
Ceramic Technology and Processing, King
.pdf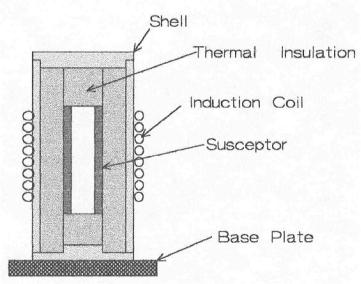
Firing 263
connected to a power supply establishing a current in the susceptor and causing it to heat. Optical pyrometry is common for measuring the temperature. One should be careful as voltage and amperage can be deadly.
Figure 8.13: Induction Furnace. Lab-sized, induction furnaces are commercially available or can be made in the lab.
Matching the furnace size, coil, and furnace configuration to the power supply takes some experience. Modern induction power supplies are solid state and are easier to match with the coil. Power supplies operate at different frequencies and unless one has the experience, call an expert. Overdesign of the power supply will impart flexibility that gives one a wider choice on furnace design and size. Suppliers of the power supply can help with these choices. Many lab induction furnaces are home made, probably because they are so simple. There are many other uses for induction furnaces, mostly in industry. This discussion is abbreviated to the most common experiences in the lab.
264 Ceramic Technology and Processing
Vacuum Furnaces
Some materials have to be fired in a vacuum or in a protective atmosphere. Equipment for this is commercially available and is complex, versatile, and expensive. However, it is better buying this equipment from a supplier because of the extensive engineering and experience involved. Cosider the following summary.
Size/Configuration. Hot zones are one to three cubic feet. Shells are stainless steel and are cylindrical with hemispherical end bells. The door swings out, giving front access. The door can be vertical or horizontal, but it is usually horizontal.
Temperature/Cooling. Ni/Cr 1000 °C
Mo 1650 °C
C 2200-2600 °C
W 2500 °C
Insulation/Shell Cooling. Graphite fiber, Mo multiple heat reflectors. The shell is cooled with a water jacket, which can be recirculating. Forced gas cooling is available through a heat exchanger.
Vacuum/Pressure. Mechanical fore pumps, diffusion, turbo, or cryogenic high vacuum pumps/Pressure to 2500 psi
Atmosphere. Vacuum to 10-6Torr (.013Pa), H2, N2, Ar, and air with Ni/Cr.
Burnout. Binders and wax can be burned out with special equipment.
Controls. Modern computer controls, interlocks, and alarms
Research. Obtain a customer list and personally check out the performance of identical or very similar equipment.
Firing 265
Check List, Other furnace types
•Rotary: temperature, size, tube material, clean out, contamination
•Induction: Get expert advice on size, materials, power supply, and safety.
•Vacuum: size, temperature, materials, heating elements, atmosphere.
3.0SETTING PRACTICES
Formed ware is set on the hearth in many ways, depending on composition, sag resistance, shrinkage, size, and shape. The best case is as follows: the composition of the hearth and ware is identical, the part does not sag at the soak temperature, the part has no or very little firing shrinkage, and the part is small with a blocklike shape. Such hypothetical scenarios do not reflect real life, however. This section describes ways to set the ware on the hearth of the kiln. Often, conditions are less than ideal. For example, the hearth reacts with the ware, both the ware and hearth sag, the ware shrinks up to a fraction of its green size, or the ware is huge, fragile and has a thin cross section. Firing in air is often different from firing in an atmosphere and will be discussed separately.
Firing in Air
Setting practices follow the same principles for a variety of kiln types, except that the size and configuration can change.
Composition
Isolate the body when it reacts chemically with the hearth. These reactions are often predictable, from the free energies of formation. When
266 Ceramic Technology and Processing
