
методички / 4010 ЭИ
.pdfрадиостанции, прожекторной установки, фонаря, состояние защитного ограждения рабочего места.
О всех обнаруженных неисправностях осмотрщик вагонов обязан сообщить мастеру или оператору ПТО для принятия мер по их устранению.
Во время осмотра вагонов в движущемся поезде осмотрщику вагонов запрещается выходить за пределы ограничительной стойки «островка безопасности».
Встреча поезда «сходу» является одним из основных методов выявления неисправностей грузовых вагонов. При встрече поезда «сходу» диагностика производится по характеру движения ходовых частей, колесных пар и работы рычажной передачи (особое внимание осмотрщики должны обращать на наличие дефектов на поверхности катания колес, перемещение боковин и надрессорных балок тележек вагонов, наличие дыма и специфический запах смазки, на пощелкивание и периодическое подергивание буксы, характерный стук колеса о рельс при вращении колесной пары) в соответствии с рекомендациями, приведенными в документе «Методы выявления неисправностей грузовых вагонов по внешним признакам», № 711-2008 ПКБ ЦВ. При встрече поезда «сходу» выявлению подлежат ниже перечисленные дефекты деталей и узлов грузовых вагонов, а так же волочащиеся элементы вагона:
-обнаружение неисправных буксовых узлов, в т.ч. трение буксы (писк, свист от трения металла, дым, пламя из буксы);
-ползун (колесо не вращается, частые удары колеса об рельс);
-нарушение крепления груза;
-обрыв бортов платформы (провисание бортов, угрожающее падением на путь);
-выход груза за пределы габарита;
-обрыв двери крытого вагона (провисание двери, сход ее с роликов, угрожающие падением на путь двери или груза, задир крыши, касающийся контактного провода);
-открытие или обрыв крышки люка полувагона;
-выход стрелы грузоподъемных механизмов за пределы габаритов погрузки;
-обрыв или разъединение тормозных тяг, предохранительных устройств и триангеля (провисание тормозных тяг и триангеля, угрожающее падением на путь, скрежет, искрение от соприкосновения деталей, волочение их);
-провисание торцовой двери вагона;
-отсутствие хвостового сигнала (по наличию хвостового сигнала контролируется проследование поезда в полном составе);
-несоблюдение нижнего габарита (сбита габаритная планка) [4].
Наиболее характерные внешние признаки неисправных буксовых узлов с подшипниками качения при встрече поезда «сходу» указаны в таблице 1 [5].
11
|
Таблица 1 |
Внешние признаки неисправных буксовых узлов при встрече поезда «сходу» |
|
|
|
Признаки неисправных буксовых узлов |
Возможные неисправности |
с подшипниками качения |
|
|
|
Буксы пассажирских и грузовых вагонов |
|
|
|
Колесная пара идет юзом при отжатых тормозных |
Подшипник разрушен, ролики заклинены и не |
колодках, слышно пощелкивание |
вращаются |
|
|
Выброс смазки хлопьями на диск и обод колеса |
Подшипник разрушен |
|
|
Сильные потеки в зоне смотровой и крепительной |
Подшипник может быть разрушен |
крышек |
|
|
|
Букса у пассажирского вагона перемещается вдоль |
Подшипник разрушен, повреждение торцового |
шейки оси, а у грузового боковая рама тележки |
крепления, гайка М110 полностью сошла с шейки |
вместе с буксой смещены вдоль шейки оси, цвета |
оси или оборваны головки болтов М20 тарельчатой |
побежалости, окалина на смотровой или |
шайбы |
крепительной крышке, деформация крышек |
|
|
|
Выброс искр пучком со стороны лабиринта |
Проворот внутреннего кольца или разрушение |
|
заднего подшипника |
|
|
Выделение дыма, появление запаха из буксы (при |
Разрушение полиамидного сепаратора подшипника |
приеме «сходу» и после остановки поезда) |
буксового узла |
|
|
Буксы пассажирских вагонов |
|
|
|
Между колесной парой и буксой, а также рамой |
Излом шейки оси колесной пары |
тележки и колесной парой видны искры, слышен |
|
скрежет, пощелкивание |
|
|
|
Тележка вибрирует, один ее конец трясет, букса |
Разрушен сепаратор, ролики сгруппировались в |
имеет частые вертикальные колебания, слышен |
нижней части буксы |
резкий стук рычажной передачи, разработаны |
|
отверстия в кронштейне для валика подвески |
|
башмака, выпали валики рычажной передачи |
|
|
|
Буксы грузовых вагонов |
|
|
|
Корпус буксы имеет наклон по отношению к шейке |
Проворот внутреннего кольца переднего |
оси; боковая рама тележки опирается на корпус |
подшипника на шейке оси |
буксы одним краем |
|
|
|
Порядок выполнения работы
1.Описать, какие дефекты деталей и узлов грузовых вагонов подлежат выявлению.
