
i-141823804
.pdf7.2. Определение дефектов в сварных швах цветным методом (2-я часть работы)
1.Составить по соответствующему рецепту и тщательно размешать
краску.
2.Зачистить поверхность сварных швов и околошовной зоны и протереть их бензином.
3.При помощи кисточки нанести на контролируемую поверхность тонкий слой жидкости – краски.
4.Промыть поверхность 5%-ным раствором кальцинированной соды.
5.Протереть поверхность насухо.
6.При помощи пульверизатора нанести на поверхность тонкий слой раствора в воде каолина или мела.
7.Просушить поверхность рефлектором.
8.Рассмотреть контролируемый шов, выявить дефекты и замерить их, зарисовать поверхность шва и отметить места расположения дефектов.
9.Составить заключение о качестве шва.
Содержание отчета второй части работы
В отчете следует описать технику контроля цветным методом. Выполнить необходимые зарисовки и сделать выводы по качеству сварного шва.
7.3. Испытание плотности сварных соединений керосином (3-я часть работы)
1.Развести молотый мел в воде до густоты побелки.
2.Процедить раствор через мелкое сито или марлю.
3.Зачистить поверхность шва до металлического блеска.
4.При помощи кисточки нанести меловой раствор на одну сторону шва.
5.Просушить шов рефлектором или электрической плиткой.
6.При помощи тряпки или кисточки (лучше пульверизатором) смочить керосином обратную сторону шва.
7.Выдержать 15-20 мин, в течение которых следить за появлением пятен (ржавых) и делать отметки мелом обнаруженных дефектных участков.
8.Зарисовать шов и отметить на нем места расположения дефектов.
9.По окончании испытания промыть шов водой и протереть тряпкой или просушить.
Содержание отчета по третьей части работы
В отчете должна быть описана методика контроля сварных швов керосином и проведены зарисовки швов с указанием обнаруженных мест.
21
Контрольные вопросы
1.В чем состоит сущность испытания люминесцентным, цветным методом, а также керосином?
2.Указать области рационального применения названных методов.
3.Привести составы люминофоров и красок.
4.Как устроен люминесцентный осветитель?
5.Каково назначение светофильтров?
6.Пояснить недостатки и преимущества рассмотренных методов контроля сварных соединений.
Список литературы
1. Сварка. Резка. Контроль : справочник : в 2 т. / Н. П. Алешин, Г. Г. Чернышов, Э. А. Гладков и др. ; ред. : Н. П. Алешин, Г. Г. Чернышев. – М. : Машино-
строение, 2004. – 619 с.
2. Сварка. Резка. Контроль : справочник : в 2 т. / Н. П. Алешин, Г. Г. Чернышов, А. И. Акулов ; ред. Н. П. Алешин, Г. Г. Чернышев. – М. : Машино-
строение, 2004. – 478 с.
3. Лукьянов, В. Ф. Изготовление сварных конструкций в заводских условиях / В. Ф. Лукьянов, В. Я. Харченко, Ю. Г. Людмирский. – Электрон. текстовые дан. (7,32 Мб.). – Ростов-н/Д: Феникс, 2009. – 315 с.
4. Алешин, Н. П. Контроль качества сварочных работ / Н. П. Алешин, Г. В. Щербинский. – М. : Высш. шк., 1981.
5. Контроль качества сварки / под ред. В. Н. Волченко. – М. : Машиностроение,
1975.
22
Лабораторная работа 3
КОНТРОЛЬ СВАРНЫХ СОЕДИНЕНИЙ МАГНИТОПОРОШКОВЫМ МЕТОДОМ
1.Цель работы: Ознакомиться с методикой и аппаратурой для магнитопорошкового контроля сварных соединений. Приобрести навыки по контролю сварных соединений магнитопорошковым методом.
2.Техника безопасности
а) при включении соленоида в сеть переменного тока напряжением 220 В следить за состоянием изоляции;
б) источник питания постоянного тока следует надежно заземлить; в) под суспензию, стекающую с детали, необходимо подставлять ванночку; г) при работе запрещается пользоваться источником открытого огня.
