
Учебник по Технологии
.pdf
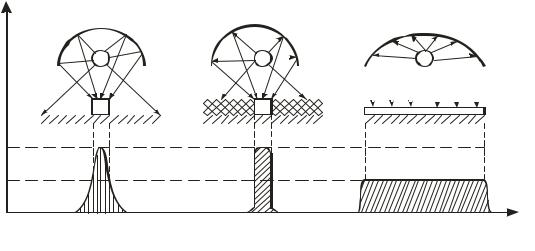
E |
) |
|
|
|
|
|
|
|
|
|
|
|
|
|
|
|
|
|
|
|
|
|
|
|
|
|
|
|
|
|
|
||
|
|
|
|
|
|
|
|
|
|
|
|
|
|
|
|
|
|
|
|
|
|
|
|
|
|
|
|
|
|
|
|
|
|
|
|
|
|
|
|
|
|
|
|
|
|
|
|
|
|
|
|
|
|
|
|
|
|
|
|
|
|
|
|
|
|
|
|
|
|
|
|
|
|
|
|
|
|
|
|
|
|
|
|
|
|
|
|
|
|
|
|
|
|
|
|
|
|
|
|
|
|
|
|
|
|
|
|
|
|
|
|
|
|
|
|
|
|
|
1,0
0,5
X
Х
а) |
б) |
в) |
Рис. 59. Способы фокусировки ИК-излучения:
а − оптическая; б − оптическая локальная; в − диффузионная
Первой стадией физико-химического взаимодействия расплава припоя с паяемым материалом является смачивание, в результате которого две свободные поверхности заменяются одной границей фаз между паяемым материалом и расплавом припоя с более низкой свободной поверхностной энергией системы. Для осуществления смачивания работа сил адгезии расплава к твердой поверхности Wa должна быть больше работы сил когезии, определяемой силами сцепления частиц припоя Wk:
W − |
1 |
W > 0 . |
(38) |
|
|||
a |
2 |
k |
|
|
|
|
В результате смачивания припой растекается по поверхности паяемого материала до установления равновесия выражаемого соотношением
s1,3 = s2,3 + s1,2 ×cos q , |
(39) |
где σ1,3, σ1,2, σ2,3 – поверхностные натяжения на границах: твердое
тело-газ, жидкость – твердое тело, |
жидкость-газ соответственно; |
θ – краевой угол смачивания (рис. |
60). Краевой угол смачивания |
характеризует смачивающую способность припоя и применяется в качестве одного из критериев паяемости. Паяемость металла или покрытия считается плохой, если θ > 50°, удовлетворительной –
20° < θ < 50°, хорошей – θ ≤ 10–20°, отличной, если θ = 1–10°.
296