2.Отобразить в виде блок-схемы последовательность организации работ при встрече поезда «сходу».
3.Представить в виде таблицы внешние признаки неисправных буксовых узлов при встрече поезда «сходу».
4.Ответить на контрольные вопросы.
12
Контрольные вопросы
1.Каким документом регламентируется организация работ при встрече пассажирских и грузовых поездов «сходу»?
2.Как называется рабочее место осмотрщика вагонов при встрече поезда «сходу»?
3.Какие требования предъявляются к «островку безопасности»?
4.Какие действия выполняет осмотрщик вагонов при встрече поезда «сходу»?
5.Какие меры должен принять осмотрщик при обнаружении неисправности угрожающей безопасности движения?
6.Кому обязан сообщить осмотрщик вагонов о всех обнаруженных неисправностях вагонов?
Практическая работа № 3
ОРГАНИЗАЦИЯ РАБОТЫ ПОСТОВ С ОТРИЦАТЕЛЬНЕЙ ДИНАМИКОЙ (2 часа)
Цель работы: изучить организацию работы постов с отрицательней динамикой.
Краткие теоретические сведения
Динамика вагона – это физический процесс возникновения сил, моментов (упругих, трения и инерционных), перемещений составных элементов вагона вследствие взаимодействия его ходовых частей и рельсового пути, а также локомотивов и вагонов в движущемся поезде [6].
Железнодорожный путь и подвижной состав представляют единую механическую систему, в которой они взаимодействуют, находясь в зависимости друг от друга.
Вагоны в составе грузовых поездов, особенно порожние, даже при отсутствии отступлений в содержании пути, при скоростях движения более 35 км/ч, в случае отклонений в параметрах ходовых частей тележек склонны к отрицательной динамике (автоколебаниям параметрического типа – виляния, боковые колебания и галопирование кузова).
Основные причины возникновения отрицательной динамики (автоколебаний) следующие:
непараллельность осей колесных пар вследствие различий межчелюстных расстояний у правой и левой боковины или увеличенных значений зазоров между буксой
ичелюстями боковин;
различие кругов катания колес, эллипсность, различная конусность, наличие дефектов на поверхности катания, неравномерный износ гребней;
ослабление или износ клиновой системы, излом или просадка пружин рессорного комплекта.
13
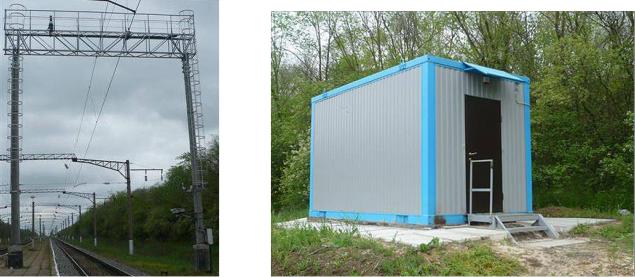
Следствие отрицательной динамики вагонов – это повышенное воздействие вагона на путь и при определенных условиях его раздвижка, интенсивный износ головки рельса, узлов «пятник–подпятник», гребней колесных пар, фрикционных накладок и клиньев.
