
Гацков Прогрессивные технологии изготовления деталей 2011
.pdfмкм) в виде разорванной по ячейкам объемной сетки (рис. 4.18, а), крупные (размеры частиц более 15÷30 мкм) в виде отдельных равномерно распределенных частиц (рис. 4.18, б).
4.2.5 Количественные соотношения порошковых компонентов в материалах
Оптимальные количественные соотношения порошковых компонентов в материалах каркасного и наполненного типов могут быть определены влиянием количества фторопласта в материалах на их служебные свойства (в зависимости от назначения). При этом следует учитывать и влияние других факторов: размеров частиц порошковых компонентов, способов и режимов процесса изготовления, условий горячего прессования.
Для оптимизации количественного соотношения порошковых компонентов неопровержимо знание предельных количественных соотношений, при которых формируются структуры каркасных и наполненных материалов. Предельные значения количества фторопласта в материалах могут быть определены, как указано, по зависимостям (2.12) и (2.15) или экспериментально. Количество фторопласта, при котором изменяется структура материалов, экспериментально определено зависимостями физикомеханических свойств от количества фторопласта в материалах при плотностях близких к плотностям компактных композиций.
На рис. 4.19 и 4.20 представлены зависимости предела прочности при срезе и удельного электрического сопротивления от количества фторопласта (в процентах по объему) и соотношения размеров частиц компонентов в материалах, изготовленных при обеспечении наивыгоднейших условий формирования металлического каркаса и структуры наполненного фторопласта.
Увеличение содержания фторопласта ведет к известному снижению механических характеристик. При 60–65 % фторопласта в материалах, изготовленных из смесей мелкого порошка бронзы и крупного порошка фторопласта (зависимость 1), и 50–55 % в материалах, изготовленных из смесей крупного порошка бронзы и мелкого порошка фторопласта (зависимость 2), изменяется характер
71

зависимостей предела прочности при срезе и удельного электрического сопротивления. В этих же интервалах процентного содержания фторопласта в материалах изменяется характер зависимостей твердости и предела прочности при сжатии.
Рис. 4.19. Зависимость предела прочности при срезе от количества фторопласта-4ДПТ в композициях:
1 – бронза (d = 1÷10 мкм), фторопласт (dф = 30÷160 мкм); 2 – бронза (d = 30÷160 мкм), фторопласт (dф = 1÷15 мкм)
Рис. 4.20. Зависимость удельного электрического сопротивления:
1– бронза (d = 1÷10 мкм), фторопласт (dф = 30÷160 мкм);
2– бронза (d = 30÷160 мкм), фторопласт (dф = 1÷15 мкм)
72
Такие изменения комплекса характеристик композиций могут быть в интервалах переходных значений количественных соотношений компонентов, входящих в них, в интервалах, в пределах которых перестает формироваться структура одного типа материалов
иначинается формирование структур другого типа.
4.3.Влияние оксидов металлов порошковых компонентов и технологических факторов на свойства материалов, содержащих фторопласт
4.3.1. Испытание образцов материалов
Образцы материалов каркасного типа с размерами D·h = 15·20 мм испытывали на твердость, прочность при сжатии и срезе и электросопротивление.
Образцы материалов наполненного типа с теми же размерами изготовляли из смесей порошков фторопласта-4ДПТ, 4ПФТ и металлических наполнителей.
Образцы с бронзовым наполнителем испытывали на твердость, прочность при срезе, на трение и износ. Образцы с никелевым наполнителем испытывали на ползучесть с постоянным давлением при сжатии 12,5 МПа в течение 8 ч. Ползучесть материала оценивали его податливостью (ξt), определяемой отношением величины относительной деформации образца за время t к испытываемому им напряжению:
ξt = |
|
lt |
–1 |
|
|
|
|
, МПа , |
(4.13) |
||
l0 |
σсж |
||||
|
|
|
где lt – величина пластической деформации за время t, мм; l0 – длина образца до испытаний, мм; σсж – сжимающее напряжение, МПа.
