
- •1. ПРИПУСК НА МЕХАНИЧЕСКУЮ ОБРАБОТКУ
- •1.1. Общие сведения
- •1.2. Классификация припусков на обработку
- •2. РАСЧЁТНО-АНАЛИТИЧЕСКИЙ МЕТОД ОПРЕДЕЛЕНИЯ ПРИПУСКОВ
- •2.1. Факторы, определяющие величину припуска
- •2.2. Формулы и указания к расчету припусковна механическую обработку и предельных размеров
- •2.3. Порядок расчёта припусков на обработку и предельных размеров
- •2.4. Примеры расчёта припусков на обработку и предельных размеров
- •3. ОПЫТНО – СТАТИСТИЧЕСКИЙ МЕТОД ОПРЕДЕЛЕНИЯ ПРИПУСКОВ
- •3.1. Припуски на обработку наружных цилиндрических поверхностей
- •3.2. Припуски на обработку торцовых поверхностей
- •3.3. Припуски на обработку плоскостей
- •Оглавление

Оглавление |
|
1. ПРИПУСК НА МЕХАНИЧЕСКУЮ ОБРАБОТКУ ................................. |
3 |
1.1. Общие сведения............................................................................................ |
3 |
1.2. Классификация припусков на обработку .................................................. |
4 |
2.РАСЧЁТНО-АНАЛИТИЧЕСКИЙ МЕТОД ОПРЕДЕЛЕНИЯ
ПРИПУСКОВ..................................................................................................... |
5 |
2.1. Факторы, определяющие величину припуска........................................... |
5 |
2.2. Формулы и указания к расчету припусковна механическую обработку |
|
и предельных размеров..................................................................................... |
28 |
2.3. Порядок расчёта припусков на обработку и предельных размеров..... |
33 |
2.4. Примеры расчёта припусков на обработку и предельных размеров.... |
34 |
3.ОПЫТНО – СТАТИСТИЧЕСКИЙ МЕТОД ОПРЕДЕЛЕНИЯ
ПРИПУСКОВ................................................................................................... |
50 |
3.1. Припуски на обработку наружных цилиндрических поверхностей..... |
50 |
3.2. Припуски на обработку торцовых поверхностей................................... |
75 |
3.3. Припуски на обработку плоскостей......................................................... |
81 |
БИБЛИОГРАФИЧЕСКИЙ СПИСОК........................................................... |
89 |
90
ФЕДЕРАЛЬНОЕ АГЕНТСТВО ПО ОБРАЗОВАНИЮ Федеральное государственное образовательное учреждение высшего профессионального образования
«Сибирский федеральный университет» (СФУ)
ПОЛИТЕХНИЧЕСКИЙ ИНСТИТУТ
В.Е. Авраменко, Е.Г. Зеленкова
ПРОЕКТИРОВАНИЕ ТЕХНОЛОГИЧЕСКИХ ПРОЦЕССОВ СБОРКИ
Красноярск 2007

УДК 621.757 (07)
Проектирование технологических процессов сборки: Учеб. пособие/Сост. В.Е. Авраменко, Зеленкова Е.Г.
Политехнический институт СФУ, Красноярск 2007.– 72 с.
В учебном пособии рассматриваются вопросы проектирования технологических процессов сборки изделий в машиностроении. Предназначено для студентов, выполняющих курсовые и дипломные проекты по специальностям: 120100 «Технология машиностроения», 120200 «Металлообрабатывающие станки и комплексы».
2

1. ИСХОДНЫЕ ДАННЫЕ ДЛЯ ПРОЕКТИРОВАНИЯ
Исходными данными для проектирования технологического процесса сборки являются:
1сборочные чертежи собираемого изделия (узла или машины);
2технические условия на сборку изделия;
3рабочие чертежи деталей, входящих в изделие;
4годовая программа выпуска изделия и предполагаемая продолжительность его производства.
При проектировании необходимо использовать:
-каталоги паспорта, характеристики сборочного оборудования и механизированного инструмента [4, 5, 7, 10, 23, 24];
-стандарты и нормали на механизированный сборочный инструмент;
-технологические процессы сборки типовых узлов машин [1, 2, 3];
-альбомы типовых и нормальных сборочных приспособлений [6];
-нормативы времени на сборочные работы [13];
-бланки технологических карт сборки [30, 31, 32].
Приступая к разработке технологического процесса необходимо изучить:
1.Конспекты лекций по «Технологии машиностроения» и разделы, посвященные проектированию технологических процессов сборки,
учебников [1, 2, 3, 4, 8, 26].
2.Ознакомиться с указанными выше технологическими процессами сборки типовых узлов, каталогами сборочного инструмента, нормативами времени на выполнение сборочных работ, ГОСТами, относящимися к сборке, и рекомендуемой литературой по проектированию технологических процессов сборки.
3

2.ИЗУЧЕНИЕ И АНАЛИЗ ЧЕРТЕЖЕЙ ИЗДЕЛИЯ
1.При ознакомлении с собираемым изделием необходимо выяснить: - служебное назначение узла или машины; - конструкцию и назначение каждой сборочной единицы (комплекта,
подузла) и деталей, входящих в собираемое изделие;
-характер соединений и закреплений узлов и деталей (подвижные, неподвижные, разборные, неразборные, прессовые, клепаные сварные и т.д.);
-сущность и порядок работы изделия, т.е. характер и последовательность движений узлов и деталей.
2. Одновременно с изучением чертежа изделия осуществляется его контроль. При этом проверяется наличие:
-технических условий на сборку;
-проекций и разрезов, дающих полное представление о конструкции собираемого изделия;
-посадок выполняемых соединений и других размеров, выдерживаемых при сборке;
-спецификаций сборочных единиц и деталей, входящих в изделие. При отсутствии каких-либо из этих данных необходимо пополнить
недостающие в сборочном цехе или КБ завода в период практики, а также на основании литературных источников.
3. При ознакомлении изделием выясняются все замыкающие звенья, которые необходимо выдержать при сборке, и методы достижения их точности, предусмотренные конструкцией и отраженные в чертежах.
При выявлении замыкающих звеньев их целесообразно разделить на две группы.
В первую входят звенья, метод достижения которых не вызывает сомнения:
а) зазоры и натяги цилиндрических и резьбовых соединений. Посадки этих соединений либо указаны на сборочном чертеже, либо определяются по рабочим чертежам сопрягаемых деталей.
Точности этих звеньев можно добиться методами полной, неполной и групповой взаимозаменяемости. В последнем случае на чертеже должно быть указано количество групп, на которые необходимо рассортировать детали и допуск на группу;
4

б) боковые зазоры, возникающие при сборке цилиндрических шестерен, замыкающие звенья, определяющие относительное положение осей цилиндрических, конических и червячных передач, обеспечиваемые методами полной и неполной взаимозаменяемости;
в) совпадение вершин делительных конусов конических шестерен, средней плоскости червячного колеса и оси червяка, обеспечиваемые методом регулирования.
Во вторую группу входят замыкающие звенья, метод достижения заданной точности которых может быть установлен только на основе размерного анализа:
а) замыкающие звенья многозвенных размерных цепей, состоящих из линейных, осевых размеров;
б) замыкающие звенья, получающиеся в результате соединения двух собранных узлов.
4. Изучив работу изделия, выявив замыкающие звенья и методы достижения их точности, необходимо критически оценить заданные технические условия на сборку с точки зрения их содержания, соответствия служебному назначению изделия и полноты.
При этом решаются следующие вопросы: а) для чего дано то или техническое условие;
б) какие технические условия должны быть заданы дополнительно, чтобы изделие выполняло свое служебное назначение;
в) чем обосновывается численная величина технического условия; г) когда в процессе сборки эти условия выдерживаются; д) какие проверки (контроль) необходимы в процессе сборки изделия.
Эти вопросы, а так же предложения по дополнению и изменению технических условий должны быть выяснены и согласованы в сборочном цехе или КБ завода в период практики.
Обоснование численных величин основных технических условий делают на основе расчета размерных цепей.
В качестве примера рассмотрим служебное назначение плунжерного насоса. Общая формулировка задачи, для решения которой создается насос – перекачивание жидкости.
5

3. РАЗМЕРНЫЙ АНАЛИЗ ИЗДЕЛИЯ И ВЫБОР МЕТОДА ДОСТИЖЕНИЯ ТОЧНОСТИ ЗАМЫКАЮЩЕГО ЗВЕНА
Важной задачей, решаемой в процессе конструкторскотехнологической подготовки производства изделия (машины) является установление связей между ее служебным назначением и техническими условиями на сборочные единицы и отдельные детали.
Качество и экономичность машины в значительной степени определяются правильной простановкой размеров и назначением допусков.
В основе размерной отработки конструкции лежит анализ двух уровней размерных связей: вначале между деталями механизмов и узлов, а затем между поверхностями каждой детали.
Размерный анализ конструкций является одним из обязательных этапов конструкторско-технологической подготовки производства, позволяющим:
-выявить взаимосвязи деталей и сборочных единиц, требования к точности относительного расположения сборочных единиц;
-определить методы достижения требуемой точности замыкающих звеньев при сборке машины;
-оптимизировать схему компоновки машины;
-обосновать простановку размеров, назначить технические условия и допуски;
-повысить технологичность конструкции;
-установить последовательность сборки машины.
Размерный анализ машины рекомендуется выполнять в следующем порядке:
1.На начальной стадии разработки технического проекта машины составить возможные схемы ее общей компоновки.
2.Выявить замыкающие звенья, определяющие требования к точности относительного расположения сборочных единиц и деталей машины.
3.Исходя из служебного назначения машины, обосновать номинальные значения, допуски и предельные отклонения замыкающих звеньев на основе:
- стандартов на типовые изделия, соединения, передачи; - теоретических расчетов;
6

-опыта проектирования и эксплуатации аналогичных конструкций;
-испытаний опытных образцов.
4.Выявить размеры деталей, влияющих на точность замыкающих звеньев, и составить расчетные схемы (размерные цепи), фиксирующие размерные взаимосвязи узлов и деталей, компонуемых в машине.
5.Определить среднюю точность Тср составляющих звеньев размерных цепей при заданной точности их замыкающих звеньев.
6.Оценить возможность обеспечения Тср в производстве и обосновать метод достижения точности для данного замыкающего звена.
Если значения Тср находятся в пределах средне экономических норм точности используемых методов обработки деталей, требуемую точность замыкающего звена можно обеспечить методами полной или неполной
взаимозаменяемости. При очень жестких значениях средних допусков Тср, точность может быть достигнута методами пригонки или регулирования.
Возможен и другой подход к выбору метода достижения точности: можно назначить приемлемые значения допусков Тi для каждого составляющего звена и вычислить возможную погрешность замыкающего звена:
Т Р = t |
m∑−1λiTi2 , |
(1) |
|
i=1 |
|
Сопоставляя расчетный допуск Т∆р с заданным допуском Т∆, выбирают метод достижения требуемой точности замыкающего звена. Если допуск Т∆р меньше допуска Т∆ или мало отличается от него, то требуемая точность может быть обеспечена методами взаимозаменяемости. Если Т∆р › Т∆, то требуемую точность нужно обеспечивать методами пригонки или регулирования.
Если по каким-либо причинам применение методов пригонки или регулирования невозможно, следует уменьшить допуск Т∆р, добиваясь выполнения условия Т∆р ≈ Т∆.
Уменьшить допуск Т∆р можно двумя путями: сокращением числа составляющих звеньев и уменьшением их допусков. Первый способ требует изменения схемы компоновки или конструкции сборочных единиц, ворой связан с усложнением технологии изготовления деталей.
На рис. 1, 2 приведены возможные варианты схем компоновки машины [13]:
7

Рис.1. Схемы компоновки сборочной единицы
8

Рис.2. Схемы компоновки сборочной единицы
9

При сборке расточных головок 1 и 2 со станиной 3 необходимо обеспечить соосность осей вращения шпинделей в вертикальной (В∆,β∆) и горизонтальной (В′∆,β′∆) плоскостях.
На рис. 1 приведена схема компоновки, согласно которой головки 1 и 2 устанавливают на плоскости и поджимают к направляющим буртикам плиты станины 3.
При этой схеме компоновки требования точности к относительному положению сборочных единиц 1 и 2 можно обеспечить различными методами:
1. Метод полной взаимозаменяемости – путем установки головок на станине и поджима к направляющим буртикам. Для этого необходимо, чтобы линейные размеры В1 - В3, В′1 - В′3 и угловые размеры β1 - β3, β′1 - β′3 выполнялись с такой точностью, чтобы сумма их погрешностей не превышала допускаемые величины В∆, В′∆, β∆, β′∆. Сборка по этой схеме наиболее проста, но механическая обработка деталей усложняется предъявляемыми к ним требованиями точности.
2.Пригонкой плиты станины 3 или основных баз головок 1 и 2.
3.Методом регулирования – путем применения компенсаторовпрокладок, клиньев.
При компоновке по схеме, приведенной на рис. 2.а, направляющие буртики отсутствуют. Благодаря этому сборочные единицы имеют степени свободы перемещения по осям X и Y и поворота вокруг вертикальной оси, что позволяет обеспечить требуемую точность совпадения и параллельность осей в горизонтальной плоскости методом регулирования. Для этого перемещают и поворачивают узлы в этой плоскости до тех пор, пока оси валов не совпадут и не будут параллельными. Точность совпадения осей будет зависеть от применяемых сборочных приспособлений, точности контрольных средств и квалификации сборщиков.
Совпадение и параллельность осей шпинделей в вертикальной плоскости, как в предыдущей схеме, можно обеспечить методами взаимозаменяемости, т.е. точным изготовлением деталей по размерам В1 - В3, β1 - β3, пригонкой или применением компенсаторов.
В схеме компоновки, приведенной на рис. 2.б, головку 2 крепят к вертикальной торцевой плоскости плиты. Базовые плоскости станины для
10

головок 1 и 2 расположены взаимно перпендикулярно. Каждая головка имеет при установке по три степени свободы. Это дает возможность обеспечить совпадение осей шпинделей в вертикальной и горизонтальной плоскостях и их параллельность в горизонтальной плоскости выверкой положения расточных головок. И лишь параллельность осей шпинделей в вертикальной плоскости обеспечивается точным изготовлением деталей по угловым размерам β1 –β3.
В схеме компоновки, показанной на рис. 2.в, головка 2 установлена на боковой вертикальной плоскости плиты. Каждая из головок имеет три степени свободы во взаимно перпендикулярных плоскостях, что дает возможность обеспечить все требования точности к относительному положению сборочных единиц выверкой их положения.
Если компоновочные схемы равноценны с точки зрения удобства эксплуатации и габаритных размеров, тогда выбор наилучшей схемы компоновки будет зависеть от результатов экономических расчетов: принимается вариант схемы, обеспечивающей минимальную стоимость изготовления машины.
Наиболее простую и дешевую сборку обеспечивает схема, приведенная на рис. 1, т.к. она требует выверки, пригонки или регулирования. Наиболее трудоемкой будет сборка по схеме, приведенной на рис. 2.в. Зато схема, приведенная на рис. 1, потребует больших затрат
на механическую обработку деталей для обеспечения необходимой точности размеров В1 - В3, В′1 - В′3 и β1 - β3, β′1 - β′3.
11

4. РАЗМЕРНЫЙ АНАЛИЗ СБОРОЧНОЙ ЕДИНИЦЫ
Проведем размерный анализ шестеренного масляного насоса трактора (рис. 3), [13].
Рис.3.Схемы размерных цепей шестеренного насоса
12

Насос предназначен для подачи смазки к трущимся поверхностям деталей трактора под давлением 0,6 МПа, в объеме не менее 30 л/мин при частоте вращения зубчатых колес 2350 об/мин.
При изготовлении насоса необходимо обеспечить с требуемой точностью:
-радиальный зазор между зубчатыми колесами и корпусом насоса;
-зазор между корпусом и торцами зубчатых колес (торцовый зазор);
-боковой зазор между зубьями зубчатых колес;
-зазор между торцом оси ведомого зубчатого колеса и крышкой корпуса;
-зазор между корпусом и торцом ведомого зубчатого колеса; плотность контакта зубьев; легкость вращения зубчатых колес.
Первые пять задач могут быть решены при помощи размерных цепей А, Б, В, Г и Д (рис. 3). Плотность контакта зубьев зубчатых колес зависит от относительного поворота образующих эвольвентных поверхностей зубьев в двух координатных плоскостях.
Для легкого вращения зубчатых колес необходимо, чтобы между торцами колес, корпусом и крышкой был выверен зазор не меньше толщины масляной пленки. Для этого должны быть обеспечены с соответствующей точностью расстояния между дном корпуса и торцами колес и поворот их относительно дна корпуса. Эти задачи позволяют решить в одной из координатных плоскостей размерные цепи Б и γ
(рис. 4,а).
Необходимо также, чтобы были соблюдены требуемые зазоры в подшипниках, зависящие от диаметральных размеров отверстий втулок и валика (рис. 4,а, размерная цепь Е) и от точности относительного смещения и поворота осей отверстий в двух координатных плоскостях. Эти задачи могут быть решены в одной из координатных плоскостей при помощи размерных цепей К и µ (рис. 4,б).
Выявленные размерные цепи дают возможность выбрать методы достижения точности каждого из перечисленных параметров и оценить правильность простановки размеров и допусков на чертежах деталей насоса.
13

Рис.4.Схемы размерных цепей шестеренчатого насоса
14

Например, радиальный зазор А∆ (рис. 4) описывается следующим уравнением размерной цепи А:
А = -А1+А2+А3+А4+А5. |
(2) |
Подставив номинальные значения составляющих звеньев из |
|
чертежей деталей, получим |
|
А = -48,75+0+0+0+4,75=0. |
(3) |
После допуска замыкающего звена при расчете по методу полной взаимозаменяемости
|
TA p = m∑−1TAi =17 +30 +72 +50 +50 = 219мкм. |
(4) |
|||
|
|
i=1 |
|
|
|
Координаты середины поля допуска этого звена |
|
||||
0А = 0А1 + |
0А2 + |
0А3 + |
0А4 + |
0А5 =8 +0 +0 +0 +100 =108мкм. |
(5) |
Верхнее и нижнее предельные отклонения |
|
||||
ВА р = |
0А Р +0,5ТА р =108 +0,5 219 = 218мкм. |
(6) |
|||
НА р = |
0А Р −0,5ТА р =108 −0,5 219 = 2мкм. |
(7) |
|||
Техническими |
условиями |
на |
насос зазор задается в пределах |
70-150 мм. Таким образом, при значениях допусков на размеры деталей, заданных чертежами, невозможно получить требуемый радиальный зазор методом полной взаимозаменяемости.
Проверим возможность достижения радиального зазора в требуемых пределах по методу неполной взаимозаменяемости при риске 0,25% ( t=3) и при условии, что рассеяние погрешностей составляющих звеньев подчинено закону Гаусса ( λAi=1/9). При этом целесообразно несколько уменьшить зазор в подшипниках, который обычно назначается для насосов среднего давления в пределах 0,002-0,003 от диаметра вала. Для вала
15

диаметром 15 мм можно считать допустимым зазор в подшипниках от 30 до 45 мкм. Изменив в соответствии с этим значение допуска ТА3, при расчете точности радиального зазора по методу неполной взаимозаменяемости можно получить погрешность
ТА = t |
m∑−1λAi TAi |
2 =3 (172 +302 + 452 +502 )/9 =90мкм. |
(8) |
|
i=1 |
|
|
причем ВА
НА
=108 +0,5 90 =153мкм
=108 −0,5 90 = 63мкм
Таким образом, при условии, что допуск на зазор в подшипниках изменен, радиальный зазор в насосе можно обеспечить методом неполной взаимозаменяемости при риске 0,27%, если при заданном объеме выпуска такой риск приемлем.
Аналогично можно найти метод решения каждой из сформулированных выше задач и, если нужно, внести необходимые коррективы в чертежи деталей.
Кроме нахождения метода достижения точности замыкающего звена, размерный анализ позволяет определить последовательность сборки узла. Например, последовательность сборки насоса рассматриваемой конструкции существенно зависит от того, каким методом обеспечивается соосность отверстий подшипников скольжения вала.
Минимальный зазор в подшипниках, как было установлено выше, должен составлять 30 мкм, наименьшая толщина масляного слоя в любой точке касания вала не должна быть меньше 10мкм. Следовательно, для компенсации отклонения от соосности отверстий втулок остается 30-10=20 мкм. Отклонение от соосности отверстий втулок состоит из относительного смещения К и поворота µ их осей в двух координатных плоскостях (см. рис. 4,б)
Допуски на размеры деталей, заданные на чертежах, составляют:
звено |
К1К4 |
К2 |
К3 |
µ1µ4 |
µ2 |
µ3 |
допуск, мкм |
50 |
70 |
150 |
20/45 |
100/45 |
70/45 |
Если зазор в подшипниках полностью использовать для компенсации погрешностей только в одной из координатных плоскостей, то допуски замыкающих звеньев размерных цепей К и µ составляют
16

ТХ = 10 мкм и Тµ = 100/45 мкм/мм.
Согласно допускам на размеры деталей, указанным на чертежах, образуются следующие значения погрешностей К и µ :
ТК Р = 50+70+150+50 = 320 мкм; |
|
Тµ Р = (20+10+70+20)/45 = 210/45 мкм/мм. |
(9) |
Очевидно, что в этом случае для обеспечения требуемого зазора в подшипниках нельзя использовать ни один из методов взаимозаменяемости. Нельзя достичь этого и уменьшением допусков, поскольку это уменьшение должно быть очень значительным и сильно усложнит изготовление деталей.
Метод регулирования в данном случае также неприемлем. Следовательно, возникшую задачу, даже при большой программе выпуска, следует решать методом пригонки. При этом целесообразна расточка отверстий во втулках в сборе, обеспечивающая необходимую точность размеров, формы и относительного положения отверстий.
17

5. СЛУЖЕБНОЕ НАЗНАЧЕНИЕ ИЗДЕЛИЯ. ПЕРЕХОД ОТ СЛУЖЕБНОГО НАЗНАЧЕНИЯ ИЗДЕЛИЯ К ТЕХНИЧЕСКИМ УСЛОВИЯМ НА ОТДЕЛЬНЫЕ ДЕТАЛИ. ПРИМЕРЫ
Пример 1. Разработка служебного назначения плунжерного насоса.
Под служебным назначением понимается максимально уточненная и четко сформулированная задача, которую решает машина (изделие).
Служебное назначение плунжерного насоса – перекачивание жидкости. Насос выполнит свое служебное назначение, если будет соответствовать параметрам, характеризующим его качество.
Такими параметрами являются давление и производительность, которые должны быть заданы количественно, с допустимыми отклонениями:
Р = 50+5 атм, Q = 30 л/с.
На основе служебного назначения изделия выявляют:
1. Функциональные параметры. Для плунжерного насоса таким параметром является зазор в плунжерной паре (рис. 5).
Рис.5.Схема и размерная цепь плунжерной пары
Величину минимального зазора определяют тепловые деформации, а максимальная величина зазора зависит от интенсивности износа, расчетных сроков службы, а также условий недопустимости катастрофического износа и падения производительности.
18

Переход от параметров служебного назначения к функциональным параметрам производится на основе расчетов, исследований, опыта [3].
2. Технические условия. Технические условия на сборочную единицу устанавливают исходя из служебного назначения изделия и его функциональных параметров на основе технико-экономических расчетов.
Необходимо учитывать при этом следующее:
-возрастание себестоимости и трудоемкости изделия с «ужесточением» технических условий на его изготовление (рис. 6,б);
-возрастание расходов на эксплуатацию более дешевого варианта
изделия с «заниженными» техническими требованиями в связи с ростом замен частей, сокращением сроков эксплуатации до ремонта (рис. 6,в).
Таким образом, существует некоторое оптимальное значение допуска (технического условия), обеспечивающее минимальные суммарные расходы на изготовление и эксплуатацию изделия (рис. 6,а).
Следовательно, максимальный зазор в новом изделии (плунжерный насос) недопустим (нельзя весь допуск на зазор отдать изготовителю).
Для плунжерной пары (рис. 5) назначают:
- функциональные параметры: Zном = 0, Zmin =0,0096, Zmax 0,3;
-технические условия на сборочную единицу: Z = 0 ++00,,3095
3.Служебное назначение деталей входящих в изделие, формируется исходя из служебного назначения изделия и технических условий на его изготовление на основе построения и анализа конструкторских размерных цепей.
4.Технические условия на отдельные детали определяются на основе расчета сборочных размерных цепей и выбора детали методов достижения точности.
Последовательность перехода от служебного назначения изделия к техническим условиям на сборочную единицу и отдельные детали можно представить в виде схемы (рис.7).
19

Рис.6. Графическое представление взаимосвязи точности изделия с себестоимостью и
расходами на эксплуатацию
20

Рис.7.Схема перехода от служебного назначения изделия к техническим условиям на сборочные единицы и детали
Пример 2. Формулировка служебного назначения специального станка.
Специальный горизонтальный фрезерный полуавтомат предназначен для фрезерования поверхностей К стоек (рис. 8).
После обработки на станке деталь должна иметь:
21

Рис. Схема базирования стойки при фрезеровании поверхности К
1)размер А - 0,12 мм;
2)перпендикулярность поверхности К установочной базе (допустимое отклонение от перпендикулярности ±0,05/300);
3)плоскостность поверхности К в пределах 0,03 мм;
4)шероховатость 2,5 .
Параметры качества и точности детали получают на станке при колебании припуска на обработку от 0,5 до 1,2 мм, колебании твердости в пределах НВ 180-220 и температуры – в пределах 15-45ºС.
Напряжение сети 380 В. Обработка деталей будет осуществляться на режиме: V = 50 м/мин; S = 0,05 мм/об.
Производительность обработки должна быть не менее 30 шт/ч. Шум не более 70 децибел; срок службы станка – 6 лет.
Пример 3. Разработка технических условий на изделие (станок).
В результате обработки деталей на станке необходимо обеспечить перпендикулярность поверхности К установочной базе (рис. 9):
номинал заданного параметра точности β = 90º;
допуск .β = 0,1/300;
координата середины поля допуска º β = 0. Получаемый в процессе обработки размер
βдет =βу +βст +βд |
или900 = 00 +900 +00 , |
где: βдет – номинальное значение заданного параметра; βy – номинальная величина погрешности установки; βст – номинальное значение технического
22

условия на станок; βд – номинальная величина отклонения обрабатываемой поверхности (погрешность динамической настройки).
Рис. 9. Схема технологической размерной цепи фрезерной операции
Погрешность установки, связанную с базированием и закреплением назначают исходя из принятой схемы установки [9-10]:
βy = ±0,005/300 мм.
Погрешность динамической настройки для данного режима обработки и диапазона колебания припуска и твердости [9-10]:
βд = + 0,02/300 мм.
В связи с тем, что допуски на βi даны в виде tgβi, при расчете допусков на повороты поверхностей их вначале необходимо привести к одной длине катета (общему знаменателю). Затем, отбросив знаменатель, можно использовать методику расчета для линейных размеров [11].
После расчета допусков следует добавить отброшенный знаменатель:
βдет =βу +βст +βд и δдет = δβу +δβст +δβд или
0,1 = 0,01+δβст +0,02, отсюда δβст = 0,07 /300
Координата середины поля допуска замыкающего звена
0 = 0 + βст +0,01, отсюда βст = −0,01/300
23

Таким образом,
δβст =900+−0,0250,045 /300
Схема расположения предельных отклонений технического условия на изделие (станок) приведена на рис. 10.
Для обеспечения заданной долговечности часть допуска размера статической настройки выделяют на компенсацию износа, а часть – на компенсацию погрешностей обработки. Из величины δβст = 0,07/300
выделяют на изготовление – 0,04 мм и эксплуатацию – 0,03 мм.
Размер на изготовление станка βст =900+−0,010,03 /300
Итак, исполнительная поверхность инструмента должна быть перпендикулярна установочной плоскости станка.
Допустимое отклонение +−00,,0103 на длине 300 мм.
Пример 4. Выбор метода достижения точности замыкающего звена.
Переход от служебного назначения изделия к техническим условиям на отдельные детали.
Задача. Рассчитать и установить допуски на относительные повороты поверхностей деталей технологической системы горизонтально-фрезерного станка с целью достижения требуемой перпендикулярности исполнительной поверхности инструмента к установочной поверхности станка.
Исходные данные:
β = 90º; δβΔ = 0,04/300; º = -0,01/300.
Схема размерной цепи, с помощью которой решается поставленная задача, представлена на рис. 10.
При построении размерной цепи необходимо руководствоваться рекомендациями [11, 12, 13]. В частности, при изображении размерной цепи, определяющей относительные повороты поверхностей, необходимо выполнять условие: стрелки должны идти от вспомогательных баз к основным и сходиться на базовой детали.
24

Рис.10. Схема расположения предельных отклонений
Для определения увеличивающих и уменьшающих звеньев принимаем в качестве исходного направления поворот против часовой стрелки вспомогательной базы относительно основной. Если при этом размер 90º у замыкающего звена увеличивается, то звено является увеличивающим.
Правильность простановки номинальных размеров устанавливается из решения уравнения размерной цепи (рис. 11):
11.Схема технологической размерной цепи фрезерной операции
β = β1 + β2 + β3 + β4 +β5 или 90º = -0 º - 0 º - 0 º + 0 + 90 º. |
(10) |
25
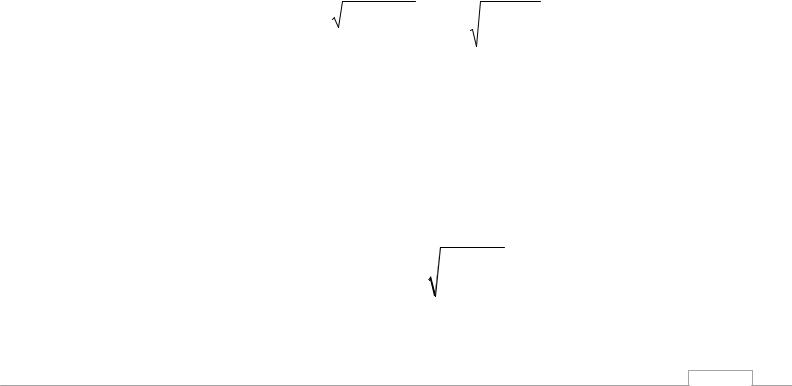
Следовательно, номиналы проставлены, верно.
Рассмотрим возможность применения метода полной взаимозаменяемости [1, 11].
Средний допуск составляющих звеньев
δβ ñð = |
δ |
|
= |
0,04 |
|
= 0,008/ 300 |
(11) |
|
m −1 |
6 −1 |
|||||||
|
|
|
|
Сопоставление этого допуска с параметрами средне экономической точности, получаемыми при обработке плоскостей различными методами [10], показывает, что изготовление деталей с отклонениями, не выходящими за пределы рассчитанного среднего допуска, экономически целесообразно. Поэтому необходимо отказаться от метода полной взаимозаменяемости.
Рассмотрим возможность применения метода неполной взаимозаменяемости. Принимаем следующие исходные данные:
Закон рассеяния размеров близок к закону Гаусса [1]:
λñð/ = 19
Допустимый процент брака
Р = 1%; t = 2,57.
Средний допуск составляющих звеньев для этих исходных данных:
δβ ñð |
= |
|
δ |
= |
|
0,04 |
|
(12) |
||
t |
λñð/ (m −1) |
|
|
1 |
|
|
||||
|
|
2,57 |
(6 |
−1) |
||||||
|
|
|
|
9 |
Этот средний допуск можно считать экономически приемлемым. Скорректируем его с учетом сложности изготовления составляющих
звеньев: δβ1 = 2,0; δβ2 = 0,02/300; δβ3 = 0,02/300; δβ4 = 0,03/300; δβ5 = 0,015/300.
Назначенные параметры точности составляющих звеньев приведены в табл.1.
Допуск на замыкающее звено определяется из уравнения
δβΔ =t |
m∑−1λi/ δβ2i |
|
i=1 |
26

