
Тема 3-2
.pdfфотошаблоне необходимо увеличивать на величину заужения. Из этого следует, что субтрактивная технология имеет ограничения по разрешению, которые определяются толщиной фольги и процессами травления. Минимально воспроизводимая ширина проводников и зазоров составляет порядка:
50 мкм при толщине фольги 5-9 мкм;
100 - 125 мкм при толщине проводников 20 - 35 мкм;
150 - 200 мкм при толщине проводников 50 мкм.
Аддитивные методы. Для изготовления печатных плат с шириной проводников и зазоров 50 -100 мкм с толщиной проводников 30-50 мкм рекомендуется использовать аддитивный метод формирования рисунка (метод ПАФОС). Это полностью аддитивный электрохимический метод, по которому проводники и изоляция между ними (диэлектрик) формируются селективным гальваническим осаждением проводников и формированием изоляции только в необходимых местах прессованием. Метод ПАФОС, как аддитивный метод, принципиально отличается от субтрактивного тем, что металл проводников наносится, а не вытравливается. Проводящий рисунок формируется (рис. 9) последовательным наращиванием слоев: 1 – получение на временных "носителях" – листах из нержавеющей стали – медной шины толщиной 2÷20 мкм; 2 – формирование рисунка в СПФ; 3 – гальваническое осаждение тонкого слоя никеля (2÷3 мкм) и меди (30 ÷ 50 мкм) по рисунку освобождений в рельефе пленочного фоторезиста. В защитном рельефе пленочного фоторезиста на верхнюю поверхность сформированных проводников производится также нанесение адгезионных слоев. После этого пленочный фоторезист удаляется, и проводящий рисунок на всю толщину впрессовывается в препрег или другой диэлектрик. Полученный прессованный слой вместе с медной шиной механически отделяется от поверхности носителей. Если не нужны межслойные переходы, то медная шина стравливается.
По способу создания токопроводящего покрытия аддитивные методы разделяются на химические и химико-гальванические. При химическом процессе на каталитически активных участках поверхности происходит химическое восстановление ионов металла. В разработанных растворах скорость осаждения меди составляет 2-4 мкм/ч и для получения необходимой толщины процесс продолжается длительное время.
Для изготовления печатных плат с шириной проводников и зазоров 50 -100 мкм с толщиной проводников 30-50 мкм рекомендуется использовать аддитивный электрохимический метод формирования рисунка, по которому проводники и изоляция между ними (диэлектрик) формируются селективным гальваническим осаждением проводников и формированием изоляции только в необходимых местах прессованием. Метод, как аддитивный, принципиально отличается от субтрактивного тем, что металл проводников наносится, а не вытравливается.

Рисунок 9 – Метод ПАФОС
При изготовлении двухсторонних слоев с межслойными переходами перед травлением тонкой медной шины сверлятся и металлизируются отверстия. Проводящий рисунок, утопленный в диэлектрик и сверху защищенный слоем никеля, при травлении медной шины не подвергается воздействию травильного раствора. Поэтому форма, размеры и точность проводящего рисунка определяются формой и размерами освобождений в рельефе пленочного фоторезиста, т.е. процессами фотохимии (фотолитографии). Отсюда к процессам фотолитографии предъявляются более жесткие требования, в частности, оптической плотности белых и черных полей фотошаблонов, резкости края изображения, стабильности температуры и влажности в рабочих помещениях.
При обеспечении требуемых параметров технологического процесса аддитивная технология позволяет получать рисунок проводников на плате с большей точностью и воспроизводимостью:
–ширина проводников, сформированных в рельефе пленочного фоторезиста, практически по всей высоте проводника равна ширине изображения на фотошаблоне, интервал разброса не превышает 5-10 мкм;
–искажения ширины проводников на поверхности подложки относительно размеров на фотошаблоне в среднем составляют от 10 мкм до 20 мкм;
–суммарный интервал разброса ширины проводников по всей высоте фоторельефа не превышает 15-20 мкм.
Таким образом, в отличие от субтрактивной технологии аддитивные процессы принципиально позволяют получать ПП по самым высоким классам точности.
