
Сварка
.pdfзначенный для освещения, запрещается использовать тракторный керосин, смесь керосина с бензином и бензин ввиду их повышенной взрывоопасности.
5 Методические указания по выполнению работы
Работа выполняется индивидуально каждым студентом. Необходимо ознакомиться с сущностью процесса воздушно-плазменной резки металлов, по рисунку и натурным образцам изучить устройство плазмотрона. По описанию, схемам и натурным образцам(в разрезах) ознакомиться с конструкциями аце- тилено-кислородного резака и керосинореза и изучить принцип их работы. Уяснить преимущества и недостатки одних конструкций перед другими.
6 Содержание отчета
1 В отчете описать сущность воздушно-плазменной резки металлов, нарисовать схему и расписать устройство плазмотрона, указать преимущества и недостатки воздушно-плазменной резки перед другими способами резки, указать наименования отдельных деталей резаков в соответствии с рисунками в руководстве.
2 Подготовить устно ответы на контрольные вопросы.
7 Контрольные вопросы
1Сущность воздушно-плазменной резки металлов.
2Устройство плазмотрона для воздушно-плазменной резки металлов.
3Преимущества и недостатки воздушно-плазменной резки металлов перед другими способами разделительной резки металлов
4Целесообразность применения жидких горючих при резке металлов.
5Отличие газового резака от газовой горелки.
6Назначение двух сопел в ацетилено-кислородном резаке.
7Назначение трех сопел в керосинорезе.
8Литература
1 Думов С. И. Технология электрической сварки плавлением. Л. : Машиностроение. Ленингр. отд-ние, 1987. 461 с.
2 Некрасов Ю. И. Справочник молодого газосварщика и газорезчика. М. :
Высш. шк., 1984. 168 с.
3 Петров Г. Л., Буров Н. Г., Абрамович В. Р. Технология и оборудование газопламенной обработки металлов. Л. : Машиностроение. Ленингр. отд-ние, 1978. 277 с.
4 Хренов К. К. Сварка, резка и пайка металлов. Изд. 4-е, стереотип. М. : Машиностроение, 1973. 408 с.
30
Лабораторная работа № 4
КОНТРОЛЬ КАЧЕСТВА СВАРНЫХ СОЕДИНЕНИЙ. ИСПЫТАНИЕ НЕПРОНИЦАЕМОСТИ СВАРНЫХ ШВОВ
1 Цель работы
Ознакомление с технологией, оборудованием и аппаратурой, предназначаемой для контроля непроницаемости сварных швов.
2 Задание
Ознакомиться с техникой испытания плотности сварных швов с помощью керосина, пневматическим методом, с помощью аммиака и вакуумированием.
3 Необходимое оборудование и материалы
1Керосин.
2Металлическая щетка.
3Мел.
4Кисточка.
5Сварной сосуд с наличием дефектов в швах.
6Компрессор.
7Сварная емкость с манометром до 5 атм.
8Мыло хозяйственное.
9Ветошь.
4 Основные теоретические сведения
4.1 Испытания сварных соединений с помощью керосина
Керосин имеет свойство проникать через мельчайшие капиллярные сосуды, обладая при этом высокой смачивающей способностью и сравнительно малой вязкостью, что обеспечивает большой эффект этого способа контроля.
Перед проведением испытания сварные швы очищают от шлака, ржавчины, масла и других загрязнений. Сварные швы покрывают меловым раствором (350–450 г молотого мела или каолина на 1 л воды), с той стороны, которая более доступна для осмотра. После высыхания мелового раствора другую сторону шва обильно смачивают керосином и выдерживают в течение определенного времени (20–50 мин). О наличии пор, свищей и других дефектов свидетельствуют жирные желтые точки или полоски керосина на меловом слое, которые с течением времени растворяются в пятна. Поэтому необходимо тщательно следить за появлением точек или полосок и своевременно отмечать границыде фектных участков. Дефектные участки шва вырубают и вновь переваривают, после чего производится повторное испытание керосином. Испытание керосином проводят на сосудах и резервуарах, которые работают без давления.
