
Гацков Прогрессивные технологии изготовления деталей 2011
.pdfсушат, измельчают и просеивают. Этот способ позволяет получить равномерную смесь при применении высокодисперсных, легких наполнителей. Наиболее подходящей для этого способа является суспензия марки 4ДВ.
Приготовление смесей из порошков проводят совместным помолом и перемешиванием порошка фторопласта с порошкообразным наполнителем при низких температурах (охлаждение жидким азотом), пропусканием исходных компонентов (порошка фторопласта и относительно легких наполнителей), смешанных с этиловым спиртом, сначала через лопастную мешалку, а затем через коллоидную мельницу конусного или ударно-кавитационного типа.
При использовании высокодисперсных наполнителей с насыпной массой, близкой к насыпной массе фторопласта-4, смесь готовят из предварительно просеянных через сито в 48меш порошков сухим смешиванием в смесителе с последующим просеиванием через сито с такими же или чуть большими ячейками. При недостаточной однородности смеси смешивание повторяют. Перед прессованием смесь подсушивают для удаления адсорбированной влаги при температуре 393–403 К в течение 1–2 ч. После предварительного прессования при давлении 20–60 МПа полученные заготовки высушивают при температуре 393–423 К, затем окончательно прессуют и спекают.
1.4. Исследования материалов, содержащих фторопласт
Разработка и совершенствование антифрикционных и уплотнительных материалов на основе фторопластов, связаны с выбором компонентов и исследованием влияния ряда факторов на их свойства. Выбор материалов компонентов основан на знании свойств, реализующихся при изготовлении композиционных материалов и в условиях их работы. Основные принципы выбора компонентов материалов приводятся в работе [3].
Применение фторопластов в качестве компонентов антифрикционных и уплотнительных материалов стало возможным в результате изучения проявления их свойств в различных условиях.
11
1.4.1. Исследования фторопластов
Исследованиям ПТФЭ и материалов, содержащих его, посвящено значительное количество работ как за рубежом, так и в нашей стране. Основные свойства фторопластов приведены в работах [3, 5].
Виспытаниях ряда полимеров выявлено минимальное трение ПТФЭ при низких скоростях скольжения по стали и в одноименном сочетании. При скоростях 0,1–0,3 мм/с коэффициент трения (без смазки) находится в пределах 0,04–0,05. Практически такой же коэффициент трения у ПТФЭ при низкой скорости скольжения в вакууме.
Сувеличением скорости скольжения до 0,5–2 м/с и выше коэффициент трения повышается и достигает значений 0,20–0,25. Максимального значения он достигает при скорости 5 м/с.
Сувеличением температуры коэффициент трения уменьшается,
илишь при температурах выше 593 К он увеличивается до относительно высоких значений.
Вработе [3] приводятся результаты исследований влияния скорости скольжения, температуры в контакте, давления, степени кристалличности и проникающего излучения на трение и изнашивание. Авторами получена обобщенная зависимость коэффициента
трения ПТФЭ от скорости скольжения и температуры: f = (1670,3–3,1)Т ·υ0,3 · 10–4 ,
где Т – температура, К; υ – скорость скольжения, см/с.
Из зависимостей (рис. 1.1) [3] видно увеличение коэффициентов трения при увеличении скоростей скольжения и уменьшение при увеличении температуры.
Зависимость получена в интервале температур 303–423 К и скоростей скольжения – 0,01–1 см/с.
В работе показано также изменение интенсивности изнашивания ПТФЭ в зависимости от температуры в контакте (рис. 1.2) при скорости скольжения 0,5 м/с и нагрузке 400 Н по схеме вал – плоский образец.
Испытания образцов ПТФЭ с разной степенью кристалличности показало, что с повышением степени кристалличности скорость
12
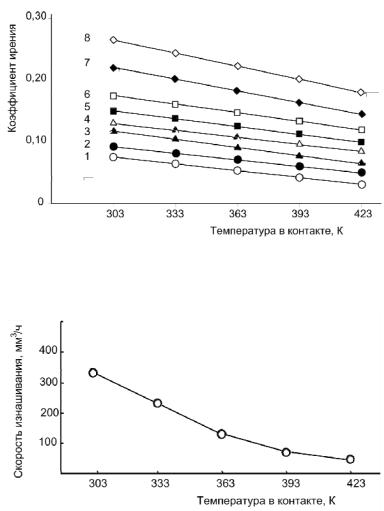
изнашивания ПТФЭ увеличивается, а коэффициент трения уменьшается. Такое влияние степени кристалличности на трение объясняется ухудшением большинства механических характеристик с увеличением степени кристалличности.
