
Ceramic Technology and Processing, King
.pdfSlip Preparation Procedures 113
Storage of coarse-grained slips is done by rolling, but unlike their fine grained counterparts, there is a top speed above which the slip will set up. Settling is a major problem for coarse-grained slips, not so much in storing as in slip casting. One can reduce settling by either increasing the slip viscosity with polymers or inorganic colloids such as hectorite or by speeding the casting rate. Pressure casting is a very good idea for these slips.
Check List, Slip Conditioning and Storage
Observe the following factors for slip conditioning and storage:
•Adsorption/desorption equilibration
•Filtering
•De-airing
•Slip sorage
•Particle packing
•Slip rolling and solids content increase
•Rolling in storage
•Settling out of coarse particles Increase viscosity Pressure casting
REFERENCES
1.Fred F. Lange, "Powder Processing Science and Technology for Increased Reliability." J. Am. Ceram. Soc. 72 [1], 3-15, 1989.
2.Greenleaf, J. Personal Communication.
3.Anne Bagley Hardy, Wendel E. Rhine, and H. Kent Bowen, "Preparation of Spherical, Submicrometer Oxide Particles by Hydrolysis of Emulsified Alkoxide Droplets." J. Am. Ceram. Soc. 76 [1], 97-104, 1993.
4.K. S. Venkataraman, "Predicting the Size Distributions of Fine Powders During Comminution," Advanced Ceramic Materials, 3 [5], 1988.
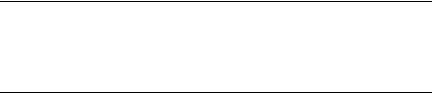
5
Mixing Coarse Grained
Materials
1.0 MIXING CONSIDERATIONS
Whenever one uses a coarse mix for extrusion, pressing, or ramming, it is not always made up as a slip. Usually, it is mixed dry or semi-dry in a mixer or blender. Perhaps, the primary distinction between mixing equipment is the intensity of mixing. Current practice is toward higher intensity mixing. The other requirements include uniformly mixing all of the batch, recovery of the mix, and cleanup.
The impeller is generally thought to do the mixing by impact with the grain. While there is some of this, autogenous impact between the particles themselves may be the primary deagglomerating process in the fines. The impeller establishes shear in the mix which invigorates the grain. In turn, the grain particles impinge upon each other and do most of the work. It can be looked at as a miniature sand mill where the coarse particles themselves are the media deagglomerating the fines. The purpose of mixing is to generate a uniform distribution of particles of different size, shape, and density. One should review the extensive literature available on this subject to consider the possible variables. One can start by reading papers on the grading of aggregates by Furnas and Anderegg. These papers and other literature address the ratios of the volume fraction of each constituent for obtaining the highest density, which is usually the objective unless the ceramic is for a permeable application. Figure 4.29 shows the general
114
Mixing Coarse Grained Materials 115
location of highest density for three sizes of particles. Design your experiment around this region in the diagram. Dry mixing and wet mixing will be discussed.
2.0 DRY MIXING AND EQUIPMENT
It is easier to handle ceramic mixes when they are dry or damp as wet mixes stick to everything. One uses dry mixes for the following applications: mixing ingredients for calcination to form a different phase such as with a ceramic pigment, pressing to form a shape with refractories being a common application, and ramming where the shape is unusual such as in a foundry induction furnace lining or for a long coarse-grained tube or rod. Large SiC resistors and long tubes can be end-rammed tamped.
Making a uniform mix is difficult in at least two ways. Coarse or dense grains will easily segregate into coarse, fine, light, or heavy fractions. It is very difficult to minimize these tendencies. Secondly, it is difficult to determine if segregations are present in the mix. Extreme cases are visually apparent, but too often one cannot tell by casual observation. This is further discussed in a following section on mix uniformity.
There are five types of dry mixers: high intensity, mullers, sigma blade, V blenders, and ribbon blenders.
