
Учебник по Технологии
.pdf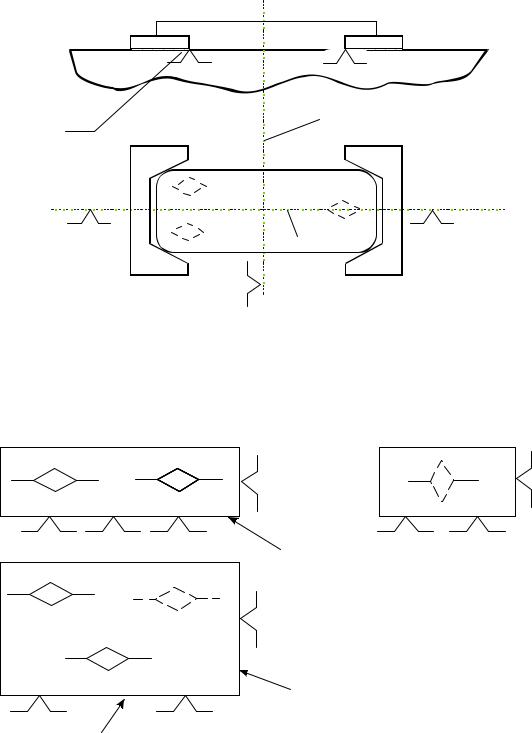
поверхности, разметочной риски или точки пересечения рисок
(рис. 105).
1,2 |
3 |
I |
III |
|
2 |
|
|
1 |
|
3 |
II |
5 |
|
1 |
|
6
Рис. 105. Скрытая база
Схема базирования – схема расположения опорных точек на базах заготовки или изделия (рис. 106).
|
4 |
|
5 |
|
6 |
|
|
|
6 |
|
4,5 |
1 |
2 |
3 |
I |
1,3 |
2 |
|
1 |
|
3 |
|
|
|
|
|
|
|
|
|
|
|
6 |
|
|
|
|
2 |
|
|
|
|
|
|
|
III |
|
4 |
II |
5 |
|
|
|
|
|
|
|
||
|
|
|
|
|
Рис. 106. Схема базирования призматической детали
Здесь I, II, III – базы детали, 1–6 опорные точки.
Все опорные точки на схеме базирования изображают услов-
409
ными знаками и нумеруют порядковыми номерами, начиная с базы, на которой располагается наибольшее количество опорных точек.
5.4. Производственные погрешности, причины возникновения, законы распределения
Любой ТП производства электронной аппаратуры характеризуется циклом последовательных операций изготовления деталей и сборочных единиц. На каждой операции неизбежно появляются некоторые колебания геометрических характеристик, режимов выполнения и физико-механических свойств материалов, которые отражают закономерности соответствующей операции и обусловлены комплексом случайных и систематических внешних и внутренних факторов, действующих в производстве. Они вызывают отклонение выходных параметров изделий.
Для нормального функционирования аппаратуры необходимо, чтобы отклонения параметров деталей, сборочных единиц и всего устройства в целом от номинальных находились в пределах, заданных в технической документации. Степень соответствия параметров изготовленных изделий установленным допускам определяет их технологическую точность.
Анализ точности производственного процесса позволяет для каждой технологической операции вскрыть причины возникновения производственных погрешностей, обосновать границы технологического допуска, правильно настроить ТП и выбрать экономичный метод достижения требуемой точности.
Под производственными погрешностями понимают отклонения параметров от номинальных данных, указанных в чертежах, нормалях, ТУ и другой технической документации, которые возникают при изготовлении деталей и сборочных единиц РЭА. Границы изменения параметров в процессе производства определяют технологические допуски, которые рассчитываются и устанавливаются заранее. В зависимости от того, какие параметры изделий они ограничивают, различают механические (геометрические) и электрические допуски.
Производственные погрешности подразделяются на систематические, которые вызываются детерминированными причинами и могут быть постоянными во времени или изменяться в пределах партии по определенному закону, и случайные, изменение величины и знака которых носит статистический характер.
