
i-141823804
.pdf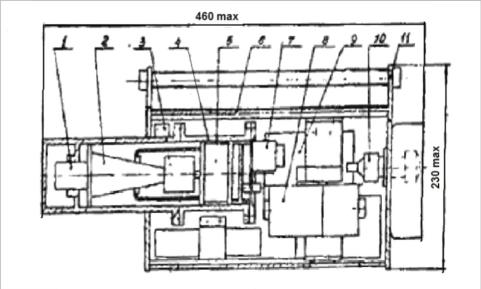
Время заряда конденсатора С5, а, следовательно, и время экспозиции зависит от величины сопротивления одного из резисторов R7...R10, R12, которое выбирается с помощью кнопочного переключателя S4 ВЫДЕРЖКА.
Для защиты аппарата от случайного включения предусмотрен тумблер S1, соединенный с замком безопасности. Неоновые лампы V1, V8 сигнализируют о включении аппарата в сеть и о его запуске.
Конструктивно аппарат состоит из 3 частей: рентгеновского блока, настольного пульта управления, высоковольтного кабеля, соединяющего пульт с рентгеновским блоком.
В рентгеновском блоке (рис.1.3) расположен высоковольтный блок, в который входят: рентгеновская трубка 1, катушка индуктивности 2, раз- рядник-обостритель 3, импульсный трансформатор 5, объединенные металлическим корпусом 4. Кроме того, в рентгеновском блоке расположены накопительные конденсаторы 9 и первичный зарядник 8, закрытые кожухом 6. Маслорасширитель 7 предназначен для компенсации избыточного давления в высоковольтном блоке при колебаниях температуры. На задней стенке 11 расположен высоковольтный разъем 10.
Рис. 1.3. Блок рентгеновский
В пульте управления находится зарядный трансформатор, схема удваивания напряжения, реле времени, цепи управления аппаратом и контроля его работы.
4.4. Радиографические пленки и усиливающие экраны
Радиографические пленки являются основным средством регистрации прошедшего ионизирующего излучения. По свойствам и назначению выпускаемые рентгеновские пленки подразделяются на две группы: безэ-
11
кранные для использования без флуоресцентных экранов или с металлическими усиливающими экранами и экранные пленки с использованием флуоресцентных усиливающих экранов. К первой группе относятся пленки типа РТ-5, РТ-4, РТ-3, РТ-1; ко второй группе – РТ-2, РМ-1, РМ-2, РМ-3.
Усиливающие металлические и флуоресцентные экраны применяют для сокращения времени просвечивания. Усиливающее действие экранов характеризуется коэффициентом усиления, определяемым отношением времени просвечивания без экрана к времени просвечивания с экраном.
Усиливающее действие металлических экранов основано на освобождении из них вторичных электронов под воздействием ионизирующего излучения. Освобожденные электроны действуют на эмульсию пленки и вызывают дополнительную фотохимическую реакцию, усиливающую влияние первичного излучения. Металлические экраны рекомендуют применять с безэкранными пленками.
Усиливающее действие флуоресцентных экранов обусловлено дополнительным влиянием на пленку свечения, возникающего в люминофоре от рентгеновского излучения. Эти экраны выполняются в виде пластмассовых или картонных подложек, на которые наносится слой люминофора. Их рекомендуется использовать с экранными пленками. Применение экранов позволяет снизить время экспозиции в 2-5 раз. Металлические экраны снижают время экспозиции в 2-3 раза и одновременно повышают чувствительность, поэтому они нашли более широкое применение, чем флуоресцентные экраны.
Для определения относительной чувствительности радиографического контроля используют специальные эталоны. Эталон представляет собой пластину с идеальными дефектами, контуры которых резко очерчены. Наиболее часто применяют канавочные и проволочные эталоны четырех типоразмеров каждый. На границе искусственных дефектов эталона происходит резкое изменение суммарной толщины просвечиваемого материала, в тот время как реальный дефект дает постепенное изменение толщины на границе «дефект – бездефектная зона».
Кроме того, реальные дефекты часто рассредоточены и имеют неправильные очертания. Вследствие этого поры или шлаковые включения, диаметры которых равны соответственно высоте прорези или диаметру проволоки, могут быть не выявлены, несмотря на то, что изображения искусственных дефектов в эталоне четко видны.