31
4.2 Проверка плотности сварных швов пневматическим способом
При пневматическом испытании в испытываемый резервуар нагнетается воздух до давления, указанного в технических условиях на испытание данного резервуара. Обычно давление не превышает 3 атм, так как при большем давлении и наличии дефектов может произойти разрыв всего сосуда. С наружной стороны сварные швы обмазывают мыльным раствором или каким-либо другим пенным индикатором. В местах неплотностей сварных швовобразуются мыльные пузыри. По количеству и интенсивности выделения мыльных пузырей можно судить о характере и величине дефекта.
Широкое применение пневматический способ контроля имеет при испытании сосудов малой емкости как наиболее удобный и доступный в заводских условиях. В этом случае испытуемый сосуд погружают в ванну с водой и -не плотности в сварных швах определяют по образованию пузырьков воздуха. При пневматическом испытании сосудов не разрешается производить обстукивание сварных швов, так как это может привести к разрыву сосуда.
4.3 Испытание плотности сварных швов аммиаком
При этом виде испытания в проверяемый сосуд нагнетают смесь воздуха с аммиаком (1 %) под давлением до 0,2 МПа. С внешней стороны сварные швы обматывают бумагой или бинтами, пропитанными в 5%-м растворе азотнокислой ртути или фенолфталеина. Аммиак, обладая высокой проницаемостью, пройдет через неплотности в сварном шве и оставит след на бумаге или бинте. По скорости появления на бинте пятен, их форме и размерам судят о характере и размерах дефекта.
Время проникновения аммиака зависит от толщины металла сварного изделия. Данный способ на производстве находит малое применение.
4.4 Контроль плотности сварных швов с помощью вакуум-аппаратов
Контроль плотности сварных швов с помощью вакуум-аппаратов производится в тех случаях, когда доступ к сварным швам возможен только с одной стороны (например, контроль плотности сварных швов в днище резервуара, газгольдеров и др.).
Сущность этого метода заключается в создании над испытываемым швом разряжения при помощи аппарата. Перед установкой вакуум-аппарата испытуемый шов обмазывается мыльным раствором. После включения вакуумнасоса вакуум-аппарат плотно прижимают к металлу. При создании внутри ва- куум-аппарата разряжения воздуха в дефектных местах шва появляются мыльные пузыри, хорошо видимые через органическое стекло. Дефектные участки отмечаются и подлежат исправлению (вырубке и повторной заварке).
5 Методические указания по выполнению работы
Перед выполнением лабораторной работы учебная группа делится на бригады по три человека.
32
В целях качественного выполнения лабораторной работы студенты должны быть ознакомлены с основными теоретическими положениями и применяемым оборудованием по данной теме.
Работа включает в себя проведение контроля следующими методами:
1Испытанием сварных швов с помощью керосина.
2Пневматическим испытанием сварного сосуда.
3Испытанием аммиаком.
4Вакуумированием.
Методы 1 и 2 выполняются на натурных сварных емкостях, с методами 3 и 4 студенты знакомятся теоретически (знакомство с макетами).
6 Содержание отчета
1 Дать эскизы проверяемых сосудов, указав основные габаритные размеры. Показать дефектные участки, обнаруженные при испытании сосудов на плотность (в виде таблиц произвольной формы).
2 Сделать заключение о пригодности проверяемых сосудов (по каждому в отдельности). В случае их непригодности перечислить выполнение работ, необходимых для устранения неплотностей в сварных швах.
3 Подготовить устно ответы на контрольные вопросы.
7 Контрольные вопросы
1 Методы испытания сварных швов и соединений на непроницаемость. 2 Сущность испытания плотности сварных швов с помощью керосина.
3 Область рационального применения контроля плотности сварных швов с помощью керосина.
4 Контроль керосином двухсторонних нахлесточных швов.