Таблица 1
Параметры точности составляющих звеньев
27

0,04 = 2,57 1/ 9(δβ1 |
2 + 0,022 + 0,022 + 0,032 + 0,0152 ) |
(13) |
Отсюда техническое условие на изготовление приспособления
δβ1 = 0,015/300
Устанавливаем координаты середин полей допусков:
оβ = m∑−1 |
0 βi |
(14) |
i=1 |
|
|
ºβ = -0,01/300 (заведомо гарантируемый наклон оси шпинделя); ºβ = 0 (так удобно); ºβ2 = ºβ3 = ? (принимаем за неизвестное);
ºβ4 = -0,015/300;
ºβ5 = 0.
После подстановки числовых значений координат середины полей допусков получим:
-0,01 = -0 - ºβ2 - ºβ3 + (-0,015) + 0. |
(15) |
Отсюда 2 ºβ2 = -0,005; ºβ2 = ºβ3 = -0,0025/300.
Параметры точности изделия и технические условия на детали
представлены в табл. 2.
Таблица 2
Параметры точности изделия и технические условия на детали
Расчеты |
Т-эконом. Соображения, деление |
На основе выбора |
|
|
допуска на изготовление и |
метода достижения |
|
|
эксплуатацию |
точности |
|
Служебное |
Функц. параметр |
ТУ на |
ТУ на отдельные |
назначение |
|
сборочную |
детали |
|
|
единицу |
β1 = 0º ± 0,0075/300 |
Эксплуатационные |
β = 90 −+00,,025045 /300 |
β =90 −+00,,0103 /300 |
|
параметры |
|
|
β2 = 0º −+00,,00750125 /300 |
β =90º ± 0,05/300 |
|
|
и т.д |
|
|
|
28

Пример 5. Метод регулирования.
В случае, если методы полной и неполной взаимозаменяемости неприемлемы для достижения точности и замыкающего звена, может быть использован метод регулирования.
Задача. Обеспечить суммарный зазор в подшипниковом соединении в пределах 0 ++00,,0802 методом регулировки, используя неподвижный компенсатор
(рис. 12).
Рис.12.Схема размерной цепи подшипникового узла
Замыкающее звено (зазор): А =0 ++00,,0802
1. Правильность простановки номинальных размеров проверяем по формуле
m |
|
A = ∑ξ Ai |
(16) |
i=1
0 = 65 – (12,5 + 40 +12,5).
2. Устанавливаем экономичные допуски на составляющие звенья
(табл. 3).
|
|
Допуски на составляющие звенья |
Таблица 3 |
|
|||
|
|
|
|
|
|
||
|
|
|
|
|
|
|
|
|
Допуск |
А1 = А3 = 12,5 |
А2 = 40 |
А4 = 65 |
|
||
|
|
0,01 |
0,05 |
0,07 |
|
|
|
|
Координата |
|
|
|
|
|
|
|
середины поля |
- 0,005 |
- 0,025 |
- 0,035 |
|
|
|
|
допуска |
|
|
|
|
|
|
|
Размер на |
12,5- 0,01 |
40- 0,05 |
65+ 0,07 |
|
|
|
|
чертеже |
|
|
|
|
|
|
|
|
|
|
|
|
|
|
|
|
|
|
|
29 |
|
|
|
|
|
|
|
|

3. В качестве компенсатора принимаем ролики (в связи с наибольшей
технологической простотой их изготовления).
В данном случае целесообразно применить прием: удалить из размерной цепи компенсаторы, а зазор между цапфой и наружным кольцом
В = А4– А2 = 65 – 40 = 25.
Получим размерную цепь (рис. 13).
Любую размерную цепь можно свести к полученной трехзвенной цепи, просуммировав все увеличивающие и уменьшающие звенья.
Рис.13. Схема размерной цепи А
4. Рассчитаем возможные верхние |
'В и нижние |
'Н отклонения |
||
размера В: |
|
|
|
|
→ |
|
← |
|
|
'В = ∑ βi − ∑ |
|
|
Hi |
|
→ |
|
← |
|
|
'Н = ∑ ' Hi −∑ |
|
βi |
(17) |
Штрихами обозначены расширение, экономически приемлемые
допуски и координаты середины их полей относительно номиналов. Получим:
'В = 0,07 – (– 0,05) = 0,2;
'Н = 0 – 0 = 0.
Таким образом: В = 25+0,12 5. Рассчитаем максимально возможную величину компенсации:
δк = m∑−1δi −δ = (0,01+0,05 +0,01+0,07) −0,06 = 0,08
i=1
6.Число ступеней компенсаторов
30

N / = |
|
δK |
+1 = |
0,08 |
+1 = 3 |
(19) |
|
δ |
−δком |
0,06 −0,02 |
|||||
|
|
|
|
Допуск на компенсатор принят равным 0,02 мм, так как компенсатор-
ролик дважды фигурирует в размерной цепи.
7. Рассчитаем предельные отклонения компенсатора:
Вкг = |
/ В |
− |
β |
+δком = 0,12 −0,08 +0,02 = 0,06 |
|
Нкг = |
/ Н |
− |
Н |
−δком = 0 −0,02 −0,02 = −0,04 |
(20) |
Компенсатор может принимать значения:
2АК=25 +−00,,0604
8. Рассчитаем размеры компенсатора для каждой ступени компенсации, учитывая, что колебание размера В необходимо разбить на три интервала (3 ступени компенсации), а для каждого интервала размера В (для каждой ступени компенсации) определяют такие значения размеров роликов, при которых выдерживается допуск замыкающего звена:
А = 0 +−00,,0804
Тогда допуск на компенсатор составит:
δ1ком = δ3ком = 0,02 / 2 = 0,01
Разобьем колебание размера В на три интервала:
1)В = 25 ++00,,0400
2)В = 25 ++00,,0804
3)В = 25 ++00,,1204
Определим значении размеров роликов для каждой ступени компенсации (рис. 14).
Для 1 ступени:
Верхнее отклонение замыкающего звена
В.О.А. = В.О.В. – Н.О.2АК.
Отсюда
Н.О. 2АК = В.О.В. – В.О.А. = + 0,04 – 0,08 = – 0,04.
Нижнее отклонение замыкающего звена Н.О.А = Н.О.В. – В.О.2АК.
31

Рис.14.Схема размерной цепи для определения размеров роликов
Отсюда
В.О.2АК = Н.О.В. – Н.О.А. = 0 – 0,02 = – 0,02.
Для 2 ступени:
Н.О.2АК = + 0,08 – 0,08 = 0; В.О.2АК = + 0,04 – 0,02 = 0,02.
Для 3 ступени:
Н.О.2АК = + 0,12 – 0,08 = + 0,04; В.О.2АК = + 0,08 – 0,02 = + 0,06.
9.Составим таблицу значений размеров роликов, необходимых для осуществления техпроцесса сборки.
10.Определим необходимое количество роликов в каждой ступени
исходя из предположения, что рассеяние размеров А2 и А4 подчиняется закону Гаусса (рис. 15).
Рис.15.Распределение размеров компенсаторов
Рассеяние размера В в этом случае также будет подчиняться закону Гаусса. Необходимое количество роликов (в процентах) определится значением коэффициента t;
t = |
X |
, |
(21) |
|
|
|
|
||||
|
σ |
|
|
|
|
где: х – отклонение размера В (величина интервала поля |
рассеяния); |
|
|||
σ – среднеквадратичное отклонение (мера рассеяния) размера В. |
|
|
|
||
|
|
|
|
|
|
|
|
|
|
32 |
|
|
|
|
|
|

Величину σ можно определить из соотношения [1] |
|
||
Ω=±3σ |
(22) |
||
Отсюда |
0,12=6σ |
(23) |
|
Тогда |
0,12 |
|
|
σ = |
= 0,02 |
|
|
6 |
|
||
|
|
|
Подставив численные значения х и σ , получим следующие значения коэффициента t для 2 интервала размера В (второй ступени компенсации):
t = |
2X |
= |
2 0,02 |
= 2 |
(24) |
|
σ |
|
0,02 |
|
|
Этому значению коэффициента t соответствует процентное количество роликов для 2 ступени компенсации [1]:
Р = 68,26 %.
Для 1 и 2 ступеней необходимо для сборки роликов по 15,87 % от общего количества.
Цапфу и наружное кольцо необходимо изготовить с размерами
Ø40 – 0,05 и Ø65 + 0,07.
Компенсаторы (ролики) изготавливают 3 типоразмеров со значениями диаметров, приведенными в табл. 3. При этом число роликов 2 типоразмера составит 68,26 % от их общего количества, необходимого для сборки.
В процессе сборки без какого-либо выбора устанавливают в изделие цапфу и наружное кольцо. Измеряют зазор между ними или вычисляют разность их размеров (т.е. определяют размер В).
По табл. 4 определяют, в какую ступень компенсации попал полученный размер В.
Из тары выбирают соответствующий типоразмер ролика и устанавливают в сборочную единицу.
|
Значения размеров компенсаторов |
Таблица 4 |
|||
|
|
||||
|
|
|
|
|
|
№ |
В= 25+0,12 |
2А= 25−+0,040,06 |
Размеры |
|
% роликов каждого |
ступени |
|
|
роликов |
|
типоразмера |
I |
25+0,000,04 |
25−−0,040,02 |
12,5−−0,020,01 |
|
15,87 |
II |
25++0,040,08 |
25+0,000,02 |
12,5+0,000,01 |
|
68,26 |
III |
25++0,080,12 |
25++0,040,06 |
12,5++0,020,03 |
|
15,87 |
|
|
|
|
|
|
33

6. АНАЛИЗ ТЕХНОЛОГИЧНОСТИ КОНСТРУКЦИИ ИЗДЕЛИЯ
Целью анализа технологичности конструкций и вносимых на его основе изменений является обеспечение возможности оптимальных затрат труда, средств, материалов и времени при технологической подготовке производства, изготовлении, эксплуатации и ремонте.
Основное внимание в проекте необходимо обратить на производственную технологичность, т.е. технологичность конструкции изделия с точки зрения его изготовления.
Анализ производится на основе ГОСТ 14.201-83 «Технологичность конструкции. Термины и определения», ГОСТ 2.116-84*, ГОСТ 14.205-83, «Правила обеспечения технологичности конструкции изделия», а также рекомендаций [2,4,5].
Впервую очередь оцениваются качественные характеристик технологичности конструкции (ГОСТ 14.004-83):
-взаимозаменяемость;
-регулируемость конструкции;
-контролепригодность конструкции;
-инструментальная доступность конструкции.
Впроекте необходимо дать качественную оценку соответствия конструкции следующим требованиям:
– Требования к составу:
1.Сборочная единица расчленяется на рациональное число составных частей на основе принципа агрегатирования.
2.Конструкция сборочной единицы обеспечивает возможность ее компоновки из стандартных и унифицированных частей без применения сложной технологической оснастки.
3.Виды используемых соединений, их конструкции и месторасположение отвечают требованиям механизации и автоматизации сборочных работ.
4.В конструкции сборочной единицы и ее составных частей, имеющих массу более 20 кг, предусматриваются конструктивные элементы для удобного захвата грузоподъемными средствами, используемыми в процессе сборки, разборки и транспортирования.
5.Конструкция сборочной единицы предусматривает базовую составную часть, которая является основной для размещения остальных составных частей.
6.Базовую составную часть выбирают удобной для правильной установки на рабочем месте сборки (в приспособлении, на рабочем столе, сборочной площадке и пр.). Компоновка конструкции сборочной единицы
34

должна позволять производить сборку при неизменном базировании составных частей.
В конструкции базовой составной части предусматривают возможность использования конструктивных сборочных баз в качестве технологических и измерительных.
Компоновка сборочной единицы обеспечивается:
1)общей сборкой без промежуточной разборки и повторных сборок составных частей;
2)удобным доступом к местам, требующим контроля, регулировки и проведения других работ;
3)легкосъемностью составных частей с малым ресурсом;
4)рациональным расположением такелажных узлов, монтажных опор и других устройств для обеспечения транспортабельности изделия.
– Требования к конструкции соединений составных частей: Наименьшее количество поверхностей и мест соединений составных
частей в конструкции.
Доступность мест соединения составных частей при механизации сборочных работ и контроле качества соединения.
Отсутствие сложной и необоснованно точной обработки сопрягаемых поверхностей соединения составных частей.
Недопустимость дополнительной обработки составных соединений в процессе сборки конструкции.
Рациональность методов закрепления деталей (запрессовка, пластическая деформация, точечная сварка и др.).
Обоснованность посадок и ограничение их количества.
Наличие комплектов основных и вспомогательных конструкторских баз, обеспечивающих определенность базирования.
Наличие конструктивных элементов для ориентации деталей.
– Требования к точности и методу сборки:
Точность расположения составных частей обуславливается точностью изготовления составных частей. Выбирают метод сборки для данного объема выпуска и типа производства на основании расчета и анализа размерных цепей.
При выборе метода сборки следует учитывать трудоемкость сборочных работ и затраты на изготовление составных частей с точностью, необходимой для данного метода сборки.
Примечание. Методы сборки располагаются по убывающей производительности труда сборочных работ в следующем порядке:
-с полной взаимозаменяемостью;
-с неполной взаимозаменяемостью;
35

-с групповой взаимозаменяемостью;
-с регулировкой компенсаторами;
-с пригонкой.
В конструкции предусматриваются устройства, обеспечивающие заданную точность относительного расположения составных частей (центрирующие, фиксирующие, компенсирующие).
Пределы регулирования и параметры компенсаторов рассчитываются на основе теории размерных цепей.
Компенсирующие, центрирующие и фиксирующие устройства имеют простую конструкцию, свободный доступ для рабочего и контрольного инструмента.
На основе выполненного анализа технологичности конструкции определяют необходимые конструктивные изменения, упрощающие сборку. В пояснительной записке необходимо обосновать, что вносимые изменения не снижают качества изделия.
По согласованию с руководителем в проекте проводится оценка абсолютных и относительных показателей технологичности согласно работам [2,4,15].
6.1.Примеры обработки изделий на технологичность
6.1.1.Снижение трудоемкости пригоночных работ
Применение метода пригонки позволяет снизить точность изготовления деталей, входящих в изделие, но приводит к необходимости выполнения пригоночных работ, требующих высокой квалификации сборщика.
Пригонка наиболее проста, если требуется пригонять только плотность прилегания детали по одной плоскости. Трудоемкость пригонки возрастает при прилегании деталей по одной плоскости. Трудоемкость пригонки возрастает при прилегании двух и более поверхностей, т.е., кроме плотности прилегания, обеспечивают точное взаимное расположение пригоняемой поверхности сопрягаемой детали. Пригонка наиболее сложна, когда, кроме плотности прилегания и взаимного расположения поверхностей, необходимо обеспечивать определенные размеры (рис. 16).
Значительное снижение трудоемкости пригоночных работ может быть достигнуто введением в конструкцию неподвижных компенсаторов(рис. 17).
Так, при общей сборке внутришлифовального станка совпадение по вертикали осей шпинделей шлифовальной бабки и передней бабки (рис. 17, а) достигалось шабрением основания корпуса шлифовальной бабки 1, а параллельность оси шлифовального шпинделя направляющим станины –
36

шабрением его «ласточкина хвоста» по заранее обработанному «ласточкину хвосту» поперечного суппорта 2(рис. 17, б).
Рис.16.Пример нетехнологичности выполнения пригоночных работ
Рис.17.Пример отработки конструкции узла внутришлифовального станка на технологичность
37

После введения в конструкцию неподвижного компенсатора 3, (рис. 17, в) выполненного в виде прокладки, и изменения формы поперечного суппорта (ликвидирован «ласточкин хвост» для корпуса шлифовальной бабки) совпадение осей шпинделей в вертикальной плоскости обеспечивается шлифованием компенсатора, а параллельность – поворотом шлифовальной бабки с фиксацией ее контрольными шпильками.
Трудоемкость данного этапа сборки сокращается в данном случае на
75 %.
6.1.2. Снижение трудоемкости регулировки
Введение неподвижных компенсаторов при использовании метода регулировки требует разборки собранного узла после измерения замыкающего звена и снятия компенсатора с целью его замены.
После этого выполняется повторная сборка. Таких сборок и разборок может потребоваться несколько. Это резко увеличивает трудоемкость регулировочных и пригоночных работ и отрицательно сказывается на качестве деталей и выполняемых соединений.
Необходимо, чтобы конструкция обеспечивала возможность снятия компенсатора при минимальной разборке первоначального собранного узла (рис. 18). Так, при сборке узла с парой конических шестерен (рис. 18,а) необходимо:
-установить в корпус подшипник 1;
-надеть на шестерню 2 компенсатор К1 и запрессовать ее в подшипник;
-поставить промежуточные кольца 3 и 4, предварительно совместно прошлифованные по высоте;
-напрессовать подшипник 5 на шестерню, одновременно введя его наружное кольцо в корпус;
-собрать остальные детали 6, 7, 8.
После сборки шестерни 2 можно приступить к сборке шестерни 9. Для этого необходимо:
-установить в корпус подшипник 10;
-поставить компенсатор и шестерню 9;
-запрессовать в подшипник валик с установленной в него шпонкой;
-надеть промежуточную втулку (поз. 12);
-напрессовать подшипник 13 на валик, одновременно введя наружное кольцо подшипника в корпус;
38

Рис. 18. Пример отработки конструкции узла конических шестерен на технологичность
- заложить в валик шпонку, надеть на шестерню 14 и закрепить ее винтом 16 через шайбу 15.
39

После измерения полученной величины замыкающего звена и определения требуемой величины размера компенсатора, необходимо провести полную разборку узла и, установив нужный компенсатор, выполнить вторичную сборку.
Значительно упрощает регулировочные работы изменение конструкции узла (рис. 18,б) и использование в качестве компенсатора К1 набора прокладок.
Для замены компенсатора К1 в измененной конструкции узла необходимо отвернуть винт 17 и снять подузел шестерни 2, а для замены компенсатора К2 – отвернуть гайку 18, сняв шайбу 19 и шестерню 9.
Кроме того, появляется возможность параллельной сборки подузлов шестерен 2 и 9.
Наиболее рациональными, с точки зрения трудоемкости сборки, являются конструкции с подвижным компенсатором.
Предпочтительны конструкции, в которых регулировка точности взаимного расположения деталей или узлов достигается без применения в качестве подвижных компенсаторов специальных деталей, т.е. когда подвижным компенсатором является сама рабочая деталь или узел. Этот принцип реализован в конструкции восьмишпиндельных вертикальных полуавтоматов (рис. 19). Установка шпинделей 3 на заданном расстоянии А от оси шпиндельного блока 1, установленного на корпусе колонны 2, а также на одинаковый угол по окружности относительно друг друга. Роль подвижных компенсаторов выполняют сами шпиндели в сборе.
При регулировке они перемещаются по окружности и в радиальном направлении за счет боковых зазоров между фланцевыми втулками на шпинделе и стенками отверстий шпиндельного блока. По окончании регулировки и после контрольной проверки положение шпинделей фиксируется контрольными штифтами.
Рис. 19. Схема регулировки токарного восьмишпиндельного полуавтомата
40

6.1.3. Снижение трудоемкости выполнения соединений деталей и узлов
Наиболее эффективным мероприятием в этом направлении является уменьшение числа деталей в узле. Пример удачного изменения конструкции механизма переключения шестерен токарного станка приведен на рис. 16. В исходной конструкции (рис. 20,а) этот механизм состоял из рукоятки 1, насаженной на ось 2. шестерни 3, сцепляющейся с рейкой 4. Рейка скользила по направляющей планке 5. Переводной сухарь 6 был привернут к рейке 4. В измененной конструкции (рис. 20,б) перевод шестерен производится рычагом 2, заштифтованным на оси рукоятки 1. Переводной сухарь 3 устанавливают по скользящей посадке на пальце 4 запрессованном в рычаге 2.
Соединяемые детали необходимо сопрягать по минимальному количеству поверхностей, обеспечивающему определенность заданного взаимного их расположения.
Рис. 20. Пример обработки конструкции узла на технологичность уменьшением числа деталей в узле.
Примеры необходимого и достаточного количества сопрягаемых поверхностей, определяющих взаимное расположение деталей, приведены на рис. 21.
41

Рис. 21. Примеры необходимого и достаточного количества сопрягаемых поверхностей.
Повышение необходимого числа сопрягаемых поверхностей ведет к резкому увеличению трудоемкости сборки (рис. 21,б-г). Следует отметить, что такое трудоемкое соединение, как сопряжение по конусу к торцу, необходимо, когда длина конуса недостаточна для того, чтобы исключить перекос сопрягаемых деталей, в частности при центрировании планшайб на шпинделях револьверных станков.
Значительно снижают трудоемкость сборочных работ средства механизации. Поэтому конструкцией обеспечивают возможность подвода механизированного инструмента к местам выполнения соединений. Эффективность применения средств механизации повышается если в одном узле элементы крепежных деталей нормализованы и унифицированы.
42

7. РАЗРАБОТКА ТЕХНОЛОГИЧЕСКИХ СХЕМ СБОРКИ
Технологическая схема сборки показывает, в какой последовательности необходимо выполнять соединение и закрепление деталей и узлов, из которых состоит изделие.
Деталь – первичный элемент изделия, характерным признаком которого является отсутствие в нем разъемных и неразъемных соединений.
Узел представляет собой элемент изделия, состоящий из двух и более деталей, соединенных в одно целое, вне зависимости от вида соединения – разъемное или неразъемное. Характерный признак узла с технологической точки зрения – возможность сборки его независимо от других элементов изделия.
Изделие представляет собой продукт конечной стадии машиностроительного производства. Изделие может быть машина, узел или деталь, в зависимости оттого, что является объектом данного производства.
Для удобства составления технологических схем сборки все узлы, входящие в изделие, условно делят на группы и подгруппы 1-го, 2-го и т.д. порядков. При этом группой считают узел, непосредственно входящий в изделие.
Подгруппой 1 порядка считают узел, входящий в группу.
Подгруппой 2 порядка считают узел, входящий в подгруппу первого порядка и т.д.
Сборку изделий-продуктов конечной стадии данного производства называют узловой сборкой.
В учебных пособиях [2,4] подгруппы называют подузлами, а за группой сохраняет название “узел”. Элементарную сборочную единицу, состоящую из базовой детали и присоединенной к ней хотя бы одной детали, называют комплектом. Эта терминология допустима в курсовых и дипломных проектах. Следует помнить, однако, что группа, а также подгруппа (подузел) либо порядка представляет собой соединение из нескольких деталей, т.е. узел.
Технологическая схема сборки в наглядной графической форме выражает маршрут узловой и общей сборки, значительно облегчает последующее проектирование технологического процесса сборки, позволяет оценить технологичность конструкции изделия с точки зрения возможности расчленения сборки на узловую и общую.
Последовательность общей сборки изделия определяется:
-конструктивными особенностями;
-методами достижение требуемой точности конструкции;
-принятой формой организации производства.
При разработке технологической схемы сборки руководствуются следующими указаниями.
43

1.По чертежам изделия и спецификации необходимо выявить все составляющие ее сборочные единицы (узлы, подузлы, комплекты). Наибольшее количество ошибок делается при выявлении единиц (узлов). Характерным признаком узла (т.е. любой сборочной единицы изделия) является возможность сборки его независимо от других элементов изделия. Сборка узла является незаконченной, если сделано присоединение деталей друг к другу, но не выполнено их закрепление. Узел после сборки должен представлять собой единое целое, не распадающееся при перемене положения. Так, соединение вала со втулкой по посадке скольжения не является узлом. При изменении положения, например, при транспортировании такой узел может распасться на составляющие его детали.
При разбивке изделия на сборочные единицы руководствуются следующими соображениями [2]:
-сборочная единица не должна быть слишком большой по габаритным размерам и массе или состоять из значительного количества деталей и сопряжений; в то же время излишнее “дробление” машины на сборочные единицы не рационально, так как это усложняет процесс комплектования при сборке, создает дополнительные трудности в организации сборочных работ;
-если в процессе сборки требуется проведение испытаний, обкатка, специальная слесарная пригонка части изделия, это обуславливает целесообразность выделения ее в особую сборочную единицу;
-сборочная единица при следующем монтировании ее в машине не должна подвергаться какой-либо разборке, а если этого избежать нельзя, то соответствующие разборочные работы необходимо предусмотреть в технологии;
-большинство деталей машины, исключая ее главные базовые детали (станины, раму и пр.) а также крепежные детали должны войти в те или иные сборочные единицы, с тем, чтобы сократить количество отдельных деталей, подаваемых непосредственно на общую сборку;
-трудоемкость сборки для большинства сборочных единиц должна быть примерно одинаковой.
Для выявления сборочных единиц необходимо выполнить разборку изделия, установив при этом, какие части изделия можно снять в собранном виде.
2.Общую сборку изделия и сборку любой сборочной единицы следует начинать с установки на сборочном стенде или конвейере базирующей детали, в ряде случаев роль базирующей детали может выполнять комплект или даже более сложная сборочная единица.
3.Смонтированные в первую очередь сборочные единицы и детали не должны мешать установке последующих деталей и сборочных единиц.
44

4.В первую очередь необходимо монтировать сборочные единицы и детали, выполняющие наиболее ответственные функции в работе изделия.
5.При наличии параллельно связанных размерных цепей сборку следует начинать с установки тех сборочных единиц и деталей, размеры или относительные повороты поверхностей которых являются общими звеньями
ипринадлежат большему количеству размерных цепей.
6.Конструкции большинства машин не позволяют вести их сборку без предварительной частичной разборки их сборочных единиц, поступающих на общую сборку в собранном виде. Поэтому при построении схемы сборки в нее необходимо включать и все неизбежные по ходу технологического процесса разборки сборочные единицы.
7.Для облегчения построения схемы сборки рекомендуется мысленно выполнить разборку изделия и записать ее последовательность. Элементы и соединения, которые можно снять в неразобранном виде, представляют собой сборочные единицы. Произведя запись в обратном порядке получают технологическую схему общей сборки.
8.При составлении технологической схемы сборки необходимо рассмотреть возможные варианты последовательности сборки и выбрать лучший, т.е. обеспечивающий заданную точность, более удобный, производительный и экономичный.
Схему общей сборки изделия строят следующим образом.
Лист бумаги делят на зоны: деталей, комплектов, подузлов и узлов. Каждый элемент, входящий в изделие, обозначается прямоугольником,
разделенным на три части, в которых записывают:
-наименование элемента;
-количество данных элементов;
-индекс элемента.
В качестве индекса для детали принимают ее номер по спецификации. Для сборочных единиц – групп (узлов) – номер базовой детали по спецификации, перед которым ставят буквы СБ (например, СБ.5).
Для подгрупп (подузел) различных порядков – номер базовой детали по спецификации, перед которым ставят цифру, обозначающую порядок подгруппы и буквы СБ (например, 1СБ.16).
Местоположение условных обозначений деталей и сборочных единиц показывает последовательность из поступления на сборку.
Линии со стрелками обозначают направление их движения и характер выполняемого процесса сборки или разборки.
Технологическая схема сборки снабжается надписями, поясняющими основные работы, выполняемые при сборке. Короткие надписи делают на выносимых линиях, которые проводя от линии сборки. Длинные надписи выносят в примечания, которые обозначают порядковыми номерами, проставленными у места присоединения соответствующих прямоугольников
45

к линии сборки. Примеры надписей: шабрить, сверлить, развернуть, регулировать, пригнать перед сборкой, развернуть отверстия под штифты после пригонки рейки, застопорить обе гайки, завести фланец в отверстие суппорта и поворотом установить беззазорное зацепление: сверлить и развернуть отверстия под конический штифт; отрегулировать натяжку клина.
В прил.1 приведен пример технологической схемы общей сборки изделия – шпиндельного узла станка 1К282 (прил.2), а в прил.3 – технологические карты сборки фланца СБ.65 шпиндельного узла станка
1К282.
Перед составлением технологической схемы сборки следует изучить рекомендации и примеры, приведенные в [1 – 4.8,26].
46

8.РАЗРАБОТКА ТЕХНОЛОГИЧЕСКОГО ПРОЦЕССА СБОРКИ
8.1.Выявляют работы, выполняемые при сборке изделия, на основе анализа узловых чертежей деталей, а также конкретных условий, в которых выполняется сборка. К этим относятся:
−степень точности механической обработки деталей, поданных на сборку;
−состояние, в котором детали и узлы поданы на сборку;
−принятые технологические способы выполнения соединений;
−необходимые методы проверки выполняемых соединений и др.
По целевому назначению выполняемые при сборке работы можно разделить на следующие группы.
1.Механическая обработка, которая в силу различных причин выполняется в сборочном цехе;
−зачистка заусенцев;
−сверление мелких отверстий, нарезание резьб;
−совместная обработка нескольких деталей (сверление, развертывание отверстий под штифты)
−повышение точности геометрической формы поверхности ( например, шабрение плоскостей );
−притирка и доводка плоских, цилиндрических и конических сопряжений и др.
2.Распаковка, освобождения от консервации, промывка, продувка, притирка, смазка, осмотр, а в ответственных случаях – проверка соответствию узлов и деталей, поступивших на сборку, техническим требованиям на их изготовление.
3.изготовление простых деталей при сборке. К ним относятся: прокладки, пружины, цилиндрические штифты и др. Эти работы допустимы
вцехах единичного и мелкосерийного производства.
4. выполнение соединений деталей и узлов. Эта группа охватывает работы по выполнению разъемных и неразъемных, подвижных и неподвижных соединений, осуществляемые всеми технологическими способами.
Работа по выполнению соединения представляет собой сборочный переход. Он состоит из основного приема, во время, которого изменяется состояния объекта производства ( т.е осуществляется соединение ) и нескольких вспомогательных приемов, во время которых состояние объекта производство не изменяется, но которые не разрывно связаны с основным приемом.
Например, сборочный переход «напрессовать червяк на вал» состоит из следующих приемов: взять червяк и установить его на вал, включить пресс,
47