Рис. 1.1. Зависимость коэффициента трения ПТФЭ от температуры и скорости скольжения (см/с):
1– 0,01; 2 – 0,02; 3 – 0,04; 4 – 0,08; 5 – 0,16; 6 – 0,32; 7 – 0,6; 8 – 1,0
Рис. 1.2. Зависимость скорости изнашивания ПТФЭ от температуры
13
Сохранение в полимере значительного количества аморфной фазы обеспечивается резким охлаждением полимера, нагретого выше температуры плавления кристаллитов (600 К), в интервале
600–623 К.
При проведении испытаний на трение и изнашивание некоторых сополимеров ПТФЭ (4МБ, -40, -42В и -42Л) определена высокая износостойкость фторопласта 4МБ при более высоком коэффициенте трения, но стабильном при изменении температуры [3]. Однако увеличение скорости (>0,5 м/с) и нагрузки (>200 Н) в контакте приводили к повышению температуры (>350 К) и увеличению износа до катастрофического значения.
Фторопласты 4МБ и -40, стойкие к радиационному облучению [5], и представляют интерес для создания композиционных материалов для работы в условиях радиационного облучения.
1.4.2. Исследование наполненных фторопластов
Исследования наполненных фторопластов сводятся к выявлению влияния ряда факторов на их основные свойства с целью целенаправленного воздействия на них изменением влияющих факторов.
Для выявления влияния наполнителей и их содержания в материалах проведены сравнительные испытания большого количества композиций. Испытания проведены по двум схемам трения: вал – плоский образец и сфера – кольцевой образец. В табл. 1.1 [3] приведены результаты испытаний на трение и износ наиболее износостойких композиций ПТФЭ с оптимальными количествами наполнителей, полученные при скорости скольжения 0,5–1 м/с и нагрузке 400 Н по схеме трения вал – плоский образец.
Близкие к этим получены результаты и при испытании по схеме сфера – кольцевой образец.
Наиболее низкие коэффициенты трения и низкие установившиеся скорости изнашивания принадлежат композициям ПТФЭ со свинцом и бронзой. Однако у композиций со свинцом отмечается значительно больший начальный износ по сравнению с другими наполнителями.
14
Таблица 1.1
Износостойкость и коэффициенты трения материалов на основе ПТФЭ при установившейся скорости изнашивания
Наполнитель |
Содер- |
Интенсив- |
Удель- |
Относи- |
Коэф- |
|
жание, |
ность |
ный |
тельная |
фици- |
||
|
изнашива- |
износ, |
износо- |
ент |
||
|
% об. |
ния, мм3/ч |
мм3/ч Н |
стойкость |
трения |
|
Без наполнителя |
- |
200 |
0,4 |
1 |
0,19 |
|
Графит КАЗ |
20 |
0,34 |
0,000824 |
590 |
0,21 |
|
Дисульфид молиб- |
|
|
|
|
|
|
дена (частицы |
30 |
0,31 |
0,000775 |
645 |
0,20 |
|
5-30 мкм) |
||||||
|
|
|
|
|
||
Медь |
30 |
0,5 |
0,024 |
21 |
0,29 |
|
Алюминий |
30 |
6,6 |
0,0165 |
30 |
0,26 |
|
Титан |
20 |
0,77 |
0,00195 |
260 |
0,27 |
|
Молибден |
20 |
0,45 |
0,00113 |
444 |
0,24 |
|
Кобальт |
20 |
0,7 |
0,00175 |
285 |
0,16 |
|
Свинец |
15 |
0,10 |
0,00025 |
2000 |
0,15 |
|
Бронза Бр. ОЦС 5- |
20 |
0,14 |
0,00035 |
1430 |
0,14 |
|
4-4 |
||||||
|
|
|
|
|
||
Бронза Бр. ОФ 10-1 |
20 |
0,11 |
0,000275 |
1820 |
0,15 |
|
Ситалл |
20 |
0,28 |
0,00070 |
714 |
0,25 |
Для всех исследованных композиций, кроме композиций со свинцом, оптимальное количество наполнителя составляет 20–30 % по объему и в определенной степени зависит от схемы трения. Оптимальным количеством свинца в композиции является 15 %.
Выявлено также влияние дисперсности наполнителя на антифрикционные свойства материалов [3]. Анализ результатов испытаний композиций с графитом, дисульфидом молибдена и кремнезёмом разной дисперсности показал, что наибольший износ наблюдается у композиций с высокодисперсными наполнителями и для каждой концентрации наполнителя имеется оптимальный размер частиц, которому соответствует минимальный износ.
