
Пожарная безопасность технологических процессов / Shvyrkov - PB tekhnologicheskikh processov 2012
.pdf
В случае микробиологического самовозгорания импульсом служит тепловая энергия, выделяющаяся в результате жизнедеятельности термофильных микроорганизмов, использующих горючее вещество в качестве питательной среды. Самонагревание торфа, сена, силоса и других подобных материалов начинается по этой причине и часто завершается пламенным горением.
Параметры процесса теплового самовозгорания горючего вещества или материала можно оценить, решив систему уравнений:
lgt |
cр |
A |
n |
p |
lg S; |
|
|
||||
|
|
p |
|
|
|
|
|
||||
lg τ |
c |
|
1 |
(А |
lgt |
cр |
), |
(8.5) |
|||
|
|
||||||||||
|
|
|
nв |
в |
|
|
|
|
|||
|
|
|
|
|
|
|
|
|
|
где Ар, nр, Ав и nв – опытные коэффициенты; S = F/V – удельная поверхность материала; F – поверхность материала, участвующая в теплообмене
сокружающей средой; V – объем материала.
8.2.4.Способы обеспечения пожарной безопасности при возможности самовоспламенения и самовозгорания веществ и материалов
1.Исключают контакт горючих веществ, нагретых до температуры самовоспламенения и выше, а также веществ, имеющих температуру самовоспламенения ниже температуры окружающей среды, с воздухом.
2.Контролируют температуру и продолжительность хранения веществ и материалов, склонных к тепловому, химическому и/или микробиологическому самовозгоранию.
3.Снижают температуру веществ и материалов, склонных к тепловому самовозгоранию, до значения ниже 0,7 tс.
4.Исключают контакт с водой веществ и материалов, реагирующих
свыделением тепла, взрывом или самовозгоранием.
5.Исключают контакт друг с другом веществ и материалов, реагирующих с выделением тепла, взрывом или самовозгоранием.
6.Предотвращают образование пирофорных соединений и отложений в производственном оборудовании.
7.Очищают оборудование, помещения и территорию наружных установок от пирофорных веществ и материалов.
8.Смачивают стенки и днища аппаратов, на которых возможно образование пирофорных отложений, водой перед вскрытием на осмотр или ремонт, а также постоянно смачивают отложения в процессе их удаления.
9.Удаляют пирофорные отложения, загрязненную маслами ветошь, замазученный грунт и тому подобные материалы с территории производственных объектов в специально отведенные места.
111

10. |
Очищают корпуса подшипников, электродвигателей и других на- |
||
гревающихся при |
работе устройств |
от масел, отложений пуха, пыли |
|
и других материалов, склонных к самовозгоранию. |
|||
11. |
Очищают |
нагнетательные |
линии воздушных компрессоров |
от нагаромасляных отложений. |
|
12.Предотвращают контакт ацетилена с медью и ее сплавами.
13.Предотвращают температурные или механические воздействия на нестойкие химические соединения.
8.3.Тепловое проявление механической энергии
8.3.1.Пожарная опасность искр удара и трения и способы обеспечения пожарной безопасности
При соударении или трении твердых тел одно о другое от них отрываются частицы, которые нагреваются вследствие превращения части кинетической энергии в тепловую и протекания экзотермической реакции окисления. Такие частицы по способу возникновения называются искрами удара и трения, или фрикционными искрами. Они относятся к низкокалорийным источникам тепла и могут служить потенциально возможными источниками зажигания газо-, паро- и пылевоздушных горючих смесей, а также могут вызывать появление очагов тления при попадании на отложения пыли или волокон.
Экспериментально установлено, что максимальная температура фрикционных искр ограничена температурой плавления более легкоплавкого материала трущейся или соударяющейся пары (при условии, что эти материалы не способны взаимодействовать друг с другом с экзотермическим эффектом).