Самое опасное, что вагоны (особенно порожние), имеющие отрицательную динамику, склонны к сходу из-за распора гребнем колеса колеи, вкатывания гребня колес на головку рельса, а при неблагоприятном состоянии пути или торможении состава – выжимании экипажа.
Автоматизированная система обнаружения вагонов с отрицательной динамикой «АСООД» предназначена для обнаружения на ходу поезда вагонов с повышенными колебаниями (отрицательной динамикой), связанными с нарушением геометрии деталей ходовых частей вагона, измерений этих колебаний и обеспечения безопасности движения на железных дорогах ОАО «РЖД». В случае превышения заданных значений динамических характеристик, система формирует сигнал тревоги о каждом вагоне и его характеристики по каналу связи поступают на автоматизированное рабочее место оператора пункта технического обслуживания.
Автоматизированная система обнаружения вагонов с отрицательной динамикой «АСООД» (рис. 1–4) разработана для выявления потенциально опасных неисправностей вагонов подвижного состава на ходу поезда, увеличения надежности и обеспечения безопасности движения поездов. Система включает:
блок лазерных маркеров;
комплект оборудования пункта первичной обработки и передачи информации;
сервер базы данных и АРМ оператора;
педали электронные;
комплект программного обеспечения [7].
Рис. 1. Общий вид |
Рис. 2. Модульное помещение для |
оборудования «АСООД» |
размещения комплекта оборудования пункта |
|
первичной обработки и передачи информации |
|
14 |
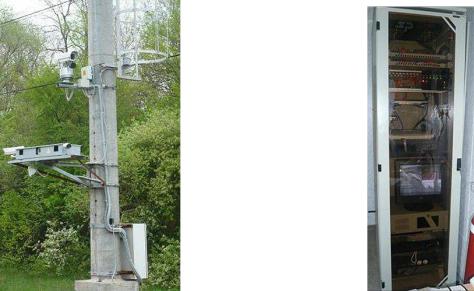
Рис. 3. Комплект наружных |
Рис. 4. Серверное оборудование системы |
датчиков и видеокамер |
«АСООД» |
|
Таблица 2 |
Основные технические характеристики «АСООД» |
|
|
|
Наименование характеристики |
Значение |
Дистанция измерений колебаний вагона, мм |
2500÷3500 |
Диапазон измерений, мм |
150 |
Амплитуда обнаруживаемых горизонтальных поперечных колебаний (разрешающая |
|
способность), мм |
10 |
Частота обнаруживаемых колебаний, Гц |
1÷12 |
Электропитание оборудования, В (Гц) |
220 (50) |
Мощность, потребляемая оборудованием, кВт |
|
на открытом воздухе |
1,2 |
в отапливаемом помещении |
1 |
Средний срок службы, лет, не менее |
5 |
Диапазон скоростей движения для выявления повышенных колебаний кузова вагонов, км/ч |
50÷75 |
Средняя наработка на отказ, ч, не менее |
10500 |
Порядок выполнения работы
1.Описать основные причины возникновения отрицательной динамики.
2.Отобразить в виде схемы, какие блоки включает система «АСООД».
3.Ответить на контрольные вопросы.
Контрольные вопросы
1.В каких случаях вагоны склонны к отрицательной динамике?
2.Что является следствием отрицательной динамики вагонов?
3.Каково назначение системы «АСООД»?
4.С какой скоростью должен двигаться состав для обнаружения вагонов с отрицательной динамикой при помощи «АСООД»?
5.Чему равен срок службы устройства «АСООД»?
15
Практическая работа № 4
РЕСУРСОСБЕРЕГАЮЩИЕ ТЕХНОЛОГИИ НА УЧАСТКЕ ТЕКУЩЕГО ОТЦЕПОЧНОГО РЕМОНТА (4 часа)
Цель работы: ознакомиться с ресурсосберегающими технологиями на участке текущего отцепочного ремонта.
