
Пожарная безопасность технологических процессов / Shvyrkov - PB tekhnologicheskikh processov 2012
.pdf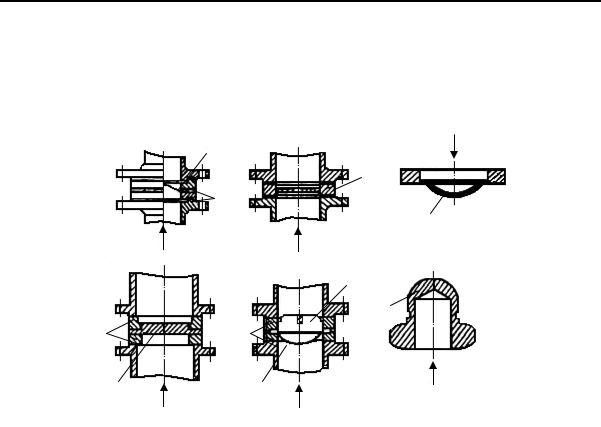
9.7.2. Виды мембранных предохранительных устройств
По характеру разрушения различают разрывные, срезные, ломающиеся, хлопающие, выщелкивающиеся и отрывные взрывные мембраны
(рис. 9.9).
|
|
|
1 |
|
|
|
|
|
|
|
|
|
|
|
|
|
р |
||||
|
|
|
2 |
|
|
|
|
|
|
|
1 |
|
|
|
|
|
|
||||
|
|
|
|
|
|
|
|
|
|
|
|
|
|
|
|
||||||
|
|
|
|
|
|
|
|
|
|
|
|
|
|
|
|
|
|
||||
|
|
|
|
|
|
|
|
|
|
|
|
|
|
1 |
|
|
|
|
|||
|
|
|
|
р |
|
|
|
|
|
|
|
р |
|
|
|
|
|||||
|
|
а |
|
|
|
|
|
в |
|
|
|
|
д |
|
|||||||
|
|
|
|
|
|
|
|
|
|
|
|
|
|
3 |
|
|
|
|
|
|
|
|
|
|
|
|
|
|
|
|
|
|
|
|
|
|
|
|
|
|
|
||
|
|
|
|
|
|
|
|
|
|
|
|
|
|
|
|
|
|
|
|
||
2 |
|
|
|
|
|
|
|
|
|
|
|
|
|
1 |
|
|
|
|
|
|
|
|
|
|
|
|
|
|
|
|
|
|
|
|
|
|
|
|
|
|
|
|
|
|
|
|
|
|
|
2 |
|
|
|
|
|
|
|
|
|
|
|
|
|
|
|
|
|
|
|
|
|
|
|
|
|
|
|
|
|
|
|
|
|
|
|
|
|
|
|
|
|
|
|
|
|
|
|
|
|
|
|
|
|
|
|
|
|
|
|
|
|
|
|
|
|
|
|
|
|
|
|
|
|
|
|
|
|
|
|
|
|
1 |
|
|
|
|
|
|
1 |
|
|
|
|
|
|
|
|
|
|
р |
|
||
|
|
|
р |
|
|
|
|
|
|
|
|
|
|
|
|
|
|
|
|||
|
|
|
|
|
|
|
|
р |
|
|
|
|
|
|
|
|
|||||
|
|
|
|
|
|
|
|
|
|
|
|
|
|
|
|
|
|
|
|||
|
|
б |
|
|
|
г |
|
|
|
|
е |
|
|
|
|
||||||
|
|
|
|
|
|
|
|
|
|
|
|
|
|
|
|
|
|||||
|
|
|
|
|
|
|
|
|
|
|
|
|
|
|
|
|
|
|
|
|
|
|
|
|
|
|
|
|
|
|
|
|
|
|
|
|
|
|
|
|
|
|
|
Рис. 9.9. Мембранные предохранительные устройства
сразрушающимися мембранами:
а– с разрывной мембраной; б – со срезной мембраной;
в– с ломающейся мембраной; г – с хлопающей мембраной; д – с выщелкивающейся мембраной; е – с отрывной мембраной; 1 – мембрана; 2 – прижимные кольца;
3 – разрезной нож
Разрывные мембраны при срабатывании разрываются, поэтому их чаще изготавливают в виде тонкой пластины, плоской или вогнутой, из пластичных металлов: алюминия, никеля, меди, латуни и др.
