
- •Теория литейных процессов
- •Тема 5.3. Управление кристаллизационными процессами
- •Раздел 6. ТЕПЛОВЫЕ ПРОЦЕССЫ. ЗАТВЕРДЕВАНИЕ ОТЛИВОК
- •Тема 6.1. Общие сведения о затвердевании
- •Тема 6.2. Инженерные методы расчета затвердевания отливок
- •Тема 7.3. Горячие трещины в отливках
- •Тема 7.4. Литейные напряжения в отливках
- •Содержание
116
−с уменьшением перепада до нуля показатель n стремится к единице, что отвечает линейному распределению температуры в сечении твердой корки.
Тема 6.2. Инженерные методы расчета затвердевания отливок
Отливка сложной конфигурации
Выше найдены закон затвердевания, линейная скорость затвердевания для плоской отливки.
Для отливок другой конфигурации – цилиндрической (полой и сплошной), шаровой (полой и сплошной) А. И. Вейником разработаны расчетные формулы, позволяющие вычислить параметры процесса затвердевания отливки в зависимости от теплофизических свойств формы и заливаемого металла [1].
На рис. 6.16 приведена зависимость показателя n от критерия N для отливок различной конфигурации, по которой можно определить значение показателя n, зная величину критерия N.
Если отливка обладает особо сложной конфигурацией, то ее не удается отнести ни к одному из трех перечисленных классов. В этих условиях отливку приходится мысленно расчленять на отдельные простые части, каждую из которых исследовать по методу эквивалентных отливок, при этом необходимо иметь в виду взаимное тепловое влияние выделенных элементов.
В случае, когда отдельные части сложной отливки различаются по толщине не очень значительно, взаимным влиянием тепловых элементов вполне можно пренебречь. Особенно это относится к третьей стадии процесса, когда происходит затвердевание металла. Следовательно, благодаря выделению теплоты кристаллизации температура различных
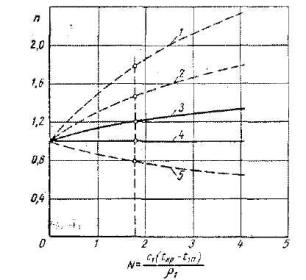
117
частей отливки естественно устанавливается на одном и том же уровне
tкр.
Рис. 6.16. Зависимость показателя n от критерия N для отливок раз-
личной конфигурации: 1 - полая шаровая отливка, затвердевающая из-
нутри; 2 - полая цилиндрическая отливка, затвердевающая изнутри;
3- плоская отливка; 4 - цилиндрическая отливка, затвердевающая снаружи; 5 - шаровая отливка, затвердевающая снаружи
Взаимное влияние (перетоки тепла) оказывается значительным, если сопряженные части отливки заметно различаются по своим массам (размерам). В этих условиях тонкие части отливки успевают затвердеть и начинается их дальнейшее охлаждение, в то время как толстые части продолжают затвердевать. Создаются большие разности температур, вследствие чего тонкие части начинают действовать на толстые как своеобразные холодильники. При расчете толстых частей приходится учитывать перетоки тепла в тонкие части.
118
Во всех случаях взаимное тепловое влияние различных частей отливки оказывается незначительным в начальный период процесса, когда толщина затвердевшей корки невелика. С ростом ξ взаимное влияние возрастает. Наибольшего значения оно достигает в период окончания затвердевания и в начальный период дальнейшего охлаждения твердой отливки.
Взаимное тепловое влияние выделенных частей зависит от термического сопротивления пограничных элементов, соединяющих эти части отливки. Термическое сопротивление этих участков рассматриваемых частей отливки возрастает с увеличением протяженности и уменьшением поперечного сечения этих участков, а также с уменьшением коэффициента теплопроводности материала. Вместе с тем огромную роль здесь играет интенсивность внешнего теплообмена: чем больше критерий Bi, тем меньше зона взаимного теплового влияния частей, тем больше относительное термическое сопротивление соседних участков, и наоборот, чем меньше критерий Bi, тем больше зона взаимного влияния частей. Например, при Bi1 >> 1 зона взаимного влияния частей не превышает толщину отливки, а при Bi1 << 1 эта зона стремится к бесконечности.
Роль интенсивности теплообмена в вопросе о характере теплового влияния различных частей сложной отливки непосредственно связана с вопросом о возможности использования приведенного размера отливки. При малых Bi1 относительное термическое сопротивление металла оказывается малым вследствие совершенного теплового взаимодействия различных частей отливки, поэтому с помощью приведенного размера R1 можно сравнивать отливки различной конфигурации. При больших Bi1 тепловая связь между удаленными частями отливки нарушается вследствие большого относительного термического сопротивления материа-
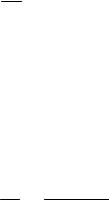
119
ла. Поэтому приведенный размер R1 уже не вполне точно отражает влияние конфигурации на процесс затвердевания отливки.
Приведенный размер отливки. На практике отливка часто имеет сложную конфигурацию, вследствие чего к ней невозможно применять формулы, выведенные в предыдущих разделах. Поэтому приходится прибегать к различным приближенным методам.
Наиболее простым методом сравнения процесса затвердевания отливок различной конфигурации является метод сопоставления приведенных размеров отливки. Такой метод часто используется на практике при расчете процесса затвердевания отливок и слитков.
Приведенный размер R1 представляет собой отношение объема V1 к площади F1 поверхности охлаждения отливки
R1 = V1 . F1
Легко видеть, что применение приведенного размера R1 по существу равноценно сравнению отливки данной конфигурации с неограниченной плоской отливкой определенной толщины. Действительно, для плоской отливки
R1 = V1 = 2Х1плF1 = X1пл ,
F1 2F1
где Х1пл – половина толщины плоской отливки.
Таким образом, приведенный размер неограниченной плоской отливки совпадает с половиной ее толщины. Для отливок другой конфигурации приведенный размер составляет долю от фактического размера отливки Х1. Например, для бесконечно длинной цилиндрической отливки радиуса Х1цил приведенный размер
R = |
V |
= |
πХ12цил |
l |
= |
1 |
X |
|
1 |
|
|
|
1цил , |
||||
|
|
|
|
|||||
1 |
F1 |
|
2πХ1цил l |
|
2 |
|
||
|
|
|
|
|
где l – длина отливки.
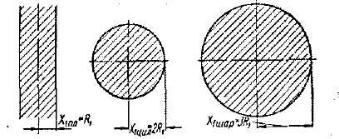
120
Для шаровой отливки радиуса Х1шар
|
V1 |
|
|
4 |
πХ13 |
шар |
|
1 |
|
R1 = |
= |
|
3 |
= |
X1шар . |
||||
|
|
|
|||||||
F |
|
4πХ 2 |
|
3 |
|||||
|
1 |
|
|
|
1 шар |
|
|
|
При одинаковых приведенных радиусах радиус цилиндрической отливки в 2 раза, а радиус шаровой отливки в 3 раза больше половины толщины плоской отливки (R1 = Х1 пл). Следовательно, согласно методу сравнения приведенных размеров получается, что цилиндрическая отливка двойной толщины, а шаровая отливка тройной толщины должны обладать одинаковым с плоской стенкой временем полного затвердевания. Это происходит только в условиях их охлаждения, при которых Bi1 << 1. Здесь же отметим, что на процесс охлаждения отливки оказывают влияние не только V1 и F1, но также и термическое сопротивление материала. Вследствие этого, в общем случае из двух отливок с одинаковыми приведенными размерами большим временем затвердевания (при прочих равных условиях) будет обладать отливка, обладающая большей фактической толщиной.
Рис. 6.17. Сравнительные размеры плоской, цилиндрической и шаровой отливок, обладающих одинаковыми приведенными размерами
Например, при одинаковых приведенных размерах цилиндрическая отливка имеет в 2 раза, а шаровая – в 3 раза больший поперечник, чем
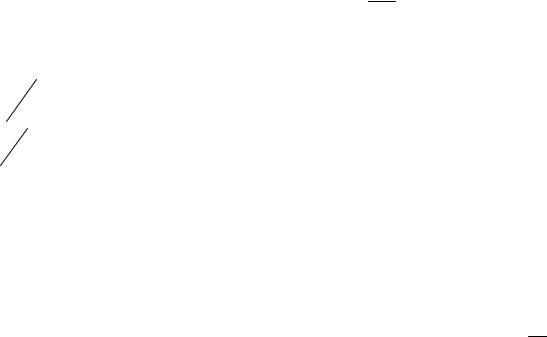
121
плоская (рис. 6.17). У этих отливок соответственно больше и термиче-
Х1
ское сопротивление, характеризуемое отношением λ1 .
С уменьшением интенсивности охлаждения (с уменьшением крите-
|
X1 |
λ |
|
рия Bi = |
|
||
|
1 |
, представляющего собой отношение термического со- |
|
|
|
||
|
1α1 |
противления отливки к термическому сопротивлению на поверхности), роль термического сопротивления отливки в пределе Bi << 1 сводится на нет. В этих условиях (нулевое термическое сопротивление равносильно бесконечно большой термической проводимости) фактически
протяженность отливки перестает влиять на процесс. Величина R1 = V1
F1
оказывается вполне пригодной для сравнения процесса затвердевания отливок различной конфигурации.
В реальных условиях относительно малая интенсивность охлаждения отливки встречается не очень часто. В других случаях (при Bi ≈ 1 и Bi >> 1) сравнение процесса затвердевания отливок различной конфигурации посредством величины R1 уже не может дать положительных результатов. Особенно это относится к слиткам, которые, как правило, охлаждаются со значительной интенсивностью.
При охлаждении отливки в неметаллической форме можно считать, что металл затвердевает с относительно малой интенсивностью по отношению к интенсивности прогрева формы, в которой распространение тепла происходит с большой интенсивностью из-за значительного термического сопротивления формы по сравнению с таковым для отливки. В результате ведущим процессом оказывается процесс прогрева формы, вследствие чего решающее значение приобретает не приведенный размер R1, а приведенный размер формы

122
R2 = V2 , F2
где V2 – объем формы.