410
Систематические погрешности вызываются следующими основными причинами:
1)методическими, которые возникают из-за ограниченных возможностей метода изготовления детали или контроля ее параметров, замены точных формул приближенными при технологических расчетах;
2)неточностью изготовления оснастки и рабочего инструмента;
3)деформацией и износом оборудования, оснастки и инстру-
мента;
4)температурными воздействиями на деталь или сборочную единицу в зоне обработки.
Случайные производственные погрешности определяются:
1)неоднородностью сырья и отклонениями параметров комплектующих изделий (резисторов, конденсаторов, транзисторов, ИС и др.);
2)колебаниями технологического режима обработки;
3)субъективными данными рабочих и т.д.
Для описания производственных погрешностей используются следующие законы распределения: Гаусса, равновероятный, обобщенный типа А (Шарлье), эксцентриситета, экспоненциальный, некруглости, модуля разности и др.
Распределение производственных погрешностей подчиняется закону Гаусса при соблюдении следующих условий:
1)общая погрешность представляет сумму частных погрешностей, вызванных действием значительного числа случайных факторов и некоторого числа первичных систематических факторов;
2)среди частных погрешностей нет доминирующих, т.е. влияние на общую погрешность одного порядка;
3)все случайные факторы взаимно независимы;
4)число случайных факторов и параметры вызванных ими частных погрешностей не изменяются во времени;
5)число систематических факторов и значения вызванных ими частных погрешностей остаются одинаковыми.
Такие условия создаются при массовом производстве деталей и сборке аппаратуры на автоматически работающем оборудовании.
Если среди причин, вызывающих производственные погрешности, имеется резко доминирующий фактор (например, износ ин-
411

струмента), равномерно изменяющийся во времени, то полное рассеивание отклонений одной производственной партии соответствует закону равной вероятности (рис. 107).
f(x)
Sn
bM(x) c
x
Рис. 107. Кривая распределения случайной величины, подчиняющейся закону равной вероятности
Плотность распределения закона равной вероятности описывается уравнением
f (x) = 1/(c − b), |
(56) |
где с и b – границы изменения значений случайной величины.
Этот закон характеризуется также двумя параметрами – средним значением и среднеквадратическим отклонением. Полное поле рассеивания погрешностей для закона равной вероятности при
Р = 0,9973
Sn = 3, 464σ . |
(57) |
Когда распределение производственных погрешностей значительно отличается от гауссовского, применяется обобщенный закон типа А (на рис. 108, 109 пунктирной линией показана кривая нормального закона распределения). Аналитическое выражение плотности распределения обобщенного закона типа А имеет вид
f |
A |
(x) = f (x) − |
r3 |
f III (x) + |
r4 − 3 |
f IV (x), |
(58) |
|
|
||||||
|
6 |
24 |
|
|
|||
|
|
|
|
412

где f(x) – |
плотность распределения нормального |
закона; f III (x), |
|
f IV (x) |
– |
производные третьего и четвертого |
порядков f(x); |
r3 , r4 – |
основные моменты третьего и четвертого порядков. |
f(x)
2
1
M(x)
x
Рис. 108. Кривые плотности вероятности с положительным (1) и отрицательным (2) коэффициентом асимметрии
f(x)
1
2
M(x) x
Рис. 109. Кривые плотности вероятности с положительным (1) и отрицательным (2) эксцессом
Обобщенный закон типа А характеризуется четырьмя параметрами: средним значением М(х), среднеквадратическим отклонением σ , коэффициентом асимметрии (мера косости) α и эксцессом
413
(мерой крутости) τ . Последние два параметра определяются по формулам
α = r3; |
(59) |
τ = r4 − 3. |
(60) |
Полное поле рассеивания погрешностей случайной величины для обобщенного закона типа А находится из равенства
Sn = tσ , |
(61) |
где t – безразмерная дробь, которая определяется по таблицам математической статистики в зависимости от величины и знака эксцесса τ .
5.4.1. Точность обработки. Производственные погрешности
На рабочих чертежах деталей, операционных эскизах и других технических документах размеры указывают в виде номинального
значения и допустимых отклонений, например: D−+ba , где D – номинальное значение размера; а – верхнее отклонение; b – нижнее отклонение. Разность верхнего и нижнего отклонений называют допуском δ = a − (−b) = a + b .
