЧ (может наблюдаться горизонтальная линия развертки)
установка максимальной амплитуды зондирующего импульса
предварительная установка исходного ( начального)
уровня ВРЧ
27

Продолжение таблицы 3.15
пп. |
|
|
|
|
|
|
Орган |
Место распо- |
Как устанавлива- |
Что происходит |
||||||||||
управления |
ложения |
ется |
||||||||||||||||||
|
|
|||||||||||||||||||
1 |
2 |
|
|
|
|
|
|
3 |
4 |
|
5 |
|||||||||
|
|
|
|
регулятор |
|
в крайнее левое |
предварительная установ- |
|||||||||||||
|
|
|
|
|
|
|
|
|
|
|
|
|
|
|
|
блок А8 |
||||
м |
|
|
|
|
|
|
|
|
|
|
|
|
|
|
|
положение |
ка зоны ВРЧ в районе |
|||
|
|
|
|
|
|
|
|
|
|
|
|
|
|
|
|
|
|
|||
|
|
|
регулятор |
блок А8 |
в крайнее левое |
зондирующего импульса |
||||||||||||||
|
|
|
|
|||||||||||||||||
|
|
|
|
|
|
|
|
|
|
|
|
|
|
|
|
|
||||
|
|
|
|
|
|
|
|
|
|
|
|
|
|
|
|
|
положение |
|
||
|
|
|
|
|
|
|
|
|
|
|
|
|
|
|
|
|
|
|
|
|
|
|
|
|
|
|
|
|
|
|
|
|
|
|
|
|
|
в положение, при |
|
||
|
|
|
|
|
|
|
|
|
|
|
|
|
|
|
|
|
котором |
правый |
|
|
|
|
|
|
регулятор |
|
горизонтальный |
|
|||||||||||||
|
|
|
|
|
|
|
|
|
|
|
|
|
|
|
|
|
участок |
второй |
установка величины уси- |
|
н |
|
|
|
|
|
|
|
|
|
|
|
|
|
|
|
блок А8 |
развертки |
«при- |
ления ВРЧ, ориентировоч- |
|
|
|
|
|
|
|
|
|
|
|
|
|
|
|
|
|
|
поднят» |
относи- |
но равной 20 дБ |
|
|
|
|
|
|
|
|
|
|
|
|
|
|
|
|
|
|
тельно левого го- |
|||
|
|
|
|
|
|
|
|
|
|
|
|
|
|
|
|
|
|
|||
|
|
|
|
|
|
|
|
|
|
|
|
|
|
|
|
|
ризонтального |
|
||
|
|
|
|
|
|
|
|
|
|
|
|
|
|
|
|
|
участка на 2 боль- |
|
||
|
|
|
|
|
|
|
|
|
|
|
|
|
|
|
|
|
шие клетки |
|
||
|
регулятор (ручка) |
|
в крайнее правое |
|
||||||||||||||||
|
|
|
|
|
|
|
|
|
|
|
|
|
|
|
|
блок А9 |
положение |
отключение отсечки |
||
|
|
|
|
|
|
|
|
|
|
|
|
|
|
|
|
|
ИЛИ |
|
||
|
|
|
|
|
|
|
|
|
|
|
|
|
|
|
|
|
|
|||
|
регулятор (ручка) |
|
|
|||||||||||||||||
|
|
|
|
|
||||||||||||||||
о |
|
|
|
|
|
|
|
|
|
|
|
|
|
|
|
блок А9 |
в положения, при |
|
||
|
|
|
|
|
|
|
|
|
|
|
|
|
|
|
|
|||||
|
|
|
|
|
|
|
|
|
|
|
|
|
|
|
|
|
которых |
отсутст- |
установка «слабой» |
|
|
|
|
|
|
|
|
|
|
|
|
|
|
|
|
|
|
||||
|
|
|
|
|
|
|
|
|
|
|
|
|
|
|
|
|
вуют шумы высо- |
|||
|
регулятор (шлиц) |
|
отсечки |
|||||||||||||||||
|
|
той) 0.5-1 боль- |
||||||||||||||||||
|
|
|
|
|
|
|
|
|
|
|
|
|
|
|
|
|
|
|||
|
|
|
|
|
|
|
|
|
|
|
|
|
|
|
|
блок А9 |
ших клеток по эк- |
|
||
|
|
|
|
|
|
|
|
|
|
|
|
|
|
|
|
|
||||
|
|
|
|
|
|
|
|
|
|
|
|
|
|
|
|
рану ЭЛТ |
|
|
||
|
|
|
|
|
|
|
|
|
|
|
|
|
|
|
|
|
|
|
||
|
|
|
|
|
|
|
|
|
|
|
|
|
|
|
|
|
|
|
|
|
|
|
|
|
регулятор |
блок А6 |
в крайнее правое |
предварительная установ- |
|||||||||||||
п |
|
|
|
|
|
|
|
|
|
|
|
|
|
|
|
|||||
|
|
|
|
|
|
|
|
|
|
|
|
|
|
|
|
положение отжать |
ка длительности развертки |
|||
|
кнопка «х 10» |
блок А6 |
||||||||||||||||||
|
|
|
|
|||||||||||||||||
|
|
|
Регулятор |
|
в положение, |
|
||||||||||||||
|
|
|
|
|
|
|
|
|
|
|
|
|
|
|
|
|
близкое к крайне |
установка режима контро- |
||
|
|
|
|
|
|
|
|
|
|
|
|
|
|
|
|
|
правому, при ко- |
ля «От поверхности» |
||
р |
|
|
|
|
|
|
|
|
|
|
|
|
|
|
|
блок А6 |
тором виден хотя |
|||
|
|
|
|
|
|
|
|
|
|
|
|
|
|
|