В практике промышленной радиографии применяют гибкие и, реже, жесткие кассеты. Гибкая кассета представляет собой двойной конверт из черной светонепроницаемой бумаги или дерматина. С целью маркировки изделия по участкам контроля применяют свинцовые маркировочные знаки, которые размещают на изделии или в кассете. После просвечивания их изображение остается на снимке.
12
4.5. Просвечивание изделия и фотообработка снимков
Перед контролем изделие должно быть очищено от шлака, пыли и других загрязнений. Сварное соединение разбивают на участки контроля, которые маркируют, с тем, чтобы после просвечивания можно было точно указать расположение выявленных внутренних дефектов. Кассету с пленкой укрепляют на изделии, а со стороны источника излучения устанавливают эталон чувствительности.
При просвечивании источник излучения необходимо установить таким образом, чтобы во время просвечивания он не мог вибрировать или сдвигаться с места, иначе изображение на пленке окажется размытым.
По истечении времени просвечивания кассеты с пленкой снимают и экспонированную пленку подвергают фотообработке.
Процесс фотообработки пленки включает следующие операции: проявление, промежуточную промывку, фиксирование изображения, промывку в непроточной воде, окончательную промывку и сушку пленки.
4.6. Оценка размеров дефекта по рентгеновскому снимку и их обозначение
Расшифровка снимков – наиболее ответственный этап в проведении работ. Задача расшифровщика состоит в выявлении дефектов, установление их видов и размеров.
Установление размера дефекта в плоскости, перпендикулярной направлению просвечивания, не представляет затруднения. Определение вертикального размера дефекта более сложно и производится по степени потемнения снимка. Для этого вместе с изделием просвечивается эталон чувствительности. В качестве эталона может применяться пластинка с канавками различной глубины.
От каждой канавки на снимке остается полоска, степень потемнения которой пропорциональна глубине канавки. Рассматривая снимок, выявляют, какой из канавок соответствует степень потемнения пленки в месте дефекта, и, зная ее глубину, определяют вертикальный размер дефекта.
Для сокращения записи результатов контроля применяют сокращенные обозначения обнаруженных на снимке дефектов: Т – трещины; Н – непровар; П – поры; Ш – шлаковые включения; В – вольфрамовые включения; Пд – подрез; См – смещение кромок; Р – разностенность; О – ослабление корня шва.
Рассмотрим пример. На изображении участка сварного соединения С5 ГОСТ 5264-80 чувствительностью 3% и длиной 300 мм выявлены две трещины длиной по 5 мм, непровар длиной 120 мм, четыре отдельных шлаковых включения размером по 3 мм и одна цепочка пор длиной 25 мм. Запись в заключении: С5, 3, 300, 2Т-5, Н-120, 4Ш-3, ЦП-25.
13
5. Порядок выполнения работы
После ознакомления с теоретической частью работы проконтролировать образцы с дефектами сварки на установке РИНА-1Д.
Установить кнопочным переключателем ВЫДЕРЖКА необходимое время экспозиции.
Вставить ключ в замок безопасности и повернуть по часовой стрелке до щелчка, обозначающего, что сработал тумблер, после чего нажать кнопку СЕТЬ. Должна загореться неоновая лампа.
Нажать кнопку ПУСК. Должна загореться неоновая лампа запуска. Во избежание перегрева зарядного трансформатора в пульте управ-
ления и выхода его из строя необходимо, чтобы суммарное время наработки в час не превышало 6 минут.
Время экспозиции, фокусное расстояние, тип рентгеновской пленки и усиливающих экранов должны выбираться потребителем, исходя из конкретных требований, предъявленных к качеству рентгенографического контроля, в соответствии с нормативно-техническими документами.
При использовании рентгеновской пленки типа РМ-1, РТ-2 с флуоресцентными усиливающими экранами рекомендуется выбирать фокусное расстояние 660-1000 мм. При этом толщина стальных изделий, доступная для контроля, составляет 20-25 мм, время экспозиции – порядка 3-5 минут, а чувствительность получаемых рентгенограмм – 3-4%.
При работе с безэкранной пленкой типа РТ-1, в комбинации со свинцовой фольгой рекомендуемая толщина стальных изделий – 10 мм, а фокусное расстояние – 200-300 мм, время экспозиции – 6 минут. В этом случае чувствительность получаемых рентгенограмм 2-2,5%.