5 Сущность пневматического испытания крупногабаритных изделий.
6 Сущность пневматического испытания малогабаритных изделий.
7 Что указывает на наличие дефектов сварных швах при испытании аммиаком?
8 Сущность гидравлического испытания сварных соединений.
9 Сущность испытания сварных швов вакуумированием.
10 Область рационального применения вакуумирования.
8 Литература
1 Сварка в машиностроении: справочник : в 4 т. Т. 4 / под ред. Ю. Н. Зорина. М. : Машиностроение, 1979. 512 с.
2 Алешин Н. П., Щербинский В. Г. Контроль качества сварочных работ.
М. : Высш. шк., 1986. 207 с.
33

Лабораторная работа № 5
НЕРАЗРУШАЮЩИЕ МЕТОДЫ КОНТРОЛЯ ДЕТАЛЕЙ ПОДВИЖНОГО СОСТАВА. МАГНИТНЫЕ МЕТОДЫ КОНТРОЛЯ
1 Цель работы
Ознакомиться с сущностью магнитного метода контроля деталей -под вижного состава.
2 Задание
1 Ознакомиться с принципом работы магнитного дефектоскопа.
2 Произвести контроль магнитным методом деталей по заданию руководителя и дать заключение о годности их.
3 Необходимое оборудование и материалы
1Дефектоскоп на постоянных магнитах МД4-КМ.
2Магнитная суспензия В 103 С.
3Очиститель DR-60.
4Контрольные образцы с уровнями чувствительности по ГОСТ.
5Намагничивающая катушка ДКМ-5503-09.
6Порошок марки ПЖ4М.
7Детали подвижного состава, расположенные на специальном стенде.
4 Основные теоретические сведения
Магнитные методы контроля основаны на обнаружении магнитных потоков (полей) рассеяния, создаваемых несплошностями (различными дефектами или неоднородностями структуры) в намагниченных изделиях из ферромагнитных материалов.
Если намагнитить изделие и на пути потока расположить дефектный участок с пониженной магнитной проницаемостью, то он вызовет местное искажение потока рассеяния у поверхности металла (рисунке 5.1).
Рисунок 5.1 – Распределение магнитного потока в изделии:
а– качественный сварной шов; б – сварной шов с дефектами
Вкачестве железного порошка часто применяют тонко размолотую в шаровой мельнице железную окалину, возникающую на поверхности стали при ее горячей обработке. Для улучшения подвижности частиц во время контроля применяют суспензию из магнитного порошка, взболтанного в легком минеральном масле или керосине, и соответственно различают «сухой» или «мок-
34
рый» метод контроля магнитными порошками. «Сухой» способ в основном применяют для контроля деталей с грубообработанными или необработанными поверхностями.
При «сухом» способе магнитного контроля деталей после намагничивания их посыпают железным порошком, а при «мокром» – кистью обмазывают магнитной суспензией проверяемые поверхности. При отсутствии дефекта порошок или суспензия равномерно распределяются по поверхности детали, а при
наличии дефекта порошок скапливается над дефектом или скапливается по кромкам трещины. Дефектоскопирование производят в несколько приемов, поворачивая деталь несколько раз. При повторном скоплении порошка в одном и том же месте деталь бракуется.
Методом контроля магнитным порошком могут быть выявлены мелкие трещины, плохо выявляемые внешним осмотром, в особенности трещины в зоне влияния на сталях, чувствительных к термообработке. Могут быть выявлены также внутренние дефекты, лежащие у поверхности. Дефекты, лежащие на глубине более 2–3 мм от поверхности, методом магнитных порошков, как правило, не выявляются.
Методика магнитопорошкового способа включает следующие операции:
– подготовку поверхности перед контролем и очистку ее от загрязнений, окалины, следов шлака после сварки;
–подготовку суспензии, заключающуюся в интенсивном перемешивании магнитного порошка с транспортирующей жидкостью(при контроле мокрым способом);
–намагничивание контролируемого изделия;
–нанесение суспензии или порошка на поверхность контролируемого из-
делия;
–осмотр поверхности изделия и выявление мест, покрытых отложениями порошка (выявление дефектов);
–размагничивание.
