
ток
.pdf1. Металлоре́жущий стано́к — станок, предназначенный для размерной обработки металлических заготовок путем снятия материала механическим способом.
Для осуществления процесса резания на металлорежущих станках необходимо обеспечить взаимосвязь формообразующих движений.
У металлорежущего станка имеется привод (механический, гидравлический, пневматический), с помощью которого обеспечивается передача движения рабочим органам: шпинделю, суппорту и т. п. Комплекс этих движений называется формообразующими движениями. Их классифицируют на два вида:
1) Основные движения (рабочие), которые предназначены непосредственно для осуществления процесса резания:
а) Главное движение Dг — осуществляется с максимальной скоростью. Может передаваться как заготовке (например в токарных станках) так и инструменту (напр. всверлильных, шлифовальных, фрезерных станках).
Характер движения: вращательный или поступательный. Характеризуется скоростью — v (м/с).
б) Движение подачи Ds — осуществляется с меньшей скоростью и так же может передаваться и заготовке и инструменту. Характер движения: вращательный, круговой, поступательный, прерывистый. Виды подач:
подача на ход, на двойной ход Sx. (мм/ход), Sдв.х. (мм/дв.ход);
подача на зуб Sz (мм/зуб);
подача на оборот So (мм/оборот);
минутная подача Sm (мм/мин).
2) Вспомогательные движения — способствуют осуществлению процесса резания, но не участвуют в нѐм непосредственно. Виды вспомогательных движений:
наладка станка;
задача режимов резания;
установка ограничителей хода в соответствии с размерами и конфигурациями заготовок;
управление станком в процессе работы;
установка заготовки, снятие готовой детали;
установка и смена инструмента и прочие.
СТАНКИ МЕТАЛЛОРЕЖУЩИЕ
машины для изготовления частей других машин в основном путем снятия с заготовки стружки режущим инструментом. Многое из того, что производится в результате человеческой деятельности в настоящее время, делается на металлорежущих станках или с помощью машин,
изготовленных с применением таких станков. Их спектр очень широк - от строгальных станков с ручным управлением до компьютеризованных и роботизованных систем. Более 500 разных типов существующих металлорежущих станков могут быть подразделены не менее чем на десять групп по характеру выполняемых работ и применяемому режущему инструменту: разрезные, токарные, сверлильные, фрезерные, шлифовальные, строгальные, зубообрабатывающие, протяжные, многопозиционные автоматические и др. Режущий инструмент того или иного вида (резец, фреза и т.п.) снимает с обрабатываемого (металлического, пластмассового, керамического) изделия стружку примерно так же, как это происходит при чистке картофеля ножом. Материал режущего инструмента должен быть значительно более твердым и прочным, чем материал обрабатываемой детали. Станок оборудуется механизмом, обычно состоящим из салазок, шпинделей, ходовых винтов и столов с поперечным и продольным перемещением, который позволяет перемещать инструмент относительно обрабатываемой детали. На станках с ручным управлением такое относительное перемещение задает оператор, пользуясь маховичками подачи для перемещения суппорта с резцедержателем. На станках с числовым программным управлением (ЧПУ) перемещения задаются программой последовательных команд, записанной в памяти компьютера. Программа включает и выключает приводные механизмы, например электродвигатели и гидроцилиндры, которые осуществляют подачу суппорта с автоматическим регулированием взаимного положения обрабатываемой детали и режущей кромки. Станки почти всех типов выпускаются как с ручным управлением, так и в варианте с ЧПУ. В механических мастерских бытового обслуживания, в любительских домашних, на машиностроительных заводах чаще всего встречаются разрезные, сверлильные, токарные, фрезерные и шлифовальные станки. Разрезные станки предназначены для разрезания и распиловки сортового проката (прутков, уголков, швеллеров, балок). Режущим инструментом служат сегментная дисковая пила, абразивные диски или ножовочное полотно. Главное движение - вращение диска или возвратнопоступательное движение ножовочного полотна. Автоматические разрезные станки работают на разных скоростях, оборудуются устройствами периодической подачи заготовки и системами двухкоординатного управления рабочим столом. Сверлильные станки, пожалуй, наиболее распространенный тип станков. Назначение - просверливание и обработка отверстий, главные движения - вращение и подача режущего инструмента (сверла). Сверло подается вручную или автоматически с переключением скорости подачи и вращения. В зависимости от материала детали и сверла, глубины сверления и диаметра отверстия частота вращения шпинделя может быть постоянной, имеющей ряд фиксированных значений или переменной.
