
- •К 40-ЛЕТИЮ ТЭЦ-21 ОАО МОСЭНЕРГО
- •Полимерные конструкционные материалы на ТЭЦ-21 ОАО Мосэнерго
- •Опыт эксплуатации детандер-генераторного агрегата на ТЭЦ-21 Мосэнерго
- •Совершенствование рабочих процессов в топках котлов ТЭЦ-21 на основе применения современных средств численного моделирования термогазодинамических процессов
- •У истоков света и тепла
- •ТЕПЛОВЫЕ ЭЛЕКТРОСТАНЦИИ
- •Обследование и ремонт фундамента под турбоагрегат мощностью 300 МВт
- •О поправке к учету потерь теплоты с утечками сетевой воды
- •Совершенствование тепловых схем турбоустановок
- •Совершенствование теплозащиты энергетического оборудования ТЭС
- •Разработка технологии пусков котлов ПК-41 на скользящем давлении во всем тракте из различных тепловых состояний
- •ЭНЕРГОСИСТЕМЫ И ЭЛЕКТРИЧЕСКИЕ СЕТИ
- •Защита от однофазных замыканий на землю в сетях 6 кВ собственных нужд ТЭЦ с двумя режимами заземления нейтрали
- •О пересмотре требований ПУЭ по вопросам электробезопасности
- •О системах принудительного охлаждения токопроводов генераторного напряжения
- •Способ определения внутреннего сопротивления сети
- •Опыт создания информационно-вычислительных систем при модернизации традиционных информационных систем котло- и турбоагрегатов ТЭС
- •ЭНЕРГОХОЗЯЙСТВО ЗА РУБЕЖОМ
- •ХРОНИКА
- •“Охрана труда в энергетике-2003”
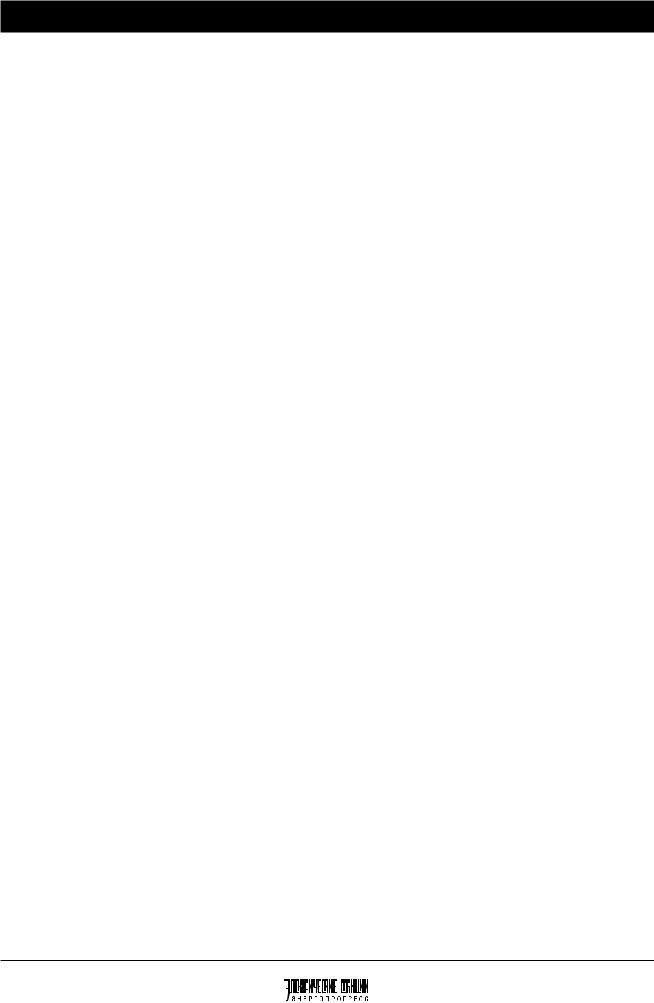
ЭНЕРГОХОЗЯЙСТВО ЗА РУБЕЖОМ
Опыт эксплуатации электростанций, работающих при сверхкритических параметрах,
и опыт применения других передовых технологий
Мураяма Х., Секита М.
Электрик Поуер Девелопмент Ко., Лтд. (EPDC) – Tachibana TPS, Япония
После нефтяного кризиса Япония стала активно увеличивать мощность угольных электростанций для обеспечения энергетической безопасности и экономичности. Однако работающие на каменном угле энергетические установки уступали в эффективности энергоустановкам, работающим на жидком топливе и природном газе. Для угольных энергоустановок характерны большие выбросы частиц золы, оксидов серы и азота. При их работе нужно тратить больше вырабатываемой электроэнергии на природоохранное оборудование и пода- чу угля. Важной задачей поэтому стало повышение КПД угольных энергоустановок.
Помимо этого, принятие в декабре 1997 г. в Киото на Всемирной конференции (СОР3) Протокола по сохранению нынешних климатических условий на Земле стимулировало развитие движения за сокращение выбросов углекислого газа. Критически настроенная общественность отметила, что углесжигающие электростанции являются одним из крупных источников углекислого газа. Поэтому актуальность повышения КПД угольных электростанций еще более возрастает.
Научно-исследовательские, опытно-конструк- торские и технологические работы по повышению эффективности традиционных энергоустановок, работающих на угольной пыли, начались 20 лет назад. Примерами достижений в этом направлении являются технологии использования сверхкритического давления и применения еще более высоких сверхкритических параметров пара. Эта технология уже подтвердила высокие показатели на новейшей мощной сжигающей уголь электростанции бухты Татибана (1050 МВт, 25 МПа, 600°С, 610°С).
Наряду с этим направлением для повышения эффективности угольных электростанций разрабатываются и создаются парогазовые опытные установки, реализующие процессы сжигания угля под давлением в топках с кипящим слоем [(PFBC – Pressurized Fluidized Bed Combustion Combined Cycle) русское обозначение ПГУ с КСД], и внутрицикловые – со сжиганием газификационного угля [(IGCC – Integrated Coal Gasification Combined Cycle) русское обозначение ПГУ с ГФ]. В Япо-
нии уже эксплуатируются промышленные установки PFBC. Компания EPDC занимается усовершенствованием этого процесса для улучшения экологических, эксплуатационных и экономиче- ских показателей.
В настоящей статье представлены положение дел с разработкой и внедрением суперкритических параметров (ССКД) и технические достижения в разработке технологии, а также общие сведения о новейшей угольной электростанции, эксплуатируемой EPDC.
Разработка ССКД. Начало и задачи разработки. Сверхкритические параметры пара начали применяться на тепловых электростанциях Японии в 1967 г. Почти 20 лет эти параметры практи- чески держались на уровне 24,1 МПа, 538/538°С или 538/566°С.
Первая энергоустановка с суперсверхкритиче- скими параметрами пара (суперсверхкритическими параметрами называются давление и температура, превышающие 24,1 МПа и 593°С) начала работать в США еще в 1957 г. За следующие 10 лет было введено еще несколько блоков с аналогичными параметрами. На них наблюдались коррозия при высоких температурах и окисление в паровой среде, препятствовавшие стабильной работе и вынуждавшие эксплуатировать построенные установки при пониженных параметрах пара. По этой причине и из-за экономических проблем строительство энергоустановок с суперкритическими параметрами пара было прекращено.
Нефтяной кризис возродил приостановившееся стремление к повышению КПД угольных электростанций путем повышения параметров пара. К этому времени производители материалов для энергооборудования успели разработать и выпустить коррозионно-устойчивые стали с достаточно высокими прочностными и экономическими показателями, что помогло создать промышленные электростанции, работающие с суперкритическими параметрами пара.
Для повышения обычных сверхкритических параметров пара необходимо решить ряд задач, касающихся турбин и котлов:
58 |
2003, ¹ 10 |

2 |
|
|
4 |
|
|
|
14 |
|
êãñ/ìì |
12 |
|
|
|
Добились |
|
|
|
|
|
|
|
|
|
|||
|
|
|
|
|
çà ñ÷åò |
|
|
|
|
|
3 |
|
|
увеличения |
|
|
|
растяжении, |
|
|
|
|
|
|
||
|
|
|
|
толщины |
12 |
|
||
10 |
|
|
|
|
|
|||
|
|
|
|
стенки |
|
|||
|
|
|
|
|
|
|
||
8 |
|
|
|
|
|
|
ìì |
|
Допустимоенапряжениепри |
|
|
|
|
|
|
10 |
Толщинастенки, |
6 |
|
|
|
|
|
|
||
|
2 |
|
|
|
Çà ñ÷åò |
|
||
|
|
À |
|
обеспечения |
8 |
|||
4 |
|
|
|
прочности |
||||
|
|
|
|
|
||||
|
1 |
Мацуура¹1 |
Мацуура¹2 |
|
Татибана¹1 |
|
||
2 |
|
|
6 |
|||||
|
|
Бухта |
||||||
0 |
|
|
||||||
|
|
|
|
|
|
|
|
|
|
500 |
550 |
600 |
|
650 |
700 |
|
|
|
|
|
Температура металла, °С |
|
|
|
) ( +) * * *
1
1 – толщина стенки труб из стали SUS304J1HTB; 2 – то же из стали SUS321J1HTB; 3 – напряжение стали SUS321J1HTB; 4 – то же стали SUS304J1HTB; % – расчетная точка; Мацуура ¹ 1, Мацуура¹ 2 – котлы энергоблоков ¹ 1, 2 ТЭС Мацуура; Бухта Татибана ¹ 1 – котел энергоблока ¹ 1 ТЭС бухты Татибана; А – для этой точки наружный диаметр труб энергоблока ¹ 2 ТЭС Мацуура одинаков с диаметром труб энергоблока ¹ 1 ТЭС бухты Татибана
1. Роторы турбин, работающих со сверхкрити- ческими параметрами пара, традиционно изготавливаются из стали CrMoV. Но для работы при температуре выше 593°С необходима сталь, температурная прочность которой выше. Вообще от материалов турбин для работы при суперкритических параметрах пара требуется высокая прочность на разрыв в условиях ползучести, так как на их лопатки действуют центробежные силы, а корпуса и другие неподвижные детали испытывают длительные напряжения, вызванные высоким внутренним давлением высокотемпературного пара.
