
- •STANDARD SERVICE PROCEDURES
- •MOPAR SILICONE RUBBER ADHESIVE SEALANT
- •MOPAR GASKET MAKER
- •GASKET DISASSEMBLY
- •SURFACE PREPARATION
- •CRANKSHAFT SPROCKET BOLT ACCESS PLUG
- •ENGINE PERFORMANCE
- •HONING CYLINDER BORES
- •MEASURING MAIN BEARING CLEARANCE AND CONNECTING ROD BEARING CLEARANCE
- •PLASTIGAGE METHOD
- •CONNECTING ROD BEARING CLEARANCE
- •LASH ADJUSTER (TAPPET) NOISE DIAGNOSIS
- •REPAIR OF DAMAGED OR WORN THREADS
- •HYDROSTATIC LOCKED ENGINE
- •GENERAL INFORMATION
- •ENGINE IDENTIFICATION NUMBER OR CODE
- •ENGINE MOUNTS
- •FRONT MOUNT
- •LEFT SIDE MOUNT
- •ENGINE MOUNT RUBBER INSULATORS
- •ENGINE ASSEMBLY
- •REMOVAL
- •INSTALLATION
- •SOLID MOUNT COMPRESSOR BRACKET SERVICE
- •ACCESSORIES REMOVAL
- •TIMING SYSTEM AND SEALS SERVICE
- •TIMING BELT SERVICE
- •CYLINDER HEAD AND VALVE ASSEMBLY SERVICE
- •CYLINDER HEAD COVER AND CURTAIN
- •REMOVAL
- •CLEANING
- •CURTAIN INSTALLATION
- •COVER SEALING AND INSTALLATION
- •CAMSHAFT SERVICE
- •REMOVAL
- •INSPECTION
- •CAMSHAFT END PLAY
- •INSTALLATION
- •LASH ADJUSTER (TAPPET) NOISE
- •INSTALLATION
- •INSTALLATION
- •CYLINDER HEAD
- •REMOVAL
- •INSPECT HEAD AND CAMSHAFT BEARING JOURNALS
- •VALVES AND VALVE SPRINGS
- •VALVE INSPECTION
- •VALVE GUIDES
- •REFACING VALVES AND VALVE SEATS
- •CLEANING
- •CYLINDER HEAD COVER SEALING
- •CYLINDER HEAD
- •TIMING BELT
- •CAMSHAFT AND CRANKSHAFT TIMING PROCEDURE
- •INSTALLATION
- •SERVICING OIL SEALS
- •CAMSHAFTS SERVICE
- •REMOVAL
- •INSPECTION
- •INSTALLATION
- •CAMSHAFT END PLAY
- •LASH ADJUSTER (TAPPET) NOISE
- •ROCKER ARM AND HYDRAULIC LASH ADJUSTER
- •VALVE SPRINGS AND VALVE STEM SEALS
- •VALVE SERVICE
- •VALVE AND VALVE SPRINGS
- •VALVE INSPECTION
- •VALVE GUIDES
- •TESTING VALVE SPRINGS
- •REFACING VALVES AND VALVE SEATS
- •VALVE GEAR REASSEMBLY AFTER VALVE SERVICE
- •CRANKSHAFT OIL SEALS SERVICE
- •REAR CRANKSHAFT SEAL RETAINER AND OIL SEAL
- •FRONT CRANKSHAFT SEAL RETAINER
- •CRANKSHAFT SERVICE
- •CRANKSHAFT MAIN BEARINGS
- •CRANKSHAFT MAIN JOURNALS
- •CHECKING CRANKSHAFT END PLAY
- •OPTIONAL CRANKSHAFT END PLAY CHECK
- •CRANKSHAFT BEARING CLEARANCE
- •BALANCE SHAFTS
- •REMOVAL
- •BALANCE SHAFTS CARRIER ASSEMBLY
- •CHAIN TENSIONING
- •INTERMEDIATE SHAFT SERVICE
- •REMOVAL
- •INSTALLATION
- •INTERMEDIATE SHAFT BUSHING SERVICE
- •CYLINDER BORE INSPECTION
- •SIZING PISTONS
- •PISTON PINS
- •PISTON PINS
- •FITTING RINGS
- •PISTON AND CONNECTING ROD ASSEMBLY INSTALLATION
- •CONNECTING RODS
- •ENGINE CORE PLUGS
- •REMOVAL
- •INSTALLATION
- •ENGINE LUBRICATION SYSTEM
- •PRESSURE LUBRICATION
- •ACCESSORY SHAFT
- •BALANCE SHAFTS
- •TURBOCHARGER (WHERE EQUIPPED)
- •SPLASH LUBRICATION
- •REMOVAL
- •OIL PAN RAIL TO BLOCK SEALING
- •INSTALLATION
- •OIL PUMP SERVICE
- •OIL PICKUP
- •INSTALLATION
- •INSPECTION
- •CHECKING ENGINE OIL PRESSURE
- •OIL FILTER
- •FILTER
- •SPECIFICATIONS
- •ENGINE SPECIFICATIONS (CONT.)