Чувствительность магнитопорошкового метода зависит от ряда факторов: размера частиц порошка и способа его нанесения; напряженности приложенного намагничивающего поля; рода приложенного тока(постоянный или переменный); формы, размера, глубины залегания дефектов, а также от их ориентации относительно поверхности изделия и направления намагничивания и др.
Для магнитных суспензий применяют магнитный порошок с мелкими частицами.
Намагничивание постоянным или переменным током, а также «сухой» или «мокрый» метод нанесения порошка существенно не влияют на обнаружение поверхностных дефектов. Однако намагничивание постоянным током имеет преимущество перед намагничиванием переменным при обнаружении подповерхностных дефектов. Это объясняется тем, что постоянный ток создает магнитное поле, более глубоко проникающее в металл. Однако детали с толщиной стенки 2 мм не следует намагничивать постоянным током, так как такие детали невозможно размагнитить после контроля.
35
«Сухой» метод контроля имеет преимущество перед«мокрым» при обнаружении подповерхностных дeфeктов.
С увеличением напряженности приложенного поля возрастает чувствительность метода.
Если на поверхности контролируемого изделия имеются резкие переходы (например, усиление валика шва, чешуйчатость, подрезы) или крупные неровности, то магнитный порошок интенсивнее скапливается не над дефектами, а в местах переходов и углублений. Поэтому при контроле сварных швов с
усилением или грубой чешуйчатостью нельзя однозначно судить о наличии внутренних дефектов.
Намагничивание деталей в процессе их контроля может осуществляться несколькими способами:
–полюсным (продольным);
–циркулярным;
–комбинированным (таблица 5.1).
Полюсное, или продольное, намагничивание осуществляется с помощью электромагнитов или соленоидов, причем намагничивать контролируемую деталь можно в продольном или поперечном направлении.
При циркулярном намагничивании ток пропускается либо по контролируемой детали или через проводник(стержень), помещенный внутри полой детали. Циркулярным намагничиванием наиболее точно выявляют продольные дефекты в валах, осях и т. п.
Комбинированное намагничивание представляет собой различные сочетания полюсного и циркуляционного намагничивания. Неотъемлемой частью магнитопорошкового метода контроля является размагничивание деталей. Для этой цели применяют два основных способа:
1)Нагрев намагниченной детали до температуры Кюри, при которой ферримагнитные свойства материала пропадают. Однако этот способ применяют редко, так как нагрев детали может изменить механические свойства металла.
2)Размагничивание переменным магнитным полем с амплитудой, равномерно уменьшающейся от некоторой максимальной величины до нуля. В зависимости от материала размагничиваемого изделия, его размеров и формы применяют переменные магнитные поля различных частот (до 50 Гц).
36

Таблица 5.1 – Основные способы намагничивания
Способ |
|
Средство |
|
|
Графическая схема |
|
намагничивания |
|
намагничивания |
||||
|
|
|||||
Продольное (полюсное) |
|
|
|
|
|
|
|
Постоянным током |
|
|
|||
|
Электромагнитом |
|
|
|||
|
Соленоидом |
|
|
|
||
|
|
|
|
|
|
|
Циркулярное |
|
|
|
|
|
|
|
|
|
|
|
||
Комбинированное |
Пропусканием |
тока |
|
|
||
|
по детали и с помо- |
|
|
|||
|
щью |
электромагни- |
|
|
||
|
та |
|
|
|
|
|
|
Пропусканием |
двух |
|
|
||
|
(или более) сдвину- |
|
|
|||
|
тых |
по |
фазе |
токов, |
|
|
|
по детали во взаим- |
|
|
|||
|
но |
перпендикуляр- |
|
|
||
|
ных направлениях |
|
|
|||
|
Индуцированием |
|
|
|||
|
тока в детали и то- |
|
|
|||
|
ком, проходящим по |
|
|
|||
|
проводнику, |
поме- |
|
|
||
|
щенному |
в |
отвер- |
|
|
|
|
стие детали |
|
|
|
5 Методические указания по выполнению работы
Работа выполняется бригадой из трех студентов. В целях более качественного выполнения лабораторной работы перед ее выполнением необходимо ознакомиться с основными теоретическими сведениями по данной теме.