Краткие теоретические сведения
Одними из главных задач стратегического развития ОАО «Российские Железные Дороги» являются рост производительности, использование всех видов ресурсов, оптимизация издержек производства. Большая роль в решении этих задач отводится вагонному хозяйству, основная цель которого – обеспечение сети железных дорог надежным, отвечающим современным стандартам и требованиям подвижным составом.
Основными резервами повышения эффективности использования вагонного парка в эксплуатации являются:
сокращение времени нахождения вагонов под грузовыми операциями и на технических станциях;
снижение числа отцепок в текущий отцепочный ремонт и простоя в неисправном состоянии.
Текущий отцепочный ремонт (ТОР) – это специфический вид услуги по ремонту грузового вагона. Неисправность может возникнуть в любое время и в любой точке железнодорожной сети. Соответственно, для обеспечения безопасности движения аварийный вагон необходимо отправить на ближайшую станцию или, при наличии такой возможности, устранить неисправность на месте. Производится такой ремонт на специально выделенных путях, оснащенных необходимым оборудованием и приспособлением на основании уведомления формы ВУ-23М, заполненного осмотрщиком вагонов или оператором пункта технического обслуживания (ПТО). При данном виде ремонта выявляются и устраняются неисправности кузовов, рам вагонов, колесных пар, боковых рам и надрессорных балок тележек, буксового узла, пружиннофрикционного рессорного комплекта, тормозного оборудования, автосцепного устройства вне зависимости от причины поступления вагона в текущий отцепочный ремонт [8].
Материалы, запасные части, применяемые при ремонте отцепленных вагонов, должны соответствовать нормативной документации и рабочим чертежам на их изготовление и ремонт, быть сертифицированы, а также должен соблюдаться порядок их хранения.
Но в действительности наблюдается неупорядоченное хранение запасных частей и материалов на участках ТОР. В результате при замене деталей вагонов в ходе
16
производства ремонта работники участка затрачивают продолжительное время, связанное с избыточным их перемещением, что приводит к простою вагона в ремонте.
На сети железных дорог во многих эксплуатационных вагонных депо (Забайкальской дирекции инфраструктуры, Октябрьской дирекции инфраструктуры, Северо-Кавказской дирекции инфраструктуры) активно внедряют технологию бережливого производства, которая позволяет оптимизировать технологические процессы производственных участков. На предприятиях ОАО РЖД широко сипользуются следующие методы бережливого производства: система блокирования и предупреждения дефектов «БАРЬЕР»; 5S – система организации и рационализации рабочего места; методика визуального контроля по системе Кайдзен; система «7-С», которая доказывает, что невозможно изменить одно, не изменив другое. Система «БАРЬЕР» направлена на выполнение следующих целей: 100% обнаружение брака в технологических процессах; постоянный анализ и улучшение технологических процессов; информирование и вовлечение всех сотрудников в решение проблем качества.
5S – это пять японских слов или 5 Шагов (5 Step):
1)«сортировка» (нужное-ненужное) – четкое разделение вещей на нужные и ненужные и избавление от последних;
2)«соблюдение порядка» (всему свое место) – организация хранения необходимых вещей, которая позволяет быстро и просто их найти и использовать;
3)«содержание в чистоте» (уборка) – содержание рабочего места в чистоте и опрятности;
4)«стандартизация» (поддержание порядка) – необходимое условие для выполнения первых трех правил;
5)«совершенствование (буквальный перевод – воспитание)» (формирование привычки) – воспитание привычки точного выполнения установленных правил, процедур и технологических операций.
Для реализации проекта «Бережливое производство» в вагонном хозяйстве распоряжением ОАО «РЖД» от 20 декабря 2013г. №2840р утверждена и введена в
действие с 1 января 2014г. «Методика визуального контроля по системе Кайдзен в структурных подразделениях Управления вагонного хозяйства Центральной дирекции инфраструктуры». Данная методика разработана проектно-конструкторским бюро вагонного хозяйства. Полигоном для практической апробации данной методики с 2014 г. определены эксплуатационные вагонные депо Октябрьской, Восточно-Сибирской и Западно-Сибирской дирекции инфраструктуры.
