
- •Содержание
- •К 30-летию Рязанской ГРЭС
- •Внедрение интегрированной АСУ ТП
- •Опыт внедрения ВИР-технологии сжигания угля на Рязанской ГРЭС
- •Диагностика металла и восстановление деталей оборудования на Рязанской ГРЭС
- •Сетевые компьютерные тренажеры для подготовки операторов энергоблоков 260 МВт Рязанской ГРЭС
- •ЭКОНОМИКА ЭНЕРГЕТИКИ
- •Оценка экономической эффективности модернизации энергетического оборудования
- •ТЕПЛОВЫЕ ЭЛЕКТРОСТАНЦИИ
- •ТЭК Красноярского края. ОАО “Березовская ГРЭС-1”. Перспективы развития
- •Совершенствование методов расчета пылеприготовительных установок ТЭС
- •Состояние исследований по разработке СНКВ-технологии и перспективы ее широкого применения в теплоэнергетике
- •Повышение эффективности теплофикационных турбоустановок
- •Опыт освоения испарительной установки для подготовки добавочной воды на Северо-Западной ТЭЦ
- •ЭНЕРГОСИСТЕМЫ И ЭЛЕКТРИЧЕСКИЕ СЕТИ
- •Об организационно-правовых аспектах управления режимами электропотребления
- •Автоматика ликвидации асинхронного режима, основанная на скорости изменения частоты и на разности частот
- •ОБОРУДОВАНИЕ СТАНЦИЙ И ПОДСТАНЦИЙ
- •Масляные насосы для систем охлаждения силовых трансформаторов
- •Ремонт статорных обмоток турбогенераторов мощностью до 100 МВт
- •ЭНЕРГОХОЗЯЙСТВО ЗА РУБЕЖОМ
- •Некоторые вопросы развития электрических сетей США
- •ХРОНИКА
- •Содержание журнала “Электрические станции” за 2003 г.

Основным результатом для Рязанской ГРЭС – как участника энергетического рынка – является возможность расширения спектра сжигаемых углей, что, несомненно, скажется на себестоимости продукции.
На основании результатов проведенных испытаний специалистами ООО “Политехэнерго” по согласованию с Рязанской ГРЭС была проведена дополнительная модернизация устройства нижнего дутья. Весь объем работ был проведен в текущий ремонт блока в августе – сентябре 2002 г. Дополнительная модернизация заключалась в увели- чении аэродинамического “носа” устройства ввода нижнего дутья и соответственно в уменьшении зазора между кромкой “носа” и дефлектора. Цель проведенной модернизации – уменьшение тепловых потерь с механическим недожогом за счет снижения горючих в провале.
После последнего текущего ремонта в феврале 2003 г. на котле были проведены эксплуатационные испытания, во время которых зафиксирована нагрузка блока 298 МВт. Максимальное значение температуры, измеренное в топке во время испытаний, составило 1357°С на отметке 12 м. Температуры газов в поворотных камерах котла по показаниям штатных приборов находились на уровне 795 – 810°С.
Потери тепла с уходящими газами q2 составили 11,49% при проектном значении, равном 13,8%, потери тепла с механическим недожогом q4 = 0,13% при проектном значении, равном 0,35%. В качестве топлива использовался уголь Бе-
резовского разреза с калорийностью 3640 ккал кг, при влажности топлива 35%, зольности 6,5% и содержании серы 0,5%. Концентрация NOõ в дымовых газах (при = 1,4) составила 219 мг м3. Все расчеты потерь проводились в соответствии с методиками, использовавшимися для расчетов во время комплексных испытаний котла.
После проведенной реконструкции энергоблок ст. ¹ 2 отработал 7500 ч при среднесуточной эксплуатационной нагрузке 220 – 240 МВт. За весь указанный промежуток времени остановов котла для расшлаковки не проводилось ни разу. Периодические осмотры конвективных шахт котла свидетельствуют об отсутствии каких-либо золовых отложений на конвективных поверхностях нагрева котла.
