
МАТЕРІАЛОЗНАВСТВО(судноперевізники)
.pdf6)фрикційні – мають високий коефіцієнт тертя, використовуються в гальмових пристроях;
7)звукота теплоізоляційні – мають здатність погано проводити звук і тепло, служать як звукота теплоізоляційні матеріали.
За хімічною природою основні пластмаси поділяють на такі види: поліолефіни, стиропласти, фторопласти, полівінілхлорид (поліхлорвініл), поліакрилати, поліметакрилати, фенопласт (поліметиленфеноли), поліаміди, целопласти та ін.
Поліолефіни (поліетилен, поліпропілен, поліізобутилен) одержують в результаті полімерізації етилену, пропілену, ізобутилену і інших неграничних вуглеводнів. Вони мають високі корозійну стійкість в агресивних середовищах (кислоти, луги, солі, органічні розчинники) та діелектричні властивості, добрі механічні та антифрикційні властивості, малу густину, високу вологота морозостійкість, відносно дешеві, сировина для їх виробництва недефіцитна. Основні недоліки полюлефінів – низька теплостійкість при нагріванні під навантаженням, підвищена усадка при твердненні і високий коефіцієнт термічного розширення,
Стиропласти одержують на основі стиролу Найбільше поширення мав полістирол, який утворюється в результаті полімерізації вінілбензолу. Він має високі діелектричні властивості, водостійкість, хімічну стійкість в кислотах і лугах, маслостійкість, малу густину, невелику усадку при твердненні, легко перероблюється різнимі методами. До недоліків полістиролу відносяться невелика міцність під дією динамічних навантажень і низька теплостійкість.
Фторопласти – фторопохідні етилену з різним ступенем заміщення в них водню фтором: полівініліденфторид, політрифторхлоретилен (фторопласт марок 3 і 3М), політетрафторетилен (фторопласт марок 4 і 4Д). До них відносяться також фторопохідні бутадієну (поліфторопрен та політетрафторбутадієн). Фторопласти мають високі антифрикційні та діелектричні властивості, теплостійкість у широкому інтервалі температур, надзвичайно високу корозійну стійкість майже до всіх агресивних середовищ, задовільну стійкість в умовах радіації, негорючість та водостійкість. Недоліки фторопластів: низька міцність, виділення отруйних газів при розпаді, відносно висока вартість та труднощі переробки у вироби.
Полівінілхлорид або поліхлорвініл (ПХВ) одержують шляхом полімерізації хлористого вінілу. Його випускають з пластифікатором (пластикат) та без пластифікатора (вініпласт). Пластикат – м'який матеріал, а вініпласт – твердий. Полівінілхлорид має високу корозійну стійкість до бензину, мастил, лугів і кислот, розчиняється лише в ацетоні і діхлоретані, має задовільні діелектричні властивості, негорючість. добру зварюваність, зносостійкість і малу вартість. Пластикат крім того має високі електроізоляційні властивості та вологостійкість. До недоліків полівінілхлориду відносяться низька теплостійкість, мала міцність пластикатів і крихкість, яка зростає по мірі старіння.
Поліакрилати одержують полімеризацією акрилової кислоти, а
поліметакрилати – полімерізацією метакрилової кислоти, їх основні
достоїнства: оптична прозорість, світлостійкість, нетоксичність, можливість переробки різними способами, водота бензостійкість. До недоліків відносяться низька теплостійкість, твердість, горючість, невисока стійкість в кислих середовищах. Типовим представником акрилатів є органічне скло, основне достоїнство якого – стійкість проти ударів.
Фенопласти (поліметиленфеноли) одержують на основі фенолоформальдегідної смоли, яка називається бакелітом. Як наповнювачі застосовують порошкові, волокнисті та шаруваті речовини. Фенопласти з порошковим наповнювачем (деревинне борошно або деревинне борошно з добавками меленої слюди та кварцового борошна), так звані преспорошки, одержали велике розповсюдження в промисловості, хоч мають відносно низькі міцностні та електроізоляційні властивості. У фенопластів, до яких як наповнювач входить деревинне борошно з добавками слюди та кварцу, ці властивості вище
Фенопласти з волокнистим наповнювачем (бавовняні пачоси, відходи текстильної промисловості, кордові нитки, азбестове волокно та скловолокно) називають волокнитами. Вони характеризуються досить високою міцністю, теплостійкістю та зносостійкістю, рівень яких залежить від виду наповнювача.