При изменении конфигурации отливки меняется конфигурация внутренней поверхности формы. Это приводит к изменению величины R2 и термического сопротивления формы при бесконечно большой интенсивности её прогрева (Bi2 >> 1). Это обстоятельство оказывает существенное влияние на затвердевание металла, вследствие чего сравнение процесса охлаждения отливок различной конфигурации с помощью параметра R1 приводит к недостаточно точным результатам. Это подтверждается данными Б. Б. Гуляева, свидетельствующими о том, что при одинаковой толщине отливки Х1 (плоской, цилиндрической и шаровой)
1 1
приведенные размеры отливок соответствуют 1; 2 ; 3 , а время затвер-
девания оказалось пропорционально числам 1; 0,76; 0,47. Если бы величина R1 в точности отражала влияние конфигурации на процесс, то время затвердевания рассматриваемых отливок изменялось бы в том же соотношении, что и приведенные размеры. Эти данные подтверждают высказанную ранее мысль о серьезном влиянии термического сопротивления отливки и формы на процесс затвердевания металла.
Тонкая отливка. При значительной интенсивности теплообмена (Bi1≈1, Bi1>>1) на процесс затвердевания важное влияние оказывает внутреннее термическое сопротивление отливки. В этих условиях задачу также можно свести к рассмотрению процесса затвердевания плоской отливки. Однако при этом приходится накладывать известные ограничения на выбор исходной конфигурации отливки.
При любой интенсивности охлаждения отливку можно рассчитать как плоскую стенку во всех случаях, когда радиус Х0 кривизны ее внут-
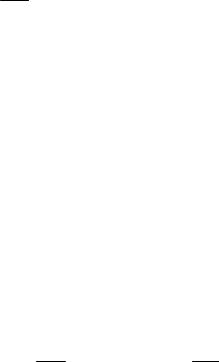
123
ренней поверхности много больше половины толщины Х1 отливки, т. е. когда соблюдается требование:
Х1 <<1.
Х0
Начальный период затвердевания. Весьма интересно, что понятие тонкой (в термическом смысле) отливки можно применять не только ко всей отливке в целом, когда ее толщина Х1 мала по сравнению с радиусом Х0 кривизны. Это понятие справедливо также для отливки произвольной конфигурации при охлаждении металла с любой интенсивностью. Однако при этом приходится ограничиваться рассмотрением лишь корки начального периода затвердевания, когда толщина ξ образовавшейся корки металла мала в сравнении с радиусом Х0 кривизны отливки. Соответствующее условие имеет вид
δ = Хξ0 <<1 или δ = Хξ1 <<1.
Отмеченное свойство процесса затвердевания отливки имеет практическое значение: при расчете начального периода затвердевания можно пользоваться простейшими формулами, выведенными для плоской стенки. Эти формулы пригодны для отливок любой конфигурации.
Справедливость высказанных соображений легко проверить путем анализа формул, выведенных для плоской, цилиндрической (сплошной и полой) и шаровой (сплошной и полой) отливок. Это можно сделать на примере большой (Bi1>>1), средней (Bi1≈1) и малой (Bi1<<1) интенсивно-
сти теплообмена, если пренебречь высшими степенями δ, так как при-
нимается δ<<1. Для плоской цилиндрической и шаровой отливок (Bi1 >> 1 или Bi0>>1) находим
Fo – Fo2 = A2 (δ2 − δ22),
|
|
1 |
1 |
|
|
|
где |
А2 = В5 = С5 = С6 = Е6 = |
|
L + |
|
|
|
|
n +1 |
|||||
|
2n |
. |
124
Для тех же отливок при средней (Bi1 ≈ 1 или Bi0 ≈ 1) и малой (Bi1 <<1 или Bi0<<1) интенсивности охлаждения получаем
Fo − Fo2 = |
L |
(δ −δ2 ) или Fo − Fo2 = |
L |
(δ −δ2 ). |
Bi |
|
|||
|
|
Bi0 |
Как видим, формулы, выведенные для цилиндрических и шаровых отливок, совпадают с формулами, выведенными для плоской отливки. При большой интенсивности охлаждения для любой отливки время τ связано с толщиной ξ корки квадратичной зависимостью. При средней и малой интенсивности охлаждения τ и ξ связаны линейной зависимо-
стью. При средней интенсивности охлаждения с ростом ξ закон затвердевания постоянно изменяется, так как в расчетных формулах важное значение приобретают слагаемые, содержащие ξ2. Разумеется, все это справедливо только для малых значений Fo, когда величина δ еще не очень большая.
Метод эквивалентных отливок
Во всех перечисленных выше случаях отливка более или менее сложной конфигурации условно приводится (приравнивается) к плоской стенке. Недостатком описанных методов расчета процесса затвердевания металла является их ограниченность: в первом случае (с помощью приведенного размера R1) влияние конфигурации может быть учтено лишь при малой интенсивности теплообмена (Bi<<1), во втором случае (тонкая отливка) интенсивность теплообмена может быть любой, но толщина отливки должна быть небольшой в сравнении с радиусом кривизны, в третьем случае конфигурация отливки и интенсивность теплообмена могут быть произвольными, но толщина затвердевшей корки должна быть малой (начальный период затвердевания). Все эти методы могут быть с успехом использованы на практике в соответствующих слу-
125
чаях литья, однако многие задачи такими методами решены быть не могут.
Рассмотрим еще один приближенный метод расчета, который позволяет исследовать процесс затвердевания отливки неправильной (неклассической) конфигурации при любой интенсивности теплообмена. В этом методе совокупность отливок различной конфигурации разделяется на три класса, которые отличаются относительными размерами в трех взаимно-перпендикулярных направлениях. Этот метод подробно рассмотрен в работах А.И. Вейника.
Физическое существо предлагаемого метода заключается в том, что предполагается постоянство общего теплового потока, проходящего через поверхности при изменении условий охлаждения на некотором участке поверхности твердого тела. Тогда вдали от рассматриваемого участка поверхности, на котором изменяются условия охлаждения, температурное поле тела остается неизмененным. Этот результат был получен экспериментально и обоснован теоретически. Отмеченный эффект стабильности температурного поля по отношению к местным возмущениям был назван принципом стабильности теплового потока. На основе этого принципа теплового потока решается поставленная задача.
Предположим, что местное возмущение температурного поля тела производится путем мысленного деформирования его поверхности. Это возмущение скажется на температурном поле тела только в области, непосредственно прилегающей к видоизмененной границе. Следовательно, видоизменение охлаждаемой поверхности тела (конфигурации) при неизменяемой величине теплового потока практически не сказывается на температурном поле отдаленных областей тела. Например, если видоизменять поверхность неограниченной плоской стенки, можно получить самые различные ее очертания. При постоянной величине те-
126
плового потока, проходящего через поверхность, температурное поле центральной зоны такой стенки будет одним и тем же.
Чтобы решить задачу о затвердевании отливки типа стенки с неправильной конфигурацией поверхности, необходимо сопоставить температурное поле этой отливки с температурным полем неограниченной плоской стенки. Отливка простейшей конфигурации, к расчету которой сводится задача о затвердевании однотипных с нею отливок неправильной конфигурации, является основной (модельной).
Для решения этой задачи отливки классифицируются по признаку конфигурации основной отливки.
Кпервому классу относятся отливки типа стенок, имеющие одно измерение конечной величины и два других измерения неограниченно большие. Основной отливкой первого класса является неограниченная плоская отливка, с которой сопоставляются все отливки первого класса.
Ко второму классу относятся отливки типа цилиндров и призм. Эти отливки имеют два конечных измерения одного порядка и третье измерение неограниченно большое. Основной отливкой второго класса является бесконечно длинный круглый цилиндр (призма). При расчете процесса затвердевания отливки второго класса данная отливка сопоставляется с основной.
Ктретьему классу относятся отливки, имеющие три конечных измерения одного и того же порядка (куб, цилиндр с длиной, мало отличающейся от диаметра, и т. п.). Основной отливкой является шар.
При решении поставленной задачи в начале отливка неправильной конфигурации относится к одному из трех классов. Затем производится
еерасчет путем сопоставления с основной отливкой соответствующего класса.
Согласно принципу стабильности теплового потока необходимо, чтобы тепловые потоки, проходящие через поверхность данной и основ-
127
ной отливок, были одинаковыми. Тогда основная отливка будет эквивалентна данной в том смысле, что вдали от поверхности процесс затвердевания этих отливок будет протекать одинаково.
Равенство тепловых потоков обеспечивается одним из условий
α1 (t1п − tc )F1dτ = α10 (t1п −tc )0 F10 dτ0
|
− λ1 |
|
∂t |
F1dτ = − λ10 |
|
∂t |
F10 dτ0 , |
||
или |
|
|
|
|
|
|
|||
|
|
||||||||
|
|
|
∂n n |
|
|
∂n n0 |
где α1 − среднее по поверхности F1 данной отливки значение коэффициента теплоотдачи; все остальные обозначения имеют прежний смысл; величины с индексом «0» относятся к основной отливке, без индекса – к данной.
Первое условие справедливо при малой (Bi1 << 1) и средней (Bi1 ≈ 1) интенсивностях охлаждения отливки, когда термическое сопротивление на поверхности отливки не равно нулю (процесс затвердевания в значительной мере зависит от условий теплообмена на поверхности, т. е. от величины коэффициента теплоотдачи α1).
Второе условие применяется при Bi>>1, когда термическое сопротивление на поверхности стремится к нулю и основную роль играет термическое сопротивление материала отливки (определяемое коэффициентом теплопроводности λ1).
Приведенные условия можно соблюсти путем соответствующего выбора величин, относящихся к основному телу. Если принять, что температурные поля данной и основной отливок в центральной зоне одинаковые, необходимо положить:
|
(t1п −tc )=(t1п −tc )0 |
|||||
|
|
∂t |
|
∂t |
||
или |
|
|
|
= |
|
. |
|
|
|||||
|
|
∂n n |
|
∂n n0 |
128
При синхронном протекании процессов затвердевания данной и основной отливок будем иметь
dτ = dτ0.