4.3.2Влияние содержания кислорода в порошке бронзы
иусловий горячего прессования на прочность материалов каркасного типа
Зависимостями 1-6 (рис. 4.21 и 4.22) показаны изменения пределов прочности при срезе материалов, содержащих 20 и 40 % фто-
73
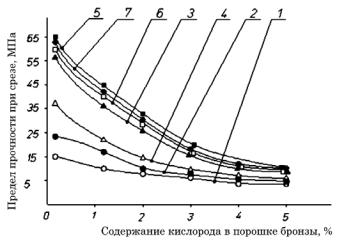
ропласта, изготовленных при давлениях горячего прессования 10, 120 и 400 МПа в водороде (Н2) и без водорода (на воздухе), от количества кислорода в исходном бронзовом порошке. Зависимостью 7 представлено изменение характеристики материалов, изготовленных при давлении 400 МПа в среде аргона.
Рис. 4.21. Зависимость предела прочности при срезе материала, содержащего 20% фторопласта:
1 – р = 10 МПа, в Н2; 2 – р = 10 МПа, без Н2; 3 – р = 120 МПа, в Н2;
4 – р = 120 МПа, без Н2; 5 – р = 400 МПа, в Н2; 6 – р = 400 МПа, без Н2; 7 – р = 400 МПа, в аргоне
Наиболее высокой прочностью при срезе обладают материалы, изготовленные из смесей порошков фторопласта и бронзы с содержанием кислорода менее 0,3 %. Увеличение количества кислорода в бронзовом порошке снижает прочность материала при всех условиях горячего прессования. Так, при увеличении кислорода до 2 %, значения пределов прочности при срезе уменьшаются в 2 и более раз, а увеличение количества кислорода до 4÷5 % ведет к снижению прочности до значений, которые имеют неспеченные материалы.
Снижение прочности материалов с увеличением кислорода в бронзовом порошке, образующего оксиды на поверхности частиц, является результатом разделения ювенильных поверхностей в контактах частиц оксидными пленками. С уменьшением контактной
74
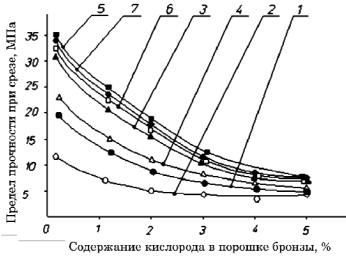
ювенильной поверхности уменьшается энергия связей, определяющая прочность металлического каркаса материала.
Рис. 4.22. Зависимость предела прочности при срезе материала, содержащего 40 % фторопласта:
1 – р = 10 МПа, в Н2; 2 – р = 10 МПа, без Н2; 3 – р = 120 МПа, в Н2; 4 – р = 120 МПа, без Н2; 5 – р = 400 МПа, в Н2; 6 – р = 400 МПа, без Н2; 7 – р = 400 МПа, в аргоне
Увеличение давления горячего прессования повышает прочность материалов при всех равных прочих условиях их изготовления. С увеличением содержания кислорода в порошке бронзы влияние давления становится несущественным (зависимости 1, 3, 5 и 2, 4, 6). Так, с увеличением давления с 10 до 120 МПа прочность при срезе материалов, изготовленных из смесей порошков бронзы, содержащих кислорода менее 0,3 % и фторопласта 20 и 40 %, повышается с 22,1 до 57,4 МПа и с 20,6 до 28,3 МПа соответственно.
