
НОВЫЕ ТЕХНОЛОГИИ
.pdfОпределение обрабатываемости материалов по физико-механическим характеристикам
Тверяков А.М., Якубовская Е.В., Василега Д.С., ТюмГНГУ, г. Тюмень
Изучение обрабатываемости металлов при выполнении различных операций разными режущими инструментами для установления условий рациональной обработки является одной из основных задач науки о резании металлов [1].
Существует несколько методов ускоренного определения обрабатываемости металлов – это метод торцевой обточки и метод радиоактивных изотопов. Первый метод заключается в том, что диск, изготовленный из испытуемого материала, обтачивают на токарном станке по торцу от центра к периферии с постоянным числом оборотов, т.е. с переменной скоростью резания. Методом торцевой обточки можно быстро определить зависимость Т-υ (между стойкостью резца и скоростью резания) и тем самым обрабатываемость соответствующего материала. Второй метод заключается в том, что после обработки облученным инструментом с помощью фотопластинки определяют интенсивность износа различных участков режущего инструмента и тем самым оценить как стойкость исследуемого инструмента, так и обрабатываемость соответствующего материала [2].
Известно, что обрабатываемость металлов обуславливается их химическим составом и структурным состоянием. Однако существующая связь является чрезвычайно сложной, поскольку на обрабатываемость металлов влияет целый комплекс их механических и теплофизических характеристик, а также ряд параметров, связанных непосредственно со свойствами кристаллической решетки материалов. Очевидно, существенное влияние на обрабатываемость оказывает как физические, так и технологические характеристики.
Таким образом, дальнейшее изучение характеристик обрабатываемости материалов является актуальным и заслуживает особого внимания.
Литература
1.Развитие науки о резании металлов [Текст]: / Н.Н. Зорев, Г.И. Грановский, М.Н. Ларин, Т.Н. Лоладзе, И.П. и др. – М.: Машиностроение,
1967.-416 с.
2.Артамонов, Евгений Владимирович. Работоспособность инструментов и физико-механические характеристики инструментальных твердых сплавов и обрабатываемых материалов. [Текст] : монография / Е.В. Артамонов, Д.С. Василега, М.С. Остапенко, В.А. Шрайнер. – Тюмень: «Вектор Бук», 2008. – 160 с.
Научный руководитель: Артамонов Е.В., д.т.н., профессор.
161

Оптимизация конструкции вала ротора центробежного насоса
Фоминцев В.С., Соловьев И.В., ТюмГНГУ, г. Тюмень
Имеется деталь – «Вал», длиной 4135мм. Проблема заключается в том, что изготовление детали такой длины связано с определѐнного рода трудностями: специальное технологическое оборудование и оснастка, высокая трудоѐмкость и себестоимость детали, низкая ремонтопригодность.
ЦЕЛЬ: Наша цель состоит в том, чтобы модернизировать конструкцию вала так, чтобы обеспечить возможность изготовления на универсальном оборудовании, снизить трудоѐмкость и увеличить ремонтопригодность.
ЗАДАЧИ:
1.Провести анализ технологичности детали.
2.Рассмотреть варианты модернизации конструкции детали.
3.Провести инженерный анализ выбранной конструкции.
4.Провести расчѐт экономической эффективности выбранной конструкции.
Анализ технологичности детали:
Вопрос технологичности конструкции является одним из самых актуальных вопросов, т.к. низкая технологичность, как правило, ведѐт к удорожанию продукции за счѐт высокой трудоѐмкости изготовления, повышает металлоѐмкость изделия, требует, применения специального инструмента и оснастки. Поэтому технологический анализ один из важнейших этапов технологической разработки. Цель такого анализа – выявление недостатков конструкции по сведениям, содержащимся в чертежах и технических требованиях, а также возможное улучшение технологичности рассматриваемой конструкции.
1.Требуется специальное технологическое оборудование и
оснастка.
2.Низкая жесткость детали ( l d 25,5 ).