Фенопласти з шаруватими наповнювачами називаються шаруватими фенопластами. До них відносяться гетинакс, текстоліт, азботекстоліт та склотекстоліт, які відрізняються за видом наповнювача. Гетинакс містить, як наповнювач, папір, має високі діелектричні властивості. У текстоліті наповнювачем є бавовняна тканина. Він водо-, маслота бензостійкий і має високу механічну міцність. У азботекстоліті наповнювачем є азбестова тканина. Він має високу міцність, теплота кислотостійкість, добрі фрикційні властивості. У склотекстоліті наповнювачем є скляна тканина, яка характеризується високою міцністю, термостійкістю та добрими діелектричними властивостями. Склотекстоліт є також представником групи пластмас, об'єднаних спільною назвою – склопластики. Ці пластмаси, у яких наповнювач – скляні матеріали, а зв'язуюча речовина – термореактивні чи термопластичні синтетичні смоли. Крім склотекстоліту до склопластиків відносяться скловолокнисті анізотропні матеріали (СВАМ), стрічка однонаправлена скляна (СОС), анізотропні прес-матеріали марок АГ-4. АГ-4С, АГ-4В та ін.. склошифер, склопластик профільний тощо. Поєднання складових склопластиків і методів виготовлення визначає їх фізико-механічні властивості. Загальними позитивними властивостями є висока міцність, теплостійкість та хімічна стійкість в агресивних середовищах.
Поліаміди (анід, капрон та ін.) – високомолекулярні кристалічні полімери. Вони характеризуються високими механічними властивостями, стійкістю до лугів, розбавлених кислот палива та мастил, опірністю до абразивного зносу, низьким коефіцієнтом тертя, негорючістю, стабільністю розмірів, нетоксичністю, можливістю переробки різними способами. Поліаміди мають такі недоліки: малу водостійкість, старіння на світлі, низьку теплопровідність, нестійкість проти дії концентрованих кислот.
Целопласти (етроли) одержують на основі целюлози. Целюлоза – основна частина оболонки клітин рослинного волокна – відноситься до
високомолекулярних сполук. У промисловості їх одержують з деревини, соломи, бавовни, комишу, стеблини кукурудзи та інших рослин. Найстаршим представником целопластів є целулоїд, виробництво якого почалося ще в 1868 р. Основу його складає продукт обробки целюлози азотною кислотою – нітроцелюлоза. Целулоїд прозорий, погано проводить тепло, легко спалахує.
Пінота поропласти одержують на основі полістиролу, поліхлорвінілу, сечовиноформальдегідних смол тощо. Розплавлену основу під високим тиском насичують газами, вводячи спеціальні газоутворювачі (порофори), і одержують чарунковий (пінопласти) або пористий (поропласти), м'який або жорсткий матеріал. М'яку пластмасу звичайно називають губкою. Пінота поропласти мають надзвичайно малу густину, в середньому 0,05 – 0,1 г/см3, високі звуко-, тепло-та електроізоляційні властивості.
В багатьох випадках пластмаси служать повноцінними замінниками чорних та кольорових металів. В деяких галузях, наприклад, в суднобудуванні, вони є здебільше незамінними матеріалами.
1.3 Способи одержання виробів та напівфабрикатів із пластмас
Основними способами одержання виробів і напівфабрикатів із пластмас є пресування, лиття, видавлювання (екструзія), штампування тощо.
Пресуванням називається обробка пластмас у прес-формах під тиском. Розрізняють звичайне та ливарне пресування.
Звичайне пресування (рис. 33, а) поділяють на холодне та гаряче.
При звичайному пресуванні потрібне точне дозування зерен або порошку пластмаси, яка завантажується у вигляді таблеток. При гарячому пресуванні прес-форми підігрівають до 130 – 160 °С парою, газом або електричним струмом. В багатьох випадках підігрівають також пластмасу до 100 – 150 °С. Для цього використовують струм високої частоти, що викликає виділення теплоти всередині матеріалу. Внаслідок підвищується продуктивність праці і зменшується тиск при пресуванні.