Влияние формы частиц на износостойкость образцов (на примере бронзы) объясняется количественным и качественным изменением приграничного объема раздела ПТФЭ – бронза.
15
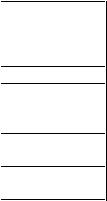
Проверкой эффекта повышения износостойкости композиций ПТФЭ со свинцом установлено его проявление в случае трения на воздухе и при повышенной температуре в контакте. Предполагается, что свинец и кислород способствуют образованию плёнки в контакте трения. Кислород облегчает деструкцию ПТФЭ при трении, а свинец оказывает каталитическое действие на образование фторидов железа.
Введение свинца в композиции вместе с другими наполнителями значительно повышает износостойкость материала и снижает коэффициент трения (табл. 1.2).
Таблица 1.2
Износостойкость и коэффициент трения композиций на основе ПТФЭ
Наполнитель и его |
Интенсивность |
Коэффициент |
Относительная |
|
концентрация, |
изнашивания, |
трения |
износостойкость |
|
(в процентах по |
мм3/ч |
|
|
|
объему) |
|
|
1 |
|
Без наполнителя |
200 |
0,19 |
||
Свинец (15) |
0,1 |
0,15 |
2000 |
|
Бронза (30) |
0,59 |
0,25 |
340 |
|
Графит (30) |
0,38 |
0,23 |
520 |
|
Бронза (15) + свинец |
0,06 |
0,13 |
3300 |
|
(15) |
||||
|
|
|
||
Графит (20) + |
0,084 |
0,15 |
2500 |
|
свинец (10) |
||||
|
|
|
Совершенствованием составов разработана композиция с интенсивностью износа в 4400 раз меньше, чем у ненаполненного ПТФЭ.
Поверхности стали и ПТФЭ обогащаются медью, на которой формируется металлополимерный слой в виде координационного соединения. Структура граничного слоя состоит из связанного с поверхностью кристаллической решетки стали слоя сервовитной плёнки меди и металлополимерного слоя, ориентированного в направлении трения.
16
Испытаниями композиций на основе фторопласта 4МБ, включающих фторопласт 4ДПТ и графит, показана возможность улучшения антифрикционных свойств и повышения износостойкости фторопласта 4МБ [3].
На свойства наполненного ПТФЭ оказывают влияние условия спекания. Образцы, спечённые под давлением, всегда имели более высокую плотность и износостойкость.
1.5. Материалы с металлическим каркасом
Материал, представляющий собой пористый каркас с введенным в поры фторопластом или фторопластом с наполнителями, применяют для подшипников и других трущихся деталей сложной формы, которые должны работать длительное время без замены с допустимыми большими износами (кольца узлов торцового уплотнения). Пористую заготовку (каркас) чаще всего изготовляют из высокооловянистой бронзы с частицами сферической или дендритной формы [3]. Для деталей, работающих в коррозионных средах, применяют металлофторопласты с пористым каркасом, изготовленным из порошков металлов или сплавов, коррозионностойких в конкретных средах.
Материал на основе пористого титана стоек к раствору азотной кислоты. Пористый каркас его изготовлен из титановых порошков ИМП-1 и ПХМ3 двусторонним прессованием под давлением 100– 150 МПа с последующим спеканием в вакууме в течение двух часов при температурах 1223–1273 К. Поры заполнены фторопластом путем многократной вакуумной пропитки суспензией фторопласта4Д с последующей сушкой и спеканием.
Известно использование для металлофторопластовых материалов пористых каркасов из железного порошка и нержавеющей стали.
Разработан материал, пористый каркас которого изготовлен прессованием и спеканием гранул 0,2–0,4мм, полученных прокаткой смеси порошков меди, свинца, марганца и бора в ленту, с последующим её дроблением. Спечённый пористый каркас заполнен графито-фторопластовой пастой.
17
Предложен материал, пористый каркас которого изготовлен из латунных проволочек длиной 5–10 мм прессованием при давлении 150–400МПа до пористости 55-60% и спеканием при температуре 1023-1223К в течение одного часа. Пористый каркас пропитан суспензией ПТФЭ с добавлением халькогенида и допрессован в процессе полимеризации при температуре 623-633К до получения беспористой заготовки.
К этой же категории материалов относят и пористые пропитанные ПТФЭ материалы на основе серебра и свинцовистой бронзы. Они содержат меньше ПТФЭ (15–40 % по объему), поэтому имеют хорошие механические свойства и теплопроводность, но меньшую износостойкость. Эти материалы нашли применение в электромеханике для работы при повышенных температурах и высоком вакууме.