3.Диаметральные шейки вала увеличиваются к центру, что затрудняет обработку за один установ. Следовательно увеличивается погрешность.
4.Наличие множества фасонных канавок, для которых требуется специальный инструмент.
Из всего вышесказанного следует, что данная деталь не отвечает современным требованиям, предъявляемым к технологичности.
Анализ экономической эффективности:
При средней цене на сталь 30Х13 – 90 тыс. руб. Стоимость замены одной детали, составляет не менее 130 тыс. руб. Что крайне экономически неэффективно.
Варианты модернизации конструкции детали:
162
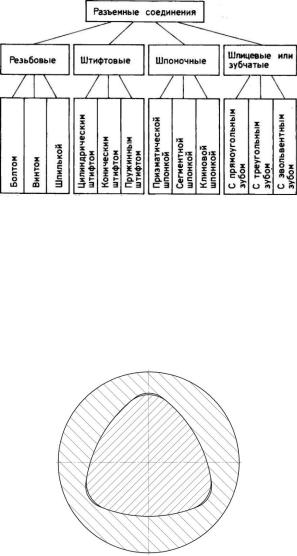
Исходя, из условий задания требуется разделить вал на три части. Для этого выбираем цилиндрическую часть диаметром 162 мм. Так как данный диаметр наибольший и обеспечивает высокую прочность соединения.
Рассмотрим варианты различных разъѐмных соединений:
Рис. 1. Виды разъѐмных соединений
Шпоночное соединение не подходит, т.к передаваемый крутящий момент 3800 Н∙м слишком велик. Для производства шлицевого соединения требуется отдельное оборудование. Поэтому остановим свой выбор на профильном соединении на основе треугольника Рело.
Рис. 2. Профильное соединение
Данное изделие обладает высокой нагрузочной способностью и отличается долговечностью, превышающей шлицевое соединение. Также данное соединение обеспечивает высокую точность центрирования, что необходимо для вала ротора насоса.
Получение такого изделия не требует специального оборудования. Его можно получить на обычном токарно-фрезерном обрабатывающем центре. Переходной стакан закрепляется тремя установочными винтами с каждой стороны, расположенных под углом 120 градусов.
163
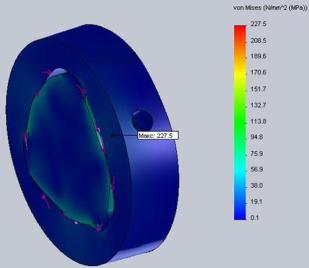
Инженерный анализ выбранной конструкции:
Проведѐм инженерный анализ выбранной конструкции с помощью программы SolidWorks Simulation.
Рис. 3. Распределение напряжений в профильном соединении
Обоснование экономической эффективности За счѐт изменения конструкции снижена металлоѐмкость изделия на
33 кг. Следовательно, составляющая стоимости материала снижается на 5,16%. Новые габариты изделия позволяют производить обработку на универсальном оборудовании без применения специального оборудования. Что также снижает себестоимость изготовления. Также появилась возможность ремонта изделия, так при повреждении одной из частей еѐ можно будет заменить на другую, а не менять всѐ изделие в целом. Трудоѐмкость изготовления за счѐт уменьшения габаритов также снижается.
Выводы:
1)Проведѐнный анализ конструкции показал еѐ не соответствие требованиям технологичности.
2)В ходе рассмотрения вариантов модернизации было выбрано профильное соединение.
3)Проведѐнный инженерный анализ показал, что данное соединение отвечает требованиям прочности, предъявляемым к данному изделию. Проведѐнная модернизация конструкции, экономически обоснована.
Литература
1.Дунаев П.Ф., Леликов О.П. Конструирование узлов и деталей машин. [Текст] – М.: Издательский центр «Академия», 2004. – 496 с.
Научный руководитель: Соловьев И.В., ассистент.