Комбинированный позитивный метод (полуаддитивный метод) получения проводящего рисунка ПП
–нарезка технологических заготовок;
–очистка поверхности фольги (дезоксидация);
–сверление отверстий (подлежащих металлизации) на станках с числовым программным управлением (ЧПУ) (эта технологическая операция применяется только при
изготовлении ДПП и заготовок внутренних слоев МПП, выполненных по методу попарного прессования со скрытыми переходными отверстиями);
–активация поверхности под химическую металлизацию;
–тонкая химическая металлизация (до 1 мкм) или палладирование при использовании технологического процесса прямой металлизации отверстий (только для ДПП и заготовок внутренних слоев МПП со скрытыми переходными отверстиями);
–предварительная тонкая гальваническая металлизация (до 6 мкм)
–нанесение и экспонирование фоторезиста через фотошаблон-позитив;
–нанесение и экспонирование фоторезиста через фотошаблон-позитив;
–основная гальваническая металлизация (до 25 мкм толщины меди внутри отверстий);
–нанесение металлорезиста;
–удаление экспонированного фоторезиста;
–травление обнаженных участков тонкой фольги между элементами печатного рисунка;
–удаление металлорезиста;
–нанесение контактных покрытий на концевые печатные ламели (только при изготовлении ДПП);
–отмывка платы (заготовки МПП), сушка;
–нанесение паяльной маски (только для ДПП);
–нанесение финишного покрытия на контактные площадки (только для ДПП).
Метод попарного прессования плат
Этапы метода (рис. 10):
–с помощью комбинированного позитивного способа формируются будущие ядра МПП. Методика изготовления описана выше. Отличие состоит лишь в том, что для будущих наружных слоев рисунок топологии не изготавливается — фольга остается целой. ДПП);
–заготовки (ядра) с готовыми внутренними слоями спрессовываются. При прессовании между ядрами размещаются слои препрега;
–сверление сквозных отверстий (подлежащих металлизации) на станках с ЧПУ;
–активация, тонкая химическая металлизация и гальваническая затяжка;
–нанесение и экспонирование фоторезиста через фотошаблон для изготовления внешних слоев;
–основная гальваническая металлизация;
–нанесение металлорезиста;
–удаление экспонированного фоторезиста;
–травление обнаженных участков тонкой фольги между элементами печатного рисунка внешних слоев;
–удаление металлорезиста;
–отмывка платы, сушка;
–нанесение паяльной маски;
–нанесение финишного покрытия на контактные площадки;
–нанесение маркировки;
–электрическое тестирование, контроль всей платы.

Рисунок 10 – Метод попарного прессования плат
Преимущества метода попарного прессования:
–относительная простота реализации;
–высокая скорость изготовления плат;
–низкая чувствительность к браку и огрехам изготовления отдельных ядер. Недостатки метода попарного прессования:
–необходимость дважды осаждать на внешних слоях МПП гальваническую медь. Это резко снижает разрешающую способность рисунка на внешних слоях МПП;
–при нанесении паяльной маски и защитных лаковых покрытий создаются затруднения
вобеспечении качества такого покрытия — лаки стекают с высоких проводников, обнажая их острые кромки;
–необходимо обеспечить достаточную жесткость заготовок (ядер). Это обстоятельство не позволяет использовать тонкие ядра, что влечет резкое увеличение толщины МПП;
–для наращивания гальванической меди требуется несколько часов.
Метод послойного наращивания
Этапы метода (рис. 11):
–с помощью субтрактивного метода формируется будущее ядро - основа МПП (формируются слои двух первых внутренних слоев МПП с рисунком печатных проводников и площадок);
–поверх ядра с обеих сторон наносится необходимое количество слоев препрега;
–поверх препрега наносится фольга;
заготовка подвергается технологической операции прессования;
–с помощью механического сверления (с контролем глубины сверловки), лазерного или плазменного прожига формируются отверстия — основа микропереходов между внешними и ближайшими внутренними слоями заготовки;
–активация, тонкая химическая металлизация и гальваническая затяжка, как и для ДПП при комбинированном позитивном способе;
–нанесение и экспонирование фоторезиста через фотошаблон для изготовления внешних слоев;
основная гальваническая металлизация (отличие от классического полуаддитивного метода большая толщина меди для полного заполнения полостей отверстий микропереходов);
–нанесение металлорезиста;
–удаление экспонированного фоторезиста;
–травление обнаженных участков тонкой фольги между элементами печатного рисунка внешних слоев;
–электрическое тестирование, контроль всей платы.