High Intensity Mixers
Perhaps best known is the Eirich type of mixer. There are a few variations, but the one with a high-speed, vertical-shaft impeller and plow blades is most common. The mixer has a rotating pan tipped up from the horizontal. The impeller is parallel to the shaft axis and has a head with impeller blades. These blades can be cemented carbide for wear resistance. There is also a plow blade that is stationary, helping to distribute the mix. The shaft housing and the plow support are fastened to the lid. This mixing action is unique in regards to distribution of the material during mixing. This is illustrated in Figure 5.1.
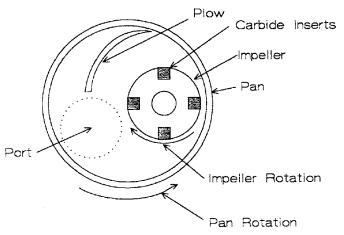
116 Ceramic Technology and Processing
Figure 5.1: High Intensity Mixer Drawing. The flow of material is back into the mixing head.
In this situation, the mixing process is thorough. The impeller rotates at a high speed, the plow moves the mix back into the center of the drum, and the drum counter rotation eliminates any dead spots where the mix is stationary. Another advantage is that the seals and bearings are up out of the mix, thus extending their productive use.
Figure 5.2 depicts a commercially available high intensity mixer (Courtesy Eirich). The mixer is tilted to cause the mix to cascade back into the mixing impellers. This mixer has two speeds by changing pulley combinations. A continuously variable speed control would be preferable.
As was stated earlier, the coarse particles themselves do much of the fines deagglomeration. Visualize what happens in the shear zone as mixing occurs. A schematic is illustrated in Figure 5.3. Particle impingement in a shear field deagglomerates the fines.
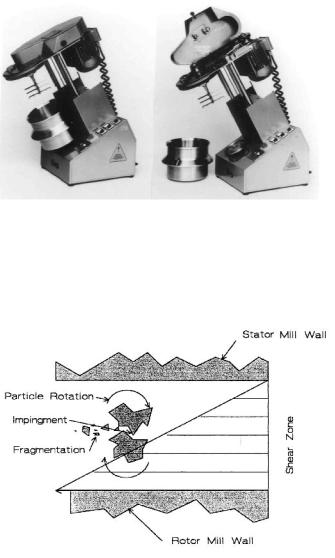
Mixing Coarse Grained Materials 117
Figure 5.2: High Intensity Mixer. Speed variation by the choice of pulleys.
Figure 5.3: Deagglomeration by Shear.
118 Ceramic Technology and Processing
A velocity gradient persists across the shear zone, causing the agglomerated particles to rotate. In Figure 5.3, the two large particles are rotating in the same direction, but their surfaces are impinging in opposite directions with the contact velocity doubled. Impact between particles can result in grinding. Large particles will have more energy and will be rotating at a higher velocity than the fine particles. Consequently, the fines are ground up by the coarse aggregate. Then, whenever the mix contains coarse material, the fines will be ground quicker than if the larger particles were not present. This all makes the grinding time a function of particle size. Coarse particles act as grinding media in the mixer. A similar mechanism also occurs in fluid slips.1
Mullers
Mullers have been used successfully for a very long time. They can be used for grinding and mixing depending on the hardness of the material and the weight of the muller wheels. A softer material like wheat is ground to flour with mullers. A harder material like SiC is mulled to knock off the sharp edges.
Muller wheels can be massive. For ceramics applications, they are usually iron as the weight helps to mix and grind the batch. In agriculture, the wheels traditionally are stone hewed out of massive blocks. When iron contamination is not tolerable, one can also use stone wheels for ceramic applications. The pan rotates counter to the two wheels, with the plow shepherding the batch into the grinding zone. The wheels also rotate on their own axis resulting in a shearing zone between the pan and the wheel surface. This wheel assembly rotates about the pan axis. Since the outermost part of the muller wheel is set out farther than the part nearer the pan axis, it moves faster and the mix is smeared as it is mulled. It is the shearing effect, primarily, which does the deagglomeration of the fines in the batch. It is not so much the purpose of the muller to grind up the coarse grog here, however the muller deagglomerates the fines and homogenizes the mix. Figure 5.4 depicts a sketch of a muller.

