
- •Введение
- •Глава 1. Котельная установка морского судна
- •1.1 Потребители пара на судне
- •1.3 Назначение и классификация котлов
- •1.4 Требования к котлам
- •2.4 Основы теории топочных процессов
- •Глава 3. Топочные устройства котлов
- •3.1 Сжигание жидких топлив в топке котла
- •Глава 4. Тепловой баланс котла
- •4.1 Уравнения прямого и обратного теплового баланса
- •4.3. Уравнения теплового баланса утилизационного котла
- •Глава 5. Процессы теплообмена в котле
- •5.3 Конвективный теплообмен
- •5.5 Теплопередача в пароперегревателях
- •Глава 6. Гидродинамические характеристики котла
- •6.1 Аэродинамические и газодинамические характеристики
- •Глава 7. Конструкции котлов и их элементов
- •7.2 Главные водотрубные котлы
- •7.3 Вспомогательные водотрубные котлы
- •7.6 Утилизационные котлы
- •9.1 Причины изменения технического состояния элементов котла
- •9.2 Коррозия в судовых котлах
- •10.1 Задачи технической эксплуатации
- •Глава 11. Водные режимы котла
- •11.2 Обработка питательной воды
- •11.3 Обработка котловой воды
- •Список литературы
ройства, обеспечивающие питание котла и необходимые параметры пара. Паропроизводительность утилизационной части (при мощности ГТУ 8700 кВт) 4500 кг/ч, топ-
ливной - 6000 кг/ч (при расходе дизельного топлива 465 кг/ч); рабочее давление пара 0,6 МПа; температура перегретого пара 180-195 °С; КПД топливной части 81 %; температура газов за ГТУ 240 "С; масса котла без воды 32600 кг, с водой 41500 кг.
7.6. УТИЛИЗАЦИОННЫЕ КОТЛЫ
Утилизационные котлы с развитыми поверхностями нагрева существенно улучшают использование топлива на современных морских дизельных судах. Принцип искусственной (или принудительной многократной) циркуляции применяют, как правило, только в утилизационных котлах теплоходов.
Общая компоновка, как и параметры пара УК, зависит от его назначения. Утилизационные котлы, помимо их основного назначения, выполняют также дополнительные функции искроулавливателя и глушителя газодинамического шума дизеля (иногда для этой цели устанавливают еще и специальные устройства).
Всовременной практике на транспортных судах с дизельными установками применяют две системы утилизации теплоты уходящих газов главного двигателя: с обычной утилизацией теплоты, в которой насыщенный пар сравнительно низкого давления (примерно 0,4-0,6 МПа) расходуется на бытовые и общесудовые потребители (теплофикационная система); с глубокой утилизацией теплоты, где утилизационный котел генерирует пар, основным потребителем которого является турбогенератор. Для высокой эксплуатационной эффективности установки требуется давление примерно 0,6-1,2 МПа и его перегрев около 260-280 "С, а также возможно низкая температура уходящих газов за котлом для увеличения его паропроизводительности и соответственно мощности турбогенератора. Для количественной оценки этого условия в первом приближении можно использовать накопленные опытом значения удельной паропроизводительности утилизационного
котла DK/Ne = 0,5 - 0,65 кг/(кВт-ч) и удельный расход пара на турбогенератор DТГ/NТГ = 6,5 - 12 кг/(кВт-ч) (где DK и Dff - паропроизводительность и расход пара, кг/ч; Ne и Nn - мощности главного дизеля и турбогенератора, кВт).
Первая схема простая, ее применяют практически на всех морских теплоходах. В этой схеме утилизационный котел часто имеет общую компоновку цилиндрической формы, поверхность нагрева которого выполняется в виде спиральных трубчатых змеевиков. Для котлов с искусственной циркуляцией необходима дополнительная пароводяная емкость для отделения пара от воды, которой может быть отдельный сепаратор (можно использовать пароводяной барабан вспомогательного котла).
Утилизационные установки, выполненные по схеме глубокой утилизации, работают только на ходовом режиме. Это дает экономию топлива примерно 4-6 % и позволяет заменить один дизельгенератор турбогенератором.
Внастоящее время как в отечественной, так и в зарубежной практике широко распространены дизельные установки, в которых нагрузка электростанции на ходовом режиме обеспечивается турбогенератором, работающим' на паре от утилизационного котла.
Успешно эксплуатируются построенные в нашей стране танкеры типа "Великий Октябрь", балкеры "Зоя Космодемьянская", балктанкеры типа "Борис Бутома", сухогрузные суда типа "Капитан Кушнаренко", лихтеровоз "Алексей Косыгин", имеющие дизельные установки с утилизационными турбогенераторами. Установками с глубокой утилизацией теплоты оборудованы суда, построенные за рубежом, в частности танкеры типов "Лисичанск" (в Японии), "Леонардо да Винчи" (в Италии), "Герои Севастополя" (в Великобритании) и др. Газотурбинные суда типа "Капитан Смирнов" оборудованы утилизационными котлами, работающими на турбогенераторы и турбины гребного вала.
На отмеченных судах с новыми энергетическими установками УК - это крупное вспомогательное оборудование. В связи с этим непрерывно повышаются требования к рациональной компоновке таких котлов и совершенствованию условий эксплуатации утилизационных установок.
Отечественные утилизационные водотрубные котлы с естественной циркуляцией (КУП70/6; КУП110/5,5; КУШ35/7-5) составляют 6 % общего количества УК. Котел (рис. 7.12, а) состоит из

водяного 4 и пароводяного 1 коллекторов и соединяющего их пучка парообразующих труб 2. Опускные трубы 3 тоже обогреваемые и выполнены в виде экрана.
Отечественные утилизационные котлы с принудительной циркуляцией выполняют с цилиндрической (15 %) и прямоугольной (13 %) компоновкой поверхностей нагрева. При этом цилиндрическую компоновку имеют, как правило, котлы небольшой паропроизводительности (КУП17/5,
КУП19/5, КУПЗО/5, КУП55/5, КУП95/5).
Рис. 7.12. Принципиальные схемы утилизационных водотрубных котлов прямоугольной компоновки.
Различия УК цилиндрической и прямоугольной компоновок заключаются в конструктивном исполнении змеевиков и их размещении в газоходе '10 отношению к потоку дымовых газов.
При цилиндрической компоновке (рис. 7.12, б) змеевики 1, выполненные в виде плоской спирали из гладких груб, размещают в газоходе горизонтально последовательно по ходу газов так, что первый змеевик находится в зоне наибольших температур дымовых газов, а последний - наименьших. Такая компоновка обусловливает вертикальное расположение входного 2 'и выходного 3' коллекторов.
При прямоугольной компоновке (рис. 7.12, в) змеевики (в виде гладких труб) имеют плоскую зигзагообразную форму и размещены в газоходе параллельно по отношению к потоку газов, т. е. все змеевики, расположенные вертикально, находятся в одинаковых температурных условиях. При этом коллекторы 2 и 3 расположены горизонтально. Только в УК большой паропроизводительности для систем глубокой утилизации теплоты применяют посеребренные змеевики.
Паропроизводительность в УК цилиндрической компоновки (см. рис. 7.12, б) регулируют, как правило, путем перепуска дымовых газов через центральный газоход 5, выполненный в виде трубы большого диаметра, на входе в которую установлена газовая заслонка 4.
В котле прямоугольной компоновки для такого регулирования необходимо предусматривать обводной газоход 5, что влечет за собой увеличение размеров котла (см. рис. 7.12, в). В этом отно-
шении цилиндрическая компоновка с центральным байпасным газоходом имеет преимущества перед прямоугольной. Кроме того, цилиндрический котел более удобно компонуется в дымовой трубе.
В установках с утилизационным турбогенератором обычной является конструктивная схема с прямоугольной компоновкой котла. Эксплуатационное преимущество утилизационного котла с искусственной циркуляцией - это возможность ввода его в действие из сухого состояния без остановки дизеля, так как змеевиковые пучки труб, приваренные к коллекторам, хорошо компенсируют тепловые изменения при подводе в них воды с невысокой температурой.
Нашей промышленностью создан ряд типоразмерных утилизационных котлов с прямоугольной компоновкой для дизельных судов с турбогенераторами. В конструкции котлов использованы унифицированные узлы.
Оригинальную конструкцию имеют утилизационные котлы прямоугольной компоновки КУП1500Р, установленные на теплоходе "Алексей Косыгин". Котел (рис. 7.12, г) состоит из двухсекционного экономайзера 1 (секции включаются последовательно), одной парообразующей секции 3 и пароперегревателя 5. Змеевики всех поверхностей нагрева изготовлены из оребренных труб (ребра круглые), прикрепляемых к коллекторам с помощью сварки. Обе секции экономайзера 1 включены по схеме противотока, а парообразующая секция 3 - по схеме прямотока (входной 4 и выходной 2 коллекторы расположены горизонтально).
Наиболее часто применяют котлы КУП700, КУП660/7 и КУП 1100 (котел утилизационный, паровой с поверхностью нагрева соответственно около 700, 660 и 1100 м2. а цифра 7 соответствует рабочему давлению 0,7 МПа). Имеются модернизированные варианты этих котлов: КУП700-1 и КУП660/7-1. Внешний вид котлов почти не различается, поэтому рассмотрим поперечный разрез котла КУП660/7-1 (рис. 7.13), который установлен на теплоходе „Зоя Космодемьянская" и других судах.
На ходовом режиме котел обеспечивает перегретым паром турбогенератор, а насыщенным - вспомогательные потребители. Поверхности нагрева водяного экономайзера 5, парообразующих элементов 7 и пароперегревателя 8 выполнены из гладких -труб диаметром 29x3 мм в виде змеевиковых пакетов.
Вода подается циркуляционным насосом в экономайзер (см. рис. 4.4), где осуществлен принцип противотока, обеспечивающий некоторое уменьшение поверхности нагрева. Экономайзер в этом котле, как и в главных агрегатах, некипящего типа.
По перепускным трубам вода поступает в секцию 7 (см. рис. 7.13). В парообразующей секции использован принцип прямотока, что позволяет надежно отводить восходящим движением пароводяную смесь, повышая надежность котла.
Из коллектора 6 пароводяная смесь отводится в сепаратор пара, откуда насыщенный пар по сообщительной трубе направляется в пароперегреватель и далее на турбогенератор. Все коллекторы, примененные в агрегате, выполнены из труб диаметром 194x8 мм. Отработавшие газы от главного двигателя подводятся снизу к приемной камере 9, в которой имеется дренажная труба для слива накапливающегося гудрона или попавшей в газоход воды. Для наружной очистки поверхностей нагрева предусмотрены сажеобдувочные устройства 4. При мощности главного двигателя 8ДКРН74/160-2, равной 8830 кВт, котел имеет паропроизводительность 5200 кг/ч, рабочее давление 0,7 МПа, температуру перегретого пара 260 "С и газов перед котлом 335 °С; поверхность нагрева экономайзера 208 м2, парообразующих труб 400 и пароперегревателя 46,5 м2, масса котла сухого 26,5 т, с водой 29,5 т.
Котел КУП 1100, установленный на балктанкере „Борис Бутома", при полной паропроизводительности 9200 кг/ч дает около 7500 кг/ч перегретого пара с температурой 260 'С. При этом мощность утилизационного турбогенератора 800. кВт; поверхность нагрева котла парообразующая 778, экономайзера 324 и пароперегревателя 56 м2. Экономайзер и пароперегреватель могут использоваться автономно как парообразующие элементы с соответствующей паропроизводительностью 2900 и 800 кг/ч; масса котла сухого 40 т, с водой 41 т.
Коэффициент использования теплоты у котлов КУП660/7 и КУШ 100 около 17,6 %, а КУП700 - 22 %. В котлах КУП660/7 и КУП И 00 установлены искроулавливатели (см. рис. 7.13), которые состоят из лопаток 3, конуса 2 и сетки 1.

