
книги / Транспортные машины и комплексы
..pdf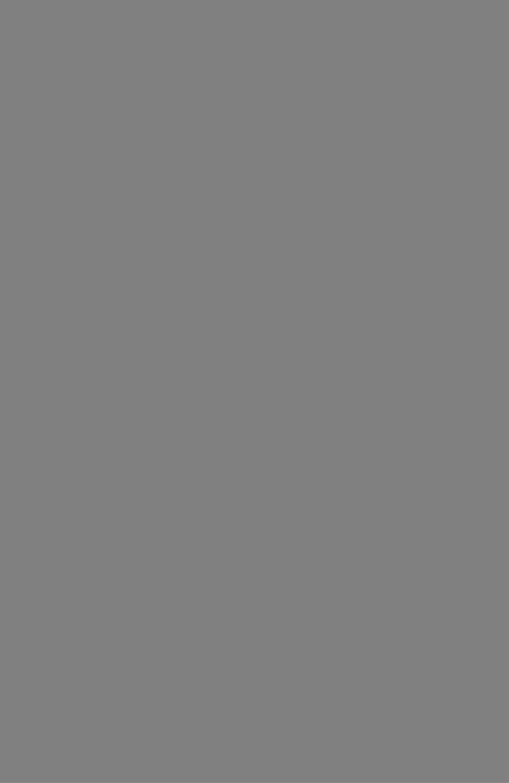
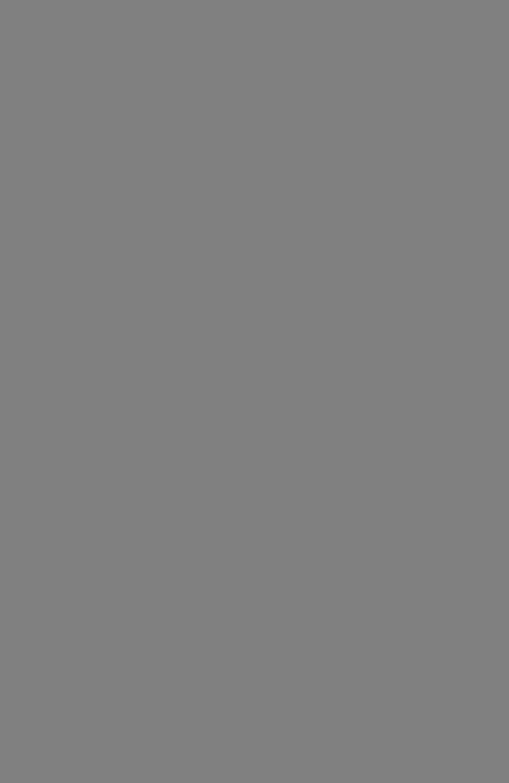
В настоящее время разрабатывается более мощный монорель совый дизелевоз (60—70 л. с.), в котором тяговые колеса прижи маются к вертикальной полке монорельса с помощью системы ры чагов и гидравлических цилиндров. Такие дизелевозы, как пока зывает опыт, имеют две секции (рис. 127), в одной из которых уста новлен дизель с гидравлической станцией, а во второй — кабина машиниста и гидроуправление.
Глава XIV
АВТОМАТИЗИРОВАННЫЕ КОМПЛЕКСЫ ПОГРУЗОЧНЫХ И РАЗГРУЗОЧНЫХ ПУНКТОВ
§ 1. ОБЩИЕ СВЕДЕНИЯ
На стыке двух видов шахтного транспорта, конвейерного и рельсового (непрерывного и прерывного), размещены перегрузоч ные пункты. К ним относятся стационарные, полустационарные и временные погрузочные пункты, где вагонетки загружаются с конвейера или из емкости. От пропускной способности погрузоч ного пункта зависит нагрузка на лаву, цикличность и интенсив ность ее работы. От равномерности работы подземных разгрузоч ных пунктов в околоствольных дворах и их пропускной способ ности зависит нагрузка на шахту, цикличность и производитель ность работы всех технологических звеньев от забоев до пунктов отгрузки продукции с территории шахты. Поэтому производи тельность и надежность конструкций комплекса погрузки или раз грузки на подземном транспорте приобретают важное значение.
