
Ceramic Technology and Processing, King
.pdfMilling and Equipment 33
Specific Gravity
The specific gravity of the media dictates the energy in the mill. High density mill balls have more energy because of their mass. Table 3.1 gives the specific gravity of commonly used materials.
Table 3.1: Specific Gravity of Commonly Used Materials
Material |
Specific Gravity g/ml |
|
|
WC/Co |
13.0 - 15.0 |
|
|
Iron |
7.8 |
|
|
TZP |
± 6.2 |
|
|
Zircon |
4.7 |
|
|
Alumina |
3.98 |
|
|
Silicon Carbide/ Silicon Nitride |
3.21/3.18 |
|
|
Porcelain |
± 2.7 |
|
|
Flint |
± 2.62 |
|
|
Media Wear
Wear tests can be done by placing a specific number of specimens
(6) in a small jar mill with a 3 mm TZP media. These specimens are about the same size as the TZP media, but they vary in shape from spheres to cubes depending on what is available. The data that follows is based on two slips: A-16 sg alumina and 600 grit Silicon Carbide (SiC). After each run, the specimens were picked out with tweezers, washed, dried, and weighed. Each type of media in the test was identifiable by its color, shape, or size. As many as 8 types of grinding media can be run together and a fresh slip was used for each cycle. Table 3.2 summarizes the ceramic material and
34 Ceramic Technology and Processing
slips that will be shown in greater detail in Figures 3.4 to 3.9.
Table 3.2: Ceramic Material vs Slips Used
Figure |
Ceramic Material |
Slip |
|
|
|
3.4 |
Aluminas |
A-16 |
|
|
|
3.5 |
Zirconias |
A-16 |
|
|
|
3.6 |
Silicon Carbide & Silicon Nitride |
A-16 |
|
|
|
3.7 |
Aluminas |
SiC |
|
|
|
3.8 |
Zirconias |
SiC |
|
|
|
3.9 |
Silicon Carbide & Silicon Nitride |
SiC |
|
|
|
The experimental data is presented in Figures 3.4 to 3.9. Each of these figures will be discussed in relation to the different sources of materials and in relation to each other.
In Figure 3.4, four sources of alumina grinding media were tested with the A-16 sg slip. Sample one is 99.99% alumina, fully dense, and with a 2 μm grain size. Sample two is 85% alumina; a conventional grinding media. Sample three is a well crafted, high density media from Japan. Sample four is 99.9% alumina, fully dense, and with a 3 μm grain size.
In this slip, three of the materials were worn essentially at the same rate. Sample one was exceptional with half the wear rate compared with the other materials. This is attributable to its high purity, density, and fine grain size.

