
- •Учебник подготовлен в рамках Инновационной образовательной программы
- •ISBN 978-5-7262-0821-3
- •ISBN 978-5-7262-0978-4 (т. 4)
- •15.1. Мольный термодинамический потенциал Гиббса
- •15.2. Система уравнений равновесия двух фаз
- •15.4. Различные трактовки системы уравнений равновесия
- •15.6. Термодинамическая теория фазовых переходов 1-го рода
- •15.7. Феноменологический метод описания фазовых переходов
- •15.8. Методы расчета параметров стабильности чистых
- •15.10. Инвариантность решений системы уравнений фазового
- •15.12.1. Обобщение правила равенства площадей Максвелла
- •15.12.2. Обобщение правила равенства площадей Максвелла
- •15.14. У-алгоритм расчета равновесия двух неизоморфных
- •15.18. Одно/двухфазные α/α+β или β/α+β фазовые границы
- •15.21. Анализ трехфазных равновесий в двухкомпонентных
- •системах. Расчет энтальпии трехфазной реакции T–p–x
- •Глава 11. ФИЗИКА ПРОЧНОСТИ МАТЕРИАЛОВ
- •11.1.1. Основные понятия
- •11.1.2. Напряжения и деформации
- •11.1.3. Диаграмма растяжения: характерные точки
- •11.2. Упругость
- •11.2.1. Закон Гука для случая одноосной деформации
- •11.2.3. Закон Гука в обобщенном виде
- •11.2.4. Модули и коэффициенты упругости
- •11.3. Процессы пластической деформации
- •11.3.1. Кристаллографическое скольжение
- •11.3.2. Фактор Шмида
- •11.3.4. Начало пластической деформации
- •11.3.6. Взаимосвязь величин сдвиговой деформации
- •11.3.7. Стадии деформационного упрочнения
- •11.3.8. Теории дислокационного упрочнения
- •11.3.9. Текстуры деформации и текстурное упрочнение
- •11.3.10. Двойникование как механизм деформации
- •11.3.15. Возникновение зуба текучести
- •11.4. Ползучесть
- •11.4.1. Неупругая обратимая ползучесть
- •11.4.2. Логарифмическая ползучесть
- •11.4.3. Высокотемпературная ползучесть
- •11.4.4. Диффузионная ползучесть
- •11.4.5. Характеристики ползучести
- •11.5. Разрушение
- •11.5.1. Основные виды разрушения
- •11.5.2. Зарождение трещины
- •11.5.7. Схема Иоффе перехода из хрупкого
- •11.5.8. Особенности охрупчивания ОЦК металлов
- •11. 6. Усталость материалов
- •11.6.1. Общие характеристики явления
- •11.6.2. Особенности протекания пластической деформации при циклическом нагружении
- •11.6.4. Влияние различных факторов на усталость
- •Контрольные вопросы
- •Список использованной литературы
- •Введение
- •Контрольные вопросы
- •Глава 13. РАДИАЦИОННАЯ ФИЗИКА ТВЕРДОГО ТЕЛА
- •Введение
- •13.5.2. Низкотемпературное радиационное охрупчивание
- •Влияние облучения на стали. Наиболее важным требованием к конструкционным материалам в процессе длительного облучения является стабильность их физических и механических свойств. Поэтому пригодность той или иной стали для изготовления узлов и деталей активной зоны атомного реактора может быть обоснована только после определения ее свойств в нейтронном поле.
- •На рис. 13.46 показаны начальные участки кривых растяжения нескольких монокристаллических образцов урана близкой ориентировки, облученных различными флюенсами (номера кривых соответствуют номерам на стереографической проекции выхода оси растяжения).
- •13.6.2. Механизмы радиационной ползучести
- •Контрольные вопросы
- •Глава 14. ОСНОВЫ КОМПЬЮТЕРНОГО МОДЕЛИРОВАНИЯ В КОНДЕНСИРОВАННЫХ СРЕДАХ
- •14.1. Задачи компьютерного моделирования

ны надреза, и последующее измерение деформации каждой из ячеек. Экспериментальным путем установлено, что в пластичных материалах зона пластической деформации может простираться от плоскости движения трещины вглубь материала на расстояние до 2–3 мм, а в хрупких – всего лишь до 10–20 мкм. Причем и размеры, и форма этой зоны в одном и том же изделии с развитой кристаллографической текстурой существенно изменяются в зависимости от ориентации трещины, что особенно заметно в металлических материалах с ГПУ решеткой, характеризующихся повышенной анизотропией свойств.