3. Оборудование и материалы
а) магнитный передвижной дефектоскоп 77ПМД-3м; б) источник питания постоянного тока напряжением 24 В; в) образцы сварных соединений с дефектами сварки; г) бачок с магнитной суспензией; д) сухой порошок;
е) ванночка с суспензией и ванночка для слива суспензии с детали; ж) чистая ветошь.
4. Физическая сущность метода контроля деталей магнитной суспензией
Метод контроля деталей магнитной суспензией принадлежит к физическим методам, позволяющим проверять качество стальных (ферромагнитных) деталей без их разрушения или повреждения. Метод основан на использовании явления возникновения на поверхности детали в местах, где находятся дефекты (трещины различного происхождения, несплавления, непровары, шлаковые включения, поры и т.д.) магнитного потока. Образование поля рассеяния при прохождении через деталь магнитного потока происходит в связи с резким изменением магнитной проницаемости в местах наличия дефекта. На рис. 3.1 показана схема образования магнитного поля рассеяния над поверхностной трещиной детали.
Силовые линии магнитного потока, проходящего через деталь, при встрече дефекта огибают его. Если дефект выходит на поверхность или расположен неглубоко, то силовые линии выходят за пределы детали, образуя местное магнитное поле рассеяния. Достаточно обнаружить на поверхности проверяемой детали каким-либо способом такое поле, чтобы установить наличие в этом месте дефекта.
23
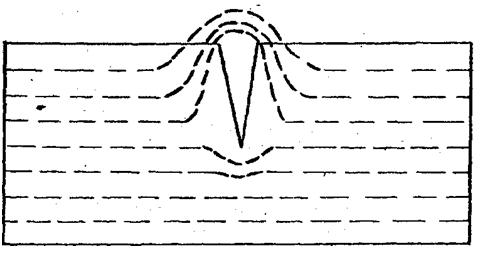
Рис. 3.1. Схема образования магнитного поля над трещиной
Для выявления поля рассеяния при магнитной дефектоскопии применяют ферромагнитный порошок. При этом намагниченную деталь обливают магнитной суспензией – жидкостью (керосином), в которой мелкие частицы ферромагнитного порошка находятся во взвешенном состоянии. Эти частицы, попав в поле рассеяния, намагничиваются и притягиваются к краям дефекта (трещины) как к полюсам магнита. Собираясь над дефектами, они образуют на поверхности детали остаток порошка в виде "жилки", ширина которой может достигать 100-кратной ширины трещины. По этому оседанию порошка определяют наличие, форму и месторасположение дефекта, а во многих случаях – и характер его (трещина, непровар, шлаковое включение).
Напряженность магнитного поля рассеяния, образующегося над дефектами, оказывает большое влияние на чувствительность метода контроля деталей магнитной суспензией. Чем интенсивнее поле рассеяния, тем отчетливее получается рисунок осевшего порошка. Напряженность магнитного поля рассеяния определяют, в основном, следующие факторы:
а) напряженность магнитного поля, которым намагничивается деталь. Чем она больше, тем сильнее поле рассеяния, образующееся над дефектными местами;
б) расположение дефекта в детали по отношению к силовым линиям намагничивающего поля. Если дефект расположен вдоль силовых линий намагничивающего поля, то магнитное поле рассеяния совершенно не образуется. Его возникновение имеет место только тогда, когда угол между направлением дефекта и силовыми линиями больше 30°. Наиболее сильное поле рассеяния получается в том случае, когда дефект расположен перпендикулярно к силовым линиям намагничивающего поля;
в) характер дефекта, его форма, величина и глубина залегания. Чем глубже залегает дефект, не выходящий на поверхность детали, тем слабее
24
вызываемое им поле рассеяния при данном намагничивающем поле. Когда дефект детали является внешним и имеет значительно большую глубину по сравнению с шириной, то получается сильное поле рассеяния. Над дефектами округленной формы оно сравнительно слабее.
5. Назначение, основные данные переносного магнитного дефектоскопа 77ПМД-3м
Переносной магнитный дефектоскоп 77ПМД-3м представляет собой универсальный аппарат, позволяющий проводить магнитный контроль деталей и узлов при помощи электромагнита, соленоида и гибкого кабеля. Электромагнит и соленоид предназначены как для намагничивания, так и для размагничивания: гибкий кабель – только для намагничивания.