Почти все металлы (за исключением благородных) взаимодействуют с кислородом воздуха, причем скорость их окисления растет с ростом температуры. При определенной температуре, когда количество тепла, полученного частицей в момент удара и выделившегося вследствие окисления, превысит количество тепла, отводимого в окружающую среду, самоускорение реакции окисления приведет к самовоспламенению металлической частицы.
Параметры фрикционных искр, образующихся при соударении конструкционных сталей (обыкновенного качества или качественных) можно оценить расчетом. Температура искр достигает температуры плавления сталей, т. е. примерно 1550 оС. Количество отдаваемого тепла искрой при ее охлаждении от начальной температуры 1550 оС до конечной температуры, равной температуре самовоспламенения горючего вещества tсв
112

(принято 100 оС tсв 700 оС – данный диапазон температур самовоспламенения охватывает практически любые горючие газы и пары), составляет всего 0,26–0,45 Дж.
Длительность существования искр, найденная из условий нестационарного теплообмена, исчисляется долями секунды (не превышает 0,45 с).
Сопоставление расчетных параметров искр с показателями пожаровзрывоопасности горючих веществ и материалов показывает, что фрикционные искры способны воспламенять не все горючие смеси. Определить реальную воспламеняющую способность искр можно лишь экспериментально. Экспериментально установлено следующее:
с увеличением энергии соударения воспламеняющая способность фрикционных искр возрастает;
бόльшую опасность представляет скользящий удар, чем прямой;
«бедные» горючие смеси зажигаются искрами удара легче, чем «богатые»;
при многократных соударениях твердых тел (например, лопастей вентилятора о корпус) горючие смеси могут зажигаться не только искрами, но и нагревшимися при трении поверхностями;
соударение алюминия, магния и их сплавов о ржавую стальную поверхность приводит к образованию частиц термита (смесей, состоящих
из алюминия (магния) и окиси железа), сгорающих при температуре око-
ло 3500 оС;
большую опасность представляют искры, образующиеся при ударах и трении титана и его сплавов;
искры, образующиеся при трении стальных деталей о корундовые
ишлифовальные круги, имеют температуру выше 3000 оС.
Способы предотвращения образования фрикционных искр при попадании в оборудование вместе с перерабатываемыми веществами и материалами инородных примесей
1.Очистка веществ и материалов от инородных примесей путем их просеивания или с помощью гравитационных, инерционных или магнитных улавливателей (сепараторов).
2.Применение искробезопасных конструкционных материалов.
3.Защита рабочих поверхностей оборудования искробезопасными футеровками.
Способы предотвращения образования фрикционных искр при ударах подвижных частей машин о неподвижные части
1.Применение искробезопасных конструкционных материалов.
2.Защита рабочих поверхностей оборудования искробезопасными футеровками.
113

3.Балансировка подвижных частей оборудования (в неподвижном состоянии и на холостом ходу).
4.Использование искробезопасных материалов для пола и изготовления обслуживающих площадок.
5.Увлажнение пола в помещениях, в которых обращается нитроклетчатка и подобные ей легковоспламеняющиеся вещества.
6.Устранение неполадок, вызывающих вибрации и удары.
7.Использование искробезопасных материалов для изготовления колес и бамперов внутрицехового транспорта.
Способы предотвращения образования фрикционных искр и их контакта с горючими смесями при выполнении ремонтных работ
1. Использование искробезопасного слесарного инструмента, имеющего сертификат безопасности для работ в конкретных взрывоопасных средах.
Примечание. Омедненный, луженый, оцинкованный и тому подобный инструмент не может считаться искробезопасным, так как тонкое защитное покрытие быстро истирается; обильная смазка инструмента тавотом или густым мыльным раствором для предотвращения образования искр ничем не обоснована; кроме того, возрастает опасность выскальзывания инструмента из рук.
2.Проведение аварийных работ в специальных укрытиях с гарантированным подпором чистого воздуха.
3.Устройство воздушного душа в месте проведения аварийных
работ.
4.Устройство защитных экранов.
5.Использование охлаждающих жидкостей для отвода тепла из зоны резания (от режущего инструмента и материала оборудования).