2.
3. Классификация станков
Станки классифицируются по множеству признаков.
По классу точности металлорежущие станки классифицируются на пять классов:
(Н) Нормальной точности
(П) Повышенной точности
(В) Высокой точности
(А) Особо высокой точности
(С) Особо точные станки (мастер-станки)
Классификация металлорежущих станков по массе:
лѐгкие (< 1 т)
средние (1-10 т)
тяжѐлые (>10 т)
уникальные (>100 т)
Классификация металлорежущих станков по степени автоматизации:
ручные
полуавтоматы
автоматы
станки с ЧПУ
гибкие производственные системы
Классификация металлорежущих станков по степени специализации:
универсальные. Для изготовления широкой номенклатуры деталей малыми партиями. Используются в единичном и серийном производстве. Также используют при ремонтных работах.
специализированные. Для изготовления больших партий деталей одного типа. Используются в среднем и крупносерийном производстве
специальные. Для изготовления одной детали или детали одного типоразмера. Используются в крупносерийном и массовом производстве
4. Технико-экономические показатели станков
Одним из основных требований, которые предъявляются к современным металлорежущим станкам являются требования точности работы. Под термином точность работы станка понимается стабильность обеспечения станком получения заданной геометрической формы обрабатываемой детали, качества ее поверхности и точности размеров, определяющих основные параметры формы. Точность работы станка зависит от многих факторов, связанных с проектированием и изготовлением станка, правильности его эксплуатации и своевременного профилактического ремонта станка. Повышение точности станка достигается совершенствованием технологии изготовления его деталей и сборки его узлов, а сохранение первоначальной точности на длительное время в эксплуатационных условиях - тщательностью ухода и принудительным профилактическим осмотром. Производительность станка характеризуется различными показателями, из которых наиболее простым и наглядным является количество

обрабатываемых деталей в единицу времени. Этот показатель является относительным, так как на одном и том же станке при различной его настройке и наличии тех или иных приспособлений, особенно на станке универсального назначения, можно получить различные значения этого показателя. Для достижения максимальной производительности основное внимание должно быть обращено на сокращение вспомогательного времени, связанного со сменой заготовки, инструмента и управлением циклом обработки на станке. При прочих равных условиях многоинструментальная обработка является одним из способов повышения производительности. Максимальное сокращение вспомогательного времени и возможность применения многоинструментальной обработки обеспечивается автоматизацией цикла работы станка.
На универсальных станках с ручным управлением производительность достигается путем рационального и удобного расположения органов управления, применения преселективного управления, позволяющего сократить время и перестройку режимов обработки, путем предварительного, в процессе рабочего хода на предыдущей операции, набора нужного сочетания блочных колес коробок скоростей и подач, требуемых на следующей операции. Автоматизация управления металлорежущим станком является основным направлением развития современного станкостроения. Автоматизированные станки получили широкое внедрение не только в крупносерийном и массовом производстве, но начали широко применяться и при мелкосерийном и единичном производстве. Последнему способствует появившиеся в последнее время станки с программным управлением, которые, как указывалось выше, могут легко переналаживаться на обработку любой детали.
пособность станка работать безотказно и обеспечивать бесперебойную обработку деталей в заданных условиях эксплуатации называется надежностью. Степень надежности характеризуется так называемым коэффициентом надежности и определяется статистическим путем, как отношение фактического времени работы станка к запланированному
где Тпр — время простоя станка вследствие неисправностей;
Трп — время рабочего периода. Значение коэффициента надежности колеблется в пределах 0,8—0,98.
5. Технико-экономические показатели станков Под понятием долговечность подразумевается срок службы станка в
заданных условиях эксплуатации, когда затраты на восстановление его работоспособности экономически целесообразны. Большое значение для обеспечения нужного класса чистоты обрабатываемых деталей, стабильности работы станка, увеличения его надежности и долговечности является

жесткость конструкции станка, что позволяет исключить или снизить возможность появления в процессе работы станка вибраций нежелательной частоты. Виброустойчивость станка обеспечивается не только увеличением массы корпусных деталей, но также учетом возможных источников возникновения вибраций и создания рациональных конструкций. В этом направлении ведутся теоретические и опытные изыскания по разработке методов расчета динамической прочности конструкции станка.