Применение рентгеновских методов исследования1 при послойном анализе поверхностей разрушения позволяет оценить искаженность кристаллической решетки и выявить другие структурные изменения в пределах зоны пластической деформации, сопряженной с движением трещины и развитием разрушения. Учитывая, что поверхность разрушения формируется при прохождении волны пластической деформации, идущей впереди трещины, структуру слоев, прилегающих к поверхности разрушения, следует рассматривать как результат суперпозиции эффектов, обусловленных последовательным положением вершины трещины на разных расстояниях от данного участка.
11.6. Усталость материалов
11.6.1.Общие характеристики явления
Под действием циклических напряжений в металлических материалах зарождаются и постепенно развиваются трещины, в конечном итоге вызывающие разрушение детали или образца. Такое разрушение особенно опасно потому, что может протекать под действием напряжений, намного меньших пределов прочности и текучести. Более 80% всех случаев эксплуатационного разрушения материалов происходит в результате их циклического нагружения.
Процесс постепенного накопления повреждений в материале под действием циклических нагрузок, приводящий к изменению
1 Физическое материаловедение. Т. 3. – М.: МИФИ, 2007. П. 8.6 – 8.9
123
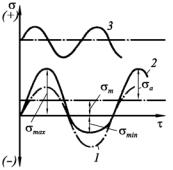
его свойств, образованию трещин и разрушению, называют усталостью, а способность противостоять усталости – выносливостью.
Усталостная трещина зарождается в поверхностных слоях и развивается вглубь материала, образуя острый надрез. Распространение усталостной трещины обычно длительно и продолжается до тех пор, пока сечение детали не окажется столь малым, что действующие в нем напряжения превысят разрушающие. Тогда происходит быстрое разрушение, как правило, хрупкое, из-за наличия острого надреза.
Для количественной оценки способности материала работать без разрушения в условиях циклического нагружения проводят ус-
талостные испытания.
Методы испытаний на усталость разнообразны и отличаются характером изменения напряжений во времени, схемой нагружения (изгиб, растяжение – сжатие, кручение), наличием или отсутствием концентраторов напряжений. Усталостные испытания проводятся при разных температурах и в разных средах.
Во время любого усталостного испытания на образец действуют циклические напряжения, непрерывно изменяющиеся по величине и часто по знаку. Типичные примеры используемых циклов напряже-
ний показаны на рис. 11.47.
Цикл напряжений – это совокупность переменных значений напряжений за один период их изменения. Для характеристики цикла используют несколько параметров: максимальное напряжение σmax, минимальное напряжение σmin, среднее напряжение цикла
σm= (σmax+σmin)/2, амплитуда напряжений σа=(σmax–σmin)/2, коэффициент асимметрии Rσ = σmin/σmax. Если Rσ = –1
(кривая 1 на рис. 11.47), то цикл называют симметричным; если напряжения изменяются по знаку, цикл называют знакопеременным (кривые 1 и 2), если только по величине – знакопостоянным (кривая 3). При усталостных испытаниях используют обычно симметричные знакопеременные циклы с Rσ = –1.
124

Наиболее распространенная схема нагружения при усталостных испытаниях – изгиб. Для испытаний в условиях циклического рас- тяжения–сжатия используют гидропульсационные и резонансные машины. В первых в качестве гидропульсатора используют однопоршневой насос, ход поршня которого устанавливают в соответствии с заданной амплитудой цикла. Резонансные машины осуществляют циклическое растяжение–сжатие с помощью вибрирующей системы, которая состоит из рессоры и массы, возбуждающей ее колебания. Результаты усталостных испытаний очень чувствительны к состоянию поверхностного слоя образца, так что для получения значимых результатов необходимо соблюдение идентичности методики подготовки образцов.