Главное требование, предъявляемое к комплексу, — четкое и бесперебойное выполнение операций по заданной программе. В об щем виде процесс погрузки состоит из следующих групп операций: подачи порожняка, заполнения вагонеток, вытягивания груженого состава. Процесс разгрузки состоит из групп операций: подачи груженого состава, последовательного опорожнения вагонеток и вытягивания порожняка. В автоматизированных комплексах, созданных для этих процессов, предусматриваются системы упра вления, которые своевременно и последовательно включают и вы ключают исполнительные механизмы, средства контроля и отбора информации, чтобы обеспечить равномерное и полное заполнение или опорожнение вагонеток при установленном режиме. В состав автоматизированных комплексов погрузки или разгрузки входят механизмы для выполнения операций перемещения состава ваго неток, торможения, загрузки или разгрузки вагонеток, уплотне ния угля в вагонетке или очистки вагонеток от остатков угля, а также элементы, обеспечивающие автоматическое выполнение операций. К последним относятся: исполнительные устройства для обеспечения дистанционного и автоматического управления;
датчики для контроля правильного выполнения последовательных операций и отбора информации; средства местного управления для обеспечения наладки и ремонта; устройства автоматического ре гулирования; средства автоматической защиты от аварийных си туаций, автоматического учета работы, производственной и ава рийной сигнализации.
Автоматизированные комплексы механизмов для погрузки и разгрузки угля всех разновидностей являются комплексами цик личного действия, механизмы которых выполняют возвратно-по ступательное или возвратно-вращательное движение, а программа управления состоит из последовательно повторяемых операций.
Можно представить структуру автоматизированного погрузоч но-разгрузочного комплекса как взаимосвязь механизмов, устрой ств и датчиков, выполняющих подготовительные, главные, заклю чительные и вспомогательные операции. Механизмы и устройства* выполняющие подготовительные операции, подразделяются на тяговые, установочные или фиксирующие, и вспомогательные — взвешивающие, сигнализирующие и др. Механизмы, выполняющие главную операцию, делятся на загрузочные в комплексах погрузки, разгрузочные в комплексах разгрузки и на сопутствующие меха низмы вспомогательных операций — уплотняющие или очища ющие. Механизмы, выполняющие заключительные операции, под разделяются на тяговые, вспомогательные — по отбору проб и взвешиванию, на сигнализирующие и др. В состав автоматизиро ванного комплекса не включаются механизмы, выполняющие внецикловые операции при подаче очередного состава и установке головной вагонетки на толкающий механизм комплекса.
Для бесперебойной работы автоматизированного комплекса необходимо обеспечить постоянный запас вагонеток. Кроме того* в процессе погрузки необходимо обеспечивать постоянную подачу угля участковым транспортом, а в процессе разгрузки — постоян ный отбор угля из приемных устройств.
Суммарная продолжительность времени, в течение которога выполняются все операции по загрузке или^разгрузке одной ва
гонетки — подготовительные 2*п0д| главная trjl, заключитель
ные 2*зак> вспомогательные 2*всп> называется периодом цикла комплекса. Поскольку в каждой операции совершаются рабочий и холостой ходы, продолжительность которых составляет £р и £х* то период цикла Т равен:
?Т= 2*Р+2**= 2 (* Р + * х )п о д + 2 (*Р~Ь* х )г л + 2 (*р +*х)зак + |
|
+ 2 ( * р + *«)всп- |
(241) |
Уравнение периода цикла дает представление о распределении времени при выполнении операций по загрузке и разгрузке ваго неток. Период цикла является исходной величиной для определе ния пропускной способности комплекса и выявления резервов еа повышения. Уменьшение периода цикла может быть достигнуто
за счет сокращения холостых ходов, вспомогательных операций, продолжительности выполнения всех операций, в том числе глав ной операции. Последнее связано с повышением средней скорости выполнения операций и ограничено технологическими возможно стями. Средняя скорость выполнения операций за цикл показана на циклограмме, построенной в виде функции пути движения ва гонетки от продолжительности ее загрузки или разгрузки. На циклограмме (рис. 128) отражаются непрерывность движения
Рве» 128» Фактическая циклограмма автоматизированного комплекса APC3 для разгрузки нерасцепленных составов в околоствольных дворах:
Z — путь вагонетки; 2 — поворот барабана опрокидывателя; 3 — рабочий ход цилинд ров платформы и вытягивателя; 4 — холостой ход цилиндров и вытягивателя
вагонетки, расстояния продвижения вагонеток, моменты начала и конца работы толкающих и других механизмов, продолжитель ность и скорость операций, совмещение операций. При остановках вагонеток во время погрузки или разгрузки на циклограмме обра зуются соответствующие ступени, по которым можно судить о пов торных включениях тяговых механизмов, что важно для динами ческого расчета комплекса. Графически можно определить на цик лограмме среднюю скорость выполнения цикла по углу между линией движения вагонетки и абсциссой:
P = tgq> = -f-* |
(242) |
|
где S — путь, пройденный |
вагонеткой за цикл, |
м; |
v — средняя скорость |
за цикл, м/с; |
|
Т — период цикла, с. |
|
|
Составные элементы периода цикла определяются расчетным путем по хронометражным замерам или по снятым осциллограм мам работы. Замеренные в условиях эксплуатации продолжитель ности отдельных операций имеют отклонения от номинальных зна чений. Например, продолжительности включений и отключений ме ханизмов неодинаковы при допустимых колебаниях напряжения тока; продолжительности рабочих ходов толкающих механизмов и переключений загрузочных устройств неодинаковы при измене
нии давления в гидросистемах и т. д. Среднее значение периода t
цикла Т = определяется методами математической стати-
/-1 стики. Для этого необходимо располагать определенным масси
вом выборки по периоду цикла комплекса. Располагая програм мой для конкретной ЭВМ, можно определить величину математи ческого ожидания, т. е. среднее значение фактического периода цикла.
