
9-2-6-01__2014__Metody_poluchenija_nanostrukturirovannyh_pokrytij_v_mashinostroenii
.pdf
Химические способы обработки
Электрохимическое полирование проводят на аноде в электролитах,
представляющих собой кислородосодержащие кислоты (фосфорная, серная, хромовая, хлорная), к которым добавляют хромовый ангидрид (для алюминия), используют растворы щелочей (для цинка), цианиды (для серебра) и т.д. При выборе растворов пользуются специальной справочной литературой, обобщающей большой практический опыт по каждому типу обрабатываемого материала.
Химическое планирование применяют редко, так как оно в большинстве случаев не обеспечивает зеркального блеска. Составы растворов для химического полирования регламентируются ГОСТ 9.047–75. Принцип электрохимической и химической полировки заключается в более интенсивном растворении металла на выступах по сравнению с впадинами микрорельефа поверхности, благодаря чему поверхность сглаживается, завершаясь образованием гладкой зеркальной поверхности. Преимущество электрохимического полирования перед химическим заключается в более ярко выраженной избирательности растворения выступающих частей поверхности, что и обеспечивает более ровную зеркальную поверхность после обработки.
51

Химические способы обработки
Ингибиторы – это некоторые органические вещества, например бутилнитрит, бензотритион, дибензилсульфооксид.
Марки ингибиторов, выпускаемых промышленностью: ЧМ, И- 1А, И-1В, И-1Е, КПИ-1, КО, БА6 и др. Скорость травления в ингибированной серной кислоте можно увеличить введением добавок окислителей типа NaNО3, KMnO4, К2Сг2О7, Н2О2, О3, Fe2(SО4)3. Особенно эффективно воздействует озон, уменьшая время травления в 2–5 раз.
52

