
НОВЫЕ ТЕХНОЛОГИИ
.pdfпокрытий, характеризующихся мелкозернистыми кристаллитами без преимущественной ориентации и неоднородной структурой. Аморфные электролитические сплавы имеют слоистую структуру, которая неоднородна по толщине. Поверхность получаемых покрытий – блестящая.
Установлено, что в чистом электролитическом железе и кристаллических сплавах железо-молибден обычно формируются внутренние напряжения растяжения. При концентрации молибдена 7 % наблюдается увеличение, а затем так же снижение внутренних напряжений.
При нагреве электроосажденных сплавов внутренние напряжения снижаются, причем наиболее интенсивно в кристаллических покрытиях в связи с изменением концентрации неравновесных дефектов структуры. В аморфных покрытиях уровень снижения напряжений менее существенен, они становятся незначительными и стабилизируются.
Электрохимическое легирование железа молибденом в концентрациях, соответствующих кристаллическому состоянию сплавов приводит к упрочнению покрытий, вследствие измельчения их структуры и повышения плотности дефектов кристаллического строения. Максимум твердости приходится на ультрадисперсные осадки с содержанием 17% молибдена. В сплавах с более высоким содержанием молибдена, имеющим аморфнокристаллическую структуру, твердость уменьшается.
Испытания на износ проводили при сухом трении по схеме «дискколодка». Полученная зависимость износостойкости от концентрации легирующих элементов коррелирует с изменением твердости. Чем выше твердость получаемых покрытий, тем меньше их износ.
Для оценки коррозионной стойкости покрытий использовали количественный гравиметрический метод. Железо-молибденовые электролитические сплавы существенно отличаются коррозионной стойкостью от покрытий чистого железа, имеющих ярко выраженную столбчатую структуру. Коррозионная стойкость изучаемых сплавов возрастает с увеличением содержания молибдена в покрытиях.
Одновременно с ростом содержания молибдена в сплавах снижаются внутренние напряжения, которые способствуют развитию коррозионного процесса, но наибольшими защитными свойствами обладают аморфные покрытия, поскольку в них отсутствуют структурные дефекты (границы зерен, дислокации, дефекты упаковки), которые являются активными центрами коррозии.
При нагреве сплавов их коррозионная стойкость снижается в связи с образованием в покрытиях оксидов молибдена и фаз Лавеса, которые в основном выделяются по границам зерен, а так же в связи с развитием пористости.
Научный руководитель: Корешкова Е.В., к.т.н., доцент.
121
Структурно-технологические особенности изготовления и эксплуатации кольца гидропяты ЦНС
Косинцева И.В., ТюмГНГУ, г. Тюмень
Вконструкции центробежных многоступенчатых секционных насосов (ЦНС) предусмотрены гидравлические разгрузочные устройства. Одним из элементов данных узлов, подвергающимся интенсивному изнашиванию и поэтому заменяемым через 1 ’ 3 месяца эксплуатации, является кольцо гидропяты. Модификации ЦНС, применяемые в нефтегазовой отрасли, оснащены кольцами из коррозионностойких сталей с наплавленным на рабочую поверхность износостойким композиционным материалом.
Вкачестве объекта исследований принято кольцо гидропяты после эксплуатации с максимально допустимым износом 3 мм. Целью работ являлось выявление влияния материала кольца на износ с последующей выработкой практических рекомендаций. Программа включала проведение макроанализа, определение состава материала кольца с покрытием, в том числе фракционного для дисперсной фазы композита, измерение микротвердости структурных составляющих с учетом зонального распределения.
Спектрометрическим методом определено, что деталь изготовлена из стали 10Х17Н13М2Т, соответствующей ГОСТ 5632-72. Наплавленный слой представляет собой композиционный материал с дисперсной фазой карбида вольфрама в матрице из сплава Х12Н10М3К3. Выбор карбида вольфрама представляется рациональным в связи с тем, что по уровню твердости, превышающей HV2400, он превосходит карбиды большинства других металлов. Материал этого типа используют для повышения износостойкости шарошек буровых долот, зубьев ковшей экскаваторов и т.п.