Рис. 7.13. Утилизационный котел КУП660/7-1.
Утилизационный котел примерно с такой же поверхностью нагрева, как у котла КУШ 100, ус-

тановлен на нефтерудовозах типа "Маршал Буденный" водоизмещением 128 тыс. т. Главный двигатель Цигельский - Зульцер 8RND90 номинальной мощностью 17 тыс. кВт (эксплуатационная мощность 14 тыс. кВт). Котельная установка состоит из трех агрегатов: утилизационного с поверхностью нагрева 1058 м2 с рабочим давлением пара 0,8 МПа и паропроизводительностью 5500 кг/ч и двух вспомогательных - один паропроизводительностью 10 т/ч и давлением 0,8 МПа, второй - 40 т/ч и 1,65 МПа. Мощность утилизационного турбогенератора около 850 кВт.
Рассмотренные котлы типа КУП имеют гладкотрубные поверхности. Утилизационный котел КУП3100 энергетической установки, работающей по газопаровому циклу, установлен на судах с горизонтальным способом гру-зообработки типа "Капитан Смирнов" водоизмещением 35,5 тыс. т. Судно - двухвальное, на каждом валу мощность около 18,4 тыс. кВт, что обеспечивает скорость 25 уз при расходе топлива около 200 т в сутки.
Рис. 7.14. Схема энергетической установки для одного вала судна типа “Капитан Смирнов”.
Энергетическая установка (рис. 7.14) одного вала представляет собой газотурбинный двигатель и теплоутилизационный контур, который состоит из утилизационного котла 11, турбины вала 4 и турбогенератора 1. Мощность от газотурбинного двигателя 2 и турбины вала 4 передается на вал через редуктор.
Котел имеет паропроизводительность 2600 кг/ч (в том числе перегретого пара 24000 кг/ч при температуре 310 °С), давление пара 1,14 МПа. Если перегретый пар расходуется только на турбину 4, ее мощность составляет 4260 кВт, при отборе (около 6000 кг/ч на турбогенератор 1 мощно-
стью 1000 кВт)-3160 кВт.
Рабочий процесс утилизационного котла определяется основными режимами СЭУ, которых предусмотрено два: „Порт" и „Море". Теплоутилизационный контур в режиме „Порт" отключается, а в режиме „Море" подключается при достижении 50 %-ной номинальной мощности газотурбинного двигателя. Это обеспечивает высокую экономичность на ходовых режимах при значительной скорости судна (около 20 уз при 50 %-ной мощности двигателя). Меньшие нагрузки и прежде всего режимы маневров требуют высокой надежности установки, что достигается отключением всего комплекса тепло-утилизационного контура, элементами которого являются также сепаратор пара 10, насосы циркуляционный 5, питательные 9 и конденсатный 7, конденсатор 6 и теплый ящик 8.
Котел КУП3100 (рис. 7.15) выполнен из змеевиковых пучков оребренных труб 22x2 мм. Ребра труб изготовлены из спиральной ленты толщиной 1 мм, которая автоматической сваркой прива-
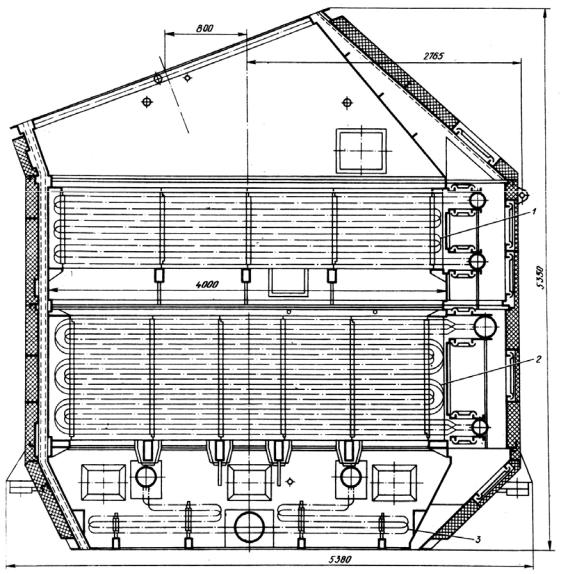
рена к трубкам, наружный диаметр оребрения 38 мм. Котел скомпонован из трех элементов: парообразующих труб 2 (поверхность нагрева 1926 м2), экономайзера 1 (1178 м2) и двухсекционного пароперегревателя 3 (268 м2).
Рис. 7.15. Утилизационный котел установки с газопаровым циклом судна типа “Капитан Смирнов”
Температура газов в патрубке перед пароперегревателем 390 °С, а за экономайзером 179 °С. Их расход 95,3 кг/с, средний коэффициент избытка воздуха α = 5,5. Котел имеет довольно высокий
коэффициент использования теплоты ~ 42 % (отнесенный к QHP ). Масса котла сухого 41,25 т, в
рабочем состоянии 42,75 т.
На стояночном режиме при неработающих утилизационных котлах судно обеспечивается паром давлением 0,5 МПа от вспомогательного котла КВВА6/5 паропроизводительностью 6000 кг/ч. Двухвальная установка позволяет при 50 %-ной нагрузке (18,4 тыс. кВт на два вала) обеспечить судну ход около 20 уз с расходом топлива в 2 раза меньше, чем при 25 уз, т.е. около 100 т в сутки. При этом на один вал будет работать газотурбинный двигатель, а на другой - паровая турбина. Компоновка цилиндрического утилизационного котла (рис. 7.16), установленного на судне „Профессор Щеголев", имеет особенности, отличающие его от обычных утилизационных котлов с принудительной циркуляцией. Сепаратор 1 скомпонован вместе с утилизационным котлом в одном агрегате. Поверхность нагрева выполнена в виде спиральных змеевиков так, как это обычно сделано в утилизационных котлах с цилиндрической компоновкой. Змеевики парообразующих труб разделены на две секции 4 и 7, поэтому водяная камера состоит из двух частей 14 и ^5, а пароводяная - из частей 5 и 6.
Вода из сепаратора может подаваться в каждую из параллельно включенных секций либо са-
мотеком по трубе 16, либо циркуляционным насосом 13, Пароводяная смесь отводится из камер 5 и 6 по перепускной трубе 3 в сепаратор, откуда насыщенный пар направляется к потребителям. Коллектор змеевикового пароперегревателя 9 разделен на две полости - насыщенного пара 12 и перегретого И. Пароперегреватель и сепаратор соединены сообщительной трубой 17. Перегретый пар может быть использован в турбине учебного электрогенератора.
В агрегате змеевики секций 4 и 7 выполнены из труб диаметром 32x3 мм, а змеевики пароперегревателя - из труб 44,5x3,5 мм. Для камер 5, 6,13, 15 и коллектора пароперегревателя применена труба 133x6 мм.
Отработавшие газы от двигателя подводятся к патрубку приемной камеры 10, а отводятся через глушитель 2. В средней части первой по ходу газов секции 7 змеевиков установлена газоперепускная заслонка 8, которая позволяет регулировать паропроизводительность парогенератора путем изменения соотношения количества газов, омывающих поверхность нагрева и протекающих, минуя ее, через центральную часть агрегата.
Полная паропроизводительность 600 кг/ч при рабочем давлении 0,5 МПа обеспечивается при горизонтальном положении заслонки. Поверхность нагрева парообразующих труб 134 м2, пароперегревателя 9м2; объем сепаратора до среднего уровня 0,31 м3, масса котла без воды 10,39 т.
Бывшая ГДР устанавливала на судах, строившихся по заказам СССР, водотрубные утилизационные котлы с принудительной циркуляцией цилиндрической (16 %) и прямоугольной (3 %) компоновки. Котлы цилиндрической компоновки (типов Ла Монт, АК, AKS) в большинстве случаев не имеют центрального байпасного газохода, и регулирование паропроизводительности осуществляется отключением либо секций, либо отдельных змеевиков с помощью игольчатых клапанов. Утилизационные котлы прямоугольной компоновки (AKSR) часто выполняют с оребренными змеевиками.
Утилизационные водотрубные котлы польской постройки (типов Л а Монт, LA, CU) выполняют как с центральным байпасным газоходом, так и без него. Конструктивно они подобны котлам постройки ГДР.
На судах сравнительно давней финской постройки (например, на теплоходе „Новгород") применялись главным образом газотрубные и комбинированные газотрубные утилизационные котлы с естественной циркуляцией (около 8 %). В последнее десятилетие фирма „Раума-Репола" разработала типоразмерные ряды вспомогательных и утилизационных котлов всех типов. Из утилизационных котлов на судах морского флота используют газотрубные котлы с естественной циркуляцией типа UNEX Н (рис. 7.17, а) паропроизводительностью 500-3000 кг/ч, комбинированные газотрубные котлы с естественной циркуляцией типа UNEX KH такой же паропроизводительности, водотрубные котлы с принудительной циркуляцией цилиндрической и прямоугольной компоновок соответственно типов UNEX P и UNEX G паропроизводительностью 500-4000 кг/ч. Особенности компоновки утилизационного котла типа UNEX G, установленного на теплоходе „Анатолий Васильев", хорошо видны на рис. 7.17, б.
Котел состоит из двух параллельно включенных по газовой стороне секций с отдельными подводами 3 и 4 питательной воды и отводами 1 и 2 пароводяной смеси. Сепаратором пара служит вспомогательный огнетрубный котел типа UNEX CH-3800 (см. рис. 7.10). Поверхности нагрева обеих секций выполнены из оребренных змеевиков 5. Ребра 6 прямоугольные, каждое ребро является общим для двух ветвей 7 змеевика. Паропроизводительность секций 1000 и 700 кг/ч при давлении 0,7 МПа. Котлы компактны, при ремонте секции легко демонтировать. При соблюдении правил технической эксплуатации котлы достаточно надежны.

Рис. 7.16. Принципиальная схема (а) и общий вид (б) утилизационного котла учебно-производственного судна типа “Профессор Щеголев”

Рис. 7.17. Принципиальные схемы утилизационных котлов финской постройки
7.7. КОТЛЫ СИСТЕМ С ОРГАНИЧЕСКИМ ТЕПЛОНОСИТЕЛЕМ
Водяной пар как теплоноситель в системах теплоснабжения имеет существенные недостатки: высокую коррозионную агрессивность; низкую температуру насыщения при малых давлениях; возможность замерзания конденсата пара в системах обогрева судовых помещений и балластных танков; необходимость жесткого контроля качества питательной воды; большие трудности и высокую стоимость технического обслуживания систем обогрева грузовых, топливных и балластных танков.
На судах, где отсутствуют турбо-приводные механизмы, целесообразно использовать в системах теплоснабжения другие виды теплоносителей, лишенные перечисленных недостатков. В последнее время в качестве таких теплоносителей используют органические жидкости на основе минеральных масел (получивших название термомасел). При использовании термомасел в судовых системах теплоснабжения снижаются трудоемкость и стоимость их технического обслуживания, упрощается техническая эксплуатация и полностью устраняется опасность замерзания теплоносителя. Кроме того, в системах с органическими теплоносителями имеется возможность обеспечить высокую точность и равномерность регулирования температуры нагреваемой среды, что в отдельных случаях имеет первостепенное значение. Поэтому термомасла можно применять на судах, предназначенных для плавания в холодных районах, на танкерах и некоторых специализированных судах.
В то же время термомаслам как теплоносителям присущи существенные недостатки: низкая термическая стойкость, что приводит к образованию на поверхностях нагрева термомасляных котлов плотных отложений нефтепродуктов, ухудшающих теплопередачу; высокая пожароопасность; высокая стоимость; отсутствие опыта (и традиций) эксплуатации' оборудования систем с органическими теплоносителями; большие трудности при ремонте сваркой; затруднение эксплуатации энергетической установки без традиционного наличия дара на судне. Все это сдерживает распространение термомасел на судах морского флота.
Основными характеристиками термомасел являются температуры вспышки (в аспекте пожароопасности), кипения (с точки зрения допустимого нагрева теплоносителя) и застывания (с позиций надежности работы систем обогрева в холодных условиях). Кроме того, чрезвычайно важным свойством термомасел является их термостойкость, определяющая максимально допустимую температуру применения, т.е. температуру, при которой начинается процесс разложения органического теплоносителя.

Рис. 7.18. Термомаслянный котел с искусственной циркуляцией.
Из отечественных органических теплоносителей можно назвать термомасла АМТ-300 и АМТ-
ЗООТ, однако на морских судах используют зарубежные термомасла: Жилотерм (на судах типа „Юрмала"); Эссотерм-500 („Николай Малахов"). По характеристикам эти теплоносители превосходят отечественные.
Термомасляные котлы впервые на нашем транспортном флоте появились на серии газовозов типа „Юрмала" (постройки ФРГ). Суда предназначены для перевозки сжиженных газов, дедвейт судна около 9655 т, грузоподъемность 8000 т (при перевозке аммиака), главный дизель имеет мощность около 7020 кВт, скорость судна 16,3 уз.
Котельная установка состоит из двух агрегатов: вспомогательного и утилизационного (постройки фирмы „Рейнсталь"), которые имеют искусственную циркуляцию, создаваемую специальным насосом термомасла.
Поверхность нагрева (77 м2) вспомогательного котла с термомасляным теплоносителем (рис. 7.18) скомпонована в виде наружного 7 и внутреннего 6 змеевиков. Котел имеет форму цилиндра диаметром 2250 мм и высотой 3045 мм, в верхней части которого размещена горелка 3 для сжигания мазута; воздух к горелке подводится по каналу 1. Термомасло поступает сверху по трубам 4 и по наружному змеевику 7 движется вниз и далее к внутреннему змеевику 6, в котором оно имеет восходящее движение к верхним элементам 5 змеевика, а затем поступает в выходную трубу 2. Змеевики 7 по всей высоте цилиндра образуют сплошную стенку, а внутренние змеевики 6 в нижней части имеют разреженный участок 9, образующий проход для дымовых газов. Продукты сгорания, образовавшиеся в топке 10, поступают в кольцевое пространство, образованное сплошными стенками змеевиков 6 и 7, а в верхней части котла газы поворачивают вниз и движутся в кольцевом пространстве между наружными змеевиками 7 и корпусом котла (движение газов показано стрелками). Отводятся газы в дымоход 8 диаметром 450 мм.
Таким образом, трубы змеевиков 7 омываются газовым потоком с двух сторон и имеют только конвективный теплообмен, а змеевики 6 воспринимают лучистую теплоту из топки 10 и получают частично конвективную теплоту со стороны кольцевого пространства между змеевиками 6 и 7. По высоте змеевики имеют соответственно по 26 и 28 витков, выполненных из труб диаметром 82,5x5
ммполностью сварной конструкций без фланцевых соединений.
Основные показатели вспомогательного котла: теплопроизводительность 1,98 МВт; давление
термомасла в змеевиках около 1 МПа, температура термомасла на входе в котел 140, а на выходе из него 180 "С; количество масла в котле 1,27 м3 (1280 кг); масса котла без масла 5400 кг.
Утилизационный котел в этой установке также змеевиковой конструкции. Трубы 44,5x3,2 мм с прямоугольными ребрами приварены точечной сваркой, змеевики (21 ряд) приварены к двум коллекторам (входа и выхода масла). Котел имеет прямоугольную компоновку (длина 2100 мм, ширина 1225, высота 1620 мм), теплопроизводительность его 1,6 МВт, поверхность нагрева 255 м2.
Термомасляная система вспомогательного и утилизационного котлов общая с одинаковыми давлением и температурой теплоносителя. Температура газов дизеля перед котлом около 350 "С. Теплопроизводительность кегельной установки определяется расходом теплоты, которая необходима потребителям на данном судне. Для газовоза основными потребителями теплоты являются системы периодического подогрева сжиженного газа, подогрева топлива, балласта и др.
ВДальневосточном морском пароходстве эксплуатируется 10 судов серки „Николай Малахов", на которых применена аналогичная система теплоснабжения, но с более совершенной системой регулирования - заданные значения температур во всех потребителях теплоты поддерживаются автоматически - с использованием бортовой ЭВМ. Максимальная температура термомасла 240 °С, минимальная 140 "С.
ВСеверном морском пароходстве в 1990 г. вступило в эксплуатацию первое судно серии лесовозов типа „Механик Ярцев", на которых применена система теплоснабжения с термомасляным теплоносителем марки „Термоойл". Принципиальных отличий от рассмотренных данная система не имеет, только утилизационный котел - цилиндрический, выполнен из спиральных змеевиков с центральным байпасным газоходом.
На некоторых судах, работающих в северных широтах, в системах отопления иногда используют два теплоносителя - водяной пар и термомасло, причем термомасло нагревается водяным паром, полученным в обычных паровых котлах. К таким судам относятся продуктовоз „Вентспилс", суда серии „Норильск" (проект СА-15) и ледоколы типа „Капитан Сорокин", на которых в системах отопления используется термомасло. Опыт эксплуатации этих судов показал, что применение