За все время работы после реконструкции котла, включая проведенные испытания, энергоблок ни разу не останавливался из-за появления свищей в трубах нижней радиационной части котла. После годового опыта эксплуатации так и не нашло подтверждения предположение о возможном абразивном износе труб в нижней части топки. Измерения, проводимые специалистами лаборатории металлов и сварки Рязанской ГРЭС во время ремонтных кампании и периодических остановов блока, ни разу не зафиксировали какого-либо утонения труб холодной воронки.
Таким образом, реконструкцию, проведенную на котлоагрегате П-59 ст. ¹ 2 Рязанской ГРЭС, следует признать успешной и эффективной в плане повышения бесшлаковочной мощности котлов.
Диагностика металла и восстановление деталей оборудования на Рязанской ГРЭС
Гурылев О. Ю., èíæ.
Рязанская ГРЭС
По мере увеличения наработки энергетического оборудования происходит старение металла, прежде всего, работающих при высоких температурах в условиях ползучести деталей. Для обеспе- чения их надежности необходим тщательный, достоверный контроль состояния этих деталей.
По приказу РАО “ЕЭС России” с 1995 г. Рязанская ГРЭС входит в группу отраслевых образцов стареющих ТЭС, на базе которых проводятся обкатка и доработка технологий, обеспечивающих безопасную эксплуатацию энергооборудования, отработавшего парковый ресурс. В соответствии с отраслевой программой обеспечения живучести стареющих ТЭС на Рязанской ГРЭС внедрена и освоена компьютерная информационно-эксперт-
ная система ISP по определению категории опасности и возможности дальнейшей надежной эксплуатации гибов паропроводов, работающих в условиях ползучести, с учетом параметров и истинного состояния металла.
Для определения состояния металла гибов лабораторией металлов и сварки (ЛМС) станции производятся все неразрушающие виды контроля, предусмотренные действующими руководящими документами. Наиболее показательной из них является диагностика по микроструктуре, которая позволяет достоверно выявлять повреждаемость на стадии образования микродефектов (микропор) с характерным размером 1 – 3 мкм.
16 |
2003, ¹ 12 |

Микроструктурная диагностика производится ЛМС путем контроля:
структуры и микроповрежденности металла непосредственно на паропроводах переносным мобильным компьютерным комплексом;
микроповрежденности металла методом реплик; структуры и микроповрежденности металла по образцам, который позволяет определить микроповрежденность. Отбор микрообразцов произво-
дится электроискровым методом (ðèñ. 1). Характеристики состояния металла по резуль-
татам контроля вносятся в компьютерную инфор- мационно-экспертную систему ISP, позволяющую проводить индивидуальное наблюдение за каждым гибом.
Микроструктурный мониторинг и в целом ин- формационно-экспертная система внедрены на станции фирмой “Живучесть ТЭС”.
На Рязанской ГРЭС, как и на многих энергопредприятиях России, в связи с известными экономическими и технико-организационными факторами, эксплуатируются турбины, рабочие лопатки которых содержат опасные концентраторы напряжений. В сегодняшних экономических условиях замена изношенных деталей весьма проблематич- на как так, является делом дорогостоящим.
Ответственные элементы паровых турбин тепловых электростанций эксплуатируются в экстремальных условиях воздействия коррозионной среды. Эрозионно-коррозионные процессы, вызываемые влажно-паровым потоком, сокращают ресурс деталей и снижают надежность эксплуатации этих элементов и турбин в целом.
Наиболее интенсивно изнашивающимися и дорогостоящими элементами проточной части являются рабочие лопатки. Стоимость комплекта лопаток последней ступени роторов среднего и низкого давления К-300-240 ЛМЗ, К-800-240 ЛМЗ состав-
1 ( , , 2
ляет более 2,7 млн. руб. Интенсивные износы входных и выходных кромок лопаток сопровождаются возникновением опасных концентраторов напряжений, повышающих вероятность внезапных разрушений лопаток.
Современные способы активной и пассивной защиты лопаток не всегда удовлетворяют эксплуатационным требованиям.
В этой связи ВТИ и Рязанская ГРЭС совместно разработали метод и создали технологию упрочнения и восстановления лопаток турбин.