электрическое тестирование, контроль полученной заготовки;
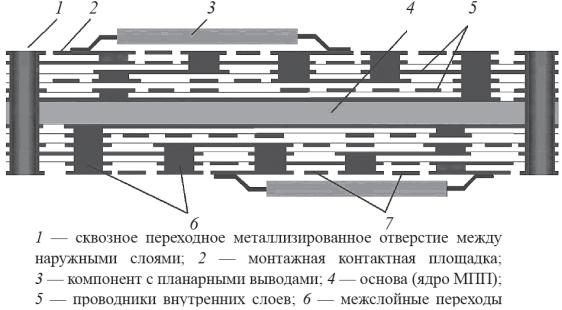
–далее снова наносится необходимое количество слоев препрега, медной фольги и все технологические операции повторяются;
–при формировании внешних слоев МПП после прессования заготовки производится сверление сквозных отверстий (подлежащих металлизации) на станках с ЧПУ;
–далее повторяется ряд технологических операций по гальванической металлизации и травлению остатков меди между элементами рисунка;
–нанесение паяльной маски;
–нанесение финишного покрытия на контактные площадки;
–нанесение маркировки;
–обрезка платы по контуру;
–электрическое тестирование, контроль всей платы.
Рисунок 11 – Метод послойного наращивания
Основным преимуществом данного метода изготовления МПП является исключительно высокая плотность размещения проводников во всех слоях печатной платы и очень высокая плотность монтажа.
Недостатки метода послойного наращивания:
–ограниченное количество слоев МПП (не более 12). Это связано с тепловым стрессом
ибольшим механическим нагрузкам.
–для наращивания гальванической меди требуется большое время — несколько часов, что делает техпроцесс изготовления каждой новой пары слоев достаточно продолжительным.
–при возникновении дефектов изготовления последующих слоев вся полученная заготовка уходит в брак.
Метод металлизации сквозных отверстий
Этапы метода (рис. 12):
–травление заготовок;
–отмывка и сушка заготовок;
–электрическое тестирование, контроль полученных заготовок;
–подготовка поверхности фольги (активация) для обеспечения лучшего сцепления фольги с препрегами при прессовании;
–прессование заготовок в единый пакет;
–сверление сквозных отверстий (подлежащих металлизации) на станках с ЧПУ;
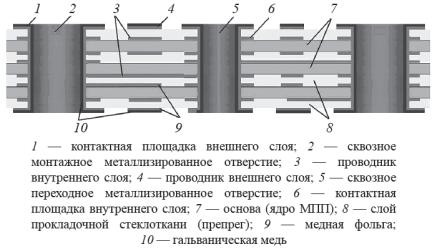
–очистка отверстий от наносов смолы (desmaer-процесс);
–активация меди, тонкая химическая металлизация и гальваническая затяжка (как и для ДПП – при комбинированном позитивном способе);
–нанесение и экспонирование фоторезиста через фотошаблон для изготовления внешних слоев;
–основная гальваническая металлизация, нанесение металлорезиста и удаление экспонированного фоторезиста;
–вырубка заготовок ядер МПП из фольгированного диэлектрика;
–подготовка поверхности фольги (дезоксидация);
–нанесение и проявление фоторезиста, закрывающего участки фольги, не подлежащих вытравливанию;
–травление обнаженных участков фольги между элементами печатного рисунка внешних слоев;
–удаление металлорезиста;
–отмывка платы, сушка;
–нанесение паяльной маски;
–нанесение финишного покрытия на контактные площадки;
–нанесение маркировки;
–обрезка платы по контуру;
–электрическое тестирование, контроль.
Рисунок 12 – Метод металлизации сквозных отверстий
Преимущества метода металлизации сквозных отверстий:
–возможность высокой автоматизации процесса изготовления МПП;
–высокая скорость изготовления плат, поскольку все заготовки;
–низкая чувствительность к браку и огрехам изготовления отдельных ядер;
–использование фольгированных диэлектриков с малой толщиной фольги позволяет уменьшить боковой подтрав и изготавливать проводники малой ширины с высокой точностью;
–этот метод позволяет изготавливать печатные платы с практически не ограниченным количеством слоев;
Недостатки метода металлизации сквозных отверстий:
–относительно механически слабая связь металлизации отверстий с торцами контактных площадок внутренних слоев;
–для обеспечения качественной металлизации отверстий необходимо соблюдать отношение минимального диаметра отверстия к толщине платы не более 1:10.
–из-за отсутствия межслойных переходов этот метод имеет несколько более низкую плотность размещения топологии и монтажа.
–необходимо точно совмещать печатные слои при изготовлении ядер, а также ядра при прессовании;
–особой тщательности требует подбор режимов прессования и качество технологической оснастки прессов (для обеспечения прочной адгезии пакета слоев).