Для расширения области применения дефектоскопа электромагнит снабжен несколькими видами съемных полюсных наконечников, которые могут поворачиваться вокруг оси сердечника электромагнита. Сердечники, в свою очередь, могут перемещаться вдоль скалки и вокруг ее оси.
Дефектоскоп 77ПМД-3м позволяет контролировать:
а) цилиндрические детали диаметром 80-88 мм в электромагните, диаметром до 30 мм – в соленоиде (постоянным и переменным током), диаметром до 90 мм – в соленоиде (постоянным током). При использовании гибкого кабеля дефектоскоп позволяет контролировать сплошные цилиндрические детали диаметром до 90 мм и полые до 120 мм;
б) плоские детали и детали сложной формы шириной до 200 мм между плоскими гранями полюсных наконечников электромагнита.
Вследствие того, что контроль может производиться по отдельным участкам, длина деталей не ограничивает возможность контроля их дефектоскопом. Принципиальная электрическая схема переносного магнитного дефектоскопа 77ПМД-3м представлена на рис. 3.2.
Для подключения электромагнита Э1 или соленоида Э2 служат штепсельные гнезда. При пользовании электромагнитом его вилки должны включаться в гнезда с различными диаметрами. При пользовании соленоидом (вместо электромагнита) вилка должна быть включена в штепсельные гнезда меньшего диаметра, а переключатель В2 должен находиться в нейтральном положении (см. рис. 3.2).
Основной элемент схемы – переключатель В6. При вращении его рукоятки по часовой стрелке срабатывают кнопочные выключатели по порядку:
а) замыкаются нормально открытые контакты выключателя IV, при этом намагничивающую цепь шунтирует разрядное сопротивление;
б) замыкаются нормально открытые контакты выключателя III, при этом рвется цепь питания; дуга, возникающая при контактах, гасится конденсатором С, а энергия магнитного поля гасится разрядным сопротивлением R2, поэтому не происходит перенапряжения между витками катушек;
25
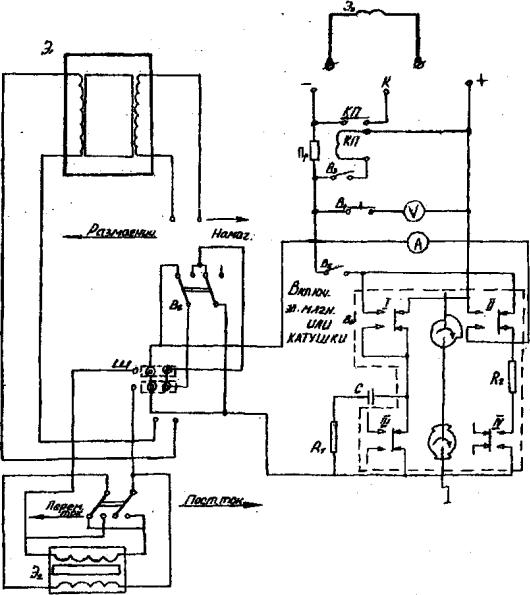
в) замыкаются нормально открытые контакты выключателя I;
г) замыкаются нормально закрытые контакты выключателей II, III и IV. При этом происходит переключение полярности питающего напряжения и замыкание цепи питания катушек. Конденсатор С разряжается через сопротивление R1. При повороте рукоятки переключателя на 180° происходят те же явления, но при этом направление тока в обмотках электромагнита или соленоида получается обратное предыдущему.
Рис. 3.2. Принципиальная электрическая схема переносного магнитного дефектоскопа 77ПМД-3м
При непрерывном вращении рукоятки переключателя электромагнит изменяет свою полярность, что необходимо при размагничивании деталей.
26
Выключатель В5 при этом должен быть замкнут, а обе обмотки электромагнита включены параллельно (переключатель В2 должен находиться в положении "Размагничивание").
6.Материалы для магнитной суспензии и способы контроля
Вкачестве материала для приготовления порошков в основном используют мелко помолотую закись-окись железа с размером частиц 5÷10 мкм. Иногда применяют чистую железную окалину, получаемую при ковке и прокатке, а также стальные опилки, образующиеся при шлифовании стальных изделий. Для лучшей индикации дефектов изделий различного цвета применяют цветные порошки. Для приготовления магнитных суспензий чаще всего используют мас- ляно-керосиновые смеси (соотношение масла и керосина 1:1), содержащие 50÷60 г порошка на 1 литр жидкости. Могут применяться и водные суспензии.