164
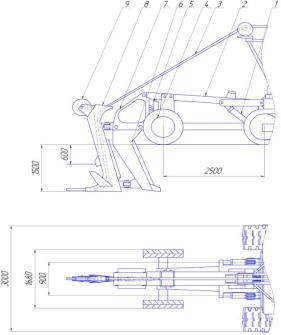
Модернизация рабочего органа кабелеукладчика КВГ-1 для прокладки полиэтиленовых трубопроводов
Хакимов З.Р., Корнилова М.А., ТюмГНГУ, г. Тюмень
Существует множество способов прокладки трубопроводов. Мы рассмотрим плужный способ, являющийся наиболее конструктивно простым, относительно недорогим и наиболее производительным.
Плужный способ прокладки трубопровода, заключается в отрывке рабочего и приемного котлованов с последующей прокладкой между ними трубопровода. Кабелеукладчик, включает в себя базовую машину, раму, рабочий орган в виде плуга с каналом для прохода кабеля или трубы. Прокладка кабеля или трубы осуществляется за счет тягового усилия базовой машины. Данным способом можно укладывать трубы до шестидесяти трех миллиметров. Плужный способ имеет высокую производительность до полутора километра в час (в зависимости от грунта и диаметра укладываемой трубы), практически не наносит вреда окружающей среде и имеет не высокую стоимость прокладки [1].
Плужный кабелеукладчик КВГ-1 обладает высокой производительностью, благодаря использованию вибрации. Кабелеукладочное оборудование состоит из рамы 2 с установленными на
Рис. 1. Рабочее оборудование КВГ – 1 1 – механизм подъема рамы трубоукладочного оборудования; 2 – рама для
крепления трубоукладочного оборудования; 3 – труба; 4 – колесная база; 5
–механизм поглощения вибрации; 6 – плуг; 7- вибрационное устройство; 8
–короб для подачи трубы; 9 – катушка с сигнальной лентой.
ней вибрационным плугом 6, шарнирно присоединенным к нему коробом 8 для подачи кабеля либо трубы диаметром до 80 мм, устройством для по-
165
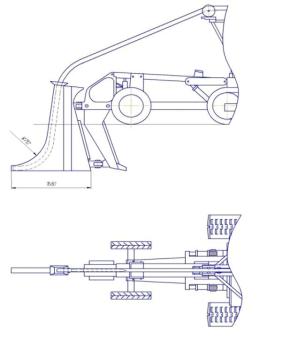
глощения вибрации 5, колесной базой 4 и шарнирно закрепленными на базовой машине гидроцилиндрами подъема и опускания рамы 1.
Для строительства межпоселкового газопровода целесообразнее использовать трубу диаметром от 110 мм. Учитывая то, что рабочий орган кабелеукладчика КВГ-1 предназначен для прокладки труб диаметром до 80 мм, требуется модернизация рабочего органа, а в частности направляющего короба (рис. 2). В связи с большим диаметром трубы значительно изменяется и геометрические параметры короба. Так минимально допустимый радиус изгиба полиэтиленовой трубы диаметром 110 мм составляет 779 мм, а ширина короба – 130 мм [2]. Таким образом, увеличивается площадь лобовой поверхности рабочего органа, а так же площадь боковой поверхности, а значит, увеличится и сопротивление грунта, возникающее при резании грунта рабочим органом кабелеукладчика.
Рис. 2. Модернизированный направляющий короб
Использование общеизвестных методик (Домбровского Н.Г., Ветрова Ю.А., Зеленина А.Н.) по определению значения сопротивления грунта при продвижении рабочего органа (разрушению грунта) не обеспечивает необходимой точности расчета. Объясняется это тем, что известные методики успешно применимы для рабочих органов, у которых составляющая сопротивления резанию и заполнению рабочего органа грунтом значительно выше по отношению к преодолению сопротивления трения о боковую поверхность. На основании экспериментальных исследований доказано, что использование известных методик для исследуемого рабочего органа показывает отклонение до 20% при сравнении действительного сопротивления разрушению грунта и расчетного.
