
НОВЫЕ ТЕХНОЛОГИИ
.pdfнии и флотации, применять центробежные силы, что позволит многократно интенсифицировать процесс разделения и повысить степень очистки воды от нефти и механических примесей.
Разделение в поле центробежных сил может быть осуществлено в аппаратах, называемых центрифугами и гидроциклонами. В центрифугах вращательное движение жидкости передается от вращающихся с большой скоростью элементов механизма (барабана, шнека), в гидроциклонах оно обеспечивается потоком жидкости, поступающей на разделение через тангенциально расположенный входной патрубок.
Американской компанией Enviro Voraxial ® Technology, Inc (EVTN)
создана серия сепарационного оборудования, в котором вращательное движение жидкости передается от крыльчатки. Сепараторы Voraxial, в зависимости от проектных требований, могут одновременно разделить системы жидкость-жидкость, жидкость-твердые частицы или жидкость- жидкость-твердые примеси, протекающие через сепаратор.
На рынке подготовки воды России и СНГ подобное оборудование отсутствует и работ по изучению разделения водонефтяных смесей в сепараторах с крыльчаткой не проводилось.
Таким образом, представляется интересным разработать аналог данного сепаратора, исследовать влияние на процесс разделения изменение геометрии и скорости вращения крыльчатки, изменение температуры, давления и плотности среды, а также изучить влияние добавления в водонефтяную смесь химических реагентов (коагулянты, флокулянты, деэмульгаторы), способные повысить степень очистки воды от нефти и механических примесей.
В рамках данной работы проведен сравнительный анализ технологии Voraxial с индуцированной флотацией и центрифугированием.
Некоторые результаты анализа приведены в нижерасположенной таблице.
Сепаратор Voraxial отличается от других аппаратов малыми размерами. Так размеры сепаратора Voraxial производительностью 20 м3/ч в 4 раза меньше чем у флотатора и примерно в 1,5 меньше чем центрифуга.
Низкое потребление энергии делает его одним из наиболее экономичных сепараторов на рынке сегодня. Потребление электроэнергии у сепаратора Voraxial в 5 раз меньше чем у флотатора и в 11 раз меньше чем у центрифуги.
Сепаратор Voraxial единственная технология, использующая разделение в поле центробежных сил, которая применяется в широком диапазоне производительностей (до 1364 м3/ч) и давлений. Гидроциклонам необходим перепад давления, поэтому они используются при высоком давлении. Центрифуги могут применяться при любых давлениях, но имеют ограничение по максимальному расходу.
101
|
|
|
Таблица 1 |
|
Сравнение оборудования подготовки воды |
||||
|
Флотатор с ин- |
|
Центробежный |
|
Показатель |
дуцированием |
Центрифуга |
сепаратор |
|
|
газа |
|
Voraxial |
|
|
|
|
|
|
Производительность, |
20 |
20 |
20 |
|
м3/ч |
||||
Степень очистки, % |
90 |
92 |
93 |
|
Тонкость очистки, |
100 |
5..10 |
50 |
|
мкм |
||||
|
|
|
||
Потребление энергии, |
19 |
45 |
4 |
|
КВт |
||||
|
|
|
||
|
|
|
|
|
Размер (ДхШхВ), |
9,9 х 2,3 х 4,5 |
2,3 х 1,5 х 2,5 |
2,5 х 1 х 1 |
|
метр |
||||
|
|
|
||
|
|
|
|
|
Масса аппарата, кг |
8000 |
4850 |
660 |
|
|
|
|
|
|
Максимальная произ- |
|
|
|
|
водительность одного |
50 |
150 |
1364 |
|
аппарата, м3/ч |
|
|
|
Таким образом, можно сделать вывод, что сепаратор Voraxial может заменить такое технологическое оборудование очистки воды, как ловушки поперечного потока, центрифуги, гидроциклоны, оборудование для флотации растворенными газами и флотации индуцированными газами.
Результаты анализа литературы показали целесообразность и перспективность применения центробежного сепаратора с крыльчаткой для очистки пластовой воды, поэтому было принято использовать его для дальнейших исследований.
Следующим этапом данной работы станет создание лабораторной установки для исследования процесса разделения многокомпонентных смесей в центробежном сепараторе с крыльчаткой и изучение влияния различных факторов на процесс разделения. Для исследования предполагается использовать модельные системы.
