
02 BOPs / Woods D.R 2008 rules-of-thumb-in-Engineering-practice (epdf.tips)
.pdf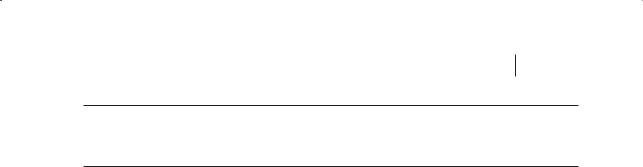
6.2 General Guideline 211
Table 6.12 How phase affects type of reactor.
Type of reactor |
Homogeneous |
Heterogeneous |
Comment |
||
|
G |
L |
S |
GL LL no-catalyst |
catalytic |
|
|
|
|
GS LS |
GS LS GLS |
6.4Burner
6.5PFTR pipe/ empty tube for fluids (tube loop, ejector into tube)
** |
|
Fast; For homogeneous endo |
|
|
or exothermic, gas phase reac- |
|
|
tions; short reaction times, |
|
|
high temperatures |
*** ** |
** ** |
bio Fast; good for consecutive re- |
|
|
actions. High temperature, |
|
|
large surface area, well-defined |
|
|
residence time. May operate |
|
|
under a vacuum. |
6.6 PFTR: static |
* |
* |
* |
* |
* |
|
|
Large heat transfer area; in- |
mixer in tube or |
|
|
|
|
|
|
|
tensive radial mixing with |
as sections in a |
|
|
|
|
|
|
|
negligible backmix; narrow |
tower |
|
|
|
|
|
|
|
RTD; suitable for processes |
|
|
|
|
|
|
|
|
where viscosity increases. |
6.7 PFTR: pipe/ |
|
|
|
|
** |
** |
** |
Very fast; good for consecutive |
empty tube for |
|
|
|
|
|
|
|
reactions. Large transfer area; |
transported or |
|
|
|
|
|
|
|
temperature can be controlled |
slurry; transfer |
|
|
|
|
|
|
|
by injection; little backmix; |
line; moving bed |
|
|
|
|
|
|
|
well-defined residence time. |
in a tube |
|
|
|
|
|
|
|
|
6.8 PFTR empty |
* |
* |
|
|
|
|
|
Fast reactions; good for conse- |
multitube |
|
|
|
|
|
|
|
cutive reactions. Large transfer |
(e static mixers) |
|
|
|
|
|
|
|
area to remove heat from |
|
|
|
|
|
|
|
|
exothermic reactions; use sta- |
|
|
|
|
|
|
|
|
tic mixers for viscous fluids. |
6.9 PFTR: fixed |
* |
|
|
|
*** |
* |
*** |
Fast; good for consecutive re- |
bed catalyst or |
in- |
|
|
|
|
|
|
actions. Simple and easy to |
inerts: adiabatic |
erts |
|
|
|
|
|
|
design.not suitable for reac- |
|
|
|
|
|
|
|
|
tions with high exo or en- |
|
|
|
|
|
|
|
|
dothermicity DTad i 100 hC. or |
|
|
|
|
|
|
|
|
that have temperature sensiti- |
|
|
|
|
|
|
|
|
vity. For fast reaction rates and |
|
|
|
|
|
|
|
|
unstable products, use shallow |
|
|
|
|
|
|
|
|
beds that give very short resi- |
|
|
|
|
|
|
|
|
dence times and some axial |
|
|
|
|
|
|
|
|
mixing. Catalyst may be a |
|
|
|
|
|
|
|
|
gauze. For noncatalytic, mix- |
|
|
|
|
|
|
|
|
ing can be promoted by inerts. |
6.10 PFTR: mul- |
|
|
|
|
** |
|
|
Large transfer area; used pri- |
tibed adiabatic |