Для пресування служать гідравлічні, пневматичні та механічні преси. Пластмасу засипають у нагріту прес-форму, виготовлену з інструментальної вуглецевої високоякісної або легованої сталі. Пластмаса розігрівається і стає пластичною. Потім створюють тиск, під дією якого розм'якшена маса заповнює прес-форму і після витримки під тиском твердне.
Спосіб гарячого пресування придатний лише для термореактивних пластмас, бо нагрівання і наступне охолодження значно знижують продуктивність праці.
Ливарне пресування (рис. 33, б) відрізняється від звичайного тим, що пластмаса розм'якшується не в камері прес-форми, а в спеціальній завантажувальній (передаточній) камері, яка з'єднана з камерою прес-форми одним або кількома литниками. Цей спосіб дозволяє одержати точні за розмірами вироби складної форми, зокрема з заглибленнями, отворами, різьбою.

Рисунок 33 – Види пресувань. |
Рисунок 34 – Схема контактного |
а – звичайне; б – ливарне; 1– матриця; |
формування корпуса судна: |
2 – вироб; 3 – пуансон; |
1– форма; 2 – роздільний шар; |
4 – завантажувальна камера. |
3– шар смоли; 4 – склотканина |
Лиття виробів та напівфабрикатів з пластмас здійснюється без тиску та під тиском. Перший спосіб, коли розплавлену пластмасу заливають у форму, де вона твердне, набуваючи потрібні розміри та форму, застосовують рідко через малу продуктивність. В основному здійснюють лиття тиском, яке виконують на спеціальних напівавтоматичних та автоматичних машинах.
Видавлювання полягає у виштовхуванні пластмаси через мундштук з отвором, переріз якого визначає форму виробу або напівфабрикату. Екструзія є високопродуктивним способом переробки пластмас.
Штампування застосовують для виготовлення виробів з пластмасової листової заготовки. Штампують целулоїд, вініпласт, органічне скло, полістирол, поліетилен, поліпропілен тощо.
Існують спеціальні способи виготовлення великогабаритних виробів:корпусів суден, кузовів автомобілів, фюзеляжів літаків і ін. Найбільш широко розповсюджений спосіб контактного формування (рис. 34), який полягає у послідовному ручному укладанні шарів склотканини на форму і просочуванні кожного шару зв'язуючою смолою. При виготовленні корпуса судна цим способом спочатку роблять форму з дерева або гіпсу. Поверхню форми вкривають розділювальною речовиною (воском або целофаном), що перешкоджає прилипанню до неї пластмаси. Потім на поверхню форми наносять шар смоли і укладають шар склотканини. Смолу наносять щіткою, валиком або пістолетом-розпилювачем. Перший шар склотканини прокатують роликами-катками наносять шар смоли і знову укладають склотканину. Таким чином, корпус судна складається з шарів, кількість яких визначається необхідною товщиною корпуса.
1.4 Застосування пластмас у суднобудуванні
В суднобудуванні, як і в інших галузях промисловості, застосування пластмас з кожним роком розширюється. З пластмас виготовляють оздоблення кают та службових приміщень, суднові меблі, арматуру суднових систем, труби вентиляції та холодної води, легкі вигородки, деталі радіота електрообладнання, теплота звукоізоляцію приміщень та ін. З пластмас будують корпуси дрібних суден, вітрильних яхт, шлюпок різних типів,
282
транспортних, прогулянкових та рятувальних катерів. Пластмасовий корпус міцний, не піддається корозії та обростанню, не потребує фарбування, легкий, довговічний та немагнітний.
Особливо велика роль пластмас як замінника дефіцитних та дорогих металів. Високий економічний ефект дає застосування пластмас замість кольорових металів (міді, алюмінію, цинку, олова, свинцю та їх сплавів), бо вартість пластмас в десятки разів нижче вартості кольорових металів. Використання пластмас замість чорних металів дає певний виграш у вартості, а також дозволяє зменшити масу конструкції, що особливо важливо при будуванні невеликих суден. Порівняно недавно почали виготовляти гребні гвинти з пластмас, внаслідок чого знизилась їх маса, значно зменшилась вартість та підвищилась довговічність. Такі властивості пластмас, як корозійна стійкість, немагнітність, звукопоглинання та мала теплопровідність, мають особливе значення для суднобудування.
З органічного скла в суднобудівній промисловості виготовляють плафони, стекла ілюмінаторів, світильників, сигнальних ліхтарів тощо. Воно добре піддається слюсарній, фрезерній, токарній обробці, легко склеюється.