Первичным результатом усталостного испытания одного образца является число циклов до разрушения (долговечность) при заданных характеристиках цикла. По результатам испытаний серии образцов определяют предел выносливости σR – наибольшее значение максимального напряжения цикла, при действии которого не происходит усталостного разрушения образца после произвольно большого или заданного числа циклов нагружения. Каждый образец серии испытывают при определенном значении максимального напряжения цикла или его амплитуды. При этом циклы для всех образцов одной серии должны быть подобны, т.е. иметь одинаковую форму и отношение различных характеристик цикла. По результатам испытания отдельных образцов строят кривую усталости в координатах «максимальное напряжение цикла σmax (или σа) – долговечность N» (рис. 11.48, а) Наиболее наглядны кривые усталости в логарифмических координатах, как этовидно на рис. 11.48, б.
Рис. 11.48. Кривые усталости в различных координатах
125
По мере уменьшения максимального напряжения цикла долговечность всех материалов возрастает. Ордината, соответствующая постоянному значению σmax, и есть предел выносливости материала σR. Удобно оценивать σR также по кривым в координатах σmax – 1/N (рис. 11.48, в). Здесь предел выносливости определяют, экстраполируя кривую в точку ее пересечения с осью ординат, где 1/N = 0. Для металлов, у которых отсутствует горизонтальный участок на кривой усталости, определяют ограниченный предел выносливости
–наибольшее напряжение σmax, которое материал выдерживает, не разрушаясь в течение определенного числа циклов нагружения.
Это число циклов называют базой испытания и обычно принимают равным 108.
Иногда при наличии на кривой усталости горизонтального участка говорят о пределе усталости, а при отсутствии такого участка
–о пределе выносливости.
Кривые усталости, построенные при использовании циклов с Rσ = –1, для многих металлических материалов хорошо описывают-
ся уравнением Вейбулла: |
|
σmax = σR + а(N +B)- α , |
(11.113) |
где а, В, α – коэффициенты.
Различают испытания на многоцикловую усталость, где используются большие базы испытания и значительная частота нагружения (от 10 до 300 Гц), и испытания на малоцикловую усталость с базой испытания, не превышающей 5·104 циклов, при частоте не более 3 – 5 Гц. Граница между мало- и многоцикловой усталостью соответствует зоне перехода от упруго-пластического к упругому деформированию в условиях циклического нагружения.
При наличии концентраторов напряжения характеристики выносливости снижаются.
Важной характеристикой сопротивления усталости является скорость роста трещины при усталости dl/dN.
11.6.2. Особенности протекания пластической деформации при циклическом нагружении
По мере увеличения числа циклов при любых напряжениях выше предела выносливости в образце последовательно идут следующие процессы:
126
1)пластическая деформация;
2)зарождение трещин;
3)постепенное развитие некоторых трещин при преимущественном распространении главной;
4)быстрое окончательное разрушение.
Вусловиях циклического нагружения развитие пластической деформации начинается аналогично тому, как это происходит при обычном нагружении: движение отдельных дислокаций инициируется при напряжениях, меньших предела упругости материала, скольжение, прежде всего, начинается в благоприятно ориентированных зернах вблизи концентраторов напряжений в тех же кристаллографических плоскостях, что и при статической деформации. Однако развитие линий скольжения, начинающееся при напряжениях ниже предела выносливости, с увеличением числа циклов нагружения приостанавливается, что свидетельствует о проявлении деформационного упрочнения даже при весьма низком уровне напряжений. При повышении напряжения линии скольжения формируются с уменьшающейся частотой вплоть до усталостного разрушения, причем усталостные трещины зарождаются внутри полос скольжения.
Усталостные испытания монокристаллов показывают, что первая стадия упрочнения, связанная с действием моноскольжения, оказывается намного более продолжительной, чем при обычных испытаниях на растяжение. Это объясняется тем, что при циклическом нагружении не происходит направленного изменения ориентации монокристалла, поскольку повороты решетки в пределах одного цикла, включающего растяжение и последующее сжатие, в значительной мере взаимно компенсируются. Поэтому ориентации, отвечающие действию нескольких систем скольжения и повышенной скорости упрочнения, в случае циклического нагружения не достигаются, если они не являлись исходными.