venturing into new materials, it is worth the time to look up this data. A test run with a small sample and setter is a good idea. A bed of chemically compatible grain spread on the hearth is a common way to isolate the part. Cover this bed with fresh grain for each run and level it. Use relatively coarse grain as it will not sinter hard or shrink. Wiggle the parts into the bed to seat them. When there is an ID, do not get any grain into the center as it will prevent shrinkage and will warp the part. After the thickness of the bed builds up, it is scrapped off and the process is repeated. One can also protect the hearth with disposable plates partially compatible with the chemistry. The area of direct contact between the plate and hearth is small, limiting the extent of interaction. One can also set parts directly on compatible plates. This is common when firing granular materials where a box or sagger is lined with plates, isolating the ceramic from the hearth.
Test runs will help to choose compatible materials. Alumina and zirconia are compatible at 1500 °C but not at 1700 °C. Some newer advanced ceramic powders sinter at lower temperatures, making setting composition simpler. Another related way is to bury the parts in a bed of grain. BaTiO3 capacitors are fired this way. The composition of the ceramic relates directly to its properties: thermal conductivity, thermal expansion, elastic modulus, and strength (if we include microstructure). The worst case is a ceramic with low thermal conductivity, high thermal expansion, a high modulus, and low strength. This material is hard to set properly because it is highly susceptible to firing conditions. High internal stresses and thermal gradients induced by uneven heating can cause it to fail by distortion or fracture. For example, a fine grained ZrO2 part will be a lot more difficult than an identical shape made from coarse grained MgO. Setting to even out temperature gradients helps to alleviate this problem.
Sag
When the composition contains a glassy phase, it is more likely to sag. Also, fine-grained materials are more likely to sag and distort than coarse materials. The glass composition in the body will determine its softening point and viscosity. Less glass, a higher softening point, and higher viscosity will reduce sag. If there is this option, the composition can
Firing 267
be adjusted. If not, one can support the part; in a grain bed, set in a V- shaped block, stacked with a little grain between layers, and confined physically by refractories often coated with a wash. A wash is a slurry painted onto the refractory surface that is then let to dry. The composition of the wash should be compatible with the ceramics being fired. Washes are not too successful as they bleed through, but one can still use them. If this is admissible, one may reduce the temperature. While not a usual laboratory procedure, the part can be set on a specially formed setter for firing. Setters are common in industry but not so much in the lab because the parts vary so much in size, composition, and shape. Another instance of sag is where the part is formed as a fluid, such as with injection or wax molding. When the part is reheated to fire it, the polymer or wax remelts and the part can slump. A common remedy for this is to pack the part in a powdered absorbent and sagger for debindering. As the binder melts, it is absorbed in the pack, leaving the green ceramic that can then be removed and fired. If the polymer is crosslinked, one can fire the part directly as it will not remelt. Binder burnout has to be very slow or the part will burst from internal gas pressure. Guidance can be provided by a thermal gravimetric analysis (TGA) on the binder. Over the region where the binder is losing weight rapidly, fire the part on a slow ramp.
Shrinkage
Consolidation of the body can result in shrinkage. Shrinkage is a problem because the part is moving, introducing distortions and stresses. Coarse-grained materials are usually packed to where the coarse part of the composition is in grain-to-grain contact, and will not shrink appreciably. Shrinkage and bonding occur internally in the fine-grained, bonding portion of the body. One can stack these low-shrinkage materials in the setting. Stacking along the edges helps inhibit cracking by keeping the material in compression. Sometimes, it is laid flat, which limits the height of the stack. It is necessary to provide gas circulation throughout the stack. Groups of parts are set crosswise to provide open spaces in the setting. Ceramics that have appreciable shrinkage are more difficult to set on the hearth. Finegrained ceramics commonly have up to 20% linear shrinkage. One usually