Обработать пленку после просвечивания.
Оценить и расшифровать снимки сварных швов, выполнить запись результатов контроля.
6. Содержание отчета
Краткие сведения о сущности рентгеновского метода контроля, техническая характеристика и краткое описание импульсного рентгеновского аппарата.
Эскиз пленки с дефектами сварки и запись результатов контроля.
Контрольные вопросы
1.В чем заключается принцип рентгеновского метода контроля?
2.Пояснить устройство рентгеновского аппарата.
3.С какой целью применяются усиливающие экраны?
4.Как оценить чувствительность рентгеновского метода контроля?
14
5.Каковы правила техники безопасности при рентгеновском методе контроля?
6.Как обозначаются дефекты на рентгеновском снимке?
7.Как осуществляется процесс фотообработки пленки?
Список литературы
1. Сварка. Резка. Контроль : справочник : в 2 т. / Н. П. Алешин, Г. Г. Чернышов, Э. А. Гладков и др. ; ред. : Н. П. Алешин, Г. Г. Чернышев. – М. : Машино-
строение, 2004. – 619 с.
2. Сварка. Резка. Контроль : справочник : в 2 т. / Н. П. Алешин, Г. Г. Чернышов, А. И. Акулов ; ред. Н. П. Алешин, Г. Г. Чернышев. – М. : Машино-
строение, 2004. – 478 с.
3. Лукьянов, В. Ф. Изготовление сварных конструкций в заводских условиях / В. Ф. Лукьянов, В. Я. Харченко, Ю. Г. Людмирский. – Электрон. текстовые дан. (7,32 Мб.). – Ростов-н/Д: Феникс, 2009. – 315 с.
4. |
Алешин, Н. П. Контроль качества сварочных работ / Н. П. Алешин, |
Г. В. Щербинский. – М. : Высш. шк., 1981. |
|
5. |
Контроль качества сварки / под ред. В. Н. Волченко. – М. : Машиностроение, |
1975. |
|
15
Лабораторная работа 2
ЛЮМИНЕСЦЕНТНЫЙ И ЦВЕТНОЙ МЕТОДЫ ДЕФЕКТОСКОПИИ СВАРНЫХ СОЕДИНЕНИЙ
1.Цель работы: Освоить технику люминесцентного и цветного методов контроля сварных соединений.
2.Техника безопасности и противопожарные мероприятия
при выполнении лабораторной работы
При люминесцентном и цветном методах контроля сварных соединений студенты пользуются источниками ультрафиолетовых лучей, а также легковоспламеняемыми веществами. Поэтому нужно знать и строго выполнять установленные правила техники безопасности и противопожарные мероприятия.
2.1.При испытании сварных швов керосином следует помнить, что пары керосина с воздухом дают взрывоопасные смеси, а поэтому во время испытания нельзя пользоваться открытым огнем!
Должно быть организовано надежное хранение керосина. Для этого хранить керосин следует в лабораторном шкафу в сосуде объемом не более 0,5 л. После отбора керосина в мензурку объемом 5-10 мл, необходимого для опытов, сосуд загерметизировать пробкой, поставить в шкаф и замкнуть последний.
2.2.Аналогично обращаться и с другими воспламеняющимися веществами, которыми пользуются студенты при изготовлении проникающих жидкостей для люминесцентного и цветных методов контроля: трансформаторным маслом, бензином, скипидаром.
2.3.При люминесцентном методе контроля для предохранения глаз от действия ультрафиолетового излучения необходимо надеть защитные очки.
3. Физическая сущность процессов
Физическая сущность люминесцентного и цветного методов контроля состоит в использовании явления проникновения хорошо смачивающей жидкости в трещины, поры и другие поверхностные дефекты сварных соединений, и на свойстве их флюоресцирования (свечения) под действием ультрафиолетовых лучей (УФЛ) или дневного света.
Процесс проникновения жидкостей в трещины, поры, дефекты швов можно выразить в общем виде формулой:
|
|
|
γ |
|
|
|
= √ ∙ cos θ ∙ √ |
, |
(1) |
||||
2η |
||||||
|
|
|
|
|
||
16 |
|
|
|
|

где l – расстояние, проходимое жидкостью по трещине, пузырькам и тому подобным дефектам в течение времени t; γ – поверхностное натяже-
ние; η – вязкость жидкости; θ – угол смачивания; √2ηγ – коэффициент
проникновения; чем больше его величина, тем больше скорость проникновения.