Полістирол служить для виготовлення радіота електротехнічних виробів (лампові панелі, каркаси котушок, баки для кислотних акумуляторів та ін.), деталей хімічної апаратури, плафонів світильників, плиток для облицювання санітарно-гігієнічних приміщень і ін.
Поліетиленові труби відзначаються легкістю (приблизно у 8 раз легше сталевих), високою корозійною стійкістю, малим опором руху рідин, здатністю поглинати шум рухомої рідини, морозостійкістю. При замерзанні води труби не руйнуються, а лише трохи деформуються. Поліетиленові труби придатні для баластної, осушувальної, питної та інших водопровідних систем. Гнучкі поліетиленові труби діаметром до 63 мм поставляють згорнутими в бухти. З листового поліетилену роблять прокладки для трубопроводів стиснутого повітря, масла та палива. Він добре піддається механічній обробці і зварюється нагріванням гарячим повітрям або електронагрівачами.
Вініпласт служить для виготовлення ванн, баків, трубопроводів, резервуарів, арматури, дверей, барельєфів та ін. Вініпласт легко пиляти, стругати, гнути, штампувати, зварювати та склеювати. Зварювання здійснюють з присадкою (вініпластовими стержнями) і без присадки за допомогою гарячого повітря, що подається спеціальним апаратом. При нанесенні пасти вініпласту на тканини одержують оздоблювально-декоративні матеріали (текстовініт, автобім, павінол), а також лінолеум, стійкий проти стирання.
Пластикат застосовують для виготовлення оболонок електричних кабелів та як оббивні та прокладочні матеріали. З фторопласту виготовляють електро- і радіотехнічні деталі, прокладки, набивки, манжети, сільфони, труби, крани та ін. Гетинакс іде на виготовлення деталей радіота електроапаратури, деталей меблів, зубчастих коліс, втулок, облицювання внутрішніх легких переборок та вигородок, електроізоляційних деталей та ін.
Із текстоліту роблять набори втулок кронштейнів гребних валів, вкладишів підшипників дейдвудних пристроїв, безшумних зубчастих коліс,
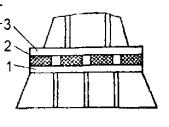
282
блоків, роликів і ін. При використанні для змащування забортної води текстолітові підшипники мають низький коефіцієнт тертя і високу зносостійкість. Недоліком його як підшипникового матеріалу є низька теплопровідність, що ускладнює відведення тепла. Дейдвуди; підшипники з текстолітовими вкладишами можуть працювати лише при достатньому надходженні води, інакше вкладиші починають оплавлятися та обвуглюватися.
Із азботекстоліту роблять різні гальмові пристрої, прокладки механізмів зчеплення та ін. Фенопласти у вигляді преспорошку застосовують для виготовлення деталей обладнання суднових приміщень, корпусів приладів судноводіння, багатьох електрорадютехнічних деталей, гальмових колодок та ін.
Із склопластиків будують рятівні шлюпи, прогулянкові та службові катери, спортивні судна, моторні човни, а також судна інших призначень з довжиною корпуса 60 м і більше. Із склопластиків виготовляють легкі переборки, вигородки, меблі та фурнітуру, двері, кришки, трапи, деталі суднового устаткування та пристроїв, трубопроводи (води, палива, масла), цільнопластмасові гребні гвинти малих і середніх розмірів, лопаті великих гребних гвинтів та ін.
Поліаміди (капрон, капролон і ін.) застосовують для виготовлення підшипників суднових механізмів, вкладишів підшипників валопровода, гребних гвинтів, трубопровідної арматури та ін. Пінота поропласти використовують для теплота звукоізоляції кают і спеціальних приміщень, а також амортизуючих матеріалів при виробництві меблів та інших речей.
Швидкотверднучі пластмаси (БКД, ФМВ та ЖМ250) являють собою суміші на основі синтетичних смол. їх застосовують у тістоподібному вигляді як компенсуючи прокладки при монтажних роботах при встановленні суднових машин і механізмів (рис. 35). В результаті значно підвищується продуктивність праці, тому що повністю виключається ручна пригонка, необхідна при установленні сталевих компенсуючих прокладок, та обробка опорних поверхонь фундаментів.