В металле деталей турбины возникают также тепловые напряжения при пуске и останове из-за изменения температуры пара. Для уменьшения их нужны материалы с небольшим коэффициентом теплового расширения и большим коэффициентом теплопроводности.
Для уменьшения повреждаемости под действием тепловых напряжений материалы должны иметь высокие предел текучести и усталостную прочность при низких температурах.
Кроме того, требуются хорошая свариваемость различных материалов, стойкость к хрупкому излому и надежность арматуры, работающей при высоких температурах и давлениях.
2. Повышение параметров пара связано с увеличением толщины стенок труб, работающих под высоким давлением. Это имеет негативную сторону – увеличение массы котлов и снижение маневренности (способности быстро воспринимать изменения нагрузки).
2 |
12 |
|
|
|
|
|
êãñ/ìì |
|
|
|
|
|
|
|
4 |
|
|
|
|
|
10 |
|
|
|
200 |
|
|
Допустимоенапряжениеприрастяжении, |
|
|
|
|
||
|
3 |
|
|
Добились за счет |
|
|
8 |
|
|
увеличения |
|
||
|
|
|
толщины стенки |
|
||
6 |
|
Улучшение свойств |
материала |
150 |
Толщинастенки,мм |
|
|
Мацуура¹1 |
Бухта Татибана¹1 |
||||
4 |
|
|||||
|
¹2 |
|||||
2 |
|
1 |
Мацуура |
100 |
||
|
2 |
|
За счет обеспечения |
|||
|
|
|
||||
0 |
|
|
прочности |
|||
|
|
|
||||
|
|
|
|
|||
500 |
550 |
|
600 |
650 |
||
|
|
Температура металла, °С |
|
) ( +) * * . 1
1 – толщина стенки труб из стали STPA28(SCMV28); 2 – то же из стали STPA27; 3 – напряжение стали STPA27; 4 – то же стали STPA28(SCMV28); % – расчетная точка
Пароперегреватель (в частности, его высокотемпературные пучки) работает в особо тяжелых условиях. Необогреваемые трубы большого диаметра, расположенные вне теплообменной зоны, должны обладать прочностью под высоким давлением. При этом, если увеличивать толщину их стенок, прочность увеличивается, зато растут тепловые напряжения, вызываемые разностью температуры между наружным и внутренним пространствами трубы при изменении нагрузки. Следовательно, необходимы теплоустойчивые высокопроч- ные материалы высокого качества.
Материалы парогенерирующих труб должны иметь хорошие показатели высокотемпературной прочности и устойчивости к окислению в паровой среде.
Исследования, проведенные EPDC для использования суперкритических параметров пара. К работе над суперкритическими параметрами EPDC приступила в 1980 г. История ее научно-исследо- вательских и опытно-конструкторских работ в этом направлении разделена на две фазы. Первая выполнена до 1994 г., а вторая с 1994 по 2000 г. Эти работы осуществлялись при сотрудничестве с производителями материалов, котлов и турбин и получили с середины их проведения поддержку от правительства.
Фаза 1 состояла из двух этапов. На первом проводились испытания ферритных сталей при параметрах пара 31,4 МПа, 593/593/593°С, на втором – аустенитных сталей при 34,3 МПа, 649/649/649°С. Стали ферритного класса уже применялись в оборудовании со сверхкритическими параметрами пара. Для приспособления к суперкритическим параметрам они были улучшены, а их прочность повышена. Иными словами, на этапе 1 разработка шла по пути эволюции технологии сверхкритиче- ских параметров пара.
На этапе 2 были проверены материалы для наиболее тяжелых в мире условий и параметров
2003, ¹ 10 |
59 |
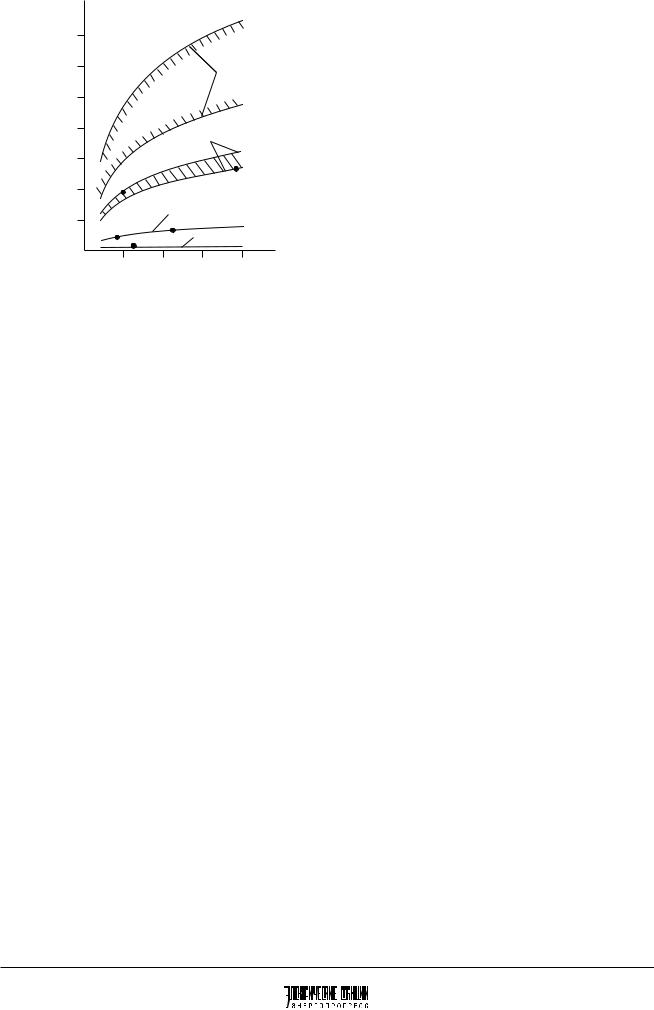
|
400 |
|
|
|
|
ìêì |
350 |
|
|
|
|
|
|
|
|
|
|
отложений, |
300 |
|
|
|
4 |
|
|
|
|
||
250 |
|
|
|
|
|
|
|
|
|
|
|
шлаковых |
200 |
|
|
3 |
|
|
|
|
|
||
150 |
|
|
|
|
|
Толщина |
|
|
|
|
|
100 |
|
|
|
|
|
|
|
|
|
|
|
|
50 |
|
|
2 |
|
|
|
|
|
|
|
|
|
|
|
1 |
|
|
0 |
|
|
|
|
|
0 |
25 |
50 |
75 |
100 |
|
|
Время воздействия пара, тыс. ч |
# 2 9 / ( . : *
+ : * 0 +) /. :
0 * * * + "%%K41
% – данные экспериментов и измерений на действующем оборудовании; —— – предполагаемая кривая; 1 – нержавеющая сталь группы 18-8 с обработкой дробеструйкой; 2 – нержавеющая сталь группы 18-8 без обработки дробеструйкой; 3 – сталь 9Cr; 4 – сталь 2 1/3Cr1Mo
пара. Испытания проводились в основном на классических аустенитных сталях, отличающихся проч- ностью и стойкостью при высокой температуре.
На каждом этапе фазы 1 проводили испытания элементов котлов для определения характеристик материалов и испытания деталей турбин из новых материалов, приведенных в òàáë. 1, на специально изготовленной модельной турбине. В заключение проводились демонстрационные испытания энергоустановки мощностью 50 МВт.
При испытаниях на этапах 1 и 2 фазы 1 по материалам для котлов получены положительные результаты по коррозионной стойкости, устойчивости к окислению в паровой среде и длительной механической прочности. Аустенитные материалы для турбин, испытанные на этапе 2, наоборот, ока-
Ò à á ë è ö à 1
зались практически негодными к применению изза большого коэффициента линейного расширения, малой теплопроводности, быстрого исчерпания срока службы вследствие малоцикловой усталости при пуске-останове и нерентабельности.