8.3.2. Пожарная опасность узлов трения в машинах и способы обеспечения пожарной безопасности
При работе машин и механизмов узлы, в которых движущиеся части сопрягаются с неподвижными, нагреваются вследствие трения. Количество выделяющегося при трении тепла dQтр определяют по формуле
dQтр = Fтр dl , |
(8.6) |
где Fтр – сила трения; dl – элементарное относительное перемещение трущихся пар.
Величину сил трения в трущихся парах можно оценить по формулам:
при скольжении пар |
Fтр = f N ; |
(8.7) |
||
при качении пар |
F k |
N |
, |
(8.8) |
|
||||
|
тр |
r |
|
|
|
|
|
|
114

где f – безразмерный коэффициент трения скольжения, зависящий от свойств материала трущихся пар, качества их обработки, наличия между ними смазки, скорости скольжения и других факторов; N – сила нормального давления между трущимися парами; k – коэффициент трения качения, имеющий размерность длины и зависящий от свойств материала трущихся пар, состояния их поверхностей и многих других факторов; r – радиус катящегося тела.
Выделяющееся за элементарный промежуток времени dτ в трущейся паре тепло расходуется на нагревание узла трения dQнагр, отводится системой охлаждения dQохл и теряется в окружающую среду dQпот. Уравне-
ние теплового баланса узла трения в общем случае имеет вид: |
|
||||
dQтр = dQнагр + dQохл + dQпот. |
(8.9) |
||||
Величину dQтр при равномерном вращательном движении можно |
|||||
найти из выражения |
|
|
|
|
|
dQ f N d |
d f N d |
n |
d , |
(8.10) |
|
|
|||||
тр |
2 |
2 30 |
|
|
|
|
|
|
где d – диаметр вращающейся детали (шейки подшипника, барабана транспортера и т. д.); ω – угловая скорость; n – частота вращения, мин–1.
Приняв а f N d2 30n dτ, имеем:
dQтр = a dτ . |
(8.11) |
Величина dQнагр зависит от массы нагревающихся деталей m, средней удельной теплоемкости металла сt и продолжительности нагрева dτ:
dQнагр = m сt dτ . |
(8.12) |
Количество отводимого тепла системой охлаждения примем равным нулю, что будет соответствовать наиболее неблагоприятному случаю:
dQохл = 0 . |
(8.13) |
Для определения потерь тепла в окружающую среду воспользуемся выражением
dQпот = (t – tср) S dτ , |
(8.14) |
где – коэффициент теплообмена от узла трения в окружающую среду, вычисляемый по формулам:
при t ≤ 60 оС |
4,07 3 t tср ; |
(8.15) |
при t > 60 оС |
α 11, 63 e0,0023 t ; |
(8.16) |
|
|
115 |
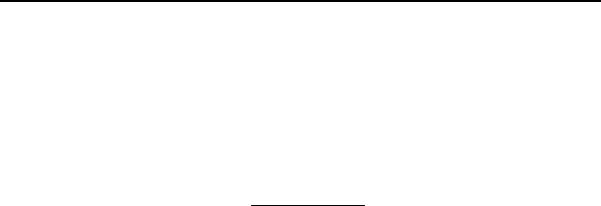
t – температура узла трения (корпуса подшипника, барабана и т. п.); tср – температура окружающей среды; S – поверхность теплообмена.