Существуют два основных способа контроля деталей с помощью магнитной суспензии:
а) контроль деталей на остаточном намагничивании. При этом способе детали предварительно намагничивают, а затем наносят на их поверхность суспензию;
б) контроль деталей в приложенном магнитном поле. В этом случае магнитную суспензию наносят на деталь в процессе намагничивания.
Намагничивание деталей производится следующими способами:
а) намагничивание в поле электромагнита. При этом деталь зажимается между полюсными наконечниками электромагнита, по обмоткам которого пропускается постоянный ток. При прохождении тока по обмоткам электромагнита между его полюсными наконечниками возникает магнитное поле, которым намагничивается зажатая деталь;
б) намагничивание в поле соленоида. Для этого деталь вводится внутрь соленоида. Этим полем намагничивается проверяемая деталь;
в) намагничивание гибким кабелем. В этом случае контролируемая деталь обматывается гибким кабелем (8÷10 витков), по которому пропускается постоянный ток.
Вприложенном магнитном поле можно проверять почти все детали, способные намагничиваться. Мелкие поверхностные и подповерхностные дефекты округленной формы также лучше выявляются в приложенном магнитном поле. К таким дефектам относятся трещины, непровары, шлаковые включения. Поверхностные дефекты выявляются, как правило, только в приложенном магнитном поле. При залегании дефектов на глубине более 2 мм они плохо поддаются выявлению (за исключением крупных) даже в поле сильного электромагнита.
Контроль деталей на остаточном намагничивании более прост и удобен, чем контроль в приложенном поле. В настоящее время он широко применяется для выявления поверхностных и приповерхностных дефектов на глубине 1-2 мм.
27
7. Содержание и порядок выполнения работы
7.1. Последовательность работы
Процесс магнитного контроля деталей дефектоскопом состоит из следующих операций:
1)подготовка образцов и дефектоскопов к контролю;
2)намагничивание образцов;
3)нанесение на поверхность образцов магнитной суспензии или порошка;
4)осмотр образцов и выявление дефектов;
5)размагничивание образцов;
6)очистка образцов.
Перед началом работы следует раскрыть чемодан дефектоскопа, вынуть из него намагничивающее устройство (электромагнит, соленоид или гибкий кабель, в зависимости от того, чем предполагается пользоваться) и расположить его возле чемодана. Взболтать суспензию в бачке и приготовить ванночку.
7.2. Намагничивание в поле электромагнита
При намагничивании деталей в поле электромагнита следует пользоваться постоянным напряжением 24 В. Детали при намагничивании этим способом проверяются в приложенном магнитном поле электромагнита.
Порядок операций при намагничивании следующий:
1)установить рукоятку коммутатора В6 в начальное положение (по риске на панели дефектоскопа);
2)установить переключатель В2 в положение, обозначенное "Намагничивание". При этом обе катушки электромагнита оказываются включенными последовательно. Если контроль детали требуется проводить в более сильном магнитном поле, то переключатель следует установить в положение "Размагничивание", при котором обе катушки оказываются включенными параллельно;
3)включить обе вилки на шнурах электромагнита в две пары штепсельных гнезд "Ш" на панели дефектоскопа, обозначенные надписью "Электромагнит";
4)выключатель В5 "Питание электромагнита или катушки" необходимо выключить.
5)подключить источник питания к двум зажимам питания на панели дефектоскопа, обозначенным "+" и "-";
6)путем нажатия на кнопку В4 убедиться в том, что источник дает полное напряжение;
7)вставить в торцы сердечников электромагнита полюсные наконечники, соответствующие форме контролируемой детали. Наконечники при-
28
жимают к детали так, чтобы место предполагаемого дефекта находилось между наконечниками, раздвинутыми на 130÷150 мм. При этом следует перемещать сердечники электромагнита по скалке и поворачивать наконечники, добиваясь их лучшего контактирования с поверхностью детали, которая должна плотно прилегать к поверхности вырезов в наконечниках. После прижатия наконечников к детали завернуть винты, крепящие сердечники и наконечники;
8)включить ток выключателем В5, одновременно обратив внимание на амперметр, стрелка которого своим отклонением (безразлично в какую сторону) укажет, что через обмотки электромагнита проходит ток и, следовательно, деталь намагнитилась;
9)оставить электромагнит включенным на все время контроля детали (контроль при этом производится в приложенном магнитном поле при последовательно включенных катушках электромагнита);
10)по окончании контроля (после размагничивания) выключить ток
выключателем В5 и отключить источник питания, если работы не будут продолжаться.