Срезные мембраны срезаются по периметру острой кромки прижимного кольца. Их также изготавливают из пластичных металлов.
Ломающиеся мембраны при срабатывании ломаются и поэтому они выполняются из хрупких материалов: чугуна, графита, стекла и т. п. Они чувствительно реагируют на нагрузки динамического характера, являются малоинерционными.
Хлопающие мембраны имеют форму сферического купола, выпуклая сторона которого обращена к зоне повышенного давления (внутрь защищаемого аппарата), и изготавливаются из тонколистового проката пластичных металлов. При повышении давления сверх критического сферический купол мембраны теряет устойчивость и выворачивается в обратную
сторону. Мембрана сталкивается с крестообразным ножом и разрезается. Выщелкивающиеся мембраны чаще изготавливают из пластмасс, они
имеют выпуклую форму и крепятся в специальном гнезде (кольцевой
141

выточке) с помощью мягкого припоя или замазки. При срабатывании выщелкивающиеся мембраны выбиваются из гнезда, полностью освобождая «живое» сечение стравливающего патрубка. После срабатывания выщелкивающиеся мембраны вновь могут быть использованы (они многоразового действия).
Отрывные мембраны применяют для защиты аппаратов с высоким рабочим давлением. Такая мембрана чаще всего имеет вид колпачка, отлитого вместе с фланцами для крепления, и имеет ослабленное сечение, по которому и происходит ее отрыв при срабатывании.
9.7.3. Расчет предохранительных мембран на заданное давление срабатывания
Давление срабатывания мембраны не должно быть больше расчетного давления и меньше рабочего давления аппарата. Это означает, что предохранительная мембрана должна быть самым слабым узлом в конструкции оборудования, не должна срабатывать при нормальных условиях эксплуатации оборудования, а при неуправляемом повышении давления в аппарате она должна разрушаться в первуюочередь.
При нагружении плоской мембраны из тонколистового проката пластичного металла перепадом давлений она приобретает форму сферического купола. Непосредственно перед разрывом мембрана работает как тонкостенная сферическая оболочка (радиус R и толщина ), защемленная по контуру (диаметр D) (рис. 9.10).
∆
D
R 0
H
Рис. 9.10. Расчетная схема разрывной мембраны
Давление срабатывания такой оболочки (мембраны) рс можно определить по формуле
рс = 2 вр / R, |
(9.23) |
где 0 – толщина мембраны при срабатывании; σвр – временное сопро-
тивление.
В формуле (9.23) неизвестной величиной является радиус R кривизны серединной поверхности оболочки, который полностью определяется пластическими свойствами материала мембраны. Очевидно, при менее пластичном материале мембраны (при всех прочих равных условиях) разрушение мембраны произойдет при меньшем давлении рс.
Общепринятой мерой пластичности материала является относительное удлинение δ при разрыве. Предел деформации оболочки
142

наступает тогда, когда ее толщина приобретет относительное утончение D¢, которое функционально связано с величиной δ выражением
1 1/ 1 δ.
Из условия сохранения объема материала при пластической деформации можно записать:
(πD2/4) 0 = S = S 0(1– ' ),
где S – поверхность купола мембраны на пределе разрыва, которую можно выразить через ее размеры:
S 2 RH 2 R R R2 (D / 2)2 .
Тогда, с учетом формулы (9.23), можно выразить минимальный (на пределе разрыва) радиус купола:
R = D |
(1+δ)/( 1+δ-1), |
4 |
|
и формула (9.23) примет вид:
р |
|
8 0σвр |
|
1 δ 1 |
. |
(9.24) |
|
|
|||||
с |
D |
|
1 δ |
|
||
|
|
|
|
Толщину проката для мембраны можно рассчитать по формуле
D = |
рсD |
|
1+δ |
, |
(9.25) |
|
|
||||
0 |
8ktσвр |
|
1+δ-1 |
|
|
|
|
|
где kt – температурный поправочный коэффициент, зависящий от материала мембраны и рабочей температуры в защищаемом аппарате.