Показано, что каждый цикл нагружения при усталостных испытаниях характеризуется петлей гистерезиса в пространстве координат напряжение–деформация (рис. 11.49). Так, при испытании монокристаллов Al было обнаружено, что ширина петли W с увеличением количества циклов N уменьшается в соответствии с зависимостью:
W = AN –q, |
(11.114) |
127

где А – постоянная и q – мера скорости деформационного упрочнения. Для кристаллов, деформирующихся вследствие их ориентации в одной системе скольжения, величина q меньше, чем для кристаллов с ориентацией, отвечающей двойному или множественному скольжению.
Типичная для усталостных испытаний петля гистерезиса является несимметричной (см. рис. 11.49). Если кристалл сначала подвергается сжатию (участок АВ), то кривая вскоре отходит от прямой линии, что свидетельствует о заметной пластической деформации в точке В. При разгрузке петля приходит в точку С по прямолинейному участку, соответствующему снятию упругой деформации. Однако при наложении растягивающего напряжения пластическая деформация возникает очень быстро, сразу же после перехода напряжения через нуль (участок СD). Это явление, характерное как для моно-, так и для поликристаллов, носит название эффекта Баушингера. Чем легче активизируется пластическая деформация при растяжении после предшествующего сжатия, тем меньше упрочнение, препятствующее развитию пластической деформации и тем шире петля гистерезиса.
Рис. 11.49. Петли гистерезиса, полученные при циклических нагружениях монокристалла алюминия после 8, 16 и 1280 циклов
Механизм эффекта Баушингера состоит, очевидно, в том, что в исходном состоянии материала присутствующие в нем дислокации и дислокационные источники как бы заблокированы взаимодейст-
128
вием с другими элементами структуры и для их «разблокирования» необходимо приложение определенного напряжения, соответствующего начальному полуциклу нагружения. Однако под действием второго полуцикла, следующего непосредственно за первым, освобожденные дислокации легче приходят в движение, не успев еще подвергнуться закреплению, что и определяет увеличение вклада необратимой пластической деформации в общую деформацию образца на этом этапе.
Материалы, у которых с увеличением числа циклов ширина петли гистерезиса уменьшается, называют циклически упрочняющимися, а те материалы, у которых ширина петли увеличивается, –
циклически разупрочняющимися. Если с ростом числа циклов ши-
рина петли гистерезиса практически не изменяется, материал назы-
вают циклически стабилизирующимся.
Циклическое упрочнение или разупрочнение металлических материалов связано с особенностями их пластической деформации, зависящими от исходной структуры. Чистые металлы и однофазные сплавы, характеризующиеся в отожженном состоянии высокой пластичностью и относительно низкой прочностью, являются циклически упрочняющимися. После сильной холодной деформации эти же материалы ведут себя как циклически разупрочняющиеся. Циклическое разупрочнение наблюдается также у высокопрочных сплавов, содержащих в структуре большое количество дисперсных выделений вторичных фаз.
Склонность материала к циклическому упрочнению или разупрочнению хорошо коррелирует с отношением σв/σ0,2: если (σв/σ0,2) < 1,2, то материал оказывается циклически разупрочняющимся; если (σв/σ0,2) > 1,4, то материал циклически упрочняется. При промежуточных значениях σв/σ0,2 материал ведет себя как циклически стабилизирующийся.
Знак упрочнения и усталостная повреждаемость металлических материалов обусловлены особенностями дислокационной структуры, формирующейся в условиях циклической деформации. Отличительный признак дислокационной структуры металлов после низкотемпературного циклического нагружения – многочисленные пороги и дислокационные петли, появляющиеся уже на начальных
129
этапах испытания. Это результат частых пересечений дислокаций и повышенной концентрации точечных дефектов, возникающих при движении дислокаций с порогами под действием переменных напряжений. С увеличением числа циклов образуются скопления петель и дислокаций со ступеньками, дислокационных сплетений, а затем формируются плоские малоугловые границы.
По мере роста числа циклов нагружения тонкие линии скольжения на поверхности превращаются в грубые полосы с необычным для статической деформации рельефом. Анализ профиля этих полос показывает наличие в них выступов и впадин. Если в случае статической деформации обнаруживающиеся на поверхности образца полосы скольжения могут быть удалены полировкой поверхности, то в случае циклического нагружения связанный с полосами скольжения рельеф оказывается более развитым, обнаруживая впадины глубиной до 30 мкм. Этим полосам скольжения соответствует специфическая дислокационная структура как в приповерхностных слоях, так и в объеме образца. В частности, для меди, подвергнутой циклическому нагружению, характерно образование дислокационных ячеек, вытянутых вдоль полос скольжения, и регулярное чередование областей с высокой и низкой плотностью дислокаций.