термомасел в значительной степени снижает трудозатраты на обслуживание систем отопления, обеспечивая комфортные условия обитания в любых условиях.
7.8. КОТЛЫ В СИСТЕМАХ ТЕРМИЧЕСКОГО ОБЕЗВРЕЖИВАНИЯ СУДОВЫХ ОТХОДОВ
Методы обезвреживания. Важность проблемы предотвращения загрязнения моря с судов очевидна. На всех судах мирового флота предусматриваются те или иные технологии обезвреживания судовых отходов. Однако комплексного решения проблемы пока не существует из-за трудности соединения различных устройств в единую систему обезвреживания разных по физикохимическим характеристикам судовых отходов - нефтесодержащих и сточных вод, мусора. Поэтому практикуются различные методы обезвреживания отходов: обработка и сброс в море, накопление и сдача на береговые установки, обработка и термическое обезвреживание на судне. Наиболее полно решает эту проблему комплексная технология обезвреживания судовых отходов (рис. 7.19), центральным элементом которой является установка для термического обезвреживания (сжигания). В качестве такого элемента могут быть использованы инсинераторы различных типов и паровые котлы, оборудованные специальными устройствами для подготовки отходов к сжиганию.
Сжигание отходов в паровых котлах позволяет утилизировать теплоту, образующуюся при сгорании. Кроме того, при этом нет необходимости устанавливать еще и инсинератор, в котором на сжигание твердых отходов затрачивается топливо. Однако сжигание отходов в котлах требует оборудования их дополнительными устройствами, может явиться причиной интенсификации процессов наружных загрязнений и коррозии, усложняет обслуживание котлов. К тому же экономический выигрыш от утилизации отходов не всегда окупает расходы на переоборудование котлов. Именно поэтому в настоящее время для сжигания твердых отходов на судах используются главным образом инсинераторы. Что же касается отходов нефтепродуктов (нефтесодержащих вод), то после соответствующей их обработки в гомогенизаторах они могут сжигаться в топках судовых котлов (см. п. 3.3).
Рис. 7.19. Принципиальная схема технологии обезвреживания судовых отходов.

Инсинераторы. В судовой практике используют разные компоновки инсинераторов. На балктанкерах типа „Борис Бутома", судах с горизонтальной грузообработкой типа „Механик Евграфов" и других установлены инсинераторы типа ASWI-400 фирмы „Атлас" (Дания). Агрегат состоит из элементов, которые позволяют сжигать нефтепродукты и шлам отходов сепарации топлива и масла, остатки, отделяемые из сточных льяльных вод, и твердые отходы бытовых помещений, камбуза и машинного отделения. В инсинераторе можно сжечь в сутки (при 20 ч работы) нефтеостатков 1750 л, шлама сточных и фекальных вод 1250 л, твердых отходов 500 кг за одну зарядку при сжигании в течение 4 ч.
Отечественной промышленностью освоен серийный выпуск судовых инсинераторов СП-50, СП-25 и СП-10 (СП - судовая печь, цифра - производительность по мусору, кг/ч), которые по своим характеристикам не уступают современным зарубежным конструкциям.
Рис. 7.20. Инсинератор.
Инсинератор типа GS-500 (рис. 7.20) является довольно сложным агрегатом. Основной его элемент - топка, которая состоит из первичной 6 и вторичной 1 камер сгорания, разделенных перегородкой 5 из огнеупорного кирпича. Первичная камера через питатель 4 наполняется твердыми отходами, где они подвергаются пиролизу. Образовавшиеся продукты поступают в камеру сгорания 1. Остатки в виде золы удаляют обычно вручную. Заданный температурный режим поддерживают с помощью полностью автоматизированной горелки 3, сжигающей дизельное топливо. Дополнительный расход сравнительно невелик и зависит от состава сжигаемых отходов. Через грязевую горелку подаются нефтеос-татки и шламы сточных вод специальным шламовым дозирующим насосом. Смесь нефтепродуктов и воды распиливается сжатым воздухом давлением около 0,5-1 МПа. Продукты сгорания из инсинератора через патрубок 2 удаляются дымососом, создающим некоторое разрежение, чтобы предотвратить попадание дыма в помещение.
Котлы для обезвреживания отходов. Особенности компоновки таких котлов рассмотрим на примере устройства вспомогательного огнетрубно-во-дотрубного котла типа AQ-10 шведской фирмы „Ольборг". В отличие от котлов этой фирмы котел AQ-10 имеет комбинированную топочную камеру (рис. 7.21), состоящую из двух отсеков, разделенных перегородкой 3 с отверстиями. Основной отсек 2 предназначен для сжигания топлива, жидких нефтеотходов и горючих газов, поступающих .из утилизационного отсека 6, где осуществляется пиролиз твердых отходов.
Жидкие нефтеотходы перед подачей на ротационную форсунку 1 обрабатываются (гомогенизируются) в циркуляционном контуре, состоящем из рабочей цистерны, комбинированной мельницы, центробежного насоса, подогревателя и дозирующего насоса с регулятором.
Твердые отходы (мусор) в количестве 4-6 мешков (объемом около 0,05 м3, массой до 20 кг) загру-

жают в утилизационную камеру 5 через специальный питатель 6 барабанного типа, снабженный жаропрочными отражателями-рефлекторами. Отходы при загрузке перекрывают часть отверстий 4 в разделительной стенке 3 и ограничивают тем самым доступ воздуха в утилизационную камеру, в результате чего в ней идет процесс пиролиза отходов, а образующиеся горючие газы поступают в основную топочную камеру (вследствие разрежения в ней). Остатки отходов в виде углей и смолистой жидкости догорают в утилизационном отсеке с образованием золы (10-15 % массы отходов).
Рис. 7.21. Котел - инсинератор
Опыт эксплуатации котлов типа AQ-10 (по данным фирмы) свидетельствует о том, что благодаря утилизации теплоты отходов экономится до 30 % котельного топлива, а затраты на установку котла и системы подготовки отходов окупаются за 3 года.
Здесь приведены лишь элементарные сведения о назначении и устройстве инсинераторов и котлов для сжигания судовых отходов. Подробные данные о характеристиках рабочих процессов этих агрегатов можно найти в специальной литературе.
7.9. АРМАТУРА И ДРУГИЕ ЭЛЕМЕНТЫ КОТЛА
Общие сведения. Арматура предназначена для обеспечения надежной и безопасной работы котла. Размещение арматуры на котле и ее количество определяются требованиями морского Регистра.
На котле устанавливают предохранительные клапаны и клапаны для подвода питательной воды, топлива, для отвода пара к потребителям. Для наблюдения за нормальной и экономичной работой котла предусмотрены контрольно-измерительные приборы (манометры, термометры и др.) и другая дополнительная арматура - клапаны продувания, выпуска воздуха, отбора пробы и ввода необходимых присадок, обеспечивающих требуемый водный режим, приборы для определения расходов рабочих сред (воды, пара, топлива, воздуха) и др.
Рассмотрим конструктивные особенности главных элементов арматуры: стопорного, питательного и предохранительных клапанов и водоуказательных приборов.
Клапаны. Конструкция главного невозвратно-запорного углового стопорного клапана (рис. 7.22) котлов КВГ34 и КВГ25 является обычной для других агрегатов. Клапан устанавливают на специальном фланцевом штуцере коллектора пароперегревателя, к которому его присоединяют с помощью фланца 12. Через угловой патрубок 13 клапан сообщается с трубопроводом пара.
Температура перегретого пара перед клапаном 470 °С, поэтому корпус 10 и крышка 6 выполнены из хромомо-либденовой стали марки 20ХМЛ. Из легированной жаропрочной стали изготовлены тарелка 8 и седло 11, которые, кроме того, имеют специальные наплавки, повышающие долговечность их сопряженных рабочих поверхностей. Для уменьшения усилия, необходимого для
закрытия клапана, предусмотрены маховик 1 и зубчатая передача 2 к ходовой гайке 4, перемещающей втулку 16; последняя имеет шпоночное соединение со стопором-указателем 15. Шлицы в стойках крышки 6 обеспечивают стопору 15 и, следовательно, втулке 16 только поступательное движение вверх или вниз. Шток 5, перемещающий тарелку 8 с гайкой 9, соединен с втулкой 16 прессовой посадкой. Для улучшения условий работы клапана втулка выполнена из нержавеющей стали 2X13, а гайка 4 -из бронзы АМЦ9-2.
Для дистанционного управления клапаном на верхнем и нижнем концах валика маховика предусмотрены квадраты. Для уплотнения штока 5 в корпусе крышки используют сальниковую набивку 14, выполненную из асбестового шнура с добавкой чешуйчатого графита. Между фланцами крышки 6 и корпусом 10 установлена уплотняющая тонкая прокладка 7. Колпачковая масленка 3 служит для периодического подвода консистентной смазки к ведущему валику передачи 2.
Питательные клапаны, установленные на котле КВГ25, КВГ34 и некоторых других, имеют аналогичную конструкцию. Запорный клапан (рис. 7.23, а) может управляться дистанционно с помощью специальных штоков, которые присоединяют к квадратам валика. Конструкция клапана и принцип действия сходны со стопорным клапаном (см. рис. 7.22).
Невозвратный клапан (рис. 7.23, б) в соответствии с требованием морского Регистра размещают перед запорным питательным клапаном, установленным непосредственно на барабане котла. Это объясняется тем, что невозвратный клапан изнашивается быстрее и при ремонте должен быть разобщен с барабаном при помощи запорного клапана. Конструкция тарелки / и седла 2 обоих клапанов одинаковая, остальные элементы клапанов понятны из чертежа (с учетом рис. 7.22). Направления движения питательной воды указаны стрелками. В соответствии с требованиями Регистра на котле устанавливают по два запорных и невозвратных питательных клапана.
Главный предохранительный сдвоенный клапан (рис. 7.24, а) применяют для современных су-
довых котлов и устанавливают непосредственно на пароводяном барабане. Клапан - непрямого действия, благодаря чему обеспечивается малая степень нечувствительности (5-6 % рабочего давления пара). Принцип непрямого действия осуществляется благодаря тому, что клапаны 7 передвигаются серводвигателем. Импульсное давление пара от сдвоенного контрольного клапана передается по трубам 3 в полость 5 под поршнем 2 серводвигателя. Если давление в барабане больше допустимого, усилие на поршень со стороны полости преодолевает усилие, создаваемое пружиной 4, и клапан 7 открывается для пропуска пара в направлении от патрубка 6 к патрубку 1. Когда давление в барабане уменьшается до заданного значения, импульсный клапан закрывается, давление в полости падает и клапан закрывается усилием пружины 4.
Предохранительный одинарный клапан, также являющийся главным, устанавливают на коллекторе пароперегревателя рядом с главным стопорным клапаном. По конструкции и принципу действия этот клапан аналогичен главному сдвоенному. Одинарный клапан имеет меньшее проходное сечение. Контрольный клапан для рассматриваемого главного клапана также одинарный, его устанавливают на пароводяном барабане.
Одну из конструкций контрольного клапана (рис. 7.24, б) фланцем 10 устанавливают на пароводяном барабане. Клапан 11 удерживается в закрытом состоянии действием пружины 8, отрегулированной на определенное давление в пароводяном барабане. Если давление превысит в барабане требуемое, клапан 11 откроется и пар по каналу 9 передаст импульсное давление в трубу 3 и в полость 5 главного предохранительного клапана.
Предохранительный клапан на пароперегревателе должен подрываться с некоторым опережением по отношению к главному сдвоенному клапану, установленному на пароводяном барабане. Это обеспечивает охлаждение труб перегревателя паром также и в момент подрыва предохранительного клапана. Выполнением указанного условия и объясняется установка предохранительного клапана у выходного патрубка коллектора пароперегревателя.
Предохранительные клапаны по Правилам Регистра должны регулироваться таким образом, чтобы максимальное давление при действии предохранительных клапанов не превышало более чем на 10 % рабочее давление. Для вспомогательных котлов и сепараторов утилизационных агрегатов, имеющих невысокое рабочее давление пара, применяют более простые предохранительные клапаны прямого действия, одинарные и сдвоенные.