Испытания фазы 2 были организованы непосредственно для создания технологии с суперкритическими параметрами (30 МПа, 630/630°С), которая может быть реализована в короткие сроки за счет применения ферритных материалов, экономические и эксплуатационные достоинства которых до этого были подтверждены. Были проведены длительные испытания выбранных для котлов новых материалов (см. òàáë. 2) и испытания на вращающихся роторах материалов, выбранных для турбин (òàáë. 3, 4).
Испытания подтвердили, что материалы, подобранные для турбин и котлов, имеют удовлетворительные свойства и годятся для применения в условиях суперкритических параметров пара.
Применение суперкритических параметров пара на промышленных энергоблоках. Â òàáë. 5 представлены основные угольные энергоблоки большой мощности, которые были построены в Японии в последние годы. Некоторые из них уже работают при температурах пара 593°С и выше, т.е. при суперкритических параметрах.
На электростанциях, эксплуатируемых EPDC, энергоблок ¹ 2 электростанции Мацуура и недавно введенные в эксплуатацию энергоблоки ¹ 1, 2 электростанции бухты Татибана успешно работают с суперкритическими параметрами пара. Далее описываются особенности энергоустановок этих двух электростанций.
Общие сведения об энергоблоках с суперкрити- ческими параметрами. Â òàáë. 6 сопоставлены суперкритические параметры пара энергоблока ¹ 2 электростанции Мацуура и энергоблоков ¹ 1, 2 электростанции бухты Татибана со сверхкритиче- скими параметрами пара энергоблока ¹ 1 электростанции Мацуура. За счет применения материалов с высокотемпературной стойкостью и охлаждения турбин температуры пара на энергоблоке ¹ 2 электростанции Мацуура и на энергоблоках
( . : + ) ( * * . > * / ( *( 0 9 /
|
|
Испытанные материалы |
|
Деталь турбины |
|
|
|
Ýòàï 1 |
|
Ýòàï 2 |
|
|
|
||
|
|
|
|
Ротор |
Кованая сталь 12Cr |
|
Кованая сталь А286 |
|
|
|
|
Внутренний корпус турбины высокого |
Литая сталь 12Cr |
|
Кованая нержавеющая сталь SUS316H |
давления |
|
||
|
|
|
|
|
|
|
|
Внутренний корпус турбины среднего |
|
Литая сталь 12Cr |
|
давления |
|
||
|
|
|
|
|
|
|
|
Наружный корпус |
|
Литая сталь 2,25CrMo |
|
|
|
|
|
Селекторный клапан |
Кованая нержавеющая сталь SUS316H |
||
|
|
|
|
Главный паропровод |
|
SUS316HTP |
|
|
|
|
|
60 |
2003, ¹ 10 |

¹ 1, 2 электростанции бухты Татибана повышены до 593/593°С и 600/610°С соответственно.
Повышение параметров пара до суперкритиче- ских позволило снизить удельные расходы топлива на выработку электроэнергии на энергоблоке ¹ 2 электростанции Мацуура на 3%, а на энергоблоках
¹1, 2 электростанции бухты Татибана – на 4%.
Âг. Иокогама планируется ввести в эксплуата-
цию энергоустановку мощностью 600 МВт с такими же, как на электростанции бухты Татибана, параметрами пара.
Далее более подробно рассмотрены техниче- ские решения, большинство которых применено для реализации суперкритических параметров пара на энергоблоках ¹ 1, 2 электростанции бухты Татибана, являющихся новейшими в данный момент установками, работающими в наиболее тяжелых условиях.
Меры, принятые для обеспечения работы котлов с суперкритическими параметрами пара. Теплопередающие поверхности котлов усовершенствованы для обеспечения необходимых параметров пара. Их увеличение при повышении температуры пара минимизировано путем оптимизации компоновки основного и промежуточного пароперегре-
Ò à á ë è ö à 2
( . : > . ( 9 /
вателей и модификации вторичного пароперегревателя.
Система управления температурой пара изменена. Применены трехступенчатая каскадная система впрысков для регулирования температуры пара в главном паропроводе, а также системы вторичной циркуляции газов и параллельной задвижки газа в задней теплопередающей зоне для регулирования температуры пара при вторичном перегреве.
Для узлов, работающих при высоких температурах, выбраны оптимальные материалы. Для труб высокотемпературной зоны перегрева применены аустенитные нержавеющие стали 18Cr9Ni и 18Cr10Ni с дробеструйной обработкой внутренних поверхностей, обладающие высокой стойкостью к высокотемпературной коррозии, окислению водяными парами и высокой жаропрочностью.
Для высокотемпературных необогреваемых деталей выбрана ферритная нержавеющая сталь 9Cr1Mo, имеющая высокую стойкость к окислению водяными парами и жаропрочность.
 òàáë. 7 указаны материалы, примененные в высокотемпературных зонах котлоагрегата, и наиболее высокие давление и температура пара, кото-
Деталь: марка стали |
Основной компонент |
Фирма-изготовитель |
|
|
|
Трубы экономайзера: |
|
|
WT780C |
0,8Cr0,5MoCu |
Nippon Steel Co |
TEMPALOY HT780 |
0,6 Cr 0,3MoCu |
NKK |
|
|
|
Трубы настенных экранов: |
|
|
NF1H |
1,25Cr1MoVNb |
Nippon Steel Co |
HCMV3 |
1,25Cr1MoV |
Sumitomo Metal Industries, Ltd. |
TEMPALOY F-2W |
2Cr0,5MoWVTi |
NKK |
|
|
|
Трубы пароперегревателя: |
|
|
ферритные стали: |
|
|
NF616 |
9Cr0,5Mo1,8WVNb |
Nippon Steel Co |
HCM12A |
12Cr0,4Mo2WCuVNb |
Sumitomo Metal Industries, Ltd. |
TEMPALOY F-12M |
12Cr0,7Mo0,7WCuVNb |
NKK |
SAVE12 |
11Cr3WCoVNbTa |
Sumitomo Metal Industries, Ltd. |
NF12 |
11Cr2,6WMoCoVNb |
Nippon Steel Co |
аустенитные стали: |
|
|
SUPER304H |
18Cr9Ni3CuNbN |
Sumitomo Metal Industries, Ltd. |
TEMPALOY AA-1 |
18Cr10Ni3CuNbTiN |
NKK |
NF709 |
20Cr25NiMoNbTiN |
Nippon Steel Co |
SAVE25 |
23Cr19Ni3,5Cu1,5WNbN |
Sumitomo Metal Industries, Ltd. |
|
|
|
Коллекторы/главный паропровод: |
|
|
NF616 |
9Cr0,5Mo1,8WVNb |
Nippon Steel Co |
HCM12A |
11Cr0,4Mo2WCuVNb |
Sumitomo Metal Industries, Ltd. |
TEMPALOY F-12M |
12Cr0,7Mo0,7WCuVNb |
NKK |
NF12 |
11Cr2,6WMoCoVNb |
Nippon Steel Co |
|
|
|
|
|
|
2003, ¹ 10 61
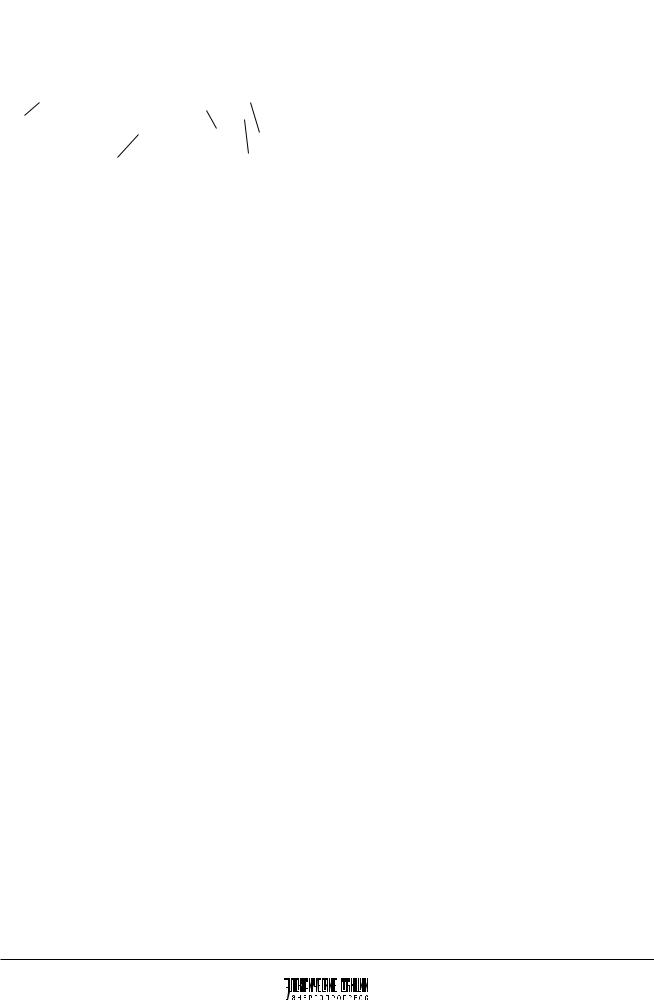
2 |
Внутренний корпус |
|
1
4
3
5
6
Ротор турбины высокого давления
6 4 0 8. + ) ( (
. 1
& – охлаждающий пар; - - - – протекающий пар высокой температуры; 1 – реактивная ступень высокого давления; 2 – рабочая лопатка регулирующей ступени; 3 – обратный паровой канал; 4 – сопловая коробка; 5 – сопло регулирующей ступени; 6 – канал для подвода охлаждающего пара
рые испытывают соответствующие детали, а на ðèñ. 1, 2 сопоставлены условия работы труб четвертого пакета промежуточного пароперегревателя и главного паропровода энергоблоков ¹ 1, 2 ТЭС Мацуура и энергоблока ¹ 1 ТЭС бухты Татибана.