В результате требования о равенстве тепловых потоков приобретают вид:
|
α10 = Аα1 |
(6.96) |
или |
λ10 = Аλ1, |
(6.97) |
|
А= |
F |
|
|
где |
1 |
. |
(6.98) |
|
F |
||||
|
|
10 |
|
|
Безразмерная величина А представляет собой критерий конфигурации, характеризующий относительную величину поверхности рассматриваемой отливки по отношению к поверхности основной отливки. Если соблюдается равенство (6.96) или (6.97), то основная отливка будет эквивалентна данной.
Суть расчета процесса затвердевания конкретной отливки по методу эквивалентных отливок заключается в том, что расчету подвергается не данная отливка, а эквивалентная ей отливка правильной конфигурации соответствующего класса. Если Bi1<<1 или Bi1≈1, то при расчете в качестве коэффициента теплоотдачи выбирается величина α10, определяемая формулой (6.96). Если Bi>>1, то эквивалентная отливка рассчитывается при значении λ10, определяемом выражением (6.97).
При расчете возникает необходимость в определении критерия А конфигурации и эквивалентного размера Х10 для отливок различных классов. Величина критерия А находится по формуле (6.98), эквивалентный радиус Х10 определяется из условия равенства объемов рассматриваемой и эквивалентной отливок.
Для отливок первого класса критерий конфигурации
А′ = |
F1 |
, |
|
||
|
2F1ср |
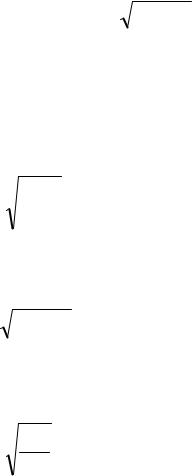
129
где F1ср – площадь средней плоскости отливки. Эквивалентный размер
′ |
|
V1 |
|
|
= 2F |
, |
|||
Х10 |
||||
|
|
1ср |
|
где V1 – объем отливки.
Для отливок второго класса критерий конфигурации
А′′ = |
S1 |
или А′′ = |
S1 |
, |
|
S |
10 |
4πF |
|||
|
|
|
1сеч |
|
где S1 – длина контура поперечного сечения данной отливки; S10 – длина контура поперечного сечения эквивалентного цилиндра; F1 сеч – площадь поперечного сечения отливки.
Эквивалентный радиус
′′ |
F1сеч |
|
|
Х10 = |
. |
||
π |
|||
|
|
Для третьего класса критерий конфигурации
А′′′ = |
F1 |
|
|
3 36πV 2 . |
|||
|
|||
|
1 |
|
Эквивалентный радиус
Х′′′ = 3 3V1 .
10 4π
Согласно выведенным формулам критерий конфигурации А для отливок неправильной формы всегда больше единицы. Это означает, что отливка неправильной формы при прочих равных условиях всегда затвердевает быстрее, чем отливка правильной формы (классической конфигурации). При А→1 отливка неправильной конфигурации обращается в отливку правильной конфигурации. Мерой несходства конфигураций различных отливок является критерий А. Величиной этого критерия
130
определяется разница во времени затвердевания отливок неодинаковой конфигурации.
Преимущество этого метода расчета заключается в том, что с его помощью удается свести задачу о затвердевании отливки неправильной конфигурации к тем простейшим частным случаям, которые были рассмотрены выше.
Обратимся теперь к изучению законов затвердевания сложной отливки. Выше уже упоминалось, что в начальный период затвердевания (третья стадия) можно пренебречь взаимным тепловым влиянием различных частей отливки. При этом толщина ξ корки относительно мала, поэтому процесс допустимо рассчитывать по простейшим формулам, выведенным для плоской отливки, применительно к соответствующей (местной) интенсивности теплообмена (корка рассматривается как тонкая отливка).
В качестве примера рассмотрим изотермы затвердевания различных по конфигурации отливок, охлаждающихся в металлических и неметаллических формах. На рис. 6.18 приведены изотермы затвердевания цинковой отливки размером 60х60х155мм в окрашенном кокиле квадратного сечения (затвердевания снаружи), полученные методом выливания незатвердевшего остатка. На рис. 6.19 показаны изотермы затвердевания цинка на поверхности алюминиевого образца (затвердевание изнутри), который погружался на определенное время в ванну с расплавленным цинком, обладающим tкр. На рис. 6.20, а–в изображены изотермы затвердевания цинка в стальном цилиндрическом кокиле. Рис. 6.20, а соответствует выливанию незатвердевшего остатка через 30 и 40 с, причем на дне кокиля краска была удалена (слой краски имел Хкр = 0,5 мм) на площади 0,5 см2. На рис. 6.20, б показаны изотермы затвердевания при сплошном слое краски на внутренней поверхности кокиля. Рис.
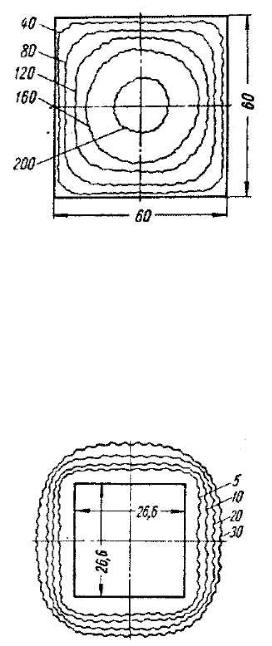
131
6.20, в соответствует случаю, когда на всем дне кокиля слой краски был тоньше, чем на боковых стенках.
Рис. 6.18. Изотермы затвердевания цинковой отливки квадратного сечения, цифры около кривых обозначают время выливания в секундах
Рис. 6.19. Изотермы затвердевания цинка на алюминиевом образце; цифры около кривых обозначают время выдержки образца в ванне в
секундах
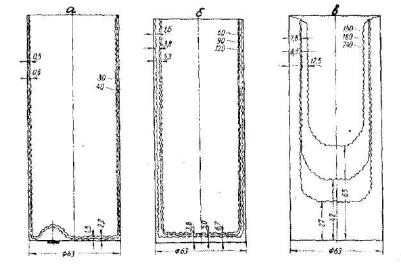
132
Рис. 6.20. Изотермы затвердевания цинка в цилиндрическом стальном кокиле; цифры около кривых обозначают время выливания в секундах (30 – 240 с) и толщину затвердевшей корки в миллиметрах (1,5 – 65)
Из рис. 6.19 – 6.20 видно, что при самых разнообразных условиях охлаждения отливки затвердевание металла в начальный период происходит так, как будто отливка является плоской, а взаимное влияние различных частей (дна, стенок, мест с отличающейся интенсивностью теплообмена и т. д.) полностью отсутствует. Это подтверждает высказанную ранее мысль о свойствах тонкой отливки или тонкой корки. Именно поэтому процесс затвердевания сложной отливки в начальный период рассчитывается по формулам, выведенным для плоской стенки, причем на каждом участке формы берутся свои локальные значения коэффициента теплоотдачи.
По мере возрастания толщины ξ корки на законе затвердевания начинает сказываться влияние конфигурации отливки. На рис. 6.18 плоские изотермические поверхности начинают закругляться при τ > 120 с, а
на рис. 6.19 – при τ > 20 с. Влияние конфигурации на процесс затверде-
вания становится заметным, когда толщина ξ оказывается того же порядка, что и половина радиуса Х1 отливки.
133
При дальнейшем затвердевании отливки на ходе изотермических поверхностей начинает сказываться не только конфигурация, но и взаимное влияние частей. В результате места сопряжения различных поверхностей отливки заметно округляются.
К концу процесса в полной мере проявляется также действие принципа стабильности теплового потока. При этом изотермы затвердевания у отливки или у ее отдельных частей рассмотренных выше трех классов приобретают правильные классические очертания. Последнее обстоятельство очень хорошо видно из рис. 6.18 и 6.19.
Изотермы затвердевания для различных моментов времени рассчитываются на основе принципа стабильности теплового потока. Согласно этому принципу, в каждый данный момент объем металла, затвердевшего в отливке или ее части данной конфигурации, равен объему металла, затвердевшего в эквивалентной отливке классической конфигурации соответствующего класса.
Характер дальнейшего затвердевания металла зависит от конфигурации охлаждаемой поверхности. Около каждого участка поверхности правильной формы (включая поверхности наружных холодильников) строится изотерма затвердевания с помощью формул, выведенных в предыдущих параграфах. По этим формулам находится толщина ξ кор-
ки, а также ее объем Vξ. Истинный объем V затвердевшего металла определяется исходя из принципа стабильности теплового потока. Объем металла Vξ корки сопоставляется с истинным объемом V. Если отливка затвердевает снаружи (рис. 6.18), то объем V превышает величину Vξ.
Разность V – Vξ идет на скругление изотермических поверхностей в уг-
лах отливки. Если затвердевание происходит изнутри (рис. 6.19), то Vξ.> V и разница Vξ. – V снимается с внешних углов отливки.
Такой ход процесса имеет место примерно до половины радиуса Х1 отливки.
134
Вторая половина процесса затвердевания сложной отливки (или ее выделенной части) практически не отличается от процесса затвердевания эквивалентной отливки соответствующего класса, так как изотермические поверхности в данной отливке приобретают правильную классическую конфигурацию изотермических поверхностей эквивалентной отливки (рис. 6.18 и 6.19). Расчет второй половины процесса ведется по методу эквивалентных отливок с помощью критерия конфигурации А.
Рассмотренный метод расчета законов затвердевания сложной отливки, безусловно, является приближенным.
Анализ законов затвердевания. Наиболее важным фактором, оказывающим решающее влияние на характер продвижения фронта затвердевания со временем, является конфигурация отливки. Именно поэтому для отливок различной конфигурации получаются неодинаковые расчетные формулы. Существенное влияние на закон затвердевания оказывает также интенсивность теплообмена (Bi1 или Bi0). Кроме того, на закон затвердевания влияют физические свойства и температурные условия процесса, определяемые критерием L.
Влияние конфигурации. Выше было установлено, что в начальный период, когда толщина корки мала в сравнении с радиусом ее кривизны, закон затвердевания отливки любой конфигурации совпадает с законом затвердевания плоской отливки. Следовательно, в этих условиях на закон затвердевания влияют лишь два других фактора, характеризуемых критериями Bi и L.
