
Ceramic Technology and Processing, King
.pdfFiring 313
Meltdown
The base support has only a little clearance around the electric lead throughways. Deposits can condense in this area, shorting out the base unit, which will arc and destroy the furnace. This equipment is very expensive, and one can lose much time. Do not buy the smallest unit. Get one large enough to provide ample clearances, and keep them clean.
Jamming
Hold-downs are pressed onto the end closure with steel rods that have a ball bearing riding on the top of the closure. Bearing races can be under-designed and will crush. The yoke cannot be rolled back, preventing the apparatus from opening. The bottom end closure also pushes out and can jam against the yoke extension. There is something indecent about beating on an expensive laboratory instrument with a sledgehammer, especially when repeated after every run.
Procedures
There are three basic procedures when running a HIP based on the method of isolating the material from the pressurized gas. Hipping only works if there is a pressure differential between the pressure vessel and the sample. This differential provides the stress that aids in the densification process. Provide isolation in three ways. Encase the sample in a refractory metal (Mo) can, sinter the sample to an impervious condition, and then hip it. Alternatively, encase the sample in a silica glass that fuses to form an impervious barrier.
314 Ceramic Technology and Processing
Canning
This was the first method. Place the sample in a sheet metal container and then weld it closed. The metal is either Mo or Ta, both of which require electron beam welding in an inert atmosphere. Then, place the can in the HIP, where the heating/pressure/time cycle is run. The can collapses as it is pressurized, transferring the stress to the sample. Special shapes such as hollow cones can be hipped against a central form that forms an accurate ID.
Sinter HIP
In this method, the sample is first sintered to an impervious state and then hipped. One usually sinters and hips in the same run, but while being convenient, this is not really necessary. After excluding the internal porosity from the pressure, the pressure hips the sample. This process is the easiest one to use under normal conditions of densifying a part. A prerequisite is that the material will densify to an impervious state.
Glass Encasement
At first, the process was to submerge the sample in a bath of silica glass and then to pressurize it. In a later process, the sample is coated with the glass, heated to melt the glass, and is then pressurized. Since the silica glass has a very low thermal expansion, it cracks upon cooling and spalls off. This process developed by ASEA requires a license even for experimental purposes. This requirement makes it difficult for a lab investigation.
Firing 315
Check List, HIP
•Do not buy a small HIP, buy at least a medium-sized unit.
•Keep the lead throughways clean.
•Consider jamming. Call users who have experience with the equipment.
•Sinter HIP is the most useful process, generally.
•Glass encapsulation is a production process and is not available for experimentation.
•Metal encapsulation is expensive, but is useful in special cases.
REFERENCES
1.J.H. Heasley, Internal Report
2.A.H. Heuer, "Alloy Design in Partially Stabilized Zirconia," in Science and Technology of Ziriconia 1981 Ed. A.H. Heuer and L.W. Hobbs, (Westerville, OH: Amer. Ceram. Soc., 1981), pp.98-115.
3.John I. Fredriksson, Slip Cast Silicon Carbide Shapes. U.S. Patent 2,964,823 (Dec. 20 1960).
4.J.H. Heasley, and A.G. King, Internal Reports
5.Prochazka, Svante, U.S. Patent 4,004,934 (1977).

9
Grinding
1.0 THE GRINDING PROCESS
The scope of this chapter is limited. Grinding is by itself a skilled or semiskilled craft. The intent is not to teach how to grind a ceramic part. In-stead, the intent is to describe the process and offer some insight about how this affects the ceramic.
Ceramics are usually ground with bonded-diamond abrasives. There are two types of bonds in common use, metal and resinoid. Metal is rougher and lasts longer. Resinoid is gentler and wears out faster. Always use resinoid for finish grinding of fine-grained, dense ceramics as there is less surface damage to the part.
Tool Type and Grit Size
There are two types of metal-bonded, diamond-cutting tools. The sintered-powder, metallurgical type with included diamond grit and the surface bonded type with electroplated Ni on sedimented diamond grit. The latter is common in metallographic grinding and polishing. The powdermetal, bonded type is more common in the machine shop and is used for
316
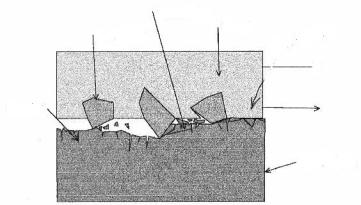
Grinding 317
percision shaping of a part. Resin-bonded and diamond-bonded cutting tools also come in these two forms for similar uses. Abrasive points protrude from the surface of the grinding wheel, as schematically shown in Figure 9.1.
|
Shattering |
|
Abrasive |
Bond |
|
Rubbing |
||
|
Cracks
Workpiece
Figure 9.1: The Grinding Process. Abrasives damage the ceramic surface to an appreciable depth. Rubbing of the wheel on the surface can cause heating.
Grinding is a scratching process, leaving jagged scratch roots and sub surface cracks. In Figure 9.1, not all the abrasive grains stick out from the wheel surface the same distance, so the longest grains do most of the grinding. Try polishing a finely ground surface. One will observe resulting deep scratches on the surface. Grinding also leaves residual stresses in the ceramic surface and a considerable amount of plastic deformation.1
Grit size is a factor when grinding ceramics. Finer grit leaves smaller scratches and lower residual stresses as long as the grinding wheel is free cutting. The down feed has to be less than the distance of the protruding diamond points from the surface. Wheels will dull with use and have to be dressed to free up a fresh cutting surface. Since these are diamond wheels and are expensive, there is a reticence to dressing the wheel and it is often abused when dull. Dull wheel surfaces rub and can raise the interfacial temperature even to the point where the part could fracture. In Figure 9.1, rubbing is shown to the right of the contact area. Pullouts leave the resin bond in contact with the work piece, generating
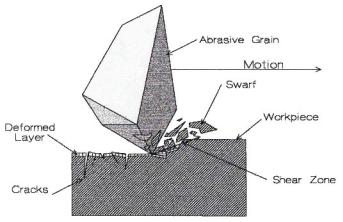
318 Ceramic Technology and Processing
heat but without any cutting. There is proportionally less cutting and proportionally more rubbing with a finer grit wheel. There is then a practical lower limit to the grit size that usually is 220-325 grit.
