
Чернов Влияние легирования 2007
.pdfУстановлено, что крупные частицы Т-фазы и их скопления являются основной причиной ранней локализации деформации при растяжении образцов сплава Э635 и определяют стадию зарождения вязкого излома в шейке, понижая равномерную пластичность и сопротивление разрушению. Следовательно, способность сплава к устойчивой пластической деформации можно повысить, снижая количество и размер крупных частиц Т-фазы, например, уменьшением содержания железа в сплаве.
31
3. КОРРОЗИОННАЯ СТОЙКОСТЬ ЦИРКОНИЯ И ЕГО СПЛАВОВ
Наибольшее практическое значение имеют вопросы коррозионной стойкости Zr и его сплавов в воде высоких параметров, пароводяной смеси и паре. Для коррозии циркония и его сплавов в этих условиях характерны следующие основные черты.
1.Коррозия начинается с адсорбции молекул воды поверхностью циркония. Молекулы диссоциируют, образуя ионы кислорода и водорода. Кислород растворяется в металле, и при достижении оп-
ределенной концентрации на поверхности образуется оксид ZrO2. Водород также частично растворяется в металле. Многочисленные
исследования показали, что зародыши ZrO2 появляются вначале по границам, а затем внутри зерна преимущественно в плоскостях
(1010).
2.После образования пленки оксида образующиеся на его поверхности ионы кислорода диффундируют сквозь пленку, достигая металла и наращивая, таким образом, пленку оксида. Водород также диффундирует сквозь пленку, при этом доля поглощаемого сплавом водорода от образующегося существенно зависит от состава сплава. Перенос атомов Zr через пленку при этом незначителен и составляет лишь несколько процентов от количества продиффундировавших атомов кислорода.
3.Исследования, проведенные с помощью стабильного изото-
па 18О, а также ядерной реакции 17О(3Не, α)16О, показывают миграцию кислорода в глубинных слоях оксидной пленки по путям облегченной диффузии («короткозамкнутым», «линейным»), а также рост оксидной пленки в результате движения кислорода по кратчайшим диффузионным путям (границам зерен, микротрещинам, микропорам).
4. Если рост оксидной пленки осуществляется путем транспорта ионов кислорода по анионным вакансиям, то большое значение приобретает транспорт электронов через пленку для обеспечения ионизации кислорода на поверхности пленки. В этом отношении чрезвычайно важной является возможность транспорта электронов по короткозамкнутым путям, в качестве которых могут выступать участки с повышенной по сравнению с оксидом проводимостью (ме-
32
таллические включения, интерметаллиды). Обобщенная картина транспорта кислорода и электронов и реакций на границах раздела показана на рис. 3.1.
5. На первых этапах окисления при переходе ZrO2 из аморфного состояния в кристаллическое по мере роста кристаллов сначала образуется кубическая форма, затем тетрагональная, последняя переходит в моноклинную. Обычно первая стадия является кратковременной, и при длительном процессе окисления оксидная пленка в основной массе состоит из моноклинного оксида циркония. В начальный период она является плотной и хорошо сцепленной с металлической поверхностью. Иногда в структуре пленки встречаются метастабильные формы высокотемпературных модификаций (кубической или тетрагональной) оксида циркония.
Кинетика окисления циркония в зависимости от толщины пленки описывается различными уравнениями. В общем случае кинетику можно описать степенной функцией типа
∆m = Аτn, |
(3.1) |
где ∆m − привес; τ — время; А и п — постоянные. В зависимости от условий окисления, состава и подготовки поверхности образца показатель степени п меняется от 1/3 до 1, что указывает на то, что характер протекания процесса окисления меняется от кубического закона до линейного.
В начальный период показатель степени п = 0,5, что соответствует механизму диффузии кислорода через слой оксида циркония по анионным вакансиям.
После достижения толщины пленки около 1 мкм закон квадратичной параболы прироста толщины сменяется на закон кубической параболы, т.е. п ≈ 0,33.
