
Ответы ГОСЫ кафедра ТС и СА
.pdf
ОТВЕТЫ ДЛЯ ГОСЭКЗАМЕНА
1. Выбор тепловой схемы ГТУ.
Теплота, подведённая к изолированной системе, расходуется на изменение внутренней энергии и совершение работу против внешних сил.
1.Схема простейшей ГТУ со сгоранием при P=const;
2.Схема простейшей ГТУ со сгоранием при P=const и регенерацией;
Степень регенерации – отношение количества теплоты сообщённое воздуху в регенераторе к предельному количеству теплоты которое можно считать переданным воздуху в бесконечно большом регенераторе при достижении .
Чем больше , тем больше температура за компрессором и тем меньше температура за турбиной. При каком-то , в этом случае регенерация невозможна.
3.Схема ГТУ с промохлаждением воздуха между компрессорами;
4.Схема ГТУ с промперегревом газа между турбинами.
2. Задачи и порядок проведения монтажа турбин.
Задачи:
1.Совместная сборка отдельных, уже собранных узлов, с целью проверки их взаимосвязи между собой и по отношению к главным осям установки.
2.Центровка и привязка сопряжённых узлов друг к другу.
3.Фиксирование узлов для сохранения постоянства их положения между собой в агрегате и по отношению к осям агрегата.
Требования:
1.Соблюдение правильного положения отдельных элементов и узлов турбины и всего вспомогательного оборудования между собой и к продольной и поперечной осям фундамента.
2.Получение плавной линии осей всех валов.
Монтаж:
Взависимости от мощности и назначения, турбины поступают на монтажную площадку
вразобранном или собранном виде.
1.По ходу монтажа первыми подготавливаются и устанавливаются фундаментные рамы.
2.Сборка ЦНД и его монтаж. После сборки ЦНД является базой для дальнейших монтажных работ.
3.Сборка ЦСД и ЦВД и их монтаж (аналогично ЦНД).
4.Установка корпусов подшипников ЦСД и ЦВД по струне и по уровню с проверкой по реакциям опор.
5.Центровка роторов ЦНД, ЦСД, ЦВД по расточкам под уплотнения и по полумуфтам.
6.Подливка фундаментных рам.
7.Проверка центровки диафрагм и обойм концевых уплотнений (борштангой).
8.Проверка зазоров в концевых уплотнениях, уплотнениях диафрагм и в проточной части.
9.Закрытие цилиндров.
10.Горячая затяжка крепежа горизонтального разъёма цилиндров.
11.Соединение полумуфт роторов и закрытие подшипников.

3. Снижение вредных выбросов из камеры сгорания ГТУ.
Для одновременного уменьшения всех вредных выбросов необходима разработка камер сгорания нового типа, которые позволяли бы удовлетворить современным и перспективным требованиям. Рассмотрим ряд вопросов, которые позволяют уменьшить поставленную задачу.
Данный график характеризует уровень выбросов СО и NОx для некоторой абстрактной КС в зависимости от температуры первичной зоны. Из графика видно, что при температуре меньше 1600 К концентрация СО слишком велика, а при температуре больше 1730-1750 К возникает избыток NОx. Предельно допустимые СО и NОx находятся в достаточно узком интервале температур (от 1600 до 1750 К). Все рассмотренные ниже перспективные методы конструирования КС основаны на том, чтобы удержать температуру в зоне (или зонах) горения в очень узком интервале на всех режимах работы ГТ.
1. Камеры изменяемой геометрии.
Конструкция КС основана на введении в КС элементов регулирования распределения воздуха. На номинальном режиме значительная часть воздуха подается в головную часть пламенной трубы, с целью минимизации образования сажи и NОx , а так же обеспечения необходимого расхода воздуха на пристенную завесу.
На частичных режимах увеличивается доля воздуха, подаваемого в зону смешения, чтобы при небольшом расходе топлива удерживать температуру в первичной зоне в интервале, который обеспечивает нужный уровень выбросов.
2. Сжигание предварительно подготовленной бедной смеси.
Данный метод предусматривает полное испарение топлива, и полное перемешивание его с воздухом до начала горения с целью исключения горения капель и создания в первичной зоне гомогенной бедной смеси, что позволяет обеспечить низкую температуру реакции,
устранить в зоне горения локальные высокотемпературные области, а значит и уменьшить выброс NOx (максимальный эффект в КС изменяемой геометрии).
3. Каталитическое горение (каталитические КС).
Катализаторы позволяют окислить топливо при температурах значительно ниже бедного предела воспламенения. Поэтому применение катализаторов в КС, которые занимают часть объёма зоны горения, даёт возможность сжигать топливо при температуре, которая приблизительно на 1000 К ниже максимальной температуры в зоне горения обычной КС. Т.к. выброс NOx зависит от температуры экспоненциально, то горение при сильно сниженных температурах уменьшает образование NOx на несколько порядков.

4. Требования к САР угловой скорости ротора турбины.
1.Высокая надёжность: достигается дублированием;
2.Требования к быстродействию:
Система регулирования угловой скорости должна обладать высоким быстродействием.