- •ENGINE SPECIFICATIONS (CONT.)
- •SPECIFICATIONS
- •3.0L ENGINE
- •GENERAL INFORMATION
- •ENGINE IDENTIFICATION NUMBER OR CODE
- •3.0L ENGINE
- •SPECIFICATIONS
- •ENGINE MOUNTS
- •FRONT MOUNT
- •LEFT SIDE MOUNT
- •ENGINE MOUNT RUBBER INSULATORS
- •ENGINE MOUNT INSULATOR ADJUSTMENT
- •ENGINE ASSEMBLY
- •REMOVAL
- •INSTALLATION
- •ACCESSORY DRIVE BELT SERVICE
- •REMOVAL
- •TIMING BELT SERVICE
- •REMOVAL
- •INSTALLATION
- •TIMING BELT TENSIONER
- •CYLINDER HEAD AND CAMSHAFT SERVICE
- •INSTALL
- •AUTO LASH ADJUSTER
- •FUNCTION CHECK
- •CAMSHAFT SERVICE
- •CAMSHAFT INSPECTION
- •CAMSHAFT INSTALL
- •ROCKER ARMS
- •ROCKER ARM SHAFTS
- •REASSEMBLE
- •ASSEMBLE ROCKER ASSEMBLY
- •INSTALL ROCKER ARM SHAFT ASSEMBLY
- •CYLINDER HEAD
- •REMOVAL
- •INSPECTION
- •INSTALLATION
- •VALVE SPRINGS
- •VALVE AND VALVE SPRINGS
- •VALVES
- •VALVE SEAT INSPECTION
- •CYLINDER BORE INSPECTION
- •FITTING PISTONS
- •FITTING PISTON RINGS
- •CONNECTING ROD CLEARANCE
- •CONNECTING ROD SIDE CLEARANCE
- •CRANKSHAFT SERVICE
- •INSPECTION
- •PLASTIGAGE MEASUREMENT
- •CHECKING CRANKSHAFT END PLAY
- •FRONT CRANKSHAFT OIL PUMP AND OIL SEAL
- •BORING CYLINDER
- •CYLINDER BLOCK
- •ENGINE LUBRICATION SYSTEM
- •OIL PAN SEALING AND INSTALLATION
- •OIL PUMP SERVICE
- •REMOVAL
- •INSPECTION OIL PUMP
- •OIL RELIEF PLUNGER
- •INSTALLATION
- •CHECKING ENGINE OIL PRESSURE
- •OIL FILTER AND BRACKET
- •OIL FILTER
- •ENGINE SPECIFICATIONS
- •ENGINE SPECIFICATIONS (CONT.)
- •TORQUE
- •GENERAL INFORMATION
- •ENGINE INDENTIFICATION NUMBER OR CODE
- •SPECIFICATIONS
- •ENGINE MOUNTS
- •FRONT MOUNT
- •LEFT SIDE MOUNT
- •ENGINE MOUNT RUBBER INSULATORS
- •ENGINE MOUNT INSULATOR ADJUSTMENT
- •ENGINE ASSEMBLY
- •REMOVAL
- •INSTALLATION
- •ROCKER ARMS AND SHAFT ASSEMBLY
- •REMOVAL
- •INSTALLATION
- •CYLINDER HEADS
- •REMOVAL
- •INSPECTION
- •INSTALLATION
- •INTAKE MANIFOLD SEALING
- •VALVE SERVICE
- •VALVES AND VALVE SPRINGS
- •REMOVAL
- •VALVE INSPECTION
- •VALVE GUIDES
- •REFACING VALVES AND VALVE SEATS
- •VALVES
- •VALVE SEATS
- •TESTING VALVE SPRINGS
- •VALVE INSTALLATION
- •REPLACE VALVE STEM SEALS OR VALVE SPRINGS, CYLINDER HEAD NOT REMOVED
- •HYDRAULIC TAPPETS
- •PRELIMINARY STEP TO CHECKING THE HYDRAULIC TAPPETS
- •OIL LEVEL TOO HIGH
- •OIL LEVEL TOO LOW
- •VALVE TRAIN NOISE DIAGNOSIS
- •TAPPET REMOVAL