Научный руководитель: Таранова Л.В., к.т.н., доцент
102
Каталитическое разложение легких С1 С4 углеводородов
для утилизации попутных нефтяных газов
Чичкань А.С., Институт катализа СО РАН, г. Новосибирск
Попутный нефтяной газ (ПНГ) считается побочным продуктом нефтедобычи и обычно сжигается на факелах. Сжигание ПНГ обычно связано с неподготовленностью инфраструктуры для сбора, подготовки, транспортировки и переработки этого газа. Уровень сжигания попутного нефтяного газа по нефтяным компаниям варьируется от 5 % до 54 %. В среднем по России сжигается 20…24 %, большая часть в Западной Сибири (до 69 %) [1]. При сжигании ПНГ теряется значительное количество ценного сырья, т.к. в отличие от природного газа, который главным образом состоит из метана, попутный нефтяной газ содержит значительные количества этана, пропана, бутана и некоторые другие углеводородные и неуглеводородные газы. Сжигание ПНГ оказывает значительное негативное воздействие на окружающую среду, и актуальность данной работы определяется высокими требованиями к состоянию атмосферного воздуха и окружающей среды в целом, поэтому в настоящее время важен поиск решения проблемы утилизации попутных нефтяных газов.
Вданной работе для утилизации попутных нефтяных газов предла-
гается метод каталитического разложения углеводородов С1-С4 фракции с получением углеродных наноматериалов и водорода в качестве главных продуктов процесса. Углеродные наноматериалы в данном случае представляют собой углеродные нанотрубки или нанонити, что зависит выбора катализатора разложения углеводородов. Для решения проблемы утилизации ПНГ в работе была поставлена цель: разработать научные основы технологии утилизации попутных нефтяных газов с получением углеродных наноматериалов и водорода.
Всоответствии с поставленной цель были обозначены следующие
задачи:
•Разработать и синтезировать высокоактивный и стабильный катализатор процесса разложения легких С1-С4 углеводородов на водород
иуглеродные нанонити, определить оптимальные условия его работы.
•Разработать и создать серию многокомпонентных металлических катализаторов для получения углеродных нанотрубок и водорода из различных углеводородов.
•Спроектировать и изготовить пилотную установку непрерывного действия для проведения процесса получения водорода и углеродных наноматериалов.
Таким образом, данное научное исследование имело два основных направления: 1) получение углеродных нанотрубок и водорода и 2) получение углеродных нанонитей и водорода каталитическим разложением легких С1-С4 углеводородов.
103
Известно, что каталитической активностью в образовании углерода обладают металлы подгруппы железа (Fe, Co, Ni), а также сплавы этих металлов с некоторыми другими. Основываясь на этих данных, были синтезированы две серии катализаторов Ni-Cu-Fe/Al2O3 для получения углеродных нанонитей и Co-Mo-Fe/Al2O3 для получения углеродных нанотрубок. Катализаторы серии Ni-Cu-Fe/Al2O3 были приготовлены методом механохимической активации, серии Co-Mo-Fe/Al2O3 – методом соосаждения соответствующих солей. Синтезированные катализаторы сначала были исследованы в проточном кварцевом реакторе с весами Мак-Бена, что позволило понять суть кинетики образования углеродных отложений на катализаторах. С лучшими по всем показаниям катализаторами были выполнены длительные опыты по разложению различных углеводородов в оригинальной установке непрерывного действия с вращающимся реактором.
При выборе типа реактора мы учитывали особенность реакции разложения углеводородов, которая состоит в увеличении объема гранул катализатора за счет роста углеродных нанонитей (до 100 раз). В связи с этим реакцию необходимо проводить в условиях большого свободного объема. Во вращающемся реакторе, в отличие от проточного с тарелками, нет градиентов по концентрациям, это обеспечивает более равномерное распределение образующегося углерода по слою катализатора. Такая установка с вращающимся реактором была разработана.
