
Сварка
.pdf
Таблица 2.2 – Технические характеристики сварочных горелок ГС-53 и ГСМ-30
Номер |
Толщина свари- |
Рабочее давление |
Расход ацетиле- |
Расход кисло- |
наконечника |
ваемой стали |
кислорода, атм |
на, м3/ч |
рода, м3/ч |
|
|
|
|
|
0 |
0,2–2,7 |
0,5–4 |
20–65 |
22–70 |
1 |
0,5–1,5 |
1–4 |
50–125 |
55–135 |
2 |
1,0–2,5 |
1,5–4 |
120–250 |
130–260 |
3 |
2,5–4 |
2–4 |
230–400 |
260–440 |
4 |
4–7 |
2–4 |
400–700 |
430–750 |
5 |
7–11 |
2–4 |
670–1100 |
740–1200 |
6 |
10–18 |
2–4 |
1050–1750 |
1150–1950 |
7 |
17–30 |
2–4 |
1700–2800 |
1900–3100 |
Горелка ГС-53 универсальная с комплектом семи наконечников(1–7) (обычный комплект четыре штуки) предназначена для сварки толщин0,5–30 мм. Горелка ГСМ-53 малолитражная с комплектом пяти наконечников(0–4) предназначена для сварки малых толщин 0,2–7 мм.
В настоящее время разработана новая горелка«Москва», более устойчивая против ударов и обеспечивающая более стабильное пламя в работе. Для пайки с использованием газов – заменителей ацетилена (метана, коксового и городского газа) используется специальная горелка или горелка ГС-53 с комплектом специальных наконечников НЗП, отличающихся от наконечников ГС-53 размерами отверстий в мундштуках, инжекторах и смесительных камерах.
Инжекторная горелка не обеспечивает постоянства состава газовой смеси, так как состав меняется в процессе сварки.
Сварщик должен непрерывно следить за характером пламени и корректировать состав смеси ацетиленовым вентилем горелки. Непостоянство состава смеси является существенным недостатком инжекторной горелки.
Основное ее преимущество в том, что можно работать на любом низком давлении ацетилена, начиная с 0,005 атм. Это преимущество является решающим, и в настоящее время наша промышленность пользуется почти исключительно инжекторными горелками, поскольку производство ацетилена среднего давления, достаточного для питания безынжекторных горелок, пока еще незначительно. Однако инжекторная горелка может работать на ацетилене не только низкого, но и высокого давления. Чем выше давление ацетилена, тем лучше работает инжекторная горелка.
Рисунок 2.5 – Схема безынжекторной горелки
20
Конструкция горелки высокого давления, или безынжекторной горелки (рисунок 2.5), проще конструкции горелки низкого давления. Кислород поступает в горелку по резиновому шлангу и через приемный ниппель и регулировочный вентиль 1 проходит в смеситель3. Аналогичный путь проходит горючий газ, поступающий через регулировочный винт 2. Из смесителя 3 смесь горючего газа с кислородом поступает в камеру смешения4, где вследствие увеличения сечения газового потока скорость его уменьшается и заканчивается смешение кислорода с горючим газом, дающее при выходе из камеры смешения по своему объему горючую смесь. Из камеры смешения 4 готовая смесь проходит по трубке наконечника 5 и через канал мундштука 6 выходит наружу, где сгорает, образуя сварочное пламя. Давление газа на выходе в горелку порядка 0,5–0,7 атм. Требующееся давление примерно одинаково как для кислорода, так и для ацетилена.
В России выпускаются безынжекторные горелки типа ГАР-2-56. Безынжекторные горелки могут быть построены как для ацетилена, так и для других горючих газов – водорода, метана. Они сравнительно просты по устройству, хорошо поддерживают постоянство состава газовой смеси, дают устойчивое сварочное пламя. Несмотря на эти положительные качества, горелки высокого давления в нашей промышленности применяются реже, потому что они могут работать лишь на ацетилене достаточного давления, а промышленность широко пользуется ацетиленом низкого давления.
5 Методические указания по выполнению работы
Работа выполняется каждым студентом индивидуально. По описанию, схемам и натурным образцам(в разрезах) ознакомиться с конструкциями ацетиленового генератора АНВ-1,25-73, ацетиленового и кислородного баллонов, редукторов, горелок и изучить принцип их работы. Уяснить преимущества и недостатки одних конструкций перед другими.
