
методички / 4010 ЭИ
.pdf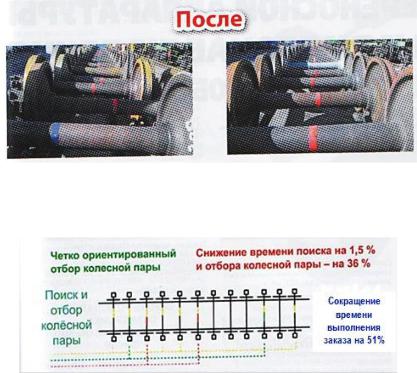
3. Получение колесных пар с ВЧДР. После возврата колесной пары из ремонта рядом
ссуществующей отметкой на оси дополнительно наносится новая полоса (см. рисунки 8, 9):зеленого цвета – для исправной колесной пары;красного цвета– для неисправной колесной пары, требующей расформирования.
Синяя полоса при этом снимается.
В дальнейшем (при отправке колесной пары в ремонт) данная отметка позволяет не осматривать все колесные пары и четко отобрать требуемую.
Рис. 8. Применение метода визуализации колесных пар после возврата колесной пары из ремонта
Рис. 9. Поиск и отбор колесных пар после внедрения метода визуализации
4. Хранение колесных пар на ТОР. Для разграничения колесных пар на участке ТОР предусмотрены три зоны хранения (рис. 10), которые подразделяются на исправные (отремонтированные), неисправные (требующие ремонта), брак (требующие расформирования).
Следовательно, визуализация колесных пар грузовых вагонов при текущем отцепочном ремонте (ТОР) позволит:
минимизировать время нахождения вагонов в ТОР;
сократить время на отбор и отправку колесных пар в ремонт;
снизить время общего простоя вагонов находящихся в собственности промышленных предприятий в текущем отцепочном ремонте;
увеличить выпуск вагонов из текущего отцепочного ремонта;
снизить количество и размеры штрафных санкций за просрочку доставки грузов.
21
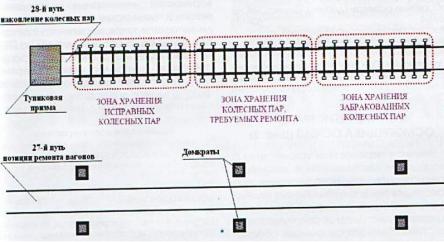
Рис. 10. Зоны хранения колесных пар на пункте текущего отцепочного ремонта
Таким образом, бережливое производство – это, прежде всего, философия, меняющая устоявшиеся взгляды на организацию производственных отношений, всю систему показателей эффективности каждого структурного подразделения, систему управления предприятием. Для бережливого производства важен каждый сотрудник РЖД, важны его инициатива и готовность добиваться улучшений в своей работе [11,12].
Порядок выполнения работы
1.Описать ресурсосберегающие технологии на участке текущего отцепочного ремонта.
2.Описать основные резервы повышения эффективности использования вагонного парка в эксплуатации.
3.Ответить на контрольные вопросы.
Контрольные вопросы
1.В чем заключается суть системы «БАРЬЕР»?
2.В чем заключается суть системы 5S?
3.В чем заключается суть системы «7-С»?
4.В чем заключается суть системы Кайдзен?
5.Дайте определение термину «непроизводительные затраты».
6.Какие виды потерь встречаются на предприятиях железнодорожного транспорта?
7.Поясните инструмент бережливого производства «визуальный менеджмент».
8.Что позволит визуализация выкаченных колесных пар грузовых вагонов при текущем отцепочном ремонте?
22
Практическая работа № 5
УПРАВЛЕНИЕ ТЕХНИЧЕСКИМ СОСТОЯНИЕМ ПОДВИЖНОГО СОСТАВА НА ОСНОВЕ СИСТЕМ ТЕХНИЧЕСКОЙ ДИАГНОСТИКИ (4 часа)
Цель работы: изучить принципы управление техническим состоянием подвижного состава на основе систем технической диагностики (СТД).