напрессовать червяк на вал, включить пресс. Здесь основным приемом является «напрессовать червяк на вал». Остальные – вспомогательные.
5.Работы обусловленные методами пригонки и регулировки. К ним относятся: измерение размера замыкающего звена: частичная разработка узла, состоящая из раскрепления и рассоединения деталей до тех пор, пока не будет снята компенсирующее звено: пригонка неподвижного компенсатора шабрением, шлифованием, точением или другими технологическими способами: разбор и установка компенсирующих колец, прокладок: регулировка положения подвижных компенсаторов с необходимыми измерениями замыкающих звеньев, откреплением и закреплением деталей и узлов: повторная сборка после частичной разработке и др.
6.Работа по проверки правильности выполнения соединений деталей и узлов в процессе сборке. К ним относятся: свободное вращение, диаметр отверстия втулки, запрессованый в корпус: соосность отверстий двух втулок, запрессованных в противоположной стенке корпуса: радиальное и торцевое биение шестерни, нарисованный навал: боковой зазор и пятно контакта зубьев у собранных шестерен и др.
Эти работы определяются исходя из конструкций собираемых элементов, их служебного назначения и технических требований, предъявляемых изделий.
7.Дополнительные работы, которые не относятся ни к одной из перечисленных выше групп, а вызывается конструктивными технологическими или эксплуатационными особенностями изделия. К ним относятся: маркировка (клеймение) собранного узла: окраска мест развальцовки деталей для предохранения их от коррозий: отжатие мест соприкосновение двух деталей с целью создания герметичности и др.
При выявлении сборочных работ необходимо определить, какие из них можно и целесообразно выполнить вне общей и узловой сборки как подготовительные. К таким работам относятся: большинство работ по механической обработке, выполняемой в сборочном цехе: ряд работ из группы б) (распаковка и др.), если это не приводит к ухудшению качества поступающих на сборку узлов и деталей: изготовление отдельных простых деталей, когда оно не связано с работой «по месту».
Остальные работы: выполнение соединений деталей и узлов; работы, обусловленные методами пригонки, регулировки и проверки правильности соединений деталей и узлов в процессе сборке, - составляют основное содержание узловой и общей сборки.
8.2. Составляют перечень работ и их нормирование. После выявления сборочных работ составляют их перечень в последовательности, предусмотренной схемой сборки и определяют затраты времени на их выполнение (табл.5)
48

Перечень сборочных работ для узла «фланец в сборе» |
Таблица 5 |
||
|
|
||
СБ – 66 (см. прил. 1.2) |
|
|
|
№ |
Содержание переходов и приемов; |
Время, |
|
п/п |
Размеры, необходимые для нормирования |
мин. |
|
1. |
Продуть фланец 66, Ø 90 х 130 |
0,11 |
|
2. |
Продуть ось 64, Ø 35 х 150 |
0,08 |
|
3. |
Протереть фланец 66, Ø 90 х 130 |
0,21 |
|
4. |
Протереть ось 64, Ø 35 х 150 |
0,18 |
|
5. |
Ввернуть в отверстие оси 64 и фланца 66 по две пробки |
0,22 х 4 |
|
|
¼; шаг резьбы 1,27мм., длина завертывания 10мм. |
|
|
|
|
|
|
6. |
Освободить от упаковки подшипник 7000103, кл. В, Ø |
0,07 |
|
|
наружный 55мм. |
|
|
7. |
То же, подшипник 7000106, кл. В, Ø наружный 35мм. |
0,06 |
|
8. |
Установить ось 64 в приспобление, вес 1кг. |
0,07 |
|
9. |
Напрессовать подшипник 7000103 на ось 64, длина на |
|
|
|
прессовке 10мм. |
0,17 |
|
10. |
Установить в приспособление ось 64, вес 1кг. |
0,07 |
|
11. |
Напрессовать подшипник 7000106, длина на прессовке |
0,19 |
|
|
50мм. |
|
|
12. |
Смазать маслом ось 64, Ø 35мм, ℓ = 90мм. |
0,08 |
|
13. |
Завести ось в отверстие фланца 66, Ø 35мм, ℓ = 110мм, |
|
|
|
вес до двух кг. |
0,12 |
|
14. |
Поставить замковое кольцо 255, Ø 55мм, толщина |
0,16 |
|
|
1,6мм. |
|
|
15. |
Поставить кольцо уплотнительное 228, Ø 80, ℓ = 20мм. |
0,19 |
|
16. |
То же, 229, Ø 99мм, ℓ = 20мм. |
0,19 |
|
17. |
То же, 223, Ø 35мм, ℓ = 20мм. |
0,16 |
|
18. |
Протереть фланец 95, Ø 40 х 20мм. |
0,12 |
|
19. |
Смазать маслом фланец 95 |
0,08 |
|
20. |
Завести фланец 95 в отв., фланца 66, Ø 40мм, ℓ = 20мм. |
0,09 |
|
21. |
Поставить замковое кольцо 242, Ø 42мм, толщина |
0,16 |
|
|
1,6мм. |
|
|
22. |
Проверить легкость вращения оси; вес вращающихся |
0,08 |
|
|
частей до 2кг. |
|
|
|
|
|
|
|
Общая трудоемкость сборки узла СБ - 66 |
3,92 |
|
49

Перечень должен быть настолько подробным, чтобы можно было нормировать по имеющимся нормативам. Для этого необходимо предварительно изучить структуру и содержание используемых нормативов.
В сборочных нормативах даются:
1.Таблицы оперативного времени на соединение деталей и узлов и на слесарные работы. В них определенно суммарное время выполнения основного приема и не разрывно связанных с ним вспомогательных приемов. Все приемы, включенные в оперативное время, перечислены в табл. 5. Например, время на запрессовывание деталей в отверстие или на валы предусматривает следующий состав работ: взять деталь и установить её, включить пресс и запрессовать деталь, включить пресс. При использовании оправах этому времени прибавляют время на установку и снятие их, которая также приведено в табл.5. Помещая эту работу в перечень, достаточно записать: «напрессовать втулку Ø 30мм, длина напрессовки 25 мм. Посадка, Н7/js6
2.Таблицы вспомогательного времени на работы, отведенного для выполнения вспомогательных приемов, например: на установку в приспособление базовых деталей или узлов, повороты их, перемещения и снятие: на перемещение инструментов: осмотр, промывку, протирку, обдувку воздухом деталей или узлов перед сборкой: застропливание и растропливание и др. в [14] приведено время в зависимости от параметров деталей и узлов. Приемы включенные во вспомогательное время, так же перечислены в табл. 5. Например: время на обдувку воздухом охватывает следующий сустав работ: взять шланг, открыть вентиль, обдуть деталь, закрыть вентиль, отложить шланг. Помещая эту работу в перечень, достаточно записать: обдуть деталь Ø 120, Ø 220.
3.На обслуживание рабочего места, перерыва на отдых и подготовительного заключительное время принимают в процентах от оперативного.
Всоставленном перечне переходы и приемы записываются в повелительном наклонении, указывают размеры, необходимые для определения времени, и время в мин.
Внормативах так же предусматривается выполнение следующих
работ:
−доставка деталей к рабочему месту и раскладка по ячейкам выполняется вспомогательными рабочими:
−сборщик перемещает детали и узлы на расстояние более 2м. (при большем расстоянии необходимо добавлять дополнительное время).
−детали и узлы весом до 20кг. перемещают и устанавливают в ручную: свыше 20кг., тельфером или мостовым краном.
50

8.3. Определяется тип и организационная форма производства, для заданной программы рассчитывается номинальный темп выпуска (мин.);
T = 60Фгод , |
(25) |
H |
N год |
|
где: Фгод – годовой фонд рабочего времени, ч: принимается по ( 17,18). При односменной работе номинальный фонд Фгод = 2070ч, при двух сменной – Фгод = 4140ч, N год – годовая программа, шт.
Затем, исходя из технологической схемы сборки, определяют характерные операции, из которых должен состоять проектируемый технологический процесс сборки, и приближенно рассчитывают продолжительность, используя составленный перечень работы.
Операция должна представлять собой технологически законченный этап сборки. Например; установка передней бабки при общей сборке токарного станка. Этап сборке часто заканчивается проверкой выполненной работы, в данном примере – проверкой параллельность оси шпинделя направляющим станицы. Одним из признаков, характеризующих законченность этапа, является то, что выполненная на данной операции сборка не нарушается при изменении положения и транспортировке объекта.
Если темп выпуска значительно выше средней продолжительности характерных сборочных операций, то сборку ведут по принципам серийного производства. В этом случае на каждом рабочем месте в течении года будет выполнятся сборка различных изделий или узлов. По форме организации сборка может быть поточной, подвижной или стационарной (при малом выпуске изделий). В случае подвижной сборке решают вопрос выбором типа транспортного средства исходя из конструкции, веса и габаритов изделия. Если темп близок или меньше средней длительности операции, то сборку ведут по принципам массового производства, закрепив за каждым рабочим местом определенную сборочную операцию. В этом случае сборку выполняют поточным методом, при чем приемлемой величиной средней продолжительности сборочных операций можно сочетать токую, при которой средний коэффициент загрузки по точной линии не ниже 0,85.
8.4. Проектирование операций условий среднего производства:
1. Объединив выявленные сборочные работы (табл.5), выполняют компоновку сборочных операций, учитывая:
−количество рабочих – сборщиков
−содержание операции как технологический законченного этапа сборки, выполняемого на одном рабочем месте.
Количество рабочих, необходимое для выполнения заданной программы, может быть рассчитано по формуле
51

P = |
Tp −Tc |
, |
(26) |
(tH −tH ) p |
где Тр – расчетная суммарная трудоемкость всех переходов сборки; Тс – расчетная трудоемкость совмещенных во времени переходов; tН – номинальный такт выпуска;
tП – расчетное время перемещение собираемого объекта с одного рабочего места на другое;
р – количество параллельных потоков, необходимых для выполнения заданной производственной программы.
Выявленные сборочные работы распределяются между рассчитанным числом сборщиков. При этом необходимо учитывать условия синхронизации операций, т.е. равенство или кратность их деятельности такту выпуска и их технологической законченности.
Однако этот путь не всегда может дать приемлемые результаты. Так, при трудоемкости сборки изделия, близкой к такту выпуска, расчетное число рабочих мест может быть равным единице, что не приемлемо по следующим причинам:
−нерационально используются сборщики высокой квалификации;
−чрезмерно загромождается рабочее место сборочным оборудованием;
−применяется стационарная сборка.
Поэтому в условиях серийного производства при объединении выявленных сборочных работ в операции исходят прежде всего из технологической законченности этапа сборки, выполненного на данной операции и организационно – технических условий производства (например: пропускной способности сборочного цеха). Если при этом длительность отдельных операций получается в 2-3 раза больше такта выпуска или длительности большинства операций, то используют рабочие места дублеров.
2.Определяется способ подачи базового элемента, комплектующих изделий и собираемых деталей на рабочее место, а также способ транспортирования самого собираемого объекта в процессе сборки.
3.Выбирается оборудование, необходимое для выполнения сборки: слесарные тиски, сборочные стенды, прессовое оборудование, механизированный инструмент для выполнения резьбовых соединений и клепки и другие средства облегчения труда и повышения производительности [2,4,5,7,24,26].
Выбор средств механизации сборки производится по заданной программе выпуска и комплекса работ, выполняемого при сборке изделия:
52

комплектование и транспортирование деталей и сборочных единиц к месту сборки, координирование их с заданной точностью, соединение, проверку достигнутой точности положения и движения монтируемых деталей, регулирование, пригонку, фиксацию относительных положений деталей и сборочных единиц, транспортирование самого собираемого объекта, испытание отдельных узлов и изделия в целом, окраску.
4.Определяются схемы установки, закрепления, повороты и перестановки базового элемента в процессе сборки.
5.Выполняются технологические расчеты, необходимые для выбора сборочного оборудования или определения режимов его работы: усилий запрессовки, клепки, развальцовки, температуры нагрева или охлаждения присоединяемых деталей и пр.
6.Уточняется составленный перечень сборочных работ (табл.5) и время их выполнения. Спроектированные операции записываются в технологические карты сборки. Пример заполнения технологических карт дан в прил.
Воформлении операционных карт сборочного технологического процесса необходимо руководствоваться [30-35].
Вкартах указывается норма времени на каждый укрупненный переход операции по всем приемам откорректированного перечня работ.
Норма штучного времени на операцию tшт рассчитывается по формуле:
|
|
α +β+ γ |
|
|
tшт = tоп 1 |
+ |
|
, |
(27) |
|
||||
|
|
100 |
|
где: tоп – оперативное время на операцию: α, β, γ - части оперативного времени; выражающие соответственно время технического, организационного обслуживания рабочего места и время перерывов на отдых, %.
При нормировании сборочных, работ время технического обслуживания принимается равным нулю. Оперативное время дается на переходы по выполнению соединений и слесарных работ без разделения на основное и вспомогательное. На работы, не являющиеся переходами, дается только вспомогательное время.
При расчете нормы штучного времени на сборочную операцию оперативное время tоп, входящее в формулу (27), складывается из двух составляющих: Σ tв и Σ tоп ;
/ |
|
β+ γ |
|
|
tшт = (∑tB + ∑tоп ) 1 |
+ |
|
, |
(28) |
|
||||
|
|
100 |
|
53

где: Σ tв – сумма вспомогательного времени на работы, входящие в операцию и не являющиеся переходами (установка, снятие, поворот базовых деталей и собираемых узлов, продувка воздухом, промывка, протирка и др.) Σ tоп – сумма оперативного времени на выполнение сборочных и слесарных переходов, входящих в операцию.
Рассчитанную по формуле (16) норму времени на операцию записывают в технологическую карту (прил.3).
7. В случае необходимости к технологическим картам прилагаются эскизы, поясняющие выполнение указанных в карте сборочных работ, проверок, испытаний.
9.ПРОЕКТИРОВАНИЕ В УСЛОВИЯХ МАССОВОГО ПРОИЗВОДСТВА
9.1.Расчет действительного темпа выпуска
При проектировании технологического процесса сборки в условиях массового производства рассчитывается действительный темп выпуска:
tд = (tH ηp −tобсл −tотд ), |
(29) |
где: tн – номинальный темп выпуска; ηp - коэффициент, учитывающий
затраты времени на ремонт оборудования (0,98 при односменной работе и 0,97 – при двусменной); tобсл – время на обслуживание рабочего места; tотд – время на перерывы для отдыха.
9.2. Выбор организационной формы и типа транспортного устройства
Наиболее эффективной организационной формой сборки в условиях массового производства является поточная сборка с непрерывным и периодическим перемещением собираемого объекта.
При непрерывном перемещении собираемого объекта, скорость которого, выбирается в пределах 3,5 – 5 м/мин, время на перемещение объекта сборки с позиции на позицию τ= 0. В этом случае время выполнения сборочных работ на рабочих местах равно действительному темпу выпуска.
При периодическом перемещении объекта время τ определяется по формуле:
54

τ = |
l |
, |
(30) |
|
v |
||||
|
|
|
где l - длина рабочего места, м (принимают минимально необходимую, исходя из габаритов собираемого изделия, габаритов применяемого сборочного оборудования, количества рабочих, работающих на одном рабочем месте); v – скорость перемещения конвейера, которая принимается равной 10-15 м/мин при ручном перемещении, до 20 м/мин при перемещении по рольгангу, 30-40 м/мин для механических транспортирующих средств, 15-
20м/мин для конвейера периодического действия.
Вэтом случае время τ является потерей, которая тем больше, чем меньше темп. Приемлемым является соотношение
τ ≤ 0,05tд, |
(31) |
Выбор между конвейером периодического и непрерывного действия определяется возможностью и удобством выполнения сборочных работ на движущемся конвейере с величиной темпа сборки [17,18].
9.3. Проектирование сборочных операций
По плану, приведённому выше (пп.7.4.), для условий серийного производства выполняется с учетом следующих особенностей:
1. Компоновка операции, т.е. объединение выявленных сборочных работ, выполняется таким образом, чтобы продолжительность операций поточной линии tр.м. не превышала темпа:
t р.м. < tд или (∑tв +∑tоп/ )+ τ ≤ tд;∑tв +∑tоп/ ≤ tд −τ, |
(32) |
Величины Σ tв и Σ tоп имеют то же значение, что и в формуле (28), но с учетом сборочных работ, выполняемых на каждом рабочем месте.
2. Синхронизация (выравнивание, приведение в соответствие с темпом) загрузки рабочих мест выполняется с целью обеспечения условия (32) в следующем порядке:
−перераспределяют работы между рабочими местами, если это, технологически возможно;
−применяют специальные приспособления, в том числе поворотные с быстродействующими установочно-зажимающими устройствами, высокопроизводительное сборочное оборудование, механизированный сборочный инструмент, многоместную и многоинструментальную сборку;
55

− изменяют технологические способы выполнения соединений например; заменяют запрессовку втулку посадкой ее с охлаждением).
Если условие (31) нельзя выдержать за счет уменьшения времени
(Σ tв + Σ tоп ), то необходимо сделать его кратным величине действительного темпа выпуска (tд - τ) и сдублировать рабочие места. Вместо дублирования за одним рабочим местом закрепляют двух или более рабочих.
3. Правильность произведенного выравнивания загрузки рабочих мест оценивают коэффициентами: Кп -загрузки каждого сборочного рабочего места и Кл. – загрузки всей поточной линии.
Коэффициент
КП = |
(∑tв +∑tоп/ )+τ |
, |
(33) |
|
tд В |
|
|
где: В – количество рабочих на сборочном месте. Для отдельных рабочих мест допустимой является величина Кп = 0,6 – 0,65.
Коэффициент
|
1 |
П |
|
|
Кл = |
|
∑КП , |
(34) |
|
П |
||||
|
1 |
|
где: П – число рабочих мест поточной линии. Приемлемой величиной можно считать Кл = 0,85 и более.
4. Расчет нормы штучного времени выполняют по формуле:
/ |
|
+ |
β+ γ |
(35) |
tшт = (∑tвmax +∑tоп.max +τ) 1 |
, |
|||
|
|
|
100 |
|
где: Σ tвmах, + Σ t′ оп.max , - длительность лимитирующего оперативного времени операции.
5. Результаты проектирования операций отражают в технологических картах сборки в соответствии с требованиями стандартов [33,34].
56

10. ПОСТРОЕНИЕ ЦИКЛОГРАММЫ СБОРКИ
После разработки схемы сборки, составления сборочных работ, т.е. перечня сборочных работ и их нормирования, стоят циклограмму сборки [1,2].
Циклограмма сборки позволяет; 1 установить возможно более короткий цикл сборки путем совмещения
во времени выполнения отдельных переходов; 2 наиболее рационально выполнить компоновку операции сборки из
намеченных переходов, обеспечить их синхронизацию, т.е. равенство или кратность их длительности темпу сборки;
3 внести необходимые изменения в конструкцию изделия, совершенствующие ее технологичность, а также в технологический процесс сборки.
11. РАЗРАБОТКА КОМПОНОВКИ И ПЛАНИРОВКИ СБОРОЧНОГО ЦЕХА (УЧАСТКА)
Последовательность выполнения работ при разработке общей компоновки и планировки оборудования сборочного цеха определяется руководящими материалами отрасли и состоит из следующих этапов.
Первый этап – предварительная компоновка отделений цеха (без планировки цеха). В этой стадии решается предварительно вопрос о расположении сборочного цеха и его отделений относительно пролетов механического цеха.
Второй этап – планировка оборудования по делениям цеха на основе разработанной технологии и уточнение площадей от делений.
Третий этап – компоновка и планировка оборудования цеха в целом с учетом уточнений площадей по планировки оборудования всех отделений и участков.
Планировку сборочного цеха (участка) разрабатывают в следующем порядке:
1.выбранную сетку колонны наносят на миллиметровую бумагу в масштабе 1:100 или 1:200.
2.определяют ширину (количество пролетов) сборочного цеха или участка исходя из подчитанных площадей от делений .
3.выполняют компоновку площадей отделений и участков на площади всего сборочного цеха.
4.наносят на план расположения сложного оборудования и магистральных проездов.
57

5.определяют расположение основных производственных вспомогательных участков.
6.на сетку колонны наносят грузопотоки цеха с учетом их связей с размещением основных производственных участков.
На планировке цеха (участка) показывают:
1)сетку колонн, их оси, конструктивные размеры колонн фундаментов;
2)стенды для общей сборки изделия, его обкатки и испытания, если оно не производится на испытательной станции;
3)рабочие места (верстаки слесарей сборки комплектов и узлов сборки, стеллажи для хранения деталей и сборочных единиц), резервные сборочные места и рабочие места контролеров;
4)сборочное оборудование для выполнения соединений, металлорежущие станки в соответствии с технологическим процессом сборки;
5)оборудование для выполнения вспомогательных работ, вынесенных из узловой и общей сборки;
6)площади для хранения запасов деталей в специальной таре и сборочных единиц, крупных деталей (рам, станин, плит, полов) в количестве обеспечивающем бесперебойную сборку машин;
7)проходы и проезды (исходя из габаритных размеров транспортных средств и перевозимых деталей и узлов);
8)вспомогательное оборудование грузоподъемные и транспортные
средства;
9)Места подвода воды, сжатого воздуха, пара и т.д.
Оборудование, а также устройство на рабочих местах и участков обозначается порядковыми номерами и вносятся в спецификацию, которая помещается в расчетно–пояснительной записки или на плане. В спецификации указываются:
−номер обозначений на плане;
−наименование оборудований или устройства;
−характеристика оборудования (основные размеры, грузоподъемности, площадь и т.д.);
−мощность электродвигателей оборудования и устройств.
При разработке общей компоновки и планировки сборочного цеха (участка) необходимо руководствоваться методическими положениями по разработке технологических планировок, нормами технологического проектирования, руководящими материалами по охране труда и техники безопасности, производственной санитарии и пожарной безопасности [17,18], а так же системой стандартов безопасности труда (ССБТ):
ГОСТ 12.1.004-85, ГОСТ 12.3.002-75, ГОСТ 12.2.002-91. ГОСТ 12.2.029-88, ГОСТ 12.1.003-83, ГОСТ 12.1.001-89, ГОСТ 3.1120-83.
58

12.АВТОМАТИЗАЦИЯ СБОРОЧНЫХ РАБОТ
12.1.Производственные ситуации автоматизации сборки.
Автоматизация сборки остается одной из острых проблем машиностроения, решение которой сдерживается нетехнологичностью конструкций изделий, недостаточной унификацией и малой серийностью и выпуска, отсутствием типового сборочного оборудования, недостаточно высоким качеством деталей изделий, а так же малым числом апробированных на производстве примеров решений.
Стадии развития процессов автоматизации сборки – частичная и комплексная механизация, частичная и комплексная автоматизация.
При частичной механизации сборки основного освобождается от трудоёмких ручных приемов по выполнению данной операции.
При комплексной механизации используют системы механизированных устройств, обеспечивающих выполнение основных и вспомогательных работ (подъем, перемещение, установку и снятие со сборочных стендов тяжелых изделий).
Частичная автоматизация заключается в том, что наряду с обычным сборочным оборудованием используются автоматы и полуавтоматы.
При комплексной автоматизации сборки системы непрерывно действующих автоматических сборочных машин функционируют как единый взаимосвязанный комплекс.
Проектирований технологических процессов автоматической сборке осуществляется в трех основных производственных ситуациях:
1.проектирование технологии сборки для нового завода с комплексной системой автоматизации производства. Разработанных технологических процессов в этом случае определяет конструкторскую строительную, транспортную, энергетическую и организационную части проекта, потребности в оборудовании, рабочей силе, материалах.
2.проектирование при реконструкции завода и внедрений производства новых изделий на действующем заводе. Инициатива технолога
вданном случае ограничено необходимостью использования имеющихся площадей, оборудования, транспортных средств, сложившейся схемы грузопотоков и другими местными условиями.
3.автоматизация сборки на действующих предприятиях при выпуске на них освоенной продукции. В этих условиях проектируют автоматические линии, участки линий, отдельные автоматические установки. Возможности автоматизации в данном случае весьма ограничены, так как срок окупаемости предлагаемых средств автоматизации не должен превышать продолжительности выпуска продукции.
59

Автоматическую сборку в основном применяют в массовом производстве. Сфера её использовании может быть расширенна унификацией и стандартизацией изделий, что приводит к увеличению количества и продолжительности их выпуска.
Применение автоматической сборки в серийном производстве ограничивается меньшими программами выпуска изделий.
Сроки окупаемости средств автоматизации не редко оказываются большими предполагаемой длительности выпуска изделий. В этом случае автоматизацию проводят на основе быстропереналаживаемого сборочного оборудования из типовых узлов и исполнительных механизмов, сборочных работ.
Автоматическая сборка в единичном и мелко серийном производстве выполняется специализированным оборудованием с программным управлением и работами. Примеры удачного решения задач автоматизации сборки: автоматическая сварка протяженных швов в крупногабаритных узлах, автоматическая клепка крупных панелей.
По организационным формам автоматическая сборка может быть стационарной и конвейерной.
Стационарную сборку выполняют на специальном оборудовании или с помощью роботов. И еще можно применить в массовом и серийном производстве в основном для не больших узлов.
Конвейерная сборка в большинстве случаев осуществима с периодической остановкой собираемых изделий (автоматические сборочные линии).
Сборка с непрерывном перемещением изделия осуществляется на конвейерах, оснащенных работами, а так же на роторных автоматических линиях.
12.2.Требование к изделию |
|
Автоматизация сборки предъявляется |
особые требования |
технологичности конструкции изделий [2,4,15,24]: |
|
1.Деталям необходимо придавать простые и симметричные формы, увеличивая, по возможности количества плоскостей симметрии. При этом упрощаются схемы пассивной и активной ориентации детали в вибробункерах.
2.Конструкция деталей должна исключать их сцепление при выдаче из вибробункерах.
3.Детали, сопрягающиеся с зазором или натягом (а также резьбовые детали), необходимо выполнять с фасками или направляющими элементами. Фаски обеспечивают лучшее направление сопрягаемых деталей на сборочной позиции автомата.
60

4.Базовые детали изделий должны иметь надежные комплекты технологических баз для установки на рабочих позициях автоматов, позволяющих реализовать принципы единства и постоянства баз.
5.Базовые детали изделий должны просто и надежно устанавливаться
изакреплятся в сборочном приспособлении.
6.Детали изделия должны иметь точно выполненные базы для надежного захвата рабочим органом робота.
7.В конструкции изделия необходимо максимально использовать унифицированные и стандартные детали. Это позволяет применить однотипные исполнительные и вспомогательные устройства сборочных автоматов.
8.Конструкция изделия должна обеспечивать подачу деталей по простым прямолинейным траекториям. Детали должны последовательно поступать в одном направлении на базовую деталь. Предпочтительная подача в вертикальном направлении. Это упрощает конструкции исполнительных механизмов автомата.
9.Конструкция изделия должна быть удобной для подвода и отвода сборочных инструментов по прямолинейным траекториям.
10.Конструкция изделия должна обеспечивать возможность сборки без изменения положения (поворота) базовой детали.
11.Сложные изделия должны допускать их расчленение на предварительно собираемые сборочные единицы. Это позволяет автоматизировать узловую сборку. Узлы после контроля передаются на общую сборку.
Автоматизация сборки облегчается переходом к более удобным видам соединений сопрягаемых деталей.
1.Применение болтовых соединений усложняет конструкцию сборочных автоматов. Более удобны винты, ввертываемые в резьбовые отверстия соединяемых деталей.
2.Неудобны при автоматической сборке валов шпоночные соединения. Их желательно заменять шлицевыми или соединениями с гарантированным натягом.
3.Автоматическая сборка упрощается при использовании в качестве фиксаторов разрезных стопорных колец вместо шайб с винтами или фиксирующих гаек.
4.Технология выполнения соединений не должна быть связана с продолжительными процессами (охлаждением нагретых деталей, сушкой, полимеризацией клеев). Несоблюдение этого условия нарушает синхронизацию переходов сборки.
61

12.3. Методы достижения точности при автоматической сборке.
Сборка с применением метода полной взаимозаменяемости обеспечивает наибольшую простоту автоматизации сборочных работ. Этот метод наиболее эффективен в малозвенных размерных цепях.
Другие методы достижения точности принципиально возможны, но применение их связано с техническими трудностями.
Сборку по методу групповой взаимозаменяемости в автоматизированном производстве применяют при повышенных требований к точности замыкающих звеньев размерных цепей. Сборочные машины в этом случае усложняются тем, что для каждой размерной группы деталей необходим отдельные бункера или магазины. Усложняются так же технологическая схема машины и система управления.
Сборка по методу регулирования принципиально возможно и допустимо при наличие сложных многозвенных размерных цепей. Сборочная машина при этом усложняется введением устройств для проверки выдерживаемого при сборке размера и установки подвижного (или неподвижного) компенсатора. Выполнение пригонок на сборочной машине целесообразно. Они нарушают темп сборки и усложняют исполнительные устройства. При необходимости пригонку следует выполнять вне автоматической линии.
Сборка с применением методом неполной взаимозаменяемости в условиях автоматизации возможна. В этом случае структура сборочных машин усложняется введением устройств для контроля выдерживаемых размеров и удаления изделий, у которых замыкающее звено выходит за пределы установленного допуска. Эти изделия подвергают дополнительной (ручной) сборке.
12.4. Особенности проектирования технологических процессов.
Проектирование технологических процессов автоматической сборки имеет свои особенности:
1.до начала проектирования выявляют перспективный объем выпуска изделий и предполагаемую продолжительность их производства. Предположительно устанавливают уровень автоматизации, намечая, какие процессы будут автоматизированы полностью и какие частично. На основе этих данных проводят технико-экономическое обоснование автоматизации.
2.Тщательно разрабатывают технологические процессы сборки, учитывая, что их последующая коррекция будет крайне затруднена в связи с большими затратами на автоматизацию.
3.За основу разрабатываемой технологии принимают существующую прогрессивную технологию и проверенные типовые решения.
62

4.При проектировании обеспечивается непрерывность протекания технологических процессов сборки и сокращение производственного цикла, оптимальная концентрация переходов при построении операции.
5.Особое внимание уделяют детальной проработке вопросов ориентации, базирования, транспортирования, контроля качества продукции,
атакже технических заданий на конструирование специальных исполнительных устройств и оснастки.
Ряд особенностей имеет проектирование операций сборки.
1.Уточняют содержание операций, степень концентрации технологических переходов, выявляют и регламентируют по времени все элементы операции – от ориентации деталей до удаления собираемого изделия, определяют силы запрессовки, клепки, затяжки резьбовых соединений, штучное время.
2.Устанавливают технологические характеристики необходимого сборочного оборудования: структурная схема, кинематика и динамика, система управления, необходимость переналадки, степень автоматизации рабочего цикла.
3.Составляют техническое задание на конструирование сборочного приспособления (и специальных сборочных инструментов) с указанием принятых схем базирования, способов автоматической подачи, ориентации деталей и снятия собранного изделия.
4.Определяют необходимый контроль выполнения сборки, включая технологические и вспомогательные элементы операции.
5.При проектировании сложных операций сборки на многопозиционных станках и автоматических линиях определяют загрузку оборудования по отдельным позициям, стоят циклограммы работы и уточняют загрузку оборудования.
6.При использовании автоматических линий устанавливают структуру и тип линии, применяемое оборудование, число участков и линий, загрузки и надёжности работы отдельных позиций, необходимые заделы и накопители, конфигурацию линии в плане. На основе этих данных составляют техническое задание на проектирование линий.
7.нормы времени на операцию сборки определяют расчетноаналитичским методом. При использовании автоматического оборудования
штучное время определяют без учета времени tоб на обслуживание рабочего места и времени tп перерывов в работе.
8.Оценки и сопоставления вариантов технологических процессов автоматической сборки производят на основе системы техникоэкономических показателей [24].
63