С ростом ξ (или δ) начинает влиять конфигурация отливки. Чтобы в чистом виде установить влияние конфигурации, необходимо исключить действие других факторов. Для этого надо положить Bi << 1.
При Bi << 1 законы затвердевания отливок различной конфигурации описываются формулами, например, (6.83) для плоской отливки. Покажем, что слагаемые в этих формулах, зависящие от δ (и следовательно,
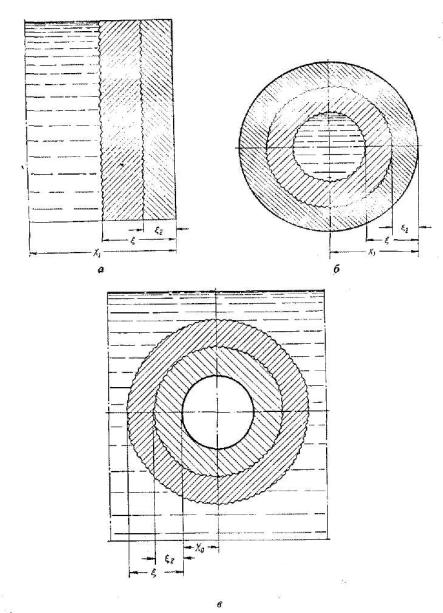
135
характеризующие геометрические свойства отливок), можно получить из чисто геометрических соображений. Для этого найдем зависимость объема V – V2 металла, затвердевшего за время τ − τ2, от толщины ξ − ξ2 корки для упомянутых выше пяти случаев. Принимается, что к началу третьей стадии (в момент τ = τ2) толщина корки ξ = ξ2 и объем затвердевания металла V = V2.
Рис. 6.21. Схема для определения объема металла, затвердевающего за время τ - τ2: а – плоская отливка; б – цилиндрическая или шаровая отливка, затвердевающая снаружи; в – цилиндрическая или шаро-
вая отливка, затвердевающая изнутри
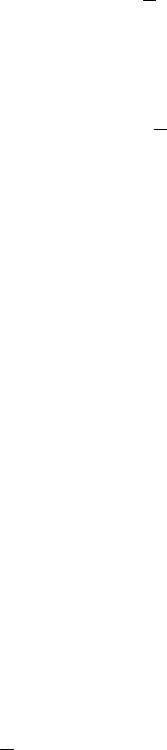
136
Для плоской отливки (рис. 6.21, а)
V −V2 = F1 X1 (δ −δ2 ).
Для цилиндрической отливки, затвердевающей снаружи (рис. 6.21, б)
V −V2 =π(Х1 −ξ2 )2 l −π(X1 −ξ)2 l = F1 X1 (δ −δ2 )− 12 (δ 2 −δ22 ).
Для полой цилиндрической отливки, затвердевающей изнутри
(рис. 6.21, в)
V −V2 =π(Х0 +ξ)2 l −π(X 0 +ξ2 )2 l = F1 X 0 (δ −δ2 )− 12 (δ 2 −δ22 ).
Для шаровой отливки, затвердевающей снаружи (рис. 6.21, б)
V −V |
2 |
= |
4 |
π(Х |
1 |
−ξ |
2 |
)3 |
− |
4 |
π(X |
1 |
−ξ)3 |
= F X |
(δ −δ |
2 |
)− (δ 2 −δ 2 )+ |
1 |
(δ 3 |
−δ 3 ) |
|
|
|
|
|||||||||||||||||||
|
3 |
|
|
|
3 |
|
|
1 |
1 |
2 |
3 |
|
2 |
|
|||||||
|
|
|
|
|
|
|
|
|
|
|
|
|
|
|
|
|
Для шаровой отливки, затвердевающей изнутри (6.21, в)
V −V2 |
= |
4 |
π(Х0 |
|
+ξ)3 − |
4 |
π(X 0 |
+ξ2 )3 = F1 X 0 (δ −δ2 )+ (δ 2 |
−δ22 )+ |
1 |
(δ 3 |
−δ23 ) . |
||||||||||||||||||
|
|
|
|
3 |
||||||||||||||||||||||||||
|
|
|
|
3 |
|
|
|
|
|
|
3 |
|
|
|
|
|
|
|
|
|
|
|
|
|
|
|||||
Примем обозначения: |
|
|
|
|
|
|
|
|
|
|
|
|
|
|
|
|||||||||||||||
r = |
V |
|
r = |
V2 |
|
|
|
y = |
|
r |
|
|
|
y |
|
= |
r2 |
|
|
|
|
|
||||||||
|
F и |
2 |
|
|
|
F |
; |
|
|
|
|
|
X |
1 |
|
и |
|
2 |
|
X |
1 |
|
|
|
|
|
||||
|
1 |
|
|
|
|
|
|
|
1 |
|
|
|
|
|
|
|
|
|
|
|
|
|
|
|
|
|
|
|
||
или |
y = |
|
r |
|
|
|
y2 |
= |
r2 |
|
|
|
|
|
|
|
|
|
|
|
|
|
|
|
|
|||||
|
X 0 |
и |
X 0 . |
|
|
|
|
|
|
|
|
|
|
|
|
|
|
|
||||||||||||
|
|
|
|
|
|
|
|
|
|
|
|
|
|
|
|
|
|
|
|
|
|
Величина r представляет собой приведенный размер эквивалентной корки. Критерий y является безразмерной приведенной толщиной затвердевшей корки. В новых обозначениях выведенные формулы приобретают вид
у− у2 =δ −δ2 ;
у− у2 = (δ −δ2 )− 12 (δ 2 −δ22 );
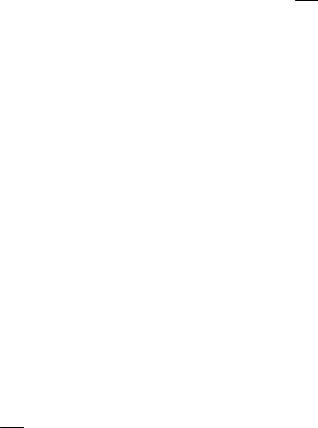
137
у − у2 |
= (δ −δ2 )+ |
|
1 |
(δ 2 |
−δ22 ); |
|
|
|
|
||||
2 |
|
|
|
|
|||||||||
|
|
|
|
|
|
|
|
|
|
||||
у − у2 |
= (δ −δ2 )− |
1 |
(δ 2 −δ22 )+ |
1 |
|
(δ 3 −δ23 ); |
|||||||
|
|
|
|||||||||||
|
|
|
2 |
|
|
3 |
|
|
|
|
|||
у − у2 |
= (δ −δ2 )+ |
|
1 |
(δ 2 |
−δ22 )+ |
|
1 |
(δ 3 |
−δ23 ). |
||||
2 |
3 |
||||||||||||
|
|
|
|
|
|
|
|
Как видим, полученные геометрические характеристики, которые определяют объем затвердевшего металла, совпадают с соответствующими геометрическими характеристиками расчетных формул (например (6.83) для плоской отливки). Это подтверждает высказанную ранее мысль о влиянии конфигурации на законы затвердевания отливок.
Для наглядного представления зависимости между законом затвердевания ξ = f(r) и конфигурацией отливки перенесем в расчетных фор-
L
мулах (например (6.83) для плоской отливки) множитель Bi из правой части в левую. Тогда в общем случае для любой из отливок будем иметь
L |
(Fo − Fo2 )= y − y2 . |
(6.99) |
|
Bi |
|||
|
|
Как видим, для плоской отливки время τ (характеризуемое критери-
ем Fo) пропорционально толщине ξ (характеризуемой критерием у) – линейный закон затвердевания. Для цилиндрической отливки, затвердевающей снаружи, наблюдается ускорение процесса при δ → 1. Еще большее ускорение процесса получается у шаровой отливки, затвердевающей снаружи. Наоборот, у полых цилиндрической и шаровой отливок, затвердевающих изнутри, с ростом δ наблюдается замедление процесса по сравнению с плоской отливкой. Соответствующая зависимость
L
толщины δ от величины Bi Fo приведена на рис. 6.22 (при расчете ве-
личины τ2 и ξ2 приняты равными нулю).

138
Рис. 6.22. Законы затвердевания отливок различной конфигурации (Bi << 1): 1 – плоская; 2 – цилиндрическая (затвердевание снаружи); 3 – полая цилиндрическая (затвердевание изнутри); 4 – шаровая (затверде-
вание снаружи); 5 – полая шаровая (затвердевание изнутри)
Влияние интенсивности теплообмена. При относительно малой толщине затвердевшей корки (δ << 1) отливка любой конфигурации затвердевает как плоская стенка. Следовательно, у любой отливки в начальный период при малой интенсивности теплообмена (Bi << 1) наблюдается линейный закон затвердевания. При относительно большой интенсивности теплообмена (Bi>>1) получается параболический закон: время τ оказывается пропорциональным квадрату толщины ξ затвер-
девшей корки. В промежуточных случаях (Bi ≈ 1) закон затвердевания изменяется от линейного до параболического.
Если толщина затвердевшей корки не мала (δ → 1), то решающее влияние на закон затвердевания оказывает конфигурация отливки, причем с ростом интенсивности теплообмена влияние конфигурации несколько ослабляется по сравнению с тем случаем, когда интенсивность теплообмена предельно мала. Это объясняется следующим образом.
В общем случае количество теплоты Q, теряемой с поверхности отливки при ее затвердевании (третья стадия), складывается из теплоты

139
Qкр и Qакк,. которая выделяется в затвердевшей корке вследствие ее охлаждения ниже температуры tкр. Имеем
Q = Qкр + Qакк.
При малой интенсивности теплообмена (Bi<<1) количество теплоты Qакк=0, так как температура в сечении затвердевшей корки практически равна tкр. В этих условиях количество отведенной теплоты в точности соответствует количеству (объему) затвердевшего металла. Именно поэтому время, которое определяется интенсивностью отвода теплоты с поверхности, оказывается связанным с толщиной ξ простой зависимостью, характеризуемой только конфигурацией отливки.