Когда толщина пленки достигает примерно 3 мкм, окисление существенно ускоряется и уже подчиняется линейному закону, т.е. значение п = 1. Явление перехода к линейному закону получило название перелома (рис. 3.2), а толщина пленки, при которой наступает перелом − критической толщины.
33
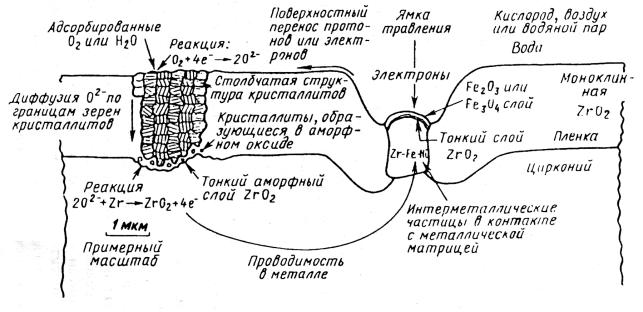
Рис. 3.1. Обобщенное схематическое изображение процессов, протекающих в оксидной пленке циркониевого сплава

Рис. 3.2. Кинетические кривые окисления Zr в воде при 370 °С:
1 − иодидный Zr с 0,007 % N; 2 − губчатый Zr с 0,003 % N;
3 − иодидный Zr с 0,003 % N
При достижении критической толщины в пленке образуются микропоры, продольные и поперечные микротрещины, через которые относительно свободно проникает вода (или пары воды), и лимитирующим фактором становится диффузия кислорода через весьма тонкий барьерный слой неповрежденного оксида циркония, прилегающего непосредственно к металлу. Толщина этого слоя остается постоянной (растет при этом внешний растрескавшийся слой), в результате чего поток диффундирующих через барьерный слой атомов остается постоянным и, следовательно, постоянна скорость роста общего слоя оксида.
С повышением температуры окисления критическая толщина пленки возрастает, а время до перелома уменьшается.
При переходе через перелом изменяется не только кинетика окисления, но и внешний вид и прочность пленки. До перелома пленка − черного цвета, блестящая, хорошо сцепленная с металлом. Она является эффективным барьером против коррозии, состав ее достехиометрический и отвечает формуле ZrO2-х, где х ≤ 0,05. После перелома цвет постепенно меняется от черного до белого, проходя через серые оттенки.
35
При толщине 50−60 мкм пленка становится рыхлой, осыпающейся. В некоторых случаях это принимается как исчерпание работоспособности изделия из циркониевого сплава. Состав белой пленки стехиометрический.
Коррозионная кинетика циркониевых сплавов чрезвычайно сильно зависит от многих факторов, основными из которых являются: наличие примесей и легирующих элементов; структурное состояние сплава, формирующееся на всех этапах обработки; качество
ичистота поверхности изделия; наличие и характер распределения остаточных напряжений; состав теплоносителя (примеси − содержание кислорода и водорода); параметры теплоносителя и его состояние (вода под давлением, пароводяная эмульсия); наличие и интенсивность нейтронного потока; различного рода механические воздействия, удары, трения и т.п.
Есть несколько гипотез, объясняющих наступление явление перелома. Чаще всего его связывают с напряжениями, возникающими в пленке вследствие разницы в удельных объемах металлического Zr и его оксида (отношение VZro2/VZr = 1,56). Напряжения в пленке
иметаллическом подслое возрастают с ростом толщины пленки. Кроме того, с ростом толщины уменьшается эластичность и увеличивается дефектность пленки. В конечном итоге, как полагают, это приводит к ее растрескиванию и наступлению перелома.
Явление перелома на кривой окисления иногда рассматривают с позиции возможности фрагментации оксидной пленки, образующейся на поверхности, так как считают, что плотная черная оксидная пленка, образующаяся в начальный период окисления на монокристалле циркония, также является монокристаллической, а белый оксид после перелома имеет поликристаллическое строение.
Вместе с тем существуют факты, говорящие о том, что прилегающий к металлу слой оксида является аморфным, и речь может идти скорее не о фрагментации, а о рекристаллизации оксидной пленки.