(Синхронного запуска |
|||||
|
|
|
|
|
|
|
|
|
|
|
|
|
|
|
|
|
бы задний фронт |
|||
|
|
|
|
|
|
|
|
|
|
|
|
|
|
|
|
|
развертки) |
|||
|
|
|
|
|
|
|
|
|
|
|
|
|
|
|
|
|
зондирующего |
|||
|
|
|
|
|
|
|
|
|
|
|
|
|
|
|
|
|
|
|||
|
|
|
|
|
|
|
|
|
|
|
|
|
|
|
|
|
импульса |
|
||
|
|
|
|
|
|
|
|
|
|
|
|
|
|
|
|
|
в положение, при |
|
||
|
пластина «μs» |
|
котором десятичная |
предварительная установ- |
||||||||||||||||
с |
передняя |
точка находится по- |
ка режима БЦО «μs» с воз- |
|||||||||||||||||
|
сенсорного |
панель |
сле третьего разря- |
можностью индикации де- |
||||||||||||||||
|
переключателя |
да (путём двойного |
||||||||||||||||||
|
|
|
|
|
|
|
|
|
|
|
|
|
|
|
|
|
прикосновения к |
сятых долей микросекунд |
||
|
|
|
|
|
|
|
|
|
|
|
|
|
|
|
|
|
сенсорной пластине) |
|
||
|
кнопка «▼» |
блок А6 |
отжать |
|
предварительная установ- |
|||||||||||||||
т |
|
|
|
|
|
|
|
|
|
|
|
|
|
|
|
|
|
|
ка БЦО в режим измере- |
|
|
|
|
|
|
|
|
|
|
|
|
|
|
|
|
|
|
|
ния параметров отражён- |
||
|
|
|
|
|
|
|
|
|
|
|
|
|
|
|
|
|
|
|
||
|
|
|
|
|
|
|
|
|
|
|
|
|
|
|
|
|
|
|
ных сигналов |
28

Продолжение таблицы 3.15
пп. |
Орган |
Место рас- |
Как |
Что происходит |
||
управления |
положения |
устанавливается |
||||
|
|
|||||
|
|
|
|
|
|
|
1 |
2 |
|
3 |
4 |
5 |
|
|
Кнопка |
|
|
включение режима работы |
||
у |
|
|
блок А10 |
нажать |
||
|
|
звукового индикатора |
||||
|
|
|
|
|
||
|
|
|
|
|
|
|
|
регулятор |
|
|
отключение третьего |
||
ф |
(«шлиц») |
блок А10 |
в крайнее правое |
(верхнего) порога АСД, |
||
«▼ 1» |
положение |
соответствующего красной |
||||
|
|
|||||
|
|
|
|
|
лампе АСД. |
3.7.4 Выбрать необходимый угол в вода луча α в зависимости от толщины контролируемого сварочного соединения и способа прозвучивания [прямым (m=0) или однократно отражённым (m= 1) лучом] в соответствии с:
-табл. 3.3 – для стыковых швов; -табл. 3.8 - для тавровых швов.
Пр и м е ч а н и я:
1)На преобразователях с металлическим корпусом (входящий в комплект по-
становки дефектоскопа УД2-12) указан угол ввода в сталь. Некоторые первые пар-
тии дефектоскопов УД2-12 были укомплектованы преобразователями из капролона с маркировкой угла призмы β . На преобразователях из оргстекла, изготовленных НИИ мостов, указан угол призмы β.
2)Соотношения между углом призмы из оргстекла и углом ввода в сталь сле-
дующие:
углу β =40º примерно соответствует угол α =50º;
углу β = 50º примерно соответствует угол α =65º.
3.7.5 Подключить кабель для реализации совмещённой схемы с отобранным преобразователем к разъемам, расположенным на передней панели.
П р и м е ч а н и е - В случае отсутствия специального кабеля или несовпадения его разъёмв с разъёмами на преобразователе совмещённую схему можно реа-
лизовать с использованием других кабелей, применяемых при УЗК, и тройка СР-50 (рис. 3.10). Тройник СР-50 подключается к одной из разъёмов на передней панели дефектоскопа, К оставшемуся свободному гнезду дефектоскопа подключается ка-
бель с двумя разъёмами СР-50, второй конец которого должен быть подсоединён к тройнику СР-50. К третьему выводу тройника подключается кабель, к которому через разъём подсоединен преобразователь.