Установлено, что наплавка износостойкого слоя осуществлялась в кольцевую канавку глубиной 4 мм с формированием выступающей части 3
ммс учетом финишной обработки, а также наличие технологического дефекта в месте инициации наплавки на рабочей плоскости кольца. На поперечных срезах зафиксированы несовершенства зоны сцепления основного материала детали с наплавленным слоем в виде трещиновидных пустот. Изношенная рабочая поверхность кольца содержит множественные царапины, направление которых согласуется с центробежными силами, возникающими при вращении ротора насоса. Вероятной причиной возникновения царапин представляется движение под нагрузкой выкрошенных твердых частиц по поверхности относительно мягкой матрицы композита. Повидимому целесообразно использовать матрицу композита из более прочного материала, например, стали, а в качестве второй фазы применить частицы карбида вольфрама сферической формы фракции до 300 мкм.
Научный руководитель: Скифский С.В., к.т.н., профессор
122
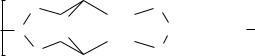
Новые полиимидные материалы для оборудования нефтегазового комплекса
Кравцова В.Д., Умерзакова М.Б., Сариева Р.Б., Болотов Д.А.
АО «Институт химических наук им. А.Б. Бектурова», г. Алматы, Республика Казахстан
Казахстанско-Британский технический университет, г. Алматы, Республика Казахстан
Известно, что нефтегазовая отрасль является энергоемкой областью. Основной объем электроэнергии потребляют различные виды силового электрического оборудования, которое содержит от 60 до 80% разных электротехнических изделий, компонентов, проводов и кабелей, которые составляют большую часть стоимости самого электрооборудования. Этот факт со всей остротой ставит задачу обеспечения надежности электрооборудования и каждой его составляющей за счет использования современных электроизоляционных материалов и разработку новых с высокими техническими характеристиками. Следует также отметить важное для нефтяной и газовой промышленности направление по дальнейшему совершенствованию эксплуатируемого электрооборудования – повышению его технической надежности, огнестойкости, взрывозащищенности, устойчивости к воздействию токов короткого замыкания, последствиями которых является электрическая дуга, приводящая к повышенному нагреву токоведущих частей и изоляции и другим осложнениям, которые могут оказать отрицательное влияние на технологический процесс [1,2]. Все это требует применения в электрооборудовании надежной изоляции с повышенными техническими характеристиками, устойчивой к воздействию перечисленных факторов.
В настоящее время в качестве изоляции для такого вида оборудования широко используются такие полимеры как сшитый полиэтилен, полипропилен, поливинилхлорид, полиэфиры, полиамиды, полиамидоимиды и т.д. Намного превосходят эти полимеры по диэлектрическим, физико-механическим, химическим и другим характеристикам выпускаемые в относительно небольшом количестве (7–8 % от общей масы полимеров) полиимиды ароматического строения [3]. В АО «Институт химических наук им. А.Б. Бектурова» разработаны новые алициклические полиимиды, из которых наиболее изученным и доступным, синтезируемым из продуктов переработки нефти является полиимид следующего строения [4,5]:
O |
|
|
|
O |
|
|
|
|
|
C |
|
|
|
C |
|
|
|
|
|
N |
|
|
|
C |
N-C6H4-O-C6H4 |
|
|
|
|
|
|
|
|
|
|
|
|||
C |
|
|
|
|
|
|
n |
||
|
|
|
|
|
|
||||
O |
|
|
|
O |
|
|
|
|
|
123
В таблице 1 приведены основные характеристики разработанного полиимида.