Более высокие значения пределов прочности материалов обеспечиваются горячим прессованием смесей в среде водорода (восстановительной среде). С увеличением содержания кислорода в бронзовом порошке разница в значениях пределов прочности материалов, изготовленных в водороде и на воздухе, уменьшается или совсем исчезает (зависимости 1 и 2; 3 и 4; 5 и 6). Причем разница в
75
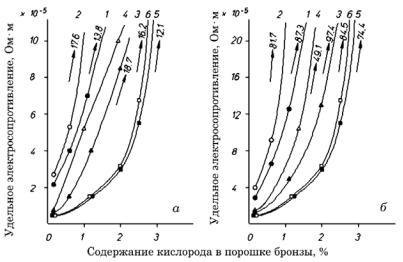
прочности зависит от давления горячего прессования, что определяется, по всей вероятности, плотностью формируемых структур, окислительными и восстановительными процессами, происходящими при изготовлении материалов. Сравнивая зависимости 5, 6 и 7 на рис. 4.21 и 4.22, можно утверждать, что при горячем прессовании в восстановительной среде оксиды металлов частично восстанавливаются, улучшаются условия спекания металлических частиц, а при горячем прессовании на воздухе металлические частицы дополнительно окисляются. На прочность материалов, изготовляемых горячим прессованием, влияют и продукты восстановления оксидов металлов и термодеструкции фторопласта как в отдельности каждый, так и во взаимодействии.
Прочность материала определяется качеством межчастичных связей. Изменение качества связей металлических частиц в процессе горячего прессования материалов из смесей порошков бронзы и фторопласта в зависимости от количественного содержания оксидов металлов и условий горячего прессования косвенно оценено изменением удельного электрического сопротивления (рис. 4.23).
Рис. 4.23. Зависимость удельного электросопротивления бронзофторопластового материала от содержания кислорода при 20 % (а) и 40 % (б) фторопласта:
1 – р = 10 МПа, в Н2; 2 – р = 10 МПа, без Н2; 3 – р = 120 МПа, в Н2; 4 – р = 120 МПа, без Н2; 5 – р = 400 МПа, в Н2; 6 – р = 400 МПа, без Н2
76
Удельное электросопротивление материалов увеличивается с увеличением содержания кислорода в исходном порошке бронзы. Это свидетельствует об уменьшении межчастичных ювенильных контактных поверхностей в результате разделения частиц оксидными пленками, имеющимися на поверхности.
С увеличением давления горячего прессования, уменьшается удельное электросопротивление (зависимости 1, 3, 5 и 2, 4, 6), что связано с увеличением суммарной ювенильной контактной поверхности или площади сечения, приведенного к компактному материалу, бронзового каркаса. Увеличение удельного электросопротивления материалов, изготовленных при высоком давлении горячего прессования смесей, в исходном порошке бронзы которых содержится более 0,2÷0,3 % кислорода, показывает на наличие в межчастичных контактах оксидных пленок, не разрушающихся полностью и при высоких давлениях (зависимости 5, 6).
Применение восстановительной среды снижает удельное электросопротивление, т.е. способствует увеличению суммарной площади контактов частиц по ювенильной поверхности, создает более благоприятные условия для спекания их в металлический каркас (зависимости 1 и 2; 3 и 4; 5 и 6). Наиболее высокая прочность бронзофторопластовых материалов каркасного типа, изготовляемых горячим прессованием, обеспечивается применением восстановленных высокодисперсных порошков бронзы (О2 ≤ 0,2 ÷ 0,3 %), восстановительной среды и высоких давлений горячего прессования.
4.3.3Влияние оксидов металлических наполнителей
иусловий горячего прессования на свойства материалов наполненного типа
Изменение предела прочности при срезе наполненных материалов, изготовленных при давлении горячего прессования 10 МПа, в зависимости от количества наполнителя (бронзы), кислорода в нем и условий горячего прессования графически иллюстрируется на рис. 4.24.
Увеличение количества кислорода в бронзовом порошке снижает прочность материалов (зависимости 1, 3 и 5). При этом изменяется и
77
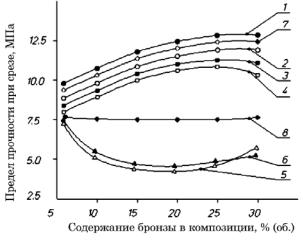
характер зависимостей предела прочности от содержания наполнителя. Так, с увеличением содержания кислорода с 0,3 до 6 % предел прочности при срезе материалов, содержащих 6 % наполнителя, уменьшается с 9,6 до 6,5 МПа.