29

Рисунок 3.10 Схема подключения ПЭП в случае отсутствия (несоответствия разъёмов) кабеля из комплекта дефектоскопа УД2-12
3.7.6 Произвести установку нуля глубиномера. Для этого установить преобра-
зователь на поверхность стандартного образца СО-3 так, чтобы отражение УЗК
осуществлялось от вогнутой поверхности. В положении максимума первого отражённого сигнала:
а) определить (уточнить) положение точки выхода луча; б) аттенюатором (при необходимости также воспользоваться регулятором «►»
на блоке А8) подвести вершину отражённого сигнала к заранее выбранному (пре-
вышающему две большие клетки снизу) уровню, напр., середине экрана; в) застробировать отражённый сигнал стробом АСД (с помощью регуляторов
« |
|
|
|
|
» и « |
|
|
|
|
» на блоке А10) или ручным стробированием (используя |
||
регулятор |
« |
|
|
|
|
» на передней панели); |
||||||
|
|
|
||||||||||
|
|
|
|
|
|
|
||||||
|
|
4) регулятором «►0◄ » на блоке А6 выставить по индикатору БЦО значение: |
-«033.7» ( если используется СО-3 радиусом 55 мм);
-«036.8» ( если используется СО-3 радиусом 60 мм).
3.7.7 Для произвольного положения преобразователя: отключить ( если при-
менялось ) |
ручное стробирование, для чего регулятор |
на передней панели уста- |
новить в исходное, крайнее левое положение. |
|
|
3.7.8 |
Произвести настройку глубиномера на требуемые значения скорости |
распространения УЗК и угла ввода луча. Для этого установить преобразователь на
30

поверхность стандартного образца СО-2 со стороны шкалы α = 0…70º. В положении
максимума эхо – сигнала от отверстия диаметром 6 мм на глубине 44 мм:
а) определить (уточнить) угол ввода луча, который не должен отличаться от выбранного более, чем на ± 2º;
б) подвести вершину отражённого сигнала к ранее выбранному уровню
( п. 3.7.6, б);
в) застробировать сигнал стробов АСД или ручным стробированием ;
г) установить сенсорным переключателем режим БЦО « mm Х»;
д) регулятором «▼ mmХ» на блоке А5 выставить по индикатору БЦО значение
Х44 из табл. 3.16 для ранее полученной величины α;
е) установить сенсорным переключателем режим « mm Y»;
ж) регулятором « ▼mmY» на блоке А5 выставить по индикатору БЦО значение
Y44 из табл. 3.16 для ранее полученной величины α.
Таблица 3.16
|
Настройка |
|
|
|
Проверка настройки глубиномера |
|
|
||||||||
|
глубиномера |
|
|
|
|
|
|||||||||
|
|
|
|
|
|
|
|
|
|
|
|
|
|
||
|
|
|
|
Прозвучивание со стороны шкалы |
|
|
|||||||||
|
|
|
|
|
|
|
|
|
|
|
|
|
|
|
|
Угол |
α =0…70º |
|
|
|
|
|
|
α = 60…80º |
|
|
|||||
ввода α, |
|
|
|
Глубина расположения центра отверстия |
|
|
|||||||||
град. |
|
|
|
|
|
|
|
|
|
|
|
|
|
|
|
Н=44 мм |
|
|
|
Н=15 мм |
|
|
|
ИЛИ Н=21 ммм |
|||||||
|
|
|
|
|
|
|
|||||||||
|
|
|
|
|
|
|
|
|
|
|
|
|
|
||
|
|
|
|
Значения координат отражателя , мм |
|
|
|||||||||
|
|
|
|
|
|
|
|
|
|
|
|
|
|
|
|
|
Х44 |
У44 |
|
|
Х15 |
|
У15 |
Х21 |
|
У21 |
|||||
|
|
|
|
|
|
|
|
|
|
|
|
|
|
|
|
48 |
46,6 |
42,0 |
|
14,4 |
|
|
13,0 |
|
|
|
21,1 |
|
|
19,0 |
|
|
|
|
|
|
|
21,9 |
|
|
|
||||||
49 |
48,3 |
42,0 |
|
15,0 |
|
|
13,0 |
|
|
|
|
|
19,0 |
|
|
|
|
|
|
|
|
22,7 |
|
|
|
||||||
50 |
50,1 |
42,1 |
|
15,6 |
|
|
13,1 |
|
|
|
|
|
19,1 |
|
|
|
|
|
|
|
|
23,6 |
|
|
|
||||||
51 |
52,0 |
42,1 |
|
16,2 |
|
|
13,1 |
|
|
|
|
|
19,1 |
|
|
|
|
|
|
|
|
24,5 |
|
|
|
||||||
52 |
53,9 |
42,2 |
|
16,8 |
|
|
13,2 |
|
|
|
|
|
19,2 |
|
|
|
|
± 2,0 |
|
± 1,5 |
|
|
|
|
|||||||
|
|
|
|
|
|
|
|
|
+ 2,0 |
|
|
+ 1,5 |
|||
|
|
|
|
|
|
|
|
|
|
|
|
|
|
||
63 |
83,7 |
42,6 |
|
26,8 |
|
|