Технология электроискрового легирования (ЭИЛ) обеспечивает восстановление живучести поврежденных лопаток в зонах повреждений входной кромки на длине почти 600 мм и выходной кромки на длине до 800 мм (ðèñ. 2).
Работы по нанесению защитно-упрочняющих покрытий могут проводиться:
à) |
á) |
3 , , , , ' "
. 0 , , . 0
2003, ¹ 12 |
17 |
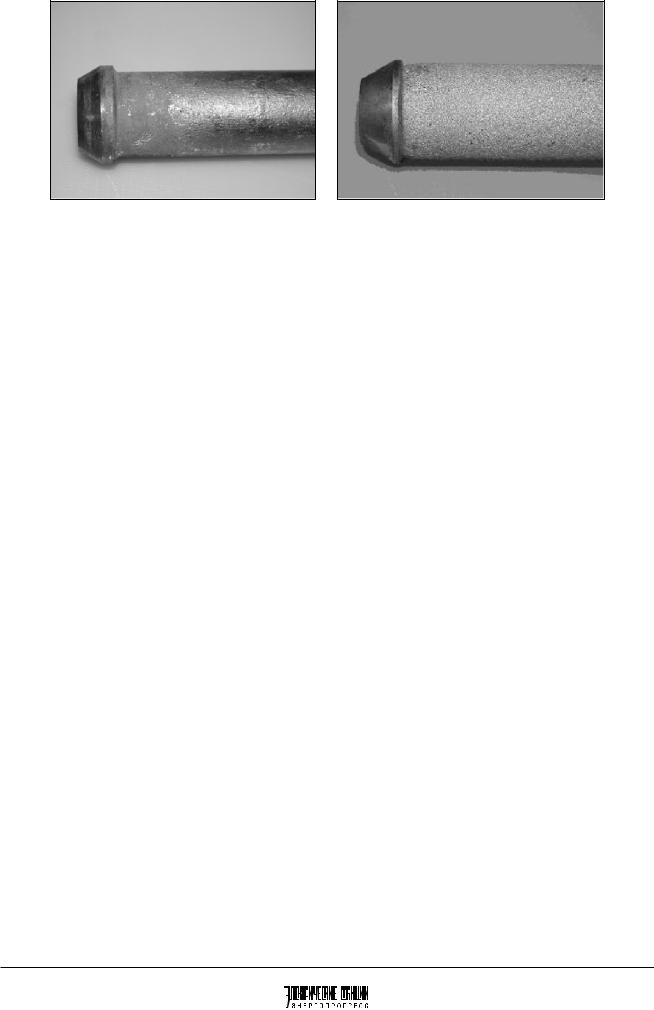
à) á)
& 4 . 0 , , . 0
на облопаченном роторе непосредственно на турбоагрегате без вскрытия крышки цилиндра че- рез конденсатор;
на облопаченном роторе непосредственно на турбоагрегате при вскрытой крышке цилиндра;
на облопаченном роторе, находящемся на опорах на ремонтной площадке;
на новых или демонтированных лопатках в условиях мастерской.
К настоящему времени технология ЭИЛ реализована на 24 ступенях турбоагрегатов ст. ¹ 1 – 6. При этом восстановлена живучесть свыше 2400 лопаток. Из них семь ступеней (670 лопаток) – дважды, одна ступень (96 лопаток) – трижды. В условиях мастерской упрочнено пять новых комплектов и восстановлено более 150 демонтированных лопаток, в том числе, на облопаченном роторе непосредственно на турбоагрегате без вскрытия крышки цилиндра через конденсатор – две ступени (192 лопатки).
Кроме лопаток последних ступеней, ЭИЛ-по- крытия нанесены в отдельных случаях при обнаружении промывов также на лопатки регулирующей ступени высокого давления и 13-й ступени низкого давления.
Преимущества метода электроискрового легирования: отсутствие нагрева материала лопаток; формирование слоя до 0,25 мм; локальность нанесения покрытия на любом протяжении входной и выходной кромок; мобильность оборудования за счет небольших габаритов (600 400 200 мм) и массы (до 15 кг); высокая производительность (до 15 лопаток в смену); оперативная обучаемость персонала технологическим приемам и навыкам.