12.5. выбор направления автоматизации.
Объём автоматизации сборочных работ зависит от конструктивного исполнения изделия, числа детали сборочной единицы, их размеров, массы и годовой программы выпуска.
В мелкосерийном производстве (ведется тысяча изделий в год) предпочтительна схема одно – и двухпозиционной сборке, выполняемо одним промышленным роботом последовательно с помощью быстросменных захватов и сборочных инструментов. Набор захватов и инструментов, необходимых для сборки партии изделий одного типоразмера, устанавливается в инструментальный магазин.
Для сборки сложных изделий с годовой программой несколько сотен тысяч изделий может быть применена многооперационная схема сборки с круговой или линейной траектории перемещения собираемого изделия соответственно на круглом длительном столе или конвейере, обслуживаемых автоматическими манипуляторами или промышленными работами.
Перспективным направлением автоматизации сборочных работ является создание типовых переналаживаемых сборочных линий, обслуживаемых несколькими операторами – сборщиками и промышленными работами и применение последних для выполнения типовых операций (клепки, сварки, сборки резьбовых соединений).
Следует использовать два робота один с многоинструментальной головкой и автоматической системой выбора инструмента, а другой – для поддержки со стороны замыкающей головки (заклепки, электрода, болта).
Определяющим фактором выбора направления автоматизации сборочных процессов является размер партии изделий. При больших партиях рациональная сборка на полностью автоматизированных сборочных линиях с высокой дифференциацией операций и минимальным временем такта.
Для мелкосерийного производства целесообразно создать сборочные центры, ориентированные на сборку законченного узла. Взаимозаменяемость таких технологических моделей с разнообразной степенью автоматизации позволит создать автоматические сборочные линии любой производительности.
12.6. Автоматизация сборочных операций.
При автоматизации сборочных операций выполняются следующие виды работ:
−анализ сетевой сборочных процессов;
−формулировка требований л автоматическому оборудованию и объектам сборки;
−выявление конструкции сборочного приспособления;
64

−формулировка условий собираемости деталей на сборочной
операции;
−анализ пространственного расположения сопрягаемых поверхностей;
−выбор оптимального варианта выделения из изделия ( сборочной единицы) типовых групп комплектов;
−анализ условий реализации сборочной операции и разработка рациональной схемы сборки;
−формулировка требований к сборочному инструменту и средствам автоматизации;
Для автоматической сборки необходимы автоматически действующие устройства, надежно выполняющие все переходы сборки;
−бункерно-ориентирующие устройства для деталей изделия, кассеты или магазины, загружаемые более сложными по своей конфигурации деталями в предварительно ориентированном виде.
−накопители, соединяемые с бункеро-ориентирующими устройствами открытыми или закрытыми лотками ( трубками);
−отсекатели-усройства для передачи детали из накопителя после освобождения ее отсекателем на сборочную позицию автомата;
−устройства для получения соединений (прессовых, развальцованных, клепанных и др.)
−устройства, выполняющие специальные функции (обдувки, смазку и др.)
−устройства, контролирующие правильность выполняемого соединения (взаимного положения, размеров, выдерживаемых при сборке, герметичность);
−механизмы для удаления собранного изделия из автомата в тару или на транспортер ( лоток) для передачи на следующий автомат без изменения ориентации.
Сложные базовые детали собираемого изделия устанавливают в приспобление на сборочной позиции вручную или механической рукой (роботом) из магазина (с конвейера) с последующим ее закреплением и откреплением в конце сборки.
Требования, предъявляемые к конструктивным особенностям промышленных роботов (ПР);
−автоматическая смена захватов и сборочного инструмента;
−адаптация роботов к определенным условиям захватывания и соединения деталей;
−диапазон скоростей перемещения исполнительных органов ПР;
−точность позиционирования или наличие устройств компенсации погрешности позиционирования при соединении деталей;
65

−контроль качества сборки.
Наиболее широкое применение получило техническое решение по автоматизации сборочных операций роботами, встроенными в сборочную машину.
Выполнение операций соединения разнообразных конструкций с помощью ПР требует создания специализированного сборочного инструмента для захватывания, перемещения, присоединения и установки:
−детали для точного позиционирования с большими зазорами;
−детали с валами зазорами или не большими натягами;
−нежестких деталей (резиновых манжет);
−упругих деталей (пружинных колец);
−резьбовых соединений (с контролем крутящего момента или других параметров);
−детали на вал, включая инструмент со встроенным механизмом дополнительной операции по базовой;
−сборки с пластической деформацией (клепки, раскатки).
−Специализированный сборочный инструмент должен
удовлетворять ряду |
требований: |
−быть универсальным по элементам базирования деталей и местам присоединения к ПР;
−допускаются по условиям сборки погрешности захватывание
деталей;
−обеспечивая надежность захватывания и транспортирования детали на сборочную позицию;
−обеспечивать компенсацию погрешности взаимного расположения сопрягаемых поверхностей перед соединением;
− допускать легкость регулировки и переналадки для присоединения однотипных деталей в установленном диапазоне размеров;
−допускать возможность встраивания элементов контрольных устройств и средств адаптации.
Выбор специализированного сборочного инструмента производится по технологическому процессу сборки.
Исходными данными для выбора типа специализированного сборочного инструмента являются:
−содержание переходов (операции);
−эскиз перехода (операций);
−вид работ, выполняемых на переходе (операций);
−характеристика работ с указанием количественных параметров;
−вид привода (электрический, пневматический, гидравлический);
−планировка оборудования на рабочем месте с указанием мест подвода источников энергии;
66

−тип подвески или установки сборочного инструмента.
При автоматизации сборочных операций, в случае невозможности их роботизации, необходимо стремиться к замене ручных работ различным механизированном инструментом, который облегчает труд и повышает его производительность.
В качестве механизированного инструмента применяется:
−электрические и пневматические сверлильные машины;
−электрические и пневматические шлифовальные машины;
−электрические и ножевые ножницы;
−электрические, гидравлические и пневматические резьбозавертывающие машины (гайковерты и винтоверты);
−пневматические рубильные молотки;
−резьбонарезные пневматические машины;
−резьбовые роликовые и быстросменные патроны для завинчивания
шпилек;
−пружинные балансиры для подвески инструмента;
−пневматические клепальные молотки;
Техническая характеристика различных типов механизированного сборочного и слесарного инструмента приведена в [30-32].
Выбор типа промышленного робота для сборочной операции производится по следующим параметрам:
−назначению (универсальные, специализированные и специальные);
−кинематике и базовой системе координат – прямоугольные (плоские и пространственные), полярные и ангулярные (плоские, цилиндрические, сферические);
−числу степеней подвижности;
−числу рук (захватов на руку);
−типу привода;
−устройству управления;
−способу программирования перемещений;
−емкости памяти системы (числу шагов);
−погрешности позиционирования;
−скоростям перемещения (линейная, угловая);
−грузоподъемности;
−размерам рабочего пространства.
Конструкции и техническая характеристика современных промышленных роботов приведена в [19,22,23].
В целях обеспечения рентабельности автоматизации сборочных операций оборудование должно иметь низкую себестоимость, высокую производительность и обеспечивать эффективность роботизации сборочных работ.
67

Оценка эффективности использования промышленных роботов производится:
−коэффициентом сервиса;
−зоной совместного обслуживания;
−возможностью встраивания ПР в сложные технологические комплексы;
−точностью позиционирования рабочих органов;
−технологической гибкостью;
−возможностью создания блочно-модульных систем;
−возможностями совместного использования с системами обслуживания, транспортировки, складирования и контроля.
Примеры использования промышленных роботов в сборочных операциях рассмотрены в [20,29].
12.7. Автоматизация технологических процессов сборки.
Промышленные роботы применяются на операциях общей и узловой сборки, на отдельных рабочих местах, оборудованных в виде сборочных комплексов, встроенными в сборочный конвейер или сборочные полуавтоматы и автоматы. При комплексной роботизации технологического процесса сборки отдельные сборочные комплексы необходимо связывать транспортными устройствами в единую сложную производственную систему робототехнические комплексы (РТК).
Характерные работы, выполняемые промышленными роботами в робототехнических комплексах, следующие:
−загрузка и разгрузка автоматов и конвейеров на автоматических и полуавтоматических линиях;
−установка деталей и узлов в заданном положении на собираемое изделие по технологическим базам;
−транспортирование и складирование деталей и узлов;
−подача подготовленных к сборке деталей на прессы для выполнения запрессовки, склеивания и других операций;
−выполнение операций контроля и испытания изделий.
Основные направления и предпосылки создания робототехнических комплексов:
−увеличение числа периферийных устройств (сборочного инструмента), используемого совместно с роботом;
−сборка сложных многокомпонентных изделий;
68

−наличие в технологическом процессе сборки большого числа типовых операций (клепка, сварка, окраска, гальванопокрытия, промывка и т.д.);
−концентрация или дифференциация операции, позволяющие создать однопозиционные или многопозиционные РТК.
Примеры организационно-технических работ по созданию РТК рассмотрены в [10, 20, 21, 27-29].
Важнейшей частью робототехнических систем являются захваты роботов, к которым предъявляются следующие требования:
−простота конструкции;
−быстродействие;
−надежность и безопасность в работе;
−точность по захвату и центрированию деталей;
−отсутствие деформаций деталей и повреждения их поверхностей;
−универсальность.
Выбор конструкции захватов промышленных роботов производится по следующим параметрам:
−типу привода;
−погрешности захвата и позиционирования;
−месту расположения относительно сборочной единицы;
−числу деталей, захватываемых одним захватом.
Сборочные приспособления, используемые для установки базовых деталей собираемого изделия, должны обеспечивать:
−необходимые размеры рабочей зоны;
−автоматическое закрепление базовой детали, открепление объекта сборки и управление от системы робота;
−возможность последовательной установки всех деталей изделия
(узла);
−передачу объекта сборки рабочим органам робота в тару или на следующую позицию без потери ориентации;
−возможность как системного, так и автономного управления. Окончательным этапом автоматизации технологического процесса
сборки является разработка планировки рабочего места, сборочного робота и компоновки РТК или участка.
На планировке указываются:
−столы или стенды для приспособлений, магазинов, бункеров или кассет с деталями собираемого изделия;
−технологическое оборудование;
−транспортные устройства для удаления собранных изделий;
−устройства техники безопасности.
69

При разработке планировки необходимо руководствоваться примерами организации и компоновки РТК, участков и линий, рассмотренными в
[10, 20, 21, 24, 27-29].
13. ОФОРМЛЕНИЕ ТЕХНОЛОГИЧЕСКИХ ДОКУМЕНТОВ
Разработанный технологический процесс сборки изделия оформляется в соответствии с требованиями комплекса стандартов единой системы технологической документации.
Стадии разработки технологической документации на сборку степень детализации описания, виды и обозначения форм документации для различных типов производства и стадий разработки используемой конструкторской документации приведены в ГОСТ 3.1102-81 “Стадии разработки и виды документов” и ГОСТ 3.1407-86 “Формы и требования к заполнению и оформлению документов на технологические процессы (операции), специализированные по методам сборки”.
Формы и правила оформления титульного листа, технологической инструкции и карты эскизов, разрабатываемых с применением различных методов проектирования, приведены в ГОСТ 3.1105-84 ”Формы и правила оформления документов общего назначения”.
Формы и правила оформления маршрутных карт приведены в ГОСТ
3.1118-82.
Общие правила оформления текстовых и графических документов приведены в ГОСТ 3.1104-81 “Общие требования к формам, бланкам и документам”.
Метрологическое обеспечение при сборке регламентируется стандартами государственной системы обеспечения единства измерения
(ГСИ): ГОСТ 16.263-70, ГОСТ 125-79, ГОСТ 8.103-73, ГОСТ 8.009-84, ГОСТ 8.002-86, ГОСТ 12.3.009-76.
70

Библиографическое описание
1.Базров, Б.М. Основы технологии машиностроения Учебник для вузов/ Б.М. Базров. -М.: Машиностроение, 2005.– 354 с.
2.Суслов, А.Г. Научные основы технологии машиностроения / А.Г. Суслов, A.M. Дальский -М.: Машиностроение, 2002.- 664 с.
3.Технология машиностроения: Спец. часть: Учеб. для машиностроит. спец. вузов/ А. А. Гусев и др.; - М.: Машиностроение, 1986.- 480 с.
4.Колесов, И.М. Основы технологии машиностроения: Учебник/ И. М. Колесов. -М.: Высшая школа, 2002.-591 с.
5.Балакшин, Б. С. Теория и практика технологии машиностроения : Избр. тр. В 2-х кн./ Б.С. Балакшин; Ред. Б.М. Базров. -М. : Машиностроение. - 1982 Кн.1 : Технология станкостроения: научное издание. -1982.-239 с.
6.Новиков, М.П. Конструктирование сборочных приспособлений/ М.П. Новиков.– М.: Машиностроение, 1975. – 315 с.
7.Новиков, М.П., Основы технологии сборки машин и механизмов/ М.П. Новиков – М.: Машиностроение, 1980. – 592 с.
8.Технология машиностроения (специальная часть)/ А.А. Гусев, Е.Р.Ковальчук, И.М.Колесов и др. - М.: Машиностроение, 1986. – 480 с.
9.Авраменко, В.Е. Технология машиностроения. Нормирование сборочных операций: Метод, указ, по курсовому проектированию для студентов спец. 0501/ В.Е. Авраменко; Краснояр. политехи, ин-т. – Красноярск: КрПИ, 1985. – 48 с.
10.Авраменко, В.Е. Технология машиностроения – нормирование сборочных операций: методические указания по курсовому и дипломному
проектированию по специальности «Технология машиностроения»/ В.Е. Авраменко.– КрПИ, Красноярск, 1988. – 48 с.
11.Замятин, В.К. Технология и оснащение сборочного производства машиностроения: Справочник/ Замятин В.К.. -М.: Машиностроение, 1995.–608с.
12.Технологичность конструкции изделия: Справочник. -2-е изд., перераб. и доп.. -М.: Машиностроение, 1990.-768 с.
13.Справочник технолога-машиностроителя. В 2х т. Т.1/Под ред. А.М. Дальского, А.Г. Косиловой, Г.К. Мещерякова, А.Г. Суслова. – 5е издание исправл. – М.: Машиностроение, - 1, 2003 г., 912 с.
14.Качество машин: Справочник: В 2 т. – Т. 1/ А.Г. Суслов, Э.Д. Браун и др. – М.: Машиностроение, 1995. — 256 с.
15. Технологичность конструкции изделия: Справочник/ Т.К. Алферова и др.; Под общ. ред. Ю.Д. Амирова. - М.: Машиностроение, 1990. - 768 с.
71

16.Общемашиностроительные нормативы времени на слесарную обработку деталей и слесарно-сборочные работы по сборке машин. Мелкосерийное и единичное производство. – М.: Машиностроение, 1974.–219 с.
17.Технологичность конструкций изделий: Справочник/ Под ред. Ю.Д. Амирова. — М.: Машиностроение, 1985. – 367 с.
18.Технологичность конструкции изделия: Справочник. 2-е изд., перераб. и доп.. –М.: Машиностроение, 1990. –768 с.
19.Сборка изделий в машиностроении: Справочник: В 2 т. Т. 1 / Под ред. В.С. Корсакова, В.К. Замятина. М.: Машиностроение, 1983.– 637 с.
20.Механизированный инструмент, отделочные машины и вибраторы: Каталог/ Под ред. Н.Д. Нефедова. – М.: ЦНИИТЭстроймаш, 1983. - 467 с.
21.ГОСТ 3. 1114-79. ЕСТД. Правила оформления документов, применяемых при нормировании технологических процессов (операций). Технико-нормировочная карта.
22.ГОСТ 3.1001-81 Общие положения
23.ГОСТ 3.1102-81 Стадии разработки и виды документов
24.ГОСТ 3.1103-82 Основные надписи
25.ГОСТ 3.1105-84 Формы и правила оформления документов общего назначения
26.ГОСТ 3.1109-82 Общие требования к комплектности и оформлению комплектов документов на единичные технологические процессы
27.ГОСТ 3.1407-86 Формы и требования к заполнению и оформлению документов на технологические процессы (операции), специализированные по методам сборки
28.ГОСТ 3.1507-84 Правила оформления документов на испытания
29.ГОСТ 3.1703-79* Правила записи операций и переходов. Слесарные, слесарно-сборочные работы
30.ГОСТ 14.201-83 Обеспечение технологичности конструкции изделий. Общие требования
31.ГОСТ 14.205-83 Технологичность конструкции изделий. Термины и определения
32.ГОСТ 23.887-79 Сборка. Термины и определения
33.РД 50-635-87 Методические указания. Цепи размерные. Основные понятия. Методы расчета линейных и угловых цепей
72

Приложения
Сборочный чертёж
73

Технологическая схема сборки шпинделя
ФЕДЕРАЛЬНОЕ АГЕНТСТВО ПО ОБРАЗОВАНИЮ
Федеральное государственное образовательное учреждение высшего профессионального образования
«Сибирский федеральный университет» (СФУ)
ПОЛИТЕХНИЧЕСКИЙ ИНСТИТУТ
В.Е. Авраменко. Н.С. Индаков
БАЗИРОВАНИЕ И БАЗЫ В МАШИНОСТРОЕНИИ
Красноярск 2007

УДК 621.8.001.66 (77)
Авраменко В.Е., Индаков Н.С. Базирование и базы в машиностроении: Учеб. пособие/КГТУ. Красноярск,2005.121с.
Изложены основные положения теории базирования. Приведена методика обоснования рационального варианта схемы базирования, задания по разработке схем базирования, примеры их выполнения и наиболее распространенные схемы базирования типовых деталей.
Учебное пособие рекомендуется для самостоятельной работы при изучении теоретического материала по курсу “Основы технологии машиностроения” выполнения курсовых и дипломных проектов и проведения практических занятий
Для студентов специальностей 151001, 151002
2

ОБЩИЕ ПОНЯТИЯ И ОПРЕДЕЛЕНИЯ
Базирование – придание заготовке или изделию требуемого положения относительно выбранной системы координат.
Эта система координат может быть связана с исполнительными поверхностями станка, приспособления для установки заготовки, измерительной системы или базами другой детали, определяющей положение данной детали.
База – поверхность или выполняющее ту же функцию сочетание
поверхностей, |
ось, |
точка, принадлежащие заготовки |
и |
используемые для |
базирования (рис. 1а, 1б) |
|
|
||
Комплект |
баз |
– совокупность трех баз, образующих |
систему координат |
заготовки или изделия (рис. 2,а)
Опорная точка – точка, символизирующая одну из связей заготовки или изделия с избранной системой координат (рис.2,б)
Для обеспечения неподвижности заготовки или изделия в избранной системе координат на них необходимо наложить шесть двухсторонних геометрических связей, для создания которых необходим комплект баз.
Если в соответствии со служебным назначением изделие должно иметь определенное число степеней свободы, то соответствующее число связей снимается.
Схема базирования – это схема расположения опорных точек на базах заготовки или изделия.
Условное изображение опорных точек и пример схемы базирования призматической детали приведены на рис.3
Все опорные точки на схеме базирования изображают условными значками и нумеруют порядковыми номерами, начиная с базы, на которой располагается наибольшее количество опорных точек.
При наложении в какой-либо проекции одной опорной точки на другую, изображается одна точка и около нее проставляют номера совмещенных точек. (Точки 4, 5 на рис. 3)
3

Рис. 1а. Поверхность или сочетание поверхностей, используемые для базирования.
4

Рис. 1б. Ось или точка, используемые для базирования.
5
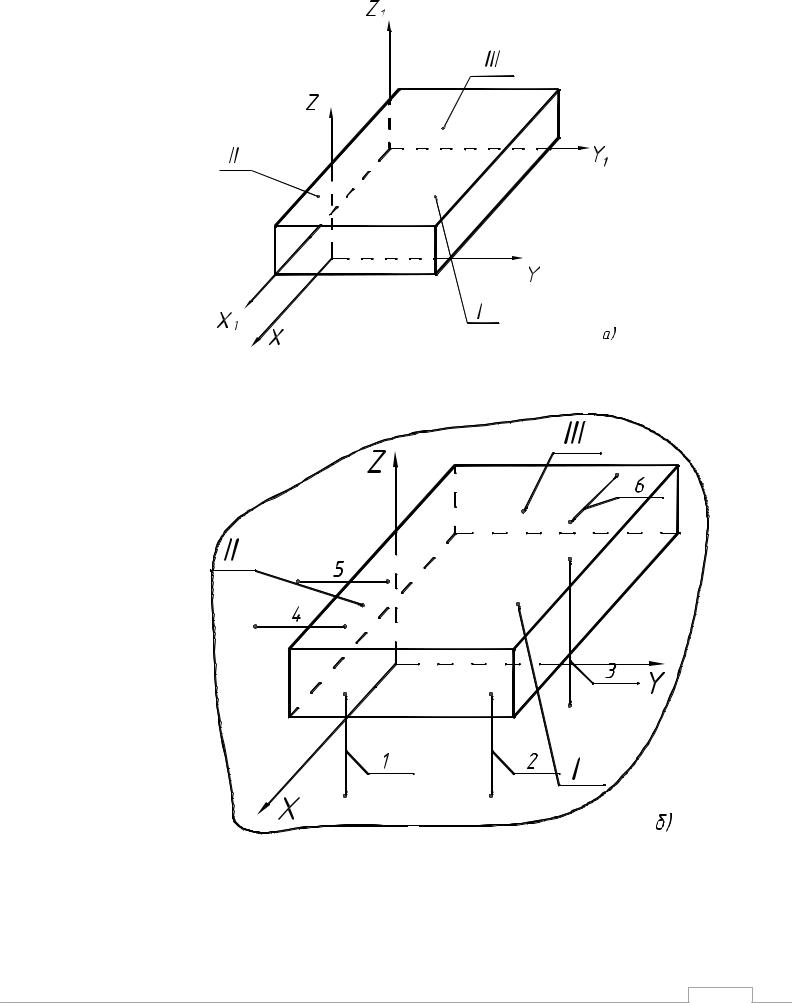
I, II, III – базы детали
I – 6 – двухсторонние связи I, II, III – базы детали
Рис.2. Определение положения твердого тела в координатной системе:
а – комплект баз призматической детали;
6

б – двухсторонние связи.
Рис.3. Условное обозначение опорных точек и схемы базирования призматической детали.
7

Число проекций заготовки или изделия на схеме базирования должно быть достаточным для четкого представления о размещении опорных точек.
Смена баз – преднамеренная или случайная замена одних баз другими с сохранением их принадлежности к конструкторским, технологическим или измерительным базам.
Погрешность базирования – отклонение фактически достигнутого положения заготовки или изделия при базировании от требуемого.
Закрепление – приложение сил или пары сил к заготовке или изделию для обеспечения постоянства их положения, достигнутого при базировании.
Установка – процесс базирования и закрепления заготовки или изделия. Погрешность установки – отклонение фактически достигнутого положения
заготовки или изделия при установке от требуемого.
ВИДЫ БАЗ
По назначению базы подразделяются на конструкторские, технологические
и измерительные.
Конструкторская база – база, используемая для определения положения детали или сборочной единицы в изделии.
Конструкторские базы, в зависимости от выполняемых ими функций, разделяют на основные и вспомогательные.
Основная база – конструкторская база, принадлежащая данной детали или сборочной единице и используемая для определения ее положения в изделии
(рис.4).
8

I, II, III – комплект основных баз шестерни
I, II – основные базы вала
I, II, III – комплект основных баз корпусной детали. Рис.4. К определению основной базы.
9

Вспомогательная база – конструкторская база, принадлежащая данной детали или сборочной единице и используемая для определения положения присоединяемой к ним детали или сборочной единицы (рис. 5).
Технологическая база – база, используемая для определения положения заготовки или изделия в процессе изготовления или ремонта (рис.6).
Измерительная база – база, используемая для определения относительного положения заготовки или изделия и средств измерения (рис.7).
По лишаемым степеням свободы различают следующие базы:
Установочная база – база, лишающая заготовку или изделие трех степеней свободы – перемещения вдоль одной координатной оси и поворотов вокруг двух других осей (рис.8).
Направляющая база – база, лишающая заготовку или изделие двух степеней свободы – перемещение вдоль одной координатной оси и поворота вокруг другой оси (рис.8).
Опорная база – база, лишающая заготовку или изделие одной степени свободы – перемещение вдоль одной координатной оси или поворота вокруг оси
(рис.8)
Двойная направляющая база – база, лишающая заготовку или изделие четырех степеней свободы: перемещений вдоль двух координатных осей и поворотов вокруг этих осей (рис.9).
Двойная опорная база – база, лишающая заготовку или изделие двух степеней свободы – перемещений вдоль двух координатных осей (рис.10).
По характеру проявления базы могут быть явными и скрытыми.
10

I, II, III – один из комплектов вспомогательных баз вала со шпонкой.
I, II, III – один из комплектов вспомогательных баз корпуса Рис.5. К определению вспомогательной базы
11

Рис.6. Технологические базы:
I, II, III – комплект технологических баз, определяющих положение заготовки в приспособлении.
12

Рис.7.Измерительная база. А – измерительная база детали
Рис.8. Схема баз призматической детали: I – установочная база заготовки, лишающая ее перемещения вдоль оси Z и поворотов вокруг
осей X и Y ;
II – направляющая база заготовки, лишающая ее перемещения вдоль оси Y и поворотов вокруг оси Z;
III – опорная база заготовки, лишающая ее
перемещения вдоль оси X;
13

Рис.9. Двойная направляющая база детали, лишающая ее перемещений вдоль осей Y и Z и поворотов вокруг осей Y иZ (Поверхность I )
Рис.10. Двойная опорная база детали, лишающая ее |
перемещений вдоль осей X и Y.(Поверхность I ) |
14

Явная база – база заготовки или изделия в виде реальной поверхности, разметочной риски или точки пересечения рисок (рис.11).
Скрытая база – база заготовки в виде воображаемой плоскости, оси или точки
(рис.11)
Полное наименование базы должно включать ее определение по трем классификационным признакам, располагаемым в следующем порядке:
по назначению; по лишаемым степеням свободы;
по характеру проявления;
Например:
“Конструкторская основная установочная явная база”. “Технологическая направляющая скрытая база”. “Измерительная опорная явная база”.
ОСНОВНЫЕ ПОЛОЖЕНИЯ ТЕОРИИ БАЗИРОВАНИЯ
Задачи установки и соединений деталей возникают:
при сборке машины;
впроцессе механической обработки, когда заготовку необходимо установить и закрепить с заданной точностью на столе или в приспособлении;
впроцессе измерения заготовки или детали.
Аналогичные задачи приходится решать при установке и закреплении режущего инструмента на шпинделе станка, борштанге, резцедержателе.
Соединение двух деталей можно представить как совмещение двух координатных систем, принадлежащих этим деталям.
Соединить деталь 1 (рис.12,а) с деталью 2, это значит привести в соприкосновение координатные плоскости X1 O1 Y1
15

Рис.11. Характер проявления баз:
I – установочная явная база заготовки;
II– направляющая скрытая база заготовки; III – опорная скрытая база заготовки;
1- 6 – опорные точки;
7 – заготовка
16

Рис.12. Схема совмещения координатных систем |
двух сопрягаемых деталей. |
17

, X1 O1 Z1 и Y1 O1 Z1 детали 1 (рис.12,б), материализованные в виде поверхностей ее основных баз, с координатными плоскостями YOX, XOZ, YOZ детали 2, материализованными в виде поверхностей ее вспомогательных баз.
Из теоретической механики известно, что каждое свободное тело имеет шесть степеней свободы относительно трех координатных осей X,Y, Z. Положение такого тела относительно выбранной системы координат определяется шестью независимыми величинами – шестью координатами. Каждая из координат лишает твердое тело одной степени свободы. Величина этой координаты определяет с требуемой точностью положение одной из точек твердого тела относительно выбранной координатной плоскости. Таким образом, требуемое положение твердого тела относительно выбранной системы координат достигается наложением геометрических связей.
При наложении геометрических связей тело лишается трех перемещений вдоль осей ОX, ОY, ОZ и трех поворотов вокруг этих осей, т.е. тело становится неподвижным в системе ОXYZ.
Наложение двухсторонних геометрических связей достигается соприкосновением поверхностей тела с поверхностями другого тела, к которому оно присоединяется, и приложением сил для обеспечения контакта между ними.
Тело, ограниченное реальными поверхностями, может контактировать с телами, определяющими его положение, в общем случае лишь по отдельным элементарным площадкам, условно считаемыми точками контакта.
При идеализации геометрической формы поверхностей соединяемых тел считается, что они полностью контактируют по сопрягающимся поверхностям.
Шесть связей, лишающих тело движения в шести направлениях, могут быть созданы контактом соединяемых тел в шести точках. В случае идеализации формы поверхностей считается, что осуществление необходимых связей достигается контактом тел по поверхностям, наличие реальных связей символизируется опорными точками, имеющими теоретический характер.
Для придания положения телу с использованием его плоскостей симметрии или осей поверхностей связи должны быть наложены непосредственно на плоскости симметрии, оси, линии или точки их пересечения.
В теоретической механике рассматривается определение положения тела относительно избранной системы координат OXYZ через определение положения связной с ним системы координат O1 X1 Y1 Z1. Жесткая связь системы O1 X1 Y1 Z1 с телом дает возможность отнести связи, налагаемые на тело, к системе O1 X1 Y1 Z1.
Для призматического тела при рассмотрении вопросов базирования целесообразно координатные плоскости системы O1 X1 Y1 Z1 строить на базах тела таким образом, чтобы одна из них, принимаемая за начало отсчета (рекомендуется X1O1Y1), бала лишена одного перемещения и двух поворотов, другая (X1O1Z1) – была перпендикулярна к X1O1Y1 и лишена одного перемещения и одного поворота, третья (Y1O1Z1) – была перпендикулярна к X1O1Y1 и Y1 O1Z1 и лишена одного перемещения.
Из требований к относительному положению координатных плоскостей следуют требования к относительному положению баз, входящих в состав комплекта и представляющих систему O1X1Y1Z1.
18