Рациональная конструкция станка и отдельных его механизмов, в свете требований охраны труда, считается такой, которая обеспечивает бесшумность его работы. При конструировании нового станка необходимо обеспечивать условия «технологичности конструкции». Под этим понятием подразумевается соблюдение при проектировании ряда условий, обеспечивающих возможность применения при обработке и сборке деталей станка наиболее прогрессивных и экономичных технологических процессов.
Технологичность конструкции характеризуется: себестоимостью станка, как суммарного показателя трудоемкости и металлоемкости, конструкции; сроком оборачиваемости средств, связанным с длительностью производственного процесса изготовления станка, степенью унификации узлов станка и нормализацией его деталей.
6. Формообразование на станках. Методы образования производящих линий.
Любую поверхность можно представить, как след движения одной линии (образующей) по другой (направляющей). Обе эти линии называют производящими, причем образующая может быть направляющей и наоборот. Например, круговая цилиндрическая поверхность может быть представлена как след движения прямой линии по окружности (а) или след движения окружности по прямой (б).
Методы образования производящих линий При обработке поверхностей резанием в зависимости от вида режущего
инструмента и формы его режущей кромки используют четыре метода образования производящих линий: копирование, обкат, след и касание.
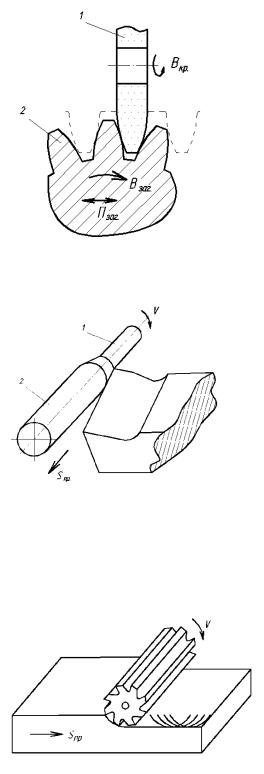
Метод копирования состоит в том, что форма производящей линии получается в виде копии (отпечатка) формы режущей кромки инструмента или его профиля. Другими словами, формы образуемой производящей линии и режущей кромки инструмента совпадают (идентичны). Этот метод применяют в тех случаях, когда для получения производящих линий используют фасонный режущий инструмент. В связи с тем, что форма образуемой производящей линии уже заложена непосредственно в режущем инструменте, для получения производящей линии методом
копирования не требуется никакого формообразующего движения.
Метод обката заключается в том, что форма образуемой производящей линии возникает в виде огибающей ряда последовательных положений, занимаемых режущей кромкой инструмента при обкатывании ею без скольжения образуемой линии. В процессе получения производящей линии либо режущая кромка инструмента катится по образуемой ею же линии, либо они взаимно обкатываются.
Другими словами, образуемая производящая линия и линия режущей кромки инструмента должны быть взаимоогибаемыми. Для получения производящей линии методом обката требуется одно, но всегда сложное формообразующее движение – движение обката (качения)
Метод следа состоит в том, что форма производящей линии получается в виде следа режущей точки (практически это весьма короткий обрезок линии) кромки инструмента при относительном движении заготовки и инструмента.
Поэтому для получения производящей линии методом следа необходимо одно простое или сложное формообразующее
движение (в зависимости от формы образуемой линии)
Метод касания заключается в том, что форма производящей линии возникает в виде огибающей мест касания множества режущих точек вращающегося инструмента в результате относительных движений оси вращения инструмента (шпинделя) и заготовки. Этот метод характерен при образовании производящих линий с участием таких инструментов, как фрезы
и шлифовальные круги, имеющих множество режущих точек, а следовательно, точек касания, формирующих траекторию образуемой производящей линии. Для получения производящей линии методом касания требуется два, реже три формообразующих движения.