6 Содержание отчета
1 В отчете указать наименования отдельных деталей ацетиленового генератора АНВ-1,25-73, редукторов, горелок в соответствии с рисунками в руководстве.
2 Указать содержание кислородного и ацетиленового баллонов и его назначение.
3 Подготовить устно ответы на контрольные вопросы.
7 Контрольные вопросы
1 Горючие газы, применяемые при газовой сварке и резке.
2Назначение ацетиленовых генераторов.
3Назначение водяного затвора ацетиленового генератора. Устройство и назначение баллонов для сжиженных газов.
4Предназначение ацетиленовых баллонов и области их применения.
21
5 Назначение пористой массы в ацетиленовом баллоне.
6 Назначение ацетона в ацетиленовом баллоне.
7 Правила испытания ацетиленовых баллонов.
8 До какого давления производится отбор ацетилена из баллона и поче-
му?
9 В каком положении должен находиться ацетиленовый баллон в процессе работы?
10 Устройство и назначение кислородных баллонов и области их применения.
11 Из какого металла изготовляются вентили кислородного и ацетиленового баллонов и почему?
12 Правила транспортировки и хранения баллонов для газовой сварки и резки металлов.
13 Правила испытания баллонов.
14 Области применения универсальных инжекторных резаков.
15 Условия газокислородной резки металлов.
16 Области применения керосинореза.
17 Порядок зажигания сварочной горелки и ее тушения.
18 Области применения безынжекторных горелок для газовой сварки и пайки.
19 Области применения инжекторных горелок для газовой сварки.
20 Назначение редукторов для сжатых газов, применяемых при газовой сварке, резке.
21 За счет чего рабочее давление в редукторе автоматически поддерживается постоянным?
22 За счет чего повышается или понижается рабочее давление газа? 23 Отличие кислородных редукторов от ацетиленовых.
24 Принцип работы безынжекторной горелки.
25 Принцип работы инжекторной горелки.
26 Преимущества и недостатки инжекторной горелки.
27 Преимущества и недостатки безынжекторной горелки.
8 Литература
1 Некрасов Ю. И. Справочник молодого газосварщика и газорезчика. М. :
Высш. шк., 1984. 168 с.
2 Хренов К. К. Сварка, резка и пайка металлов. Изд. 4-е, стереотип. М. : Машиностроение, 1973. 408 с.
22
Лабораторная работа № 3
ОБОРУДОВАНИЕ И АППАРАТУРА ДЛЯ ВОЗДУШНО-ПЛАЗМЕННОЙ И ГАЗОВОЙ
РЕЗКИ МЕТАЛЛОВ
1 Цель работы
Ознакомиться с аппаратурой и оборудованием для воздушно-плазменной и газовой резки металлов.
2 Задание
Изучить устройство установки для воздушно-плазменной резки металлов и аппаратуру для газовой резки металлов.
3 Необходимое оборудование и материалы
1 Установка для воздушно-плазменной резки УВПР-120.
2Резак ацетилено-кислородный.
3Керосинорез в разрезе.
4Планшеты с характеристиками установки для воздушно-плазменной резки УВПР-120, резаков.
4 Основные теоретические сведения
4.1 Сущность процесса воздушно-плазменной резки
Воздушно-плазменная резка – это высокопроизводительный процесс, пригодный для резки металлов в промышленных условиях. При этом скорость резания больше, чем при газовой резке, при более высоком качестве реза. Процесс воздушно-плазменной резки не требует дорогостоящих, технологически опасных и экологически вредных материалов, используется лишь электроэнергия и сжатый воздух.
Сущность процесса воздушно-плазменной разделительной резки заключается в локальном интенсивном расплавлении разрезаемого металла в объеме полости реза теплотой, генерируемой сжатой дугой, и удалении жидкого металла из полости сжатым воздухом, вытекающим из канала сопла плазмотрона.
В современной технике резки применяют две схемы плазмообразования (рисунок 3.1).
23
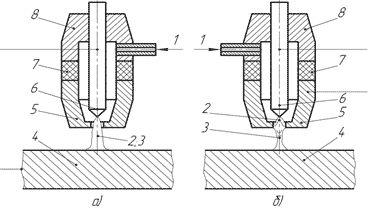
а– плазменная дуга; б – плазменная струя;
1– подача газа; 2 – дуга; 3 – струя плазмы; 4 – обрабатываемый металл; 5 – наконечник; 6 – катод; 7 – изолятор; 8 – катодный узел
Рисунок 3.1 – Схемы плазмообразования
В первом случае используют дугу прямого действия, возбуждаемую на обрабатываемом металле, являющемся одним из электродов разряда. При этом используется энергия одного из приэлектродных пятен дуги и энергия плазмы столба и вытекающего из него факела. Поэтому резку по такой схеме называют плазменно-дуговой.