В зависимости от конструкции детали, характера и условий решаемой задачи координатные плоскости системы O1X1Y1Z:
либо материализуются точками контакта или непосредственно поверхностями тела, используемыми в качестве баз;
либо представляются мысленно; либо создаются комбинированным способом.
К мысленному построению координатных плоскостей приходится прибегать, когда требуется определить положение тела, используя его центр, оси поверхностей и плоскости симметрии, а также в случае ориентации визуально.
Мысленно создаваемые координатные плоскости совмещаются с центром или осями поверхностей тела. В качестве их используются плоскости симметрии, а при отсутствии таковых координатные плоскости связываются с характерными поверхностями или сечениями, позволяющими судить о положении тела. На координатных плоскостях мысленно размещаются опорные точки, символизирующие необходимые связи (рис.2,б).
|
Z1 |
|
|
Z |
|
|
|
5 |
|
|
6 |
O1 |
|
Y1 |
|
|
3 |
|
|
|
|
|
|
|
|
2 |
Y |
|
|
|
4
1
X1
X
Рис.13. Пример построения систем O1X1Y1Z1 при контакте тел по реальным поверхностям:
I – установочная база;
II – направляющая база; III – опорная база;
1-6 – точки контакта
19

Материализация координатных плоскостей точками контакта исходит из физической сущности сопряжения тел по поверхностям, имеющим отклонение формы от идеальной. Положение тела, устанавливаемого на реальные поверхности, определяется через координаты точек контакта, возникающих на базах (рис.13).
При идеализации геометрической формы базирующих поверхностей за координатные плоскости принимаются сами базирующие поверхности (рис.14).
Создание системы координат O1X1Y1Z1 комбинированным способом имеет место, когда роль одной части баз выполняют оси поверхностей тела, плоскости симметрии и т.д., а другой – сами поверхности тела (рис.15).
КЛАССИФИКАЦИЯ БАЗ
Все многообразие поверхностей деталей изделий машиностроения сводится к четырем видам:
исполнительные поверхности – поверхности, при помощи которых деталь выполняет свое служебное назначение;
основные базы – поверхности, при помощи которых определяется положение данной детали в изделии;
вспомогательные базы – поверхности данной детали, при помощи которых определяется положение присоединяемой к ней детали;
свободные поверхности – поверхности, не соприкасающиеся с поверхностями других деталей.
Базирование деталей реализуется на всех этапах создания изделия: при конструировании, в технологическом процессе изготовления деталей, при измерении и сборке изделия. Отсюда вытекает необходимость разделения баз по назначению на три вида: конструкторские, технологические и измерительные.
Группу конструкторских баз составляют основные и вспомогательные базы. Это подразделение конструкторских баз действительно как для изображения изделия на чертеже, так и изготовленного изделия. Необходимость такого подразделения вытекает из различия роли основных и вспомогательных баз и
20

Z1Z |
|
|
6 |
5 |
|
O1 |
Y1Y |
|
3 |
4 |
O |
2 |
1 |
X1
X
Рис.14. Пример построения системы координат O1X1Y1Z1 при контакте тел по идеализированным поверхностям:
I – установочная база (т.1, 2, 3);
II – направляющая база (т.4, 5); III – опорная база (т.6);
1-6 – опорные точки
21

Рис.15. Примеры построения системы координат O1X1Y1Z1 комбинированным способом:
а – при базировании зубчатого колеса с длинной ступицей: I – двойная направляющая скрытая база;
II – опорная база; III – опорная скрытая база;
22

б – при базировании узкого зубчатого колеса:
I – установочная база; II – двойная опорная скрытая база; III – опорная скрытая база
важности учета этого при конструировании (выборе конструктивных форм поверхностей деталей, задания их относительного положения , простановке размеров, разработке норм точности и т.д.), разработке и осуществлении технологических процессов.
Законы базирования являются общими для всех стадий создания изделия. Поэтому, независимо от назначения, базы могут различаться лишь по отнимаемым от базируемых заготовки или детали степеням свободы и по характеру проявления. Это обстоятельство является основанием для выдвижения еще двух признаков классификации: по лишаемым базой степеням свободы и по характеру проявления.
Схематично классификация баз представлена на рис.11.
РАСПОЛОЖЕНИЕ ОПОРНЫХ ТОЧЕК
Можно выделить три группы деталей, отличающиеся присущим им комплектами баз, образующих их координатные системы, и расположением опорных точек на базах, символизирующих двухсторонние связи детали с избранной системой координат:
призматические детали;
цилиндрически детали (L/D>1);
диски (L/D<1).
Координатную систему O1X1Y1Z1 призматической детали образуют плоскости
(рис.2).
Опорные точки, символизирующие двухсторонние связи призматической детали с избранной системой координат OXYZ, целесообразно расположить на ее базах следующим образом:
три опорные точки (т.1,2,3) на поверхности, имеющей максимальные габариты (установочная база, определяющая положение детали относительно координатной плоскости XOY);
две опорные точки (т.4,5) на поверхности максимальной протяженности (направляющая база, определяющая положение детали относительно координатной плоскости YOZ);
одну (т.6) на поверхности с минимальными габаритами (опорная база, определяющая положение детали относительно плоскости XOZ).
Таким образом, комплект баз, формирующих координатную систему призматической (корпусной) детали составляют базы:
установочная; направляющая;
23

опорная базы;
Штриховыми линями, соединяющими поверхности детали с координатными плоскостями, изображены связи, называемые в механике удерживающими или двухсторонними.
Если у корпусной детали нет трех развитых (или обработанных) плоскостей, образующих ее координатную систему, роль направляющей и опорной баз могут выполнять крепежные (или специально обработанные технологические) отверстия на основании. (Приложение 1, схема 3).
Другие возможные варианты комплектов баз корпусных деталей приведены ниже.
Положение цилиндрической детали относительно трех выбранных координатных плоскостей определяется также шестью координатными или опорными точками.
Координатную систему, связанную с цилиндрической деталью, целесообразно “построить” следующим образом:
координатную плоскость X1O1Z1 совместить с одним из торцов детали, а ось Y1 – с осью цилиндрической поверхности (рис.16).
Двухсторонние связи детали с координатной системой OXYZ в данном случае распределятся следующим образом:
четыре координаты (т.1, 2, 3, 4) определят положение оси цилиндрической поверхности относительно координатных плоскостей XOY и YOZ; ось цилиндрической поверхности в данном случае выполняет роль двойной направляющей базы;
одна координата (т.5) определяет положение детали относительно координатной плоскости XOZ;
24

z |
|
|
|
|
z1 |
5 |
|
|
|
||
|
o1 |
x1 |
|
4 |
|
||
|
|
||
3 |
|
|
|
O |
y1 |
x |
|
2 |
|||
|
|
||
|
6 |
|
|
Y |
1 |
|
|
|
|
Рис.16. Схема определения положения цилиндрической детали (L/D>1) относительно трех координатных плоскостей
25

торец детали с опорной точкой 5 является опорной базой, лишающей возможности перемещения в направлении оси Y;
координата 6 связывает точку, лежащую на плоскости X1O1Y1, с координатной плоскостью XOY и реализует еще одну опорную базу, лишающая деталь возможности вращения вокруг собственной оси.
Таким образом, комплект баз цилиндрической детали, формирующих ее координатную систему, состоит из двойной направляющей и двух опорных баз.
Возможные схемы установки цилиндрических деталей и соответствующие им теоретические схемы базирования приведены в приложении.
Координатная система диска строится аналогично цилиндрической детали (рис.17). Координатная плоскость X1O1Z1 совмещена с базовым торцом диска, а ось Y1 – с осью цилиндрической поверхностью диска.
Расположение опорных точек, символизирующих двусторонние связи диска с координатной системой XOY в данном случае иное:
три координаты (т.1, 2, 3) определят расположение торца и связанной с ним координатной плоскости X1O1Y1 относительно плоскости XOY: торец диска выполняет роль установочной базы.
две координаты (т.4,5) определят положение оси диска относительно координатных плоскостей XOY и YOZ; ось (центр) диска является двойной опорной базой.
координата 6 связывает точку, лежащую на плоскости X1O1Y1, с координатной плоскостью XOY и реализует опорную базу, лишающую диск возможности вращения вокруг собственной оси.
Таким образом, комплект баз, образующих координатную систему диска, состоит из установочной, двойной опорной и опорной баз.
26

Z |
4 |
y1 |
O |
|
3 |
|
Z1 |
|
2 |
|
1 |
o1 |
x1 |
X
5 6
Y
Рис.17. Схема определения положения диска (L/D<1) относительно трех координатных плоскостей
27

Zz1
|
5 |
6 |
4 |
|
|
|
|
|
|
|
3 |
|
|
2 |
1 |
|
X |
Y |
|
x1 |
y1 |
|
|
Рис.18. Схема превращения координат в шесть опорных точек
28

ПРАВИЛО ШЕСТИ ТОЧЕК
Если соединение двух деталей рассматривать как совмещение двух координатных систем OXYZ и O1X1Y1Z1 (рис.18), то шесть координат, определяюших их положение на рис.12, превращаются в шесть опорных точек.
Следовательно, для определения положения детали относительно другой детали необходимо и достаточно иметь шесть опорных точек. Этот вывод получил название “правила шести точек”.
Необходимость в дополнительных опорных точках (больше шести) возникает только в случаях, когда необходимо повысить жесткость обрабатываемых деталей с целью исключения их деформаций под действием сил резания. Примером может служить применение подводимых опор на операциях фрезерования, а также дополнительных опор – люнетов при обработке нежестких валов.
29

СКРЫТЫЕ БАЗЫ
Во всех случаях установки деталей, у которых количество конструктивно оформленных баз меньше трех, приходится пользоваться так называемыми скрытыми базами.
Скрытая база – это база заготовки или изделия в виде воображаемой плоскости, оси или точки.
Скрытыми базами называют координатные плоскости, мысленно проводимые перпендикулярно к имеющимся у детали конструктивно оформленным базам для доведения их общего числа до трех.
Скрытые базы чаще всего мысленно проводят по осям симметрии деталей. Для обеспечения определенности базирования и неподвижности детали в
процессе обработки или ее работы в изделии скрытые базы должны быть материализованы. Материализация скрытых баз может осуществляться:
силами трения, веса, магнитными силами одновременно с закреплением заготовки или изделия;
путем создания специальных поверхностей.
Пример. Установка призматической детали на магнитной плите шлифовального станка (рис.19).
Особенность установки состоит в том, что на магнитной плите отсутствует установочные элементы, определяющие положение направляющей и опорной баз заготовки. Единственной конструктивно оформленной базой приспособления в данном случае является установочная база – плоскость верхней плиты.
Две недостающие координатные плоскости проводятся мысленно перпендикулярно установочной базе по осям симметрии магнитной плиты
(рис.19,а).
Аналогично координатная система мысленно привязывается к осям симметрии обрабатываемой заготовки и ее установочной технологической базе (рис.19,в).
Точность установки заготовки на магнитной плите будет зависеть от глазомера станочника, мысленно совмещающего при базировании координатные системы приспособления и заготовки.
30

Z
X
а)
Y
Z
X
Y |
|
б) |
|
|
|
4 |
|
6 |
|
5 |
|
1 |
2 |
3 |
1 |
|
2 |
|
4 |
6 |
3 |
5 |
|
|
|
в)
Рис.19. Базирование призматической детали на магнитной плите
31

Рис.20. Пример материализации двух скрытых баз в виде плоскостей, расположенных на специальных приливах
32

С целью повышения точности и сокращения затрат времени на установку скрытые базы могут быть материализованы (рис.20).
Пример 1. При обработке ступенчатого вала двойную направляющую базу (ось вала) и опорную базу, лишающих вал возможности перемещения вдоль оси, материализуют в виде двух центровых отверстий. Центровые отверстия лишают вал пяти степеней свободы (прил.1, рис.6, т.1 - 5). Шестой степени свободы (возможности свободного вращения вокруг собственной оси) вал лишается с помощью скрытой опорной базы. Ее роль выполняет координатная плоскость, проходящая через ось вращения вала и точку касания хомутика с поводковым пальцем патрона.
Пример 2. При установке заготовки зубчатого колеса в трехкулачковом патроне явными являются установочная база (торец) и двойная центрирующая база (наружная цилиндрическая поверхность), определяющая положение оси вращения диска. Недостающая опорная база, лишающая диск возможности свободного вращения вокруг собственной оси (поворота относительно кулачков патрона) мысленно достраивается в виде плоскости, перпендикулярной торцу и проходящей через ось диска (прил.1, рис.5).Радиальное положение этой базы неопределенно (в данном случае в ее определенности нет необходимости). Невозможность поворота заготовки относительно патрона обеспечивается силами трения между кулачками патрона и наружной цилиндрической поверхностью заготовки.
В ряде случаев скрытые базы материализуют в виде различных рисок и точек от накернивания, представляющих собой следы пересечения надлежащей скрытой базы с поверхностью детали (прил.1, рис.11).Скрытые базы, материализованные в виде разметочных рисок, используют для определения положения детали, например, на столе станка.
33

МЕТОДЫ ПОЛУЧЕНИЯ И ИЗМЕРЕНИЯ РАССТОЯНИЙ, РАЗМЕРОВ И ОТНОСИТЕЛЬНЫХ ПОВОРОТОВ ПОВЕРХНОСТЕЙ ДЕТАЛЕЙ
Цепной метод
Сущность метода заключается в том, что каждый последующий размер, расстояние или поворот поверхности получается или измеряется вслед за ранее полученным или измеренным, причем для этого в качестве одной из технологических или измерительных баз используется связывающая их общая поверхность.
Таким образом, при получении каждого последующего звена (размера или поворота поверхности) происходит переход к новой технологической базе и тем самым исключается влияние погрешности других звеньев на вновь получаемое звено (рис.20).
Независимость погрешности, получаемой на каждом из цепных звеньев, от погрешностей остальных звеньев, является основным преимуществом цепного метода получения расстояний и поворотов поверхностей.
В отличие от этого погрешности, получаемые при цепном методе на координатных звеньях, т.е. на звеньях, измеренных от какой-либо одной поверхности, выбранной за технологическую базу, зависят от погрешности цепных звеньев, образующих данное координатное звено.
При цепном методе получения линейных размеров А1 – А4 ступенчатого валика (рис.21) каждый его координатный размер Б2 , Б3 и Б4 представляет собой замыкающее звено размерной цепи, составляющими звеньями которой являются соответствующие цепные звенья. Например, координатный размер Б3 является замыкающим звеном размерной цепи Б3= А1+А2+А3, координатный размер Б4 является замыкающим звеном размерной цепи Б4= А1+А2+А3+А4 и т.д.В соответствии с этим погрешность каждого координатного звена при цепном методе получения размеров, расстояний и относительных поворотов поверхностей зависит от погрешностей цепных звеньев, образующих данное координатное звено:
34

Рис.20. Схема получения точности линейных размеров ступенчатого валика цепным методом.
Рис.21.Схема образования погрешностей на координатных размерах ступенчатого валика при цепном методе получения его размеров.
Рис.22.Схема образования погрешностей на цепных размерах
35

вала при координатном методе получения его размеров. |
Рис.23.Схема получения точности относительных |
поворотов поверхностей корпусной детали |
координатным методом. |
36

ωБ 3= ωА 1+ωА 2+ωА3,
ωБ 4= ωА 1+ωА 2+ωА3+ωА 4.
Координатный метод
Сущность метода заключается в том, что все размеры (расстояния или повороты) поверхностей детали получают и измеряют от одной и той же выбранной базы, независимо друг от друга. Погрешность каждого из координатных звеньев не зависит от погрешностей других координатных звеньев (рис.22.).
Погрешности, получаемые на каждом цепном звене при использовании координатного метода, зависят от погрешностей координатных звеньев, образующих данное цепное звено. Цепные размеры А2 и А3 ступенчатого вала (рис.22.) представляют собой замыкающие звенья размерных цепей А2= Б2 – Б1 и А5= Б5 – Б4 . В соответствии с этим погрешности цепных звеньев.
ωА2 = ωБ2+ωБ1;
ωА5 = ωБ5+ωБ4;
Аналогично, для цепных звеньев, определяющих относительный поворот поверхностей (осей) (рис.23),
ωγ1=ωβ2+ωβ1;
ωγ2=ωβ4+ωβ3.
Сопоставление рассмотренных методов получения расстояний, размеров и поворотов поверхностей показывает, что использование при обработке деталей координатного метода позволяет получить, как правило, более высокую точность.
37

Комбинированный метод
Сущность метода заключается в том, что при изготовлении деталей для получения одних звеньев используется координатный метод, а для получения других – цепной.
Для получения звеньев, определяющих относительные повороты поверхностей (параллельность, перпендикулярность) и большую часть расстояний, преимущественно используется координатный метод.
Цепной метод используется в тех случаях, когда:
на отдельных расстояниях при поворотах поверхностей требуется обеспечить очень высокую точность;
использование координатного метода дает на надлежащем цепном звене погрешность больше установленного допуска;
погрешность установки, связанная со сменной технологических баз, относительно невелика.
38

ПОГРЕШОСТЬ УСТАНОВКИ
Одной из причин, вызывающих погрешности выполняемого размера и отклонения взаимного положения обрабатываемых поверхностей заготовки, является погрешность ее установке на станке.
Применяют три способа установки и обработки заготовок на станке: 1.Обработка способом автоматического получения размеров, с установкой
заготовки в приспособлении без выверки. Обработка выполняется инструментом, предварительно настроенным на заданный размер. Способ применяется в серийном и массовом производстве при обработке заготовок партиями с одной наладки технологической системы.
2.Обработка способом индивидуального получения размеров (или способом пробных проходов) с установкой заготовки в приспособлении или на столе станка путем выверки положения каждой заготовки по разметочным рискам или по поверхностям заготовки.
Вэтом случае возникает погрешность установки – выверки ∆εy–b, включающая, как правило, и погрешность закрепления [ 8, табл.16 – 17].
Впроцессе установки заготовок с выверкой возникает погрешность установки
–выверки ∆εy – b, учитывающая неточность выверки по разметочным рискам или непосредственно по поверхностям заготовки. Данные для определения величины
∆εy –b, включающей и погрешность закрепления для различных способов установки приведены в табл. 16 – 17 [8].
3.Обработка на станках с ЧПУ с установкой по определенным поверхностям заготовки. При этом оценивают фактическое положение заготовки в координатной системе станка и вносят необходимую коррекцию в программу обработки, учитывающую погрешность установки. В этом случае требования к точности установки заготовки в приспособлении более низкие, чем при первых двух
вариантах установки, и погрешность установки ∆εy – n зависит от точности измерения заготовки и определения ее положения на станке.
39

При первом способе применяют специальные приспособления для установки заготовок, состоящие из установочных, зажимных и направляющих элементов, смонтированных в общем корпусе. Установку заготовок осуществляют доведением их базовых поверхностей до соприкосновения с установочными элементами приспособления (процесс базирования) и последующим закреплением заготовки зажимным устройством. Преимуществами этого способа установки являются быстрота, устранение выверки и влияния субъективных факторов на точность положения заготовки в приспособлении.
При обработке способом автоматического получения размеров станок предварительно настраивают, т.е. устанавливают режущие кромки инструмента на размер статической настройки относительно технологической базы детали. При этом обеспечивается точность заданного размера в партии заготовок при однопроходной обработке. Это положение инструмента остается неизменным до очередной поднастройки, вызванной его износом.
При обработке в приспособлении на предварительно настроенном станке погрешность установки εy складывается из погрешности базирования εδ,
погрешности закрепления εз и погрешности положения заготовки ε пр, вызываемой неточностью приспособления.
При укрупненных расчетах точности обработки погрешность εy для различных способов установки можно определить по табл. 12 – 18 [8].
Погрешность базирования возникает при несовмещении измерительной и технологической базы заготовки, относительно которой настраивали режущие кромки инструмента на заданный размер (рис.24.)
Так как указанные погрешности являются случайными величинами,
εy = εδ2 +ε32 +εпр2
.
40

Погрешность положения заготовки εпр, вызванная неточностью приспособления
εпр = ε уе2 +εи +εс2,
где εуе – погрешность, вызванная неточностью изготовления и сборки установочных элементов приспособления;
εи – погрешность, вызванная износом установочных элементов приспособления;
εс – погрешность установки и фиксация приспособления на станке. Суммарную погрешность выполняемого размера можно представить суммой
Тi=εy+ω,
где ω – часть суммарной погрешности, вызванная упругими и тепловыми деформациями, износом и погрешностью настройки инструмента; при укрупненных расчетах величину ω можно представить среднеэкономической нормой точности используемого метода обработки [ 8,9 ].
Для принятого метода обработки и схемы установки заготовки расчетное значение ожидаемой суммарной погрешности обработки должно быть меньше заданного допуска на выполняемый размер [Тi]:
Тi ≤ [Ti].
Погрешность базирования определяют для конкретного выполняемого размера как разность предельных расстояний от измерительной базы данного размера до
режущих кромок инструмента, настроенного на этот размер. Поэтому величине εδ в расчетах присваивают индекс соответствующего размера.
41

Анализ с целью определения погрешности базирования ведут в следующем порядке:
1.Определяют положение измерительной базы выполняемого размера.
2.Определяют технологическую базу, относительно которой настроены режущие кромки инструмента.
3.Если указанные измерительная и технологическая базы совпадают
(выполняется принцип единства баз), то для данного выполняемого размера εδ=0. 4.Если измерительная и технологическая базы не совпадают, погрешность
базирования не равна нулю (εδ≠0) и ее необходимо определить на основе геометрических расчетов как разность предельных расстояний от измерительной базы выполняемого размера до режущих кромок инструмента.
Формулы для расчета погрешности базирования при различных способах установки приведены в табл.18 [8].
Пример решения и задания по выбору рациональных схем базирования и расчета погрешностей установок приведены в прил.3 [6].
Рис.24. Определение погрешности базирования: 1 – измерительная и технологическая базы размера А, относительно которой настроен инструмент для достижения размера А; 2,3 – измерительные базы соответственно размеров В и Е
42

Погрешность закрепления εз возникает вследствие смещения обрабатываемой заготовки под действием зажимающего усилия.
Количественно погрешность закрепления определяют как разность предельных расстояний от измерительной базы выполняемого размера до режущих кромок настроенного на этот размер инструмента.
Погрешность закрепления, как и погрешность базирования, рассматривают применительно к конкретному размеру детали.
Погрешность закрепления относительно размера А (рис.25.) не равна нулю
(εЗА≠0),тогда как для размера Е она равна нулю (εЗА=0), т.к. измерительная база размера Е.(поверхность 3) не перемещается в направлении размера Е под действием силы Q.
Смещения измерительной базы при закреплении заготовки, а следовательно, и
величина εЗ , определяются рассеянием упругих и контактных деформаций в стыке заготовки – установочные элементы приспособления. Величины полей рассеяния упругих и контактных деформаций зависят от направления зажимающего усилия и изменения его величины ∆Q при закреплении заготовок:
∆Q = Qmax - Qmin
где Qmax и Qmin – максимальное и минимальное значение силы закрепления при обработке партии заготовок.
Погрешность закрепления для схемы обработки, приведенной на рис.25, относительно размера В
εзв = вмах – вмin=ymax – ymin;
относительно размера А
εза = Aмах – Aмin=ymax – ymin;
где вмах , вмin – предельные расстояния от измерительной базы размера В до режущих кромок инструмента;
43

Рис.25. Определение погрешности закрепления: 1, 2 – положение измерительных баз соответственно размеров А и В до закрепления силой Q
44

Aмах, аmin – предельные расстояния от измерительной базы размера А до режущих кромок инструмента.
ymax, ymin – максимальные и минимальные контактные деформации в стыке заготовка – установочные элементы приспособления при обработке партий заготовок.
Смещение вследствие контактных деформаций стыка заготовка – установочные элементы приспособления вычисляют по эмпирическим зависимостям типа
ε3=СQn cosα,
где С – коэффициент, характеризующий условия контакта, материал, твердость поверхностного слоя заготовки, шероховатость поверхности технологической базы; для партии заготовок этот коэффициент изменяется в пределах
∆С=Смах – Cmin ;
значения коэффициента С приведены в табл.22 [ 8 ] ;
Q – сила зажима, изменяющаяся в пределах ∆Q=Qmin – Qmax ;
α – угол направлением выдерживаемого размера и направлением наибольшего смещения.
Погрешность закрепления
− −n |
|
C 2 |
n Q |
2 |
||||
Eз =С Q cosα |
|
|
|
+ |
|
|
, |
|
C |
Q |
|||||||
|
|
|
|
|
|
|||
|
|
|
|
|
|
|
|
−−
где C и Q – средние значения параметров; ∆С и ∆Q – рассеяние значений С и Q.
Учитывая при расчетах только колебания твердости ∆HB и шероховатости ∆RZ поверхности заготовки, используемой в качестве технологической базы, получим
C = (K |
|
HB p -1 |
HB) |
2 |
|
R |
|
)2 . |
HB |
+ (K |
RZ |
Z |
|||||
|
|
|
|
|
|
Коэффициенты KHB и KRZ приведены в табл.22 [8]. Показатель степени ρ при установке на опоры и пластины принимают ρ = 1; при установке на призму ρ = - 1.
45

Погрешность закрепления может быть устранена или снижена за счет: 1.Выбора соответствующего направления зажимающего усилия, при котором
не происходит смещения измерительной базы выполняемого размера. 2.Стабилизации величины зажимающего усилия и условий в зоне контакта
технологической базы с установочными элементами приспособления:
-шероховатости поверхности, используемой в качестве технологической
базы;
-твердости материала заготовки.
В этом случае постоянная величина смещения измерительной базы при закреплении может быть учтена при настройке инструмента.
3.Повышения жесткости установочных элементов приспособления, увеличения площади опор.
4.Повышения качества поверхностей технологических баз и опор.
Погрешность положения заготовки εпр , вызванная неточностью приспособления, определяется ошибками изготовления и сборки его установочных
элементов εус , их прогрессирующим износом εи , а также ошибками установки и
фиксации приспособления на станке εс.
Рассматривая эти погрешности как рассеяния случайных величин, получаем
εпр = ε2 ус + ε2и + ε2с.
Составляющая εус характеризует неточность положения установочных элементов приспособления. При использовании одного приспособления она представляет собой систематическую погрешность и ее можно устранить коррекцией положения инструмента при настройке.
46

Величина εус в зависимости от размеров приспособлений находится в пределах
0,01 – 0,05 мм.
Составляющая εи характеризует изменение положения контактных поверхностей установочных элементов в результате их износа в процессе эксплуатации приспособления. Исходя из требуемой точности установки износ регламентируют заранее рассчитанной величиной.
Допустимая величина износа и определяется допустимой величиной погрешности εи и = εи – для опор и и = εи Sin α2 −для призм . Величина Eи в
предположении, что погрешности Eуc и Ec можно компенсировать настройкой инструмента, определяется как:
[ |
]= T ω= |
2 |
+ |
2 |
, |
εи |
i |
εб |
|
εз |
|
где Тi – допуск на выполняемый размер; ω – средне экономическая норма точности используемого метода обработки.
Рис.26. Определение погрешности базирования при установке в призму. |
47

Пример. Определить погрешность базирования для размеров А и В при
фрезеровании уступа на заготовке |
по схеме, приведенной на рис.25. Заготовка |
|
закреплена силой Q. Режущие кромки на торце фрезы настроены относительно |
||
технологической |
установочной |
базы 1. При обработке партии заготовок |
погрешность базирования относительно размера А равна нулю (εбА=0), так как измерительная и технологическая базы совмещены в плоскости 1 заготовки.
Измерительной базой для размера В является плоскость 2 заготовки. В этом случае технологическая база (плоскость 1), относительно которой настроены режущие кромки инструмента, не совпадает с измерительной. При обработке партии заготовок предельные расстояния от измерительной базы (плоскость 2) до режущих кромок инструмента будут изменяться в пределах допуска на размер С. Погрешность базирования для размера В равна допуску δ на размер С заготовки
(εδв=δс).
Пример. Определить погрешность базирования для размеров h1, h2, h3 при обработке плоскости на цилиндрической заготовке (рис.26). Заготовка устанавливается в призму. Двумя окружностями изображена наибольшая и наименьшая по диаметру заготовки в партии с осями в точках C / и С //. Режущие кромки инструмента перед обработкой партии заготовок настроены на размер С=Const относительно вершины двугранного угла призмы (точка 0). При выполнении размера h1 погрешность базирования определяется разностью предельных расстояний от измерительной базы размера h1 (образующих А / и А //) до режущих кромок (точка А///) инструмента, настроенного на выполнение размера h1:
εбh1=OA/ - OA//
|
|
|
|
|
|
|
|
|
OA/ = OC / +С/ A/ = |
С/ K / |
+C / А/ = |
D max |
|
1 |
|
|
|
|
|
+1 |
||||||
|
α |
|
|
α |
||||
|
Sin |
|
2 |
Sin |
|
|||
|
2 |
|
|
|
2 |
|
||
|
|
|
|
|
|
|
48

По аналогии:
|
|
|
|
|
|
|
|
|
|
|
|
OA// |
|
D min |
|
|
|
1 |
|
|
|||
= |
|
|
|
|
|
+1 . |
|||||
|
|
|
|
|
α |
||||||
|
|
2 |
|
|
|
Sin |
|
||||
|
|
|
|
|
|
|
2 |
|
|||
Следовательно. |
|
|
|
|
|||||||
|
|
|
|
|
|
||||||
ε |
= |
δD |
|
|
|
1 |
|
|
+1 |
; |
|
2 |
|
|
|
|
α |
||||||
δh1 |
|
|
Sin |
|
|
|
|||||
|
|
|
|
2 |
|
|
|
здесь δD – допуск на диаметр заготовки; α – угол призмы.
По анологии для размеров h2 и h3:
ε |
|
= |
δD |
|
1 |
|
|
|
|
1 ; |
|||
|
2 |
|
|
|
|
α |
|||||||
δh2 |
|
|
|
|
Sin |
|
|||||||
|
|
|
|
|
|
|
2 |
|
|
|
|||
ε |
= |
δD |
|
1 |
|
|
|
|
|||||
|
|
|
|
|
α |
|
|||||||
δh3 |
|
|
|
2 |
|
|
|
Sin |
|
||||
|
|
|
|
|
|
|
|
2 |
|
Пример. Определить погрешность базирования относительно размера В при подрезании торцов ступенчатого вала (рис.27).
При установке заготовки в жестких центрах (рис 27,а) измерительная база размера В (торец 1) будет изменять свое положение относительно режущей кромки резца, настроенного на размер С=Const относительно вершины конуса в пределах допуска на глубину зацентровки Тц.(hbc 27,б)
Поэтому
εδВ=Тц
При использовании плавающего переднего центра измерительная база размера В (торец 1) совпадает с технологической базой, относительно которой настроен подрезной резец (торец патрона) на выполняемый размер. В этом случае
исключается влияние глубины зацентровки на точность размера В: εбВ=0.
49

50

Рис.27. Определение погрешности базирования при подрезании торцов ступенчатого вала.
Пример. Определить погрешность базирования для размера А при установке заготовки базовым отверстием на цилиндрическую оправку с закреплением по торцам (рис.28).
При посадке без зазора (на разжимную оправку)
εδА= T2D ,
где δD – допуск на диаметр заготовки.
При наличии зазора (посадка на жесткую оправку) погрешность базирования для размера А возрастает на величину максимального значения зазора Smax:
EδA = T2D + Smax = T2D +TD + Smin +T∂ ,
где TD – допуск на диаметр базового отверстия заготовки; Smin – минимальный зазор в сопряжении; T∂ - допуск на диаметр оправки.
Пример. Определить ожидаемую суммарную погрешность обработки для размеров А1 и А2 (рис 1. прил.3) при фрезеровании уступа на втулке. Установка производится на цилиндрическую оправку.
Диаметр базового отверстия D = 30+0,039мм.
Диаметр оправки d=30−−00,,007016 мм.
Средне экономическая норма точности используемого метода обработки ω =0,120 [8 с.26].
Считать, что составляющие погрешности установки – погрешность закрепления и положения заготовки – равны нулю, т.е.
εз=εп.з.=0.
Исходя из схемы установки заготовки в приспособлении погрешность базирования при выполнении размера A1 равна половине максимально возможного зазора между поверхностями отверстия и оправки:
51