Применение защитно-упрочняющих покрытий методом электроискрового легирования обеспечи-
вает уменьшение средней скорости износа лопаток почти в 2 раза за период до следующего ремонта (восстановления защитного слоя).
На Рязанской ГРЭС освоена технология газопламенного нанесения защитно-упрочняющих покрытий. Газопламенное напыление является одним из способов обработки поверхности материалов (ðèñ. 3). Основное назначение напыления – защита от коррозии различных конструкций, изношенных поверхностей деталей машин и инструмента. Напылением можно наносить покрытия с самыми различными свойствами (теплостойкие, теплоизоляционные, износостойкие, кор- розионно-стойкие, электроизоляционные и др.).
На Рязанской ГРЭС проведены работы по восстановлению сальниковых рубашек бустерных насосов. Ранее вместо изношенных покупались новые или рубашки изготавливались в механическом цехе. Как показал опыт эксплуатации бустерных насосов, сальниковые рубашки выходят из строя через 6 – 7 мес и их приходится заменять. Восстановленные методом напыления эти детали эксплуатировались 8 мес. Кроме этого, газопламенным способом упрочняются: штоки арматуры, сальниковые рубашки насосов, шейки валов, посадочные места уплотнителъных колец клапанов и др. Восстановлено и передано для установки на рабочее оборудование более 160 деталей семи наименований.
Основной особенностью технологии является более прочное (в 3 – 5 раз) сцепление покрытия с основным металлом.
Использование рассмотренных в статье методов диагностики и восстановления деталей позволило повысить надежность ответственного оборудования ГРЭС и уменьшить ремонтные расходы.
18 |
2003, ¹ 12 |

Сетевые компьютерные тренажеры для подготовки операторов энергоблоков 260 МВт Рязанской ГРЭС
Гурылев О. Ю., èíæ.
Рязанская ГРЭС
По данным ОРГРЭС суммарная мощность турбинного оборудования, исчерпавшего свой парковый ресурс, к 2005 г. достигнет 46,3% установленной мощности Центрэнерго, а к 2010 г. увеличится до 58,6%. Для обеспечения энергетической безопасности Центрального региона России в рассматриваемый период реализуется техническая политика продления паркового ресурса оборудования ТЭС. Прежде всего, это касается мощных конденсационных блоков ГРЭС. Продлен парковый ресурс оборудования: Конаковской ГРЭС (8 300 МВт), Костромской ГРЭС (4 300 МВт), Черепетской (4 140 МВт), Каширской ГРЭС (3 300 МВт), Щекинской ГРЭС (2 200 МВт).
Продление паркового ресурса достигается в результате комплекса работ по реконструкции и замене оборудования, диагностике его остаточного ресурса, внедрению нового поколения АСУ ТП, повышению качества обучения и натренированности оперативного персонала.
В документах РАО “ЕЭС России” отмечается высокая доля вины оперативного персонала, особенно персонала котлотурбинных цехов, в авариях, повреждениях оборудования, технологических нарушениях. Доля аварий по вине персонала на современном этапе развития энергетики по некоторым оценкам составляет от 15 до 40%, а нарушений в работе по вине персонала – от 25 до 80%.
Повышение качества обучения и натренированности оперативного персонала, постоянное поддержание его профессиональных навыков на высоком уровне обеспечивают резкое снижение отказов и аварий по его вине.
Существующая система непрерывной подготовки, переподготовки и повышения квалификации персонала энергопредприятий регламентируется руководящими документами электроэнергетической отрасли (РД 34). Однако ряд из них вследствие структурных изменений в отрасли явно устарел. Это не позволяет энергопредприятиям перейти на качественно новый уровень организации подготовки персонала средствами новых информационных технологий путем создания собственного структурного подразделения – учебнотренировочного пункта (УТП).