Примененные на новых энергоблоках материалы для труб обладают одинаковыми с традиционными или более высокими показателями стойкости против окисления водяными парами внутренних поверхностей труб. На ðèñ. 3 показана зависимость толщины оксидной пленки, образующейся на внутренней поверхности труб, от времени воздействия на них пара при температуре 600°С.
Меры, принятые для обеспечения работы турбин с суперкритическими параметрами пара. Наряду с применением материалов с высокой жаропрочностью в конструкцию турбин внесены важные изменения.
 òàáë. 8 è 9 приведены данные о материалах деталей турбин высокого и среднего давления. В качестве материала роторов для турбины энергоблока ¹ 2 электростанции Мацуура применили кованую сталь 12Cr, а для турбин электростанции бухты Татибана – усовершенствованную кованую сталь 12Cr. Суть усовершенствования заключается в повышении жаропрочности за счет добавок, в частности, вольфрама. Для высокотемпературных рабочих лопаток турбин ТЭС бухты Татибана также использована усовершенствованная сталь 12Cr.
Сталь 9Cr применена для ответственных клапанов и пароподводящих патрубков, а литая сталь 12Cr – для корпусов.
Турбины высокого давления энергоблока ¹ 2 ТЭС Мацуура и энергоблока ¹ 2 ТЭС бухты Татибана выполнены с охлаждением роторов. Для этого в пространство между ротором и сопловыми коробками регулирующей ступени предусматривается подвод охлаждающего пара из камеры регулирующей ступени через каналы, выполненные в
1
2 |
|
|
|
Пергретый пар |
Охлаждающийпар |
(отрабатывающийпар высокогодавления) |
|
|
|
|
|
|
|
3 |
4 |
5 |
6 |
|
|
|
|
|
|
|
|||
|
|
|
|
|
||
A |
|
A |
|
|
|
|
|
|
|
|
|
|
|
A – A |
|
|
|
|
11 |
|
|
|
7 |
|
10 |
|
|
8
9
D 4 0 8. + ) ( .
. 1
1 – термоэлектрический термометр; 2, 4, 6 – направляющая лопатка ¹ 3, 2, 1 соответственно; 3, 5 – рабочая лопатка ¹ 2, 1 соответственно; 7 – рабочая лопатка первой и второй ступени; 8 – ротор турбины среднего давления; 9 – зазор для охлаждения; 10 – охлаждающий пар; 11 – ротор турбины
теле диска. Этот пар циркулирует затем через обратный паровой канал и каналы в сопловых коробках в надбандажное пространство регулирующей ступени. Охлаждающий пар запирает протечки пара высокой температуры из осевого зазора регулирующей ступени и предотвращает повышение температуры ротора (ðèñ. 4).
Турбины среднего давления энергоблока ¹ 2 ТЭС Мацуура и энергоблоков ¹ 1, 2 ТЭС бухты Татибана также выполнены с охлаждением ротора и хвостовика рабочей лопатки первой и второй ступени. Оно осуществляется отработавшим в турбине ВД паром, который подводится в пространство между ротором и паровпуском (ðèñ. 5).
Пароподводящие патрубки турбин высокого и среднего давления энергоблока ¹ 2 ТЭС Мацуура
èэнергоблоков ¹ 1, 2 ТЭС бухты Татибана выполнены двухстенными. Внешние корпуса турбин отлиты из стали CrMo, свойства которой обеспечи- вают работу лишь при обычных сверхкритических параметрах пара. Внутренние пароподводящие патрубки, соприкасающиеся с высокотемпературным паром, изготовлены из стали 9Cr, а внешние – из стали CrMo. В пространство между внешними
èвнутренними патрубками подводится охлаждающий пар.
Сопловая коробка двухпоточной турбины вы-
сокого давления для предотвращения тепловых напряжений выполнена сборной, сварной, с центральной опорой, что уменьшило тепловые деформации.
Эта мера предотвращает возможные изнашивания или даже повреждения с пригоранием подшипников ротора. Шейки роторов, изготовленные из стали 12Cr или улучшенной стали 12Cr, выполнены с наплавкой из стали с низким содержанием хрома.
62 |
2003, ¹ 10 |
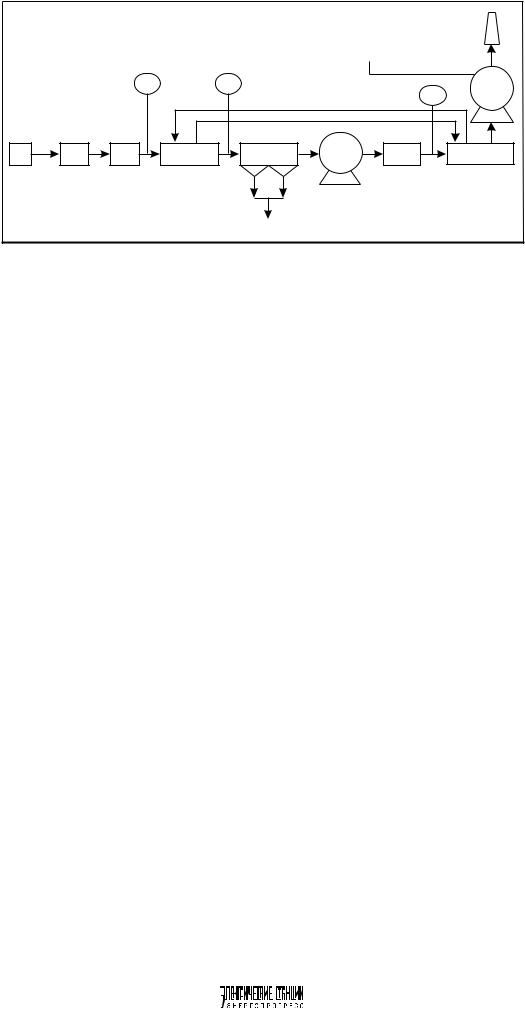
9
|
|
|
133°Ñ |
90°Ñ |
|
|
|
8 |
|
|
|
|
|
|
|
48°Ñ |
|
|
|
|
|
|
|
|
|
|
1 |
2 |
3 |
4 |
5 |
6 |
2 |
|
7 |
Система отработки золы
" * 8 / (0 + : ) 0 4 )+0 ( ) 1
1 – котел; 2 – очистка от оксидов азота; 3 – воздухоподогреватель; 4 – газо-газовый теплообменник (охлаждение); 5 – электрофильтр; 6 – дымосос; 7 – газо-газовый теплообменник (подогрев); 8 – вспомогательный вентилятор; 9 – дымовая труба
Для повышения КПД длина рабочих лопаток |
соответственно более 9 и 6 тыс. ч после пуска в |
|||||||||||||||||||
последней ступени ЦНД увеличена: для энерго- |
июле и декабре 2000 г. |
|
|
|
|
|
|
|
||||||||||||
блока ¹ 1 ТЭС бухты Татибана до 1219, а для |
Особенности новейших угольных энергобло- |
|||||||||||||||||||
энергоблока ¹ 2 – до 1168 мм. |
|
|
|
êîâ ÒÝÑ. Высокоэффективное природоохранное |
||||||||||||||||
Для энергоблока ¹ 2 ТЭС Мацуура и энерго- |
оборудование. Энергоблоки ТЭС бухты Татибана |
|||||||||||||||||||
блока ¹ 2 ТЭС бухты Татибана проточная часть и |
для очистки дымовых газов и уменьшения выбро- |
|||||||||||||||||||
лопатки ЦНД спроектированы с применением |
сов в атмосферу оборудованы установками ката- |
|||||||||||||||||||
трехмерных расчетов течения пара. Это позволило |
литического селективного восстановления окси- |
|||||||||||||||||||
повысить КПД всего ЦНД более чем на 0,6% (по |
дов азота, газо-газовыми плотными теплообмен- |
|||||||||||||||||||
расчетной оценке). |
|
|
|
|
|
никами, |
электрофильтрами, |
работающими |
ïðè |
|||||||||||
На последней ступени ЦНД энергоблока ¹ 2 |
температуре газов 90°С и мокроизвестняковыми |
|||||||||||||||||||
