
Гацков Прогрессивные технологии изготовления деталей 2011
.pdfобезжиривают и устанавливают в подготовленные приспособления для засыпки и последующего спекания и припекания порошка бронзы. После этого приспособление загружают в контейнер, помещаемый для спекания порошка бронзы в печь с восстановительной атмосферой. Спекание ведется в течение 1÷1,5 ч при температуре 1073 К, а затем в течение 10÷60 мин при поднятой температуре до 1100÷1135 К. Отслаивание напечённого пористого слоя бронзы от стальной основы не допускается.
Пасту для заполнения пор слоя бронзы изготовляют из суспензии фторопласта-4ДВ и суспензии дисульфида молибдена МЭС-1-50. На пористый слой наносится паста слоем 0,3÷0,5 мм. Поры заготовок в зависимости от типа изготовляемых деталей заполняют пастой вкатыванием валками, впрессовыванием пасты в поры, протягиванием сквозь отверстие прошивками (дорнами) специальной формы. Для втулок с наружным рабочим слоем паста впрессовывается протягиванием втулки с нанесённым слоем пасты через фильеру.
После заполнения пор пастой заготовки сушат сначала при комнатной температуре (>2 ч), а затем при температуре 363 К (2÷2,5 ч).
Спекание наполненного фторопласта в заготовке производят в течение 30÷45 мин при температуре 645 К. Для придания заготовкам размеров деталей их калибруют на приспособлениях, конструктивно похожих на приспособления для вдавливания паст в поры антифрикционного слоя.
Для нанесения покрытий из металлических порошков на внутренние поверхности использовали центробежные силы, а нагрев для спекания осуществляли токами высокой частоты.
1.8. Изготовление материалов и деталей из смесей, содержащих фторопласты
При изготовлении деталей из металлополимерных материалов сохранение полимеров в материале обеспечивают снижением температуры спекания ниже температуры термодеструкции фторопласта или применением горячего прессования.
В Германии, Франции и Великобритании были разработаны способы спекания при пониженной температуре, заключающиеся в многократном циклическом изменении атмосферы спекания с
21
окислительной на восстановительную с длительностью цикла не более 600 с.
В Австрии предложена технология, позволяющая вводить ПТФЭ непосредственно в шихту и заключающаяся в подготовке шихты из порошков ПТФЭ, тугоплавкого металла (меди, бронзы, никеля, железа), легкоплавкого металла (олова, свинца, висмута или их сплавов), твердой смазки (дисульфида молибдена, графита), формировании изделий из шихты и их спекании при температуре ниже температуры термодеструкции ПТФЭ, но выше температуры плавления легкоплавкого металла.
Метод горячего прессования был разработан в 1955 году Филлиповым А.Н. Предложено спекать материалы с твердыми смазками под давлением 400–800 МПа при температурах 573–778 К в течение 5–300 с.
Для получения металлофторопластовых покрытий на основе различных металлических порошков разработан способ [7], использующий повышение температуры термодеструкции ПТФЭ с ростом давления прессования. Покрытия на изделиях получают спеканием с одновременным припеканием антифрикционного слоя из шихты, в состав которой входят порошки металлов и ПТФЭ, электроконтактным методом при температурах 973÷1073 К и давлениях 200÷300 МПа.
Активирование процесса спекания при горячем прессовании бронзофторопластовых материалов из шихты осуществлено применением высокодисперсных восстановленных порошков бронзы.
Способ изготовления металлофторопластовых материалов и деталей из шихты отличается простотой, но не обеспечивает высоких характеристик при содержании ПТФЭ более 30 % по объему. Хорошими антифрикционными свойствами и высокой износостойкостью материал обладает при содержании ПТФЭ в нём более 42 % по объему.
Контрольные вопросы
1. Каковы физические, химические и антифрикционные свойства каркасных и наполненных материалов?
22
2.Что характерно для каркасных антифрикционных материалов, содержащих фторопласт?
3.Наполненные фторопласты. Какие характеристики определяют их уплотняющую способность?
4.Какие основные способы изготовления деталей из материалов каркасного типа?
5.Какие детали (по назначению) изготовляют из наполненных фторопластов? Какие способы изготовления применяют при этом?
6.Что представляет собой комбинированный материал, содержащий фторопласт? Какие детали из него изготавливают?
7.Какими характеристиками должны обладать порошковые компоненты материалов, содержащих фторопласт?
23
2. СТРУКТУРЫ МАТЕРИАЛОВ, СОДЕРЖАЩИХ ФТОРОПЛАСТ
Структура металлофторопластовых материалов определяет их тип, физико-механические и антифрикционные свойства, износостойкость и стойкость в химически активных средах и формируется в зависимости от ряда факторов: формы и размеров частиц основообразующих порошков; количественного соотношения компонентов и соотношения размеров частиц порошков; способов изготовления и др.
Структура материалов каркасного типа, изготовляемых раздельным способом (изготовление каркаса и введение в его сообщающиеся поры фторопласта или фторопласта с наполнителем) и её формирование достаточно хорошо изучено и приводится авторами в работе [3].