|
|
|
|
|
|
|
marily for equilibrium reac- |
with quench or |
|
|
|
|
|
|
|
tions that are temperature |
heat exchange |
|
|
|
|
|
|
|
sensitive. |
|
|
|
|
|
|
|
|
|
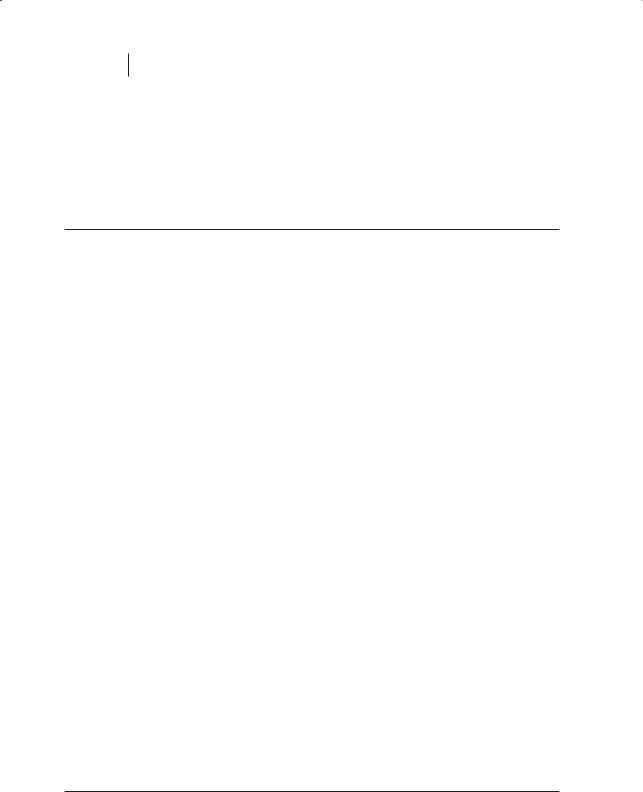
2126 Reactors
6.2.8
Using the Phases to Guide in the Choice of Reactor Configuration
Table 6.12 lists the reactor configurations that have been used for different phase conditions and can be used as a guide to select the reactor configurations that might be appropriate for the target reaction under consideration.
Table 6.12 Continued.
Type of reactor |
Homogeneous |
Heterogeneous |
|
|
Comment |
|||
|
G |
L |
S |
GL |
LL no-catalyst |
catalytic |
|
|
|
|
|
|
|
GS LS |
GS |
LS GLS |
|
|
|
|
|
|
|
|
|
|
6.11 PFTR: fixed |
|
|
|
|
|
*** |
|
Fast; good for consecutive re- |
bed catalytic radial |
|
|
|
|
|
|
|
actions. Use to minimize Dp. |
flow |
|
|
|
|
|
|
|
|
6.12 PFTR: multi- |
|
|
|
|
* |
*** |
** |
Fast; good for consecutive re- |
tube fixed bed |
|
|
|
|
|
|
|
actions. Large transfer area. |
catalyst: non |
|
|
|
|
|
|
|
Can handle exothermics. |
adiabatic |
|
|
|
|
|
|
|
|
6.13 PFTR: bubble |
|
|
|
** |
** |
|
** |
Slow reactions; consecutive |
reactor: jet loop, |
|
|
|
|
|
|
|
reactions; irreversible or rever- |
air lift with central |
|
|
|
|
|
|
|
sible with high equilibrium |
or off-center draft, |
|
|
|
|
|
|
|
constant. Relatively isother- |
external loop, bub- |
|
|
|
|
|
|
|
mal, limited in range of temps |
ble packed |
|
|
|
|
|
|
|
and pressures. High capacity, |
|
|
|
|
|
|
|
|
simple design; high backmix |
|
|
|
|
|
|
|
|
of liquid. Liquid is usually the |
|
|
|
|
|
|
|
|
key component. OK for corro- |
|
|
|
|
|
|
|
|
sive chlorinations, sulfona- |
|
|
|
|
|
|
|
|
tions, phosgenations. |
6.14 PFTR: spray |
|
|
|
** |
* |
|
** |
Fast reaction, high capacity, |
reactor and jet |
|
|
|
|
|
|
|
low Dp; fines OK. |
nozzle reactor: |
|
|
|
|
|
|
|
|
gravity spray, ven- |
|
|
|
|
|
|
|
|
turi jet, plunging |
|
|
|
|
|
|
|
|
jet, circulating |
|
|
|
|
|
|
|
|
nozzle. |
|
|
|
|
|
|
|
|
6.15 PFTR: trays, |
|
|
|
*** |
** |
|
* |
Intermediate reaction rates. |
with and without |
|
|
|
|
|
|
|
High capacity, high conversion |
downcomers |
|
|
|
|
|
|
|
in both gas and liquid phases. |
|
|
|
|
|
|
|
|
Intensive dispersion of gas in |
|
|
|
|
|
|
|
|
liquid. Large number of plates |
gives plug flow. Some flexibility in varying liquid holdup; and exchange heat via coils on plates.