Рис. 7.22. Главный стопорный клапан.

Сдвоенный прямодействующий клапан имеет конструкцию, аналогичную одинарному клапану, и отличается от него только размерами и тем, что в одном корпусе скомпонованы два одинаковых клапана. Эти клапаны имеют простую конструкцию, однако принцип действия обусловливает большую их нечувствительность. Для ж вспомогательных котлов этот недостаток не столь существен, зато простота конструкции является их большим преимуществом.
Рис. 7.23. Питательные клапаны.
Элементами предохранительного сдвоенного клапана прямого действия (рис. 7.25) являются собственно клапан 1, гнездо седла 2, пружина 3 и рычаг 4 для ручного подъема клапана.
Водоуказательные приборы. Каждый котел оборудуют двумя водоуказательными колонками, обеспечивающими требуемую -надежность в эксплуатации. Колонка сообщена с водяным и паровым пространствами барабана специальными клапанами (запорными и продувания), управляемыми дистанционно с помощью специальных тяг.
Важным элементом колонки является рамка с установленными в ней прозрачными слюдяными пластинами или специальными стеклами, прижимаемыми к рамке упорными планками с помощью болтов. Улучшает видимость уровня воды на рамке осветительная головка с электрической лампой. Начинают применять специальные выпуклые стекла (линзового типа).
Водоуказательная колонка котлов типа КВГ25К и КВГ34К (рис. 7.26) состоит из корпуса 2, в котором закреплен прозрачный материал. Для улучшения видимости уровня имеется осветительная лампа, установленная в головке 4. Уровни верхний (ВУ), средний (СУ) и нижний (НУ) отмечены планкой 1. Водоуказатель с паровым и водяным пространствами барабана сообщается клапанами соответствующих головок 3 и 6. Тяга 5 служит для ручного привода клапанов. Рабочая длина рамки водоуказательной колонки составляет примерно 300 мм.
Обычно колонки устанавливают непосредственно на пароводяном барабане, который в современном судовом главном котле находится на высоте 5-6 м и более от пульта управления. Это создает известные трудности для наблюдения за уровнем воды. Кроме того, в трубинной установке за уровнем воды необходимо следить из ЦПУ, что особенно важно при режимах маневрирования судна, поэтому водоуказатели должны быть расположены ниже, чем обычно, или обеспечивать показания дистанционно.
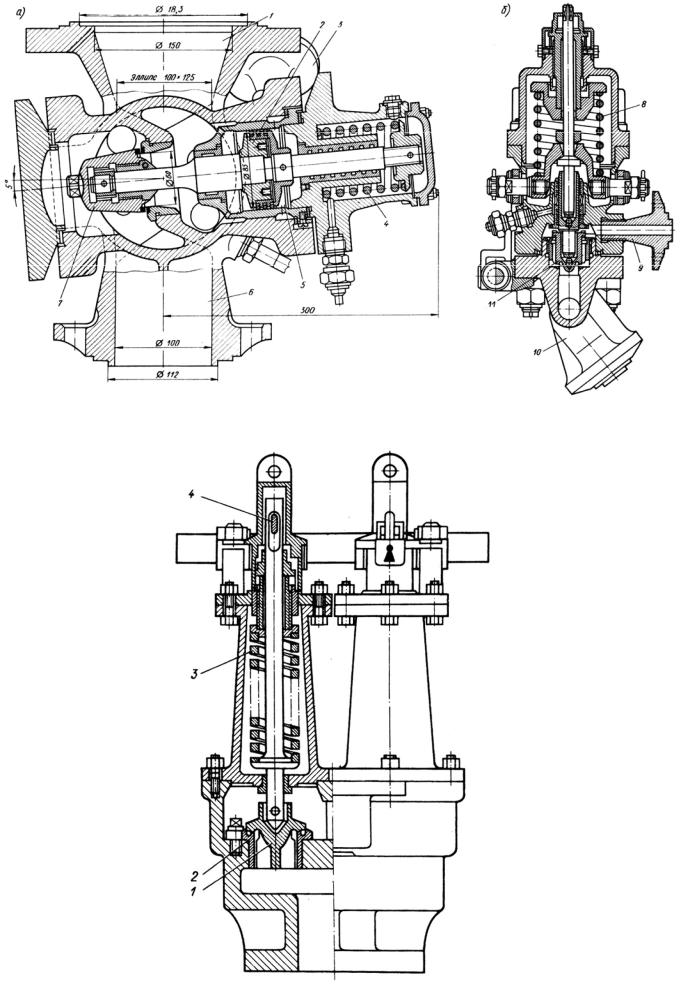
Рис. 7.24. Клапаны – главный предохранительный (непрямого действия) и контрольный
Рис. 7.25 Предохранительный сдвоенный клапан прямого действия

Рис. 7.26. Водомерная колонка (водоуказатель).
Известны указатели нескольких типов, работа которых основана на принципе использования жидкости тяжелее воды. Есть также сниженные указатели - электрические и оптические.
Основной недостаток приборов, в которых используется тяжелая жидкость (тетрахлорид, четыреххлористый углерод, ртуть), - повышенная инерционность в показаниях уровня, особенно при резких изменениях нагрузки. Кроме того, из-за протечек в неплотностях соединений прибор может давать неверные показания.
Для котлов отечественной постройки применяют электрические указатели. Измерительным элементом в таком указателе служит диафрагменное устройство, применяемое для регуляторов питания, а показывающий элемент представляет собой обычный логометр, используемый во многих электроизмерительных приборах, например в электрических термометрах. Указатель выносят на щит приборов в ЦПУ. Один из таких приборов применен в установках с котлами КВГ34К.
Из оптических приборов следует отметить указатель типа перископа, наведенного на водоуказательную колонку. Однако этот прибор сложен и не всегда удобен в эксплуатации, поэтому он не нашел широкого применения в судовой практике.
Контрольно-измерительные приборы. Для обеспечения надежной и эффективной работы судовых котлов во время эксплуатации необходимо непрерывно или периодически контролировать (в соответствии с Правилами технической эксплуатации судовых паровых котлов) следующие параметры и величины: уровень воды, давление перегретого, насыщенного и охлажденного пара; температуру перегретого и охлажденного пара; паропроизводительность (при наличии параметров); давление и температуру питательной воды, и температуру воды после экономайзера; давление и температуру топлива, поступающего к горелкам; расход топлива и его уровень в расходных цистернах; давление и температуру воздуха перед топкой; температуру и химический состав уходящих газов (при наличии штатного газоанализатора); химический состав котловой и питательной воды; расход воды (суточный и по вахтам). Кроме того, необходимо вести наблюдение за дымностью, которая характеризует качество процесса сжигания топлива.
Для выполнения указанных требований судовые котельные установки должны быть снабжены соответствующей арматурой и контрольно-измерительными приборами.
Взависимости от определяемой величины условно можно указать следующие приборы для измерения: давления (манометры, барометры), разрежения (тягомеры), температуры (термометры, термопары), уровня (указатели уровня), расхода (расходомеры, счетчики суммирующие), качества воды и пара (солемеры, рН-метры, кислородомеры), состава дымовых газов (газоанализаторы), густоты газов (дымомеры), термических расширений и вибрации (указатели перемещений и виброметры) и некоторых других показателей.
Можно отметить, что указанные приборы обычно подразделяют на несколько групп: по назначению — технические (рабочие), контрольно-образцовые и эталонные; по характеру измерения - показывающие, самопишущие и суммирующие; по принципу действия - механические, электрические, гидравлические, химические и др.; по условиям использования - штатные и переносные, местные и дистанционные, оперативные и учетные с определением показания за какой-то отрезок времени (вахту, сутки).
Требования к размещению и минимальному числу приборов определены Правилами Регистра. На каждом котле должно быть установлено не менее двух манометров, соединенных с паровым пространством отдельными трубами. К штатным обязательным приборам относятся и водомерные колонки (не менее двух на пароводяном барабане), а также приборы для измерения температуры, установленные на пароперегревателях и экономайзерах (ртутные термометры и термопары). Штатные приборы размещают на приборных щитах в ЦПУ и у котла (местный щит).
Число измеряемых параметров котла зависит также от того, используются системы технической диагностики или нет. В настоящее время разрабатываются диагностические системы, для эффективной работы которых потребуется значительно больше измерительных приборов и датчиков, чем это предусматривается требованиями Регистра и Правилами технической эксплуатации.
Взаключение отметим, что здесь приведены только общие соображения по комплектации котлов контрольно-измерительными приборами. Наиболее полная информация об измеряемых параметрах и применяемых приборах содержится в описаниях конструкций и инструкциях по обслуживанию конкретных котлов. Что же касается теории, принципов действия и конструктивного исполнения приборов, то они изучаются в специальном курсе.

Опоры, каркас и обшивка. Надежная и эффективная эксплуатация котлов, а также обеспечение нормальных условий обслуживания их в значительной степени зависят от правильной установки агрегатов на судне и от достаточной жесткости каркаса и изоляции его обшивки.
Котел устанавливают опорами на судовой фундамент / (рис. 7.27). Для обеспечения правильного расширения агрегата, исключающего появление опасных термических напряжений в каркасе, обшивке и других его элементах, предусматриваются опоры подвижные и неподвижные. Общее число опор может быть 4 - 8 (редко больше).
Рис. 7.27. Расположение и крепление опор коллекторов и корпусов котла.
На рис. 7.27 показано общее расположение опор котла КВГ34К, которое является в значительной степени аналогичным и для других агрегатов морских судов.
Котел КВГ34К имеет восемь опор. Только одна опора 3 экранного коллектора 2, расположенная со стороны переднего фронта, является неподвижной. Остальные семь опор - подвижные. Опоры 5, 6 и 9 соответственно экранного 2, пароперегревателя 7 и водяного 8 коллекторов ориентированы в основном для перемещений в продольном направлении, а опоры 4 корпуса агрегата - в поперечном. Каждая подвижная опора допускает также перемещения и в других направлениях. Особенность конструкции подвижных опор 6 коллектора пароперегревателя 7 состоит в том, что в каждой из них предусмотрены по два ролика, которые позволяют облегчить изъятие пароперегревателя из газохода парогенератора (в сторону заднего фронта), если это потребуется для ревизии или ремонта. На судне для этого специально предусмотрены место и рельсы, по которым движутся ролики.
Рассмотренная схема расположения опор проверена в течение нескольких лет эксплуатации в судовых условиях, что свидетельствует о рациональности принятого их конструктивного типа и общего количества.
Каркас котла служит для обеспечения требуемой прочности конструкции крепления обшивки и изоляции, позволяющих образовать необходимую конфигурацию газоходов ' агрегата. Топочная камера характеризуется довольно высокими температурами газов: поэтому для ее стен применяют часто изоляцию в виде кирпичной кладки.
На рис. 7.28 приведен общий вид возможной компоновки размещения кирпичной кладки на фронте и на других стенках котла, а также даны отдельные узлы крепления элементов кладки. Для рассматриваемого агрегата применены три основных типоразмера кирпичей (160 х 160 х 100; 160 х 160 х 140) и фасонный кирпич для фурм. Фурмы 2 для отечественных котлов серийных судов выполняют с разными размерами в зависимости от типа и числа горелок, установленных на фронте. Все огнеупорные кирпичи I выполнены из шамота. Каждый кирпич, обычный и фурменный, крепят отдельным болтом. Укажем для примера, что общая масса кирпичной кладки котла КВГ34К составляет около 11,6 т, а КВГ25-9,5т.
Для изоляции стен обшивки барабанов и коллекторов применяют асбест, нъювелъ и совелит в виде картона, плит, матрацев и обмазки. Следует указать, что изолируемые поверхности перед укладкой на них совелитовых плит покрывают совелитовой обмазкой толщиной 5 мм. Совелитовые плиты после укладки стягивают проволокой. Матрацы сшивают и простегивают асбестовой ниткой. Стыки матрацев сшивают латунной проволокой. Металлическая обшивка плотно прилегает к изолированным поверхностям. Суммарная масса изоляции пароводяного барабана и коллекторов (например, котла КВГ34) около 2000 кг.
7.10. СИСТЕМЫ АВТОМАТИЧЕСКОГО РЕГУЛИРОВАНИЯ, СИГНАЛИЗАЦИИ И ЗАШИТЫ КОТЛА
Режимы работы. В соответствии с назначением котла процессы, происходящие в нем, связаны с непрерывным подводом топлива, теплоты, воздуха, питательной воды и отводом образовавшихся продуктов сгорания и пара. Для нормального действия котла требуются вполне определенные во времени соотношения между количествами и параметрами указанных рабочих сред. В связи с этим работа котла может происходить как при постоянном, так и при переменном режиме.
Постоянный (стационарный) режим характеризуется материальным и тепловым равновесием (подводимых и отводимых рабочих сред), постоянством во времени количества веществ (сред) и их параметров - давлений, температур, а также уровня воды в котле.
Переменный (нестационарный), или переходный, режим от одного постоянного режима к другому, тоже постоянному, вызывается нарушением постоянства установившегося равновесия вследствие либо внешних, либо внутренних возмущений. Внешние возмущения связаны с изменением расхода пара на главные и вспомогательные механизмы, т.е. надо менять паропроизводительность. Наиболее существенными внутренними возмущениями котла являются изменение расхода топлива и качества его сжигания, а для утилизационной установки - смена режима работы главного двигателя (дизеля или ГТУ).