Производительность автоматизированного погрузочно-разгру зочного комплекса зависнув основном от продолжительности холо стых ходов по операциям, совмещения операций по времени, не прерывности выполнения операций, скорости выполнения опера ции и продолжительности автоматизированных операций в течение одного цикла.
Влияние холостых ходов характеризуется с помощью коэффи циента кх, который представляет собой отношение общей про должительности холостых ходов во всех операциях в течение цикла
к периоду условно несовмещенного цикла: |
|
*х = Т + а |
(243) |
где а — продолжительность совмещения операций за цикл.
К холостым ходам относится часть операций, связанная с воз вратом механизмов в исходное положение и их отключениями после выполнения заданной работы.
Совмещение операций, выполняемых комплексом за цикл, определяется с помощью коэффициента кс, который представляет собой отношение продолжительности совмещения операций за один цикл к периоду условно несовмещенного цикла:
*с = |
а |
(244) |
|
Т + |
|||
|
а * |
Непрерывность работы комплекса характеризуется с помощью коэффициента непрерывности /сн, который определяется отноше нием продолжительности рабочего хода главной операции к пе риоду цикла:
Если применяемые в комплексе механизмы обеспечивают протягивание состава, не прерывая операцию 8агрузки или разгрузки, то показатель непрерывности равен единице, а его влияние на про изводительно сть наибо лыпая.
Сравнением продолжительности выполнения рабочего хода главной операции с периодом условно несовмещенного цикла опре деляется коэффициент темпа работы комплекса:
кт |
11\п |
(246) |
|
Т + а |
|||
|
* |
Продолжительность автоматизированных операций характе ризуется с помощью коэффициента Аа, выраженного отношением общей продолжительности автоматически выполняемых операций в цикле к периоду условно несовмещенного цикла:
* . — т £ г - |
<М 7 > |
Перечисленные коэффициенты (холостых ходов, совмещения операций, темпа работы, продолжительности автоматизированных операций) называются характерными показателями комплекса. Все они, вместе взятые, представляют собой сумму факторов, ока зывающих самое существенное влияние на производительность автоматизированного погрузочно-разгрузочного комплекса
ваг./ч. (248)
В комплексах погрузки и разгрузки применяются в качестве тяговых устройств локомотивы, толкатели и лебедки. Локомотивы практически позволяют подавать большие составы, длина которых ограничивается возможностями пункта погрузки или разгрузки. Однако их применение в погрузочно-разгрузочных комплексах, особенно для составов вагонеток с глухим кузовом, не всегда выгодно по экономическим соображениям. Схема дистанционного управления и автоматического регулирования скорости локомо тива достаточно сложна, а расход электроэнергии выше, чем у дру гих тяговых устройств. Лебедки же не рекомендуются для приме нения в автоматизированных комплексах, поскольку вытяжка каната нарушает установленные фиксированные положения, за данные программой. Кроме того, при наличии лебедок сохра няются ручные операции по прицепке и растяжке каната. Наибо лее рациональным средством, применяемым для перемещения со става, является толкатель, устанавливаемый в наиболее удобном месте.
В автоматизированных транспортных комплексах важное зна чение приобретают установочные или фиксирующие устройства, от которых зависит точность выполнения заданной программы про
цесса загрузки или разгрузки. К ним относятся тормозные устрой ства и путевые стопоры. Их конструктивное исполнение и усло вия торможения диктуются назначением и местом установки.
Загрузочные или разгрузочные устройства, применяемые в ком плексах, обеспечивают точное выполнение операций, направлен ных на обеспечение непрерывности потока угля. Их конструкция выполняется применительно к конкретным условиям и типам ваго неток.