E |
= S |
max |
2 = |
1 |
(T |
D |
+ S |
min |
+T ) = |
1 |
(0,039 + 0,07 + 0,09) = 0,028мм |
|
|
||||||||||
|
δ A1 |
2 |
|
|
α |
2 |
|
||||
|
|
|
|
|
|
|
|
|
Погрешность базирования при выполнении размера А2 EδА2=0, так как измерительная и технологическая базы совмещены.
Поскольку по условию задачи Eз=Eп.з.=0 , суммарные погрешности обработки для размеров А1 и А2
ΣεА1= εδА1+ω=0,028+0,120=0,148мм
ΣεδА2+ω=0+0,120=0,120мм
Рис.28.Определение погрешности базирования при установке на оправку с зазором
52

ОСНОВНЫЕ ПРИНЦИПЫ БАЗИРОВАНИЯ.
Принцип единства баз
Сущность принципа единства баз состоит в том, чтобы в качестве технологической и измерительной баз использовать одни и те же поверхности, предпочтительно – основные конструкторские базы детали.
Целесообразность соблюдения этого принципа определяется тем, что по служебному назначению детали большинство ее поверхностей связаны расстояниями и относительными поворотами с ее конструкторскими базами.
В целях реализации принципа единства баз на первых операциях технологического процесса обрабатывают основные конструкторские базы, которые затем используют в качестве технологических и измерительных баз на большинстве операций обработки детали.
Совмещение технологических, измерительных и основных конструкторских баз позволяет повысить точность обработки, в частности за счет устранения погрешности базирования.
Несоблюдение принципа единства баз ведет к появлению дополнительных звеньев в технологических и измерительных размерных цепях, а следовательно, дополнительных погрешностей при достижении заданной точности размеров и относительных поворотов поверхностей.
При достижении точности размера А1 и относительного поворота γ1(рис.29) поверхность I используется в качестве измерительной и технологической базы, относительно которой режущий инструмент настраивается на достижение размера
А1 и относительного поворота γ1. Поэтому размер А1 и поворот γ1 при этой схеме базирования образуются как замыкающие звенья данной технологической системы.
При использовании схемы базирования, приведенной на рис.30, измерительная база размера А1 (поверхность I) не совпадает с технологической базой (поверхность II), относительно которой настроен инструмент на достижение размера А1.Размер А1 в этом случае формируется размерной цепью:
53

Рис.29. Схема фрезерования уступа (совпадение |
измерительной и технологической баз) |
Рис.30. Схема фрезерования уступа (несовпадение |
измерительной и технологической баз) |
54

А1=А2-А3
Погрешность размера А:
ωА1=ωА2+ωА3
Таким образом, если измерительная база не совмещена с технологической, погрешность достигаемого параметра возрастает на величину погрешности размера, связывающего измерительную и технологическую базы (ωА2).
Соответственно
ωγ1= ωγ2+ ωγ3.
При использовании основной конструкторской базы в качестве технологической и измерительной баз на большинстве операций технологического процесса в наибольшей степени реализуются преимущества координатного метода получения и измерения расстояний и относительных поворотов поверхностей.
55

Принцип постоянства баз
Сущность принципа постоянства баз состоит в том, чтобы на большинстве операций технологического процесса использовать один и тот же комплект баз.
Смена баз связана, как правило, с увеличением количества звеньев в технологических размерных цепях и как следствие, с увеличением погрешности заданных размеров.
Рассмотрим в качестве примера два варианта расточки отверстий в корпусной детали (рис.31).
Задачей обработки является обеспечение точности расстояния между осями отверстий (А∆) и параллельности этих осей.
Условно считаем, что каждое из отверстий Ø d и Ø D обрабатываются на отдельных технологических операциях.
Вариант I. Обработка отверстий с соблюдением принципа постоянства баз. На первой расточной операции (рис.32,а) обрабатывается отверстие Ø d.
Расточной инструмент настроен на размер А1 формирующийся как замыкающее звено в данной технологической системе.
На второй расточной операции обрабатывается отверстие ØD(рис.32,б). Достигаемым размером на этой на этой операции является размер А2.
Заданное расстояние между осями отверстий А∆ формируется как замыкающее звено технологической размерной цепи А (рис.32, в):
А∆=А2 – А1.
Погрешность замыкающего звена А∆ равна сумме погрешностей, присущих двум расточным операциям:
ωА∆=ωА1+ωА2.
Вариант II. Обработка отверстий со сменой технологических баз.
Первая расточная операция в этом варианте выполняется аналогично предыдущему варианту обработки (рис.33, а).
56

Рис.31. Эскиз корпусной детали
Рис.32. Обработка отверстий в корпусной детали с соблюдением принципа постоянства баз
57

Рис.33.Обработка отверстий в корпусной детали со сменой технологических баз
58

При выполнений второй расточной операции (рис.33, б) произведена смена баз, в качестве установочной технологической базы использована поверхность Б
(рис.31).
Достигаемым размером на этой операции является размер А2.
Заданное межосевое расстояние А∆ при втором варианте обработки формируется размерной цепью (рис.33,в). Помимо размеров А1 и А2 , достигаемых на двух расточных операциях, в эту размерную цепь входит размер А3, полученный на предыдущих растачиванию операциях фрезерования плоскостей А и Б.
Погрешность замыкающего звена А∆ при втором варианте обработки возрастает на величину погрешности размера А3, связывающего прежнюю (поверхность А) и новую (поверхность Б) установочные технологические базы:
ωА∆=ωА1+ωА2+ωА3.
Аналогично анализируются связи, обеспечивающие точность относительного поворота (параллельность) осей отверстий.
Последствиями смены технологических баз являются:
1.Необходимость ужесточения допусков на составляющие звенья, формирующие заданное замыкающее звено (в рассмотренном примере – размер А∆).
2. Дополнительные затраты на достижение заданной точности замыкающего звена, вызванные:
повышением точности настройки технологических систем (в рассмотренном примере – точности настройки расточного инструмента при достижении размеров А1
и А2); использованием более точного и дорогостоящего оборудования;
назначением жестких допусков на размеры, не являющие ответственными по служебному назначению детали (размер А3):
введением дополнительных технологических переходов для достижения “ужесточенных” допусков на составляющие звенья технологических размерных цепей.
59

Рис.34. Неорганизованная смена баз при установке в тисках вследствие погрешности углового
расположения направляющей технологической базы (поверхности А)
Рис.35. Неорганизованная смена баз вследствие недостаточных габаритов поверхности, используемой в качестве установочной
60

технологической базы (поверхности А)
Вряде случаев смена технологических баз является целесообразной или даже неизбежной:
вслучае физической невозможности обработки всех поверхностей детали с использованием одного комплекта технологических баз;
вслучае целесообразности использования цепного метода для достижения высокой точности отдельных размеров детали;
вцелях обеспечения точности и простоты измерений, сокращения расходов на измерительные средства.
Вотличие от рассмотренной организованной смены технологических баз в процессе обработки детали может происходить “неорганизованная” смена баз, причинами которой может быть:
разработка неверной теоретической схемы базирования; отсутствие необходимого силового замыкания;
погрешности линейных размеров и относительных поворотов поверхностей, используемых в качестве технологических баз (рис.34);
недостаточные габаритные размеры поверхностей, используемых в качестве технологических баз (рис.35).
61

ОПРЕДЕЛЕННОСТЬ И НЕОПРЕДЕЛЕННОСТЬ БАЗИРОВАНИЯ.
Необходимость силового замыкания.
Достигнутое при базировании положение детали может измениться, если возникнут силы и моменты сил, нарушающие контакт поверхностей детали с шестью опорными точками, определяющими ее положение. Следовательно, для сохранения правильного положения, полученного при базировании, необходимо обеспечить непрерывность контакта сопряженных баз двух деталей или, другими словами, определенность базирования.
Под определенностью базирования детали понимает неизменность ее положения относительно поверхностей другой детали или деталей, которые определяют ее положение при работе в машине или в процессе изготовления.
Для обеспечения определенности базирования к детали прикладываются силы, создающие силовое замыкание между соединенными деталями. Силы и их моменты, создающие силовое замыкание и обеспечивающие непрерывность контакта, должны бить больше сил и их моментов, стремящихся нарушить этот контакт.
Для создания силового замыкания используют: упругие силы материала крепежных деталей, силы трения, силу тяжести деталей, магнитные и электромагнитные силы, силы сжатого воздуха, жидкости, сочетания перечисленных сил.
Силовое замыкание вызывает контактные деформации сопряженных поверхностей, вносящие дополнительные погрешности в требуемое положение устанавливаемой детали. Эти деформации могут быть соизмеримыми с заданными допусками на обработку.
При приложении сил, обеспечивающих определенность базирования детали, наряду с контактными деформациями, возникают и собственные упругие деформации детали. Собственные деформации детали возрастают, если точки приложения сил, обеспечивающих контакт, не совпадают с расположением опорных точек. Возникавшие в этом случае моменты сил (рис. 36 ) вызывают деформации изгиба закрепляемой детали.
Под неопределенностью базирования детали понимают изменение требуемого положения детали относительно поверхностей детали (или деталей), определяющих ее положение. Неопределенность базирования характеризуется единичным или многократным нарушением контакта между базами устанавливаемой детали и деталей, определяющих ее положение.
62

Рис.36. Влияние расположения точек и приложения сил зажима на собственную деформацию детали
63

Для обеспечения определенности базирования детали необходимы: правильный выбор или создание комплекта необходимых баз; выполнение правила шести точек; создание правильного силового замыкания;
уменьшение контактных деформаций путем выбора рациональной конструкции опор, обеспечения необходимой точности геометрической формы и качества поверхностей, используемых для базирования;
уменьшение собственных упругих деформаций деталей путем применения дополнительных опор (например, люнетов), расположения зажимающих сил, по возможности, против опорных точек;
правильная последовательность приложения сил, исключающая изменения положения детали во время ее закрепления.
64

Выбор технологических баз
Последовательность выполнения первых этапов проектирования технологического процесса изготовления детали, включая выбор технологических баз, представлена на схеме (рис.37).
Основные положения по выбору технологических баз:
1.Выбору технологических баз предшествует анализ служебного назначения детали и обоснование технических условий на ее изготовление, позволяющие четко сформулировать задачи обработки.
2.Анализируя функции поверхностей деталей (исполнительные поверхности, основные и вспомогательные конструкторские базы, свободные поверхности) и размерные связи между ними, находят поверхности, относительно которых заданно положение большинства других ее поверхностей. Для достижения заданной точности требуемых размерных связей поверхностей детали кратчайшим путем следует именно эти поверхности использовать в качестве технологических баз на большинстве операций технологического процесса.
3.Чаще положение большинства поверхностей задается относительно основных конструкторских баз детали. Поэтому, в соответствии с принципом единства баз, как правило, в качестве технологических баз выбирают основные базы детали.
4.В зависимости от сформулированных задач обработки соответствующим выбором баз реализуют преимущества координатного и цепного методов достижения точности.
5.Реализация принципа постоянства баз, т.е. обработка большинства поверхностей заготовки с использованием одного постоянного комплекта технологических баз, позволяет использовать преимущества координатного метода достижения точности. При координатном методе исключается влияние погрешности установки на точность относительных поворотов поверхностей и устраняются дополнительные погрешности, возникающие при смене баз.
6.В зависимости от конкретной ситуации и задачи обработки возможны отступления от принципа единства и постоянства баз в частности, если:
65

Анализ служебного назначения изделия (сборочной единицы)
Анализ служебного назначения детали
Обоснование технических условий на изготовление детали
Анализ функций поверхностей детали
Анализ размерных связей между поверхностями детали
Разработка |
|
|
|
|
|
|
|
последовательности |
|
Выбор рационального |
|
изготовления детали |
|
варианта базирования |
|
|
|
|
|
|
|
Выбор комплекта |
|
|
|
постоянных |
|
|
|
технологических баз |
|
|
|
для большинства опе- |
|
|
|
раций технологического |
|
|
|
процесса |
|
|
|
|
|
|
|
Выбор баз для первой |
|
|
|
(первых) |
операций |
|
|
технологического |
|
|
|
процесса |
|
|
|
|
|
Рис.37. Последовательность выполнения первых этапов проектирования технологического процесса изготовления детали
66

положение большинства поверхностей детали задано не относительно основных баз, а относительно других поверхностей, например, вспомогательных баз (станина токарного cтанка);
габаритные размеры основных баз детали недостаточны для создания надежного комплекта технологический баз обеспечения определенности базирования) или их физически неудобно использовать в качестве технологических баз;
принципы единства и постоянства баз и координатный метод получения размеров на обеспечивают или: затрудняет обеспечение заданной точности отдельных размеров, заданных от поверхностей, которые не являются основными базами. Для достижения точности этих размеров на соответствующих операциях в качестве технологических баз попользуют те поверхности, относительно которых они непосредственно заданы. В данном случае целесообразно использовать преимущество цепного метода, обеспечивающего кратчайшую размерную цепь и
наибольшую точность указанных размеров. |
|
|
|
|
|
|
|
|
||||||||
7. |
Выбор |
|
технологических |
баз |
|
|
определяет |
|
реализацию |
|||||||
принципа |
кратчайшего |
пути |
при |
достижении |
точности |
(минимиза- |
||||||||||
цию количества составляющих звеньев в размерной |
|
цепи, |
обес- |
|||||||||||||
печивающей |
|
точность |
заданного |
размера). |
|
Высокие |
требования |
к |
||||||||
точности обеспечиваются |
самым |
кратчайшим |
путем, |
когда |
дости- |
|||||||||||
гаемый |
размер |
является |
замыкающим |
звеном |
в |
технологической |
||||||||||
размерной |
цепи |
системы |
“станок |
- |
приспособление |
- |
инструмент |
|||||||||
- заготовка”. |
|
|
|
|
|
|
|
|
|
|
|
|
|
|
|
|
8. |
В |
первую |
очередь |
|
технологические |
базы |
выбирают |
|
для |
|||||||
обеспечения |
|
точности |
|
относительных |
|
поворотов |
|
поверхностей |
||||||||
детали, |
а |
затем |
- |
точности |
расстояний. |
|
Это объясняется |
|
тем, |
|||||||
что |
точность |
относительных |
поворотов |
обеспечивается |
на |
стан- |
||||||||||
ках |
методами |
взаимозаменяемости, |
что |
|
практически |
исключает |
||||||||||
возможность |
|
коррекции, а точность расстояний - |
методом |
|
регу |
|||||||||||
лирования, при котором возможна компенсация отклонений. |
|
|
|
|
9. Выбранный комплект технологических баз должен обеспечивать выполнение правила шести точек и условий определенности базирования детали.
10.При отсутствии надежного комплекта технологических баз, недостаточных габаритах или физическом неудобстве использования основных баз в качестве технологических, создают искусственные технологические базы в виде приливов, центровых отверстий и т.д.
11. Если деталь невозможно обработать с одной установки, задача выбора технологических баз решается в две стадии:
выбирается схема базирования для большинства операций технологического процесса;
выбирается база для первой (первых) операции.
67

Анализ функционального назначения поверхностей и размерных связей между ними можно облегчить и сделать путем построения графа связи поверхностей детали (рис.38.). Для этого поверхности детали обозначают индексами из букв O, В, K, С и цифр, которые устанавливаю функциональное назначение поверхности и ее номер. Буквы, входящие в индекс, обозначают:
О - основные базы, В- вспомогательные базы,
К - крепежные и резьбовые отверстия, С - свободные поверхности детали, включая и необрабатываемые
Для поверхностей основных баз нумерацию делают в порядке уменьшения числа располагаемых на них опорных точек.
Например 01 - установочная база, 02 - направляющая или двойная опорная, 03 - опорная. Для остальных поверхностей цифры обозначают последовательность их нумерации.
Построения графа связи поверхностей начинают с нанесения узлов, определяющих функциональное назначения поверхностей деталей. Затем узлы соединяют ребрами, которые обозначают наличие размерных и угловых связей между соответствующими поверхностями детали. Размерные связи наносят штриховыми линиями, а угловые – сплошными со стрелкой, направления которой указывает на базу. На ребрах могут быть проставлены также номиналы и допуски соответствующих размеров и относительных поворотов поверхностей деталей. На рис.38 приведен пример построения графа связи поверхностей для корпуса сверлильной головки. Анализ приведенных связей показывает, что положение главных отверстий (В1) и других обрабатываемых поверхностей (В2) определяется по отношению к основным базам корпуса.
68
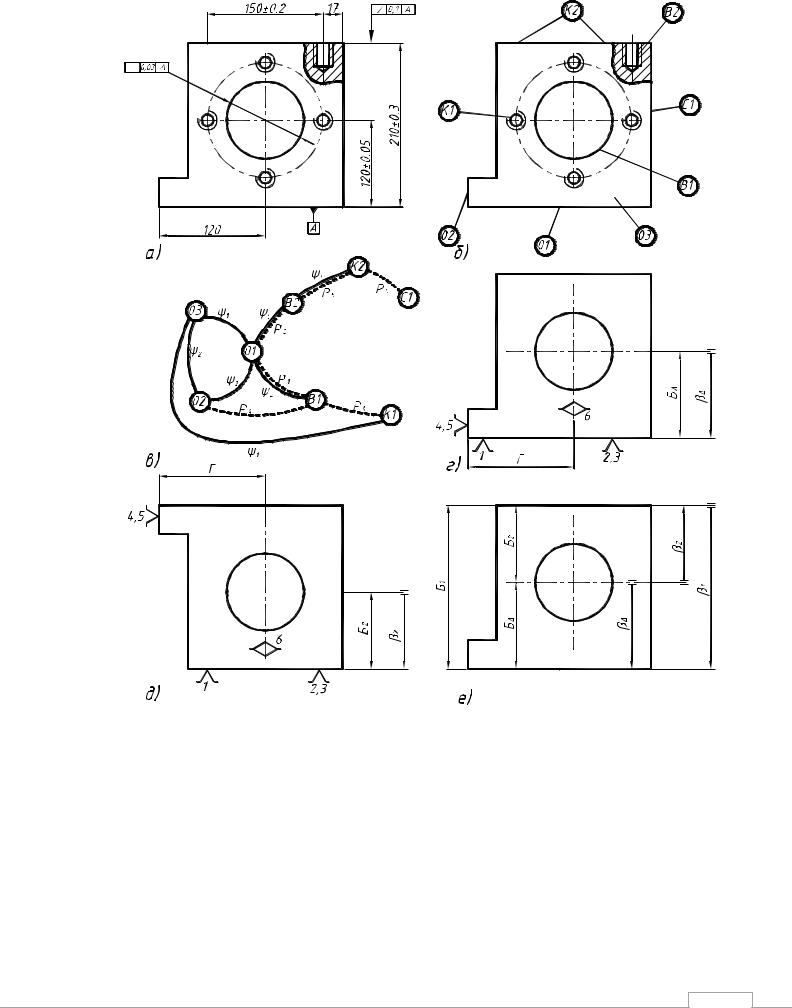
Рис.38. Выбор технологических баз для корпуса сверлильной головки
69

В соответствии с принципом единства баз для корпуса сверлильной головки в качестве технологических баз для большинства операций целесообразно использовать плоскость основания 01 и плоскости 02, 03, образующие координатный угол.
Если при обработке отверстий в корпусе сверлильной головки в качестве установочной технологической базы взять противолежащую поверхность В2 (рис.38,д), то возникают более длинные технологические размерные цепи. Точность параметров Б∆ и β , определяющих положение отверстия В1 относительно плоскости 01, в этом случае будет зависеть не только от точности операции расточки отверстия 01 (т.е. точности звеньев Б2 и β2), но и от точности операции фрезерования плоскости К2 (звенья Б1 и β1 ):
Б∆=Б1-Б2, |
β∆=β1+β2 |
ωБ∆=ωБ1-ωБ2, |
ωβ∆=ωβ1+ωβ2 |
Необходимость получения допуска δБ∆=0,1 и δβ∆= 0,03/300 потребует в этом случае ужесточить допуски на межоперационные размеры:
δБ1=0,07, δБ2=0,03
δβ1=0,015/300, δβ2=0,015/300
δБ∆=0,07+0,03=0,1 ,
δβ∆=0,015/300+0,015/300=0,03/300.
Выполнить это не всегда представляется возможным. Поэтому необходимо стремиться к тому, чтобы на основе принципа единства баз наиболее ответственные параметры точности детали с жесткими допусками получались при обработке как замыкающие звенья технологической системы (станок - приспособление - инструмент – заготовка) одного станка.
Решив задачу выбора баз для обработки большинства поверхностей заготовки, необходимо определить технологические
70

базы для выполнения первой или первых операций технологического процесса. На этих операциях обрабатывают поверхности, которые затем используют в качестве технологических баз на большинстве последующих операций технологического процесса. При выборе технологических баз на первой операции необходимо исходить из решения следующих задач:
1.Установление связей, определяющих расстояния и повороты поверхностей, получаемых в результате обработки, относительно свободных необрабатываемых поверхностей.
2.Обеспечение равномерного распределения фактического
припуска на поверхностях, подлежащих обработке.
Первая задача определяется техническими условиями, вытекающими из служебного назначения детали. Вторая задача определяется требованиями технологии. При решении второй задачи при выборе баз на первой операции руководствуются двумя основными положениями:
необходимостью сохранения наиболее качественного слоя материала на поверхностях детали, подвергающихся при ее работе в машине интенсивному износу:
необходимостью обеспечения равномерного распределения припуска на обработку поверхностей (прежде всего, отверстий). При обработке плоскостей равномерный припуск позволяет снять минимально необходимый слой материала и сохранить наиболее качественную зону поверхностного слоя материала.
При обработке отверстий равномерный припуск (рис.39.) позволяет устранить колебания упругих отжатий инструмента и вызываемые ими погрешности геометрической формы и за счет этого уменьшить необходимое количество технологические переходов, необходимых для достижения заданной точности геометрической формы.
Таким образом, в качестве количественных критериев для сравнения вариантов базирования на первой или первых операциях принимают точность связи между обрабатываемыми и необрабатываемыми поверхностями и равномерность припуска на обработку.
Для выбора наиболее предпочтительного варианта базирования необходимо проанализировать возможные их схемы путем
71

Рис.39. Распределение припуска на обработку отверстия а) равномерный припуск;
б) неравномерный припуск, вызванный несовпадением оси литого отверстия и оси вращения расточного инструмента
72

выявления и расчета возникающих технологических размерных связей. Для этого в первую очередь надо определять то место в технологическом процессе, где поставлен гая задача находит свое окончательное решение. Так, если стоит задача обеспечения требуемой точности положения обрабатываемой поверхности относительно свободных необрабатываемых поверхностей, то ее решение следует искать на операции окончательной обработки этой поверхности. Если же стоит задача обеспечения равномерного припуска при обработке определенной поверхности заготовки» то ее решение проявляется на операций обработки этой поверхности.
Определив операцию, на которой решается поставленная задача, т.е. место получения замыкавшего звана, необходимо выявить все составляющие звенья этой технологической размерной цепи. Для этого следует найти те межпереходные размеры, полученные на данной и предшествующих операциях, и те размеры заготовки» которые влияют на точность замыкающего звена.
Пример. Обеспечить в процессе изготовления корпуса статора электродвигателя симметричность отверстия относительно необрабатываемых наружных поверхностей в горизонтальной плоскости (рис.40. ).
Несимметричность А∆ обнаружится при выполнении расточной операций и через составляющее звено А1 будет зависеть от принятой схемы базирования детали на первой операций, в которой обрабатываются плоскость основания и установочные отверстия. На (рис.40,б, в) приведены два варианта базирования детали на первой операции, отличающиеся только тем, что в первом варианте опорная база (точка 6) создана на боковой поверхности корпуса, а во втором варианте в качестве опорной базы принята плоскость симметрии наружных поверхностей корпуса. Скрытая опорная база во втором варианте может быть создана с помощью самоцентрирующего приспособления, губки которого условно показаны стрелками, обеспечивающего точность расположения обрабатываемых установочных отверстий относительно плоскости симметрии.
73

4 |
5 |
1 |
A2
A1
a)
6
2,3
A |
Б2
Б1 А1=Б
4 |
6 |
1
5 |
2,3
А1=В
4 |
1
б)
5 |
2,3
в) 6
Рис 40. Анализ вариантов базирования при обработке корпуса
74

статора электродвигателя
Анализируя технологические размерные цепи и оценивая возможные погрешности их составляющих звеньев, получит:
в первом варианте
ωА∆=ωА1 + ωА2 = ωБ1 + ωБ2 + ωА2=0,1+2,4+0,1=2,6мм;
во втором варианте
ωА∆=ωА1 + ωА2 = ωВ∆+ ωА2=0,3+0,1=0,4мм
Пример . При обработке корпуса (рис. 41 ) необходимо обеспечить равномерность припуска в отверстии D.
Неравномерность припуска обнаружится на операции растачивания отверстия. Для большинства операций обработки корпуса в качества технологических баз используется основание и два технологически отверстия. При избранной схеме базирования детали на расточной операции неравномерность припуска проявится как относительное смещение оси отверстия в заготовке и оси вращения борштанги с резцом (рис. 41,а ). Рассматривая решение этой задачи в вертикальной плоскости, такое смещение можно представить замыкающим звеном А∆ размерной цепи А, составляющими звеньями которой будут: A1 - расстояние между осью отверстия в заготовке и установочной технологической базой детали и А2 - расстояние между осью обработанного отверстия (осью вращения борштанги с резцом) и той же базой детали. Точность расстояния А2 зависит только от расточной операции. Расстояние А1 установится при обработке основания К на первой операции технологического процесса. Точность расстояния A1 будет зависеть от схемы базирования на первой операции. При обработке поверхности К могут быть использованы различные варианты базирования детали.
По первому варианту (рис.41,б) в качестве установочной базы можно использовать поверхность полок (т. 1, 2,-3), а в качестве направляющей и опорной технологических баз – боковые поверхности основания детали.
75

d |
|
|
|
|
D |
|
|
А |
|
|
|
|
|
|
5 |
4 |
6 |
А1 |
А2 |
|
|
|
|
|
1,2 |
K |
3 |
|
|
а) |
|
|
|
|
|
|
|
|
|
|
|
|
|
|
|
|
|
|
|
|
|
|
|
|
|
|
|
|
|
|
|
|
|
|
|
|
|
|
|
|
|
|
|
|
|
|
|
|
|
|
|
|
|
|
|
|
|
|
|
|
|
|
|
|
|
|
|
|
|
|
|
|
|
|
|
|
|
|
|
|
|
|
|
|
|
|
|
|
|
|
|
|
|
|
|
|
|
|
|
|
|
|
|
|
|
|
|
|
|
|
|
|
|
|
|
|
|
|
|
|
|
|
|
|
|
|
|
|
|
|
|
|
|
|
|
|
|
|
|
|
|
|
|
|
|
|
|
|
|
|
|
|
|
|
|
|
|
|
|
|
|
|
|
|
|
|
|
|
|
|
|
|
|
|
|
|
|
|
|
|
|
|
|
|
|
|
|
|
|
|
|
|
|
|
|
|
|
|
|
|
|
|
|
|
|
|
|
|
|
|
|
|
|
|
|
Б1=В |
|
|
В1 |
|
|
|
|
|
|
|
|
|
|
|
|
|
|
|
|
|
|
|
|
|
|
|
|
|
|
|
|
|
|
|
|
|
|
|
||
|
|
|
|
|
|
|
|
|
|
|
|
|
|
|
|
|
|
|
|
|
|
|
|
|
|
|
|
|
|
|
|
|
|
||
|
|
|
|
|
|
|
|
|
|
|
|
|
|
|
|
|
|
|
|
|
|
|
|
|
|
|
|
|
|
|
|
|
|
||
|
|
|
|
|
|
|
|
|
|
|
|
|
|
|
|
|
|
|
|
|
|
|
|
|
|
|
|
|
|
|
В2 |
|
|
||
|
|
|
|
|
|
|
|
|
|
|
|
|
|
|
|
|
|
|
|
|
|
|
|
|
|
|
|
|
|
|
|
|
|
||
|
|
|
|
|
|
|
|
|
|
|
|
|
|
|
|
|
|
|
|
|
|
|
|
|
|
|
|
|
|
|
|
|
|
||
|
|
|
|
|
|
|
|
|
|
|
|
|
|
|
|
|
|
|
|
|
|
|
|
|
|
|
|
|
|
|
|
|
|
|
|
в)
|
K |
|
|
|
4 |
5 |
|
Б2 |
|
6 |
|
1=АБ |
||
1,2 |
|
3 |
Б1 |
|
|
|
|
||
|
|
|
|
|
б) |
K |
|
|
|
|
|
|
|
|
6 |
|
|
А1=Г |
|
3 |
4 |
|
|
|
|
|
|
||
1 |
|
2 |
|
|
|
|
5 |
|
|
|
г) |
|
|
|
Рис.41. Анализ вариантов базирования при обработке отверстий в корпусной детали
76

При такой схеме базирования детали на первой операции расстояние А1 получается как замыкающее звено Б∆ трехзвенной размерной цепи Б:
ωА1=ωБ∆=ωБ1+ ωБ2.
Составляющее звено Б2 – это выдерживаемый размер при обработке детали на настроенном станке, а звено Б1 – размер, принадлежащий заготовке. Его точность достигается в процессе получения заготовки и зависит от простановки размеров на чертеже заготовки. Если размеры заготовки будут проставлены и выдержаны в процессе ее получения так, как показано на рис.42в, то размер Б1 будет
формироваться как замыкающее звено В∆ размерной цепи В и его погрешность ωБ1
будет равна погрешности ωВ∆, представляющей сумму погрешности составляющих звеньев В1 и В2:
ωБ1 =ωВ∆= ωВ1+ ωВ2.
В соответствии с выявленной схемой образования погрешности ωА∆ в первом варианте базирования детали на первой операции
ωА∆=ωА2 + ωА1 = ωА2 + ωБ2 + ωБ1=ωА2 + ωБ2 + ωВ1 + ωВ2
Численные значения возможных погрешностей: ωА2, ωБ2, ωВ1, ωВ2, - могут бать определены с помощью нормативов средне экономической точности используемых методов обработки и допусков на размеры заготовки. В соответствии с этими нормативами и при условии, что в рассматриваемом примере габаритные размеры корпусной детали находятся в пределах 280 – 500мм, расстояние В1 – в пределах 120 – 280мм, расстояние В2 будет менее 50мм, а отливка будет выполнена по второму классу точности.
ωА∆=0,1+0,3+2,4+1,6=4,4мм
77