Сегодня в этом направлении значительных успехов достигли отечественные АЭС, которые в период постановки их под контроль МАГАТЭ (Международное агентство по атомной энергии)
были вынуждены в кратчайшие сроки создать собственные УТП или УТЦ (учебно-тренировочный пункт, центр) в качестве самостоятельных структурных подразделений, укомплектовать их штатом инструкторов и методистов из числа высококвалифицированных специалистов, активно внедрять новейшие информационные технологии. В настоящее время при каждой АЭС функционирует на постоянной основе УТП или УТЦ, выполняя весь непрерывный цикл работы с персоналом: отбор, обу- чение, специальную подготовку, переподготовку, повышение квалификации, аттестацию.
Очевидно, что для ТЭС также необходимо создание собственных УТП. УТП как самостоятельное структурное подразделение обеспечит выполнение требований руководящих документов в части подготовки персонала. Внедрение компьютерных технологий позволит приблизить процесс получения знаний, навыков и умений к реальному рабочему месту оператора.
Ï |
|
Ï |
|
Ò |
|
Ñ |
|
Ñ |
|
Ò |
|
Ï |
Ï |
|||||||
|
|
|
|
|
|
|
|
|
|
|
|
|
|
|
|
|
|
|
|
|
|
|
|
|
|
|
|
|
|
|
|
|
|
|
|
|
|
|
|
|
|
Ì Ì |
Ì Ì |
|
|
|
|
|
||||||||
|
|
|
|
|
|
|
|
|
|
|
|
|
|
|
ÑÏÎ |
|
|
|
|
|
|
ÑÏÎ |
|
||||||
|
|
|
|
|
|
|
|
|
|
|
|
|
|
|
|
|
|
|
|
|
|
|
|
|
|
|
|
|
|
|
|
|
|
|
|
|
|
|
|
|
|
|
|
|
|
|
|
|
|
|
|
|
|
|
|
|
|
|
|
|
ÏÓ |
|
ÏÓ |
|
|
|
|
|
|
|
||||
|
|
|
|
|
|
|
|
|
|
|
|
|
|
|
(ÐÌ ÌÝÁê) |
|
(ÐÌ ÌÝÁò) |
|
|
||||||||||
|
|
|
|
|
|
|
|
|
|
|
|
|||
|
|
|
|
|
|
ÀÐÌ |
Ïð |
|||||||
|
|
|
|
|
|
|
|
|
|
|
|
|
|
|
|
|
|
|
|
|
|
|
|
|
|
|
|
|
|
! ( , 5 , - , "
5 ' %
Ï – приборы; Ò – тренды; Ñ – табло сигнализации; Ì – мнемосхемы; ÑÏÎ – система поддержки оператора; ÏÓ – пульт управления; ÀÐÌ – автоматизированное рабочее место инструктора; Ïð – принтер
2003, ¹ 12 |
19 |

6 7 8 9 : 7; ,
Следует отметить, что оперативный персонал крайне заинтересован в компьютеризации процесса собственной подготовки, прежде всего, по таким направлениям:
обучение на должность; проверка знаний; противоаварийная подготовка;
оперативное информационное обеспечение. Наиболее эффективным средством подготовки
оперативного персонала энергопредприятий, с точки зрения комплексного приобретения знаний, навыков и умений, являются тренажерные системы. В настоящее время доминирует подход, предполагающий проведение противоаварийных тренировок с помощью компьютерных тренажерных систем (КТС). Классификационный анализ существующих КТС по методам математического моделирования управляемого технологического процесса и форме имитации рабочего места оператора позволяет выделить три основных направления развития компьютерных тренажеров:
полномасштабные функционально-аналитиче- ские тренажеры (ФАТ);
локальные (участковые) ФАТ; логические тренажеры (ЛТ).
Полномасштабные ФАТ функционально предназначены для обучения и тренировки оперативного персонала в составе смены (с участием персонала различных цехов) ведению режимов пусковых, нормальных и с отклонениями.
Локальные ФАТ прежде всего имеют целью отработку действий оператора при управлении отдельными технологическими системами.
Логические тренажеры предполагают обуче- ние и тренировку последовательности выполнения операций определенной оперативной задачи.