Во всяком случае, все рассмотренные механизмы обеспечивают наличие коротких «быстрых» каналов диффузии кислорода.
36
3.1. Влияние примесей и легирующих элементов на коррозионную стойкость циркония
Полагают, что наиболее высоким сопротивлением окислению в сухом кислороде обладает чистый цирконий. Однако коррозионная стойкость Zr в очень сильной степени зависит от содержания даже малых количеств примесей, что особенно проявляется при взаимодействии с водой или паром при повышенных температурах.
Растворенный в Zr кислород в количестве, не превышающем несколько десятых долей процента, незначительно влияет на скорость окисления циркония. С увеличением содержания кислорода скорость окисления заметно возрастает.
К наиболее вредным примесям относится азот. Азот, так же как и кислород, образует с Zr твердые растворы больших концентраций (при 500 °С в α-Zr растворяется до 3,7 % азота). Присутствие азота существенно уменьшает коррозионную стойкость Zr и его сплавов. При этом эффект присутствия азота реализуется как в случае растворения его в сплаве, так и в коррозионной среде. Представление о влиянии азота дает рис. 3.2, из которого следует, что увеличение содержания азота от 0,003 до 0,007 % снижает время до достижения перелома на порядок величины. Допустимым считается его содержание не более 0,002−0,003 %.Отрицательное влияние азота связывают с увеличением числа анионных вакансий при его растворении в оксиде ZrO2. С другой стороны, азот образует нитрид ZrN, нерастворимый в ZrO2 и потому располагающийся по границам зерен оксида. Это облегчает транспорт кислорода к поверхности Zr вследствие появления дополнительных путей проникновения кислорода к металлу.
К примесям, отрицательно влияющим на коррозионную стойкость, следует отнести и углерод, образующий с Zr карбид ZrC. Поэтому он действует аналогично азоту.
Следует отметить и отрицательную роль водорода. Водород в α-Zr растворяется незначительно, поэтому при выделении водорода по реакции
Zr + 2Н2О → ZrO2 + 2Н2 |
(3.2) |
37
он образует гидриды ZrH2 в приповерхностном слое. При этом защитная оксидная пленка при росте гидридов может быть повреждена и тем самым ускорены коррозионные процессы.
Отрицательная роль водорода может усилиться, если в приповерхностном слое имеются интерметаллиды или неметаллические включения, создающие условия для концентрирования водорода.
В воде и паре примеси и легирующие элементы следующим образом влияют на коррозионную стойкость циркония:
1)Н, N, С, О, Ti, U, Al, Са, Mg, Cl, Si, Pb, Mo, Zn, La, Ce, Ga, V, Be, Та ускоряют коррозию;
2)Sn, Sb, Fe, Cr, Ni ослабляют вредное действие элементов первой группы;
3)Hf, Cu, W нейтральны.
Существенно, что действие вредных примесей при одновременном их содержании в Zr суммируется; при этом может проявляться явление синергизма, т.е. усиления действия при одновременном содержании примесей. Это приводит к тому, что использование чистого Zr возможно только при таком низком содержании вредных примесей, достижение которого требует неоправданно больших усилий. Поэтому отрицательное влияние примесей стараются компенсировать соответствующим легированием.
При выборе легирующих элементов исходят из необходимости обеспечения комплекса свойств сплава, необходимого для выполнения своего функционального назначения, например, оболочки твэлов или канальные трубы. В этот комплекс свойств входят: обеспечение низкого сечения захвата тепловых нейтронов, обеспечение механической надежности (т.е. высокие прочностные свойства при достаточно высокой пластичности), отсутствие долгоживущих радиоактивных изотопов, обладающих жестким гамма-излучением и, наконец, высокая коррозионная стойкость.
Наиболее широко используют в практике следующие легирующие элементы: Nb, Sn, Fe, Cr, Cu, Mo, Ni. Если говорить строго в отношении очень чистого Zr, то все эти элементы ухудшают его коррозионную стойкость (рис. 3.3). Единственным элементом, практически не изменяющим коррозионную стойкость чистого Zr, является железо. Указанные элементы различным образом влияют также на поглощение сплавом водорода.