ТЭС бухты Татибана укрупнили хвостовики лопа- |
установками очистки газов от оксидов серы с по- |
|||||||||||||||||||
ток и межлопаточные каналы в целях снижения |
лучением гипса. Последовательность расположе- |
|||||||||||||||||||
возникающих напряжений, а также применили це- |
ния газоочистных устройств показана на ðèñ. 6. |
|||||||||||||||||||
льные бандажированные лопатки для снижения |
По договоренности с местной администрацией со- |
|||||||||||||||||||
вибрационных напряжений. Все это привело к по- |
держание оксидов серы в отходящих дымовых га- |
|||||||||||||||||||
вышению надежности турбин. |
|
|
|
зах не должно превышать 50 млн – 1, оксидов азота |
||||||||||||||||
Эксплуатация энергоблоков, работающих с су- |
45 ìëí – 1 è çîëû 10 ìã/ì3 в нормальных условиях. |
|||||||||||||||||||
перкритическими параметрами пара. Энергоблок |
В действительности достигнуты вдвое меньшие |
|||||||||||||||||||
¹ 2 ТЭС Мацуура и энергоблоки ¹ 1, 2 ТЭС бух- |
выбросы. |
|
|
|
|
|
|
|
|
|
||||||||||
ты Татибана эксплуатируются со скользящим дав- |
В апреле |
2001 г. начал |
|
работать энергоблок |
||||||||||||||||
лением пара на частичных нагрузках. Это позволя- |
¹ 1 ТЭС Синьисого, на котором впервые для элек- |
|||||||||||||||||||
ет повысить маневренность, уменьшить время пу- |
тростанций Японии установлена очистка дымо- |
|||||||||||||||||||
сков и быстрее изменять нагрузки. Блоки обычно |
вых газов от оксидов серы сухим методом с испо- |
|||||||||||||||||||
эксплуатируются непрерывно с изменением на- |
льзованием активированного угля. Она будет рабо- |
|||||||||||||||||||
грузки по суточному графику, редкими останова- |
тать вместе с установкой селективной каталитиче- |
|||||||||||||||||||
ми и последующими пусками (особенно для ТЭС |
ской очистки газов от оксидов азота и электрофи- |
|||||||||||||||||||
бухты Татибана). |
|
|
|
|
|
|
льтром. При такой системе очистки содержание в |
|||||||||||||
Энергоблок ¹ 2 ТЭС Мацуура проработал бо- |
дымовых газах оксидов серы |
уменьшится до |
||||||||||||||||||
лее 32 тыс. ч после ввода в эксплуатацию в июле |
20 ìëí – 1, азота – до 20 млн – 1 и оксидов золы – до |
|||||||||||||||||||
1997 г., а энергоблоки ¹ 1, 2 ТЭС бухты Татибана – |
10 ìã/ì3 в нормальных условиях. Установка очист- |
|||||||||||||||||||
Ò à á ë è ö à |
3 |
|
|
|
|
|
|
|
|
|
|
|
|
|
|
|
|
|
|
|
L : : *-0&> * /+ (0 . / * |
|
|
|
|
|
|
|
|||||||||||||
|
|
|
|
|
|
|
|
|
|
|
|
|
|
|
|
|
|
|
|
|
Сталь |
|
C |
|
Si |
Mn |
Ni |
Cr |
Mo |
V |
|
Nb |
W |
|
N |
|
Co |
|
B |
|
Re |
|
|
|
|
|
|
|
|
|
|
|
|
|
|
|
|
|
|
|
|
|
Марка «C» |
|
0,11 |
|
0,04 |
0,51 |
0,5 |
11,02 |
0,15 |
0,19 |
|
0,08 |
2,61 |
|
0,029 |
|
2,89 |
|
0,014 |
|
– |
Марка «D» |
|
0,11 |
|
0,05 |
0,5 |
0,6 |
10,5 |
0,10 |
0,2 |
|
0,10 |
2,5 |
|
0,03 |
|
1,0 |
|
0,01 |
|
0,2 |
|
|
|
|
|
|
|
|
|
|
|
|
|
|
|
|
|
|
|
|
|
|
|
|
|
|
|
|
|
|
|
|
|
|
|
|
|
|
|
|
|
|
2003, ¹ 10 |
|
|
|
|
|
|
|
|
|
|
|
|
|
|
|
|
|
|
63 |
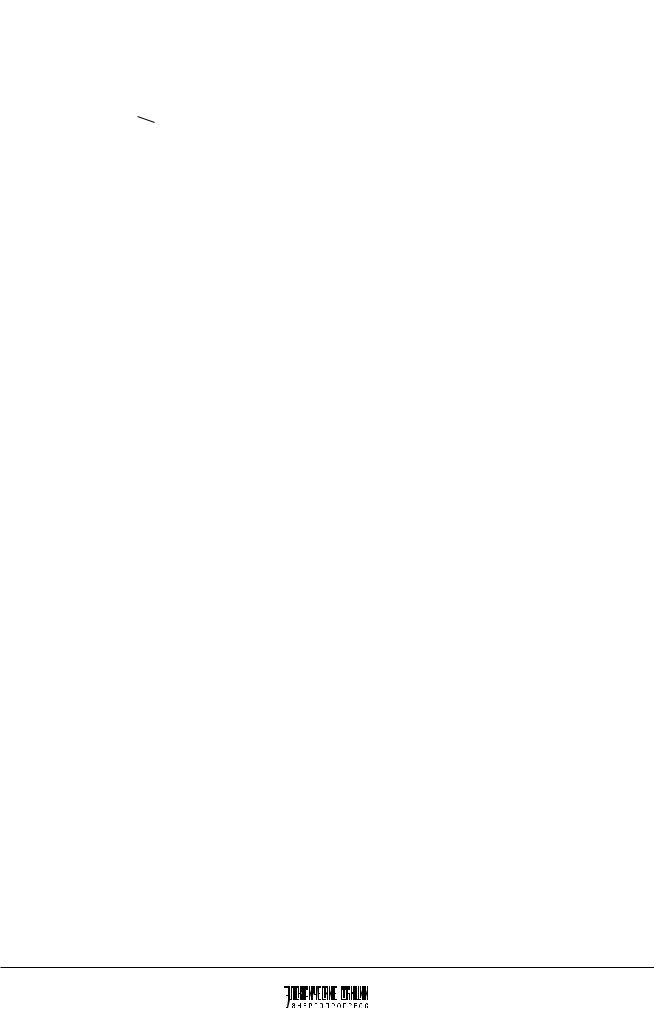
4 |
|
5 |
|
|
Селективное |
|
Охладитель |
|
|
|
некаталитическое |
|
уловленной |
6 |
|
|
восстановление NOõ |
|
çîëû |
|
|
|
|
|
|
|
|
|
9 |
|
Çîëà |
|
|
|
10 |
|
Çîëà |
|
|
|
|
|
|
|
|
|
|
2 |
|
7 |
2 |
Çîëà |
7 |
Селективная |
|
|
|
|
|
|
|
|
|
|
|
каталитическая |
|
|
|
|
|
азотоочистка |
|
|
|
|
|
11 |
Уголь |
|
|
|
Уголь |
|
известняк, |
12 |
|
|
известняк, |
|
âîäà |
|
|
||
1 |
1 |
|
âîäà |
||
a) |
|
|
á) |
||
|
|
|
|
E 4 * .-: 32 <4; > 9 / & 32 <4; > 9 / &1
1 – дымовая труба; 2 – газовая турбина; 3 – генератор 14,8 МВт; 4 – керамический трубчатый фильтр (CTF) 2; 5 – первичный циклон ( 7); 6 – наружный корпус; 7 – паровая турбина; 8 – генератор 56,2 МВт; 9 – циклон циркуляции золы ( 2); 10 – вертикальная труба ( 2); 11 – экономайзер; 12 – котел
ки от оксидов серы активированным углем также способна удалять оксиды азота и их содержание будет таким же, как в дымовых газах ТЭС, работающих на природном газе.
Оборудование для разгрузки, транспортировки и хранения угля. При постройке ТЭС бухты Татибана важной задачей было сокращение площади участков хранения и транспортировки угля и обеспечение эксплуатационных удобств, технологич- ности ремонта и экологичности. С учетом этих требований сооружены бункеры, использованы высокопроизводительные разгрузчики угля, для подачи части угля применены пневмотранспортеры с наибольшей в мире производительностью и вертикальные конвейеры.
Расположение щита управления. Для уменьшения трудоемкости, улучшения организованно-
Ò à á ë è ö à 4
(> , . *
) (0 (0 . 0
Деталь |
Материал |
|
|
Фланцы на главных па- |
|
ропроводах: |
|
корпуса |
Высокопрочная кованая сталь 9Cr |
болты |
Сплав на основе никеля |
гайки |
Òî æå |
|
|
Фланцы клапанов на |
|
главных паропроводах: |
|
корпуса |
Новая кованая сталь 12Cr |
болты |
Сплав на основе никеля |
гайки |
Сталь 19Cr12Ni3W |
|
|
Корпуса: |
|
корпуса |
Высокопрочная кованая сталь 9Cr |
болты |
Высокопрочная кованая сталь 12Cr |
|
|
Стопорные клапаны: |
|
корпуса |
Новая кованая сталь 12Cr |
штоки клапанов |
Сталь 40Ni13CrTiMoFe(Bal.) |
|
|
сти работ и условий труда щит управления, с которого централизованно управляют практически всем оборудованием, размещен не в котлотурбинном цехе, а в отдельном административном корпусе.
