
kontemirov
.pdf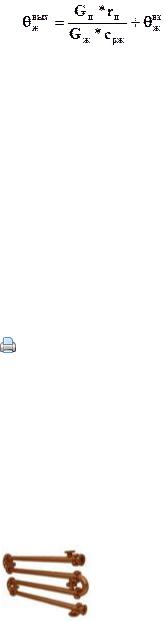
· Наиболее эффективные каналы управления:
.
Анализ статической характеристики объекта.
Из уравнения статики выразим в явном виде:
. (30)
·Статическая характеристика линейна по отношению к воздействиям по: .
·Статическая характеристика нелинейна по отношению к воздействию по Gж.
·Статическую характеристику можно линеаризовать по отношению к Gж введением стабилизации соотношения расходов: , тогда получим:
. (31)
Преимущества, недостатки
и применение кожухотрубных теплообменников
A-A+
27.12.2012 | Санкт-Петербург | Пищевая промышленность
Как известно, существует множество типов теплообменников (ТО). Они разделяются на поверхностные (рекуперативные и регенеративные, в зависимости от одновременного или
Яндекс.Директ
Кожухотрубный теплообменник«Гарант-
сервис»- сертифицированное производство теплообменников. Доставка!О компанииВодоводяные
бойлерыПароводяные бойлерыФильтры,грязевикиgarant- servis74.ruАдрес и телефонСкрыть объявление
Спасибо. Объявление скрыто.
Как известно, существует множество типов теплообменников (ТО). Они разделяются на поверхностные (рекуперативные и
регенеративные, в зависимости от одновременного или поочерёдного контакта теплоносителей с разделяющей их стенкой) и смесительные. ТО поверхностного типа в свою очередь делятся на кожухотрубные, типа «труба в трубе», витые, погружные, оросительные, спиральные, пластинчатые и кожухопластинчатые.
Кожухотрубный |
теплообменник представляет |
|||
собой |
пучок |
трубок, |
помещенных |
в |
цилиндрический кожух (корпус) таким образом, что внутренность корпуса является межтрубным пространством. Теплообменные трубки завальцованы в концевых трубных досках, приваренных к корпусу теплообменника. В некоторых кромки трубок дополнительно обвариваются для гарантии герметичности соединения. Промежуточные трубные решетки предназначены как для поддержки трубок, так и для организации поперечного тока среды. К трубным доскам крепятся камеры с патрубками для отвода среды, текущей внутри трубок. В зависимости от наличия и количества в камерах перегородок, теплообменники могут быть одноходовыми, двухили многоходовыми относительно движения среды, текущей в трубках. Также корпус снабжен патрубками для подвода пара и отвода конденсата. Трубки изготавливают из углеродистой или нержавеющей стали, меди, латуни или титана. Корпус обычно выполняется из углеродистой или нержавеющей стали. Когда теплообменник нагревается, происходит его удлинение. Существует несколько способов компенсации температурных расширений, например, применение «плавающей головки» или межсекционных компенсаторов. Кожухотрубные теплообменники обычно используются при давлении насыщенного пара выше 15 бари или при температуре выше 190°С, а также при
перегретом |
|
паре. |
Преимущества |
и |
недостатки |
Кожухотрубные теплообменники характеризуются стойкостью к гидроударам, пониженными требованиями к чистоте сред, относительно низким коэффициентом теплопередачи и, как следствие, большими габаритами и площадями, требуемыми для обслуживания, а также высокой ценой из-за большой металлоемкости. Кроме того, ремонт таких теплообменников обычно
связан с заглушкой поврежденных трубок, что ведет к уменьшению площади теплообмена. Поэтому обычно теплообменники выбираются с большим запа¬сом по поверхности, что также обуславливает их большие габа¬риты. Попытка регулирования по конденсату на горизонтальных кожухотрубных теплообменниках вызывает сложности. Это про¬исходит по причине того, что при незначительном изменении уровня конденсата, площадь теплообмена меняется нелинейно и намного существеннее. Тем не менее, современные кожухотрубные теплообменники по показателям эффективности,
коэффициента |
теплопередачи и габаритам |
||
приближаются |
к |
пластинчатым |
и |
кожухопластинчатым |
теплообменникам. |
Это достигается за счет применения так называемых турбу лизаторов потока — перегородок в трубках и межтрубном пространстве, а также рифленых трубок, в которых поток среды сильно турбулизирован, что ведет к повышению коэффициента теплопередачи, и, как следствие, к уменьшению габаритов. В последнее время для уменьшения использования производственной площади применяются вертикальные кожухотрубные теплообменники. Они позволяют организовать регулирование по конденсату, если это необходимо.