Химические способы обработки
Травление нержавеющих сталей обычно производят в азотной кислоте с добавками HF, KF и других веществ. Смесь азотной и плавиковой кислот используют при травлении титана.
Травление при этом развивается по реакции
3Тi + 4HNО3 + 12HF = 3TiF4 + 8Н2О + 4NО.
При этом не выделяется водород, чем предотвращается явление водородной хрупкости.
Травление алюминия и его сплавов чаще ведут в горячих щелочных растворах 20–30 % NaOH при температуре 80–90 °С. Медь и медные сплавы травят обычно в концентрированных кислотах (азотной, серной, соляной, фосфорной) или их смесях. Процесс осуществляют в одну или
две-три последовательно идущие стадии в зависимости от материала и
состояния обрабатываемой поверхности. Если изделия из меди и медных сплавов покрыты относительно толстым слоем окалины, то их предварительно травят в 10–15 %-ном растворе серной кислоты при 50– 60 °С. Перед травлением в последнем концентрированном растворе кислот во избежание его разбавления водой изделия не промывают. Перед нанесением покрытий на медные сплавы можно применять и разбавленные растворы кислот, если они не вызывают дефектов слоя при
покрытии.
53
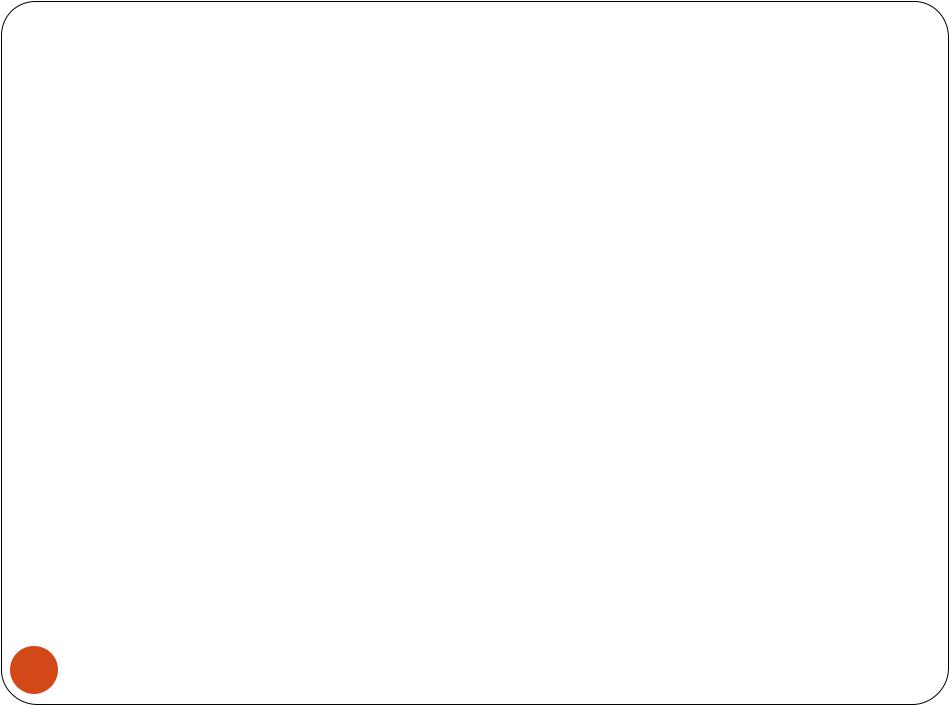
Химические способы обработки
Электрохимическое полирование проводят на аноде в электролитах,
представляющих собой кислородосодержащие кислоты (фосфорная, серная, хромовая, хлорная), к которым добавляют хромовый ангидрид (для алюминия), используют растворы щелочей (для цинка), цианиды (для серебра) и т.д. При выборе растворов пользуются специальной справочной литературой, обобщающей большой практический опыт по каждому типу обрабатываемого материала.
Химическое планирование применяют редко, так как оно в большинстве случаев не обеспечивает зеркального блеска. Составы растворов для химического полирования регламентируются ГОСТ 9.047–75. Принцип электрохимической и химической полировки заключается в более интенсивном растворении металла на выступах по сравнению с впадинами микрорельефа поверхности, благодаря чему поверхность сглаживается, завершаясь образованием гладкой зеркальной поверхности. Преимущество электрохимического полирования перед химическим заключается в более ярко выраженной избирательности растворения выступающих частей поверхности, что и обеспечивает более ровную зеркальную поверхность после обработки.
54
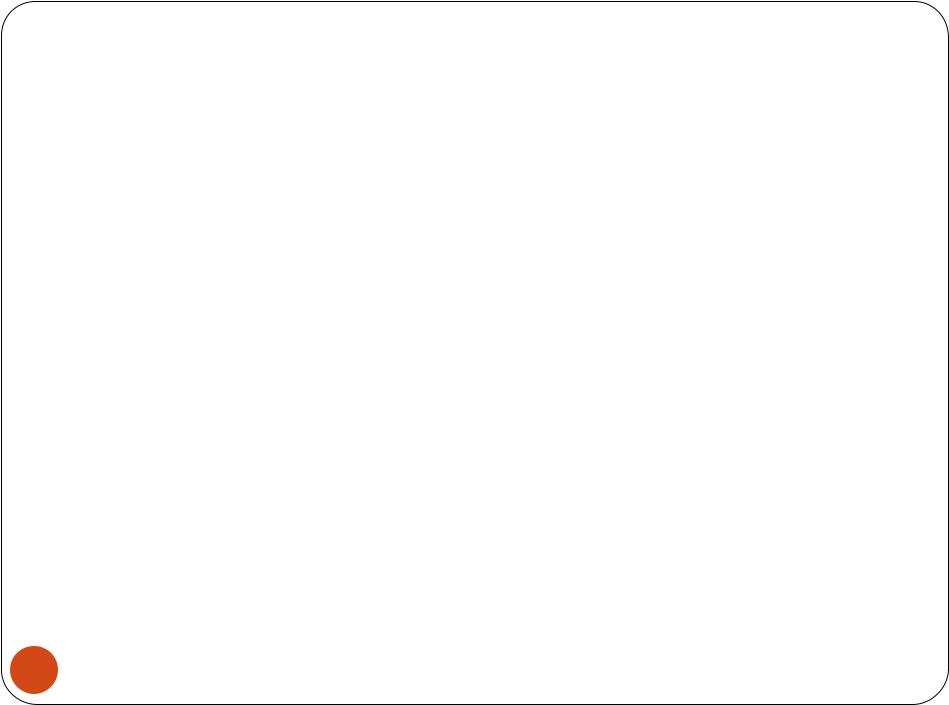
Установки для вакуумного
напыления
55