Метод оконтуривания. Прототипы печатных плат могут быть изготовлены без применения фотохимических процессов – методом фрезерования. Основное преимущество механического метода - высокая оперативность и простота реализации.
Механическое изготовление плат происходит полностью на одном станке и включает следующие этапы:
подготовка управляющего файла для станка с ЧПУ
автоматическая сверловка заготовки
фрезерование изолирующих каналов
металлизация переходных отверстий (возможны различные способы) Этапы изготовления печатных плат фрезерованием
1.Компьютерная обработка. Разработка принципиальной схемы устройства. Проектирование принципиальных схем производится разработчиками печатных плат. Производится в программных продуктах Pcad, Orcad, Accel Eda и др.
2.Трассировка. Трассировка производится также разработчиками печатных плат в программных продуктах Pcad, Orcad, Accel Eda и др. Форматы файлов Pcad, Dxf, Gerber
3.Доработка файлов. Вывод файлов сверления и фрезерования. Обычно производится изготовителями печатных плат. Обработка под конкретное оборудование. Используются программные продукты такие как CАМ 350, Instant САМ, Circuit САМ.
4.Механическая обработка
5.Сверление отверстий. Сверление - распространенный метод получения отверстий в сплошном материале. Сверлением получают сквозные и несквозные (глухие) отверстия. Методы сверления для двухсторонних и многослойных печатных плат идентичны при использовании автоматизированного оборудования, за исключением того, что будут необходимы многократное сверления, если ваша многослойная плата содержит скрытый переход.
6.Фрезерование (Гравирование фольгированного текстолита). Фрезерование - один из высокопроизводительных и распространенных методов обработки поверхностей заготовок многолезвийным режущим инструментом - фрезой. Фрезерование обычно производится на той же установке что и сверления. Фрезерование может проводится несколькими методами - это как простое фрезерование контура проводниров, так и выфрезеровывания какой-то какой-то площади для облегчения последующей пайки.В настоящее время фрезерование обычно производится на той же установке, что и сверление. Для ускорения процесса проводится не удаление всех пробельных участков, а всего лишь оконтуривание проводников, выделение их из слоя фольги. Фрезерование обычно ведется коническими фрезами с углом при вершине 60 или 30 градусов (в ряде случаев - менее 18 градусов). Для получения стабильной ширины контурной канавки необходимо строго контролировать глубину врезания фрезы в заготовку. Неплоскостность стеклотекстолита, неравномерный прижим заготовки к рабочему столу могут привести к разбросу ширины реза. Именно поэтому ряд фирм применяют специальные прижимные головки.
7.Создание электрических межслойных соединений. Помимо электрохимической металлизации, которая производится перед фрезерованием, применяется ряд альтернативных методов: пустотелые заклепки, впрыскивание проводящей пасты, перемычки, пистоны, переходные втулки, показанные на рис. 13.
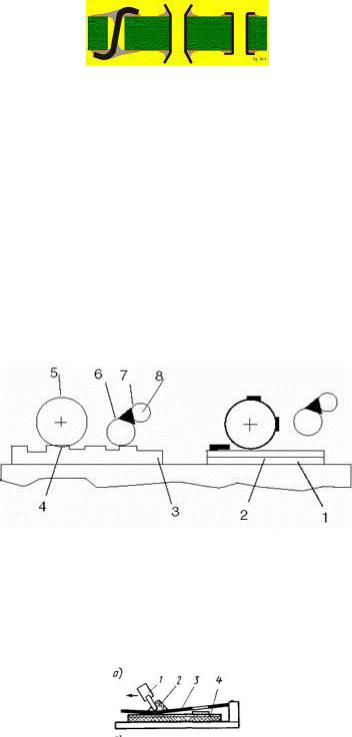
Рисунок 13 – Создание электрических межслойных соединений
4 Методы нанесения рисунка ПП
Основными методами, применяемыми в промышленности для создания рисунка печатного монтажа, являются офсетная печать, сеткография и фотопечать. Выбор метода определяется конструкцией ПП, требуемой точностью и плотностью монтажа, производительностью оборудования и экономичностью процесса.