7. Образование поверхностей
Процесс образования поверхностей резанием состоит в том, что за счет согласованных относительных движений заготовки и инструмента непрерывно образуются обе производящие линии при одновременном относительном их перемещении. Каждая производящая линия образуется одним из указанных выше четырех методов, поэтому образование поверхностей характеризуется сочетанием двух из четырех методов образования производящих линий, причем это может быть сочетание одноименных методов. Например, при образовании круговой цилиндрической поверхности с помощью резца обе производящие линии (окружность и прямая) получаются одним и тем же методом – методом следа. В общем случае число движений формообразования для создания поверхности определяется суммой движений формообразования необходимых для образования обеих производящих линий.
Во всех случаях общее число формообразующих движений при формировании поверхностей резанием практически не превышает трех. Поэтому металлорежущие станки бывают с одним, двумя или тремя движениями формообразования.
Так как в металлорежущих станках образование поверхностей осуществляется резанием, то все формообразующие движения станка одновременно являются движениями резания. Причем, если в станке имеется одно движение формообразования, то оно является движением скорости резания (обозначается ФV). Если в станке есть два движения формообразования, то одно из них, имеющее большую скорость, является движением скорости резания ФV, а второе, имеющее меньшую скорость, является движением подачи (обозначается ФS). Из трех движений формообразования в станке одно будет движением скорости резания ФV, имеющим наибольшую скорость, а два других – движениями подачи ФS1 и
ФS2.
Кинематическая группа
Каждое исполнительное движение в станках осуществляется кинематической группой, представляющей собой совокупность источника движения, исполнительного органа, кинематических связей и органов настроек, обеспечивающих требуемые параметры движения. Название кинематической группы аналогично названию создаваемого ею исполнительного движения. Например, группу, создающую формообразующее движение, называют
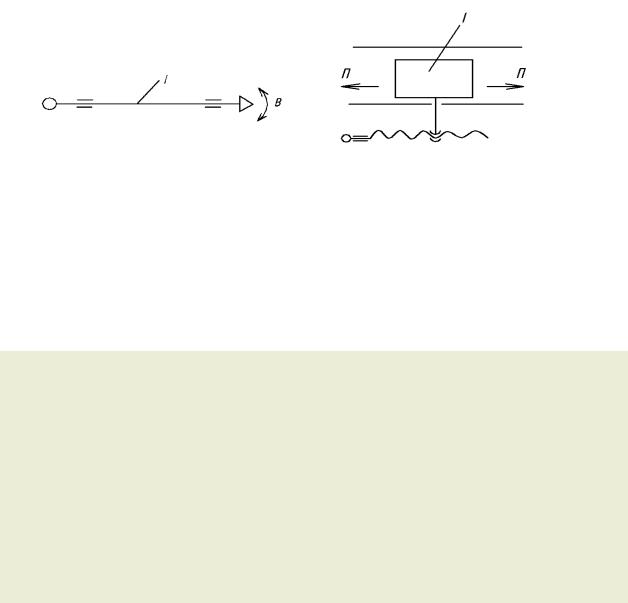
формообразующей группой и т.п. Структура кинематической группы может быть разнообразной и зависит от характера осуществляемого движения, числа исполнительных органов, потребности регулирования параметров движения.
Под исполнительными органами понимают подвижные конечные звенья кинематической группы, непосредственно участвующие в образовании траектории исполнительного движения. Исполнительные органы, осуществляющие абсолютное или относительное движение заготовки или режущего инструмента в процессе формообразования, называют рабочими. Например, рабочими органами являются такие звенья станка, как стол, шпиндель, суппорт, ползун и т.п.
В большинстве случаев исполнительные органы совершают вращательное или прямолинейное движение, т.е. являются подвижными звеньями вращательной или поступательной исполнительной кинематической пары.
а) вращательная б) поступательная В зависимости от числа исполнительных органов кинематические группы
делятся на простые и сложные. Простые группы имеют один исполнительный орган, а сложные – два и более исполнительных органов. Любая кинематическая группа включает в себя два качественно различных вида кинематической связи – внутреннюю и внешнюю.
8. Ступенчатое изменение чисел оборотов
Ступенчатое изменение чисел оборотов может быть осуществлено с помощью многоскоростного асинхронного электродвигателя, ступенчатых шкивов и коробок скоростей и подач с зубчатыми колесами.