Краткие теоретические сведения
В основе работы пункта технического обслуживания сетевого значения (СПТО) лежит кардинальное изменение технологии диагностирования технического состояния грузовых вагонов. Работа осмотрщиков вагонов заменяется использованием автоматизированных систем неразрушающего контроля, осуществляющих определение дефектов вагонов на ходу поезда при подходе к станции. При этом отбраковка узла или детали вагона производиться автоматически без участия оператора. Это накладывает жесткие требования к надежности, быстродействию и условиям эксплуатации используемых диагностических средств. На центральный пункт управления ПТО должны передаваться данные от каждой диагностической системы. Далее по ним принимается решение о необходимости ремонта или отцепки забракованного вагона. Данные о параметрах каждого проконтролированного поезда регистрируются для последующего хранения, часть из них передается на следующий СПТО, так как их наличие увеличивает достоверность диагностирования многих дефектов.
Автоматизированные диагностические комплексы контроля технического состояния вагона на ходу поезда должны выявлять следующие неисправности вагонов:
-контроль температуры буксового узла и заторможенных колес;
-контроль волочения;
-контроль габаритных размеров вагонов;
-контроль дефектов колеса по кругу катания;
-контроль геометрических параметров колеса;
-контроль параметров ударно тягового механизма;
-контроль неравномерности загрузки вагонов;
-контроль сползания буксы с шейки оси.
Приведем средства технической диагностики параметров грузовых вагонов [6].
1) Комплекс технических средств многофункциональный
Комплекс технических средств многофункциональный КТСМ-02 представляет собой систему автоматического контроля, включающая в себя одну или несколько подсистем для обнаружения дефектных узлов и деталей подвижного состава (например: букс, колес, тормозов, габарита и т.д.). Основное назначение КТСМ-02 заключается в контроле параметров подвижного состава, привязанных к конкретным осям, или подвижным единицам, а также координации работы подключенных к нему подсистем и
23
обеспечении информационного взаимодействия через систему централизации с системами контроля и управления верхнего уровня (АСК ПС, ДНЦ, ДГП) [13].
2) Комплекс технических измерений КТИ «КОМПЛЕКС»
Автоматизированный бесконтактный комплекс контроля колесных пар подвижного состава предназначен для бесконтактного контроля и анализа параметров колесных пар подвижного состава. Параметры диагностики: толщина гребня колеса, разность и сумма толщин гребней на колесной паре, равномерный прокат, расстояние между внутренними гранями ободов колес, разность расстояний между внутренними гранями ободов, толщина обода, ширина обода, диаметр колеса, разность диаметров колес в одной колесной паре и в тележке, счет количества осей, определение типа подвижного состава, определение количества вагонов в составе, регистрация скорости движения поезда, регистрация времени контроля, направление движения состава.
3) Система автоматизированного контроля механизма автосцепки «САКМА»
Данная подсистема применяется для контроля наличия неисправностей автосцепных устройств, по причине которых может произойти саморасцеп автосцепок грузовых вагонов на ходу поезда. Она контролирует: износ замков; излом направляющего зуба; излом предохранителя от саморасцепа; поверхностей контура зацепления, перемычки между направляющим зубом и сигнальным отростком; полуутопленное состояния замков; трещины в большом и малом зубе, приводящие в режиме тяги поезда к уширению зуба; уширение зева. В состав системы САКМА входят напольная камера; блок лазерных излучателей; стойка сопряжения; компьютер для обработки информации в помещении диагностического пункта; блок бесперебойного питания и модем.
4)Автоматизированная система контроля открытых, незафиксированных
идеформированных люков и дверей вагонов
Система предназначена для контроля технического и коммерческого состояния грузовых вагонов в прибывающих на станцию поездах. Система автоматизированного анализа и обработки информации обеспечивает автоматизированное выявление деформаций, открытых люков, качки и других неисправностей на основе обработки и суммирования данных, поступающих от камер и датчиков. Система осуществляет отображение данных и сигналов тревоги в прибывающих на станцию поездах на АРМ оператора, а также предоставляет возможность оператору осуществлять анализ технического и коммерческого состояния грузовых вагонов по видеозаписи.