Формирование металлического каркаса материалов, изготовляемых горячим прессованием непосредственно из смесей, более сложный процесс, на который первостепенное влияние оказывают технологические свойства металлических порошков, количество фторопласта в смеси, режимы и условия горячего прессования.
Ряд факторов качественно-количественного и технологического характера влияют и на формирование структур материалов наполненного типа.
2.1. Структуры материалов, изготовляемых горячим прессованием смесей порошковых компонентов
2.1.1. Формирование структур металлофторопластовых материалов
Условием формирования металлического каркаса при горячем прессовании смесей является наличие контактов между частицами металлических порошков и спекаемость их при температуре, ниже температуры термодеструкции фторопласта.
При этом условии может быть получен каркасный материал трех видов: с фторопластом в сообщающихся порах каркаса; с
24
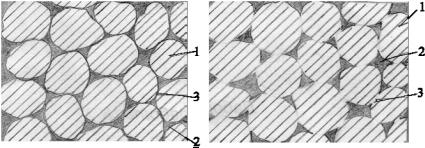
фторопластом в закрытых порах во всем объеме каркаса и с комбинированной структурой.
Структура с сообщающимся фторопластовым заполнением формируется при использовании металлических порошков с размерами частиц, при которых образуются сообщающиеся пространства, заполняемые фторопластом (рис. 2.1).
а б
Рис. 2.1. Схема структуры спрессованной заготовки до (а) и после (б) спекания
Количество фторопласта по объему должно соответствовать суммарному объему межчастичного пространства. Увеличение количества фторопласта 2 (рис. 2.1, а) вызовет уменьшение контактной поверхности 3 между металлическими частицами 1; уменьшение прочности каркаса из-за меньшего количества сформированных мостиков сварки 3 (рис. 2.2, б) в процессе спекания. Применение металлических порошков с частицами близкими по форме к шаровой создает благоприятные условия для их сближения при прессовании с выдавливанием фторопласта из зоны контакта.
Наиболее благоприятные условия для формирования металлического каркаса создаются равномерным распределением фторопласта, объемы частиц которого соизмеримы с объемами пор формируемого каркаса. Частицы металлических порошков будут сближаться в результате скольжения по границам частиц фторопласта и деформировать их в соответствии с формой образующих пор. При этом уменьшается вероятность попадания фторопласта в зону контактирования и механодеструкции его при сближении
25
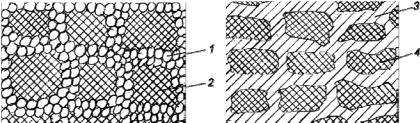
металлических частиц, увеличивается контактная поверхность, что способствует лучшему спеканию частиц в каркасе с сообщающимися порами, заполненными фторопластом.
Структура таких материалов идентична структуре материалов, получаемых изготовлением пористой металлической основы (каркаса) из порошков с размерами частиц 70–300 мкм с последующим введением фторопласта в поры основы и его спеканием.
Структура материала с фторопластом в закрытых порах показана на рис. 2.2. Материал с такой структурой представляет собой сформированный в процессе горячего прессования каркас с закрытыми порами, в которых находится фторопласт. Такая структура предопределяется при смешивании порошков. Размер и формы ячеек в каркасе материала формируются в соответствии с формой частиц фторопласта, изолированных при подготовке смесей, и возможной их деформации в процессе горячего прессования.
а б
Рис. 2.2. Схема структуры до (а) и после (б) нагружения и выдержки при температуре:
1 – частицы металлического порошка; 2 – частица фторопласта; 3 – металлический каркас; 4 – фторопласт
При сухом смешивании металлических порошков с порошками фторопластов поверхности частиц фторопластов покрываются более мелкими частицами металлических порошков, а более крупные металлические частицы покрываются более мелкими частицами фторопластов. Образуются гранулы с ядрами из крупных частиц порошков и оболочками из мелких порошков.
Формирование гранул из частиц порошков обусловлено адгезией их к поверхности других частиц в результате действия сил
26
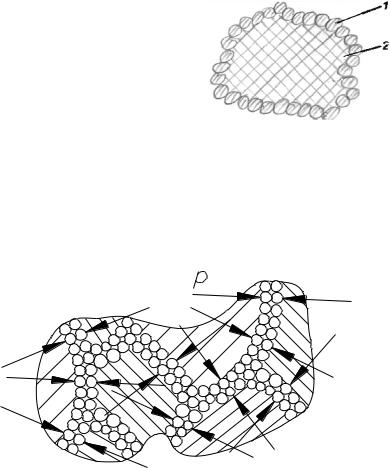
различного происхождения [3]. При |
|
||
значениях сил адгезии больших сил |
|
||
отрыва, частицы оболочек удержи- |
|
||
ваются на поверхностях более круп- |
|
||
ных частиц (рис. 2.3). |
|
|
|
Совокупность сформированных |
|
||
гранул |
представляет |
полученную |
|
при смешивании смесь из порошков. |
Рис. 2.3. Гранула из частиц |
||
Контактирование между гранулами в |
порошков: |
||
смеси, |
получаемыми |
в результате |
1 – частица оболочки; |
созданных условий для их формиро- |
2 – частица ядра |
||
|
вания, происходит по частицам оболочек. Формирование при горячем прессовании материалов из таких смесей сопровождается уплотнением частиц оболочки и развитием контактов между ними под действием сил, распределенных в объемах прессовок (рис. 2.4).