Это обусловлено тремя причинами:
Система регулирования должна держать сброс. Это значит, что при отключении генератора от сети система регулирования должна так прикрыть регулирующие клапана, что бы угловая скорость не достигла уровня противоразгонной защиты;
Обеспечение собственно устойчивости системы регулирования: классическое
условие устойчивости |
; |
Связана с необходимостью эффективного участия турбины в аварийном регулировании энергосистемы (для повышения статического и динамического запаса устойчивости ЛЭП.)
3.Требования к степени неравномерности регулирования:
4.Требования к степени нечувствительности:
МЭК:
Евро стандарт:
5. Требования, вытекающие из условия работы турбины в объединённой энергосистеме:
Регламентируется поведение турбины и системы регулирования при синхронном качании частоты электрического тока в энергосистеме;
Направлена на повышение статической устойчивости ЛЭП;
Для обеспечения статической устойчивости ЛЭП турбина должна как можно быстрее снизить мощность до заданного уровня и в дальнейшем в случае необходимости восстановить мощность. Для реализации в электрической части системы регулирования используется быстродействующий ограничитель мощности.
Направлена на повышение динамической устойчивости ЛЭП; Для повышения динамической устойчивости турбины система регулирования должна
как можно быстрее и точнее отреагировать на импульсное управляющее воздействие поступающие от противоаварийной автоматики. Для реализации в ЭЧСР сформирован блок АИР (автоматической импульсной разгрузки)

5. Цель и задачи охлаждения деталей ГТ.
Известно, что с повышением начальной температуры рабочего тела увеличивается КПД ГТУ и мощность (почитать об этом). С повышением температуры газа снижается надёжность работы ряда элементов проточной части турбины. Наибольшую трудность представляет обеспечение надёжной работы рабочих лопаток первой ступени ГТ.
На вращающиеся детали ГТ действуют огромные ЦБС. Напряжения от ЦБС достигают до 30 кг/мм2. Такие же напря-
жения и в гребнях диска и в полости диска. Напряжения от ЦБС достигает 30 кг/мм2 , а прочностные свойства материалов зависят от температуры. Они резко снижаются у перлитных сталей при T>480°С, у аустенитных >650°С, у никелевых >750-800°C, кобальтовых >900°С. Аустенитные, никелевые, кобальтовые стали и сплавы намного дороже перлитных. Изготовить из них технологически сложнее, чем из перлитных (трудно изготовить из них поковки роторов). Коэффициент расширения этих материалов в 1,5 раза больше, чем у перлитных, что приводит к большим деформациям деталей и узлов. Для выбранного материала можно определить допустимую рабочую температуру (с учетом напряжений, возникающих в материале от действия ЦБС и др. сил). Превышение действительной температуры над максимально допустимой должно быть снято охлаждением. В виду обеспечения максимальной экономичности турбоустановки, необходимо так охлаждать детали, чтобы они работали при температуре, близкой к максимально допустимой (меньше затраты на охлаждающий агент, его подвод и т.д.).
Количество отведённой теплоты определяется по формуле:
∫ ( |
) |
–допустимая температура металла;
–температура газа.
При создании системы охлаждения стремятся снизить количество отведённого тепла.
Основные требования:
При минимальном расходе и начальном давлении охлаждаемого воздуха его распределение по элементам тракта должно обеспечивать максимальный уровень температуры всех элементов и градиенты температур в них, допустимые по условиям длитель-
ной прочности ( |
|
– коэффициент запаса). |
|
Расчёт охлаждения деталей делится на 2 части:
1.Тепловой расчёт системы охлаждения, при котором определяются зависимость температуры детали от расхода и параметров охлаждающей среды (определяется его расход, давление, температура...).
2.Гидравлический расчёт системы охлаждения, при котором определяются размеры проходных сечений охлаждаемого тракта. Эти проходные сечения должны обеспечивать распределение расхода охлаждающего агента, выбранного в результате теплового расчёта и снизить до минимума потери (гидравлические потери в каналах).
6. Статическая и динамическая балансировка роторов.
Заключительной операцией изготовления роторов является проведение статической и динамической балансировки. Статическая балансировка, как правило, проводится отдельных элементов ротора, в частности дисков. Такая балансировка позволяет сократить время динамической балансировки.
Для проведения статической балансировки диск насаживают на валик, который опирается на опоры, позволяющие перекатываться валику по ним. Опорные поверхности валика, а так же сами опоры имеют закалку. В случае неуравновешенности части диска валик перекатывается по опорам, занимает положение тяжёлой и неуравновешенной частью вниз. Для уравновешивания диска может быть применено два метода:
1.Снятие лишнего веса;
2.Добавление на противоположной стороне уравновешивающего груза.
Обычно поступают таким образом: на диске делают пазы типа ласточкиного хвоста, подбирают соответствующий груз и устанавливают его. Дополнительный груз или уравновешивающий груз имеет сверление нарезкой, куда заворачивается болт и фиксирует положение груза – это статическая балансировка. Статическая балансировка не позволяет гарантировать отсутствие вибрации ротора при работе, в связи с тем, что может быть динамическая неуравновешенность роторов в сборе. Поэтому после статической проводят динамическую балансировку.