Управляющие операции осуществляются не с помощью тумблеров, а компьютерной мышью с отображениями на шести 100-дюймовых (2,54 м) экранах.
Гармония с природой. ТЭС бухты Татибана построена на берегу островка, расположенного в бухте Татибана. Берег насыпан грунтом, вырытым из того же островка. ТЭС окружена зеленью и морем. Ее сооружения соответственно окрашены и расположены так, чтобы они вписались в пейзаж.
Разработка ПГУ со сжиганием угля в кипящем слое под давлением (ПГУ с КСД). Энергетики западно-европейских стран давно обратили внимание на экономичность ПГУ с КСД и начали разработку и испытания энергоблоков этого типа. В целях быстрого внедрения этой технологии в своих тепловых электростанциях EPDC во второй половине 80-õ годов построила на территории лаборатории по разработке технологии использования угля “Вакамацу” демонстрационную ПГУ с КСД мощностью 71 МВт. В трехгодовой период (фаза 1), начавшийся с 1994 г., испытания проводились для демонстрации экологической безопасности, экономичности и других достоинств этой технологии. Достижения этого периода использовались затем при создании промышленных ПГУ с КСД большей мощности.
За 10 лет, прошедших после начала исследований, общественные требования к экологической безопасности и экономичности ужесточились. Это повлияло на внедрение промышленных ПГУ с КСД. Существовала и другая проблема. Характеристики топки кипящего слоя традиционной конструкции, использованной при испытаниях фазы 1, не позволяли регулировать размеры частиц материалов, образующих кипящий слой, что не давало возможности использовать различные виды топлива, в частности, уголь с высоким содержанием серы.
64 |
2003, ¹ 10 |
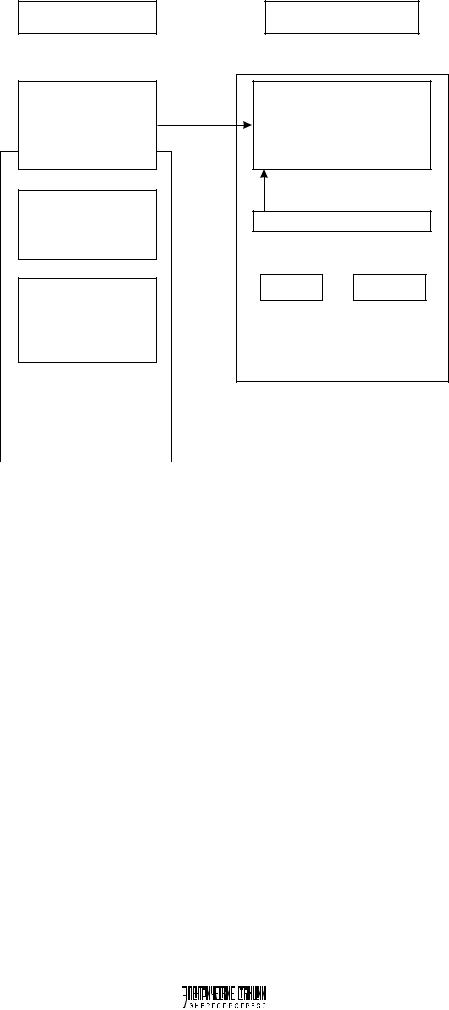
Высокие экологические |
Снижение производственных |
|||
характеристики |
|
затрат |
|
|
|
Эксплуатационные |
|||
Основные характеристики |
|
затраты |
|
|
Низкий уровень выбросов |
Расширение ассортимента |
|||
SOx < 10 ìëí–1 |
топлива [некачественный уголь, |
|||
NOx < 10 ìëí–1 |
мазут с высоким содержанием серы, |
|||
Частицы меньше 1 мг/м3 |
тяжелые мазуты, нефтяной кокс |
|||
в нормальных условиях |
|
(биомасса)] |
||
|
Очень высокий КПД сгорания |
|||
Повышение эффективности |
|
ñ > 99,9 % |
||
|
|
|
||
связывания оксидов серы |
Сокращение потребности в топливе |
|||
вследствие уменьшения |
||||
|
|
|
||
размеров известняковых |
|
|
|
|
частиц |
Повышение времени пребывания |
|||
|
частиц в кипящем слое |
|||
Сочетание селективного |
Возврат |
èëè |
Снижение |
|
çîëû |
|
|||
каталитического |
качества золы |
|||
|
|
|
||
восстановления |
Сокращение эксплуатационного |
|||
и некаталитического |
||||
|
персонала |
|
||
восстановления |
|
|
||
Хорошая технологичность в управлении |
||||
оксидов азота |
||||
|
оборудованием, уменьшение числа |
|||
|
вспомогательного оборудования |
|||
|
Расходы на строительство |
|
Улавливание тонких |
|
|
|
|
|
|
|
|
|
Простота и компактность |
|
|
|
твердых частиц |
|
|
|
|
|
|
|
|
|
|
|
|
|
|
|
|
|
|
|
|
керамическим фильтром |
|
|
|
Уменьшение габаритов котла, |
|
|
|
|
|
снижение высокотемпературной |
|
|
|
|
|
|
|||
|
|
|
|
коррозии, упрощение системы |
|
|
|
|
|
|
|||
|
|
|
|
вывода золы |
|
|
|
|
|
|
|
|
|
5 ) > ) * @ ( 0 8 * / . (0 / 32 4<;
Для преодоления этих трудностей и реализа- |
кипящим слоем. Наполнителем псевдоожиженно- |
ции высоких потенциальных возможностей техно- |
го слоя является известняк, который также служит |
логии ПГУ с КСД, подтвержденных испытаниями |
для обессеривания дымовых газов. Псевдоожиже- |
фазы 1, было рассмотрено использование в ПГУ |
ние осуществляется воздухом, подаваемым через |
технологии сжигания угля в циркулирующем ки- |
сопла, расположенные под нижней частью топки, |
пящем слое под давлением (ЦКСД). Блок был до- |
который служит также окислителем топлива при |
оборудован циклоном и системой циркуляции и |
сжигании. При реконструкции котла не измени- |
возврата золы в топку и проведена фаза 2 демонст- |
лись линейная скорость газов в зоне воспламене- |
рационных испытаний для подтверждения работо- |
ния топлива (0,9 м/с) и технические решения пода- |
способности такой измененной ПГУ (в дальней- |
чи топлива и турбинной системы. Были передела- |
øåì ÏÃÓ ñ ÖÊÑÄ). |
ны только системы очистки дымовых газов от час- |
Демонстрационные испытания фазы 1 прово- |
тиц и удаления золы. |
дились с сентября 1994 по декабрь 1997 г. После |
Íà ðèñ. 7 сравниваются технологические схе- |
их окончания котел был реконструирован для со- |
мы до и после реконструкции. До реконструкции |
здания контура возврата золы. Демонстрационные |
95% золы, выходящей из кипящего слоя, размер |
испытания фазы 2 заняли 1,5 года – с августа 1998 |
частиц которой не более 250 мкм, улавливалось |
по декабрь 1999 г. Продолжительность эксплуата- |
семью первичными циклонами и выводилось из |
ции в период фазы 1 составила 10 981, фазы |
системы. Зола меньших размеров, прошедшая |
2 – 5156 ч. Общее время эксплуатации 16 137 ч, в |
циклоны, улавливалась керамическим трубчатым |
том числе 1508 ч непрерывной работы в фазе 2. |
фильтром и выводилась отдельно от улавливаемой |
Испытания дали ценную информацию о техниче- |
циклонами золы. |
ских характеристиках и надежности энергоблока. |
При реконструкции были сняты все первичные |
Система комбинированного с циркуляцией золы |
циклоны и установлены два циклона циркуляции |
блока типа PFBC. Котел демонстрационного бло- |
золы. Уловленная в них крупная зола возвраща- |
ка ПГУ с КСД в “Вакамацу” оборудован топкой с |
лась через вертикальную трубу в нижнюю часть |
|
|
2003, ¹ 10 |
65 |

Ò à á ë è ö à 5
H :, ( ) + 8 @ 0 4 M*
|
|
Номинальная |
Давление в |
|
|
|
|
Энергетическое |
главном |
Температура |
Дата введения |
||
Энергоблок |
выходная |
|||||
предприятие |
паропроводе, |
ïàðà, °Ñ |
в эксплуатацию |
|||
|
мощность, МВт |
|||||
|
|
ÌÏà |
|
|
||
|
|
|
|
|
||
|
|
|
|
|
|
|
Рэйхоку ¹ 1 |
Kyusyu Electric Power Co |
700 |
24,1 |
566/566 |
Èþëü 1995 |
|
Хараномати ¹ 1 |
Tohoku Electric Power Co |
1000 |
24,5 |
566/593 |
Èþëü 1997 |
|
Мацуура ¹ 2 |
EPDC |
1000 |
24,1 |
593/593 |
Èþëü 1997 |
|
Нанао-Оота ¹ 2 |
Hokuriku Electric Power Co |
740 |
24,1 |
593/593 |
Èþëü 1998 |
|
Хараномати ¹ 2 |
Tohoku Electric Power Co |
1000 |
24,5 |
600/600 |
Èþëü 1998 |
|
Мисуми ¹ 1 |
Tyugoku Electric Power Co |
1000 |
24,5 |
600/600 |
Èþëü 1998 |
|
Бухта Татибана |
Kyusyu Electric Power Co |
700 |
24,1 |
566/593 |
Èþëü 2000 |
|
Бухта Татибана ¹ 1 |
EPDC |
1050 |
25 |
600/610 |
Èþëü 2000 |
|
Цуруга ¹ 2 |
Hokuriku Electric Power Co |
700 |
24,1 |
593/593 |
Октябрь 2000 |
|
Рэйхоку ¹ 2 |
Kyusyu Electric Power Co |
700 |
24,1 |
593/593 |
Èþëü 2001 |
|
Бухта Татибана ¹ 2 |
EPDC |
1050 |
25 |
600/610 |
Èþëü 2001 |
|
|
|
|
|
|
|
кипящего слоя. Таким образом осуществлялась циркуляция золы между топкой и циклонами, пока размер ее частиц не уменьшался до такой степени, при которой они уже не сепарируются в циклонах. Доля циркулирующей золы определяется эффективностью золоулавливания в циклонах, которая составляет по расчету 90%. При такой эффективности отделяются частицы, размеры которых превышают 10 мкм, и материал слоя (зола, прореагировавший и избыточный известняк) в количестве,
â10 раз превышающем количество образующейся
âтопке золы, циркулирует между котлом и циклонами. В отличие от исходного варианта, в котором золоулавливание происходило в две ступени – в первичных циклонах и керамическом трубчатом фильтре, применение циркулирующего кипящего слоя упростило процесс, так как осталась одна ступень золоулавливания – керамический трубча- тый фильтр.