В результате проведенных исследований был определен наиболее эффективный катализатор серии Ni-Cu-Fe/Al2O3, который имеет состав: 70%Ni-10%Cu-10%Fe/Al2O3. Такой катализатор позволяет получать углеродные нанонити из природного газа с выходом до 160 гС/гкат, из пропанбутановой смеси – до 350 гС/гкат. Рост углеродных нанонитей на 70%Ni- 10%Cu-10%Fe/Al2O3 происходит одновременно на нескольких гранях каталитически активной частицы сплава Ni-Cu-Fe, и такие образования получили в литературе название "octopus" (осьминог) (рис. 1). При разложении легких углеводородов на 70%Ni-10%Cu-10%Fe/Al2O3 катализаторе газовая смеси на выходе из реактора содержит до 75% водорода, остальное не превратившиеся углеводороды
104
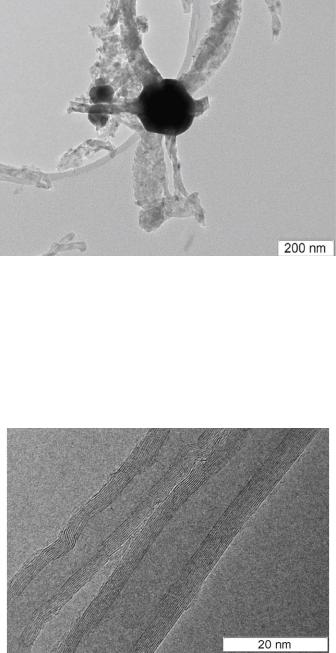
Рис. 1. Углеродные нанонити, полученные разложением метана на 70%Ni-10%Cu-10%Fe/Al2O3 катализаторе при температуре 700 oC.
Среди многокомпонентных металлических катализаторов наилучшими показателями по получению углеродных нанотрубок и водорода обладал 31%CoO-7%MoO3-24%Fe2O3-Al2O3 катализатор (рис.2). Выход углеродных нанотрубок из природного газа ≈ 13 гС/гкат , из пропан-бутаной сме-
си – ≈ 75 гС/гкат.
Рис. 2. Электронно-микроскопическая фотография углеродных нанотрубок, полученных из природного газа на 31%CoO-7%MoO3-24%Fe2O3-Al2O3 катализаторе при температуре 700 оС.
Литература 1. А. Книжников, Н. Пусенкова Проблемы и перспективы исполь-
зования попутного нефтяного газа в России // Выпуск 1 (рабочие материалы) ежегодного обзора проблемы в рамках проекта ИМЭМО РАН и WWF России «Экология и Энергетика. Международный контекст», Москва,
2009.
Научный руководитель: Чесноков В.В., д.х.н.
105
НЕФТЯНОЕ МАШИНОСТРОЕНИЕ, МАТЕРИАЛОВЕДЕНИЕ
Совершенствование конструкции узла «штуцер-корпус» сосуда давления на основе анализа его напряженно-деформированного состояния
Аписов И.В., Аллабирдин Р.З., Каретников Д.В., УфГНТУ, г. Уфа
Присоединение трубной арматуры к аппарату, а также технологических трубопроводов для подвода и отвода различных жидких и газообразных продуктов производится с помощью штуцеров или вводных труб. Узел присоединения штуцера к корпусу аппарата является одним из наиболее нагруженных узлов конструкции. В этих узлах создаются дополнительные конструктивные концентрации деформаций и напряжений по сравнению с прямыми участками конструкции ввиду различной деформационной способностью свариваемых узлов. Материал корпуса в данном узле в процессе эксплуатации находится в сложном напряженно-деформированном состоянии (НДС) и наличие в этой области такого концентратора напряжений, как сварной шов повышает вероятность износа. Анализируя данные по износу различного вида нефтеперерабатывающей аппаратуры можно увидеть, что до 40% разрушений приходится на узел ответвления. На практике при изготовлении нефтехимических аппаратов используют различные исполнения узлов «штуцер – корпус», руководствуясь конструктивными особенностями аппарата, ГОСТ 24755-89 «Сосуды и аппараты. Нормы и методы расчета на прочность укрепления отверстий» и технологичностью изготовления данного узла. При этом не учитывается, в каком НДС будет находиться данный узел аппарата в процессе его эксплуатации. Имея данные рекомендации и удовлетворяя всем вышеуказанным параметрам выбора конструктивного исполнения узла «корпус – штуцер» возможно повысить срок службы данного узла только за счет выбора исполнения с меньшим НДС.