9.7.4. Расчет площади сбросных отверстий
Повышение давления в защищаемом объеме при горении среды должно быть полностью компенсировано снижением давления вследствие истечения газов через сбросное отверстие. Для этого необходимо удалять за единицу времени из объема максимальное количество паров:
G = Fuρ(ε – 1), |
(9.26) |
где F – поверхность фронта пламени; u – нормальная скорость распространения фронта пламени; ρ – плотность удаляемого газа; ε – степень расширения газов при сгорании.
Предельное значение плотности газа можно выразить формулой
143
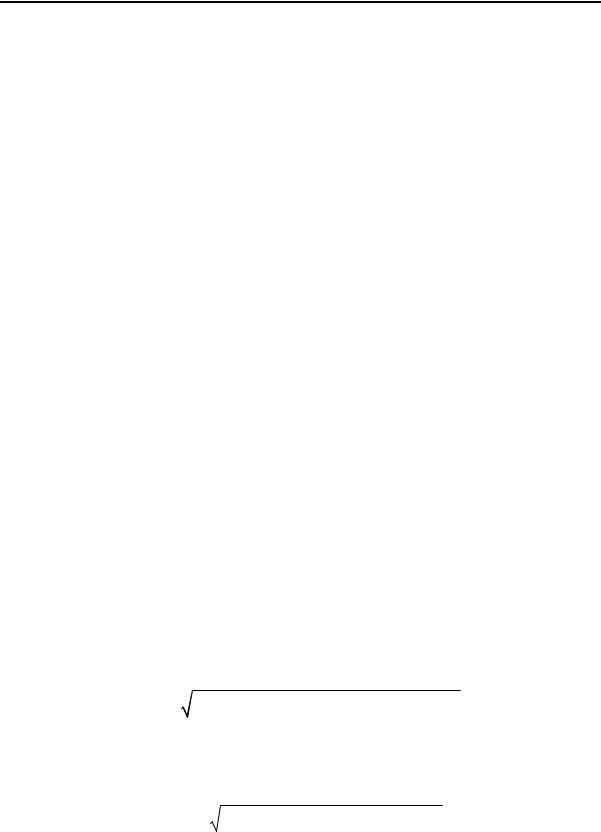
0 р/ р0 1/ k , |
(9.27) |
где р – абсолютное значение давления в защищаемом аппарате; k – показатель адиабаты; индекс «0» обозначает начальное значение параметров.
При адиабатическом сжатии ГГ в процессе развития взрыва величину ε можно выразить в зависимости от давления:
1 0 |
1 р / р0 (1 k ) / k . |
(9.28) |
Для эффективной взрывозащиты любого объекта, обусловленной сбросом давления, необходимо, чтобы предохранительное устройство могло обеспечить расход газов не менее:
G Fu 0 0 1 p / p0 (2 k ) / k . |
(9.29) |
Максимальную поверхность фронта пламени можно выразить формулой:
F = f Fmax, |
(9.30) |
где Fmax – максимальная поверхность пламени, найденная геометрически в предположении, что от точки поджога пламя распространяется во все стороны с одинаковой скоростью и поэтому имеет сферическую форму; f – коэффициент искривления фронта пламени.
Наиболее неблагоприятный случай – когда через сбросное отверстие истекают не продукты сгорания, а холодные газы. Тогда их температуру можно выразить как:
Т Т0 р/ р0 (k 1) / k . |
(9.31) |
Площадь сбросного отверстия определяется по формулам:
|
|
|
|
|
р0 |
|
|
|
|
|
k/ k-1 |
|
длядокритическогорежимаистечения, когда |
=ν>é2/ |
(k +1)ù |
( ) |
|||||||
|
|
||||||||||
|
|
|
|
|
рр |
|
|
ë |
û |
|
|
|
S ³ αp |
Fuρ (ε-1)( p / p )1/k |
|
|
|
|
(9.32) |
||||
|
(2uM / RT )k / (k -1)(ν2/k -ν(k+1)/k ) ; |
|
|||||||||
|
|
|
0 |
0 |
|
|
|
|
|
|
|
|
для критического режима истечения, когда ν£ |
é2/ |
(k +1)ùk /(k-1) |
||||||||
|
|
|
|
|
|
|
ë |
|
û |
|
|
|
S |
Fu 0 ( 1)( p / p0 )1/ k |
|
, |
|
|
(9.33) |
||||
|
p (kuM / RT )[2 /(k 1)](k 1) /(k 1) |
|
|
|
где u – нормальная скорость распространения пламени в данной смеси;0 – начальная плотность горючей смеси; α – коэффициент истечения газа
через сбросное отверстие; М – молекулярная масса; R – универсальная газовая постоянная.