Mixing Coarse Grained Materials 119
Figure 5.4: Muller Mechanism Drawing. Shear between the wheels and pan base deagglomerates the particles.
Mullers have a bottom port that can be opened to discharge the mix, with the plow forcing the mix into the port. Bearings are out of the abrasive mix, making the equipment durable. Clean up is easy as the pan can be hosed down, with the water exiting out of the port. Mullers are useful and will probably be used at least for a few more millennia. A commercial lab-sized muller is shown in Figure 5.5. The muller wheels and side can be removed for easy cleaning.

120 Ceramic Technology and Processing
Figure 5.5: Laboratory Muller (courtesy of Simpson Mix-Muller).
Sigma Blade Mixers
This type of mixer is a trough with two sigma-shaped arms that rotate to blend the mix. One can use either pug or sigma blades, but they are not interchangeable without dismantling the mixer. Sigma, named after the Greek letter, is shaped like the letter S. Two blades intertwine while rotating, resulting in a moderate shearing intensity and homogenization. The trough tips to dump the batch providing for easy clean up. The seals and bearings are in the batch during mixing, requiring maintenance. In this mixer, the shearing effect is not intense enough for fine-grained batches, but one can satisfactorily mix relatively coarse mixes.

Mixing Coarse Grained Materials 121
V Blenders
This equipment consists of two cylindrical sections joined together to make a V shape as shown in Figure 5.6.
Figure 5.6: V Blender. Unequal volumes on the two sides help to cross blend. The intensifier bar aids in deagglomeration and is used to add binder solutions.
The entire assembly revolves around the axis, tumbling the mix repeatedly from the base to the top of the cylinders. When the capacity of the two cylinders is different, there is transfer of material from one side to the other, as suggested in Figure 5.6. There is the option of adding an intensifier bar that also rotates on the axis but at a much higher speed. The bar increases the shearing effect in the mixer; it also has a central channel for adding a liquid, such as a binder solution. This is a very useful feature, as the batch can be blended dry before adding the binder. Being able to observe the mix consistency during addition of the binder solution takes some of the guess work out of just how much to add to obtain the desired consistency. Too little binder solution and it will not press properly. Too much binder solution and the mix will coat the sides creating a compromised batch and a cleanup problem.
122 Ceramic Technology and Processing
Ribbon Blender
Like the sigma blade mixer, ribbon blenders are horizontal troughs with a small number (about three) of helical blades that rotate around the trough axis. Like the sigma blade, the trough tips to dump the batch. Mixing is gentle, making ribbon blenders useful for premixing batches or for calcining mixes.
How well is the batch mixed? There is a quick way to tell when the materials are of a different color. Pour a little of the mix onto a piece of white paper and run one's finger across it. Colored streaks reveal that the agglomerates have not been broken down. At most, this is undesirable and one should either mix longer, mix at a higher speed, or mix with a higher intensity mixer.
3.0 WET MIXING AND EQUIPMENT
Wet mixing is used where the material has to flow during the forming process. Dry mixes have very little flow. Wet mixes are plastic similar to modeling clay. Examples are extruded parts such as coarsegrained tubes and deep-crucible shapes where the mix has to flow up the sides of the mold to fill the cavity, a mud pressing process.
Two types of wet mixers will be discussed: pug mills and extruders. Both have a horizontal axis mixing arm with blades in the pug mill and a screw in the extruder. In both cases, the mix is forced down the length of the mixer as the mixing arm rotates. Consequently, one batches the mixes in a separate apparatus to feed a homogeneous mix into the mixer. In the polymer literature, there is extensive material on the topic of extrusion. The difference being that the volume per cent of solids is much lower and the molten polymer dominates the rheology. Additionally, the polymer remains in the finished article while with ceramics it is burned out. Still one might want to refer to these references.1,2