Ступенчатошкивные передачи обычно с клиновыми ремнями применяются сравнительно редко, в основном при узком диапазоне изменения чисел оборотов малом числе ступеней и небольшой мощности, на небольших сверлильных станках, некоторых моделях фрезерных станков, настольных токарных.
Асинхронные многоскоростные двигатели применяются, как правило, совместно с коробками скоростей.
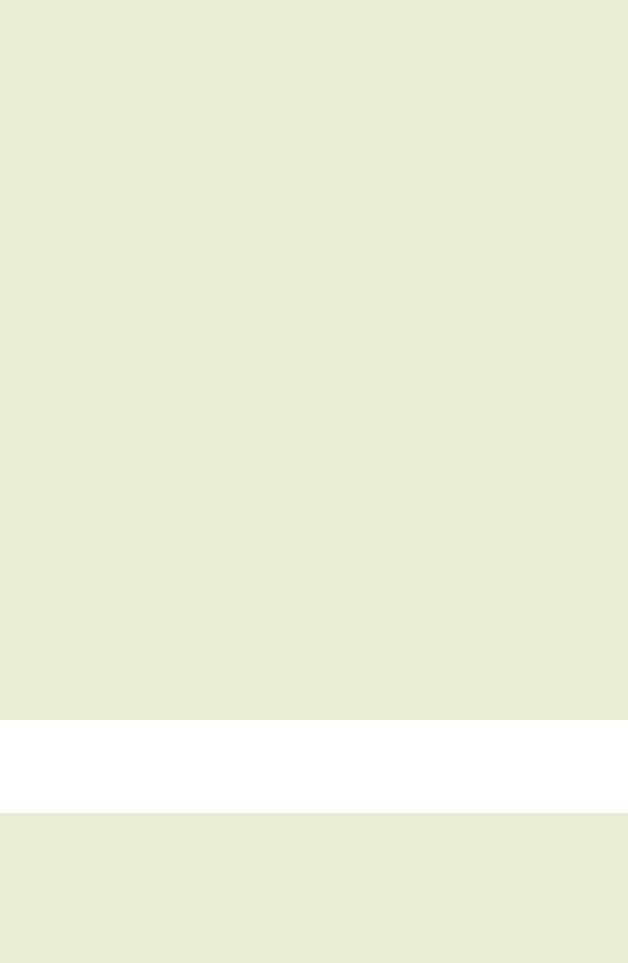
Наибольшим распространением пользуются коробки скоростей и подач с зубчатыми колесами.
В коробках скоростей и подач изменение чисел оборотов достигается поочередным включением различных зубчатых передач между валами коробок скоростей и подач. Для поочередного включения могут быть использованы либо сменные зубчатые колеса (рис. 16), либо постоянные зубчатые колеса (рис. 17), для включения которых используются те или иные из рассмотренных выше механизмов включения.
Прежде чем перейти к рассмотрению различных элементарных механизмов, заметим, что в станках передаточные отношения зубчатых колес рекомендуется ограничивать следующими значениями: для коробок скоростей imax = 2, imin = 1/4, для коробок подач imax= 2,5, imin = 1/5. В
отдельных случаях допускаются увеличение imax до 2,5—4. Применение передаточных отношений, выходящих за указанные пределы, приводит к увеличению габаритов механизма, снижению к.п.д. и появлению конструктивных трудностей при размещении механизмов переключения, увеличению шума.
Сменные шестерни 3 и 5 (рис. 16) устанавливаются на консольных концах валов 4 и 6 на шпонках или шлицах. Шестерни закрепляются с помощью быстросъемных шайб и гаек. Если исходить из указанных выше предельных передаточных отношений, то сменные шестерни могут обеспечить изменение чисел оборотов в диапазоне 10—12. При проектировании кожуха 2 необходимо предусмотреть возможность установки как ведомой, так и ведущей шестерен с наибольшим числом зубьев.
При постоянных поочередно включаемых шестернях, установленных на двух параллельных валах, диапазон изменения чисел оборотов находится в указанных для сменных шестерен пределах. Так как в большинстве случаев требуется значительно больший диапазон, то коробки скоростей и подач выполняются многоваловыми. Для включения различных зубчатых передач между двумя смежными валами используются элементарные механизмы
9. Бесступенчатое регулирование частот вращения
Для бесступенчатого изменения чисел оборотов преимущественно применяются различного рода фрикционные передачи. Лобовой фрикционный вариатор (рис. 18, а) состоит из двух дисков, ведомого 3 и ведущего1, между которыми расположен ролик 2, перемещающийся в осевом направлении. Диски 1 и 3 прижимаются к ролику 2. Передача момента происходит благодаря силам трения, возникающим в зоне контакта ролика с дисками. Передаточное отношение плавно изменяется от R1/r1 до R2/r2.