Подача топлива в котел осуществлялась мокрым способом: в виде пастообразной смеси воды, измельченного до 6 мм частиц угля и известняка. Содержание твердых частиц в пасте принималось равным 70 – 75%. Температура горения была постоянной независимо от нагрузки и составляла около 860°С, а давление воздуха в слое при номинальной нагрузке – примерно 1 МПа. Под высоким парциальным давлением кислорода достигалась высокая полнота сгорания угля. В составе ПГУ использовали ту же паровую турбину, что и при демонстрационных испытаниях при температурах и давлении пара, соответственно 593°С/593°С и 10 МПа, проводившихся в обоснование проектирования блока с суперкритическими параметрами пара.
Преимущества циркуляции золы и результаты испытаний. Одной из главных проблем в традиционной ПГУ с КСД является необходимость постоянно подавать в топку крупнозернистый известняк
для обеспечения уровня кипящего слоя, так как мелкие частицы известняка быстро выносятся из топки. Вследствие этого при сжигании малосернистого угля приходится подавать в топку больше известняка, чем требуется для обессеривания дымовых газов, а при угле с высоким содержанием серы – еще больше из-за низкой обессеривающей способности крупнозернистого известняка. EPDC решила использовать циркуляцию золы для того, чтобы продлить продолжительность нахождения материала слоя в газовом тракте котлоагрегата с учетом истирания частиц известняка.
Внедрение циркуляции истирающейся золы в тракте котла, продление времени нахождения золы в системе и уменьшение диаметра ее частиц, как предполагалось, создали следующие преимущества:
сократилось количество известняка, который необходимо было подавать для образования кипящего слоя требуемой высоты и, следовательно, количество образующейся золы. При сравнительных испытаниях угля одной марки и с одним размером частиц расход известняка уменьшился на 40, а количество полученной золы на 17%;
уменьшились размеры частиц материала кипящего слоя, что привело к повышению коэффициента теплопередачи примерно на 12% и улучшило эффективность обессеривания с 88 до 99% при сокращении количества подаваемого известняка;
возможность применения известняка с небольшими размерами частиц (несколько десятков микрометров) расширила ассортимент пригодного для использования известняка (по маркам и диаметрам частиц);
стало возможным эксплуатировать котел на малосернистом угле при меньшем отношении Ca/S. При работе на угле с высоким содержанием серы уменьшение размера частиц известняка повысило эффективность связывания серы и способствовало максимальному сбережению известняка. В целом
66 |
2003, ¹ 10 |

Ò à á ë è ö à 6
) + 8 @ 0 4 NOPQ> ) @ 0 +* 0 * *
Параметр |
Бухта Татибана ¹ 1, 2 |
Мацуура ¹ 2 |
Мацуура ¹ 1* |
|
|
|
|
Номинальная мощность, МВт |
700/1050 |
1000 |
1000 |
Давление пара, МПа |
25,0 |
24,1 |
24,1 |
Температура пара, °С |
600/610 |
593/593 |
538/566 |
Снижение удельного расхода тепла, % |
+4 |
+3 |
Áàçà |
Год начала эксплуатации |
2000 |
1997 |
1990 |
|
|
|
|
* Сверхкритические параметры пара. |
|
|
|
испытания подтвердили, что ПГУ с ЦКСД благодаря возможности тонкого регулирования размера находящихся в тракте котла частиц допускает соответствующую свойствам топлива эксплуатацию, с которой не справляется традиционная ПГУ с КСД.
Недостатком традиционной технологии является также пониженная полнота сгорания, особенно при неполной нагрузке, вызванная улавливанием в циклонах золы вместе с несгоревшим топливом с последующим их выводом из системы.
Вывод золы в ПГУ с ЦКСД осуществляется только через керамический трубчатый фильтр, а собранная вместе с золой сажа несгоревшего топлива независимо от нагрузок горит в нем. Выделяющееся при этом тепло используется в цикле ПГУ, а КПД горения повышается до 99,5%. Это на 0,5% выше, чем в традиционной ПГУ с КСД.
Выгоды применения ПГУ с ЦКСД. Основные преимущества ПГУ с ЦКСД заключаются в том, что она обеспечивает высокую экологическую безопасность при работе на широком ассортименте углей и требует меньших производственных затрат, чем традиционная ПГУ с КСД. На ðèñ. 8 показаны экологические и производственно-эконо-
Ò à á ë è ö à 7
мические преимущества ПГУ с ЦКСД. Путем со- четания связывания оксидов серы в слое, эффективность которого резко возросла после уменьшения размеров частиц известняка, одновременного использования некаталитического восстановления оксидов азота в тракте горячих газов и установки для их селективного каталитического восстановления и полного улавливания керамиче- ским фильтром твердых частиц при высокой температуре в ПГУ с ЦКСД достигнуты хорошие показатели чистоты уходящих дымовых газов даже
при работе |
на серных |
(S = 1 2%) è |
зольных |
(çîëû = 14%) |
углях: |
SOx < 10 ìëí – 1, |
NOx < |
10 ìëí – 1, частицы меньше 1 мг/м3 в нормальных условиях.