144

Контрольные вопросы
1.Назовите основные причины быстрого распространения пожара
вусловиях производства.
2.Основные направления по снижению количества горючих веществ на стадии проектирования.
3.Решения по снижению количества горючих веществ при эксплуатации производства.
4.Требования к системе аварийного слива ЛВЖ и ГЖ.
5.Основные меры обеспечения пожарной безопасности для систем аварийного выпуска горючих газов и паров.
6.Дайте классификацию огнепреградителей.
7.Принцип действия сухого огнепреградителя. В каких случаях используются сухие огнепреградители?
8.Что называется критическим диаметром канала огнепреградителя? Как определить критический диаметр канала огнепреградителя?
9.Виды жидкостных огнепреградителей.
10.Принцип действия гидрозатвора.
11.Принцип действия шнекового дозера-питателя. В каких случаях он используется?
12.Способы предотвращения распространения пожара по производственным коммуникациям с горючими отложениями.
13.С какой целью на производстве применяют рукавные фильтры?
14.Принцип действия автоматических заслонок и задвижек.
15.Какие защитные устройства ограничивают растекание горючих жидкостей при аварии?
16.Какие мероприятия включает в себя защита технологического оборудования от разрушения?
17.Как определить максимальное давление взрыва?
18.От каких параметров зависит величина давления взрыва?
19.Для чего в технологическом оборудовании применяют взрывные мембраны?
20.Как классифицируются мембраны? В каких случаях в технологическом оборудовании применяют выщелкивающие мембраны?
145

Глава 10
ОСОБЕННОСТИ ПОЖАРНОЙ ОПАСНОСТИ ОГНЕВЫХ РЕМОНТНЫХ РАБОТ И СПОСОБЫ ОБЕСПЕЧЕНИЯ ПОЖАРНОЙ БЕЗОПАСНОСТИ
Согласно статистике доля пожаров в промышленном секторе России при производстве регламентных, ремонтных и огневых работ составляет 13 % от общего количества пожаров. При этом из-за нарушений технологии проведения работ, правил пожарной безопасности при проведении электрогазосварочных работ, правил устройства и эксплуатации электрооборудования и теплогенерирующих установок происходит порядка 10 тыс. пожаров ежегодно, сопровождающихся гибелью людей (100–150 человек) и огромным материальным ущербом. На предприятиях нефтегазового комплекса доля пожаров при производстве предремонтной подготовки, ремонтных и огневых работ достигает 50 %, а на резервуарах 60 %. Пожары на технологическом оборудовании сложны, практически всегда присутствует угроза взрыва. Поэтому основное внимание необходимо уделять профилактической составляющей системы обеспечения пожарной безопасности, используя существующие методы и способы обеспечения пожарной безопасности. Основной особенностью пожарной опасности при проведении огневых ремонтных работ является присутствие технического персонала, поэтому пожары нередко сопровождаются травматизмом и гибелью людей.
10.1. Способы и принципы обеспечения пожарной безопасности
Способы обеспечения пожарной безопасности основаны на принципе разрыва связей мнемонического треугольника горения, тремя сторонами которого являются: окислитель, горючее и источник зажигания. Анализ результатов современных исследований позволяет классифицировать способы обеспечения пожаровзрывобезопасности (ПВБ) при ликвидации аварий, чрезвычайных ситуациях и ремонтно-восстановительных работах на технологическом оборудовании по следующим группам (методам):
1)снижению концентрации паров (газов) углеводородов;
2)предотвращению контакта источника зажигания с ВОК паров (газов) углеводородов;
3)флегматизации (ингибирование) газового пространства технологического оборудования.