|
|
|
|
|
|
|
|
6.2 |
General Guideline |
213 |
Table 6.12 Continued. |
|
|
|
|
|
|
|
|
|
|
|
|
|
|
|
|
|
|
|
||
|
|
|
|
|
|
|
||||
Type of reactor |
Homogeneous |
Heterogeneous |
|
|
|
Comment |
||||
|
G |
L |
S |
GL |
LL no-catalyst |
catalytic |
|
|
|
|
|
|
|
|
|
GS |
LS |
GS LS |
GLS |
||
|
|
|
|
|
|
|
|
|
|
|
6.16 PFTR: pack- |
|
|
|
** |
* |
|
|
** |
Very fast reactions. essentially |
|
ing, full column, |
|
|
|
|
|
|
|
|
plug flow for both G and L. |
|
shallow, RBC, |
|
|
|
|
|
|
|
|
High capacity, high conversion |
|
trickle filter |
|
|
|
|
|
|
|
|
in both gas and liquid phases. |
|
|
|
|
|
|
|
|
|
|
Difficult to control tempera- |
|
|
|
|
|
|
|
|
|
|
ture, adiabatic. Conversion is |
|
|
|
|
|
|
|
|
|
|
often limited by equilibrium. |
|
|
|
|
|
|
|
|
|
|
Design like an absorber, Sec- |
|
|
|
|
|
|
|
|
|
|
tion 4.8. |
|
6.17 PFTR: |
|
|
|
|
|
|
* |
*** |
Use for very fast reactions, all |
|
trickle bed |
|
|
|
|
|
|
|
|
reaction is in the liquid film |
|
|
|
|
|
|
|
|
|
|
and is mass transfer con- |
|
|
|
|
|
|
|
|
|
|
trolled. |
|
6.18 PFTR: |
|
|
|
|
|
|
* |
|
Use when mass transfer af- |
|
monolithic |
|
|
|
|
|
|
|
|
fects selectivity or reactivity. |
|
|
|
|
|
|
|
|
|
|
Perhaps not for highly |
|
|
|
|
|
|
|
|
|
|
exothermic reactions because |
|
|
|
|
|
|
|
|
|
|
limited in radial heat transfer |
|
|
|
|
|
|
|
|
|
|
unless cross flow is used. |
|
6.19 PFTR: thin |
|
* |
|
* |
|
|
|
* |
Mass transfer controlled, fast |
|
film, including |
|
|
|
|
|
|
|
|
absorption and highly |
|
agitated thin film |
|
|
|
|
|
|
|
|
exothermic reactions or highly |
|
|
|
|
|
|
|
|
|
|
endothermic reactions prod- |
|
|
|
|
|
|
|
|
|
|
ucing a volatile compound |
|
|
|
|
|
|
|
|
|
|
whose desorption is desirable |
|
|
|
|
|
|
|
|
|
|
to shift the equilibrium or |
|
|
|
|
|
|
|
|
|
|
prevent side reactions. Agi- |
|
|
|
|
|
|
|
|
|
|
tated for very exothermic re- |
|
|
|
|
|
|
|
|
|
|
actions in viscous liquids. |
|
6.20 Scraped |
|
* |
|
* |
|
* |
|
|
Very exothermic reactions in |
|
surface |
|
|
|
|
|
|
|
|
viscous liquids. OK for foam- |
|
|
|
|
|
|
|
|
|
|
ing, fouling and particles with |
|
|
|
|
|
|
|
|
|
|
up to 65 % w/w solids. Sulfo- |
|
|
|
|
|
|
|
|
|
|
nations and polymerizations |
|
6.21 PFTR: |
|
|
* |
|
* |
* |
|
|
|
|
multiple hearth |
|
|
|
|
|
|
|
|
|
|
6.22 PFTR: |
|
|
* |
|
* |
|
|
|
|
|
traveling grate |
|
|
|
|
|
|
|
|
|
|
6.23 PFTR: |
|
|
* |
|
* |
* |
|
|
|
|
rotary kiln |
|
|
|
|
|
|
|
|
|
|
|
|
|
|
|
|
|
|
|
|
|

214 |