Во второй схеме, соответствующей косвенной (независимой) дуге, объект обработки не включают в электрическую цепь. Вторым электродом сжатой дуги служит формирующий наконечник плазмотрона. Поток плазмы, вытекая из сопла, образует свободную струю плазмы. Для резки используется только энергия плазменной струи (резка плазменной струей).
Энергетическая оценка обеих схем показывает, что плазменно-дуговая резка наиболее эффективна, поскольку полезная мощность сжатой дуги реализуется в частях разряда, вынесенных за пределы наконечника. Поэтому для резки металлов, как правило, используют схему плазменно-дуговой резки. Плазменную струю применяют относительно редко, преимущественно для резки неметаллических материалов.
Основными элементами плазмотрона, предназначенного для плазменной резки, являются электрод (катод), сопло и изолятор между ними (рисунок 3.2).
24
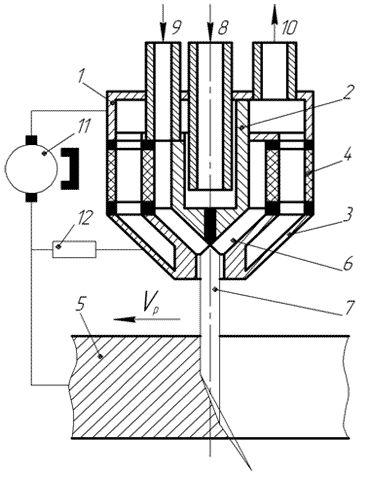
|
|
|
1 – корпус; |
2 – электрод |
(катод); 3 – формирующий наконечник; |
||||
4 |
– изолятор; 5 – |
разрезаемый |
металл; 6 – дуговая |
камера; 7 – столб дуги; |
|||||
8 |
|
– |
подача |
охлаждающей |
воды; 9 – подача |
плазмообразующего |
газа; |
||
10 |
– |
слив |
воды; |
11 – источник |
тока; 12 – устройство зажигания |
дуги; |
Vр – направление резки
Рисунок 3.2 – Режущий плазмотрон
Корпус режущего плазмотрона содержит цилиндрическую дуговую камеру малого диаметра с выходным каналом, формирующим сжатую (плазменную) дугу. Для возбуждения плазмогенерирующей дуги служит электрод, располагаемый обычно в тыльной стороне дуговой камеры. Столб дуги ориентируется по оси формирующего канала и заполняет практически все его сечение.
В дуговую камеру подается рабочий газ(плазмообразующая среда). Газ, поступая в столб дуги, заполняющий формирующий канал, превращается в плазму. Вытекающий из сопла поток плазмы стабилизирует дуговой разряд.
Газ |
и |
жесткие |
стенки |
формирующего канала |
ограничивают сечение столба |
||
дуги |
(сжимают |
его), что |
приводит к |
повышению температуры |
плазмы до |
||
15 000–20 000 ºС. При этих температурах электрическая проводимость плазмы |
|||||||
приближается к электропроводимости металлического проводника. Скорость |
|||||||
плазмы |
в струе, |
истекающей из сопла |
режущего |
плазмотрона, может |
превы- |
25
шать 2–3 км/с. Плотность энергии в формирующих соплах режущих плазмотронов достигает 10 Вт/см.
При воздушно-плазменной резке наиболее эффективно используется энергия в режущей дуге постоянного тока прямой полярности(анод на металле). В качестве рабочей плазмообразующей среды при воздушно-плазменной резке используется воздух.
В отличие от газокислородной резки, при которой пламя выделяет мало теплоты и имеет относительно низкую температуру, для врезания в металл требуется затратить некоторое время на местный подогрев металла до температуры его воспламенения. Сжатая дуга вследствие высокой температуры и скорости потока плазмы врезается в металл почти мгновенно.
Технология воздушно-плазменной резки
Для того чтобы осуществить плазменную разделительную резку металла, необходимо расплавить определенный объем материала вдоль предполагаемой линии реза и удалить его из полости реза скоростным потоком плазмы.
Расплавленный металл, образующийся на лобовой поверхности реза, удаляется скоростным потоком плазмы сжатой дуги.