13,6 |
|
|
|
38,5 |
|
19,6 |
||
|
|
|
|
|
|
|
|
|
|||||||
|
|
|
|
|
|
|
|
19,7 |
|
||||||
64 |
87,5 |
42,7 |
|
28,1 |
|
|
13,7 |
|
|
|
40,3 |
|
|
|
|
|
|
|
|
|
|
|
|
19,7 |
|
||||||
64 |
91,6 |
42,7 |
|
29,4 |
|
|
13,7 |
|
|
|
42,3 |
|
|
|
|
|
|
|
|
|
|
|
|
19,8 |
|
||||||
66 |
96,1 |
42,8 |
|
30,9 |
|
|
13,8 |
|
|
|
44,4 |
|
|
|
|
|
|
|
|
|
|
|
|
19,8 |
|
||||||
67 |
100,9 |
42,8 |
|
32,6 |
|
|
13,8 |
|
|
|
46,7 |
|
|
|
|
|
|
|
|
|
|
|
|
|
|
||||||
|
|
|
|
|
|
|
|
|
|
|
|
|
|
|
|
31

3.7.9 Для произвольного положения преобразователя: отключить ( если
применялось) ручное стробирование, для чего регулятор |
|
|
|
на передней |
панели установить в исходное , крайнее левое положение. |
|
|
||
3.7.10 Проверить точность настройки глубинометра, для чего установить пре- |
||||
образователь на поверхность стандартного образца СО-2 со |
стороны шкалы |
α =60….80º .В положении максимума эхо-сигнала от отверстия диаметром 6 мм на
глубине Н=15 мм ( если СО-2 высотой 59 мм) или на глубине Н=21 мм ( если СО-2
высотой 65 мм):
а) подвести вершину отражённого сигнала до ранее выбранного уровня;
б) застробировать сигнал стробом АСД или ручным стробированием; в) установить сенсорным переключателем режим БЦО « mmX»;
г) считать значение ХБЦО с индикатора БЦО; оно должно соответствовать указанному Х15 или Х21 в табл. 3.16 для имеющегося α;
д) установить сенсорным переключателем режим «mmY»;
е) считать значение УБЦО с индикатора БЦО; оно должно соответствовать ука-
занному У15 или У 21 в табл. 3.16 для имеющегося α.
П р и м е ч а н и е - Если при проверке точности работы глубиномера показания БЦО отличаются от указанных в табл. 3.16, следует повторить настойку.
3.7.11 Для произвольного положения преобразователя: отключить (если
применялось) ручное стробирование, для чего регулятор |
|
|
|
на передней |
панели установить в исходное, крайнее левое положение. |
|
|
|
|
3.7.12Выбрать образец для настройки чувствительности в соответствии с : - табл. 3.5 – для стыковых швов; - табл. 3.10 – для тавровых швов.
3.7.13Сенсорным переключателем установить режим БЦО « dB».
3.7.14Установить преобразователь на поверхность выбранного образца. В положении максимума эхо-сигнала от требуемого эталонного отражателя ( для толщин
10-20 мм -с учётом значения m=0 или m=1; см: - рис.3.5- для стыковых сварных швов;
- рис. 3.9 – для тавровых сварных швов:
1) аттенюатором ( при необходимости также воспользоваться регулятором
«►» на блоке А8) добиться одновременного выполнения следующих условий (рис.
13.11, а):
-положение вершины отражённого сигнала – на уровне 6 больших клеток снизу по экрану ЭЛТ;
32

-значение ослабления кнопочного аттенюатора ΝоКН удовлетворяет допустимым ( по возможности, меньшим из допустимых) значения ΝoКН.доп. соответственно
из:
-табл.3.6 –3.7 – для стыковых швов;
-табл.3.11- 3.14для тавровых соединений; б) застробировать сигнал стробом АСД или ручным стробированием;
в) |
считать и запомнить показание с БЦО NоБЦО ; оно должно составлять |
NоБЦО |
=2,5 ± 1дБ; |
г) рассчитать (с учетом знака) и зафиксировать в рабочем журнале (карте кон-
троля) значение амплитуды от эталонного отражателя Nо = ΝоКН - NоБЦО;
д) выставить порог АСД, соответствующий чувствительности оценки К, для чего регулятором «▼II» на блоке А10 добиться загорания (но на пороге) жёлтой лампы АСД;
е) кнопочным аттенюатором внести дополнительное ослабление, равное К = 6дБ (рис. 3.11,б);
ж) убедиться, что показание NБЦО также увеличилось на ( 6±0,2) дБ.