После подстановки значений (8.11)–(8.14) в уравнение (8.9) имеем:
|
|
a dτ = m сt dτ + 0 + (t – tср) S dτ . |
(8.17) |
||||||||||
Разделяем переменные: |
|
|
|
|
|
|
|
|
|||||
|
|
|
m c |
dt |
|
|
|
|
|
||||
|
|
d |
|
t |
|
|
|
(8.18) |
|||||
|
|
a S t tср |
|
||||||||||
и после интегрирования находим: |
|
|
|
|
|
|
|
|
|||||
|
|
ln a S t tср |
|
|
|
|
|
|
сonst . |
(8.19) |
|||
|
|
|
|
|
|
|
|
|
|||||
|
S |
|
m ct |
|
|
||||||||
|
|
|
|
|
|
|
|
||||||
Постоянную интегрирования определяем из начального условия: |
|||||||||||||
|
|
при τ = 0 |
t – tср = 0, |
|
|||||||||
тогда |
|
сonst |
ln a |
. |
|
|
|
|
(8.20) |
||||
|
|
|
|
|
|
||||||||
|
|
|
|
S |
|
|
|
|
|
|
|
После подстановки значения (8.20) в выражение (8.19) и несложных преобразований окончательно получаем выражение
m ct |
|
a |
|
|
|
|
ln |
|
|
|
(8.21) |
||
a S t t |
|
|
||||
S |
|
ср |
|
|
||
|
|
|
|
|
||
|
|
|
|
|
|
|
для определения температуры узла трения в любой момент времени после возникновения аварийной ситуации, т. е. после прекращения отвода тепла системой охлаждения.
Решив выражение (8.21) относительно t, имеем:
|
a |
|
|
|
α S τ |
|
|
|
t tср |
e |
m c |
|
|
||||
|
1 |
|
t |
, |
(8.22) |
|||
|
||||||||
|
α S |
|
|
|
|
|
|
|
|
|
|
|
|
|
|
|
|
а максимальную температуру в узле трения (при ∞) можно определить по формуле
tmax tср |
a |
. |
(8.23) |
|
|||
|
F |
|
116

На действующих производствах отмечены случаи возгорания горючих материалов вследствие перегрева подшипников и сальников машин, барабанов и лент транспортеров и норий, шкивов и приводных ремней, выделения тепла при обработке древесины, пластмасс и металлов резанием, таблетировании лекарств, прессовании пластмасс и отходов древесины, а также при сжатии газов.
Подшипники скольжения сильнонагруженных и высокооборотистых валов и осей машин могут перегреваться вследствие ряда причин: некачественной смазки, загрязнения подшипников, перекосов валов, чрезмерной затяжки подшипников, перегрузки машин, загрязнения корпусов подшипников отложениями.
При наличии систем централизованной смазки перегрев подшипников, помимо указанных причин, происходит из-за повышения температуры масла, поступающего в подшипники; снижения расхода масла; загрязнения масла механическими примесями.
Примерную температуру подшипников в случае прекращения их охлаждения можно определить по формулам (8.22) и (8.23).
Для предотвращения перегрева подшипников применяют следующие способы:
1)смазку подшипников и подвижных частей машин и механизмов производят в соответствии с рекомендованными технической документацией маслами и смазками в установленные сроки;
2)тщательно регулируют узлы трения при сборке и ремонте машин;
3)предотвращают перегрузки машин и механизмов;
4)очищают корпуса подшипников от наслоений краски, отложений пыли, волокнистых материалов и тому подобных загрязнений, ухудшающих теплообмен с окружающей средой (это мероприятие снижает также опасность самовозгорания отложений);
5)устраивают системы воздушного, водяного или масляного охлаждения подшипников высоконагруженных и высокооборотистых машин
имеханизмов;
6) устраивают системы централизованной смазки подшипников с автоматическим контролем и регулированием давления и температуры масла в системе, а также с контролем уровня масла в маслобаке;
7)устраивают автоматическую блокировку, обеспечивающую включение резервного насоса системы централизованной смазки при остановке основного маслонасоса или падении давления в напорной линии, а также срабатывание звуковой и световой сигнализации;
8)очищают масла от механических примесей в фильтре, установленном за насосом, подающим масло в подшипники;
117

9)очищают теплообменные поверхности в масляном холодильнике системы централизованной смазки от отложений;
10)заменяют подшипники скольжения подшипниками качения.