Скорость потока плазмы возрастает с увеличением расхода плазмообразующего газа и тока и быстро уменьшается с увеличением диаметра сопла. Она может достигать примерно 800 м/с при токе 250 А.
Скорость течения расплава зависит от скорости потока плазмы на границе раздела фаз, т. е. на границе жидкий металл – поток плазмы. Так, при резке металла толщиной 5–20 мм со скоростью 0,75–6 м/мин и ширине реза3–6 мм скорость течения расплавленного металла 20–40 м/с.
Задача плазменной разделительной резки – вырезка контуров с перпендикулярными кромками в соответствии с заданными размерами.
Предполагается, что поверхности резов должны быть ровными и гладкими, а качество металла у кромок равноценно качеству основного металла. Однако из-за несовершенства процессов резки не всегда удается выполнить указанные требования.
Наиболее характерными отклонениями от этих требований являются неплоскостность и неперпендикулярность поверхностей реза из-за непостоянства сечения плазменно-дугового реза по высоте. Это вызвано тем, что различные участки режущей дуги вводят в разрезаемый металл неодинаковое количество теплоты, а следовательно, на различной глубине реза расплавляется неодинаковое количество металла.
В верхней части реза, в которой металл может расплавляться за счет излучения столба разряда, теплопередача равномерна и рез имеет параллельные кромки. Тепловую энергию в нижнюю часть реза может вводить факел дуги. Температура плазмы в факеле и интенсивность теплопередачи постепенно уменьшаются по высоте нижней части реза, поэтому его кромки на этом участке сходятся книзу. Наиболее интенсивно передает тепловую энергию активное пятно дуги. В зависимости от его расположения по глубине реза или зоны его
26
перемещения, а также от толщины разрезаемого металла рез может получиться уширенным кверху или книзу или бочкообразной формы. Расположение активного пятна дуги в полости реза зависит от параметров дуги, характера ее формирования, скорости резки, толщины и свойств разрезаемого металла. При изменении этих параметров изменяется и форма сечения реза. Так, при уменьшении скорости резки общая ширина реза увеличивается, особенно в нижней его части, поверхности реза становятся почти параллельными друг другу, при очень малых скоростях в нижней части расширяются.
С увеличением силы тока режущей дуги ширина реза увеличивается, особенно в нижней его части, а поверхности реза становятся почти параллельными друг другу. При увеличении расхода газа уменьшаются общая ширина реза и непараллельность его поверхностей. Подъем режущего сопла над металлом сопровождается уширением реза, особенно в верхней его части, и увеличением непараллельности кромок.
Форма сечения реза зависит от толщины разрезаемого металла и от рабочего напряжения режущей дуги. При резке металла небольшой(5–20 мм) толщины резы имеют, как правило, сходящиеся кромки. Если резать металл такой толщины жесткой режущей дугой (рабочее напряжение 140–150 В и более), то формы поверхностей реза близки к плоским формам и их непараллельность незначительна. Форма кромок резов, выполненных мягкой режущей дугой, зависит от скорости резки. При малых скоростях резки могут быть получены кромки, близкие к вертикальным, однако с увеличением скорости сечение реза получается неправильной формы: вертикальная плоскость верхней части исчезает или становится вогнутой, а затем выпуклой в сторону реза.
При резке металла большой (40–50 мм и более) толщины наряду со сходящимся книзу сечением реза наблюдается уширение в средней его части(бочкообразный рез). Однако и в этом случае режущая дуга с высоким рабочим напряжением обеспечивает получение резов с поверхностями более плоскими и параллельными, чем при резке мягкой дугой.
При плазменной разделительной резке кроме отклонений от заданных размеров и форм кромок вырезаемых деталей происходят видимые и невидимые изменения качества поверхностей реза. После резки кромки могут быть гладкими и шероховатыми, матовыми и блестящими, темными и светлыми. У
нижних кромок реза часто образуются наплывы в виде небольшого валика вдоль нижних кромок реза, цепочки застывших натеков в виде капель металла («бороды»), приварившегося к кромкам грата(многочисленные нитеобразные натеки различной длины).
В процессе резки у кромки реза возникает зона термического влияния из двух участков: литого, состоящего из не удаленного с твердых поверхностей расплава металла, который образовался при резке, и с измененной структурой, в котором металл не расплавился, но в результате быстрого нагрева и охлажде-
ния в нем произошли рост или уменьшение зерен и другие структурные -пре вращения.