Таблица 1 Некоторые свойства пленочной полиимидной изоляции
Параметр |
|
Температура, оС |
|
|||
|
|
-70 |
25 |
200 |
250 |
300 |
Тангенс угла ди- |
0,001‒ |
0,001‒ |
0,003‒ |
0,002‒ |
0,004‒ |
|
электрических |
0,003 |
0,003 |
0,005 |
0,004 |
0,007 |
|
потерь,tgδ (1 кГц) |
|
|
|
|
|
|
Диэлектрическая |
2,1‒2,3 |
2,4‒2,8 |
2,4‒2,8 |
2,6‒3,0 |
2,8‒3,2 |
|
проницаемость,ε′ |
|
|
|
|
|
|
Удельное |
объем- |
(1‒ |
(1‒ |
(1‒ |
(1‒3) |
(1‒ |
ное сопротивле- |
3)•1015 |
3)•1015 |
3)•1015 |
•1015 |
3)•1015 |
|
ние,ρv, Oм•м |
|
|
|
|
|
|
Удельное поверх- |
(2- |
(2‒ |
(2‒ |
(1‒ |
(1‒ |
|
ностное |
сопро- |
5)•1014 |
5)•1014 |
6)•1012 |
3)•1012 |
3)•1012 |
тивление,ρ,Oм |
|
|
|
|
|
|
Электрическая |
150‒170 |
160‒180 |
150‒170 |
120‒140 |
115‒125 |
|
проч- |
|
|
|
|
|
|
ность,Епр,кВ/мм |
|
|
|
|
|
|
Прочность |
на |
100 |
140‒150 |
125‒135 |
100‒105 |
70‒80 |
разрыв,ζв,МПа |
|
|
|
|
|
Полиимид имеет хорошие пленкообразующие свойства. К настоящему времени выпущены опытные и опытно-промышленные партии новых электроизоляционных изделий ‒ пленок и термостойких эмаль-проводов, проведены работы по применению нового материала в качестве электрической изоляции класса нагревостойкости 200о.
Несмотря на довольно высокие диэлектрические и физикомеханические характеристики материалы из немодифицированного алициклического полиимида имеют некоторые недостатки, ограничивающие их использование в массовом объеме, в частности – это повышенная воспламеняемость при попадании в открытое пламя, с повышенным дымо- и газовыделением продуктов сгорания. В результате проведения соответствующих исследований были разработаны полимерные лаки и изделия на их основе с пониженной горючестью. Новые полимерные композиции, включающие от 5 до 15 масс. % модификатора ‒ трифенилили трикрезилфосфата по диэлектрическим и физико-механическим параметрам не уступают исходному полиимиду, кислородный индекс при этом возрастает от 0,23 до 0,45, при вынесении из из открытого пламени они не поддерживают горения [6]. Улучшаются температурные и прочностные характеристики ‒ температуры разложения на 10‒25оС выше по сравнению с исход-
124
ным полимером, прочность на разрыв на 10‒30 МПа. Некоторые характеристики пленок приведены в таблице 2.
Таблица 2 Электрические параметры и механическая прочность композиционных
пленок (25оС)
Параметры |
ПИ+ТФФ |
ПИ+ТФФ |
ПИ+ТКФ |
|
(5 масс. %) |
(15 масс. %) |
(15 масс. %) |
tgδ (1 кГц) |
0,005 |
0,007 |
0,008 |
|
|
|
|
ε' |
2,3–2,5 |
3,1–3,3 |
3,8–4,1 |
ρv, Oм•м |
(1–3)∙1015 |
2,5∙1015 |
4,4·1014 |
Епр, кВ/мм |
190–210 |
190–220 |
160–170 |
|
(до 250) |
|
|
ζв, МПа |
150‒170 |
155‒180 |
160‒180 |
Литература
1.Ведерников В.А., Козлов В.В. Роль оценки ресурса изоляции ПЭД в решении задач оперативного управления УЭЦН // Материалы Всероссийской научно-технической конференции «Проблемы автоматизации в топливноэнергетическом комплексе западной Сибири на современном этапе». Тюмень: Нефтегазовый университет. ‒ 2007. ‒ С. 32‒34.
2.Козлов В.В. Оперативное управление погружными установками добычи нефти с учетом ресурса изоляции электродвигателя. Автореф. на соиск. уч. степени канд. техн. наук. Тюмень. ‒ 2009. ‒ 17 с.
3.Котон М.М., Лайус Л.А. Роль ароматических полиимидов в современной науке и технике // Журн. прикл. химии. ‒ 1996. ‒ Т. 68. ‒ № 5. ‒ С. 822–826.