Рисунок 35 – Монтаж механізму на пластмасовій прокладці:
1 – судновий фундамент; 2 – пластмасова прокладка; 3 – фундамент механізму.
Пластмасу БВД (бакеліт + контакт Петрова + деревинна тирса) використовують для прокладок під нецентровані допоміжні механізми при установленні їх на фундамент. їх готують на місці з бакелітової смоли (зв'язуюча речовина), контакту Петрова (затвердник), деревинної тирси
282
(наповнювач) та води. Остаточно затверділа пластмаса не руйнується під дією води, машинних масел та рідкого палива. З підвищенням температури вона не розм'якшується і не горить.
Оскільки пластмаса БКД при твердненні дає значну усадку (до 4 % і більше), її не можна застосовувати при установленні центрованих механізмів. В цьому випадку використовують пластмасу ФМВ (формуєма малоусадочна волокниста), яка являє собою композицію, виготовану на місці з епоксидної смоли (зв'язуюча речовина), скловолокна та азбестового волокна (наповнювачі), поліетиленполіаміну (затвердника), дібутилфталату (пластифікатора). Властивості пластмаси ФМВ при підвищенні температури та заморожуванні не змінюються. Вона стійка проти дії нафтопродуктів та морської води, не горить і не виділяє шкідливих речовин. Недоліком її є підвищена адгезія (прилипання) до металу. Внаслідок малої усадки пластмаси ФМВ (0,2 – 0,4 %) зберігається центровка механізмів при зніманні тимчасових болтів та обтискуванні штатними (постійними) болтами.
Пластмасу ЖМ250 (рідкотекуча малоусадочна з 250 % наповнювача) застосовують в тих випадках, коли потрібно забезпечити міцне водонепроникне кріплення суднових механізмів на фундаменті. їх готують на місці з епоксидної смоли (зв'язуюча речовина), залізного порошку (наповнювач), поліетиленполіаміну (затвердника) та дібутилфталату (пластифікатор). При твердненні пластмаса ЖМ250 майже не дає усадки.
Глава 2 ІНШІ НЕМЕТАЛЕВІ МАТЕРІАЛИ
2.1 Гумові матеріали та клеї
Гумові матеріали займають значне місце у промисловості, зокрема в суднобудуванні. Висока еластичність (подовження при розтягуванні досягає 800 %), звукопоглинання та корозійна стійкість, достатня механічна міцність та добрі електроізоляційні властивості – основні якості, завдяки яким гума одержала розповсюдження в техніці. З неї виготовляють шини, ремені, стрічки, напорні та всмоктуючі рукава, манжети, сальники, прокладки, ізоляцію проводів і кабелів, шланги, бачки акумуляторів, деталі електрообладнання та радіоапаратури, предмети масового вжитку тощо. Вихідна сировина для одержання гуми – каучук, який за походженням ділять на натуральний та синтетичний.
Натуральний каучук (НК) одержують з латексу, який являє собою молочно-білу речовину, що видобувається з каучуконосних рослин (бразильської гевеї, коксагизу та ін.). Каучукова маса утворюється внаслідок коагуляції латексу, на який діють 5 %-ним розчином оцтової кислоти. Одержану масу просушують і вальцюють в листи.
Натуральний каучук при температурі від -70° С до +70 °С дуже еластичний, при температурі нижче -70 °С стає крихким, а вище +70 °С плавиться. Він не розчиняється і не поглинає воду, спирт, ацетон та інші
282
рідини; з жирними та ароматичними вуглеводними утворює в'язкі розчини, які використовують як клей.
Синтетичний каучук (СК) одержують синтезом простих органічних речовин. На даний час відомо декілька десятків видів синтетичного каучуку, які відрізняють за вихідною сировиною, складом та фізико-механічними властивостями. Як каучукогени (основа) для одержання синтетичного каучуку застосовують бутадієн, стирол, хлоропрен, акрилонітрил, ізобутилен і ін. Ї х одержують з нафтопродуктів, природного газу, ацетилену, деревини тощо.
Для одержання гуми застосовують, такі синтетичні каучуки: бутадієн-стирольний, бутадієн-нітрильний, поліхлоропреновий, поліуретановий, бутадієн-метилвінілпіридиновий, уретановий, кремніймісткий. фторомісткий та ін.
