
Ceramic Technology and Processing, King
.pdfMixing Coarse Grained Materials 123
Pug Mills
The mill is a trough with a horizontal mixing arm with angled blades that shear the mix and move it from one end to the other. Since the mix is viscous, the arm is massive and driven by a high horsepower gear reduction drive to withstand the stresses. The rotational speed and viscosity of the mix govern the mixing intensity. Speed is limited by the stresses imposed on the apparatus, so most of the mixing is a consequence of the high viscosity. One uses pug mills to prepare a mix for extrusion as preliminary blending is often necessary.
Extruders
Auger Extruders
An auger extruder is similar to a meat grinder for making hamburger meat in a butcher's shop. It has an entry port feeding the mix down into the auger where it is mixed and extruded out of a die. A laboratory auger extruder is shown in Figure 5.7.
Wear is intensive and the barrels often have replaceable liners. Both augers and blades can be coated with a wear-resistant material. Figure 5.7 depicts an extruder with a variety of features. One feeds the mix from the right side into the hopper where an auger forces it into a rotating cutter. The function of the cutter is to shred the mix and to remove the entrained air in a vacuum. It is necessary to feed fast enough to maintain the vacuum in the machine. After shredding and deairing, the mix is dropped into a second auger that mixes and compresses the mix into a solid mass. The mass is then forced through a die with a size and shape as selected. The size of the die has to be appropriate with the feed rate, since if it is too small the machine will overload. A useful feature of this extruder is that the working parts are fastened to the base with toggle clamps for quick change and cleanup between mix compositions.

124 Ceramic Technology and Processing
Figure 5.7: Laboratory Extruder. The extruder has a port for adding material, a chopper in a vacuum chamber, and a die. (Courtesy of Fate International).
Wire/Knife Cutting. The extrusion is usually wire cut to length. Wear on the wire is severe and breakage can be a serious problem as it shuts the process down. This can be avoided by slowly feeding the wire from a spool, through a tensioning device, and onto a take-up spool. In this fashion, fresh wire is continuously supplied to the cutter.
Mixing efficiency. Not all of the mix receives the same amount of shear in an extruder. Material next to the wall of the barrel is not mixed as intensely as material in the middle of the flight. There can even be dead areas where the mix is stationary. Since mixing is not uniform, the extruded piece is not uniform in green density or in breaking up of agglomerates. There are many extrusion problems almost all of which are attributable to poor mixing. This
Mixing Coarse Grained Materials 125
subject will be expanded in a later section in this chapter. The following can be done in case of an extrusion:
•send the extrusion back for a second and/or third pass,
•premix in another apparatus,
•increase the shearing effect by using a multi-orifice die with small openings for preliminary mixing, or
•change the viscosity of the mix.
Ram Extruders
A second type of extruder uses a hydraulic cylinder rather than an auger to force the mix through the die. One supplies the mix to the ram extruder as a premixed cylinder that drops into place in the barrel, as ram extruders do not mix the material. This will be discussed in greater detail in the chapter on forming. One can set up ram extruders with two barrels that alternately rotate in place, making the process almost continuous.
Hydraulic ram extruders supply material at a constant rate. Cutters can be time controlled. Another way to control the cut is with a fiber-optic sensor and an actuator, such as a solenoid connected to a wire cutter. Tolerance on the length of cut can be as precise as 0.005 inches.
Combinations of equipment
These combinations have been alluded to in the previous discussion. A mixer, pug mill, and extruder can be coupled into a lab process line. This is not at all uncommon and is often necessary. Most lab work, however, is not
that structured, and mixes are often carried from one piece of equipment to another. Figure 5.8 is a schematic of a combination process line.

126 Ceramic Technology and Processing
Figure 5.8: Mixing Process Line. Mixing is often done in three steps: mulling, pug milling, and extruding with deairing.
The material is batched in the muller, then transferred to the pug mill. The function of the muller is to distribute the mix ingredients uniformly on an overall scale and deagglomerate the fines. All of the ingredients are batched in the muller and mixed as a batch. This function can also be done in a pug mill if the port emptying the mill is closed. In this case, there is very little linear transfer of material. The function of the pug mill is to homogenize the material by shear and to provide a more uniform batch to the extruder. The extruder sketch shown has two compartments. The first is to introduce the material into the extruder and force it into the chopper. A vacuum is pulled in the chopper chamber to remove entrained air. (Chopping exposes the air pockets to the vacuum.) Then, the chopped mix is dropped into the extruder auger, where it is intensively sheared and mixed. Auger flights move the material to the extrusion die under pressure; this compacts the mix and forms it into the die configuration. It is not uncommon to use only the muller and extruder for processing. When more mixing is needed, the pug mill can be put into the line.
Special Purpose Mixers
Many other type of mixers are available other than those discussed. One of these is a closed, vacuum-tight chamber with a jacket for either heating or cooling. Figure 5.9 is a lab-sized mixer of this type.