По этой же формуле можно определить и время, необходимое для проникновения жидкости на заданную глубину.
Проникновение жидкости в дефекты ухудшается при наличии в них загрязнений, а также воздуха, который сжимается под действием проникающей жидкости, например, в трещине, до высоких давлений. Таким образом, выявляемость дефектов люминесцентным методом во многом зависит от чистоты поверхности и свойств люминесцирующей жидкости.
Практическое проведение контроля обусловлено выполнением требований, указанных далее.
Поверхность исследуемого шва изделий больших размеров очищают от загрязнений и на чистую поверхность наносят флуоресцирующую жидкость. Для получения высокой чувствительности метода к выявлению дефектов важно иметь жидкость, обладающую хорошей смачивающей способностью и интенсивным свечением при освещении ее ультрафиолетовыми лучами. При приготовлении раствора дефектоль растворяют в бензине, затем доливают керосин, а потом масло.
Под действием ультрафиолетовых лучей флуоресцирующий раствор ярко светится желто-зеленым светом с голубым оттенком. Состав жидкости №1 светится в УФЛ синевато-белым свечением. Высокая чувствительность этого метода позволяет выявить дефекты шириной до 0,01 мм и глубиной до 0,03-0,04 мм. Она дает возможность применять его для выявления трещин в околошовной зоне многих сварных соединений, особенно немагнитных сталей и швов цветных металлов и сплавов.
4. Люминесцентный метод контроля
Преимущества люминесцентного метода следующие: простота аппаратуры; возможность контроля любых материалов – металлов, керамики, пластмассы и т.п.; низкая стоимость контроля и высокая его производительность.
Общая схема люминесцентного метода обнаружения поверхностных дефектов приведена на рис. 2.1.
17
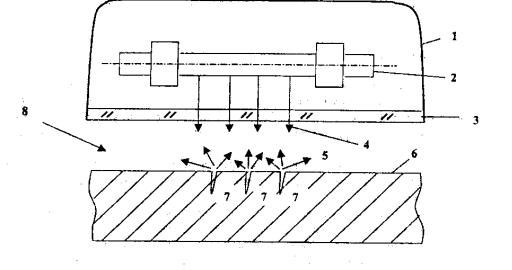
Рис. 2.1. Схема люминесцентного метода обнаружения дефектов:
1 – рефлектор; 2 – ртутно-кварцевая лампа; 3 – светофильтр, пропускающий УФЛ; 4 – пучок УФЛ; 5 – поток люминесценции от находящихся в плоскости дефектов; 6, 7 – поверхностные дефекты; 8 – направление осмотра
В качестве проникающей и светящейся жидкости применяют следующие составы:
– 15% трансформаторного масла и 85% керосина, где масло является светящейся жидкостью;
– 50% керосина, 25% бензина, 25% трансформаторного масла и 0,02–0,03% флуоресцирующего вещества – дефектоля.
Дефектоль представляет собой концентрат, который дает яркое жел- то-зеленое свечение при ультрафиолетовом облучении и тем самым улучшает выявляемость дефектов.
В качестве оборудования для контроля применяются люминесцентные дефектоскопы, как, например, ЛА-2, ЛКМ-7, Л-84.
Для получения ультрафиолетовых лучей применяют ртутные и ртут- но-кварцевые лампы различных типов (например, ПРК-7, СВД-420а и др.). Ртутные лампы излучают не только ультрафиолетовый свет, но и видимый инфракрасный. Для выделения ультрафиолетовых лучей и погашения остальных применяются специальные стеклянные светофильтры, изготовленные из увиолевого силикатного или фосфатного стекла, в состав которого вводятся окиси кобальта и никеля (например, стекла УФС-3, УФС-4).
Нужно помнить, что ультрафиолетовые лучи вредно действуют на глаза и кожу, вызывая их воспаление. Поэтому кожух при работе ртутной лампы должен быть герметичным и не пропускать УФЛ в нерабочую зону.