Применение Кожухотрубные теплообменники чаще всего
применяются в химической, нефтяной, газовой
промышленности, |
а |
также |
большой |
теплоэнергетике, |
|
где |
используются |
теплоносители высоких параметров. Кроме этого их можно встретить на пивном, молочном и других пищевых производствах.
22) Автоматизация хлебопекарных печей
В настоящее время основным направлением в конструировании печей хлебопекарного производства является создание высокопроизводительных печей каркаснозасыпного типа с туннельной рабочей камерой, с электрическим либо рециркуляционным обогревом, сетчатым конвейерным подом и металлической обшивкой. Такие печи сравнительно легко
поддаются автоматизации, хорошо вписываются в топочные линии, режимные параметры их работы быстро достигают заданных значений, что позволяет решить вопрос о переходе на двух- и односменную работу оборудования. При электрическом либо рециркуляционном обогреве пекарной камеры снижаются тепловые потери печью и, как следствие, обеспечиваются низкие удельные энергозатраты на выпечку. Автоматизация процесса выпечки и установка печи в поточной линии способствует сокращению численности обслуживающего персонала на предприятиях.
Система автоматического управления печей включает системы автоматического контроля, регулирования, блокировок и защиты. В туннельных печах контролируют следующие параметры: температуру среды пекарной камеры и газов, поступающих на рециркуляцию; давление пара, идущего на увлажнение, и газа перед топкой; продолжительность выпечки и др.
Контроль температуры по длине пекарной камеры осуществляют отдельно по тепловым зонам печи. Температуру греющих газов измеряют термопарами.
Давление пара, поступающего на увлажнение в пекарную камеру, контролируют двумя манометрами: на паропроводе перед регулирующим вентилем и за вентилем, непосредственно на коллекторе, откуда по трубам пар поступает в пекарную камеру. Давление горючего газа, поступающего в горелки печи, проверяют непосредственно перед задвижкой на линии подачи газа в горелки.
Продолжительность выпечки определяют по схеме тахоге-нератор — миллиамперметр. В некоторых печах длительность выпечки контролируют по шкале на вариаторе
скоростей.
Автоматическое регулирование температуры пекарной камеры у разных типов печей осуществляется по-разному.
В печах БН датчик температуры установлен на выходе из камеры смешения, “Термоэлектро” — во всасывающем патрубке вентилятора рециркуляции, “Орланди” — в пекарной камере, в печах ПХК применяют два датчика, по показаниям которых вырабатывается пропорциональное управляющее воздействие на регулятор.
Во многих типах печей (РЗ-ХПУ и др.) используют двухпозиционное регулирование ^топочного процесса. В печах БН, “Орланди” в зависимости от сигнала от термопары уменьшается или увеличивается расход топлива, т.е. горелка работает по схеме “большой факел — малый факел” с отклонением, составляющим 30% от максимальной производительности. В печи “Термоэлектро” с поступлением сигнала либо прекращается подача топлива, либо горелка зажигается и работает с максимальной производительностью.
Продолжительность переходного процесса в печи БН-50 составляет 18-20,а в печи ПХК50 — 13-15 мин, что объясняется более рациональной конструкцией последней печи и лучшими ее динамическими свойствами.
В печах ПХК система автоматизации обеспечивает автоматическое регулирование температуры в пекарной камере по двум сигналам с помощью электронного регулятора. Основной сигнал поступает от термо/ары, установленной в первой зоне пекарной камеры. Регулирующее воздействие передается на привод исполнительного механизма, который управляет работой регулирующего клапана,
подающего газ на горелки.