Рис. 2.4. Смесь из порошков фторопластов и металлов под давлением (р – равномерно распределенная сила)
В результате контакта гранул по оболочкам из металлических частиц, распределения давления по всему объему прессовок и уплотнения металлических оболочек создаются наивыгоднейшие условия формирования и спекания металлического каркаса материалов, содержащих фторопласт. Получают структуру, изображенную на рис. 2.2, б.
27
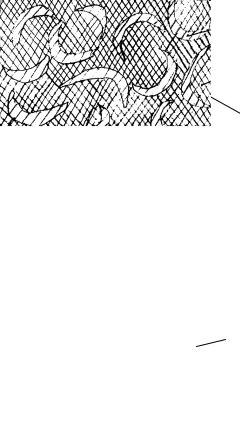
Прочность каркаса зависит от количества и соотношений фторопласта и металлических порошков, режимов и условий горячего прессования и спекаемости металлических порошков.
При контакте гранул с оболочками из частиц фторопласта при прессовании и спекании формируется структура с образованием по всему объему полимерной основы и равномерным регулярным распределением металлических частиц другого материала в её основе. Так получают наполненный фторопласт с ячейчатой основой, показанной на рис. 2.5.
1
2
Рис. 2.5. Структура наполненного фторопласта: 1 – фторопластовая основа; 2 – частицы наполнителя
При сухом смешивании крупных порошков фторопластов и мелких порошков наполнителей при их недостаточном количестве образуются гранулы с открытыми участками частиц фторопласта. В процессе горячего прессования материалов из таких смесей по открытым участкам спекаются частицы фторопласта с формированием основы и образованием в её объёме разорванной пространственной сетки из частиц наполнителя (рис. 2.6).
2
1
Рис. 2.6. Структуры с мелкими наполнителями:
1 – фторопластовая основа; 2 – фрагменты сетки из частиц наполнителя
28
Гомогенность смесей фторопластов с микроскопическими порошками наполнителей и соответствующую им структуру материалов обеспечивают размолом при низких температурах (ниже 173 К) и помолом в коллоидной мельнице с добавлением жидкого носителя и последующим его удалением.
2.2. Формирование структур многокомпонентных материалов, содержащих фторопласт
Введением в состав материалов антифрикционных порошков – добавок (графита, дисульфида молибдена и др.) в комплексе с фторопластом можно создать условия формирования металлического каркаса при горячем прессовании смесей, если учитывать взаимодействие частиц порошковых компонентов и порядок их смешивания.
При сухом смешивании крупного порошка фторопласта с мелкими порошками графита, дисульфида молибдена и других порош- ков-компонентов получают агрегаты частиц с оболочками из последних. Смешиванием полученной смеси с мелкими порошками металлов или сплавов формируют оболочки из металлических частиц. В результате такого последовательного смешивания получают смесь, агрегаты которой представляют фторопластовые час- тицы-ядра, покрытые двумя оболочками.
Контактирование агрегатов по наружным металлическим оболочкам в процессе горячего прессования способствует, как и при горячем прессовании двухкомпонентных смесей, спеканию металлического порошка в каркас. В объеме каркаса регулярно распределяется фторопласт с оболочкой из частиц-компонентов добавки (графита, дисульфида молибдена, свинца, оксида свинца и др.).
Для создания наивыгоднейших условий для фторопластовой основы многокомпонентных материалов наполненного типа нужно формировать агрегаты из частиц компонентов с наружной оболочкой из фторопластового порошка. Такие агрегаты получают последовательным смешиванием сначала крупных порошков наполнителя с мелкими порошками добавок, а затем смешиванием полученных агрегатов с мелкими порошками фторопластов.
29
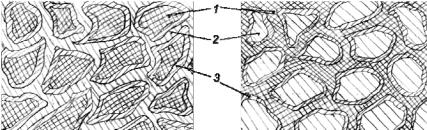
На рис. 2.7 приведены структуры материалов каркасного и наполненного типов, формируемые при наивыгоднейших условиях из фторопласта, металла и порошковых добавок.
а |
б |
Рис. 2.7. Материал каркасного (а) и наполненного (б) типов: 1 – фторопласт; 2 – металл; 3 – порошковые добавки
При подготовке смесей без учета размеров частиц компонентов и последовательности их смешивания создаются условия, ухудшающие формирование приведенных структур.
2.3. Предельные условия для формирования структур материалов, содержащих фторопласт
Целенаправленное управление формированием структур материалов возможно при знании предельных условий, при которых формируются структуры каркасных и наполненных типов материалов. Основными факторами, определяющими условия формирования структур материалов, являются размеры частиц порошковых компонентов, их соотношения и количественное содержание в материалах, режимы и порядок выполнения операций при изготовлении материалов и деталей из них.
2.3.1. Определение критических значений размеров частиц порошковых компонентов материалов
Критические значения размеров частиц, при которых прекращается образование агрегатов, определяют из условий движения
30