П р и м е ч а н и е- Если показания NБЦО для пп. 2.3.15, в и 2.3.15,ж отличаются от указанных, то данный дефектоскоп применять для контроля не допускается.
з)выставить порог АСД, соответствующей чувствительности поиска Кп, для чего регулятром «▼ III» на блоке А10 добиться загорания (но на пороге) зеленой лампы
АСД;
и) убедится, что при зажигании зелёной лампы АСД работает звуковой индикатор, а в случае её погасания при снятии ПЭП с образца – звуковой индикатор перестаёт работать.
3.7.15 Для произвольного положения преобразователя выполнить:
а) реализовать на дефектоскопе чувствительность поиска Кп, для чего кнопоч-
ным аттенюатором уменьшить ослабление на величину Кп ( рис. 3.11,в) согласно:
-табл. 3.6 – 3.7 – для стыковых швов;
-табл. 3.11 – 3.14 – для тавровых швов.
б) считать и запомнить величину ослабления на кнопочном аттенюаторе N контр.КН, при которой будет производиться контроль;
в) отключить ( если применялось) ручное стробирование, для чего регулятор « » на передней панели установить в исходное крайнее левое положение.
33

Рисунок 3.11 Изменение сигнала на экране ЭЛТ при настройке
чувствительности
34

3.7.16 Уточнить настройку ВРЧ (для подавления зондирующего импульса) и проверить «мёртвую зону». Для этого:
а) выбрать отверстие и образец для проверки «мёртвой зоны» М исходя из то-
го, что: |
|
|
|
|
|
|
|
-допустимые значения М равны: |
|
||||||
М=8 – для |
|
α =50º ± 2º ; |
|
||||
М=3 – для |
|
α =65º± 2º; |
|
||||
-отверстия для проверки М имеются в следующих образцах: |
|||||||
на глубине |
3 |
мм – в стальном образце СО-2; |
|
||||
|
|
- в испытательном образце 2-го вида; |
|||||
на глубине |
8 |
мм –в стальном образце СО-2; |
|
||||
б) установить регулятор « |
|
|
|
» на блоке А8 так, чтобы начало |
|||
|
|
|
|||||
|
|
|
|
|
|
|
|
экспоненциального участка (зоны ВРЧ) на кривой ВРЧ ( второй развертке) соответ-ствовало ориентировочно середине зондирующего импульса;
в) установить регулятор |
|
|
|
на блоке А8 так, чтобы конец |
экспоненциального участка кривой ВРЧ находился ориентировочно у первого края зондирующего импульса (включая шумы преобразователя);
г)установить преобразователь на поверхность образца и выявить требуемое
отверстие диаметром 2 мм ( рис. 12,а); |
|
|
|
|
|
|
|
|
|
||
д) уточнить положение регуляторов |
|
|
|
|
и |
|
|
на блоке А8, ис- |
|||
|
|
|
|
|
|
||||||
|
|
|
|
|
|
||||||
пользуя их совместно с регулятором |
|
|
на блоке А8, с целью одновременного вы- |
полнения следующих условий ( рис. 3.12,б):
-в зоне зондирующего импульса отсутствуют шумы преобразователя; -требуемое отверстие для проверки мертвой зоны уверено выявляется ( т.е.
амплитуда шумов преобразователя правее эхо-сигнала от отверстия ниже порога АСД, соответствующего чувствительного поиска, а амплитуда эхосигнала от отверстия выше порога АСД, соответствующего чувствительности оценки);
-максимум эхо-сигнала от отверстия расположен за пределами экспоненциального участка ВРЧ ( т.е. в пределах правого горизонтального участка) либо в пределах экспоненциального участка у его правого края.
П р и м е ч а н и е - Если «мертвая зона» не соответствует указанным значениям, то данный преобразователь применять для контроля не допускается.
35

Рисунок 3.12 Изменение сигналов на экране ЭЛТ при настройке ВРЧ
3.7.17 Настроить параметры строба АСД, для чего:
а) сенсорным переключателем установить режим БЦО « mmY» ;
б) перевести БЦО в режим измерения в контрольных гнездах путём нажатия кнопки «▼» на блоке А6;
в) обеспечить режим измерения параметра ( 2tп )у путём соединения коммутационным проводом гнезд «4» и «3» на блоке А6;
г) считать с БЦО и запомнить значение (2tп)у ;
д) обеспечить режим измерения задержки строба относительно зондирующего импульса путём соединения коммутационным проводом гнезда «4» на блоке А6 с гнездом «1» на блоке А10;
е) регулятором на блоке А10 с учётом измеренного значения (2tп)у
выставить требуемую величину У сл из:
-табл. 3.4– для стыковых швов;
-табл. 3.9 – для тавровых швов.