27
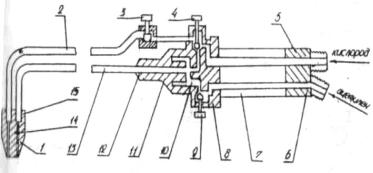
Плазменная резка металла имеет преимущества перед другими способами резки (кислородная, лазерная резка и резка водой с абразивом):
Преимущества перед кислородной резкой: более высокая скорость, минимальные деформации материала в результате термического воздействия.
Преимущества перед лазерной резкой: более низкая стоимость, равная или более высокая скорость резки, достаточно высокие качественные показатели.
Преимущества перед водоструйной резкой с абразивом: более высокая скорость, более низкая стоимость, низкий уровень загрязнения окружающей среды.
4.2 Универсальные резаки для резки металла
Резак представляет собой специальную горелку, при помощи которой осуществляется газовая резка. От обыкновенной сварочной горелки резак отличается тем, что в нем кроме устройства для смешения горючего газа с кислородом и мундштука для выхода горючей смеси в атмосферу имеется дополнительный мундштук для выхода в атмосферу струи режущего кислорода и устройство для подачи этого кислорода. Ручные резаки классифицируются по следующим признакам:
а) по роду горючего – на ацетиленовые, для газов – заменителей ацетилена, для жидких горючих;
б) по принципу действия – на инжекторные и безынжекторные; в) по области применения – на универсальные (применяемые для разде-
лительной резки толщин от5 до 300 мм) и специально применяемые для отдельных работ (для резки больших толщин, подводной резки и др.).
На рисунке 3.3 показан универсальный ацетилено-кислородный резак РР-53 инжекторного типа, предназначенный для резки стали толщиной от5 до 300 мм и работающий при давлении ацетилена в пределах 0,01–1,5 атм и давлении кислорода 3–14 атм.
Резак имеет рукоятку 7 и корпус 8, к которому при помощи гайки 11 присоединена смесительная камера 12 с инжектором 10. Кислород, поступающий через шланговый ниппель 5, идет по двум направлениям. Кислород подогревательного пламени регулируется вентилем4 и поступает в центральный канал инжектора 10.
Рисунок 3.3 – Схема ацетилено-кислородного резака
28

Попадая в смесительную камеру 12, струя кислорода создает разряжение в каналах, по которым через ниппель6 и вентиль 9 подсасывается ацетилен. Горючая смесь по трубке 13 идет в головку резака и, выходя через зазор между наружным 15 и внутренним 14 мундштуками, сгорает, образуя подогревательное пламя. Другая через вентиль 3 проходит в трубку 2 и поступает в головку 1 через центральный канал внутреннего мундштука 14, образуя струю кислорода.
Ацетилено-кислородными резаками можно разрезать металл толщиной от 3 до 300 мм, при скорости резания 550–80 мм/мин (соответственно). Примерная ширина разреза получается от 2 до 5 мм (соответственно).
Данные резаки могут работать и на заменителях ацетилена – природном газе и пропан-бутане. В этом случае необходимо изменять диаметры мундштуков инжектора.
Кроме ацетилена и газов-заменителей, для резки широко применяются жидкие горючие (бензин, керосин), которые, имея сравнительно невысокую стоимость и хорошие тепловые характеристики, оказываются в ряде случаев более экономичными горючими, чем ацетилен. При использовании жидких горючих для резки применяется специальная аппаратура, имеющая устройство для испарения горючего до поступления его в смесительную камеру резака.
На рисунке 3.4 показана схема керосинореза, предназначенного для резки стали толщиной 5–200 мм.
Рисунок 3.4 – Схема керосинореза
Кислород через вентиль 7 и инжектор 4 поступает в горелку 3, где смешивается с парами керосина. Керосин поступает через вентиль 8 в асбестовую набивку 9 испарителя, где испаряется в результате нагрева его пламенем вспомогательного мундштука 10. Горючая смесь выходит наружу через кольцевой зазор между наружным 1 и внутренним 2 мундштуками, образуя подогревающее пламя.
Режущий кислород проходит через вентиль6 по трубке 5 в центральный клапан мундштука 2.
Головка керосинореза имеет кольцевые мундштуки целевого типа. Резак снабжен рукояткой, в которой размечаются трубки для керосина и кислорода. Керосин подается в резак под давлением l,5–3 кгс/см2 из бачка емкостью 5 дм3, снабженного ручным насосом, манометром и запорным вентилем. В качестве горючего для керосинорезов рекомендуется применять только керосин, предна-
29