Во втором варианте может быть выбрана схема базирования на первой операции, приведенная на рис.41, г: отверстие в заготовке большего диаметра использовано в качестве двойной направляющей технологической базы, роль опорных баз выполняют отверстие меньшего диаметра и боковая поверхность основания. В этом случае расстояние А1 будет получено как замыкающее звено Г∆ размерной цепи технологической системы, на которой выполняется первая операция:
ωА∆= ωА2+ ωА1= ωА2+ ωГ∆=0,6мм
Так как второй вариант дает более короткий путь достижения точности А∆ и полностью исключает влияние погрешностей заготовки на величину неравномерности припуска при обработке отверстия ØD, его можно считать более удачным решением поставленной задачи.
Пример. Обеспечить при обработке направляющих поверхностей станины токарного станка с сохранение наиболее качественной и износостойкой зоны поверхностного слоя материала.
Станины отливают направляющими вниз, чтобы получить на них наиболее плотный и однородный слой материала. Следовательно, для сохранения износостойкости направляющих с них необходимо снять при обработке равномерный и минимальный слой материала.
Эта задача решается путем выбора рациональной последовательности обработки станины, в частности, построением первой операции – ее содержанием и схемой базирования. На первой операции следует обрабатывать поверхности основания, используя в качестве технологических баз направляющие поверхности станины.
78

6 |
4 |
5 |
|
||
1 |
2 |
3 |
а)
6 |
4 |
5 |
|
|
1,2 |
3 |
б)
6
4
5
|
|
|
|
|
|
|
|
|
|
|
|
|
|
|
|
|
|
|
|
|
|
|
|
|
|
|
|
|
|
|
|
|
|
|
|
|
|
|
|
|
|
|
|
|
|
|
|
|
|
|
|
|
|
|
|
|
|
|
|
|
|
|
|
|
1,2 |
3 |
в)
79

Рис.42. Анализ вариантов базирования на первой операции обработки станины
При этом погрешности литой заготовки будут удалены в виде неравномерного слоя металла, снимаемого с поверхностей ножек (рис.42, а). На следующей операции обработки направляющих поверхностей обработанные поверхности ножек используются в качестве технологических баз. Это позволит снять с направляющих равномерный слой металла (рис.42, б).
Если обработку станины начать с фрезерования направляющих поверхностей с установкой на необработанные поверхности ножек, то наиболее качественный слой металла может быть удален путем снятия неравномерного припуска.
Неравномерность припуска возникает из – за установки на необработанные поверхности ножек (рис.42,в).
80

ПРАКТИЧЕСКИЕ ЗАНЯТИЯ ПО ВЫБОРУ ТЕХНОЛОГИЧЕСКИХ БАЗ
Первые этапы проектирования технологического процесса изготовления детали, включая выбор технологических баз, выполняются в следующем порядке:
1.Анализ служебного назначения изделия (сборочной единицы). Обоснование технических условий на изготовление изделия.
2.Размерный анализ изделия. Переход от служебного назначения изделия и технических условий на его изготовление к техническим условиям на отдельные детали.
3.Анализ служебного назначения детали.
Определение функций ее поверхностей и связей между ними.
4.Выбор комплекта постоянных технологических баз (КПТБ) для большинства операций технологического процесса.
5.Выбор баз на первой (первых) операциях технологического процесса для обработки поверхностей, входящих в КПТБ.
6.Разработка общей последовательности изготовления детали.
ПРАКТИЧЕСКОЕ ЗАНЯТИЕ № 1
Служебное назначение изделия, определение точностных требований и построение конструкторских размерных цепей.
Приведенный на рис.43 узел предназначен для передачи вращения и изменения его направления.
При монтаже узла в изделие он участвует своими размерами в решении следующих задач:
совмещении вершин делительных конусов зубчатых колес (замыкающие звенья А∆, Б∆);
обеспечении угла β∆ между осями делительных конусов колес.
Для выполнения узлом служебного назначения при сборке его должны быть обеспечены дополнительно следующие точностные требования:
натяг в подшипниках Г∆ соосность ввинчиваемых в корпус болтов с осью отверстий в крышках
подшипников Е∆.
В работе необходимо:
1. Определить численные значения перечисленных выше точностных
требований (А∆, Б∆, β∆, Е∆).
2. Выявить размерные связи узла, обеспечивающие выполнение точностных требований и построить соответствующие конструкторские размерные цепи.
81

3. Выбрать метод достижения точности для каждой размерной цепи и соответствующего точностного требования.
r =0+0,07+0,15 |
Прокладка |
Основание привода |
Узел привода №1 |
Узел привода №2
β =0 +-0,02
β
Б =0+0,06
-
А =0+0,06
-
β =90+0,06/150
-
82

Рис.43.Узел привода №1
Методические указания
В рассмотренном примере изделием является привод, смонтированный на общей плите (рис.43).
Узлы N1 и N2 привода, несущие конические шестерни смонтированы, на общей плите – основании привода.
Регулирование положения узла N1 в вертикальной плоскости (при обеспечении точности замыкающего звена В∆ ) осуществляется с помощью прокладки, устанавливаемой между корпусом и общей плитой привода.
Переход от служебного назначения изделия (привода) к техническим условиям на изготовление детали (корпуса) можно осуществить в два этапа.
На первом этапе осуществляется переход от технических требований на изделие (А∆, Б∆, В∆, β∆) к точностным требованиям на узлы N1 и N2.
Эта задача решается размерной цепью (В∆, В1, В2, В3), приведенной на рис.44,а.
Точность в размерной цепи (В∆, В1, В2, В3) может быть обеспечена методом регулирования. Результатом расчета являются точностные требования к размерам В1 и В2 и параметры компенсатора (звено В2).
На втором этапе осуществляется переход от точностных требований к узлу N1 к техническим требованиям на отдельные детали узла (корпус).
Эта задача решается размерной цепью
{Β/ ,Β1/ ,Β2/ ,Β3/ ,Β4/ ,Β5/ } (рис.44,б).
Расчетом размерной цепи В/ устанавливается допуск на размер В/5 корпуса, которым он участвует в выполнении изделием его служебного назначения.
Аналогичный анализ приводится по всем размерным цепям, определяющим точностные требования к изделию (А∆, Б∆, β∆ ).
Примеры расчета подобных размерных цепей приведены в [7].
83

|
|
|
|
Ось делительного |
|
В4 |
|
|
|
|
|
|
|
|
|
|
|
|
|
|
|
|
|||||||||
|
|
|
|
|
|
|
|
|
|
|
|
|
|
|
|
|
|
|
|
|
|||||||||||
|
В1 |
|
|
конуса узла №1 |
|
|
|
Ось делительного |
|
||||||||||||||||||||||
|
|
|
|
|
|||||||||||||||||||||||||||
|
|
|
|
|
|
|
|
|
|
|
|
|
|
|
|||||||||||||||||
|
|
|
Основание корпуса |
|
|
|
конуса узла №2 |
|
В3 |
||||||||||||||||||||||
|
|
|
|
|
|
|
|||||||||||||||||||||||||
|
|
|
|
|
|
|
|
|
|
|
|
|
|
|
|
|
|
|
|
||||||||||||
|
|
|
|
|
|
|
|
|
|
|
|
|
|
|
|
|
|||||||||||||||
|
|
|
|
|
|
|
|
|
|
|
|
|
|
|
|
|
|
|
|
|
|
|
|
|
|
|
|
|
|
|
|
|
Прокладка |
|
|
|
|
|
|
|
|
|
|
|
|
|
|
|
|
|
|
|
|
|
|
|
|
|
|
||||
|
|
|
|
|
|
|
|
|
|
|
|
|
|
|
|
|
|
|
|
|
|
|
|
|
|
|
|||||
|
|
|
|
|
|
|
|
|
|
|
|
|
|
|
|||||||||||||||||
|
В2 |
|
|
Поверхность общей плиты-основания привода |
|||||||||||||||||||||||||||
|
|
|
|
||||||||||||||||||||||||||||
|
|
|
|
|
|
|
|
|
|
|
|
|
|
|
|
|
|
|
|
|
|
|
|
|
|
|
|
||||
|
|
|
|
а) |
|
|
|
|
|
|
|
|
|
|
|
|
|
|
|
|
|
|
|
|
|
|
|
|
|
|
|
|
|
|
|
|
|
|
|
|
|
|
|
|
|
|
|
|
|
|
|
|
|
|
|
|
|||||||
Ось делительного конуса узла №1 |
|
|
|
В'1 |
|
|
|
|
В'2 |
|
|
|
|
|
|
|
|
||||||||||||||
|
|
|
|
|
|
|
|
|
|
|
|
|
|||||||||||||||||||
|
|
|
|
|
|
|
|
|
|
|
|
|
|
|
|
|
|
|
|
|
|
|
|
|
|||||||
|
|
|
|
Ось отверстия в шестерне |
|
|
|
|
|
|
|
|
|
|
|
|
|||||||||||||||
|
|
|
|
|
|
|
|
|
|
|
|
|
|||||||||||||||||||
|
|
|
|
|
|
|
|
|
|
|
|
|
|
|
|
|
|
|
|
|
|
|
|
|
|
|
|
||||
|
Ось центрирующей шейки вала |
|
|
|
|
|
В3 |
||||||||||||||||||||||||
|
|
|
|||||||||||||||||||||||||||||
|
|
|
|
|
|
|
|
|
|
|
|
|
|
|
|
|
|
|
|
|
|
|
|
' |
|
|
|
|
|
|
|
|
В1=В |
Ось опорной шейки вала |
|
|
|
В'4 |
|||||||||||||||||||||||||
|
|
|
|
|
|
||||||||||||||||||||||||||
|
|
|
|
||||||||||||||||||||||||||||
|
|
|
|
|
|||||||||||||||||||||||||||
|
|
|
|
|
|
|
|
|
|
|
|
|
|
|
|
|
|
|
|
|
|
||||||||||
|
|
|
|
|
|
|
|
|
|
|
|
|
|
|
|
|
|
|
|
|
|
|
|
|
|
|
|||||
' |
|
|
Ось отверстия в корпусе |
|
|
|
|
|
|
|
|
||||||||||||||||||||
|
|
|
|
|
|
|
|
|
|
||||||||||||||||||||||
|
|
|
|
|
|
|
|
|
|
|
|
|
|
|
|
|
|
|
|
|
|
|
|
|
|
|
|
|
|
|
|
В'5
Основание корпуса
б)
Рис.44.Размерный анализ узла привода: а – размерная цепь В; б – размерная цепь В/
84

ПРАКТИЧЕСКОЕ ЗАНЯТИЕ № 2
Точностные требования к детали и выбор комплекта постоянных технологических баз (КПТБ).
Целью работы является обоснование комплекта постоянных технологических баз, используемых на большинстве операций технологического процесса изготовления корпусной детали сборочной единицы, приведенной на рис.45.
Порядок выполнения
1. Выявить, какими размерами корпус участвует в достижении точностных требований к узлу, и записать эти размеры в таблицу.
Таблица
ТТ №
Размер
2.На основе расчета размерных цепей установить допуски на выявленные в п.1 размеры корпуса.
3.Сформулировать служебное назначение корпуса с точки зрения его участия в достижении точностных требований к узлу.
4.Составить граф размерных связей между поверхностями корпуса по трем координатным осям.
Размерные связи и обозначение поверхностей корпуса приведены на рис.45.
5.На основе анализа размерных связей по каждой координатной оси выявить комплект из трех поверхностей (баз), по отношению к которым ориентированно большинство поверхностей в направлении данной оси.
6.Разработать теоретические схемы базирования корпуса.
Выбрать КПТБ, в наибольшей степени соответствующий всем его размерным связям и приемлемый для большинства операций технологического процесса изготовления корпуса.
7. Привести схему приспособления, материализирующего предложенный вариант КПТБ.
85

С целью выбора КПТБ размерные связи корпуса (рис.45) целесообразно представить в виде графа связей поверхностей (рис.46).
Граф в данном случае служит для наглядного представления связей и удобства их анализа.
Граф позволяет установить:
1.Угловые и линейные связи между поверхностями.
2.С какой поверхностью (поверхностями) связано большинство других поверхностей.
3.Приоритетность связей (т.е. степень их жесткости).
4.Возможность (физическая ) использования поверхностей в качестве баз.
Из графа следует, что большинство поверхностей корпуса связано с поверхностями основных конструкторских баз корпуса – основанием 6 и осями крепежных отверстий 30 и 120, которые целесообразно использовать в качестве КПТБ на большинстве операций технологического процесса.
После выбора КПТБ устанавливаются точностные требования к базам (в данном случае – точности расстояния между осями отверстий 30 и 120, см. прил.4).
86

87

|
Z |
|
|
|
|
|
|
4отв М10 |
|
|
|
|
|
|
|
1,0 |
90 |
+0,05 |
0,1 |
0,1 |
|
20 |
100 |
|
+ |
+- |
|
|
|
|
=50И2 |
=60К2 |
=70Л2 |
|
|
|
|
|
|
- |
|
|
|
|
80 |
|
|
|
|
|
10 |
|
|
|
|
0,05 |
|
|
|
|
|
|
+- |
|
|
9 |
|
|
|
=42Е |
-=15Д2 |
7 |
|
|
|
|
|
|
|
8 |
|||
|
|
30 |
|
|
|
|
|
|
|
|
|
|
|
|
2 |
3 |
|
5 |
|
|
|
4 |
|
|
|
||
|
Б=5 |
+ |
|
|
|
|
|
- 1 |
|
+ |
|
|
|
|
|
В=50 |
+ |
Г=5-1 |
|
|
|
|
- 0,5 |
|
|
|
|
|
|
А=100-0,3 |
|
|
|
|
|
|
Z |
|
|
|
|
|
|
|
+ |
|
|
|
|
|
|
Ж=0 - 0,1 |
|
|
|
|
Х |
80 |
|
|
|
|
|
|
|
|
|
|
|
|
|
90 |
З=0 +-0,5 |
|
|
|
|
|
|
|
1,5 |
||
|
|
|
|
|
|
|
|
|
|
|
|
|
+- |
|
|
|
|
|
|
82 |
2отв. |
10-0,03 |
|
|
|
|
|
|
|
|
+ |
1 |
|
|
|
|
|
C=66- |
|
|
11 |
|
|
|
У=50 |
+ |
|
|
|
12 |
|
|
13 |
||
|
|
|
|
|
||||||||||
|
|
|
|
|
|
|
|
|
|
|
|
|
||
|
|
|
|
|
|
|
|
|
|
|
|
|
||
|
|
|
|
|
|
|
|
|
|
|
|
|
||
|
|
|
|
|
|
|
|
|
|
|
|
|
||
|
|
|
|
- 0,05 |
|
|
|
|
|
|
|
|
|
|
|
|
|
|
|
Т=120 |
+ |
|
|
|
20 |
|
|
||
|
|
|
|
|
- 0,05 |
|
|
|
|
|
|
|||
|
|
|
|
|
|
Р=132-3 |
|
|
|
|
|
|
У
Рис.45.Чертеж корпуса
88

По координате Z |
по У |
по Х |
|
14 |
|
|
13 |
6 |
7 |
11 |
80 |
|
|||
80 |
1 |
2 |
100 |
100 |
5 |
30 |
90 |
|
4 |
|
|
90 |
|
|
|
|
|
|
120 |
|
30 |
|
|
Рис.46. Граф связей между поверхностями корпуса
линейная
угловая
89

ПРАКТИЧЕСКОЕ ЗАНЯТИЕ №3
Выбор баз для обработки поверхностей, входящих в КПТБ
Целью работы является выбор баз на первой (005) или двух первых (005 и 010) операциях технологического процесса при обработке поверхностей, входящих в комплект постоянных технологических баз. Имеется в виду, что КПТБ может быть обработан за одну установку на первой операции (005) или на двух первых операциях (005 и 010) технологического процесса.
Порядок выполнения
1.Установить точностные требования к поверхностям, входящим в КПТБ.
2.Установить последовательность обработки поверхностей входящих в КПТБ
3.На основе расчета технологических размерных цепей выбрать оптимальный вариант схемы базирования для операции 005:
3.1.Операция 005. Наименование и содержание операции.
3.2.Формулировка задачи базирования (обеспечение равномерности припуска на обработку отверстия, обеспечения точности связи между обрабатываемыми и необрабатываемыми поверхностями и т.д.) в каждом из направлений X, Y, Z.
3.3.Выявление размеров, которые необходимо обеспечить, исходя из сформулированных задач базирования.
3.4.Первый вариант базирования (теоретическая схема базирования в направлениях X, Y, Z.) (рис.47).
3.5.Преимущества и недостатки предложенного варианта.
3.6.Второй вариант базирования, лишенный недостатков первого.
3.7.Построение схем технологических размерных цепей.
3.8.Выявление уравнений размерных цепей и расчет замыкающих звеньев.
3.9.Анализ результатов.
Выбор варианта базирования предпочтительного с точки зрения сформулированных в п.3.2 задач базированя.
3. Следуя последовательности, изложенной в п.3, выбрать вариант базирования для операции 010.
90

X |
Z |
y
Рис.47.Эскиз корпуса |
91

ПРИМЕР
1.Выбор КПТБ. В качестве комплекта постоянных технологических баз для большинства операций обработки корпуса (рис.45) могут быть использованы основание и два технологических отверстия.
Операция по обработке КПТБ:
операция 005 – обработка основания 6; операция 010 – обработка двух отверстий 3 и 12.
2.Формулирование задач, решение которых зависит от выбора схем базирования на операциях 005 и 010.
Задача 1 – установление размерных связей между обрабатываемыми и необрабатываемыми поверхностями.
Эти связи устанавливаются:
по оси Z – размерами Д=15-2 и З=0±0,5, зависящими от построения операции
005;
по оси Y – размерами Б=5±1 и Г=5±1, получаемыми на операции 010.
Задача 2 – распределение припусков на обработку:
ωZ10 – отверстие,
ωZ6 – основание,
ωZ1 ωZ5 торцы.
(Z – припуск, ω– колебание, рассеяние значений, погрешность).
3.Формулирование вариантов базирования (рис.48). 4. Построение схем размерных цепей (рис.49, 50).
4.1. В зоне “размеры детали” по каждой проекции необходимо указать: размеры, связывающие обрабатываемые и необрабатываемые поверхности. размеры готовой детали, связывающие обработанные поверхности (5 – 7
наиболее ответственных размеров).
4.2. В поле каждой операции проставить размеры, связывающие технологическую базу с обработанной поверхность. Если обрабатывается цилиндрическая поверхность, то проставляется размер от технологической базы до ее оси и радиус.
Помимо размеров в поле операций указываются снимаемые припуски с использованием обозначений:
92

-исчезающая поверхность
-возникающая поверхность
-припуск (расстояние между исчезающей и возникающей поверхностями)
-ось
- обозначение припуска на обработку отверстия
-ось
4.4.Проставить размеры заготовки от технологических баз на первой операции
93

4 |
5 |
6 |
1 |
|
2,3 |
а)
1,2 |
3 |
|
|
|
|
|
|||||
|
|
|
|
|
|
|
|
|
|
|
|
|
|
|
|
|
|
|
|
|
|
|
|
|
|
|
|
|
|
|
|
|
|
|
|
|
|
|
|
|
|
|
|
|
|
|
|
|
|
|
|
|
|
|
|
|
|
|
|
4,5
6
б)
Рис.48. Схемы базирования на операциях обработки поверхностей комплекта постоянных технологических баз (КПТБ):
а – операция 005 (I вариант); б – операция 010 (I вариант)
94

|
|
|
|
Y |
|
|
|
|
Номер поверхности, оси |
|
|
||
|
1 |
2 |
30 |
4 |
5 |
|
Размеры |
|
[Б] |
|
[Г] |
|
|
|
|
|
[А] |
|
|
|
детали |
|
|
|
[Б] |
|
|
|
|
|
|
|
|
|
|
|
К15 |
|
В15 |
|
|
Обработка |
|
|
|
4,6 |
15 |
] |
|
|
|
[Z5 |
|||
от КПТБ |
|
15 |
|
|
|
|
|
|
[Z1 ] |
|
|
|
|
|
010 |
|
|
В10 |
6 |
|
Обработка |
|
|
|
|
||
|
|
|
|
|
|
|
КПТБ |
|
|
|
|
|
|
|
005 |
|
|
4.5 |
|
|
Размеры заготовки |
|
|
Г0 |
|
|
|
от технологических |
|
|
Л0 |
|
|
|
баз на первой |
|
|
А0 |
|
|
|
операции |
|
|
|
|
|
|
|
|
|
|
|
|
|
Рис.49 Технологические размерные цепи по оси Y |
|
|
95

|
|
|
|
Z |
|
|
Номер поверхности, оси |
80 |
|||
|
6 |
7 |
10 |
100 |
|
Размеры |
[Д] |
|
|
[И] |
|
|
[Е] |
|
|
|
|
детали |
|
|
[3] |
|
|
|
|
|
|
||
|
|
Е15 |
|
|
|
Обработка |
1 |
|
|
И15 |
|
2 |
|
|
|
|
|
от КПТБ |
15 |
|
|
|
|
|
|
|
|
||
3 |
[Z10] |
|
|
|
|
|
|
|
|
|
|
010 |
1,2 |
|
|
|
|
3 |
|
|
|
|
|
Обработка |
|
|
|
|
|
КПТБ |
Д5 |
|
|
|
|
005 |
5 |
|
|
|
|
[Z6] |
|
|
|
|
|
Размеры |
Д0 |
|
|
И0 |
|
|
|
|
М0 |
|
|
заготовки |
|
|
|
|
|
|
|
|
З0 |
|
|
|
|
|
|
|
|
Рис.50 Технологические размерные цепи по оси Z |
|
96

4.5.Проставить замыкающие звенья технологических размерных цепей, которыми являются:
снимаемые припуски размеры готовой детали, которые непосредственно не получаются ни на
одной из операций.
Замыкающие звенья обозначаются квадратными скобками, например: [Z515]. Индексы при буквенном обозначении припуска обозначают:
нижний – номер поверхности, верхний – номер операции.
Индекс при буквенном обозначении размера обозначает номер операции. Размеры готовой детали обозначаются буквой без индекса. Размеры заготовки обозначаются буквой с индексом “0”.
4.6.Выявить контуры технологических размерных цепей. Для каждого замыкающего звена формируется только одна размерная цепь, реализующая принцип “кратчайшего пути”.
При построении размерных цепей и составлении их уравнений нельзя проходить через разрывы осей и участки расположения припусков.
5. Составление уравнений размерных цепей и зависимостей для расчета погрешностей замыкающих звеньев.
Замыкающими звеньями для размерных цепей по оси Y (рис.49) являются припуски и размера А, Б, Г.
Уравнения размерных цепей:
[Z115] = - K15 – B10 + A0 ,
[Z515] = - B15 + B10 ,
[Б] = К15 + В10 – А0 , [А] = В15 + К15 , [Г] = - В15 + В10 – Г0
97

Зависимости для расчета погрешностей замыкающих звеньев:
ωz115 = ωК15 + ωВ10 + ωА0 ,
ωz515 = ωВ15 + ωВ10 ,
ωБ = ωК15 + ωВ10 + ωА0 ,
ωА = ωВ15 + ωК15 ,
ωГ = ωВ15 + ωВ10 + ωГ 0 ,
Уравнение размерных цепей по оси Z (рис.50):
[Z1015 ]=и15 – E15 +Д5+M0 – и0,
[Z65 ]=Д5 – Д0 ,
[З]= - Е15 + Д5+М0+З0.
Соответствующие колебания припусков и погрешности:
ωz1015 = ωu 15 + ωЕ15 + ωD5 + ωМ 0+ ωu 0 ,
ωz65 = ωД5 + ωД0 ,
ωЗ = ωЕ15 + ωД5 + ωМ 0 + ωЗ 0.
Расчет колебаний припусков и погрешностей замыкающих звеньев для различных вариантов базирования по осям Y и Z. Погрешности составляющих звеньев размерных цепей определяются по таблицам средне экономических норм точности.
7. Сопоставление колебаний припусков и погрешностей с заданными допусками, выбор варианта базирования, обеспечивающего наименьшее колебание припуска и заданную точность обработки.
Построение и расчет размерных цепей выполняются на бланках (рис.50).
98

Эскиз |
|
|
|
|
|
Расчет размеров на |
||||
заготовки |
|
|
|
|
|
технологические |
|
|||
|
|
|
|
|
|
переходы |
|
|
|
|
Операция |
60 |
70 |
100 |
1000 |
900 |
800 |
Исходные данные |
|
||
1 |
|
|
|
|
|
|
||||
000 |
2 |
|
|
|
|
Р-Р |
А |
в |
Н |
Zmin |
заготов |
3 |
|
|
|
|
|
|
|
|
|
|
4 |
|
|
|
|
|
|
|
|
|
Операция |
5 |
|
|
|
|
|
|
|
|
|
005 (черн) |
6 |
|
|
|
|
|
|
|
|
|
фрезерная |
|
|
|
|
|
|
|
|
|
|
Операия |
7 |
|
|
|
|
|
|
|
|
|
010 (чист) |
8 |
|
|
|
|
|
|
|
|
|
фрезерная |
|
|
|
|
|
|
|
|
|
|
Операция 015 |
9 |
|
|
|
|
|
|
|
|
|
расточная |
10 |
|
|
|
|
|
|
|
|
|
черновая |
11 |
|
|
|
|
|
|
|
|
|
Операция |
12 |
|
|
|
|
|
|
|
|
|
020 |
13 |
|
|
|
|
|
|
|
|
|
расточная |
14 |
|
|
|
|
|
|
|
|
|
чистовая |
|
|
|
|
|
|
|
|
|
|
Операция |
15 |
|
|
|
|
|
|
|
|
|
сверлильно-резьбонарезная |
|
|
|
|
|
|
|
|
|
|
Операция |
16 |
|
|
|
|
|
|
|
|
|
030 |
17 |
|
|
|
|
|
|
|
|
|
протяжная |
18 |
|
|
|
+ |
|
|
|
|
|
|
|
|
|
|
|
|
|
|
||
|
|
|
|
З=0-0,5 |
|
|
|
|
||
|
19 |
|
Н=25 +0,025 |
|
|
|
|
|
||
Деталь |
20 |
|
+ |
|
|
|
|
|
|
|
Е=42-0,5 |
|
|
|
|
|
|
|
|||
|
21 |
Д= 19-0,2 |
|
|
+ |
|
|
|
|
|
|
22 |
|
|
Z=0-0,7 |
|
|
|
|
|
|
|
6 |
7 |
10 |
100 |
90 |
80 |
|
|
|
|
Расчет размерных цепей |
|
|
|
|
|
|
|
Порядок расчета
Уравнения
размерных
цепей
Рис.51. Форма бланка для расчета и построения размерных цепей
99
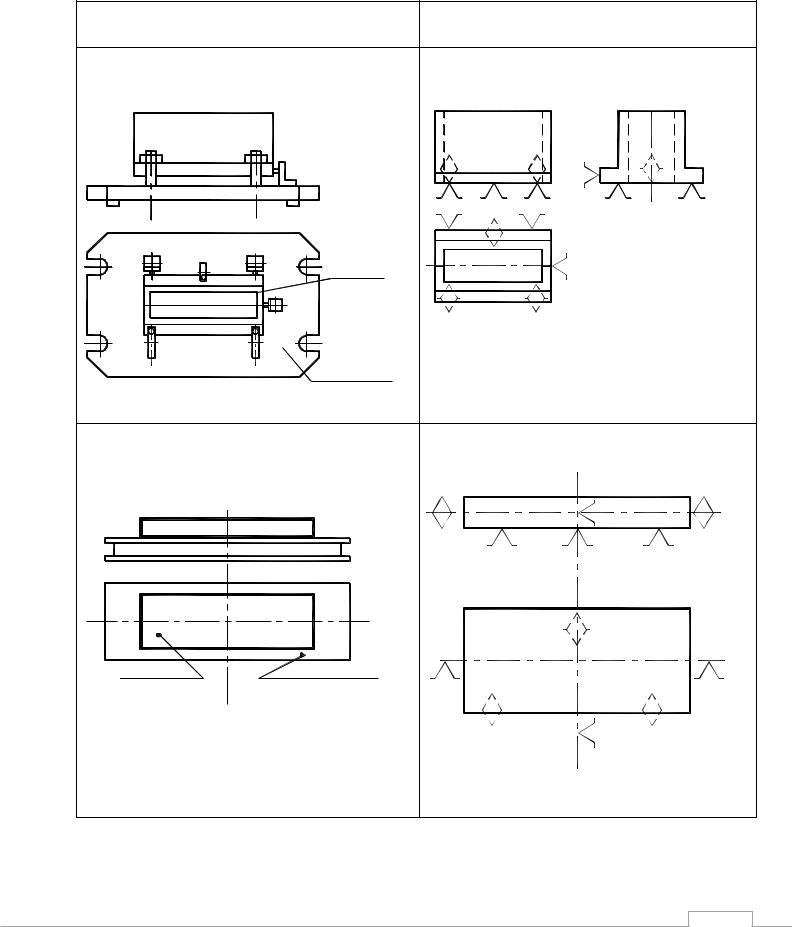
|
Приложение 1 |
|
|
|
||
РАССПРОСТРАНЕННЫЕ СХЕМЫ БАЗИРОВАНИЯ ДЕТАЛЕЙ |
||||||
|
Схема установки |
|
Теоретическая схема базирования |
|||
1.Установка заготовки по плоскостям |
|
|
|
|
|
|
основания и двум боковым сторонам |
|
|
|
|
|
|
|
|
|
4 |
5 |
|
6 |
|
|
|
4,5 |
|
||
|
|
|
|
|
|
|
|
|
2 |
1 |
3 |
1 |
2,3 |
|
|
|
||||
|
|
|
4 |
5 |
|
|
|
|
|
1 |
|
|
|
|
Заготовка |
|
|
|
6 |
|
|
|
|
|
|
|
|
|
|
|
2 |
3 |
|
|
|
Приспособление |
|
|
|
|
|
2. Установка заготовки по плоскости |
|
|
|
|
|
|
(на магнитной плите) |
|
|
|
|
|
|
|
|
|
4 |
|
6 |
5 |
|
|
|
|
|
||
|
|
|
3 |
|
1 |
2 |
|
|
|
|
|
ΙΙΙ |
|
|
|
|
|
|
1 |
|
|
|
|
ΙΙ |
|
|
ΙΙ |
Заготовка |
Магнитная плита |
|
4 |
|
|
5 |
|
|
|
|
|
||
|
|
|
3 |
|
|
2 |
|
|
|
|
|
6 |
|
|
|
|
|
|
ΙΙΙ |
|
|
|
|
|
|
|
100 |

|
|
Продолжение прил.1 |
|
Схема установки |
Теоретическая схема базирования |
||
3.Установка заготовки по плоскости и двум |
|
|
|
отверстиям |
|
|
|
|
4 |
|
|
|
5 |
|
6 |
|
1 |
2 |
3 |
|
5 |
|
|
|
|
2 |
|
|
1 |
|
3 |
|
|
|
6 |
|
4 |
|
|
101