Проскальзывание (буксование) конвейерных лент и приводных ремней клиноременных передач относительно приводных барабанов
ишкивов приводит к перегреву последних и воспламенению лент и ремней. К буксованию приводит: перегрузка конвейеров или машин, слабое натяжение лент или ремней, завал башмака элеватора, т. е. такая ситуация, когда ковш элеватора не может пройти сквозь толщу сыпучего материала, защемление ленты (ремня) или ее перекос, замасливание ленты (ремня).
Максимальную температуру барабана или шкива при длительном буксовании ленты или ремня можно определить по формуле (8.23).
Для предотвращения буксования лент и ремней используют следующие способы:
1)предотвращают перегрузку транспортеров путем ограничения толщины слоя материала на ленте транспортера, равномерной подачи материала с помощью питателей и тому подобных устройств;
2)контролируют и при необходимости регулируют натяжение лент конвейеров и приводных ремней;
3)устраивают натяжные станции, автоматически обеспечивающие требуемое натяжение лент конвейеров;
4)предотвращают завал башмака элеватора сыпучим материалом, ограничивая толщину его слоя;
5)применяют защитные устройства и приспособления, автоматически сигнализирующие о перегрузке и отключающие привод конвейеров
имашин;
6)устраняют перекосы лент, контролируют и регулируют зазоры между лентами конвейеров и кожухами или другими неподвижными предметами, находящимися рядом с конвейерами;
7)очищают приводные барабаны и шкивы, ленты и ремни от загряз-
нений;
8)своевременно заменяют изношенные ленты и приводные ремни.
Загорание волокнистых материалов при наматывании их на ва-
лы (оси) машин и механизмов наблюдается на прядильных фабриках, льнозаводах, а также в комбайнах при уборке зерновых культур. Иногда загорание происходит при наматывании волокнистых материалов на валы конвейеров, транспортирующих отходы и готовую продукцию. На прядильных фабриках загорания часто возникают в результате наматывания на валы оборвавшихся шнуров, с помощью которых приводятся во вращение веретена прядильных машин. Сущность процесса загорания заключается в следующем: волокнистый или соломистый материал
118
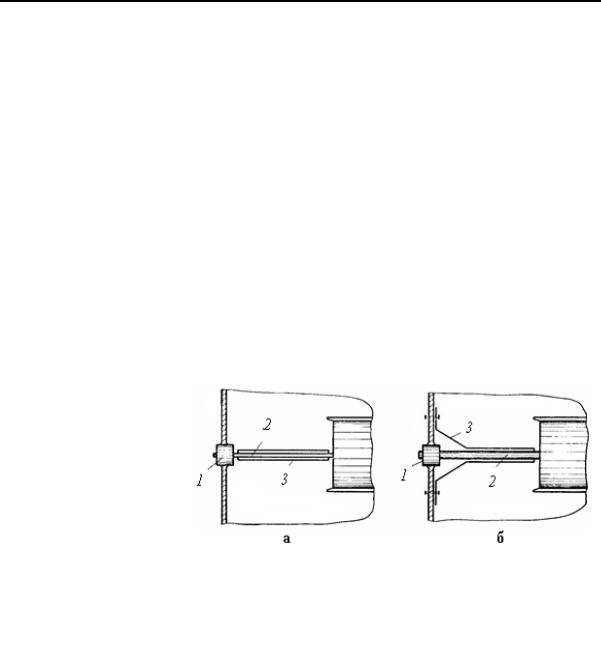
наматывается на вал (ось) около подшипника, что сопровождается образованием жгута, постепенным его уплотнением, сильным нагреванием при трении о стенки машины с последующим обугливанием и воспламенением.
Наматыванию волокнистых материалов на вращающиеся валы машин способствует: наличие увеличенных зазоров между валами и подшипниками (волокно, попадая в зазоры, защемляется, начинает наматываться на валы, все более и более уплотняясь); наличие оголенных участков валов и осей, с которыми могут соприкасаться волокнистые материалы; использование влажного и загрязненного сырья.