Условиями обеспечения пожаровзрывобезопасности с помощью первого метода являются:
146

а) снижение концентрации паров (газов) в газовом пространстве технологического аппарата р до величины меньше значения н с учетом коэффициента безопасности Kб.н, т. е. при этом должно соблюдаться соотношение
р |
н |
; |
(10.1) |
|
|||
|
Kб.н |
|
|
б) очистка поверхностей технологического объекта |
от отложений |
и жидкой фазы до невоспламеняемой толщины слоя пожароопасных углеводородных остатков с соблюдением условия
mПДПН |
mкр |
, |
(10.2) |
|
K б.м |
||||
|
|
|
где mПДПН – предельно допустимая масса пожарной нагрузки; mкр – критическое значение массы пожарной нагрузки; Kб.м – коэффициент безопасности, принимаемый для предельно допустимой пожарной нагрузки.
Исходя из соотношения (10.2) и зная, что m = , справедливо условие
ПДПН |
|
кр |
, |
(10.3) |
||
K |
б.м |
|||||
|
|
|
|
где ПДПН – предельно допустимая толщина остаточного слоя загрязнения;кр – критическая максимальная невоспламеняемая толщина остаточного слоя технологических углеводородных жидких (твердых) остатков.
Для оценки пожаровзрывобезопасности необходимо знать коэффициент безопасности. Значение Kб.н при проведении огневых и искроопасных работ рекомендуется принимать не менее 20 (5 % от НКПР). Условие (10.1) обеспечивает взрывобезопасность, но не исключает пожарную опасность в том случае, если в технологическом процессе имеются горючие твердые или жидкие вещества. Очистка технологического объекта, мест утечек, аварий обычно осуществляется ручным способом с выполнением значительного объема трудоемких работ во вредных для здоровья рабочих условиях.
Первый метод (группа способов) обеспечения пожаровзрывобезопас-
ности при предремонтной подготовке объекта реализуется с помощью следующих технологических операций: принудительной вентиляции, пропаривания, гидравлической мойки, сорбции паров и газов, компремирования парогазовоздушных смесей, механической очистки. В зависимости от экономической целесообразности и свойств горючей нагрузки указанные способы могут применяться отдельно или в комбинации.
147

Обоснование методов обеспечения ПВБ целесообразно проводить с учетом оценки пожарной опасности и критических условий воспламенения и горения тонких слоев (пленок) углеводородосодержащей нагрузки.
Второй метод обеспечения ПВБ основан на исключении контакта источника зажигания и горючих веществ. Пожарная безопасность обеспечивается с помощью воздушно-механических пен и/или твердеющих пен. Учитывая широкое распространение пен в практике пожаротушения и наличие на объектах значительного количества пенообразователя с истекшим сроком хранения, целесообразно более детально рассмотреть способы изоляции источника зажигания с помощью воздушно-механических пен. Обеспечение безопасности при этом достигается:
а) снижением концентрации в газовом пространстве технологического оборудования до ПДВК, т. е. должно выполняться условие (10.1);
б) покрытием поверхности нефтепродуктов (отложений) слоем изоли-
рующего вещества при соблюдении условий: |
|
|
|||||
без |
|
кр |
; |
|
(10.4) |
||
|
|
|
|
||||
|
|
|
Kб.и.п |
|
|
||
V |
|
|
крF |
; |
|
(10.5) |
|
|
|
|
|||||
з.п |
|
Kб.и.п |
|
|
|||
|
о з п , .р |
.п |
(10.6) |
где без, кр – безопасная и критическая толщина покрытия, исключающая
газопроницаемость; Kб.и.п – коэффициент безопасности, принимаемый для толщины изолирующего покрытия; Vз.п – объем защитного покрытия; з.п – время действия защитного покрытия; F – площадь горючих остатков; о.р – длительность огневых работ; п – продолжительность перерывов в работе.
Необходимость выполнения условия (10.1) при реализации данного метода обусловливается возможностью образования искр (расплавленных капель).
Предотвращение возникновения пожара (взрыва) может быть обеспечено также путем изоляции места проведения огневых работ от горючей среды. При использовании в качестве изолирующего покрытия быстро разрушающихся пен в процессе подачи происходит одновременная дегазация газового пространства. Если применяются твердеющие пены, пленкообразователи, микрошарики, при подаче которых практически отсутствует эффект снижения концентрации, то после покрытия ими поверхности испарения требуется дегазация технологического аппарата путем его вентиляции.