Пр и м е ч а н и е - Если для случая m=0 при требуемом значении Усл начало
строба АСД оказывается в зоне зондирующего импульса, то передний фронт строба следует устанавливать сразу же за зондирующим импульсом. При этом БЦО будет индицировать фактическую задержку строба, отличающуюся от требуемой на величину М.
ж) обеспечить режим измерения длительности строба путём соединения коммутационным проводом гнезда «4» на блоке А6 с гнездом «2» на блоке А10;
з) регулятором |
|
|
|
на блоке А10 выставить требуемое значение У сл из: |
36

-табл. 6 – для стыковых швов; -табл. 11 – для тавровых швов.
П р и м е ч а н и я :
1. В случае , когда начало строба было сдвинуто вправо на величину М за задний фронт зондирующего импульса, - длительность строба должна составлять (
Усл.- М).
2. При установке требуемой длительности строба необходимо следить за тем, чтобы конец строба был в пределах экрана ( длительности развертки). В необхо-
димых случаях увеличить длительность развертки регулятором |
, а также |
|||
кнопкой « х 10» на блоке А6. |
|
|
|
|
|
|
|||
3.7.18 Настроить длительность развертки для чего регулятором |
на |
|||
|
|
|||
блоке А6 добиться, чтобы конец строба находился у правого края экрана |
. |
|
3.7.19Установить БЦО и режим измерения параметров отраженных сигналов путём отжатия кнопки «▼» на блоке А6.
3.7.20Для удобства наблюдения отражённых сигналов на экране ЭЛТ дефектоскопа в ряде случаев (особенно в яркоосвещённых местах), а также, когда из-за высокого уровня шумов неудовлетворительно наблюдается строб АСД, может быть
дополнительно подключена вторая развертка путём нажатия кнопок |
|
|
на блоке |
|
А6 и АСД / ВРЧ на блоке А10. В этом случае: |
|
|
|
|
-на вторую развертку, так же как и на первую ( основную) развертку, выводится строб АСД;
-уровень второй развертки определяется вершиной отражённого эхосигнала, попадающего в строб АСД, если в стробе несколько сигналовто вершиной наибольшего из них. При отсутствии каких-либо сигналов в стро-
бе АСД уровень второй развертки находится у нижнего края экрана.
3.8 Подготовка сварного соединения к контролю
3.8.1Перед началом контроля соединения дефектоскопист должен визуально убедиться в отсутствии недопустимых поверхностных дефектов. В случае их наличия они должны быть удалены представителями подразделения, представляющего
соединение на контроль.
3.8.2Перед контролем стыкового сварного шва дефектоскопист обязан проверить соответствие требованиям табл. 3, обеспечивающих дефектоскопичность со-
единения.
37
3.8.3На соединении и в журнале ( карта) контроля должны быть отражены участки швов, которые не могут быть проконтролированы из-за неудовлетворитель-
ного качества контактной поверхности или отсутствия доступа к ним.
3.8.4Подготовленные к контролю контактные поверхности непосрественно пе-
ред контролем необходимо тщательно протереть ветощью и покрыть слоем контактирующей жидкости ( минеральное масло, солидол, технический глицерин и другие контактные смазки).
4.ПРОВЕДЕНИЕ КОНТРОЛЯ
4.1Контроль проводят в два этапа, которые могут быть совмещены во време-
ни:
-этап поиска дефектов;
-этап оценки сомнительных сечений, в которых по результатам первого этапа
прилагается наличие дефектов.
4.2На этапе поиска дефектов преобразователь следует перемещать без особого усилия со скоростью не превышающей 10 мм/с, обеспечивая надёжный
акустический контакт и заданный шаг сканирования в соответствии с:
-табл. 3.3 и рис 3.3 ( для стыковых швов);
-табл. 3.9 и рис 3.7 ( для тавровых соедингений).
При сканировании следует располагать преобразователь перпендикулярно к шву и в процессе перемещения, соблюдая шаг сканирования, систематически поворачивая его в обе стороны на 10….15º.
Для выявления дефектов, расположенных у торцов в стыковых и тавровых со-
единениях, следует дополнительно прозвучивать зону у каждого торца, постепенно
поворачивая преобразователь в пределах до 45º между торцов соединения и плос-
костью падения волны.
В случае обнаружения дефекта в стыковом соединении проводится проверка на наличие поперечной трещины, для чего преобразователь поворачивается таким образом, чтобы плоскость падения волны составляла с продольной осью шва угол
10…40º.
