
Учебник по Технологии
.pdfмых при испытании. Для изделий, предназначенных для работы в сочлененном состоянии, необходимость испытания в этом состоянии указывают в стандартах и ТУ на изделия и ПИ. Изделия, предназначенные для применения в микромодулях, испытывают в составе условного микромодуля, если другие условия не указаны в стандартах и ТУ на изделия и ПИ. Если масса, габаритные размеры и конструкция изделий не позволяют испытывать их в полном комплекте, то осуществляют испытания отдельного блока. Если последовательность испытания блоков не позволяет проверять соответствие изделий требованиям ТЗ или стандартов и ТУ на изделия, то испытания электрически связанных между собой блоков проводят одновременно при размещении их в нескольких камерах или на нескольких стендах. Изделия, состоящие из нескольких блоков (узлов), находящихся в неодинаковых условиях эксплуатации, испытывают раздельно по нормам, соответствующим условиям эксплуатации этих блоков (узлов).
Если масса и габаритные размеры изделия не позволяют провести его испытания на существующем оборудовании и изделие после изготовления не может быть разобрано на блоки, то такие изделия оцениваются по специальной программе, согласованной с заказчиком.
При испытании изделий с собственными амортизаторами на устойчивость и прочность при воздействии синусоидальной или широкополосной случайной вибрации в диапазоне частот 0,7–1,4 от резонансной частоты колебаний изделий на амортизаторах допускается:
∙уменьшать амплитуду перемещения или ускорения таким образом, чтобы ускорение, воздействующее на само изделие, установленное на амортизаторах, соответствовало требованиям, предъявляемым к изделию в целом. В этом случае контрольную точку располагают на изделии и ее положение указывают в стандартах и ТУ на изделия и ПИ;
∙испытывать изделия без амортизаторов (с отключенными амортизаторами) по нормам, предъявляемым к изделию.
По согласованию с заказчиком при наличии в изделии элементов на подвеске допускается уменьшать амплитуду ускорения или исключать испытание изделия на резонансных частотах элементов на упругой подвеске, если в стандартах и ТУ на изделия указаны резонансные частоты этих элементов.
518
Применяемые виды механических испытаний и их последовательность указываются в ПИ и зависят от назначения РЭС, условий эксплуатации, типа производства. Например, в программу определительных испытаний опытного образца и образцов установочной серии обычно включают все виды механических испытаний, а для образцов, изготовляемых в серийном производстве, – только испытания, предусмотренные в стандартах и ТУ на РЭС.
Надежная работа РЭС обеспечивается за счет конструктивных запасов по вибропрочности, виброустойчивости, резонансной частоте и другим характеристикам. Конструктивный запас РЭС по резонансной частоте оценивается коэффициентом конструктивного запаса
Kз = fн / fв,
где fн – наименьшая резонансная частота испытываемого изделия; fв – верхняя частота рабочего диапазона, заданная в НТД. Из формулы видно, что чем выше наименьшая резонансная частота, тем больше Kз и, следовательно, выше вибропрочность при равных рабочих условиях.
Внешние механические воздействия подробно рассмотрены в гл. 2, а методы испытаний – в ГОСТах.
6.4.4. Испытание радиоэлектронных средств на климатические воздействия
Испытание РЭС (изделия) на воздействие климатических факторов проводят для проверки способности изделий выполнять свои функции, сохранять параметры и (или) внешний вид в пределах установленных норм при воздействии климатических факторов. Для воспроизводимости результатов испытания необходимо его полное
иточное описание, исключающее всякую неопределенность толкования. Исходя из этого в НТД принята такая последовательность операций (этапов) испытания РЭС на климатические воздействия: предварительная выдержка изделий (стабилизация их свойств); первоначальные измерения параметров и внешний осмотр; установка изделий в камеры и выдержка их в условиях испытательного режима; извлечение из камер и выдержка для восстановления свойств изделий (конечная стабилизация свойств); внешний осмотр
изаключительные измерения параметров изделий.