Учет добычи угля, поступающего на пункт погрузки, ведется с помощью конвейерных весов, устанавливаемых на подающем конвейере. Конвейерные весы делятся на тензометрические, электрогидравлические и электроимпульсные. На угольных шахтах внедрены взрывобезопасные электрогидравлические конвейерные весы типа ЭГВ.
Важное значение имеет полное использование объема вагоне ток в процессе их загрузки. Для этого применяют уплотняющие устройства, среди которых распространение получили установки с навесными взрывобезопасными вибраторами направленного дей ствия типа ВНДВ.
В подземных автоматизированных погрузочно-разгрузочных комплексах применяются следующие средства во взрывобезопас ном исполнении: для автоматического регулирования скорости движения состава; скорости потока или проходного сечения за грузочных или разгрузочных устройств; отбора информации о типе вагонетки^и ее положении, о правильности загрузки и др.; пере работки и выдачи информации о весе отгруженного состава, но мере локомотива, о марке и качестве отгруженного угля и др. Соответственно различаются по функциональным и конструктив ным признакам применяемые датчики, исполнительные механизмы, регуляторы и др.
Автоматизированные погрузочно-разгрузочные комплексы раз личаются по конструктивным и кинематическим признакам. Они делятся на агрегатированные и составленные из отдельных меха низмов. Первые представляют собой кинематически связанные конструкции механизмов, имеющие единые опорные базы и еди ные системы управления. Вторые представляют собой набор са мостоятельных механизмов, предназначенных для выполнения от дельных операций, связанных между собой только системой упра вления. Агрегатированные комплексы отличаются значитель ными преимуществами: меньшее число приводов, применение об щей насосной установки при наличии гидравлических исполни тельных механизмов и приводов, упрощение системы управления, ускорение цикла выполняемого процесса за счет уменьшения числа холостых ходов и большего совмещения операций, повышен ная надежность, компактность конструкции и уменьшение про изводственной площади. Основными требованиями, предъявляе мыми к автоматизированным комплексам, являются эксплуата ционные и конструктивные.
Эксплуатационные требования направлены на обеспечение за данного технологического режима, высоких показателей произ водительности, безотказности работы комплекса, соблюдения пра вил эксплуатации и безопасности работ, удобства монтажа и ре монта, снижения эксплуатационных расходов и др.
Конструктивные требования направлены на обеспечение рабо тоспособности узлов машины и их конструктивного оформления. К ним относятся требования по надежности и долговечности, впи сыванию в заданные габариты, встраиванию средств автоматики и управления, промышленно-эстетическому оформлению, обеспе чению блокировок для согласованной работы всех механизмов комплекса и др.
§ 2. ТОЛКАТЕЛИ
Одним из главных структурных элементов автоматизирован ного комплекса погрузки или разгрузки является толкатель, который предназначен для принудительного передвижения нерасцепленных составов или отдельных вагонеток в подземных выра ботках или на поверхности шахты.
Толкатели различаются:
по способу воздействия на вагонетку — толкатели нижнего действия, перемещающие вагонетку за ось, подвагонный упор или колесо; толкатели верхнего действия, у которых рабочий ор ган воздействует на борт вагонетки;
по роду потребляемой приводом энергии — электрические, пневматические и электрогидравлические;
по способу монтажа — фундаментные и бесфундаментные; по типу тягового органа — цепные, канатные, поршневые,
с толкающей тележкой.
Широкое распространение получили на шахтах толкатели ниж него действия, предназначенные для обмена грузовых вагонеток, проталкивания нерасцепленных составов и одиночных вагонеток при обмене их в опрокидывателях и проталкивания вагонеток по откаточным путям.1; Предусматриваются следующие типы толкате лей: ТЦ — цепные с замкнутой цепью и электроприводом, ТЦН— то же, с незамкнутой цепью, ТК — канатные с электроприводом, ТШП — штоковые с пневматическим приводом, ТШГ — штоко вые с гидравлическим приводом. Все они могут изготовляться в исполнениях: К — при посадке на жесткие посадочные устрой ства, П — при посадке клети на качающиеся площадки, С — для проталкивания составов. Исполнение толкателя определяет его основные размеры и ход кулака толкателя.
У толкателей типа ТЦ толкающее усилие составляет от 8000 до 60 000 кН при скорости 0,5—0,8 м/с, у толкателей типа ТЦН — от 8000 до 16 000 кН при скорости 0,8 м/с, у толкателей типа ТК —
от 2800 до 22 000 кН при скорости 0,5—0,8 м/с, |
у толкателей |
|
типа ТШП — от 8000 |
до 16 000 кН при скорости |
0,6—1,0 м/с, |
а у толкателей ТШГ — |
от 40 000 до 60 000 кН при скорости 0,6 м/с. |