4.3Признаком обнаружения дефекта при контроле является наличие на экране сигнала:
а) находящегося в пределах установленной зоны временной селекции (стро-
бирования);
38

б) превышающего уровень чувствительности поиска; в) вызывающего срабатывание:
-светового индикатора ( загорание зелёной или жёлтой ламп АСД);
- |
звукового индикатора ( если на блоке А10 нажата кнопка |
|
|
и горит зелё- |
|
|
|||
|
|
|
|
|
|
ная лампа (АСД); |
|
||
|
|
|||
П р и м е ч а н и е - Для контролируемых толщин свыше 20 мм, при необходи- |
||||
мости ( сложность ремонта или контроль особо ответственного соединения), |
||||
превышение сигналов от дефекта уровня чувствительности поиска уточняется |
||||
в соответствии с приложением 2 после определения коэффициента выявляе- |
||||
мости дефекта ( п. 4.5.3) и глубины его расположения ( п. 4.5.1). |
|
|||
г) перемещающегося по развертке при поперечном сканировании преобразова- |
||||
телем. |
|
|
|
|
4.4 |
Любым из индикаторов дефектоскопа могут быть зафиксированы также |
импульсы помех, обусловленные следующими причинами:
-неровностями на околошовной поверхности и валике шва; -подрезами допустимой величины;
- резкими переходами валика шва в основной металл; шумами из призмы преобразователя.
Импульсы шумов преобразователя отличаются от других импульсов тем, что располагаются в начале развертки и не перемещаются по ней при движении преоб-
разователя.
Для того, чтобы отличить импульсы помех от импульсов, вызванных дефектами, следует определить координаты отражающей поверхности. Импульсы относят к помехам, если координаты отражающей поверхности совпадают с поверхностью соединения.
4.5 Зафиксированные на этапе поиска по признакам, изложенным в п. 2.4.3, сечения должны быть отмечены на соединении и повторно проконтролированы с целью:
-уточнения координат дефекта ( глубина расположения У и расстояние Х от точки ввода луча до проекции дефекта на контактную поверхность) в миллиметрах; -изменения амплитуды эхо-сигнала от дефекта Nд в децибелах и определения
коэффициента выяляемости дефекта Кд в децибелах;
-изменения условной протяжённости дефекта Lд в миллиметрах;
- изменение условного расстояния L между рядом расположенными дефектами в миллиметрах.
39

П р и м е ч а н и е - Условную протяженность и условное расстояние между рядом расположенными измеряют для дефектов, амплитуды эхо-сигналов от кото-
рых превышают уровень поиска Кп, но не превышают уровень оценки Кo. 4.5.1.Координаты дефекта определяют:
- при установке преобразователя в положение максимальной амплитуды эхосигнала от дефекта ( при необходимости ослабления сигнала воспользоваться аттенюатором);
- при нахождении вершины отражённого сигнала на выбранном уровне
(см. п. 3.7.6,б);
-в соответствии с табл. 4.1
П р и м е ч а н и е - Если в стробе находится несколько сигналов, причем БЦО осуществляет измерения не для требуемого сигнала, следует воспользоваться
ручным стробированием ( регулятор на передней панели). В режиме измерений
с использованием ручного стробирования уровень второй развертки (если она
включена; п. 3.7.20) определяется первым непогашенным сигналом, превышающим две большие клетки снизу.
По окончании измерений:
а)восстановить исходную чувствительность, т.е. требуемое ослабление на ат-
тенюаторе №контр. (см.п.2.3.7.15,2);
б)отключить ( если применялось) ручное стробирование, для чего регулятор на
передней панели установить в исходное, крайнее левое положение.
Таблица 4.1
Определение координат дефекта
Координата Х
непосредственно по показанию БЦО: Х= Х БЦО m= 0 непосредственно по показанию БЦО: У=У БЦО
Координата У m=1 с учетом значения контролируемой толщины δ и показания БЦО У БЦО по выражению У= 2δ - У БЦО
4.5.2 Амплитуду эхо-сигнала от дефекта Ν д определяют:
-при установке преобразователя в положение максимума (при необходимости ослабления сигнала воспользоваться аттенюатором);
-при нахождении вершины отражаемого сигнала в пределах экрана что соот-
ветствует показанию БЦО 0,1…..20 дБ;
40
-по выражению ( с учетом знака) Nд = NдКН - NдБЦО, используя измеренные значения NдКН и NдБЦО .
П р и м е ч а н и е - Если в стробе находится несколько сигналов, причем БЦО осуществляет измерения не для требуемого сигнала, следует:
-добиться, чтобы вершина анализируемого сигнала находилась выше уровня двух больших клеток снизу по экрану ЭЛТ;
-воспользоваться ручным стробированием (регулятор на передней панели).
В режиме измерений с использованием ручного стробирования уровень второй развертки ( если она включена: п. 3.7.20) определяется первым непогашенным
сигналом, превышающим две большие клетки снизу. По окончании измерений:
а) восстановить исходную чувствительность, т.е. требуемое ослабление на ат-
тенюаторе Nконтр. кн ( см. п. 3.7.15, б);
б)отключить ( если применялось) ручное стробирование, для чего регулятор на
передней панели установить в исходное, крайнее левое положение. 4.5.3.Коэффициент выявляемости дефекта определяют относительно: -соответствующего эталонного отражателя ( отражателя, по которому произво-
дилась настройка чувствительности для данного случая контроля) на испытательном образце – при контроле соединений листов толщиной 10…20 мм;
-эталонного отражателя в стандартном образце СО-2 |
( диаметром 6 мм на |
|
глубине 44 мм) – при контроле соединений листов толщиной более 20 мм. |
||
Коэффициент выявляемости дефекта с учетом знака |
определяют по выраже- |
|
нию |
|
|
Кд = Nд – No , |
(1) |
|
где Nд – максимальная амплитуда эхо-сигнала от дефекта
(определена согласно п. 4.5.2);
Nомаксимальная амплитуда эхо-сигнала от эталлонного отражателя (определена согласно п. 3.7.14, г).