- •DISASSEMBLY (FIG. 27)
- •CLEANING AND ASSEMBLY
- •INSTALLATION
- •VALVE TIMING
- •TIMING CHAIN COVER, OIL SEAL AND CHAIN
- •COVER
- •MEASURING TIMING CHAIN FOR STRETCH
- •TIMING CHAIN COVER EXTERNAL OIL SEAL
- •CAMSHAFT
- •INSTALLATION
- •REMOVAL
- •INSTALLATION
- •ENGINE CORE OIL AND CAM PLUGS
- •REMOVAL
- •INSTALLATION
- •CLEANING AND INSPECTION
- •CYLINDER BORE INSPECTION
- •FINISHED PISTONS
- •FITTING PISTONS
- •PISTON PINS
- •FITTING RINGS
- •INSTALLING PISTON AND CONNECTING ROD ASSEMBLY
- •CONNECTING RODS
- •INSTALLATION OF CONNECTING ROD BEARINGS
- •CRANKSHAFT SERVICE
- •CRANKSHAFT MAIN BEARINGS
- •CRANKSHAFT MAIN JOURNALS
- •CHECKING CRANKSHAFT END PLAY
- •CRANKSHAFT OIL CLEARANCE
- •CRANKSHAFT OIL SEALS SERVICE
- •REMOVAL
- •INSTALLATION
- •REAR CRANKSHAFT SEAL RETAINER
- •ENGINE LUBRICATING SYSTEM
- •OIL PAN SERVICE
- •REMOVAL
- •CLEANING AND INSPECTION
- •INSTALLATION
- •OIL PUMP SERVICE
- •DISASSEMBLY
- •INSPECTION AND REPAIR
- •OIL PUMP ASSEMBLY AND INSTALLATION
- •CHECKING ENGINE OIL PRESSURE
- •OIL FILTER
- •ENGINE SPECIFICATIONS
- •ENGINE SPECIFICATIONS (CONT.)
- •ENGINE SPECIFICATIONS (CONT.)
- •ENGINE SPECIFICATIONS (CONT.)
- •TORQUE
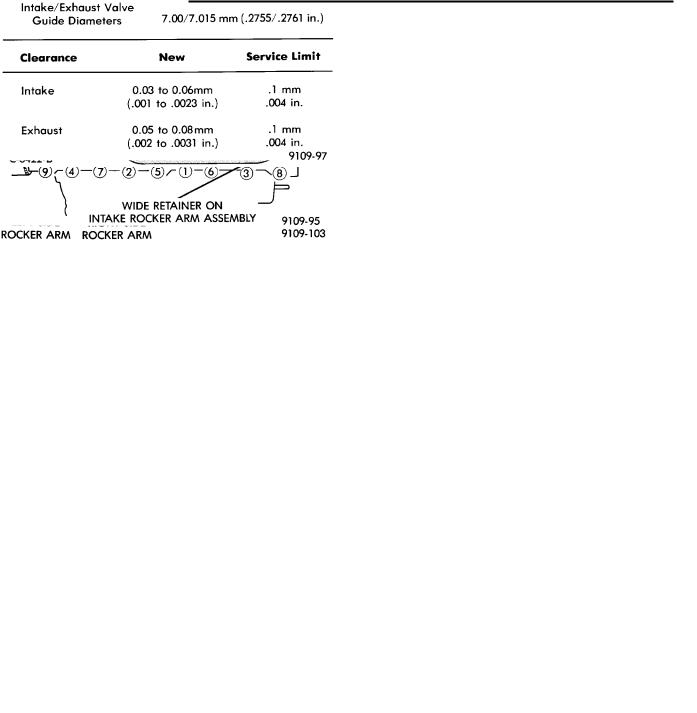
9 - 38 2.2/2.5L ENGINES
INSTALLATION
(1)Install rocker arm on the shaft in there original position (Fig. 9).
(2)Install hydraulic lash adjusters making sure that adjusters are at least partially full of oil. This is indicated by little or no plunger travel when the lash adjuster is depressed.
(3)Install rocker arm shaft assembly tighten in sequence shown in (Fig. 10).
(4)Install valve cover as previously outlined.
Ä
(2)Remove valve retaining locks, valve spring retainers, valve stem seals and valve springs.
(3)Before removing valves, remove any burrs from valve stem lock grooves to prevent damage to the valve guides. Identify valves to insure installation in original location.
Fig. 9 Intake and Exhaust Rocker Arm Assemblies
Fig. 10 Rocker Arm Shaft−Installation
VALVE SPRINGS AND VALVE STEM SEALS
VALVE SERVICE
² CYLINDER HEAD MUST BE REMOVED TO SERVICE VALVE SPRINGS AND VALVE STEM SEALS.
VALVE AND VALVE SPRINGS
REMOVAL
(1) With cylinder head removed, compress valve springs using Valve Spring Compressor Tool C-3422-B with adopters 6537 and 6526 (Fig. 11).