При возрастании интенсивности теплообмена количество отведенной теплоты уже не равно количеству теплоты кристаллизации, так как Qакк > 0. С увеличением Bi количество теплоты Qакк возрастает. В результате с ростом ξ закон затвердевания несколько искажается. Влияние конфигурации несколько ослабляется действием интенсивности теплообмена, что обусловлено влиянием количества теплоты Qакк. Однако это влияние не нарушает основных закономерностей процесса. Например, с увеличением ξ даже при Bi>>1 наблюдается ускорение процесса затвердевания цилиндрических и шаровых отливок, охлаждаемых снаружи, и замедление процесса затвердевания цилиндрических и шаровых отливок, охлаждаемых изнутри, по сравнению с плоской отливкой, охлаждаемой в тех же условиях.
Влияние критерия L. Физические свойства материала и тепловые условия процесса, характеризуемые критерием L = C1 (tкрρ1− tc ), также
влияют на особенности закона затвердевания отливки. Это влияние объясняется тем, что от величины критерия L непосредственно зависит
Q |
кр |
|
|
|
|
|
|
|
|
||
соотношение между количествами теплоты Qкр и Qакк |
|
. |
Qакк
140
Влияние критерия L обратно влиянию критерия Bi. Однако ввиду того, что в реальных условиях критерий L изменяется не очень сильно, а критерий Bi может изменяться от 0 до ∞, то решающее значение приобретает все же критерий Bi.
Из ранее изложенного ясно, что в начальный период процесса характер закона затвердевания в основном определяется интенсивностью теплообмена, а в конечный период – конфигурацией отливки.
Затвердевание отливки в интервале температур подробно описано в
[1].
Вопросы для самоконтроля знаний
1.Какие законы описывают теплообмен теплопроводностью, конвекцией, излучением?
2.Как определяется коэффициент теплоотдачи?
3.Как определяется теплопроводность среды?
4.Как подсчитывается количество теплоты, передаваемой через неограниченную плоскую стенку, разделяющую среды с разными температурами и коэффициентами теплоотдачи?
5.Как определяется полное термическое сопротивление?
6.Что такое температурный напор и температурный перепад в отливках?
7.Как рассчитывается критерий Био?
8.Что означает: Bi « 1; Bi ≈ 1; Bi » 1?
9.Как рассчитывается приведенный размер отливки?
10.В чем заключается расчет процесса затвердевания по методу эквивалентных отливок?
11.Какие способы воздействия на процесс затвердевания отливки Вы знаете?
141
12.Как влияет материал литейной формы на процесс затвердевания отливки?
13.Как влияет конфигурация отливки на процесс её затвердевания?
14.Как влияет значение критерия Bi на скорость затвердевания отлив-
ки?
Раздел 7. УСАДОЧНЫЕ ПРОЦЕССЫ Тема 7.1. Физическая природа и основные понятия усадочных
явлений
Коэффициенты усадки
Под усадочными процессами понимают совокупность явлений изменения объема и размеров металла, залитого в литейную форму, при его охлаждении в жидком состоянии, затвердевании и остывании в твердом состоянии.
Как правило, при затвердевании объем металлов обычно уменьшается, но у некоторых металлов (Sb, Bi, Si, Ge), наоборот, увеличивается. При полиморфных превращениях в твердом состоянии, когда происходит изменение типа и размеров кристаллической решетки, наблюдается скачкообразное изменение размеров тела, проявляющееся либо в сжатии, либо в расширении.
Численные характеристики изменений размеров тел при охлаждении называют коэффициентами усадки, которые могут рассчитываться как изменение объемных или линейных величин и выражаться в долях единицы или в процентах.
Различают следующие коэффициенты усадки. 1. Коэффициент усадки в жидком состоянии
αж = |
|
V −V0 |
|
|
|
, |
(7.1) |
||
V (T −T ) |
||||
|
0 |
0 |
|
|
142
где V и V0 – начальный и конечный объемы жидкого металла соответственно при температуре Т и при охлаждении до Т0.
2. Коэффициент усадки при затвердевании
αз = |
Vж −VТ |
; |
(7.2) |
|
|||
|
Vж |
|
где Vж и VT – объемы металла в жидком и твердом состояниях. Соответственно:
VT =Vж (1 −αз ).
3. Коэффициент усадки в твердом состоянии
Л |
|
l |
−l0 |
|
|
αТ |
= |
|
|
, |
|
l (T −T |
) |
||||
|
|
0 |
0 |
|
|
(7.3)
(7.4)
где l 0 и l – соответственно линейные размеры тела при температурах Т0 и Т.
Коэффициенты αж, αз характеризуют объемную усадку, αТЛ - линей-
ную усадку. Они выражаются в долях единицы. Связь между коэффици-
ентами линейной усадки αТЛ и объемной усадки αТО в твердом состоя-
нии можно продемонстрировать следующим образом.
|
Для куба с длиной сторон l0 при исходной температуре Т0: |
|
||||
|
V0 = l 03 – начальный объем. |
|
|
|
||
l |
= l0 [1−αTл (Т0 −Т)]при снижении температуры от Т0 до Т. |
(7.5) |
||||
|
Тогда при Т |
|
|
|
|
|
|
|
V |
= l03 [1−αTл (Т0 −Т)]3 . |
(7.6) |
||
|
Следовательно, |
|
|
|
|
|
α0 |
= l03 −l03 [1 −αTл (T0 −T )]3 |
= 3αТЛ (Т0 −Т)−3[αТл (Т0 −Т)]2 +[αТл (Т0 −Т)]3 . |
(7.7) |
|||
T |
l3 |
(T −T ) |
Т |
0 |
−Т |
|
|
0 |
0 |
|
|
|

143 |
|
Поскольку величина αТл незначительна, то членами, |
стоящими во |
второй и третьей степени, можно пренебречь. Тогда |
|
αТ0 ≈ 3 αТл . |
(7.8) |
4. Коэффициент литейной усадки, характеризующий изменения размеров отливки от температуры заливки жидкого металла до температуры окружающей среды и измеряемый в процентах:
αл = |
l0 −l |
100 % , |
(7.9) |
|
l |
||||
|
|
|
где l 0 – размер полости формы при заливке (принимается равным раз-
меру модели); l – размер отливки при комнатной температуре.
В табл. 7.1 приведены значения коэффициентов усадки некоторых металлов.
Таблица 7.1
Коэффициенты усадки металлов
Металл |
αж 105 |
αз |
αТл 106 |
|
|
|
21 |
Al |
40 |
0,066 |
|
Mg |
35 |
0,051 |
29 |
Cu |
20 |
0,044 |
20 |
Fe |
9 |
0,03 |
12 |
Ti |
- |
0,01 |
10 |
|
|
|
|
Строение области затвердевания
Литейные сплавы всегда кристаллизуются в некотором интервале температур. В затвердевающей отливке в общем случае можно выде-
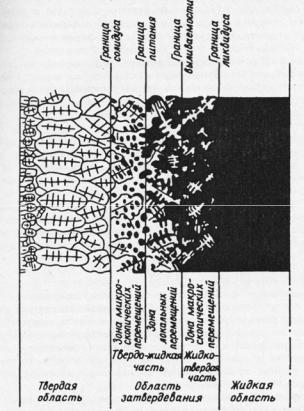
144
лить три области: область твердого состояния, область затвердевания и область жидкого состояния (рис. 7.1).
Рис. 7.1. Строение области затвердевания
Области разделены границами: область жидкого состояния и область затвердевания – границей ликвидус; области затвердевания и твердого состояния – границей солидус. В области затвердевания можно условно выделить три зоны:
-зону макроскопических перемещений жидкого металла; в ее пределах твердые кристаллы не связаны жестко между собой и свободно плавают в жидкости, а при выливании незатвердевшей жидкости удаляются вместе с нею, обнажая так называемую границу выливаемости;
-зону локальных перемещений жидкого металла; в ее пределах кристаллы образуют связанный каркас, но жидкость сравнительно свободно может перемещаться между ними. При выливании незатвердев-
145
шей жидкости часть ее остается в промежутках между кристаллами этой зоны;
- зону микроскопических перемещений жидкого металла; в ее пределах незатвердевшая жидкость разделена растущими кристаллами на изолированные несообщающиеся между собой объемы. Перемещение жидкости может происходить только внутри таких объемов. Поступление жидкости из зоны локальных перемещений в эту зону не происходит. Эта зона отделена от предыдущей границей питания.
Границы ликвидус и солидус являются физико-химическими характеристиками сплава; эти температуры указываются на диаграммах состояния. Границы выливаемости и питания являются технологическими характеристиками сплава. Они зависят от условий формирования отливки. Если кристаллизация будет происходить в форме разветвленных кристаллов, связанный каркас между ними образуется быстро и граница выливаемости будет располагаться вблизи границы ликвидус; к ней будет примыкать и граница питания. Если кристаллизация будет происходить в глобулярной форме с образованием равноостных неразветвленных кристаллов, граница выливаемости питания будет располагаться вблизи границы солидус. Параметры области затвердевания во многом определяют развитие усадочных процессов, заполнение литейной формы, формирование литой поверхности.
Тема 7.2. Усадочные раковины и усадочная пористость в отливках
Усадочные раковины
Усадочной раковиной называют концентрированную группу пустот (или одну пустоту), образующуюся в результате усадки при затвердевании и охлаждении жидкого металла в отливке. Процесс перемещения
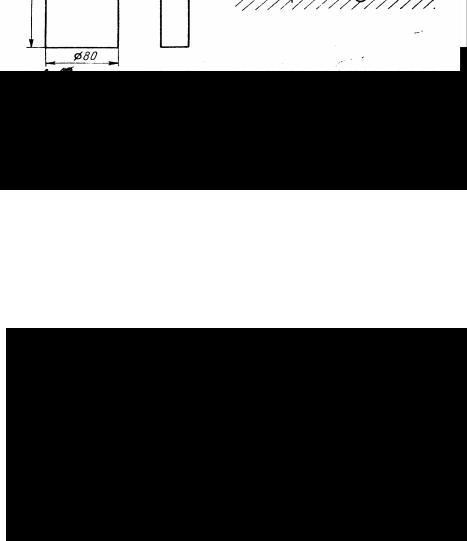
146
жидкого металла внутри затвердевающей отливки, нарушение которого приводит к образованию усадочных пустот, называется питанием.