2.4.5.4Условную протяженность Lд измеряют между крайними положениями
преобразователя, перемещаемого вдоль сварочного соединения, при которых ам-
плитуда эхосигнала от дефекта соответствует уровню чувствительности поиска Кп,
т.е. погасанию ( на пороге) зелёной лампы АСД (рис. 4.1).
2.4.5.5Условное расстояние между рядом расположенными дефектами l из-
меряют как расстояние между крайними положениями преобразователя соответст-
вующими (рис. 4.1):
41

- |
измерению условной протяженности дефекта, если условная протяженность |
|
этого дефекта Lд > 10 мм; |
|
|
- |
максимуму эхо-сигнала от дефекта, если |
условная протяжённость |
Lд < 10мм. |
|
Рисунок 4.1 Схема измерения условной протяжённости дефекта Lд
и условного расстояния l между рядом расположенными дефектами
42
5 ОЦЕНКА КАЧЕСТВА ШВОВ СВАРНЫХ СОЕДИНЕНИЙ
5.1 Основными измеряемыми характеристиками выявленных дефектов являются:
а) коэффициент выявляемости К д;
б)условная протяженность Lд;
в)условное расстояние между дефектами l;
г) координаты дефекта Х и У в сечении шва с учётом типа и размеров соедине-
ния;
д) число К дефектов на участке шва длиной 400 мм.
5.2По результатам ультразвукового контроля качества среднего шва оценивают по системе:
- «годен»;
- «не годен»;
- «условно годен».
«Годным» считают шов без дефектов или с допустимыми дефектами. «Негодным» считают шов с недопустимыми дефектами; «Условно годным» считают шов с возможно допустимыми дефектами ( кото-
рые нельзя однозначно отнести к допустимым или недопустимым); такой шов дол-
жен быть подвергнут дополнительному контролю для уточнения характера и разме-
ров дефектов. При невозможности дополнительного контроля его относят к категории « не годен».
5.3К недопустимым дефектам в сварных швах относят:
1)любой дефект, максимальная амплитуда эхо-сигнала от которого превышает уровень оценки ( п. 4.3, в);
2)любой дефект, для которого ( одновременно):
- максимальная амплитуда эхо-сигнала превышает уровень поиска и не пре-
вышает уровень оценки;
- условная протяженность превышает заданное значение Lд* (табл. 5.1);
3)любые два дефекта, для которых ( одновременно):
-максимальная амплитуда эхо-сигналов ( для каждого) превышает уровень
поиска и не превышает уровень оценки;
-условная протяжённость (для каждого) не превышает значение Lд*
(табл.5.1);
43
- условное расстояние между дефектами меньше заданного значения l*
(табл.5.1);
4)любые дефекты, для которых (одновременно):
максимальная амплитуда эхо-сигналов ( для каждого) превышает уровень по-
иска и не превышает уровень оценки;
условная протяженность (для каждого) не превышает значения Lд* (табл.5.1); условное расстояние между соседними дефектами больше заданного
значения l *, ( табл. 5.1);
количество дефектов на участках шва длиной 400 мм превышает заданное значение К* ( табл. 5.1);
5) любой дефект, для которого (одновременно):
максимальная амплитуда эхо-сигнала превышает уровень поиска и не превышает уровень оценки,
при обнаружении дефекта акустическая ось преобразователя расположена под
углом 10….40º к продольной оси шва.
Схематически указанный алгоритм приведен в приложении 3.
5.4.К возможно допустимым относят дефекты, для которых ( одновременно): -амплитуда эхо-сигналов превышает уровень чувствительности поиска
( п. 4.3, в);
-не выполняются требования п. 5.3.
Для таких дефектов необходимо уточнить их конфигурацию с использованием дополнительных характеристик выявленного дефекта или методом просвечивания.
Если по результатам оценки конфигурации возможно допустимого дефекта установлено, что он плоскостной, его относят к недопустимым.
Если по результатам оценки конфигурации возможно допустимого дефекта ус-
тановлено, что он объёмный, его относят к допустимым.
При невозможности оценки конфигурации возможно допустимого дефекта его
относят к недопустимым.
5.5. К допустимым дефектам относят:
-отражатели, амплитуда эхо-сигналов от которых, не превышает уровень чувствительности поиска ( т.е. не вызывает срабатывание ламп АСД; для более точного
анализа – см. приложение 2 );
-возможно допустимые объёмные дефекты ( см. п. 5.4).
44