4.Жубанов Б.А., Кравцова В.Д., Алмабеков О.А. и др. Полиимидные лаки для электроизоляционных материалов // Лакокрасочные материалы и их применение. ‒ 1993. ‒ №4. С. ‒ 17‒18.
5.Жубанов Б.А., Кравцова В.Д., Бекмагамбетова К.Х. Полиимидные лаки для обмоточной эмалевой изоляции // Электротехника. ‒ 1998. ‒ № 11. ‒ С. 57‒60.
6.Жубанов Б.А., Кравцова В.Д., Искаков Р.М., Бекмагамбетова К.Х. Термическая устойчивость и огнестойкость галогенсодержащих алициклических полиимидов // Сб. трудов Х Межд. конф. по химии и физико-химии олигомеров. Волгоград. ‒ 2009. ‒ С. 203.
Научный руководитель: Кравцова В.Д., д.х.н., доцент
125
Влияния малоцикловой усталости на сталь 09Г2С.
Кусков К.В., Хучахмедов А.Р., ТюмГНГУ, г. Тюмень
Отдельные участки магистральных нефтепроводов испытывают более 350 циклов повторных нагрузок в год [1], вызванных различными технологическими и эксплуатационными факторами: переключением насосов, нарушением технологического режима, возникновением аварий, плановыми ремонтно-восстановительными работами, сезонными и суточными колебаниями температуры. В результате этого происходят накопления необратимых микропластических деформаций в структурно-неоднородных объемах металла, которые приводят к увеличению прочности, твердости и одновременно к уменьшению пластичности (до 20 %) и ударной вязкости (почти в 2 раза) [2 – 3], а следовательно, к снижению сопротивляемости стали разрушению.
В работе исследовали низколегированную сталь 09Г2С, которая широко используется при изготовлении трубопроводов [1].
Образцы для испытаний представляли собой пластины размером 500х15х8 (длина ширина толщина), сваренные встык с разделом кромок, механизированной сваркой в среде углекислого газа. Образцы прошли рентгенографический контроль, в результате которого были выявлены дефекты сварного соединения, с размерами не выходящими за рамки допустимых (ВСН 012-88). Для сравнения использовали однотипные пластины без сварного соединения.
Исследования проводили на разрывной машине ЦД-20 с пульсатором Пу-10. Переменная растягивающая нагрузка от максимального напряжения растяжения ζmax (менее условного предела текучести образцов стали) до минимального с амплитудой изменения напряжения Aζ действовала вдоль оси образца (перпендикулярно сварному шву). Частота циклов нагружения составляла 10 Гц. В каждой серии использовали по 7 образцов. Результаты испытаний приведены в таблице.
|
|
|
|
Таблица 1 |
|
Параметры усталостных испытаний |
|
||
|
Тип образцов |
Максимальное |
Амплитуда |
Количество |
№ |
|
напряжение рас- |
изменения |
циклов до |
серии |
|
тяжения ζmax, |
напряжения |
разрушения |
|
|
МПа |
Aζ, МПа |
N |
1 |
|
330 |
36 |
16000 |
2 |
Б – со сварным |
330 |
27 |
35000 |
3 |
соединением |
330 |
18 |
125000 |
4 |
|
330 |
16 |
150000 |
5 |
|
283 |
23 |
97000 |
|
|
126 |
|
|
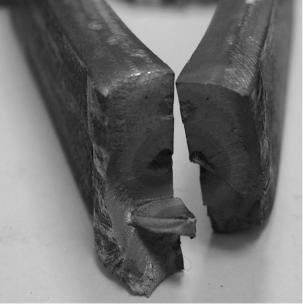
|
|
|
|
Продолжение табл. 1 |
|
6 |
|
250 |
36 |
|
50700 |
7 |
|
250 |
27 |
|
97600 |
8 |
|
250 |
18 |
|
250300 |
|
|
|
|
|
|
9 |
|
205 |
36 |
|
57200 |
10 |
|
205 |
18 |
|
323500 |
11 |
|
250 |
12 |
|
528700 |
12 |
|
430 |
46 |
|
17300 |
13 |
|
330 |
46 |
|
64100 |
14 |
|
330 |
36 |
|
198200 |
15 |
А – без сварно- |
330 |
27 |
|
346000 |
16 |
го соединения |
330 |
18 |
|
497000 |
17 |
|
250 |
36 |
|
239000 |
18 |
|
205 |
36 |
|
322900 |
19 |
|
250 |
12 |
|
632500 |
Испытания проводили до полного разрушения образцов. Результаты свидетельствуют, что поверхность разрушения представляет собой классический усталостный излом, на котором выделяются зона усталости и зона долома. Усталостные трещины наблюдаются как в корневом шве, так и в зоне термического влияния на верхней поверхности образца вблизи облицовочного шва. Их зарождение происходит вблизи пор, утяжин и несплавлений. В дальнейшем трещина может ветвиться в нескольких направлениях с возникновением новых трещин вблизи других концентраторов напряжения (Рис.).