Большинство печей оборудовано системой блокировок и аварийной защиты. Аварийная сигнализация и автоматическая система защиты печи от взрыва и перегрева срабатывает в следующих случаях: при падении разряжения в топке из-за отказа
вентилятора рециркуляции, в случае погасания факела горелки или повышения температуры в топке печи выше заданной.
При разработке системы автоматического регулирования работы отечественных печей используют серийно выпускаемые приборы и аппаратуру. Этой системой предусмотрена продувка газопроводов перед каждым розжигом.
При увеличении температуры газов в конце камеры смешения сверх допустимой (примерно 600 °С) специальное устройство обесточивает систему, что приводит к прекращению подачи топлива к горелочному устройству.
Системы автоматизации в большой степени обеспечивают безопасную работу печей. Запрещается эксплуатировать печь, если система автоматизации ее не функционирует.
Введение
Нагрев металла является важнейшей технологической операцией, в значительной мере определяющей экономические показатели производственного процесса в целом. Технология прокатки предъявляет жесткие требования к качеству нагрева. Распределение температур по сечению заготовки, обеспечивающее необходимую пластичность металла, должно быть достигнуто за определенное время без чрезмерного перегрева поверхности металла. Нагревательные устройства должны обеспечить кондиционный нагрев металла в условиях переменного ритма работы стана и при минимальном расходовании топлива. Качество нагрева определяется избранным графиком нагрева металла, т. е. скоростью и продолжительностью нагрева в каждой из зон печи.Каждому графику нагрева
соответствуют конечная температура поверхности металла,неравномерность температур по сечению заготовки и величина угара металла. В современных методических печах кривая, характеризующая распределение температур по длине печи, круто поднимается на участке, соответствующем загрузочному концу печи, и становится пологой на участке, соответствующем высокотемпературной зоне ее.
Соблюдение такого графика обеспечивается высокой температурой отходящих газов. Применение его особенно целесообразно при нагреве толстых заготовок, так как теплопроводность металла уменьшается с повышением его температуры. С повышением температуры в сварочной зоне трехзонных печей необходимое время выдержки в томильной зоне часто удлиняется в большей степени, чем сокращается время нагрева в методической и сварочной зонах. Поэтому оптимальное значение температуры сварочной зоны,соответствующее нагреву металла до заданных кондиций, соответствует в первую очередь, заданной неравномерности температур по сечению заготовки.
1. ЛИТЕРАТУРНЫЙ ОБЗОР
В прокатных цехах заканчивается цикл металлургического производства. Процесс получения готового прокатного изделия обычно разбивается на несколько этапов: вначале слиток прокатывают на крупных обжимных и заготовительных станах до заготовки, которую затем для получения готового профиля передают на сортовые, листопрокатные или специальные (колесопрокатные, трубопрокатные и др.) станы.
Качество продукции и производительность прокатных станов во многом определяются работой нагревательных печей, причем в большинстве случаев ошибки, возникающие при нагреве металла, уже не могут быть исправлены. Проявляясь на последующих переделах, эти ошибки приводят к снижению выхода годной продукции.
Нагревательные печи прокатного производства предназначены для нагрева слитков перед прокаткой на обжимных
станах и заготовок (слябов и блюмов) – перед листовыми и сортовыми станами.
Являясь начальным звеном технологической линии прокатного производства, нагревательные печи в своей работе тесно связаны с ритмом работы прокатного оборудования, и наряду с этим сохраняют особенности, присущие всем теплотехническим агрегатам. Основное время печи работают в переходных режимах, вызванных изменением сортамента, марки нагреваемых заготовок и темпа их выдачи. В прокатном производстве для нагрева металла перед прокаткой используются в основном три вида нагревательных печей:нагревательные колодцы, методические и секционные.
Современные нагревательные печи представляют собой высокомеханизированные агрегаты,удовлетворяющие технологическим и экологическим требованиям, однако жизнь выдвигает новые задачи развития печной техники.
Требования к работе нагревательных печей включают в себя:
-обеспечение заданной производительности;
-обеспечение качества нагрева, удовлетворяющего технологов по структуре и по механическим свойствам металла, по степени окалинообразования и обезуглероживания;
-эффективное использование топлива, характеристикой которого служит удельный расход энергии на единицу продукции в кг условного топлива на 1 тонну продукции;
-соответствие экологическим нормам по предельно допустимому выбросу в атмосферу пыли и вредных газов: СО, СО2, NOx, SO2, C20H12 и других углеводородов;
-механизация труда при эксплуатации и ремонте печи и автоматизация её теплового режима.