Вакуумные технологии
Оптические - |
с |
применением |
ионных, |
ионно-плазменных |
и |
молекулярных пучков с возможностью получения покрытий высокой
группы прочности.
Упрочняющие - с использованием ионных, ионно-плазменных источников
низких и средних энергий, позволяющие получать покрытия с высокими
физико-механическими и химическими свойствами.
Защитно-декоративные и коррозионностойкие - с применением ионно-
плазменных источников, позволяющие наносить покрытия в широком
спектре цветов при пониженных температурах на различные материалы.
Алмазоподобные - с использованием ионно-плазменных источников,
позволяющие получать покрытия высокой твердости и низким
коэффициентом трения.
Вакуумная металлизация - с применением ионно-плазменных источников, источников тлеющего разряда, позволяющие получать качественные
56 покрытия на различные материалы.

Оборудование для формирования качественных вакуумных пленок комплектуется современными анализаторами плазменных процессов, а также технологическими источниками плазмы разных классов, что делает установки вакуумного напыления универсальными и позволяет улучшить вакуумные покрытия:
-при вакуумной металлизации Al, Cr, Ni снижается пористость, увеличивается адгезия;
-при нанесении сульфидов ZnS, фторидов MgF2 значительно возрастает адгезия, плотность покрытия;
при нанесении |
окислов |
Al2O3 |
, TiO2, Cr2O3, ZrO2, |
V2O3 снижается поглощение, возрастает адгезия; |
|||
- при нанесении |
карбидов, нитридов, карбонитридов TiN, |
||
TiCN, ZnN, CrN, AlCrN, AlTiN |
возрастает адгезия и плотность |
||
покрытия. |
|
|
|
Вакуумное |
напыление |
может быть в ручном, |
полуавтоматическом и автоматическом режиме работы.
57

1. Вакуумное оборудование для реализации вакуумных технологий по нанесению защитно-декоративных покрытий включает применение ионно-плазменных источников; магнетронов, ионных источников газа, источников тлеющего разряда, вакуумных дуговых испарителей. Сочетание данных технологических источников, а также применение импульсных блоков питания позволяет формировать покрытия широкого спектра цветов на изделия из различных материалов при пониженных температурах. С целью обеспечения воспроизводимости результатов установки комплектуются приборами анализа плазмы. Помимо этого, особенно для вакуумных декоративных покрытий, вакуумной металлизации изготавливаются электролитно-плазменные установки УПП, которые предварительно подготавливают поверхность, повышают качество на 2-3 класса (уменьшают шероховатость), тем самым обеспечивают получение покрытий с высокими свойствами.
58

2. В основу создания вакуумного оборудования для реализации вакуумных технологий по осаждению упрочняющих покрытий, начиная с 1980г., заложен цикл работ исследования поверхности при взаимодействии ионных потоков с поверхностью подложки, отработки конструкций технологических источников, блоков питания и управления, приборов анализа остаточной среды, и других элементов вакуумных систем. В процессе данных работ исследованы физико-механические и химические свойства покрытий в зависимости от параметров технологического процесса, в частности:
влияние ионной обработки, как ионами материала катода, так и ионами газа,
температурные процессы, происходящие при формировании структур,
структурно-фазовые превращения при получении покрытий.
В результате чего, были разработаны вакуумные технологии нанесения упрочняющих покрытий на разлиную подложку и создана гамма вакуумных установок.
59

3. Применение различных технологических источников, таких как магнетронные, резистивные, электронно-лучевые, ионные (в режиме очистки и в режиме ассистирования) в установках для реализации вакуумной технологии по осаждению оптических покрытий с приборами оптического контроля позволяет формировать воспроизводимые от цикла к циклу сложные функциональные покрытия (токопроводящие, просветляющие, отражающие, интерференционные и т.д.) с неравномерностью по толщине не более 3%.
4. DLC покрытия или алмазоподобные иначе говоря аморфные углеродные покрытия получаемые при реализации вакуумной технологии обладают широким спектром свойств - высокая твердость, износостойкость, коррозиостойкость, тем самым защищая изделия от агрессивных сред в течение долгого времени и увеличивая срок службы в несколько раз.
60