6 |
Reactors |
|
|
|
|
|
|
|
|
|
|
|
|
|
|
|
|
|
|
|
Table 6.12 Continued. |
|
|
|
|
|
|
|
|
||
|
|
|
|
|
|
|||||
Type of reactor |
Homogeneous |
Heterogeneous |
|
|
Comment |
|||||
|
|
G |
L |
S |
GL |
LL |
no-catalyst |
catalytic |
|
|
|
|
|
|
|
|
|
GS LS |
GS LS |
GLS |
|
|
|
|
|
|
|
|
|
|
|
|
6.24 PFTR, shaft |
|
|
* |
|
|
* |
|
|
|
|
furnace |
|
|
|
|
|
|
|
|
|
|
6.25 PFTR, melt- |
|
|
* |
|
|
* |
|
|
|
|
ing cyclone burner |
|
|
|
|
|
|
|
|
||
6.26 PFTR: series |
|
* |
|
* |
|
|
* |
** |
Slow reactions, RTD similar |
|
of CSTR. Cascade |
|
|
|
|
|
|
|
cas- |
to PFTR; can change reaction |
|
or multistage or |
|
|
|
|
|
|
|
cade |
conditions along the route |
|
multichamber |
|
|
|
|
|
|
|
|
|
|
tank |
|
|
|
|
|
|
|
|
|
|
6.27 STR: batch, |
|
* |
|
* |
* |
* |
** |
** |
Slow, consecutive reactions. |
|
with or without |
|
|
|
|
|
|
|
|
Moderate reaction rates, con- |
|
gas sparge |
|
|
|
|
|
|
|
|
version in the liquid phase. |
|
|
|
|
|
|
|
|
|
|
|
Flexible. |
6.28 STR: semi- |
|
* |
|
* |
* |
|
* |
|
Moderate reaction rates, con- |
|
batch: with and |
|
|
|
|
|
|
|
|
version in the liquid phase, |
|
without gas sparge |
|
|
|
|
|
|
|
parallel reactions. fast and very |
||
|
|
|
|
|
|
|
|
|
|
exothermic reactions; flexible; |
|
|
|
|
|
|
|
|
|
|
and if some of the reactants |
|
|
|
|
|
|
|
|
|
|
may decompose, or if want |
|
|
|
|
|
|
|
|
|
|
gradual addition of reactants. |
6.29 CSTR: me- |
|
*** |
|
** |
** |
* |
** |
*** |
Slow to moderate reaction |
|
chanical mixer: |
|
|
|
|
|
|
|
|
rates, conversion in the liquid |
|
with or without |
|
|
|
|
|
|
|
|
phase; Suitable for fast, highly |
|
gas sparge |
|
|
|
|
|
|
|
|
endo or exothermic reactions. |
|
|
|
|
|
|
|
|
|
|
|
Flexible. |
6.30 STR: fluidized bed, BFB, CFB or spouted
* |
* |
** * |
*** Very fast reactions; When |
|
|
|
temp control is needed or |
|
|
|
when nearly isothermal |
|
|
|
needed. Poor flexibility. |
|
|
|
Some axial mixing. |
6.31 |
TR: tank or * |
* |
|
|
** |
|
drum reactor: |
|
|
|
|
|
|
ponds, lagoons |
|
|
|
|
|
|
6.32 |
Mix of CSTR, * |
* |
* |
* |
|
Slow reactions. |
PFTR with recycle. |
|
|
|
|
|
|
6.33 |
STR: PFTR |
* |
|
* |
* |
Good backmixing and heat |
with large recycle |
|
|
|
|
removal; suitable for slow |
|
|
|
|
|
|
|
reactions. |
6.34 |
Reaction in- |
* |
|
* |
|
Highly viscous. |
jection molding and |
|
|
|
|
|
|
reactive extrusion |
|
|
|
|
|
|
|
|
|
|
|
|
|

|
|
|
|
6.3 |
How the Type of Reaction Affects the Size of the Reactor |
215 |
|||