Рис. 7.28. Расположение кирпичной кладки котла.
При небольших возмущениях котел без постороннего вмешательства (ручного или автоматического) может перейти к новому стационарному режиму благодаря тепловой инерционности и так называемому самовыравниванию (например, по давлению пара). В случае значительных возмущений, особенно внешних, требуется принудительно восстанавливать равновесие путем соответствующего регулирования элементов и устройств, обеспечивающих необходимые количества рабочих сред и их параметры. Автоматизация котла и дает возможность обеспечить указанные процессы в основном без вмешательства обслуживающего персонала.
Автоматическое регулирование судовых котлов должно обеспечивать: соответствие количеств подаваемой питательной воды и отводимого пара и поддержание уровня воды в заданных пределах; соответствие расхода топлива (теплоты) количеству отводимого пара и таким образом поддержание давления пара в заданных пределах; соответствие температуры перегретого пара количеству отбираемого пара на главный двигатель.
Для решения рассматриваемых задач судовые котлы оборудуют системами автоматического регулирования: главные котлы - процессов питания и горения (в некоторых установках может быть автоматизирован и третий процесс - перегрев пара), вспомогательные котлы - питания и горения, утилизационные КУ - подачи питательной воды в сепаратор и поддержания заданного давления пара (регулирование паропроизводительности). На теплоходах топливная и утилизационная части котельной установки могут иметь общую систему автоматизации.
Система автоматического регулирования процесса питания. Основным регулируемым па-
раметром в этой системе является уровень воды в пароводяном барабане главного или вспомогательного котла и в сепараторе утилизационной установки.
Вэлементарной схеме регулирования уровня воды в барабане 1 (рис. 7.29, а) автоматический регулятор уровня состоит из измерительного элемента 2 (в данной схеме поплавкового типа), устройства связи (серводвигателя) 3 для передачи усилия и исполнительного органа - автоматического питательного клапана 4, который установлен на питательном трубопроводе 5.
Вэтой схеме измеряется только один регулируемый параметр - уровень воды h, его же используют для управления автоматическим питательным клапаном. Такая система является одноимпульсной и имеет статическую характеристику (рис. 7.29, б), т.е. зависимость уровня воды от паропроизводительности h(DK). Для подачи большего количества воды в барабан необходимо уве-

личить открытие автоматического питательного клапана, а это возможно, если поплавок 2 опустится, т.е. если уменьшится уровень воды в барабане. Если обозначить при минимальной DKmin максимальной DKmax и номинальной DK0 паропроизводительности соответственно уровень воды hmin, hmux, ho, можно ввести понятие о неравномерности регулятора уровня.
Рис. 7.29. Принципиальная схема автоматического регулирования уровня воды
вбарабане.
Вданном случае относительное изменение уровня воды при полном статическом изменении паропроизводительности называют коэффициентом неравномерности регулятора уровня (доли
единицы или %): |
|
|
δ = hmax −hmin |
(7.1) |
|
|
h |
|
|
|
Существуют и более сложные системы - двух- и даже трехимпульсные. Применение той или иной системы определяется свойствами самого объекта регулирования - котла, и прежде всего его инерционными характеристиками.
Аккумулирующая способность котла зависит от количества теплоты, которое может накапливаться в паре, воде, кирпичной кладке, металле труб и барабанов. Наибольшее количество теплоты может аккумулировать вода, которая содержится в парообразующих элементах котла. Количественным показателем аккумулирующей способности, как отмечалось, является водосодержание, характеризующее такое важное свойство, как инерционность.
Рис. 7.30. Изменение уровня воды в барабане при переходном режиме работы котла.
При переходном режиме уровень воды в барабане изменяется примерно следующим образом. При набросе нагрузки (увеличении DK) падает давление в барабане рк, что вызывает образование пузырьков пара, и уровень воды увеличивается с h2 до h1 (рис. 7.30, о). Такое насыщение водяного объема барабана пузырьками пара при набросе нагрузки называется явлением набухания. При сбросе нагрузки наблюдается обратная картина: в барабане давление рк повышается и часть паровых пузырьков в водяном объеме конденсируется, следствием чего является снижение уровня (рис. 7.30, б). После того как переходный режим закончится, новые уровни воды в барабане устанавливаются в соответствии со статической характеристикой регулятора (например, как показано на рис. 7.29, б). Исходя из рассмотренного условия можно оценить действие одноимпульсной сис-

темы регулирования уровня при переходном режиме.
Вмомент наброса нагрузки из-за набухания уровня автоматический питательный клапан закрывается, а при сбросе нагрузки - открывается. Таким образом, при переходном режиме котла одноимпульсный регулятор действует наоборот: в момент увеличения нагрузки уменьшает подачу воды в барабан, а при сбросе нагрузки повышает ее.
Котел с большим водяным объемом |может иметь настолько большие водосодержание и соответствующую аккумулирующую способность, что значительное несоответствие количества подаваемой питательной воды и отбираемого пара в переходном режиме мало сказывается на изменении уровня в барабане. В таком котле одноимпульсный регулятор уровня может обеспечить вполне надежную работу.
Вкотле с малой аккумулирующей способностью несоответствие в подаче воды и отводе пара вызывает быстрое и значительное изменение уровня воды в переходном режиме (повышенное значение ∆h - см. рис. 7.30). Для обеспечения надежной работы такого агрегата при стационарном
ипереходном режимах регулирование питания должно осуществляться по двум импульсам: уровню воды и количеству отбираемого пара (по нагрузке). Главные водотрубные котлы с естественной циркуляцией, применяемые в установках морских судов, имеют умеренные значения водосодержания, что позволяет применять для них систему автоматического регулирования питания двухимпульсного типа. Более сложные трехимпульсные системы применяют лишь в некоторых специальных конструкциях котлов с очень малым водосодержанием. Это в основном относится к котлам некоторых стационарных установок.
Рис. 7.31. Принципиальная схема САР питания с двухимпульсным регулятором уровня.
В системе регулирования питания с двухимпульсным регулятором уровня (рис. 7.31) импульс по уровню h поступает от его измерителя 3, а импульс по количеству отбираемого пара DK - от измерителя 12; устройство 4 суммирует оба импульса и управляет автоматическим питательным клапаном 5. Вода в барабан 2 подается питательным насосом 7, который в данной схеме приводится в действие паровой турбиной 8. Нагрузка котла по пару измеряется по перепаду давления, определяемому сопротивлением на участках барабана 2, перепускной трубы 1, пароперегревателя 14 и главного паропровода 13. Требуемое количество воды, подаваемой по трубопроводу 6, регулируется расходом пара на турбину 8, для чего на трубопроводе пара установлен автоматический клапан 9, импульс к которому поступает по линии 10 от измерителя 11 перепада давления Ар на питательном клапане. Таким образом, система автоматизации процесса питания состоит из автоматического регулятора уровня воды и турбопитательного насоса с автоматическим регулятором его подачи. Питательный насос может иметь также электрический привод. В современных установках для повышения экономичности и упрощения оборудования питательный насос может иметь непосредственный привод от главного турбоагрегата (насос навешенного типа).