5) Детектор дефектных колес ДДК
Аппаратура ДДК относится к напольным средствам автоматической диагностики технического состояния вагонов на ходу поезда и предназначена для выявления
24
колесных пар с дефектами на поверхности катания колес, вызывающих недопустимые динамические перегрузки неподрессоренных элементов вагонов и пути. Принцип действия аппаратуры ДДК основан на измерении специальными тензометрическими схемами вертикальных сил, действующих между колесом и рельсом при их динамическом взаимодействии, и сравнении измеренных значений с допустимыми нормируемыми уровнями сил. Превышение нормируемого уровня означает, что на поверхности катания колеса имеется неровность (или несколько неровностей), вызывающая недопустимые динамические перегрузки колес и рельсов. Сведения о наличии в составе поезда вагонов с колесными парами, подлежащими осмотру и браковке, передаются по линии связи на ПТО, перед которым установлена аппаратура ДЦК, в виде текстового файла с выходов специализированного компьютера, установленного на посту диагностики. Аппаратура ДДК включает перегонное и станционное оборудование, связанное между собой линией связи. Напольное оборудование аппаратуры ДДК размещается в непосредственной близости от помещения постового оборудования. При этом сигналы от напольного оборудования по кабелю передаются к постовому оборудованию. Постовое оборудование аппаратуры ДДК состоит из двух электронных блоков: тензометрического усилителя типа «Sрider-8» и контроллера (специализированного компьютера).
Станционное (приемное) оборудование аппаратуры ДДК устанавливается непосредственно на ПТО станции прибытия. При этом возможны два варианта станционного оборудования. Первый вариант предусматривает конечный компьютер ДДК на ПТО с устройством печати результатов контроля и звуковыми сигналами тревоги при обнаружении колесных пар с дефектами. По второму варианту вывод результатов контроля с аппаратуры ДДК производится через локальную связь в систему централизации информации от различных устройств диагностики с выдачей оператору ПТО единого документа – смотрового листа.
6)Автоматизированный диагностический комплекс для измерения колесных пар вагонов на подходах к станции
Данный комплекс предназначен для измерения геометрический параметров поверхности катания, а также выявления износа и дефектов цельнокатаных колес на ходу поезда, регистрации неисправностей колесных пар и оперативной передачи полученной информации на ближайшее ПТО. Он контролирует параметры поверхности катания колесных пар грузовых вагонов: толщину и высоту гребня, толщину и ширину обода, диаметр по поверхности катания.
7)Устройство контроля сползания буксы с шейки оси
Автоматическое устройство контроля сползания буксы с шейки оси предназначено для выявления на ходу поезда роликовых букс, имеющих сползание корпуса с шейки
25
оси, вследствие разрушения торцевого крепления, регистрации таких букс и оперативной передачи полученной информации на ближайший ПТО.
8) Устройство контроля тормозов поезда УКТП
Устройство УКТП предназначено для ускоренной зарядки и опробования тормозов поездов на ПТО. Устройство производит автоматическую регистрацию хода опробования тормозов и расчет параметров тормозной системы состава и локомотива с выводом данных в реальном времени на монитор, в сеть АСУ ПТО и на бумажный носитель в виде графиков и по форме «Справка об обеспечении поезда тормозами и исправном их действии».
Устройство позволяет автоматизировать процессы подготовки тормозов подвижного состава в парках отправления, осуществлять контроль над качеством подготовки тормозов и соблюдением технологической дисциплины в парке отправления. Устройство обеспечивает:
-обработку тормозов при подключении тормозной сети состава и локомотива к питательным стационарным напольным колонкам, располагаемым в междупутье парка отправления;
-обработку тормозов состава;
-контроль пневматической части тормозов локомотива;
-непрерывный контроль на мониторе ПК за изменением утечки и давления воздуха
втормозной магистрали состава;
-регистрацию процессов подготовки тормозов;
-выдачу на основе измеренных параметров рекомендаций по ведению обработанного на маршруте с учетом местных инструкций и состояний автотормозов состава;
-создание пакета документов о работе ПТО («Справка об обеспечении поезда тормозами и исправном их действии»и др.);
-зарядку и опробование тормозов в полуавтоматическом режиме с дистанционным управлением процессами при использовании радиостанций.
Устройство включает в себя:
-пульт оператора парка ПОП, имеющий в составе: персональный компьютер ПК; принтер ПУ; блок связи БС; радиостанцию оператора РС;
-пульт дистанционного управления ПДУ, подключенный к радиостанции осмотрщика;
-блок БС;
-электрические коммуникации, предназначенные для обмена информацией между блоками устройства и подачи питающего напряжения на БПК;
-блок питательной напольной колонки БПК;
26
-пневматические коммутации, предназначенные для подвода воздуха от напорной сети парка к БПК;
-блок хвостового вагона БХВ, предназначенный для контроля давления в тормозной магистрали хвостового вагона.