В связи с этим был проведен сравнительный анализ НДС типовых исполнений узла «штуцер - корпус», возникающего в процессе эксплуатации аппарата. Для сравнительного анализа НДС различных конструктивных исполнений узлов, принимались одни и те же расчетные условия. Для исполнения с отбортовкой, с целью определения оптимальных параметров отбортовки принимали различные значения радиуса гиба Rг. Толщина отбортованной части принималась равной толщине стенки. В расчете не учитывали напряженно-деформированное состояние узла, возникающее в процессе его изготовления, т.е. в процессе приварки штуцера или отбортовки. Расчеты проводились с применением метода конечных элементов (МКЭ) использованием программного продукта ANSYS.
Научный руководитель: Файрушин А.М., канд. техн. Наук, доцент.
106
Повышение эксплуатационных характеристик соединений из двухслойной стали 09Г2С+12Х18Н10Т путѐм применения низкочастотной вибрационной обработки
Ахтямов Р.З., Зарипов М.З., Файрушин А.М.,УГНТУ, г. Уфа
Анализ применяемых биметаллов в нефтяном и газовом аппаратостроении показывает, что наиболее часто среди двухслойных сталей используется сталь марки 09Г2С+12Х18Н10Т. Это объясняется тем, что плакирующий слой данной стали, обладает хорошей свариваемостью, высокой пластичностью и ударной вязкостью, высокими механическими свойствами при отрицательных температурах, устойчивостью против окисления на воздухе и в атмосфере продуктов сгорания топлива при температурах ниже 900 оС, что обеспечивает надежную работу сварных конструкций в течение длительного времени.
Однако, при уникальном комплексе физико-механических свойств сталь 12Х18Н10Т имеет недостатки - подверженность сварных швов межкристаллитной коррозии (МКК).
Известно, что возникновение склонности к МКК и скорость роста коррозионных трещин у этих сталей связано с образованием в границах зерен карбидной сетки Ме23С6—(Cr,Fe)23C6 и обезлегированием по хрому приграничных областей твердого раствора, по которым развивается коррозионная трещина. Скорость роста карбидных частиц, в свою очередь, связана с температурой разогрева и химическим составом стали, в основном с содержанием углерода, никеля, кремния и др. примесей.
Также установлено, что пластическая деформация повышает склонность хромоникелевых сталей к МКК.
С учетом установленных причин образования МКК были разработаны технологии снижения склонности металла сварного шва к МКК, основными из которых являются:
-стабилизация;
-снижение содержания углерода в стали до 0,03 % и меньше;
-термическая обработка.
Следует отметить, что приведенные выше способы снижения склонности металла сварного шва к МКК обладают рядом существенных недостатков.
Технологии стабилизации и снижения содержания углерода в стали являются материально затратными, а термическая обработка, как основной метод снятия остаточных напряжений в конструкциях и предотвращения разрушения металла, является энергоемким технологическим процессом, требующим больших производственных площадей и, кроме того, является нежелательным процессом для двухслойных сталей.
107
Все это вызывает необходимость в исследованиях, направленных на поиск новых путей к снижению склонности металла сварного шва к МКК, при этом менее затратных и максимально продуктивных.
Теоретическое изучение этой проблемы позволило сделать вывод о целесообразности продолжения исследований в вопросе установленного ранее воздействия вибрационных колебаний, приложенных к свариваемой детали в процессе сварки, на свойства получаемых сварных соединений. Такой подход к решению задачи разработки более эффективной технологии снижения склонности к МКК с точки зрения уменьшения себестоимости, объясняется возможностью применения в технологии более простых по конструкции вспомогательных приспособлений и способностью адаптации к промышленному применению.
Для этого были проведены эксперименты по воздействию на сварочную ванну вибрационных колебаний в процессе сварочного цикла с целью изучения их влияния на прочностные характеристики металла сварного шва и склонность к МКК. Виброколебания в процессе сварки прикладывали на специальном вибростоле. Амплитуда виброобработки составляла от 0,6 до 0,8 мм, частота 50Гц.
После сварки на заданных режимах из сварных заготовок были вырезаны образцы для проведения исследований на стойкость к МКК. Испытания на МКК проводились по ГОСТ 6032-2003 методом АМУ . Результаты испытаний показали, что образцы, сваренные без вибрационной обработки оказались подвержены МКК. Образцы, полученные с применением вибрационной обработки, показали стойкость к МКК без образования трещин при загибе.
Литература
1.Семѐнова И.В. Коррозия и защита от коррозии. - М.: ФИЗМАТЛИТ, 2002, 336 с.
2.Коховский Н.И. Сварка нержавеющих сталей. - «Техника»,
1968, 312 с.