Table 6.12 Continued. |
|
|
|
|
|
|
|
|
|
|
|
|
|
|
|
|
|
||
|
|
|
|
|
|
||||
Type of reactor |
Homogeneous |
Heterogeneous |
|
|
Comment |
||||
|
G |
L |
S |
GL |
LL no-catalyst |
catalytic |
|
|
|
|
|
|
|
|
GS LS |
GS LS |
GLS |
|
|
|
|
|
|
|
|
|
|
|
|
6.35 Reactive |
|
* |
|
|
|
|
|
Reaction window = distillation |
|
distillation/ |
|
|
|
|
|
|
|
window; reaction equilibrium |
|
extraction/ |
|
|
|
|
|
|
|
can be shifted by removing one |
|
crystallization, |
|
|
|
|
|
|
|
or more of the species from the |
|
HIGEE |
|
|
|
|
|
|
|
reaction space. |
|
6.36 Membrane |
|
|
|
* |
|
* |
* |
Reaction equilibrium can be |
|
reactors |
|
|
|
|
|
|
|
shifted by removing one or |
|
|
|
|
|
|
|
|
|
more of the species from the |
|
|
|
|
|
|
|
|
|
reaction space or reactant can |
|
|
|
|
|
|
|
|
|
be provided through the |
|
|
|
|
|
|
|
|
|
membrane |
|
6.37 Transport- |
|
|
|
* |
|
|
|
Fast reaction between a liquid |
|
react: liquid ring |
|
|
|
|
|
|
|
and an unstable gaseous reac- |
|
pump |
|
|
|
|
|
|
|
tant (produced under vacuum). |
|
|
|
|
|
|
|
|
|
|
|
6.3
How the Type of Reaction Affects the Size of the Reactor
In Section 6.2 we used the phases for the reaction to guide in the selection of the type of reactor. We consider now how the type of reaction might guide in the estimation of the size of the reactor. Figure 6.4 illustrates how the type and size of reactor relates to the production rate and the residence time. From the residence time we can estimate the size of the reactor or of the catalyst bed. For a continuous process, the residence time is usually based on the volume of the reactor or catalyst bed/volumetric feedrate of reactants to the reactor at inlet conditions. For a batch or semibatch process, the residence time is the length of time the batch is operated at reaction conditions.
As an aside, some authors use the term “space velocity”: such as, the liquid hourly space velocity, LHSV, the gas hourly space velocity, GHSV, the mass hourly space velocity, WHSV, or mol-volume space velocity, mol feed/hour litre of catalyst, MvolHSV. Unfortunately, the flowrates used in space velocity data are defined at conditions different from the typical reaction conditions. Thus, LHSV is measured at 20 hC; GHSV, at 15 hC and 0.1 MPa. As an approximation, we can convert space velocity to residence time, in seconds, = 3600/(the hourly space velocity corrected to volumetric conditions using the temperature and pressure to reactor inlet conditions).