Вбільшості випадків застосовують синтетичний каучук, який дешевше натурального, а за своїми властивостями близький до нього. Синтез каучуку в великому заводському масштабі вперше у світі було здійснено в 1932 р. в СРСР за способом, розробленим С.В.Лебедєвим.
Гуму одержують внаслідок переробки каучуку (вулканізації), яка сприяє підвищенню його еластичності, вібростійкості, хімічної стійкості, морозостійкості, стійкості проти стирання та старіння. В залежності від ступеня вулканізації і вмісту сірки (основної вулканізуючої речовини) розрізняють м'яку, напівтверду та тверду гуму. Тверду гуму (ебоніт) одержують при тривалому нагріванні (протягом 20 г) гумової суміші з 45 % сірки. Ебоніт має високу механічну міцність і твердість, добрі електроізоляційні властивості та стійкість проти агресивних середовищ. Існує гаряча та холодна вулканізація. Гарячу вулканізацію виконують в гарячому повітрі, гарячій воді або атмосфері насиченої водяної пари. При холодній вулканізації каучук обробляють розчином напівхлористої сірки.
Всуднобудуванні використовують: гумові вкладиші підшипників гребних та дейдвудних валів; ущільнюючі елементи горловин, кришок люків, ілюмінаторів та водогазонепроникних дверей; прокладки та набивки водяних, масляних та паливних суднових систем; амортизаційні вставки систем спеціальних суден; ізоляційні покриття суднових електричних кабелів і проводів; антикорозійні покриття; шланги та рукава; надувні плоти; рятівні конструкції; правильні пристрої тощо. Широко застосовують гуму при
виготовленні амортизаторів, на які установлюють суднові прилади і механізми для того, щоб зменшити їх вібрацію (коливання) та виключити передачу на корпус судна шумів від працюючих двигунів. Найбільше розповсюдження в суднобудуванні мають амортизатори типу КАС (корабельний амортизатор зварний), АКСС (амортизатор корабельний зварний із страхуванням), АПС (амортизатор пластинчастий зварний) (рис. 36).
Клеї являють собою речовини, які за своїми специфічними властивостями здатні міцно з'єднувати однакові або різні за складом матеріали, їх широко застосовують у промисловості для з'єднання окремих деталей та елементів конструкцій, виготовлених із металевих і неметалевих матеріалів.

282
Рисунок 36 – Амортизатор типа АКСС:
1 – сталевий корпус; 2 – гума; 3 – сталева втулка.
В суднобудуванні склеюють деталі, меблів, дерев'яні, металеві і пластмасові корпусні конструкції, елементи пристроїв, приклеюють ізоляцію, лінолеум, гуму тощо. Спосіб з'єднання деталей склеюванням прискорює, спрощує та полегшує технологічний процес збирання або виготовлення виробів і конструкцій, дозволяє зменшити їх масу.
Процес склеювання оснований на адгезії клею з поверхнею виробу, внаслідок чого утворюється з'єднання необхідної міцності При склеюванні неметалевих матеріалів (дерева, гуми, пластмаси, шкіри та ін.) можуть бути одержані сполуки, рівноміцні склеюваним матеріалам, а іноді і вище. При склеюванні металевих матеріалів лише конструкційні (силові) клеї нових марок можуть забезпечити рівноміцність з'єднань.
Клеї, які використовуються в суднобудуванні, за походженням поділяють на дві основні групи: природні і синтетичні.
До природних клеїв відносяться: міздровий, кістковий, казеїновий та рослинний. Міздровий клей виробляють з відходів шкіряної та м'ясної промисловості. Випускають міздровий клей у вигляді плиток або порошку і застосовують при склеюванні дерев'яних конструкцій. Казеїновий клей являє собою порошкоподібну суміш подрібненого технічного казеїну (знежиреного молока), лугів (гашене вапно) та мінеральних солей (мідного купоросу, фтористого натрію та ін.). Призначений для приклеювання захисних тканин і ізоляції в умовах підвищеної вологості, тому що має більш високу у порівнянні з іншими природними клеями водостійкість. Рослинний клей готують з борошневого пилу, питльованого борошна і різних видів крохмалю Використовують для наклеювання тканин на зовнішню поверхню ізоляції трубопроводів і конструкцій. Природні клеї в суднобудуванні застосовують досить рідко, тому що з'єднання, виконані ними, мають низьку водостійкість і потребують тривалої витримки після склеювання та захисту від зволоження.