Для проведения динамической балансировки используют специальные балансировочные станки, опоры которого имеют возможность колебаться. Для крупных роторов динамическая балансировка проводится в специальных вакуумных камерах на рабочих числах оборотов. Вакуумная камера имеет герметичную конструкцию, а сама она выполнена из железобетона. В этой камере кроме динамической балансировки производится разгонная проба ротора для проверки механической прочности ротора. Разгонная проба проводится один раз с подъёмом числа оборотов, превышающих номинал на 15-20%. На этом же станке проводится и динамическая балансировка ротора, которая позволяет исключить неуравновешенность ротора на рабочих числах оборотов. После проведения динамической балансировки ротор консервируется и отправляется заказчику.
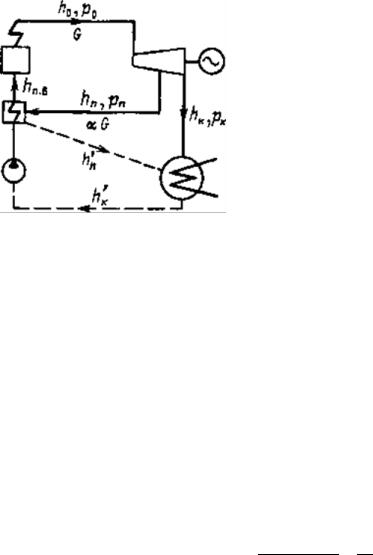
7. Регенеративный подогрев питательной воды в цикле ПТУ.
Вместо того чтобы питательную воду греть в самом котле за счёт теплоты сжигаемого топлива, для повышения температуры питательной воды можно использовать пар, отбираемый из промежуточной ступени турбины и совершивший определённую работу при расширении от начального состояния до давления в отборе. Таким образом, можно осуществить регенерацию теплоты, т. е. передать питательной воде часть теплоты, отдаваемой охлаждающей воде.
На рис. показана принципиальная схема установки конденсационной турбины с одним регенеративным подогревателем поверхностного типа. Питательный насос прокачивает воду, подаваемую в котёл через трубчатую систему теплообменника и обогреваемую паром из промежуточного отбора турбины. Конденсат греющего пара отводится в конденсатор турбины.
В поверхностном подогревателе питательная вода может быть нагрета до температуры, близкой к температуре насыщения обогревающего пара. Допустим, что разность между
энтальпией конденсата греющего пара |
и энтальпией питательной воды |
в при выходе из |
подогревателя составляет |
. Если обозначить через а количество отбираемого |
пара, выраженное в долях расхода пара, подаваемого к турбине, и принять, что энтальпия воды на входе в подогреватель равна , то уравнение теплового баланса подогревателя напишется так:
( )
Отсюда доля отбираемого пара составит
и мощность, развиваемая отбираемым паром |
|
|
||
( |
) |
( |
) ( |
) |
|
|
|
||
|
|
|
||
Максимальная величина |
достигается при |
|
. |
|
|
||||
Выводы: |
|
|
|
|
1.Любому выбранному числу ступеней подогрева соответствует своя оптимальная температура питательной воды;
2.Оптимальная величина подогрева растёт с увеличением z;
3.Чем больше z, тем больше экономия от РППВ.
При больших |
увеличиваются потери тепла в ПГ с уходящими газами. |

8.Характерные виды разрушения деталей турбоустановок и основные причины поломок. Хрупкий излом. Пластическое разрушение. Усталостные трещины. Ползучесть.
Существует два типичных излома – кристаллический (хрупкий) и волокнистый (вязкий). Первый происходит в результате отрыва одной части кристалла от другой по кристаллографическим плоскостям (поэтому излом обычно блестящий), а второй – в результате образования и слияния пор, что сопровождается большой пластической деформацией поверхности (поэтому излом матовый). Исследования изломов проводят на электронном микроскопе. Хрупкое разрушение характеризуется так называемым ручьистым изломом, а вязкое – чашечным. Для хрупкого разрушения типична острая (рис. а), часто ветвящаяся трещина, большая скорость её распространения и отсутствие пластической деформации при её распространении. Трещина движется за счёт накопленной упругой энергии. Для вязкого разрушения характерна тупая, раскрывающая трещина (рис б), малая скорость её распространения и значительная пластическая деформация металла при её продвижении.
Напряжения, величина которого находится в заштрихованном интервале, деформирует металл во времени. Это явление, то есть деформация образца во времени под действием напряжения, постоянного по величине, называется ПОЛЗУЧЕСТЬЮ. Кривая ползучести характеризует деформацию образца во времени под дей-
ствием постоянного напряжения. ОА – упругая и пластическая деформация, возникшие в момент приложения нагрузки; АВ – неустановившейся участок на кривой ползучести (деформация с непостоянной скоростью); ВС – установившийся режим ползучести (металл деформируется с постоянной скоростью); СД – ползучесть происходит при непрерывном усложнении процесса заканчивается разрушением в точке Д.