519
Предварительную выдержку проводят с целью полного или частичного устранения последствий воздействия на изделия в предыдущих условиях эксплуатации. Изделия выдерживают, как правило, в нормальных климатических условиях. Выдержку изделий, на результаты измерения параметров которых может существенно влиять относительная влажность, выполняют в условиях, обеспечивающих воспроизводимую толщину влаги, адсорбированной на поверхности изделий. Эти условия предусматривают строгое поддержание температуры (допустимое отклонение ±1 ° С) при относительной влажности 73–77 %. Продолжительность предварительной выдержки определяется временем, достаточным для установления теплового равновесия изделий с окружающей средой. Обычно оно не превышает 2 ч. Первоначальные и заключительные измерения параметров изделий рекомендуется проводить при одних и тех же значениях температуры и влажности окружающей среды.
При установке изделий в камере климатических испытаний необходимо следить за тем, чтобы между изделиями и стенками камеры, а также между самими изделиями свободно циркулировал воздух. Способ установки и положение изделий при испытании имеют важное значение для воспроизводимости его результатов. Если при эксплуатации возможно несколько вариантов положения изделия, то следует выбрать вариант, обеспечивающий наибольшую жесткость испытания. Если в процессе испытания электрическая нагрузка на РЭС не подается, изделия располагают на сетках из капроновых нитей, натянутых на опоры. При испытании с электрической нагрузкой изделия устанавливают на специальных платах, приспособлениях (кассетах, держателях, контактирующих устройствах). Металлические части приспособлений обязательно должны иметь антикоррозионные покрытия. Время выдержки в испытательном режиме отсчитывают с момента установления режима в камере. Это время при повышенной (пониженной) температуре должно быть достаточным для прогрева (охлаждения) изделий по всему объему.
Изделия в выключенном состоянии считаются достигшими температуры окружающей среды (теплового равновесия), если температура самых массивных частей (или других частей, указанных в ПИ и ТУ), определяющих прогрев по всему объему, отличается от температуры окружающей среды не более чем на ±3 ° С. Время прогрева (охлаждения) изделий по всему объему устанавливают на этапе предварительных испытаний с помощью датчиков для кон-
520
троля температуры. Допускается не контролировать температуру частей аппаратуры, если эти части не имеют защиты, предназначенной для теплоизоляции. В этом случае изделие в зависимости от массы выдерживают для достижения температуры окружающей среды: 2 ч – при массе изделия не более 2 кг; 3 ч – 2–10 кг; 4 ч – 10–20 кг; 6 ч – 20–50 кг; 8 ч – 50–100 кг; 10 ч – 100–300 кг.
Требования к объему камеры в зависимости от размеров испытываемой аппаратуры и значения теплорассеивания с единицы ее поверхности устанавливают с учетом рекомендаций государственных стандартов.
Подвижные наземные изделия, смонтированные в кузовах автомобилей, прицепов и других средствах передвижения, испытывают вместе со средствами передвижения.
При невозможности измерения параметров изделия без извлечения из испытательной камеры при различных видах испытаний допускается проводить эти измерения вне камеры. Методика и время измерения параметров после извлечения из камеры оговариваются в ПИ и ТУ на изделие.
Воспроизводимость результатов испытания в значительной мере зависит от точности поддержания заданных параметров испытательного режима. Допуски на значения воздействующих факторов выбирают исходя из компромисса между точностью испытания, с одной стороны, и стоимостью его – с другой. При испытании на влагоустойчивость допуски на температуру и относительную влажность воздуха в камере устанавливают равными соответственно ±2 ° С и ±3 %. При определении указанных допусков учитывают неравномерность распределения температуры по объему камеры, погрешность измерения ее приборами, а также изменение температуры во времени. При верхнем значении температуры 40 ° С и относительной влажности воздуха 90 % изменение температуры на 2 ° С приводит к изменению относительной влажности на 9 %. При высокой относительной влажности даже незначительное изменение температуры может привести к выпадению росы (неконтролируемый процесс), что в свою очередь существенно снижает воспроизводимость результатов испытания. Допустимые отклонения воздействующих климатических факторов не должны превышать значений, указанных в табл. 38, если в НТД не указаны иные допускаемые отклонения, обусловленные спецификой эксплуатации изделий.