Номинальные значения размеров определяют при конструировании деталей теоретическим расчетом и округляют до ближайших целых значений, нормированных ГОСТ 6636–69.
Применение стандартных номинальных значений размеров дает возможность ограничить номенклатуру режущего и измерительного инструмента в производстве изделий, сократить потребляемый ассортимент материалов, а следовательно, снизить расходы на изготовление деталей.
Весьма важными геометрическими параметрами являются отклонения формы и расположения поверхностей деталей. К числу таких параметров относятся неплоскостность, непрямолинейность, некруглость, несимметричность, несоосность и др. Определение этих параметров и их допустимые отклонения нормированы ГОСТ 10366–63. Номинальные значения этих параметров приняты равными нулю, и в стандарте нормированы только их предельные отклонения. Детали, имеющие отклонение действительных
414
геометрических параметров в пределах допусков, предусмотренных чертежом, считаются годными и направляются на сборку. Детали, действительные геометрические параметры которых выходят за пределы допусков, указанных в чертеже, считаются браком производства и к сборке не допускаются.
Геометрическая точность деталей радиоэлектронной аппаратуры является весьма важным количественным критерием оценки их качества. Как известно, назначаемая при конструировании точность размеров определяется служебной функцией детали в изделии и в ряде случаев необходимостью обеспечения взаимозаменяемости и экономической эффективности производства.
В основе технологических операций обработки, как правило, лежит теоретическая модель процесса, однако реальное исполнение процесса всегда отличается от теоретического вследствие целого ряда внешних воздействий, т.е. причин, вызывающих отклонение реального процесса от теоретического. Применительно к способам обработки изделий на металлорежущих станках эти причины называют технологическими факторами, а их влияние на результаты формирования обрабатываемых поверхностей – погрешностью обработки. Таким образом, технологические факторы являются причинами, а погрешность обработки – следствием, сопровождающим всякий технологический процесс формообразования деталей. Однако необходимо отметить, что функциональная зависимость между погрешностью обработки как следствием и технологическими факторами как причинами не всегда может быть выражена аналитически, и это создает определенные трудности в проектировании и организации процессов формообразования деталей – процессов обработки.
Процессы обработки деталей на металлорежущих станках сопровождаются большим количеством технологических факторов, влияющих на точность обработки, изучению которых посвящены труды многих советских ученых: Н. А. Бородачева, А. П. Соколовского, А. Б. Яхина, В. С. Корсакова, А. И. Гаврилова, А. Н. Малова
имногих других.
Вобщем виде технологические факторы могут быть разделены на три группы:
1) факторы, обусловленные неточностью функциональных узлов и деталей технологического оборудования и оснастки;
415
2)факторы, обусловленные упругими деформациями деталей системы СПИД;
3)факторы, обусловленные отклонениями в регулировании и управлении технологической системой.
Основные технологические факторы при обработке на металлорежущих станках:
1)отклонение геометрической формы рабочих поверхностей шпинделя станка (некруглость, отклонение профиля в продольном сечении), направляющих станины (неплоскостность, непараллельность);
2)отклонение во взаимном расположении рабочих поверхностей шпинделя и станины (непараллельность, неперпендикулярность);
3)деформация изгиба основных деталей станка под воздействием внешних сил во время работы;
4)отклонение геометрических параметров формы и расположения рабочих поверхностей режущего инструмента;
7) неточность установки детали в позицию обработки;
6)изменение размеров инструмента под воздействием тепла, выделяемого в зоне резания;
7)неточность установки детали в позицию обработки;
8)упругая деформация заготовки под воздействием сил связи, сил резания, сил, вызываемых неравномерностью внутренних напряжений, и др.;
9)погрешность настройки режущего инструмента на исполняемый размер;
10)неточность измерительных инструментов;
11)ошибки при измерении операционного размера;
12)изменение в процессе обработки геометрических параметров инструмента вследствие износа и др.