Рис. 1. Излом сварного соединения после усталостных испытаний
127
Установлено существенное влияние амплитуд изменения напряжения при растяжении (в диапазоне от 18 до 36 МПа) на количество циклов до разрушения образца. При значениях Aζ менее 18 МПа практически перестает влиять на количество циклов до разрушения образца, которое может составлять более 105 при испытаниях образцов.
Литература
1.Марочник сталей и сплавов /В. Г. Сорокин, А. В. Волосникова, С. А. Вяткин и др. ; Под общ. ред. В. Г. Сорокина. -М.: Машиностроение, 1989. 640 с.
2.Гумеров А.Г., Зайнуллин Р.С., Ямалеев К.М. Старение труб нефтепроводов. –М. : Недра, 1995. 222 с.
3.Трещиностойкость металла труб нефтепроводов / А.Г. Гумеров, К.М Ямалеев, Г.В. Журавлев, Ф.И. Бадиков. - М. : ООО "НедраБизнесцентр", 2001. 231 с.
Научный руководитель: Ковенский И.М., д.т.н., профессор
Определение температуры максимальной работоспособности твердосплавных режущих пластин
Тверяков А.М., Лактионова Ю.А., Василега Д.С., ТюмГНГУ, г. Тюмень
Температура максимальной работоспособности твердых сплавов в настоящее время определяется по зависимости ударной вязкости от температуры [1].
На графике зависимости ударной вязкости твердого сплава от температуры начало зоны упругопластического разрушения наблюдается при температуре 750°С, которая принимается за температуру максимальной работоспособности режущего твердосплавного инструмента θм.р..
Однако для установления зависимости ударной вязкости от температуры для интересующего сплава необходимо изготовление специальных образцов в большом количестве, а как следствие больших финансовых затрат.
Существует еще один способ [2] определения температуры максимальной работоспособности твердосплавных режущих пластин по характерному участку зависимости критерия вязкости разрушения (трещиностойкости) твердосплавных режущих пластин от температуры.
Недостатком этого способа является необходимость проводить расчеты критерия вязкости разрушения (трещиностойкости) К1с твердосплавных режущих пластин на основании определения диагоналей отпечатков, полученных при нанесении отпечатка индентора микротвердомера, и величины сопротивления развитию трещины. Расчет К1с усложняет процеду-
128
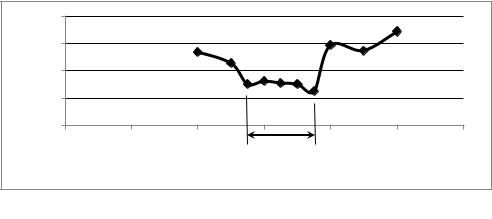
ру определения температуры максимальной работоспособности твердосплавных режущих пластин и повышает погрешность измерений.
Предлагаемый нами способ снижает погрешность измерений структурночувствительной характеристики твердосплавных режущих пластин в результате снижения трудоемкости ее определения и упрощения расчетов.
Снижение погрешности измерений наблюдается за счет выбора в качестве структурночувствительной характеристики среднюю длину трещин lср, возникающих в твердосплавной режущей пластине в процессе испытаний, а в качестве характерного участка на выявленной температурной зависимости принимают интервал температур, в котором средняя длина трещин минимальна (рис. 1).