521
Таблица 38
Допустимое отклонение воздействующих климатических факторов
Воздействующий фактор |
Допустимое |
|
отклонение |
||
|
||
1 |
2 |
|
Температура, ° С: |
|
|
-200... -85 |
|
|
±5 ° С |
||
-85...+ 100 |
|
|
+2 ° С |
||
100...200 |
|
|
±5 ° С |
||
свыше 200 |
|
|
±10 ° С |
||
|
|
|
Скорость изменения температуры окружающей среды, |
|
|
° С/мин: |
|
|
1-5 |
±20 % |
|
5-10 |
|
|
±50 % |
||
|
|
|
Относительная влажность по ТУ |
±3 % |
|
|
|
|
Пониженное давление: |
|
|
выше 1,33×102 Па (1 мм рт. ст.) |
±5 % или 1,33×102Па* |
|
1,33×102-1,33 Па (102 мм рт. ст.) |
|
|
+60 % |
||
ниже 1,33 Па |
|
|
±30 % |
||
|
|
|
Повышенное избыточное давление |
±20 % |
|
|
|
|
Солнечное излучение: |
|
|
- интегральная плотность потока по ТУ |
±10 % |
|
- плотность потока ультрафиолетовой |
|
|
±25 % |
||
- температура по ТУ, Вт×м−2 |
|
|
±40 |
||
|
|
|
Интенсивность дождя, кг/м−2 |
± 25 |
|
Массовая концентрация пыли по ТУ, г/л−1 |
± 10 |
|
Скорость ветра по ТУ, м/с−1 |
±10 |
|
Массовая концентрация коррозионно-активных |
±10 |
|
агентов среды по ТУ г/л−1 |
||
|
* Допустимое отклонение в паскалях берется в том случае, если оно больше допустимого отклонения в процентах.
Внешний осмотр изделий осуществляют в соответствии с НТД. Климатические испытания проводят не только на стадии проектирования РЭС, но и в серийном производстве для отбраковки потенциально ненадежных изделий (приемосдаточные испытания) и для контроля стабильности производства (периодические испытания). Режимы и условия испытания РЭС устанавливают в зависи-
522

мости от степени жесткости, которая в свою очередь определяется условиями дальнейшей эксплуатации РЭС в составе системы. Изделия считают выдержавшими испытание, если они во время и после его проведения удовлетворяют требованиям, заданным в ПИ и ТУ для данного вида испытаний.
Для повышения информативности и эффективности климатических испытаний при освоении и производстве изделий целесообразно проводить их последовательности, при которых каждое последующее испытание усиливает воздействие предыдущего, которое могло бы остаться незамеченным. Рекомендуется так назы-
ваемая нормализованная последовательность климатических ис-
пытаний, включающая испытание при повышенной температуре, кратковременное испытание на влагоустойчивость в циклическом режиме (первый цикл), испытания на воздействия пониженных температуры и атмосферного давления, испытание на влагоустойчивость в циклическом режиме (остальные циклы). При этом между любыми из указанных испытаний допускается перерыв не более 3 сут, за исключением интервала между испытаниями на влагоустойчивость и на воздействие пониженной температуры, который не должен превышать 2 ч. Параметры изделий обычно измеряют в начале и конце нормализованной последовательности.
Методы испытаний подробно описаны в ГОСТе.
6.4.5. Виды дефектов и способы их обнаружения
Для контроля качества пайки BGA при использовании технологии поверхностного монтажа стало широко распространенным использование рентгеновского излучения. Число поставщиков оборудования увеличилось, но средства рентгеновского контроля не продвинулись дальше простых и очевидных дефектов, таких как пропущенные выводы и неуместные пустоты пайки (рис. 125).
«Слияние» |
«Отсутствующие выводы» «Пустоты пайки» |
Рис. 125. Основные виды дефектов
523

Рассмотрим концепцию рентгеновского контроля с «идентификацией подписи» как расширение обычной рентгеновской проверки за рамки набора вышеупомянутых дефектов. Эту своего рода «полноценность» можно достичь, если лучше понять, как рентгеновские изображения связаны с процессами сборки и пайки. Кроме того, идентификация подписи может обеспечивать быструю и эффективную рентгеновскую проверку качества пайки BGA даже при очень скромных затратах на оборудование рентгеновского контроля.