3.Ризванов Р.Г., Исследование влияния виброобработки в процессе сварки на свойства сварных соединений нефтегазового оборудования из стали 09Г2С / Файрушин А.М., Карпов А.Л., Зарипов М.З.// Нефтегазовое дело. - 2007. – № 5 - С. 183-186.
4.ГОСТ 6032-2003 Стали и сплавы коррозионно-стойкие. Методы испытания на стойкость к межкристаллитной коррозии. 24 с.
5.ГОСТ 6996-2005 Соединения сварные. Методы определения механических свойств. 41 с.
Научный руководитель: Ибрагимов И.Г., д.т.н., профессор.
108
Установка для испытаний на усталость образцов с электролитическими покрытиями
Венедиктов А.Н., Анкудинова А.С., ТюмГНГУ, г. Тюмень
Электролитические покрытия используют для улучшения функциональных характеристик металлических деталей – твердости, износостойкости, коррозионной стойкости. Наряду с улучшением одних функциональных характеристик, происходит снижение показателей по другим. В частности, известно снижение усталостной прочности деталей с покрытиями [1]. К причинам, снижающим усталостную прочность композиции деталь-покрытие, относятся – наводораживание поверхности основного металла, внутренние напряжения растяжения в покрытии, трещиноватость осадков и другие. Однако, нет однозначного мнения о степени влияния перечисленных факторов на величину усталостной прочности.
С целью изучения влияния переменных нагрузок на изменение структуры и свойств электролитических покрытий, возникла необходимость изготовления установки позволяющей проводить испытания на усталость. Предварительно был проведен анализ имеющихся схем нагружения образцов и конструкций установок для испытаний на усталость.
Для равномерного нагружения покрытия по всей поверхности образца подходят схемы испытаний с чистым изгибом в одной плоскости и повторно-переменного растяжения-сжатия. Чтобы на прочностные свойства образца материал покрытия оказывал большее влияние, необходимо использовать образец с небольшим поперечным сечением. Такие условия испытания позволят изучить изменение структуры материала покрытия при приложении повторно-переменных нагрузок и влияние покрытия на свойства основного металла.
На основании проведенного анализа разработана принципиальная схема, конструкция и изготовлена установка для испытаний образцов с покрытиями при повторно-переменном растяжении-сжатии с максимальной нагрузкой до 5 кН.
Кинематическая схема установки представлена на рисунке. Образец материала с покрытием 1 закреплен в зажимах 2, имеющих возможность возвратно-поступательного движения в направляющих 3. Один зажим соединен с механизмом поступательного перемещения 4 через динамометр 5. Динамометр оборудован тензодатчиками регистрирующими величину растягивающего усилия, прикладываемого к образцу. Сигнал с тензодатчиков через усилитель и АЦП подается на ПЭВМ, что позволяет контролировать и регистрировать величину и амплитуду прикладываемой к образцу нагрузки, частоту колебаний и число циклов нагружения. Второй зажим соединен с коромыслом 6 и через пружину 7 с механизмом
109

поступательного перемещения 4. При приложении растягивающей нагрузки к образцу перемещением захватов механизмами поступательного перемещения, часть нагрузки компенсируется растягивающейся пружиной, а коромысло находится в нейтральном положении. С помощью кривошипно-коромыслового механизма 6, 8, 9 задается амплитуда колебаний образца. Конструкция кривошипа позволяет изменять его размеры, за счет чего устанавливается необходимая для исследований амплитуда напряжений в образце. Благодаря разной длине плеч коромысла, на кривошип и электродвигатель 10 действует нагрузка в несколько раз меньше, чем на образец, что увеличивает их срок службы и облегчает настройку параметров испытания. В установке использован электродвигатель постоянного тока с переменной частотой вращения с возможностью возбуждать колебания с частотой до 30 Герц, что позволяет проводить испытания за короткие сроки.
Рис. 1. Кинематическая схема установки для испытаний на усталость
Изготовленная установка прошла лабораторную апробацию и получены первые результаты испытаний.
Литература 1. Л.И. Тушинский, А.В. Плохов, А.О. Токарев, В.И. Синдеев
Методы исследования материалов: Структура, свойства и процессы нанесения неорганических порытий М.: Мир, 2004 – 384 с.
Научный руководитель: Венедиктов Н.Л., к.т.н., доцент.
110