Рис. 7.32. Принципиальная схема САР процесса горения топлива.
Рассмотренная особенность действия системы автоматизации процесса питания показывает, что система предназначена прежде всего для обеспечения надежности работы котла, облегчения условий его обслуживания и незначительно влияет на экономичность.
Система автоматического регулирования процесса горения. Задача системы состоит в обеспечении соответствия расхода топлива количеству отбираемого на потребители пара. Кроме того, для каждой нагрузки котла система автоматического регулирования горения должна обеспечивать оптимальное соотношение между расходами топлива и воздуха, подводимыми в топку. При этом количественный показатель процесса горения топлива - оптимальный коэффициент избытка воздуха - должен быть минимальным в широком диапазоне изменения нагрузок котла. Это показывает, что данная система предназначена для обеспечения надежности, экономичности и облегчения обслуживания котла.
Вслучае работы котла на систему инертных газов танкера должно обеспечиваться требуемое содержание кислорода в уходящих газах. Расход топлива изменяется топливорегулирующим клапаном, а регулирование количества подаваемого воздуха -путем изменения частоты вращения вентилятора или перемещением воздухорегулирующих заслонок. Основным импульсом является давление пара, которое представляет в данной системе регулируемый параметр, измеряемый главным регулятором.
Всистеме автоматического регулирования горения (рис. 7.32) главный регулятор 4 измеряет давление пара в главном паропроводе 3, которое является импульсом, воздействующим на подачу топлива и воздуха (на схеме это условно показано элементом 7). Топливорегулирующий клапан 5, установленный на топливном трубопроводе 6, получает импульс от регулятора 7 соотношения воздух - топливо. Серводвигатель 8 управляет воздухорегулирующими заслонками вентилятора 9, который подает воздух к топочным устройствам 10. пар из барабана 1 поступает в пароперегреватель 2, сопротивление в котором возрастает пропорционально квадрату расхода пара. В связи с этим целесообразно отбирать импульс по давлению пара за пароперегревателем (как показано на рис. 7.32), где имеется ощутимое падение давления при повышении нагрузки. При любых изменениях нагрузки главный регулятор 4 поддерживает примерно постоянным давлением пара либо в магистрали 3, либо в барабане 1. Достигается это путем поддержания требуемого соотношения расходов топлива через клапан 5 и воздуха, подаваемого вентилятором 9. Рассмотренная на рис.
7.32общая схема является характерной в основном для главных котлов. Для вспомогательных котлов применяют более простые системы автоматизации процесса горения. Это объясняется тем, что вспомогательные котлы часто не имеют пароперегревателя и пар от них расходуется на общесудовые нужды и другие потребители, режим работы которых упрощает автоматизацию котлов.
Для вспомогательных котлов применяют иногда так называемую позиционную систему регулирования, при которой давление пара изменяется в определенных заданных пределах ступенчато. При достижении верхнего предела давления пара подвод топлива выключается, а при снижении давления до нижнего предела (вследствие расхода пара на потребители) происходит включение расхода топлива. Примером такой системы атвоматизации вспомогательных котлов является оборудование их топочным устройством типа Монарх.
Система автоматического регулирования температуры перегретого пара. Температура перегретого пара, которую должен обеспечить пароперегреватель, определяется как типом главного (двигателя, так и режимом работы пароэнергетической установки.
Всудовых и стационарных установках применяют несколько принципиально различных систем регулирования температуры перегретого пара, большинство из которых автоматизиро-ванны. Однако почти все системы в зависимости от компоновки собственно пароперегревателя и главного элемента регулирования могут быть разделены на две основные группы, предусматривающие принципиально различные способы регулирования, - газовый и паровой.
С помощью регулирования газовым способом можно изменять тепловосп-риятие поверхности нагрева пароперегревателя в основном путем изменения количества дымовых газов, протекающих через газоход пароперегревателя, соответственно расходу перегреваемого пара и требуемой его температуре. Газовое регулирование осуществляется обычно с помощью специальных шиберов, устанавливаемых в газоходах.
При использовании газовых байпасных шиберов тепловосприятие поверхности нагрева регулируют главным образом изменением коэффициента теплоотдачи от газов к трубам, так как при любых манипуляциях с шиберами меняется скорость потока газов. Для повышения надежности приходится устанавливать несколько шиберов, размеры которых выбирают исходя из условий минимально допустимой их деформации. Кроме увеличения надежности, несколькими шиберами меньших размеров легче управлять, а также получать больший диапазон изменения тепловосприятия поверхности нагрева пароперегревателя. Байпасными шиберами, как правило, управляют вручную, хотя можно и автоматизировать этот процесс.
Для регулирования температуры перегретого пара применяют паровой способ. При использовании пара с высокой температурой (470 - 550 0С) требуется определенная схема включения пароперегревателя в общую САР температуры перегретого пара. Из возможных компоновок пароперегревателя в агрегате следует отметить две схемы. Их общей особенностью является использование
вкачестве основного элемента регулирования пароохладителя, включаемого в рассечку между двумя секциями пароперегревателя.
Впервую схему, применяемую на многих судах, входит главный пароохладитель внутрибарабанного типа. Вторая схема, предложенная акад. Н. А. Долежалем, имеет существенную особенность: для регулирования температуры перегретого пара используется система впрыска так называемого собственного конденсата, который получается из пара, отбираемого непосредственно из пароводяного барабана. Пока в судовой практике применяется первая схема, в которой температура перегретого пара регулируется автоматически или вручную с помощью внутрибарабанного пароохладителя.
Температуру перегретого пара регулируют изменением соотношения количества пара, пропускаемого через пароохладитель или обходной паропровод (минуя пароохладитель).
Кроме рассмотренных двух схем, могут быть применены и другие, например с выносными пароохладителями воздушного типа или с впрыском питательной воды.
Взаключение следует отметить, что системы автоматизации в зависимости от способа измерения регулируемых параметров и типа рабочей среды, используемой для передачи и усиления импульсов, могут быть механическими, гидравлическими, пневматическими, электрическими, электромеханическими, с использованием электронных элементов и др.
Системы сигнализации и защиты. Для обеспечения эффективной и безаварийной работы судовых котлов, особенно в условиях безвахтенного обслуживания, они должны быть оборудованы специальными средствами защиты и сигнализации. Защита устанавливается прежде всего на такие параметры и процессы, которые при отклонении их от нормальных условий могут привести к аварии котла или отдельных его элементов. В этом отношении следует отметить уровень воды и давление пара, наличие факела горящего топлива и подачи воздуха в топку. Требования к системам
защиты и сигнализации определяются Правилами Регистра.
Защита по .аварийному снижению уровня воды в барабане судового котла включает сигнализацию (световую, звуковую), а также БЗК, прекращающий подачу топлива к форсункам. При чрезмерном повышении уровня воды также должна включаться защита, исключающая дальнейшее ненормальное повышение уровня. При работающем котле требуется устойчивое горение топлива: погасание факела недопустимо, так как это может вызвать взрыв в топке при повторном зажигании топлива. Основным элементом защиты является фотодатчик с фотосопротивлением, проводимость которого зависит от излучательной способности пламени факела в топке. При погасании факела сигнал от фотодатчика поступает через усилительное устройство на электромагнитный БЗК топливоподачи и на сигнальное устройство
Топочное устройство современных главных и вспомогательных котлов снабжается запальнозащитными устройствами, которые обеспечивают дистанционный или автоматический розжиг топлива. В этом случае предусматривается блокировка с автоматизацией вентиляторов, обеспечивающей вентиляцию топки перед розжигом во избежание взрыва в топке из-за воспламенения горючих газов при соответствующей их концентрации.
При работе котла может произойти прекращение подачи воздуха в топку. Для электроприводного вентилятора это аварийное состояние возможно при обесточивании системы. Специальная защита обеспечивает при обесточивании электромагнита быстрозапорного клапана закрытие его и прекращение подачи топлива. Аналогично действует БЗК и в случае обрыва подачи топлива к топочным устройствам. При этом в каждом случае дополнительно включается также сигнализация.
Следует отметить, что котлы оборудуют и другими сигнальными устройствами, которые указывают, включена или выключена система автоматики, работают или остановились вентилятор, топливный или питательный насос и т. д. Наличие этих и других средств защиты, сигнализации и дополнительной информации повышает надежность и облегчает условия обслуживания котлов.
Контрольные вопросы и задания
1.Дать общую характеристику конструкций судовых котлов.
2.Каковы конструктивные особенности главных судовых котлов (на примере котла КВГ80/80)?
3.Проанализировать особенности конструкций вспомогательных водотрубных котлов (на примерах котлов КАВ, KB и ESH).
4.Каковы конструктивные особенности вспомогательных огнетрубно-водогрубных котлов (на примере котла VX)?
5.Дать общую характеристику конструкций огнетрубных котлов (на примере котла UNEX СН).
6.Каковы конструктивные особенности современных утилизационных котлов цилиндрической
ипрямоугольной компоновок?
7.Проанализировать достоинства и недостатки котлов с органическим теплоносителем.
8.Проанализировать особенности конструкций арматуры и других элементов котлов.
9.Рассмотреть принцип действия системы автоматического регулирования процесса питания котла.
10.Выполнить анализ особенностей системы автоматического регулирования процесса горения.
8. МАТЕРИАЛЫ. ПРОЧНОСТЬ КОТЛОВ. ТРЕБОВАНИЯ РЕГИСТРА
8.1. МАТЕРИАЛЫ ДЛЯ ПОСТРОЙКИ И РЕМОНТА КОТЛОВ
Факторами, определяющими выбор материалов для изготовления и ремонта элементов судовых котлов, являются температурные условия их работы, механические нагрузки и степень агрессивности рабочих сред (воды, пара, дымовых газов), во многом зависящие от параметров пара (давления и температуры). Влияние этих факторов на разные элементы котлов неодинаково, что обусловливает применение для их изготовления различных материалов при непременном обеспечении минимальной стоимости и высокой степени надежности и безопасности.
Для изготовления элементов собственно котлов применяют главным образом углеродистые, углеродисто-марганцевые и низколегированные стали перлитного класса. Для отдельных деталей, работающих при температуре свыше 600 0С (например, деталей крепления пароперегревателей в газоходе), могут быть применены высоколегированные стали аустенитного класса.
Длительный опыт постройки и эксплуатации судовых котлов показывает, что стали, используемые для изготовления элементов, должны удовлетворять следующим требованиям: сохранять высокие прочностные характеристики и устойчивость против изменения структуры во всем диапазоне рабочих температур и давлений; обладать высокими пластичностью, жаропрочностью, жаростойкостью и выносливостью; не иметь внутренних дефектов и отличаться плотностью строения и равномерностью структуры.
Характеристиками прочности стали являются предел текучести от, МПа, - напряжение, при котором материал деформируется без заметного увеличения механической нагрузки, и временное сопротивление разрыву (предел прочности) αВ, МПа, - напряжение, соответствующее наибольшей нагрузке, предшествующей разрыву образца. Напряжения σТ и σВ являются количественными характеристиками, определяющими допустимые напряжения в элементах котла при данных температурных условиях и, следовательно, металлоемкость.
Важно отметить, что предел текучести от при температуре 20 0С достаточно легко определяется во время испытаний по наличию площадки текучести на диаграмме деформирования при растяжении. Однако при повышенных температурах площадка текучести становится все менее заметной и приходится определять условный предел текучести σ0,2 - напряжение, которое вызывает в образце остаточную деформацию 0,2 %.
Характеристиками пластичности сталей являются относительное удлинение δ % относи-
тельное сужение φ %, и ударная вязкость αК, МПа. Котельные стали должны обладать высокой пластичностью, т.е. способностью воспринимать без разрушения остаточную деформацию. Требование высокой пластичности обусловлено прежде всего тем, что технология котлостроения базируется на пластической деформации (гибка и развальцовка труб, штамповка днищ и т.д.). Кроме того, в условиях эксплуатации вследствие различия температурных условий отдельные элементы имеют разные температурные удлинения, а это при достаточно высокой жесткости их соединений может привести к тому, что локальные напряжения (например, в сварных угловых соединениях, вальцовочных соединениях труб и т.п.) превысят предел текучести. В пластичных материалах эти пики напряжений (если они являются единичными случаями) сглаживаются вследствие местной остаточной деформации без нарушения геометрических размеров элемента и без образования трещин. Так как информация о численных значениях показателей δ, ф и ак часто отсутствует, на практике используют более доступный, хотя и менее точный, показатель пластичности: отношение предела текучести σТ к временному сопротивлению разрыву σВ. При σТ/σВ = 0,5 - 0,6 стали считаются пластичными, при σТ/σВ = 0,6 - 0,75 -пластичность удовлетворительная, а при σТ/σВ > 0,75 - материалы хрупкие.
Обычно с повышением температуры прочность снижается, а пластичность повышается. Исключением в этой тенденции является интервал температур синеломкости (200 - 300 °С), в котором следует избегать пластического деформирования углеродистых сталей из-за повышения ее хрупкости (этот интервал назван так потому, что после выдержки стали при температуре около 300 0С светлая ее поверхность приобретает синий цвет вследствие образования тонкой окисной
пленки). Синеломкость стали характеризуется повышением прочности и снижением ударной вязкости. Кроме того, по снижению ударной вязкости судят о старении стали, вызываемом предварительным наклепом в холодном состоянии (например гибка, вальцовка) и последующим длительным нахождением при комнатной температуре или кратковременным нагревом до 100 - 300 0С. Старение может явиться одной из причин образования трещин в гибах, вальцовочных соединениях и' других деформированных участках элементов. Склонность к старению уменьшается с повышением содержания углерода в стали, применением нормализации с последующим отпуском при 600 - 650 0С, а также при добавках некоторых легирующих элементов (титана, ванадия).
Правильный учет перечисленных показателей прочности и пластичности позволяет обеспечить длительную надежную работу углеродистых сталей при температуре не более 400 - 450 °С. Однако при более высоких температурах, которые наблюдаются в пароперегревателях с tnep > 425 0С, а также в парообразующих трубах при наличии внутренних отложений (накипи) толщиной более 0,3 мм, в углеродистых сталях начинает проявляться ползучесть, заключающаяся в непрерывной пластической деформации элементов, находящихся в напряженном состоянии. При этом накопление деформации происходит при напряжениях, более низких, чем предел текучести при рабочей температуре.
Ползучесть приводит к утонению стенок элемента и, следовательно, к повышению напряжений, что в свою очередь интенсифицирует процесс ползучести. Если элемент должен работать в условиях ползучести, то применение рассмотренных механических характеристик уже не может гарантировать надежный выбор марки стали. Иными словами, стали, предназначенные для работы при высоких температурах, должны обладать еще одним свойством - жаропрочностью, под которой подразумевается способность стали сопротивляться разрушению в условиях ползучести. В качестве характеристики жаропрочности служит условный предел ползучести σП - напряжение, которое вызывает остаточную деформацию в 1 % за 100 тыс. ч. эксплуатации при данной темпера туре (или напряжение, вызывающее скорость ползучести 10-5 %/ч)
Однако более употребительна другая характеристика жаропрочности сталей, работающих в условиях 'высоких температур и напряжений. С точки зрения эксплуатации, важно, чтобы металл в таких условиях отработал требуемое время и не разрушился Поэтому материалы испытывают на
длительную прочность и определяют предел длительной прочности σ tДП - напряжение, приводя-
щее металл к разрушению при данной температуре за определенный (обычно 100 тыс. ч) промежуток времени.
Основным способом повышения длительной прочности и сопротивляемости ползучести сталей является рациональное легирование (наиболее эффективными легирующими элементами являются хром и молибден) и применение оптимальных режимов термической обработки.
С ползучестью тесно связано такое явление в сталях, как релаксация напряжений - процесс самопроизвольного затухающего снижения напряжений при постоянных температуре и степени деформации. При высоких температурах в шпильках, болтах, вальцовочных соединениях и других деталях котла напряжения снижаются в результате перехода упругой деформации в пластическую при постоянной суммарной деформации. На практике для обеспечения плотности соединений детали крепежа через определенное время подтягивают, создавая необходимую упругую деформацию в них. После этого снижение напряжений идет медленнее.
В условиях ползучести такие периодические подтягивания могут привести к недопустимому утонению деталей и их разрушению. Поэтому при выборе сталей для деталей прочноплотных соединений следует учитывать релаксационную стойкость материала, т.е. его способность сопротивляться релаксации напряжений. Определяют релаксационную стойкость при специальных испытаниях кольцевых образцов и характеризуют отношением σ0/σК где σ0 - начальное, а ок - конечное напряжения (после релаксации). Легирование сталей хромом, молибденом, ванадием повышает релаксационную стойкость.
К сталям, предназначенным для работы при высоких .температурах, предъявляется также требование повышенной жаростойкости, под которой подразумевается способность металла сопротивляться образованию окалины (часто это свойство называют окалиностойкостью). Это требование обусловлено тем, что элементы котла (прежде всего поверхности нагрева и детали их крепления) при высоких температурах окисляются кислородом, содержащимся в перегретом паре и дымовых газах. Повышение окалиностойкости достигается легированием сталей хромом.
Впроцессе эксплуатации детали элементов котлов подвергаются переменным напряжениям, обусловленным периодическими колебаниями давлений и температур рабочих сред. Разрушение металла под действием переменных напряжений называется усталостью, а сопротивление этому разрушению - циклической прочностью, или выносливостью. Это очень важное свойство характе-
ризуется так называемым физическим пределом усталости σ1, представляющим собой максимальное напряжение цикла с определенной характеристикой асимметрии, при котором металл выдерживает бесконечно большое число циклов N. Однако на практике определяют условный предел усталости (или предел ограниченной выносливости) как напряжение, при котором металл выдерживает определенное число циклов.
Для элементов судовых котлов более опасной является малоцикловая термическая усталость - процесс разрушения металла под действием термических напряжений, обусловленных повторными нагреваниями и охлаждениями с малым числом циклов за весь срок службы. Общая причина термической усталости - свойство материала изменять размеры при изменении температуры.
Следует обратить внимание на тепловую хрупкость, которая проявляется в том, что деталь, длительное время работавшая в условиях высоких температур (400 - 500 °С) и охлажденная до комнатной температуры, приобретает высокую хрупкость и может разрушиться даже от незначительных ударных нагрузок. Интересно также, что в нагретом состоянии хрупкость исчезает и деталь может работать даже при значительных ударных нагрузках. Это особенно полезно помнить при ремонте котлов и избегать ударных нагрузок на те элементы котла, которые обычно работают при высоких температурах.
Вэксплуатации отдельные детали котла (чаще всего трубы поверхностей нагрева) могут работать при температуре выше 450 °С. При достаточно длительной работе в этих условиях пластинки цементита в зернах перлита углеродистых и перлитных легированных сталях дробятся на части, которые принимают сферическую форму (процесс сфероидизации). В дальнейшем отдельные частицы соединяются (коагулируют) в более крупные и диффундируют к. границам зерен, значительно ослабляя сечение. В результате сфероидизации ухудшаются прочностные характеристики и снижается сопротивляемость ползучести. Прочностные характеристики при сфероидизации могут быть частично восстановлены термообработкой - нормализацией с последующим отпуском.
Внекоторых случаях (упуске воды, значительных отложениях и т.п.) возможно повышение температуры металла до 700 °С и выше. При таких температурах резко интенсифицируется про-
цесс распада цементита Fe3C на железо и углерод (графит) - так называемый процесс графитизации. Образующиеся в результате графитизации отдельные зерна непрочного графита, являясь, по существу, „пустотами", вызывают местную концентрацию напряжений и делают сталь хрупкой. Часто явление графитизации наблюдается в районе сварных швов, где металл прогревался до температуры 750 - 800 °С, поэтому перед сваркой деталь необходимо прогреть, а после сварки произвести отжиг.
Чтобы материалы, применяемые для изготовления тех или иных деталей котла, удовлетворяли сформулированным ранее требованиям, необходимо прежде всего определить рабочую темпера-
туру стенки детали. Материалы основных элементов современных вспомогательных и утилизационных котлов при нормальной эксплуатации работают при температуре ниже 450 0С и невысоком давлении (< 3 МПа). Исключение составляют элементы крепления трубных пучков в газоходе, га-
зонаправляющие щиты, заслонки, а также трубы и коллекторы пароперегревателей при температуре перегретого пара выше 400 0С. Отсюда следует, что для труб, поверхностей нагрева эконо-
майзеров, воздухоподогревателей, парообразующих пучков, а также пароперегревателей при tnep ≤ 425 °С вполне допустимо применение углеродистых сталей. Из углеродистых сталей изготовляют также детали опор, каркасов, трубопроводов и т.п.
Правилами Регистра одобрены и применяются в котлостроении стали марок 10, 12К, 15К, 16К, 18К, 20, 20К. При современных параметрах пара для изготовления коллекторов и камер всех поверхностей нагрева вспомогательных и утилизационных котлов, корпусов (бочек) огнетрубных и огнетрубно-водотрубных котлов и сепараторов пара УК, топочных камер и жаровых труб также применяют в большинстве случаев углеродистые стали. Однако с целью снижения металлоемкости водяные и пароводяные коллекторы котлов могут быть изготовлены из углеродистомарганцевых сталей марки 22ГК или низколегированных сталей марок 16ГС и 09Г2С. Для деталей, работающих при температуре выше 400 °С, рекомендуется применять низколегированные
хромомолибденовые стали марок 15ХМ и 12Х1МФ (здесь Г -марганец, С - кремний, X - хром, М - молибден, Ф - ванадий). По требованию Правил Регистра для изготовления элементов судовых котлов следует применять только спокойную сталь с содержанием углерода не более 0,2 %.
Характеристики прочности котельных сталей (табл. 8.1 и рис. 8.1) получены по результатам испытаний стандартных образцов по стандартным методикам. Однако в силу случайных колебаний размеров образцов, испытательной нагрузки, параметров окружающей среды и погрешностей
измерительных приборов результаты определения σВ, σТ, σ tДПР , δ, Φ, αК также случайны и колеб-
лются вокруг каких-то средних значений, принимаемых за расчетные. Кроме того, всегда имеется разброс значений механических характеристик сталей не только разных плавок, но даже одной и той же плавки из-за неравномерности структуры, колебаний температуры при термообработке и других причин. К этому следует добавить случайные колебания (допуски) геометрических размеров деталей (толщин стенок, диаметров труб и т.п.) и, следовательно, фактических рабочих напряжений. Чтобы избежать разрушения деталей в эксплуатации, их прочность рассчитывают по допускаемому напряжению, которое определяется делением пределов прочности, текучести и длительной прочности на коэффициент запаса прочности в соответствии с требованиями Правил Регистра.
Таблица 8.1
|
Предел |
Предел текучести σТ МПа, при расчетной температуре 0С |
Показа- |
||||||||
|
прочно- |
|
|
|
|
|
|
|
|
тель пла- |
|
Марка стали |
сти |
20 |
100 |
200 |
250 |
300 |
350 |
400 |
450 |
стичности |
|
20 |
20 |
||||||||||
|
|||||||||||
|
σВ |
|
|
|
|
|
|
|
|
σТ |
|
|
МПа |
|
|
|
|
|
|
|
|
σ 20 |
|
|
|
|
|
|
|
|
|
|
|
В |
|
Углеродистая: |
|
|
|
|
|
|
|
|
|
|
|
Сталь 10 |
330 |
195 |
186 |
177 |
162 |
147 |
127 |
108 |
78 |
0,591 |
|
12К и 15К |
350 |
205 |
196 |
181 |
167 |
142 |
118 |
98 |
78 |
0,586 |
|
Ст.3 |
370 |
205 |
196 |
186 |
177 |
157 |
- |
- |
- |
0,554 |
|
16К, 20 и 20К |
400 |
235 |
226 |
206 |
186 |
157 |
137 |
118 |
98 |
0,5875 |
|
18К |
430 |
255 |
245 |
226 |
206 |
177 |
157 |
137 |
118 |
0,593 |
|
Легированная: |
|
|
|
|
|
216 |
|
|
|
|
|
15ХМ |
440 |
225 |
225 |
221 |
216 |
206 |
196 |
191 |
0,511 |
||
12Х1МФ |
440 |
255 |
255 |
250 |
245 |
235 |
226 |
216 |
206 |
0,58 |
|
16ГС и 09Г2С |
450 |
265 |
255 |
235 |
226 |
196 |
177 |
157 |
123 |
0,589 |
|
С повышенным содержанием |
|
|
|
|
|
|
|
|
|
|
|
марганца |
|
|
|
|
|
275 |
|
|
|
|
|
22ГК |
530 |
335 |
324 |
304 |
284 |
255 |
245 |
235 |
0,632 |
Кроме сталей, для постройки и ремонта судовых котлов применяют и другие материалы. Большое значение придается правильному выбору огнеупорных и теплоизоляционных материалов, применяемых для защиты коллекторов, каркаса и обшивки котла от прямого воздействия дымовых газов, а также для обеспечения безопасности обслуживающего персонала и уменьшения потерь теплоты в окружающую среду.
Первостепенную роль играет кирпичная кладка, защищающая стенки топки от воздействия теплоты, излучаемой факелом, температура которого достигает 1800-1900 °С. Поэтому кирпичная кладка должна обладать высокими огнеупорностью (способностью кирпича сохранять при высоких температурах свою форму и механические свойства) и термостойкостью (способностью кирпича выдерживать без растрескивания резкие изменения температуры). Огнеупорность характеризуется температурой, при которой кирпич сохраняет свои свойства. Для судовых котлов рекомендуется использовать материалы с огнеупорностью 1700 - 1800 0С. Термостойкость характеризуется числом теплосмен, которые выдерживает кирпич без разрушения при специальных испытаниях.
Важными характеристиками огнеупорных материалов являются коэффициенты теплопроводности и линейного расширения. Если первый из них должен быть достаточно большим, чтобы обеспечить требуемую термостойкость, то второй - по возможности меньше, чтобы предотвратить выкрошивание и образование трещин (особенно в заделке температурных швов и болтовых отверстий). Огнеупорный кирпич должен обладать высокими значениями сопротивления сжатию и температуры размягчения, характеризующими механические свойства.
Для обмуровки топок и изоляции стенок газоходов вспомогательных судовых котлов рекомендуются в основном огнеупорные изделия марки ШСТ и шамотные общего назначения марки ША, а также изделия легковесные теплоизоляционные огнеупорные и высокоогнеупорные марки ШЛА-1,3. Составы защитных обмазок, наносимые на кирпичную кладку, должны соответствовать указаниям инструкций по их применению.
Для изоляции стен обшивки котлов, а также коллекторов, котельной арматуры и трубопроводов, температура наружных поверхностей которых превышает 60 0С, применяют ньювель, совелит и асбест. Эти изоляционные материалы выполняют в виде плит, картона, матрацев, шнуров и закрепляют на изолируемых поверхностях. Основной характеристикой теплоизоляционных материалов является коэффициент теплопроводности, который должен быть по возможности меньше, чтобы обеспечить эффективную теплоизоляцию при небольших массе и толщине слоя изоляции.
8.2. РАСЧЕТ НА ПРОЧНОСТЬ ОСНОВНЫХ ЭЛЕМЕНТОВ КОТЛА
Общие сведения. Конструктивные расчеты судовых котлов на прочность выполняют по Правилам классификации и постройки морских судов Регистра как при проектировании новых агрегатов, так и при установлении Регистром допустимого рабочего давления пара в котлах, находящихся в эксплуатации. Цель подобных расчетов состоит в обеспечении условия надежной и безопасной работы судовых котлов при всех режимах эксплуатации пароэнергетической установки. Однако метод количественной оценки требуемой надежности в каждом из двух отмеченных случаев расчета на прочность будет иметь некоторые особенности. Прежде всего это относится к различным условиям определения качества материалов, используемых для элементов котлов, которые работают под внутренним давлением и подвержены действию дымовых газов или пара с повышенной или высокой температурой. При проектировании котлов рассчитывают допустимую прочность их элементов, для изготовления которых используются новые материалы. Необходимые для расчета механические свойства таких материалов могут быть оценены с весьма высокой точностью. Для второго случая расчета, связанного с установлением допустимого рабочего давления пара в эксплуатируемом котле, конструктивные размеры которого известны, рассматриваемая задача усложняется тем, что свойства материалов с течением времени изменяются.
В связи с этим при решении задач, относящихся ко второму случаю, приходится более широко использовать опытные данные, накопленные при эксплуатации судовых установок. В данной главе рассмотрен расчет на прочность элементов только водотрубных котлов, которые установлены на всех современных судах как отечественного, так и зарубежного транспортного флота.
Условия общей надежности водотрубных котлов определяются прежде всего достаточной прочностью тех элементов, которые находятся под внутренним давлением воды и пара (расчеты прочности регламентируются Правилами Регистра). К таким элементам относятся пароводяные и водяные барабаны (цилиндрическая часть и днища), коллекторы экранов, пароперегревателей, цилиндрические камеры (трубы большого диаметра) водяных экономайзеров и утилизационных котлов, трубы этих поверхностей нагрева.
Условия работы перечисленных элементов различаются довольно существенно, главным образом температурным режимом, при котором они работают. При расчете на прочность эти условия учитывают соответствующим выбором как материалов, так и допускаемых напряжений (коэффициентов запаса прочности).
При оценке надежности проектируемого котла по прочностным показателям необходимо выполнять также расчеты конструктивных его звеньев, нагрузки на которые непосредственно не определяются рабочим движением пара. Такими звеньями служат, в частности, опоры, каркас и обшивка, фланцы, лазы, лючковые затворы и элементы крепежных соединений арматуры и трубопроводов в пределах котлоагрегата.
Детальные расчеты этих элементов обычно выполняют в стадии рабочего проектирования с преимущественным использованием эмпирических методов конструкторских бюро и заводовизготовителей котлов. Поэтому они здесь не рассматриваются.
Расчетные формулы для определения прочности элементов котлов периодически корректируют на основании данных, накопленных опытом их проектирования, постройки и эксплуатации. При этом используют результаты последних исследований в области конструктивных расчетов и
определения механических свойств материалов, применяемых для постройки котлов.
Прочность материалов оценивают на основе сопоставления возникающих в них усилий от действующих нагрузок (механических, тепловых, радиационных и т.п.) с усилиями, приводящими материалы в предельное состояние. При традиционных расчетах статической прочности основным условием надежной работы детали является σР ≤ σДОП (где σР , σДОП - соответственно рабочее и номинальное допускаемые напряжения, МПа). Расчетные формулы для выбора главных размеров несущих сечений деталей основаны на анализе зависимостей теорий упругости и пластичности (причем концентрации напряжений, остаточные и температурные напряжения в них не учитываются).
В зависимости от условий работы и вида нагружения детали величина σДОП устанавливается по пределам текучести σТ (или σ0,2) прочности σВ, длительной прочности σДП,, и ползучести σП с введением соответствующих запасов:
|
|
σ |
|
σ ДОП = |
Т |
n |
|
|
T |
|
σ |
|
σ |
ДП |
|
σ |
|
|
; |
B ; |
|
; |
|
|
|||
|
|
|
|
П |
(8.1) |
|||
n |
n |
|
n |
|||||
|
B |
ДП |
|
|
|
|||
|
|
|
|
|
П |
|
где nT, nB, nДП, nП - соответствующие коэффициенты запаса прочности.
При температуре металла > 350 0С допускаемое напряжение σДОП определяют по уравнениям (8.1) и для расчета принимают наименьшее из них.
В настоящее время откорректированы рекомендации по коэффициентам запаса прочности и будут внесены в следующее издание Правил Регистра. Рекомендуется принимать: nДП = 1; nП = 1; nT = 1,5 - 1,6 для пластичных сталей при σТ /σВ ≤ 0,7; nB = 2,4 - 2,6 для хрупких материалов при σТ /σВ > 0,7. Численные значения σТ, σВ , σДП, σП выбирают по таблицам в зависимости от температуры металла, при которой будет работать деталь. Согласно Правилам Регистра, расчетную температуру стенки /и парообразующих труб, пароводяных и водяных барабанов, коллекторов водяных экономайзеров утилизационных котлов, а также защищенных от непосредственного воздействия лучистой теплоты и дымовых газов экранных коллекторов выбирают на 30 °С выше средней температуры нагреваемой среды tСР, т.е. tСТ = tСР + 30 °С. Для труб, подверженных воздействию
лучистой теплоты, tСТ = tСР + 50 0С.
При выборе марки стали для коллекторов и труб пароперегревателя определяющим фактором служит рабочая (номинальная) температура перегретого пара tПЕР. Для вынесенных за пределы газохода коллекторов при температуре перегретого пара до 450 °С расчетную температуру стенки принимают равной tСТ = tСР + 25 °С , а если коллекторы подвержены воздействию горячих газов, то tСТ = tСР + 35 °С; при температуре пара выше 450 "С принимают tСТ = tСР + 50 °С. В зависимости от значения tСТ пароперегреватели могут быть выполнены как из обычных углеродистых сталей, так и из легированных - жаропрочных.
Здесь рассмотрен расчет на прочность только основных элементов, находящихся под внутренним давлением. Это позволяет составить общее представление о методике расчетов судовых котлов на прочность. Недостающие здесь данные могут быть, получены из других источников и прежде всего из Правил Регистра.
Расчет цилиндрических барабанов и труб. Толщину стенки труб, цилиндрической части пароводяного барабана, цилиндрических коллекторов пароперегревателя, водяного экономайзера и утилизационного котла 6, мм, рассчитывают по одной из формул:
δ = |
pDH |
+c |
|
2σ ДОПφ + p |
|
||
δ = |
pDВ |
+ c |
|
2σ ДОПφ − p |
где р - расчетное внутреннее давление, МПа;
DH, DB - наружный и внутренний диаметры барабана или трубы, мм; σДОП - допускаемое напряжение в стенке барабана, МПа; φ - коэффициент прочности;
(8.2)
(8.2)