Обеспечение высокой экологической безопасности при различных свойствах топлива позволяет использовать недорогие низкосортные угли, нефтяной кокс и др. Недорогое топливо, как правило, имеет высокую зольность и высокое содержание серы. В ПГУ с ЦКСД благодаря большой длительности пребывания частиц в кипящем слое и уменьшению размеров частиц известняка он используется более эффективно. Расход известняка и
( . ( * + : / ( ( ( . * +
Деталь |
Бухта Татибана ¹ 1, 2 |
Мацуура ¹ 2 |
Мацуура ¹ 1 |
|
|
|
|
|
|
Конечный пароперегреватель |
Супер 304H (18Cr9Ni3CuNbN); |
Супер 304H (18Cr9Ni3CuNbN); |
SA213-TP321H (18Cr10NiTi); |
|
|
27,7 MÏa, 642°C |
26,7 MÏa, 631°C |
27,1 MÏa, 573°C |
|
Выходной коллектор конечно- |
SA 335P91 (9Cr1MoNbV); |
SA 335P91 (9Cr1MoNbV); |
HCM9M (9Cr2Mo); 27,1 MÏa, |
|
го пароперегревателя |
27,7 MÏa, 613°C |
26,7 MÏa, 606°C |
543°C |
|
Трубы главного паропровода |
SA 335P91 (9Cr1MoNbV); |
SA 335P91 (9Cr1MoNbV); |
HCM9M (9Cr2Mo); 25,4 MÏa, |
|
26,3 MÏa, 605°C |
25,4 MÏa, 598°C |
543°C |
||
|
||||
|
|
|
|
|
Перепускные трубы турбины |
SA 335P91 (9Cr1MoNbV); |
SA 335P91 (9Cr1MoNbV); |
– |
|
высокого давления |
26,3 MÏa, 605°C |
25,4 MÏa, 598°C |
||
|
||||
|
|
|
|
|
Вторичный промперегрева- |
Tempaloy A-1 (18Cr10NiTiNb); |
Tempaloy A-1(18Cr10NiTiNb); |
SA213-TP321H; 5,3 MÏa, |
|
òåëü |
5,7 MÏa, 674°C |
5,5 MÏa, 654°C |
607°Ñ |
|
Трубы выходного коллектора |
SA 335P91 (9Cr1MoNbV); |
SA387 Gr.91 (9Cr1MoNbV); |
SA387 Gr.22 (2,25Cr1Mo); |
|
вторичного промперегревате- |
||||
5,7 MÏa, 626°Ñ |
5,5 MÏa, 604°Ñ |
5,3 MÏa, 569°Ñ |
||
ëÿ |
||||
|
|
|
||
|
|
|
|
|
Трубы паропровода с высоко- |
SA 335P91 (9Cr1MoNbV); |
SA387 Gr.91 (9Cr1MoNbV); |
SA387 Gr.22 (2,25Cr1Mo); |
|
температурным перегретым |
||||
5,4 MÏa, 613°Ñ |
5,2 MÏa, 596°Ñ |
5,0 MÏa, 569°Ñ |
||
паром |
||||
|
|
|
||
|
|
|
|
|
Перепускные трубы турбины |
SA387 Gr.91 (9Cr1MoNbV); |
SA387 Gr.91 (9Cr1MoNbV); |
– |
|
высокого давления |
5,4 MÏa, 613°Ñ |
5,2 MÏa, 596°Ñ |
||
|
||||
|
|
|
|
|
|
|
|
|
2003, ¹ 10 67

Ò à á ë è ö à |
8 |
|
|
|
|
|
|
( + ) ( . |
|
|
|
|
|||
|
|
|
|
|
|||
Деталь |
Бухта Татибана ¹ 2 |
Бухта Татибана ¹ 1 |
Мацуура ¹ 2 |
Мацуура ¹ 1 |
|||
|
|
|
|
|
|
||
Ротор |
|
Новая улучшенная кова- |
Улучшенная кованая |
Кованая сталь12Cr |
Кованая сталь CrMoV |
||
|
ная сталь 12Cr |
сталь 12Cr |
|||||
|
|
|
|
||||
|
|
|
|
|
|||
Рабочие лопатки |
Сплав NiCoCr1 (ступени |
Новая сталь12Cr (1-я |
Сплав NiCoCr1 (ступени |
Сталь NiCrMoWV2 |
|||
|
|
1 – 3); сталь |
ступень); улучшенная |
1 – 4); сталь NCrMoWV2 |
(ступени 1 – 5); сталь |
||
|
|
NiCrMoWV2 (ступени |
сталь12Cr (2-я ступень); |
(ступени 5 – 11) |
NiCrMo (ступени 6 – 10) |
||
|
|
4 – 11) |
сталь 12CrMoVNbN |
|
|
||
|
|
|
(ступени 3 – 8) |
|
|
||
|
|
|
|
|
|||
Силовые лопатки |
Кованая сталь 9Cr |
Сталь 12CrMoVNbN |
Кованая сталь 9Cr |
Кованая сталь12Cr |
|||
|
|
(ступени 1 – 2); кованая |
(ступени 1 – 3); сталь |
(ступени 1 – 2); кованая |
(ступени 1 – 10) |
||
|
|
сталь 12Cr (ступени |
12Cr (ступени 4 – 8) |
сталь12Cr (ступени |
|
||
|
|
3 – 11) |
|
|
3 – 11) |
|
|
|
|
|
|
|
|||
Сопла и диафрагмы |
Литая сталь 12Cr |
Кованая сталь 12Cr |
Литая сталь 12Cr |
Литая сталь 2 1/4CrMo |
|||
|
|
|
|
|
|||
Внутренние корпуса |
Литая сталь 12Cr |
Литая сталь 12Cr |
Литая сталь 12Cr |
Литая сталь 1 1/4CrMo |
|||
|
|
|
|
|
|||
Стопорные клапаны |
Кованая сталь 9Cr |
Кованая сталь 9Cr |
Кованая сталь 9Cr |
Кованая сталь |
|||
|
|
|
|
|
|
2 1/4CrMo |
|
|
|
|
|
|
|||
Регулирующие клапаны |
Кованая сталь 9Cr |
Кованая сталь 9Cr |
Кованая сталь 9Cr |
Кованая сталь |
|||
|
|
|
|
|
|
2 1/4CrMo |
|
|
|
|
|
|
|||
Пароподводящие трубы |
Стальная труба 9Cr |
Стальная труба 9Cr |
Стальная труба 9Cr |
Стальная труба |
|||
|
|
|
|
|
|
2 1/4CrMo |
|
|
|
|
|
|
|
||
1 37Ni20Co18Cr; 2 11Cr0,5Ni0,4Mo1,7W0,2V. |
|
|
|
|
|||
количество образующихся отходов уменьшается, |
Высокая экологичность и экономичность ПГУ |
||||||
что экономически выгодно, так как упрощает сис- |
с ЦКСД делают их привлекательными для созда- |
||||||
тему вывода золы и уменьшает затраты на ее пере- |
ния тепловых электростанций в урбанизирован- |
||||||
работку. Хорошая |
технологичность и меньшее |
ных районах. Например, они могут служить само- |
|||||
стоятельным источником электроэнергии, удов- |
|||||||
число операций позволяют сократить штат персо- |
|||||||
летворяющим нужды жителей крупных и средних |
|||||||
нала, что также экономит эксплуатационные рас- |
|||||||
городов, или теплоэлектроцентралями в индустри- |
|||||||
ходы. Повышение коэффициентов теплопередачи |
|||||||
ализированных районах с учетом возможности ис- |
|||||||
в циркулирующем кипящем слое позволяет умень- |
|||||||
пользования широкого ассортимента топлива, в |
|||||||
шить габариты котла и сократить капиталовложе- |
том числе и промышленных отходов, таких как не- |
||||||
ния в оборудование. |
|
|
фтяной кокс и др. |
|
|||
Ò à á ë è ö à |
9 |
|
|
|
|
|
|
( + ) . . |
|
|
|
|
|||
|
|
|
|
|
|||
Деталь |
Бухта Татибана ¹ 2 |
Бухта Татибана ¹ 1 |
Мацуура ¹ 2 |
Мацуура ¹ 1 |
|||
|
|
|
|
|
|
||
Ротор |
|
Новая улучшенная кова- |
Улучшенная кованая |
Кованая сталь 12Cr |
Кованая сталь CrMoV |
||
|
|
ная сталь 12Cr |
сталь 12Cr |
|
|
|
|
|
|
|
|
|
|||
Рабочие лопатки |
Сплав NiCoCr1 |
Новая сталь 12Cr (1-я |
Сплав NiCoCr1 |
Сплав NiCoCr1 |
|||
|
|
(ступени 1 – 4); сталь |
ступень); улучшенная |
(ступени 1 – 4); |
(ступени 1 – 2); |
||
|
|
NiCrMoWV2 |
сталь 12Cr (2-я ступень); |
сталь NiCrMoWV2 |
сталь NiCrMoWV2 |
||
|
|
(ступени 5 – 7) |
сталь 12CrMoVNbN |
(ступени 5 – 7) |
(ступени 3 – 7) |
||
|
|
|
(ступени 3 – 7) |
|
|
||
Сопловые лопатки |
Кованая сталь 9Cr |
Сталь 12CrMoVNbN |
Кованая сталь 9Cr |
Кованая сталь 12Cr |
|||
|
|
(ступени 1 – 2); |
(ступени 1 – 3); |
(ступени 1 – 2); |
(ступени 1 – 7) |
||
|
|
кованая сталь 12Cr |
сталь 12Cr |
|
кованая сталь 12Cr |
|
|
|
|
(ступени 3 – 7) |
(ступени 4 – 7) |
(ступени 3 – 7) |
|
||
|
|
|
|
|
|||
Внутренние корпуса |
Литая сталь 12Cr |
Первичные турбины – |
Литая сталь 12Cr |
Литая сталь |
|||
|
|
|
литая сталь 12Cr; |
|
2 1/4CrMo |
||
|
|
|
вторичные турбины – |
|
|
||
|
|
|
литая сталь CrMoV |
|
|
||
|
|
|
|
|
|||
Стопорные клапаны |
Кованая сталь 9Cr |
Комбинированные |
Кованая сталь 9Cr |
Литая сталь |
|||
|
|
|
клапаны – новая литая |
|
2 1/4CrMo |
||
|
|
|
сталь 12Cr |
|
|
|
|
Отсечные клапаны |
Òî æå |
Òî æå |
|
Кованая сталь 9Сr |
Кованая сталь |
||
|
|
|
|
|
|
2 1/4CrMo |
|
|
|
|
|
|
|
||
1 37Ni20Co18Cr; 2 11Cr0,5Ni0,4Mo1,7WO2V. |
|
|
|
|
|||
|
|
|
|
|
|
|
|
68 |
|
|
|
|
|
2003, ¹ 10 |