Now consider rules of thumb about residence time. As an approximation, one option might be to assume that the same residence time is required when the same net bond energy is required. Bond energy data are available. For example,
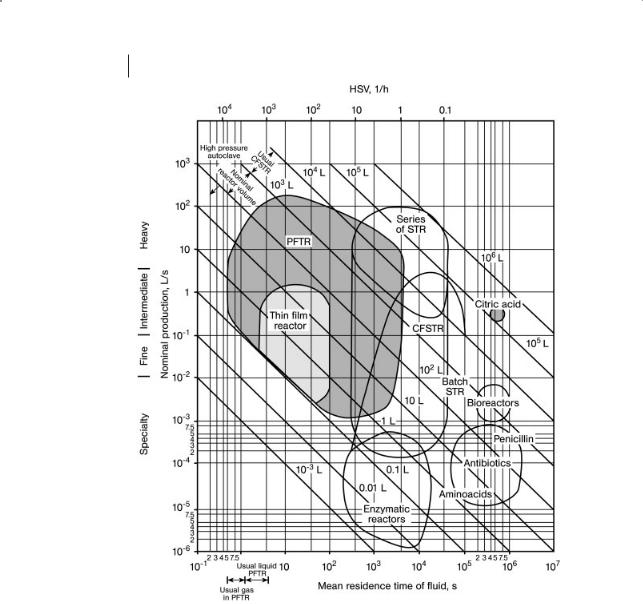
216 6 Reactors
Figure 6.4 Some characteristics of fluid processing reactors.
the C–C bond in the gas phase has an average bond energy of 347 MJ/kmol. Breaking this bond requires 347 MJ/kmol, endothermically; forming the bond releases this energy exothermically.
For any given reaction (with its making and breaking of bonds), the heat of reaction can be estimated by considering the sum of the energies of the bonds broken less the sum of the bonds created. Table 6.13 summarizes typical heats of reactions, MJ/kmol, for different types of reactions. Also given in this table is a brief description of the reaction, and a percentage representing the number of accidents out of 100 that have occurred with this type of reaction.
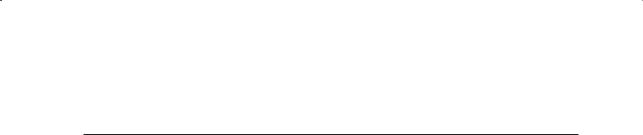
6.3 |
How the Type of Reaction Affects the Size of the Reactor |
217 |
Table 6.13 Example types of reactions. |
|
|
|
|
|
|
|
|
Net forming of bonds |
Net breaking of bonds |
acetylation, –220 MJ/kmol
addition, add moiety to unsaturated compound –110 to –120 MJ/kmol
alkylation, add alkyl group, (4 %)
aromatic + olefin, AlCl3 –100, –120 MJ/kmol paraffin + olefin, –80 to –112 [4, alkali acetylides, diazoalkane + aldehyde]
amination, add amino group by ammonolysis or by reduction –120 MJ/kmol
carbonylation, add CO to olefin
(oxo, hydroformylation): add CO and hydrogen to olefin, Fischer Tropsch: react CO and hydrogen to produce alkanes –165 MJ/kmol
to produce alcohols, –245 MJ/kmol
chlorination, add chlorine (6 %) –180 MJ/kmol
condensation add moiety to saturated compound [4, CS2 + aminoacetamide p pyrazoles] –30 to –90 MJ/kmol
diazotization, –65 MJ/kmol (3 %)
esterification, split off water and join acid and alcohol. (1 %) –40 MJ/kmol [4, carboxylic acid + diazomethane; acetylene + carboxylic acid vinylester]
epoxidation, –100 MJ/kmol
ethynylation, acetylene adds across a carbonyl group; –230 MJ/kmol
vinylation, add acetylene to form =
hydration, add water to = –155 MJ/ kmol
hydrogenation, add hydrogen depends very much on the degree of hydrogenation
–600 MJ/kmol
isomerization, change structural arrangement AlCl3 –10 to –20 MJ/kmol
oxidation, addition of O2 or remove H
–170 to –990 MJ/kmol (1.5 %) [4, ozonolysis; nitrous acids; low MM peracids]
neutralization, –50 to –100 MJ/kmol (6 %)
nitration, insert NO2 –130 MJ/kmol (11 %) polymerization –55 to –95 MJ/kmol (45 %)
hydrodealkylation, dealkylation in presence of H2 –100 MJ/kmol
diazo decomp –140 MJ/kmol
hydrolysis, add water and cleave into two parts. –15 MJ/kmol (7 %)
dehydration, take off water, –295 MJ/kmol
dehydrogenation, take off hydrogen +50 to +230
reforming, +200 to –890 MJ/kmol
combustion, +600 MJ/kmol pyrolysis, +150 MJ/kmol
cracking, decompose at high temperature +600 MJ/kmol
Nitrodecomposition, –400 MJ/kmol
dehydrocyclization + 200 to 250 MJ/kmol
sulfation, sulfonation, addition of sulfate, sulfonate |
desulfurization |
or sulfonic acid to aromatic –100 MJ/kmol (10 %) |
|
|
|

218 6 Reactors