Слои металла, разделяющие отдельные пустоты усадочной раковины и закрывающие ее сверху, называют мостами. Часть отливки, в которой располагается усадочная раковина вместе с мостами, называют областью усадочной раковины.
При наличии моста, закрывающего усадочную раковину сверху, она называется закрытой (рис. 7.2, а – в), при отсутствии моста – открытой
(рис. 7.2, г).
Рис. 7.2. Типы усадочных раковин
Для оценки склонности сплавов к развитию усадочных раковин применяются технологические пробы (рис. 7.3).
Рис. 7.3. Пробы для определения развития усадочных раковин:
а – цилиндрическая; б – ступенчатая; в – коническая
147
Объем раковины в пробе определяют путем засыпки ее песком или заливки керосином через мерную пипетку.
Объем усадочной раковины, отнесенный к объему отливки, можно определить по формуле Н. Г. Гиршовича и Ю. А. Нехендзи:
Vр.отн =αжо (Тж.ср −Т0 ) +αзо− β3αТЛ (Т0 −ТТ.ср ), |
(7.10) |
где Тж.ср и ТТ.ср – средние температуры металла соответственно |
в мо- |
мент начала и в момент конца затвердевания отливки; Т0 – температура кристаллизации; β – коэффициент, характеризующий влияние массы твердой корки на формирование раковины (его значение рекомендуется принимать равным приблизительно 1/2).
Индексы «о» и «л» при коэффициентах усадки означают, что они выражаются соответственно в объемных и линейных величинах.
Усадочная раковина начинает формироваться с момента образования сплошной твердой корки по всей поверхности отливки.
Усадка затвердевшего металла может выжимать жидкость из средней части отливки и способствовать сокращению объема раковины.
Образование в твердом и жидком состоянии новых фаз (графита в чугуне, карбидов, интерметаллидов и т. д.), изменяющих удельный объем, может в той или иной степени компенсировать усадку, сокращая объем усадочной раковины.
Влияние технологических факторов и состава сплава на процессы усадки
Температура заливки. Влияние температуры заливки на развитие усадочной раковины сводится к воздействию на усадку в жидком состоянии. Ее учет, согласно формуле (7.10), требует знания средней температуры жидкого металла в момент начала образования раковины. Поскольку обычно требуется вычислить максимально возможный объем

148
усадочной раковины, разность Тж.ср – Т0 можно заменить величиной перегрева t. Применение формулы (7.10) требует также определения средней температуры твердого металла в момент окончания затвердевания. Приближенно ее можно определить как половину температурного перепада на поверхности отливки Т за время затвердевания. Тогда выражение (7.10) упрощенно можно записать в виде
Vр отн = αжt +αз − |
1 |
αT0 |
Т . |
(7.11) |
|
4 |
|||||
|
|
|
|
В этом случае все коэффициенты усадки выражены в объемных единицах. Величина ¼ в третьем члене правой части получена как произведение β = ½ на половину температурного перепада Т.
При литье, например, стали в песчаные формы с учетом
αT0 ≈ 3αTЛ = 3 12 10−6 (табл. 7.1) величина третьего члена равна
14 αT T = 14 3 12 10−6 50 = 0,00045 ;
при литье в металлические формы
14 αT T = 14 3 10−6 400 = 0,00360 .
Полученные величины очень малы по сравнению с коэффициентом усадки стали при затвердевании α3 = 0,030. Поэтому усадкой в твердом состоянии можно пренебречь. Тем более что она имеет отрицательный знак, а для расчетов требуется максимальное значение объема усадочной раковины.
Окончательно для расчета объема усадочной раковины в отливках из стали и большинства цветных сплавов можно принять выражение
Vр. отн = α3 + αжt. (7.12)
Металл, затвердевающий на стенках формы за время заливки, в усадочных процессах, определяющих объем усадочной раковины, уча-

149
стия не принимает, так как его учет приведет к сокращению этого объема.
Температурный интервал кристаллизации. В сплаве, кристаллизующемся в интервале температур, формирование области усадочной раковины заканчивается раньше, чем отливка затвердевает полностью.
Характер затвердевания реальной отливки может быть различным – последовательным и объемным. Он зависит от температурного интервала кристаллизации сплава и скорости охлаждения отливки, определяемой теплофизическими характеристиками формы.
В качестве критерия для оценки характера затвердевания можно использовать отношение
К = Ткр δТ , |
(7.13) |
где ΔΤкр − интервал температур кристаллизации; δΤ − перепад температур в сечении отливки.
При малом интервале температур кристаллизации ΔΤкр по сравне-
нию с перепадом температур δΤ (ΔΤкр <δΤ) затвердевание является последовательным (К < 1). При большом интервале температур кристаллизации и сравнительно малом перепаде температур (К > 1) происходит объемное затвердевание.
Поверхность контакта твердой и жидкой фазы может быть относительно ровной – имеет место последовательное затвердевание. Если поверхность контакта расплава и твердой фазы имеет весьма сложную конфигурацию, обе фазы находятся в соприкосновении друг с другом в определенном интервале по сечению отливки. Этот интервал и называют областью затвердевания (рис. 7.1).
Двухфазная область затвердевания на стороне, обращенной к расплаву, ограничена так называемой изоликвидой, то есть поверхностью, все точки которой в один и тот же момент времени имеют температуру
150
начала кристаллизации – ликвидус. На стороне, обращенной к твердой фазе, она ограничена изосолидой, т.е. поверхностью, все точки которой в один и тот же момент времени имеют температуру конца кристаллизации – солидус. Расстояние между поверхностями изосолиды и изоликвиды, измеренное перпендикулярно к ним, представляет ширину двухфазной области затвердевания. Если она так велика, что существует определенное время по всему сечению отливки, пока не начнется кристаллизация от поверхности, то это явление называют объемным затвердеванием. Последовательное затвердевание протекает при одной и той же температуре без интервала затвердевания, т.е. когда линии ликвидуса и солидуса совпадают. Таким образом, последовательно могут затвердевать только эвтектические сплавы, кристаллизующиеся при постоянной температуре, и чистые металлы.
При последовательном затвердевании отливки в тепловом центре или в тепловых узлах отливки формируется сосредоточенная усадочная раковина. При объемном затвердевании внутри зоны микроскопических перемещений жидкой фазы (рис. 7.1) формируется рассеянная пористость в результате отделения друг от друга последних порций затвердевающего расплава, который подвергается усадке.
Общий объем усадочных пустот Vу.п. можно выразить соотношением
Vy.п. = Vp + Vп,
где Vp – объем сосредоточенной усадочной раковины; Vп – объем пористости.
На рис. 7.4, а показана схема развития усадочных раковин и пустот в соответствии с диаграммой состояния двойной системы сплавов, построенная впервые академиком А.А. Бочваром на основе обобщенных экспериментальных исследований. В чистых металлах и эвтектике (составы 1 и 4) формируются полноценные усадочные раковины и пористость почти не имеет развития. При увеличении интервала кристаллиза-
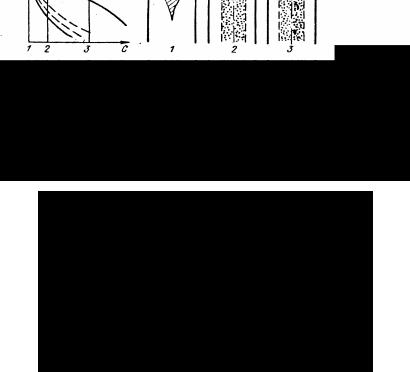
151
ции (составы 2 и 3) существенная часть усадочных пустот представлена порами. Пористость получает максимальное, а усадочная раковина минимальное развитие для состава 3, соответствующего концентрации в точке пересечения линии температур на границе выливаемости и эвтектической платформы.
Рис. 7.4. Связь развития усадочных пустот с диаграммой состояния (а) и положением технологических границ (б)
На рис. 7.4, б показана схема распределения усадочных пустот между раковиной и порами в зависимости от положения границ выливаемости и питания (1,2,3 - составы сплавов). При смещении этих технологических границ к ликвидусу зона осевой пористости сужается, но рассеянная пористость может увеличиваться. При смещении технологических границ к солидусу зона осевой пористости может расшириться, но общий объем всех видов пористости должен уменьшиться.
Выделение графита в серых чугунах сопровождается существенным увеличением объема. В зависимости от состава чугуна, модифицирования расплава, скорости охлаждения и других факторов его выделение
152
может происходить в различных температурных интервалах и с различной скоростью и компенсирует усадку при затвердевании. Усадочные пустоты не получают существенного развития. В высокопрочных чугунах выделение графита вблизи солидуса вызывает расширение твердой корки или так называемое предусадочное расширение. При этом происходит дополнительное опускание зеркала жидкого металла, а объем усадочной раковины резко возрастает. Увеличивая жесткость формы, можно затормозить предусадочное расширение и предотвратить увеличение объема усадочной раковины.
Скорость охлаждения сплава оказывает большое влияние на конечную усадку отливки и величину усадочной раковины. Известно, что при заливке металла с высокой температурой перегрева образуется большая усадочная раковина, чем при заливке с низкой температурой (выражение 7.10). На процесс затвердевания отдельных участков отливки может оказать влияние сопряжение стенок различной толщины, близость питателя или прибыли. В частях отливки, где имеются условия для замедленного охлаждения по сравнению с окружающими зонами, возникает опасность образования усадочных дефектов. Особенно чувствительны к дефектам этого вида отливки из сплавов с большой объемной усадкой.
В табл. 7.2 приведены значения объемной усадки промышленных литейных сплавов.