4.Установка вала в трехкулачковом |
|
|
|
|
самоцентрирующем патроне |
|
|
|
|
Штангенциркуль |
|
6 |
|
|
6 |
|
|
|
|
|
3,4 |
3 |
4 |
5 |
|
|
|
||
1,2 |
|
1 |
2 |
|
|
|
|
|
|
|
|
Продолжение прил.1 |
Схема установки |
Теоретическая схема базирования |
|
5.Установка диска в трехкулачковом |
|
|
самоцентрирующем патроне |
|
|
|
6 |
6 |
|
2 |
2 |
|
5 |
5 |
|
|
|
|
4 |
4 |
|
1 |
3 |
|
|
1,3 |
102

6. Установка вала в центрах |
|
|
|
|
|
6 |
6 |
|
|
|
|
|
|
|
|
3,4 |
3 |
|
4 |
|
1,2 |
1 |
|
2 |
|
5 |
|
Общая ось |
|
|
|
|
центровых |
|
|
|
|
отверстий |
|
|
5 |
|
|
|
7. Установка вала на призме |
I – общая ось центровых отверстий |
|||
|
6 |
|
|
6 |
|
|
5 |
1 |
2 |
|
1,2 |
|
|
|
|
|
|
|
|
|
3,4 |
|
3 |
4 |
|
|
|
||
|
|
Продолжение прил.1 |
Схема установки |
Теоретическая схема базирования |
103

8. Установка втулки на цилиндрической |
|
|
|
|
|
оправке (с зазором) |
|
|
|
|
|
А А |
А |
|
|
|
|
|
|
|
|
|
|
|
|
6 |
|
|
6 |
|
А |
3,4 |
|
1 |
2 |
|
|
1,2 |
|
3 |
4 |
|
|
5 |
|
5 |
|
|
|
|
|
|
|
9. Установка втулки на разжимной оправке |
|
|
|
|
|
(без зазора) |
|
|
|
|
|
|
А |
6 |
|
|
6 |
|
|
|
3,4 |
3 |
4 |
|
|
|
|
||
|
|
1,2 |
|
1 |
2 |
|
|
5 |
|
5 |
|
|
А |
|
|
|
|
|
|
|
|
|
|
|
|
|
|
Продолжение прил.1 |
104

|
Схема установки |
|
Теоретическая схема базирования |
|||
10. |
Установка |
заготовки |
на |
|
|
|
обрабатываемой |
поверхности |
при |
|
|
|
|
бесцентровом врезном шлифовании |
|
|
|
|
||
|
|
Заготовка |
|
|
|
|
|
|
|
|
6 |
|
3,4 |
|
|
|
|
|
|
|
|
|
Ведущий |
|
1,2 |
|
|
|
|
|
|
|
||
Шлифующий |
круг |
|
|
|
|
|
Опора |
|
|
|
|
||
круг |
|
|
|
|
||
|
|
|
|
|
||
|
Продольный |
|
|
|
|
|
|
упор |
|
|
|
|
|
|
|
|
|
|
|
5 |
|
|
|
|
|
2 |
4 |
|
|
|
|
6 |
1 |
3 |
|
|
|
|
|
||
|
Примечание. На теоретических схемах базирования арабскими цифрами |
|||||
|
|
обозначены опорные точки |
|
|
||
|
|
|
|
|
|
105 |

Схема установки |
|
11. Установка на станке заготовки |
|
корпусной детали с выверкой ее положения |
|
по разметочным рискам |
|
Рейсмус |
|
|
Заготовка |
Линейка |
Домкратики |
|
|
|
Разметочная риска |
Продолжение прил.1
Теоретическая схема базирования
4,5 |
2,3 |
1 |
|
|
6 |
6
5 |
3 |
|
1
2
4
106

Приложение 2 ПРИМЕРЫ РАЗРАБОТКИ СХЕМ БАЗИРОВАНИЯ
Технологическая задача |
Теоретическая схема базирования |
|
|
Пример возможной реализации |
||||||||||||||
|
|
|
теоретической схемы базирования |
|||||||||||||||
1.При фрезеровании паза шириной h |
|
|
|
|
|
|
|
|
|
|
|
|
|
|
|
|
|
|
выдержать размер а и в , параллельность оси |
|
|
|
|
|
|
|
|
|
|
|
|
|
Заготовка |
||||
паза относительно поверхности Б, а два паза |
|
|
|
|
|
|
|
|
|
|
|
|
|
|
|
|
|
|
|
|
|
|
|
|
|
|
|
|
|
|
|
|
|
|
|
|
|
– основанию А |
|
|
|
|
|
|
|
|
|
|
|
|
|
|
|
|
|
|
|
|
|
|
|
|
|
|
|
|
|
|
|
|
|
|
|
|
|
|
|
|
|
|
|
|
|
|
|
|
|
|
|
|
|
|
|
|
А |
4,5 |
|
|
6 |
h |
6 |
|
4 |
5 |
|
|
1 |
3,2 |
1 |
2 |
3 |
а |
|
|
|
|
|
|
А |
4 |
|
|
|
в |
2 |
|
|
|
|
|
1 |
5 |
|
|
|
|
|
|
|
|
|
|
Б |
3 |
|
|
|
|
|
|
|
|
|
|
|
6 |
|
|
|
|
Б |
|
|
|
Приспособление |
|
|
|
|
|

|
|
|
|
|
Продолжение прил.2 |
Технологическая задача |
Теоретическая схема базирования |
Пример возможной реализации |
|||
|
|
|
|
|
теоретической схемы базирования |
2. При обработке отверстия d в диске |
|
|
|
|
|
выдержать размеры а и в и обеспечить |
|
|
|
Кондукторная |
|
перпендикулярность оси отверстия |
|
|
|
плита |
|
относительно поверхности А. |
|
|
|
|
Заготовка |
|
|
|
|
|
|
d |
|
|
4 |
|
|
|
|
|
6,5 |
|
|
|
|
|
|
|
|
А |
А |
1 |
2 |
3 |
|
|
|
|
|
|
О |
|
2 |
|
|
5 |
|
|
|
|
|
|
в |
4 |
|
|
1 |
3 |
|
|
а |
|
|
Призматические губки |
|
|
6 |
|
|
|
самоцентрирующих тисков |
3. При обработке поверхностей диаметром d1 и d2 обеспечить их соосность с отверстием d и выдержать размер а

|
|
а |
d1 |
d |
d2 |
|
А |
А |
|
|
|
6 |
3 |
4 |
5 |
|
1 |
2 |
Установка заготовки на цилиндрической оправке с без зазорной (прессовой посадкой)
6
3,4
1,2

|
|
|
|
Продолжение прил.2 |
Технологическая задача |
Теоретическая схема базирования |
Пример возможной реализации теоретической |
||
|
|
|
|
схемы базирования |
4. При обработке отверстия d в шаре |
|
|
|
Кондукторная |
выдержать размер а и обеспечить |
|
|
|
плита |
|
|
|
|
|
прохождение оси отверстия через точку 0 – |
2,4 |
|
4 |
|
центр шара |
3 |
2 3 |
||
d |
1,5 |
6 |
1,6 |
5 |
а |
|
|
|
|
О |
О |
|
|
О |
|
1 |
2 |
|
|
|
|
|
||
|
|
|
|
|
|
|
6 |
|
|
|
|
3 |
|
|
5 4
Конусные губки самоцентрирующих
тисков

|
|
|
|
|
|
|
|
|
Продолжение прил.2 |
|
Технологическая задача |
Теоретическая схема базирования |
Пример возможной реализации теоретической |
||||||
|
|
|
|
|
|
|
|
|
схемы базирования |
5. При расточке отверстия d выдержать размер |
|
|
|
|
|
Подвижная |
|||
а, параллельность оси отверстия к плоскости |
|
|
|
|
|
призма |
|||
|
|
|
|
|
|
||||
А, перпендикулярность оси отверстия к |
|
|
|
|
|
|
|||
плоскости Б в сечении I-I, симметричность |
|
|
|
|
6 |
|
|||
отверстия относительно наружного контура |
|
|
|
|
|
||||
|
|
6 |
|
|
|
||||
|
|
|
|
|
|
|
|
|
|
В |
H |
|
А |
|
|
|
|
|
|
|
|
|
4 |
|
5 |
4,5 |
|
|
|
|
|
|
|
|
|
|
|||
|
|
|
|
|
|
|
|
|
|
|
|
|
d |
|
|
|
|
|
|
|
|
|
а |
|
|
|
|
|
|
|
|
Б |
А |
2 |
1 |
3 |
1 |
2,3 |
|
|
|
|
|
||||||
|
|
|
|
4 |
|
5 |
|
|
|
В |
d |
|
Б |
|
1 |
|
|
|
|
|
|
|
|
2 |
|
3 |
|
|
|

|
|
Продолжение прил.2 |
Технологическая задача |
Теоретическая схема базирования |
Пример возможной реализации теоретической |
|
|
схемы базирования |
6. Обработать с применением кондуктора отверстия d1 и d2 во втулках рычага, обеспечив выполнение следующих требований:
а)перпендикулярность осей отверстий к плоскости А и симметричность отверстий относительно общей плоскости симметрии втулок рычага Б;
Б |
1 |
|
|
|
3 |
||||
6 |
|
d1
d2
4 |
2 |
5 |
|
|
Б |
|
d1 |
А |
d2 |
|
|
А

|
|
|
|
|
Продолжение прил.2 |
Технологическая задача |
Теоретическая схема базирования |
Пример возможной реализации теоретической |
|||
|
|
|
|
|
схемы базирования |
б)перпендикулярность осей отверстий |
|
|
|
||
к плоскости А и симметричность |
|
|
|
||
отверстий относительно плоскостей |
|
|
|
||
симметрии втулок X и Y; |
|
|
|
|
|
|
Б |
|
У |
|
|
|
У |
|
|
|
|
|
Б |
|
6 |
|
|
|
|
1 |
|
|
|
|
В |
Х |
3 |
Х |
|
|
|
|
|||
d1 |
В |
4 |
2 |
5 |
|
d2 |
Резьба левая |
Резьба правая |
|||
|
|
|
|
||
d1 |
А |
d2 |
|
|
|
|
|
|
|
|
|
|
А |
|
|
|
|

|
|
|
|
|
|
Продолжение прил.2 |
|
Технологическая задача |
|
|
Теоретическая схема базирования |
Пример возможной реализации теоретической |
|
|
|
|
|
|
|
схемы базирования |
в)Перпендикулярность осей отверстий к плоскости |
|
|
||||
А, симметричность отверстий |
|
|
|
|
|
|
|
Б |
|
|
|
|
|
В |
|
|
|
|
6 |
|
Б |
|
|
|
|
|
|
|
|
|
|
1 |
|
|
|
|
|
|
|
|
|
D1 d1 |
|
|
d2 |
Х |
3 |
Х |
|
|
|
||||
|
|
4 |
5 |
|
||
|
|
|
|
|
||
|
|
|
|
|
2 |
|
относительно плоскости симметрии втулок X и |
|
|
|
|||
соосность отверстия d1 относительно наружной |
|
|
|
|||
поверхности втулки |
|
|
|
|
|
|
В |
d1 |
А |
d2 |
|
|
|
|
|
А |
|
|
|
|
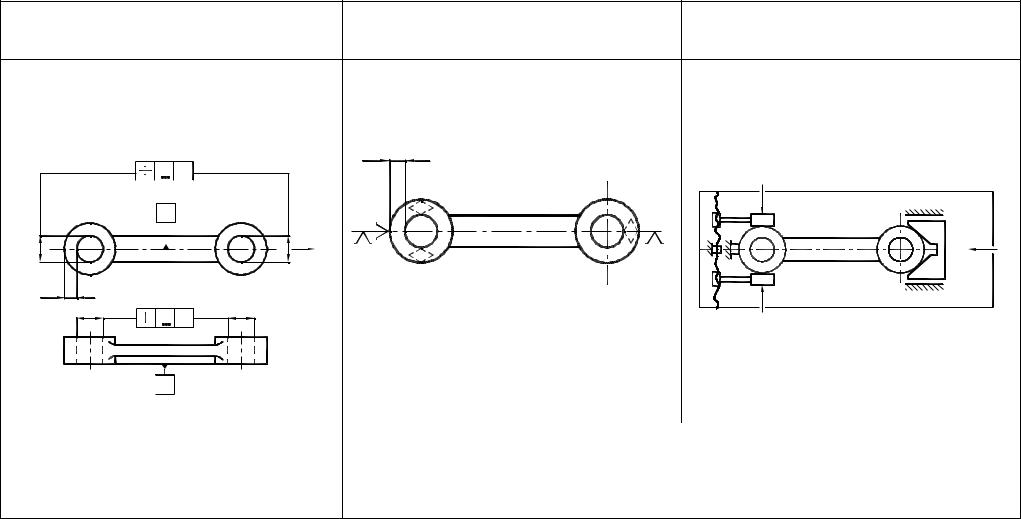
|
|
|
|
|
|
Продолжение прил.2 |
Технологическая задача |
|
|
Теоретическая схема базирования |
Пример возможной реализации теоретической |
||
|
|
|
|
|
|
схемы базирования |
г) перпендикулярность осей отверстий к |
|
|
|
|
||
плоскости А, симметричность отверстий |
|
|
|
|
||
относительно плоскости симметрии X и |
|
|
|
|
||
постоянство толщины С стенки левой втулки |
S |
|
|
|||
|
Б |
|
|
|
|
|
|
|
|
|
|
|
|
Б |
|
|
|
|
1 |
|
|
|
|
6 |
3 |
|
|
d1 |
|
d2 |
Х |
5 |
|
4 |
|
|
2 |
||||
|
|
|
|
|||
|
|
|
|
|
|
|
S |
|
|
|
|
|
|
d1 |
А |
d2 |
|
|
|
|
|
|
|
|
|
|
|
А |
|
|
|
|
|
|
|
|
|
|
Примечание: на теоретических схемах базирования арабскими цифрами обозначены опорные |
||
|
|
|
|
точки. |
|
|

Приложение 3
Задания для расчета точности обработки и погрешности базирования
1. На вертикально-фрезерном станке обрабатывают ступенчатую поверхность втулки, установленную на цилиндрический палец с буртом (рис. I). Диаметр базового отверстия D=30+0,039мм, диаметр установочного пальца d=30−−00,,007016 мм.
Требуется определить ожидаемую точность выполнения размеров А1 и А2, если известно, что составляющие погрешности установки (погрешности закрепления и положения заготовки) равны 0, т.е. Ез=Еп.з=0. Точность метода обработки принять равной ω =0,120мм. Исходя из схемы установки заготовки в приспособлении погрешность базирования при выполнении размера А1 определяется по уравнению:
Εб А1=Smax=ТD+Smin+Td=0,039+0,007+0,09=0,055мм,
а погрешность базирования при выполнении размера А2 поскольку измерительная и технологическая базы совмещены.
Поскольку по условию задачиεз=εп.з=0 то соответственно
ТА1=εб А1+ω =0,055+0,120=0,175мм ТА2 =εб А2+ω =0+0,120=0,120мм
2. Обработка наружной цилиндрической поверхности втулок диаметром 115мм производится при установке их с зазором на жесткой шпиндельной оправке (рис.2). Базовое отверстие имеет диаметр Ø65+0,035мм. Цилиндрическая рабочая поверхность оправки диаметром 65(−−00,,0306 )мм имеет радиальное биение
относительно ее конусной поверхности 0,020мм, а биение шпинделя станка составляет 0,010мм. Точность метода обработки ω =0,05мм. Определить ожидаемую точность обработки наружной цилиндрической поверхности втулки и
еевозможное отклонение от соостности относительно базового отверстия.
3.Для фрезерования паза концевой фрезой рычаг устанавливается в призмах
(рис.3). Найти зависимости погрешности базирования для размеров А1, А2, А3, А4. Угол призм α =900. Размер LD между осями базовых цилиндрических поверхностей (d1 и d2) выполнен с отклонениями ±ТL 0 /2.
1

4.На горизонтальнофрезерном станке набором фрез одновременно производят обработку поверхностей 1,2,3,4 (рис.4). Вывести расчетные зависимости для определения погрешности базирования при выполнении
размеров А1, А2, А3, А4, А5, А6. Указать размеры, на точность выполнения которых будет оказывать влияние непостоянство силы зажима заготовки. Размеры А7 и А8 выполнены соответственно с отклонениями ±ТА7/2 и ±ТА8/2.
5.На вертикально-сверлильном станке производят обработку ступенчатого отверстия комбинированным зенкером (рис.5).
Вывести зависимости для определения погрешности базирования размеров
А1, А2, А3, А5, D1 и D2.
6. При обработке поверхностей заготовки на горизонтально фрезерном станке набором фрез возможно два варианта установки (рис.6). Требуется определить, какая схема установки обеспечивает выполнение заданной точности размеров: 50+0,3 мм, 75-0,2 мм и 40±0,1 мм. Наружная цилиндрическая поверхность заготовки R =30-0,1 мм, диаметр отверстия D =30+0,021 мм. Размеры установочных пальцев d =30−−00,,007020 мм. Угол призмы α =900. Средняя экономическая точность
метода обработки ω =0,050 мм. Погрешностями закрепления заготовки и погрешностью положения заготовки в приспособлении пренебречь, т.е. принять
εз=εп.з=0.
7. При установке заготовок на плоскую поверхность и два отверстия производят обработку поверхностей 1,2,3 и паза, выдерживая размеры А1, А2, А3, А4, А5, А6 и А7 (рис.7). Требуется: определить погрешность базирования для указанных размеров, если известно, что базовые отверстия заготовок D1 и D2 выполнены с допуском ТD1=ТD2=0,013 мм установочные пальцы d1 и d2 с допуском Тd1=Тd2=0,009 мм, а минимальный зазор в сопряжении базовых отверстии с установочными пальцами S1min=S2min =0,007мм. Размер между осями базовых отверстий выполнен с отклонениями ±0,05 мм.
8. У цилиндрических втулок с наружным диаметром d =80-0,2 мм и
внутренним D=40+0,050 мм требуется фрезеровать шпоночный паз шириной В=18+0,1 мм, выдерживая размеры H=70-0,2 мм h =90+0,8 мм (рис.8). Смещение оси шпоночного паза е относительно диаметральной плоскости втулки не должно
превышать 0,1 мм. Выбрать такую схему установки (из шести), для которой расчетная погрешность базирования для выполняемых размеров В1 Н1 h и отклонения от соостности е минимально и обеспечивается достижение заданной точности обработки.
Угол призм α =900, максимальный зазор при установке заготовки на палец или во втулку Smax=0,01 мм. Допуск на изготовление установочного пальца и центрирующей втулки равен 0,02 мм. Точность метода обработки ω =0,060 мм.
Принять εз=εп.з=0.
2

|
А1 |
V |
Q |
|
|
|
|
|
|
D |
|
|
d |
А2 |
|
|
|
|
|
+ S |
Рис.1. Схема фрезерования втулки (к задаче 1) |
|
|
1.6 |
115 |
+0,035 |
65 |
Рис.2. Схема установки втулки (к задаче 2)
3

L0
А4 d2
d1 |
|
|
|
А3 |
|
|
|
А1 |
А2 |
|
|
Рис.3. Схема установки рычага (к задаче 3) |
|||
А1 |
|
А5 |
|
А2 |
|
|
|
А8 |
А3 |
|
|
1 2 |
3 |
|
Q |
|
|
А6 |
|
|
4 |
4 |
|
|
А |
|
|
|
|
|
|
|
А7 |
|
Рис.4. Схема обработки поверхностей заготовки (к задаче 4)
4

|
V |
|
D1 |
S |
|
Q |
|
Q |
|
3 |
|
|
А |
|
|
2 |
А4 |
|
А |
|
D2 |
1 |
|
А |
|
|
А5 |
|
|
Рис.5.Схема обработки отверстия (к задаче 5) |
|
5

|
|
75-0,2 |
|
+-0,1 |
50+0,3 |
+-0,1 |
|
|
|
||
40 |
|
|
40 |
R |
|
|
|
|
|
D |
|
|
|
|
20 |
L=150 +- 0,1 |
50 |
||
а) |
|
|
|
|
|
75-0,2 |
|
+-0,1 |
50+0,3 |
+-0,1 |
|
|
|
||
40 |
|
|
40 |
R |
|
|
|
|
|
D |
|
L=150 |
+ |
0,1 |
50 |
- |
б)
Рис.6. Схемы установки заготовки при фрезеровании (к задаче 6)
6

|
|
|
|
|
D1 |
|
A2 |
|
|
|
|
|
D2 |
||||||||||||
|
|
|
|
|
|
|
|
|
|
|
|
|
|
|
|
|
|
|
|
|
|
|
|
|
|
|
|
|
|
|
|
|
|
|
|
|
|
|
|
|
|
|
|
|
|
|
|
|
|
|
|
|
|
|
|
|
|
|
|
|
|
|
|
|
|
|
|
|
|
|
|
|
|
|
|
|
|
|
|
|
|
|
|
|
|
|
|
|
|
|
|
|
|
|
|
|
|
|
|
|
|
|
|
|
|
|
|
|
|
|
|
|
|
|
|
|
|
|
|
|
|
|
|
|
|
|
|
|
|
|
|
|
|
|
|
|
|
|
|
|
|
|
|
|
|
|
|
|
|
|
|
|
|
|
|
|
|
|
|
|
|
|
|
|
|
|
|
|
|
|
|
|
|
|
|
|
|
|
|
|
|
|
|
|
|
|
|
|
|
|
|
|
|
|
|
|
|
|
|
|
|
|
|
|
|
|
|
|
|
|
|
|
|
|
|
|
|
|
|
|
|
|
|
|
|
|
|
|
|
|
|
|
|
|
|
|
|
|
|
|
|
|
|
|
|
|
|
|
|
|
|
|
|
|
|
|
|
|
|
|
|
|
|
|
|
|
|
|
|
|
|
|
|
|
|
|
|
|
|
|
|
|
|
|
|
|
|
L 0 |
S/2 |
|
3 |
|
|
|
|
||
|
d1 |
|
d2 |
|
|
|
|
A6 |
|
|
|
1 |
S |
1/2 |
|
2e |
A4 |
|
|
|
|||
|
|
|
|
|
|
|
2 |
A2 |
|
|
|
|
|
|
|
|
|
A |
1 |
A |
3 |
5 |
|
|
A |
|
A |
|
|
Рис.7. Схема установки заготовки при механической обработке (к задаче 7) |
|
7

|
d |
|
|
|
D |
Q |
|
|
|
|
|
|
|
|
|
|
H |
Q |
H |
|
|
|
||
|
|
|
|
h |
|
а) |
|
|
б) |
|
|
|
|
|
|
В |
|
|
|
|
|
|
|
H |
Q |
е |
Q |
|
Q |
|
H |
|
|
|
|
в) |
|
|
г) |
|
|
|
|
Q |
15 |
h |
|
|
|
|
|
Q |
|
H |
|
|
H |
|
|
|
д) |
|
|
е) |
|
|
|
|
Рис.8. Схемы установки заготовки при обработке шпоночного паза (к задаче 8)
8

9

Приложение 4
ОБОСНОВАНИЕ ВЫБОРА БАЗ И ТЕХНОЛОГИЧЕСКИЕ РАЗМЕРНЫЕ ЦЕПИ |
|
||||||||||||||||||||
|
|
|
|
|
|
|
|
|
|
|
|
|
|
|
|
|
|
Z |
|
|
|
|
|
|
|
|
80 |
|
90 |
|
|
|
|
|
|
|
|
|
90 |
80 |
|
|
|
|
|
|
|
100 |
|
|
|
|
|
|
|
|
|
|
|
|
|
|
|
||
|
|
|
|
|
|
|
|
|
|
|
|
|
|
|
|
|
100 |
|
|
||
|
|
|
|
|
|
|
|
|
|
|
|
|
|
|
|
|
10 |
|
|
||
|
|
1 |
|
10 |
|
|
|
|
|
|
|
|
|
|
|
|
|
|
|
|
|
|
|
|
|
|
|
|
|
|
|
|
|
|
|
|
|
|
|
|
|
||
|
|
|
|
|
30 |
7 |
|
|
|
|
|
|
|
|
34 |
|
|
|
|
|
120 |
|
|
|
|
|
|
|
|
|
|
|
|
|
|
|
|
|
|
|
|||
|
|
|
2 |
3 |
|
4 |
у |
|
|
|
|
|
Х |
11 |
|
|
|
|
|
|
13 |
|
|
|
|
|
|
|
|
|
|
|
|
+ |
|
|
|
|
|||||
|
|
|
|
1 |
|
|
|
|
|
|
|
|
|
|
|
|
|
|
|
|
|
|
|
|
|
|
|
|
|
|
|
|
|
|
|
|
|
|
у=55-0,06 |
|
|
|
|
|
|
1 |
2 |
3 |
4 |
5 |
8 |
7 |
10 |
100 |
90 |
80 |
|
11 |
30 |
10 |
90 |
100 |
80 |
120 |
13 |
|
|
|
+ |
|
|
|
|
Д=15-2 |
|
|
|
|
|
|
|
+ |
|
|
|
|
|
РАЗМЕРЫ |
Б=5-1 |
|
|
|
|
|
|
|
|
|
|
|
Т=120-0,05 |
|
|
|
|||||
|
|
|
|
|
|
+ |
|
|
|
|
|
|
|
|
|
|
|
+ |
|||
|
А=100-0,3 |
|
+ |
|
Е=42-0,05 |
|
+0,025 |
|
|
|
|
|
Р=132-3 |
|
|
С=66-1 |
|||||
ДЕТАЛИ |
|
|
В=50-1 |
|
|
|
И=25 |
|
|
|
|
|
|
|
|
|
|||||
|
|
|
С=5+1 |
|
|
|
Ж=0+0,1 |
|
|
|
|
|
|
|
+ |
|
|
||||
|
|
|
- |
|
|
|
- |
З=0+0,5 |
|
|
|
|
+ |
|
З=0-0,5 |
|
|||||
|
|
|
|
|
|
|
|
|
|
|
|
- |
|
|
|
|
Ж=0-0,1 |
|
|
|
|
|
|
|
|
|
|
|
|
|
|
|
|
|
|
|
|
|
И=25+0,025 |
|
|
|
|
|
|
ЧИСТОВАЯ |
|
|
|
|
|
|
|
|
|
|
|
|
|
|
|
|
|
|
|
ОБРАБОТКА С |
|
|
|
|
|
|
|
|
|
|
|
|
|
|
|
|
|
|
|
|
|
ИСПОЛЬЗОВАНИЕМ |
|
|
|
|
|
|
|
|
|
|
|
|
|
|
|
|
|
|
|
||
КОМПЛЕКТА ПТБ |
ЧЕРНОВАЯ |
|
|
|
|
|
|
|
|
|
|
|
|
|
|
|
|
|
|
|
|
|
|
СВЕРЛЕНИЕ |
|
|
|
|
|
|
|
|
|
|
|
|
|
|
|
|
|
|
|
|
1 |
2 ОТВ |
|
|
|
|
|
|
|
|
|
|
|
|
|
|
|
|
|
|
|
ОБРАБОТКИ |
|
|
|
|
|
|
|
|
|
|
|
|
|
|
|
|
|
|
|
|
|
ВАРИАНТ |
ФРЕЗЕРОВАНИЕ |
|
|
|
|
|
|
|
|
|
|
|
|
|
|
|
|
|
|
|
|
ПЛОСКОСТИ |
|
|
|
|
|
|
|
|
|
|
|
|
|
|
|
|
|
|
|
||
ЗАГОТОВКА |
|
|
|
|
|
|
|
|
|
|
|
|
|
|
|
|
|
|
|
||
|
|
|
|
|
|
|
|
|
|
|
|
|
|
|
|
|
|
|
|
||
ВЫБОРДЛЯБАЗ КОМПЛЕКТАПТБ |
|
СВЕРЛЕНИЕ |
|
|
|
|
|
|
|
|
|
|
|
|
|
|
|
|
|
|
|
ВАРИАНТ 2 |
2 ОТВ |
|
|
|
|
|
|
|
|
|
|
|
|
|
|
|
|
|
|
|
|
ФРЕЗЕРОВАНИЕ |
|
|
|
|
|
|
|
|
|
|
|
|
|
|
|
|
|
|
|
||
ПЛОСКОСТИ |
|
|
|
|
|
|
|
|
|
|
|
|
|
|
|
|
|
|
|
||
ЗАГОТОВКА |
|
|
|
|
|
|
|
|
|
|
|
|
|
|
|
|
|
|
|
||
|
|
|
|
|
|
|
|
|
|
|
|
|
|
|
|
|
|
|
|
|

Библиографическое описание
1.ГОСТ 21495 -.Базирование и базы в машиностроении.М.,1976.
2.Балакшин Б.С. Теория и практика технологии машиностроения: В 2 кн..М. : Машиностроение, 1982. 310 с.и 286 с.
3.Технология машиностроения (специальная часть): Учебник для машиностроительных специальностей вузов / А.А.Гусев, Е.Р.Ковальчук, И.М.Колесов и др.М. : Машиностроение, 1986.480с.
4.Корсаков В.С. Основы конструирования приспособлений: Учеб.для вузов.М. :Машиностроение, 1983.277с.
5.Горохов В.А. Проектирование и расчет приспособлений: Учеб.пособие. Минск: Высшая школа, 1986.238с.
6.Сборник задач и упражнений по технологии машиностроения: Учеб.пособие для машиностроительных вузов по спец. “Технология машиностроения”, “ Металлорежущие станки и инструметы”/ В.И. Аверченков, О.А.Горленко, В.Б. Ильицкий и др.М. : Машиностроение,1988.192с.
7.Размерный анализ технологических процессов / В.В.Матвеев, М.М. Тверской, Ф.И.Бойков и др. М. : Машиностроение, 1982.264с.
8.Косилова А.Г., Мещеряков Р.К., Калинин М.А. Точность обработки, заготовки и припуски в машиностроении: Справочник технолога. М. : Машиностроение, 1985. 288 с.
9.Колесов И.М. Основы технологии машиностроения: Учебник для машиностроительных вузов. – М.: Машиностроение, 2001 г. 591 с.
10.Солонин И.С., Солонин С.И. Расчет сборочных и технологических размерных цепей. – М.: Машиностроение, 1980. – 110 с.
11.Справочник технолога - машиностроителя : В 2-х т. -М. : Машиностроение Т.1/ В. Б. Борисов [и др.] ; ред. А. Г. Косилова, ред. Р. К. Мещеряков. -4-е изд., перераб. и доп. -2001.-655 с.
12.Обработка металлов резанием; Справочник технолога А.А. Панов, Н.Г. Бойм и др. Под общей редакцией А.А. Панова 2е издание. – М.: Машиностроение, 2004, – 784 с.: ил.
13.Станочные приспособления: Справочник в 2-х т. Б.Н. Вардашкин и др.
– М.: Машиностроение, 1984, – Т.1 – 256 с. Т2 – 656 с.
14.Станочные приспособления. Альбом А.Г. Схиртладзе, В.Ю. Новиков и др. – Йошкар – Ола, 1988. – 169 с.