Синтетичні клеї мають більш високі властивості і широко застосовуються в суднобудуванні. За призначенням їх ділять на три групи: конструкційні; для обробних матеріалів, гуми та керамічних покриттів; для теплота звукоізоляційних матеріалів.
До групи конструкційних клеїв відносяться: епоксидно-поліамідний (ЕПК-518, ЕПК-519, ЕПК-520), епоксидно-тіоколовий (К-153), епоксидний (КВС-1. КВС-2, КВС-3, ЗК-1 та ін.) епоксидно-поліуретановий (ВК-16),
епоксидно-каучуковий (ВК-17), поліуретановий |
(ВК-5), кремнійорганічний |
|||
(ВК-15), |
бутилметакрилатний |
(КС-609), |
фенолакрилатний |
(ВК-І4), |
282
фенолоформальдегідний (ВІАМ-Б-3), сечовино-формальдегідний (К-17) та ін. Вони призначені для склеювання різких конструкційних матеріалів. Наприклад, клей марки ВІАМ-Б-3 застосовують для склеювання, в основному, деревини та деревинних матеріалів, текстоліту та поліхлорвінілу. Склеювання проводять при температурі 15 – 25 °С та тиску 0,2 – 0,4 МПа. Тривалість тверднення від 12 до 18 г. Клеєве з'єднання можна експлуатувати при температурі від -25 °С до
+80 °С.
Клей марки К-153 призначений для склеювання сталі і шаруватих пластиків. Склеювання необхідно виконувати при температурі 20 – 30 °С і тиску 0,002 – 0,5 МПа; тривалість тверднення від 24 до 48 г. Вироби допускається експлуатувати при температурі від -30 ° до +60 °С.
Клей марки ВК-1 склеює сталь, алюмінієві та титанові сплави, склотекстоліт. Склеюють при температурі 100 – 150° С і тиску 0,02 – 0,2 МПа; тривалість тверднення близько 10 г. Вироби можна експлуатувати при температурі від -60 до +150 °С.
До групи клеїв для обробних матеріалів, гуми та керамічних покриттів відносяться: епоксидно-перхлорвініловий (ПЕД-Б), нітроглифтальовий (ЛКС-Т), полівінілацетатний (ПВА-П, ПВА-Е, ЕКП), цементно-латексний (целаліт), бутифенолоформальдегідний (88-НС, 88-НП), гумовий (ВКР-17) та ін. Наприклад, клей марки ПЕД-Б застосовують для склеювання вініпласту та поліхлорвінілу, а також приклеювання їх до металу, дерева, бетону. Клей марки ЛКС-Т використовують для склеювання лінолеуму та приклеювання його до металу, деревини, бетону та склопластика. За допомогою клею типу «целаліт» приклеюють керамічні плитки. Клей марок 88-НС та 88-НП служить для склеювання та приклеювання пуми та інших обробних матеріалів до металу, бетону, деревини та склопластика.
Для склеювання обробних матеріалів та приклеювання їх до поверхонь суднових конструкцій застосовують також конструкційні клеї марок; ЕПК-5І8, ЕПК-5І9. ЕПК-520, К-153 та ін. Для теплота звуко-ізоляціїних матеріалів застосовують нітроглифтальовий (ЛКС), феноло-формадьдегідний (ІДС та ІДС-Т). цементно-латексний (целаліт-3, целаліт-4), поліхлорпреновий (НІР) та інші клеї. Промисловість випускає велику кількість клеїв різних марок і виробництво їх безперервно розширюється.
2.2 Лакофарбові матеріали
На морському транспорті лакофарбові матеріали, широко застосовують для захисту металевого корпуса судна, механізмів та обладнання від корозії, а дерев'яних конструкцій від гниття, охорони підводної частини корпуса судна від обростання, для декоративної обробки приміщень, обладнання та ін.
Склад лакофарбових матеріалів. Лакофарбові матеріали складаються з таких основних речовин: плівкоутворюючих (зв'язуючих), пігментів, сикативів (сушок), розчинників, розріджувачів та наповнювачів.
До плівкоутворюючих речовин відносяться висихаючи масла, оліфа, природні смоли, штучні та синтетичні плівкоутворюючі. Вони сприяють