166
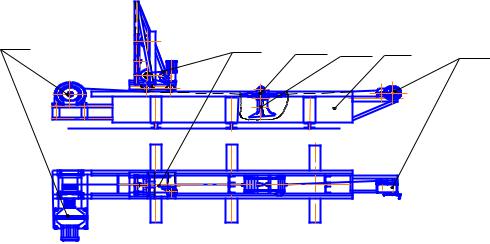
Для определения сил сопротивления грунта резанию при прокладке трубопровода была сконструирована лабораторная установка «Грунтовый канал» (рис. 3). Рабочее оборудование установки состоит из лоткаконтейнера 1, который жестко смонтирован на несущей раме. Несущая рама имеет жесткую пространственную конструкцию из двутавров, на которой наряду с лотком монтируют узлы привода перемещения тележки. Тележка 2 перемещается по рельсам, смонтированным вдоль канала по обе стороны от траншеи, с помощью лебедки 3, приводимой от электродвигателя, через планетарный редуктор. Она служит для монтажа исследуемых рабочих органов и сообщения им поступательного горизонтального движения при резании грунта. Тележка имеет сварную раму. На тележке имеется место для крепления сменных моделей рабочих органов 6 для бестраншейной прокладки трубопроводов. Ее возвращают в первоначальное положение с помощью ручной лебедки 4, которая установлена с противоположной стороны.
Рабочая зона грунтового канала заполнена грунтом, подготовленным с заданными параметрами по гранулометрическому составу и плотности таким образом, что его физико-механические характеристики приближаются к естественным. Грунт помещают в участок грунтового канала длинной 1 м, шириной 0,32 м и глубиной 0,5 м, отделѐнный швеллерами (120 мм.), имеющий щели между швеллерами для входа и выхода рабочего органа. Стендовое оборудование грунтового канала включает подготовительную тележку 5 и силовую установку. На подготовительной тележке смонтирована трамбующая установка.
3 |
5 |
2 |
6 |
1 |
4 |
Рис. 3. Схема грунтового канала
На основании положений физического моделирования были сконструированы и построены 2 модели направляющего короба в масштабах
1:4 и 1:6 [3] (рис. 4)
167
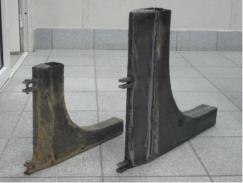
Рис. 4. Короба с масштабными коэффициентами 1:4 и 1:6
В процессе работы были проанализированы общеизвестные методики расчета сил сопротивления грунта резанию рабочим органом кабелеукладчика КВГ-1 (Н. Г. Домбровский, А. Н. Зеленин, Ю.А. Ветров). Экспериментальным путем определили необходимое тяговое усилие базовой машины для преодоления сопротивления грунта резанию модернизированным рабочим органом
Установлено, что тяговые характеристики базовой машины кабелеукладчика КВГ-1 позволят прокладывать трубу диаметром до 110 мм в грунтах до 3 категории прочности, это существенно снижает затраты на прокладку газопровода диаметром до 110 мм и увеличит производительность работ. Сменное рабочее оборудование позволяет расширить использование базовой машины для различных видов работ.
Литература
1.Серебренников Д.А. Опыт и перспективы сооружения полиэтиленовых трубопроводов для транспорта газа // "Вопросы состояния и
перспективы развития нефтегазовых объектов западной Сибири". Сборник научных трудов. – Тюмень: Нефтегазовый университет, 2002г. – 20 – 34 с.
2.Серебренников Д.А. Диссертация на соискание учѐной степени Кандидат технических наук на тему « Обоснование рабочих параметров
машины для бестраншейной прокладки полиэтиленовых газопроводов. – Тюмень: ТюмГНГУ, 2004г. – 12 – 17 с.
3.Баловнев В.И. Моделирование процессов взаимодействия со средой рабочих органов дорожно-строительных машин: Учеб. Пособие для
студентов высш.учеб. заведений. 2-е изд., перераб. – М.: Машиностроение,
1994.- 432 с.
Научный руководитель: Серебренников А.А., д.т.н., профессор.