7.3. Намагничивание в поле соленоида
При питании соленоида постоянным током для намагничивания проверяемой детали обе секции обмотки соленоида соединять параллельно переключателем на соленоиде В1, поставив его в положение "Постоянный ток". Намагничивание соленоидом можно производить, включив его в сеть переменного тока напряжением 220 В. Секции обмотки соленоида при этом соединять последовательно, поставив переключатель на панели в положение "Переменный ток". Контроль деталей при намагничивании их в поле соленоида производится на остаточном намагничивании.
Порядок операций при намагничивании в поле соленоида, питаемого постоянным током, следующий:
1)поставить переключатель на панели соленоида в положение "Постоянный ток".
2)включить штепсельную вилку шнура соленоида в два гнезда меньшего диаметра на панели дефектоскопа, обозначенные "Катушка".
3)установить переключатель В6 в начальное положение .
4)установить переключатель В2 в нейтральное положение.
5)выключить выключатель В5.
6)подключить источник к двум зажимам на панели дефектоскопа, обозначенным "+" и "-", и проверить его напряжение путем нажатия на кнопку В4.
7)поместить контролируемую деталь в середину соленоида. Если
деталь крупная, то соленоид надеть на деталь. Если деталь длинная и вы-
29
ходит за пределы соленоида, то следует иметь в виду, что сильнее намагничивается та часть, которая находится непосредственно в соленоиде.
8)включить на 0,5÷1 с ток путем включения выключателя В5.
9)вынуть деталь из соленоида.
Порядок операции при намагничивании в поле соленоида, питаемого переменным током напряжением 220 В, следующий:
1)поместить контролируемую деталь внутрь соленоида;
2)соединить последовательно секции соленоида, поставить переключатель на соленоиде в положение "Переменный ток";
3)включить на 0,5÷1 с вилку шнура в штепсельную розетку осветительной сети переменного тока напряжением 220 В;
4)вынуть деталь из соленоида.
7.4. Нанесение на поверхность деталей магнитной суспензии
При контроле на остаточном намагничивании суспензия наносится на поверхность образцов после намагничивания. При контроле в приложенном магнитном поле суспензия наносится во время намагничивания.
Магнитную суспензию можно наносить двумя способами:
1)обливанием поверхности детали суспензией из бачка через отверстие со специальной пробкой или с помощью ложки.
2)окунанием детали в ванночку с суспензией. Способ окунания для мелких деталей предпочтительнее, так как исключена возможность смывания частиц порошка, осевших в дефектных местах.
При обливании детали суспензией необходимо следить, чтобы струя не была особенно сильной и не смывала частиц порошка, осевших на дефектных местах. При слабом намагничивании порошок легко смывается.
Струю следует направлять на деталь таким образом, чтобы суспензия медленно стекала по местам, где наиболее вероятно наличие дефектов. Под струю суспензии, стекающей с детали, всегда следует подставлять ванночку. При контроле в приложенном магнитном поле следует избегать попадания суспензии на обмотки электромагнита.
Магнитную суспензию перед каждым употреблением необходимо хорошо перемешивать. Детали нужно выдерживать в суспензии 1÷2 мин.
При осмотре образцов следует выявить на их поверхности участки, на которых осел порошок, обратив особое внимание на те из них, где наиболее вероятно наличие дефектов. Магнитный рисунок осевшего порошка на дефектах различного происхождения неодинаков. Он зависит от характера, величины и глубины залегания дефекта. По рисунку построить график B=f(h), где В – ширина полоски порошка; h – величина дефектов в % к толщине металла.
Каждая деталь после окончательного осмотра должна быть размагничена так как остаточный магнетизм детали может оказать вредное действие при эксплуатации. Чтобы размагнитить деталь, необходимо уничто-
30