Здесь приведен неполный перечень первичных технологических факторов, свойственных процессам обработки резанием. Многие из этих факторов присущи и другим способам обработки, таким как холодная штамповка, обработка ультразвуком, электроискровая обработка и др. Таким образом, для достижения высоких классов точности (квалитетов) и шероховатости поверхностей необходимо свести к минимуму влияние технологических факторов. Эта задача
416
решается созданием металлообрабатывающих станков и технологической оснастки высокой точности, применением автоматических измерительных устройств, управляющих положением режущего инструмента относительно обрабатываемой поверхности (средства активного контроля), применением расчетов технологических операций на точность.
При проектировании технологических процессов, а также при освоении производства новых деталей необходимо знать ожидаемую погрешность обработки. Для расчета ожидаемой погрешности обработки применяются два метода: аналитический и математической статистики. Оба метода предполагают следующие виды производственных погрешностей: систематические постоянные, систематические переменные, случайные.
Систематические постоянные производственные погрешности заметно не изменяются во времени, например, вызванные некруглостью (эллипсностью или огранкой) рабочих шеек шпинделя станка; неточностью координат отверстий, направляющих втулок кондуктора и т.п.
Систематические переменные, производственные погрешности изменяются по величине и направлению в процессе каждого цикла обработки, например, вызванные износом режущего инструмента. В некоторых случаях числовые значения систематических погрешностей могут быть заранее рассчитаны аналитически или обнаружены соответствующими измерениями. А это почти всегда означает, что их можно устранить полностью или частично.
Случайные производственные погрешности возникают в результате не всегда известных факторов, их числовое значение и время появления определить не всегда возможно. К числу таких погрешностей можно отнести погрешность установки детали на станке, рассеяние диаметров отверстий, обработанных одной разверткой, рассеяние размеров детали, прессуемой в одной пресс-форме, и др. Определение влияния действия случайных производственных факторов на погрешность (точность) обработки достигается методом математической статистики.
5.5. Влияние шероховатости поверхностей на точность изделия
417
К числу показателей качества деталей относят параметры, характеризующие состояние микрогеометрии поверхности: среднее арифметическое отклонение профиля Ra; высоту неровностей профиля по десяти точкам Rz; наибольшую высоту профиля Rmax; средний шаг неровностей по средней линии Sm; средний шаг неровностей по вершинам профиля 5; относительную опорную длину профиля tp. Определение параметров и их числовые значения для различных классов шероховатости поверхности даны в ГОСТ 2789–73, здесь же нормированы типы неровностей (преобладающие направления следов инструмента на поверхности). В ГОСТ 2.309–73 установлены стандартные обозначения шероховатости поверхности на чертежах деталей.
Степень (класс) шероховатости рабочих поверхностей детали оказывает существенное влияние на такие эксплуатационные свойства, как износостойкость, электропроводность, отражательная способность, сопротивление коррозии, адгезия и т.п.
Влияние шероховатости на износ трущихся поверхностей деталей. В начальный период работы τп износ поверхностей весьма интенсивен. После окончания периода приработки шероховатость поверхностей уменьшается и интенсивный износ прекращается – наступает длительный период нормального износа τн, за которым следует интенсивный износ – разрушение τp . Однако сниже-
ние шероховатости поверхностей с целью повышения их износостойкости оправдывается не всегда. В некоторых случаях наилучшие условия для смазки и уменьшения износа обеспечиваются определенной оптимальной шероховатостью.
Влияние шероховатости на коррозию. Коррозия протекает наиболее активно во впадинах рельефа, она интенсивно распространяется по микротрещинам в глубь металла, что приводит к разрушению поверхностного слоя. Снижение шероховатости замедляет течение коррозии.
Влияние шероховатости на усталостную прочность. Со-
противление металлических деталей разрушению под действием переменной нагрузки возрастает с уменьшением шероховатости поверхности. Усталостная прочность хорошо отполированной детали из легированной стали на 30–40 % выше, чем у грубо обработанной. Глубокие царапины, риски и трещины ослабляют поверхностный слой металла, снижают его усталостную прочность.
418