168
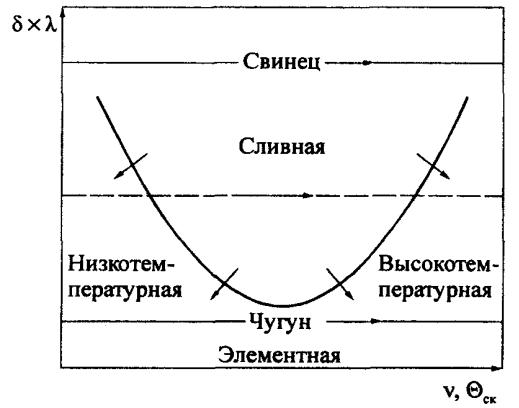
Определение условий максимальной работоспособности режущих элементов по виду стружки
Шевченко А. Р., Васильев Д. В., Бакум К. В., ТюмГНГУ, г. Тюмень
Изложены результаты исследования зависимости изменения вида стружки при обработке материалов резанием от температуры резания, как определяющего фактора во всей взаимосвязи явлений при резании металлов.
Одной из главных проблем в современном машиностроении является определение режимов резания при обработке, как известных материалов, так и новых труднообрабатываемых материалов. Для определения оптимальных режимов резания и условий максимальной работоспособности инструментов необходимы продолжительные дорогостоящие стойкостные лабораторные испытания, что приводит к определѐнным финансовым затратам, а также к потере времени.
Профессор Полетика М.Ф. сформулировал гипотезу о том, что вид стружкообразования определяется температурно-скоростным фактором и свойствами обрабатываемого материала (Рис.1.)
Рис.1. Схематическая диаграмма, иллюстрирующая воздействие темпера- турно-скоростного фактора и свойств обрабатываемого материала на вид стружкообразования
Для большинства машиностроительных материалов стружка имеет виды: элементная, суставчатая, сливная. Для некоторых высокопластичных
169
материалов (например, свинца) имеет вид только сливная стружка, эти материалы не образуют элементной стружки ни при каких условиях. Другая группа (например, чугун) во всем диапазоне изменения температурноскоростного фактора не образует сливную стружку[3].
В лаборатории резания ИПТИ ТюмГНГУ было спроектировано и собрано несколько экспериментальных установок, с помощью которых был проведен ряд лабораторных опытов и разработана экспериментальная методика определения оптимальных режимов резания для новых обрабатываемых и инструментальных материалов. При измерении температуры резания применялись: естественная термопара при измерении ТЭДС, при измерении температуры стружки - пирометр. Исследование проводилось при разных режимах резания (S=0,11, S=0,21 и S=0,52) и разных скоростях резания. Режимные условия формировались так, чтобы охватить весь тем- пературно-скоростной диапазон начиная с температуры 200C и заканчивая температурой потери формоустойчивости режущего клина из ВК8 – более 9000С. В качестве обрабатываемого материала использовались: стали
1Х18Н9Т, 1Х12Н2ВМФ, 40Х.
Анализируя данные полученные при эксперименте прослеживается общая закономерность для всех материалов в зависимости от температурного диапазона:
Температурный диапазон от 200С до 3000С – стружка элементная;
Температурный диапазон от 3000С до 4000С – стружка суставчатая;
Температурный диапазон от 4000С до 5000С – стружка сливная;
Температурный диапазон от 5000С до 7000С – стружка суставчатая;
Температурный диапазон свыше 7000С – стружка элементная.
Результаты исследования доказывают гипотезу профессора Полетики М. Ф. о зависимости вида стружки от температурного диапазона, в котором проходит резание металлов.
На основании результатов исследования Макарова А. Д. по оптимизации режимов резания[2], установленная температура резания 7600С является оптимальной при точении стали 1Х18Н9Т резцом из ВК8, что соответствует условию максимальной работоспособности инструментального твердого сплава ВК8 [1]. Данной температуре резания, по результатам наших исследований, соответствует элементная стружка (1 завиток, to=750о см. рис. 2.), т.е., по виду стружки могут быть определены условия максимальной работоспособности режущего элемента.
170