Mixing Coarse Grained Materials 127
Figure 5.9: Special Purpose Mixer. This mixer provides heat for melting binders and vacuum for deairing. (Courtesy of Ross and sons).
One ceramic application for this mixer is to make up flowable mixes for wax injection. The mixer can be evacuated to remove entrained air and is then heated to melt the wax.
Check List, Mixers
The following is a check list for mixers.
•Amount of Shear: high intensity, mullers, sigma blade, V blenders, ribbon blenders.
•Effect of Coarse Grog on Blending
•Plastic Mixers:
Pug mills
Extruders, shaping
128Ceramic Technology and Processing
•Mixing Lines
•Dry(damp) Mixers:
High intensity
Mullers
Sigma blade
Ribbon
•Special Purpose
4.0MIX UNIFORMITY
Coarse-grained mixes will have a large range of particle sizes, from very coarse grog to fines. These will tend to segregate, altering the local mix composition. Almost anything will cause the particles to segregate. They will segregate even when standing in a silo. Proper mixing is to obtain uniformity and to retain it during handling and die filling. The objective of this section is to discuss forces that cause coarse and fine particles to separate during processing and ways to retain that homogeneous mixture.
Segregation of Particles
Gravity
Consider three cases where the coarse-grain pack is mixed with a slip containing the fines: when the coarse-grain pack has a greater volume than the fines, when they are equal, and when the coarse-grain pack has a lesser volume than the fines. Figure 5.10 shows this schematically.

Mixing Coarse Grained Materials 129
Figure 5.10: Volumetric Grain Packing. Just enough fine material is required to fill the interstices in the grain pack in case 2.
In illustration 1, the coarse pack fills the volume while the fines do not. When the fill is vibrated, the fines will settle and sift down to the bottom of the cavity and segregate. A body such as this is not uniform and will sinter denser at the base than at the top. The base will be stronger and will have a higher modulus. Coarse packs of the grains will form in every case if the grains are free to move. These coarse packs do not sinter because of the low surface area. In case 2, both the coarse and fines fill the volume and the density is homogeneous; this material will tend to sinter uniformly. In case 3, there are excess fines, and the coarse material will sink to the bottom and segregate. The illustration is also valid for a slip mixture.
These effects are due to the size distribution in a gravitational field. Particles can also segregate by another mechanism - shear. In a fluid shear field, the coarse particles will preferentially drift to the zone of highest velocity. This is the basis for particle size classifiers such as air or liquid cyclone classifiers. Shear occurs in all mixers. In this case involving coarse grained mixes that are semi-dry, segregation still occurs.
130 Ceramic Technology and Processing
Visualize what is occurring in a mixer. Some sort of impeller is shearing the mix. The coarse grain impinges upon the fine agglomerates and breaks them up. When the mix binder is present in the right quantity including an appropriate level of stickiness, the fines can adhere to the coarse particles in tending to restrain segregation. This will work if the shearing intensity is not so high that it breaks them up again. One way to mix the material is to mix dry at a high intensity to break up the soft agglomerates in the fines and then to slowly add the binder solution at a lower intensity of the impeller. To minimize clumping, the solution can be sprayed into the mix with low intensity mixing. The objective is to pelletize the mix with uniform pellets all of which have the right grain size distribution. The process in all cases for determining uniformity is to sample with progressively smaller sample sizes. When the sample no longer has the batched volume fraction of constituents, one can detect the scale of uniformity. For coarse ceramics, one can apply a series of screen analyses or other particle size analytical techniques when size is relevant. In the case when the density of different fractions is relevant, the mix might be separated by a heavy liquid, with the light fraction floating and the dense fraction sinking. The densest practical heavy liquid is at 3.25 g/ml, making the technique limited in its usefulness. As a postmortem analysis, one can section and polish the material after sintering and observe it microscopically. Chapter 9 describes such an example.
Firing Shrinkage
Constituents in the mix have different firing shrinkages depending upon their particle size. Figure 5.11 schematically illustrates the differences.
Coarse particles shrink little if at all.
Fines shrink up to about 20% linearly. The discrepancy creates a problem in crafting the ceramic. This is illustrated in Figure 5.12 showing schematically the fines that have shrunk away from the coarse-grain pack.
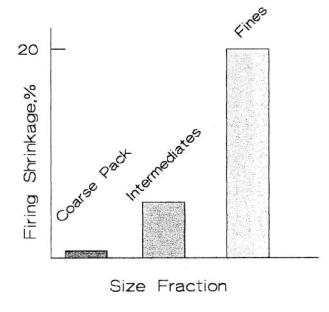
Mixing Coarse Grained Materials 131
Figure 5.11: Firing Shrinkages. Fine particles shrink more than coarse. The mix has to be balanced to produce a good microstructure.
This, while exaggerated, is a common occurrence that weakens the body. Alleviation of the problem is to add intermediate-sized particles to the formulation to reduce the discrepancy in firing shrinkage. Microstructural analysis will help attain the best formulation. Mechanical properties will detect when something is amiss.
There are four important factors to make a good mix: grain size packing, sintering shrinkage of each fraction, the binder, and the impeller speed. Clues for each are as follows:
Packing. Put the dry mix on a vibrating table and observe what separation occurs or sinter the body and measure the grain size distribution along the length of the piece.
Shrinkage. Add intermediate sizes to reduce the shrinkage of the fines. Also, look at the microstructure of the fired body to see if the fines are shrinking away from the coarse grains.

132 Ceramic Technology and Processing
Figure 5.12: Shrinkage Separation of Structure. Fines shrink away from the coarse-grain pack leaving voids.
Binder. There are two things to consider: the amount necessary to hold the body together during handling, and the amount necessary to stick the fines to the coarse particles. One popular way is to grab and squeeze a handful of the mix. If it sticks together without being plastic, then the binding capacity is good. To mix it correctly, it is essential to scrape down the mixer once or twice to get everything back into the bulk of the material. Dry mix first to break up the fines and then add the binder solution slowly at a slower impeller speed.
Impeller Speed. Shear will segregate the mix into fine and coarse fractions. Scrape down the mixer and mix at a slower speed to homogenize the distribution. The angular velocity on the periphery of the impeller is the important criterion for speed.