5. Цветной метод
Этот метод применяется также для выявления трещин и других дефектов сварки, выходящих на поверхность шва. В отличие от люминес-
18
центного метода, где для рассмотрения дефектов швов необходимы ультрафиолетовый свет и затемнение, при цветном методе контроля никакой аппаратуры не требуется.
Сущность цветного метода состоит в том, что на очищенную от грязи поверхность контролируемого изделия наносят слой подкрашенной проникающей жидкости. Жидкость – краска, наносится за три-четыре приема для лучшего проникновения ее в мельчайшие дефекты. Время выдержки для проникновения краски в дефекты составляет 10-15 мин.
После покрытия краской поверхность изделия промывается 5% водным раствором кальцинированной соды и просушивается. Далее на просушенную поверхность сварного шва пульверизатором для проверки наносят тонкий слой суспензии – раствора (на 1 дм3 воды 400-500 г каолина).
Вместо каолина может быть применен сухой, тонко помолотый мел. Выделявшаяся из дефектов жидкость окрашивает каолин или мел в красный цвет. Для ускорения выделения жидкости поверхность просушивают теплым воздухом или рефлектором.
Из многочисленных существующих рецептов на проникающую жидкость наибольшее применение нашла краска следующего состава: 20% скипидара, 80% керосина, 10 г краски «Судан-4» на 1 дм3/л жидкости.
Чувствительность метода краски примерно такая же, как чувствительность люминесцентного метода. Цветной метод контроля дает хорошие результаты при выявлении дефектов в сварных швах из алюминия, титана, нержавеющих сталей и других металлов и сплавов. Кроме выявления дефектов сварки плавлением цветной метод используется для выявления межкристаллитной коррозии.
Цветной метод является хорошим дополнением к другим физическим методам контроля: рентгеновскому и ультразвуковому для выявления дефектов, имеющих размеры за пределами чувствительности. К цветному методу можно условно отнести и контроль на непроницаемость керосином.
Практически, для обнаружения неплотности швов, их покрывают меловой краской со стороны, доступной для осмотра и высыхания меловой краски. Обратная сторона швов смачивается керосином или на шов накладывается ткань, пропитанная керосином, и выдерживается необходимое по расчету время от 15 до 60 мин. Керосин проходит сквозь дефекты в шве и выступает на окрашенные мелом поверхности в виде ржавых пятен и полос, и тем самым выявляет дефектные участки шва. Если на поверхности шва в течение короткого времени не обнаруживается пятен от керосина, то сварное соединение считается выдержавшим испытание. Керосиновой пробе подвергаются главным образом сосуды и изделия, предназначенные для хранения жидкостей.
19
6.Оборудование и материалы, необходимые для выполнения работы
1.Ультрафиолетовый осветитель.
2.Рефлектор или электроплитка.
3.Набор дефектных сварных швов.
4.Кисточки.
5.Шторы для затемнения ультрафиолетового осветителя.
6.Обтирочный материал.
7.Набор веществ для составления красок и люминофора: а) керосин, б) бензин,
в) трансформаторное масло, г) зелено-золотистый дефектоль, д) скипидар, ж) краска «Судан-4»,
з) каолин или мел.
8.Кальцинированная сода.
7. Порядок выполнения работы
7.1. Определение дефектов в сварных швах люминесцентным методом (1-я часть)
1.Ознакомиться с устройством ультрафиолетового осветителя.
2.Составить и приготовить флюоресцирующий состав (люминофор).
3.Тщательно очистить от загрязнений поверхность сварных швов и околошовной зоны.
4.При помощи распылителя или кисточки нанести люминофор на поверхность швов и околошовной зоны образца, подогретого до температуры 60-70 .
5.Дать остыть образцу и выдержать 15-20 мин для проникновения люминофора в трещины.
6.Тщательно протереть шов и подсушить его под рефлектором.
7.Рассмотреть поверхность шва в затемненном месте при освещении ультрафиолетовым светом.
8.Замерить размеры обнаруженных трещин, зарисовать поверхность шва и отметить места расположения дефектов.
9.Составить заключение о качестве швов.
Содержание отчета по первой части работы
В отчете следует описать устройство люминесцентного осветителя, изложить технику контроля, выполнить необходимые зарисовки и сделать собственные выводы по качеству сварного шва.
20