Для понимания рентгеновских снимков надо досконально знать объект изучения. Рассмотрим анатомические особенности, которые следует знать перед изучением рентгеновских изображений.
1. Тип корпуса даст информацию об ожидаемых тепловых эффектах, таких как тепловое расширение, теплоемкость и тенденции к деформации. Если во время пайки что-то пошло не так, то будет отчетливо наблюдаться физическая деформация PBGA (рис. 126).
Деформация может быть обнаружена на рентгеновском снимке.
«Plastic BGA» |
«Super BGA» |
«Ceramic BGA»
«Tab BGA»
Рис. 126. Виды физической деформации
524

2. Паяльная паста.
Если используется паяльная паста, то могут возникнуть проблемы, связанные с ее избытком или недостатком. Это будет видно на рентгеновском изображении.
3. Конструкция печатной платы.
Платы с высокой теплоемкостью во время пайки могут подвергаться тепловому расширению, что можно наблюдать на рентгеновском снимке.
Автор сделал запись процесса пайки в рентгеновском диапазоне в режиме реального времени. Три стадии пайки показаны на рис. 127.
Стадия А |
Стадия Б |
Стадия В |
Рис. 127. Основные этапы пайки
Стадия А. В результате размещения компонентов происходит полное или частичное выравнивание BGA относительно выводов платы.
525

Стадия Б. В течение начального таяния шары припоя начнут смачивать выводы, и только когда все шары расплавятся, корпус будет точно выровнен относительно выводов.
Стадия В. Полное слияние. После выравнивания там, где выводы полностью смочены, может наблюдаться полное слияние.
6.4.6. Описание стадий пайки и их связь
срентгеновскими изображениями
1.На стадии А (предварительный нагрев) зазор между корпусом и платой равен высоте шара, а диаметр рентгеновского изображения шара равен номинальному диаметру шара.
2.На стадии Б (начало слияния) зазор между корпусом и платой составляет около 80 % от начальной высоты шара.
3.На стадии В (полное слияние) зазор между корпусом и платой приближается к 50 % от начальной высоты шара, диаметр рентгеновского изображения шара будет увеличен на 17 %, а площадь увеличится на 37 % от начальной.
Изменение размеров и формы рентгеновских изображений шаров после пайки является ключом к пониманию значения конечного рентгеновского изображения.
Однородность.
На этом этапе можно с уверенностью сказать, что если изображения всех выводов на рентгеновском снимке однородны и являются равными окружностями (допуск 10–15 %), то существует очень хорошая вероятность отсутствия дефектов пайки (рис. 128).
Рис. 128. Однородность пайки BGA
526
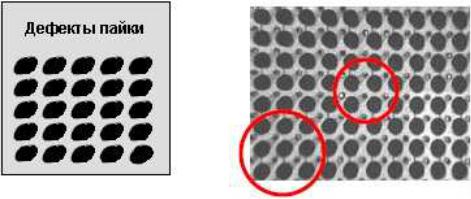
Однородность является первой и наиболее важной характеристикой при использовании рентгеновского контроля, позволяющей быстро квалифицировать качество пайки BGA.
Наличие неоднородностей на рентгеновском изображении BGA может носить как случайный характер, так и иметь вид некоторого образца. И случайный, и шаблонный варианты указывают на возможный дефект или проблему, а также на то, что ее вызвало.
Подписи и их значение.
Поняв это, мы сможем, глядя на некоторые рентгеновские подписи, судить о том, что пошло неправильно в процессе монтажа.
1. Дефекты пайки.
Если качество пайки невысокое, то можно наблюдать большое количество «подписей» (рис. 129). Если BGA после размещения точно не совмещен с выводами, то могут наблюдаться эллиптические соединения. Во время начальной стадии таяния припой будет смачивать вывод, создавая эллиптическое изображение, пока не наступит полное выравнивание.
Рис. 129. Дефекты пайки
Если необходимое качество пайки не достигнуто, то полного выравнивания не произойдет и некоторые или даже все изображения окажутся эллиптическими. Эллиптическое изображение наблюдается, когда вывод платы не совмещен с выводом BGA.
2. Соединение холодным припоем.
«Подпись» холодного припоя – это одно из увеличенных изображений соединения с неровными гранями (рис. 130).
527