Интегральным экономическим показателем технологии нагрева и конструкции печи является себестоимость нагрева и срок окупаемости капиталовложений в строительство или реконструкцию печи при гарантированном качестве продукции и соответствии экологическим нормам.
В настоящее время производительность печи является варьируемым фактором. Одну и ту же производительность можно обеспечить при работе одной или нескольких печей.Существует понятие оптимальной производительности печи, соответствующей минимуму расхода энергии на нагрев металла, либо минимуму себестоимости нагрева.
На передний план выдвигается требование эффективного использования топлива и других ресурсов,т.е. проблема энерго- и ресурсосбережения. В связи с этим меняется актуальность научных проблем. Например, утратила своё значение задача интенсификации теплообмена в печах, как средство повышения скорости нагрева, а, значит, и производительности нагревательных печей. Скоростной нагрев и высокая производительность сегодня не являются самоцелью, поскольку промышленной практике нужны не рекорды, а экономическая целесообразность.
Из анализа теплового баланса печи, записанного в форме, предложенной И.Д.Семикиным, следует вывод о том, что возможны три направления энергосбережения:
-уменьшение теплового дефицита металла Δi, т.е. количества теплоты, которое должен поглотить 1 кг металла в печи, чтобы нагреться от начальной до конечной температуры;
-уменьшение потерь теплоты из рабочего пространства печи через футеровку и окна в окружающую среду, а также на разогрев футеровки до рабочей температуры;
-повышение коэффициента использования теплоты топлива (КИТ), т.е. доли теплоты сгорания топлива,которую удается использовать в пределах рабочего пространства печи. Расход топлива на печь обратно пропорционален величине КИТ.
Рассмотрим конкретные способы реализации каждого из трёх направлений энергосбережения в современных печах металлургии и машиностроения.
1 способ. УменьшениеΔi достигается на практике путем повышения начальной температуры металла при посаде его в печь. Так называемый "горячий посад" возможен при сохранении в металле теплоты,
полученной им в предыдущем переделе, в том числе теплоты кристаллизации слитков. Применяемая на комбинате "Запорожсталь"технология посада в нагревательные колодцы слитков с незатвердевшей сердцевиной обеспечивает, по свидетельству комбината, сокращение удельного расхода топлива на 40%, с 51,7 до 30,7 кг условного топлива на тонну слитков. Подобные результаты получены на комбинате "Криворожсталь". Согласно расчетам,в момент посада слитков в колодцы примерно 30% их объема занимает жидкая сердцевина.
Необходимо как можно меньше охлаждать заготовки, полученные на МНЛЗ, перед посадом в нагревательные печи для последующей прокатки. Примером осуществления такой энергосберегающей технологии являются литейно-прокатные модули.
В ряде случаев удаётся вообще исключить промежуточный нагрев металла между двумя последовательными прокатными станами, т.е. довести тепловой дефицит до нуля благодаря уменьшению потерь теплоты раскатами при транспортировке от одного стана к другому. На комбинатах "Запорожсталь" и им. Ильича внедрена технология"транзитной" прокатки слябов на непрерывных листовых станах, при которой 95% слябов прокатываются без промежуточного нагрева в методических печах. В данном случае удельный расход условного топлива в методических печах сокращен с 85 до 15 кг/т.
Уменьшить Δi можно также путем снижения температуры нагрева металла в печи. Однако надо учитывать,что это повлечет за собой не только уменьшение расхода топлива, угара и обезуглероживания металла, но и увеличит расход электроэнергии на прокатку и,вероятно, сократит срок службы прокатных валков. Таким образом, выбор температуры нагрева заготовок представляет собой задачу оптимизации по минимуму всех затрат на процессы нагрева и прокатки.
2 способ. Потери теплоты из рабочего пространства имеют место в любых печах, но они особенно существенны в нагревательных и термических печах циклического действия, когда в цикл термообработки входит охлаждение печи до низкой температуры или когда такое охлаждение обусловлено длительными промежутками между