Метод офсетной печати (рис.14) состоит в изготовлении печатной формы, на поверхности которой формируется рисунок слоя. Форма закатывается валиком трафаретной краской, а затем офсетный цилиндр переносит краску с формы на подготовленную поверхность основания ПП. Метод применим в условиях массового и крупносерийного производства с минимальной шириной проводников и зазоров между ними 0,3-0,5 мм (платы 1 и 2 классов плотности монтажа) и с точностью воспроизведения изображения ±0,2 мм. Его недостатками являются высокая стоимость оборудования, необходимость использования квалифицированного обслуживающего персонала и трудность изменения рисунка платы.
Рисунок 14– Метод офсетной печати
Сеткографический метод (рис.15) основан на нанесении специальной краски на плату путем продавливания ее резиновой лопаткой (ракелем) через сетчатый трафарет, на котором необходимый рисунок образован ячейками сетки, открытыми для продавливания. Метод обеспечивает высокую производительность и экономичен в условиях массового производства. Точность и плотность монтажа аналогичны предыдущему методу.
Рисунок 15 – Сеткографический метод
Фотопечать представляет собой способ нанесения изображения рисунка печатных проводников на материал основания, покрытый светочувствительным слоем (фоторезистом), экспонируемым через фотошаблон с требуемым изображением, характеризуется самой высокой точностью (±0,05 мм) и плотностью монтажа, соответствующими 3–5 классу (ширина проводников и зазоров между ними 0,1-0,25 мм).

Фотошаблон рисунка ПП – это негативное или позитивное изображение требуемого рисунка в масштабе 1 1 на стеклянной фотопластинке или пленочном материале, полученные путем фотографирования с оригинала рисунка ПП.
Наиболее целесообразным является получение оригиналов фотошаблонов в системах автоматизированного проектирования ПП.
Фоторезисты представляют собой тонкие пленки органических растворов, которые должны обладать свойствами после экспонирования полимеризоваться и переходить в нерастворимое состояние. Основные требования, предъявляемые к фоторезистам высокая разрешающая способность, светочувствительность, устойчивость к воздействию травителей и различных химических растворов, хорошая адгезия с поверхностью платы. По способу образования рисунка фоторезисты делятся на негативные и позитивные.
Негативные фоторезисты изготовляют на основе поливинилового спирта. Участки негативного фоторезиста, находящиеся под прозрачными участками фотошаблона, под действием света получают свойство не растворяться при появлении. Участки фоторезиста, расположенные под непрозрачными местами фотошаблона, легко удаляются при проявлении в растворителе. Таким образом, создается рельеф, представляющий собой изображение светлых элементов фотошаблона (рис. 16 а).
Их широко применяют вследствие отсутствия токсичных составляющих, высокой разрешающей способности, простотой проявления и низкой стоимостью. Недостатком этих фоторезисты является невозможность хранения заготовок (более 3...5 часов) с нанесенным слоем, так как происходит задубливание даже в темноте.
Позитивные фоторезисты применяют на основе диасоединений, которые состоят из светочувствительной полимерной основы, растворителя и некоторых других компонентов. Позитивный фоторезист под действием облучения изменяет свои свойства таким образом, что при обработке в проявителях растворяются его облученные участки, а необлученные (находящиеся под непрозрачными участками фотошаблона) остаются на поверхности платы (рис. 16, б).
По адгезионной и разрешающей способности они превосходят негативные фоторезисты, но имеют более высокую стойкость и содержат токсичные растворители. Достоинством позитивных фоторезистов, является отсутствие дубления при хранении заготовок с нанесенным светочувствительным слоем.
Рисунок 16 –Образование защитного слоя фоторезиста: а) негативного: б) позитивного; 1 – фотошаблон; 2 – фоторезист; 3 – плата
В технологическом процессе производства ПП применяют жидкие и сухие фоторезисты. Жидкие фоторезисты наносят погружением, поливом с центрифугированием,
накатыванием ребристым валиком и др.
Недостатком жидких фоторезистов является малая толщина и неравномерность слоя покрытия, большая трудоемкость процесса нанесения и невозможность его использования на плате с отверстиями.
Сухие фоторезисты в настоящее время получили широкое применение. Они заменили жидкие как более технологические и простые в применении. Сухой пленочный фоторезист представляет собой тонкую пленку, полимеризующуюся под действием ультрафиолетового излучения.
Однослойные ПП и ГПК изготавливают преимущественно субтрактивным сеточнохимическим или аддитивным методом, а ДПП и ГПП химико-гальваническим аддитивным или комбинированными фотохимическими (негативным или позитивным) методами. Производство МПП основано на типовых операциях получения ОПП и ДПП и некоторых специфических процессах, таких как прессование слоев, создание межслойных соединений и др.