Рис. 4.24. Зависимость предела прочности при срезе фторопласта, наполненного бронзой:
1 – О2 = 0,3 %, спекание в Н2; 2 – О2 = 0,3 %, без Н2; 3 – О2 = 1,6 %, в Н2; 4 – О2 = 1,6 %, без Н2; 5 – О2 = 6 %, в Н2; 6 – О2 = 6 %, без Н2;
7 – О2 = 0,3 %, в аргоне; 8 – О2 = 4 %, в Н2
При увеличении количества наполнителя при малом содержании кислорода предел прочности увеличивается (зависимости 1 и 3). При содержании кислорода в количестве 4 % изменения прочности практически нет во всем интервале содержания количества наполнителя в материалах, а при содержании кислорода в наполнителе более 4 % предел прочности при срезе с увеличением количества наполнителя уменьшается (зависимости 8 и 5).
Горячепрессованные в водороде материалы имеют более высокую прочность (зависимости 1, 3), чем материалы, изготовленные на воздухе (зависимости 2, 4). При увеличенном содержании кислорода в порошке бронзы (> 3 %) восстановительная среда не дает положительного эффекта, а материалы с наполнителем, содержащим кислорода более 5 %, изготовленные в водороде, имеют проч-
78
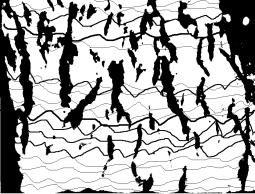
ность ниже, чем такие же материалы, изготовленные на воздухе. Это связано, вероятно, с процессом взаимодействия водорода с оксидами металла и появлением дефектов в приконтактных к частицам наполнителя слоях основы материалов в результате образования паров воды при температуре горячего прессования.
Это подтверждается дополнительными опытами, которые показали, что бронзовый окисленный порошок при температурах 570÷620 К (ниже температуры горячего прессования) восстанавливается водородом. О восстановлении оксидов бронзы в структуре материалов свидетельствует и изменение цвета частиц наполнителя при горячем прессовании образцов в водороде с черного до темнокрасного. Частицы восстановленного наполнителя (бронзы) при горячем прессовании материалов в водороде или аргоне цвета не изменяют.
В результате образования паров воды при восстановлении оксидов появляется возможность появления микро и макротрещин в материалах (рис. 4.25).
Рис. 4.25. Разрез образца материала с наполнителем, содержащим 8 % кислорода (×15)
Испытание образцов материалов на трение и износ показали, что наиболее высокой износостойкостью при скорости в контакте υ = 2 м/с и удельных нагрузках pк = 0,5 и 1 МПа обладают материалы, включающие восстановленный наполнитель и изготовленные в восстановительной среде (рис. 4.26, зависимость 1). С увеличением
79
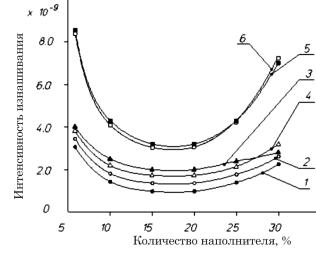
количества кислорода в наполнителе увеличивается интенсивность изнашивания, изменяется характер её зависимости от содержания наполнителя (зависимости 1, 3, 5).
Горячее прессование в водороде при наличии оксидов наполнителя не способствует повышению износостойкости материалов (зависимости 3, 4 и 5, 6).
Рис. 4.26. Зависимость интенсивности изнашивания фторопласта, наполненного бронзой:
1 – О2 = 0,3 %, в Н2; 2 – О2 = 0,3 %, без Н2; 3 – О2 = 1,6 %, в Н2; 4 – О2 = 1,6 %, без Н2; 5 – О2 = 6 %, в Н2; 6 – О2 = 6 %, без Н2
4.3.4 Влияние давления горячего прессования на свойства материалов, содержащих фторопласт
Выше отмечено влияние давления горячего прессования на свойства материалов. Представляет интерес определение характера влияния давления с целью оптимизации его значений. Характер изменения предела прочности при срезе, более выражено зависящего от структуры и энергии межчастичных связей и просто определяемого экспериментально, для материалов каркасного типа иллюстрируется графиками на рис. 4.27.
80