с - прибавка к расчетной толщине стенки, мм.
Основной первый член правой части уравнения (8.2) может быть получен из условия применения третьей теории прочности для сложного напряженного состояния цилиндрической части барабана. Если выделить кубический элемент (рис. 8.2, о) из рассматриваемой части барабана (рис. 8. 2, б), то на него будут действовать три главных напряжения: σ1, σ2, σ3. Как известно,
σ1 = |
pDBl |
= |
pDB |
; |
σ2 = |
зπDB2 |
= |
pDB |
|
4πDBδ |
4δ |
||||||||
2δl |
2δ |
||||||||
|
|
|
|
|
Наименьшее напряжение σ3 определяют для среднего волокна элемента: |
||
σ |
3 |
= σr +(σr + dσr ) |
|
2 |
|
|
|
Рис. 8.2. Схема для определения расчетного напряжения в цилиндрической части барабана.
Подставив в эту зависимость граничные значения напряжений σr = - р (сжатие) и σr + dσr = 0 (так как на наружной поверхности барабана напряжения отсутствуют), получим σ3 = - р/2. Согласно третьей теории прочности (наибольших касательных напряжений) можно записать: τmax < τДОП = σДОП/2 или τmax = (σmax - σmin)/2, поэтому условие прочности запишется в виде
σmax −σmin ≤σ ДОП |
(8/4) |
|||||||||
Подставив в уравнение (8.4) значения σmax |
= σ1 |
= |
pDB |
; σmin = σ3 = pDB/2, получим: |
|
|||||
|
|
|||||||||
|
|
|
|
|
|
|
2δ |
|
||
|
pDB |
+ |
p |
=σ ДОП |
(8.5) |
|||||
|
|
|
||||||||
|
2δ |
2 |
|
|
|
|
|
|||
откуда |
|
|
|
|
|
|
|
|
||
|
δ = |
|
|
|
pDB |
|
(8.6) |
|||
|
|
2σ ДОП − p |
||||||||
|
|
|
За расчетное давление р принимают его наибольшее значение, которое возможно в условиях эксплуатации судовых котлов. При расчете прочности пароводяных и водяных барабанов расчет-