9) Автоматизированная система контроля подвижного состава
Автоматизированная система контроля подвижного состава (АСК ПС) предназначена для автоматизации процесса сбора, передачи и обработки показаний аппаратуры контроля перегретых букс типа КТСМ с целью обеспечения централизованного контроля технического состояния поездов на участках движения. Контроль за показаниями аппаратуры контроля перегрева буксовых узлов вагонов осуществляется оператором центрального поста контроля АСК ПС регионального ДЦУП. При обнаружении в составе поезда вагона (локомотива) с повышенным уровнем нагрева буксового узла на экране монитора появляется информационное окно и раздается звуковой сигнал. В информационном окне выводятся данные о показании установки КТСМ, которые содержат: название пункта контроля, зафиксировавшего повышенный нагрев буксового узла с указанием направления (четное, нечетное), порядкового номера вагона в поезде, начиная с головы, порядкового номера оси вагона, стороны вагона и уровня нагрева буксового узла с каждой стороны вагона.
Комплекс технических средств АСК ПС представляет собой распределенную структуру специализированных аппаратно-программных комплексов, объединенных единой системой передачи данных. По своему функциональному назначению технические средства АСК ПС подразделяются на технические средства линейных пунктов контроля (ЛПК) и оборудование центрального поста контроля (ЦПК).
Применение комплексных систем технической диагностики подвижного состава позволяет повысить безопасность движения за счет выработки рекомендаций об индивидуальных объемах ремонта каждой единицы подвижного состава с учетом действительного технического состояния. Экономический эффект от внедрения указанной системы можно представить в виде трех составляющих. Первая составляющая экономического эффекта реализуется на сетевом уровне. Он связан с безопасностью движения, с уменьшением затрат энергии и топлива на тяговое усилие локомотивов, уменьшение числа повреждений стрелочных переводов и динамических нагрузок на путь. Вторая составляющая экономического эффекта реализуется за счет снижения затрат на техническое обслуживание. Третья составляющая экономического эффекта реализуется при повышении срока службы подвижного состава. Например, по данным опыта эксплуатации систем контроля и паспортизации колесных пар в США при профилактике достижения 50%-ного износа гребня бандажей колес срок службы или пробег колесной пары повышается на 20% [14,15].
27
Порядок выполнения работы
1.Описать назначение диагностических комплексов контроля технического состояния вагона на ходу поезда.
2.Представить в виде блок-схемы средства технической диагностики параметров грузовых вагонов, указать назначение и принцип действия СТД.
3.Ответить на контрольные вопросы.
Контрольные вопросы
1.Какие СТД предусмотрены для контроля параметров колесных пар на ходу
поезда?
2.Какие СТД предусмотрены для контроля параметров тормозного оборудования на ходу поезда?
3.Каково назначение блока хвостового вагона?
4.Что представляет собой станционное оборудование СТД? Где оно располагается?
5.Какие преимущества предоставляет применение комплексных систем технической диагностики подвижного состава?
Практическая работа № 6
ПРИМЕНЕНИЕ ЕДИНОЙ ТЕХНИЧЕСКОЙ ТЕХНОЛОГИИ ПРИ ТЕХНИЧЕСКОМ ОБСЛУЖИВАНИИ ВАГОНОВ (4 часа)
Цель работы: изучить единую техническую технологию при техническом обслуживании вагонов.
Краткие теоретические сведения
Вцелях приведения к единым требованиям технического обслуживания грузовых поездов на сортировочных станциях распоряжением ОАО «РЖД» от 13.07.2010 № 1518р на всех пунктах технического обслуживания грузовых вагонов сортировочных станций была введена в действие «Единая технология технического обслуживания составов грузовых поездов на сортировочных станциях» с 1 августа 2010 года [16].
Втехническом обслуживании вагонов принимают участие работники ПТО, работающие в должности осмотрщика-ремонтника вагонов. Техническое обслуживание вагонов проводится комплексной бригадой, состоящей из 2 функциональных групп. 1 группа осуществляет осмотр ходовых частей, автосцепного устройства, кузова вагона и пневматического оборудования с нанесением меловых разметок, а также полное опробование тормозов, ремонт пневматической части тормозного оборудования устранение утечек воздуха в тормозной магистрали; 2 группа проводит соединение тормозных рукавов, ремонт ходовых частей, автосцепного устройства и кузова вагона.