153
Таблица 7.2
Усадка литейных сплавов
Сплав |
Объемная усадка при кристаллизации, % |
|
|
Углеродистая сталь (0,5 % С) |
2,5…3,0 |
Углеродистая сталь (0,1 % С) |
4,0 |
Белый чугун |
4,0…4,5 |
Серый чугун |
Расширение 2,5 |
Латунь (30 % Zn) |
4,5 |
Силумин (12 % Si) |
3,8 |
|
|
Прибыли
Основным средством устранения усадочной раковины в отливках является прибыль, представляющая собой технологический элемент, в котором должна быть сосредоточена область усадочной раковины и который отделяется от отливки в процессе обработки. В процессе формирования отливки прибыль составляет с нею единое целое. Кроме того, прибыль является средством ослабления развития зональной пористости и сборником загрязнений, всплывающих из жидкого металла в процессе затвердевания.
Сложная отливка, состоящая из элементов различной толщины, при затвердевании обычно разделяется на несколько обособленных узлов питания. Образование усадочных раковин в каждом узле питания можно компенсировать за счет одного источника питания (рис. 7.5, а).
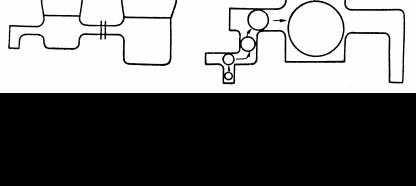
154
Рис. 7.5. Разделение отливки на узлы питания (а) и метод выкатывания шарика (б)
Процесс питания отливки должен быть организован таким образом, чтобы применительно к каждому узлу питания реализовался принцип направленного затвердевания от тонких элементов к толстым и, наконец, к прибыли. Проверка выполнения этого принципа осуществляется методом выкатывания шарика. В самый тонкий элемент узла мысленно помещают шарик (рис. 7.5, б), который при переходе в каждый новый элемент расширяется (сжиматься он не должен). Если он беспрепятственно выкатывается в прибыль, значит, принцип направленного затвердевания выполнен.
Прибыли классифицируются по расположению относительно узла питания отливки, по способу формовки (рис. 7.6, а) и по конфигурации
(рис. 7.6, б).
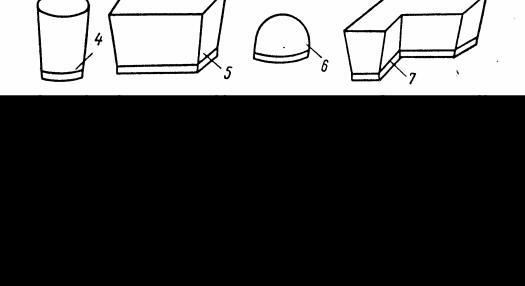
155
Рис. 7.6. Классификация прибылей
По расположению относительно узла питания прибыли делятся на прямые, или верхние 1; отводные, или боковые 2; в том числе групповые, питающие несколько отливок 3. По способу формовки прибыли делятся на открытые 1 и закрытые 2. По конфигурации – на цилиндрические 4, плоские 5, сферические 6 и фигурные 7.
Основными требованиями к размерам прибыли являются, вопервых, обеспечение объема, достаточного для компенсации усадочной раковины в литой заготовке, во-вторых, обеспечение необходимой продолжительности ее затвердевания.
В практике встречаются следующие сочетания конфигураций отливки и прибыли.
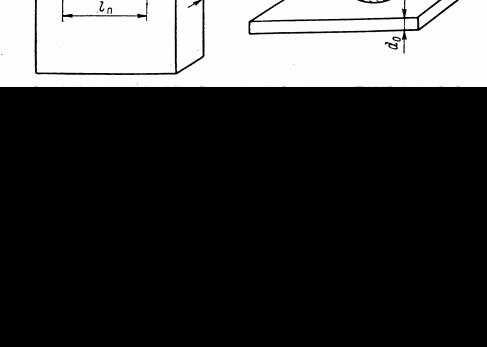
156
Рис. 7.7. Определение сечений прибылей
1. Отливка имеет конфигурацию куба (или сферы), а прибыль является ее продолжением (рис. 7.7, а). Для обеспечения надежности питания в этом случае рекомендуется выбирать следующие соотношения прибыли и отливки:
dn |
=1,05 −1,10 , |
(7.14) |
|
d0 |
|||
|
|
где dп и d0 – диаметры окружностей, вписанных в сечения открытой прибыли и отливки.
Для закрытой прибыли допускается соотношение диаметров dп/d0=0,96 - 1,0.
2.Отливка имеет конфигурацию цилиндра или призмы, расположенной вертикально, а прибыль является ее продолжением (рис. 7.7, б). Для этого случая рекомендуются те же соотношения, что и для предыдущего.
3.Отливка имеет форму горизонтально расположенной призмы (цилиндра), прибыль – плоская (рис. 7.7, в). К этому же виду относится отливка
157
типа кольца. В отдельных случаях можно применять прибыли в форме призмы или цилиндра. В случае применения плоской прибыли ее ширину следует выбирать, руководствуясь соотношением (7.14). Соотноше-
ние длины прибыли l п к ее ширине dп рекомендуется следующее:
lп |
≥ 2,5 . |
(7.15) |
|
||
dп |
|
Если это требование не будет выполнено, то ускоренное охлаждение с торцевых поверхностей не даст возможности осуществлять питание до самого конца затвердевания отливки.
4.Отливка – вертикально расположенная плита, прибыль – плоская (рис. 7.7, г). Соотношения размеров прибыли и отливки должны удовлетворять выражениям (7.14) и (7.15).
5.Отливка – горизонтально расположенная плита, прибыль – цилиндрическая (рис. 7.7, д). Опыты показывают, что в этом случае достаточно обеспечить соотношение
lп |
= 3,0 −3,5 . |
(7.16) |
|
||
dп |
|
Вбоковых прибылях затвердевание происходит не только с боковых
иверхних поверхностей, но и снизу. Поэтому их высоту по сравнению с вертикальными прибылями необходимо увеличивать дополнительно еще на величину радиуса прибыли.
Для обеспечения направленности затвердевания и дифференцированного охлаждения отливки используют смеси с различной теплоаккумулирующей способностью и холодильники (внутренние и наружные). Внутренние холодильники представляют собой прутки, сетки и другие более сложные конструкции из заливаемого сплава, которые устанавливаются в полости формы, соответствующие узлам питания отливки, и предназначаются для снижения температуры и компенсации усадки сплава в указанных объемах. Наружные холодильники - это в большин-
158
стве случаев металлические части формы, соответствующие конфигурации поверхности той части отливки, которая требует ускоренного охлаждения.
Регулирование работы прибылей производится тепловым и механическим методами. Расход металла на прибыли в случае стали составляет от 15 (для слитков) до 100 % (для фасонных отливок) от массы литой заготовки. В то же время объем усадочной раковины, для ликвидации которой прибыли предназначены, не превосходит 4 %. Остальной металл требуется для поддержания источника питания в жидком состоянии до конца затвердевания отливки. Любое сокращение скорости охлаждения металла в прибыли должно позволить соответственно уменьшить ее объем.
Теплоизоляция прибыли осуществляется путем засыпки зеркала жидкого металла теплоизолирующими порошками. В простейшем случае это сухой песок, в других случаях – малотеплопроводные смеси – отходы производства слюды, вермикулит и др.
Еще больший эффект дает одновременное оформление боковой поверхности прибыли теплоизолирующим огнеупорным материалом. При литье в песчаные формы это достигается путем заключения прибыли в стаканы из пеношамота или другого материала. При литье в металлические формы прибыли оформляют стержнями.
Еще более эффективным средством, чем теплоизоляция, является обогрев прибылей. Предложен ряд методов обогрева прибылей стальных отливок, в особенности слитков.
Экзотермические смеси используют для засыпки открытых прибылей и изготовления стаканов, оформляющих прибыли. Смеси разогреваются под действием протекания в них реакций с большим тепловым эффектом. Реакции начинаются при контакте с расплавленным металлом. Смеси включают следующие компоненты:
159
-горючие – обычно алюминий в порошке;
-окислитель – обычно окислы железа в виде руды или окалины или азотнокислые соли;
-замедлитель реакции, необходимый для того, чтобы реакция горения продолжалась по возможности в течение всего периода затвердевания отливки;
-связующая добавка, необходимая в случае, если из смеси изготовляется часть формы; она может также служить замедлителем реакции.
Втабл. 7.3 приведены два типичных состава экзотермических сме-
сей.
Таблица 7.3
Составы разогревающих смесей
Материал |
Диаметр прибыли, мм |
|
|
|
|
|
100 |
150 – 300 |
|
|
|
Алюминий в порошке |
19 |
17 |
|
|
|
Окалина или железная руда |
57 |
46 |
|
|
|
Соли (Na2NO3 или KNO3) |
- |
10 |
Шлак или зола |
- |
12 |
|
|
|
Глина |
- |
5 |
|
|
|
Цемент |
25 |
10 |
|
|
|
Под действием теплоты затвердеваемого металла алюминиевый порошок взаимодействует с окисью железа по реакции
3Al + Fe2O3 = Al2O3 + 2Fe + Q.
Образующийся при сгорании смеси шлак покрывает прибыль хорошо теплоизолирующей коркой.
Подпитка жидкого металла от прибыли к отливке происходит под действием металлоостатического напора и атмосферного давления.
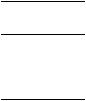
160
Давление в 1 кг/мм2 уравновешивает столб расплавленной стали или чугуна длиной 1450 мм. Высота прибыли большинства стальных отливок средней массы составляет 200 - 400 мм. Следовательно, атмосферное давление оказывает большое влияние на процессы питания.
На работу прибыли и формирование усадочной раковины оказывает влияние вибрация, под действием которой область усадочной раковины приобретает форму блюдечка, ее глубина уменьшается, и размер прибыли может быть уменьшен.
Прибыль должна устанавливаться на наиболее массивном элементе каждого крупного узла питания. Присоединять отводные прибыли к боковым поверхностям отливки целесообразно только в тех случаях, когда они используются как групповые или когда установка вертикальной прибыли усложнит механическую обработку литой заготовки.
Рекомендуются следующие значения максимальных расстояний между прибылями при установке их на отливках с постоянной толщиной стенок (табл. 7.4).