ное давление принимают равным давлению, на которое установлены предохранительные клапаны. Это давление в соответствии с Правилами Регистра для водотрубных котлов может быть выбрано равным р = l,05pK (где рK - рабочее давление в пароводяном барабане при максимальной паропроизводительности).
Коллекторы пароперегревателя также необходимо рассчитывать на то же давление p несмотря на то, что при установившейся нагрузке давление pЛЕР ниже, чем p на значение гидравлических потерь в пароперегревателе. Правильность такой оценки расчетного давления для пароперегревателя обусловливается тем, что при возможной в судовых условиях внезапной остановке главного двигателя отвод пара из котла прекращается и давление в пароводяном барабане и пароперегревателе становятся равными.
Для коллекторов водяного экономайзера расчетное давление можно выбрать р = pK + ∆рВЭ (где ∆рВЭ - гидравлическое сопротивление водяного экономайзера).
При проверочных расчетах прочности труб допускаемое рабочее давление среды
p = |
2δσДОП |
|
(8.7) |
|
D −δ |
||||
|
||||
|
H |
|
||
где δ - фактическая толщина стенки трубы в том сечении, где она наименьшая, мм; |
|
σДОП - допускаемое напряжение, определяемое по фактическим значениям σТ, или σВ, МПа. Коэффициент прочности φ, входящий в формулы (8.2) и (8.3), зависит от конструкции рассчитываемого элемента. При расчете толщины стенки труб и обертки барабанов коэффициент φ выбирают равным единице, так как эта часть барабана не ослаблена отверстиями для труб, а соединение обертки с трубной решеткой осуществляется сваркой, которая в современной практике
обеспечивает высокое качество шва.
При расчете толщины стенки трубной решетки барабанов коэффициент φ определяют в зави-
симости от характера ослабления решетки отверстиями для труб. В случае коридорной компонов- |
||
ки труб |
φ = s − d |
(8.8) |
|
|
s
а поперечный и продольный шаги отверстий (расстояние между осями труб) обычно одинаковы,
т.е. s1 = s2 = s.
При шахматном расположении отверстий, имеющих одинаковый диаметр, в случае обычной их компоновки с постоянными шагами в продольном и поперечном направлениях (по отношению к оси барабана) для расчета выбирают наименьшее значение коэффициента прочности из φ рассчитанного по формуле (8.8), в которую подставляют s1 или sK вместо s (где sK диагональный шаг отверстий). В судовых котлах пучки труб при шахматном расположении имеют такие геометрические параметры, при которых поперечный и диагональный шаги обычно равны (s1 = sK)
Для обеспечения приемлемой (с точки зрения прочности) толщины стенок барабана и коллекторов рекомендуется выполнять компоновку трубных пучков, чтобы φ ≥ 3.
Расчет выпуклых днищ. Днища для барабанов судовых котлов выполняют бесшовными штампованными обычно эллиптической формы. Плоские днища применяют только для барабанов с внутренним диаметром до 500 мм. Выпуклые днища эллиптической формы позволяют обеспечить достаточную прочность и приемлемую с конструктивной точки зрения толщину стенки. Днища коробовой формы для барабанов современных котлов применяют редко.
Для расчета прочности эллиптических днищ, подверженных внутреннему давлению, толщина стенки днища:
глухого, т.е. не имеющего отверстий (рис. 8.3, а),
δ = |
pDH v |
+с |
(8.9) |
|
|||
|
4σ ДОП |
|
имеющего лазовые (одно или два) либо иные отверстия - вырезы (рис. 8.3, б, в),
δ = |
pDH v |
+c |
(8.10) |
4σ ДОПφ |
|

где DH - наружный диаметр днища, мм;
v - коэффициент формы, зависящий от отношения высоты днища hB к наружному диаметру
DН определяемый по Правилам Регистра. |
|
|||
Коэффициент прочности определяют по формуле, аналогичной (8.8): |
|
|||
φ = |
DH −d |
|
(8.11) |
|
DH |
||||
|
|
Приведенные формулы справедливы для следующих соотношений размеров днищ:
hB |
≥ 0,18 ; |
δ |
≥ 0,003 ; RB ≤ DH |
(8.12) |
|
||||
|
|
|||
DH |
DH |
|
Днище с переменной толщиной стенки (рис. 8.3, г) рассчитывают в зависимости от наличия или отсутствия в нем лазовых или других отверстий по соответствующим формулам (8.9) или (8.10). Расчетную толщину стенки днища в этом случае выбирают равной среднеарифметическому значению минимальной и максимальной толщин, т.е. .
δ = 0,5(δ1 +δ2 ) |
(8.13) |
Рис. 8.3. Конструктивные формы днищ.
При этом минимальную толщину стенки днища δ1, которая должна быть не менее расчетной толщины цилиндрического борта днища, рассчитывают согласно формулам (8.2) и (8.3). При наличии в разностенном днище подреза для уплотнения лазового затвора толщина стенки δ3 такого днища в месте подреза должна быть не менее толщины δ1 цилиндрического борта.
В формулах (8.2), (8.10) во всех случаях принимают с не менее 1 мм, если это не оговорено особо. При толщинах стенки более 30 мм по согласованию с Регистром можно принимать с = 0.
Допускаемые напряжения σДОП и расчетное давление р, введенные в формулы (8.9) и (8.10), определяют в соответствии с теми же рекомендациями, которые были приведены в пояснениях к формулам (8.2) и (8.3).
8.3. ВИДЫ ОСВИДЕТЕЛЬСТВОВАНИЯ КОТЛОВ РЕГИСТРОМ
Высокие надежность и безопасность эксплуатации главных, вспомогательных и утилизационных котлов, устанавливаемых на морских судах с различными типами главных двигателей, могут быть обеспечены при условии выполнения всех требований Регистра, который осуществляет технический надзор за исполнением его требований. Эту работу Регистр выполняет как орган государственного технического надзора и классификации гражданских судов.
Таким образом, требования Регистра и его деятельность позволяют обеспечить четыре основных показателя надежной работы морских судов: условия технической безопасности мореплавания судов в соответствии с их назначением; охраны человеческой жизни на море; надежной перевозки грузов; предотвращения загрязнения моря с судов.
Надзорную деятельность Регистр осуществляет на основании Кодекса торгового мореплавания. Для осуществления своих функций Регистр издает правила и другую документацию надзорной деятельности, применение и выполнение которых обязательны для проектных организаций, судовладельцев, заводов и других предприятий, строящих, ремонтирующих и эксплуатирующих суда. Следует иметь в виду, что надзорная деятельность Регистра осуществляется в соответствии с его Уставом, но не заменяет органов технического контроля упомянутых организаций, значимость которых определяется требованием постоянного повышения качества оборудования и эффективности его использования в эксплуатации.
К этому следует добавить, что Регистр поручает выполнение работ достаточно квалифицированным специалистам, однако согласно Уставу не несет имущественной ответственности за убытки, которые могут произойти в связи с осуществлением им своей деятельности.
Учитывая отмеченные общие указания, можно привести следующие основные соображения об объеме и содержании надзора Регистра, в частности судовых котлов. Надзор Регистра осуществляется как в процессе проектирования и постройки котлов, так и при эксплуатации их по назначению судовладельцем. В связи с этим надзор начинается еще до постройки агрегата путем рассмотрения и одобрения Регистром необходимой технической документации, в том числе конструктивных чертежей и всех данных, которые требуются для проверки расчетов и конструкций, а именно: размеров, материалов, технологии и др.
Надзору Регистра подлежат главные, вспомогательные и утилизационные котлы, их перегреватели и экономайзеры с рабочим давлением 0,07 МПа и более.
Освидетельствования котлов могут совпадать по времени с такой работой по судну в целом, а иногда и проводиться самостоятельно. В этом отношении следует указать, что освидетельствования могут быть первоначальными, очередными, ежегодными и внеочередными, а производятся они согласно нормативному документу Регистра Руководству по техническому надзору за судами в эксплуатации.
Первоначальное освидетельствование проводят с целью установить возможность присвоения класса судну. При этом учитывают техническое состояние и возраст судна, механизмов, в том числе котлов.
Очередное освидетельствование проводят для возобновления класса с целью удостовериться, что техническое состояние в данном случае механического оборудования и котлов удовлетворяет требованиям Регистра.
Ежегодное освидетельствование осуществляют для подтверждения класса, оно необходимо для проверки работы механизмов и котлов, на которые распространяются требования Правил.
Внеочередное освидетельствование требуется обычно после ремонта или аварии по заявке судовладельца.
Во время освидетельствования Регистр может выполнять внутренние и наружные осмотры для выявления дефектов и повреждений, гидравлические испытания котлов, а также регулирование и проверку на срабатывание предохранительных клапанов с необходимым их пломбированием. Освидетельствуют также средства подготовки и подачи питательной воды, топлива и воздуха, автоматизации и защиты котлов, арматуру и КИП.
Давление, при котором производят гидравлические испытания, называется пробным. Оно в основном равно 1,5 рабочего давления, но не менее чем pПР = pP + 0,1 МПа. Для пароперегревателей
|
|
|
σ 350 |
|
350 |
|
и их элементов |
pПР |
|
T |
|
и |
|
=1,5 p p |
t |
|
, если они работают при температуре 350 °С и выше (где σТ |
|||
|
|
|
σT |
|
|
|
σТt - пределы текучести стали соответственно при 350 0С и рабочей температуре t). Паровой котел
иего элементы (перегреватель, экономайзер, пароохладитель) выдерживают при пробном давлении в течение 10 мин, после чего давление постепенно снижают до рабочего, при котором продолжают осмотр агрегата и его арматуры. Гидравлические испытания считают законченными успешно, если пробное давление при выдержке не снижалось и при осмотре не обнаружено течи и видимых изменений формы и остаточных деформаций.
Предохранительные клапаны должны быть отрегулированы на следующее давление открытия:
pОТКР ≤ 1,05рр для pp ≤ 1 МПа и pОТКР ≤ 1,03рр для pp > 1 МПа. Максимально допустимое давление при действии предохранительного клапана рmax < 1,1рр.
Наружный осмотр котлов в комплексе с арматурой, трубопроводами и системами производят под паром при рабочем давлении и по возможности совмещают с проверкой в действии судовых механизмов.
Результаты освидетельствования заносит инспектор Регистра в регистровую книгу парового котла и главного паропровода, которая выдается инспекцией Регистра при первоначальном освидетельствовании каждого агрегата.
В заключение необходимо отметить, что Регистр присваивает класс судну на 4 года, что позволяет осуществлять классификационные операции по 12-летнему циклу. В пределах 4 лет выполняют три ежегодных освидетельствования на подтверждение класса и одно - на возобновление. Таким образом, в течение всего цикла судну 3 раза возобновляется класс. Объем периодических освидетельствований для котла, как и для другого судового оборудования, установлен Правилами Регистра.
КОНТРОЛЬНЫЕ ВОПРОСЫ И ЗАДАНИЯ
1.Дать определение понятий „предел текучести", „предел длительной прочности", „предел ползучести".
2.Перечислить показатели пластичности, жаропрочности и жаростойкости котельных сталей.
3.Назвать определяющие факторы при выборе материалов для котла.
4.Дать определение понятия „коэффициент запаса прочности".
5.Выполнить анализ действующих в стенке трубы напряжений и на этой основе пояснить содержание формулы для расчета толщины стенки.
6.Назвать функции Регистра и перечислить виды освидетельствования судовых котлов.
7.На какое давление регулируются предохранительные клапаны котла?
8.Назвать марки углеродистых котельных сталей и значения предельных температур их использования.