Технологический процесс изготовления заготовок или деталей из материалов каркасного типа включает следующие общие операции:
1)прессование заготовок металлического каркаса в прессформах или свободная засыпка порошковой шихты в формы из огнеупорного материала;
2)спекание пористого каркаса в восстановительной атмосфере или вакууме;
3)заполнение пор суспензией ПТФЭ или суспензией ПТФЭ с наполнителями;
4)сушка заготовок при температуре 373 К;
5)термообработка для спекания ПТФЭ при температуре 648– 653 К;
6)калибрование.
1.6. Материалы с металлическим пористым каркасом на тонкой стальной подложке и пропитанным фторопластом
Материалы, представляющие собой металлический пористый каркас с заполненными фторопластами или фторопластами с наполнителями порами, обладают ценным комплексом свойств.
18
Нанесение тонкого слоя такого материала на конструкционную основу повышает его нагрузочную способность, износостойкость, уменьшает расход цветных металлов и фторопластов.
Наиболее прогрессивными являются ленточные металлополимерные материалы. Тонкий пористый металлический слой с заполненными чистым или наполненным фторопластом сообщающимися порами этих материалов нанесен на основу из стальной ленты.
Результаты разработки и создания технологий производства металлофторопластового ленточного материала приведены в работе [3]. Пористый слой из частиц оловянистой бронзы диаметром около 0,1 мм, толщиной 0,3–0,4 мм и объёмом сообщающихся пор 30–40 % наносят на основу из малоуглеродистой стали через тонкий слой меди. Стальная лента (основа) толщиной 0,1÷2,5 мм гальваническим методом покрывается медью, на этот слой наносится слой порошка бронзы, из которого спекается и одновременно припекается к ленте пористый слой. Поры заполняют фторопластом 4ДВ, содержащим 25 % по объёму дисульфида молибдена.
Материал работоспособен без смазки в температурном интервале от 73 до 550 К при нагрузках до 30 – 40 МПа при малом коэффициенте трения (0,04–0,22). Из него выпускают свёртные втулки и неразрезные подшипники скольжения.
Наиболее распространенный за рубежом ленточный материал марки «DU» выпускается фирмой «Глассир» (Великобритания), представляет собой стальную омеднённую ленту с пористым бронзовым слоем, заполненным смесью ПТФЭ со свинцом (20 % по объёму).
Сравнительные испытания на трение и износ фторопластового материала отечественного производства и материала марки «DU» при скорости 0,37 м/с и удельных нагрузках от 1,0 до 9,5 МПа показали практически одинаковые результаты. Коэффициент трения изменялся от 0,22 до 0,11.
Технология изготовления металлофторопластовых подшипников из ленточных материалов включает следующие основные операции:
1) покрытие поверхности стальной ленты слоем меди для облегчения припекания частиц бронзы;
19
2)нанесение на омеднённую поверхность стальной ленты дозированного слоя порошка бронзы;
3)спекание пористого слоя и одновременное его припекание к стальной основе в восстановительной атмосфере;
4)заполнение пор спечённого слоя бронзы фторопластом или фторопластом с наполнителями;
5)спекание фторопласта или фторопласта с наполнителями в порах и в поверхностном слое;
6)калибровка ленты;
7)покрытие электролитическим способом нерабочей стороны ленты слоем олова от коррозии;
8)изготовление подшипников штамповкой и механической обработкой.
Кроме перечисленных основных операций, процесс включает ряд других (всего около 20) операций, что сказывается на стоимости выпускаемой продукции.
1.7. Детали из комбинированного материала
Комбинированный материал чаще всего получают на финишных операциях процесса изготовления деталей, к которым предъявляются требования по износостойкости.
Комбинированные детали (детали с пористым покрытием из антифрикционных металлов, заполненным ПТФЭ) сочетают качества ленточного материала и спечённых пропитанных деталей.
Существуют различные методы формирования слоя из металлических порошков на поверхности стальных деталей [7]. Наиболее высокая прочность сцепления пористого слоя из металлических частиц порошков к стальной чистой или омеднённой поверхности детали была достигнута припеканием шихты в восстановительной атмосфере.
Для получения хорошего сцепления антифрикционного слоя с поверхностью основного металла толщина слоя меди должна находиться в пределах (10÷20)·10-6 м.
Для нанесения пористого слоя, подготовленные заготовки деталей из углеродистых конструкционных сталей покрывают слоем меди толщиной (12÷15)·10-6 м и слоем олова толщиной (1÷3)·10-6 м,
20