Consistent with our concern for safety, Table 6.1 listed types of reactions that might be considered hazardous but only some specific reactions of a particular type are hazardous. For example, many condensation reactions do not pose a hazard. However, the reaction between carbon disulfide and aminoacetamide to make pyrazoles is hazardous. If a hazard rating = 0 means negligible hazard; 4 means extremely hazardous, then in Table 6.13 are listed some example 4 reactions that pose hazards. Another way of considering hazardous reactions is to identify the types of bonds that are potentially hazardous. These include vinyl, conjugated double bonds with carbon, nitrogen, and oxygen atoms (e.g., butadience, isoprene, cyclopentadiene, acrolein), adjacent double bonds (toluene diisocyanate), three membered rings (ethylene oxide), aldyhydes, isopropyl compounds, alkyl compounds, haloalkenes and dienes.
Thus, for Option 1 to estimate residence time we might plot residence time as a function of temperature with the heat of reaction as a parameter.
Option 2 for estimating the residence time might be related to the type of reaction. That is, at a given temperature, all gas phase chlorinations, for example, might require the same residence time.
Now for the specifics. Rules of thumb given here for residence times are based on
xthe phase: G, L, GL
xwhether catalyzed or uncatalyzed
xthe inlet temperature
xthe heat of reaction or the type of reaction.
Few data have been published about the residence time of commercial reactors. Thanks to the help of many colleagues, I was able to work with 250 species and over 650 data1). From the data available we can provide some order-of-magni- tude estimates (within a factor of ten) of the residence time used industrially.
Option 1: given the phase, assume that reactions with the same heat of reaction require the same residence time. Here we use a generic trajectory plot of residence time versus reaction temperature. We use the term trajectory because the data do not represent how the rate of reaction changes with temperature for any specific reaction. Figure 6.5 shows such data for gaseous, catalyzed reactions for three different ranges of heats of reaction: 5–100 MJ/kmol; 150–300 MJ/kmol and 600–900 MJ/kmol. For a given reaction temperature, the higher the heat of reaction, the longer the residence time required. Also shown above and below the 150–300 MJ/kmol line are lines indicating the arbitrary “factor-of-ten” region. Similar lines for the other two heats of reaction are also shown. For catalyzed gas reactions, with 44 species and 150 data, the data were within these bounds except for fluidized bed operations, for acrolein via oxidation (prediction low, data are above the line, (+), ethanol via hydration (+), cyclohexanol (–), aniline (+) and ammonia (+ +) via hydrogenation and butadiene via dehydration (++). Over 80 % of the available data are within the bands.
1) I would appreciate receiving residence time |
improve this analysis. My e-mail is |
data for industrial processes so that I can |
I woodsdr@mcmaster.cai . Thanks. |
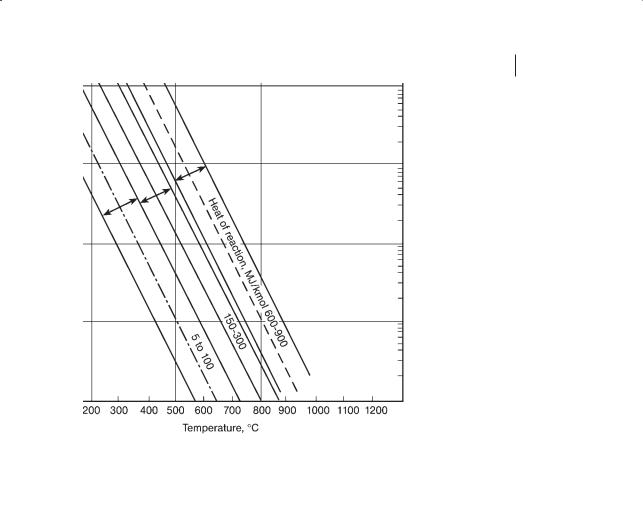
6.3 How the Type of Reaction Affects the Size of the Reactor 219
Figure 6.5 Residence time versus temperature for gaseous, catalyzed reactions with the heat of reaction as a parameter, 5–100 MJ/kmol; 150–300 MJ/kmol and 600–900 MJ/kmol with the factor-of-ten lines.