С 2002 г. на Рязанской ГРЭС для целей подготовки оперативного персонала активно разрабатываются и внедряются перечисленные КТС.
За прототип взят пылеугольный блок 260 МВт [котлоагрегат Пп-990/255 (П-59)], турбина К-300-240 ЛМЗ, поверхностные ПНД, деаэратор на 7 кгс/см2, РОУ 255/40, схема пылеприготовления прямого вдувания с молотковыми мельницами типа ММТ и инерционными сепараторами, топливо: бурый уголь (мазут, газ).
На основании принципа декомпозиции прямоточный котельный агрегат СКД типа П-59 с нали- чием вспомогательных технологических систем, обеспечивающих его нормальное функционирование во всех эксплуатационных режимах, рассматривается как совокупность моделей процессов, аппаратов, механизмов, систем, взаимосвязанных по каналам поступления внешних управляющих воздействий, внешних и внутренних возмущений. С этих позиций котлоагрегат представляет следующую совокупность взаимосвязанных математиче- ских моделей в виде отдельных программных модулей, описывающих:
топочные процессы; состояние газовоздушного тракта;
гидродинамику и теплообмен рабочей среды по тракту котлоагрегата;
питание топливом (газовое кольцо, мазутное кольцо, паровое кольцо, пылеугольный тракт);
состояние растопочного узла в режимах пуска; положение запорно-регулирующей и предохра-
нительной арматуры; управление арматурой, агрегатами и механиз-
мами; срабатывание сигнализации, блокировок, защит.
Особенностью рассматриваемой модели котлоагрегата является моделирование его состояния во всех режимах работы не как отдельно выделенного объекта численного исследования, а как неразрывной части управляемых технологических процессов энергоблока единой динамической системы.
20 |
2003, ¹ 12 |

Базовый вариант КТ (ðèñ. 1) предусматривает два рабочих места обучаемых для подготовки машинистов энергоблока по котлу (ÌÝÁê ) и по турбине (ÌÝÁò ).
Тренажер рассчитан для работы в локальной или корпоративной сети ТЭС под управлением Windows 98 или Windows 2000 в одноранговой сети Microsoft.
Для имитации структуры блочного щита управления конфигурация тренажера предусматривает оптимально пять-восемь мониторов для размещения моторных и информационных полей на одном рабочем месте подготавливаемого оператора (органы управления – один; схемы – один, два; приборы контроля – один, два; сигнализация
– один; тренды – один). В состав тренажера входит выделенное автоматизированное рабочее место (АРМ) инструктора тренировки.
В объем моделирования компьютерного тренажера входят: технологические схемы и оборудование блока; система контроля и управления; система защит и блокировок оборудования; перечень режимов нормальной эксплуатации; перечень нарушений и отказов в работе оборудования блока; пределы моделирования; удаленное автоматизированное рабочее место (АРМ) инструктора для подготовки, управления и протоколирования результатов тренировки.
Перечень моделируемых режимов нормальной эксплуатации предусматривает:
пуски из любого теплового состояния; нагружение и разгружение блока во всем энер-
гетическом диапазоне его работы; останов блока с расхолаживанием и без расхо-
лаживания турбины.
Пределы моделирования тренажера включают: выполнение подготовительных, пусковых и остановочных операций; ручное, дистанционное и автоматическое управление оборудованием в нормальных, с отклонениями и аварийных режимах работы блока в соответствии с положениями инструкции по эксплуатации энергоблока-прототипа.
Íà ðèñ. 2 изображены фрагменты оконного меню АРМ инструктора для задания нарушений и отказов в работе регулирующих клапанов.
Перспективы развития и становления имитационного математического моделирования всережимной динамики сложных управляемых технологических систем в аспекте разработки КТС открывают пути для создания и внедрения на передовых энергопредприятиях интеллектуальных информационных динамических систем реального времени в общеблочной постановке задачи для целей оптимального управления, диагностики, экспертного оценивания, прогнозирования, планирования и поддержки принятия решений.
2003, ¹ 12 |
21 |