Термин «бережливое производство» (leanmanufacturing) применяется для обозначения базовых принципов эффективной организации деятельности кампании. Он фокусирует внимание на избавлении от любых непроизводительных затрат. К непроизводительным затратам относят любые действия и затраты, не связанные
17
напрямую с доставкой грузов потребителю точно в срок, обладающие потребительской ценностью. Потери – это действия, которые увеличивают затраты и время доставки грузов, но не добавляют ценности конечной продукции. На предприятиях железнодорожного транспорта встречаются следующие виды потерь:
перепроизводство – потери, связанные с выпуском продукции в большем количестве;
излишние запасы – вид потерь, связанный с наличием сверхнормативного количества изделий, непосредственно хранящихся на предприятии или за его пределами. Наличие излишних запасов указывает на нестабильность производства на предприятии;
транспортировка – вид потерь, связанный с перемещением материалов и запасных частей;
потери из-за дефектов – вид потерь, связанный с наличием дефектов, затратами на их выявление и устранение;
потери при излишней обработке – вид потерь, возникающий при выполнении операций и процессов, без которых можно обойтись;
потери при излишних перемещениях – вид потерь, возникающий в связи с движениями персонала, которые не являются необходимыми;
простои – вид потерь, связанный с задержками и возникающий в результате ожидания готовности оборудования, персонала, транспортных задержек, неравномерного темпа работы отдельных подразделений предприятия.
Бережливым считают производство, в котором любые непроизводительные затраты сведены к минимуму или отсутствуют вовсе, т.е. все ресурсы предприятия используются только для создания потребительской ценности. Именно эту задачу ставит перед собой ОАО «РЖД», совершенствуя свою деятельность и внедряя методики по сокращению и исключению непроизводительных затрат [9].
Внедряемая «Методика визуального контроля по системе Кайдзен в структурных подразделениях Управления вагонного хозяйства Центральной дирекции инфраструктуры» позволит высвободить дополнительные производственные площади участков, сэкономить материалы и энергоресурсы, уменьшить количество брака, поломок оборудования и инструмента (а это – снижение затрат на ремонт), снизить трудоемкость различных производственных процессов, повысить безопасность труда и улучшить эргономику рабочих мест на производственных участках (рис. 5).
Один из мощных инструментов бережливого производства – это визуальный менеджмент, который создает начальные условия для эффективного труда, организует размещение инструментов, деталей, составных частей конструкций и других индикаторов состояния производства. Одной из целей применения методов визуализации является удаление ненужного, создание начальных условий для эффективного труда и возникновения свободного пространства. Классификация объектов сопровождается их пометкой с помощью ярлыков зеленого, желтого, красного и других цветов [9].