Для предотвращения наматывания волокнистых и соломистых материалов на валы и оси машин и механизмов применяют следующие способы:
1.При проектировании машин и механизмов обеспечивают минимальные зазоры между цапфами валов (осей) и подшипниками, не допуская их увеличения в процессе эксплуатации.
2.Валы (оси) за-
щищают от непосред- |
|
|
|
|
|
|||
ственного |
контакта с |
|
|
|
|
|
||
обрабатываемыми во- |
|
|
|
|
|
|||
локнистыми |
и |
соло- |
|
|
|
|
|
|
мистыми материалами |
|
|
|
|
|
|||
втулками (рис. 8.3), |
|
|
|
|
|
|||
кожухами, |
противона- |
|
а |
|
б |
|
||
моточными |
щитками, |
Рис. 8.3. Защита вала от наматывания волокнистых |
||||||
острыми |
|
ножами, |
|
|
материалов: |
|||
разрезающими |
нама- |
а – свободно насаженной цилиндрической втулкой; |
||||||
тываемое |
|
волокно, |
б – неподвижной конусной втулкой; |
|||||
и тому |
подобными |
1 – подшипник; 2 – вал; 3 – защитная втулка |
устройствами.
3. Контролируют состояние валов, на которые могут наматываться волокнистые и соломистые материалы, и своевременно очищают их.
8.3.3. Пожарная опасность нагрева газов при сжатии и способы обеспечения пожарной безопасности
Сжатие (компримирование) газов производят специальными машинами – компрессорами. При сжатии температура газа может подниматься
с20 °С примерно до 870–1040 °С (при начальном давлении 0,1 МПа
иконечном давлении 15,0 МПа), что, в свою очередь, приводит к повышению температуры деталей, узлов и компрессора в целом. При высоких температурах может не только нарушаться процесс сжатия газов,
119

ухудшаться смазка и происходить ускоренный износ деталей и узлов компрессора, но могут возникать аварийные ситуации, в особенности при отказе систем охлаждения (заклинивание поршней, поломка привода, термическое разложение (иногда со взрывом) сжимаемого горючего газа, самовоспламенение масла в картере компрессора и т. д.).
При эксплуатации воздушных компрессоров повышенная температура сжатого воздуха способствует разложению смазки с образованием нагара на стенках цилиндров и клапанах, что приводит к снижению их герметичности при закрытии и дальнейшему резкому повышению температуры сжимаемого воздуха. Под влиянием вибраций, неизбежных при работе компрессора, нагар частично отстает от стенок и уносится в трубопровод, холодильник, воздушный аккумулятор, осаждается в них и формирует вместе с парами масел весьма прочные отложения. Скопление нагара в трубопроводах уменьшает их сечение, вызывая потерю энергии, повышение давления и температуры сжатого газа. Кроме того, нагаромасляные отложения способны самовозгораться при высоких температурах сжатого воздуха.
Максимальную температуру газа при сжатии в компрессоре и отсутствии охлаждения определяют по формуле
n 1
tк tн 273 рк n 273, (8.24)рн
где tн и tк – температура газа в компрессоре соответственно до сжатия (начальная) и после сжатия (конечная); рн и рк – начальное и конечное
давление газа соответственно; n – показатель политропы (n 0,9 k , где k – показатель адиабаты).
Для обеспечения пожарной безопасности при сжатии газов применяют следующие способы:
1. Сжатие газов до высоких давлений производят в многоступенчатых компрессорах. Исходя из условий безопасного режима эксплуатации компрессора, число ступеней сжатия газа определяют по формуле
x |
lg pк lg pн |
, |
(8.25) |
lg ε |
где [ ] – допустимая степень сжатия газа, определяемая из выражения
|
без |
273 |
|
n |
|
|
||
n 1 |
|
|
||||||
ε |
tр |
|
, |
(8.26) |
||||
|
273 |
|
||||||
|
t |
н |
|
|
|
|||
|
|
|
|
|
|
|
где tрбез – безопасная температура газа в конце сжатия, в качестве которой принимают минимальное значение одной из следующих величин:
120