В отличие от К1с величину температуры максимальной работоспособности твердосплавных режущих пластин определяют без трудоемких расчетов по средней длине трещин lср, что снижает погрешность измерений.
Известно, что с изменением температуры свойства инструментального твердого сплава меняются. С увеличением температуры он переходит из хрупкого в хрупко-пластическое состояние, при этом склонность к развитию трещин снижается, а прочностные характеристики соответственно увеличиваются. Исходя из этого, средняя длина трещины может быть принята в качестве характеристики для определения диапазона температур максимальной работоспособности твердосплавных режущих пластин.
8 |
|
|
|
|
|
|
lср, |
|
|
|
|
|
|
мкм 6 |
|
|
|
|
|
|
4 |
|
|
|
|
|
|
2 |
|
|
|
|
|
|
0 |
|
|
|
|
|
|
0 |
200 |
400 |
600 |
800 |
1000 |
1200 |
|
|
|
|
|
|
Θ, ˚С |
|
|
|
Рис.1. |
|
|
|
|
|
|
θм.р. |
|
|
|
|
|
Литература |
|
|
|
1.Артамонов, Евгений Владимирович. Работоспособность инструментов и физико-механические характеристики инструментальных твердых сплавов и обрабатываемых материалов. [Текст] : монография / Е.В. Артамонов, Д.С. Василега, М.С. Остапенко, В.А. Шрайнер. – Тюмень: «Вектор Бук», 2008. – 160 с.
2.Артамонов, Евгений Владимирович. Выбор инструментального твердого сплава по обрабатываемому материалу на основе физико-механических характеристик. [Текст]: учебное пособие / Е.В. Артамонов, Д.С. Василега, В.Б. Трифонов/под общей ред. М.Х. Утешева. – Тюмень: ТюмГНГУ, 2010. – 128 с.
Научный руководитель: Артамонов Е.В., д.т.н., профессор.
129
Влияние режимов вибрационной обработки в процессе сварки на напряженно-деформированное состояние сварной конструкции
Латыпов А.А., УфГНТУ, г.Уфа
Данные исследования были проведены с целью установления режимов вибрационной обработки в процессе сварки, применяемой для снижения напряженно-деформированного состояния (НДС) сварной конструкции.
Существует необходимость устранения или снижения деформаций сварных конструкций в производственных условиях, в связи с тем, что НДС полученное в процессе сварки значительно затрудняет процесс сборки и ухудшает эксплуатационные свойства изделия.
В процессе сварки в конструкции возникает сложное НДС, причинами которого являются: температурный цикл сварки, неоднородные структурные превращения в металле шва и в зонах термического влияния, а также изменение растворимости газов, окружающих сварной шов.
Известно, что одним из наиболее экономичных и экологичных способов снятия остаточных напряжений является вибрационная обработка. Однако применение данного способа обработки сварных соединений не находит широкого распространения из-за малой изученности данного процесса.
С целью практического изучения влияния вибрационной обработки на напряженно-деформированное состояние сварной конструкции были проведены эксперименты по сварке двух пластин с наложением на них вибрационной нагрузки. Пластины длиной 220 мм, шириной 140 мм и толщиной 3 мм, изготовленные из стали 09Г2С закреплялись к столу, после чего приваривались между собой ручной дуговой сваркой. Вибрационную обработку на изменяющейся по нелинейному закону частоте с амплитудой до 1 мм создавали на специальном столе с помощью вибрационного устройства.
После сварки полученное соединение освобождали от прихватов. Уровень остаточных сварочных напряжений условно определялся по величине глубины прогиба сваренных пластин в продольном направлении сварного шва.
Результаты проведенных экспериментов показывают, что наибольший уровень остаточных напряжений возникает при сварке пластин без вибрационной обработки. При сварке пластин с вибрационной обработкой средняя глубина прогиба значительно понизилась, что подтверждает данные о снижении уровня остаточных напряжений как в сварном шве, так и в конструкции в целом.
Научный руководитель: канд. техн. наук, доцент Файрушин А.М.
130