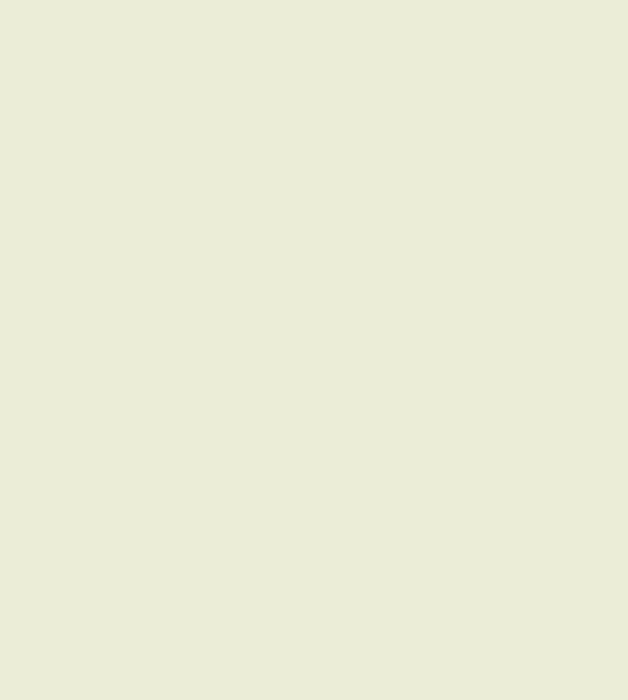
Диапазон изменения чисел оборотов находится в пределах 15. Окружная скорость точек диска вдоль линии контакта с роликом переменна, ролик же имеет среднюю окружную скорость, вследствие чего во всех других точках происходит скольжение, что приводит к сравнительно быстрому износу ролика и снижению к. п. д. передачи. Передаваемый крутящий момент определяется усилием прижима дисков к ролику и коэффициентом трения. Так как усилие прижима ограничено допускаемыми контактными напряжениями, то с целью увеличения передаваемого крутящего момента необходимо увеличивать длину линии контакта, что, в свою очередь, приводит к увеличению скольжения, а следовательно, износа и потерь. Поэтому вариаторы данного типа применяются при сравнительно небольшой мощности, в частности в станкостроении можно указать на механизм привода кулачково-распределительного вала токарно-револьверных автоматов, где этот механизм используется для изменения скорости вращения вала, а соответственно и величины подачи. В вариаторах с тороидными дисками 1 и 3 (рис. 18, б) вращение передается тремя роликами 2, что позволяет уменьшить их ширину, а следовательно, и скольжение, что способствует улучшению условий работы вариаторов, однако приводит к усложнению их конструкции.
Изменение чисел оборотов производится путем поворота роликов вокруг осей 0. При трех роликах конструкция механизмов крепления и поворота роликов становится довольно сложной. Диапазон изменения чисел оборотов находится в пределах 8.
В станкостроении данный вариатор используется весьма редко.
Разновидность тороидного вариатора, представленная на рис. 18, в, позволяет уменьшить скольжение до минимума, что выгодно отличает его от других форм вариаторов. Диапазон изменения чисел оборотов находится в пределах 4—8. Подобный вариатор был использован в приводе главного движения токарно-винторезного станка 1620, однако широкого применения он не получил.
12. Токарные станки.
Значительную долю станочного парка составляют станки токарной группы. По классификации токарные станки относятся к 1-й группе. Она включает девять типов станков, отличающихся по назначению, конструктивной компоновке, степени автоматизации и другим признакам.
На токарных станках обрабатывают детали типа валов, дисков и втулок, осуществляя обтачивание наружных цилиндрических поверхностей, торцов и уступов, прорезание канавок и отрезку, растачивание отверстий (цилиндрических, конических и фасонных), обтачивание конических и фасонных поверхностей, сверление, зенкерование и развертывание