Figure 6.6 presents data for gaseous, noncatalyzed reactions (pyrolysis, thermal cracking, oxidation, 10 species and 21 data) with typical heats of reaction of 120– 150 MJ/kmol. In general, noncatalyzed reactions take about 1000 times longer than the same catalyzed reaction at the same reaction temperature. Data lying outside the factor-of-ten bands are benzene (+) via hydrodealkylation and benzene
(+) via hydrogenation of biphenyl (+).
For liquid reactions (192 product species, 450 data) Fig. 6.7 provides data for liquid, liquid–liquid, gas–liquid, gas–liquid–solid reactions. Over 80 % of the data lie within the factor-of-ten bands. Data lying outside the factor-of-ten bands are: acetaldehyde (–) via oxidation; acetone (++) via oxidation; adipic acid (–) via oxidation; aldol (–) via condensation; alkylate (– –) via alkylation; amino undecanoic acid (–) via hydrolysis; benzoic acid (–) via oxidation; butanol (–) via carbonylation; butene diol (–) via hydrogenation; butyl acetate (–) via alkylation; cellulose
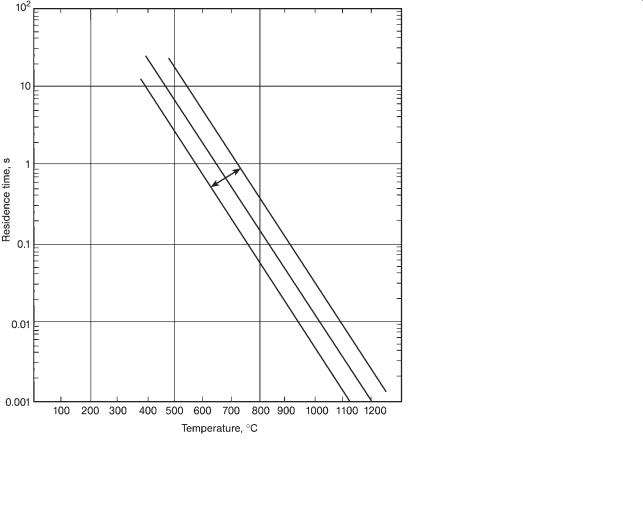
220 6 Reactors
Figure 6.6 Residence time versus temperature for gaseous, uncatalyzed reactions. The factor-of-ten lines are drawn. The heat of reaction is about 120–150 MJ/kmol.
triacetate (– –) via acetylation; chloroprene (– –) via chlorination; DDT (–) via condensation; dimethyl terephthalate, (+) via esterification; dimethylaniline (+ +) via alkylation; erythritol (+) via aerobic fermentation; ethanol from corn or whey (–) via anaerobic fermentation; ethylene glycol (–) via hydration; ethyl hexanol (–) via hydrogenation; ethyl hexanol (+) via carbonylation; lactic acid from 15 % sugar, (+) via aerobic fermentation; methyl butynol (– –) via ethynylation; penicillin (+) via aerobic fermentation; polyester (++) via esterification; polyester (+ +) via condensation; polyetherpolyol (+) via addition; polyethylene, high pressure process for LDPE (– – –) via polymerization; polyethylene terephthalate (+) via polymerization; polyisoprene (–) via polymerization; polystyrene crystal and high impact
(+) , via polymerization; polyurethane RIM (– – –) via polymerization; propylene oxide (+) via oxidation; SCP ex methane (–) via aerobic fermentation; sodium benzoate (– –) via neutralization; sorbitol (–) via hydrogenation; terephthalic