В целом, развитие пластической деформации при знакопеременном циклическом нагружении является много более сложным, чем при статическом нагружении. Все дислокационные механизмы деформации, разработанные применительно к статическому нагружению, модифицируются в условиях «раскачивания» исходной дислокационной структуры посредством попеременного приложения напряжений разных знаков и при создании противоположно направленных потоков дефектов. Повышение подвижности дислокаций при низких напряжениях за счет эффекта Баушингера способствует, в частности, более раннему возникновению условий для зарождения трещин при образовании дислокационных скоплений вблизи границ. Знакопеременное нагружение играет роль инструмента, позволяющего вновь и вновь активизировать движение одних и тех же дислокаций до тех пор, пока они не образуют конструкцию, характеризующуюся повышенной устойчивостью, или же петли, поры и трещины.
130

11.6.3. Зарождение и распространение усталостных трещин
Прямыми микроскопическими наблюдениями показано, что зародышами усталостных трещин являются поверхностные впадины в полосах скольжения. Для объяснения образования выступов и впадин на поверхности образцов при усталостных испытаниях предложен ряд возможных дислокационных механизмов.
Так, согласно механизму Коттрелла и Халла, впадины и выступы на поверхности образуются в результате последовательного действия источников, генерирующих дислокации в разных систе-
мах (рис. 11.50).
Рис. 11.50. Механизм образования поверхностных выступов и впадин при циклическом нагружении
Находящиеся в разных плоскостях источники М1 и М2 под действием прямого полуцикла генерируют дислокации, которые, выходя на поверхность, образуют ступеньки А и В. На обратном полуцикле источники генерируют дислокации противоположного знака, образующие ступеньки С и D. Так как при смене знака напряжений смещаются плоскости скольжения, по которым движутся дислокации от каждого источника, уничтожения ступенек А и В не происходит; напротив, за полный цикл на поверхности образуются выступ и впадина, растущие с увеличением числа циклов.
Согласно механизму Мотта выступы и впадины на поверхности образуются в результате кругового движения винтовых дислокаций, переходящих из одной плоскости в другую за счет поперечного скольжения под действием циклически изменяющихся напряжений (рис. 11.51). Если один конец дислокации выходит на поверхность, то в результате последовательного перехода дислокации АА' в положения BB', CC' и DD', объем, ограниченный контуром ABCD,
131
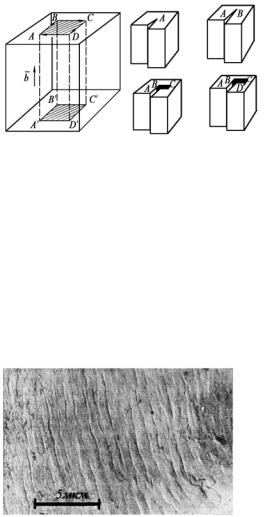
переместится вверх или вниз параллельно линии дислокации на расстояние, равное ее вектору Бюргерса, образуя выступ или впадину.
Рис. 11.51. Механизм образования впадины на поверхности при движении винтовой дислокации
Усталостные трещины зарождаются уже на начальных стадиях испытания и растут сначала за счет притока вакансий, в большом количестве возникающих при циклическом нагружении. Впадины в полосах скольжения могут достигать такой глубины, при которой их дальнейшее развитие идет в результате концентрации напряжений у дна впадины, оказывающегося в роли вершины трещины.
Вначале усталостные трещины распространяются вдоль полос скольжения, а затем растут перпендикулярно к направлению растягивающих напряжений, т.е. нормально к поверхности образца. Усталостные трещины развиваются скачками, которым отвечают бороздки на усталостном изломе, отражающие последовательные положения распространяющейся трещины (рис. 11.52).
Рис. 11.52. Усталостные бороздки в структуре излома
На начальных стадиях испытания в образце возникает множество трещин, но большинство их почти не развивается из-за упрочнения материала в примыкающих к трещинам объемах из-за концен-
132