Milling and Equipment 35
Figure 3.4: Wear-Aluminas, A-16 sg Slip
Figure 3.5 shows data for zirconia ceramics in A-16 sg slip. Samples one and two are TZP materials with 3 m/o Y2O3. Sample three is a magnesia stabilized zirconia with about 3.5 m/o MgO. This material is substantially less wear resistant than the TZP media. There is a large difference in wear rates for the TZP ceramics and since these materials are so expensive, it would be a good idea to run a test before a selection is made. Sample two is a much better buy than sample one; it is also less contaminating.
Zirconia does not necessarily outperform alumina as there are other factors such as microstructure that have to be considered. Wear results on both ceramics show that actual tests have to be done before wear characteristics can be predicted.
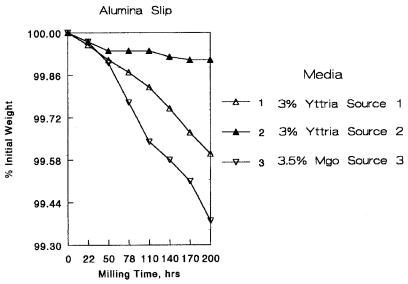
36 Ceramic Technology and Processing
Figure 3.5: Wear-Zirconias, A-16 sg Slip
Figure 3.6 displays data with the Silicon Carbide (SiC) and Silicon Nitride (Si3N4) media in the alumina slip. Silicon Carbide does not show any detectable wear. The initial drop is probably due to a small chip that broke off the satellite sphere edge. Silicon nitride shows an initial, no-wear zone before it starts to wear at a slow rate. (The figures are at different scales, so it is necessary to read the values on the ordinate.) It seems that a tough skin on silicon nitride prevents initial wear. This seems real as there are four data points, each of which is the weight loss (none) of six samples.
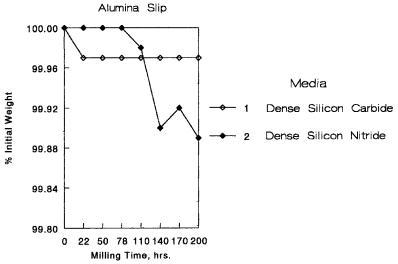
Milling and Equipment 37
Figure 3.6: Wear-Silicon Carbide/Silicon Nitride, A-16 sg Slip
Figures 3.7 to 3.9 display data for the above ceramics but in a silicon carbide slip.
Figure 3.7 displays the data for alumina ceramics. Three of these ceramics behaved in a similar fashion, wearing at a higher rate in the SiC slip as expected. The other alumina, the 85% material, wears at a much higher rate than the others. This is comparable to the alumina slip and suggests a change in the wear mechanism..

38 Ceramic Technology and Processing
Figure 3.7: Wear-Aluminas, Silicon Carbide Slip
Zirconia media wear results are shown in Figure 3.8. Sample three is the magnesia stabilized zirconia; it performed poorly in both slips. TZP ceramics held up very well even though the hardness of SiC in the slip is much higher than that of zirconia. Amazingly, the two TZP ceramics acted differently in the alumina slip, but acted in a similar fashion in the SiC slip.

Milling and Equipment 39
Figure 3.8: Wear-Zirconias, Silicon Carbide Slip
Figure 3.9 displays the data for both the SiC and Si3N4 media in the SiC slip. Again, SiC did not show detectable wear; this is surprising as the slip particles are of the same hardness. However, Si3N4 showed a normal wear pattern without the initial no-wear zone seen in the alumina slip results. While this is perplexing, one can at least measure the wear rates to select the grinding media. This type of test can be scaled up and is commonly used on larger media.

40 Ceramic Technology and Processing
Figure 3.9: Wear-Silicon Carbide/Silicon Nitride, SiC Slip
The wear rate is a function of media size. Smaller diameter media wear faster than larger diameter media. Figure 3.10 shows data on the TZP media in the SiC slip (from the TOSOH manufacturer).
The curves are linear with milling time. There does not seem to be a quantitative relationship between the wear rate and the media diameter in this test. There are other factors other than surface area or mass that should be considered here.

Milling and Equipment 41
Figure 3.10: Wear of TZP vs Media Diameter
Data using commercial spherical grinding media of the modified fused zircon is shown in Figure 3.11(Courtesy of SEPR). This material has the advantage of being cheap relative to other higher purity types. It is also durable in many applications when compared to those of severe attrition. The microstructure is of interest as it suggests a reason for the good wear resistance.

42 Ceramic Technology and Processing
Figure 3.11: SEPR Beads (Courtesy of SEPR)
The microstructure of the SEPR beads is shown in Figure 3.12. Zirconia dendrites are seen in the microstructure radiating out from central sources. The matrix is a glass with silica and other constituents added during manufacture.
The TZP media is much more wear resistant under highly innocuous conditions. This media has a pearly luster due to a fully dense microstructure and a very high index of refraction. When this happens, the wear mechanism is on a molecular scale producing the high polish. This polish is retained on the media surfaces. These TOSOH beads are shown in Figure 3.13 (Courtesy of TOSOH).