18
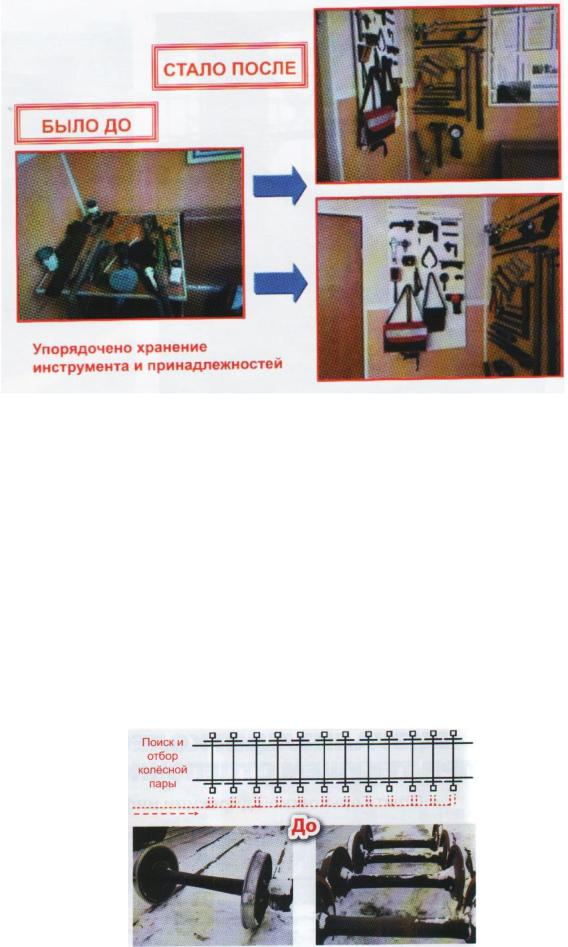
Рис. 5. Помещение старшего осмотрщика вагонов. Метод визуализации: рациональное размещение инструмента
Так, например, в условиях эксплуатационных вагонных депо, а именно на участках ТОР, хранение колесных пар, требующих ремонта в грузовых вагонных ремонтных депо (ВЧДР), обезличено. Из-за ограничения производственных площадей и непрерывного производственного процесса оно осуществляется без определения колесных пар по принадлежности и без выделения отдельных участков хранения для разных собственников, а именно:
ОАО «РЖД»;
собственников, которые осуществляют ремонт по договорам;
собственников, осуществляющих ремонт по гарантийным письмам.
Рис. 6. Поиск и подбор колесных пар до внедрения метода визуализации
19
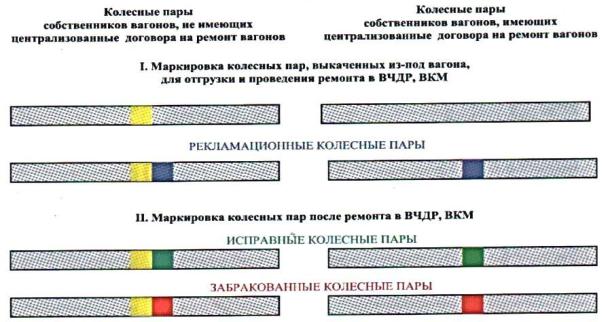
Такое хранение (рис. 6) требует дополнительной проверки всех колесных пар, чтобы определить их принадлежность предприятию-собственнику.
Помимо разделения всех колесных пар на требующих покупки (договорные отношения с собственником) и требующих ремонта в ВЧДР с последующей подкаткой под этот же вагон (отсутствие договорных отношений), существует группа колесных пар, по которым необходимо провести комиссионное расследование, установить виновное предприятие и составить рекламационные документы, необходимые для предоставления собственнику вагона для оплаты за проведенный ТОР [10].
Рис. 7. Порядок маркировки колесных пар при проведении текущего отцепочного ремонта вагонов
Чтобы сократить время отправки колесных пар в ремонт и минимизировать риски, возникающие при хранении и отправке колесных пар из-под приватных вагонов, можно предложить следующую технологию маркировки колесных пар (рис. 7):
1.Выкатка неисправных колесных пар. После выкатки колесной пары из-под вагона бригадир определяет и (в зависимости от наличия договорных отношений с собственником вагона) наносит на ось колесной пары специальную маркировку цветным скотчем. Для колесных пар, выкаченных из-под вагонов приватного парка, на которые отсутствуют договорные отношения на проведение ТОР, на среднюю часть оси колесной пары наносится полоса желтого цвета.
Колесные пары, выкаченные из-под вагонов собственников, имеющие договора на проведение ТОР, впоследствии приобретаемые у собственника и переходящие в парк ОАО «РЖД», при отправке в ремонт не маркируются. При этом на колесные пары, по которым требуется комиссионное расследование, наносится полоса синего цвета.
2.Отправка размеченных колесных пар. При погрузке колесных пар на платформу для отправки ее в то или иное ВЧДР бригадир руководствуется разметкой и безошибочно отгружает колесные пары с нанесенной маркировкой.
20