268 Ceramic Technology and Processing
uses short stacks of three. The part is moving on the hearth as it shrinks, resulting in friction on the base. This friction introduces a counter force in the opposite direction from that due to sintering. As a result, the base of the fired part is wider than the top. One often uses shrinkage plates to address this problem. Figure 8.14 illustrates a typical use of a shrinkage plate.
Figure 8.14: Shrinkage Plate Setting. Use of a shrinkage plate relieves basal shrinkage stresses on the part being fired.
Since the part and plate shrink together, the drag is at the hearthplate interface and not at the part-plate interface. Shrinkage plates are expendable, with a new one used every run. They are usually the same composition as the part. The cost of a plate is not a big factor in the lab, but it can be prohibitive in production. Even then, there is no other reasonable choice. Figure 8.15 illustrates how a part distorts without a shrinkage plate.

Firing 269
Figure 8.15: Sintering without Shrinkage Plate. When a shrinkage plate is not used the part can distort and crack.
There are two opposing forces on the interface: the sintering force pulling toward the center and the drag force, due to friction, pulling in the opposite direction. Sintering is inhibited on the base of the part, so it shrinks less and has a lower density. It can also crack when the drag exceeds the strength of the material. This sort of problem is exacerbated when the part sticks to the hearth, often due to a glassy phase weeping out onto the hearth. In the last two figures, it was assumed that the green part had a uniform density throughout. This is a false assumption when the part is die pressed. In this case, the pressure in the center is less, the green density is less, shrinkage is greater, and the part hourglasses. This effect is shown in Figure 8.16.
Hourglassing is always present for die pressed parts that have appreciable firing shrinkage, unless they are plates. Otherwise, one can diamond grind the fired piece or change the forming method.

270 Ceramic Technology and Processing
Figure 8.16: Hourglass Distortion. Pressure gradients, during pressing, increase the firing shrinkage in the middle of the part causing hourglassing.
Size
Large pieces are more difficult because of their mass and internal temperature gradients during firing. Coarse materials are much less limited, as they have little shrinkage. Fine-grained materials that shrink are size limited, and anything larger than about a 4-inch cube or an 8-inch-diameter plate is tough to make. Best chances are to set the piece on a shrinkage plate and fire slowly. A monthlong firing is not uncommon. Set the part so that it heats evenly. Make sure that the heat can surround the piece, and it is common to enclose the part in a covered sagger, sometimes buried with coarse grain. The idea is to minimize thermal gradients in the part. When a gradient occurs, the outside will start to shrink sooner than the interior, setting up stresses. A big piece where thermal diffusion takes longer gives

Firing 271
the most problems. Most cracks occur during forming, drying, or heating, often during binder burnout. Incipient cracks will open during firing despite the setting and ramp schedule. Looking at the crack edges with a microscope will provide information about when the crack occurred. When the edges are rounded, the crack was present before the soak. If the edges are sharp, the crack occurred during cooling.
Shape
When the shape is complex and fragile, the setting will support the piece during firing, which is often done in a bed of grain. Keep in mind that as the part shrinks, the grain pack will not. Grain packs do not flow well. Spherical ceramic beads can be used as a pack as they will flow a little better than angular grain. Additionally, one can use sintered, screened, coarse, and spray-dried spheres as a pack or setting sand. One can also use a small, 2-mm-diameter, spherical, grinding media. When grain is trapped in an interstice, part shrinkage will be restrained and the part will distort or break. It is essential for the part to be free to shrink. It is difficult when the shape has both thin and thick cross sections, such as a turbine rotor. Figure 8.17 illustrates an idealized, tough shape.
Figure 8.17: Thin/Thick Wall Part. It is difficult to sinter a part with radically different cross sections due to warpage and cracking.

272 Ceramic Technology and Processing
Thin sections of the part will start to sinter sooner than thick sections, resulting in distortions and cracking. The thick section will shrink after the thin portion is all done, putting stress on the shear zone..
Another tough shape is a thin flat plate, shown as it sinters in Figure 8.18.
Figure 8.18: Sintering Thin Flat Plate. A thin plate tends to warp during sintering due to uneven heating.
A ceramist was trying to produce a flat capacitor part and had tight specifications on flatness. The plate would come out of the kiln sometimes curved up, and sometimes curved down. A perplexing problem? After trying a number of options, it was decided to observe the part during the firing process as in Figure 8.18. First the part lays flat as in stage one. Then it curved up as in stage two. It flattened out as in stage three. Finally, it curved down for the final shape as in stage four. The best solutions are often the simple ones; the part was taken out of the kiln at stage three. The