Fig. 11 Valve Spring Compressor
Fig. 12 Valve Guide Specificaton
VALVE INSPECTION
(1)Clean valves thoroughly and discard burned, warped and cracked valves.
(2)Measure valve stems for wear. Refer to (Fig. 14) for specifications.
(3)Remove carbon and varnish deposits from inside of valve guides with a reliable guide cleaner.
VALVE GUIDES
Measure valve guides in 3 places top, middle and bottom (Fig. 13). Using a small hole gauge and a micrometer, refer to (Fig. 12) for specifications.
Replace cylinder head if guides are not within specifications.
TESTING VALVE SPRINGS
(1)Refer to Testing Valve previously described in this Group for procedure. Test springs at 36.8mm (1-7/16 to 1-15/32 in.) 1000 N 225 lbs.) 6 40 N (9 lbs.). Discard the springs that do not meet specifications.
(2)Inspect each valve spring for squareness with a steel square and surface plate, test springs from both ends. If the spring is more than 1.65mm (1/16 inch) out of square, install a new spring. Spring free length is 53.2 mm 6 .25 mm (2.094 in. 6 .010 in.)

Ä |
|
2.2/2.5L ENGINES 9 - 39 |
|
Fig. 13 Measuring Valve Guides
Fig. 14 Valve Dimensions
REFACING VALVES AND VALVE SEATS
(1)The intake and exhaust valve seats and valve face have a 45 degree angle.
(2)Inspect the remaining margin after the valves are refaced (Fig. 11). Exhaust valves with less than 1.07mm (3/64 inch) margin and intake valves with less than 1.06mm (3/64 inch) margin should be discarded.
(3)When refacing valve seats, it is important that the correct size valve guide pilot be used for reseating stones. A true and complete surface must be obtained.
(4)Measure the concentricity of valve seat using a valve seat dial indicator. Total runout should not exceed 0.1 mm (.004 inch) (total indicator reading).
(5)Inspect the valve seat with Prussian blue to determine where the valve contacts the seat. To do this, coat valve seat LIGHTLY with Prussian blue then set valve in place. Rotate the valve with light pressure. If the blue is transferred to the center of valve face, contact is satisfactory. If the blue is transferred to top edge of the valve face, lower valve seat with a 15 degree stone. If the blue is transferred to the bottom edge of valve face raise valve seat with a 65 degrees stone.
²Intake valve seat diameter 34.0mm (1.338 inch)
²Exhaust valve seat diameter 29.4mm (1.157 inch)
Fig. 15 Refacing Intake and Exhaust Valves
Valve seats which are worn or burned can be reworked, provided that correct angle and seat width are maintained. Otherwise cylinder head must be replaced.
(6)When seat is properly positioned the width of intake seats should be 1.87mm (0.73 inch) The width of the exhaust seats should be 2.00mm (.078 inch) (Fig. 16 Dimension 1).
(7)Check valve tip for scoring, if necessary, the tip chamfer should be reground to prevent seal damage when the valve is installed.
(8)Check the valve spring installed height after refacing the valve and seat (Fig. 17).
Fig. 16 Refacing Valve Seats
VALVE GEAR REASSEMBLY AFTER VALVE SERVICE
(1)Coat valve stems with lubrication oil and insert in cylinder head.
(2)Install new valve stem seals on all valves. The valve stem seals should be pushed firmly and squarely over valve guide. The lower edge of the seal should be resting on the valve guide boss.
(3)Install valve spring seats and springs and retainers. Compress valve springs only enough to in-

9 - 40 2.2/2.5L ENGINES
stall locks, taking care not to misalign the direction of compression. Nicked valve stems may result from misalignment of the valve spring compressor.
CAUTION: When depressing the valve spring retainers with Valve Spring Compressor Tool C-3422-B with adopters 6537 and 6526 (Fig. 11) the locks can become dislocated. Check to make sure both locks are in teir correct location after removing tool.
(4)Check installed height of springs. Measurement is to be taken from the lower edge of the valve spring to its upper edge. Do not include the spring seat or retainer flange. Correct height is 44.0mm (1.73 inches). If seats have been reground an additional spring seat may be required to maintain correct installed spring height (Fig. 17).
(5)Install camshaft and rocker arms as previously described, see Camshaft-Install.
Ä
Fig. 17 Checking Spring Installed Height

Ä |
|
2.2/2.5L ENGINES 9 - 41 |
|
CRANKSHAFT, INTERMEDIATE AND BALANCE
SHAFT SERVICE
Fig. 1 Crankshaft Intermediate and Balance Shaft Assemblies and Oil Seals