28
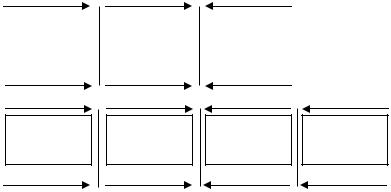
Технологическая численность осмотрщиков-ремонтников вагонов (ОВР) в зависимости от количества вагонов в составе поезда и норматива времени представлен в таблице 3. Порядок расстановки смотровых групп ОВР показан на рисунке 11.
Таблица 3
Технологическая численность ОВР в зависимости от количества вагонов в составе поезда и норматива времени
Количество |
|
|
Норматив времени |
Средний норматив времени на ТО с пролазкой, чел/мин |
|||||
вагонов в составе |
на осмотр 1 вагона, чел/мин |
|
|
|
|||||
|
время ТО |
Кол-во ОВР (групп х чел.) |
|||||||
|
|
|
|
|
|
|
|
|
|
до 51 |
2,32 |
|
|
30 |
4 (2х2) |
||||
|
|
|
|
|
|
|
|
|
|
до 77 |
2,32 |
|
|
30 |
6 (3х2) |
||||
|
|
|
|
|
|
|
|
|
|
до 103 |
2,32 |
|
|
30 |
8 (4х2) |
||||
|
|
|
|
|
|
|
|
|
|
1 группа |
|
|
2 группа 3 группа |
4 группа |
|
||||
а) |
|
|
|
|
|
|
|
|
|
|
|
|
|
|
|
|
|
|
|
|
|
|
|
|
|
|
|
|
|
б)
Рис. 11. Схемы расстановки ОВР в смотровых группах:
а – при 6 ОВР в составе бригады; б – при 8 ОВР в составе бригады
Сокращенное опробование тормозов поездам, которым предварительно полное опробование тормозов было проведено от стационарной установки УЗОТ, осуществляют 2 осмотрщика вагонов, не входящие в комплексную бригаду.
Встреча поездов своего формирования производит осмотрщик вагонов по сокращенному опробованию тормозов в хвостовой части состава с правой стороны. Контроль отправляемого поезда производит осмотрщик вагонов по сокращенному опробованию тормозов в головной части состава с левой стороны.
Разделение зон обслуживания поезда осмотрщикам-ремонтникам вагонов проводит оператор ПТО по натурному листу поезда, передавая номера сходных вагонов осмотрщикам-ремонтникам.
Оператор ПТО отмечает сходные вагоны в натурном листе, обеспечивает контроль количества осмотренных вагонов по докладу осмотрщиков-ремонтников, не допуская
29
неосмотренных вагонов. Номера сходных вагонов оператор вносит в график исполненной работы смены.
При производстве технического обслуживания осмотрщики-ремонтники вагонов на сходных вагонах обязаны нанести следующую меловую разметку на кузовах вагонов, бортах платформ, котлах цистерн:
осмотрщик головной группы – Т1; осмотрщики средней группы – Т2 (на обоих сходных вагонах), Т3 и т.д.
Информацию о выявленных неисправностях вагонов осмотрщик по радиосвязи передает оператору ПТО: номер пути, сторону осматриваемой части состава, наименование ремонтных работ.
В случае выявления при контроле технического состояния тормозного оборудования неисправностей, на боковых стенках кузова вагона (между угловой и боковой стойками), на бортах платформ, на котлах цистерн наносятся условные меловые пометки (таблицы 4; 5) [16].
|
|
Таблица 4 |
|
Вид работы |
|
|
|
|
Вид работы |
|
Шифр буквенный |
|
|
|
Сменить |
|
«С» |
|
|
|
Поставить |
|
«П» |
|
|
|
Проверить |
|
«Пр» |
|
|
|
Укрепить |
|
«У» |
|
|
|
Устранить |
|
«УС» |
|
|
|
Отремонтировать |
|
«Р» |
|
|
|
На концевой балке крайних вагонов наносится условная меловая разметка для смежной ремонтно-смотровой группы. Так, на концевой балке вагона, с которого начинается осмотр, наносят дату и букву «Н» (начало осмотра), а на котором заканчивается осмотр – дату и букву «К» (конец осмотра).
Разделение по количеству и назначению проходов при подготовке поезда своего формирования изображено на рис. 12–16 (для примера приведена схема технического обслуживания грузового поезда длиной 71 усл. ед., который условно делится на 6 зон для 1 группы и на 2 зоны для 2 группы и осматривается бригадой из 8 осмотрщиковремонтников вагонов – «6+2») [16].
30