Перед выполнением работы необходимо убедиться в чистоте поверхностей проверяемых деталей, в отсутствии на них грязи, ржавчины и других за-
37
грязнений. При необходимости произвести зачистку. Перед намагничиванием деталей необходимо принять меры, обеспечивающие полный сбор железного порошка после проведения контроля.
6 Содержание отчета
1 Дать характеристику проверяемых деталей, указав на эскизах их основные размеры.
2 Дать заключение об их пригодности, в случае непригодности указать, какие необходимо выполнить операции для восстановления данных деталей.
3 Подготовить ответы на контрольные вопросы.
7 Контрольные вопросы
1 Сущность магнитной дефектоскопии деталей.
2 Порядок выполнения работ по магнитной дефектоскопии.
3 Состав суспензии при «мокром» способе магнитной дефектоскопии.
4 Области применения «сухого» и «мокрого» способа магнитного метода контроля деталей.
5 Применяемые способы магнитной дефектоскопии.
6 Области применения циркулярного намагничивания.
7 Области применения полюсного намагничивания деталей.
8 Методы размагничивания деталей после магнитной дефектоскопии.
9 Области применения магнитопорошкового способа контроля.
10 Можно ли применять металлические опилки цветных металлов при магнитном способе контроля?
11 Как проконтролировать магнитопорошковым методом контроля детали из цветных металлов?
8 Литература
1Хренов К. К. Сварка, резка и пайка металлов. Изд. 4-е, стереотип. М. : Машиностроение, 1973. 408 с.
2Алешин Н. П., Щербинский В. Г. Контроль качества сварочных работ.
М.: Высш. шк., 1986. 207 с.
38
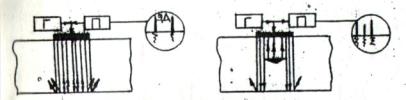
Лабораторная работа № 6
НЕРАЗРУШАЮЩИЕ МЕТОДЫ КОНТРОЛЯ ДЕТАЛЕЙ ПОДВИЖНОГО СОСТАВА. УЛЬТРАЗВУКОВОЙ МЕТОД КОНТРОЛЯ. ГАММАГРАФИРОВАНИЕ СВАРНЫХ ШВОВ
1 Цель работы
Ознакомиться с технологией, оборудованием и аппаратурой, предназначенной для контроля внутренних дефектов сварных швов.
2 Задание
Ознакомиться с техникой контроля качества сварных швов и соединений с помощью гаммаграфирования и ультразвука.
3 Необходимое оборудование и материалы
1Ультразвуковой дефектоскоп типа ДУК-13ИМ.
2Сварные образцы с наличием дефектов.
3Стальная щетка.
4Минеральное масло или мыльная пена.
5Миллиметровая линейка.
6Мел.
7Макет установки для гаммаграфирования сварных швов.
8Макет контейнера с ампулой.
4 Основные теоретические сведения
4.1 Контроль швов ультразвуком
Методы ультразвукового контроля основаны на исследовании процесса распространения упругих колебаний с частотой0,6–10 МГц в контролируемых изделиях. Ультразвук обладает способностью отражаться от поверхности разделяющей среды с различными акустическими свойствами. В практике контроля качества сварных соединений используют в основном эхо-импульсный метод, или метод эхолокации (рисунок 6.1).
Рисунок 6.1 – Схема ультразвукового контроля эхо-импульсным методом Г – генератор зондирующих импульсов П – приемник ЭД – экран дефектоскопа
39