38
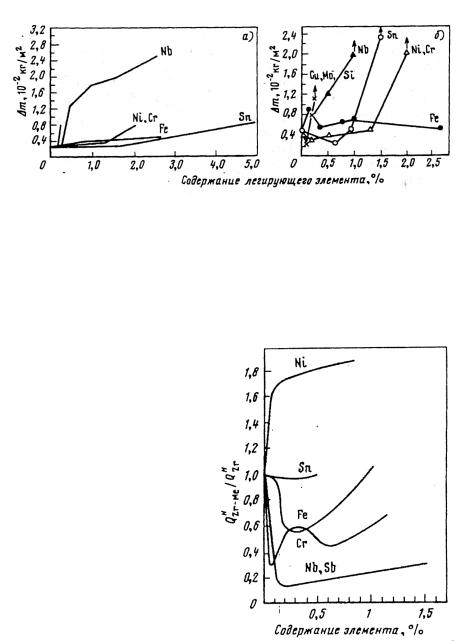
Рис. 3.3. Влияние легирующих элементов на коррозию Zr:
а − в воде (350 °С, 3000 ч); б − в паре (400 °С, 3000 ч)
На рис. 3.4 представлены отношения поглощения водорода сплавом к поглощению чистым цирконием. Видно, что Nb и Sb существенно уменьшают поглощение водорода; в наибольшей степени увеличивает поглощение водорода никель.
Рис. 3.4. Отношение количества поглощенного водорода бинарным сплавом Zr−Me к поглощению чистым цирконием
39
Если в отечественной практике реакторостроения получили распространение, главным образом, Zr−Nb-сплавы (см. табл. 2.1), то за рубежом основными являются сплавы, основанные на легировании оловом (циркалой-2 и циркалой-4). Это различие сложилось исторически на основании того, что отечественная циркониевая промышленность начинала развиваться на иодидном чистом Zr, в то время как западная базировалась на более загрязненном − губчатом цирконии.
Ниобий не только повышает прочностные характеристики циркониевых сплавов (см. раздел 1.2), но в небольших количествах (см. рис. 3.3, а) оказывает стабилизирующее действие на их коррозионную стойкость в воде, нейтрализуя влияние вредных примесей. Для сплавов, легированных до 5 % Nb, отмечается отсутствие резкого перелома на кривой окисления в области температур 300−500 °С; относительно слабо изменяя влияние N, Al и С, ниобий существенно блокирует отрицательное влияние Si, Ni, Fe.
С повышением содержания ниобия коррозионная стойкость сплавов Zr−Nb снижается, поэтому сплав Zr + 2,5 % Nb, обладая повышенными прочностными свойствами, менее коррозионностоек, чем сплав Zr + 1 % Nb. Полагают, что один из механизмов положительного влияния Nb заключается в том, что в процессе окисления в пленке ZrO2 возможно присутствие ниобия в виде Nb2O5 или 6ZrO2 Nb2O5, которые, располагаясь по границам кристаллитов ZrO2, способствует «залечиванию» дефектов защитной пленки.
Олово, введенное в небольших количествах в загрязненный Zr, повышает коррозионную стойкость сплавов в воде и паре (рис. 3.5). Смысл введения Sn двоякий: во-первых, Sn улучшает механические свойства и жаропрочность циркония (см. раздел 2); во-вторых, оно парализует вредное влияние примесей, особенно азота, однако повышение содержания Sn выше 0,5−1 % приводит вновь к увеличению привеса (см. рис. 3.5). Положительное влияние Sn на коррозионную стойкость Zr объясняется возможностью образования двухфазной пленки (ZrO2−SnO2), свойствами и характером распределения оксида SnO2, в частности расположением его на межкристаллитных границах оксида ZrO2. При этом между содержанием Sn и допустимой концентрацией N существует следующая зависимость:
40