Another limitation for most shop surface grinders is a minimum down feed of 0.0001inches; this is not too precise especially after adding in all of the machine tool compliance. With a small grit size, the distance the grain protrudes is of the same order as the down feed, jamming the wheel surface against the work piece. The modulus of many ceramics is about 30-60x106 psi while the modulus of phenolic resins is about 1x106 psi. Forces between the cutting point and the ceramic surface can push the point up into the wheel surface either elastically or by deformation of the bond. All of this is why there is a practical lower limit on the grain size that is effective. When one needs a finer surface, switch to lapping or polishing with loose abrasives. The part wheel interface in Figure 9.2 is at a higher magnification.
Figure 9.2: Grinding Damage. An abrasive grain scratches the ceramic surface. Damage includes: gouges, cracks, and surface deformation.
Grinding 319
The above figure shows an abrasive grain scratching the ceramic surface. This leaves damage in the ceramic, including gouges, cracks, and a deformed surface layer. The grain creates a shearing zone in front of the cutting tip. Fracture occurs in this shearing zone, removing material.
Surface Damage
The grinding process damages the ceramic surface. Scratches, because of their shape, act as stress risers. Sub surface cracks and residual stresses weaken the ceramic. Two cases are illustrative, lowering the modulus of rupture and lowering the impact strength.
Modulus of Rupture
This example is taken from work on high purity, hot pressed alumina, fully dense, and with an average grain size of three μm.2 Chemically polishing alumina with a borax fusion allows removal of the damaged layers. Figure 9.3 illustrates the solution rate of strength vs. depth of damage.
Strength increases as material dissolves off the damaged surface, from 72,000 psi to 95,000 psi over a depth of five μm. This depth is also about the size of the largest grains in the microstructure. This leads to the unproven but likely conclusion that the damage is blocked at the grain boundaries.
Impact Strength3
Using the same type of ceramic as in the preceding section and varying the hot pressing temperature results in a range of grain sizes. All of the specimens were fully dense. With the discs supported by an annular knife edge around the edge, a half-inch steel ball bearing was dropped onto the center of each disc at a variety of heights. Figure 9.4 illustrates the results.
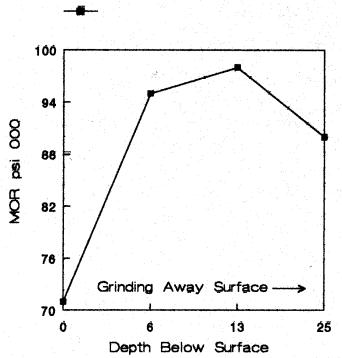
320 Ceramic Technology and Processing
Figure 9.3: Strength with Distance from the Surface. Strength increases as the surface damage is dissolved away.
There are three important observations in Figure 9.4. Impact strength decreases markedly as one reduces the hot pressing temperature, coarser grit grinding lowers the impact strength, and annealing at 1300 °C removes the grinding damage. (By way of explanation, the tools were not available in the lab to measure the grain submicron size, so temperature was the criterion by default.) Annealing is not a common practice for finegrained, dense, ceramic parts. Maybe it should be tried more often, unless this results in bloating.

Grinding 321
Figure 9.4: Impact Strength/ Microstructure. Impact strength is substantially reduced with lower hot pressing temperatures and larger grit grinding wheels. Damage can be removed by annealing.
2.0 GRINDING SHOPS
There are three-setup, grinding choices: another department in the institution, a setup in the ceramic lab, and outside sources. It is well worth the time to consider these alternatives.
322 Ceramic Technology and Processing
Another Department
Machine shops in the institution are usually in another department, which have their own priorities. While also doing work for production departments, lab work is at the bottom of the list, and sometimes for all practical purposes, not even on the list. The process for making parts in the lab is sequential: processing powders, forming, sintering, and shaping. Each of these steps may require machine shop services. Consider the worst scenario that one may encounter. For example, a filter may need to be adapted for powder processing, a die may be needed for pressing the part, an end seal may be required for atmosphere sintering, and test specimens have to be ground for measurements. With a four-week hiatus between each step due to machine shop scheduling, it will take too long to get the experiment completed. The author retracts an earlier statement; this is not the worst scenario as a four-week queue is quite timely for such jobs.
Availability for machine work varies depending on the location in question. Generally, place the choice of an inside department on the bottom of one's list.
Setting Up Grinding in the Ceramic Department
When under control of the lab, priorities are set internally, which can be a great relief. However, there is the problem of getting the necessary skills, and this can be a sizable obstacle. When the work in question is repetitive, such as grinding test bars, the level of skill is manageable. A comprehensive grinding shop requires a lot of expensive equipment and knowhow. With operations going broke, both equipment and skilled people are sometimes available. This will cut the lead time, cost, and acquisition of skills. There is also the question of facility utilization. It will take much work to fill the capacity of a comprehensive shop. When these requirements are well satisfied, an internal machine shop could well be the preferred choice.