Таблица 7.4
Зависимость максимального расстояния между прибылями от толщин стенок отливки
Толщина стенок отливки, мм |
20 |
40 |
60 |
|
|
300-400 |
|
Максимальное расстояние между прибыля- |
200-300 |
400-600 |
|
ми, мм |
|
|
|
|
|
|
|
При выборе типа прибыли следует отдавать предпочтение прямым цилиндрическим закрытым прибылям, так как при этом упрощается изготовление моделей; кроме того, закрытые прибыли упрощают формовку, препятствуют окислению металла при заливке, способствуют сокраще-
161
нию их необходимого объема за счет возможности теплоизоляции сверху, обеспечивают постоянство объема прибыли.
Открытые прибыли целесообразно применять при изготовлении крупных отливок, когда можно осуществить доливку в них свежих порций горячего жидкого металла для улучшения питания или применить теплоизолирующие засыпки.
Усадочная пористость
Усадочной пористостью называют скопления мелких пустот, образующихся в результате усадки при затвердевании небольших объемов жидкого металла, изолированных в процессе формирования отливки от источников питания жидким металлом.
Формирование пор связано с фильтрацией жидкого металла между твердыми кристаллами в области затвердевания.
Усадочная пористость делится на следующие виды.
1.Рассеянная, распределенная более или менее равномерно по всему объему отливки.
2.Зональная, сосредоточенная в определенных зонах или частях отливки:
-в осевых частях;
-в утолщениях и сопряжениях стенок;
-в зонах местных разогревов при подводе литников.
Развитие пористости в утолщениях и зонах местных разогревов зависит от объема изолированного жидкого металла. При больших его размерах усадочные пустоты приобретают характер усадочных раковин.
Рассеянная пористость образуется по всему объему отливки. Каждая пора возникает в результате усадки при затвердевании микроскопического объема жидкого металла, обособленного от зоны локальных пе-
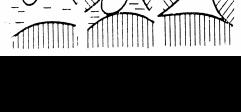
162
ремещений вследствие неравномерного роста кристалов. Чем мельче их размер, тем меньше радиус рассеянной пористости.
В случае полного отсутствия газовыделения при кристаллизации усадочная пористость формируется в условиях вакуума. Если при кристаллизации выделяются газы, то они могут вытеснять жидкий металл из района поры. Поэтому реальная пористость всегда имеет смешанный газоусадочный характер (рис. 7.8).
Рис. 7.8. Схема формирования газоусадочной поры
Для повышения плотности (уменьшения пористости) и улучшения свойств сплавов, кристаллизующихся в широком интервале температур, применяется обработка давлением в автоклаве (5 - 10 ати под газом). Кроме влияния на пропитку отливки, повышение давления способствует растворению газов в металле, тем самым тормозит развитие пористости.
Наиболее широкое развитие в отливках имеет осевая пористость, образующаяся в плоских и призматических элементах. При затвердевании происходит опускание зеркала жидкого металла вследствие усадки. В начале затвердевания жидкий металл движется внутри твердой корки беспрепятственно. Однако по мере сокращения расстояния между растущими навстречу друг другу фронтами кристаллизации начинает возрастать влияние трения потока о стенки канала. Поток питающего жид-
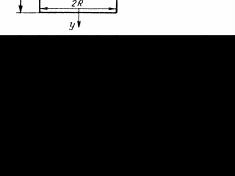
163
кого металла, имеющего температуру кристаллизации, может нести с собой частицы кристаллов, и вязкость расплава возрастает. При достаточном сужении канала режим течения становится ламинарным, а затем структурным.
На некотором расстоянии от верха отливки скорость усадочного перемещения жидкого металла vу должна сравняться с допустимой из гидравлических условий скоростью движения vг (рис. 7.9).
Рис. 7.9. Схема механизма возникновения осевой пористости
Если бы затвердевание происходило очень медленно, то, начиная с момента выравнивания скоростей, процесс питания определялся бы гидравлическими условиями, а не усадкой. Однако затвердевание происходит независимо от условий потока питающего металла. Это означает, что, начиная с момента выравнивания скоростей, нарушается условие неразрывности потока и начинается образование осевой усадочной пористости.
Условие равенства скоростей выражается уравнением
dy |
= vy = vг . |
(7.17) |
dτ |
|
|
Рассмотрим это равенство применительно к плоской отливке высотой Н и толщиной 2R (рис. 7.10).

164
Рис. 7.10. Схема к расчету ширины зоны осевой усадочной пористости
Для простоты пренебрежем затвердеванием отливки с торцов. Предположим, что к некоторому моменту времени жидкая часть от-
ливки достигла в диаметре размера 2r. При уменьшении толщины жидкой части на величину dr уровень жидкости переместится на dh. Тогда
2r dh = α2Hdr, так как vy = vr, (7.18)
где α − коэффициент усадки при затвердевании. В соответствии с законом квадратичного корня
x = R − r = K |
τ , |
|
|||||||||
где К – коэффициент затвердевания, |
|
|
|
|
|
||||||
dr = dx = |
k dτ |
. |
|
|
|
(7.19) |
|||||
2 |
τ |
|
|
|
|||||||
Тогда |
|
|
|
|
|
|
|
|
|
|
|
rdh = α H |
|
k |
|
|
dτ . |
(7.20) |
|||||
|
|
τ |
|||||||||
|
|
|
2 |
|
|
|
|||||
Следовательно, скорость усадочного перемещения |
|
||||||||||
vy = |
dh |
= |
|
|
αHk2 |
|
|
|
|||
dτ |
|
2 (R |
− r) r . |
|
|||||||
|
|
|
|
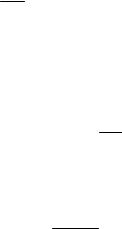
165
Пусть на единицу сечения жидкой части вдоль оси пластинки действует сила Р. На все сечения шириной, равной единице, и толщиной 2а действует усилие 2аР. Оно уравновешивается трением на границе жид-
кой части, равным 2Hη dadv ,
где v – скорость движения жидкости; η − вязкость расплава. Приравнивая эти силы, получаем
2aP = − 2Hη dadv
или
dv = −P |
a da |
|
η H . |
(7.21) |
Интегрируя выражение (7.21) от 0 до v и от r до а, получим
v = |
P (r2 |
− a2 ) |
. |
(7.22) |
||
2η H |
|
|||||
|
|
|
Расход жидкости через единицу ширины пластины будет равен
Q = ∫r |
vrda =∫r |
P (r2 − a2 ) |
da = |
2 Pr3 |
. |
(7.23) |
|
ηH |
|
|
|||||
0 |
0 |
|
3ηH |
|
Средняя скорость движения потока через канал сечением 2r равна
v |
= |
Q |
= |
Pr2 |
|
|
|
2r |
3ηH . |
(7.24) |
|||||
r |
|
|
Движение потока питающего металла происходит под действием атмосферного давления Ра и металлостатического напора Н:
Р = Ра + γ Н. (7.25)
Приравнивая скорости vy и vr, получим
αHk2 |
(Pa +γH ) r2 |
|
|
|
= |
|
(7.26) |
2 (R − r) r |
3ηH |
или
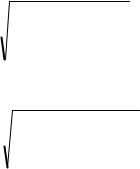
166
3αηk2 H 2 |
3 |
|
4 |
|
|
|
|
= Rr |
|
− r |
|
. |
(7.27) |
2 (Pa +γH ) |
|
|
Поскольку образование пористости происходит при малых значениях радиуса канала, пренебрежем вторым членом в правой части равенства (7.27) и решим его относительно половины толщины зоны осевой пористости rп. Тогда
r =3 |
|
3αη k2H |
|
|
|
2 |
(Pa+γH) R . |
(7.28) |
|||
п |
|||||
|
|
|
|
Деля обе части равенства на R, получим
r |
=3 |
3αη k2H |
|
|
n |
|
. |
(7.29) |
|
R |
2 (Pa+γH) R4 |
Это относительное значение толщины жидкой части сечения отливки в момент, когда поток питающего металла теряет сплошность и начинает формироваться осевая пористость, т.е. относительная (по отношению к толщине отливки) ширина зоны осевой пористости.
На основании проведенного анализа можно сделать следующие выводы:
1.Ширина зоны осевой пористости пропорциональна кубическому корню из произведения усадки при затвердевании α на вязкость η.
2.Ширина зоны осевой пористости прямо пропорциональна коэффициенту затвердевания k в степени 2/3. Следовательно, с увеличением скорости затвердевания относительное развитие осевой пористости возрастает. При переходе из песчаной формы в металлическую (при удвоении скорости охлаждения) она возрастает в 1,6 раза.
3.Развитие осевой пористости обратно пропорционально кубическому корню из суммы атмосферного и гидравлического давления жидкого металла. Это означает, что затвердевание в вакууме будет способствовать
167
развитию осевой пористости и, наоборот, кристаллизация под давлением будет ее подавлять.
4. При уменьшении толщины R и увеличении длины стенки H относительное развитие пористости будет существенно возрастать. Причем изменение толщины имеет большее значение, чем длины.
Развитие зон пористости вблизи места подвода литника зависит от степени его разогрева жидким металлом. Особенно интенсивно развивается пористость при подводе литника в тонкую часть отливки. Для предупреждения местных разогревов в районе подвода металла увеличивают количество литников, уменьшая таким образом объем металла, пропускаемого через один летник.
Меры борьбы с усадочной пористостью заключается в следующем. 1. Кристаллизация под повышенным газовым давлением уменьшает пористость.
2. Создание направленного затвердевания от отдаленных частей отливки к источнику питания способствует уменьшению осевой пористости.
3.Снижение пористости может быть достигнуто путем применения напусков, т. е. придания уклона стенкам отливок, направленного к источнику питания.
4.Эффективный путь снижения пористости заключается в предварительном нагреве формы с перепадом температур, понижающихся от источника питания к возможному месту возникновения пористости.
Устранить полностью рассеянную пористость не удается. Но ее можно уменьшить соответствующими технологическими приемами.
Рассеянная пористость бывает тем больше, чем шире двухфазная зона в сечении затвердевающей отливки. Поэтому все средства уменьшения двухфазной зоны приводят к ограничению рассеянной пористости.