148

Третий метод обеспечения ПВБ огневых работ основан на снижении концентрации окислителя в газовом пространстве и не требует предварительной очистки технологического аппарата.
Условиями ПВБ этого метода являются:
а) снижение концентрации кислорода при использовании инертных флегматизаторов (азот, аргон, углекислый газ, продукты сгорания и т. п.) до значения меньше минимального содержания кислорода в смеси (МВСК) с учетом коэффициента безопасности Kб.к:
без.к |
МВСК |
, |
(10.7) |
|
|||
|
Kб.к |
|
где без.к – безопасная концентрация кислорода в газовом пространстве трубопровода;
б) поддержание безопасной концентрации ингибитора (смеси ингибитора и инертного газа) без.ф выше минимальной флегматизирующей концентрации флегматизатора ф с учетом коэффициента безопасности Kб.ф:
без.ф фKб.ф ; |
(10.8) |
в) поддержание избыточного содержания паров углеводородов (при-
родного или нефтяного газа) выше значения в с учетом коэффициента безопасности Kб.в:
|
вKб.в. |
(10.9) |
без.г |
|
|
10.2. Предельно допустимая пожарная нагрузка
Известно, что 90–95 % загрязнений обычно удаляется с поверхности в течение первой половины времени очистки. Экспериментально установлено, что не только при механической очистке, но и при вентиляции, пропарке, гидравлической очистке 3–10 % технологических остатков очищаются за такое же по продолжительности время, как и основная масса углеводородных отложений. Для преодоления сил межмолекулярного взаимодействия (сил адгезии) нужны очень большие энергетические затраты, поэтому ручным способом полностью удалить технологические отложения практически невозможно.
Исследования в области определения пожарной опасности тонких пленок горючих жидкостей, а также аналитическое изучение воспламенения пленок органических жидкостей, двухфазных сред и конденсированных веществ свидетельствуют о существовании толщины слоя горючего вещества, не способного к воспламенению. Такой слой называется крити-
ческим по условиям воспламенения.
149

При разработке критериев предельно допустимой пожарной нагрузки (ПДПН) анализируются следующие условия пожарной безопасности:
1)допускается возможность локального горения на определенной площади в течение времени, не создающего воздействия опасных факторов пожара на людей, с нормированной вероятностью и не наносящего повреждений технологическому аппарату;
2)исключается возможность возникновения и распространения горения по поверхности горючих остатков.
Предварительные расчеты по методике, разработанной применительно
кзамкнутым помещениям с различной степенью герметизации, выполненные в Академии ГПС МЧС России, подтвердили возможность образования вакуума на стадии затухания горения.
Исходя из анализа результатов исследований, можно сделать выводы, что при кратковременном горении внутри технологического оборудования создаются условия затухания и образуется вакуум порядка 200 кПа, что может привести к повреждению технологических аппаратов. Поэтому при обосновании ПДПН целесообразно исходить из принципа исключения возможности возникновения и распространения горения по поверхности горючих органических остатков.
Вкачестве критерия оценки готовности резервуара к огневым работам принимают невоспламеняемую толщину слоя технологических остатков. Для определения толщины слоя органических остатков применяют специальные приборы толщиномеры, а при их отсутствии используется весовой метод. Весовой метод оценки поверхности позволяет путем взвешивания органических остатков, снятых с единицы площади поверхности, определить толщину остаточного слоя.
Количественно ПДПН представляет собой массу горючих остатков, находящуюся на единице площади загрязненной поверхности. Величина ПДПН связана с критической невоспламеняемой толщиной технологиче-
ских остатков кр соотношением
mПДПН |
ρ δкр |
. |
(10.10) |
|
|||
|
Kб.м |
|
|
Условие пожаробезопасности (10.2) запишется в виде |
|
||
mост mПДПН , |
(10.11) |
где mост – остаточная загрязненность поверхности; mПДПН – ПДПН. Налипаемость горючих жидкостей на вертикальную стенку в процессе
опорожнения составляет в среднем (5–100)10–3 кг/м2 в зависимости от вязкости и длительности хранения горючих жидкостей.
150